- 1Chemistry and Nanoscience Center, National Renewable Energy Laboratory, Golden, CO, United States
- 2Lawrence Berkeley National Laboratory, Energy Storage and Distributed Resources Division, Berkeley, CA, United States
Efforts in oxygen evolution catalyst development have significantly increased and often use rotating disk electrode half-cells to evaluate intrinsic kinetics and screen materials for short-term durability. Standardizing rotating disk electrode test protocols is critical to experimental accuracy, to realistically assess their potential impact at a device level and to assess how different catalyst approaches and concepts are prioritized. The goal of this study is to provide standardized test protocols and suggest best practices to help reduce variability in ex situ materials characterization in the broader community. Specifically, these protocols focus on test cleanliness and materials choices, including how electrodes are prepared and tested, and the impact on activity observations.
1 Introduction
While hydrogen historically has had a limited market in energy storage and conversion, electricity cost reductions have enabled growth opportunities. Further cost reductions in electrochemical water splitting, however, are needed to be cost-competitive with other technologies. While advanced manufacturing accounts for a large portion of that reduction, catalyst development has been extensively pursued to address iridium scarcity and the performance, durability, and cost of proton exchange membrane-based systems (Pivovar et al., 2018; Ayers et al., 2019; IRENA, 2020; Alia, 2021).
Most catalyst development efforts use rotating disk electrode (RDE) testing to focus on intrinsic capabilities and to avoid the complications of materials integration and cell-level testing. There is wide variability, however, in RDE baseline activity (several orders of magnitude) and stability metrics that complicate catalyst development (Alia and Anderson, 2019). This article provides standardized protocols and best practices for screening acidic oxygen evolution (OER) materials in RDE, discusses sources for discrepancies, and provides troubleshooting recommendations. This effort focuses on the impact of electrode coating and test choices on activity/stability evaluations and leverages previous studies in RDE activity/stability testing (Alia et al., 2016a; Yu et al., 2018; Alia and Anderson, 2019; Rakousky et al., 2019), surface area quantification (Zhao et al., 2015; Alia et al., 2016b), and cell-level testing comparisons (Alia et al., 2019).
2 Protocol Scope
2.1 Scope and Applicability
This protocol standardizes RDE testing for OER catalysts intended for use in proton exchange membrane-based electrolyzers. It includes procedures related to activity, stability, and surface area determinations for acidic OER catalysts.
2.2 Summary of Method
The protocol describes the preparation and execution of RDE experiments as follows:
• Preparation of the catalyst ink.
• Coating the catalyst film onto an electrode.
• Setup of the electrochemical cell and its components.
• Execution of RDE tests.
2.3 Personnel Qualifications/Responsibilities
• All personnel should be trained to handle chemicals and mitigate chemical hazards.
2.4 Health and Safety Warming
• Chemical Hazards–This test protocol uses concentrated acids for the preparation of the electrolyte and the cleaning of the glassware. Follow SDS safety precautions when handling concentrated perchloric acid or sulfuric acid solutions. All concentrated acids should be handled in a fume hood. Standard personal protective equipment, including safety glasses and gloves (acid-compatible), must be worn. Ensure that gas cylinders are properly secured and regulated.
• Rotation Hazard–The RDE working shaft rotates during testing.
2.5 Equipment and Supplies
• Personal Protective Equipment
• Safety glasses
• Gloves
• Lab coat
• Glassware
• Beakers, volumetric flask (50 ml, 1 L)
• 20-ml vials
• RDE electrochemical cell
• Optional: Luggin capillary, counter bridge/junction
• Equipment
• Electrode rotator (Pine Research: AFMSRCE)
• RDE tip (Pine Research: AFE5TQ050)
• RDE working electrode—gold disk (Pine Research: AFED050P040AU)
• Reference electrode (reversible hydrogen preferred)
• Wire and mesh counter electrode (gold preferred)
• Bath, horn sonicator
• Chemicals
• Perchloric acid (70%, Veritas® Double Distilled, GFS Chemicals: 230)
• Sulfuric acid
• Inert gas, nitrogen, or argon
• Deionized water (Milli-Q Millipore quality minimum standard)
• Isopropanol (certified ACS)
• Nafion® dispersion, 1100 EW at 5 wt%
• Iridium oxide (Alfa Aesar 43396)
• ALNOCHROMIX™ solution (Alconox Inc.)
