- 1Cooperative Innovation Center of Unconventional Oil and Gas, Yangtze University (Ministry of Education & Hubei Province), Wuhan, China
- 2Hubei Key Laboratory of Drilling and Production Engineering for Oil and Gas, Yangtze University, Wuhan, China
- 3School of Petroleum Engineering, Yangtze University, Wuhan, China
- 4Chuanxi Drilling Company, CNPC Chuanqing Drilling Engineering Co. Ltd., Chengdu, China
1 Introduction
With the rise in offshore oil and gas, their exploration and development are moving toward deep-water (500–1500 m) and ultra-deep-water (>1500 m) areas, making deep-water–related technology a competitive field among countries (Brockway et al., 2019; Zhong, 2021). China is a newcomer in deep-water oil and gas exploration and lacks key technologies. Compared with onshore drilling, the environment of offshore oil drilling is more complex, and conventional drilling equipment and methods are difficult to adapt to unexpected situations (Gao et al., 2016).
Some field engineering cases show that as the water depth increases, the safe window between fracture-pressure and pore-pressure becomes narrow, and oil and gas development will face many technical difficulties, such as poor drilling conditions and high risks, which eventually lead to huge losses. Conventional drilling technology is costly and risky, and cannot meet the technical requirements of deep-water drilling. Dual-gradient drilling (DKD) can increase the drilling window through certain technical means, which can adapt to the harsh conditions of deep-water well and reduce the drilling risk. Since the 1990s, DKD has been developed and applied to tackle these challenges (Li et al., 2020).
This paper provides a series of outlooks to lead the exploration and development of deep-water oil and gas resources by reviewing the technology and equipment of dual-gradient drilling in deep water, detailing its principles, technical characteristics, and adaptability. Considering the characteristics and challenges, this paper divides dual-gradient drilling into two branches, riser drilling and riserless drilling (Xu et al., 2005).
2 Dual-Gradient Drilling Technology
In conventional drilling, the bottom hole pressure is equal to the drilling fluid column pressure from the sea surface to the bottom hole, which can be expressed as
where
While DGD can have two liquid column gradients in the wellbore annulus (Xu et al., 2005; Scanlon and Medeiros, 2012), the bottom hole pressure is equal to the sum of the fluid column pressure (seawater or a fluid with a density equal to that of seawater) from the sea level to the seafloor and the mud column from the seafloor to the bottom hole. The formula can be expressed as
where
After adopting DGD, the starting point of mud column pressure changes from the sea level to the mud on the seabed line theoretically, increasing the mud safety density window and improving the safety and reliability of underwater operating systems.
The present DGD techniques are shown in Figure 1; the implementation is mainly divided into riser drilling and riserless drilling. Riser drilling includes two categories: a subsea pumping system (SMD, Deep Vision) and a dual-density system (Hollow Microsphere, LSU riser gas-lift/dilution). Riser drilling is of two types: a jetting conductor setting and a riserless mud recovery system.
