- Technische Chemie, Institute of Chemistry, Technische Universität Berlin, Berlin, Germany
Hydrogen (H2) produced using renewable energy could be used to reduce greenhouse gas (GHG) emissions in industrial sectors such as steel, chemicals, transportation, and energy storage. Knowing the delivered cost of renewable H2 is essential to decision-makers looking to utilize it. The cheapest location to source it from, as well as the transport method and medium, are also crucial information. This study presents a Monte Carlo simulation to determine the delivered cost for renewable H2 for any usage location globally, as well as the most cost-effective production location and transport route from nearly 6,000 global locations. Several industrially dense locations are selected for case studies, the primary two being Cologne, Germany and Houston, United States. The minimum delivered H2 cost to Cologne is 9.4 €/kg for small scale (no pipelines considered), shipped from northern Egypt as a liquid organic hydrogen carrier (LOHC), and 7.6 €/kg piped directly as H2 gas from southern France for large scale (pipelines considered). For small-scale H2 in Houston, the minimum delivered cost is 8.6 €/kg trucked as H2 gas from the western Gulf of Mexico, and 7.6 €/kg for large-scale demand piped as H2 gas from southern California. The south-west United States and Mexico, northern Chile, the Middle East and north Africa, south-west Africa, and north-west Australia are identified as the regions with the lowest renewable H2 cost potential, with production costs ranging from 6.7—7.8 €/kg in these regions. Each is able to supply differing industrially dominant areas. Furthermore, the effect of parameters such as year of construction, electrolyser, and H2 demand is analysed. For the case studies in Houston and Cologne, the delivered H2 cost is expected to reduce to about 7.8 €/kg by 2050 in Cologne (no pipelines considered, PEM electrolyser) and 6.8 €/kg in Houston.
Introduction
In order to combat climate change, many industrial sectors need to find ways to reduce greenhouse gas (GHG) emissions. (Rogelj, 2018) Growing industries such as steel and chemicals production, which make up 7% (International Energy Agency, 2020) and 2% (Leimkühler, 2010) of global GHG emissions, respectively, are under political pressure to find low-carbon alternatives to the fossil fuels currently used in such sectors. Hydrogen gas (H2) has the potential to be used to reduce GHG emissions in some industries, including steel production and energy storage. (Jarraud and Steiner, 2014) It does not produce carbon dioxide (CO2) or other carbon-based gases when burned, and when produced through electrolysis using renewable energy, has a relatively low GHG emissions footprint. (International Energy Agency, 2019) Currently, most H2 is produced using fossil fuels, but there is a swift change underway to renewably produced H2, and it is expected that both the total amount of H2 produced and the share of renewable H2 will grow dramatically in the next few decades. (International Energy Agency, 2019) It is crucial for industries planning to utilize renewable H2 to know how much it will cost and the most cost-effective location to obtain it from.
To evaluate the most cost-effective location for H2 production, both production and transport costs must be considered. A major component of production costs is electricity production, of which wind and solar are the two most flexible and developed renewable energy candidates. Places with strong wind or solar potential are therefore more likely to be candidates for producing low-cost renewable H2. Transport costs of H2 have been less investigated, resulting in a potentially significant neglection of a major cost component of H2 cost. Estimations of the transport cost help to determine where the cheapest production location of H2 might be for a particular desired use location. Possible transport methods include ship, truck, or pipeline. H2 can also be converted into a variety of mediums for easier or cheaper transportation and storage, including ammonia (NH3), liquid H2 (LH2), or organic compounds such as toluene known as liquid organic hydrogen carriers (LOHCs). (Preuster et al., 2016) While it is costly and energy-inefficient to convert and re-convert gaseous H2 to these mediums and back again, they are generally cheaper, easier and safer to transport and store than gaseous H2. Knowing which of these transport mediums and methods is the most cost-effective for the unique combination of H2 demand, location, year of consumption, and other factors that each H2 consumer requires would be necessary information to these consumers when developing the business case for their process.
Also needed for future development and planning is to investigate which electrolyser types and transport mediums have the highest potential for cost reduction due to efficiencies of conversion and further technological development. A stakeholder planning to purchase H2 for a steel mill built in 2030 is not interested in using costs based on the year 2020, but rather an estimation for costs at the time they want to build the mill. As well as smaller individual H2 consumers, it would likely be the case that groups of large consumers, for example in industrial parks, together require an extensive amount of renewable H2. In these cases, large H2 pipelines could potentially be built from regions with the potential to produce vast amounts of renewable H2, similarly to the natural gas pipelines that exist today, for example between Russia and the EU. Economies of scale could work in favour of these scenarios and potentially reduce the H2 cost for consumers by reducing the transport cost. Knowing if such pipelines are economically viable would help industrial and government stakeholders in planning for future H2 transport networks. Government stakeholders want to ensure a reliable and cheap source of low carbon energy, and must therefore also take geopolitical factors into account as the energy landscape shifts away from a dependence on fossil fuels to renewables.
Some studies have performed localized techno-economic assessments on H2 electrolysis, (Glenk and Reichelstein, 2019; Christensen, 2020) and also national level H2 network optimization analyses, (Han et al., 2012; Baufumé, 2013; Hwangbo et al., 2017; Aditiya and Aziz, 2021) however no studies were found that aim to find the minimum delivered cost (and associated location) to produce and transport renewable H2 to a given location on a global scale. While localized studies are useful in some cases, in reality, it may be more cost-effective to produce H2 in another country or continent with more abundant renewable resources. Determining the most cost-effective location to purchase H2 from, and the cost of the H2, is currently a major knowledge gap and is essential information for stakeholders planning current or future processes that require renewable H2, especially if a model could be tailored to their individual process needs. There is also a large discrepancy between the H2 production costs estimated by various studies (values ranging from 1.5—14 €/kg) perhaps due to the variety of different assumptions and locations that are used in the studies, which can be confusing and intimidating to stakeholders interested in planning a process using H2 for a specific location. Knowledge of the delivered H2 cost for a particular location, demand, electrolyser type and year would help to clarify these discrepancies for stakeholders planning such a process.
Background
H2 Production Methods
H2 is conventionally produced by a variety of fossil-fuel-based methods such as steam reforming (Kaiwen et al., 2018) or auto-thermal reforming from natural gas, (Khojasteh Salkuyeh et al., 2017) with about 80% of the 120 Mt of H2 produced worldwide annually coming from natural gas and 98% from fossil fuels in general. (Muradov, 2017) Steam methane reforming (SMR) is the most common production method, which reacts methane from natural gas with steam to form H2, CO and CO2 before being further reacted in a “water-gas shift” reaction to produce CO2 and H2. However, there is a relatively high GHG emissions impact associated with the SMR process (4.8 (Dufour et al., 2011)—11.9 (Spath et al., 2001) kg-CO2-eq./kg H2 for cradle-to-gate system boundaries). H2 can also be produced from coal gasification, which has an even higher GHG emissions impact of about 19 kg-CO2-eq./kg H2. (International Energy Agency, 2019) As an economic fossil-fuel benchmark, SMR has a production cost of around 2.2 €/kg H2. (Gielen et al., 2019)
Due to the need to reduce emissions of H2 production, low-carbon production methods are being increasingly investigated. The most commonly studied low-emissions H2 production method is water electrolysis, which splits H2O into H2 and O2. (International Energy Agency, 2019) While H2 electrolysis requires substantial amounts of electricity (39 kWh/kg H2 if 100% efficient (Levene et al., 2007)), with quickly decreasing costs for renewable electricity from solar and wind sources, it is a promising option for renewable H2 production, with solar-powered H2 electrolysis having a GHG emissions impact of about 2.0 kg-CO2-eq./kg H2. (Bhandari et al., 2014) Electrolysis also produces the purest H2 of the major production methods, up to 99.999% for standard production facilities. (Element Energy Ltd, 2018)
There are three major H2 electrolysis technologies: alkaline (AE) electrolysis, proton exchange membrane (PEM) electrolysis, and solid oxide electrolysis (SOE). AE electrolysis is the most mature and developed production method, for which non-noble metals such as nickel are used for the electrodes, and the electrolyte is a concentrated lye. (Brauns and Turek, 2020) A diaphragm keeps the two electrodes and their product gases separate while allowing passage for water and hydroxide ions. It is relatively cheap because it does not require as many high-value materials, while also maintaining a relatively long lifetime of around 75,000 h (International Energy Agency, 2019) It is considered a low-temperature type of electrolysis, as it operates between 40 and 90°C. (Rashid et al., 2015) The weaknesses of AE electrolysis include a low partial load range (10—110%) and operating pressure (1–30 bar). It currently makes up the largest share of electrolysers in commercial use. (International Energy Agency, 2019)
PEM electrolysis was first developed by General Electric in the 1960s to overcome the weaknesses of AE electrolysis (Shiva Kumar and Himabindu, 2019) and uses more expensive noble metals such as platinum or iridium as electrode catalysts while utilizing a solid acidic polymer membrane to transmit protons from the anode to the cathode. (Rashid et al., 2015) They also operate at relatively low temperatures between 20 and 100°C. Advantages of PEM electrolysis include a compact design, high efficiency, small footprint (0.048 m2/kW compared to 0.095 m2/kW for AE electrolysers), easy scalability, high H2 purity, and perhaps most importantly, the H2 can already be produced at high pressures of 30—60 bar, reducing the need for energy-intensive compression after production. (International Energy Agency, 2019) Weaknesses include a high investment cost, especially as special construction materials are required due to the corrosive environment. (Carmo and Fritz, 2013) Recently, PEM electrolysis has been growing at a rapid rate since around 2015, making up the largest share of new electrolyser projects. (International Energy Agency, 2019)
The third main kind of electrolysis technology is solid oxide electrolyser (SOE) cells. These are run at very high temperatures of 700–1,000°C and are the least developed and used of the three major technology options, (Rashid et al., 2015) despite being theoretically able to reach stack efficiencies of almost 100%. (Brauns and Turek, 2020) Steam is used, requiring a high energy input, although the investment costs are relatively low as the electrodes are made of ceramic. (International Energy Agency, 2019) A ZrO2 solid is commonly used as the electrolyte. (Laguna-Bercero, 2012) A negative aspect is that they have a relatively low lifetime (∼20,000 h) due to high material degradation, hindering their industrial adoption. Increasing the durability and lifetime of SOE cells is currently undergoing research and development to improve their viability. (Wang et al., 2020)
Other methods of producing low-carbon H2 include combining carbon capture and storage (CCS) with H2 produced from natural gas or coal, (Office of Energy Efficiency and Renewable Energy, 2020) from biomass using fermentation, or solar thermochemical production routes. (Christopher and Dimitrios, 2012) Coupling fossil-fuel-based H2 methods with CCS uses up valuable CO2 storage space, which could be used for other sectors that do not have a GHG emissions-free alternative technology. Other renewable-based methods of H2 production such as photobiological H2 production or biomass combustion are not yet developed enough to fill a significant market share or struggle with high costs in comparison to electrolysis and fossil-fuel-based H2.
Uses of Renewable H2
H2 is a versatile energy carrier that can be used in a wide variety of applications and industries. Currently, about 120 Mt of H2 is produced each year, used primarily for ammonia (NH3) production, oil refining, and methanol production. (Gielen et al., 2019) As well as replacing the H2 produced from fossil fuels that are used in these sectors, there is a range of other applications where renewable H2 could replace fossil fuels. One major example is the steel sector, which is responsible for about 7% of global GHG emissions. (Collis et al., 2021) The most common route of steel production, the integrated steel mill, uses CO from coal gasification to reduce iron ore to pig iron. (Ho et al., 2013) Renewable H2 could replace the coal used in this process, which would significantly reduce the GHG emissions of steel production, the majority of which are caused by coal combustion. (Germeshuizen and Blom, 2013) Demonstration steel mills using H2 as a reduction agent are currently being built in several locations across Europe. (Bhaskar et al., 2020)
H2 is also heavily used in the chemicals industry, where it is used to make base chemicals including NH3 and methanol, but also more complex chemicals such as polymers and fuels. (Zang et al., 2021) Synthetically produced fuels or e-fuels are expected to grow in scale significantly as they are seen as promising options to decarbonise the shipping (Lindstad et al., 2021) and aviation (Scheelhaase et al., 2019) sectors, two industries that are difficult to decarbonise using batteries or CO2 capture. (Ueckerdt et al., 2021) In some use cases, H2 could also be directly combusted as a fuel source. (Cai et al., 2020)
H2 could also be used for small to large scale energy storage. As renewably produced electricity takes up an increasingly larger share of electricity production, the intermittency of solar and wind power poses problems for the grid. Electricity supply could be much greater than demand during some hours, and much less at other times. This excess renewable electricity could be converted into H2 during the times the demand outpaces supply and re-converted when demand is greater than supply. (Steilen and Jörissen, 2015) It could also be used in buildings as small scale energy storage in the form of fuel cells, (Andaloro et al., 2019) or blended with natural gas to reduce the GHG emissions intensity of stove burners. (Zhao et al., 2019) Overall, it is expected that H2 could provide 24% of total energy demand by 2050 within the EU, mainly across the transportation, building and industry sectors. (Kakoulaki et al., 2021) A summary of the usages discussed here is shown in Figure 1.
Current Literature on H2 Networks and Economic Assessment
A large number of studies have been performed assessing the economics of electrolytic H2 production, with the most in-depth recent studies being Glenk et al. (Glenk and Reichelstein, 2019) and Christensen. (Christensen, 2020) Most assessments usually focus on a singular H2 production location for the base scenario. While Christensen’s analysis is in-depth and detailed, the analysis is only based on data for the country level for Europe and the state level for the United States and does not account for the rest of the world. (Christensen, 2020) IEA (International Energy Agency, 2019) is the only study found to perform a global analysis on the H2 production cost, which is based on a hybrid solar-wind system, but the assumptions used in the analysis are unclear. No date of analysis is shown, and the nature of the hybrid system and its capacity factor are not explained. Several important system costs are also not accounted for, resulting in very low H2 production costs of 1.6—4 €/kg, as is the case for many reports by international agencies and businesses. (International Energy Agency, 2019; Hydrogen Council, 2020; International Renewable Energy Agency, 2020) For comparison, Christensen (Christensen, 2020) and Glenk et al. (Glenk and Reichelstein, 2019), who include a range of further costs required to build a functioning H2 electrolysis system, such as compression and installation costs, find H2 production costs in Europe to be between 6.5–14 €/kg in 2020 and 5.1—9.1 €/kg in 2050.
