- 1BioEnergy Engineering and Low Carbon Technology Laboratory, College of Engineering, China Agricultural University, Beijing, China
- 2School of Ecology and Environment, Zhengzhou University, Zhengzhou, China
- 3National Research Center for Environmental Analysis and Measurement, Beijing, China
- 4Violence and Injury Research Unit, SA Medical Research Council and Institute for Social and Health Sciences, University of South Africa, Tshwane, South Africa
- 5Unit for Environmental Sciences and Management, North-West University, Potchefstroom, South Africa
- 6School of Public Health, University of the Witwatersrand, Johannesburg, South Africa
- 7Key Laboratory of Clean Production and Utilization of Renewable Energy, Ministry of Agriculture and Rural Affairs, Beijing, China
- 8National Center for International Research of BioEnergy Science and Technology, Ministry of Science and Technology, Beijing, China
Usage of inefficient and unsafe cookstoves is a cause of significant health losses and injuries in low-income communities. Efforts to develop and disseminate clean cookstoves have concentrated on optimizing thermal and emission performance, but minimal attention was given to safety aspects. Discussions conducted by the ISO TC285 Technical Committee are ongoing on the derivation of a universal biomass cooking stove standard that aims to guide the development and marketing of products that are safe and efficient with clean burning. Under this, cooking stove safety guidelines addressing a range of hazards have been issued to the community of practice. This work critically addressed the current guideline on cooking stove stability by pointing out the inadequacy of the test and suggesting extra tests for an improved rating of a candidate stove. With a pot and fuel introduced to the research, there may be three different failure modes for various pot and stove combinations, which were tipping, sliding, or spilling. The tests were conducted on an inexpensive purposely built “tiltometer” that allowed testing the angles for stove tipping and sliding, as well as cooking pot sliding and spilling failure. The results indicated that tipping angles for a selected list of modern stoves varied widely based on different shapes and masses, from 18° to 72.2°. Also, the performance of the three different failure modes would place the same stove in different tiers by the current safety protocol. Theoretical geometric calculations for the tipping angle were conducted, and the relative errors were within 2.9%–12.7% for the three different orientations. It is suggested that a revision of the interim stove safety standard should be promoted to incorporate the findings of this study.
1 Introduction
A large number of the population in developing countries uses basic fuels and inefficient stoves for cooking and heating. Pollutant emissions and inherently unsafe natures of basic combustion technologies are causes of morbidity and mortality. The World Health Organization (WHO) estimates that household air pollution (HAP) from cooking fires results in the premature death of over 4 million people each year and illness of many more (Bruce et al., 2015). Missing from the WHO estimates are statistics for health losses and deaths associated with direct injuries from the cookstoves, including accidental fires, liquid and food burns, contact burns, scalds, and poisonings. The injuries related to safety failures of cookstoves are significant, especially in developing countries such as South Africa that have incorporated transitional liquid fuels in their energy mix (Kimemia et al., 2014). Research in China reports that stove burns accounts for 10% of a total of 115 patients, with a mortality rate of 1.11% (Gallagher et al., 2016). Another research study reports a total of 16,595 pediatric burns caused by bedside stoves in a certain region of China from January 1996 to December 2010 (Chen et al., 2014). Research on a kerosene stove explosion shows that more females will be affected as they are the main users at home (Ndaguatha et al., 2012). Research in South Africa reports that 70.0% of burns in children are caused by knocking the stove over (Parbhoo et al., 2010). Burns mainly occur when refueling (Neubrech et al., 2016; Nthumba, 2016), but injuries may also result from careless operations, making the stove tip (Stockhausen and Katcher, 2001); from this aspect, electrical stoves without flame may have this kind of failure (Still et al., 1998).
Historically, interest in improved stove development was motivated by the need to improve fuel efficiency, based on predictions that high fuel wood consumption will cause deforestation and escalated poverty (Kshirsagar and Kalamkar, 2014). The need to reduce emissions to safeguard humans and the environment arose later. As more safety issues have been reported, stove designers have to consider safety aspects in improved cookstoves alongside earlier goals for fuel efficiency and emission reduction. In recent years, technical challenges in the development of clean and user-friendly cookstoves have received greater attention from researchers, leading to a new generation of cooking stove designs (Sutar et al., 2015).
A key strategy in the achievement of the stove promotion goals is creating global standards for the safety, efficiency, and cleanliness of cookstoves. Widely accepted standards and testing protocols are needed to qualify advanced cookstoves as safe, efficient, and with clean burning (Kumar et al., 2013). However, there were no internationally accepted guidelines on the expected performance of a cooking stove. Discussions facilitated by the International Standards Organization (ISO) have led to the enactment of interim performance tiers, defined by the ISO International Workshop Agreement (IWA: 2012) (International Standards Organization, 2012). In this regard, standards for testing emissions and thermal performances have received much attention and are discussed in an advanced stage. However, the development of safety standards has received minor consideration, although an interim safety protocol has been suggested (Johnson, 2005; Johnson and Bryden, 2015; Kimemia and Van Niekerk, 2017). The safety testing of the IWA then developed into a “biomass stove safety protocol” (BSSP) (Global Alliance for Clean Cookstoves (GACC), 2015). According to Johnson and Bryden (2015), the safety tests are for solid fuel stoves. However, in the absence of an alternative, this protocol is also applied to cookstoves fired with liquid or gaseous fuels, or even electrical stoves.
