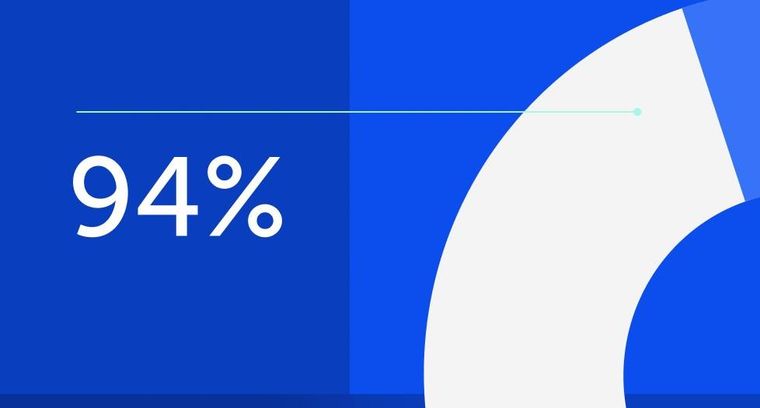
94% of researchers rate our articles as excellent or good
Learn more about the work of our research integrity team to safeguard the quality of each article we publish.
Find out more
ORIGINAL RESEARCH article
Front. Energy Res., 09 August 2022
Sec. Carbon Capture, Utilization and Storage
Volume 10 - 2022 | https://doi.org/10.3389/fenrg.2022.908658
Numerous carbon capture, utilization, and storage (CCUS) technologies are under development to reduce CO2 emissions. To evaluate the status of a CCUS technology under development and identify potential gaps for further advancement, we have established a new technology assessment framework and are developing a decision-making tool, the technology development matrix (TDM), starting with available carbon capture technology (CCT) data. TDM is a data inventory system and screening tool. As a screening tool, it can be used for resource allocation decisions in research, development, and deployment (RD&D) by academia, government, and industry. It shares data with techno-economic analysis (TEA) and life-cycle assessment (LCA) tools as an inventory system. By using available data, this TDM framework has been demonstrated on amine-based (monoethanolamine) absorption post-combustion CO2 capture, for pulverized coal (PC) power plant flue gas, as the best available technology (BAT) for comparison. Three groups of promising post-combustion CCTs under development are presented as Alternative Technology (Alt Tech) case studies, including membrane, solid adsorption, and calcium-based chemical looping. By using available data, preliminary analysis enabled technology benchmarking and highlighted knowledge, data, and technology gaps, all providing potential future RD&D focus.
Carbon capture, utilization, and storage (CCUS) technologies are critical for achieving net emissions reductions (Haszeldine et al., 2018) and realizing the Paris Agreement Commitments (Board et al., 2019). However, due to the diverse characteristics of several components in the CCUS value chain, systematic planning for large-scale deployment of these technologies becomes a challenging task. The availability of various options for CO2 emission sources (e.g., fossil fuel sources and industrial plants); capturing methods (i.e., pre-combustion, oxy-fuel combustion, chemical looping combustion, and post-combustion); utilization and storage technologies {including chemical synthesis [e.g., carbonates and cyanates]; energy products [e.g., methanol and hydrocarbons]; CO2 injection [e.g., Enhanced Oil Recovery (EOR)]; oil and gas reservoirs; unmineable coal beds; deep saline aquifers; and CO2 mineralization} can all be mentioned in this context. Furthermore, in integrated CCUS planning, to maximize economic profits while minimizing CO2 emissions, several scalability issues (such as matching system components’ time-based and spatial features, integration of CCUS into the energy grid, construction of pipeline infrastructure, coping with uncertainties in storage site’s geophysical characteristics, social recognition, and legal framework) that can be addressed at various technological scales should also be considered (Tapia et al., 2018). Therefore, for the success of CCUS projects, there is a substantial need for developing planning frameworks and decision-making tools to help and facilitate identifying optimal solutions. The following paragraphs will review existing CCUS decision-making tools in the literature and give an overview of both commercial CCUS technologies, specifically Carbon Capture Technologies (CCTs), as well as promising ones under development. CCT for pulverized coal (PC) fired power plant flue gas was chosen because it has a complete data set.
First, a bibliometric analysis of CCUS literature reveals that, due to a lack of maturity, CCUS research is not as extensive as that of other low-carbon technologies such as solar and wind (Tapia et al., 2018). A few articles discussed how optimization tools can aid in CCUS planning. Tian et al. (2016) conducted a survey of process models to demonstrate how each component of CCUS can be modeled, highlighting unresolved issues for future progression in this field. A more recent review by Tapia et al. (2018) provided an in-depth overview of the advances in the planning of CCUS solutions, with a particular emphasis on process systems engineering methodologies that help in decision-making while taking multiple scalability issues into account. According to their survey, most CCUS planning tools used in the literature can be classified as mathematical programming, pinch-based analysis, automated targeting, and other computational approaches, such as numerical simulation and P-graph. While mathematical programming techniques have the advantage of simultaneously considering multiple factors that must be incorporated into a single model, they face some difficulties in communicating optimal model solutions to decision-makers, particularly when these solutions contradict common expectations (Tapia et al., 2018). On the contrary, pinch-based analyses require little computational effort because they are only capable of considering limiting factors at the same time, making finding solutions for larger problems difficult, whereas quick insights can be easily obtained for simplified or stylized problems by this method.
Generally, a comprehensive CCUS decision-making framework should mainly consist of i) energy models (focusing on an energy balance of CCUS systems), ii) pipeline infrastructure design focusing on a CO2 distribution network), and iii) CO2 source–sink matching, which can be further broken down into several subcategories (Huang et al., 2013). Attempting to address all these issues simultaneously by means of a single mathematical model can lead to over-complexity and unnecessary computational effort (Biegler and Grossmann, 2004). As an alternative, a multi-step approach can be adopted, with the results of each phase used to customize and simplify the subsequent step of model formulation (Tapia et al., 2018). In such a case, more accurate and realistic CCUS system planning can be accomplished for large-scale implementation through flexible and customizable tools created by the integration of individual component models. These individual assessment tools that can be related to planning and decision-making for the CO2 capture, transport, utilization, and storage components of a CCUS system should be able to be integrated to produce a single model. With this background, the present study focuses on establishing a technology assessment framework and developing a decision-making tool using available data to help experts develop/select an appropriate CCT as an important component of assessing a CCUS system’s economic and environmental impacts.
Second, CCTs could be classified into two groups depending on where the carbon is captured: directly from the atmosphere or at the point of emission. The first group consists of direct air carbon capture, often referred to as DAC (Haszeldine et al., 2018). This technology is relatively new, with limited field data available in peer-reviewed literature. The second group consists of technologies enabling CO2 capture at the point of emission from fossil fuel-based electricity production and industrial processes. In this second group, four CO2 capture design approaches have been used for large-scale CO2 emitters, including pre-combustion, post-combustion, oxy-fuel, and chemical looping combustion (Leung et al., 2014). Point emission, post-combustion, and chemical looping CCTs (the focus of this study) are the most widely developed, have available data, and are ready to deploy through retrofitting existing emitters.
Depending on the pre-capture and the required post-capture conditions and parameters, different groups of CO2 capture approaches are available for post-combustion (Board et al., 2019), including cryogenic, absorption, membrane, adsorption, and chemical looping. Each of these CO2 capture approaches consists of multiple process steps with options for optimization and hybrid approaches combining different technologies [such as membrane/liquefaction (Anantharaman et al., 2014) or membranes with scrubbing (Scholes et al., 2013; Freeman et al., 2014)]. When considering both diversity in CO2 input characteristics (affected by the source of CO2 emissions, such as a cement plant) and CO2 output requirements (affected by the target CO2 application, including sequestration), these different options give rise to a multitude of pathways at different research, development, and deployment (RD&D) Technology Readiness Levels (TRLs) of lab, pilot, and demonstration. In such a complex task, assessment frameworks and decision-making tools can substantially help technology developers in academia, government, and industry to recognize knowledge, data, and technology gaps to make better resource allocation decisions in order to accelerate RD&D of new CCTs and improve their competitiveness. Moreover, identification of the optimal CCT can also provide valuable feedback throughout RD&D in optimizing detailed engineering, techno-economic analysis (TEA), and life-cycle assessment (LCA), all using a shared data inventory.
After reviewing planning frameworks and decision-making tools, a few, if any, provide quantitative assessments based on specific data for comparing among different CCTs. The five-step sequence depicted in Figure 1 summarizes the hierarchical process presented in this study to identify, assess, and optimize suitable CCTs among different options and find current knowledge, data, and technology gaps. Although early steps deal mostly with strategic and tactical decisions, later steps are more operational and less tactical. The preliminary strategic and tactical steps (stages 1 and 2, which are the focus of this study) enable comparing, ranking, and selecting among different technology candidates (mostly based on the input/output characteristic of CO2), as well as identifying current knowledge, data, and technology gaps. This is done with available data, including modeling and simulation, lab experiments, and preliminary TEA and LCA studies. Detailed engineering, cost (TEA), and life-cycle (LCA) assessments (stages 3 and 4) help design and optimize the selected CCUS technology before construction (stage 5).
FIGURE 1. Proposed five-step process to identify, assess, and optimize suitable CCTs among different options and find current technology gaps.
This study aims to establish a new technology assessment framework, develop a decision-making tool, namely, a Technology Development Matrix (TDM) (Malek and Nathwani, 2015), and apply it to CCT assessments. Excel is used to initiate TDM tool development; then, validation is done using available CCT data. As a research and development (R&D) decision-making tool and a data inventory system, TDM will help assess the current state of CCTs, benchmark them, and then help determine the next steps in ongoing TEA and LCA work (Zimmermann et al., 2018). Kearns et al. recently updated CCT-specific TRLs for various technologies, some specific to unique manufacturers (Kearns, 2021). Three different Alternative Technologies (Alt Techs) at different TRLs or phases of RD&D, including membrane, solid adsorption, and calcium looping, are investigated as case studies. Monoethanolamine (MEA) absorption was selected as the best available technology (BAT) because it is the only CCT currently demonstrated at a commercial stage. Hence, MEA is used in this work to demonstrate the TDM’s concept applied to CCTs and provide qualitative comparisons with CCT Alt Techs using radar plots. Details for the studied BAT and Alt Techs are summarized in Table 1. The TDM’s quantitative comparisons, including technology ranking and benchmarking the three Alt Techs against the BAT, are the subject of ongoing work. Here, the BAT and three other Alt Techs are applied to flue gas from an operating, commercial PC-fired power plant as the base case or baseline. Knowledge, data, and technology gaps, as well as next steps, are summarized.