2.5.1 Nomenclature and Definitions
• RDE: rotating disk electrode
• OER: oxygen evolution reaction
2.6 Recommended Reading
• S.M. Alia, G.C. Anderson, Journal of The Electrochemical Society, 166, F282 (2019).
3 Procedure
3.1 Step-by-Step Procedure
- Preparing, polishing, and assembling the RDE Tip. Fixed gold working electrodes are preferred.
1. For standard cleaning, affix a microfiber polishing cloth to a polisher or a flat, stationary surface. Place a small amount of 0.05 μm polishing slurry onto the microfiber cloth. In a figure-8 pattern, polish the gold disk for about 4 min. Rinse the disk thoroughly with deionized water when polishing is completed. Sonicate in deionized water for 3 × 3 minutes, replacing the deionized water between each step to ensure the removal of leftover alumina polishing paste.
2. Repeatedly wipe electrode surface with a water-soaked Kimwipe, followed by a 2-propanol, then water-soaked Kimwipe.
- Preparation and application of the catalyst ink
1. Using a small, clean spatula, measure 3.5 mg of iridium oxide into a clean the vial. Cap the vial to prevent contamination.
2. Using a pipette, dispense a total of 7.6 ml of deionized water into the vial. After replacing the tip, use the pipette to dispense a total of 2.4 ml of 2-propanol into the vial.
3. Ice ink for 5 min before adding ionomer. Use a clean 10–100 μl micropipette to dispense 20 μl of Nafion® dispersion (1100 EW at 5 wt%) into the catalyst ink. Tightly cap the vial. NOTE: Depending on the type of material, the Nafion content may have to be altered for optimal activity.
4. Sonicate the ink for 20 min. Validate dispersion of the ink by observing if there is catalyst settling. One example protocol is the following:
⁃ Sonicate the catalyst ink for 30 s in a horn sonicator, followed by 20 min in a bath sonicator.
⁃ NOTE: Use an ice bath to prevent heating of the ink. Not icing the ink can have a significant impact on the dispersion quality, how the ink dries, and the resulting activity (Alia and Anderson, 2019).
5. Place the RDE tip and rod into the rotator upside down so that the ink can be drop cast on the RDE tip.
6. Once sonicated, use the micropipette to dispense a 10 μl drop of catalyst ink onto the gold disk of the working electrode rotating at 100 rpm. Turn up the rotator slowly from 100 to 700 rpm. Wait until dry (20 min) before turning off the rotation.
⁃ NOTE: To avoid spillage anchor elbows on a stationary surface and ensure that the rotator/shaft is not damaged (rotation on-axis). The drop of catalyst ink should not contain bubbles, should dry on the surface of the gold disk, and should not contact the PTFE shroud. After drying, the coating should be uniform (without a coffee ring). If any of these issues are observed, repolish the electrode and repeat.
- Glassware cleaning. Should be used for all glassware used at any point in RDE preparation or testing.
1. Soak all glassware in concentrated sulfuric acid, then ALNOCHROMIX™ overnight.
2. Immerse the electrochemical cell and components (stoppers, cleaned counter electrode, cleaned reference electrode if hydrogen) in deionized water and boil the water.
3. Remove the water, refill, and repeat the procedure 8 times.
4. Following the conclusion of each test, store glassware in a cleaned beaker filled with deionized water. Periodically reclean beaker/cell.
- 0.1 M Perchloric Acid Electrolyte. Recommend completing in a washdown fume hood.
1. Fill a clean 1-L volumetric flask 2/3 full with deionized water.
2. Weigh 14.39 g of concentrated perchloric acid into a clean beaker and add the perchloric acid into the volumetric flask.
3. Rinse the beaker that contained the perchloric acid multiple times with deionized water and pour the diluted perchloric acid into the volumetric flask until the solution is near to the 1 L mark. Slowly fill the volumetric flask to the 1 L mark.
4. Mix the flask to ensure that the electrolyte solution is homogeneously mixed.
- RDE Cell Setup. For temperature control during testing, jacketed cells could be used if cleanliness can be maintained.