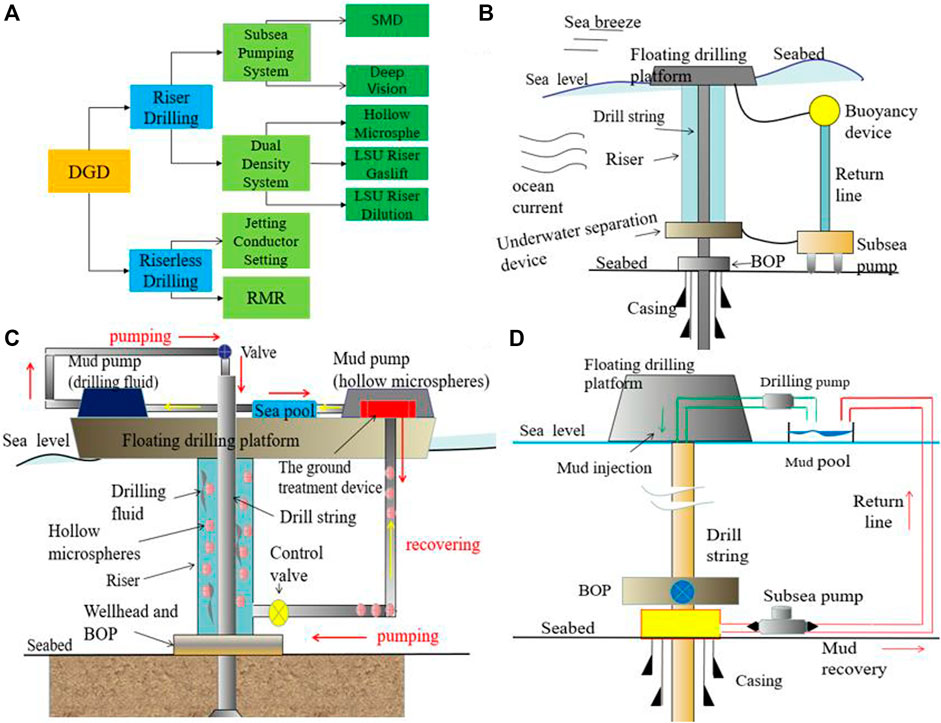
FIGURE 1. (A) Classification of DKD. (B) Schematic diagram of SMD. (C) Schematic diagram of the hollow microsphere system. (D) Schematic diagram of RMR.
3 Riser Drilling
At present, the main methods of realizing DKD with a riser in the industry include a subsea pumping system and a dual-density system (Wang et al., 2019; Pei et al., 2021).
3.1 Subsea Pumping System
The present subsea pumping system takes returns from the well annulus at the seafloor and pumps them back to the surface. By adjusting the inlet pressure of the seafloor pump to near seawater hydrostatic pressure, the idea of dual-gradient drilling is realized.
3.1.1 SMD (Subsea Mudlift Drilling)
In 1996, SMD JIP developed a subsea mudlift drilling system; the principle is as follows: The rig’s mud pumps displace the mud down the drill string, through the bit, and back up the annulus to the seafloor. A subsea rotating diverter (similar to a rotating control device) diverts the mud flow from the annulus to a cutting processor, which crushes large cuttings into a size small enough to pass through the seafloor pump and up the return lines without clogging. After the mud and cuttings pass through the cutting processor, the seafloor pump displaces the returns up the return line and back to the rig.
3.1.2 Deep Vision System
The principle of dual-gradient drilling in the Deep Vision system is similar to the SMD. The difference is that the Deep Vision system adopts coiled tubing drilling technology, which ensures that when a drill tube is connected, the pump can be continuously circulated to ensure safe drilling when encountering a narrow density window and reduce the probability of sticking accidents.
3.2 Dual-Density System
The concept of dual gradients can be accomplished by injecting some specific substances (hollow microspheres, gas, and low-density fluid) into the annulus to reduce the density of the riser annulus and to make it equal to seawater, realizing dual-gradient drilling.
3.2.1 Hollow Microsphere System
The first annular injection method was based on the injection of hollow microspheres at the base of the riser. The hollow microspheres and drilling fluid are mixed in offshore pump sets to form a low-density fluid, which is pumped into the annulus from the seabed through pipelines to reduce the fluid density in the riser. The returning drilling fluid is separated by the ground-handling unit to separate the hollow microspheres and drill cuttings from the drilling fluid. These isolates enter the seawater pool, where the heavy drill cuttings sink to the bottom and the light hollow spheres float on the surface. The advantage of this system is that the hollow microspheres are incompressible and the linear pressure gradient generated can be better combined with the DKD ideas.
3.2.2 Riser Gas Lift
The second substance injected into the annular space is gas, which is similar to the previous system. In this system, the treated gas is compressed through the pipeline and injected at the base of the riser. The mud/gas separation equipment is used to separate the gas from the mud stream when circulated to the surface, realizing the secondary utilization of gas.
