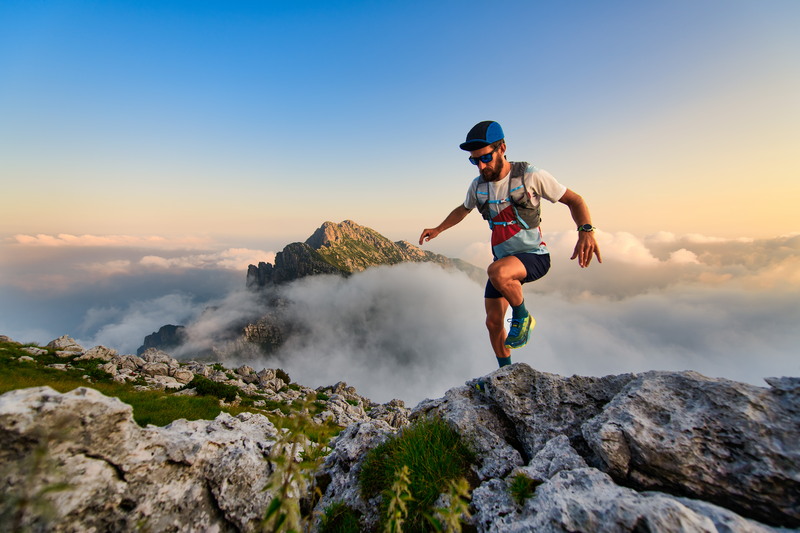
95% of researchers rate our articles as excellent or good
Learn more about the work of our research integrity team to safeguard the quality of each article we publish.
Find out more
ORIGINAL RESEARCH article
Front. Energy Res. , 08 April 2022
Sec. Bioenergy and Biofuels
Volume 10 - 2022 | https://doi.org/10.3389/fenrg.2022.868181
This article is part of the Research Topic Lignocellulose Valorization: Fractionation, Conversion and Applications View all 14 articles
The efficiency of the enzymatic digestibility of certain lignocellulosic biomass has been observed as a function of their structural and chemical changes which in turn depends on the ionic liquid (IL) used as the pretreatment solvent. This study demonstrated and compared the feasibility of the IL pretreatment process for two woody biomasses, namely maple and aspen, using two mechanistically distinct ILs, i.e., 1-ethyl-3-methylimidazolium acetate (C2mim][OAc]) and cholinium lysinate ([Ch][Lys]) as the solvent. The pretreatment was performed at three different temperatures of 100°C, 140°C, and 160°C at a high solid loading of 25 wt% to understand the impact of lignin content and crystallinity index on enzymatic digestibility. Saccharification of the biomass obtained after the IL pretreatment afforded 30–85% glucan conversions. For aspen, both [C2mim][OAc] and [Ch][Lys] exhibited the highest glucan conversion at 140°C. For maple, the highest glucan conversion was obtained at 140°C with [C2mim][OAc], whereas [Ch][Lys] had an optimum glucan conversion at 160°C. These pretreatments resulted in negligible delignification irrespective of the IL used. A significant loss of crystallinity was observed for all [C2mim][OAc]-pretreated biomasses, whereas the pretreatment with [Ch][Lys] resulted in an increase in the crystallinity index.
The depletion of fossil resources and stricter environmental regulations, along with an increasing demand for renewable carbon-based fuels and chemicals, have led to the need to find alternatives such as human-inedible lignocellulosic biomass (Bastidas-Oyanedel and Schmidt, 2019; Wang et al., 2020). The use of clean and sustainable energy along with the promotion of decarbonization processes is driving the economic recovery in the energy sectors. For instance, according to the 2021 report on World Total Primary Energy Supply in 2019, biofuels and waste were a leading contributor (>9%) other than non-renewable energy sources (IEA 2021).
Lignocellulosic biomass comprising agricultural, forest, and herbaceous residues serves as a good source for carbon-neutral and renewable carbon resources. Nevertheless, owing to the structural complexity of the constituent cellulose, hemicellulose, and lignin, the facile utilization of biomass is challenging (Gibson, 2012). Among the various cutting-edge technologies developed to tackle the recalcitrance issues, pretreatment with ionic liquids (ILs, organic salts with a melting point below 100°C) has attracted significant attention (Usmani et al., 2020; Yao et al., 2021).
