- 1Beihang University, Beijing, China
- 2Institute for Future Transport and Cities, Coventry University, Coventry, United Kingdom
- 3College of Automotive Engineering, Jilin University, Changchun, China
- 4Dyson School of Design Engineering, Imperial College London, London, United Kingdom
Lithium-ion batteries (LiBs) are the key power source for electric vehicles (EVs). Battery thermal management system (BTMS) is essential to ensure safety and extend service life of LIBs. This paper reviews the various refrigeration materials used in the BTMS in EVs, including liquid coolant, phase change material (PCM). The thermal properties of these refrigerant materials are summarized and the innovative ways to improve the cooling efficiency of the BTMS are analyzed. The various ways to enhance the battery’s thermal performance by modifying the materials of the electrode, separator, and electrolyte are also reviewed. Finally, the research prospect in area of BTMS is summarized. This review will inspire new BTMS design and further improvement in battery safety and performance with the aid of advanced intelligent technologies.
1 Introduction
Due to depletion of fossil fuels and climate crisis, the development of new and renewable energy sources has attracted more and more attention in recent years (Li et al., 2018b; Jilte et al., 2019). Electric vehicles (EVs) play a key role in decarbonizing the transport sector (Zhou et al., 2021; Zhu et al., 2022). In addition, battery energy storage is essential to promote the integration of renewable generation in the power grid. Many countries have proposed EV roadmaps. For example, Chile promised to convert all public transport vehicles to EVs in 2040, while China proposed to electrify all passenger vehicles (95% of those will be battery-powered EVs) by 2035. Colombia plans to reach 6,00,000 EV stock by 2030 (International Energy Agency, 2021).
Battery reliability is vital to the development of EVs. Lithium ion batteries (LiBs) are widely used in EVs due to their many advantageous characteristics, such as high energy/power density and long life cycle (Yang et al., 2014; Ji et al., 2020; Feng et al., 2021; Kang et al., 2021; You et al., 2022). However, the thermal safety issue of LiBs is still a barrier to EV rollout (Chen et al., 2021; Gao et al., 2021; Wang et al., 2021). As an example, on 8 May 2020, an EV caught fire in Tangxia Town, Dongguan City, China, caused by simultaneous combustion of LiBs. On 16 August 2020, there is another battery thermal runaway (TR) incident in an EV in Taiyuan City (Liu et al., 2020). Compare to the internal combustion engine vehicle, spontaneous combustion of electric vehicles is due to the thermal runaway of the lithium battery, instead of the aging of the circuit. LIB thermal runaway is a chain of vigorous exothermic reactions (Chen et al., 2021). Thus, the threshold of the reaction is hard to predict, and the reaction process is difficult to control. And the potential damage of battery TR could be disastrous.
An efficient battery thermal management system (BTMS) is critical to improve the safe and reliability and to prevent TR of the battery system in EVs (Yang et al., 2020; Yang et al., 2021). Additionally, thermal barrier material should be applied to suppress battery TR after it occurs (Zhang et al., 2022). In general, the commonly used cooling methods in BTMS include air based, liquid based and phase change material (PCM) cooling (Saw et al., 2015; Wu et al., 2022). These cooling strategies have their advantages and disadvantages (Shen et al., 2021). Firstly, air cooling is the simplest method. Forced-air cooling can limit the temperature rise of the batteries, but it causes a uneven temperature distribution among cells during intense driving and high ambient temperatures (Rao and Wang, 2011). The liquid cooling strategy is more effective than air cooling in heat dissipation, but the cost and complexity of liquid-cooling system are noticeably increased due to the pumps, pipes and exchanger. Inserting PCM into the battery pack could effectively limit the maximum temperature, but it also increases the weight and volume of battery pack. Heat pipe cooling strategy offers high cooling performance, but it is limited by weight, gravity and passive control (Zhang et al., 2015). Therefore, when choosing a cooling strategy, it is necessary to consider many aspects, such as system complexity, cost, cool efficiency and power consumption.
In addition to battery thermal management under normal operating conditions, thermal barrier materials are effective methods to suppress TR after it occurs in the battery. The various thermal barrier materials used as additives in the cathode, anode and electrolyte of the battery to improve the no-flammable performance (Li et al., 2011; Zeng et al., 2018; Yuan et al., 2019) are reviewed in this paper.
As reported in (Wang et al., 2017b) the air based cooling based BTMS could limit the maximum temperature of the battery module below 55°C and the temperature difference between cells within 5°C during standard drive cycles of the hybrid electric vehicles (HEVs). However, air cooling is generally considered insufficient for battery thermal management in EVs, especially under high power charging and discharging (Choi and Kang, 2014), and the system structure of air cooling BTMS is much simpler compared with liquid cooling and PCM. Therefore, air cooling is not elaborated in this paper, while a comprehensive review of the liquid and PCM cooling system is presented in this work.
The rest of the paper is structured as follows. The liquid-cooling materials used in BTMS is first reviewed in Section 1; next the various PCMs, including solid-liquid and solid-gas, are discussed in Section 2; then, the thermal barrier materials used as battery additives are analyzed in Section 3; finally, Section 4 provides a summary of the future development of BTMS.
2 BTMS Materials Based on Liquid Cooling System
The liquid medium in BTMS should have high thermal conductivity and heat capacity, which is essential to achieve a homogeneous temperature distribution inside the battery pack. Other favorable characteristic include low toxicity, low flammability, and low environmental impact (Li et al., 2015).
Generally, the liquid media can be divided into the conventional liquid coolant and the nanofluids coolant. In this section, these two parts are analyzed and summarized. The specific classification as depict in Figure 1.
2.1 The Conventional Liquid Cooling Media
In liquid based BTMS, the coolant can pass through battery with direct or indirect contact. When the coolant passes over the surface of battery cells, it is direct contact. In contrast, when coolant passed by the tubes, channels and cold plates, it is the indirect contact (Barsotti and Boetcher, 2014). At present, the direct contact method has no application, because using the direct contact method will increase the coolant sealing requirements and high-voltage insulation requirements. At the same time, in order to prevent the coolant from corroding the battery, the type of coolant that can be selected is also greatly limited.
The conventional liquid cooling media include water, ethylene, silicone oil, mineral oil, and antifreeze solutions etc. Water is a popular coolant since it is accessible in operation and has high thermal conductivity. A novel BTMS using water as coolant and thermal silica plate was studied in (Wang et al., 2017a). An efficient mini-channel liquid cooling system for batteries in EV also adopted water as the coolant (Li et al., 2019). Because water freezes at sub-zero temperature, ethylene can be added in water to improve the low temperature performance. The low temperature limit of water/glycol mixtures is around −40°C. Meanwhile, the mixture has relatively high viscosity at low temperature that will reduce thermal conductivity and increase energy consumption (Li et al., 2015). Compared with water/glycol mixtures, silicone oil and mineral oil have a few advantages in terms of thermal conductivity and low temperature performance. A two-dimensional and transient model was used to study the influences of ambient temperature, Reynolds number, and discharge rate on the temperature distribution in the battery stack with air, liquid (silicone oil), and PCM cooling systems. The results show that silicone oil offers the most effective cooling under normal ambient temperature (Liu et al., 2014). Furthermore, the use of dielectric mineral oil in a channel with two Conducting-Lubricating (CO-LUB) surface walls for forced convective cooling of batteries was invested in [23]. In this work, the CO-LUB surface is a hydrophilic surface formed on solid copper. The experiment found that the water on the CO-LUB surface is equivalent to lubricating layer with high thermal conductivity, which helps to improve the heat transfer coefficient (Reyes and Kota, 2017). The disadvantage of the mineral oil coolant is that it needs a high flow rate to achieve the ideal cooling effect, which increases energy consumption. Moreover, silicone oils and mineral oils are typically flammable, hence a coolant leakage will significantly increase the risk of combustion and explosion of the module (Ulrych et al., 2014; Kalaf et al., 2021). Combining the above factors, the antifreeze-cooled battery system shows advantages from the perspective of low temperature and thermal conductivity. The cooling performance of the antifreeze-based BTMS mainly depends on the properties of antifreeze (Kwon and Park, 2016).
2.2 The Nanofluids Liquid Cooling Media
Nanofluid has been developed to further improve the thermal conductivity of liquid coolant. Nanofluid was made by dispersing nano-size materials in the base fluid to form nanotubes, nanoparticles, and nanosheets that can enhance thermo-physical properties, such as thermal conductivity and thermal diffusivity. Nanofluids have been considered as the most appropriate material for improving heat transfer characteristic of liquid coolant (Ali et al., 2018). There are two methods (Mukherjee et al., 2018) to prepare nanoliquids, i.e., one-step method and two-step method as shown in Figure 2. The based fluids of nanofluids include water, engine oil and ethylene glycol (EG) (Shdaifat et al., 2020). In Figures 3A–D, experimental data shows that, the thermal conductivity of nanofluid increases with viscosity and volume concentration. As it is shown in Figure 3E, the thermal conductivity of nanofluids is linearly proportional to the volume fraction (Liu et al., 2006). However, increasing viscosity could lead to excessive power consumption of the pump, which is not advisable in engineering. Additionally, the aggregation degree of nanofluids also influences the thermal conductivity, as depict in Figure 3F. There is an optimal aggregation degree of nanofluids that shows the highest thermal conductivity (Mukherjee et al., 2018).
