- 1Energy Storage Research Group, Faculty of Ocean Engineering Technology and Informatics, Universiti Malaysia Terengganu, Kuala Nerus, Malaysia
- 2Faculty of Innovative Design and Technology, Universiti Sultan Zainal Abidin, Kuala Nerus, Malaysia
- 3Casa Armada Sdn. Bhd., Kemaman, Malaysia
- 4Department of Mechanical Engineering, Institut Teknologi Sepuluh Nopember (ITS), Surabaya, Indonesia
The problem of providing compact and safe storage solutions for hydrogen in solid-state materials is demanding and challenging. The storage solutions for hydrogen required high-capacity storage technologies, which preferably operate at low pressures and have good performances in the kinetics of absorption/desorption. Metal hydrides such as magnesium hydride (MgH2) are promising candidates for such storage solutions, but several drawbacks including high onset desorption temperature (>400°C) and slow sorption kinetics need to be overcome. In this study, we reviewed the recent developments in the hydrogen storage performance development of MgH2 and found that the destabilization concept has been extensively explored. Lithium alanate or LiAlH4 has been used as a destabilizing agent in MgH2–LiAlH4 (Mg–Li–Al) due to its high capacity of hydrogen, which is 10.5 wt.%, and low onset desorption temperature (∼150°C). In this article, a review of the recent advances in the Mg–Li–Al system for the solid-state hydrogen storage material is studied. We discussed the effect of the ratio of MgH2 and LiAlH4, milling time, and additives in the Mg–Li–Al system. After the destabilization concept was introduced, the onset of the desorption temperature and activation energy of MgH2 were reduced, and the sorption properties improved. Further study showed that the intermetallic alloys of Li0.92Mg4.08 and Mg17Al12 that were formed in situ during the dehydrogenation process provide synergetic thermodynamic and kinetic destabilization in the Mg-Li-Al composite system.
De/rehydrogenation measurements indicate that the intermetallic alloys of Li0.92Mg4.08 and Mg17Al12 were fully reversibly absorbed and desorbed hydrogen. Next, the remaining challenges and a possible development strategy of the Mg–Li–Al system are analyzed. This review is the first systematic study that focuses on the recent advances in the Mg–Li–Al system for storage solutions for hydrogen in solid-state materials.
Introduction
Due to global environmental issues and the search for new energy sources and carriers, hydrogen is viewed as the most promising alternative to replace fossil fuel-based energy (Yang et al., 2019; Yao L. et al., 2020; Zhang et al., 2019b). Hydrogen is an environment-friendly energy carrier since it has near-zero greenhouse gas emissions. In addition, hydrogen can also reduce the dependence on imported oil for countries without natural resources (Peláez Peláez et al., 2021; Sartbaeva et al., 2008). Hydrogen is not found naturally, but it can be produced from a variety of primary energy sources (e.g., fossil fuels and biomass) and secondary energy sources (e.g., renewable electricity from wind and hydropower) (Abdin et al., 2020; Thapa et al., 2021). As reported by Dunn (Dunn, 2002), since the mid-19th century, the world has been shifting slowly from one form of energy to another, from solids to liquids and gases, as shown in Figure 1. Compared to fossil fuel, hydrogen holds high energy content and can be stored in large quantities over a long time (Satyapal et al., 2007; Sadhasivam et al., 2017). Hydrogen can offer a long-term solution as it can be continuously supplied and can contribute to a variety of automotive fuel sources. As a result, important research and developmental activities are being carried out to improve the efficiency of the hydrogen-based energy system to make it competitive with the existing fossil fuels.
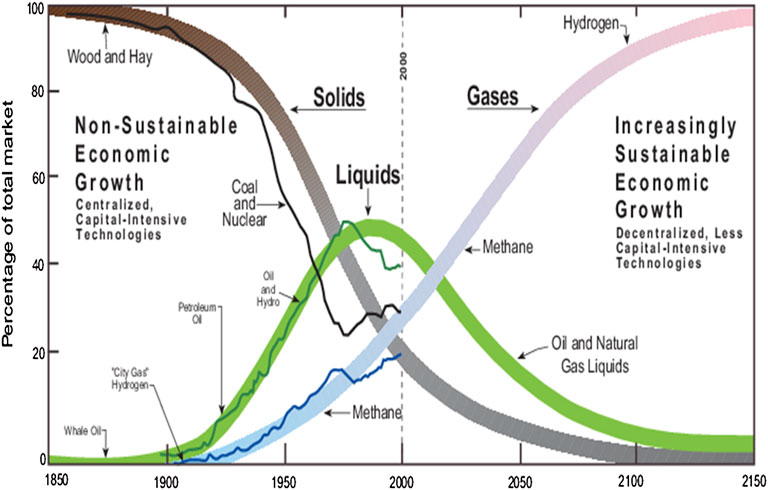
FIGURE 1. Global transition of energy systems 1850–2150 (Dunn, 2002).
In addition to the lack of infrastructures for hydrogen (for example, production, distribution, and refueling), one of the main roadblocks to the spread of hydrogen is reliable hydrogen storage. Hydrogen-compressed gas tanks, hydrogen liquid tanks, and solid-state storage of hydrogen are possible current approaches to store hydrogen (Sazelee et al., 2018; Doğan et al., 2020). Liquid hydrogen storage systems present a promising opportunity to efficiently increase the capacity of hydrogen fueling stations and are also preferred for space missions (Jiang et al., 2021; Correa-Jullian & Groth, 2022). Although liquid hydrogen tanks are usually super-insulated tanks, at approximately 20 K, boil-off may occur due to the substantial temperature difference between the ambient and liquid hydrogen (Khurana et al., 2006; Zuo et al., 2020). On the other hand, although storage in a compressed gas tank is possible, technical simplicity and the fast filling-releasing rate requires very high pressure and has high costs (Zheng et al., 2012). Therefore, solid-state hydrogen storage draws more attention due to its security, high storage capacity, and hydrogen purification (Niaz et al., 2015; Sazelee et al., 2020b; Ye et al., 2020). However, a drawback of the solid-state hydrogen storage materials, especially for metal/complex hydrides, is their high decomposition temperature and sluggish sorption kinetics (absorb and desorb hydrogen) (Daulbayev et al., 2022).
An Overview of the Mg–Li–Al Systems
A wide variety of materials are currently being considered as the future reversible solid-state hydrogen storage materials (Zacharia & Rather, 2015). As claimed by David (David, 2005), the ability to separate hydrogen differs from each metal, and this ability depends on the metals’ purity, surface structure, and morphology. The list of the storage systems with their gravimetric capacities is shown in Table 1.
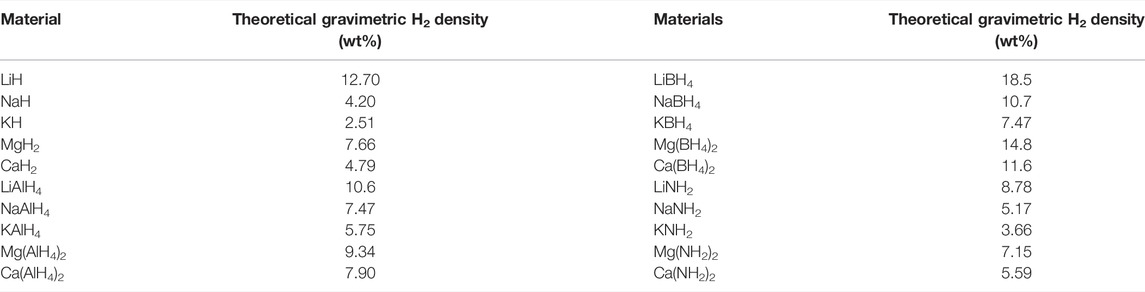
TABLE 1. Hydride materials and theoretical gravimetric hydrogen density (Kojima, 2019).
Globally, among the solid-state hydrogen storage materials, research into the use of magnesium (Mg) in hydrogen storage applications is of considerable importance (Jain et al., 2010; Crivello et al., 2016; Zhang et al., 2019a; Ouyang et al., 2020). In recent years, much attention has been given to examining the specific material properties of Mg alloys for the development of new functional materials (Yang et al., 2021). Mg is also one of the most abundant and lightly packed solid materials (1.738 g/cm3) (Li et al., 2015). Increasing interest in MgH2 has been shown due to its high hydrogen storage capacity (7.6 wt.%), low cost, and superior reversibility (Imamura et al., 2005; Sakintuna et al., 2007; Montone et al., 2010; El Khatabi et al., 2018).
Thus, researchers suggested that hydrogen interaction with Mg is one of the most promising approaches (Eftekhari & Fang, 2017; Luo et al., 2019). While Mg satisfies many practical application requirements, the on-board applications can still not be used for many reasons, such as 1) the desorption/absorption kinetics process is very slow for pure Mg (Schlapbach et al., 1979) and 2) releasing hydrogen at high temperatures (>400°C), is correlated with the high stability of Mg–H bonds and is expressed in the high enthalpy of hydride formation (Zaluska et al., 1999; Dornheim et al., 2007; Jain et al., 2010). To boost MgH2 hydrogen storage properties, numerous techniques have been developed including alloying (Li et al., 2019; Liang et al., 2020; Marques et al., 2020; Dematteis et al., 2021), nanosizing (Ranjbar et al., 2009; Zhang et al., 2015; Yu et al., 2017; Ma et al., 2021), and catalyzing (Polanski et al., 2011; Baricco et al., 2012; Ismail et al., 2016; Jangir et al., 2018; Yao P. et al., 2020; Ismail, 2021; Liu et al., 2021; Lu et al., 2021; Zhang et al., 2021). The remarkable improvements of these techniques have been demonstrated as the most successful methods but still do not fulfill the Department of Energy (DOE) target for solid-state hydrogen storage materials (Urgnani et al., 2008).
The ‘destabilization concept’ has been introduced as another method to enhance the sorption kinetics and alter the thermodynamics of MgH2 (Vajo et al., 2004; Vajo et al., 2007; Vajo & Olson, 2007; Ali et al., 2021; Sulaiman et al., 2021b). The concept aims to modify the thermodynamics and kinetics of the hydrogen sorption reaction (Barkhordarian et al., 2007). Thermodynamic destabilization is achieved when the mixed hydrides react and form a new intermediate compound that alters the thermodynamic properties and facilitates hydrogen release and absorption (Reilly & Wiswall, 1968; Ismail & Mustafa, 2016; Ali & Ismail, 2021). Since several studies have been reported on this concept, researchers attempted to destabilize MgH2 by using the reactive hydride composite approach, as in the systems such as MgH2–AlH3 (Liu et al., 2013; Liu et al., 2014; Ismail, 2016), MgH2–Mg(AlH4)2 (Wang et al., 2014), MgH2–NaAlH4 (Ismail et al., 2013; Rafi-ud-din et al., 2014; Bendyna et al., 2015; Ali & Ismail, 2021), MgH2–NaBH4 (Mao et al., 2009; Kato et al., 2012; Mulas et al., 2012), and other promising destabilizing systems. Among all the destabilizing systems, the researchers tried the destabilizing concept with the most studied materials under the complex hydride, which is LiAlH4, in order to enhance the performance for the practical use of MgH2. Due to its high capacity for storage (10.5 wt.%), LiAlH4 is interesting compared to the other complex hydrides such as NaAlH4 (5.5 wt.%) (Sazelee & Ismail, 2021). LiAlH4 decomposes in three steps (Liu C. et al., 2020). With 5.3 wt.% of H2 at 150°C, the first decomposition occurs as in Eq. 1. Meanwhile, the second decomposition occurs at ∼180°C (2.6 wt.%), and the third decomposition occurs with a temperature above 350°C (2.6 wt.%), as in Eqs 2, 3, respectively.