1. Rinse the electrochemical cell at least twice with the prepared perchloric acid electrolyte.
2. Fill the electrochemical cell with a measured volume of electrolyte solution so that the reference electrode, gas bubbler, and counter electrode are all submerged in the electrolyte solution and not in contact with each other. The working electrode should be submerged, but below the electrode/rotator junction to prevent contact corrosion, contamination, and resistance accumulation. If there are any unused ports on the electrochemical cell, cover the ports with cleaned glass. Record volume of solution for effluent analysis purposes.
3. Assemble cell components.
⁃ High surface area counter electrode (mesh spot welded to wire) is preferred to minimize counter contributions to electrochemical measurements, including counter/working plating.
⁃ CAUTION: The high purity gold counter electrode is fragile.
⁃ Gold counter electrodes are preferred since upon dissolution, they will not improve OER activity or add contaminants (Alia and Pivovar, 2018).
4. If using a non-hydrogen reference electrode, calibrate the reference. Hydrogen reference electrodes are preferred to prevent contamination and data inaccuracies due to miscalibration and potential drift during testing (Garsany et al., 2010). For non-hydrogen references, sulfates (mercurous sulfate) are preferred to chloride (silver chloride, calomel) due to individual contaminant effects.
⁃ Use the RDE setup (cleaned glassware, 0.1 M perchloric acid electrolyte) just prior to electrochemical testing.
⁃ Saturate the electrolyte with hydrogen and use a polycrystalline platinum electrode as the working.
⁃ Complete 10 cyclic voltammograms in the potential range −0.1–1 V versus a reversible hydrogen electrode (approximate from past calibrations) at 100 mV s−1, then one cathodic linear sweep voltammogram at 10 mV s−1 in the same potential range.
⁃ Use the hydrogen oxidation/evolution intercept as the reference to hydrogen calibration.
5. Connect an inert gas (nitrogen/argon) cylinder with the gas bubbler. Slowly increase the regulator pressure from the cylinder until gas begins bubbling in the electrochemical cell. The gas should purge through the electrochemical cell for at least 15 min prior to beginning electrochemical measurements. A bubbler/scrubber is also preferred to remove line contaminants prior to the gas entering the electrochemical cell.
6. Using the potentiostat, attach the appropriate cables to the working electrode port, reference electrode, and counter electrode.
- Electrochemical Testing. Electrochemical measurements may begin once the electrochemical cell has been purged with inert gas, the RDE components are immersed in the electrolyte, and the potentiostat is on and connected to the RDE setup.
1. OER activity measurements
⁃ If potentiostat allows, immerse the RDE working electrode at 1.2 V (vs. RHE). Otherwise, immerse under closed or open circuit voltage conditions.
⁃ Condition for 50 cycles, 1.2–1.8 V vs. RHE at 100 mV s−1 and 2,500 rpm.
⁃ Remove the working electrode, rinse with water, and allow to dry to remove bubbles that formed on the electrode surface or within the catalyst layer. Re-immerse the working electrode into the electrolyte for the activity evaluation.
⁃ Reduce the scan rate to 20 mV s−1 to collect activity data. Scan from 1.2 to a variable upper potential limit.
⁃ NOTE: It is preferable to correct for internal resistance (current interrupt) in the program file and not during data analysis to minimize inaccuracies. The upper potential can vary, and the intent is to balance the current range (fixed when correcting for internal resistance) and to capture the entire kinetic region (moderate current range) while minimizing noise (low current range). The potential of comparison (1.5–2 V) may also need to change based on catalyst loading and intrinsic activity. Tafel plots should be consulted to ensure that activities were compared at a potential where the observed current was within the kinetic region and not biased by capacitance or transport.
2. Cyclic voltammogram measurements.
⁃ Potential cycle 0–1.5 V vs. RHE at 100 mV s−1 for five cycles or until the current response becomes stable. Limit excessive cycling at the low potential to minimize the impact of near-surface reduction on OER activity/stability.
⁃ Record voltammograms 0–1.5 V vs. RHE at 20 mV s−1 and 10 mV s−1 for three cycles.
