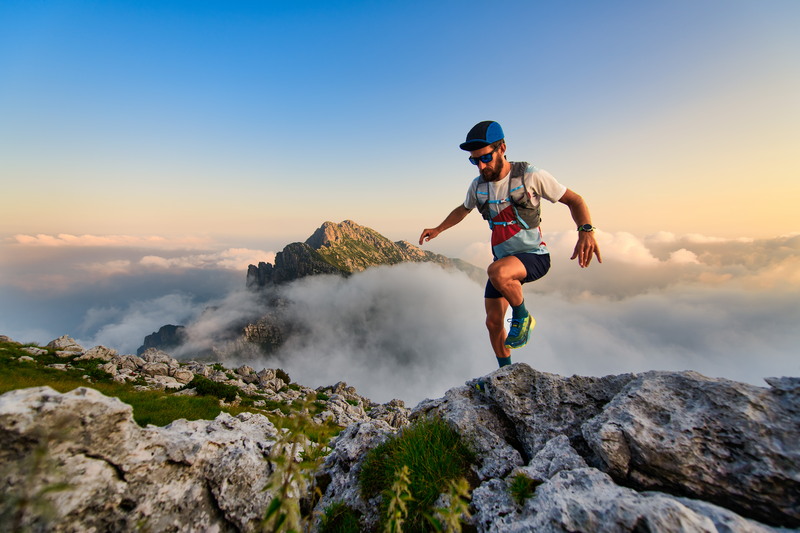
95% of researchers rate our articles as excellent or good
Learn more about the work of our research integrity team to safeguard the quality of each article we publish.
Find out more
OPINION article
Front. Energy Res. , 02 June 2022
Sec. Process and Energy Systems Engineering
Volume 10 - 2022 | https://doi.org/10.3389/fenrg.2022.923454
This article is part of the Research Topic Heat Transfer in Data Centers, Volume II View all 14 articles
The continuous progress of the internet and microelectronics, especially portable devices such as smartphones, tablet computers, and smartwatches, has resulted in compact, integrated, and miniaturized tools, consuming high power. The 11th and 12th generation CPUs are the main CPUs used in laptops in the past 2 years. The operating power consumption has reached 180 W with a size of 50 × 25 mm. The surface heat flux can be up to 14.4 W/cm2 (Liu et al., 2013). The miniaturization of electronic devices has greatly reduced the effective area of heat dissipation. With the continuous upgrading of the power consumption of electronic devices, the surface heat flux will inevitably increase rapidly, bringing tough challenges against the safe cooling limits of portable electronics due to the limited space (Micheli et al., 2013; Tang et al., 2018).
The reliability of electronic devices is apparently sensitive to temperature that should be reserved within safe operational limits. Therefore, developing the advanced heat dissipation technology is continuously required to avoid damage and failure of electronic devices due to overheating. As a passive cooling technology, heat pipe has become an effective approach for electronic cooling, considering high thermal conductivity, simple structure, and no external driving force (Su et al., 2018). However, traditional heat pipes, such as loop heat, pulsating heat, and oscillating heat pipes, can no longer satisfy high heat dissipation in a limited space for portable electronic devices, which are lighter and thinner (Dai et al., 2020). Therefore, ultra-thin heat pipes (UTHP) have been widely investigated and used in high heat flux portable electronic cooling due to their compact size, high stability, and effective temperature uniformity. This study summarizes the recent development of UTHP technology and wick structures and analyzes the challenges and future prospects (Zhong et al., 2020).
UTHP is defined as a flat heat pipe with a thickness of less than 2 mm. UTHP can effectively remove the heat generated by electronic devices because of its thin thickness, high equivalent thermal conductivity, and being closely attached to the electronic devices. The thickness of UTHP for laptops, tablets, and smartphones/watches is 1–2, 0.8–1.2, and 0.4–0.6 mm, respectively (Hong et al., 2017).