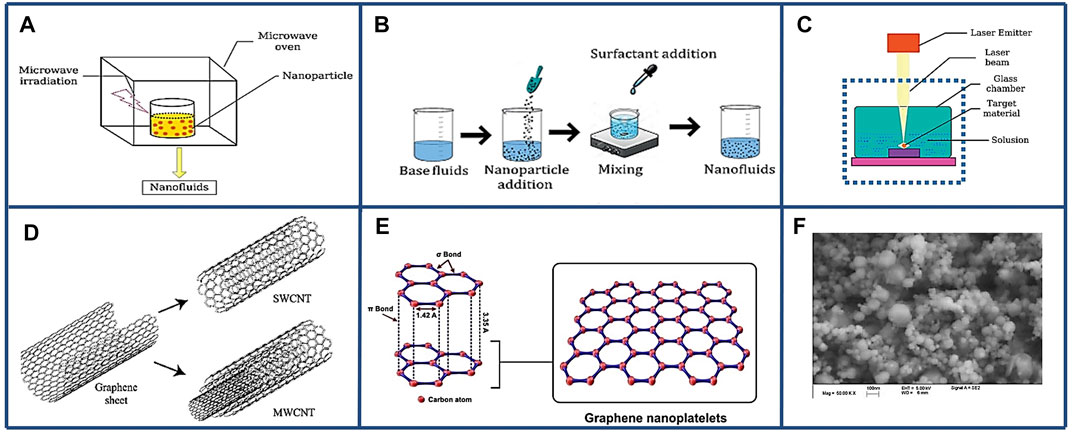
FIGURE 2. Preparation method of nanofluids, structure, and morphology of nanoparticles. (A) One-step method, (B) Two-step method, and (C) One-step method. Reproduced with permission (Mukherjee et al., 2018). Copyright 2018, Wiley Online Library. (D) Single-wall CNT and Multi-wall CNT. Reproduced with permission (Yazid et al., 2016). Copyright 2016, Elsevier. (E) Graphene nanoplatelets. Reproduced with permission (Madhad et al., 2021). Copyright 2021, SAGE Journals. (F) SEM CuO nanoparticles Reproduced with permission (Liu et al., 2006). Copyright 2006, Wiley Online Library.
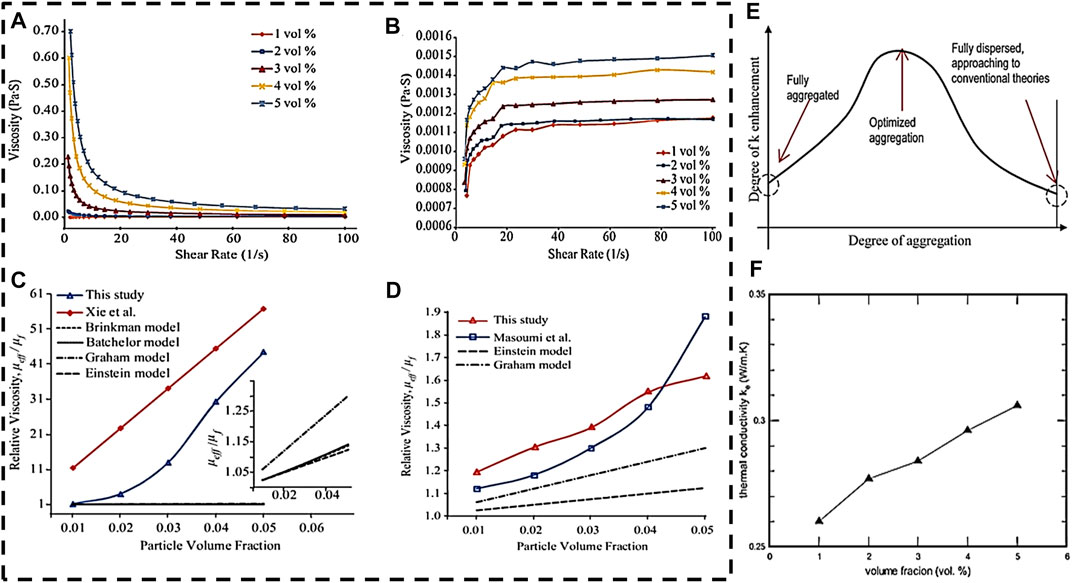
FIGURE 3. Physical properties of nanofluids. (A–D) effect of the stability on the viscosity of Al2O3 nanofluids at different concentrations, (A) viscosity as function of the shear rate 2 weeks after preparation, (B) viscosity as a function of the shear stress after re-sonication, (C) relative viscosity 2 weeks after preparation, (D) relative viscosity after re-sonication. (E) Effect of aggregation on the thermal conductivity enhancement of nanofluids. (F) The thermal conductivity of CuO nanofluids as a function of volume fraction. Reproduced with permission (Mukherjee et al., 2018; Liu et al., 2006). Copyright 2018 and 2006, Wiley Online Library.
At present, nanofluids have been widely studied in BTMS due to its good thermo-physical properties such as high thermal conductivity and high heat transfer rate. Table 1 shows the thermal conductivity of different nanofluids. The commonly used nanofluids in BTMS include Fe3O4/Carbon nanotubes (CNT)-water, Al2O3/AgO/CuO, Boehmite (AlOOH.xH2O), graphene nanoplatelets and TiO2 etc.
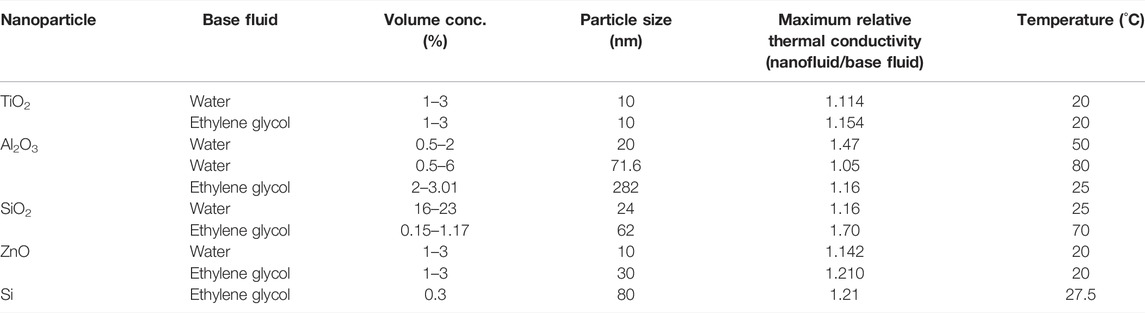
TABLE 1. The thermal conductivity of nanofluids (Munyalo and Zhang, 2018).
In general, CNT has the highest thermal conductivity among the known nanoparticles (Yazid et al., 2016), as shown in Figure 2, which include single wall carbon nanotube (SWCNT) and multi-walled carbon nanotube (MWCNT). In addition, metal oxide nanoparticles are an important class of nanofluids that have found several applications in BTMS (Nikam et al., 2018). The BTMSs based on the alumina (Al2O3), copper oxide (CuO), and silver oxide (AgO) nanofluids show high cooling efficiency, because the suspended metallic oxide nanoparticles dispersed in the base fluid enhance the heat transfer coefficient. According to study in (Shdaifat et al., 2020), the CuO nanoparticles have higher relative thermal conductivity coefficient than Al2O3 nanoparticles due to the higher density. CuO nanoparticles has great potential in BTMS applications because of the thermal conductivity of CuO nanoparticles (Ashraf et al., 2019) with a volume fraction of 0.05 (5 vol%) by 22.4%. In contrast, the Al2O3 nanofluids have lower thermal resistance that CuO nanoparticles. As shown in Figure 3, by characterizing the effect of alumina particle concentration on viscosity, it can be concluded that the stability of nanofluids aggregation has impact on their rheological behavior (Mukherjee et al., 2018). In addition, it is worth noting that TiO2-water nanofluid has a higher thermal conductivity than Al2O3 nanofluid under certain conditions. Numerical simulation analysis of an EV battery cooling module using TiO2 nanofluid as a refrigerant shows that the battery with higher nanofluid concentration has a lower maximum temperature (Wiriyasart et al., 2020), as the movement of nanoparticles suspending in the base fluid enhances the cooling capacity of system.
In addition to Boehmite, graphene nanoplatelets nanofluids (GNPs) also show favorable physical properties such as high aspect ratio, electrical, mechanical, and thermal conductivity owing to its atomic structure. A comparison between GNPs and distilled water shows that the convective heat transfer coefficients for distilled water and GNPs both increase as the Reynolds number increases. Meanwhile, at lower heat flux GNPs nanofluid have better thermal performance as compared to higher heat flux. And it can provide a high pump power even at lower heat flux (Arshad and Ali, 2017). Lastly, according to the study (Moldoveanu et al., 2019), the thermal conductivity of hybrid nanofluids is higher than single nanoparticle. However, the thermal conductivity and heat transfer rate of hybrid nanofluid has rarely been studied. More future work is needed for in-depth study of the hybrid nanofluids.
In summary, the nanofluid-based liquid cooling BTMS has higher cooling efficacy. However, their engineering application is still limited by the complex preparation process and the high cost of nanoparticles.
Liquid cooling BTMS is the most popular cooling methods in the EVs due to the high heat conductivity and high flexibility in integration (Wang et al., 2018). The challenges facing the liquid cooling BTMS are briefly summarized as follows. When the EV is climbing or accelerating, the battery heat generation increases significantly, which usually leads to non-uniform temperature distribution in battery. In addition, BTMS with liquid circulation loop has a complex structure due to the accessories (pipes, pump, etc.). Meanwhile, it has a potential hazard of coolant leakage.