While calculating the H2 production cost is naturally essential information, it is likely that for many locations worldwide importing renewable H2 that is produced somewhere else could be cheaper due to better solar or wind conditions. Most studies do not consider transport costs, or if they do, only consider one or two predefined scenarios. IEA has a considerably detailed breakdown of the transport costs for H2 and other mediums by several different transport modes, as well as analysing the production and transport costs together for a few specific scenarios, such as producing H2 in Australia and shipping it to Japan. (International Energy Agency, 2019) Likewise, the Hydrogen Council has analysed the total costs for several supply chain scenarios, such as the Middle East to the EU and Chile to the US, including transport and conversion costs. (Hydrogen Council, 2021) However, it is not clear if the H2 production locations chosen for these scenarios are the most economically viable for the given H2 usage location, nor that the medium and mode of transportation selected are the most cost-efficient, as no different production locations are analysed and compared for each H2 usage location. While the IEA also has an analysis on the production cost of renewable H2 across the globe, no transport costs are included, making it impossible to determine the actual cheapest cost for obtaining renewable H2 for a particular location. (International Energy Agency, 2019)
Many H2 production, distribution and usage networks have been created, utilizing geo-analysis to create the most efficient network for a particular country or region. (De-León Almaraz et al., 2012; Han et al., 2012; Baufumé, 2013; Hörsch and Brown, 2017) Baufumé (2013) conduct a detailed simulation for a Germany-wide H2 pipeline infrastructure in 2050; however, the study assumes H2 fuel cell vehicles will be heavily used and focuses on H2 supply to fuelling stations, which is far from certain given their relatively high costs, low durability and potential storage issues. (Wilberforce et al., 2017) Han et al. (2012) and De-León Almaraz et al. (2012) simulate a detailed nationwide network for South Korea and Great Britain, respectively, complete with production, storage and usage locations. Woo and Kim (2019) investigate the effectiveness of several different algorithms (standard genetic algorithm, hybrid genetic algorithm, genetic algorithm-based matheuristic) on a H2 supply chain network problem, with a case study on Jeju island. In reality, as is the case with the current energy market, H2 will likely often not be produced in the same country as it is used in. For example, Lahnaoui et al. (2021) optimize an in-depth network for Germany and France and find that Germany will likely have a greater H2 demand than supply, while in France production may be able to match consumption. However, due to geographical variations of solar irradiation and wind power density, in some regions renewable electricity is much cheaper than in others. For example, it may be cheaper for France to obtain renewable H2 from north Africa or the Middle East than producing it locally. Aditiya and Aziz (2021) uses technical, economic and social indicators to assess the potential for an inter-country H2 network in the Asia-Pacific region, including likely H2 production locations and potential H2 flows. However, the paper does not provide a network capable of estimating production, transport or delivery costs for areas of high H2 demand.
Instead of local models, an economic model with a global scope that could determine the cheapest point of H2 supply for any desired end location would be useful for large future H2 consumers. The closest such model found in the literature is that created by Hwangbo et al. (2017), who present a stochastic mixed integer linear model that optimizes for lowest cost while taking into account H2 production, storage, and transport. While the model is thorough and complex, it only considers H2 produced by SMR, which has a very high GHG emissions footprint (4.8 (Dufour et al., 2011)—11.9 (Spath et al., 2001) kg-CO2-eq./kg H2). A similar cost-optimized global model focusing on renewably produced H2 would be more applicable for the next few decades, as most H2 will have to be produced from low-emissions methods in order to meet the goals of the Paris agreement. (IEA. Global, 2017) Additionally, the case study presented by Hwangbo et al. (2017) focuses on production, storage and transportation in South Korea. While this would be interesting for public bodies or companies for infrastructure planning, large H2 consumers also need information on the most cost-effective global H2 production site, as well as transport method and route for their individual situation of H2 demand, location, and build year.
Goal and Scope
The goal of the study is to create a model to evaluate the most cost-effective location to produce H2 using a solar or wind-powered electrolyser for a variety of usage locations, as well as the identification of the most cost-efficient H2 production sites and transport routes to meet global renewable H2 demand. For example, if renewable H2 is to be used in Cologne, Germany, the goal is to find the location globally with the lowest cost to produce and transport the desired amount of H2 to Cologne, using solar or wind to power an electrolyser. As currently electrolytic H2 makes up only 0.5% of global H2 supply, (International Energy Agency, 2019) and production is expected to grow substantially in the medium term, it is expected that many new electrolyser sites will be built in the next few decades. Determining the most cost-effective location for these sites is beneficial for H2 producers and consumers.
While the most cost-effective H2 production location for individual processes is important information for that process, if there are multiple processes located close to each other requiring a large amount of H2, for example in industrial parks, it could be feasible for larger pipelines to be built to take advantage of economies of scale. Several industrial parks within Europe are investigated and proposals for such pipelines are presented, along with the associated cost reductions. Large-scale pipelines are especially important for scenarios in later years (2035—2050), as by this time it is expected the volumes of renewable H2 being consumed will be much greater than at present, and more processes will be adapted to use H2 instead of fossil fuels (such as steel production).
The study has a geographically global scope, although it uses masks to remove areas of unfeasible terrain for H2 production facilities, such as mountains, farmland, cities, and protected areas. From a process perspective, the scope includes the whole value chain until the time the H2 reaches the purchaser, which can be broken down into production of H2 and transport of H2, as shown in Figure 2. Blending H2 into natural gas pipelines is not considered in this study, as for many chemical processes relatively pure H2 is required.
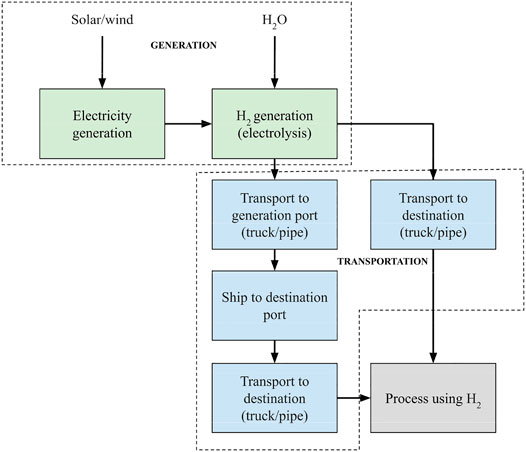
FIGURE 2. Scope of the study showing the two main parts, H2 production and transportation. Everything within the dotted lines is the scope of the study. Transport is either directly to the destination (if possible) by truck or pipeline, or else it is shipped from the nearest port to the closest port to the destination. If both transportation routes are possible, the more cost-effective is chosen.
A grid-connected electrolyser is not within the scope of this study due to the difficulty of dealing with differing electricity prices, taxes, levies, curtailment data and emissions footprints for each country individually. Additionally, offshore wind is not considered in this study due to the high degree of complexity it would add to the spatial analysis—it is very unlikely that H2 will also be produced offshore, which opens an excessive range of scenarios for where the H2 would actually be produced. Additionally, data on promising offshore wind locations are scarce due to the logistical complexity of building offshore wind systems with regards to ocean depth, currents and tides, and ocean sovereignty. In most cases, it is more expensive than onshore wind (International Renewable Energy Agency, 2016) and it is likely there would be few scenarios in this study where it would provide cheaper electricity than onshore wind power. (Green and Vasilakos, 2011)
Hybrid wind-solar systems are also not considered in the scope of this study, due to the large degree of added complexity regarding operating times, size of each power source, and resulting capacity factor. While hydropower could be used in some locations, many countries do not have access to hydropower resources and as hydropower is considered to have a greater environmental impact, it is not accounted for in this study. (Botelho et al., 2017)
Scenario Definition
It is possible to investigate a large variety of scenarios where current knowledge gaps exist, such as different geographic regions, electrolyser types, years, and H2 demand. The base scenario is defined as an alkaline electrolyser producing 100 kt/y H2 in the year 2030 with the desired end location in Cologne, Germany. Other scenarios and parameters that are analysed are done so by altering variables from this base scenario. The full range of scenarios investigated in this study is listed below. Any of the below variables can be altered to best simulate the conditions applicable to individual stakeholders for planning purposes, creating thousands of possible scenarios, as shown in the Supplementary Figure S3.
End (H2 usage) location (exact GPS oordinates):
• Cologne, Germany (50.9763, 6.9818)
• Abu Dhabi, UAE (24.2780, 54.4835)
• Tokyo-Yokohama, Japan (35.6205, 139.8965)
• Guangzhou, China (23.0550, 113.4242)
• Houston, USA (29.6084, -95.0527)
H2 produced (electrolyser size assuming electrolyser efficiency of 0.7):
• 2 kt/y (20 MW—largest electrolyser available today)
• 10 kt/y (100 MW—largest electrolysers in construction)
• 100 kt/y (1000 MW—mass H2 production in future facilities)
• 1000 kt/y (10 GW—largest conceptual H2 production facilities for 2030)
Year
• 2020
• 2030
• 2040
• 2050
Electrolyser type:
• Alkaline (AE)
• Polymer electrolyte membrane (PEM)
• Solid oxide electrolyser (SOE)
Medium conversion and reconversion
• Centralised
• Decentralised
The locations were selected based on being areas of high industrial importance, in particular containing industries that are likely to require renewable H2 in the future, such as chemicals and steel production. Additionally, the locations all have substantial civilian populations, which would require significant H2 if building heating and cooking utilizes H2 in the future. Cologne was chosen as the base scenario due to the large amounts of steel and chemical industry in the area, which includes not only the Ruhrgebiet area of Germany but also Belgium and the Netherlands. The exact locations were selected to be locations of already existing steel and chemical manufacturing areas.
The electrolyser sizes were chosen in order to have a large range of capacities, from the largest electrolysers available today to large-scale H2 production that would be required in future facilities. However, it is conceivable that even larger H2 production facilities will be required in the future. A singular steel mill producing 2 Mt of steel annually would require about 144 kt of H2 to fully decarbonize using H2. (Hoffmann et al., 2020) As steel production is only predicted to grow over the next decades, reaching 2200 Mt annual production by 2050, (Bellevrat and Menanteau, 2009) immense quantities of H2 will be needed to decarbonise the steel industry, not to mention the myriad of other industries requiring renewable H2, such as chemicals. However, as the largest currently conceptualised electrolysers have capacities of around 10 GW, renewable H2 production plants larger than this are currently unimaginable, and therefore are not considered in this study.
The year 2030 is chosen as the base scenario as it is near enough in the future to have more certain predictions on cost data but far enough that renewable H2 production will likely be considerably higher than it is today. 2030 is also seen as a short-term goal for GHG emissions reduction and many governments and industries are investigating what can be accomplished by this year, resulting in a range of predictions on renewable H2 production and cost in 2030. The years 2040 and 2050 are also examined, with 2050 being a mid-term goal for many countries to reach net-zero GHG emissions. (Net Zero Tracker, 2021) Although renewable H2 production will likely be higher still in 2040 or 2050, there is higher data uncertainty associated with looking further into the future. The present time of the data used in this study (2020) is also considered due to the relative certainty of data on costs; it could also be useful to stakeholders considering planning or constructing H2 electrolysers in the short term.
All three major kinds of electrolysers are investigated in this study: AE, PEM and SOEs. As AE electrolysers are the most mature and commonly used technology, (International Energy Agency, 2019) they are taken as the base scenario. However, all three kinds of electrolysers are being further developed and studied and it is possible in the future that another kind could control the dominant market share, or even a more even spread between the three kinds. Therefore, it is still important to consider each of them in this study.
When gaseous H2 is converted to a medium such as NH3, LH2 or LOHCs for cheaper and easier transportation, it must be re-converted to gaseous H2 either at a distribution centre such as a port or the final usage location. When this is done at a large-scale distribution centre, known as centralised reconversion, economies of scale play a role in reducing reconversion costs. However, when reconversion is performed at each end-user (decentralised reconversion), it can be more expensive, especially for very small end-users such as a H2 fueling station. Centralised reconversion is assumed to be the case for the baseline scenario as the H2 consumption is relatively large.
Data Collection and Processing
Data Collection
Firstly, possible H2 production sites had to be determined, as it is not feasible for manufacturing facilities to be built in mountainous areas, cities, farmland or protected areas. Geographic masks were used to determine spaces appropriate for production. The “practical PV potential” data set provided by Global Solar Atlas was used to mask unsuitable areas, of which the “Level 1” masks were chosen. (ESMAP. Global, 2020) These masks exclude ‘areas due to physical/technical constraints, such as rugged terrain, presence of urbanized/industrial areas, forests, and areas that are too distant from the centres of human activity’, as well as “areas that might be unsuitable due to regulations imposed by national or regional authorities (such as conservation of cropland or nature conservation)”. From the remaining area, one location at every full digit of latitude and longitude (e.g., 47, -52) was taken to create a set of 5970 possible distinct locations which represent the available global area where a H2 production facility could be constructed. The Python library Rasterio was used to apply the geographic masks and retrieve the annual solar energy potential (kWp) of each possible location. (Mapbox. Rasterio, 2016) Wind power density (W/m2) was obtained for each identified production location from Global Wind Atlas. (Technical University of Denmark, 2021) A map of European industrial emitters provided by the project Carbon4PUR was used to determine important locations in Europe that might require renewable H2 in the future. (Carbon4PUR, 2020)
Creation of Shipping Network
In order to calculate the most cost-effective method of transportation from production sites to the desired end location, the shipping distance between the production and end locations had to be determined. A shapefile of world shipping routes based on Automatic Identification System (AIS) data was obtained from NCEAS. (Halpern et al., 2015) A network was created from this shapefile using the Python module created by Benita et al. (2019) although several changes were required to the module code for it to produce a working network of shipping routes, such as not simplifying the resulting network by removing intermediate nodes, and the connections between nodes that crossed over the International Date Line had to be manually added. A list of global ports and their associated port codes and global positioning system (GPS) locations was obtained from Novikov (2019) which was used to find the closest port to every possible production location as well as the desired end location. These ports represented the possible start and end nodes of the shipping network. It should be noted that the nodes are positioned 20 km offshore from the ports to ensure shipping paths don’t overlap the coastline. Therefore, 40 km is added to the distance of every shipping route. The finished network was then used to determine the shortest path between the two desired ports and is shown in Figure 3.