In the following sections, the TDM framework’s structure and overall approach (§2.1), the required steps to establish a TDM tool (§2.2), and TDM linkage to TEA and LCA (§2.3) are discussed in more detail.
The TDM makes it possible to compare CCTs based on key criteria in three categories of performance, cost, and lifetime that can be measured through appropriate index metrics called key indicator parameters (KIPs). Performance, cost, and lifetime are broad categories of KIPs defined by technical operation, financial installation and operation, and years of operation, respectively. Three data sets of inputs for these KIPs are considered: the BAT, the user’s Alt Tech, and a Target needed to be achieved. The Alt Tech is a CCT under development that the TDM user would like to compare to both the BAT and Target. The Target is the set of KIPs that both the BAT and Alt Tech need to reach in order for R&D to achieve commercial deployment. Targets can be defined by a commercial market or application of the technology, as well as a goal defined by leading academic, industrial, or governmental organizations. The values of the KIPs for the BAT and Target can be affected by variables such as CO2 target application and emission source, as well as the scale of capture technology. Therefore, in the first steps, these variables should be specified. The TDM is populated and designed in a way that the corresponding KIP data values for the BAT and Target will be retrieved from the database after the selection of the mentioned variables. Then, in the next step, the user will enter the KIP data values for the Alt Tech under study. The user can also change the TDM suggested KIP data values for the Target to a default value defined by users such as governmental organizations or R&D consortiums. In the absence of a Target for a particular KIP, the BAT KIP can be used as a guide.
The next stage is making qualitative and/or quantitative relative comparisons among BAT, Target, and Alt Tech using these three sets of KIP data. In a qualitative comparison (the scope of this study), a radar chart is generated that visualizes how close (in terms of KIPs) the user’s technology (Alt Tech) is to the BAT and the Target. These results can be used to find R&D gaps and aid in decision-making for resource allocation. Regarding a quantitative technology ranking (the aim of our ongoing study), the ranking score of different user technologies will be calculated by analyzing and objectifying the relationships among the KIPs using a suitable method (e.g., combined scoring factor).
Figure 2 depicts the overall approach of the TDM, which is sorted by seven successive key blocks. This flow of information starts with selecting: i) the scale or size of the CCT, ii) the CO2 emission source, and iii) the target CO2 application. After selecting the above-mentioned variables, iv) the KIP data values for the BAT and Target will be retrieved by the TDM from its’ database, and then. v) the user will enter the corresponding KIP data values for the Alt Tech under study. As mentioned before, in this step, the user also has the option to start with the default peer-defined Target values. The next step is related to vi) data processing by the TDM tool through qualitative/quantitative analysis of the three sets of data. Finally, vii) the results (radar charts/ranking scores) are produced, which could further be used for R&D decision-making purposes, as well as providing feedback for more detailed TEA/LCA analyses.
FIGURE 2. Structure and overall approach of TDM tool. Note: items marked with * in columns 4, 6, and 7 are enhancements in the next generation of our TDM study.
Creating a TDM tool entails five steps, as depicted in Figure 3, which will be discussed further in this section. For their initial development, the TDM tool and database were created using Excel.
The first step is related to identifying appropriate metrics, allowing comparisons of CCTs based on three data categories of performance, cost, and lifetime, with all KIP data at the same TRL, and representing the entire CCT process being studied. These three data categories cover the main criteria required for technology commercialization. As far as specific KIPs in each of these three categories, we are following the approach developed by the University of Michigan’s Global CO2 Initiative (GCI) (Zimmermann et al., 2018) and using available CCT data. Data categories of performance, cost, and lifetime were identified in the context of TDM development for grid scale, Front of the Meter Electrical Energy Storage (Malek and Nathwani, 2015; Malek, 2019; Shi, 2020), and National Research Council (NRC) of Canada’s previous TDM work in Proton Exchange Membrane Fuel Cell (PEMFC) R&D. These three categories are further broken down into individual KIPs, measuring the CCT under study. The question in this step is, “What are the best representative KIPs for each category?” These parameters should cover plant energy efficiency before and after CO2 capture (e.g., lower heating value (LHV) efficiency, higher heating value (HHV) efficiency, CO2 capture penalty), CO2 capture efficiency and capacity, investment effort [e.g., capital expenditure (CapEx) including Total Capital Required (TCR)], processing effort [e.g., operational expenditure (OpEx)], cost of CO2 (captured and avoided), electricity costs (Levelized Cost of Electricity (LCOE) before and increase with CC), and plant technical and economic lifetimes. Table 2 shows an example of the main TDM data table with detailed KIPs for each category of performance, cost, and lifetime.
All masses are listed in metric tonnes of CO2 or tCO2. Because available data are published in different years, the largest cost component—Carbon Capture Compression and Liquefaction (CCCL) TCR—is inflation adjusted from the costing year indicated in the publication to the most recent complete calendar year, which is 2020 at the time of this publication. Currencies are US dollars ($) or US cents (c).
A sub-level of technology-specific KIPs can be added to make comparisons within one CCT. Future work could explore comparisons among one CCT and include technology-specific KIPs.
Data are critical for proper technology evaluation. A lack of standardized and systematic assessment methods prevents an accurate technology evaluation and makes benchmarking quite challenging. Newly detailed frameworks for systematic TEA and LCA of CO2 capture and CCUS technologies have been published (Rubin et al., 2013b; Zimmermann et al., 2018). The work was coordinated by the GCI and supported by Europe’s EIT Climate-KIC (Zimmermann et al., 2020a). This work did not assess the economic and environmental impact of different capture technologies.
A reliable and meaningful assessment of different pathways cannot be achieved without a similar (if not the same) project scope, system boundaries, KIP calculation methods, and technology maturity (Rubin et al., 2013b; Zimmermann et al., 2020b). Furthermore, a reasonable overlap between temporal and geographical conditions, affecting the corresponding assumptions and design parameters, is also required (Zimmermann et al., 2020b). Therefore, data from various studies must be finally reviewed and harmonized to ensure that the same units, calculation methods, cost year (i.e., accounting for inflation), CO2 compression pressure and purity, and plant scales are used (Kuramochi et al., 2012).
As seen in Figure 2, options for technology scale include laboratory and bench (Research: TRL of 1–3), pilot (Development: TRL of 4–6), and finally demo/commercial (Deployment: TRL of 7–9) scales (Buchner et al., 2018; Zimmermann et al., 2018). Laboratory and bench scales can be gram production of novel carbon capture (CC) materials and would serve to determine the disruptive potential of new absorbents, membranes, or adsorbents. For TRL 1–3, a simplification of the entire process can be used. Starting at TRL 4, all necessary equipment for that same process is included. This is the main CCT unit plus the Balance of Plant (BoP) or Balance of System (BoS). Pilot plants can be anywhere from <1% to 10% of the intended scale of application and would encompass all ancillary processes. The key technology from the laboratory and bench would be developed further to validate the concept and start scale-up preparation. At TRL 5–6, there would be well-established process diagrams, heat and energy balances, and process simulations. Finally, at TRL 7–9, demo/commercial can also vary widely, where conventional coal-fired power plants range from 200 to 600 MW, with the accompanying range of CO2 emissions. The options for CO2 sources can be found in §2 in the Supplementary Material.
In order to create the TDM’s database of KIP values for the BAT and Target, data can be collected from complete TEA and LCA studies (at the same TRL) in available literature and reports based on the experimental or operating plant and process simulation results. In this work, published CCT data were used to create an Excel database. For details, see §3 in the Supplementary Material.
Qualitative radar plot outputs compare the user’s Alt Tech, the BAT, and an aggregate of the Target application or goal. Radar plot outputs can be used by technology developers, such as academia, government, and industry (including small-to-medium-sized enterprises). Here, Excel was used to construct the initial data analysis model and radar plot.
For each KIP, the Alt Tech is first compared to the BAT, as shown in Eq. 1. Then, BAT and Alt Tech are compared to Target, as shown in Eqs 2, 3, respectively. Using Cost CO2 Captured ($/tonne) as an example KIP,
Different quantitative methods can be used for analyzing and objectifying the relationships among the KIPs (e.g., combined scoring factor) (ES-Select™, 2012). However, these quantitative assessments require more data than available at the time of this report and are thus the subject of ongoing work. Quantitative methods include the analytical hierarchy process, mathematical programming, data envelopment analysis, and fuzzy logic.
TEA and LCA tools are used to assess CCUS technologies based on technical, economic, and environmental performance indicators. TEA is often performed to assess the economic (e.g., cost) impact of technologies identified based on a set of technical criteria along with CAPEX and OPEX data. Often done separately, LCA is used to assess environmental impact where energy efficiency and greenhouse gas (GHG) emissions are the most widely reported environmental indicators for those identified technologies. The inputs and outputs from these two tools are key in building the proposed TDM components (KIPs) required to provide preliminary technology screening. Separately, the CCT under study can be modeled to extract mass and energy flows, equipment, and operating and maintenance requirements for a specific scale to provide the necessary input data for TEA/LCA tools. Moreover, data can also be obtained from experiments and operating plants. After the initial screening of the CCTs by the TDM, in the next step, the potential successful deployment of the down-selected CCT(s) could be assessed by detailed TEA and LCA. As shown in Figure 4, in this way, the TDM tool, along with TEA and LCA tools, integrates within an overall framework enabling preliminary screening and final technology benchmarking. For the initial Excel TDM tool, data are exchanged manually with TEA and LCA tools. However, NRC has also developed an LCA and life-cycle inventory-based webserver, the Economic and Environmental Evaluation of Carbon Conversion (NRC, 2022). Future versions of the TDM tool will be integrated into (thus be able to share data with) NRC’s webserver using a more automated process.
FIGURE 4. TDM linkage to TEA and LCA. Overall framework for preliminary screening and final CCT benchmarking.
It is worth mentioning that, to exchange data among TEA, LCA, and the corresponding TDM, they must be standardized as outlined in §2.2.2 (Zimmermann et al., 2018). In this way, data sharing could result in accurate and better decision-making as technology progresses in scale and TRL from lab or bench top to pilot, demonstration, and finally commercial deployment.
The current embodiment of the TDM does not account for CO2 credits/debits based on LCA or sales of CO2 or reagents, such as spent CaO in calcium looping. Tang and You performed both TEA and LCA for different calcium looping scenarios but did not add CO2 accounting from the LCA analysis to the metrics calculated for the CO2 capture process (Tang and You, 2018). Just as the CO2 avoided cost is usually higher than the CO2 capture cost because the former accounts for additional CO2 produced and changes in power output for the CCT, LCA would assign additional CO2 penalties to a CCT. These are all within the system boundary and can only be completely accounted for in the second and higher iterations of the process in Figure 4. However, other CO2 penalties could be accounted for in the first iteration. Examples could be CO2 emissions associated with MEA production and breakdown products or mining of CaO/CaCO3.