3 BTMS Materials Based on PCMs
PCMs include solid-liquid PCMs, liquid-gas PCMs, and solid-gas PCMs. Because solid-gas PCMs is rarely used in practice, solid-liquid and liquid-gas PCMs are mainly discussed in this section. As shown in Figure 4, the solid-gas PCMs can be categorized as organic, inorganics and eutectic materials, wherein the inorganic PCMs include water, salt hydrate, and molten salt. The organic PCMs include paraffin, organic acid and alcohol (Rathod, 2018). Additionally, the liquid-gas can be divided into organic and inorganic, the organic includes Freon, Hydrofluoroolefin, and Hydrocarbon etc. the inorganic includes Carbon dioxide, Ammonia and other small molecular inorganic compounds. This section focus on summarizing the study process in the PCM materials thermal management from two aspects of solid-liquid and liquid-gas phase transition.
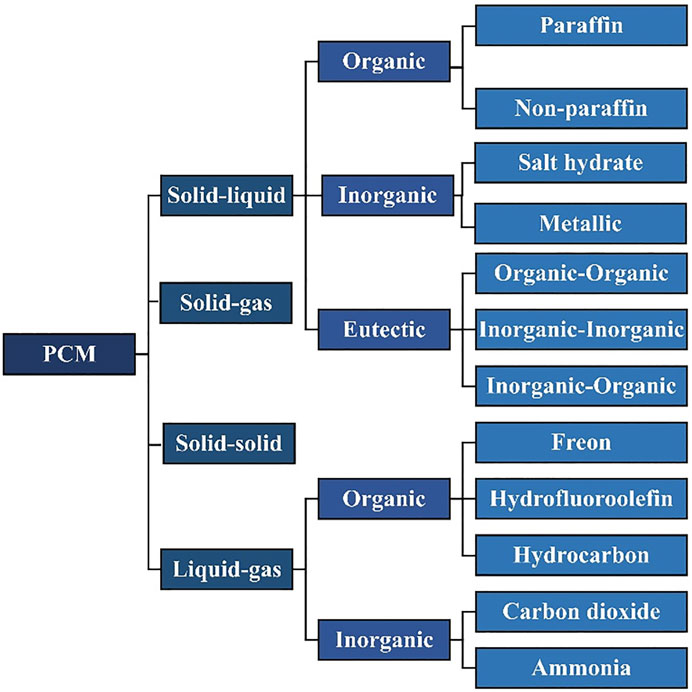
FIGURE 4. Classification of PCM. Reproduced with permission (Rathod, 2018). Copyright 2018, IntechOpen.
3.1 Solid-Liquid Phase Change System
The solid-liquid PCMs system is widely used because its volume change rate is low and easy to control (Jaguemont et al., 2018). Table 2 summarizes the physical parameters of solid-liquid PCMs. Under different ambient temperatures, the PCM shows similar temperature plateau, however it has different duration when the same heating power is applied. Under low ambient temperature, the initial melting of PCMs is delayed and the overall melting time is prolonged (Wang et al., 2017c). The BTMS performance can be enhanced by using proper materials, and the phase changes latent heat, thermal conductivity and melting point are vital parameters for PCMs. The high latent heat PCM can greatly decrease the temperature rise and the temperature difference among cells (Moraga et al., 2016). The commonly used solid-liquid PCMs include paraffin, Paraffinic hydrocarbons and composite phase change material (CPCM). As depict in Figure 5, the CPCM can be divided into zero-dimensions encapsulation, one-dimensional carbon nanotubes, two-dimensional graphene and three-dimensional metal foam according to the dimension.
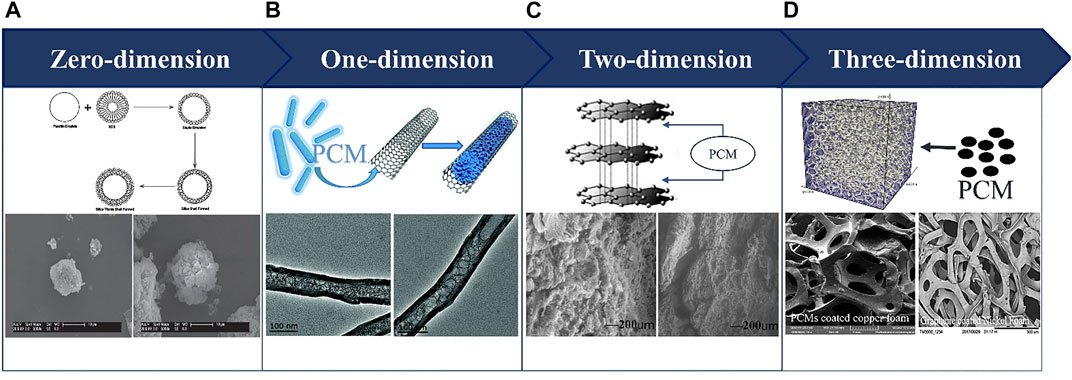
FIGURE 5. Solid-liquid composite phase change materials. (A) Encapsulation. Reproduced with permission (Li et al., 2018a). Copyright 2018, Elsevier. (B) Carbon Nanotubes. Reproduced with permission (Aftab et al., 2018). Copyright 2018, RSC. (C) Graphene. Reproduced with permission (Mantilla Gilart et al., 2012; Al-Shannaq and Farid, 2018). Copyright 2012 and 2018, Elsevier. (D) Metal Foam. Reproduced with permission (Abishek et al., 2018). Copyright 2018, Elsevier.
BTMS using solid-liquid PCMs has a favorable effect in solving the safety problem of LiBs (Lazrak et al., 2018). In order to enhance the heat transfer rate of paraffin, a computational model of paraffin melting in the cavity is established to study the solid-liquid phase change process. Experimental results show that the position of heating wall has great influence on the melting process. When the heating wall is located at the bottom, the paraffin melts fastest in the furnace cavity (Zhang et al., 2016). Materials with alike latent heat and density (heneicosane, tetracosane, and heptacosane) were compared, and the effect of the melting temperatures of the PCMs on the BTMS performance during battery overcharge process were studied. Therein, adiabatic overcharge tests at 0.1, 0.2, 0.5, 1, and 2 current rates (C-rate) were conducted. This work found that the cooling performance of heneicosane with low melting temperature is better than tetracosane and heptacosane with high melting temperature (Huang et al., 2018).
It is easy for pure PCMs to reach thermal saturation due to the low thermal conductivity. So BTMS based on pure PCMs cannot effectively control the pack temperature under long-term and high-power operations of LiBs (Wei et al., 2019). Therefore, it is vital to enhance the thermo-physical properties of pure PCM. Current research to improve the thermal conductivity of polymers is focused on adding materials with high thermal conductivity into PCM to form a composite PCM (CPCM). The common additives are metal foam, carbon-based materials, metallic (Ag, Al, and Cu) and metal oxide (Al2O3, CuO, MgO, and TiO2) nanoparticles (Zou et al., 2018). The study in (Abishek et al., 2018) revealed that the thermal conductivity of CPCM is related to the macroscopic properties (porosity and isotropy) of the metal foam. Several recent studies focused on the effect of metal foam materials (e.g., nickel, aluminum, copper) on the performance of CPCM. For instant, the BTMS based on Graphene coated nickel (GcN) foam shows outstanding performance. The thermal conductivity of pure paraffin wax was enhanced by 23 times after infiltrating it into the GcN foam. Meanwhile, the latent heat and specific heat of the GcN foam saturated with paraffin is decreased by 30 and 34%, respectively comparing to pure paraffin (Hussain et al., 2018). Wang et al. (2015) studied the influence of aluminum foam on the thermal conductivity of paraffin. Wherein, the theoretical thermal conductivity of CPCM is about 218 times higher than pure paraffin. The experiment indicated that the use of aluminum foam can accelerate the melting process and enhance the temperature consistency of the PCM. The research showed that adding CPCM can reduce the temperature rise of the heat sink, and the base temperature decreases with the increase of the volume fraction of PCM (Rehman et al., 2018). In addition to the above, numerical methods employed PCM and CNT-saturated carbon foam matrices as thermal management systems to investigate the effects of RT65 and CNTs embedded in carbon foam matrices with different porosity. The results indicated that insertion of RT65/MWCNT in CF-20 led to 11.5% decrease in the module surface temperature when the carbon foam porosity was below 75% (Alshaer et al., 2015). Another work also studied the influence of nanoparticles (TiO2, CuO, and GO) additives on the thermal properties of PCM, and the results show that the thermal conductivity of base material (paraffin) was increased by 25.0, 28.8, and 101%, respectively through the TiO2, CuO, and GO nanoparticles additives (Rufuss et al., 2018). As shown in Figure 6, Peng et al. (2022) developed and validated a three-dimensional numerical model against experimental data for a cylindrical lithium-ion battery module with a compact hybrid cooling system of phase change material (PCM) and heat pipes. More attractively, Wan et al. (2017) proposed a simple method to manufacture PCM microcapsules, wherein, copolymerzing styrene, acrylic acid, n-butyl acrylate, and pentaerythritol triacrylate were utilized as crosslinking agents to prepare the hybrid microcapsules’ shell. The experimental results show that the PCM microcapsules show high heat storage capacity and thermal conductivity. The performance of BTMS can be improved by optimizing the thermal conductivity of solid-liquid phase transition.
