Introduction
In recent years, with the integration and miniaturization of electronic equipment, the high-flux heat dissipation problem in confined space draws increasing attention. Available studies show that a sharp rise of operating temperature poses a serious threat to the stability and reliability of electronic equipment (Laguna et al., 2018; Li et al., 2022). Therefore, the efficient cooling technology has become the key issue for safe and steady operation of electronic equipment (Zhang et al., 2011; Zhang et al., 2019). Micro-oscillation heat pipe (MOHP), as a new cooling technology, is an attracting device for efficient electronic cooling due to its advantages of small size, simple structure, high thermal conductivity, and so on (Vasiliev, 2008; Liu et al., 2013). MOHPs commonly exhibit as the flat-plate structures with one serpentine micro-channel or several ones in them, which are usually fabricated by microelectromechanical systems (MEMS). The MOHPs are able to effectively improve the heat transfer performance in a confined space due to the good combination of internal sensible and latent heat transfer of vapor–liquid two-phase flow. Note that, owing to effects induced by more confined space in the micro-channel, the MOHPs exhibit different thermo-hydrodynamic characteristics when compared with the conventional oscillating heat pipes (OHPs) with minichannel. Recently, many researchers have made a series of progress in the field of MOHP, which is of great significance to develop its heat transfer enhancement methods and practical application in the future. Hence, the research progress of the MOHPs are briefly reviewed in this study, including the hydrodynamic characteristics, thermal performance, enhancement investigation on thermal performance, and the prospects in application field. Typical MOHPs and their characteristics involved in this paper are shown in Figure 1.
Hydrodynamic Characteristics in the MOHPs
The thermal performance of a heat pipe is largely determined by the internal flow motions of the working fluid, and thus it is of great significance to analyze the hydrodynamic characteristics in the MOHPs through visual thermal experimental studies. Therefore, researchers conducted a large number of visualization experiments on silicon-based MOHPs. It was found that due to influences in the micrometer-scale channels (e.g., large flow resistance and prominent interface tension), the operation of working fluid in the MOHPs has some different characteristics from that in the conventional OHPs. Especially, the complete fluid circulation under a relatively high-power inputs in the conventional OHPs was not observed in the MOHPs (Qu and Wu, 2011; Qu et al., 2012b; Liu et al., 2019). For example, Qu et al. (2012b) carried out simultaneous visualization and measurement study on MOHPs with trapezoidal cross section. Results show that for these MOHPs with hydraulic diameters of 251, 352, and 394 μm (numbered #1, #2, and #3, respectively), the characteristic bulk circulation can only be observed in #3 of the largest hydraulic diameter at high heat loads. Instead, a characteristic bulk circulation was observed at relatively high-power inputs (Qu and Wu, 2011; Qu et al., 2012b). Under this fluid motion mode, the working fluid oscillates with a temporary and incomplete directional flow. Also, affected by the efficient heat conduction of the working fluid between the evaporator and condenser, the heat transfer performance of heat pipe was further enhanced in a characteristic bulk circulation state (Qu and Wu, 2011). On the other hand, more similar flow motions to the traditional OHPs were observed in the MOHPs. For example, in the experimental study conducted by Liu et al. (2019) on a MOHP with rectangular section having hydraulic diameter of 550 μm, the fluid flow mainly presented three motion modes including stop-over, small oscillation, and bulk oscillation. The oscillatory motions of the fluid in the MOHP are characterized by intermittent or individual appearance of these three modes.
Furthermore, MOHPs also have some flow patterns different from the conventional OHPs. Flow patterns commonly seen in conventional OHPs include semi-annular/annular flow, plug/slug flow, bubbly flow, and transitional flow between them (Xu et al., 2005; Liu et al., 2016). In addition to these flow patterns mentioned before, another flow pattern called injection flow was observed in the MOHPs (Qu and Wu, 2010; Qu et al., 2012b; Liu et al., 2019). Generally, under the condition of bulk oscillation, the vapor phase with thick liquid film continuously shrink and break up in the condensation process, forming the injection flow at the end of the annular flow. Accordingly, the bubbly-slug flow and the annular flows come out in the upper and lower parts of the injection flow, respectively. Moreover, nucleate boiling is also an important aspect in the studies on the MOHPs. Commonly, nucleation was hard to be observed during the boiling in the micrometer-scale channels. However, nucleate boiling was observed in MOHPs with larger diameter at the quasi-steady oscillation state (Qu and Wu, 2010; Qu et al., 2012b). This is because the intense film evaporation, instead of bubble’s generation and expansion, drives the two-phase fluid oscillating in the MOHPs with small diameter.