Even though LiAlH4 offers several benefits, it suffers from slow desorption kinetics (hard to release hydrogen at certain conditions), and the last reaction temperature is quite high (Hsu et al., 2014a; Ismail et al., 2021). The enthalpy change of Eq. 1 is calculated to be −27 kJmol−1 (Ke & Chen, 2007), which indicates that the hydrogen evolution from the solid LiAlH4 is thermodynamically allowed at low temperatures but is restricted by a relatively high kinetic barrier in transforming tetrahedron (AlH4)− to octahedron (AlH6)3− (Chen et al., 2010). All the theoretical and experimental works showed that the LiAlH4 system could absorb hydrogen when a higher hydrogen pressure is applied (more than 8.0 MPa) (Sazelee & Ismail, 2021). This is because LiAlH4 is restricted by weak reversibility and very high thermodynamic stability (Graetz et al., 2008). For instance, Jang et al. (Jang et al., 2006) stated that more than 103 bar of hydrogen partial pressure is required for the absorption reaction of Li3AlH6 to LiAlH4 above the room temperature.
To that end, this review concentrated on the destabilized MgH2–LiAlH4 composite (Mg–Li–Al system). This idea is based on the hypothesis that so-called mechano-chemical reactions could occur between MgH2 and LiAlH4, and the intermediate phases (Li0.92Mg4.08 and Mg17Al12) could be formed to modify the thermal stability of the Mg–Li–Al system. The primary goal of this article is to review the progress of the destabilized MgH2–LiAlH4 system in improving the performance of MgH2 and LiAlH4 hydrogen storage. Up to date, no researchers have been reviewing this Mg–Li–Al system. Therefore, we believed that the researchers and practitioners involved in research on hydrogen storage materials will benefit from this review article. Figure 2 illustrates the main topics discussed in this review.
The Effect of the MgH2 and LiAlH4 Ratios
The first systematic study on the mutual destabilization between MgH2 and LiAlH4 was reported by Zhang et al. (Zhang et al., 2008). They studied the different molar ratios (1:1, 2:1, and 4:1) of MgH2–LiAlH4. The result showed that the initial desorption temperature for the MgH2–relevant decomposition in all the different molar ratios of the MgH2–LiAlH4 composite was decreased to ∼250°C, which is 50°C lower than the milled MgH2, as shown in Figure 3. By using the Kissinger method, the activation energy value of MgH2–relevant decomposition in the composite was reduced dramatically compared to the undoped MgH2. The dehydrogenation enthalpies of the MgH2–LiAlH4 composites with different molar ratios 4:1, 2:1, and 1:1 are 61, 48.66, and 45 kJ/mol, respectively. These enthalpy values were smaller than the undoped MgH2 (76 kJ/mol), which indicates that MgH2 was destabilized by LiAlH4. Further study revealed that the dehydrogenation process in the MgH2–LiAlH4 system can be divided into two steps: the first step is due to the two-step decomposition of LiAlH4 (The first step is the decomposition of LiAlH4 to Li3AlH6 and Al (as in Eq. 1), and the second step is the decomposition of Li3AlH6 to LiH and Al (as in Eq. 2) and the second step is due to the reaction between LiH and Al phases to form Li0.92Mg4.08 and Mg17Al12 phases, as indicated in Eqs 4, 5.
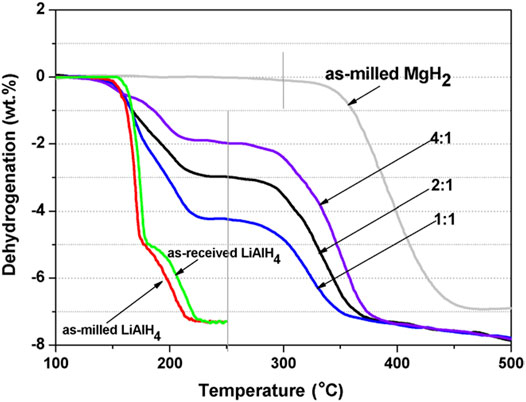
FIGURE 3. Initial desorption temperature for the as-milled LiAlH4, as-milled MgH2, and MgH2–LiAlH4 composites with different molar ratios (1:1, 2:1, and 4:1) (Zhang et al., 2008).
Moreover, rehydrogenation measurement shows that Li0.92Mg4.08 and Mg17Al12 are the fully absorbed hydrogen, as shown in Eqs 6, 7.
Lin and Tsai (Lin & Tsai, 2017) in their study exposed that the diffraction peak intensity of LiAlH4 decreased with an increasing amount of MgH2 addition, as in Figure 4. No other compounds were found after milling, indicating that no reaction occurred between LiAlH4 and MgH2 during the milling process. This result is in agreement with a previous study by Hsu et al. (Hsu et al., 2014b), in which the diffraction peak intensity of MgH2 increased with a decreasing amount of LiAlH4 in the MgH2–LiAlH4 mixture.
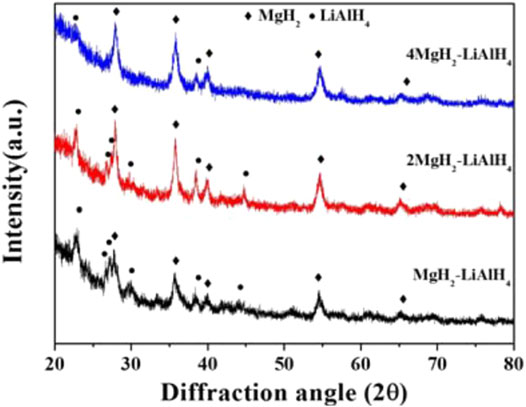
FIGURE 4. XRD patterns of different ratios of MgH2 and LiAlH4 in the Mg–Li–Al system after the milling process (Lin & Tsai, 2017).
Next, the temperatures of desorption and the amount of hydrogen released from the composites of MgH2–LiAlH4 were quantitively evaluated by the thermogravimetric analysis (TGA), as shown in Table 2. It was evident that with the increasing MgH2 content in the composites, the first desorption temperature was lowered. These findings showed that MgH2 played an effective role in reducing the initial desorption temperature of these composites. As soon as the desorption of these composites was completed, absorption kinetics was initiated with a temperature maintained at 400°C, while charging hydrogen to the target pressure. As displayed in Table 2, the total amount of hydrogen absorbed (wt.%) increased from 0.3 to 3, and the onset desorption temperature also decreased to 85°C compared to 100°C with an increase in the MgH2 content in the composites. The results proved that MgH2 was the main compound that exhibited reversibility concerning the hydrogen absorption/desorption reaction. As shown in Table 2, the ability of the MgH2–LiAlH4 composite to absorb hydrogen increased as the MgH2 ratio increased.

TABLE 2. TGA results show the temperature of desorption and the amount of hydrogen absorption/desorption from MgH2–LiAlH4 with different amounts of composites (Lin & Tsai, 2017).
The LiAlH4–MgH2 hydrogen storage system was studied by Chen et al. (Chen et al., 2010). The commercial LiAlH4 was decomposed at 163°C; meanwhile, the commercial MgH2 decomposed at 405°C. However, LiAlH4 and MgH2 mixtures start to release hydrogen at ∼107°C, indicating that the combination of LiAlH4 and MgH2 may improve their thermodynamic properties. Measurement of the XRD was performed after desorption, and the results showed that in all the LiAlH4–xMgH2 composites (LiAlH4–MgH2, LiAlH4–2.5MgH2, and LiAlH4–4MgH2), the Mg17Al12 phase was formed. In addition, the LiAlH4–4MgH2 composite contained major Li0.92Mg4.08 phases, whereas LiAlH4–2.5MgH2 contained minor Li0.92Mg4.08 phases, as shown in Figure 5. This indicates that Li0.92Mg4.08 can be formed while the ratio of MgH2/LiAH4 is relatively high. These composites also undergo an absorption process at 350°C under a pressure of 10 MPa hydrogen. In 60 min, the LiAlH4–4MgH2 composites reach 90% of their maximum absorption capacity. In brief, these reported studies indicated that the combination of LiAlH4 and MgH2 may have been shown to affect the thermal stability of both LiAlH4 and MgH2 by the formation of intermetallic Mg17Al12 and Li0.92Mg4.08.
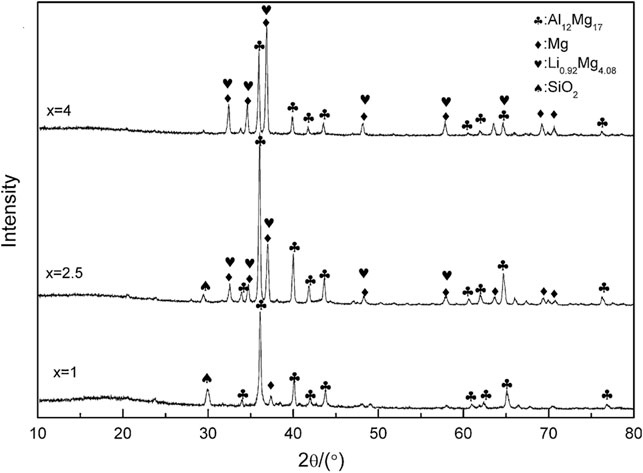
FIGURE 5. XRD patterns of LiAlH4 + xMgH2 (x = 1, 2.5, and 4) after dehydrogenation at 350°C (Chen et al., 2010).
Based on the abovementioned discussions, the different molar ratios of the MgH2–LiAlH4 composites also affected the performance of the Mg–Li–Al system. This review article outlined that 4MgH2–LiAlH4 shows the best performance compared to the other ratios (e.g., 1:1, 2:1, and 2.5:1). The 4MgH2–LiAlH4 composite created an intermediate compound of Li0.92Mg4.08 and Mg17Al12 that helps to enhance the hydrogen storage performance of the Mg–Li–Al system.
The Effect of Different Milling Times
Vittetoe et al. (Vittetoe et al., 2009) explored the destabilization effects of the combination of LiAlH4 with a nanocrystalline MgH2 by mechanical–chemical milling concerning reversibility and kinetics problems. Interestingly, they investigated the LiAlH4–MgH2 composite with different durations of milling (1, 2, 3, and 5 h). They discovered that the LiAlH4–MgH2 samples that have been milled for 1, 2, and 3 h started to decompose at ∼100°C. Researchers verified that for an optimal ball milling period of 2 h, a three-step hydrogen desorption response with an early-onset temperature and greater amount of hydrogen release is required. In addition, further study elucidates LiAlH4–MgH2 and LiAlH4–nanoMgH2 of TGA and differential scanning calorimetry (DSC) profiles milled for 2 h, as seen in Figure 6. The LiAlH4–nanoMgH2 systems show a greater weight loss of approximately 5.2 wt.% (∼200°C), at least 1.0 wt.% higher capacity than the commercial-grade sample (LiAlH4–MgH2).
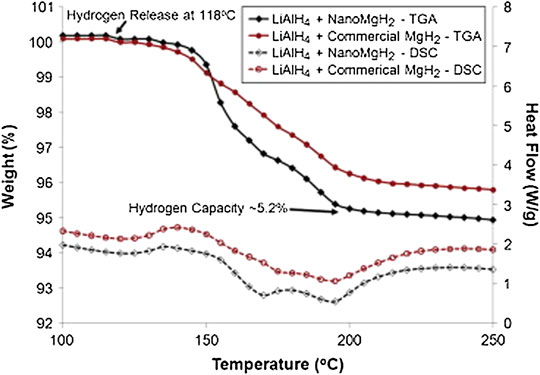
FIGURE 6. Comparison of TGA/DSC mechano-chemically milled for 2 h for LiAlH4-MgH2 and LiAlH4–nanoMgH2 (Vittetoe et al., 2009).