The properties of ILs including basicity and H-bonding ability can be tuned to dissolve, fractionate, and even convert the lignocellulosic components by changing the ion composition(s) (Yao et al., 2021). This ability of ILs makes them a powerful solvent for lignocellulose processing. For instance, imidazolium-based ILs with adequate basicity of the anion are reported to dissolve cellulose under mild conditions of time and temperature by disrupting the existing interunit H-bonds in cellulose and establishing new H-bonds with the polymer chain (Da Costa Lopes et al., 2018; Jian Sun et al., 2016, Shaoni Sun et al., 2016). However, the major concerns associated with the imidazolium ILs involve high cost, high viscosity, and limited compatibility with the downstream processes. The use of aqueous solutions of imidazolium ILs was suggested as a probable solution to the aforementioned issues. For a non-woody biomass pretreatment with an aqueous solution of 1-ethyl-3-methylimidazolium acetate ([C2mim][OAc]) and 1-butyl-3-methylimidazolium acetate ([C4mim][OAc]), no significant decrease in the pretreatment efficacy was observed with water content up to 40% (Perez-Pimienta et al., 2017).
The search for biocompatible ILs to facilitate a consolidated biomass processing, cholinium cations coupled with amino acid anions [e.g., cholinium lysinate (Ch)(Lys)] were introduced (Sun et al., 2014). This class of ILs was generally found to be less toxic to enzymes and microorganisms than the imidazolium ILs and had a high delignification ability at a higher biomass loading and lower temperatures (Perez-Pimienta et al., 2020; Sun et al., 2014, Jian Sun et al., 2016; Shaoni Sun et al., 2016).
In addition to the pretreatment solvents and efficient processes, the identification of appropriate bioenergy feedstock is equally important given the availability of a variety of lignocellulosic feedstock depending on the geographical location (White, 2010; Gelfand et al., 2020). In this regard, woody biomasses are promising candidates owing to their higher carbohydrate content, availability, abundance, and reduced logistic expenses including storage (Socha et al., 2013; Lauri et al., 2014; Das et al., 2021). Lauri et al. (2014) predicted that woody biomass, if utilized to its full potential, could provide up to 40% of the total global energy consumption in 2050. Nevertheless, woody biomass has a higher lignin content and higher cellulose crystallinity that further complicates the direct or facile utilization for energy (or chemical) applications. This necessitates the development of pretreatment processes to identify potential woody biomass feedstock for sustainable future biorefinery and energy applications.
In this work, we compared the feasibility of IL pretreatment processes for two woody biomasses, namely, maple and aspen, using two mechanistically distinct ILs i.e., [C2mim][OAc] and [Ch][Lys] (see Scheme 1) at different pretreatment temperatures. To the best of our knowledge, no reports exist in the literature studying the effect of temperature on the delignification and crystallinity of aspen and maple during their pretreatment with [C2mim][OAc] and [Ch][Lys]. Furthermore, saccharification of the pretreated biomass was evaluated as a measure of the pretreatment efficacy and understanding the potential of the woody biomass under study.
All materials were used as supplied unless otherwise noted. Water was deionized, with a specific resistivity of 18 MΩ cm at 25°C, from Purelab Flex (ELGA, Woodridge, IL). Cholinium lysinate ([Ch][Lys]) was purchased from Proioincs GmbH (Grambach, Austria), while 1-ethyl-3-methylimidazolium acetate ([C2mim][OAc]) was procured from BASF (Ludwigshafen, Germany). Citric acid (ACS reagent ≥99.5%), sodium citrate tribasic dihydrate (ACS reagent, ≥99.0%), and sodium azide were obtained from Sigma-Aldrich (St. Louis, MO). Sulfuric acid (72% and 95–98%) was purchased from VWR. Ethanol (200 proof) was purchased from Decon Labs, Inc. (King of Prussia, PA). Sulfuric acid (72%) was procured from RICCA Chemical Company (Arlington, TX). J. T. Baker, Inc. (Phillipsburg, NJ) supplied hydrochloric acid. Analytical standard grade glucose and xylose were also obtained from Sigma-Aldrich (St. Louis, MO) and used for calibration.
The biomass studied here were aspen and maple, which were dried for 24 h in a 40°C oven. Subsequently, it was knife-milled with a 1 mm screen (Thomas-Wiley Model 4, Swedesboro, NJ). The resulting biomass was then placed in a leak-proof bag and stored in a dry cool place. The moisture content of the dried biomass was determined gravimetrically by subtracting the weight of the oven-dried biomass (105°C, overnight) and starting biomass. The content of extractives was determined using the protocol reported elsewhere (Mansfield et al., 2012).
Commercial cellulase (Cellic® CTec3, 1853 BHU-2-HS g−1, 1.212 g ml−1) and hemicellulase (Cellic® HTec3, 1760 FXU g−1, 1.210 g ml−1) mixtures were provided by Novozymes, North America (Franklinton, NC).