Compared with the conventional heat pipe, the structure and wick of the UTHP are quite different due to the miniaturization of the size. At present, UTHP can be divided into flattened heat pipe (FHP), vapor chamber (VC), and ultra-thin loop heat pipe (UTLHP) (Li and Lv, 2016), as shown in Figures 1A–C.
FIGURE 1. Schematic diagram of UTHP: (A) FHP, (B) VC, (C) UTLHP, (D) sintered wick structure, (E) microgrooved wick structure (Gillot et al., 2003), and (F) composite wick structure (Li et al., 2016)
As demonstrated in Figure 1A, the FHP usually is composed of the evaporation section, the insulation section, and the condensation section along the axial direction, which are similar to those of the conventional heat pipe (Cui et al., 2022). The liquid working medium absorbs heat, evaporates in the evaporation section, and condenses into liquid in the condensation section. The liquid working medium flows back from the condensation section end to the evaporation section by capillary force in the wick. The long flat structure manufactured by flatting cylindrical copper pipes enables the FHP to achieve multiple heat sources and long-distance heat transfer. The FHP is widely applied in small mobile devices such as smartphones and tablet computers. However, FHP has the defects of small surface area, single shape, and poor adaptability. The VC consists of a closed container with a plate-like structure (Li et al., 2021). The evaporation and condensation sections are located on both sides of the container while the inner wall is covered with a wick structure, as shown in Figure 1B. The VC has the advantages of lighter weight, larger condensation area, and more flexible structure, which makes the VC widely applied in electronic cooling with high heat flux. The UTLHP is deemed to be more adaptive, and it usually consists of an evaporator, vapor passage, condenser, and liquid return passage, which is in a ring structure as a whole, as illustrated in Figure 1C. All components of the UTLHP are made of smooth walls because of the lower resistance of the working fluid flow, except for the wick structure (Hong et al., 2016). The smooth-walled tube is conducive to the long-distance heat transfer of the UTLHP. In addition, different from other UTHP, separate evaporators and condensers of UTLHP cannot only eliminate possible entrainment effects but also remove more heat generated by electronic devices.
As a core part of the UTHP, wick supplies capillary force through the gas-liquid interface to actuate the working fluid circulation. The heat transfer characteristic of UTHP primarily depends on the wick capillary flow phase transition behavior. At present, the wick structure of UTHP mainly includes the sintered wick, microgrooved wick, and composite wick, as demonstrated in Figures 1D–F.
Currently, most UTHP uses sintered wick structures because of their excellent capability and low cost. The sintered wick can be divided into sintered powder wick, sintered mesh wick, and sintered fiber wick, as shown in Figure 1D for sintered mesh wick (Zu et al., 2021). The most widely used sintered powder wick in the traditional heat pipe has almost been substituted for sintered mesh/fiber wick that is employed to fabricate ultra-high temperature polymers due to thicker powder layers and cracks caused by leveling in UTHP. Using sintered mesh/fiber as wick, thinner, more flexible flat heat pipe can be obtained. The microgrooved wick structure has gradually become the preferred option for UTHP because of unique advantages such as high permeability and low thermal resistance, as shown in Figure 1E (Zeng et al., 2017). The shells of UTHP with the microgrooved wick structure are usually made of non-metallic materials. Moreover, the microgrooved wick structure is mostly fabricated by laser micromachining and plasma etching. Although the micromachining process can obtain thinner UTHP with higher heat transfer characteristics, its high cost, unstable quality, and complicated process limit the applications. The wick of UTHP with good thermal performance should ensure high permeability and large capillary force. The sintered wick structure has higher capillary pump force with lower liquid permeability, while the microgrooved wick structure has the opposite performance. Therefore, composite wick structures that combine two or more types of single wick structures have been investigated to equilibrate the contradiction between high permeability and large capillary force (Jiang et al., 2014). At present, the most used composite wick in UTHP are the sintered mesh-groove composite wick and sintered powder-groove composite wick, as shown in Figure 1F. However, owing to the complicated manufacturing procedure, high cost of manufacture, and low production efficiency, the application of composite wick structure is limited in ultra-thin electronic cooling.