Three examples of alternative CC technologies, namely, membrane, solid adsorption, and calcium looping, all using flue gas from a baseline PC-fired power plant, are investigated in this section. Amine-based (MEA) absorption scrubbing retrofitted to a PC-fired power plant is considered the BAT (Ciferno, 2007) to assess the feasibility of Alt Techs. The three aforementioned promising CCTs are assessed using a qualitative radar plot in this study and compared to MEA.
The basic principles are provided in §3.1. Then, the selected MEA absorption as BAT is described in §3.2. An overview of the technological fundamentals of each post-combustion CCT followed by identification of the specific characteristics of the selected Alt Tech in that category is discussed in §3.3. Finally, the knowledge and data gaps in applying TDM to the selected Alt Techs are discussed in §3.4.
Generally, in a conventional coal-fired power plant, steam (which is generated through burning fossil fuel with air in a boiler) is transformed into electricity using a steam turbine. In the next steps, before emitting the flue gases into the atmosphere, NOx, particulate matter (PM), mercury, and SOx are removed. While in a retrofitted power plant with CCT, the flue gas, which mainly consists of N2, is emitted into the atmosphere after CO2 capture. Therefore, in a retrofitted power plant, more resources (requiring additional energy and materials) must be used to enable CO2 capture. This includes material treatment and circulation, heat exchangers, solvent/sorbent regeneration, and CO2 purification and compression (Ciferno, 2007).
As mentioned in §2.2.2, a meaningful and accurate comparison among different CCTs that can be used for retrofitting a CO2 emission source plant (e.g., a PC-fired power plant) cannot be achieved unless sufficient alignment in the overall system boundaries, major assumptions, and KIP measurement methods has been considered. A commonly used system boundary for assessing a retrofitted power plant includes the main constituents and auxiliaries from flue gas desulfurization (FGD) to CO2 conditioning (CO2 purification and compression). This means that, in addition to the CO2 capture unit, the required flue gas pre-treatment, in particular expansion of the FGD unit, if required, and the changes to the boilers are also considered. Furthermore, purity, temperature, and pressure of the final compressed CO2 product, CO2 capture rate, year of cost estimate, plant size (gross power output), plant capacity factor, type of fuel used in the power plant, and conversions between LHV and HHV are some examples of major assumptions that should be suitably aligned and harmonized for a proper technology assessment. CO2 storage and maintenance charges are recommended but are normally not applied in most studies (Rubin et al., 2013a).
Amine-based absorption technology is the most mature and commercially available process to capture and separate CO2 from flue gas; as such, it is often used as a benchmark (Alstom UK, 2011; Anantharaman et al., 2016). MEA is the most widely deployed amine-based absorption technology. Although MEA is presently the most cost-effective CCT, it has drawbacks. MEA incurs a considerable energy penalty during solvent regeneration, has a narrow operating temperature range, and produces substantial waste during cycling, and the spent materials are difficult to dispose of (US DOE/NETL, 2015a). Currently, research is focusing on developing new amines and mixtures to improve energy efficiency and thus cost and reduce the overall carbon footprint.
Other potential scrubbers exist and are used on large scales. Selexol (dimethyl ethers of polyethylene glycol), Purisol (n-methyl-2-pyrrolidone), and Rectisol (methanol) are viable alternatives. These are used to remove CO2 from natural gas wellheads or where H2S is involved because H2S can be removed from CO2. Physical solvents, Selexol and Purisol, require high pressure and high CO2 concentrations to achieve reasonable CO2 loading. As a result, they are generally applied to CO2 and H2S removal in integrated gas combined cycle (IGCC) power plants (Chen, 2022). Rectisol is ideal for processes where gases are already at the right conditions for methanol to solubilize/absorb H2S and CO2 (Hochgesand, 1970). Methanol spontaneously releases CO2 when pressure is released and avoids the parasitic power losses associated with MEA. These scrubbers are better suited to IGCC power plants and natural gas well heads than PC power plants.
The NETL study (Ciferno, 2007) of the Conesville #5 unit in Ohio is a rare example of studies reported in great detail. The Conesville #5 unit, shown in Figure 5, is a 460 MWe gross PC power plant producing 9,440 tCO2/day. The study considers pre-existing flue gas treatment and its expansion to meet MEA requirements, physical restrictions at the site, changes to boilers, waste disposal, and other factors. The TDM parameters (KIPs) relevant for this process as the BAT are shown in Table 4.
FIGURE 5. Process flow diagram for a pulverized coal power plant retrofitted with MEA absorption technology for CO2 capture. Adapted from Ciferno (2007). Note: the new equipment is shown in green; ESP, Electro-Static Precipitator; SCAH, Steam Coil Air Heater; FGD, Flue Gas Desulfurization; and MEA, Monoethanolamine.
MEA is a relatively mature CCT with numerous large-scale demonstration plants. However, limited field data on alternative CCTs are available. Often, these Alt Techs are at lower TRLs, and any available data come from lab and occasionally pilot scales, combined with data from process simulations and TEA studies. As a result, there are limited Alt Tech data from operational units that include the entire process and use the same KIPs across all CCTs. Three promising CCT Alt Techs are presented below, for which there are enough data from lab and pilot scales combined with simulations and TEA studies. In the case where KIPs were not the same, the authors recalculated KIP values from the data.
Although not yet commercialized but operated as large-scale pilots, 20 tCO2/day and 200 tCO2/day planned, membrane technologies are a relatively mature technology combining attributes related to scalability and potential future improvements (Merkel, 2018). The Polaris membrane developed by MTR is undoubtedly the most advanced system for CO2 capture (Merkel et al., 2010; Baker et al., 2018). Membrane development consists of several stage gates, including the following:
• Development of a material for the actual CO2/N2 separation,
• Preparation of this material in a form suitable for large-scale production while achieving high throughput and defect-free production,
• Implementation of the membrane in an appropriate pressure vessel (module) and addressing the mass transfer of CO2 and N2 in the membrane module (Merkel et al., 2009),
• Optimization of the process flow diagram using these membranes (Wei et al., 2015),
• Demonstration of long-term flux and separation performance (Kniep et al., 2018).
The Polaris™ membrane is a multilayer thin-film composite (TFC) prepared in flat sheets and enclosed in spiral-wound modules to separate feed and CO2-rich product streams. The separation is affected at the top layer, which has a low permeability, but the high flux is achieved via the ultrathin thickness of this layer, under 100 nm. The MTR design is like the more familiar spiral wound modules used for reverse osmosis desalination of seawater but with critical modifications to the permeate side to avoid CO2 build-up and allow for a “sweep gas,” which dramatically improves the overall CC performance of Merkel et al. (2010). MTRs approach to improving its technology is toward developing higher throughput rather than selectivity. The first generation Polaris™ membrane (Gen-1) achieved 1,000 gas permeation units (GPU) and a CO2/N2 selectivity of 50. Gen-2 membranes with a permeance of 2,000 GPU have been fabricated in prototype modules. Gen-3 membranes have achieved 3,000 GPU at the lab scale, with all three generations maintaining the initial selectivity (Kniep et al., 2018). Further improvements to the module design have reduced pressure drops and are projected to reduce power consumption by 15 MWe on a full-scale plant (Merkel, 2018).
Other approaches to ultra-high permeance membranes are achieved by using materials with higher permeability and thicker separation layers (Shao et al., 2013). Recent developments have seen further dramatic improvements, where CO2/N2 selectivity increases up to 242, with 823 GPU achieved (Wang et al., 2020). Further increases in permeance to 3,000 GPU, with an excellent selectivity of 78, have also been obtained (Qiao et al., 2019). Both of the latter membranes are still at the lab scale but have been prepared in large areas (100 cm2) for this stage of development, using polymers with reduced defects. While still at an early development stage, improvement in membrane quality is expected to be integrated into higher TRL CCT systems.
Other dramatic improvements in membrane technology were reported by McNeil et al. (2020). In this novel design, silver-based dual-phase ceramic-based membranes are used, giving rise to the selectivity of 1,000 and permeability of >200,000 Barrer. This class of membranes has great potential, as explained Anantharaman et al. (2014) in process simulations with IGCC and coal gasification-based power generation. However, these novel membranes are probably less suited to conventional coal-fired plants. The dual-phase membranes require >600°C operating temperatures and, like Rectisol processes, can take advantage of process conditions to permeate CO2 and retain combustible gases at high pressure. Cost and scale up to areas required for CCUS are to be overcome, and the TRL for these membranes must be considered low, 1–2, may not advance quickly, and likely never reach the costs of polymeric TFC membranes (Merkel et al., 2010). However, they may be the only CCT option for IGCC.
Hollow fiber membranes are usually the design of choice because the membrane area/volume is typically 10 times that of spiral wound modules. This benefit of hollow fiber packing density was negated when membranes for CO2/N2 separations saw 10–100-time increase in flux with the Polaris™ membrane. Hollow fiber modules with such high GPU ratings have yet to be produced from any polymer. Furthermore, concentration polarization (poor mixing on the feed side of hollow fibers on the shell side) is exacerbated with high flux membranes, and 1,000 GPU membranes (now 2,000 and potentially 3,000 GPU membranes) with a CO2/N2 selectivity of 50 would not see the theoretical performance in practice.
The MTR studies indicated that improved economics lie in the direction of increased flux after a given selectivity is obtained. This finding is specific to their approach, where low feed pressure and partial vacuum on the permeate side of the membrane are used as driving forces for CO2 permeation. The study by Anantharaman et al. (2014) benefited from higher selectivity, but only at the very high operating pressures in that particular application, those pressures in a conventional PC post-combustion capture scenario would consume too much power.
This initial MTR study for 90% capture and liquefaction of CO2 from a 600 MW coal-fired plant (producing 11,040 tCO2/day) was later updated for a cost-optimized case as 80% overall capture (Baker et al., 2018) and used in this work. At the time of publication, Dillon reported on a cost estimate for retrofitting MTR’s second-generation Polaris™ membrane based on a DOE field study of an existing coal-fired power plant (Dillon, 2021). The basic block diagram of the MTR process is shown in Figure 6. A key process modification is using a sweep gas on the membrane stage before the stack, which returns a portion of the CO2 to the boiler. This increases the overall flux and CO2 concentration in permeates of the other membrane stages, thereby reducing CAPEX and OPEX. Similar approaches are used with natural gas turbine power plants, where the exhaust gas recirculation is used to increase the exiting CO2 concentration for all CCTs, not only membranes.