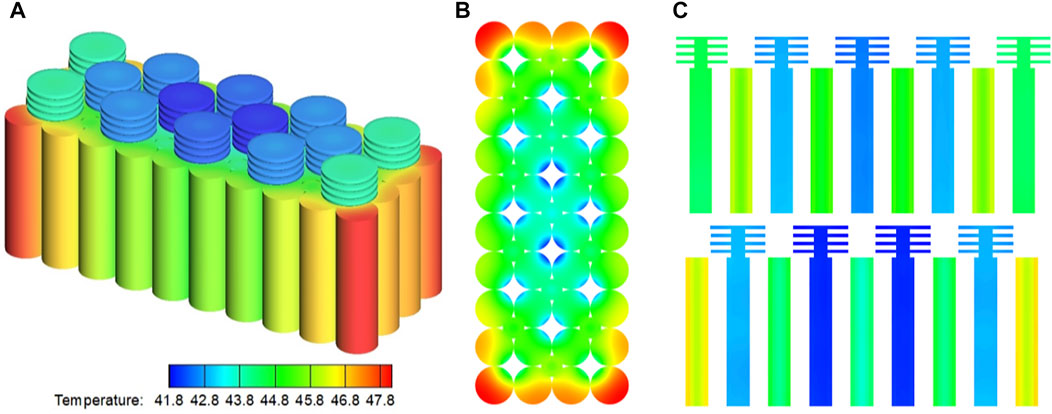
FIGURE 6. Contours of temperature at the end discharge process: (A) plot with all the parts included; (B) top view with heat pipes and fins not included; (C) section planes. Reproduced with permission (Peng et al., 2022). Copyright 2018, Elsevier.
3.2 Liquid-Gas Phase Change System
In addition to solid-liquid PCMs, liquid-gas PCMs (Xu et al., 2014) have gradually attracted more attention due to many advantages, such as excellent heat transfer and ease of addition and removal.
Liquid-gas PCMs have also been utilized in the BTMS of EVs (Ren et al., 2017). The conventional liquid-gas PCMs can be divided into boiling system and evaporation system. In addition, heat pipe (HP) is an efficient heat transfer equipment by using the phase change of internal working fluid to conduct abundant heat from one side to the other. It has found applications in electronics cooling, power generation, chemical engineering and spacecraft cooling (di Francescantonio et al., 2008).
For the boiling system, a dielectric fluid can be adopted as the coolant to eliminate the risk of short circuiting, which is essential for LiBs. Moreover it can effectively decrease the internal temperature heterogeneity of the batteries during the boiling process (van Gils et al., 2014). In boiling-liquid BTMS, the batteries are immersed in hydrofluoroether liquid. The liquid should have high electric resistance, non-inflammability, environmental friendliness, and the boiling temperature close to the working temperature of the battery. In the boiling system developed in [65], the battery temperature is maintained below 36°C during cyclic charging and discharging, even under high rate discharging and charging (around 20°C) (Hirano et al., 2014). As shown in Figure 7A, integrating flow boiling in mini-channel into BTMS could effectively decrease the battery’s maximum temperature and the maximum temperature difference at battery surface (An et al., 2017). In the ammonia boiling system, the cells are partly submerged in a liquid ammonia pool that boils through absorbing the heat generated by the battery. The ammonia vapor then passes to the electricity generator to produce electrical energy for driving the vehicle or charging the batteries (Al-zareer et al., 2018).
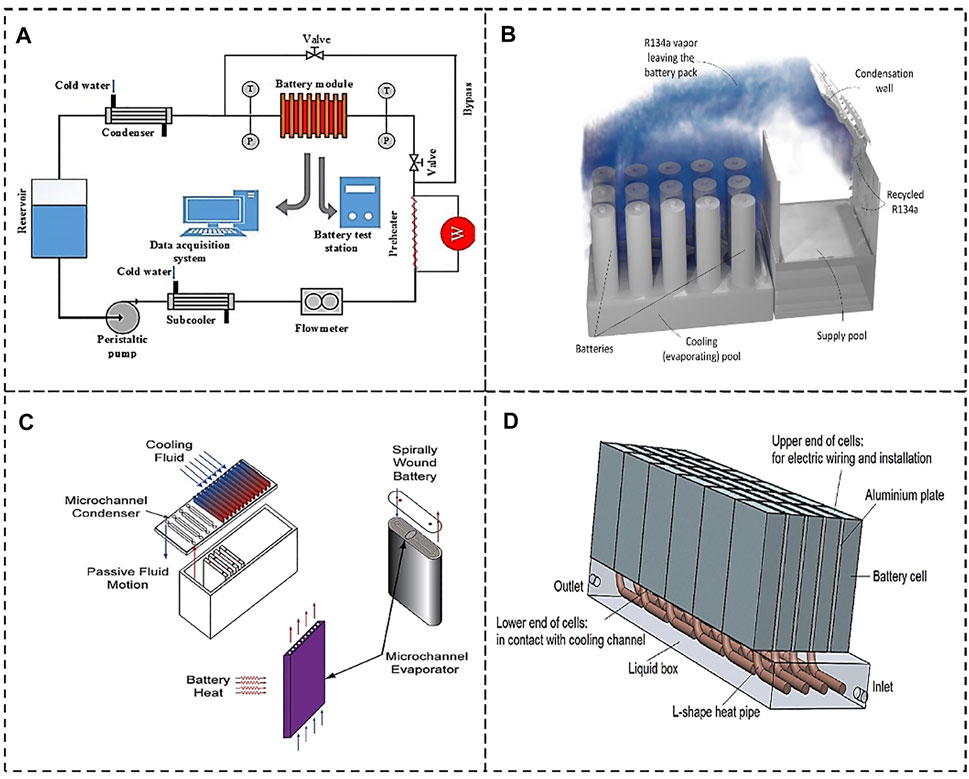
FIGURE 7. Liquid-gas cooling system. (A) Boiling cooling based mini-channel. Reproduced with permission (Zou et al., 2018). Copyright 2017, Elsevier. (B) Liquid-vapor phase-change cooling. Reproduced with permission (Al-Zareer et al., 2020). Copyright 2020, Elsevier. (C) Liquid-vapor BTMS based on microchannels. Reproduced with permission (Bandhauer and Garimella, 2013). Copyright 2013, Elsevier. (D) BTMS combined HP. Reproduced with permission (Wang et al., 2014). Copyright 2014, Elsevier.
Al-Zareer et al. (2019) proposed a new cooling system, which adopted liquid-vapor PCM to decrease the temperature rise and temperature gradient of LiBs. The liquid-vapor cooling system has high latent heat, which can remove vast amount of heat generated by the battery while maintaining a constant PCM temperature. Further, as depict in Figure 7B, they also studied (Al-Zareer et al., 2020) the influence of R134a vapor pool on the battery lifetime. In the system, the battery was immersed in the saturated R134a solution pool, and the refrigerant R134a evaporates and cools the battery. Under the Artemis realistic motorway cycle, the maximum battery temperature is limited to below 31.5°C.
In addition, there is a new type of BTMS employing water evaporation. The thin sodium alginate film (SA-1 film) with water content of 99 wt% is prepared by spraying method, which is affixed on the pack surface to suppress heat accumulation. The study revealed that under constant current charge/discharge larger than 1°C, the battery’s temperature rise rate is decreased by half using the developed BTMS in comparison with conventional BTMS. Even under the New Europe Drive Cycle that causes higher heat generation, the BTMS can still maintain the battery temperature from evident rise (Ren et al., 2017). Another study investigated the cooling efficiency of BTMS using R134a and microchannels, as shown in Figure 7C. The heat generation of battery is transferred to the microchannel evaporator placed inside the collector, where the working fluid R134a is turned into vapor phase. Due to the density difference, the vaporized fluid then flows to the condenser and is condensed there. This method can effectively manage the battery’s temperature rise (Bandhauer and Garimella, 2013).
HP is a novel strategy for the temperature control of battery (Zou et al., 2016). Many works have shown the HP can efficiently limit the peak temperature of LiBs. For example, the study in ref (Zou et al., 2016) shows that, if the battery generates less than 10 W/cell, the heat pipe using water glycol as the coolant can maintain the battery’s surface temperature below 40°C, as shown in Figure 7D. Meanwhile, the HP can keep the battery’s peak temperature below 70°C under thermal abuse conditions (e.g., 20e40 W/cell) (Wang et al., 2014). Rao et al. (2013) studied the performance of HP for battery thermal management in EVs. In the experiment the heat pipes are installed between two prismatic heaters and the condenser is cooled by a water bath. The results indicated that the maximum temperature could be limited below 50°C when the heat generation rate was lower than 50 W. Additionally, when the maximum heat generation rate is below 30 W, the temperature difference among cells can be kept less than 5°C.
Due to the latent heat effect, the liquid-vapor cooling can achieve higher heat dissipation rate compared to the single phase liquid convection cooling. As for heat pipe based BTMS, future development is needed to enhance the heat transfer rate and to demonstrate the system in real battery modules. Moreover, it is also very important to develop a numerical model of the liquid-gas phase change refrigeration system for vehicular applications (Liu et al., 2017a).
4 Thermal Barrier Management Materials
Battery TR is a very complex process involving electrochemistry, material science and engineering, and thermal dynamics. The TR process depends on multiple factors, from electrode and electrolyte materials to cell and module design (Wang et al., 2012), as shown in Figure 8. At high temperatures, excessive oxygen will be generated from the cathode decomposition, which is one of the key causes of TR of LiBs. Therefore, improving the thermal stability of the cathode can effectively prevent TR (Belharouak et al., 2003). Cathode modification by coating is important method to increase thermal stability. Typical protective coatings can be divided into inorganic films (such as ZnO, Al2O3, AlF3, etc.), organic films (such as poly diallyldimethylammonium chloride), and the protective films formed by additives [such as a γ-Butyrolactone, multi-component additive (composed of vinylene car-bonate, 1,3-propylene sulfite, and dimethylacetamide)] (Liao et al., 2019). When the surface of the cathode materials (such as LiCoO2, LiNiO2, and LiMn2O4) is coated with oxides (MgO, Al2O3, SiO2, TiO2, ZnO, SnO2, and ZrO2) and other materials, the coatings can isolate the cathode from the electrolyte solution, restrain the phase transition, enhance the structural stability, and reduce the disorder of cations in crystal sites (Li et al., 2006). Simultaneously the internal side reaction and heat generation of the battery are reduced during cycling.