Recently, increasing heat dissipation demands in portable electronic devices with high heat flux has unveiled opportunities and challenges that can affect the progress and applications of UTHP. Considering the research actuality and application requirements of UTHP, the following aspects need to be further studied:
1) Develop more accurate and reliable machining technology and packaging technology for UTHP. Traditional machining methods such as cylindrical heat pipe flattening technology have certain defects, which will cause deformation of the shell, poor sealing performance, and low manufacturing yield. It greatly increases the manufacturing cost and restricts its large-scale development and applications of UTHP.
2) Due to the increasing integration of portable electronic devices, the operating environment of UTHP is becoming continuously complex. It is indispensable to design UTHP with different cross-sectional shapes suitable for the surface structure of the heat source according to the specific operating environment. In addition, the research on the reliability and stability of the UTHP in intermittent operation under the location and conditions of variable heat fluxes and variable heat sources should be carried out, which lays a scientific foundation for further development and applications of UTHP.
ZH contributed to guiding the study. TZ wrote the draft of the manuscript and revised it.
Natural Science Foundation of Jiangsu Province (no. BK20210239).
The authors declare that the research was conducted in the absence of any commercial or financial relationships that could be construed as a potential conflict of interest.
All claims expressed in this article are solely those of the authors and do not necessarily represent those of their affiliated organizations or those of the publisher, the editors, and the reviewers. Any product that may be evaluated in this article, or claim that may be made by its manufacturer, is not guaranteed or endorsed by the publisher.
Cui, Z., Jia, L., Wang, Z., Dang, C., and Yin, L. (2022). Thermal Performance of an Ultra-thin Flat Heat Pipe with Striped Super-hydrophilic Wick Structure. Appl. Therm. Eng. 208, 118249. doi:10.1016/J.APPLTHERMALENG.2022.118249
Dai, X., Tang, Y., Liu, T., and Wang, S. (2020). Experimental Investigation on the Thermal Characteristics of Ultra-thin Flattened Heat Pipes with Bending Angles. Appl. Therm. Eng. 172, 115150. doi:10.1016/J.APPLTHERMALENG.2020.115150
Gillot, C., Avenas, Y., Cezac, N., Poupon, G., Schaeffer, C., and Fournier, E. (2003). Silicon Heat Pipes Used as Thermal Spreaders. IEEE Trans. Comp. Packag. Technol. 26, 332–339. doi:10.1109/TCAPT.2003.815092
Hong, S., Wang, S., and Zhang, L. (2017). Effect of Groove Configuration on Two-phase Flow Instability for Ultra-thin Looped Heat Pipes in Thermal Management System. Int. J. Therm. Sci. 121, 369–380. doi:10.1016/J.IJTHERMALSCI.2017.07.024
Hong, S., Wang, S., and Zhang, Z. (2016). Multiple Orientations Research on Heat Transfer Performances of Ultra-thin Loop Heat Pipes with Different Evaporator Structures. Int. J. Heat Mass Transf. 98, 415–425. doi:10.1016/J.IJHEATMASSTRANSFER.2016.03.049
Liu, X., Chen, Y., and Shi, M. (2013). Dynamic performance analysis on start-up of closed-loop pulsating heat pipes (CLPHPs). Int. J. Therm. Sci. 65, 224–233. doi:10.1016/J.IJTHERMALSCI.2012.10.012