3.2.3 Riser Dilution
This is similar to the riser gas lift principle; the difference is that the injected gas is replaced with a drilling base fluid or low-density fluid by adjusting the base fluid injection rate to control the density of the annular fluid. The advantage of this system is that the system does not require special subsea equipment and some older drilling platforms can be implemented with minimal modification.
4 Riserless Drilling
The technology can be divided into the following two categories: a jetting conductor setting and riserless mud recovery (Beck et al., 1991; Jonggeun, 1999; Jeanjean, 2002; Cohen et al., 2008).
4.1 Jetting Conductor Setting
In the 1960s, Mint-on proposed the jet casing technology, which has now become the preferred technology for deep-water and ultra-deep-water drilling worldwide. The combination of tubing and subsea drilling tools is placed in the water, and when the tubing reaches the subsea mud line, the subsea pump set is activated for drilling.
4.2 RMR (Riserless Mud Recovery)
The riserless mud recovery (RMR) system is a new and emerging technology for open-hole drilling, which is applied for the open hole sections (no BOP installed), enabling return of fluid and cuttings in a closed system. As one of the essential pieces of equipment of a deep-water RMR system, the mud recovery line (MRL) is the only channel for subsea mud, which contains cuttings returning from the bottom hole to be transferred from the subsea to the rig for handling. The system is effectively a subsea pump, drawing mud returns from a suction module mounted on the wellhead via a hose line and pumping the fluid and cuttings back up to the rig.
5 Conclusion
1) The subsea pumping system, as one of the most prevalent and well-established methods for achieving dual-gradient drilling, can efficiently reduce the annular pressure of the riser; nevertheless, subsea pumps are expensive, and the reliability of complex subsea pumping systems is uncertain. In comparison, the dual-density system is more cost-effective. It does not necessitate a complex subsea pumping system, and it can provide a suitable pressure gradient with only a small amount of power. However, the primary problem of dual-density systems is the efficiency of the separator and the appropriate injection method. As a result, it is critical to continue developing a new type of high-efficiency downhole separator to realize the precise control of the wellbore pressure gradient.
2) Riserless drilling is an emerging drilling technology that avoids riser-related pipe string difficulties, reduces the complexity of the subsea system, enhances the safety of well control, and lowers the risk of underwater complications. Due to the huge consumption of drilling fluid, which is in short supply in offshore operations, the necessary way to achieve uninterrupted drilling is to solve the problem of high drilling fluid consumption.
3) In general, DKD has matured into a robust deep-water drilling technology. Although China has developed DKD to an industrial level, the main equipment is still dependent on imports, and the basic theoretical research needs to be improved. To make the DKD technology better serve the development of China’s deep-water resources, its basic theory should be further expanded: invest in the development of the related core equipment, and establish a complete basic theoretical system. Achieving a breakthrough in this field will provide a technical guarantee for the exploration and development of deep-water resources in China.
Author Contributions
All the authors conceived and designed the study. QC and QD contributed toward writing the original draft and review.
Funding
This study was supported by the Open Foundation of Cooperative Innovation Center of Unconventional Oil and Gas, Yangtze University (Ministry of Education & Hubei Province), No. UOG 2022-03, and by the Open Fund of Hubei Key Laboratory of Drilling and Production Engineering for Oil and Gas (Yangtze University), No. YQZC202206.
Conflict of Interest
LT was employed by Chuanxi Drilling Company, CNPC Chuanqing Drilling Engineering Co. Ltd.
The remaining authors declare that the research was conducted in the absence of any commercial or financial relationships that could be construed as a potential conflict of interest.
Publisher’s Note
All claims expressed in this article are solely those of the authors and do not necessarily represent those of their affiliated organizations or those of the publisher, the editors, and the reviewers. Any product that may be evaluated in this article, or claim that may be made by its manufacturer, is not guaranteed or endorsed by the publisher.
References
Beck, R. D., Jackson, C. W., and Hamilton, T. K. (1991). “Reliable Deepwater Structural Casing Installation Using Controlled Jetting,” in SPE Annual Technical Conference and Exhibition, Dallas, TX, October 6-9, 1991 (Society of Petroleum Engineers).