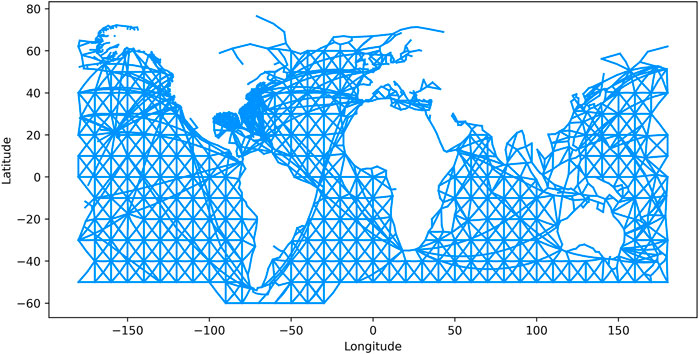
FIGURE 3. Global network of shipping routes created from AIS data, used to evaluate the shortest shipping distance between ports.
Model Description
A model in Python was constructed that takes as input the H2 demand in kt/y, the year that the facility will be constructed, GPS coordinates of the desired end location, the type of electrolyser, if pipelines are permitted (and if so, the maximum pipeline length), and if the distribution centres are centralised or decentralised. As well, many of the economic parameters can be adjusted if desired, such as the interest rate and the full load hours of the electrolyser per year. The model calculates the cost to produce H2 at each of the possible H2 production locations derived in Data Collection and Assumptions, followed by the transport cost from each of these locations to the desired end location. The location with the minimum sum of production and transportation cost is therefore the most cost-effective location to produce H2 for the desired end location.
A Monte-Carlo simulation was conducted on the Python model to effectively cover the reasonable range of cost uncertainties. Particularly in future scenarios, uncertainties for electrolyser investment and operating costs are relatively large, with high range estimates being up to 600% of low range estimates. (Glenk and Reichelstein, 2019) Using a Monte-Carlo simulation, the uncertainties of these variables are accounted for using probability distributions. The probability density functions of each variable were determined using the methodology presented by Hawer et al. (Hawer et al., 2018)
Production Cost
Firstly, the capacity of the electrolyser required (S) was calculated from the H2 demand in tons per hour (F) and the electrolyser efficiency (ηE):
The coefficient 39 represents the amount of electricity a theoretical 100% efficient electrolyser takes to produce H2 (39 kWh/kg H2). (Christensen, 2020) The total amount of electricity required (ER) is then equal to the electrolyser capacity (S) plus the electricity required for H2 compression (C):
For each location, the levelized cost of electricity (LCOE) for the required electricity amount was determined for both solar and wind power, and the cheaper of the two power sources was used as the electricity source for the electrolyser. The LCOE was calculated by dividing the total life cycle cost by the total lifetime power produced (Branker et al., 2011):
Where It is the initial investment required (CapEx), Mt is maintenance and operational expenditures (OpEx), Et is the total electricity generated, r is the discount rate of the project, and t is the lifetime of the system. The individual wind turbine power (PW) was calculated using the following formula:
Where WPD is the wind power density [W/m2], ηW is the wind turbine efficiency, and LB is the length of the turbine blades. The solar array size required (SA) [kWp] was calculated by dividing the yearly electricity demand (Et) [kWh] by the solar energy potential (SP) [kWh/kWp] for each production location:
From here, the CapEx of the wind and solar power required can be directly calculated by multiplying with the appropriate CapEx factors (Table 1) and then used in the LCOE formula above.
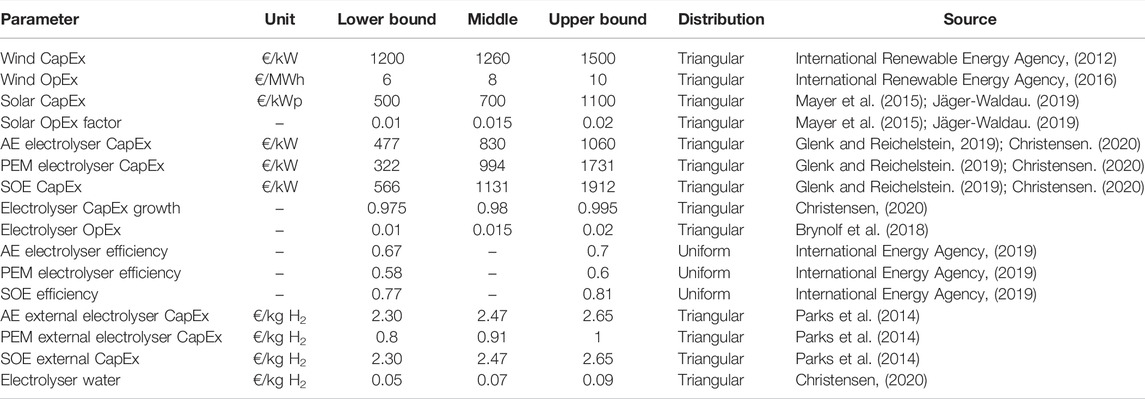
TABLE 1. Parameters and distributions used in Monte-Carlo simulation of the production cost of H2 from electrolysis in 2020.
Once the LCOE has been determined, the H2 production cost was evaluated by summing the electrolyser OpEx (mostly consisting of the renewable electricity production cost) and annualised electrolyser CapEx. (Chiuta et al., 2016) The change of parameters over time was calculated using the expected change per year to the power of the number of years after the base year (2020):
Where Var is a variable that is expected to undergo yearly changes, x is the year of the study, and ΔYr is the yearly change of the variable. The parameters used in the Monte-Carlo simulation are shown along with the lower and upper bounds and associated distribution in Table 1. A full list of economic assumptions relating to the production cost of H2 is shown in Table 2.
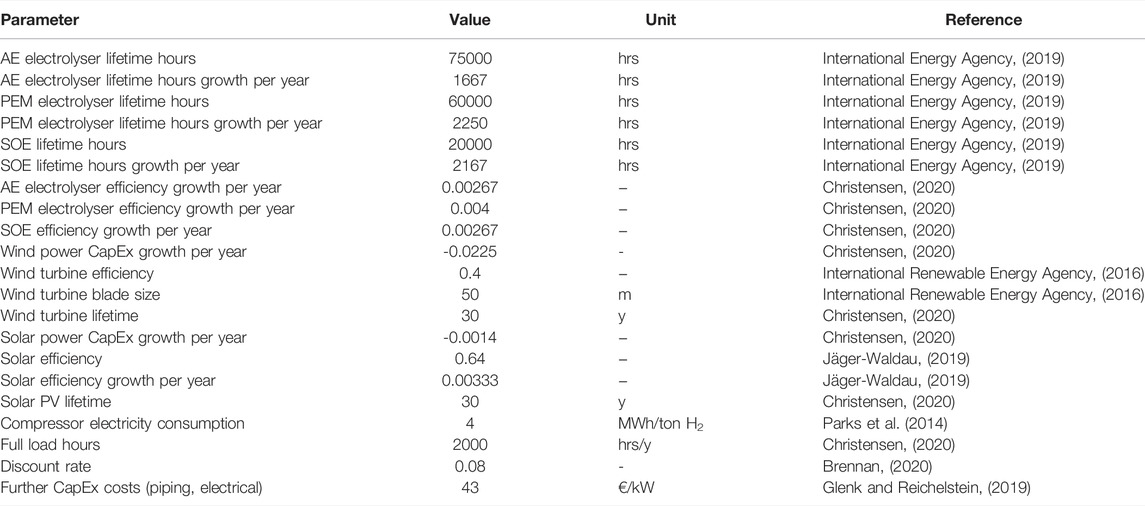
TABLE 2. Static economic parameters assumed for the production cost of H2 in 2020. “Growth per year” refers to the assumed increase of the parameter, per year from 2020, if the electrolyser was to be built in a future year.
Transport Cost
Four different transport mediums are considered: gaseous H2, LH2, ammonia (NH3), and a sample LOHC (toluene). Cost functions for shipping, trucking and piping these mediums as a function of distance were derived from IEA, (International Energy Agency, 2019) which includes the costs of any intermittent storage that is required. Not each of the three transport methods can be used for all four transport mediums; while NH3 can be shipped, trucked or piped, LOHCs and LH2 can only be trucked or shipped, and gaseous H2 can only be trucked or piped. Driving distances between locations were calculated using the OSRM API. (OSRM, 2020) Pipeline distances were determined as straight-line distances over the Earth’s surface, using the Python library GeoPy, (GeoPy Contributors, 2018) with 20% of the straight line distance added on to account for necessary deviations over unsuitable land such as private land or areas of rough terrain. Shipping distances were evaluated using the created shipping network (see Creation of Shipping Network); firstly, the nearest port to each production site as well as the desired end location was determined from a list of global ports; then, a “closest node” search of the shipping network revealed the nearest node to the port. Dijkstra’s algorithm was implemented over the shipping network using the Python package NetworkX (NetworkX Developers, 2014) to find the shortest path between the start port of each production site and the end port, as well as the length of the path.
The most cost-effective transport method between the possible H2 production locations and the desired end location had to be determined. The possible transportation options are shown in Figure 4 for example production and usage locations, namely a solar power plant in Spain to a steel mill in Germany. Firstly, the driving distance between the production and end location was calculated. If the route existed and was less than 1,000 km, a direct truck between the production and end location was considered an option, and the cost for trucking the required distance was calculated. Secondly, the pipeline distance was also calculated as the direct distance between the production location and the usage location, with an additional 20% added to account for the fact that most pipelines cannot be built in a straight line, and the associated pipeline cost determined. Next, the cost for shipping was evaluated, which in reality is a three-step transportation process; the produced H2 must be either piped or trucked from the production location to the nearest port, then shipped to the port closest to the end location, and finally trucked or piped from the end port to the end location.

FIGURE 4. Example showing the possible transport options from the production locations to the desired usage location. H2 can be trucked or piped directly to the usage location, or it can be trucked or piped to the nearest port and shipped to the port closest to the usage location, from where it is trucked or piped to the usage location. The gaseous H2 produced can be converted into other mediums at the production location or start port and re-converted at the end port or usage location.
To determine which transportation option and medium was the cheapest, each complete ‘production site to end location route’ was calculated for each medium possibility, with two possible conversion and re-conversion points. The gaseous H2 produced can be converted to other mediums either at the production site or the start port, and re-conversion could occur at the end port or the desired end location. The assumed conversion, re-conversion and export costs are shown in Table 3. It should also be noted that there are also technological and environmental differences between the different transport mediums. As the model only accounts for the economic cost of the transportation medium, these are discussed in Transport Cost Analysis.
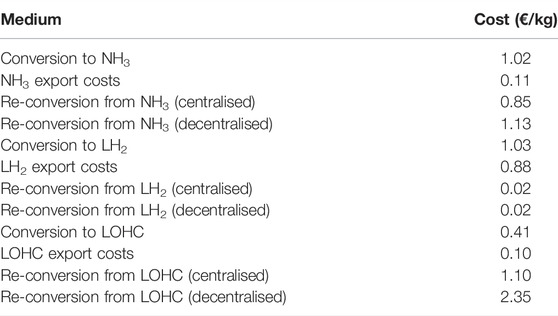
TABLE 3. Costs of conversion and re-conversion from and to gaseous H2, as well as export costs for each medium (International Energy Agency, 2019).
Model Assumptions
It is assumed that the electrolyser is directly connected to the renewable energy source and is not connected to the grid. Consequently, the operating time of the electrolyser is the same as the capacity factor of the renewable electricity source. Additionally, no assumptions are made as to the political stability and safety of areas; as the study considers years until 2050, it is difficult to predict the stability of regions into the future. It is assumed that terrain suitable for building solar and wind plants is also appropriate for construction of electrolysers and their associated operations, as the terrain is usually flat and with enough space for a comparatively small electrolysis plant.
Regarding the shipping network, it is assumed that the nearest port to the production site can be used for shipping H2. While this is likely the case for most ports, there may be some cases where the port lacks the infrastructure required to ship industrial chemicals. In other situations, the nearest port may lie in a different country, which could add extra tariffs to trade (or in the most extreme cases, deny access to the port). However, as this data is both highly uncertain and impractical to obtain for every possible production site, the authors assume that each production site can freely ship from the port closest to it. Due to the high costs associated with the conversion of H2, it is assumed that converting and re-converting more than once is not economically viable and is therefore not considered.
Results
Global Production and Transport Cost Results
This section discusses the cost of producing H2 for the baseline scenario, including transport to each of the five locations specified in Scenario Definition. Firstly, the H2 production cost at each of the possible production sites selected (described in Data Collection and Assumptions) was calculated and is shown in Figure 5. The production cost ranges from 6.7—11.4 €/kg H2 (average standard deviation 0.37 €/kg H2), with the lowest cost areas being northern Africa and the Middle East (7.0—7.5 €/kg), the central Andes around southern Peru, Bolivia and northern Chile (6.7—7.8 €/kg), the south-west of the United States and western Mexico (7.0—7.4 €/kg), south-west Africa around Namibia and western South Africa (7.0—7.4 €/kg), Mongolia and northern China (7.2—7.7 €/kg), and north-west Australia (7.2—7.3 €/kg) all offering large areas with production costs lower than 7.5 €/kg H2. More expensive production areas include most of Europe and central Asia, as well as south-east and central China, coastal west Africa and the eastern half of the United States and Canada, due to their relative lack of either solar or wind power potential.