All compositional analysis experiments were conducted in duplicate. The compositional analysis of the biomass before and after pretreatment was performed using the National Renewable Energy Laboratory (NREL) two-step acid hydrolysis protocols (LAP) LAP-002 and LAP-005 (Sluiter et al., 2011). Briefly, 300 mg of extractive-free biomass and 3 ml of 72% sulfuric acid (H2SO4) were incubated at 30°C while shaking at 200 rpm for 1 h. The solution was diluted to 4% H2SO4 with 84 ml of DI water and autoclaved at 121°C for 1 h. The reaction was quenched by cooling down the flasks before removing the solids by filtration using medium-porosity filtering crucibles. The filtrates were spectrophotometrically analyzed for the acid-soluble lignin or ASL (NanoDrop 2000; Thermo Fisher Scientific, Waltham, MA) using the absorbance at 240 nm. Additionally, monomeric sugars (glucose and xylose) were determined by HPLC using an Agilent 1200 series instrument equipped with a refractive index detector and a Bio-Rad Aminex HPX-87H column. An aqueous solution of H2SO4 (4 mM) was used as the mobile phase (0.6 ml min−1, column temperature 60°C) for the separation of products (total run time being 20 min). The amount of glucan and xylan was calculated from the glucose and xylose content multiplied by the anhydro correction factors of 162/180 and 132/150, respectively. Finally, acid-insoluble lignin was quantified gravimetrically from the solid after heating overnight at 105°C (the weight of acid-insoluble lignin and ash) and then at 575°C for at least 6 h (the weight of ash).
All pretreatment reactions were conducted in duplicate. Aspen or maple samples of 1 mm and [C2mim][OAc] were mixed in a 1:3 ratio (w/w) to afford a biomass loading of 25 wt% in a 38 ml capped glass pressure tube and pretreated for 3 h in an oil bath heated at 100, 140, and 160°C, respectively. After pretreatment, the samples were removed from the oil bath and allowed to cool. A measure of 10 ml DI water was slowly added to the biomass-IL slurry and mixed well. The mixture was transferred to 50 ml Falcon tubes and the pressure tubes were washed with additional water to obtain a total volume of 40 ml. The mixture was centrifuged at high speed (4000 rpm) to separate solids and remove any residual IL. The water-washed solid was freeze-dried to obtain dried pretreated biomass for further analysis.
All pretreatment reactions were conducted in duplicate. The 1 mm aspen or maple samples, [Ch][Lys], and DI water were mixed in a 5:2:13 ratio (w/w) to afford a biomass loading of 25 wt% in a 38 ml capped glass pressure tube and pretreated for 3 h in an oil bath heated at 100, 140, and 160°C. After pretreatment, the samples were removed from the oil bath and allowed to cool. Then 10 ml DI water was slowly added to the biomass-IL slurry and mixed well. The mixture was transferred to 50 ml Falcon tubes and the pressure tubes were washed with additional water to obtain a total volume of 40 ml. The mixture was centrifuged at high speed (4000 rpm) to separate solids and remove any residual IL. The water-washed solid was freeze-dried to obtain dried pretreated biomass for further analysis.
All enzymatic saccharification was conducted in duplicate. Enzymatic saccharification of the pretreated biomass was carried out using commercially available enzymes, Cellic® CTec3 and HTec3 (9:1 v/v) from Novozymes, at 50°C in a rotary incubator (Enviro-Genie, Scientific Industries, Inc.). All the reactions were performed at 2.5 wt% biomass loading in a 15 ml glass tube. The pH of the mixture was adjusted to 5 with 50 mM sodium citrate buffer supplemented with 0.02% sodium azide to prevent microbial contamination. The total reaction volume included a total protein content of 10 mg per g biomass. The amount of sugar released was measured by HPLC as described previously.
The crystallinity index of untreated and pretreated biomass was analyzed using a PANalytical Empyrean X-ray diffractometer equipped with a PIXcel3D detector and operated at 45 kV and 40 mA using Cu Kα radiation (λ = 1.5418 Å). The diffraction patterns were collected in the 2θ range of 5–55° with a step size of 0.026° and an exposure time of 300 s. A reflection-transmission spinner was used as a sample holder and the spinning rate was set at 8 rpm throughout the experiment. The crystallinity index (CI) was determined from the crystalline and amorphous peak areas of the measured diffraction patterns using the following equation as reported previously (Park et al., 2010).