Thermal Performance of the MOHPs
In addition to the hydrodynamic characteristics, many researches about the MOHPs were focused on the thermal performance, which is a most important issue for its practical application. The efficient heat transfer of MOHPs has been proved according to the rapid start-up and stable operation (Qu and Wu, 2011; Qu et al., 2012b; Liu et al., 2019). However, driven by the phase change process of the working fluid, the MOHPs are not able to operate before the heat input reaches a critical value. As the MOHPs start-up, the working fluid vaporizes rapidly and takes away a large amount of heat from the evaporator, resulting in the decrease of evaporator temperature. Qu et al. (2012a) analyzed the thermal performance of the heat pipes in the experimental study and proposed that the MOHPs can effectively reduce the evaporator temperature, and the maximum temperature reduction can reach 42.1°C. Moreover, Qu and Wu (2011), Qu et al. (2012b), and Liu et al. (2019) also stated that the thermal performance was closely related to the fluid flow patterns in the micro-channels under the oscillating state of the MOHPs. The heat input into the evaporator of the MOHPs was transferred efficiently to the condenser by the bulk oscillation of the fluid, resulting in a smaller thermal resistance. Simultaneously, the injection flow, which was never observed in conventional OHPs, also facilitated the condensation heat transfer in the MOHPs (Sun et al., 2017). Thereafter, Liu et al. (2019) analyzed the oscillating wall temperature of the evaporator and the condenser of the MOHPs in detail and confirmed the relationship between thermal performance of the MOHPs and fluid flow motions in the micro-channels. Note that, when stop-over occurred, the evaporator temperature rose due to heat accumulation, while the condenser temperature dropped due to continuous cooling, which was shown as a series of corresponding peaks and valleys on the wall temperature oscillation at the evaporator and the condenser, respectively. In addition to the factors mentioned before, the thermal performance of the MOHPs was also related to the physical properties of working fluid, filling ratios, power inputs, inclination angles, channel sections, etc (Youn and Kim, 2012; Lee and Kim, 2017; Liu et al., 2019). Also, it needs to be emphasized that Lee and Kim (2017) pointed out that the heat transfer limit of the MOHPs is positively correlated with the cubic of the micro-channel hydraulic diameter regardless of the cross-sectional shape.
Enhancement of MOHPs’ Thermal Performance
As studies on the MOHPs continue, the complex heat and mass transfer characteristics had been gradually revealed. A new problem, heat transfer enhancement of the MOHPs, was increasingly noticed. In terms of the working fluid, considering the ultrahigh flow resistance in the micro-channels (Qu et al., 2014; Wang et al., 2018), the thermal physical property is a decisive factor in the selection of working fluid (Qu et al., 2016; Deng et al., 2022). Yang et al. (2015) experimentally proved that the high (dP/dT)sat of methanol contributes to the fluid oscillating and improved the thermal performance of the MOHPs. In addition, increasing number of researches concentrated on optimizing the structural design to improve the MOHPs’ thermal performance (Chen et al., 2021). Sun et al. (2018) pointed out that micro-cavities embedded on the micro-channel wall can promote nucleation, thus enhancing the thermal performance of MOHPs. Thereafter, Kim W. and Kim S. J. (2018) confirmed that cavities of different sizes promote nucleation and reduce the start-up power of the MOHPs in different degrees. Also, the thermal resistance of the MOHPs with embedded cavities was reduced by up to 57%. Furthermore, in order to avoid the dry-out in evaporator, Kang and Huang (2002) and Hung and Seng (2011) successively proposed to modify the channel section into star-shaped, diamond-shaped, and other structures with sharp corners to enhance the capillary force, thus improving the rewetting of evaporator. Recently, Lee and Kim (2017) confirmed that, at the same hydraulic diameter, the maximum allowable heat flux of the MOHPs with square section was increased by 70% than that of the MOHPs with circular section. Moreover, from the perspective of channel optimization design, Kwon and Kim (2015) designed the MOHPs with a dual-diameter channel and proposed that the design with double-diameters reduces the flow resistance of the working fluid and promotes the formation of bulk oscillation, thus improving the thermal performance of the MOHPs. Huang et al. (2018), Xia et al. (2019), and Li et al. (2020) introduced curved structures into the micro-channels and proved that curved channels can effectively improve thermal performance of the micro-channels by promoting nucleation and destroying the heat transfer boundary layer. The curved micro-channel mentioned before with sinusoidal and triangular wavy sidewall gives new clues in terms of heat transfer enhancement methods for the MOHPs. In addition, Kim J. and Kim S. J. (2018) also studied the influence of condenser length on the thermal performance. The results indicate that there exists an optimal condenser length for the MOHPs of different designs.