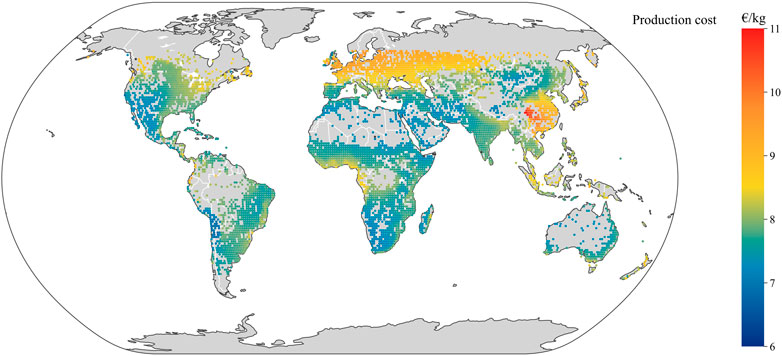
FIGURE 5. Production cost of H2 at each of the 5970 studied locations for the baseline scenario (100 kt/y AE electrolyser in 2030, centralised reconversion). Results are from a Monte Carlo simulation with 1,000 iterations.
The transport cost from each of the production locations to Cologne is shown in Figure 6. As expected, the area around Cologne has the lowest transport cost, slowly increasing as the distance from Cologne increases, with the closest measured location having a transport cost of 0.56 €/kg H2. Once the distance from the production site to Cologne surpasses around 1,000 km, in most cases becomes more economical to transport the H2 to the nearest port and ship it to Cologne rather than truck it directly, unless the production location is far from a port. It should be noted that all mediums are considered in Figure 6. For example, for a production location in South Africa, it might be more economically feasible to convert the H2 to NH3, whereas in India converting to a LOHC might make more financial sense.
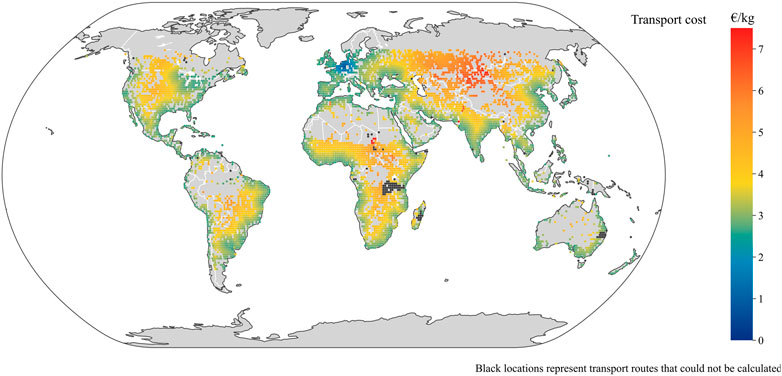
FIGURE 6. The transport cost of H2 to Cologne, Germany, in the baseline scenario (100 kt/y AE electrolyser in 2030, centralised reconversion), from each of the 5970 selected global locations. Black dots represent locations where possible transport routes could not be found. Pipelines are not considered in this scenario. All transport mediums are considered. Results are from a Monte Carlo simulation with 1,000 iterations.
The most cost-effective transport medium for each of the production locations is shown in Figure 7. For the baseline scenario with H2 required in Cologne, LOHCs are the most cost-effective transport medium for 64% of the production locations, followed by NH3 being the cheapest for 34% of the production locations. H2 gas is the cheapest only for 1.2% of production locations, all of which are locations closely surrounding Cologne, as the costs for trucking gaseous H2 increase quickly with respect to distance. The locations where LOHCs are cheaper are closer to the coast, whereas locations where NH3 is cheaper are further inland. This is because it is slightly cheaper to ship LOHCs than NH3, but more expensive to truck them, meaning that for locations far inland that must be trucked a long distance, it is cheaper to use NH3. For other locations close to the coast, LOHCs are the more cost-effective medium. LH2 is not preferred from a cost perspective for any production location, due to the combination of high conversion and export costs as well as high shipping and trucking costs per kilometre.
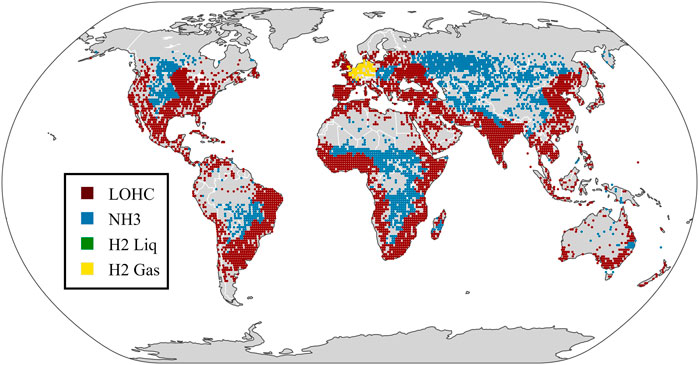
FIGURE 7. The most cost-effective transport medium for H2 required in Cologne, Germany, in the baseline scenario (100 kt/y AE electrolyser in 2030, centralised reconversion), from each of the 5970 selected global locations. Pipelines are not considered as a transport method in this scenario. Results are from a Monte Carlo simulation with 1,000 iterations.
Case Studies for Particular H2 Usage Locations
Figure 8 shows the total delivered cost of producing and transporting H2 to Cologne, Germany, from each possible H2 production location. The mean of the Monte Carlo simulation for each location was taken for the visualizations in this section. The costs range from 9.4—16.9 €/kg H2 (average standard deviation 0.31 €/kg H2), with the cheapest overall location being at (28, 34) near Sharm El-Sheikh, Egypt, with the H2 being converted to a LOHC, shipped to the closest port to Cologne and trucked the rest of the way before being reconverted. In general, there are an abundance of locations that could supply cheap renewable H2 to Cologne, with the cheapest production locations being in coastal north Africa (9.8—10.5 €/kg), the Middle East (9.8—11.0 €/kg), southern Spain (9.6—10.6 €/kg), and the area directly around Cologne (9.9—10.9 €/kg), closely followed by the other aforementioned low-cost generation areas. Western Germany’s relatively high H2 production costs (9.2—9.4 €/kg) are offset by the very low transportation distance to the usage location.
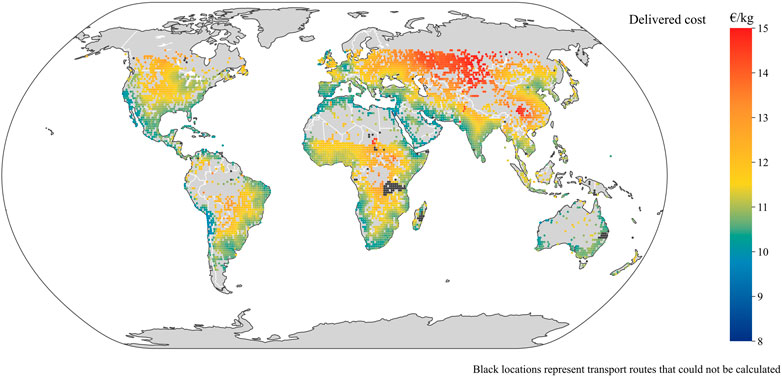
FIGURE 8. The total delivered cost (production and transport cost) of H2 required in Cologne, Germany, in the baseline scenario (100 kt/y AE electrolyser in 2030, centralised reconversion), from each of the 5970 selected global locations. Black dots represent locations where possible transport routes could not be found. All transport mediums are considered. Results are from a Monte Carlo simulation with 1,000 iterations.
The total delivered cost for the other studied locations is shown in Figure 9. For Abu Dhabi, the total costs reach lower values when compared to Cologne, with costs as low as 8.4 €/kg. The cheapest locations are directly around Abu Dhabi in the UAE, closely followed by Oman and southern Iran (8.9—9.8 €/kg). In the case of UAE and Oman, the H2 is transported by truck either in gaseous form, which although is more expensive than transporting NH3 or LH2, avoids the expensive conversion and re-conversion costs. From southern Iran, the H2 is transported in gaseous form to the nearest port, where it is converted to NH3 or LOHCs, shipped across the Persian Gulf to Abu Dhabi, and re-converted. No locations outside the Middle East offer costs under 9.4 €/kg. For Abu Dhabi and indeed most locations in the Middle East, using renewable H2 produced in the Middle East is the most desirable solution. As most of the region is very sunny, most countries will be able to produce renewable H2 at low costs themselves, reducing their energy reliance on other countries, as well as transport costs. Most countries in the region have a strong chemical and energy industry already and that expertise and infrastructure could be useful for renewable H2 generation.
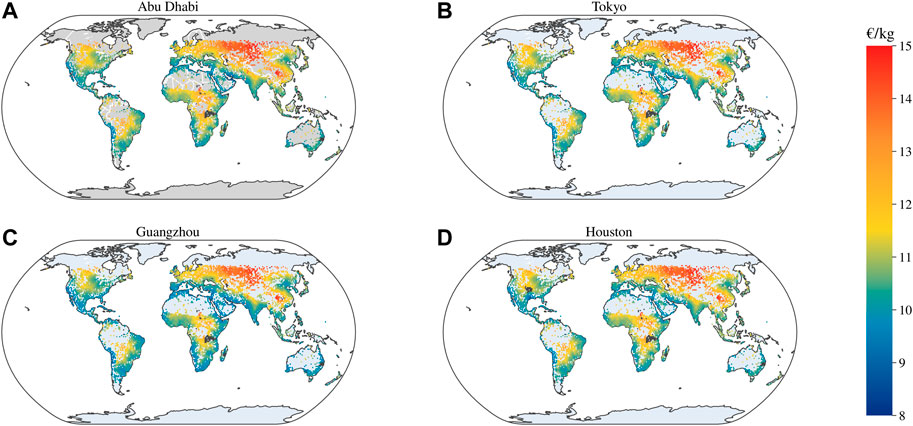
FIGURE 9. The total (delivered) cost per kg of producing and transporting H2 to Abu Dhabi (A), Tokyo (B), Guangzhou (C), and Houston (D), from each of the 5970 selected global locations. Black dots represent locations where possible transport routes could not be found. The rest of the parameters remain the same as for the baseline scenario (100 kt/y AE electrolyser in 2030). Results are from a Monte Carlo simulation with 1,000 iterations.
The minimum cost to produce and transport renewable H2 to Tokyo-Yokohama is 9.0 €/kg, from a location to the north of Tokyo utilizing wind power. However, most other areas in Japan are considerably more expensive, with the bulk ranging from 10.0—11.0 €/kg. It is possible that these smaller areas with strong renewable potential within Japan will not be able to produce enough H2 for the country’s requirements. Also, Japan might utilize these areas renewable potential to produce electricity for its population, instead of renewable H2. The safest most cost-effective options for the Tokyo-Yokohama region are north-west Australia and north Chile, with both having costs ranging from 9.3—9.8 €/kg. Indeed, Japan has already signed a partnership agreement with Australia to secure a supply of renewable H2 in the future. (FuelCellsWorks. Australia, 2020; Taylor, 2021) The Middle East (9.4—10.0 €/kg) and the west coast of Mexico (9.3—9.9 €/kg) are also strong alternatives.
For Guangzhou, the cheapest production location including transport is the coastal regions of south-west US and west Mexico (8.6—9.6 €/kg). Again, northern Chile (8.7—8.9 €/kg), north-west Australia (9.0—9.4 €/kg) and the Middle East (9.0—9.7 €/kg) are also very promising production locations. From these regions, the H2 is converted into either NH3 or LOHCs and shipped to Guangzhou. Costs in the region directly around Guangzhou range from 9.3—10. €/kg. The region is relatively cloudy and lacks consistent strong winds, resulting in locally renewably produced H2 being significantly more expensive than importing it, despite the additional transportation costs.
Lastly, the cheapest production locations for H2 required in Houston are in the western Gulf of Mexico, in a relatively large area directly around Houston with total costs ranging from 8.6—9.4 €/kg, from where the H2 can be trucked in gaseous form to the desired usage location. This area is relatively sunny, and although it has higher production costs than coastal south-west United States, the proximity to the usage location and thereby low transport cost outweigh the difference in production cost. The next cheapest locations include the coastal regions of southwest US and west Mexico (9.1—9.8 €/kg) and northern Chile (9.1—9.6 €/kg). The other low production cost areas such as the Middle East (9.7—10.2 €/kg) and north-west Australia (9.4—9.8 €/kg) are slightly more expensive than for the other usage locations studied, due to the large shipping distances required to transport the H2 to Houston. Therefore, it is likely that renewable H2 for the Houston area could be produced within Texas, allowing for energy independence.
Distribution of Results
The Monte Carlo simulation resulted in a distribution of costs for each production location analysed. Shown in Figure 10 are the distributions of the four major cost components calculated for the production site near Cairo with the lowest total cost per kg of H2 for the baseline scenario; the total cost of H2 (including transport to Cologne) (subplot A), the production cost of H2 (subplot B), and the cost of wind (subplot C) and solar (subplot D) electricity. All distributions resemble normal distributions with differing variances. Producing H2 at this location near Cairo and transporting it to Cologne has a mean total cost of 9.4 €/kg with a standard deviation of 0.43 €/kg. The production cost has a mean of 6.6 €/kg and a standard deviation of 0.39/kg. The distribution of the production cost is the same as that of the total cost but shifted by 2.2 €/kg, which is the transportation cost. As the transportation cost parameters are not included in the Monte Carlo simulation, the shape of the distribution of the total cost and production cost are the same. The cost of wind electricity at this location averages 32 €/MWh with a standard deviation of 1.5 €/MWh, while solar electricity costs on average 48 €/MWh with a standard deviation of 7.8 €/MWh. Wind electricity is the cheaper option at this location, although it has a much lower standard deviation due to the greater certainty of wind power costs. Therefore, the electricity cost from wind power is also more certain than the electricity cost from solar power.
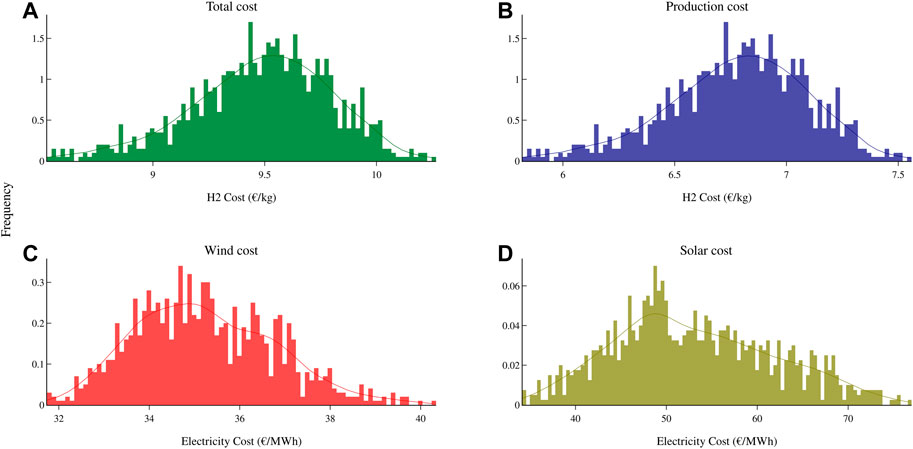
FIGURE 10. Distributions of the total (delivered) H2 cost including transport (A), the production cost (B), and the cost of wind (C) and solar (D) electricity from the Monte Carlo analysis (1,000 iterations) of the baseline scenario (100 kt/y AE electrolyser in 2030, H2 usage location in Cologne, centralised reconversion). The distributions represent the costs of the production site with the lowest total cost of H2 per kg, in Cairo, Egypt.