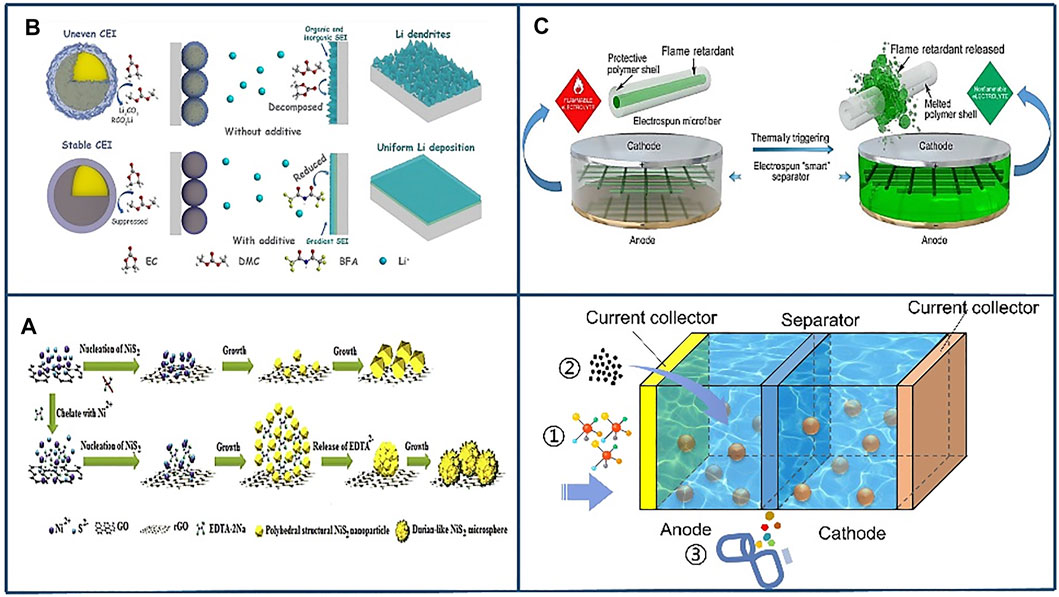
FIGURE 8. Application of thermal barrier material additives in battery thermal runaway. Reproduced with permission (Yang et al., 2019). Copyright 2019, Elsevier. (A) NiS2@rGO electrode additives. Reproduced with permission(Mishra et al., 2018). Copyright 2018, KeAi. (B) Bisfluoroacetamide (BFA) electrolyte additives. Reproduced with permission (Li et al., 2021). Copyright 2020, GDCh. (C) Thermoresponsive Polymer switch materials. Reproduced with permission (Liu et al., 2017b). Copyright 2017, Europe PMC.
In addition to cathode coating, thermoresponsive polymer switching material can be placed in the separator to suppress TR. The study in (Chen et al., 2016) indicates that batteries with thermoresponsive polymer switching (TRPS) material showed outstanding characteristic at normal temperature and shut down quickly under abnormal conditions, such as overheating and shorting (Chen et al., 2016).
Many side reactions will occur in the anode under low temperature or fast charging, such as the growth of lithium dendrite and SEI growth. Many materials have been developed, including graphite carbon and silicion-based material, or cover coatings on the anode surface, to suppress the formation lithium dendrites (Zheng et al., 2014; Liu et al., 2017c). In additional, the SEI film at the anode surface can be modified by silicon dioxide coating, which can improve the cycling stability of the batteries (Yang et al., 2007).
Besides electrode modification, electrolyte additive is another vital factor to inhibit TR. Lithium ions migrate between the cathode and the anode through the electrolyte inside the LIBs. The common electrolytes materials include LiPF6, LiClO4, LiAsF6, and LiCF3SO3 (Han et al., 2019). Nevertheless, the conventional carbonate electrolyte is flammable, which could cause fire and explosion under abusive conditions. Consequently, improving the thermal stability of the electrolyte is an effective strategy to suppress TR. Adding 5% ethoxy (pentafluoro) cyclotriphosphazene (EFPN) to the electrolyte can make the carbonate based electrolyte flame inhibiting and increase its stability under abuse-testing conditions (Feng et al., 2015). Furthermore, Ma et al. developed bisfluoroacetamide (BFA) as the electrolyte additive to induce a gradient SEI structure. BFA molecules change the solvation structure of Li+ by reducing the free solvent in the electrolyte, preventing the overall degradation of the electrolyte on the cathode surface, thereby forming an excellent cathode-electrolyte interface (CEI). This method can inhibit lithium plating and enhance the cycling stability of electrolyte, which effectively prevents TR (Li et al., 2021).
The separator plays a crucial role in ensuring the safety of LiBs, because it prevents direct contact between the cathode and anode, while allowing lithium ions to migrate (Jiang et al., 2017). At present, the separator utilized in LIB is mainly based on microporous polyolefin membranes, such as polypropylene (PP) and polyethylene (PE), because of their eximious mechanical strength and chemical stability. But the polyolefin membranes present high thermal shrinkage under high temperatures, which could bring about an internal short circuit and consequently cause fire or even explosion (Dai et al., 2016). Therefore, it is crucial to improve the thermal properties of the separator to avoid TR. To alleviate the issue, a new “smart” nonwoven electrospun separator with heat-triggered flame-retardant characteristics is used to prevent TR. The separator encapsulates the flame retardant in a protective polymer shell, and during TR of the LiBs, the protective polymer shell will melt due to temperature increase, releasing the flame retardants, thereby effectively inhibiting the burning of the highly flammable electrolytes (Liu et al., 2017b).
These modifications of the battery’s electrode, electrolyte and separator to enhance the BTMS performance to inhibit TR has a promising future.
5 Conclusion and Future Task
This paper mainly summarizes the applications of liquid cooling, PCM cooling and emergency battery thermal barrier (EBTB) materials in thermal management. The research prospects are summarized as follows. Firstly, one direction of future development is to improve the thermal conductivity, latent heat and no-flammable performance through changing the thermo-physical properties of the refrigeration materials. Next, for the liquid medium, hybrid nanofluids have great application prospect, and it is necessary to study the behavior of hybrid nanofluids in laminar flow and the physical properties of different combinations of hybrid nanoparticles (Moldoveanu et al., 2019). In terms of PCM, on the one hand, for the metal foam structure, the influence of the specific surface area of mental foam, pore size and filling rate of PCM on thermal conductivity should be further studied in the future (Abishek et al., 2018). On the other hand, the shape, size and aspect ratio of nanoparticles have a pivotal role in the thermal conductivity of PCM (Qureshi et al., 2018). The dispersion uniformity and aggregation of nanoparticles could be the next research hotspot. Finally, a promising solution to alleviate the TR issue is to use additives to improve the material properties of the battery.
In the future, we hope to use the numerical simulation model to assist the design and optimization of BTMS, reduce its design cost and cycle, and improve the comprehensive performance of BTMS. At the same time, we also expect artificial intelligence (AI) networks and digital twins to be used not only for information exchange functions, but also to guide the design and production of new phase change materials, and to define structural properties through material functions.
Author Contributions
SY: Conceptualization, Methodology, Writing—Original Draft. JL: Methodology, Software, Visualization. ZZ: Investigation, Validation. CZ: Data Curation. XZ: Validation. WX: Visualization. LW: Writing—Review and Editing. SC: Supervision. XL: Supervision.
Funding
This work is supported by the National Natural Science Foundation of China under the No. U1864213.
Conflict of Interest
The authors declare that the research was conducted in the absence of any commercial or financial relationships that could be construed as a potential conflict of interest.
The reviewer TZ declared a shared affiliation with the author XL to the handling editor at the time of review.
Publisher’s Note
All claims expressed in this article are solely those of the authors and do not necessarily represent those of their affiliated organizations, or those of the publisher, the editors and the reviewers. Any product that may be evaluated in this article, or claim that may be made by its manufacturer, is not guaranteed or endorsed by the publisher.