FIGURE 6. A simplified process flow diagram illustrating the impact of a selective recycle membrane on a two-stage membrane system. The recycle step raises the feed gas concentration while simultaneously lowering the discharge CO2 concentration to 3.7% (80% CO2 capture). Power consumption is reduced by 30 kWe/tonne of CO2 captured. The CO2 condensation column operates at 30 bar and −25°C. Adapted from Baker et al. (2018).
CO2 capture using solid adsorbents is another method in the category of post-combustion CCTs, which provides several advantages over the traditional commonly used liquid scrubbing (such as aqueous MEA absorbents). Compared to an aqueous solvent-based process, considerable reduction in the regeneration energy penalty (due to the solid adsorbents’ lower specific heat capacity and decreased water evaporation), a wider range of operating temperatures (from ambient temperatures to 700°C), less waste production during cycling, and easier disposal of spent materials, are advantages of solid adsorbent-based technology (US DOE/NETL, 2015a). However, for large-scale CO2 capture, in many or most cases, the adsorbent-based technology is still not as cost-effective as the solvent or membrane alternatives. The high cost of solid adsorbents [e.g., zeolites and Metal–Organic Frameworks (MOFs)] and adsorbent attrition are examples of the main challenges associated with this technology (US DOE/NETL, 2015a).
Solid adsorbents for CO2 capture are typically categorized based on the operating temperature regimes for adsorption and desorption (regeneration). Indeed, they fall into three categories of i) low temperature (<200°C, such as supported solid amine-based, zeolite-based, MOF-based, carbon-based, and alkali metal carbonate-based); ii) intermediate temperature [200°C–400°C, such as layered double hydroxide- (LDH-) based]; and high temperature (>400°C, such as CaO-based and alkali ceramic-based) solid adsorbents (US DOE/NETL, 2015a).
The performance of solid adsorbents can be evaluated based on different attributes such as their equilibrium CO2 adsorption capacity, adsorption/desorption kinetics, CO2 selectivity, multicycle durability (affected by their tendency for moisture uptake, tolerance to impurities, and mechanical strength), and regeneration (Samanta et al., 2012; Krutka et al., 2013).
Several research groups have investigated this subject in recent years, with many of them focusing on new material development (Samanta et al., 2012). However, to commercially use solid adsorbents for CO2 capture, research on the development of the effective process, including gas-solid contactors (e.g., fixed-bed, fluidized-bed, and moving-bed), adsorbent regeneration process, and the overall process integration (primarily thermal integration with the emission source plant) is also required. In order to meet the technical and economic constraints, it is expected that researchers’ focus will be more on investigating the use of innovative gas-solid contactor configurations (e.g., structured bed, fast-fluidized-bed, circulating bed, and transport-bed) (Samanta et al., 2012), adsorbent performance under actual operating conditions, reducing solid adsorbents’ cost and operability issues (such as adsorbent degradation and associated emissions), and performing more precise and reliable process design and economics analysis (US DOE/NETL, 2015a; Pardakhti et al., 2019).
NRG Energy, Inc. (NRG), in collaboration with Svante (formerly Inventys), using Svante’s VeloxoTherm™ CCT (Stevenson and Armpriester, 2016), evaluated their solid adsorbent at a scale of 10 MWe. Their target was 90% CO2 capture efficiency with a purity greater than 95% (Target defined by a solicitation (DE-FOA-0001190) from the U.S. DOE) (US DOE/NETL, 2015b). The VeloxoTherm™ uses a rotary adsorption machine, an evolution of well-developed, large-scale, rotary air preheaters. This technology relies on three key innovations: i) an intensified rapid cycle temperature swing adsorption (TSA) process, ii) a patented architecture of structured solid adsorbents, and iii) a rotary embodiment (Rezaei and Webley, 2009; Stevenson and Armpriester, 2016). Important advantages compared to traditional TSA processes are a low-pressure drop, immobilized adsorbent (eliminating mechanical degradation), high heat and mass transfer, and high heat retention. The NRG study identified shortfalls in the performance of the structured bed solid adsorbents, leading to reduced capacity and increased steam consumption. Recently, Hovington et al. reported the development of a zinc triazolate MOF adsorbent at large production volumes (Hovington et al., 2021) and demonstrated the technology on cement flue gas (Lin et al., 2021). The new adsorbent’s properties surpass those of the ideal material in the NRG study, but the TEA for PC power plants has not yet been revised.
The study by ADA (Sjostrom et al., 2016), which is used as the Alt Tech for solid adsorption in the current study, evaluated benzylamine immobilized on pellets. The solid adsorbents were benchmarked against MEA, and two costing methods were presented, based on DOE guidelines and ADA best experience, where the latter TCR was 32% higher than DOE guidelines. The process flow diagram is shown in Figure 7. A preliminary plant design and TEA were based on lab-scale performance for a power plant with a net electrical output of 550 MW before and after CC. The adsorbent capacity for the initial TEA was 15 gCO2/100 gadsorbent and a contact time of 10–15 min, requiring four parallel adsorption/desorption trains. Pilot studies (Sjostrom et al., 2016) at a scale of 1 MWe were performed and showed reduced CO2 capture performance with a reduced adsorbent capacity of 5.4 gCO2/100 gadsorbent and an increased contact time of up to 65 min. The TEA study was repeated based on the downrated pilot plant performance: the number of parallel adsorption/desorption trains increased from 4 to 44. The TDM in our work uses costing data based on the ideal adsorbent performance and the DOE guidelines. Both ADA and Svante studies had promising TEA results based on lab-scale data, but performance decreased at the pilot scale. Kearns et al. ranked the new solid adsorbent TRL from Svante at 5–6 in a CO2 from capture scenario from cement production. As a result, we ranked the TRL for ADA’s Solid adsorption at 4. However, future improvements in ADA’s performance at the pilot scale are possible; if so, the TRL would increase.
FIGURE 7. Process flow diagram of the ADAsorb solid adsorption carbon capture process. Adapted from Sjostrom et al. (2016).
CaO/CaCO3 (or calcium) looping technology emerged over a decade ago as one of the promising technology pathways to achieve low-cost post-combustion CO2 capture in the near future. In this process, the reversible reaction of calcium between its carbonate and oxide forms allows CO2 separation from flue gases coming from either power plants or any other industrial CO2 emission sources as follows:
Shimizu et al. were the first to propose the use of a high-temperature CaO sorbent for post-combustion CO2 capture, and it has since become widely used in calcium looping process research (Shimizu et al., 1999). A typical process flow diagram abstracted from the work of several active groups in this field is shown in Figure 8 (Zhao et al., 2013). Flue gas containing a low-to-medium concentration of CO2 is fed to the circulating fluidized bed (CFB) carbonator, containing refreshed solid CaO sorbents, where the exothermic carbonation reaction (Eq. 4) happens at around 650°C. The CaCO3 formed is then passed to a CFB calciner where the endothermic calcination reaction (Eq. 5) occurs around 850°C–950°C, resulting in regeneration of CaO (which is passed back to the carbonator) and the formation of an almost pure stream of CO2. The CO2-depleted flue gas is emitted into the atmosphere, whereas the CO2-rich stream is released for further purification and compression before being utilized or stored. Due to temperature differences between the carbonation and calcination reactions (650°C vs. 850°C–950°C), heat from exothermic carbonation cannot be directly used to provide the heat needed for endothermic calcination in the calciner. As a result, fuel (powdered coal) can directly be burned with oxygen provided by an air separation unit (ASU) in the calciner (as a fluidized-bed oxy-fuel combustor) to provide the necessary heat for calcination.
FIGURE 8. Schematic presentation of the calcium looping process for post-combustion CO2 capture. Adapted from Zhao et al. (2013). Note: FGD, Flue Gas Desulphurization; and ASU, Air Separation Unit. Possibilities for heat recovery include heat that can be released from i) exothermic carbonation reaction (Q1), which is higher than what is required to maintain the CFB carbonator’s temperature; ii) and iii) hot CO2-depleted flue gas (Q2) and hot CaO/CaCO3 streams (Q3) leaving carbonator cyclone at a temperature >600°C; and finally iv) very hot CO2 rich gas (>800°C) leaving oxy-fuel CFB calciner’s cyclone (Q4). Q2 and Q4 can generate steam cycles for extra electricity output.
Compared to the market-ready MEA absorption process, lower capital cost, energy penalty, CO2 capture cost, and less complex integration with the CO2 emission source plant can be achieved by the calcium looping process (Cormos and Simon, 2013; Zhao et al., 2013). This happens due to i) the high availability of low-cost, non-hazardous, limestone-derived CaO sorbent from natural sources (Zhao et al., 2013), ii) no need for a separate FGD unit (as CaO itself can act as the desulphurization agent) (Zhao et al., 2013), and iii) the potential of spent CaO to be used elsewhere (mostly in the cement industry) (Dean et al., 2011a; Dean et al., 2011b). As a result, this technology emerged as a near-term alternative to the current MEA-based post-combustion CCT (Zhao et al., 2013).
The main concerns about the calcium looping process are the rapid decay in the CO2 carrying capacity of CaO-based sorbents over multiple calcination-carbonation cycles and an efficient process design with optimal heat integration. Regarding sorbent deactivation, the decrease in the reactivity of CaO can be attributed to the i) sintering of particles during high-temperature carbonation—calcination processes, ii) particle attrition in fluidized beds, and iii) poisoning by sulfation/sulfidation reactions with SOx, resulting in an outer sulfated layer forming on the particles, which prevents CO2 uptake (Sun et al., 2007; Manovic and Anthony, 2009; Wang et al., 2010). However, it has been reported that the presence of steam under real operating conditions significantly increases CaO sorbent activity, making CaO activity loss less of a concern (Manovic and Anthony, 2010; Donat et al., 2012). Regarding the necessity of heat integration, it should be mentioned that providing the required heat for calcination through direct fuel burning under oxy-fuel conditions (by oxygen rather than air) prevents CO2 dilution with N2 and facilitates its purification. However, this coincides with the large energy consumption needed for the ASU, which results in a ∼6% energy penalty (comparable with ∼5% for CO2 compression) (Abanades et al., 2007). Fortunately, excess heat recovery and integration into new steam cycles are possible through the process configuration presented in Figure 8, which can keep the energy penalty at an economically satisfactory level (Zhao et al., 2013). It has been reported that an 82% reduction in energy penalty and a 50% decrease in the cost of electricity increase of calcium looping can be achieved by integrating the potential heat that can be recovered from a calcium looping process used for post-combustion CO2 capture from a power plant (Yang et al., 2010).