Parameter-Specific Results
The effect of changing other model parameters, such as the type of electrolyser used, the year the plant will be constructed, and the size of the plant was also analysed. In Figure 11, how the total cost in €/kg H2 is expected to change over time is shown for the three major electrolyser types for usage locations in Cologne and Houston. The mean value of the ‘total cost’ distribution in Figure 10 is shown. The study found that costs are expected to decrease in the future for all electrolyser types due to improvements in electrolyser design and efficiencies. Using AE electrolysers, the lowest calculated total cost for H2 required in Cologne decreases from 10.2 €/kg in 2020 to 8.6 €/kg by 2050, a drop of about 16%. PEM electrolysers are currently slightly more expensive (10.3 €/kg in 2020) but are projected to have a stronger reduction in costs of 26% to 7.6 €/kg by 2050. SOEs are the most expensive but are expected to have the sharpest decrease in costs over the next 30 years (33%), going from 12.9 €/kg in 2020 to 8.7 €/kg by 2050. The costs for Houston are about 1 €/kg less than for Cologne for all scenarios because it is cheaper to produce H2 close to Houston than close to Cologne, meaning the transport costs for H2 required in Cologne are higher. The transport costs are the same irrespective of the type of electrolyser used, as the H2 produced by different electrolysers is the same.
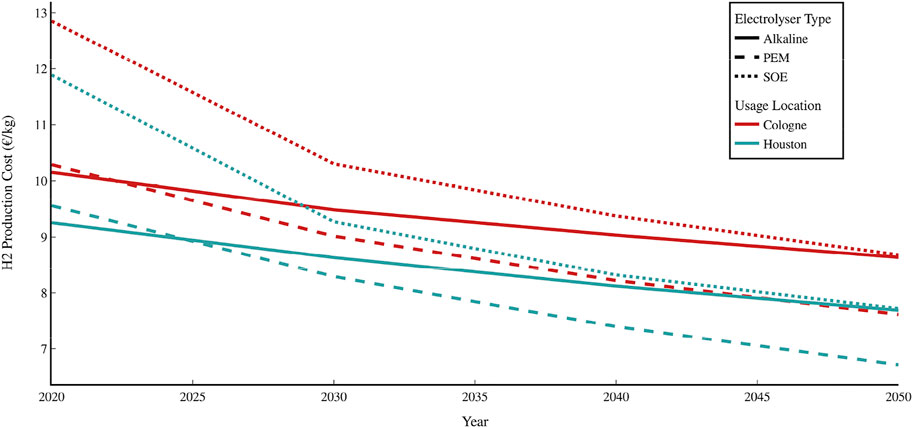
FIGURE 11. Cost per kg of producing and transporting H2 to Cologne and Houston for each electrolyser type from 2020–2050. The other parameters are the same as for the baseline scenario (100 kt/y capacity, centralised reconversion). Results are the average from a Monte Carlo simulation with 1,000 iterations.
The cost comparison between centralised and decentralised reconversion is shown in Figure 12 for H2 required in Cologne, Houston and Guangzhou. It should be noted that only the cheapest total production and transport option is shown in each case; if H2 is being produced and transported from another location, the costs and their relative difference could change. For Cologne, where it is cheapest to get H2 shipped as a LOHC from Egypt when conversion is centralised, the transport (and therefore also total) cost is about 0.4 €/kg H2 higher when conversion is decentralised. When conversion is decentralised, it is cheaper to produce the H2 close by to Cologne and transport it directly in trucks as gaseous H2 than to obtain it from Egypt in the form of LOHCs. Likewise, Guangzhou achieves a cost reduction of 0.95 €/kg H2 when conversion is centralised, a more significant cost reduction than in Cologne. When reconversion is decentralised in Guangzhou, it is more economically viable to transport using NH3 as the medium, due to the lower reconversion costs for decentralised conversion (see Figure 9). For Houston, no difference between centralised and decentralised reconversion is apparent; this is because for Houston, the cheapest H2 would be already transported in gaseous form by trucks from a production site close by; therefore, conversion is not necessary. In this case, the trucks could be directly dispatched to even small-scale end consumers directly, saving costs and time transporting the H2 first to a large-scale reconversion centre before distributing it to end consumers.
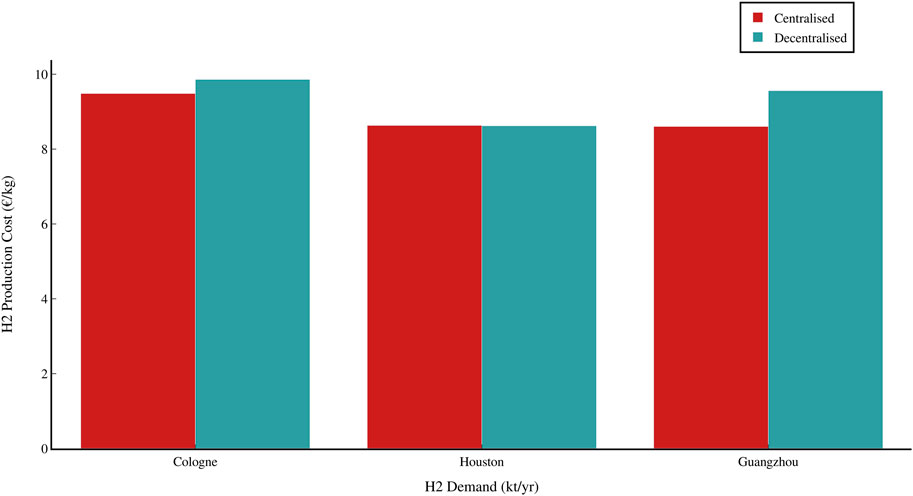
FIGURE 12. Lowest cost of producing and transporting H2 to Cologne, Houston and Guangzhou for the baseline scenario (100 kt/y AE electrolyser in 2030), showing both centralised and decentralised reconversion to gaseous H2. Results are from a Monte Carlo simulation with 1,000 iterations.
Use of Pipelines for Large Scale Transport
While pipelines are impractical for smaller H2 consumers, for large industrial consumers the cheaper operating cost of pipelines at large H2 volumes could be worth the high investment cost. Pipelines could also be used to cheaply supply large areas or even small countries if the H2 is piped to a central point before being distributed from there to smaller end users. Two particular pipeline scenarios were investigated for either large consumers or groups of consumers located in the areas of Cologne and Houston. When the use of large-volume (1,000 kt/y H2) pipelines is considered, the cheapest production location for H2 required in Cologne and its associated cost changes significantly. As well as direct pipelines between the production locations and the desired H2 usage location, pipelines were also considered between the production location and the closest port, from where H2 could still be shipped to the usage location, as well as between the usage location and the closest port. Three production locations offer the most cost-effective H2 to Cologne at similar prices: northern Scotland, the south coast of Ireland, and southern France close to Spain on the Mediterranean Sea, which all have strong wind resources. As the potential production location in France is better situated in terms of closeness to other potential industry and population centres and does not require an undersea pipeline, it will be investigated over the locations in Ireland and Scotland. The lowest-cost location is a place called Parc Eolien de Port la Nouvelle, which is actually already home to a wind park. If H2 was to be produced from the wind power generated in Parc Eolien de Port la Nouvelle, the estimated pipeline length required to transport H2 to Cologne would be about 1,120 km. Having such a pipeline would significantly reduce the costs for H2 in Cologne to 7.6 €/kg, as compared to the cheapest obtainable H2 without using pipelines, which is 9.4 €/kg for H2 shipped as a LOHC from Egypt and re-converted at Cologne. The total delivered cost per kg for H2 required in Cologne if pipelines are considered is shown in Figure 13 for all studied locations.
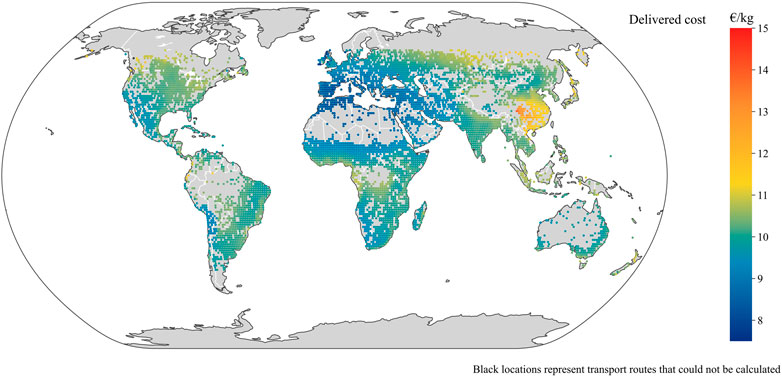
FIGURE 13. The total (delivered) cost per kg of producing and transporting H2 to Cologne, Germany, for large demand (1,000 kt/y) and allowing pipelines from production sites to Cologne. Other parameters follow the baseline scenario (AE electrolyser in 2030, centralised reconversion). Black dots represent locations where possible transport routes could not be found. Results are from a Monte Carlo simulation with 1,000 iterations.
As well as the three locations mentioned, other low-cost production locations for H2 needed in Cologne include southeast Spain, Italy, and the north coasts of Morocco, Algeria and Tunisia. Locations such as the Middle East, northern Chile and the southwest US, which are cost-competitive if no pipelines are built, are no longer economically viable compared to more local options if H2 pipelines are constructed. If a pipeline was built from the production site near Sharm El-Sheikh, Egypt, that was determined to be the most optimal production site for H2 required in Cologne if no pipelines are to be constructed, H2 required in Cologne would cost 8.4 €/kg, which is considerably more than H2 produced in Parc Eolien de Port la Nouvelle and piped to Cologne. The pure production cost of H2 in Parc Eolien de Port la Nouvelle is 7.2 €/kg H2, which is slightly higher than the production cost of 7.0 €/kg H2 for Sharm El-Sheikh. However, the transport cost using pipeline from Parc Eolien de Port la Nouvelle is only around 0.4 €/kg H2, considerably lower than the pipeline cost of 1.4/kg H2 to transport H2 from Sharm El-Sheikh to Cologne, and outweighing the slightly cheaper production cost at Sharm El-Sheikh. Another advantage of obtaining H2 from France as opposed to Egypt is geopolitical stability; France is also in the EU and a close ally of Germany, making it a more secure energy source. It could be possible that areas in the EU with high renewable energy resources, such as France, Ireland, or Spain could produce enough H2 to supply the future needs of the EU, reducing the energy reliance of the EU on foreign providers.
If pipelines are considered for the scenario of H2 required in Houston, the cheapest production location changes to (27, -104), a sunny location in north-central Mexico requiring a pipeline length of about 1,080 km, decreasing the minimum total cost to 7.6 €/kg H2 from a cost of 8.6 €/kg H2 if pipelines are not allowed. In general, a variety of locations across Mexico and the southern US are strong candidates for production sites, as shown in Figure 14. As with the Cologne scenario, it makes more sense for the US to produce H2 within the country to ensure a greater degree of energy self-sufficiency. A production site on the New Mexico/Texas border at (32, -105) could provide H2 to Houston at only 0.04 €/kg H2 more than the aforementioned site in Mexico while ensuring control over the production facilities. Other low-cost production locations that are competitive if no pipelines are allowed, such as northern Chile, are considerably more costly than closer locations in the southwest US and Mexico if pipelines are permitted. For these further away locations, shipping is still more cost-effective than a pipeline when large volumes are considered, while for closer locations, a pipeline becomes a much more economically viable option.
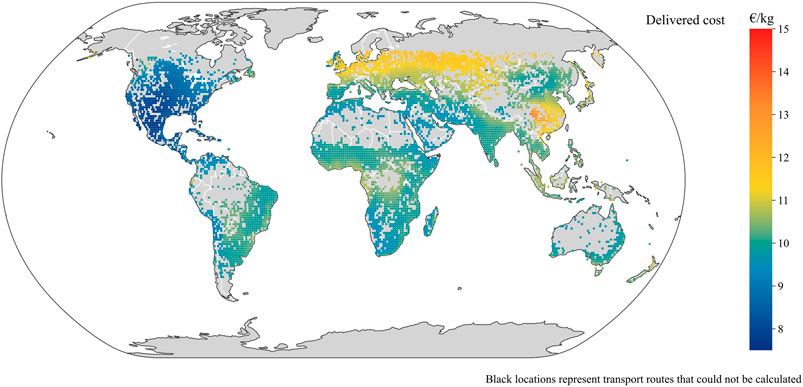
FIGURE 14. The total (delivered) cost per kg of producing and transporting H2 to Houston, United States, for large demand (1,000 kt/y) and allowing pipelines from production sites to Houston. Other parameters follow the baseline scenario (AE electrolyser in 2030, centralised reconversion). Black dots represent locations where possible transport routes could not be found. Results are from a Monte Carlo simulation with 1,000 iterations.
The most cost-effective transport medium for H2 required in Cologne when pipelines are considered is shown in Figure 15. H2 gas is now the cheapest medium for 42% of cases, as large-scale pipelines allow for much cheaper transport without expensive conversion and re-conversion to other mediums. However, the cost of pipelines increases more quickly per kilometre than shipping, and therefore shipping becomes more cost-effective for this scenario at distances greater than 6–7,000 km. Beyond that distance, LOHCs are a cheaper medium to use, being the most cost-effective medium for 58% of all production locations. LOHCs are favoured over NH3 in this scenario because as the produced amount is so large, pipelines are also considered from the production location to the closest port, and from the port closest to Cologne to the final usage location. LOHC pipelines are cheaper than NH3 pipelines, and so they are favoured for every production location where shipping is still cheaper than a pipeline.