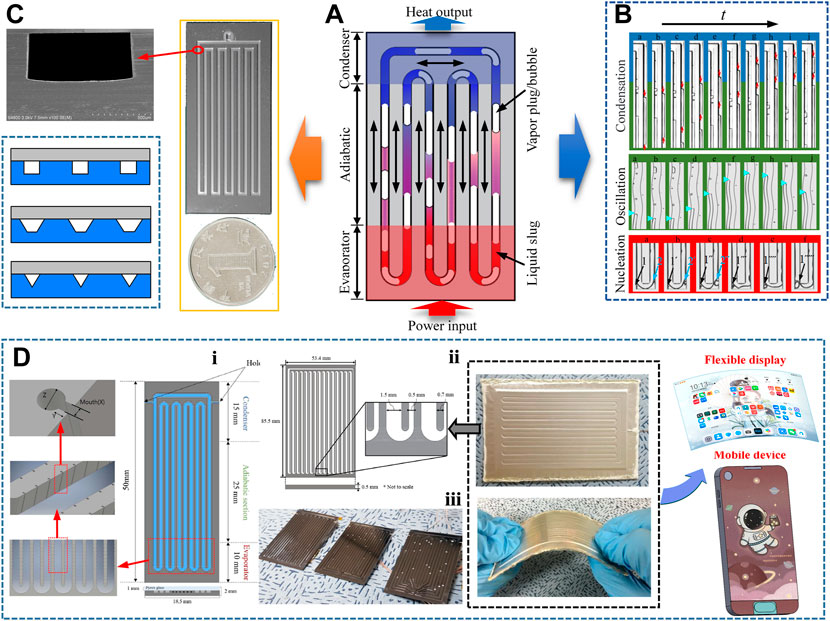
FIGURE 1. Typical MOHPs and their characteristics: (A) operating principle of the MOHPs; (B) typical hydraulic characteristics in micro-channel; (C) photo of typical MOHPs and common section shapes of micro-channel; (D) developed MOHPs with practical value (Kim W. and Kim S. J., 2018)i, (Lim and Kim, 2017; Lim and Kim, 2018; Jung et al., 2020)ii, (Lim and Kim, 2017; Lim and Kim, 2018; Jung et al., 2020)iii.
Prospects of the MOHPs’ Applications
Based on the broad prospects in aerospace, electronic, and other potential applications, various MOHPs with potential application value have been developed (Chen et al., 2022). Obviously, the application of the MOHPs in high-power heat dissipation is an important aspect. Luo et al. (2015) tested a silicon–aluminum MOHPs used for LED heat dissipation, results show that the MOHPs can effectively control the LED operating at a normal temperature. Previously, many researchers have carried out a lot of research on silicon-based MOHPs with integrated chips (Qu et al., 2012b; Kim W. and Kim S. J., 2018; Liu et al., 2019; Lim and Kim, 2021). Recently, with the development of flexible display technology, flexible MOHPs based on polymers is considered to be a solution to the heat dissipation due to its advantages of integration into flexible electronic packaging (Lim and Kim, 2018; Jung et al., 2020).