An alternative calcium looping process has been suggested (Junk et al., 2016) that could eliminate the need for an ASU; the combustion of additional fuel in a second combustor provides indirect heat for the calciner. The additional flue gas/CO2 is combined with that of the main power plant. The cost of the heat transfer equipment is offset by the elimination of the ASU. The indirect heating methodology has been tested at a 300 kWth scale with plans for 20 MWth pilot plant (Hilz et al., 2019; Ströhle et al., 2021).
In this study, Tang et al.’s third case (Tang and You, 2018) is considered the representative Alt Tech for calcium looping technology.
Data entry for each CCT pathway is a key step in TDM development and is summarized in §3.4.1. Next, the key characteristics of each pathway are obtained, organized, and entered (§3.4.2). Finally, a radar plot comparing each Alt Tech to the BAT is generated (§3.4.3). The TDM tool and database were initially developed using Excel (§2.2, §2.3).
User data entry is in two areas, as shown in Figure 2. In the first steps (the first three columns on the left side of Figure 2), the user should select among different available options from the drop-down menus for the project scale, CO2 source, and CO2 target application, whereupon the TDM tool retrieves the corresponding KIP data values for the BAT and Target. The second data entry step is related to the KIP data values for the user’s CCT Alt Tech to be studied (column 5 of Figure 2) and the year of the costing. Once there is enough data for all KIPs in the tables, relative comparisons can be made for the Alt Tech or user’s CO2 capture under study to the BAT and Target. Output results will be generated for further analysis to see where R&D resources could be reallocated. Samples of the qualitative outputs are presented in §3.4. As per §2.2.1, an inflation index is applied to CCCL TCR in generating the radar plots for the BAT and Alt Techs.
Key characteristics of the BAT and three Alt Techs described in the previous paragraphs are summarized in Table 3. This comparison highlights the importance of ongoing development to address current technology gaps. For each Alt Tech, a TRL range has been identified because it is quite difficult to precisely assign specific TRLs for non-commercial technologies. There are several criteria when identifying TRL (Buchner et al., 2018; Kearns, 2021).
TABLE 3. Summary of BAT and three post-combustion CCTs as user’s Alt Techs, TRL ranges, and pros and cons for those CCTs.
These attributes need to be translated into measurable KIPs so they can be qualitatively and quantitatively analyzed by the TDM to support RD&D resource allocation decisions. The KIPs for the BAT and three Alt Techs are shown in Table 4 and represent a subset of the KIPs extracted from available studies on these technologies. KIP values that had to be recalculated from TEA data in the publications referenced are indicated by underlined text. In addition to §2.2.2, this was to align KIPs and their units of measurement across CCTs studied in the TDM.
TABLE 4. TDM KIPs for the selected MEA scrubbing (BAT) and three post-combustion CCTs as user’s Alt Techs of this work.
By combining data from lab and pilot scales with those from simulations and TEA studies and then recalculating any missing KIP values from existing data, there is sufficient data in the literature for the BAT (Ciferno, 2007) and three Alt Techs (Sjostrom et al., 2016; Baker et al., 2018; Tang and You, 2018). However, knowledge and data gaps for the end application Target prevent a complete comparison of the Alt Techs against the BAT and Target. In terms of knowledge gaps, a few, if any, KIPs have been defined for performance, cost, or lifetime and then prioritized for a given application or desired market. In terms of data gaps, only a handful of Target values were found for those KIPs. One comparison can be made for the DOE target of no more than a 20% LCOE Increase with CC (US DOE/NETL, 2015b). In descending order and relative to the 20% LCOE Increase with the CC target: the BAT is 108% or a little more than five times; solid adsorption is 99% or a little less than five times; membrane is 78% or a little less than four times; and calcium looping is 42% or about double. Although the relative % LCOE Increase with CC is the least for calcium looping, the BAT and three Alt Techs all exceed the DOE target (US DOE/NETL, 2015b). The other Target, 90% CO2 Recovery Efficiency, was only achieved for the BAT and solid adsorption. For membrane and calcium looping, their CCT performed best at CO2 Recovery Efficiencies, less than 90%. A detailed explanation is given later in this section.
Any KIPs can be selected from Table 4, with at least three needed to generate a Radar Plot. Among the three equations shown in §2.2.5, Eq. 1 has been used. The BAT is normalized to serve as a comparison point in the radar plot. Table 5 shows relative comparisons of each Alt Tech to the BAT using Eq. 1. In Table 5, six KIPs are chosen: CCUS Energy Efficiency, Net Energy/tCO2 Emitted after CC, LCOE Increase with CC, CO2 Avoidance/Mitigation Cost, CCCL TCR, and Tech Replacement Costs.
TABLE 5. Relative comparisons of three Alt Techs of this study to BAT using Eq. 1 for the selected KIPs from Table 4.
Comparisons can now be made among the KIPs for BAT, and three Alt Techs from Table 4 are shown in Table 5 and the radar plot in Figure 9.
FIGURE 9. Qualitative radar plot showing carbon capture performance using six KIPs for the BAT and Alt Techs. BAT is MEA absorption, Alt Tech 1 is membrane, Alt Tech 2 is solid adsorption, and Alt Tech 3 is calcium looping. BAT/BAT
Alt Tech 1/BAT
Alt Tech 2/BAT
Alt Tech 3/BAT
Before progressing further in comparing the three Alt Techs based on Table 5 and Figure 9, it is worth noting that the difference in TRLs could affect the relative quality of data inputs. Indeed, although the membrane technology is tested at a pre-commercial stage, this is not the case with calcium looping, which is often based on simulation and pilot scale data. In Figure 9, the KIP CCCL TCR is similar to all the CCTs studied. However, the other five KIPs showed differences in CCT performance and cost relative to the BAT. For CC Energy Efficiency, all Alt Techs were lower or more efficient than MEA, and membrane technology used 89% of the energy per tonne of CO2 captured. Calcium looping used 75% compared to MEA, and solid adsorption (based on benzyl amide’s ideal performance) consumed only 41% of the energy of MEA. All the Alt Techs had similar net energy production per tonne of CO2 emitted before CC, from approximately 1,100–1,220 kWhenet/tCO2 emitted. For Net Energy/tCO2 Emitted after CC, solid adsorption is best, generating the most saleable power for a given amount of CO2 emitted, approximately 20% more than MEA. Membrane technology and calcium looping are similar at 60% of MEAs performance. Note that both MEA and solid adsorption use the DOE Target of 90% CO2 Recovery Efficiency, whereas membrane and calcium looping do not. The “poor” performance of both membrane technology and calcium looping with this KIP is directly linked to the lower CO2 capture rates of 80% and 83%, respectively. This halves the numeric value of this KIP because the energy production is normalized by the CO2 emitted, not captured, or 20% rather than 10% for MEA and solid adsorption. However, membrane technology’s CC Energy Efficiency, the first KIP, was minimized at 80% capture, not 90%. Junk et al. and Abanades et al. used CO2 capture rates of 80% and 86%, respectively (Abanades et al., 2007; Junk et al., 2016). Therefore, the calcium looping penalty on this KIP is not unique to Tang and You’s study (Tang and You, 2018).
Regarding LCOE Increase with CC, calcium looping was the lowest at 32% of BAT, then membrane technology with a 57% increase, and finally solid adsorption at 103%. When normalized by the % LCOE Increase for MEA as the BAT (108%), the relative performance between the Alt Techs is, of course, unchanged and is similar because the % LCOE Increase of the BAT was close to 100%.
The same trend can be seen for CO2 Avoidance or Mitigation Cost. Calcium looping is dramatically lower at 34% than the BAT. The membrane is also lower than the BAT at 72% but more than double that for calcium looping. Solid adsorption is slightly more than the BAT at 107%. The similarity between the LCOE Increase with CC and CO2 Avoidance or Mitigation Cost is not surprising because the LCOE is a component in the equation to calculate CO2 Avoidance or Mitigation Cost.
CCCL TCR based on the CC rate of 1 tCO2/day was the lowest for calcium looping at 60%, followed by solid adsorption at 69% of the BAT, respectively. The membrane was the highest at 79% of the BAT. The BAT and solid adsorption studies listed the Bare Erected Cost (BEC), Total Installed Cost (TIC), and, finally, the highest TCR. The membrane and calcium looping studies listed total capital or TIC, and so it is assumed for the purposes of comparisons in this work that they also used the same cost basis because these costs were used to determine their capture or avoided CO2 costs. However, if the membrane and calcium studies did not include contingencies and overhead costs, the TCR for these may be underestimated.
The greatest relative difference is for Tech Replacement Costs, where calcium looping is more than double, or the most expensive, relative to MEA, whereas the other two Alt Techs have lower costs relative to MEA. The membrane has high initial costs, but its technology lifetime was specified at 3 years by MTR (Baker et al., 2018). The solid sorbent cost is very high, $US 10,100/tonne, compared to limestone, $US 25/tonne, but the makeup of limestone per tonne of CO2 is much higher due to CaO deactivation.
The next step is to confirm what is causing the relative differences seen in the radar plot. Particularly for new research fields and low TRLs, one must ask if TEA source data, calculations, equations, and assumptions are valid and equal. It follows that TDM qualitative outputs are another tool to check for knowledge and data gaps, or how the TEA was done and how it compares to those for similar technologies. This enables standardization or consensus among CCUS researchers and serves as a way to make more accurate, transparent comparisons of knowledge, data, and technology gaps and hence another way to help accelerate CCUS RD&D. Future work could explore validating TEA source data used in Figure 9 to see if and how differences in TEA assumptions among CCT affect results used in the TDM.
For example, potential variations in the TCR (or overnight costs, investment costs, etc.) were discussed above. However, it is not always clear if all contingencies are included or what factors are used for those contingencies. The BAT contained detailed costs for, using that studies terminology, major Capital Costs, BEC, and Total Investment Cost (not TIC). The BEC was 212%, and the Total Investment Cost was 370% of the major Capital Costs, based on rates for that study. The process and project contingencies were 25% and 18% of the BEC in that study. Different values may be used in different TEAs and for different technologies, and Total Investment Cost and TCR are interchangeably used in different studies.
Similar questions regarding comparisons with different assumptions were raised when the KIPs for CO2 Avoidance or Mitigation Cost and LCOE Increase with CC were calculated. The TCR will impact the LCOE in terms of not only the capital value but also the Fixed Charge Factor (FCF). The FCF is a multiplier for the TCR, accounting for the levelization or financing period and the interest rate assumed.