As LiAlH4–nanoMgH2 showed better performance than LiAlH4–MgH2, this material underwent repeated absorption of hydrogen (80 bars) and desorption at two different temperatures (300 and 350°C). After numerous attempts of hydrogen absorption–desorption experiments, these samples were carefully examined under a scanning electron microscope (SEM), as shown in Figure 7. SEM images of LiAlH4–nanoMgH2 after cycling indicated that the sample had a relatively smaller grain with a highly porous matrix and uniform (as in Figure 7B) as compared to LiAlH4–nanoMgH2 (as in Figure 7A). This is due to the host structure’s effective uptake and release of hydrogen.
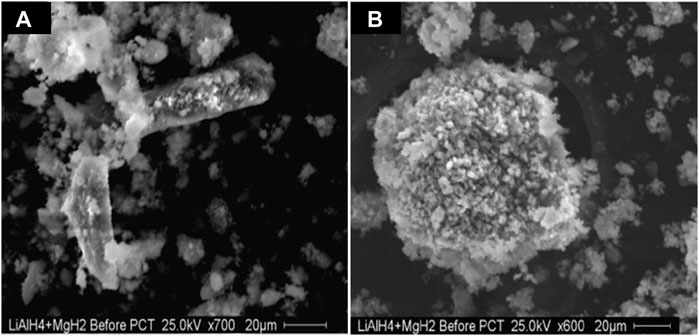
FIGURE 7. SEM images of LiAlH4–nanoMgH2 (A) after milling for 2 h and (B) after absorption–desorption cycling (Vittetoe et al., 2009).
Milanovic et al. (Milanović et al., 2013) investigated the catalytic influence on the desorption of hydrogen from MgH2. Indeed, when mixing MgH2 with a 5 wt.% of LiAlH4 for 15 min, the peak of the hydrogen desorption shifts to a lower temperature than as received MgH2 and as milled MgH2. In this study, milling up to 30 and 60 min of the MgH2–LiAlH4 composites may reduce the catalytic activity of the LiAlH4 additive, as revealed by the shift to a higher peak of desorption temperatures. According to Leon et al. (Léon et al., 2009), experiments conducted under various conditions revealed that the milling parameters, in particular the milling speed and milling time, can be of great importance through reactive ball milling for the formation of the new hydride phase. Next, Ding et al. (Ding et al., 2013) studied the MgH2–LiAlH4 composites milled at different milling times (2, 5, and 9 h). The result revealed that MgH2–LiAlH4 composites milled for 2 h decompose in the temperature ranges of ∼130–183°C; meanwhile, after the MgH2–LiAlH4 composites were milled for 5 h, the composites start to release hydrogen at 102°C. However, the capacity of hydrogen released decreased compared with 2 h milled composites. In addition to that, the initial desorption temperature decreases to 86°C when the milling time increases to 9 h, but the amount of hydrogen released also decreases. The XRD pattern showed that the peaks of Li3AlH6 and Al appeared after milling the MgH2–LiAlH4 composites up to 5 h. Interestingly, milling up to 9 h proved that the intensity peaks of Li3AlH6 and Al become stronger. This indicated that more LiAlH4 has been decomposed into Li3AlH6 and Al, accounting for the lowest onset desorption temperature. Based on the results obtained, the lower decomposition temperature was attributed to the decomposition of LiAlH4 that had occurred, and more LiAlH4 decomposed as the milling time increased. In addition, the peaks of the Mg17Al12 phase can also be detected when the MgH2–LiAlH4 composites were heated to 250°C. Furthermore, Ding et al. (Ding et al., 2013) also studied the reversibility of the destabilized MgH2–LiAlH4 composite under a hydrogen pressure of 3 MPa and at 300°C, and the results show that the MgH2–LiAlH4 composite exhibits fast ab/desorption kinetics in the first two cycles, but the ab/desorption kinetics worsened during the third cycle, as shown in Figure 8. Moreover, SEM images indicated that the morphology of MgH2–LiAlH4 composites was smaller. A reduction in the particle size and crystallite size results in the introduction of high surface defect density and the creation of more grain boundaries. In addition to that, a high density of the nanosized catalyst particles forms a large number of nucleation sites at the surface of the LiAlH4 matrix, leading to the larger surface area of LiAlH4 particles, as indicated by Zhai et al. (Zhai et al., 2012). Xia et al. (Xia et al., 2020) also stated that the morphological change should be beneficial for the enhancement of the desorption properties of LiAlH4, owing to the reduction of the particle size and the process of creating small crystallite sizes. Halim Yap et al. (Halim Yap et al., 2019), in their study, revealed that the decrement of the grain sizes led to the increment of the contact surface area. As a result, the desorption reaction of hydrogen has been improved due to the reduction of the hydrogen diffusion length. A study conducted by Czujko et al. (Czujko et al., 2011) revealed that the average particle size of MgH2+50 wt% LiAlH4 composites was reduced to ∼3.5 ± 2.7 µm. It demonstrated that during MgH2 ball milling, lithium alanate could act as a lubricant, and the reduction of particle size is much less efficient when the LiAlH4 additive level reaches 50 wt.%. Based on this subsection, appropriate milling time is beneficial to the Mg–Li–Al systems. This indicates that the milling time at a suitable time is helpful to improve the hydrogen storage performance of the Mg–Li–Al system. The variation of the milling duration has obvious effects on the onset desorption temperature, activation energy, and morphology of the samples.
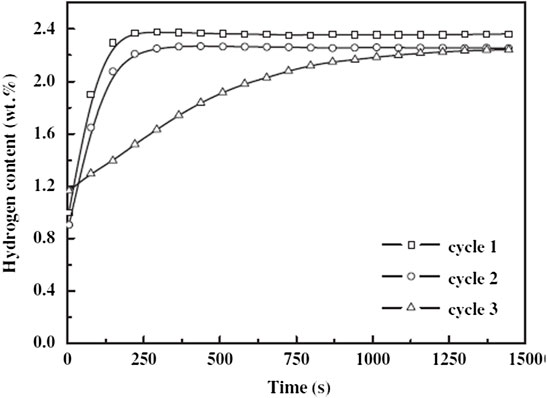
FIGURE 8. Reversibility study for the initial three cycles of the destabilized MgH2–LiAlH4 composite under a hydrogen pressure of 3 MPa and at 300°C (Ding et al., 2013).
The Effect of Different Additives
A study conducted by Halim Yap and Ismail (Halim Yap & Ismail, 2017) indicated that the hydrogen sorption properties of the MgH2–LiAlH4 system can be enhanced by the addition of K2ZrF6. The onset desorption temperature for 4MgH2–LiAlH4 exhibited two significant stages. For the 4MgH2–LiAlH4 systems, the onset desorption temperature was 135 and 275°C for the first and second desorption stages, with the total amount of hydrogen desorption being 7.5 wt.%. After the addition of 10 wt.% K2ZrF6, the desorption temperature for the first and second stages was decreased by 40 and 25°C, respectively. In addition, 4MgH2–LiAlH4 + 10 wt.% K2ZrF6 demonstrates better kinetics of desorption, and the value of activation energy was decreased to 102.9 kJ/mol compared to the undoped composites (129.8 kJ/mol). However, the absorption kinetics under 33.0 atm at 320°C exposed that adding 10 wt.% of K2ZrF6 to 4MgH2–LiAlH4 showed no improvement in the absorption of hydrogen. Meanwhile, the SEM images for comparing the morphology of undoped and doped samples are shown in Figure 9. The doped samples show that the particles size is less agglomerated and smaller as in Figure 9D than the undoped samples (Figure 9C). This result was also supported by Ranjbar et al. (Ranjbar et al., 2010) who suggested that the smaller particle size improves hydrogen ab/desorption as it makes the particle larger surface area and reduces the diffusion length of hydrogen.
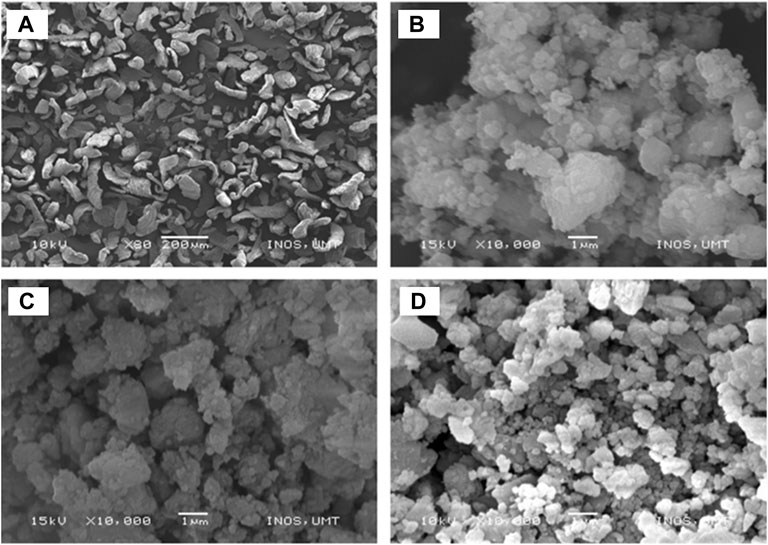
FIGURE 9. SEM images for the (A) as-received MgH2, (B) as-milled MgH2, (C) 4MgH2-LiAlH4, and (D) 4MgH2-LiAlH4 + 10 wt.% K2ZrF6 (Halim Yap & Ismail, 2017).
Further research indicated that the new peaks of Al3Zr and KH (indicating LiAlH4 react with K2ZrF6) were formed after 4MgH2–LiAlH4 + 10 wt.% K2ZrF6 were heated at 200°C. In addition, the peaks of MgH2 were also present as well as LiH and Al (illustrated the decomposition as in Eq. 2). Heating up to 450°C, the peaks of Mg, Li0.92Mg4.08, and Mg17Al12 were detected, whereas the Al3Zr and KH peaks remained unchanged. Furthermore, the XRD pattern of absorption for K2ZrF6-doped 4MgH2–LiAlH4 sample at 300°C also exposed the peaks of Al3Zr, KH, LiH, and Al remain unchanged. However, the peaks of the Mg17Al12 and Li0.92Mg4.08 disappeared, and it is suggested that a reaction occurred during the absorption process, as indicated in Eqs 6, 7. The amount of K2ZrF6 was increased to 20 wt.% to obtain a better insight into the F-containing, Zr-containing, and K-containing phase structures. New minor peaks attributed to LiF were detected along with the KH and Al3Zr phases. Therefore, it is recognized that the new LiF, KH, and Al3Zr products created during the heating process worked together as active components to work on improving the 4MgH2–LiAlH4 system of the hydrogen storage performance. The hydrogen storage properties of MgH2/LiAlH4 were improved by the addition of SrFe12O19, as suggested by Sulaiman and Ismail (Sulaiman & Ismail, 2017). The result disclosed that the addition of 5 wt.% of SrFe12O19 resulted in a decrease of 40 and 10°C in the first and second stages of desorption, respectively, compared to the MgH2/LiAlH4 system. The doped samples begin to release hydrogen at ∼80°C for the first stages and ∼260°C for the second stages. Interestingly, the hydrogen released by the doped samples was 7.1 wt.%, which is the amount of hydrogen released equivalent to milled MgH2. The energy barriers for the release of hydrogen affected the kinetic desorption performance of the samples. From the calculation of as-received MgH2, the activation energy was 175 kJ/mol. However, the activation energy was decreased to 133 kJ/mol after MgH2 was milled for 1 h. This proves that the value of the activation energy is also affected by the milling process (Sabitu & Goudy, 2012; Ismail, 2015; Lin et al., 2015; Zhang et al., 2017). Furthermore, after destabilizing MgH2 with LiAlH4, the activation energy was reduced to 121 kJ/mol, which showed a reduction of 12 kJ/mol compared to the milled MgH2 (133 kJ/mol). The improvement of desorption kinetics is related to the energy barrier for the hydrogen release from the composite. Lower activation energy means faster kinetics. In this context, the activation energy is the least energy required to instigate the decomposition process of the system (Ismail et al., 2020). The activation energy decreased to 104 kJ/mol, after the addition of 5 wt.% SrFe12O19 to 4MgH2–LiAlH4. Furthermore, these findings appear to be comparable to the previous studies reporting on the role of catalysts in reducing the activation energy, leading to improved dehydriding kinetics (Sazelee et al., 2019). Conversely, the newly developed products formed during the heating process of in situ Li2Fe3O4 and Al2Sr exhibit a synergistically catalytic effect on the improvement of the 4MgH2–LiAlH4 composites.