Conclusion
This study reviews the hydrodynamic characteristics, thermal performance, and its enhancement methods as well as prospects of the MOHPs’ applications. The characteristic fluid motions and flow patterns during the operation of the MOHPs are introduced, and the related thermal performance is discussed. In addition, the on-going investigation of heat transfer enhancement methods for the MOHPs are also summarized and analyzed. Finally, the potential applications of the MOHPs are pointed out. It is believed these viewpoints on the recent advances of MOHPs could not only help the researchers to establish an overview of studies on the MOHPs but also contribute to study and development of the MOHPs in future.
Author Contributions
HL wrote the first draft of the manuscript. LL developed the concept of the study and revised the manuscript. All authors revised the manuscript and read and approved the submitted version.
Funding
This work was partially supported by the Natural Science Foundation of Jiangsu Province (No. BK20210819).
Conflict of Interest
The authors declare that the research was conducted in the absence of any commercial or financial relationships that could be construed as a potential conflict of interest.
Publisher’s Note
All claims expressed in this article are solely those of the authors and do not necessarily represent those of their affiliated organizations, or those of the publisher, the editors, and the reviewers. Any product that may be evaluated in this article, or claim that may be made by its manufacturer, is not guaranteed or endorsed by the publisher.
References
Chen, X., Chen, S., Zhang, Z., Sun, D., and Liu, X. (2021). Heat Transfer Investigation of a Flat-Plate Oscillating Heat Pipe with Tandem Dual Channels under Nonuniform Heating. Int. J. Heat Mass Transf. 180, 121830. doi:10.1016/j.ijheatmasstransfer.2021.121830
Chen, X., Liu, X., Xu, D., and Chen, Y. (2022). Thermal Performance of a Tandem-Dual-Channel Flat-Plate Pulsating Heat Pipe Applicable to Hypergravity. Int. J. Heat Mass Transf. 189, 122656. doi:10.1016/j.ijheatmasstransfer.2022.122656
Deng, Z., Gao, S., Wang, H., Liu, X., and Zhang, C. (2022). Visualization Study on the Condensation Heat Transfer on Vertical Surfaces with a Wettability Gradient. Int. J. Heat Mass Transf. 184, 122331. doi:10.1016/j.ijheatmasstransfer.2021.122331
Huang, H., Wu, H., and Zhang, C. (2018). An Experimental Study on Flow Friction and Heat Transfer of Water in Sinusoidal Wavy Silicon Microchannels. J. Micromech. Microeng. 28 (5), 055003. doi:10.1088/1361-6439/aaad46
Hung, Y. M., and Seng, Q. b. (2011). Effects of Geometric Design on Thermal Performance of Star-Groove Micro-heat Pipes. Int. J. Heat Mass Transf. 54 (5-6), 1198–1209. doi:10.1016/j.ijheatmasstransfer.2010.09.070
Jung, C., Lim, J., and Kim, S. J. (2020). Fabrication and Evaluation of a High-Performance Flexible Pulsating Heat Pipe Hermetically Sealed with Metal. Int. J. Heat Mass Transf. 149, 119180. doi:10.1016/j.ijheatmasstransfer.2019.119180
Kang, S.-W., and Huang, D. (2002). Fabrication of Star Grooves and Rhombus Grooves Micro Heat Pipe. J. Micromech. Microeng. 12 (5), 525–531. doi:10.1088/0960-1317/12/5/303