The impact of these different financial assumptions is summarized in Table 6. The Tang calcium looping TEA used a levelization period of 30 years and an interest rate of 7.0%, or an FCF of 0.0806 (Tang and You, 2018). The BAT baseline reported an FCF of 0.1750, corresponding to 15 years and 15.5% interest (Ciferno, 2007). The BAT also applied levelization charge factors of 1.157 to their Variable Operation and Maintenance (VOM) and Fixed Operation and Maintenance (FOM). When those BAT financing assumptions are used for the calcium looping case, the CO2 Avoidance or Mitigation Cost increased from 29.8 to 72.2 $/tCO2. Changes to other KIPs are in column “BAT.” In order to compare the effect of different financial assumptions on CO2 Avoidance or Mitigation Costs in Table 6, values were calculated using Tang et al.’s LCOE equations and CO2 produced. Therefore, the CO2 Avoidance or Mitigation Cost in Table 6 is different from that in Table 4. The calculated LCOE values, however, matched the reported values to within 1 c/kWh.
TABLE 6. Comparison of calcium looping KIPs as a function of various levelization periods, interest rates and VOM, FOM charge factors.
The % LCOE Increase with CC did not change dramatically because the BAT financial parameters were also applied to the new reference power plant without CC. Furthermore, the impact of the VOM and FOM Charge Factor is greater than that of plant financing. Assuming the BAT FCF and Tang’s value of 1 for VOM and FOM Charge Factor, the CO2 Avoidance Cost increased from 29.8 to 36.7 $/tCO2, column “BAT, Tang.”
In the previous paragraphs, we used several KIPs to compare different CCTs and generated Tables 4–6 for this. We need an additional step to capture and integrate all the outputs to facilitate decision-making. The whole TDM process of determining KIPs, units of measurement, measurement standards, tabulating KIP data, and then making qualitative comparisons in radar plots can be useful for RD&D at each TRL stage. It can be a facile process for users to check data from TEA and or measured data to uncover knowledge gaps at lower TRLs (1–3) through measurement and data gaps at mid-TRLs (4–6) and, finally, technology gaps at higher TRLs (7–9). Thus, at each stage of RD&D, researchers can use the TDM to make valid comparisons, support decision-making, and accelerate commercial deployment of the most promising technologies for a given end application.
The current TDM assumes a relative weighting of 1.0 for each KIP. Future TDM versions could include adding a range of KIP weightings to correspond to prioritizing KIPs for a given CCT application. Some decision-making tools include KIP weightings of 0.0–2.0 in increments of 0.5, and something similar could be done for the CCT TDM (ES-Select™, 2012). Another approach is to 1) identify the minimal requirement for each KIP and 2) use cost per unit CO2 capture (additional cost of per unit electricity production) as the final ranking. A recent IEA report showed this approach (Baylin-Stern and Berghout, 2021).
Of interest, the US DOE has updated its CCUS target using a new indicator based on the cost of per unit CO2 mitigation (DOE/EE-2362, 2021). Often referred to as Levelized Cost of Carbon Abatement (LCCA) (Friedmann et al., 2020), this provides a good indicator to compare different technologies, including CCUS. This indicator is more suitable for assessing policy incentives for CO2 mitigation. However, this indicator could not be used in this study as CO2 capture needs to be combined with CO2 storage and utilization stages. This work is ongoing at NRC to integrate utilization and storage technology options in the proposed TDM. As shown in Figure 2, the proposed TDM framework is designed to compare different CCUS pathways.
All four CCTs discussed in this study have progressed past the lab scale (TRL 1–3), so their fundamental technologies are essentially unchanged from the pilot scale (TRL 4–6) onward. Thus, there are limited opportunities for disruptive or step-change improvements. However, commercial deployment and resulting economies of scale could still lead to per-unit cost reductions while decreasing GHG emissions. System optimization could lead to marginal reductions in cost and GHG emissions. Materials’ cost alone will have some impact on the CO2 Capture Cost. Furthermore, future improvements in both cost and performance of functional materials could have a significant, step-change impact when incorporated into existing high TRL systems.
As an example, the impact of the key technology’s materials cost is discussed first, and its performance is second. First, MTR membrane materials account for 6.4 $/tCO2 captured or 13.6% of the total 47 $/tCO2 captured. If the membrane cost were halved to 3.2 $/tCO2 captured, then the CO2 capture cost would decrease by at least 6.8%. However, the 47 $/tCO2 capture cost also includes 19 $/tCO2 captured of interest or depreciation. Because membranes represent 31% of initial capital cost and the total capital expenses, a 50% reduction of membrane costs also corresponds to 50% of 31% of 19 $/tCO2 captured or 2.95 $/tCO2 captured representing an overall reduction of 3.2 + 3.0 = 6.2 $/tCO2 captured, which is a more significant contribution.
Second, additional improvements could be achieved through increased materials performance. Again, using the MTR membrane includes a higher capture rate (permeance and/or specificity), longer lifetime, and/or lower temperature. These parameters could reduce energy input requirements. MTR has already developed second- and third-generation membranes, which have double and triple the throughput with the same selectivity. Doubling the throughput is analogous to the discussion above, where the specific membrane cost is halved but also has an additional impact on capital costs with fewer pressure vessels and the associated installation infrastructure, as well as piping.
Ciferno’s study, used as the BAT, compared the cost of three generations of amines with different regeneration energy requirements and their impact on the PC power plant’s net power output (Ciferno, 2007). Case 1 in the 2007 study is used in this study, and Case 1a is the same plant but with lower regeneration energy. The new amine reduced the LCOE incremental cost from 69.2 to 63.2 $/MWh, and the CO2 avoided cost decreased from 89 to 81 $/tCO2 (currencies in US dollars from the year of the study) (Ciferno, 2007). In summary, adding up these material costs and performance improvements could result in significant improvement in CCT’s overall cost and GHG emissions. This indicates the relative importance of improving functional materials cost and performance in future commercial CCT deployment.
The concept, framework, and methodology were established, and a new decision-making tool, a TDM, was developed using Excel and then applied to CCUS and specifically to CCTs. The TDM is a technology screening and data inventory tool to perform complimentary analysis and assessment with TEA and LCA tools to evaluate the cost, GHG, and market impacts of both disruptive CCUS technologies and their novel materials. The TDM can also be used to cross-check several CCTs and support continuous improvement of the respective TEA methods, calculations, and data.
KIPs across three categories of performance, cost, and lifetime at the same TRL, representing the entire CCT process being studied, were introduced to measure and compare among CCTs consisting of the BAT, Alt Tech under study, and the end application Target or Goal it will be used for. A PC-fired power plant retrofitted with commercially available monoethanolamine (MEA) CO2 capture absorption technology served as the BAT. Three promising CCT Alt Techs were presented: membrane, solid adsorption, and calcium looping.
Collecting KIP data for the BAT, Alt Techs, and Target revealed knowledge (how to measure a technology) and data (corresponding data measurement) gaps. Although there are international organizations active in this field, a knowledge gap is at this relatively early stage of CO2 capture research. There is not yet an agreed set of KIPs, and neither the units of measurement nor the measurement standards have been finalized. The corresponding data gaps are limited operational or in situ data at the lab bench top, pilot, or demo scales for both promising CCTs Alt Techs under development and CCT Targets. Specifically, a lack of a complete data set for CCT end application Targets or goals prevented TDM comparisons among BAT, Alt Tech, and Target.
The TDM’s KIP data table and resulting qualitative radar chart were demonstrated using available data for the BAT and three Alt Techs. This was accomplished by combining data from lab and pilot scales with those from simulations and TEA studies and then recalculating any missing KIP values from existing data. Relative comparisons were then made by normalizing each Alt Tech to the BAT for six KIPs to generate the radar plot. CCT performance and cost were compared among the four CCTs, and differences were easily visualized. However, these apparent differences must then be cross-checked against the original TEA data to understand if they are due to the CCT itself (technology gaps) or from the experimental or operational measurements (data gaps), or assumptions, equations, and KIPs used to generate the TEA (knowledge gaps). An examination of TEA financial assumptions revealed knowledge gaps of how different levelization periods, interest rates, FOM, and VOM charge factors impact CO2 Avoidance Cost and LCOE increase. Future work includes further TDM development, including using software other than Excel, integrating the TDM with NRC’s webserver, validating across TEA source data, TDM comparisons within the same CCT, improving KIPs, introducing KIP weighting, and introducing quantitative TDM outputs, including technology ranking based on a combined scoring factor, obtaining end application Target or Goal data, and finally expanding the TDM to include carbon conversion and utilization.
The original contributions presented in the study are included in the article/Supplementary Material. Further inquiries can be directed to the corresponding author.
RB, OA, MMD-C, and FB were all involved in the writing and editing of the article. All authors approved the final version of the article.
This work is part of the Materials for Clean Fuels (MCF) Challenge Program funded by and housed in NRC, Energy Mining and Environment Research Center.
The authors declare that the research was conducted in the absence of any commercial or financial relationships that could be construed as a potential conflict of interest.
All claims expressed in this article are solely those of the authors and do not necessarily represent those of their affiliated organizations or those of the publisher, the editors, and the reviewers. Any product that may be evaluated in this article, or claim that may be made by its manufacturer, is not guaranteed or endorsed by the publisher.
The authors would like to thank Natural Resources Canada’s Marzouk Benali, University of Toronto’s Heather Maclean, and University of Laval’s Faical Larachi for valuable discussions, as well as NRC’s Jianjun Yang, Titichai Navessin, Kourosh Malek, and James Butler for their work on earlier TDM versions for ES and PEMFCs.
The Supplementary Material for this article can be found online at: https://www.frontiersin.org/articles/10.3389/fenrg.2022.908658/full#supplementary-material
Abanades, J. C., Grasa, G., Alonso, M., Rodriguez, N., Anthony, E. J., and Romeo, L. M. (2007). Cost Structure of a Postcombustion CO2 Capture System Using CaO. Environ. Sci. Technol. 41, 5523–5527. doi:10.1021/es070099a
Alstom UK (2011). European Best Practice Guidelines for Assessment of CO2 Capture Technologies. Trondheim Nor.SINTEF 4.3, 1–112. doi:10.5281/zenodo.1312801
Anantharaman, R., Berstad, D., and Roussanaly, S.The International Conference on Applied Energy, I. (2014). Techno-economic performance of a hybrid membrane - Liquefaction process for post-combustion CO2 capture. Energy Procedia 61, 1,244–1,247.doi:10.1016/j.egypro.2014.11.1068
Anantharaman, R., Peters, T., Xing, W., Fontaine, M.-L., and Bredesen, R. (2016). Dual Phase High-Temperature Membranes for CO2 Separation - Performance Assessment in Post- and Pre-combustion Processes. Faraday Discuss. 192, 251–269. doi:10.1039/c6fd00038j
Baker, R. W., Freeman, B., Kniep, J., Huang, Y. I., and Merkel, T. C. (2018). CO2 Capture from Cement Plants and Steel Mills Using Membranes. Ind. Eng. Chem. Res. 57, 15963–15970. doi:10.1021/acs.iecr.8b02574
Baylin-Stern, A., and Berghout, N. (2021). Is Carbon Capture Too Expensive? [Online]. International Energy Agency. Paris, France, Available: https://www.iea.org/commentaries/is-carbon-capture-too-expensive [Accessed 20 January 2022].