⁃ Complete surface area determinations if equipment and safety considerations allow (Zhao et al., 2015; Alia et al., 2016b).
3. Stability testing. The purpose of this test is to assess the short-term stability of the electrocatalyst (test results should not be used to predict long-term durability). Rotate the working electrode at 2,500 rpm, or the highest rotation speed allowed to limit the impact of transport.
⁃ Stability testing is marginally relevant for device-level testing. Longer-term testing at high potential is preferred if inferring electrolysis-relevant durability. Test the stability of the catalyst at 2 V vs. RHE for 13.5 h (Alia and Anderson, 2019).
⁃ NOTE: Longer durations and high potentials are preferred in RDE durability testing. If these conditions (2 V for 13.5 h) cannot be completed due to poor catalyst stability, short-term stability testing (example 1.55 V for 1 h) can be used to assess whether a catalyst is suitable for device-level performance testing.
⁃ Following the conclusion of the stability test, withdraw the RDE working electrode, rinse it with water, and allow it to dry to remove bubbles that formed on the electrode surface or within the catalyst layer. Pipette 10 ml of the solution into a centrifuge tube for analysis with inductively coupled plasma mass spectrometry (ICP-MS). Replicates and repeated tests are encouraged.
⁃ Discard electrolyte, rinse electrochemical cell (water, then fresh perchloric acid electrolyte), and fill with perchloric acid electrolyte. Re-immerse the working electrode into the electrolyte for the activity evaluation and cyclic voltammograms after the stability test (repeat procedures in steps 1 and 2).
⁃ NOTE: For catalyst stability, report dissolution data (ICP-MS) and OER activity following the potential hold. It is not preferable to report the raw current decrease during the potential hold due to the significant impact of transport on electrode activity over time, which is not a relevant loss mechanism. Potential holds are preferred for stability tests, since potential drives catalyst dissolution; RDE current holds can result in large differences in potential exposure that narrow in device-level testing (catalyst integration and site access differences, use of a membrane); RDE transport losses can increase potential and catalyst dissolution in a way that is not device relevant; and at particularly low current density, RDE may not be reflective of device-level operation or catalyst layer stresses (Alia et al., 2019; Alia, 2021; Alia et al., 2021).
3.2 Sample Handling and Preservation
• If significant time passes between the working electrode coating drying and the start of testing, cover the working electrode to ensure that nothing touches the thin film prior to or during testing.
• If there is a brief amount of time between the drying of the film and the start of the testing, place a small drop of deionized water or electrolyte solution on the thin film to prevent contamination from the air.
• If there are any open ports to the electrochemical cell, cover with a cleaned, glass stopper. Ensure that the electrolyte does not touch any foreign material.
• Following the conclusion of each test, ensure that all glassware is stored in a cleaned glass beaker filled with deionized water. Cover the beaker with a cleaned watch glass to prevent contamination and limit evaporation. The beaker and cell must be recleaned periodically.
• When checking for the presence of catalyst material in the electrolyte (catalyst degradation), stir the electrolyte to ensure mixing, then carefully pour or pipette 10 ml of the solution into an aliquoting vessel for ICP-MS. Record the volume/mass of cells with and without electrolytes at the starting point of the test.
3.3 Computer Hardware and Software
• The potentiostat software will be required to perform the electrochemical tests and may be able to assist in data analysis. This software may be hardware specific and not standardized for this protocol.
4 Results
Comparisons of OER activities between NREL and LBNL are included in Figure 1. This comparison was completed on four different catalysts–iridium from Tanaka Kikinzoku Kogyo (TKK, product number US171109), iridium from Johnson Matthey (JM, product number C2026/160000), iridium oxide from Alfa Aesar (AA, product number 43396), and iridium oxide supported on titania from Umicore (0821/01-D5). While similar activities were found at 1.55 V vs. RHE for JM iridium, significant differences were observed for the other catalysts (2.3x TKK, 1.8x AA, 4.2x Umicore) and continued efforts are needed to close these gaps. These differences, however, tend to be smaller than for the broader community (Alia and Anderson, 2019).