Kim, J., and Kim, S. J. (2018a). Experimental Investigation on the Effect of the Condenser Length on the Thermal Performance of a Micro Pulsating Heat Pipe. Appl. Therm. Eng. 130, 439–448. doi:10.1016/j.applthermaleng.2017.11.009
Kim, W., and Kim, S. J. (2018b). Effect of Reentrant Cavities on the Thermal Performance of a Pulsating Heat Pipe. Appl. Therm. Eng. 133, 61–69. doi:10.1016/j.applthermaleng.2018.01.027
Kwon, G. H., and Kim, S. J. (2015). Experimental Investigation on the Thermal Performance of a Micro Pulsating Heat Pipe with a Dual-Diameter Channel. Int. J. Heat Mass Transf. 89, 817–828. doi:10.1016/j.ijheatmasstransfer.2015.05.091
Laguna, G., Vilarrubí, M., Ibañez, M., Betancourt, Y., Illa, J., Azarkish, H., et al. (2018). Numerical Parametric Study of a Hotspot-Targeted Microfluidic Cooling Array for Microelectronics. Appl. Therm. Eng. 144, 71–80. doi:10.1016/j.applthermaleng.2018.08.030
Lee, J., and Kim, S. J. (2017). Effect of Channel Geometry on the Operating Limit of Micro Pulsating Heat Pipes. Int. J. Heat Mass Transf. 107, 204–212. doi:10.1016/j.ijheatmasstransfer.2016.11.036
Li, W., Li, C., Wang, Z., and Chen, Y. (2022). Enhanced Flow Boiling in Microchannels Integrated with Supercapillary Pinfin Fences. Int. J. Heat Mass Transf. 183, 122185. doi:10.1016/j.ijheatmasstransfer.2021.122185
Li, Y. F., Xia, G. D., Ma, D. D., Yang, J. L., and Li, W. (2020). Experimental Investigation of Flow Boiling Characteristics in Microchannel with Triangular Cavities and Rectangular Fins. Int. J. Heat Mass Transf. 148, 119036. doi:10.1016/j.ijheatmasstransfer.2019.119036
Lim, J., and Kim, S. J. (2021). A Channel Layout of a Micro Pulsating Heat Pipe for an Excessively Localized Heating Condition. Appl. Therm. Eng. 196, 117266. doi:10.1016/j.applthermaleng.2021.117266
Lim, J., and Kim, S. J. (2017). “A Polymer-Based Pulsating Heat Pipe: Fabrication and Investigation of Thermal Performance,” in 2017 16th IEEE Intersociety Conference on Thermal and Thermomechanical Phenomena in Electronic Systems (ITherm), Orlando, FL, USA, 30 May-2 June 2017. doi:10.1109/itherm.2017.7992542
Lim, J., and Kim, S. J. (2018). Fabrication and Experimental Evaluation of a Polymer-Based Flexible Pulsating Heat Pipe. Energy Convers. Manag. 156, 358–364. doi:10.1016/j.enconman.2017.11.022
Liu, X., Chen, Y., and Shi, M. (2013). Dynamic Performance Analysis on Start-Up of Closed-Loop Pulsating Heat Pipes (CLPHPs). Int. J. Therm. Sci. 65, 224–233. doi:10.1016/j.ijthermalsci.2012.10.012
Liu, X., Sun, Q., Zhang, C., and Wu, L. (2016). High-Speed Visual Analysis of Fluid Flow and Heat Transfer in Oscillating Heat Pipes with Different Diameters. Appl. Sci. 6 (11), 321. doi:10.3390/app6110321
Liu, X., Xu, L., Wang, C., and Han, X. (2019). Experimental Study on Thermo-Hydrodynamic Characteristics in a Micro Oscillating Heat Pipe. Exp. Therm. Fluid Sci. 109, 109871. doi:10.1016/j.expthermflusci.2019.109871
Luo, Y., Yu, B., Shan, Q., and Wang, X. (2015). “A Silicon-Aluminum Micro Heat Sink for Light Emitting Diode (LED) Chips,” in 2015 16th International Conference on Electronic Packaging Technology (ICEPT), Changsha, China, 11-14 Aug. 2015, 526–529.