According to Mao et al. (Mao et al., 2011), dehydrogenation has been improved after LiAlH4 was combined with MgH2, in which the first-stage desorption temperature is close to LiAlH4 (∼150°C), while the second-stage desorption was completed at 233°C. This suggested that in the binary LiAlH4–MgH2 system, a mutual destabilization occurred. However, after being doped with TiF3, hydrogen starts to release at ∼60°C (100°C lower than the undoped LiAlH4–MgH2 system). The desorption and absorption kinetics were also improved after the addition of TiF3. For the LiAlH4–MgH2–TiF3 system, the amount of hydrogen desorbed was 2.48 wt.% after 10 min, compared to the LiAlH4–MgH2 system (1.59 wt.%) at 300°C. Furthermore, the reversibility of this system was performed at 300°C under ∼2 MPa for both samples. LiAlH4–MgH2–TiF3 systems demonstrate the ability to absorb 2.68 wt.% hydrogen after 5 min, which is greater than the LiAlH4–MgH2 system (1.75 wt.%). Further study showed that the intermediate phase of Mg17Al12 and Li3Mg7 produced during the heating process is mainly due to the Al/LiH reaction with MgH2, as shown in Eqs 5, 8:
The hydrogen sorption properties of 4MgH2–LiAlH4 were greatly improved after the addition of 5 wt.% Fe2O3, as eloquently stated by Mustafa et al. (Mustafa & Ismail, 2014). As-milled MgH2 can release hydrogen at 350°C; meanwhile, the as-milled LiAlH4 can release at 135–160°C. For the destabilized system of 4MgH2–LiAlH4, the onset desorption temperature was reduced similar to the as-milled LiAlH4. However, after the addition of Fe2O3, the onset of desorption was decreased to 95°C. The desorption and absorption kinetics were also improved after the addition of Fe2O3. The apparent activation energy of 4MgH2–LiAlH4 + Fe2O3 was reduced to 117 kJ/mol compared to the undoped 4MgH2–LiAlH4 systems. Further research exposed that the Li2Fe3O4 was developed by heating 4MgH2–LiAlH4 + Fe2O3 up to 400°C and revealed that the Li2Fe3O4 also plays a crucial role in reducing the value of desorption temperature and activation energy in the 4MgH2–LiAlH4 systems.
According to Wan et al. (Wan et al., 2013), the hydrogen storage performance of MgH2–LiAlH4 was effectively improved after the addition of MnFe2O4 nanoparticles. As indicated in Table 3, the onset desorption temperature for MgH2–LiAlH4 + 5 mol% of MnFe2O4 and MgH2–LiAlH4 + 7 mol% of MnFe2O4 revealed the lowest onset desorption temperature. However, the total amount of hydrogen released for MgH2–LiAlH4 + 5 mol% of MnFe2O4 is higher than the addition of 7 mol% of MnFe2O4. Nonetheless, the addition of MnFe2O4 can reduce the onset desorption temperature of the MgH2–LiAlH4 systems.

TABLE 3. Onset desorption temperature and the total amount of hydrogen released for MgH2–LiAlH4 and MgH2–LiAlH4 + xMnFe2O4 composites (x = 1, 2, 5, and 7 mol% of MnFe2O4 nanoparticles) (Wan et al., 2013).
For the desorption kinetics at 200°C, under 0.1 MPa, the MgH2–LiAlH4 systems release 0.94 wt.% hydrogen, whereas the MgH2–LiAlH4 + 5 mol% of MnFe2O4 can release 2.91 wt.%. Furthermore, the reversibility for those samples was investigated at 300°C under 3 MPa, and the doped samples show better absorption kinetics than the undoped samples. For MgH2–LiAlH4 + 5 mol% of MnFe2O4, a hydrogen absorption capacity of 3.64 wt.% was achieved within 300 s. In the meantime, the MgH2–LiAlH4 systems only absorbed 2.81 wt.% of hydrogen under the same conditions. Moreover, after heating up to 400°C, the XRD pattern shows the peaks of Li0.92Mg4.08 and Mg17Al12. Furthermore, the new peak of Fe0.872O observed also indicated that the interaction between LiAlH4 and MnFe2O4 had occurred. However, no Mn-containing peak has been seen due to the low amount of MnFe2O4 that has been used. Also, the XRD pattern observed after the absorption kinetics at 300°C stated that no peaks of Li0.92Mg4.08 and Mg17Al12 have been detected. The peaks of Fe0.872O can still be seen in the XRD pattern of the absorption results. Therefore, they concluded that the in situ formed Fe oxide and the Mn-containing peak enhanced hydrogen storage performances of the MgH2–LiAlH4 system.
The impact of various additives on the hydrogen storage properties of the MgH2-LiAlH4 system was studied by Ismail et al. (Ismail et al., 2011). Milled MgH2 starts to decompose at 330°C and desorb about 7.1 wt.% of hydrogen at 420°C. Meanwhile, the as-milled LiAlH4 decomposes at ∼142°C for the first and ∼173°C for the second stage. After the two hydrides (MgH2–LiAlH4) with ratio 4:1 have been mixed, the samples began to decompose at 130°C for the first stage (attributed to the decomposition of LiAlH4), while at 270°C for the second stages (corresponding to the decomposition of Li3AlH6). The 4MgH2–LiAlH4 was completed at ∼360°C with 7.5 wt.% of hydrogen released (attributed to the decomposition of MgH2). After the addition of metal halides, the temperature-programmed desorption (TPD) curves of 4MgH2–LiAlH4 systems were significantly improved. TiF3 followed by NiF2, CrF2, NbF5, and YF3 showed a strong catalytic influence on the decomposition of MgH2–LiAlH4, as shown in Figure 10. The MgH2–LiAlH4 composite doped with TiF3 begins to decompose at 70°C. However, the desorption kinetics of the MgH2–LiAlH4 composite were significantly enhanced after the addition of 5 wt.% of metal halides. Furthermore, the addition of metal halide additives could reduce the activation energy of the MgH2–LiAlH4 composite. The apparent activation energy for the MgH2–LiAlH4 composite with the selected different metal halides is shown in Table 4.
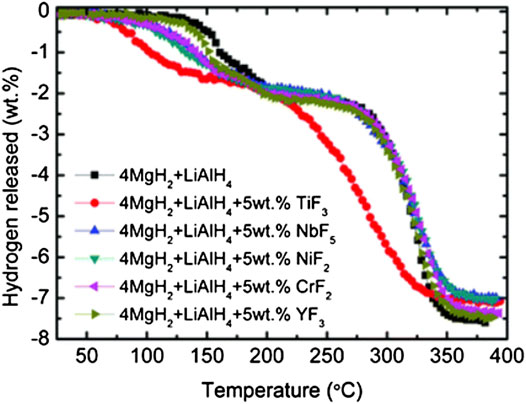
FIGURE 10. Decomposition temperature results of the MgH2-LiAlH4 composite with different selected metal halides (Ismail et al., 2011).
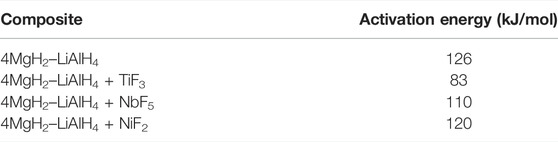
TABLE 4. Apparent activation energy for the MgH2-LiAlH4 composite with different selected metal halides (Ismail et al., 2011).
In order to study the phase structure of these samples, the 4MgH2–LiAlH4 samples were characterized by using XRD. After the samples were heated up to 400°C, apart from Mg, the intermediate phases of Li0.92Mg4.08 and Al12Mg17 were eventually created in the composite system. The XRD measurements were also carried out on the absorption kinetics. The results showed that the peaks of Li0.92Mg4.08 and Al12Mg17 disappeared; meanwhile, the appearance of peaks of Al3Mg2 indicated that the reaction, as in Eqs 6, 7, occurred during the absorption process. For the doped samples, further research showed that LiF and Al3Ti are believed to act as the actual catalyst that can enhance the interaction of the MgH2–LiAlH4 system, while speeding up the hydrogen desorption process of the MgH2–LiAlH4 system. According to Mustafa et al. (Mustafa et al., 2015), the addition of K2TiF6 improves the 4MgH2–LiAlH4 system of hydrogen storage performance. The desorption temperature of the 4MgH2–LiAlH4 system was reduced to 80 and 250°C for the first and second stages, respectively, after the addition of K2TiF6. Meanwhile, the 4MgH2–LiAlH4 composite decomposed at 130 and 270°C for the first and second stages, respectively. In addition, after the addition of K2TiF6, desorption and absorption kinetics were also enhanced. The activation energy for 4MgH2–LiAlH4 systems has also been reduced from 126 to 107 kJ/mol. The XRD analysis was conducted on 4MgH2–LiAlH4 + K2TiF6 for the possible reaction of catalytic additives on the 4MgH2–LiAlH4 systems. The intermediate phases of Li0.92Mg4.08, Al12Mg17, and Mg were eventually formed after desorption at 400°C. The complete recovery of LiH and MgH2 from the Li–Mg and Al–Mg alloys was accomplished in the absorption samples due to the reaction of Al12Mg17 and Li0.92Mg4.08 with hydrogen. Further verification stated that the peaks of TiH2, LiF, and Al3Ti act as the real catalyst, thus proving that the addition of K2TiF6 enhanced the sorption properties of the 4MgH2–LiAlH4 systems.
Recently, Sulaiman et al. (Sulaiman et al., 2021a) observed an improvement in the onset desorption temperature and the morphology of the 4MgH2–LiAlH4 systems when 5 wt.% of Al2TiO5 was added. The hydrogen started to release at 85°C which is decreased by 35°C for the undoped systems. It is important to note that the inclusion of Al2TiO5 to the 4MgH2–LiAlH4 systems resulted in significantly smaller particle sizes which help to shorten the diffusion length and larger nucleation sites. Moreover, based on the XRD result, the new in situ active species of LiTi2O4, TiH2, and AlTi2 were detected after the de/rehydrogenation process which is believed to act as a true catalyzer in improving the hydrogen storage performance of the Al2TiO5-doped Mg–Li–Al systems. From the results, it is noted that the addition of additives ameliorates the performance of the MgH2–LiAlH4 composite by reducing the onset decomposition temperature and fastening the sorption kinetics performance than the unary MgH2 and LiAlH4, as demonstrated in Table 5. Table 5 presents the onset desorption temperature, total desorption, absorption capacity, and activation energy for the MgH2–LiAlH4 system doped with several additives. The undoped MgH2, LiAlH4, and MgH2–LiAlH4 systems are also included in Table 5 for comparison purposes.