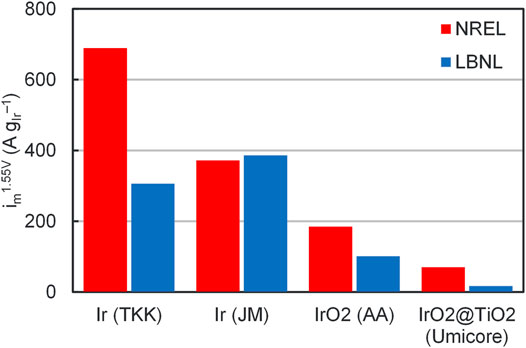
FIGURE 1. Catalyst OER mass activities at 1.55 V for NREL (red) and LBNL (blue), comparing TKK, JM, AA, Umicore catalysts. Data adapted from (Alia et al., 2016a; Alia and Anderson, 2019).
Several differences in material, ink, and test conditions were noted that may have contributed to activity differences. First, the catalyst tested by NREL/LBNL were from different batches/lot numbers, and time elapsed between when these materials were purchased. Catalyst differences over time and between batches can have a significant effect on activity and have been observed in several instances. For the TKK catalyst, the higher NREL activity may have been due to higher metal content and a more complete oxide was generally found in later batches (Alia and Anderson, 2019). Second, differences in how electrodes were cleaned and coated were found. This included electrode polishing (automated polisher/manual), ink icing (iced/not), and sonication (bath/horn and duration). Third, differences were also found in how electrodes were tested, including the experimental setup (cell design, glassware manufacturer and purity, hydrogen/chloride reference electrode, Luggin capillary) and whether or not working electrodes were rinsed and dried between conditioning and activity testing to minimize transport concerns.
Specific considerations and concerns are also included to address potential deviations that focus on the electrode coating process and test methodology. A demonstration of a preferred and not preferred working electrode coating is included in Figure 2, after having been coated with AA iridium to loading of 17.8 µgIr cm−2. In this particular instance, differences were based on whether the electrode was rotated during the coating/drying process. In general, however, significant ink or coating inadequacies tend to present visually on the working electrode surface. For the ink, these nonidealities include low ionomer content, unoptimized solvent ratios, less sonication, not thoroughly iced inks, and catalyst settling; for coating, these include coating/drying without rotation and electrodes that have been roughened or inadequately resurfaced.

FIGURE 2. Working electrodes coated with AA iridium to a loading of 17.8 µgIr cm−2, (A) without and (B) with electrode rotation (Alia and Anderson, 2019). © The Electrochemical Society. Reproduced by permission of IOP Publishing. All rights reserved.
In activity determinations, chronoamperometry and voltammograms can be valid provided that the comparisons are made in the kinetic region. Voltammograms include the capacitive region and force the user to make evaluations at moderate potential/current density to avoid the capacitance or incorporate capacitance in kinetic comparisons. Chronoamperometry experiments remove the capacitive region, but also dramatically increase transport losses at moderate potential/current density due to the increased experiment duration allowing for higher gas generation rates (Figure 3) (Alia and Anderson, 2019). The increase in transport loss lowers the potential window for kinetic comparisons and puts higher-performing catalysts at a disadvantage due to the higher gas generation rate. Chronoamperometry experiments thereby force the user to make evaluations at low potential/current density to avoid or minimize transport. Linear sweep voltammograms at 20 mV s−1 are preferred to avoid capacitance (faster scan rates), avoid transport (slower scan rates, chronoamperometry), and expand the kinetically-valid potential window to moderate current density (measurement accuracy).
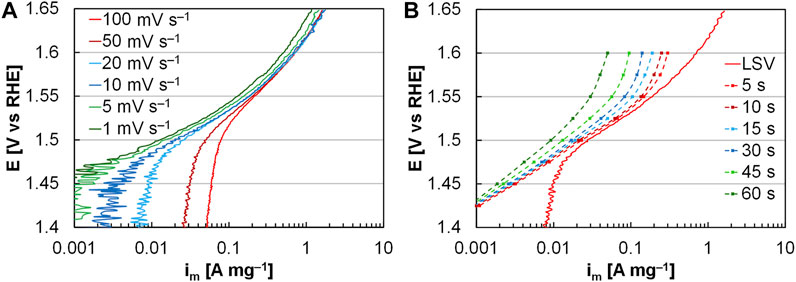
FIGURE 3. (A) Linear sweep voltammograms at varying scan rates. (B) Successive chronoamperometry tests, varied by duration, compared to a linear sweep voltammogram at 20 mV s−1. Electrodes were coated with AA iridium to a loading of 17.8 µgIr cm−2 (Alia and Anderson, 2019). © The Electrochemical Society. Reproduced by permission of IOP Publishing. All rights reserved.