Qu, J., Wang, Q., Li, C., Han, X., and He, Z. (2014). A Simple Model for Taylor Flow Induced Contact Angle Hysteresis and Capillary Pressure inside Mini/micro-Scale Capillary Tubes. Int. J. Heat Mass Transf. 78, 1004–1007. doi:10.1016/j.ijheatmasstransfer.2014.07.048
Qu, J., Wang, Q., and Sun, Q. (2016). Lower Limit of Internal Diameter for Oscillating Heat Pipes: A Theoretical Model. Int. J. Therm. Sci. 110, 174–185. doi:10.1016/j.ijthermalsci.2016.07.002
Qu, J., Wu, H.-Y., and Wang, Q. (2012a). Experimental Investigation of Silicon-Based Micro-pulsating Heat Pipe for Cooling Electronics. Nanoscale Microscale Thermophys. Eng. 16 (1), 37–49. doi:10.1080/15567265.2011.645999
Qu, J., Wu, H., and Cheng, P. (2012b). Start-up, Heat Transfer and Flow Characteristics of Silicon-Based Micro Pulsating Heat Pipes. Int. J. Heat Mass Transf. 55 (21-22), 6109–6120. doi:10.1016/j.ijheatmasstransfer.2012.06.024
Qu, J., and Wu, H. (2010). Flow Visualization of Silicon-Based Micro Pulsating Heat Pipes. Sci. China Technol. Sci. 53 (4), 984–990. doi:10.1007/s11431-009-0391-y
Qu, J., and Wu, H. Y. (2011). Silicon-Based Micro Pulsating Heat Pipe for Cooling Electronics. Amr 403-408, 4260–4265. doi:10.4028/www.scientific.net/amr.403-408.4260
Sun, Q., Qu, J., Yuan, J., and Wang, H. (2018). Start-up Characteristics of MEMS-Based Micro Oscillating Heat Pipe with and without Bubble Nucleation. Int. J. Heat Mass Transf. 122, 515–528. doi:10.1016/j.ijheatmasstransfer.2018.02.003
Sun, Q., Qu, J., Yuan, J., and Wang, Q. (2017). Operational Characteristics of an MEMS-Based Micro Oscillating Heat Pipe. Appl. Therm. Eng. 124, 1269–1278. doi:10.1016/j.applthermaleng.2017.06.109
Vasiliev, L. L. (2008). Micro and Miniature Heat Pipes - Electronic Component Coolers. Appl. Therm. Eng. 28 (4), 266–273. doi:10.1016/j.applthermaleng.2006.02.023
Wang, J., Gao, W., Zhang, H., Zou, M., Chen, Y., and Zhao, Y. (2018). Programmable Wettability on Photocontrolled Graphene Film. Sci. Adv. 4 (9), eaat7392. doi:10.1126/sciadv.aat7392
Xia, G. D., Tang, Y. X., Zong, L. X., Ma, D. D., Jia, Y. T., and Rong, R. Z. (2019). Experimental Investigation of Flow Boiling Characteristics in Microchannels with the Sinusoidal Wavy Sidewall. Int. Commun. Heat Mass Transf. 101, 89–102. doi:10.1016/j.icheatmasstransfer.2019.01.006
Xu, J. L., Li, Y. X., and Wong, T. N. (2005). High Speed Flow Visualization of a Closed Loop Pulsating Heat Pipe. Int. J. Heat Mass Transf. 48 (16), 3338–3351. doi:10.1016/j.ijheatmasstransfer.2005.02.034
Yang, K.-S., Cheng, Y.-C., Liu, M.-C., and Shyu, J.-C. (2015). Micro Pulsating Heat Pipes with Alternate Microchannel Widths. Appl. Therm. Eng. 83, 131–138. doi:10.1016/j.applthermaleng.2015.03.020
Youn, Y. J., and Kim, S. J. (2012). Fabrication and Evaluation of a Slicon-Based Micro Pulsating Heat Spreader. Sensors Actuators A Phys. 174, 189–197. doi:10.1016/j.sna.2011.12.006
Zhang, C., Chen, Y., Wu, R., and Shi, M. (2011). Flow Boiling in Constructal Tree-Shaped Minichannel Network. Int. J. Heat Mass Transf. 54 (1), 202–209. doi:10.1016/j.ijheatmasstransfer.2010.09.051
Keywords: micro-oscillation heat pipes, hydrodynamic characteristics, thermal performance, heat transfer enhancement, application
Citation: Li H and Li L (2022) Viewpoints on the Recent Advances of Micro-Oscillation Heat Pipes. Front. Energy Res. 10:947453. doi: 10.3389/fenrg.2022.947453
Received: 18 May 2022; Accepted: 27 May 2022;
Published: 08 July 2022.
Edited by:
Chengbin Zhang, Southeast University, ChinaReviewed by:
Jinli Lu, Anhui University of Technology, ChinaCopyright © 2022 Li and Li. This is an open-access article distributed under the terms of the Creative Commons Attribution License (CC BY). The use, distribution or reproduction in other forums is permitted, provided the original author(s) and the copyright owner(s) are credited and that the original publication in this journal is cited, in accordance with accepted academic practice. No use, distribution or reproduction is permitted which does not comply with these terms.
*Correspondence: Lirong Li, bGlyb25nbGlAeXp1LmVkdS5jbg==