Brockway, P. E., Owen, A., Brand-Correa, L. I., and Hardt, L. (2019). Estimation of Global Final-Stage Energy-Return-On-Investment for Fossil Fuels with Comparison to Renewable Energy Sources. Nat. Energy 4 (7), 612–621. doi:10.1038/s41560-019-0425-z
Cohen, J., Stave, R., Schubert, J., and Elieff, B. (2008). Dual-gradient Drilling. Manag. Press. Drill. 2008, 181–226. doi:10.1016/b978-1-933762-24-1.50014-0
Gao, D., Zhu, W., Li, J., Zhang, J., and Meng, Q. (2016). Scientific Problems and Technical Bottlenecks in Deepwater Oil &Gas Engineering ——Academic Review of the 147th Shuangqing Forum. China Basic Sci. 18 (03), 1–6.
Jeanjean, P. (2002). “Innovative Design Method for Deepwater Surface Casings,” in SPE Annual Technical Conference and Exhibition, San Antonio, Texas, September 2002 (Society of Petroleum Engineers).
Jonggeun, C. (1999). Analysis of Riserless Drilling and Well-Control Hydraulics. SPE Drill. Complet. 14 (1), 71–81. doi:10.2118/55056-PA
Li, H., Zhang, M., Lau, H. C., and Fu, S. (2020). China's Deepwater Development: Subsurface Challenges and Opportunities. J. Petroleum Sci. Eng. 195 (4), 107761. doi:10.1016/j.petrol.2020.107761
Pei, Y., Liu, Q., Wang, C., and Wang, G. (2021). Energy-efficient Pressure Regulation Model and Experiment of Lift Pump System in Deepwater Dual-Gradient Drilling. J. Petroleum Sci. Eng. 203 (9), 108621. doi:10.1016/j.petrol.2021.108621
Scanlon, T., and Medeiros, F. (2012). “Enhanced Drilling Solution for Tophole Sections on Jackup Wells with Environmentally - Improved Method and Dual-Gradient Drilling Techniques,” in SPE LatinAmerica and Caribbean Petroleum Engineering Conference, Mexico City, Mexico, April 2012 (Society of Petroleum Engineers).
Wang, J., Li, J., Liu, G., Huang, T., and Yang, H. (2019). Parameters Optimization in Deepwater Dual-Gradient Drilling Based on Downhole Separation. Petroleum Explor. Dev. 46 (4), 819–825. doi:10.1016/s1876-3804(19)60240-5
Xu, L., Jiang, S., Yin, Z., and Chen, G. (2005). Research on Principle of Dual-Gradient Drilling Technology. China Offshore Oil Gas 2005(04), 260–264.
Keywords: deep-water wells, managed pressure drilling, dual-gradient drilling, riser drilling, subsea mudlift drilling
Citation: Chen Q, Deng Q, Tan L, Qi G and Zhang J (2022) Status and Prospects of Dual-Gradient Drilling Technologies in Deep-Water Wells. Front. Energy Res. 10:920178. doi: 10.3389/fenrg.2022.920178
Received: 14 April 2022; Accepted: 26 April 2022;
Published: 01 June 2022.
Edited by:
Qi Zhang, China University of Geosciences, Wuhan, ChinaReviewed by:
Wenlong Li, China National Offshore Oil Corporation, ChinaSong Yu, China University of Petroleum, Beijing, China
Copyright © 2022 Chen, Deng, Tan, Qi and Zhang. This is an open-access article distributed under the terms of the Creative Commons Attribution License (CC BY). The use, distribution or reproduction in other forums is permitted, provided the original author(s) and the copyright owner(s) are credited and that the original publication in this journal is cited, in accordance with accepted academic practice. No use, distribution or reproduction is permitted which does not comply with these terms.
*Correspondence: Qiao Deng, ZGVuZ3FpYW8yMDA4QDE2My5jb20=