%CI = [(I002—Iam)/I002]*100, where I002 is the intensity of the crystalline plane (002) and Iam is the minimum between (002) and (101) peaks and is at about 18°.
The composition of the two woody biomasses, namely, aspen and maple, were determined as per the NREL protocol and the results are summarized in Table 1. There were <7% extractives found to be present in both biomasses. Higher glucan content of 41.85% was found in aspen compared with that of 36.63% glucan in maple. On the other hand, the acid-insoluble lignin (or AIL) content was higher in maple amounting to 21.69% compared to 18.5% in aspen.
As described earlier, pretreatment is a critical step to enhance the accessibility of the cellulosic component of the biomass. In general, the effective pretreatment of woody biomasses with both [C2mim][OAc] and [Ch][Lys] has been reported at temperatures between 90 and 160°C, mostly with a time interval of 3 h to achieve high sugar yields (Sun et al., 2014; Yoo et al., 2017; Usmani et al., 2020; Das et al., 2021; Yao et al., 2021). The influence of the temperature was examined on the pretreatment efficacy of the ILs under investigation on aspen and maple as a function of solid recovery and biomass composition. In this study, we have chosen three pretreatment temperatures 100, 140, and 160°C, respectively. Although a higher temperature has been shown to favor delignification and thus a higher sugar yield, the stability of the IL at higher temperatures is always a subject to consider. It should be noted that we expect a small percentage of both [C2mim][OAc] and [Ch][Lys] to decompose when heated at 160°C for 3 h (Clough et al., 2013; Yao et al., 2021).
The glucan, xylan, and AIL content of aspen and maple before and after pretreatment with [C2mim][OAc] and [Ch][Lys] at 100, 140, and 160°C, respectively, for 3 h is tabulated in Table 2. While considering the amount of dried biomass recovered after pretreatment with ILs followed by washing (see Experimental Section for details), termed here as solid recovery, a significant impact of temperature was observed for [Ch][Lys]-based pretreatments. For both aspen and maple, a high solid recovery between 80 and 90% was afforded under all temperature conditions with [C2mim][OAc] and at 100 and 140°C with [Ch][Lys]. Only ∼67% solids were recovered after pretreatment of these woody biomasses with [Ch][Lys] at 160°C. In general, [C2mim][OAc] is reported to have a higher solid recovery for woody biomass irrespective of the temperature employed for the pretreatment (Torr et al., 2016), whereas [Ch][Lys] is reported to have lower solid recovery at higher pretreatment temperatures (Sun et al., 2014; Yao et al., 2021).
TABLE 2. Compositional analysis of aspen and maple after IL pretreatments at different temperatures.
The carbohydrate (including glucan and xylan) and lignin amount of the IL-pretreated biomass was also determined to understand the impact of pretreatment as a function of IL and pretreatment temperature. Interestingly, the carbohydrate and lignin content was found to be similar to that of the untreated aspen and maple woody biomass. For aspen, the glucan, xylan, and AIL content were in the range of 36–45%, 13–15%, and 13–18%, respectively, compared with the 41.8, 15.3, and 18.5% glucan, xylan, and AIL content in untreated aspen. Similarly, untreated maple contained 36.6% glucan, 14% xylan, and 21.7% AIL, whereas the IL-pretreated samples were composed of 31–42% glucan, 10–16% xylan, and 17–23% AIL (see Table 2).
To realize the actual loss or removal of the holocellulosic or lignin component, the percentage removal of each component was also calculated as follows:
Although the carbohydrate and lignin content were similar for the untreated and IL-pretreated biomasses, the inclusion of solid recovery into the calculation in the form of percentage removal highlighted the differences between the efficacies of the pretreatment. In general, a higher loss of glucan, xylan, and AIL was observed at 160°C. Overall, [C2mim][OAc] pretreatment resulted in higher loss of glucan (up to 27%) and xylan (up to 36%), whereas [Ch][Lys] removed up to 47% AIL from maple wood. On the contrary, in the case of aspen, [Ch][Lys] pretreatment resulted in the maximum loss of glucan (28.8%), xylan (33.1%), and AIL (49.8%). These result of higher lignin removal by [Ch][Lys] in comparison to the [C2mim][OAc] was consistent with the previous reports (Sun et al., 2014; Usmani et al., 2020; Yao et al., 2021). It should be noted that [C2mim][OAc] was reported to dissolve higher amounts of lignin compared with [Ch][Lys], but the use of water (anti-solvent) to remove the IL crashes out the soluble biopolymers in the solution in the case of [C2mim][OAc]. On the other hand, [Ch][Lys] with a higher pKa value than [C2mim][OAc] results in higher removal of lignin from the slurry when washed with water.