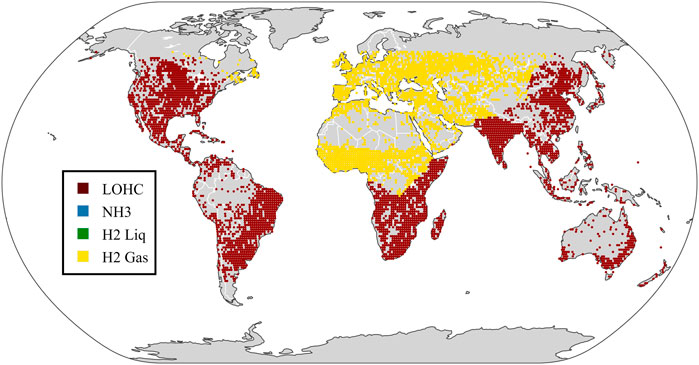
FIGURE 15. The most cost-effective transport medium for H2 required in Cologne, Germany, for large demand (1,000 kt/y) and allowing pipelines, from each of the 5970 selected global locations. Results are from a Monte Carlo simulation with 1,000 iterations.
Discussion
Production Cost Analysis
As expected, there is a strong correlation between locations with good wind or solar resources and low H2 production costs, as production cost variables other than electricity price remain constant between locations. In 85.7% of the studied locations, it is cheaper to generate electricity from solar power than from wind power; however, there are still many locations where wind power is the cheaper option, for example locations at far northerly or southerly latitudes, many coastal locations, or locations that have strong winds due to unique geographical circumstances, such as northern and western Europe (particularly the British Isles), the plains of central North America, and the Kazakh and Russian steppe. The average cost of wind power across all locations studied was 432 €/MWh, significantly higher than the 55 €/MWh for solar power, but also with much greater variance (standard deviation of 672 €/MWh for wind compared to 10 €/MWh for solar). The high mean of wind power is a result of many locations with very little wind in central and western Africa, South America and south-east Asia. In these locations, solar power is much more economically viable than wind power. The costs of generating both solar and wind power are shown for all locations in the Supplementary Figures S1, S2. In general, it is promising that a variety of regions have the potential to produce cheap renewable H2, as many countries could benefit that do not currently profit from an abundance of industry or resources.
The location-based trends in production cost over the world calculated in this study (shown in Figure 5) correlate strongly with the IEA (International Energy Agency, 2019) map of production costs of renewable H2 worldwide, which also shows northern Chile, south-west Africa, south-west United States and Mexico, the Middle East and Australia having the lowest H2 production cost. As the IEA did not exclude locations based on physical or human features, they also show Tibet as the cheapest region to produce renewable H2; however, this (and many of the other locations shown on their map) are unrealistic due to altitude, tough terrain, distance from industrial and urban centres, and a variety of other man-made and natural features. The Hydrogen Council (Hydrogen Council, 2021) also notes similar areas as having the best solar/wind resources for renewable H2 production. While the overarching trends between this study and the IEA report look very similar, it should be noted the costs reported by the IEA, as well as several other agencies, are markedly lower than those calculated here. For example, the IEA reports a H2 production cost of 2.0—3.4 €/kg H2 in the EU ‘in the future’ (assumed to be 2050 for the purposes of comparison). Bloomberg (Bloomberg New Energy Finance, 2020) has an even more aggressive estimation of a delivered cost of 2.0 USD/kg H2 in western Europe by 2030 and 1.0 USD/kg H2 by 2050, while IRENA (International Renewable Energy Agency, 2020) assumes costs of 2.5—3.5 USD/kg H2 in 2030 to 1.4 USD/kg H2 by 2050. For comparison, this study finds production costs of 7.5—9.7 €/kg H2 in western Europe in 2030, and 6.5—8.3 €/kg H2 in 2050, with the cheapest production costs worldwide being 6.0 €/kg H2 in 2050, which is similar to those reported by Christensen (Christensen, 2020) (7.5—16.0 USD/kg H2 in the EU in 2020 and 5.8—10.5 USD/kg H2 in 2050). In order to benchmark the results of this study against others, an overview of the H2 production costs from various studies is shown in Table 4, along with short notes about the factors considered in each study.
The IEA’s calculations for the levelized cost of hydrogen (LCOH) are unclear as to what year the costs are calculated for, what capacity the hybrid solar-wind power system achieves and most importantly, what is included in their calculations for “production cost”. Christensen (Christensen, 2020) was “able to reproduce the IEA data... but only if we neglected all system costs beyond the electricity and electrolyser CAPEX costs”. The Bloomberg (Bloomberg New Energy Finance, 2020) and IRENA (Gielen et al., 2019) studies also seem to neglect these extra systems costs. In this study, the H2 production cost is calculated including the required compression, storage, OpEx and other maintenance, piping, and dispense costs required to ensure the H2 is ready to be transported to its required destination, which explains the discrepancy between the production costs of the aforementioned agencies and those presented here. The costs calculated in this study are at this stage not cost-competitive with the benchmark of H2 produced by SMR (2.2 €/kg H2). (Gielen et al., 2019) However, with a combination of CO2 taxes and technological development, it is possible that renewable H2 could be cost-competitive in the future.
Transport Cost Analysis
Although the transport costs are almost always lower than the production cost, they still make up a significant portion of the total cost. For production locations, the distance from the nearest port is important—coastal regions usually have lower transport costs, whereas far inland regions such as Mongolia have very high transport costs. If the production location is close enough to the usage location to truck the H2 in gaseous form, the huge cost of conversion and re-conversion is saved. Interesting to note is that a large increase in shipping distance results in only a slight increase to the transport cost; for example, transport to Cologne from a coastal location in southern France has a transport cost of around 2.7 €/kg H2, but transport from Brazil costs only 2.9—3.0 €/kg H2. The bulk of these costs is the conversion and re-conversion into either NH3 or a LOHC, which is expensive but drastically reduces the cost of shipping. This is expected; ships are the most cost-effective transport method for transporting goods long distances, especially when large volumes of cargo are transported, and are currently used to transport oil, natural gas, minerals, and many other goods (International Transport Forum, 2019). A bigger contributor to cost is the distance from the coast—it can be seen from Figure 6 that across the world the transport costs increase as the production locations go further inland. It can then be inferred that trucking from the production location to the port, either for gaseous H2 or any transport medium, is a large cost contributor. Therefore, having production locations on the coast, and in particular close to ports, would heavily reduce transport costs to far-away locations that require H2.
Other studies, such as those done by the IEA (International Energy Agency, 2019) and the Hydrogen Council, (Hydrogen Council, 2021) estimate the transport cost for a few particular scenarios. The Hydrogen Council calculates the transport costs for three similarly distanced shipping routes (7000–8500 km); one using NH3 as a medium, one using LH2, and the last being converted to a LOHC, with the resulting transport costs ranging from 1.8—2.7 €/kg H2. The IEA calculates a transport cost of 1.8—3.6 €/kg H2 from Australia to Japan. While there are some differences, the costs are comparable to the transport costs calculated in this study for similar routes, as highlighted in Table 5, and show much more similarity than the production costs from the same studies. The largest discrepancy is for LH2 and gaseous H2 transport; this is probably due to differing assumptions on how fast transport technology for LH2 will progress. As it is still in a relatively early stage of development, the transport costs for LH2 and gaseous H2 are quite uncertain, and it is therefore natural to have greater discrepancies than for LOHCs and NH3. The transport costs calculated in this study for NH3 and LOHCs are slightly higher than those from the IEA and Hydrogen Council, but they are generally more similar than the H2 transport costs and within the realms of normal uncertainty.
While the most cost-effective transport mediums for each production location (Figure 7) currently heavily favour LOHCs and NH3 due to the ease of transportation and storage, this could change in the future due to differences in energy conversion efficiency between the different mediums. Comparing the energy efficiency between different mediums is complex, as not only must the energy losses of conversion and re-conversion be considered but also the energy losses during storage and transportation, which differ for every medium. Such calculations would be different for every production location and could be the subject of a complete study on its own. However, as the energy losses for H2 gas (5–15% for compression (Energy Transition Institute, 2014)) are lower than for LH2 (9–22% round trip efficiency (Baker and Shaner, 1978)), NH3 (11—19% round trip efficiency (Giddey et al., 2017)), and LOHCs (26—43% round trip efficiency (Modisha et al., 2019)), it could end up being the most cost-effective transport medium if energy efficiency can be preserved along the transport route. For comparison, Bøe et al. (Bøe et al., 2021) find average total supply chain efficiencies of 20—30% for LH2, 15—27% for NH3, and 15—25% for a sample LOHC. These efficiencies suggest pipelines of gaseous H2 could be the most energy-efficient transport method when the production site is close enough, and demand high enough, to justify the high CapEx of the pipeline.
It should also be mentioned that although this study focuses only on the economic cost of storage and transportation, there are many physical and technological factors to be considered, such as H2 density of the carrier, leakage, and corrosivity. For example, NH3 has a relatively high H2 density (17.7 wt%) and has a low leakage rate, making it an attractive transport and storage medium from a technological perspective. (Wijayanta et al., 2019) While it is corrosive and toxic, it can be stored in low-cost tanks currently used for LPG, and transport and storage of NH3 is already widespread. Therefore, it is the most technologically ready transport medium.
LOHCs have a lower H2 density (6.16 wt% for toluene), requiring notably larger tank sizes to transport the same amount of H2. (Wijayanta et al., 2019) As this is stoichiometrically set, this places inherent space and weight limitations on the transport and storage of H2 using LOHCs. LH2, while naturally being very pure, requires immense energy for cooling (-250°C) and has relatively high boil off (0.2—0.3%/d), while is problematic for long-term storage and long-haul transportation. (Wijayanta et al., 2019) While NH3 and LOHCs can already be shipped, the first LH2 ship has only just been launched in 2022, and gaseous H2 pipelines still require further research and development. (Carbon capture needed for expansion, 2020) Hence, LOHCs and especially NH3 might be more beneficial transport mediums in the near future. LOHCs and NH3 could also use existing pipeline infrastructure, whereas new or heavily retrofitted pipelines would have to be installed to accommodate H2. (International Energy Agency, 2019)
Parameter Analysis
In general, CapEx costs for electrolysers are predicted to decrease significantly in the next few decades, primarily due to advances in technology and efficiency as the number of electrolysers constructed increases dramatically, but also due to the increasing capacity of electrolyser systems, which can take advantage of economy of scale effects. The difference in cost reductions over the next 30 years is likely due to the differing levels of industrial development of the three electrolyser types; AE electrolysers, as the most commonly used industrially in the present day, have already undergone the most development and there are therefore less cost reduction breakthroughs to be made in the future. PEM electrolysers are expected to have a greater cut in cost as their market share increases and natural development continues, and even more so for SOEs, which are currently the least industrially proven option. Especially in the short term, over the next decade, SOEs are expected to have a drastic reduction in costs due to further industrial development. PEM electrolysers are believed to offer the cheapest H2 from around 2023 onwards due to their high scalability and efficiency, as well as the fact that it is possible to obtain already compressed H2 out of the process, heavily reducing the H2 compression costs that are required for storage or transport.
Pipeline Analysis
As H2 can be piped in gaseous form without the need for conversion into a different medium or liquefaction, this can drastically reduce transport costs, especially for larger H2 demands. Capital investment per unit of product generally decreases as the amount of product increases due to economies of scale effects. (Gim and Yoon, 2012) As pipelines have by far the most capital investment required of the transport methods studied, the scaling effect has a more pronounced cost reduction for pipelines compared to trucks and ships, of which the bulk of the costs come from operational expenditures and do not decrease much as the amount transported increases.
It is still cheaper to ship H2 in the form of a chemical medium long distances than to pipe it in gaseous form, despite the conversion and re-conversion costs. However, it is much cheaper to pipe H2 short distances than ship H2, meaning the inclusion of pipelines favours more locally based H2 production sites, at least for large-scale H2 demand. Using pipelines would be particularly attractive for countries or regions with strong renewable resources looking to be energy independent, provided they have a large enough demand for H2 to justify the high capital investment of pipelines.
A weakness of the pipeline calculations is the assumption that the pipeline distance is 20% greater than the straight-line distance between the locations. In reality, this number might often be quite different; in some scenarios, it might be possible to build a pipeline directly from the production location to the usage location, and in other situations, the pipeline could have to circumvent a variety of obstacles such as other properties or rough terrain. However, as assessing optimal pipeline routes is a complex task for just a single pipeline, it is impractical to assume different values for different routes in this study.
Data, Uncertainty and Model Analysis
There are some limitations imposed by the scope of the model. For some unique locations that have both good wind and solar resources, such as south-west Europe and northern Africa, the Middle East, Western Australia, and northern Chile, hybrid systems could potentially allow for an increase in the capacity factor of the electrolyser, as there would be a greater fraction of time that electricity could be generated compared to a single renewable electricity generation system. Nevertheless, building a hybrid wind-solar system would likely result in a slightly higher cost of electricity than a single system due to capital investment “economy of scale” effects. (Gim and Yoon, 2012) Additionally, offshore wind could be the most cost-effective electricity generation source for some H2 usage locations, such as countries like the UK or Denmark.
Labour and infrastructure costs could vary in different countries. Additionally, there could be instances of the closest port to a production site being in another country. In many scenarios, this may not make a difference, but it could in some scenarios where the neighbouring country does not allow the production site use of the port.
There are likely some cases where NH3 or LOHCs are desired as the final product instead of H2. In this case, the high re-conversion costs can be avoided, which would lower the cost. As the market share of NH3, in particular, is comparatively large, a relatively high amount of renewable H2 could be used to produce NH3 (Fortune Business Insights, 2020) Although the cost is greater than conventional NH3, it could become competitive as CO2 prices increase. (ChemAnalyst. Ammonia Price, 2020)
Grid-connected electrolysis systems could likely reduce the H2 production cost and increase the capacity factor, as electricity can be sold to the grid when there is an oversupply of renewable power and drawn from the grid when not enough is produced. (Christensen, 2020) It should be noted, however, that grid power in most countries is not yet fully renewable, which would increase GHG emissions of H2 production. As grids become more and more renewable, however, most electrolysers will likely be grid-connected to maximize their capacity factor. In general, estimating the capacity factor for different locations is difficult. In this study, a constant value was assumed, which would likely vary in reality for different locations, as well as being dependent on whether solar or wind power is used. Other ways to increase the electrolyser capacity factor include oversizing the renewable electricity generator, adding batteries as an energy storage, and hybrid PV-wind systems. (Christensen, 2020) However, these have associated extra costs and research is required to determine their economic plausibility.