There are 10 aspects included in the current BSSP, including sharp edges, surface temperature, and the temperature of operational construction. The results are combined in a spreadsheet template, with weighting factors, to derive an ordinate score of the overall safety rating, and an adjunct rating table to categorize the score into one of five tiers. According to the aforementioned research studies, one of the most important aspects is “cookstove tipping” parts. However, there are still some drawbacks for the current version, such as only taking stove tipping into consideration, without fuel, pot, or the combined system; the operations to get the tipping angle are not easy; and the definitions of repeats for different orientations are not clear.
A test protocol that enables accurate grading of stoves according to the safety performance is a much-needed input for empowering a thriving market for clean, safe, and efficient cookstoves. This research contributes to the development of cooking stove safety standards, particularly addressing tipping and sliding aspects. This contribution would be useful in suggesting an effective but still simple method for the overall rating of the mechanical stability of candidate stove/pot combinations.
2 Materials and methods
In the BSSP, the pot and fuel are not considered when testing stove stability. However, in a real situation, stove failure always occurs with the fuel and pot. The introduction of the fuel and pot further classifies the “stove + pot” system failure modes into three main kinds (tipping, sliding, or spilling) and five specific failures (stove only tipping failure; stove only sliding failure; stove plus pot tipping failure; stove plus pot sliding failure; and pot spilling/tipping/sliding failure). The different situations of spilling/sliding/tipping with the pot are given in Figure 1.
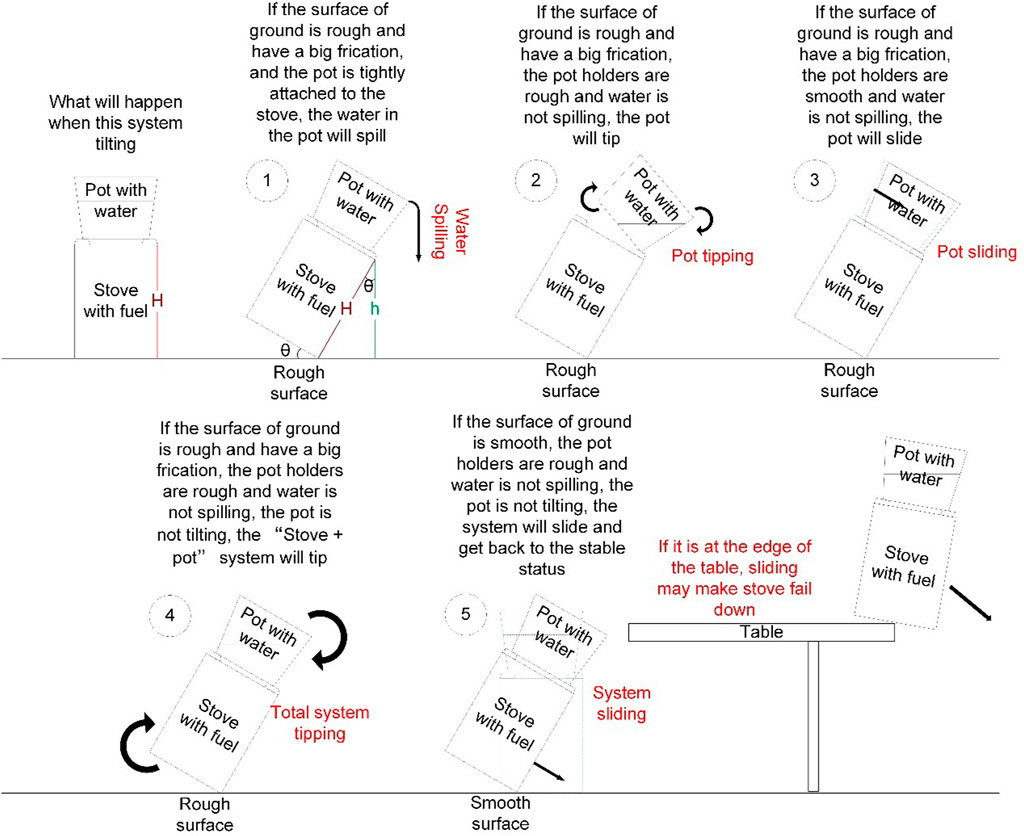
FIGURE 1. Failure modes when tilting with the pot and fuel. With the increase in the angle, five situations may occur for the stove + pot system.