References
Abishek, S., King, A. J. C., Nadim, N., and Mullins, B. J. (2018). Effect of Microstructure on Melting in Metal-Foam/paraffin Composite Phase Change Materials. Int. J. Heat Mass Transf. 127, 135–144. doi:10.1016/j.ijheatmasstransfer.2018.07.054
Aftab, W., Huang, X., Wu, W., Liang, Z., Mahmood, A., and Zou, R. (2018). Nanoconfined Phase Change Materials for Thermal Energy Applications. Energy Environ. Sci. 11, 1392–1424. doi:10.1039/c7ee03587j
Al Shdaifat, M. Y., Zulkifli, R., Sopian, K., and Salih, A. A. (2020). Thermal and Hydraulic Performance of CuO/water Nanofluids: A Review. Micromachines 11, 416. doi:10.3390/MI11040416
Al-Shannaq, R., and Farid, M. M. (2018). A Novel Graphite-PCM Composite Sphere with Enhanced Thermo-Physical Properties. Appl. Therm. Eng. 142, 401–409. doi:10.1016/j.applthermaleng.2018.07.008
Al-Zareer, M., Dincer, I., and Rosen, M. A. (2019). A Novel Approach for Performance Improvement of Liquid to Vapor Based Battery Cooling Systems. Energy Convers. Manag. 187, 191–204. doi:10.1016/j.enconman.2019.02.063
Al-Zareer, M., Dincer, I., and Rosen, M. A. (2020). A Thermal Performance Management System for Lithium-Ion Battery Packs. Appl. Therm. Eng. 165, 114378. doi:10.1016/j.applthermaleng.2019.114378
Al-zareer, M., Dincer, I., and Rosen, M. A. (2018). Development and Evaluation of a New Ammonia Boiling Based Battery Thermal Management System. Electrochimica Acta 280, 340–352. doi:10.1016/j.electacta.2018.05.093
Ali, H., Babar, H., Shah, T., Sajid, M., Qasim, M., and Javed, S. (2018). Preparation Techniques of TiO2 Nanofluids and Challenges: A Review. Appl. Sci. 8, 587. doi:10.3390/app8040587
Alshaer, W. G., Nada, S. A., Rady, M. A., Le Bot, C., and Palomo Del Barrio, E. (2015). Numerical Investigations of Using Carbon foam/PCM/Nano Carbon Tubes Composites in Thermal Management of Electronic Equipment. Energy Convers. Manag. 89, 873–884. doi:10.1016/j.enconman.2014.10.045
An, Z., Jia, L., Li, X., and Ding, Y. (2017). Experimental Investigation on Lithium-Ion Battery Thermal Management Based on Flow Boiling in Mini-Channel. Appl. Therm. Eng. 117, 534–543. doi:10.1016/j.applthermaleng.2017.02.053
Arshad, W., and Ali, H. M. (2017). Graphene Nanoplatelets Nanofluids Thermal and Hydrodynamic Performance on Integral Fin Heat Sink. Int. J. Heat Mass Transf. 107, 995–1001. doi:10.1016/j.ijheatmasstransfer.2016.10.127
Ashraf, M. A., Li, C., Zhang, D., and Ross, D. (2019). RETRACTED: Battery Thermal Management with Conjugate Heat Transfer in Heat Sink with Fe3O4/CNT-Water Nanofluid Using Lattice Boltzmann/finite Volume Method. Chem. Eng. Process. - Process Intensif. 146. doi:10.1016/j.cep.2019.107708
Bandhauer, T. M., and Garimella, S. (2013). Passive, Internal Thermal Management System for Batteries Using Microscale Liquid-Vapor Phase Change. Appl. Therm. Eng. 61, 756–769. doi:10.1016/j.applthermaleng.2013.08.004
Barsotti, D. L., and Boetcher, S. (2014). Novel Battery Cold Plate Design for Increased Passive Cooling. SAE Tech. Pap. 1. doi:10.4271/2014-01-1919
Belharouak, I., Sun, Y.-K., Liu, J., and Amine, K. (2003). Li(Ni1/3Co1/3Mn1/3)O2 as a Suitable Cathode for High Power Applications. J. Power Sources 123, 247–252. doi:10.1016/S0378-7753(03)00529-9
Chen, S., Gao, Z., and Sun, T. (2021). Safety Challenges and Safety Measures of Li‐ion Batteries. Energy Sci. Eng. 9, 1647–1672. doi:10.1002/ese3.895
Chen, Z., Hsu, P.-C., Lopez, J., Li, Y., To, J. W. F., Liu, N., et al. (2016). Fast and Reversible Thermoresponsive Polymer Switching Materials for Safer Batteries. Nat. Energy 1. doi:10.1038/nenergy.2015.9
Choi, Y. S., and Kang, D. M. (2014). Prediction of Thermal Behaviors of an Air-Cooled Lithium-Ion Battery System for Hybrid Electric Vehicles. J. Power Sources 270, 273–280. doi:10.1016/J.JPOWSOUR.2014.07.120
Dai, J., Shi, C., Li, C., Shen, X., Peng, L., Wu, D., et al. (2016). A Rational Design of Separator with Substantially Enhanced Thermal Features for Lithium-Ion Batteries by the Polydopamine-Ceramic Composite Modification of Polyolefin Membranes. Energy Environ. Sci. 9, 3252–3261. doi:10.1039/c6ee01219a
di Francescantonio, N., Savino, R., and Abe, Y. (2008). New Alcohol Solutions for Heat Pipes: Marangoni Effect and Heat Transfer Enhancement. Int. J. Heat Mass Transf. 51, 6199–6207. doi:10.1016/j.ijheatmasstransfer.2008.01.040
Feng, J., An, Y., Ci, L., and Xiong, S. (2015). Nonflammable Electrolyte for Safer Non-aqueous Sodium Batteries. J. Mat. Chem. A 3, 14539–14544. doi:10.1039/c5ta03548a
Feng, J., Gao, Z., Sheng, L., Hao, Z., and Wang, F. R. (2021). Progress and Perspective of Interface Design in Garnet Electrolyte‐based All‐solid‐state Batteries. Carbon Energy 3, 385–409. doi:10.1002/cey2.100
Gao, X.-L., Liu, X.-H., Xie, W.-L., Zhang, L.-S., and Yang, S.-C. (2021). Multiscale Observation of Li Plating for Lithium-Ion Batteries. Rare Mater. 40, 3038–3048. doi:10.1007/s12598-021-01730-3
Han, X., Feng, X., Ouyang, M., Lu, L., Li, J., Zheng, Y., et al. (2019). A Comparative Study of Charging Voltage Curve Analysis and State of Health Estimation of Lithium-Ion Batteries in Electric Vehicle. Automot. Innov. 2, 263–275. doi:10.1007/s42154-019-00080-2
Hirano, H., Tajima, T., Hasegawa, T., Sekiguchi, T., and Uchino, M. (2014). “Boiling Liquid Battery Cooling for Electric Vehicle,” in Proceeding of the 2014 IEEE Conference and Expo Transportation Electrification Asia-Pacific (ITEC Asia-Pacific), 1–4.
Huang, P., Verma, A., Robles, D. J., Wang, Q., Mukherjee, P., and Sun, J. (2018). Probing the Cooling Effectiveness of Phase Change Materials on Lithium-Ion Battery Thermal Response under Overcharge Condition. Appl. Therm. Eng. 132, 521–530. doi:10.1016/j.applthermaleng.2017.12.121
Hussain, A., Abidi, I. H., Tso, C. Y., Chan, K. C., Luo, Z., and Chao, C. Y. H. (2018). Thermal Management of Lithium Ion Batteries Using Graphene Coated Nickel Foam Saturated with Phase Change Materials. Int. J. Therm. Sci. 124, 23–35. doi:10.1016/j.ijthermalsci.2017.09.019
International Energy Agency (2021). Global EV Policy Explorer. Available at: https://www.iea.org/articles/global-ev-policy-explorer.
Jaguemont, J., Omar, N., Van den Bossche, P., and Mierlo, J. (2018). Phase-change Materials (PCM) for Automotive Applications: A Review. Appl. Therm. Eng. 132, 308–320. doi:10.1016/j.applthermaleng.2017.12.097
Ji, Y.-R., Weng, S.-T., Li, X.-Y., Zhang, Q.-H., and Gu, L. (2020). Atomic-scale Structural Evolution of Electrode Materials in Li-Ion Batteries: a Review. Rare Mater. 39, 205–217. doi:10.1007/s12598-020-01369-6
Jiang, X., Zhu, X., Ai, X., Yang, H., and Cao, Y. (2017). Novel Ceramic-Grafted Separator with Highly Thermal Stability for Safe Lithium-Ion Batteries. ACS Appl. Mat. Interfaces 9, 25970–25975. doi:10.1021/acsami.7b05535
Jilte, R. D., Kumar, R., and Ahmadi, M. H. (2019). Cooling Performance of Nanofluid Submerged vs. Nanofluid Circulated Battery Thermal Management Systems. J. Clean. Prod. 240, 118131. doi:10.1016/j.jclepro.2019.118131
Kalaf, O., Solyali, D., Asmael, M., Zeeshan, Q., Safaei, B., and Askir, A. (2021). Experimental and Simulation Study of Liquid Coolant Battery Thermal Management System for Electric Vehicles: A Review. Int. J. Energy Res. 45, 6495–6517. doi:10.1002/er.6268
Kang, H. J., Lee, T. G., Kim, H., Park, J. W., Hwang, H. J., Hwang, H., et al. (2021). Thick Free‐standing Electrode Based on Carbon-Carbon Nitride Microspheres with Large Mesopores for High‐energy‐density Lithium-Sulfur Batteries. Carbon Energy 3, 410–423. doi:10.1002/cey2.116
Kwon, H., and Park, H. (2016). Numerical Investigation of Cooling Performance of Liquid-Cooled Battery in Electric Vehicles. Trans. Korean Soc. Mech. Eng. B 40, 403–408. doi:10.3795/KSME-B.2016.40.6.403
Lazrak, A., Fourmigué, J.-F., and Robin, J.-F. (2018). An Innovative Practical Battery Thermal Management System Based on Phase Change Materials: Numerical and Experimental Investigations. Appl. Therm. Eng. 128, 20–32. doi:10.1016/j.applthermaleng.2017.08.172