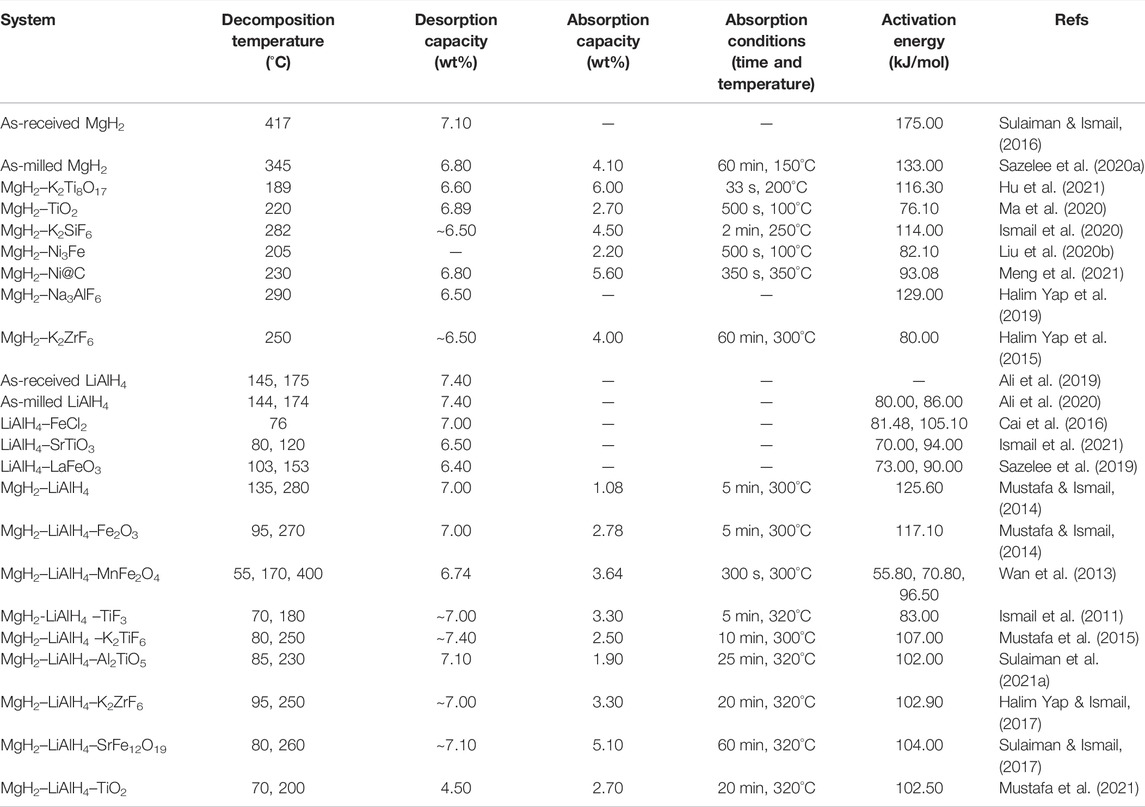
TABLE 5. Hydrogen storage performance of the Mg–Li–Al doped system with several additives compared with the undoped Mg–Li–Al system and unary MgH2 and LiAlH4.
Based on the abovementioned discussion and Table 5, it can be stated that the addition of the additives significantly enhanced the hydrogen storage performance of the MgH2–LiAlH4 systems. It is reported that the active species that are in situ formed during the heating process are believed to play a catalytic role in enhancing the hydrogen sorption performance of the MgH2–LiAlH4 additive system. Up to this date, the addition of MnFe2O4 to Mg–Li–Al composites has presented the best performance which can release hydrogen approximately at 55°C (Wan et al., 2013). In addition, the MgH2–LiAlH4–MnFe2O4 system can absorb 3.64 wt.% of hydrogen in only 300 s and desorb more hydrogen (approximately 4 wt.% in 200 s), which shows a better performance in the sorption kinetics of MgH2–LiAlH4 systems.
Challenges and Possible Development Strategies
Continuous plans to improve solid-state hydrogen storage materials will undoubtedly demonstrate a further positive effect on the development of hydrogen storage technologies and the widespread use of hydrogen in global energy transitions. Continuous research to identify new hydrogen storage materials indicates that the Mg–Li–Al system is a promising material for the future storage of hydrogen. Although the destabilized system of the Mg–Li–Al system has attracted a lot of attention and many types of research and development were carried out in this field, some problems and challenges still exist in achieving a suitable hydrogen storage material for practical applications. A few possible developmental strategies are listed as follows:
1) The addition of additives has shown considerable promise in improving the Mg–Li–Al system’s performance. It is interesting to investigate the effect of other catalysts/additives to boost the performance of the Mg–Li–Al system and to understand the way catalysts/additives have an effect on improving the hydrogen storage properties of the Mg–Li–Al system.
2) The investigation on the reversible absorbs and desorbs hydrogen of the Mg–Li–Al system under moderate temperature and pressure must be the main target, and significant work is required to find the solution for the release and hydrogen uptake kinetics deteriorated during the cycling process.
3) It is reported that the formation of the Mg2Al3 during the rehydrogenation process has a negative effect on the hydrogen capacity and kinetic performance of the Mg–Li–Al system. The formation of Mg2Al3 could be avoided by applying a high pressure of hydrogen (> 10 MPa) during the rehydrogenation process. It is necessary to explore the ways of preventing the formation of Mg2Al3 without applying a high pressure of hydrogen, such as by using an appropriate additive or catalyst.
4) The hydrogen storage performance of the Mg–Li–Al system has been discovered to be influenced by the molar ratio and milling time. Furthermore, it is critical to investigate the other approaches, such as embedding materials in nanoconfinement, which could improve the hydrogen storage properties of the Mg–Li–Al system.
Therefore, we believe that with continuous effort, the limitations on the development of the Mg–Li–Al system as an ideal hydrogen storage material might be overcome and that the Mg–Li–Al system with favorable kinetics and thermodynamics should be one of the near-term goals.
Conclusion
In this review, it was clear that the transition from the current energy economy to cleaner energy like hydrogen was motivated by environmental and economic factors. Possible current approaches to store hydrogen are in the liquid state, compressed gas state, and solid state. However, due to the large amount of hydrogen that can be stored in a small amount and safety considerations, solid-state hydrogen storage systems are attractive to research. This comprehensive review highlighted the higher desorption temperature and sluggish sorption kinetics in MgH2, which can be overcome through the destabilization concept (addition of LiAlH4). Many researchers explored the reaction between the Mg–Li–Al system, including the ratio, the milling time, and the addition of an additive/catalyst to this composite. Interestingly, the doping Mg–Li–Al system with the catalyst can reduce the onset desorption temperature to below 60°C. The intermediate forms of Li0.92Mg4.08 and Mg17Al12 were eventually formed in the Mg–Li–Al composites. Cycling measurements show that Li0.92Mg4.08 and Mg17Al12 are fully reversible absorbs and desorbs of hydrogen. However, the Mg–Li–Al composites are still in their early development and need more time to prove themselves as viable long-term solutions for solid-state hydrogen storage. Further study, such as on doping with other additives/catalysts, could investigate the different milling times and ratios that should be focused on for the further design of advanced solid-state hydrogen storage materials.
Author Contributions
All authors listed have made a substantial, direct, and intellectual contribution to the work and approved it for publication.
Funding
This work was financially supported by the Golden Goose Research Grant (GGRG) VOT 55190, University Malaysia Terengganu and Casa Armada Sdn. Bhd. VOT 53468.
Conflict of Interest
MG was employed by the company Casa Armada Sdn. Bhd.
The remaining authors declare that the research was conducted in the absence of any commercial or financial relationships that could be construed as a potential conflict of interest.
Publisher’s Note
All claims expressed in this article are solely those of the authors and do not necessarily represent those of their affiliated organizations, or those of the publisher, the editors, and the reviewers. Any product that may be evaluated in this article, or claim that may be made by its manufacturer, is not guaranteed or endorsed by the publisher.
Acknowledgments
The authors would like to acknowledge Universiti Malaysia Terengganu for providing complete facilities to perform this research. SS and MI thank the World Class Professor Program 2021 managed by the Indonesian Ministry of Education, Culture, Research and Technology. N. A. Sazelee and N. A. Ali are grateful for the BUMT and SIPP scholarship provided by UMT.
References
Abdin, Z., Zafaranloo, A., Rafiee, A., Mérida, W., Lipiński, W., and Khalilpour, K. R. (2020). Hydrogen as an Energy Vector. Renew. Sust. Energ. Rev. 120, 109620. doi:10.1016/j.rser.2019.109620
Ali, N. A., Idris, N. H., Sazelee, N. A., Yahya, M. S., Yap, F. A. H., and Ismail, M. (2019). Catalytic Effects of MgFe2O4 Addition on the Dehydrogenation Properties of LiAlH4. Int. J. Hydrogen Energ. 44 (52), 28227–28234. doi:10.1016/j.ijhydene.2019.09.083
Ali, N. A., and Ismail, M. (2021). Advanced Hydrogen Storage of the Mg-Na-Al System: A Review. J. Magnesium Alloys 9 (4), 1111–1122. doi:10.1016/j.jma.2021.03.031
Ali, N. A., Sazelee, N. A., and Ismail, M. (2021). An Overview of Reactive Hydride Composite (RHC) for Solid-State Hydrogen Storage Materials. Int. J. Hydrogen Energ. 46 (62), 31674–31698. doi:10.1016/j.ijhydene.2021.07.058
Ali, N. A., Sazelee, N., Yahya, M. S., and Ismail, M. (2020). Influence of K2NbF7 Catalyst on the Desorption Behavior of LiAlH4. Front. Chem. 8 (457), 457. doi:10.3389/fchem.2020.00457
Baricco, M., Rahman, M. W., Livraghi, S., Castellero, A., Enzo, S., and Giamello, E. (2012). Effects of BaRuO3 Addition on Hydrogen Desorption in MgH2. J. Alloys Comp. 536, S216–S221. doi:10.1016/j.jallcom.2011.12.008
Barkhordarian, G., Klassen, T., Dornheim, M., and Bormann, R. (2007). Unexpected Kinetic Effect of MgB2 in Reactive Hydride Composites Containing Complex Borohydrides. J. Alloys Comp. 440 (1), L18–L21. doi:10.1016/j.jallcom.2006.09.048
Bendyna, J. K., Dyjak, S., and Notten, P. H. L. (2015). The Influence of ball-milling Time on the Dehydrogenation Properties of the NaAlH4-MgH2 Composite. Int. J. Hydrogen Energ. 40 (11), 4200–4206. doi:10.1016/j.ijhydene.2015.01.026
Cai, J., Zang, L., Zhao, L., Liu, J., and Wang, Y. (2016). Dehydrogenation Characteristics of LiAlH 4 Improved by In-Situ Formed Catalysts. J. Energ. Chem. 25 (5), 868–873. doi:10.1016/j.jechem.2016.06.004
Chen, R., Wang, X., Xu, L., Chen, L., Li, S., and Chen, C. (2010). An Investigation on the Reaction Mechanism of LiAlH4-MgH2 Hydrogen Storage System. Mater. Chem. Phys. 124 (1), 83–87. doi:10.1016/j.matchemphys.2010.05.070