To further elucidate the impact of IL pretreatment on the woody biomass, the glucan, and xylan digestibility was measured using commercial enzyme cocktails (Novozymes Cellic CTec3 and HTec3) as shown in Figure 1. The saccharification of the pretreated biomass was carried out at a protein loading of 10 mg per g of biomass at 50°C for 72 h.
FIGURE 1. Sugar yields from (A) aspen and (B) maple after IL pretreatments at different temperatures. Glucose (dark gray bars) and xylose (light gray bars). The percentage of lignin removal is shown in black closed circles.
Among [C2mim][OAc]- and [Ch][Lys]-based pretreatments, [C2mim][OAc] pretreatment enhanced the glucan digestibility and hence, glucose yields. Interestingly, the pretreatment of aspen at 160°C was not favorable for higher sugar release for both ILs under study (Figure 1A). The yields of glucose after pretreatment with [C2mim][OAc] was in the following order: 140°C (82.7%) > 100°C (63.9%) > 160°C (56.6%). However, the glucan digestibility after [Ch][Lys] pretreatment of aspen follows the order: 140°C (70.9%) > 160°C (50.2%) > 100°C (34.4%).
In the case of maple (Figure 1B), the highest glucose yield, that is 78.2%, was achieved at 140°C after the pretreatment with [C2mim][OAc] and the order of the glucose yields could be summarized as 140°C (78.2%) > 160°C (76.4%) > 100°C (53%). Switching the pretreatment solvent from [C2mim][OAc] to [Ch][Lys] demanded a higher temperature to release sugar from the pretreated biomass, 160°C (56.4%) > 140°C (49.6%) > 100°C (46.7%).
Because lignin is considered to limit cellulose accessibility, delignification (or lignin removal) is the most common strategy to improve cellulose accessibility. Consequently, the amount of lignin removal was plotted against the sugar yield, however, no significant relationship was derived from the plots. This indicated that factors other than lignin removal govern the saccharification of the woody biomass.
Xylose yields were also observed to have a trend similar to glucose yields and were in the range of 27–62%. For both [C2mim][OAc] and [Ch][Lys]-pretreated aspen solids, maximum xylose yields were attained at 140°C (Figure 1A). For maple (Figure 1B), 140°C was found to be optimal for maximum xylose when pretreated with [C2mim][OAc], whereas pretreatment with [Ch][Lys] was more effective at 160°C.
A majority of the effort in the lignocellulosic pretreatment has been made to disrupt the crystallinity of cellulose and enhance the accessibility for an accelerated conversion (Park et al., 2010; Karimi and Taherzadeh 2016; Baruah et al., 2018; Pena et al., 2019; Usmani et al., 2020). PXRD patterns were recorded for untreated and IL-pretreated biomass to determine the crystalline (cellulose forms and the degree of crystallinity) and non-crystalline components (amorphous cellulose, hemicellulose, and lignin). A change in the crystallinity index is an indication of structural changes, however, the crystallinity of the overall biomass depends on both 1) amount of crystalline cellulose dissolved and precipitated during biomass pretreatment, and 2) loss of non-crystalline components during washing of the pretreatment solvent (IL in the present study).
PXRD patterns of untreated and IL-pretreated woody biomass were plotted as shown in Figure 2. As shown in Figures 2A,C, [C2mim][OAc]-pretreated woody biomass was highly amorphous after the IL-pretreatment. This could be explained based on the H-bond disruption ability of [C2mim][OAc] to swell and/or dissolve cellulose in the lignocellulosic biomass (Swatloski et al., 2002). Typically, for any given biomass, maxima at 2θ = ∼16° is assigned to the (101) plane of the cellulose I form, while the dominant (002) plane of cellulose II form is observed at 2θ = ∼22°. Pretreatment with [C2mim][OAc] resulted in the disappearance of the (101) plane with an increase in the pretreatment temperature resulting in a broad peak around 2θ = 20°. These patterns are clearly different from the untreated biomass and indicate the disruption of interunit H-bonding in crystalline cellulose of woody biomass.
FIGURE 2. PXRD patterns of aspen (top; (A,B)) and maple (bottom; (C,D)) in the presence of [C2mim][OAc] (left; (A,C)) and [Ch][Lys] (right; (B,D)). (A) Untreated biomass and pretreatment at (B) 100°C, (C) 140°C, and (D) 160°C.