To demonstrate these failures, a series of tipping and sliding tests were conducted on a range of stove technologies and geometries. The stoves selected were taken from items in commercial production and distribution in China and South Africa. The approach was taken to retain as far as possible the classification system of the previously published safety standard (Johnson and Bryden, 2015) but to allow the testing of all three possible modes of failures. The safety rating assigned to the stove would be based on the smallest angle of all the failure modes considering the stove position (on the table or floor).
2.1 Testing system of the tipping/sliding angle
The current protocol calculates the tipping inductor R using the equation R = h/H, where H is the height of the reference point while the stove is in the upright position, and h is the height of this reference point while the center of gravity is above the rotation point (Johnson and Bryden, 2015). By this definition, this ratio R equals to cos θT, where θT is the angle of the tipping failure (Figure 2).
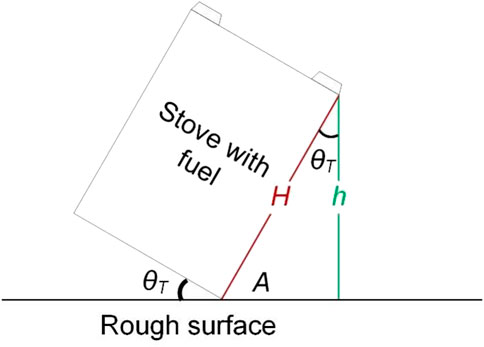
FIGURE 2. Geometry for the determination of the tipping angle for the stove safety test as specified in the BSSP standards. The tipping angle T is the angle at which the center of gravity would pass the rotation point A.
In the proposed alternative method to determine the tipping angle θT, the method measured three edges of an equilateral triangular. The equilateral triangular waists were defined by the arms of a simple device named the “tiltometer” (Kimemia and Van Niekerk, 2017). The “tiltometer” was constructed using two boards of ∼20 mm thickness, 380 mm width, and 700 mm length. The two boards were flush with each other, connected by a hinge at one end. At the end of the top board close to the hinge was a thin strip of wood (point A), termed the “stop” (∼20 mm wide and 3 mm thick) that prevented the stove from sliding during the tipping tests. Point B was on the bottom board of the “tiltometer” with a certain distance c to point A, while point C was the same distance as b but on the top board of the “tiltometer”.
A fully fuelled testing stove was placed on the top board, which would be slowly lifted up until the tipping point was reached. The distance a between B and C should be measured until the stove starts tipping. The test was repeated for each of the possible orientations of the stove, which depended on the asymmetrical features (such as a fuel feed support grid or exhaust gas outlet). For stove tipping tests, the stove was placed with its lower edge or the foot against the stopper at the hinge edge of the board. Alternatively, for the sliding tests, the stove was placed several centimeters away from the stopper. For safety, an operator was needed to stand ready to prevent the stove from falling over completely. The stove tipping angle was calculated using the following cosine equation:
As b = c, the equation can be simplified to
The only measured number was the distance a, always from the same marked positions B and C on the boards of the “tiltometer.” Unlike the measurement of h, the measurement of distance a did not depend on measuring a possibly indeterminate point on the about-to-tip stove, while the measurement of height h may be problematic in practice. The value of cos θT determined in this manner is entirely equivalent to the metric R defined in the existing method, so the categorical rating applied in the existing standard can be implemented without modification.
To calculate the forces or impulse needed for spilling/sliding/tipping the stove, a simple test was designed to estimate the relative feature. The test used a pulley to convert the force into gravity and further into a measured mass of a pot and water, which minimized equipment requirements. Figure 3 shows the design of the test. The force was measured at the top of the stove which, by the lever principle, had the smallest force making the stove tip.
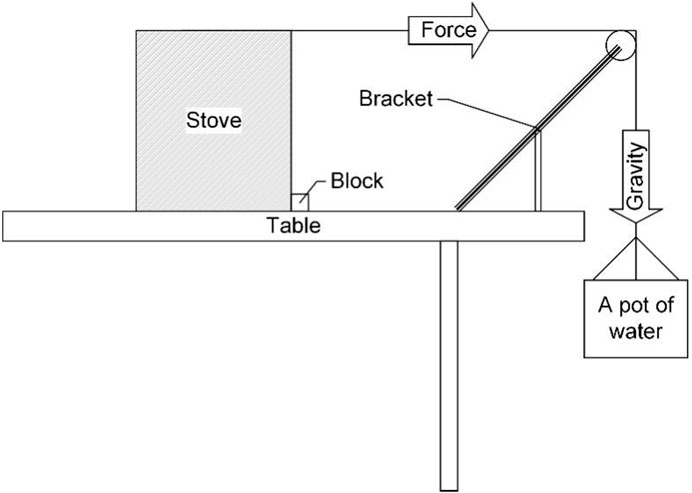
FIGURE 3. Testing system for the tipping force. In order to minimize the requirements of instruments, the force is converted into mass.