5 Quality Control and Quality Assurance
5.1 Instrument or Method Calibration and Standardization
Two aspects of RDE testing require calibration and standardization: the electrochemical test setup, including glassware cleanliness, and electrode choice and placement; working electrode preparation, including the catalyst evaluated, electrode/substrate polishing, ink formulation, and electrode coating. These aspects can be verified and standardized through:
• Verify cell cleanliness with activity evaluations of a polycrystalline iridium disk (OER) or a polycrystalline platinum disk (oxygen reduction) (Shinozaki et al., 2015; Alia et al., 2016a). Verifying activity is preferred due to the higher sensitivity over evaluating cyclic voltammograms for specific adsorbates.
• Verify catalyst, ink, and coating process with evaluations of baseline materials (Alia and Anderson, 2019).
5.2 Cautions
Contamination is a significant source of activity error. Ensure that all cleaning procedures have been followed prior to testing.
5.3 Common Issues
Cleanliness, and the degree to which it is required, is a common issue in suboptimal performance. Cleaning procedures (acid exposure, water boiling) is needed for not only the electrochemical cell but anything that comes into contact with it. This includes other cell components (stoppers, counter electrode), glassware used for storage and to prepare the electrolyte, and glassware used for inks. Care should be taken to not introduce contaminants through contact (skin, countertop), storage, or working electrode polishing.
5.4 Interferences
There is a potential for signal noise to interfere with the electrochemical measurements. Grounding and proper current ranges need to be used to minimize signal noise.
5.5 Troubleshooting
Differences in the setup orientation, cleanliness, ink optimization, and test parameters can all impact activity values and published baselines can be used as comparison points (Alia et al., 2016a; Yu et al., 2018; Alia and Anderson, 2019; Rakousky et al., 2019). Testing of both nanoparticle catalysts and a polycrystalline iridium disk can be used to troubleshoot sub-optimal activity and the source of deficiencies. The disproportionately lower polycrystalline activity would suggest issues with cleaning protocols; disproportionately lower nanoparticle activity would suggest issues with catalyst ink or working electrode coating.
5.6 Error Analysis
Error analysis is critical in separating causes of suboptimal activity. Use a polycrystalline iridium electrode to separate errors due to the cell setup (cleanliness and configuration) and the catalyst/working electrode fabrication process.
6 Discussion
Materials and test choices are critical in minimizing differences in baseline activity.
In materials choices, the electrodes and their composition have impact on activity observations. While non-hydrogen reference electrodes are a cost-effective solution, the inaccuracy makes standardization more difficult. While the use of platinum hydrogen evolution/oxidation can minimize those inaccuracies (compared to a multimeter), regular calibration is needed as the value drifts (typically a few millivolts per day) and before/after each electrode set is preferred. The use of non-hydrogen references may also introduce contaminants (chloride, sulfate), and more frequent cell cleaning is needed to minimize the impact. Gold is also typically used as the working electrode substrate and the counter electrode, to improve stability at high potential (working) while minimizing contaminant effects (carbon counter) and a plating benefit (Pourbaix, 1974; Alia and Pivovar, 2018). A gold working substrate, however, can oxidize and electronically isolate portions of the catalyst layer; dissolution can also delaminate the catalyst layer. Electrode polishing (as smooth as possible) and ink/coating process optimization are necessary to minimize substrate/electrolyte contact and substrate contributions to catalyst durability measurements, along with limiting the operating potential and avoiding internal resistance corrections (Alia and Anderson, 2019). Gold as a substrate also impacts surface area measurements, and duplicate experiments with glassy carbon electrodes may be necessary for surface area validation (Alia et al., 2016b). Although the counter electrode choice is less critical in OER due to the operating potential, gold may be necessary under circumstances where a negative current is applied to condition the working electrode (Alia and Pivovar, 2018).