Jiang, L., Ling, J., Jiang, L., Tang, Y., Li, Y., Zhou, W., et al. (2014). Thermal Performance of a Novel Porous Crack Composite Wick Heat Pipe. Energy Convers. Manag. 81, 10–18. doi:10.1016/J.ENCONMAN.2014.01.044
Li, D., Huang, Z., Zhao, J., Jian, Q., and Chen, Y. (2021). Analysis of Heat Transfer Performance and Vapor-Liquid Meniscus Shape of Ultra-thin Vapor Chamber with Supporting Columns. Appl. Therm. Eng. 193, 117001. doi:10.1016/J.APPLTHERMALENG.2021.117001
Li, J., and Lv, L. (2016). Experimental Studies on a Novel Thin Flat Heat Pipe Heat Spreader. Appl. Therm. Eng. 93, 139–146. doi:10.1016/J.APPLTHERMALENG.2015.09.038
Li, Y., Zhou, W., He, J., Yan, Y., Li, B., and Zeng, Z. (2016). Thermal Performance of Ultra-thin Flattened Heat Pipes with Composite Wick Structure. Appl. Therm. Eng. 102, 487–499. doi:10.1016/J.APPLTHERMALENG.2016.03.097
Micheli, L., Sarmah, N., Luo, X., Reddy, K. S., and Mallick, T. K. (2013). Opportunities and Challenges in Micro- and Nano-Technologies for Concentrating Photovoltaic Cooling: A Review. Renew. Sustain. Energy Rev. 20, 595–610. doi:10.1016/J.RSER.2012.11.051
Su, Q., Chang, S., Zhao, Y., Zheng, H., and Dang, C. (2018). A Review of Loop Heat Pipes for Aircraft Anti-icing Applications. Appl. Therm. Eng. 130, 528–540. doi:10.1016/J.APPLTHERMALENG.2017.11.030
Tang, H., Tang, Y., Wan, Z., Li, J., Yuan, W., Lu, L., et al. (2018). Review of Applications and Developments of Ultra-thin Micro Heat Pipes for Electronic Cooling. Appl. Energy 223, 383–400. doi:10.1016/J.APENERGY.2018.04.072
Zeng, J., Lin, L., Tang, Y., Sun, Y., and Yuan, W. (2017). Fabrication and Capillary Characterization of Micro-grooved Wicks with Reentrant Cavity Array. Int. J. Heat Mass Transf. 104, 918–929. doi:10.1016/J.IJHEATMASSTRANSFER.2016.09.007
Zhong, G., Tang, Y., Ding, X., Rao, L., Chen, G., Tang, K., et al. (2020). Experimental Study of a Large-Area Ultra-thin Flat Heat Pipe for Solar Collectors under Different Cooling Conditions. Renew. Energy 149, 1032–1039. doi:10.1016/J.RENENE.2019.10.093
Keywords: ultra-thin heat pipe, wick structure, heat dissipation, portable electronic device, thermal management
Citation: Zhao T and Hu Z (2022) Opportunities and Challenges for the Development of Ultra-Thin Heat Pipe. Front. Energy Res. 10:923454. doi: 10.3389/fenrg.2022.923454
Received: 19 April 2022; Accepted: 02 May 2022;
Published: 02 June 2022.
Edited by:
Xiangdong Liu, Yangzhou University, ChinaReviewed by:
Feng Yao, Suzhou University of Science and Technology, ChinaCopyright © 2022 Zhao and Hu. This is an open-access article distributed under the terms of the Creative Commons Attribution License (CC BY). The use, distribution or reproduction in other forums is permitted, provided the original author(s) and the copyright owner(s) are credited and that the original publication in this journal is cited, in accordance with accepted academic practice. No use, distribution or reproduction is permitted which does not comply with these terms.
*Correspondence: Zheng Hu, emh1QG1pY3JvZmxvd3MubmV0
Disclaimer: All claims expressed in this article are solely those of the authors and do not necessarily represent those of their affiliated organizations, or those of the publisher, the editors and the reviewers. Any product that may be evaluated in this article or claim that may be made by its manufacturer is not guaranteed or endorsed by the publisher.
Research integrity at Frontiers
Learn more about the work of our research integrity team to safeguard the quality of each article we publish.