Correa-Jullian, C., and Groth, K. M. (2022). Data Requirements for Improving the Quantitative Risk Assessment of Liquid Hydrogen Storage Systems. Int. J. Hydrogen Energ. 47 (6), 4222–4235. doi:10.1016/j.ijhydene.2021.10.266
Crivello, J.-C., Denys, R. V., Dornheim, M., Felderhoff, M., Grant, D. M., Huot, J., et al. (2016). Mg-based Compounds for Hydrogen and Energy Storage. Appl. Phys. A. 122 (2), 85. doi:10.1007/s00339-016-9601-1
Czujko, T., Zaranski, Z., Malka, I. E., and Wronski, Z. (2011). Composite Behaviour of MgH2 and Complex Hydride Mixtures Synthesized by ball Milling. J. Alloys Comp. 509, S604–S607. doi:10.1016/j.jallcom.2010.08.133
Daulbayev, C., Lesbayev, B., Bakbolat, B., Kaidar, B., Sultanov, F., Yeleuov, M., et al. (2022). A Mini-Review on Recent Trends in Prospective Use of Porous 1D Nanomaterials for Hydrogen Storage. South Afr. J. Chem. Eng. 39, 52–61. doi:10.1016/j.sajce.2021.11.008
David, E. (2005). An Overview of Advanced Materials for Hydrogen Storage. J. Mater. Process. Tech. 162-163, 169–177. doi:10.1016/j.jmatprotec.2005.02.027
Dematteis, E. M., Cuevas, F., and Latroche, M. (2021). Hydrogen Storage Properties of Mn and Cu for Fe Substitution in TiFe0.9 Intermetallic Compound. J. Alloys Comp. 851, 156075. doi:10.1016/j.jallcom.2020.156075
Ding, X., Zhu, Y., Wei, L., Li, Y., and Li, L. (2013). Synergistic Hydrogen Desorption of HCS MgH2 + LiAlH4 Composite. Energy 55, 933–938. doi:10.1016/j.energy.2013.04.043
Doğan, M., Sabaz, P., Bi̇ci̇l, Z., Koçer Kizilduman, B., and Turhan, Y. (2020). Activated Carbon Synthesis from Tangerine Peel and its Use in Hydrogen Storage. J. Energ. Inst. 93 (6), 2176–2185. doi:10.1016/j.joei.2020.05.011
Dornheim, M., Doppiu, S., Barkhordarian, G., Boesenberg, U., Klassen, T., Gutfleisch, O., et al. (2007). Hydrogen Storage in Magnesium-Based Hydrides and Hydride Composites. Scripta Materialia 56 (10), 841–846. doi:10.1016/j.scriptamat.2007.01.003
Dunn, S. (2002). Hydrogen Futures: toward a Sustainable Energy System. Int. J. Hydrogen Energ. 27 (3), 235–264. doi:10.1016/S0360-3199(01)00131-8
Eftekhari, A., and Fang, B. (2017). Electrochemical Hydrogen Storage: Opportunities for Fuel Storage, Batteries, Fuel Cells, and Supercapacitors. Int. J. Hydrogen Energ. 42 (40), 25143–25165. doi:10.1016/j.ijhydene.2017.08.103
El Khatabi, M., Naji, S., Bhihi, M., Benyoussef, A., El Kenz, A., and Loulidi, M. (2018). Effects of Double Substitution on MgH2 Hydrogen Storage Properties: An Ab Initio Study. J. Alloys Comp. 743, 666–671. doi:10.1016/j.jallcom.2017.11.083
Graetz, J., Wegrzyn, J., and Reilly, J. J. (2008). Regeneration of Lithium Aluminum Hydride. J. Am. Chem. Soc. 130 (52), 17790–17794. doi:10.1021/ja805353w
Halim Yap, F. A., Mustafa, N. S., and Ismail, M. (2015). A Study on the Effects of K2ZrF6 as an Additive on the Microstructure and Hydrogen Storage Properties of MgH2. RSC Adv. 5 (12), 9255–9260. doi:10.1039/C4RA12487A
Halim Yap, F. A., Sulaiman, N. N., and Ismail, M. (2019). Understanding the Dehydrogenation Properties of MgH2 Catalysed by Na3AlF6. Int. J. Hydrogen Energ. 44 (58), 30583–30590. doi:10.1016/j.ijhydene.2018.02.073
Hsu, W.-C., Yang, C.-H., Tan, C.-Y., and Tsai, W.-T. (2014b). In Situ synchrotron X-ray Diffraction Study on the Dehydrogenation Behavior of LiAlH4-MgH2 Composites. J. Alloys Comp. 599 (0), 164–169. doi:10.1016/j.jallcom.2014.02.064
Hsu, W.-C., Yang, C.-H., and Tsai, W.-T. (2014a). Catalytic Effect of MWCNTs on the Dehydrogenation Behavior of LiAlH4. Int. J. Hydrogen Energ. 39 (2), 927–933. doi:10.1016/j.ijhydene.2013.10.155
Hu, S., Zhang, H., Yuan, Z., Wang, Y., Fan, G., Fan, Y., et al. (2021). Ultrathin K2Ti8O17 Nanobelts for Improving the Hydrogen Storage Kinetics of MgH2. J. Alloys Comp. 881, 160571. doi:10.1016/j.jallcom.2021.160571
Imamura, H., Masanari, K., Kusuhara, M., Katsumoto, H., Sumi, T., and Sakata, Y. (2005). High Hydrogen Storage Capacity of Nanosized Magnesium Synthesized by High Energy ball-milling. J. Alloys Comp. 386 (1), 211–216. doi:10.1016/j.jallcom.2004.04.145
Ismail, M. (2021). Effect of Adding Different Percentages of HfCl4 on the Hydrogen Storage Properties of MgH2. Int. J. Hydrogen Energ. 46 (12), 8621–8628. doi:10.1016/j.ijhydene.2020.12.068
Ismail, M. (2015). Effect of LaCl 3 Addition on the Hydrogen Storage Properties of MgH 2. Energy 79, 177–182. doi:10.1016/j.energy.2014.11.001
Ismail, M., and Mustafa, N. S. (2016). Improved Hydrogen Storage Properties of NaAlH4MgH2LiBH4 Ternary-Hydride System Catalyzed by TiF3. Int. J. Hydrogen Energ. 41 (40), 18107–18113. doi:10.1016/j.ijhydene.2016.07.090
Ismail, M., Sazelee, N. A., Ali, N. A., and Suwarno, S. (2021). Catalytic Effect of SrTiO3 on the Dehydrogenation Properties of LiAlH4. J. Alloys Comp. 855, 157475. doi:10.1016/j.jallcom.2020.157475
Ismail, M. (2016). The Hydrogen Storage Properties of Destabilized MgH2-AlH3 (2:1) System. Mater. Today Proc. 3 (Suppl. 1), S80–S87. doi:10.1016/j.matpr.2016.01.011
Ismail, M., Yahya, M. S., Sazelee, N. A., Ali, N. A., Yap, F. A. H., and Mustafa, N. S. (2020). The Effect of K2SiF6 on the MgH2 Hydrogen Storage Properties. J. Magnesium Alloys 8 (3), 832–840. doi:10.1016/j.jma.2020.04.002
Ismail, M., Yap, F. A. H., Sulaiman, N. N., and Ishak, M. H. I. (2016). Hydrogen Storage Properties of a Destabilized MgH2Sn System with TiF3 Addition. J. Alloys Comp. 678, 297–303. doi:10.1016/j.jallcom.2016.03.168
Ismail, M., Zhao, Y., and Dou, S. X. (2013). An Investigation on the Hydrogen Storage Properties and Reaction Mechanism of the Destabilized MgH2-Na3AlH6 (4:1) System. Int. J. Hydrogen Energ. 38 (3), 1478–1483. doi:10.1016/j.ijhydene.2012.11.035
Ismail, M., Zhao, Y., Yu, X. B., and Dou, S. X. (2011). Effect of Different Additives on the Hydrogen Storage Properties of the MgH2-LiAlH4 Destabilized System. RSC Adv. 1 (3), 408–414. doi:10.1039/C1RA00209K
Jain, I. P., Lal, C., and Jain, A. (2010). Hydrogen Storage in Mg: A Most Promising Material. Int. J. Hydrogen Energ. 35 (10), 5133–5144. doi:10.1016/j.ijhydene.2009.08.088
Jang, J.-W., Shim, J.-H., Cho, Y. W., and Lee, B.-J. (2006). Thermodynamic Calculation of LiH↔Li3AlH6↔LiAlH4 Reactions. J. Alloys Comp. 420 (1), 286–290. doi:10.1016/j.jallcom.2005.10.040
Jangir, M., Jain, A., Agarwal, S., Zhang, T., Kumar, S., Selvaraj, S., et al. (2018). The enhanced de/re-hydrogenation performance of MgH2 with TiH2 additive. Int. J. Energ. Res 42 (3), 1139–1147. doi:10.1002/er.3911
Jiang, W., Sun, P., Li, P., Zuo, Z., and Huang, Y. (2021). Transient thermal Behavior of Multi-Layer Insulation Coupled with Vapor Cooled Shield Used for Liquid Hydrogen Storage Tank. Energy 231, 120859. doi:10.1016/j.energy.2021.120859
Kato, S., Borgschulte, A., Bielmann, M., and Züttel, A. (2012). Interface Reactions and Stability of a Hydride Composite (NaBH4 + MgH2). Phys. Chem. Chem. Phys. 14 (23), 8360–8368. doi:10.1039/C2CP23491B
Ke, X., and Chen, C. (2007). Thermodynamic Functions and Pressure-Temperature Phase Diagram of Lithium Alanates Byab Initiocalculations. Phys. Rev. B 76 (2), 024112. doi:10.1103/PhysRevB.76.024112
Khurana, T., Prasad, B., Ramamurthi, K., and Murthy, S. (2006). Thermal Stratification in Ribbed Liquid Hydrogen Storage Tanks. Int. J. Hydrogen Energ. 31 (15), 2299–2309. doi:10.1016/j.ijhydene.2006.02.032
Kojima, Y. (2019). Hydrogen Storage Materials for Hydrogen and Energy Carriers. Int. J. Hydrogen Energ. 44 (33), 18179–18192. doi:10.1016/j.ijhydene.2019.05.119
Léon, A., Zabara, O., Sartori, S., Eigen, N., Dornheim, M., Klassen, T., et al. (2009). Investigation of (Mg, Al, Li, H)-based Hydride and Alanate Mixtures Produced by Reactive ball Milling. J. Alloys Comp. 476 (1-2), 425–428. doi:10.1016/j.jallcom.2008.09.023
Li, X., Qin, Y., Fu, J., and Zhao, J. (2015). A Gupta Potential for Magnesium in Hcp Phase. Comput. Mater. Sci. 98, 328–332. doi:10.1016/j.commatsci.2014.11.023
Li, Z., Wang, H., Ouyang, L., Liu, J., and Zhu, M. (2019). Achieving superior De-/hydrogenation Properties of C15 Laves Phase Y-Fe-Al Alloys by A-Side Substitution. J. Alloys Comp. 787, 158–164. doi:10.1016/j.jallcom.2019.02.074
Liang, Z., Yao, Z., Xiao, X., Kou, H., Luo, W., Chen, C., et al. (2020). The Functioning Mechanism of Al Valid Substitution for Co in Improving the Cycling Performance of Zr-Co-Al Based Hydrogen Isotope Storage Alloys. J. Alloys Comp. 848, 156618. doi:10.1016/j.jallcom.2020.156618
Lin, H.-J., Matsuda, J., Li, H.-W., Zhu, M., and Akiba, E. (2015). Enhanced Hydrogen Desorption Property of MgH2 with the Addition of Cerium Fluorides. J. Alloys Comp. 645, S392–S396. doi:10.1016/j.jallcom.2014.12.102