Biegler, L. T., and Grossmann, I. E. (2004). Retrospective on Optimization. Comput. Chem. Eng. 28, 1169–1192. doi:10.1016/j.compchemeng.2003.11.003
Board, O. S.National Academies of Sciences, E., and Medicine (2019). Negative Emissions Technologies and Reliable Sequestration: A Research Agenda. National Academies Press. Washington, D.C., United States.
Buchner, G. A., Zimmermann, A. W., Hohgräve, A. E., and Schomäcker, R. (2018). Techno-economic Assessment Framework for the Chemical Industry-Based on Technology Readiness Levels. Ind. Eng. Chem. Res. 57, 8502–8517. doi:10.1021/acs.iecr.8b01248
Chen, Z. (2022). A Review of Pre-combustion Carbon Capture Technology, Proceedings of the 2022 7th International Conference on Social Sciences and Economic Development (ICSSED 2022), Wuhan, China, March 25–27, 2022. Atlantis Press, 524–528.
Ciferno, J. P. (2007). Carbon Dioxide Capture from Existing Coal-Fired Power Plants. National Energy Technology Laboratory. Pittsburgh Pennsylvania, United States.
Cormos, A., and Simon, A. (2013). Dynamic Modelling of CO2 Capture by Calcium-Looping Cycle. Chem. Eng. Trans. 35, 421–426. doi:10.3303/CET1335070
Dean, C. C., Blamey, J., Florin, N. H., Al-Jeboori, M. J., and Fennell, P. S. (2011a). The Calcium Looping Cycle for CO2 Capture from Power Generation, Cement Manufacture and Hydrogen Production. Chem. Eng. Res. Des. 89, 836–855. doi:10.1016/j.cherd.2010.10.013
Dean, C. C., Dugwell, D., and Fennell, P. S. (2011b). Investigation into Potential Synergy between Power Generation, Cement Manufacture and CO2 Abatement Using the Calcium Looping Cycle. Energy Environ. Sci. 4, 2050–2053. doi:10.1039/c1ee01282g
Dillon, D., Swisher, J., Freeman, B., Mckaskle, R., Chu, R., Lu, H., et al. (2021).Engineering Design of a Full Scale Membrane Post-Combustion CO2 Capture System Retrofit for Duke Energy’s East Bend Station, 15th International Conference on Greenhouse Gas Control Technologies, GHGT-15, Abu Dhabi, UAE, March 15–18, 2021. SSRN.
DOE/EE-2362 Carbon Negative Shot [Online] (2021). United States: US Department of Energy. Available: https://www.energy.gov/fecm/carbon-negative-shot [Accessed 20 November 2021].
Donat, F., Florin, N. H., Anthony, E. J., and Fennell, P. S. (2012). Influence of High-Temperature Steam on the Reactivity of CaO Sorbent for CO2 Capture. Environ. Sci. Technol. 46, 1262–1269. doi:10.1021/es202679w
ES-Select™ (2012). Documentation and User's Manual, Ver. No. 2.0. Department of Energy, Sandia National Lab. Albuquerque, New Mexico, United States.
Freeman, B., Hao, P., Baker, R., Kniep, J., Chen, E., Ding, J., et al. (2014). Hybrid Membrane-Absorption CO2 Capture Process. Energy Procedia 63, 605–613. doi:10.1016/j.egypro.2014.11.065
Friedmann, J., Fan, Z., Byrum, Z., Ochu, E., Bhardwaj, A., and Sheerazi, H. (2020). Levelized Cost of Carbon Abatement: An Improved Cost-Assessment Methodology for a Net-Zero Emissions World. New York, NY, USA: Columbia University SIPA Center on Global Energy Policy.
Haszeldine, R. S., Flude, S., Johnson, G., and Scott, V. (2018). Negative Emissions Technologies and Carbon Capture and Storage to Achieve the Paris Agreement Commitments. Phil. Trans. R. Soc. A 376, 20160447. doi:10.1098/rsta.2016.0447
Hilz, J., Haaf, M., Helbig, M., Lindqvist, N., Ströhle, J., and Epple, B. (2019). Scale-up of the Carbonate Looping Process to a 20 MWth Pilot Plant Based on Long-Term Pilot Tests. Int. J. Greenh. Gas Control 88, 332–341. doi:10.1016/j.ijggc.2019.04.026
Hovington, P., Ghaffari-Nik, O., Mariac, L., Liu, A., Henkel, B., and Marx, S. (2021). Rapid Cycle Temperature Swing Adsorption Process Using Solid Structured Sorbent for CO2 Capture from Cement Flue Gas. Proceedings of the 15th Greenhouse Gas Control Technologies Conference, 15-18 March 2021, Available at SSRN 3814414. Available at: http://dx.doi.org/10.2139/ssrn.3814414 (Accessed July 12, 2022).
Huang, Y., Rebennack, S., and Zheng, Q. P. (2013). Techno-economic Analysis and Optimization Models for Carbon Capture and Storage: a Survey. Energy Syst. 4, 315–353. doi:10.1007/s12667-013-0086-0
Junk, M., Reitz, M., Ströhle, J., and Epple, B. (2016). Technical and Economical Assessment of the Indirectly Heated Carbonate Looping Process. J. Energy Resour. Technol. 138. 4033142. doi:10.1115/1.4033142
Kearns, D., Liu, H., and Consoli, C. (2021). TECHNOLOGY READINESS AND COSTS OF CCS. Melbourne Australia: Global CCS Institute.
Kniep, J., Baker, R., Casillas, C., Chan, K., Huang, I., Merkel, T., et al. (2018). “Small Pilot Test Results from a Polaris Membrane 1 MWe CO2 Capture System,” in 14th Greenhouse Gas Control Technologies Conference Melbourne, Melbourne, Australia, October 21–25, 2018, 21–26.
Krutka, H., Sjostrom, S., Starns, T., Dillon, M., and Silverman, R. (2013). Post-combustion CO2 Capture Using Solid Sorbents: 1 MWe Pilot Evaluation. Energy Procedia 37, 73–88. doi:10.1016/j.egypro.2013.05.087
Kuramochi, T., Ramírez, A., Turkenburg, W., and Faaij, A. (2012). Comparative Assessment of CO2 Capture Technologies for Carbon-Intensive Industrial Processes. Prog. Energy Combust. Sci. 38, 87–112. doi:10.1016/j.pecs.2011.05.001
Leung, D. Y. C., Caramanna, G., and Maroto-Valer, M. M. (2014). An Overview of Current Status of Carbon Dioxide Capture and Storage Technologies. Renew. Sustain. Energy Rev. 39, 426–443. doi:10.1016/j.rser.2014.07.093
Lin, J.-B., Nguyen, T. T. T., Vaidhyanathan, R., Burner, J., Taylor, J. M., Durekova, H., et al. (2021). A Scalable Metal-Organic Framework as a Durable Physisorbent for Carbon Dioxide Capture. Science 374, 1464–1469. doi:10.1126/science.abi7281
Malek, K., and Nathwani, J. (2015). "Technology Management Tools for Assessing Emerging Technologies: The Case of Grid-Scale Storage", in: 2015 Portland International Conference on Management of Engineering and Technology (PICMET), 02-06 Aug. 2015, Portland, OR, USA, 2346–2354.
Malek, K. (2019). Typology of Business Models for Emerging Grid-Scale Energy Storage Technologies. Waterloo, Ontario: UWSpace. Available at: http://hdl.handle.net/10012/14503
Manovic, V., and Anthony, E. J. (2010). Carbonation of CaO-Based Sorbents Enhanced by Steam Addition. Ind. Eng. Chem. Res. 49, 9105–9110. doi:10.1021/ie101352s
Manovic, V., and Anthony, E. J. (2009). Long-Term Behavior of CaO-Based Pellets Supported by Calcium Aluminate Cements in a Long Series of CO2 Capture Cycles. Ind. Eng. Chem. Res. 48, 8906–8912. doi:10.1021/ie9011529
McNeil, L. A., Mutch, G. A., Iacoviello, F., Bailey, J. J., Triantafyllou, G., Neagu, D., et al. (2020). Dendritic Silver Self-Assembly in Molten-Carbonate Membranes for Efficient Carbon Dioxide Capture. Energy Environ. Sci. 13, 1766–1775. doi:10.1039/c9ee03497h
Merkel, T., Amo, K., Baker, R., Daniels, R., Friat, B., He, Z., et al. (2009). Membrane Process to Sequester CO2 from Power Plant Flue Gas. USA: Membrane Technology and Research Inc.
Merkel, T. C., Lin, H., Wei, X., and Baker, R. (2010). Power Plant Post-combustion Carbon Dioxide Capture: An Opportunity for Membranes. J. Membr. Sci. 359, 126–139. doi:10.1016/j.memsci.2009.10.041
Merkel, T., Kniep, J., and Hofmann, T. (2018). “Scale up and Testing of Advanced Polaris Membrane CO2 Capture Technology (DE FE0031591),”. Editor U. S. D. O. E. U. Doe (Pittsburgh PA: DOE National Energy Technology Laboratory (NETL)).
NRC (2022). Economic & Environmental Evaluation of Carbon Conversions [Online]. Government of Canada. Available: https://eeecc.nrc-cnrc.gc.ca [Accessed June 14 2022].
Pardakhti, M., Jafari, T., Tobin, Z., Dutta, B., Moharreri, E., Shemshaki, N. S., et al. (2019). Trends in Solid Adsorbent Materials Development for CO2 Capture. ACS Appl. Mat. Interfaces 11, 34533–34559. doi:10.1021/acsami.9b08487
Qiao, Z., Zhao, S., Sheng, M., Wang, J., Wang, S., Wang, Z., et al. (2019). Metal-induced Ordered Microporous Polymers for Fabricating Large-Area Gas Separation Membranes. Nat. Mater 18, 163–168. doi:10.1038/s41563-018-0221-3
Rezaei, F., and Webley, P. (2009). Optimum Structured Adsorbents for Gas Separation Processes. Chem. Eng. Sci. 64, 5182–5191. doi:10.1016/j.ces.2009.08.029
Rubin, E., Booras, G., Davison, J., Ekstrom, C., Matuszewski, M., Mccoy, S., et al. (2013a). Toward a Common Method of Cost Estimation for CO2 Capture and Storage at Fossil Fuel Power Plants. Australia: Global CCS Institute.