In test choices, conditioning protocols vary dramatically and are often shorter or to lower potential than those presented here. Minimal to no conditioning may be necessary to preserve faceting or to minimize the impact of electrochemical testing. Longer protocols however are generally needed to marginally project device-level kinetics and should be included with statements on the far-reaching impact of a specific materials approach (Alia et al., 2019). Transport in RDE also has a significant effect on activity and stability assessments, due to the convective working electrode rotation (as opposed to a flowing electrolyte) and orientation (level, face-down). In activity testing, care needs to be taken to avoid incorporating transport into assessments and including site-level gas trapping and bulk bubble formation. When using longer conditioning protocols, electrodes need to be rinsed and dried prior to activity assessments due to the role bubble formation plays in blocking catalyst sites. In stability testing, the unprocessed performance decrease should not be reported as material stability since the RDE transport does not correspond to a relevant loss mechanism and reporting of the dissolution rate and activity after testing (with rinsing, drying) is preferred. Transport, however, still alters these measurements through bubble formation lessening site access and other experimental approaches (flow cell) may be better suited to evaluate material stability in a less qualitative way.
Data Availability Statement
The original contributions presented in the study are included in the article/Supplementary Material, further inquiries can be directed to the corresponding author.
Author Contributions
All authors listed have made a substantial, direct, and intellectual contribution to the work and approved it for publication.
Funding
This work was authored by the National Renewable Energy Laboratory, operated by Alliance for Sustainable Energy, LLC, for the U.S. Department of Energy (DOE) under Contract No. DE-AC36-08GO28308, and Lawrence Berkeley National Laboratory under Contract Number DE-AC02-05CH11231. Funding was provided by U.S. Department of Energy Office of Energy Efficiency and Renewable Energy, Hydrogen and Fuel Cell Technologies Office.
Author Disclaimer
The views expressed in the article do not necessarily represent the views of the DOE or the U.S. government. The U.S. government retains and the publisher, by accepting the article for publication, acknowledges that the U.S. government retains a nonexclusive, paid-up, irrevocable, worldwide license to publish or reproduce the published form of this work, or allow others to do so, for U.S. government purposes.
Conflict of Interest
The authors declare that the research was conducted in the absence of any commercial or financial relationships that could be construed as a potential conflict of interest.
Publisher’s Note
All claims expressed in this article are solely those of the authors and do not necessarily represent those of their affiliated organizations, or those of the publisher, the editors, and the reviewers. Any product that may be evaluated in this article, or claim that may be made by its manufacturer, is not guaranteed or endorsed by the publisher.
References
Alia, S. M., and Anderson, G. C. (2019). Iridium Oxygen Evolution Activity and Durability Baselines in Rotating Disk Electrode Half-Cells. J. Electrochem. Soc. 166, F282–F294. doi:10.1149/2.0731904jes
Alia, S. M. (2021). Current Research in Low Temperature Proton Exchange Membrane-Based Electrolysis and a Necessary Shift in Focus. Curr. Opin. Chem. Eng. 33, 100703. doi:10.1016/j.coche.2021.100703
Alia, S. M., Ha, M.-A., Anderson, G. C., Ngo, C., Pylypenko, S., and Larsen, R. E. (2019). The Roles of Oxide Growth and Sub-surface Facets in Oxygen Evolution Activity of Iridium and its Impact on Electrolysis. J. Electrochem. Soc. 166, F1243–F1252. doi:10.1149/2.0771915jes