2.2 Stoves
During the experiments in South Africa, six stoves were subjected to tipping and sliding tests. Of the six appliances, five were commercially available while one was in the final stage of development. The different stoves were designed for using either liquid, ethanol gel, or solid fuels. The dimensions, fuel types, and images of the stoves are given in Table 1 and Supplementary Figure S1 (Supporting Information). An aluminum cooking pot with a capacity of 5 L was used when performing the cooking pot sliding test. The cooking pot had 2.5 L of water for test purposes. The cooking pot had a diameter of 25.5 cm and a depth of 12.2 cm.
For the experiments in China, two Chinese stoves (one with a chimney and one without) were subjected to the tipping and slide tests (Table 2 and Suppplementary Figure S2). A stainless steel cooking pot with a capacity of 5 L was used during the experiments. The cooking pot had a diameter of 26 cm and a depth of 18 cm.
2.3 Test protocol
As there were five specific failures for the “stove + pot” system, tipping/sliding/spilling tests were conducted as follows:
(1) Stove only tipping failure: the simulation of stove tipping without a pot on a rough surface. The stove edge or foot rests were placed against the stop bar and then the upper board of the “tiltometer” was slowly lifted up. The tests should be repeated for all distinct stove orientations.
(2) Stove only sliding failure: the simulation of stove sliding without a pot on a smooth surface. In the case of a floor-standing stove, sliding would not constitute a hazard for most cases as it will move back to the original angle. In contrast, for a stove that could or would normally be placed on a raised surface such as a table or kitchen bench, then sliding could constitute a risk if the stove were to fall off the edge. The stove edge or foot rests were placed several centimeters away from the stop bar and then the upper board of the “tiltometer” was slowly lifted up. In this test, the surface was unvarnished pine wood, sanded smooth. It should be noted that if the surface condition changed, there may be a tipping failure before sliding. The tests should be repeated for all distinct stove orientations, and the point of the first failure was noted (either stove tipping/sliding).
(3) Stove plus pot tipping failure: the simulation of the stove + pot system tipping on a rough surface. The stove edge or foot rests were placed against the stop bar, the 80% full 5 L pot was fastened to the stove with rubber ties, and then the upper board of the “tiltometer” was slowly lifted up. The tests should be repeated for all distinct stove orientations.
(4) Stove plus pot sliding failure: the simulation of the stove + pot system sliding on a smooth surface. The stove edge was placed several centimeters away from the stop bar, the 80% full 5 L pot was fastened to the stove with rubber ties, and then the upper board of the “tiltometer” was slowly lifted up. The tests should be repeated for all distinct stove orientations, and the point of the first failure was noted (either stove + pot system tipping/sliding).
(5) Pot sliding/tipping/spilling failure: the simulation of pot sliding/tipping/spilling if stove tipping and sliding does not occur. The stove edge or foot rests were placed against the stop bar, the stove was fastened to the top board and the 80% full 5 L pot was placed on it, and then the upper board of the “tiltometer” was slowly lifted up. Based on whether there was enough friction between the pot holder and the pot bottom or not, two situations may happen: 1) pot spilling/tipping before sliding; and 2) pot sliding. The tests should be repeated for all distinct stove orientations, and the point of the first failure was noted (no matter if pot sliding/tipping/spilling).
3 Results and discussion
3.1 Testing results
Tipping angles for the different South African stoves tested in this study are given in Table 3. There were wide variations in the mechanical stability of the different stoves, with the stove only tipping angle changing from 18° to 72.2°. The squat stoves had larger tipping and sliding angles, which implied better stability. With a certain top board surface, most of the stoves would slide rather than tip except Tshulu. The stove with a higher center of gravity (i.e., Phillips, Green stove, and Tshulu) did not have a cooking pot sliding angle as the failure occurred with a stove slid or tipped. But under this surface condition, compared with the sliding stoves (sliding angles for Phillips was from 14. 2°–15.7° and the Green stove was from 13.9° to 19.1°), the presence of a cooking pot on the stove significantly reduced the stability of the tipping stove (the tipping angle for Tshulu was from 18.0° to 12.5°) instead of increasing it. This occurrence implied that injury risks in the form of hot liquid and food burns, as well as contact burns and fire hazards, were heightened for the Tshulu stove.