Rubin, E. S., Short, C., Booras, G., Davison, J., Ekstrom, C., Matuszewski, M., et al. (2013b). A Proposed Methodology for CO2 Capture and Storage Cost Estimates. Int. J. Greenh. Gas Control 17, 488–503. doi:10.1016/j.ijggc.2013.06.004
Samanta, A., Zhao, A., Shimizu, G. K. H., Sarkar, P., and Gupta, R. (2012). Post-combustion CO2 Capture Using Solid Sorbents: A Review. Ind. Eng. Chem. Res. 51, 1438–1463. doi:10.1021/ie200686q
Scholes, C. A., Anderson, C. J., Cuthbertson, R., Stevens, G. W., and Kentish, S. E. (2013). Simulations of Membrane Gas Separation: Chemical Solvent Absorption Hybrid Plants for Pre- and Post-Combustion Carbon Capture. Sep. Sci. Technol. 48, 1954–1962. doi:10.1080/01496395.2013.793201
Shao, P., Dal-Cin, M. M., Guiver, M. D., and Kumar, A. (2013). Simulation of Membrane-Based CO2 Capture in a Coal-Fired Power Plant. J. Membr. Sci. 427, 451–459. doi:10.1016/j.memsci.2012.09.044
Shi, S. Y., Jianjun , , Gonzales-Calienes, Giovanna, Baker, Ryan, Malek, Kourosh, and Skrivan, Will (2020). Canadian Energy Storage Report: 2019 Case Study for the Ontario Market. NRC Publications Archive: National Research Council of Canada. Ottawa, Ontario, Canada.
Shimizu, T., Hirama, T., Hosoda, H., Kitano, K., Inagaki, M., and Tejima, K. (1999). A Twin Fluid-Bed Reactor for Removal of CO2 from Combustion Processes. Chem. Eng. Res. Des. 77, 62–68. doi:10.1205/026387699525882
Sjostrom, S., Denney, J., Senior, C., and Morris, W. (2016). Evaluation of Solid Sorbents as a Retrofit Technology for CO2Capture. ADA-ES, Highlands Ranch, CO: US Department Of Energy Topical Report: US Department Of Energy Final Technical Report. DOE DE-FE004343 [Online]. United States. Available at: https://www.osti.gov/servlets/purl/1261627 [Accessed 20 January 2022].
Stevenson, M., and Armpriester, A. (2016). NRG CO2NCEPT - Confirmation of Novel Cost-Effective Emerging Post-combustion Technology. Houston, Texas, United States: NRG Energy, Inc. and USDOE Office of Fossil Energy.
Ströhle, J., Hofmann, C., Greco-Coppi, M., and Epple, B. (2021).CO2 Capture from Lime and Cement Plants Using an Indirectly Heated Carbonate Looping Process–The Anica Project, TCCS–11. CO2 Capture, Transport and Storage. Short Papers from the 11th International Trondheim CCS Conference, Trondheim, 22nd–23rd June 2021. SINTEF Academic Press.
Sun, P., Grace, J. R., Lim, C. J., and Anthony, E. J. (2007). The Effect of CaO Sintering on Cyclic CO2 Capture in Energy Systems. AIChE J. 53, 2432–2442. doi:10.1002/aic.11251
Tang, Y., and You, F. (2018). Life Cycle Environmental and Economic Analysis of Pulverized Coal Oxy-Fuel Combustion Combining with Calcium Looping Process or Chemical Looping Air Separation. J. Clean. Prod. 181, 271–292. doi:10.1016/j.jclepro.2018.01.265
Tapia, J. F. D., Lee, J.-Y., Ooi, R. E. H., Foo, D. C. Y., and Tan, R. R. (2018). A Review of Optimization and Decision-Making Models for the Planning ofCO2capture, Utilization and Storage (CCUS) Systems. Sustain. Prod. Consum. 13, 1–15. doi:10.1016/j.spc.2017.10.001
Tian, Q., Zhao, D., Li, Z., Zhang, J., Li, Q., Liu, H., et al. (2016). Modelling and Evaluating CCUS: a Survey. Ijcat 53, 1–12. doi:10.1504/ijcat.2016.073607
US DOE/NETL (2015a). DOE/NETL Carbon Capture Program: Carbon Dioxide Capture Handbook [Online]. , Available: https://netl.doe.gov/sites/default/files/netl-file/Carbon-Dioxide-Capture-Handbook-2015.pdf [Accessed 15 March 2021].
US DOE/NETL (2015b). Funding Opportunity Announcement DE-FOA-0001190 Entitled "Small And Large Scale Pilots For Reducing The Cost Of CO2Capture And Compression [Online]. , Available at: https://www.netl.doe.gov/node/8590 [Accessed 20 January 2022].
Wang, B., Qiao, Z., Xu, J., Wang, J., Liu, X., Zhao, S., et al. (2020). Unobstructed Ultrathin Gas Transport Channels in Composite Membranes by Interfacial Self-Assembly. Adv. Mat. 32, 1907701. doi:10.1002/adma.201907701
Wang, J., Manovic, V., Wu, Y., and Anthony, E. J. (2010). A Study on the Activity of CaO-Based Sorbents for Capturing CO2 in Clean Energy Processes. Appl. Energy 87, 1453–1458. doi:10.1016/j.apenergy.2009.08.010
Wei, X., Baker, R. W., Merkel, T. C., and Freeman, B. C. (2015). Sweep-based Membrane Gas Separation Integrated with Gas-Fired Power Production and CO2Recovery. U.S. Patent No 9. Washington, DC: U.S. Patent and Trademark Office, 140–186.
Yang, Y., Zhai, R., Duan, L., Kavosh, M., Patchigolla, K., and Oakey, J. (2010). Integration and Evaluation of a Power Plant with a CaO-Based CO2 Capture System. Int. J. Greenh. Gas Control 4, 603–612. doi:10.1016/j.ijggc.2010.01.004
Zhao, M., Minett, A. I., and Harris, A. T. (2013). A Review of Techno-Economic Models for the Retrofitting of Conventional Pulverised-Coal Power Plants for Post-combustion Capture (PCC) of CO2. Energy Environ. Sci. 6, 25–40. doi:10.1039/c2ee22890d
Zimmermann, A., Müller, L. J., Marxen, A., Armstrong, K., Buchner, G., Wunderlich, J. K., et al. (2018). Techno-Economic Assessment & Life-Cycle Assessment Guidelines for CO2 Utilization. Sheffield UK: CO2 Chem Media and Publising Ltd.
Zimmermann, A., Müller, L., Wang, Y., Langhorst, T., Wunderlich, J., Marxen, A., et al. (2020a). Techno-Economic Assessment & Life Cycle Assessment Guidelines for CO2 Utilization (Version 1.1). Ann Arbour, Michigan: Global CO2 Initiative at the University of Michigan and EIT Climate-KIC.
Zimmermann, A. W., Wunderlich, J., MüLler, L., Buchner, G. A., Marxen, A., Michailos, S., et al. (2020b). Techno-Economic Assessment Guidelines for CO2 Utilization. Front. Energy Res. 8, 1–23. doi:10.3389/fenrg.2020.00005
Alt Tech(s) Alternative Technology(ies)
ASU Air Separation Unit
BAT Best Available Technology
BEC Bare Erected Costs
BoP Balance of Plant
BoS Balance of System
CAPEX CAPital Expenditure
CC Carbon Capture
CCCL Carbon Capture Compression and Liquefaction
CCUS Carbon capture, utilization, and storage
CCT(s) Carbon Capture Technology(ies)
CFB Circulating Fluidized Bed
DAC Direct Air (carbon) Capture
DOE Department of Energy
EOR Enhanced Oil Recovery
ES Energy Storage
ESP Electro-Static Precipitator
FCF Fixed Charge Factor
FGD Flue Gas Desulfurization
FOA Funding Opportunity Announcement
FOM Fixed Operation and Maintenance
GCI Global CO2 Initiative
GHG Green House Gas
GPU Gas Permeation Units
HHV Higher Heating Value
IEA International Energy Agency
IGCC Integrated Gas Combined Cycle
KIP(s) Key Indicator Parameter(s)
LCA Life-cycle assessment
LCCA Levelized Cost of Carbon Abatement
LCOE Levelized Cost of Electricity
LDH Layered Double Hydroxide
LHV Lower Heating Value
MEA MonoEthanol Amine
MOF Metal–Organic Framework
MTR Membrane Technology Research
NETL National Energy Technology Laboratory
NRC National Research Council of Canada
O&M Operation and Maintenance
OPEX Operational EXPenditure
PC Pulverized Coal
PM Particulate Matter
PEMFC Proton Exchange Membrane Fuel Cell
R&D Research and Development
RD&D Research, Development and Deployment
SCAH Steam Coil Air Heater
TDM Technology Development Matrix
TEA Techno-Economic Analysis
TFC Thin Film Composite
TCR Total Capital Required
TIC Total Installed Cost
TRL(s) Technology Readiness Level(s)
TSA Temperature Swing Adsorption
US United States
VOM Variable Operation and Maintenance
Keywords: carbon capture, decision-making tool, monoethanolamine, membrane, solid adsorption, calcium looping, techno-economic analysis, life-cycle assessment
Citation: Baker R, Alizadeh Sahraei O, Dal-Cin MM and Bensebaa F (2022) A Technology Development Matrix for Carbon Capture: Technology Status and R&D Gap Assessment. Front. Energy Res. 10:908658. doi: 10.3389/fenrg.2022.908658
Received: 30 March 2022; Accepted: 21 June 2022;
Published: 09 August 2022.
Edited by:
Graeme Douglas Puxty, Commonwealth Scientific and Industrial Research Organisation (CSIRO), AustraliaReviewed by:
Iftekhar A. Karimi, National University of Singapore, SingaporeCopyright © 2022 Baker, Alizadeh Sahraei, Dal-Cin and Bensebaa. This is an open-access article distributed under the terms of the Creative Commons Attribution License (CC BY). The use, distribution or reproduction in other forums is permitted, provided the original author(s) and the copyright owner(s) are credited and that the original publication in this journal is cited, in accordance with accepted academic practice. No use, distribution or reproduction is permitted which does not comply with these terms.
*Correspondence: Ryan Baker, cnlhbi5iYWtlckBucmMtY25yYy5nYy5jYQ==
Disclaimer: All claims expressed in this article are solely those of the authors and do not necessarily represent those of their affiliated organizations, or those of the publisher, the editors and the reviewers. Any product that may be evaluated in this article or claim that may be made by its manufacturer is not guaranteed or endorsed by the publisher.
Research integrity at Frontiers
Learn more about the work of our research integrity team to safeguard the quality of each article we publish.