Alia, S. M., Hurst, K. E., Kocha, S. S., and Pivovar, B. S. (2016). Mercury Underpotential Deposition to Determine Iridium and Iridium Oxide Electrochemical Surface Areas. J. Electrochem. Soc. 163, F3051–F3056. doi:10.1149/2.0071611jes
Alia, S. M., Manco, J., Anderson, G. C., Hurst, K. E., and Capuano, C. B. (2021). The Effect of Material Properties on Oxygen Evolution Activity and Assessing Half-Cell Screening as a Predictive Tool in Electrolysis. J. Electrochem. Soc. 168, 104503. doi:10.1149/1945-7111/ac28c5
Alia, S. M., and Pivovar, B. S. (2018). Evaluating Hydrogen Evolution and Oxidation in Alkaline Media to Establish Baselines. J. Electrochem. Soc. 165, F441–F455. doi:10.1149/2.0361807jes
Alia, S. M., Rasimick, B., Ngo, C., Neyerlin, K. C., Kocha, S. S., Pylypenko, S., et al. (2016). Activity and Durability of Iridium Nanoparticles in the Oxygen Evolution Reaction. J. Electrochem. Soc. 163, F3105–F3112. doi:10.1149/2.0151611jes
Ayers, K., Danilovic, N., Ouimet, R., Carmo, M., Pivovar, B., and Bornstein, M. (2019). Perspectives on Low-Temperature Electrolysis and Potential for Renewable Hydrogen at Scale. Annu. Rev. Chem. Biomol. Eng. 10, 219–239. doi:10.1146/annurev-chembioeng-060718-030241
Garsany, Y., Baturina, O. A., Swider-Lyons, K. E., and Kocha, S. S. (2010). Experimental Methods for Quantifying the Activity of Platinum Electrocatalysts for the Oxygen Reduction Reaction. Anal. Chem. 82, 6321–6328. doi:10.1021/ac100306c
IRENA (2020). Green Hydrogen Cost Reduction: Scaling up Electrolysers to Meet the 1.5⁰C Climate Goal. Abu Dhabi: International Renewable Energy Agency.
Pivovar, B., Rustagi, N., and Satyapal, S. (2018). Hydrogen at Scale (H 2 @Scale): Key to a Clean, Economic, and Sustainable Energy System. Electrochem. Soc. Interface 27, 47–52. doi:10.1149/2.f04181if
Pourbaix, M. (1974). Atlas of Electrochemical Equilibria in Aqueous Solutions. Houston, Texas: National Association of Corrosion Engineers.
Rakousky, C., Shviro, M., Carmo, M., and Stolten, D. (2019). Iridium Nanoparticles for the Oxygen Evolution Reaction: Correlation of Structure and Activity of Benchmark Catalyst Systems. Electrochimica Acta 302, 472–477. doi:10.1016/j.electacta.2018.11.141
Shinozaki, K., Zack, J. W., Richards, R. M., Pivovar, B. S., and Kocha, S. S. (2015). Oxygen Reduction Reaction Measurements on Platinum Electrocatalysts Utilizing Rotating Disk Electrode Technique. J. Electrochem. Soc. 162, F1144–F1158. doi:10.1149/2.1071509jes
Yu, H., Danilovic, N., Wang, Y., Willis, W., Poozhikunnath, A., Bonville, L., et al. (2018). Nano-size IrOx Catalyst of High Activity and Stability in PEM Water Electrolyzer with Ultra-low Iridium Loading. Appl. Catal. B Environ. 239, 133–146. doi:10.1016/j.apcatb.2018.07.064
Keywords: electrolysis, rotating disk electrode, oxygen evolution, catalysis, acidic systems
Citation: Alia SM and Danilovic N (2022) Rotating Disk Electrode Standardization and Best Practices in Acidic Oxygen Evolution for Low-Temperature Electrolysis. Front. Energy Res. 10:857663. doi: 10.3389/fenrg.2022.857663
Received: 18 January 2022; Accepted: 18 April 2022;
Published: 09 September 2022.
Edited by:
Roel Van de Krol, Helmholtz Association of German Research Centers (HZ), GermanyReviewed by:
Diogo M. F. Santos, University of Lisbon, PortugalBranimir Nikola Grgur, University of Belgrade, Serbia
Copyright © 2022 Alia and Danilovic. This is an open-access article distributed under the terms of the Creative Commons Attribution License (CC BY). The use, distribution or reproduction in other forums is permitted, provided the original author(s) and the copyright owner(s) are credited and that the original publication in this journal is cited, in accordance with accepted academic practice. No use, distribution or reproduction is permitted which does not comply with these terms.
*Correspondence: Shaun M. Alia, c2hhdW4uYWxpYUBucmVsLmdvdg==