Lin, I.-C., and Tsai, W.-T. (2017). “In Situ synchrotron X-ray Diffraction Study on the Rehydrogenation Behavior of MgH2-LiAlH4 Composites,” in SituSynchrotron X-ray Diffraction Study on the Rehydrogenation Behavior of MgH2-LiAlH4 Composites. Sapporo, Japan: International Conference on Applied System Innovation, 1918–1921. doi:10.1109/ICASI.2017.7988326
Liu, C., Guo, P., Qiao, Y., and Zhang, S. (2020a). A First-Principle Study on the Formation and Migration of AlH3 Defect on (1 1 2) NaAlH4 Surface. Chem. Phys. 538, 110871. doi:10.1016/j.chemphys.2020.110871
Liu, H., Lu, C., Wang, X., Xu, L., Huang, X., Wang, X., et al. (2021). Combinations of V2C and Ti3C2 MXenes for Boosting the Hydrogen Storage Performances of MgH2. ACS Appl. Mater. Inter. 13 (11), 13235–13247. doi:10.1021/acsami.0c23150
Liu, H., Wang, X., Liu, Y., Dong, Z., Cao, G., Li, S., et al. (2013). Improved hydrogen storage properties of MgH2 by ball milling with AlH3: preparations, de/rehydriding properties, and reaction mechanisms. J. Mater. Chem. A. 1 (40), 12527–12535. doi:10.1039/c3ta11953j
Liu, H., Wang, X., Liu, Y., Dong, Z., Ge, H., Li, S., et al. (2014). Hydrogen Desorption Properties of the MgH2-AlH3 Composites. J. Phys. Chem. C 118 (1), 37–45. doi:10.1021/jp407018w
Liu, J., Ma, Z., Liu, Z., Tang, Q., Zhu, Y., Lin, H., et al. (2020b). Synergistic Effect of rGO Supported Ni3Fe on Hydrogen Storage Performance of MgH2. Int. J. Hydrogen Energ. 45 (33), 16622–16633. doi:10.1016/j.ijhydene.2020.04.104
Lu, X., Zhang, L., Yu, H., Lu, Z., He, J., Zheng, J., et al. (2021). Achieving superior Hydrogen Storage Properties of MgH2 by the Effect of TiFe and Carbon Nanotubes. Chem. Eng. J. 422, 130101. doi:10.1016/j.cej.2021.130101
Luo, Q., Li, J., Li, B., Liu, B., Shao, H., and Li, Q. (2019). Kinetics in Mg-Based Hydrogen Storage Materials: Enhancement and Mechanism. J. Magnesium Alloys 7 (1), 58–71. doi:10.1016/j.jma.2018.12.001
Ma, Z., Liu, J., Zhu, Y., Zhao, Y., Lin, H., Zhang, Y., et al. (2020). Crystal-facet-dependent Catalysis of Anatase TiO2 on Hydrogen Storage of MgH2. J. Alloys Comp. 822, 153553. doi:10.1016/j.jallcom.2019.153553
Ma, Z., Panda, S., Zhang, Q., Sun, F., Khan, D., Ding, W., et al. (2021). Improving Hydrogen Sorption Performances of MgH2 through Nanoconfinement in a Mesoporous CoS Nano-Boxes Scaffold. Chem. Eng. J. 406, 126790. doi:10.1016/j.cej.2020.126790
Mao, J. F., Yu, X. B., Guo, Z. P., Liu, H. K., Wu, Z., and Ni, J. (2009). Enhanced Hydrogen Storage Performances of NaBH4-MgH2 System. J. Alloys Comp. 479 (1-2), 619–623. doi:10.1016/j.jallcom.2009.01.012
Mao, J., Guo, Z., Yu, X., Ismail, M., and Liu, H. (2011). Enhanced Hydrogen Storage Performance of LiAlH4-MgH2-TiF3 Composite. Int. J. Hydrogen Energ. 36 (9), 5369–5374. doi:10.1016/j.ijhydene.2011.02.001
Marques, F., Pinto, H. C., Figueroa, S. J. A., Winkelmann, F., Felderhoff, M., Botta, W. J., et al. (2020). Mg-containing Multi-Principal Element Alloys for Hydrogen Storage: A Study of the MgTiNbCr0.5Mn0.5Ni0.5 and Mg0.68TiNbNi0.55 Compositions. Int. J. Hydrogen Energ. 45 (38), 19539–19552. doi:10.1016/j.ijhydene.2020.05.069
Meng, Q., Huang, Y., Ye, J., Xia, G., Wang, G., Dong, L., et al. (2021). Electrospun Carbon Nanofibers with In-Situ Encapsulated Ni Nanoparticles as Catalyst for Enhanced Hydrogen Storage of MgH2. J. Alloys Comp. 851, 156874. doi:10.1016/j.jallcom.2020.156874
Milanović, I., Milošević, S., Matović, L., Vujasin, R., Novaković, N., Checchetto, R., et al. (2013). Hydrogen Desorption Properties of MgH2/LiAlH4 Composites. Int. J. Hydrogen Energ. 38 (27), 12152–12158. doi:10.1016/j.ijhydene.2013.05.020
Montone, A., Aurora, A., Mirabile Gattia, D., and Vittori Antisari, M. (2010). On the Barriers Limiting the Reaction Kinetics between Catalysed Mg and Hydrogen. Scripta Materialia 63 (4), 456–459. doi:10.1016/j.scriptamat.2010.05.003
Mulas, G., Campesi, R., Garroni, S., Napolitano, E., Milanese, C., Dolci, F., et al. (2012). Hydrogen Storage in 2NaBH4+MgH2 Mixtures: Destabilization by Additives and Nanoconfinement. J. Alloys Comp. 536, S236–S240. doi:10.1016/j.jallcom.2011.12.042
Mustafa, N. S., Idris, N. H., and Ismail, M. (2015). Effect of K 2 TiF 6 Additive on the Hydrogen Storage Properties of 4MgH 2 -LiAlH 4 Destabilized System. Int. J. Hydrogen Energ. 40 (24), 7671–7677. doi:10.1016/j.ijhydene.2014.10.112
Mustafa, N. S., and Ismail, M. (2014). Enhanced Hydrogen Storage Properties of 4MgH2 + LiAlH4 Composite System by Doping with Fe2O3 Nanopowder. Int. J. Hydrogen Energ. 39 (0), 7834–7841. doi:10.1016/j.ijhydene.2014.02.118
Mustafa, N. S., Yahya, M. S., Itam Sulaiman, N. N., Abdul Halim Yap, M. F. A., and Ismail, M. (2021). Enhanced the Hydrogen Storage Properties and Reaction Mechanisms of 4MgH 2 + LiAlH 4 Composite System by Addition with TiO 2. Int. J. Energ. Res 45 (15), 21365–21374. doi:10.1002/er.7187
Niaz, S., Manzoor, T., and Pandith, A. H. (2015). Hydrogen Storage: Materials, Methods and Perspectives. Renew. Sust. Energ. Rev. 50, 457–469. doi:10.1016/j.rser.2015.05.011
Ouyang, L., Liu, F., Wang, H., Liu, J., Yang, X.-S., Sun, L., et al. (2020). Magnesium-based Hydrogen Storage Compounds: A Review. J. Alloys Comp. 832, 154865. doi:10.1016/j.jallcom.2020.154865
Peláez-Peláez, S., Colmenar-Santos, A., Pérez-Molina, C., Rosales, A.-E., and Rosales-Asensio, E. (2021). Techno-economic Analysis of a Heat and Power Combination System Based on Hybrid Photovoltaic-Fuel Cell Systems Using Hydrogen as an Energy Vector. Energy 224, 120110. doi:10.1016/j.energy.2021.120110
Polanski, M., Bystrzycki, J., Varin, R. A., Plocinski, T., and Pisarek, M. (2011). The Effect of Chromium (III) Oxide (Cr2O3) Nanopowder on the Microstructure and Cyclic Hydrogen Storage Behavior of Magnesium Hydride (MgH2). J. Alloys Comp. 509 (5), 2386–2391. doi:10.1016/j.jallcom.2010.11.026
Rafi-ud-din, , Xuanhui, Q., Zahid, G. H., Asghar, Z., Shahzad, M., Iqbal, M., et al. (2014). Improved Hydrogen Storage Performances of MgH2-NaAlH4 System Catalyzed by TiO2 Nanoparticles. J. Alloys Comp. 604, 317–324. doi:10.1016/j.jallcom.2014.03.150
Ranjbar, A., Guo, Z. P., Yu, X. B., Wexler, D., Calka, A., Kim, C. J., et al. (2009). Hydrogen Storage Properties of MgH2-SiC Composites. Mater. Chem. Phys. 114 (1), 168–172. doi:10.1016/j.matchemphys.2008.09.001
Ranjbar, A., Ismail, M., Guo, Z. P., Yu, X. B., and Liu, H. K. (2010). Effects of CNTs on the Hydrogen Storage Properties of MgH2 and MgH2-BCC Composite. Int. J. Hydrogen Energ. 35 (15), 7821–7826. doi:10.1016/j.ijhydene.2010.05.080
Reilly, J. J., and Wiswall, R. H. (1968). Reaction of Hydrogen with Alloys of Magnesium and Nickel and the Formation of Mg2NiH4. Inorg. Chem. 7 (11), 2254–2256. doi:10.1021/ic50069a016
Sabitu, S. T., and Goudy, A. J. (2012). Dehydrogenation Kinetics and Modeling Studies of MgH2 Enhanced by Transition Metal Oxide Catalysts Using Constant Pressure Thermodynamic Driving Forces. Metals 2 (3), 219–228. doi:10.3390/met2030219
Sadhasivam, T., Kim, H.-T., Jung, S., Roh, S.-H., Park, J.-H., and Jung, H.-Y. (2017). Dimensional Effects of Nanostructured Mg/MgH 2 for Hydrogen Storage Applications: A Review. Renew. Sust. Energ. Rev. 72, 523–534. doi:10.1016/j.rser.2017.01.107
Sakintuna, B., Lamaridarkrim, F., and Hirscher, M. (2007). Metal Hydride Materials for Solid Hydrogen Storage: A Review☆. Int. J. Hydrogen Energ. 32 (9), 1121–1140. doi:10.1016/j.ijhydene.2006.11.022
Sartbaeva, A., Kuznetsov, V. L., Wells, S. A., and Edwards, P. P. (2008). Hydrogen Nexus in a Sustainable Energy Future. Energy Environ. Sci. 1 (1), 79–85. doi:10.1039/B810104N
Satyapal, S., Petrovic, J., Read, C., Thomas, G., and Ordaz, G. (2007). The U.S. Department of Energy's National Hydrogen Storage Project: Progress towards Meeting Hydrogen-Powered Vehicle Requirements. Catal. Today 120 (3), 246–256. doi:10.1016/j.cattod.2006.09.022
Sazelee, N. A., Idris, N. H., Md Din, M. F., Mustafa, N. S., Ali, N. A., Yahya, M. S., et al. (2018). Synthesis of BaFe12O19 by Solid State Method and its Effect on Hydrogen Storage Properties of MgH2. Int. J. Hydrogen Energ. 43 (45), 20853–20860. doi:10.1016/j.ijhydene.2018.09.125
Sazelee, N. A., Idris, N. H., Md Din, M. F., S.Yahya, M., Ali, N. A., and Ismail, M. (2020a). LaFeO3 Synthesised by Solid-State Method for Enhanced Sorption Properties of MgH2. Results Phys. 16, 102844. doi:10.1016/j.rinp.2019.102844
Sazelee, N. A., and Ismail, M. (2021). Recent Advances in Catalyst-Enhanced LiAlH4 for Solid-State Hydrogen Storage: A Review. Int. J. Hydrogen Energ. 46 (13), 9123–9141. doi:10.1016/j.ijhydene.2020.12.208
Sazelee, N. A., Yahya, M. S., Ali, N. A., Idris, N. H., and Ismail, M. (2020b). Enhancement of Dehydrogenation Properties in LiAlH4 Catalysed by BaFe12O19. J. Alloys Comp. 835, 155183. doi:10.1016/j.jallcom.2020.155183