On the other hand, [Ch][Lys]-pretreated samples (Figures 2B,D) were less amorphous compared with the untreated biomass accounted for by the loss of non-crystalline components. The peak for the crystalline component (002) plane of cellulose II increased in intensity with the increase in temperature suggesting a decrease in the non-crystalline components from the woody biomass. This agreed with the compositional data of the IL-pretreated woody biomass shown in Table 2.
The crystallinity index of untreated and pretreated biomass was calculated as reported previously (Park et al., 2010) and plotted as shown in Figure 3. The crystallinity index of the untreated and IL pretreated maple was in the following order: [Ch][Lys]/160°C (57.5%) ∼ [Ch][Lys]/140°C (58.3%) > [Ch][Lys]/100°C (55.8%) > untreated maple (47.7%) > [C2mim][OAc]/100°C (34.7%) >> [C2mim][OAc]/140°C (19.1%) > [C2mim][OAc]/160°C (13.9%). Similar to this trend, the crystallinity index of untreated and pretreated aspen was in the following order: [Ch][Lys]/160°C (62.1%) ∼ [Ch][Lys]/140°C (61.7%) > [Ch][Lys]/100°C (60.2%) > untreated aspen (55.8%) > [C2mim][OAc]/100°C (34.3%) >> [C2mim][OAc]/140°C (20.2%) > [C2mim][OAc]/160°C (16.9%).
FIGURE 3. Crystallinity index of biomass pretreated with [C2mim][OAc] and [Ch][Lys] at different temperatures. Maple pretreated with [C2mim][OAc] (black squares), maple pretreated with [Ch][Lys] (dark gray triangles), aspen pretreated with [Ch][Lys] (gray circles), and aspen pretreated with [C2mim][OAc] (light gray diamonds).
SCHEME 1. Chemical structures of (A) 1-ethyl-3-methylimidazolium acetate ([C2mim][OAc]) and (B) Cholinium lysinate ([Ch][Lys]).
In summary, the pretreatment efficacy of two woody biomass (aspen and maple) with two distinct ILs ([C2mim][OAc] and [Ch][Lys]) was compared at three different temperatures. Pretreatment with [C2mim][OAc] afforded the highest sugar yields for both aspen and maple. At 140°C, 82.7% glucose and 62.1% xylose were released from aspen, whereas 78.2% glucose and 54% xylose yields were obtained. The comparisons of the IL at different temperatures suggested aspen to be the better source as an energy crop owing to the sugar release efficacy even with diluted [Ch][Lys]. Based on the compositional data, negligible delignification was observed for all pretreatment conditions other than the biomass pretreated with [Ch][Lys] at 160°C. In agreement with previous reports, pretreatment with [C2mim][OAc] resulted in reduced crystallinity due to the swelling/dissolution of crystalline cellulose, whereas the pretreatment with [Ch][Lys] removed non-crystalline components from the biomass, enhancing the overall crystallinity of the biomass sample.
The original contributions presented in the study are included in the article/Supplementary Material; further inquiries can be directed to the corresponding author.
HC collected and analyzed data and wrote the original draft. BAS supervised the project and edited the draft. JMG supervised the project and edited the draft.
This work was part of the DOE Joint BioEnergy Institute (http://www.jbei.org) supported by the U.S. Department of Energy, Office of Science, Office of Biological and Environmental Research, through contract DE-AC02-05CH11231 between Lawrence Berkeley National Laboratory and the U.S. Department of Energy.
The authors declare that the research was conducted in the absence of any commercial or financial relationships that could be construed as a potential conflict of interest.
All claims expressed in this article are solely those of the authors and do not necessarily represent those of their affiliated organizations, or those of the publisher, the editors, and the reviewers. Any product that may be evaluated in this article, or claim that may be made by its manufacturer, is not guaranteed or endorsed by the publisher.
The authors acknowledge Novozymes for providing the CTec3 and HTec3 enzymes used in this work. They are thankful to Dr. Vitalie Stavila of Sandia National Laboratories for assistance in collecting the PXRD data.