The parameters of the cost calculations with the biggest impact on the final cost are the CapEx of the electrolyser and the electricity price. The solar and wind data have very low uncertainty as they were obtained from reputable public sources and were cross-checked against other databases to ensure an acceptable degree of similarity. The low, medium and high electrolyser CapEx were taken from Christensen’s (Christensen, 2020) analysis of the study conducted by Glenk et al., (Glenk and Reichelstein, 2019) who thoroughly investigated a large range of original data sources of electrolyser investment costs. While the sample size of electrolyser costs taken is large (n = 52 for AE electrolysers), the standard deviation is also comparably high (±345 €/kW or ±29% for AE electrolysers), which infers the data is quite uncertain. As H2 electrolysis is a technology still undergoing development at larger industrial scales, cost data is likely to both become more certain and decrease in the next few decades. As the uncertainty of each electrolysis CapEx obtained from literature is high, taking the mean of all obtained values from reputable studies is the most certain option available at the moment. The uncertainty of transport cost data is difficult to ascertain due to the various ways it is reported in different studies; many papers only report the cost for a particular case study. Transport costs were taken from the IEA report (International Energy Agency, 2019) and were verified against other reports and data to ensure costs were similar. Costs for transportation of NH3 and LOHCs were more similar than for LH2 and gaseous H2, largely because transportation of H2 is much less developed and therefore cost data are by nature more uncertain. Overall, the delivered costs reported in the study have a moderate uncertainty, largely due to the aforementioned uncertainty regarding future electrolysis and H2 transport costs.
The production locations were selected at intervals of one-degree latitude and longitude, resulting in 5970 locations once the masked areas were excluded. Selecting points with smaller intervals, for example every 0.5°, would increase the resolution of the study and potentially find some slightly more advantageous locations, but at the expense of a vastly increased computation time. For example, decreasing the intervals to 0.5° would increase the number of production locations and therefore also the computation time by a factor of four, which is unfeasible in this study for the relatively small preciseness gain that would result.
1,000 iterations were completed for each scenario in the Monte Carlo simulation. Although more iterations would have slightly improved the accuracy of the predictions, it would drastically increase the computation time and render it unfeasible within the limitations of the study. For example, increasing the number of iterations from 1,000 to 10,000 would likely only increase the accuracy of the simulation by about 0.5%, but would take 10 times longer to compute. (Oberle, 2015)
Conclusion
Replacing fossil fuels or fossil-fuel-based H2 with renewable H2 is a promising solution to reduce GHG emissions in industries such as steel and chemicals. For stakeholders wishing to use renewable H2, the cost, as well as the production location and transport route, are essential information for process development. A model was created to determine the minimum delivered cost of renewable H2 to any location worldwide, as well as the associated cheapest production location, transport route and transport medium.
Locations with high population and heavy industry, such as Cologne, Germany, and Houston, United States, were selected as case studies. Total delivered H2 costs range from 9.4—11.0 €/kg in Cologne and 8.6—10.2 €/kg in Houston, with the most promising production locations being the Middle East for Cologne and either the southwest United States or northern Chile for Houston. South-west Africa and north-west Australia also have low H2 production costs, and along with the aforementioned production locations are the best suited to offer relatively low-cost H2 worldwide. For small demands, when pipelines are not economically feasible, LOHCs are the most commonly preferred transport medium, except for production locations close (<1,000 km) to the usage location, for which trucking gaseous H2 is more economically feasible. For larger demands such as industrial areas, large pipelines transporting H2 gas similar to those used for natural gas today can be considered, which could reduce the cost significantly to 7.6 €/kg H2 for both Cologne and Houston, as well as favouring closer production locations in southern France and Texas, respectively. In general, NH3 and LOHCs are the preferred transport medium for longer distances, while H2 gas pipelines are a more cost-effective option for short to medium distances, particularly if there is a large demand. (Hydrogen Council, 2020) In the short term, NH3 and LOHCs are likely to be more attractive transport mediums, as they can be transported by currently existing infrastructure. LH2 ships and H2 pipelines require time to be built, as well as further technological development. However, in the future, they may become more attractive due to high conversion efficiencies. H2 production costs are expected to decrease over the next few decades by up to 1.8 €/kg, largely due to decreasing electrolyser CapEx and renewable energy costs, particularly for PEM and SOEs.
Needed further studies include investigating the effect of rising CO2 prices on the economic feasibility of renewable H2 (Gerbelová, 2014) and evaluating the full-trip energy efficiency of different transport mediums to determine the potential for cost reduction. (Cerniauskas et al., 2019) As well, examining particular case studies in more depth, such as considering hybrid PV-wind systems, offshore wind generation, and scenarios where NH3 and LOHCs are desired as an end product would be a logical next step.
Data Availability Statement
The original contributions presented in the study are included in the article/Supplementary Material, further inquiries can be directed to the corresponding author. The model used in this study can be found at the following link: https://github.com/jooooohannes/h2-mapping.
Author Contributions
JC performed literature research, envisaged and developed the model, and was the main author of all text. RS provided guidance and structure to the manuscript.
Funding
This research was carried out within the project BAC-2-FUEL, which received funding from the European Union’s Horizon 2020 research and innovation program under grant agreement no. 825999. The European Commission is neither responsible nor liable for the content of this document.
Conflict of Interest
The authors declare that the research was conducted in the absence of any commercial or financial relationships that could be construed as a potential conflict of interest.
Publisher’s Note
All claims expressed in this article are solely those of the authors and do not necessarily represent those of their affiliated organizations, or those of the publisher, the editors and the reviewers. Any product that may be evaluated in this article, or claim that may be made by its manufacturer, is not guaranteed or endorsed by the publisher.
Acknowledgments
The authors would also like to thank Till Strunge for proof-reading the manuscript.
Supplementary Material
The Supplementary Material for this article can be found online at: https://www.frontiersin.org/articles/10.3389/fenrg.2022.909298/full#supplementary-material
References
Aditiya, H. B., and Aziz, M. (2021). Prospect of Hydrogen Energy in Asia-Pacific: A Perspective Review on Techno-Socio-Economy Nexus. Int. J. Hydrogen Energy 46, 35027–35056. doi:10.1016/j.ijhydene.2021.08.070
Andaloro, L., Ferraro, M., Brunaccini, G., Sergi, F., and Antonucci, V. (2019). From Distributed Generation to Smart Grids: Integration of H2 and Renewable Energy towards Zero Emissions Home. ECS Trans. 17, 673–684.
Baker, C., and Shaner, R. L. (1978). A Study of the Efficiency of Hydrogen Liquefaction. Int. J. Hydrogen Energy 3, 321–334. doi:10.1016/0360-3199(78)90037-x
Baufumé, S. (2013). GIS-based Scenario Calculations for a Nationwide German Hydrogen Pipeline Infrastructure. Int. J. Hydrogen Energy 38, 3813–3829.
Bellevrat, E., and Menanteau, P. (2009). Introducing Carbon Constraint in the Steel Sector: ULCOS Scenarios and Economic Modeling. Rev. Metall. Paris 106, 318–324. doi:10.1051/metal/2009059
Benita, F., Bansal, G., Piliouras, G., and Tunçer, B. (2019). Short-distance Commuters in the Smart City.
Bhandari, R., Trudewind, C. A., and Zapp, P. (2014). Life Cycle Assessment of Hydrogen Production via Electrolysis - A Review. J. Clean. Prod. 85, 151–163. doi:10.1016/j.jclepro.2013.07.048
Bhaskar, A., Assadi, M., and Somehsaraei, H. N. (2020). Decarbonization of the Iron and Steel Industry with Direct Reduction of Iron Ore with Green Hydrogen. Energies 13, 1–23. doi:10.3390/en13030758
Bøe, A. V., Gullbrå, D. O., and Reinertsen, T. A. (2021). An Efficiency Comparison of Liquid Hydrogen, Ammonia, and Liquid Organic Hydrogen Carriers for Maritime Use. ACS Sustain. Chem. Eng.
Botelho, A., Ferreira, P., Lima, F., Pinto, L. M. C., and Sousa, S. (2017). Assessment of the Environmental Impacts Associated with Hydropower. Renew. Sustain. Energy Rev. 70, 896–904. doi:10.1016/j.rser.2016.11.271
Branker, K., Pathak, M. J. M., and Pearce, J. M. (2011). A Review of Solar Photovoltaic Levelized Cost of Electricity. Renew. Sustain. Energy Rev. 15, 4470–4482. doi:10.1016/j.rser.2011.07.104
Brauns, J., and Turek, T. (2020). Alkaline Water Electrolysis Powered by Renewable Energy: A Review. Processes 8. doi:10.3390/pr8020248
Brynolf, S., Taljegard, M., Grahn, M., and Hansson, J. (2018). Electrofuels for the Transport Sector: A Review of Production Costs. Renew. Sustain. Energy Rev. 81, 1887–1905. doi:10.1016/j.rser.2017.05.288
Cai, L., Jacobs, S., Langer, R., vom Lehn, F., Heufer, K. A., and Pitsch, H. (2020). Auto-ignition of Oxymethylene Ethers (OMEn, N = 2-4) as Promising Synthetic E-Fuels from Renewable Electricity: Shock Tube Experiments and Automatic Mechanism Generation. Fuel 264, 116711. doi:10.1016/j.fuel.2019.116711
Carbon capture needed for expansion, (2020). World-first Hydrogen Tanker Arrives in Victoria to Test Potential for Exporting Fuel Source to Japan - ABC News. Available at: https://www.abc.net.au/news/2022-01-21/world-first-hydrogen-tanker-docks-at-port-of-hastings/100769138.
Carbon4Pur, (2020). CO2/CO Sources and Consumer Map. Available at: https://carbon4pur.github.io/mapping/index.html.
Carmo, M., and Fritz, D. L. (2013). A Comprehensive Review on PEM Water Electrolysis. Hydrog. Energy 8. doi:10.1016/j.ijhydene.2013.01.151
Cerniauskas, S., Grube, T., Praktiknjo, A., Stolten, D., and Robinius, M. (2019). Future Hydrogen Markets for Transportation and Industry: The Impact of CO2 Taxes. Energies 12. doi:10.3390/en12244707
ChemAnalyst. Ammonia Price, (2020). Prices, Pricing, Market & Analysis. Available at: https://www.chemanalyst.com/Pricing-data/ammonia-37.
Chiuta, S., Engelbrecht, N., Human, G., and Bessarabov, D. G. (2016). Techno-economic Assessment of Power-To-Methane and Power-To-Syngas Business Models for Sustainable Carbon Dioxide Utilization in Coal-To-Liquid Facilities. J. CO2 Util. 16, 399–411. doi:10.1016/j.jcou.2016.10.001
Christensen, A. (2020). Assessment of Hydrogen Production Costs from Electrolysis: United States and Europe. Berlin: International Council on Clean Transportation. Available at: https://theicct.org/sites/default/files/publications/final_icct2020_assessment_of _hydrogen_production_costs v2.pdf.
Christopher, K., and Dimitrios, R. (2012). A Review on Exergy Comparison of Hydrogen Production Methods from Renewable Energy Sources. Energy Environ. Sci. 5, 6640–6651. doi:10.1039/c2ee01098d
Collis, J., Strunge, T., Steubing, B., Zimmermann, A., and Schomäcker, R. (2021). Deriving Economic Potential and GHG Emissions of Steel Mill Gas for Chemical Industry. Front. Energy 9, 1–22. doi:10.3389/fenrg.2021.642162
De-León Almaraz, S., Azzaro-Pantel, C., Montastruc, L., Pibouleau, L., and Senties, O. B. (2012). Design of a Hydrogen Supply Chain Using Multiobjective Optimisation. Comput. Aided Chem. Eng. 30, 292–296.
Dufour, J., Serrano, D. P., Gálvez, J. L., Moreno, J., and González, A. (2011). Hydrogen Production from Fossil Fuels: Life Cycle Assessment of Technologies with Low Greenhouse Gas Emissions. Energy fuels. 25, 2194–2202. doi:10.1021/ef200124d
Esmap. Global, (2020). Photovoltaic Power Potential by Country. Washington, DC: World Bank. Available at: https://globalsolaratlas.info/global-pv-potential-study.
Fortune Business Insights (2020). Ammonia Market Size & Share | Industry Analysis Report. Available at: https://www.fortunebusinessinsights.com/industry-reports/ammonia-market-101716.
FuelCellsWorks. Australia, (2020). Japan Sign Hydrogen Agreement: An Exciting Step towards Hydrogen Future. Available at: https://fuelcellsworks.com/news/australia-japan-sign-hydrogen-agreement-an-exciting-step-towards-hydrogen-future/.
GeoPy Contributors (2018). GeoPy. Available at: https://geopy.readthedocs.io/en/stable/#.
Gerbelová, H. (2014). Potential of CO2 (Carbon Dioxide) Taxes as a Policy Measure towards Low-Carbon Portuguese Electricity Sector by 2050. Energy 69, 113–119.
Germeshuizen, L. M., and Blom, P. W. E. (2013). A Techno-Economic Evaluation of the Use of Hydrogen in a Steel Production Process, Utilizing Nuclear Process Heat. Int. J. Hydrogen Energy 38, 10671–10682. doi:10.1016/j.ijhydene.2013.06.076
Giddey, S., Badwal, S. P. S., Munnings, C., and Dolan, M. (2017). Ammonia as a Renewable Energy Transportation Media. ACS Sustain. Chem. Eng. 5, 10231–10239. doi:10.1021/acssuschemeng.7b02219
Gielen, D., Taibi, E., and Miranda, R. (2019). Hydrogen: A Renewable Energy Perspective. Abu Dhabi: International Renewable Energy Agency. Available at: www.irena.org.