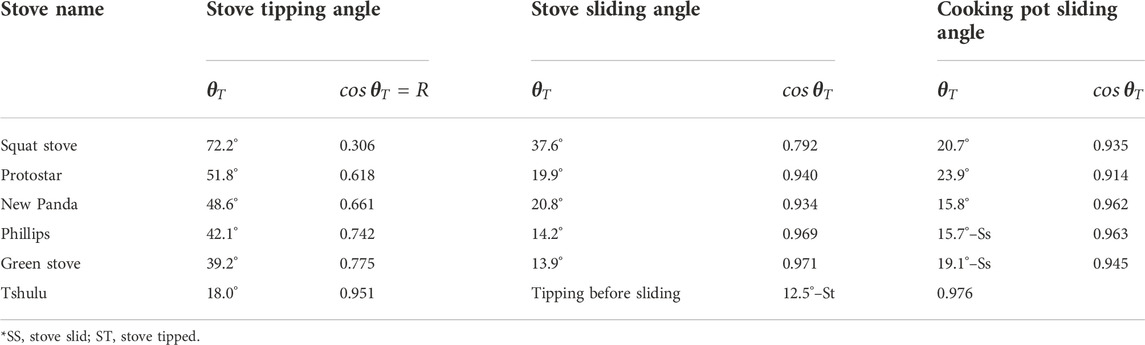
TABLE 3. Results of tipping, sliding, and spilling tests on South African stoves in various configurations with or without a pot in place.
Matching the cosine of the tipping angles to the IWA safety protocol ranking, five of the six stoves fell into tier 4 for the tipping test while the sliding tests placed the same devices in different tiers (Table 4). Again, this finding underscored the need to test for three different failure modes when assessing the mechanical stability of a cooking stove and its associated equipment (pot, fuel load, and utensils).
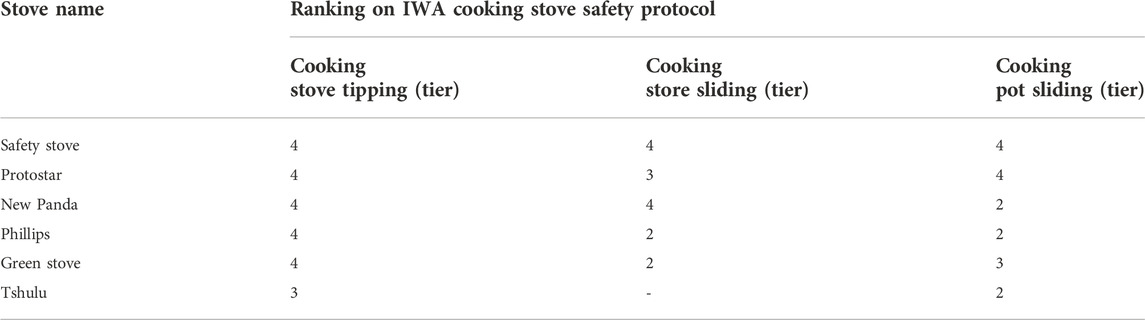
TABLE 4. Ranking of the mechanical stability of South African stoves based on the IWA safety protocol tipping criterion.
Tipping angles for the two Chinese stoves tested in this study are given in Table 5. It is to be noted that in the experiments, the stoves were evaluated for the force (N) required to either slip or tip the stove and highly repeatable test results were reported. A stove with high thermal mass would require a larger force to move or tip it than a stove with low thermal mass. When the stove mass was similar, the dominant factors were the stove design. Stove A had a larger mass than stove B; at the same time, it has a bigger support area and four feet and required more force to tip it (Table 3). However, using force as one of the indicators used for considering the stove mass may not be sensitive for ordinary people, and some indicators related to the force can be later developed. Results showed that even with 80% water in a pot, there were not too many spilling failures (Table 5).
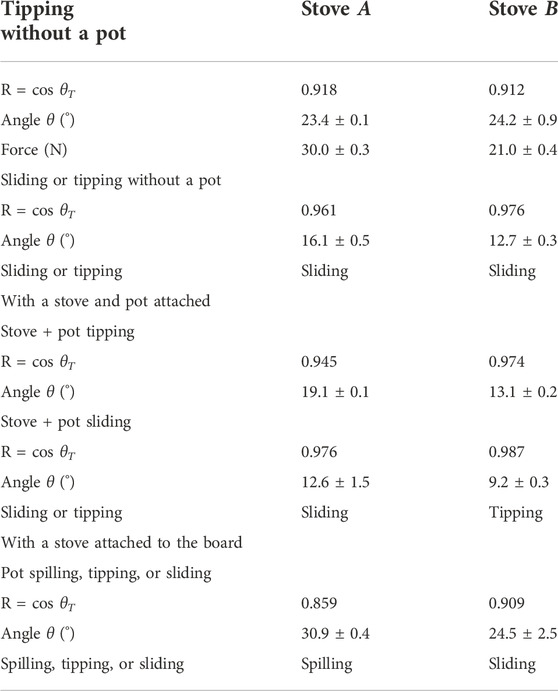
TABLE 5. Results of tipping, sliding, and spilling tests on two Chinese stoves in various configurations with or without a pot in place.
Matching the cosine of the tipping angles to the IWA safety protocol ranking, the two stoves fell into tier 4 for the tipping test, while the sliding tests placed the same devices in different tiers (Table 6). Both stoves showed tier 2 for sliding, while cooking pot sliding fell in tier 4. With almost the same failure angle, the occurrence implied that injury risks in the form of hot liquid and food burns were almost the same as contact burns and fire hazards.