Baruah, J., Nath, B. K., Sharma, R., Kumar, S., Deka, R. C., Baruah, D. C., et al. (2018). Recent Trends in the Pretreatment of Lignocellulosic Biomass for Value-Added Products. Front. Energ. Res. 6, 141. doi:10.3389/fenrg.2018.001410.3389/fenrg.2018.00141
J. -R. Bastidas-Oyanedel, and J. E. Schmidt (Editors) (2019). “Biorefinery,” Integrated Sustainable Processes for Biomass Conversion to Biomaterials, Biofuels, and Fertilizers (Cham: Springer Nature). doi:10.1007/978-3-030-10961-5
Clough, M. T., Geyer, K., Hunt, P. A., Mertes, J., and Welton, T. (2013). Thermal Decomposition of Carboxylate Ionic Liquids: Trends and Mechanisms. Phys. Chem. Chem. Phys. 15, 20480–20495. doi:10.1039/C3CP53648C
Da Costa Lopes, A. M., Lins, R. M. G., Rebelo, R. A., and Łukasik, R. M. (2018). Biorefinery Approach for Lignocellulosic Biomass Valorisation with an Acidic Ionic Liquid. Green. Chem. 20, 4043–4057. doi:10.1039/c8gc01763h
Das, L., Achinivu, E. C., Barcelos, C. A., Sundstrom, E., Amer, B., Baidoo, E. E. K., et al. (2021). Deconstruction of Woody Biomass via Protic and Aprotic Ionic Liquid Pretreatment for Ethanol Production. ACS Sust. Chem. Eng. 9, 4422–4432. doi:10.1021/acssuschemeng.0c07925
Gelfand, I., Hamilton, S. K., Kravchenko, A. N., Jackson, R. D., Thelen, K. D., and Robertson, G. P. (2020). Empirical Evidence for the Potential Climate Benefits of Decarbonizing Light Vehicle Transport in the U.S. With Bioenergy from Purpose-Grown Biomass with and without BECCS. Environ. Sci. Technol. 54, 2961–2974. doi:10.1021/acs.est.9b07019
Gibson, L. J. (2012). The Hierarchical Structure and Mechanics of Plant Materials. J. R. Soc. Interf. 9 (76), 2749–2766. doi:10.1098/rsif.2012.0341
IEA (2021). IEA World Total Energy Supply. Available from: https://www.iea.org/reports/key-world-energy-statistics-2021/supply.
Jian Sun, J., Konda, N. V. S. N. M., Shi, J., Parthasarathi, R., Dutta, T., Xu, F., et al. (2016). CO2 Enabled Process Integration for the Production of Cellulosic Ethanol Using Bionic Liquids. Energy Environ. Sci. 9, 2822–2834. doi:10.1039/C6EE00913A
Karimi, K., and Taherzadeh, M. J. (2016). A Critical Review of Analytical Methods in Pretreatment of Lignocelluloses: Composition, Imaging, and Crystallinity. Bioresour. Tech. 200, 1008–1018. doi:10.1016/j.biortech.2015.11.022
Lauri, P., Havlík, P., Kindermann, G., Forsell, N., Böttcher, H., and Obersteiner, M. (2014). Woody Biomass Energy Potential in 2050. Energy Policy 66, 19–31. doi:10.1016/j.enpol.2013.11.033
Mansfield, S. D., Kim, H., Lu, F., and Ralph, J. (2012). Whole Plant Cell wall Characterization Using Solution-State 2D NMR. Nat. Protoc. 7, 1579–1589. doi:10.1038/nprot.2012.064
Park, S., Baker, J. O., Himmel, M. E., Parilla, P. A., and Johnson, D. K. (2010). Cellulose Crystallinity index: Measurement Techniques and Their Impact on Interpreting Cellulase Performance. Biotechnol. Biofuels 3, 10. doi:10.1186/1754-6834-3-10
Pena, C. A., Soto, A., King, A. W. T., and Rodríguez, H. (2019). Improved Reactivity of Cellulose via its Crystallinity Reduction by Nondissolving Pretreatment with an Ionic Liquid. ACS Sust. Chem. Eng. 7, 9164–9171. doi:10.1021/acssuschemeng.8b06357
Perez-Pimienta, J. A., Sathitsuksanoh, N., Thompson, V. S., Tran, K., Ponce-Noyola, T., Stavila, V., et al. (2017). Ternary Ionic Liquid-Water Pretreatment Systems of an Agave Bagasse and Municipal Solid Waste Blend. Biotechnol. Biofuels 10–15. doi:10.1186/s13068-017-0758-4
Pérez-Pimienta, J. A., Icaza-Herrera, J. P. A., Méndez-Acosta, H. O., González-Álvarez, V., and Méndoza-Pérez, J. (2020). Bioderived Ionic Liquid-Based Pretreatment Enhances Methane Production from Agave Tequilana Bagasse. RSC Adv. 10, 14025–14032. doi:10.1039/d0ra01849j
Sluiter, A., Hames, B., Ruiz, R., Scarlata, C., Sluiter, J., Templeton, D., et al. (2011). Determination of Structural Carbohydrates and Lignin in Biomass. Golden, CO: National Renewable Energy Laboratory (NREL) Analytical Procedures. TP-510-42618 Available from: https://www.nrel.gov/docs/gen/fy11/42618.pdf.