Li, C., Zhang, H. P., Fu, L. J., Liu, H., Wu, Y. P., Rahm, E., et al. (2006). Cathode Materials Modified by Surface Coating for Lithium Ion Batteries. Electrochimica Acta 51, 3872–3883. doi:10.1016/j.electacta.2005.11.015
Li, F., He, J., Liu, J., Wu, M., Hou, Y., Wang, H., et al. (2021). Gradient Solid Electrolyte Interphase and Lithium‐Ion Solvation Regulated by Bisfluoroacetamide for Stable Lithium Metal Batteries. Angew. Chem. 133, 6674–6682. doi:10.1002/ange.202013993
Li, J., Daniel, C., and Wood, D. (2011). Materials Processing for Lithium-Ion Batteries. J. Power Sources 196, 2452–2460. doi:10.1016/j.jpowsour.2010.11.001
Li, M., Liu, J., and Shi, J. (2018a). Synthesis and Properties of Phase Change Microcapsule with SiO2-TiO2 Hybrid Shell. Sol. Energy 167, 158–164. doi:10.1016/j.solener.2018.04.016
Li, T., Liu, H., Shi, P., and Zhang, Q. (2018b). Recent Progress in Carbon/lithium Metal Composite Anode for Safe Lithium Metal Batteries. Rare Mater. 37, 449–458. doi:10.1007/s12598-018-1049-3
Li, W., Peng, X., Xiao, M., Garg, A., and Gao, L. (2019). Multi‐objective Design Optimization for Mini‐channel Cooling Battery Thermal Management System in an Electric Vehicle. Int. J. Energy Res. 43, 3668–3680. doi:10.1002/er.4518
Li, Z., Chen, Y., Xin, Y., and Zhang, Z. (2015). Sensitive Electrochemical Nonenzymatic Glucose Sensing Based on Anodized CuO Nanowires on Three-Dimensional Porous Copper Foam. Sci. Rep. 5, 16115. doi:10.1038/srep16115
Liao, Z., Zhang, S., Li, K., Zhang, G., and Habetler, T. G. (2019). A Survey of Methods for Monitoring and Detecting Thermal Runaway of Lithium-Ion Batteries. J. Power Sources 436, 226879. doi:10.1016/j.jpowsour.2019.226879
Liu, C., Xu, D., Weng, J., Zhou, S., Li, W., Wan, Y., et al. (2020). Phase Change Materials Application in Battery Thermal Management System: A Review. Materials 13, 4622–4637. doi:10.3390/ma13204622
Liu, H., Wei, Z., He, W., and Zhao, J. (2017a). Thermal Issues about Li-Ion Batteries and Recent Progress in Battery Thermal Management Systems: A Review. Energy Convers. Manag. 150, 304–330. doi:10.1016/j.enconman.2017.08.016
Liu, K., Liu, W., Qiu, Y., Kong, B., Sun, Y., Chen, Z., et al. (2017b). Electrospun Core-Shell Microfiber Separator with Thermal-Triggered Flame-Retardant Properties for Lithium-Ion Batteries. Sci. Adv. 3, 1–9. doi:10.1126/sciadv.1601978
Liu, K., Pei, A., Lee, H. R., Kong, B., Liu, N., Lin, D., et al. (2017c). Lithium Metal Anodes with an Adaptive "Solid-Liquid" Interfacial Protective Layer. J. Am. Chem. Soc. 139, 4815–4820. doi:10.1021/jacs.6b13314
Liu, M.-S., Lin, M. C.-C., Huang, I.-T., and Wang, C.-C. (2006). Enhancement of Thermal Conductivity with CuO for Nanofluids. Chem. Eng. Technol. 29, 72–77. doi:10.1002/ceat.200500184
Liu, R., Chen, J., Xun, J., Jiao, K., and Du, Q. (2014). Numerical Investigation of Thermal Behaviors in Lithium-Ion Battery Stack Discharge. Appl. Energy 132, 288–297. doi:10.1016/j.apenergy.2014.07.024
Madhad, H. V., Mishra, N. S., Patel, S. B., Panchal, S. S., Gandhi, R. A., and Vasava, D. V. (2021). Graphene/graphene Nanoplatelets Reinforced Polyamide Nanocomposites: A Review. High. Perform. Polym. 33, 981–997. doi:10.1177/09540083211011216
Mantilla Gilart, P., Yedra Martínez, Á., González Barriuso, M., and Manteca Martínez, C. (2012). Development of PCM/carbon-based Composite Materials. Sol. Energy Mater. Sol. Cells 107, 205–211. doi:10.1016/j.solmat.2012.06.014
Mishra, A., Mehta, A., Basu, S., Malode, S. J., Shetti, N. P., Shukla, S. S., et al. (2018). Electrode Materials for Lithium-Ion Batteries. Mater. Sci. Energy Technol. 1, 182–187. doi:10.1016/j.mset.2018.08.001
Moldoveanu, G. M., Minea, A. A., Huminic, G., and Huminic, A. (2019). Al2O3/TiO2 Hybrid Nanofluids Thermal Conductivity. J. Therm. Anal. Calorim. 137, 583–592. doi:10.1007/s10973-018-7974-4
Moraga, N. O., Xamán, J. P., and Araya, R. H. (2016). Cooling Li-Ion Batteries of Racing Solar Car by Using Multiple Phase Change Materials. Appl. Therm. Eng. 108, 1041–1054. doi:10.1016/j.applthermaleng.2016.07.183
Mukherjee, S., Mishra, P. C., and Chaudhuri, P. (2018). Stability of Heat Transfer Nanofluids - A Review. ChemBioEng Rev. 5, 312–333. doi:10.1002/cben.201800008
Munyalo, J. M., and Zhang, X. (2018). Particle Size Effect on Thermophysical Properties of Nanofluid and Nanofluid Based Phase Change Materials: A Review. J. Mol. Liq. 265, 77–87. doi:10.1016/j.molliq.2018.05.129
Nikam, A., Prasad, V. L. B., and Kulkarni, A. A. (2018). Wet Chemical Synthesis of Metal Oxide Nanoparticles: a Review. CrystEngComm 20. doi:10.1039/c8ce00487k
Peng, P., Wang, Y., and Jiang, F. (2022). Numerical Study of PCM Thermal Behavior of a Novel PCM-Heat Pipe Combined System for Li-Ion Battery Thermal Management. Appl. Therm. Eng. 209, 118293. doi:10.1016/j.applthermaleng.2022.118293
Qureshi, Z. A., Ali, H. M., and Khushnood, S. (2018). Recent Advances on Thermal Conductivity Enhancement of Phase Change Materials for Energy Storage System: A Review. Int. J. Heat Mass Transf. 127, 838–856. doi:10.1016/j.ijheatmasstransfer.2018.08.049
Rao, Z., and Wang, S. (2011). A Review of Power Battery Thermal Energy Management. Renew. Sustain. Energy Rev. 15, 4554–4571. doi:10.1016/j.rser.2011.07.096
Rao, Z., Wang, S., Wu, M., Lin, Z., and Li, F. (2013). Experimental Investigation on Thermal Management of Electric Vehicle Battery with Heat Pipe. Energy Convers. Manag. 65, 92–97. doi:10.1016/j.enconman.2012.08.014
Rathod, M. K. (2018). “Phase Change Materials and Their Applications,” in Phase Change Materials and Their Applications. doi:10.5772/intechopen.75923
Rehman, T.-u., Ali, H. M., Saieed, A., Pao, W., and Ali, M. (2018). Copper foam/PCMs Based Heat Sinks: An Experimental Study for Electronic Cooling Systems. Int. J. Heat Mass Transf. 127, 381–393. doi:10.1016/j.ijheatmasstransfer.2018.07.120
Ren, Y., Yu, Z., and Song, G. (2017). Thermal Management of a Li-Ion Battery Pack Employing Water Evaporation. J. Power Sources 360, 166–171. doi:10.1016/j.jpowsour.2017.05.116
Reyes, J., and Kota, K. (2017). Convective Performance of a Dielectric Liquid in a Channel with Conducting-Lubricating (CO-LUB) Walls for Liquid Cooling of Electronics. Int. Commun. Heat Mass Transf. 89, 147–153. doi:10.1016/j.icheatmasstransfer.2017.10.004
Rufuss, D. D. W., Suganthi, L., Iniyan, S., and Davies, P. A. (2018). Effects of Nanoparticle-Enhanced Phase Change Material (NPCM) on Solar Still Productivity. J. Clean. Prod. 192, 9–29. doi:10.1016/j.jclepro.2018.04.201
Saw, L. H., Tay, A. A. O., and Zhang, L. W. (2015). “Thermal Management of Lithium-Ion Battery Pack with Liquid Cooling,” in Annual IEEE Semiconductor Thermal Measurement and Management Symposium 2015-April, 298–302. doi:10.1109/SEMI-THERM.2015.7100176
Shen, Z.-G., Chen, S., Liu, X., and Chen, B. (2021). A Review on Thermal Management Performance Enhancement of Phase Change Materials for Vehicle Lithium-Ion Batteries. Renew. Sustain. Energy Rev. 148, 111301. doi:10.1016/j.rser.2021.111301
Ulrych, J., Svoboda, M., Polansky, R., and Pihera, J. (2014). “Dielectric Analysis of Vegetable and Mineral Oils,” in Proceeding of the 2014 IEEE 18th International Conference on Dielectric Liquids (ICDL). doi:10.1109/icdl.2014.6893085
van Gils, R. W., Danilov, D., Notten, P. H. L., Speetjens, M. F. M., and Nijmeijer, H. (2014). Battery Thermal Management by Boiling Heat-Transfer. Energy Convers. Manag. 79, 9–17. doi:10.1016/j.enconman.2013.12.006
Wan, X., Guo, B., and Xu, J. (2017). A Facile Hydrothermal Preparation for Phase Change Materials Microcapsules with a Pliable Self-Recovering Shell and Study on its Thermal Energy Storage Properties. Powder Technol. 312, 144–151. doi:10.1016/j.powtec.2017.02.035