TABLE 6. Ranking of the mechanical stability of Chinese stoves based on the IWA safety protocol tipping criterion.
With the chimney and fuel entry door making the stove asymmetrical, the Chinese stove had to be tested three times based on different geometric shapes and symmetries (shown in Figure 4, tipping direction toward outside the paper). The results of different orientations for both stoves without a pot are shown in Table 7.
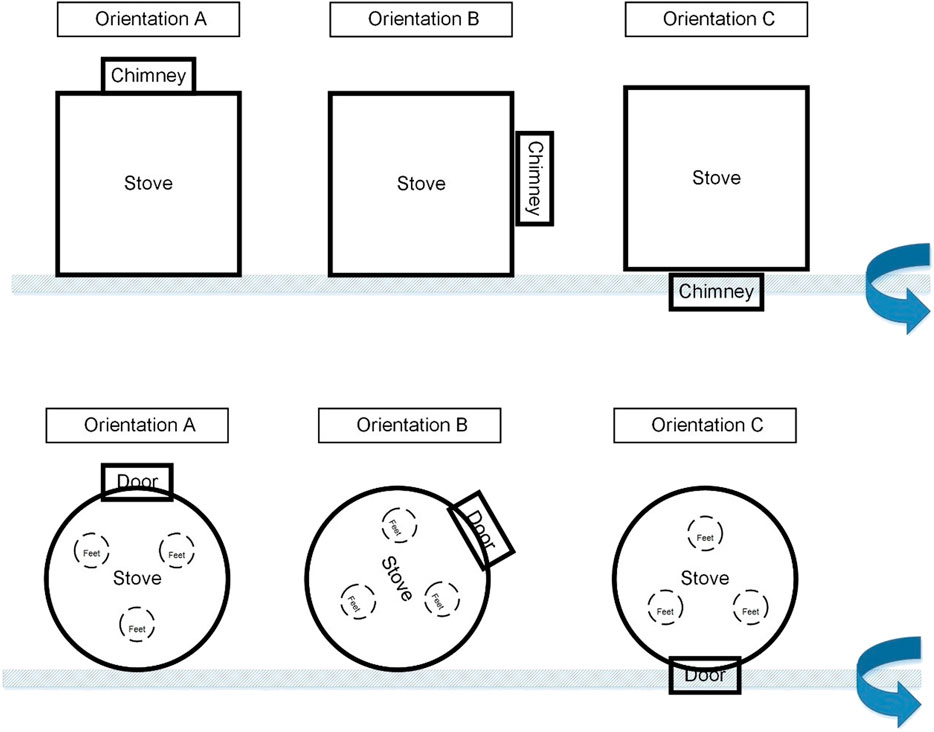
FIGURE 4. Orientations tested with Chinese stoves, designed based on different geometric shapes and symmetries, tipping direction toward outside the paper.
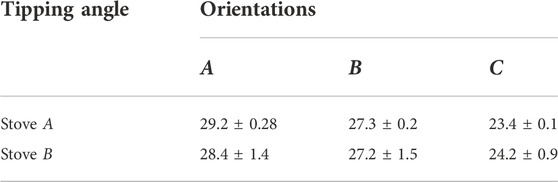
TABLE 7. Ranking of the mechanical stability of Chinese stoves from different orientations based on IWA safety protocol tipping.
Tipping angles for the same stove changed a lot. Compared with the regulations on orientation in the BSSP, the results showed that the leg numbers had no certain relationship with the repeat times. The suggestion was considering the symmetry instead of the leg numbers.
3.2 Theoretical calculation of the tipping angle
The theoretical calculation of the center of gravity is shown in Eq. 3. If the stove was simplified with the same material everywhere, taking Chinese stove A as an example (Figure 5), the center of gravity could be calculated by dividing the complex shape into different parts:
Take the left bottom point of the stove as the coordinate origin, the center of gravity of A1 is
The center of gravity of A2 is
The center of gravity of A3 is
The center of gravity of A4 is
The center of gravity should be calculated by combining Eqs 4–7:
This mode made the three orientations’ tipping tests (in Figure 6) much easier as it only needed to solve the triangles being shown as follows.
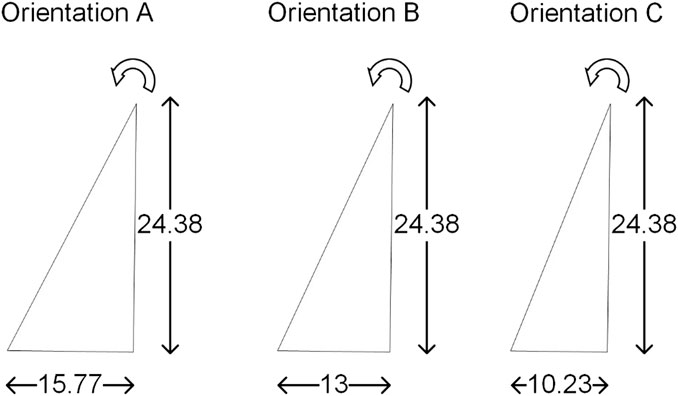
FIGURE 6. Converted equivalent triangles for calculating the tipping angles of three orientations of stove A, orientation A, B, and C: 32.9°, 28.1°, and 22.8° (unit: centimeter).