Sazelee, N. A., Yahya, M. S., Idris, N. H., Md Din, M. F., and Ismail, M. (2019). Desorption Properties of LiAlH4 Doped with LaFeO3 Catalyst. Int. J. Hydrogen Energ. 44 (23), 11953–11960. doi:10.1016/j.ijhydene.2019.03.102
Schlapbach, L., Shaltiel, D., and Oelhafen, P. (1979). Catalytic Effect in the Hydrogenation of Mg and Mg Compounds: Surface Analysis of MgMg2Ni and Mg2Ni. Mater. Res. Bull. 14 (9), 1235–1246. doi:10.1016/0025-5408(79)90220-4
Sulaiman, N. N., and Ismail, M. (2016). Enhanced Hydrogen Storage Properties of MgH2 Co-catalyzed with K2NiF6 and CNTs. Dalton Trans. 45 (48), 19380–19388. doi:10.1039/C6DT03646E
Sulaiman, N. N., Ismail, M., Rashid, A. H. A., Ali, N. A., Sazelee, N. A., and Timmiati, S. N. (2021a). Hydrogen Storage Properties of Mg-Li-Al Composite System Doped with Al2TiO5 Catalyst for Solid-State Hydrogen Storage. J. Alloys Comp. 870, 159469. doi:10.1016/j.jallcom.2021.159469
Sulaiman, N. N., and Ismail, M. (2017). Study the Effect of SrFe12O19 on MgH2/LiAlH4 Composite for Solid-State Hydrogen Storage. Int. J. Hydrogen Energ. 42 (50), 29830–29839. doi:10.1016/j.ijhydene.2017.10.071
Sulaiman, N. N., Ismail, M., Timmiati, S. N., and Lim, K. L. (2021b). Improved Hydrogen Storage Performances of LiAlH 4 + Mg( BH 4 ) 2 Composite with TiF 3 Addition. Int. J. Energ. Res 45 (2), 2882–2898. doi:10.1002/er.5984
Thapa, B. S., Neupane, B., Yang, H.-s., and Lee, Y.-H. (2021). Green Hydrogen Potentials from Surplus Hydro Energy in Nepal. Int. J. Hydrogen Energ. 46 (43), 22256–22267. doi:10.1016/j.ijhydene.2021.04.096
Urgnani, J., Torres, F. J., Palumbo, M., and Baricco, M. (2008). Hydrogen Release from Solid State NaBH4. Int. J. Hydrogen Energ. 33 (12), 3111–3115. doi:10.1016/j.ijhydene.2008.03.031
Vajo, J. J., Mertens, F., Ahn, C. C., Bowman, R. C., and Fultz, B. (2004). Altering Hydrogen Storage Properties by Hydride Destabilization through Alloy Formation: LiH and MgH2 Destabilized with Si. J. Phys. Chem. B 108 (37), 13977–13983. doi:10.1021/jp040060h
Vajo, J. J., and Olson, G. L. (2007). Hydrogen Storage in Destabilized Chemical Systems. Scripta Materialia 56 (10), 829–834. doi:10.1016/j.scriptamat.2007.01.002
Vajo, J. J., Salguero, T. T., Gross, A. F., Skeith, S. L., and Olson, G. L. (2007). Thermodynamic Destabilization and Reaction Kinetics in Light Metal Hydride Systems. J. Alloys Comp. 446-447 (0), 409–414. doi:10.1016/j.jallcom.2007.02.080
Vittetoe, A. W., Niemann, M. U., Srinivasan, S. S., McGrath, K., Kumar, A., Goswami, D. Y., et al. (2009). Destabilization of LiAlH4 by Nanocrystalline MgH2. Int. J. Hydrogen Energ. 34 (5), 2333–2339. doi:10.1016/j.ijhydene.2009.01.025
Wan, Q., Li, P., Li, Z., Zhai, F., Qu, X., and Volinsky, A. A. (2013). Improved Hydrogen Storage Performance of MgH2-LiAlH4 Composite by Addition of MnFe2O4. J. Phys. Chem. C 117 (51), 26940–26947. doi:10.1021/jp410449q
Wang, Y., Wang, Y., Wang, X., Zhang, H., Jiao, L., and Yuan, H. (2014). Destabilization Effects of Mg(AlH 4 ) 2 on MgH 2 : Improved Desorption Performances and its Reaction Mechanism. Int. J. Hydrogen Energ. 39 (31), 17747–17753. doi:10.1016/j.ijhydene.2014.08.117
Xia, Y., Wei, S., Huang, Q., Li, J., Cen, X., Zhang, H., et al. (2020). Facile Synthesis of NiCo2O4-Anchored Reduced Graphene Oxide Nanocomposites as Efficient Additives for Improving the Dehydrogenation Behavior of Lithium Alanate. Inorg. Chem. Front. 7 (5), 1257–1272. doi:10.1039/C9QI01451A
Yang, L., Yu, L. L., Wei, H. W., Li, W. Q., Zhou, X., and Tian, W. Q. (2019). Hydrogen Storage of Dual-Ti-Doped Single-Walled Carbon Nanotubes. Int. J. Hydrogen Energ. 44 (5), 2960–2975. doi:10.1016/j.ijhydene.2018.12.028
Yang, Y., Xiong, X., Chen, J., Peng, X., Chen, D., and Pan, F. (2021). Research Advances in Magnesium and Magnesium Alloys Worldwide in 2020. J. Magnesium Alloys 9 (3), 705–747. doi:10.1016/j.jma.2021.04.001
Yao, L., Lyu, X., Zhang, J., Liu, Y., Zhu, Y., Lin, H., et al. (2020a). Remarkable Synergistic Effects of Mg2NiH4 and Transition Metal Carbides (TiC, ZrC, WC) on Enhancing the Hydrogen Storage Properties of MgH2. Int. J. Hydrogen Energ. 45 (11), 6765–6779. doi:10.1016/j.ijhydene.2019.12.139
Yao, P., Jiang, Y., Liu, Y., Wu, C., Chou, K.-C., Lyu, T., et al. (2020b). Catalytic Effect of Ni@rGO on the Hydrogen Storage Properties of MgH2. J. Magnesium Alloys 8 (2), 461–471. doi:10.1016/j.jma.2019.06.006
Yap, F. A. H., and Ismail, M. (2017). The Hydrogen Storage Properties of Mg-Li-Al Composite System Catalyzed by K 2 ZrF 6. J. Phys. Chem. Sol. 104, 214–220. doi:10.1016/j.jpcs.2017.01.021
Ye, Y., Lu, J., Ding, J., Wang, W., and Yan, J. (2020). Numerical Simulation on the Storage Performance of a Phase Change Materials Based Metal Hydride Hydrogen Storage Tank. Appl. Energ. 278, 115682. doi:10.1016/j.apenergy.2020.115682
Yu, X., Tang, Z., Sun, D., Ouyang, L., and Zhu, M. (2017). Recent Advances and Remaining Challenges of Nanostructured Materials for Hydrogen Storage Applications. Prog. Mater. Sci. 88, 1–48. doi:10.1016/j.pmatsci.2017.03.001
Zacharia, R., and Rather, S. U. (20152015). Review of Solid State Hydrogen Storage Methods Adopting Different Kinds of Novel Materials. J. Nanomater. 2015, 1–18. doi:10.1155/2015/914845
Zaluska, A., Zaluski, L., and Ström Olsen, J. O. (1999). Nanocrystalline Magnesium for Hydrogen Storage. J. Alloys Comp. 288 (1), 217–225. doi:10.1016/S0925-8388(99)00073-0
Zhai, F., Li, P., Sun, A., Wu, S., Wan, Q., Zhang, W., et al. (2012). Significantly Improved Dehydrogenation of LiAlH4 Destabilized by MnFe2O4 Nanoparticles. J. Phys. Chem. C 116 (22), 11939–11945. doi:10.1021/jp302721w
Zhang, J., Li, Z., Wu, Y., Guo, X., Ye, J., Yuan, B., et al. (2019a). Recent Advances on the thermal Destabilization of Mg-Based Hydrogen Storage Materials. RSC Adv 9(1), 408–428. doi:10.1039/C8RA05596C
Zhang, J., Shan, J., Li, P., Zhai, F., Wan, Q., Liu, Z., et al. (2015). Dehydrogenation Mechanism of ball-milled MgH 2 Doped with Ferrites (CoFe 2 O 4 , ZnFe 2 O 4 , MnFe 2 O 4 and Mn 0.5 Zn 0.5 Fe 2 O 4 ) Nanoparticles. J. Alloys Comp. 643, 174–180. doi:10.1016/j.jallcom.2015.04.135
Zhang, J., Yan, S., Xia, G., Zhou, X., Lu, X., Yu, L., et al. (2021). Stabilization of Low-Valence Transition Metal towards Advanced Catalytic Effects on the Hydrogen Storage Performance of Magnesium Hydride. J. Magnesium Alloys 9 (2), 647–657. doi:10.1016/j.jma.2020.02.029
Zhang, J., Zhu, Y., Yao, L., Xu, C., Liu, Y., and Li, L. (2019b). State of the Art Multi-Strategy Improvement of Mg-Based Hydrides for Hydrogen Storage. J. Alloys Comp. 782, 796–823. doi:10.1016/j.jallcom.2018.12.217
Zhang, T., Isobe, S., Jain, A., Wang, Y., Yamaguchi, S., Miyaoka, H., et al. (2017). Enhancement of Hydrogen Desorption Kinetics in Magnesium Hydride by Doping with Lithium Metatitanate. J. Alloys Comp. 711, 400–405. doi:10.1016/j.jallcom.2017.03.361
Zhang, Y., Tian, Q.-F., Liu, S.-S., and Sun, L.-X. (2008). The destabilization mechanism and de/re-hydrogenation kinetics of MgH2-LiAlH4 hydrogen storage system. J. Power Sourc. 185 (2), 1514–1518. doi:10.1016/j.jpowsour.2008.09.054
Zheng, J., Liu, X., Xu, P., Liu, P., Zhao, Y., and Yang, J. (2012). Development of High Pressure Gaseous Hydrogen Storage Technologies. Int. J. Hydrogen Energ. 37 (1), 1048–1057. doi:10.1016/j.ijhydene.2011.02.125
Keywords: Mg–Li–Al system, magnesium hydride, lithium alanate, hydrogen storage, solid-state storage
Citation: Sazelee N, Ali NA, Yahya MS, Mustafa NS, Halim Yap FA, Mohamed SB, Ghazali MZ, Suwarno S and Ismail M (2022) Recent Advances on Mg–Li–Al Systems for Solid-State Hydrogen Storage: A Review. Front. Energy Res. 10:875405. doi: 10.3389/fenrg.2022.875405
Received: 14 February 2022; Accepted: 08 March 2022;
Published: 08 April 2022.
Edited by:
Claudia Zlotea, Centre National de la Recherche Scientifique (CNRS), FranceReviewed by:
Claudio Pistidda, Helmholtz Centre for Materials and Coastal Research (HZG), GermanyRaphael Janot, Laboratoire Réactivité et Chimie des Solides (LRCS), France
Copyright © 2022 Sazelee, Ali, Yahya, Mustafa, Halim Yap, Mohamed, Ghazali, Suwarno and Ismail. This is an open-access article distributed under the terms of the Creative Commons Attribution License (CC BY). The use, distribution or reproduction in other forums is permitted, provided the original author(s) and the copyright owner(s) are credited and that the original publication in this journal is cited, in accordance with accepted academic practice. No use, distribution or reproduction is permitted which does not comply with these terms.
*Correspondence: Mohammad Ismail, bW9oYW1tYWRpc21haWxAdW10LmVkdS5teQ==