Gim, B., and Yoon, W. L. (2012). Analysis of the Economy of Scale and Estimation of the Future Hydrogen Production Costs at On-Site Hydrogen Refueling Stations in Korea. Int. J. Hydrogen Energy 37, 19138–19145. doi:10.1016/j.ijhydene.2012.09.163
Glenk, G., and Reichelstein, S. (2019). Economics of Converting Renewable Power to Hydrogen. Nat. Energy 4, 216–222. doi:10.1038/s41560-019-0326-1
Green, R., and Vasilakos, N. (2011). The Economics of Offshore Wind. Energy Policy 39, 496–502. doi:10.1016/j.enpol.2010.10.011
Halpern, B., Frazier, M., Potapenko, J., Casey, K., and Koenig, K. (2015). Cumulative Human Impacts: Raw Stressor Data (2008 and 2013). Knowl. Netw. Biocomplexity. doi:10.5063/F1S180FS
Han, J.-H., Ryu, J.-H., and Lee, I.-B. (2012). Modeling the Operation of Hydrogen Supply Networks Considering Facility Location. Int. J. Hydrogen Energy 37, 5328–5346. doi:10.1016/j.ijhydene.2011.04.001
Hawer, S., Schönmann, A., and Reinhart, G. (2018). Guideline for the Classification and Modelling of Uncertainty and Fuzziness. Procedia CIRP 67, 52–57. doi:10.1016/j.procir.2017.12.175
Ho, M. T., Bustamante, A., and Wiley, D. E. (2013). Comparison of CO2 Capture Economics for Iron and Steel Mills. Int. J. Greenh. Gas Control 19, 145–159. doi:10.1016/j.ijggc.2013.08.003
Hoffmann, C., Hoey, M. Van., and Zeumer, B. (2020). Decarbonization Challenge for Steel. Available at: https://www.mckinsey.com/∼/media/McKinsey/Industries/Metals and Mining/Our Insights/Decarbonization challenge for steel/Decarbonization-challenge-for-steel.pdf.
Hörsch, J., and Brown, T. (2017). The Role of Spatial Scale in Joint Optimisations of Generation and Transmission for European Highly Renewable Scenarios. Frankfurt am Main: Frankfurt Institiute for Advanced Studies.
Hwangbo, S., Lee, I.-B., and Han, J. (2017). Mathematical Model to Optimize Design of Integrated Utility Supply Network and Future Global Hydrogen Supply Network under Demand Uncertainty. Appl. Energy 195, 257–267. doi:10.1016/j.apenergy.2017.03.041
Hydrogen Council (2021). Hydrogen Insights. Available at: https://hydrogencouncil.com/wp-content/uploads/2021/02/Hydrogen-Insights-2021.pdf.
Hydrogen Council (2020). Path to Hydrogen Competitiveness: A Cost Perspective. Available at: ww.hydrogencouncil.com.
International Energy Agency, (2020). Iron and Steel Technology Roadmap. Paris: Iron and Steel Technology Roadmap. doi:10.1787/3dcc2a1b-en
International Energy Agency, (2019). The Future of Hydrogen. Paris: The Future of Hydrogen. doi:10.1787/1e0514c4-en
International Renewable Energy Agency, (2020). Green Hydrogen Cost Reduction. Available at: https://www.irena.org/-/media/Files/IRENA/Agency/Publication/2020/Dec/IRENA_Green_hydrogen_cost_2020.pdf.
International Renewable Energy Agency, (2016). The Power to Change: Solar and Wind Cost Reduction Potential to 2025.
International Renewable Energy Agency, (2012). Wind Power, 20. Abu Dhabi: Green Energy and Technology.
International Transport Forum, (2019). ITF Transport Outlook 2019. Paris: OECD. doi:10.1787/transp_outlook-en-2019-enITF Transport Outlook 2019
Jäger-Waldau, A. (2019). PV Status Report 2019. Brussels: JRC Science for Policy Report. doi:10.2760/326629
Jarraud, M., and Steiner, A. (2014). Climate Change 2014: Synthesis Report. Geneva: IPCC, 9781107025.
Kaiwen, L., Bin, Y., and Tao, Z. (2018). Economic Analysis of Hydrogen Production from Steam Reforming Process: A Literature Review. Energy Sources, Part B Econ. Plan. Policy 13, 109–115. doi:10.1080/15567249.2017.1387619
Kakoulaki, G., Kougias, I., Taylor, N., Dolci, F., Moya, J., and Jäger-Waldau, A. (2021). Green Hydrogen in Europe - A Regional Assessment: Substituting Existing Production with Electrolysis Powered by Renewables. Energy Convers. Manag. 228, 113649. doi:10.1016/j.enconman.2020.113649
Khojasteh Salkuyeh, Y., Saville, B. A., and MacLean, H. L. (2017). Techno-economic Analysis and Life Cycle Assessment of Hydrogen Production from Natural Gas Using Current and Emerging Technologies. Int. J. Hydrogen Energy 42, 18894–. doi:10.1016/j.ijhydene.2017.05.219
Laguna-Bercero, M. A. (2012). Recent Advances in High Temperature Electrolysis Using Solid Oxide Fuel Cells: A Review. J. Power Sources 203, 4–16. doi:10.1016/j.jpowsour.2011.12.019
Lahnaoui, A., Wulf, C., and Dalmazzone, D. (2021). Optimization of Hydrogen Cost and Transport Technology in france and germany for Various Production and Demand Scenarios. Energies 14. doi:10.3390/en14030744
Leimkühler, H. (2010). Managing CO2 Emissions in the Chemical Industry. Wiley-VCH Verlag GmbH & Co. KGaA.
Levene, J. I., Mann, M. K., Margolis, R. M., and Milbrandt, A. (2007). An Analysis of Hydrogen Production from Renewable Electricity Sources. Sol. Energy 81, 773–780. doi:10.1016/j.solener.2006.10.005
Lindstad, E., Lagemann, B., Rialland, A., Gamlem, G. M., and Valland, A. (2021). Reduction of Maritime GHG Emissions and the Potential Role of E-Fuels. Transp. Res. Part D Transp. Environ. 101, 103075. doi:10.1016/j.trd.2021.103075
Mapbox. Rasterio, (2016). Access to Geospatial Raster Data. Available at: https://rasterio.readthedocs.io/en/latest/index.html.
Mayer, J. N., Philipps, S., Hussein, N. S., Schlegl, T., and Senkpiel, C. (2015). Current and Future Cost of Photovoltaics Long-Term Scenarios for Market Development, 82.
Modisha, P. M., Ouma, C. N. M., Garidzirai, R., Wasserscheid, P., and Bessarabov, D. (2019). The Prospect of Hydrogen Storage Using Liquid Organic Hydrogen Carriers. Energy Fuels 33. doi:10.1021/acs.energyfuels.9b00296
Muradov, N. (2017). Low to Near-Zero CO2 Production of Hydrogen from Fossil Fuels: Status and Perspectives. Int. J. Hydrogen Energy 42, 14058–14088. doi:10.1016/j.ijhydene.2017.04.101
Net Zero Tracker, (2021). Hydrogen Production from Renewables - Renewable Energy Focus. Available at: http://www.renewableenergyfocus.com/view/3157/hydrogen-production-from-renewables/.
NetworkX Developers, (2014). NetworkX — NetworkX Documentation. Available at: https://networkx.org/.
Novikov, A. (2019). Creating Sea Routes from the Sea of AIS Data. Towards Data Sci. Available at: https://towardsdatascience.com/creating-sea-routes-from-the-sea-of-ais-data-30bc68d8530e.
Oberle, W. (2015). Monte Carlo Simulations: Number of Iterations and Accuracy. Adelphi: US Army Research Laboratory.
Office of Energy Efficiency and Renewable Energy, (2020). Hydrogen Production Processes. Washington, D.C.: US Department of Energy. Available at: https://www.energy.gov/eere/fuelcells/hydrogen-production-processes.
Osrm, (2020). Project OSRM. Available at: http://project-osrm.org/.
Parks, G., Boyd, R., Cornish, J., and Remick, R. (2014). Hydrogen Station Compression, Storage, and Dispensing Technical Status and Costs: Systems Integration. Golden: National Renewable Energy Laboratory Publication. Available at: http://www.osti.gov/scitech//servlets/purl/1130621/.
Preuster, P., Papp, C., and Wasserscheid, P. (2016). Liquid Organic Hydrogen Carriers (LOHCs): Toward a Hydrogen-free Hydrogen Economy. Acc. Chem. Res. 50, 74–85. doi:10.1021/acs.accounts.6b00474
Rashid, M. M., Mesfer, M. K. Al., Naseem, H., and Danish, M. (2015). Hydrogen Production by Water Electrolysis: A Review of Alkaline Water Electrolysis, PEM Water Electrolysis and High Temperature Water Electrolysis. Int. J. Eng. Adv. Technol., 2249–8958.
Rogelj, J. (2018). Mitigation Pathways Compatible with 1.5°C in the Context of Sustainable Development. Special Report. Geneva: Intergovernmental Panel on Climate Change. Available at: https://www.ipcc.ch/site/assets/uploads/sites/2/2019/02/SR15_Chapter2_Low_Res.pdf.
Scheelhaase, J., Maertens, S., and Grimme, W. (2019). Synthetic Fuels in Aviation - Current Barriers and Potential Political Measures. Transp. Res. Procedia 43, 21–30. doi:10.1016/j.trpro.2019.12.015
Shiva Kumar, S., and Himabindu, V. (2019). Hydrogen Production by PEM Water Electrolysis - A Review. Mater. Sci. Energy Technol. 2, 442–454. doi:10.1016/j.mset.2019.03.002
Spath, P. L., Mann, M. K., and Mann, M. K. (2001). Life Cycle Assessment of Hydrogen Production via Natural Gas Steam Reforming.
Steilen, M., and Jörissen, L. (2015). Electrochemical Energy Storage for Renewable Sources and Grid Balancing, 143–158. doi:10.1016/B978-0-444-62616-5.00010-3Hydrogen Conversion into Electricity and Thermal Energy by Fuel Cells
Taylor, A. (2021). Japan-Australia Partnership on Decarbonisation through Technology. Minist. Dep. Industry, Sci. Energy Resour. Available at: https://www.minister.industry.gov.au/ministers/taylor/media-releases/japan-australia-partnership-decarbonisation-through-technology.
Technical University of Denmark, (2021). Global Wind Atlas. Available at: https://globalwindatlas.info.
Ueckerdt, F., Bauer, C., Dirnaichner, A., Everall, J., Sacchi, R., and Luderer, G. (2021). Potential and Risks of Hydrogen-Based E-Fuels in Climate Change Mitigation. Nat. Clim. Chang. 11, 384–393. doi:10.1038/s41558-021-01032-7
Wang, Y., Li, W., Ma, L., Li, W., and Liu, X. (2020). Degradation of Solid Oxide Electrolysis Cells: Phenomena, Mechanisms, and Emerging Mitigation Strategies-A Review. J. Mater. Sci. Technol. 55, 35–55. doi:10.1016/j.jmst.2019.07.026
Wijayanta, A. T., Oda, T., Purnomo, C. W., Kashiwagi, T., and Aziz, M. (2019). Liquid Hydrogen, Methylcyclohexane, and Ammonia as Potential Hydrogen Storage: Comparison Review. Int. J. Hydrogen Energy 44, 15026–15044. doi:10.1016/j.ijhydene.2019.04.112
Wilberforce, T., El-Hassan, Z., Khatib, F. N., Al Makky, A., Baroutaji, A., Carton, J. G., et al. (2017). Developments of Electric Cars and Fuel Cell Hydrogen Electric Cars. Int. J. Hydrogen Energy 42, 25695–25734. doi:10.1016/j.ijhydene.2017.07.054
Woo, Y.-B., and Kim, B. S. (2019). A Genetic Algorithm-Based Matheuristic for Hydrogen Supply Chain Network Problem with Two Transportation Modes and Replenishment Cycles. Comput. Industrial Eng. 127, 981–997. doi:10.1016/j.cie.2018.11.027
Zang, G., Sun, P., Elgowainy, A. A., Bafana, A., and Wang, M. (2021). Performance and Cost Analysis of Liquid Fuel Production from H2 and CO2 Based on the Fischer-Tropsch Process. J. CO2 Util. 46, 101459. doi:10.1016/j.jcou.2021.101459
Zhao, Y., McDonell, V., and Samuelsen, S. (2019). Influence of Hydrogen Addition to Pipeline Natural Gas on the Combustion Performance of a Cooktop Burner. Int. J. Hydrogen Energy 44, 12239–12253. doi:10.1016/j.ijhydene.2019.03.100
Nomenclature
Abbreviations
AE Alkaline
CapEx Capital expenditures
CCS Carbon capture and storage
GHG Greenhouse gas
GPS Global positioning system
LCOE Levelized cost of electricity
LCOH Levelized cost of hydrogen
LH2 Liquid hydrogen
LOHC Liquid organic hydrogen carriers
OpEx Operational expenditures
PEM Proton-exchange membrane
PV Photovoltaic
SMR Steam methane reforming
SOE Solid oxide electrolysis
Keywords: H2 electrolysis, network, techno-economic assessment, green hydrogen, hydrogen, cost
Citation: Collis J and Schomäcker R (2022) Determining the Production and Transport Cost for H2 on a Global Scale. Front. Energy Res. 10:909298. doi: 10.3389/fenrg.2022.909298
Received: 31 March 2022; Accepted: 02 May 2022;
Published: 27 May 2022.
Edited by:
Rahul R. Bhosale, Qatar University, QatarReviewed by:
Yusuf Bicer, Hamad bin Khalifa University, QatarMuhammad Aziz, The University of Tokyo, Japan
Copyright © 2022 Collis and Schomäcker. This is an open-access article distributed under the terms of the Creative Commons Attribution License (CC BY). The use, distribution or reproduction in other forums is permitted, provided the original author(s) and the copyright owner(s) are credited and that the original publication in this journal is cited, in accordance with accepted academic practice. No use, distribution or reproduction is permitted which does not comply with these terms.
*Correspondence: Reinhard Schomäcker, c2Nob21hZWNrZXJAdHUtYmVybGluLmRl