The results of the tipping angle for orientation A to C were 32.9°, 28.1°, and 22.8°, respectively. With actual testing results for orientation A to C were 29.2°, 27.3°, and 23.4°, respectively, with fuel in the combustion chamber, it meant this kind of mode could give a reasonable prediction for the tipping angle of the stove if it had relatively regular geometry. It is important to note that if different materials were used in the mode, the density of the material needs to be considered in the calculation.
4 Conclusion
The results presented in this paper showed that the mechanical stability of a stove + pot system depends on its performance in five specific failures (stove only tipping failure; stove only sliding failure; stove plus pot tipping failure; stove plus pot sliding failure; and pot spilling/tipping/sliding failure). As a result, the testing for one failure in the current IWA safety protocol does not provide enough information. The findings show that the presence of a cooking pot on the stove can either reduce or increase the mechanical stability of the system, based on the surface characteristics and stove position. Yet, the IWA protocol does not clarify whether the candidate stove should be assessed with a cooking pot on.
It is important to conduct the stove tipping and sliding tests on a purposely built rig as shown in this study. The rig (“tiltometer”) is simple to fabricate and improves the accuracy of results compared to testing on stools or chairs or on the floor. The restraining bar (stopper) on the “tiltometer” ensures that the cooking stove being tested does not slide before the tipping angle is reached as it often happens with IWA protocol tests.
A ranking of the results on the IWA safety protocol shows that the tested stoves attain different perform tiers for the different failure modes. Therefore, the mechanical stability of a candidate stove should be assessed as a comprehensive consideration of the three parameters of stove tipping and sliding and cooking pot sliding angles (based on stove/pot combination).
This paper addressed the ambiguity of the IWA safety protocol criterion by identifying three separate failure modes of the mechanical stability of a stove and designing specific test procedures for each. The findings presented herein show a need to revise the standard for cooking stove safety, taking into account the possibility of the stove tipping or sliding, or a cooking pot tipping, slipping, or spilling during use.
Data availability statement
The original contributions presented in the study are included in the article/Supplementary Material; further inquiries can be directed to the corresponding author.
Author contributions
NZ: conceptualization and writing—review and editing. YZ: writing—original draft, review, and editing and supervision. XL: writing—review and editing. DK: writing—reviewing and editing. HA: writing—original draft and supervision. TM: writing—original draft. RD: conceptualization. YZ: writing—original draft and funding acquisition.
Funding
This study was supported by the National Natural Science Foundation of China (Grant Nos. 42177431 and U20A2086); the Special Project on Innovation Methodology, Ministry of Science and Technology of China (Grant No. 2020IM020900); and the Inner Mongolia Autonomous Region Science and Technology Plan Project (Grant No. 2020GG0123). This study was supported by the National Natural Science Foundation of China (Grant No. 52200177) and the Open Research Fund Program of the State Key Laboratory of Clean and Efficient Coal Utilization of Taiyuan University of Technology (Grant No. SKL2022004).
Acknowledgments
The team appreciates the great help of the series training courses (Belt and Road Talent Exchange Program, Grant No. DL2021108001L) for academic writing guidance conducted by HA. The team acknowledges the support from the Key Laboratory of Clean Production and Utilization of Renewable Energy, Ministry of Agriculture and Rural Affairs, China Agricultural University; the National Center for International Research of BioEnergy Science and Technology, Ministry of Science and Technology, China Agricultural University; and the Beijing Municipal Key Discipline of Biomass Engineering.
Conflict of interest
The authors declare that the research was conducted in the absence of any commercial or financial relationships that could be construed as a potential conflict of interest.
Publisher’s note
All claims expressed in this article are solely those of the authors and do not necessarily represent those of their affiliated organizations, or those of the publisher, the editors, and the reviewers. Any product that may be evaluated in this article, or claim that may be made by its manufacturer, is not guaranteed or endorsed by the publisher.
Supplementary material
The Supplementary Material for this article can be found online at: https://www.frontiersin.org/articles/10.3389/fenrg.2022.958303/full#supplementary-material
References
Bruce, N., Pope, D., Rehfuess, E., Balakrishnan, K., Adair-Rohani, H., and Dora, C. (2015). WHO indoor air quality guidelines on household fuel combustion: Strategy implications of new evidence on interventions and exposure–risk functions. Atmospheric Environment, 106, 451–457. doi:10.1016/j.atmosenv.2014.08.064
Chen, X. J., Sun, W. J., Wang, J., Han, D. Z., Gao, G. Z., Yan, D. X., Zhao, X., Yao, X., Wang, L., and Wang, G., (2014). Epidemiology of bedside stove burns in a retrospective cohort of 5089 pediatric patients. Burns 40 (8), 1761–1769. doi:10.1016/j.burns.2014.03.018
Gallagher, M., Beard, M., Clifford, M. J., and Watson, M. C. (2016). An evaluation of a biomass stove safety protocol used for testing household cookstoves, in low and middle-income countries. Energy Sustain. Dev. 33, 14–25. doi:10.1016/j.esd.2016.03.008
Global Alliance for Clean Cookstoves (Gacc), (2015). Biomass Stove Safety Protocol Guidelines, 12/08/2015. Washington, DC: United Nations Foundation.