Wang, C., Zhang, G., Meng, L., Li, X., Situ, W., Lv, Y., et al. (2017a). Liquid Cooling Based on Thermal Silica Plate for Battery Thermal Management System. Int. J. Energy Res. 41, 2468–2479. doi:10.1002/er.3801
Wang, J., Kang, Q., Yuan, J., Fu, Q., Chen, C., Zhai, Z., et al. (2021). Dendrite‐free Lithium and Sodium Metal Anodes with Deep Plating/stripping Properties for Lithium and Sodium Batteries. Carbon Energy 3, 153–166. doi:10.1002/cey2.94
Wang, J., Xu, H., Xu, X., and Pan, C. (2017b). Design and Simulation of Liquid Cooled System for Power Battery of PHEV. IOP Conf. Ser. Mat. Sci. Eng. 231, 012025. doi:10.1088/1757-899X/231/1/012025
Wang, Q., Jiang, B., Xue, Q. F., Sun, H. L., Li, B., Zou, H. M., et al. (2015). Experimental Investigation on EV Battery Cooling and Heating by Heat Pipes. Appl. Therm. Eng. 88, 54–60. doi:10.1016/j.applthermaleng.2014.09.083
Wang, Q., Ping, P., Zhao, X., Chu, G., Sun, J., and Chen, C. (2012). Thermal Runaway Caused Fire and Explosion of Lithium Ion Battery. J. Power Sources 208, 210–224. doi:10.1016/j.jpowsour.2012.02.038
Wang, Y., Gao, Q., Wang, G., Lu, P., Zhao, M., and Bao, W. (2018). A Review on Research Status and Key Technologies of Battery Thermal Management and its Enhanced Safety. Int. J. Energy Res. 42, 4008–4033. doi:10.1002/er.4158
Wang, Z., Zhang, H., and Xia, X. (2017c). Experimental Investigation on the Thermal Behavior of Cylindrical Battery with Composite Paraffin and Fin Structure. Int. J. Heat Mass Transf. 109, 958–970. doi:10.1016/j.ijheatmasstransfer.2017.02.057
Wang, Z., Zhang, Z., Jia, L., and Yang, L. (2015). Paraffin and Paraffin/aluminum Foam Composite Phase Change Material Heat Storage Experimental Study Based on Thermal Management of Li-Ion Battery. Appl. Therm. Eng. 78, 428–436. doi:10.1016/j.applthermaleng.2015.01.009
Wei, S., Duan, Z., Xia, Y., Huang, C., Ji, R., Zhang, H., et al. (2019). Preparation and Thermal Performances of Microencapsulated Phase Change Materials with a Nano-Al2O3-Doped Shell. J. Therm. Analysis Calorim. 138 (1), 233–241. doi:10.1007/s10973-019-08097-9
Wiriyasart, S., Hommalee, C., Sirikasemsuk, S., Prurapark, R., and Naphon, P. (2020). Thermal Management System with Nanofluids for Electric Vehicle Battery Cooling Modules. Case Stud. Therm. Eng. 18, 100583. doi:10.1016/j.csite.2020.100583
Wu, W., Ye, G., Zhang, G., and Yang, X. (2022). Composite Phase Change Material with Room-Temperature-Flexibility for Battery Thermal Management. Chem. Eng. J. 428, 131116. doi:10.1016/J.CEJ.2021.131116
Xu, H., Zhong, W., Jin, B., and Wang, J. (2014). Flow Pattern and Transition in Gas-Liquid-Solid Three Phase Spouted Bed. Powder Technol. 267, 18–25. doi:10.1016/j.powtec.2014.07.010
Yang, R., Zhang, X. J., Fan, T. F., Jiang, D. P., and Wang, Q. (2014). Improved Electrochemical Performance of Ternary Sn–Sb–Cu Nanospheres as Anode Materials for Lithium-Ion Batteries. Rare Met., 39, 1159–1164. doi:10.1007/s12598-014-0303-6
Yang, Y., Peng, W., Guo, H., Wang, Z., Li, X., and Zhou, Y. (2007). Effects of Modification on Performance of Natural Graphite Coated by Si02 for Anode of Lithium Ion Batteries. Transact. Nonferrous Met. Soc. China 17, 1339–1342. doi:10.1016/S1003-6326(07)60273-8
Yang, S.-c., Hua, Y., Qiao, D., LianPan, Y.-b., Pan, Y.-w., and He, Y.-l. (2019). A Coupled Electrochemical-Thermal-Mechanical Degradation Modelling Approach for Lifetime Assessment of Lithium-Ion Batteries. Electrochimica Acta 326, 134928. doi:10.1016/j.electacta.2019.134928
Yang, S., He, R., Zhang, Z., Cao, Y., Gao, X., and Liu, X. (2020). CHAIN: Cyber Hierarchy and Interactional Network Enabling Digital Solution for Battery Full-Lifespan Management. Matter 3, 27–41. doi:10.1016/j.matt.2020.04.015
Yang, S., Zhang, Z., Cao, R., Wang, M., Cheng, H., Zhang, L., et al. (2021). Implementation for a Cloud Battery Management System Based on the CHAIN Framework. Energy AI 5, 100088. doi:10.1016/j.egyai.2021.100088
Yazid, M. N. A. W. M., Sidik, N. A. C., Mamat, R., and Najafi, G. (2016). A Review of the Impact of Preparation on Stability of Carbon Nanotube Nanofluids. Int. Commun. Heat Mass Transf. 78, 253–263. doi:10.1016/j.icheatmasstransfer.2016.09.021
You, H., Zhu, J., Wang, X., Jiang, B., Sun, H., Liu, X., et al. (2022). Nonlinear Health Evaluation for Lithium-Ion Battery within Full-Lifespan. J. Energy Chem. 72, 333–341. doi:10.1016/j.jechem.2022.04.013
Yuan, H., Song, W., Wang, M., Gu, Y., and Chen, Y. (2019). Lithium-ion Conductive Coating Layer on Nickel Rich Layered Oxide Cathode Material with Improved Electrochemical Properties for Li-Ion Battery. J. Alloys Compd. 784, 1311–1322. doi:10.1016/j.jallcom.2019.01.072
Zeng, Z., Murugesan, V., Han, K. S., Jiang, X., Cao, Y., Xiao, L., et al. (2018). Non-flammable Electrolytes with High Salt-To-Solvent Ratios for Li-Ion and Li-Metal Batteries. Nat. Energy 3, 674–681. doi:10.1038/s41560-018-0196-y
Zhang, L.-S., Gao, X.-L., Liu, X.-H., Zhang, Z.-J., Cao, R., Cheng, H.-C., et al. (2022). CHAIN: Unlocking Informatics-Aided Design of Li Metal Anode from Materials to Applications. Rare Mater. 41, 1477–1489. doi:10.1007/s12598-021-01925-8
Zhang, Q., Huo, Y., and Rao, Z. (2016). Numerical Study on Solid-Liquid Phase Change in Paraffin as Phase Change Material for Battery Thermal Management. Sci. Bull. 61, 391–400. doi:10.1007/s11434-016-1016-z
Zhang, T., Gao, C., Gao, Q., Wang, G., Liu, M., Guo, Y., et al. (2015). Status and Development of Electric Vehicle Integrated Thermal Management from BTM to HVAC. Appl. Therm. Eng. 88, 398–409. doi:10.1016/j.applthermaleng.2015.02.001
Zheng, G., Lee, S. W., Liang, Z., Lee, H.-W., Yan, K., Yao, H., et al. (2014). Interconnected Hollow Carbon Nanospheres for Stable Lithium Metal Anodes. Nat. Nanotech 9, 618–623. doi:10.1038/nnano.2014.152
Zhou, C.-C., Su, Z., Gao, X.-L., Cao, R., Yang, S.-C., and Liu, X.-H. (2021). Ultra-high-energy Lithium-Ion Batteries Enabled by Aligned Structured Thick Electrode Design. Rare Mater. 41, 14–20. doi:10.1007/s12598-021-01785-2
Zhu, J., Wang, Y., Huang, Y., Bhushan Gopaluni, R., Cao, Y., Heere, M., et al. (2022). Data-driven Capacity Estimation of Commercial Lithium-Ion Batteries from Voltage Relaxation. Nat. Commun. 13, 2261. doi:10.1038/s41467-022-29837-w
Zou, D., Ma, X., Liu, X., Zheng, P., and Hu, Y. (2018). Thermal Performance Enhancement of Composite Phase Change Materials (PCM) Using Graphene and Carbon Nanotubes as Additives for the Potential Application in Lithium-Ion Power Battery. Int. J. Heat Mass Transf. 120, 33–41. doi:10.1016/j.ijheatmasstransfer.2017.12.024
Keywords: refrigerant materials, battery thermal management, liquid cooling, phase change material, thermal safety
Citation: Yang S, Lin J, Zhang Z, Zhang C, Zheng X, Xie W, Wang L, Chen S and Liu X (2022) Advanced Engineering Materials for Enhancing Thermal Management and Thermal Safety of Lithium-Ion Batteries: A Review. Front. Energy Res. 10:949760. doi: 10.3389/fenrg.2022.949760
Received: 21 May 2022; Accepted: 13 June 2022;
Published: 01 July 2022.
Edited by:
Xuekun Lu, University College London, United KingdomReviewed by:
Tom Tranter, National Physical Laboratory, United KingdomTao Zhu, Imperial College London, United Kingdom
Copyright © 2022 Yang, Lin, Zhang, Zhang, Zheng, Xie, Wang, Chen and Liu. This is an open-access article distributed under the terms of the Creative Commons Attribution License (CC BY). The use, distribution or reproduction in other forums is permitted, provided the original author(s) and the copyright owner(s) are credited and that the original publication in this journal is cited, in accordance with accepted academic practice. No use, distribution or reproduction is permitted which does not comply with these terms.
*Correspondence: Lijing Wang, d2FuZ2xpamluZ0BidWFhLmVkdS5jbg==; Siyan Chen, Y2hlbnNpeWFuMTk4N0BqbHUuZWR1LmNu; Xinhua Liu, bGl1eGluaHVhMTlAYnVhYS5lZHUuY24=