Socha, A. M., Plummer, S. P., Stavila, V., Simmons, B. A., and Singh, S. (2013). Comparison of Sugar Content for Ionic Liquid Pretreated Douglas-fir Woodchips and Forestry Residues. Biotechnol. Biofuels 6, 61. doi:10.1186/1754-6834-6-61
Sun, N., Parthasarathi, R., Socha, A. M., Shi, J., Zhang, S., Stavila, V., et al. (2014). Understanding Pretreatment Efficacy of Four Cholinium and Imidazolium Ionic Liquids by Chemistry and Computation. Green. Chem. 16, 2546–2557. doi:10.1039/c3gc42401d
Shaoni Sun, S., Sun, S., Cao, X., and Sun, R. (2016). The Role of Pretreatment in Improving the Enzymatic Hydrolysis of Lignocellulosic Materials. Bioresour. Tech. 199, 49–58. doi:10.1016/j.biortech.2015.08.061
Swatloski, R. P., Spear, S. K., Holbrey, J. D., and Rogers, R. D. (2002). Dissolution of Cellose with Ionic Liquids. J. Am. Chem. Soc. 124, 4974–4975. doi:10.1021/ja025790m
Torr, K. M., Love, K. T., Simmons, B. A., and Hill, S. J. (2016). Structural Features Affecting the Enzymatic Digestibility of pine wood Pretreated with Ionic Liquids. Biotechnol. Bioeng. 113, 540–549. doi:10.1002/bit.25831
Usmani, Z., Sharma, M., Gupta, P., Karpichev, Y., Gathergood, N., Bhat, R., et al. (2020). Ionic Liquid Based Pretreatment of Lignocellulosic Biomass for Enhanced Bioconversion. Bioresour. Tech. 304, 123003. doi:10.1016/j.biortech.2020.123003
Wang, C., Zhang, X., Liu, Q., Zhang, Q., Chen, L., and Ma, L. (2020). A Review of Conversion of Lignocellulose Biomass to Liquid Transport Fuels by Integrated Refining Strategies. Fuel Process. Tech. 208, 106485. doi:10.1016/j.fuproc.2020.106485
White, E. M. (2010). Woody Biomass for Bioenergy and Biofuels in the United States: A Briefing Paper. Gen. Tech. Rep. PNW-GTR-825. Portland, OR: U.S. Department of Agriculture, Forest Service, Pacific Northwest Research Station, 45.
Yao, A., Choudhary, H., Mohan, M., Rodriguez, A., Magurudeniya, H., Pelton, J. G., et al. (2021). Can Multiple Ions in an Ionic Liquid Improve the Biomass Pretreatment Efficacy? ACS Sust. Chem. Eng. 9, 4371–4376. doi:10.1021/acssuschemeng.0c09330
Keywords: ionic liquid, woody biomass, enzymatic hydrolysis, biofuel, sustainability, delignification, cellulose crystallinity
Citation: Choudhary H, Simmons BA and Gladden JM (2022) Comparative Study on the Pretreatment of Aspen and Maple With 1-Ethyl-3-methylimidazolium Acetate and Cholinium Lysinate. Front. Energy Res. 10:868181. doi: 10.3389/fenrg.2022.868181
Received: 02 February 2022; Accepted: 11 March 2022;
Published: 08 April 2022.
Edited by:
Chen Huang, Chinese Academy of Forestry, ChinaReviewed by:
Zhe Ling, Nanjing Forestry University, ChinaCopyright © 2022 Choudhary, Simmons and Gladden. This is an open-access article distributed under the terms of the Creative Commons Attribution License (CC BY). The use, distribution or reproduction in other forums is permitted, provided the original author(s) and the copyright owner(s) are credited and that the original publication in this journal is cited, in accordance with accepted academic practice. No use, distribution or reproduction is permitted which does not comply with these terms.
*Correspondence: John M. Gladden, am1nbGFkZGVuQGxibC5nb3Y=
Disclaimer: All claims expressed in this article are solely those of the authors and do not necessarily represent those of their affiliated organizations, or those of the publisher, the editors and the reviewers. Any product that may be evaluated in this article or claim that may be made by its manufacturer is not guaranteed or endorsed by the publisher.
Research integrity at Frontiers
Learn more about the work of our research integrity team to safeguard the quality of each article we publish.