International Standards Organization (2012). Iwa 11:2012 – guidelines for evaluating cookstove performance. Washington, DC: International Standards Organization.
Johnson, N. G., and Bryden, K. M. (2015). Field-based safety guidelines for solid fuel household cookstoves in developing countries. Energy Sustain. Dev. 25, 56–66. doi:10.1016/j.esd.2015.01.002
Johnson, N. G. (2005). Risk analysis and safety evaluation of household stoves in developing nations. Ames: Iowa State University.
Kimemia, D., and Van Niekerk, A. (2017). Cookstove options for safety and health: Comparative analysis of technological and usability attributes. Energy Policy 105, 451–457. doi:10.1016/j.enpol.2017.03.022
Kimemia, D., Vermaak, C., Pachauri, S., and Rhodes, B. (2014). Burns, scalds and poisonings from household energy use in South Africa: Are the energy poor at greater risk? Energy Sustain. Dev. 18, 1–8. doi:10.1016/j.esd.2013.11.011
Kshirsagar, M. P., and Kalamkar, V. R. (2014). A comprehensive review on biomass cookstoves and a systematic approach for modern cookstove design. Renew. Sustain. Energy Rev. 30, 580–603. doi:10.1016/j.rser.2013.10.039
Kumar, M., Kumar, S., and Tyagi, S. (2013). Design, development and technological advancement in the biomass cookstoves: A review. Renew. Sustain. Energy Rev. 26, 265–285. doi:10.1016/j.rser.2013.05.010
Neubrech, F., Kiefer, J., Schmidt, V. J., Bigdeli, A. K., Hernekamp, J. F., Kremer, T., Kneser, U., and Radu, C. A., (2016). Domestic bioethanol-fireplaces–a new source of severe burn accidents. Burns 42 (1), 209–214. doi:10.1016/j.burns.2015.10.004
Nthumba, P. M. (2016). Burns in sub-saharan Africa: A review. Burns 42 (2), 258–266. doi:10.1016/j.burns.2015.04.006
Ombati, A. N., Ndaguatha, P. L. W., and Wanjeri, J. K. (2013). Risk factors for kerosene stove explosion burns seen at Kenyatta National Hospital in Kenya. Burns 39 (3), 501–506. doi:10.1016/j.burns.2012.07.008
Parbhoo, A., Louw, Q. A., and Grimmer-Somers, K. (2010). A profile of hospital-admitted paediatric burns patients in South Africa. BMC Res. Notes 3 (1), 165. doi:10.1186/1756-0500-3-165
Still, J., Craft-Coffman, B., Law, E., Colon-Santini, J., and Grant, J. (1998). Burns of children caused by electric stoves. J. Burn Care Rehabil. 19 (4), 364–365. doi:10.1097/00004630-199807000-00018
Stockhausen, A. L., and Katcher, M. L. (2001). Burn injury from products in the home: Prevention and counseling. Wis. Med. J. 100 (6), 39–44.
Keywords: cookstove, safety, stability evaluation, household air pollution, sustainable development
Citation: Zhao N, Zhang Y, Li X, Kimemia DK, Annegarn HJ, Makonese T, Dong R and Zhou Y (2023) Safety certification of improved biomass cooking stoves—A test method for tipping, sliding, and spilling stability. Front. Energy Res. 10:958303. doi: 10.3389/fenrg.2022.958303
Received: 31 May 2022; Accepted: 31 October 2022;
Published: 13 January 2023.
Edited by:
N. L. Panwar, Maharana Pratap University of Agriculture and Technology, IndiaReviewed by:
Neelam Rathore, Maharana Pratap University of Agriculture and Technology, IndiaRohan Pande, Sardar Vallabhbhai National Institute of Technology Surat, India
Copyright © 2023 Zhao, Zhang, Li, Kimemia, Annegarn, Makonese, Dong and Zhou. This is an open-access article distributed under the terms of the Creative Commons Attribution License (CC BY). The use, distribution or reproduction in other forums is permitted, provided the original author(s) and the copyright owner(s) are credited and that the original publication in this journal is cited, in accordance with accepted academic practice. No use, distribution or reproduction is permitted which does not comply with these terms.
*Correspondence: Xin Li, bHhpbkBjYXUuZWR1LmNu