- Faradion Limited, Sheffield, United Kingdom
Bipolar electrodes can be defined as electrodes where cathode and anode active materials exist on either side of a shared current collector substrate. The resultant rechargeable bipolar batteries, using series-connected electrochemical cells within one sealed enclosure, can enable high-voltage systems irrespective of the voltage of the cathode//anode couple used. The sodium-ion battery, being well-suited for the bipolar concept, is now rapidly being commercialized and has higher energy densities than most rechargeable battery technologies. However, bipolar sodium-ion batteries using commercially-feasible liquid electrolytes and manufacturing methodologies, have not been demonstrated at scale yet. Herein, we explore the design methodology needed to enable commercial realization of such bipolar sodium-ion batteries, using liquid electrolytes and different types of cathode//anode couples. We show good cycling stabilities over 200 cycles and potential for voltages beyond 6 V for bipolar Na-ion pouch cells. We also introduce a scalable method to fabricate nSmP Na-ion/mixed-chemistry bipolar cells (n cells in series; m cells in parallel) in a single, sealed cell. Our results point to realistic promise for high voltage and sustainable bipolar sodium-ion batteries.
Introduction
The most energy-dense rechargeable battery technology commercially available currently is the layered oxide cathode//graphite anode-based lithium-ion (Li-ion) battery (The Faraday Institution, 2020). The nominal voltage of such Li-ion cells is around 3.6 V (Ha and Park, 2018; Lain et al., 2019). However, for most applications nowadays such as electric vehicles and stationary energy storage, or even consumer electronics, the battery’s voltage is designed to be higher than that of a single Li-ion cell’s voltage: system voltages in excess of 48 V or even 420 V are common for the former (ZVEI - German Electrical and Electronic Manufacturers’ Association, 2013; Vynakov et al., 2016; Sonnen GmbH, 2019; Nguyen et al., 2020; Sehil et al., 2020), while battery output voltages such as 7.2 V or 14.6 V can be routinely used for the latter (Canon, 2022; HPJC04, 2022). This is because, as noted by Professor Huggins, high voltage batteries fundamentally have a higher energy quality than low voltage batteries, a concept analogous to heat quality from thermodynamics (Huggins, 2008). Thus, the rechargeable battery community, over the last hundred years, has been constantly looking to increase the voltage of individual electrochemical cells, with the modern-day Li-ion battery delivering one of the highest voltage values per electrochemical cell. Today’s sodium-ion (Na-ion) batteries’ delivered voltages and capacities can be slightly lower than those of high-voltage layered oxide cathode-based Li-ion batteries, resulting in lower energy densities (Rudola et al., 2021a; Lilley, 2021; Tapia-Ruiz et al., 2021). However, the Na-ion battery uses Al current collectors for both the anode and cathode: this is different from that of graphite anode-based Li-ion batteries, which are forced to use Cu current collector on the anode, due to Cu dissolution concerns (Rudola et al., 2021c). Apart from Al being lighter and cheaper than Cu and endowing Na-ion batteries the option of safe overdischarge capabilities to 0 V (Rudola et al., 2021c), the use of Al current collectors for both cathodes and anodes opens the door for rechargeable Na-ion batteries using bipolar electrodes.
The concept of bipolar electrodes (where anode and cathode active materials exist on either side of a shared current collector material) for use within a rechargeable battery, has been known at least since 1899 when Leonard Paget patented a bipolar rechargeable lead-acid battery (Paget, 1899). Over the ensuing decades, this concept has been optimized further in rechargeable lead-acid batteries (Bullock, 1995; Ellis et al., 2004; Karami et al., 2007; Pradhan and Chakraborty, 2020), and spilled over onto other types of rechargeable battery technologies, such as nickel metal hydride (Wiesener et al., 1999), alkali-metal based (Gambe et al., 2015), or the modern-day Li-ion (Marsh et al., 1997; Ogihara et al., 2014; Hu, 2016; Kim et al., 2018; Liu et al., 2020), and Na-ion batteries (Liu et al., 2019). In such bipolar batteries, various electrochemical cells are connected in series (S) within one sealed enclosure—this is different from the conventional battery design, where individual cells are connected in parallel (P) within one sealed entity. Thus, if n number of cells are series-connected within one sealed battery enclosure, the resultant nS(1P) bipolar battery will display n times the voltage and the same capacity as that of one electrochemical cell. In contrast, conventional Li-ion/Na-ion batteries might have m number of cells in parallel-connection within the battery enclosure, resulting in a (1S)mP configuration: here, the battery’s voltage will be the same as that of a single electrochemical cell, but the capacity will be m times the capacity of a single electrochemical cell. It should be noted that in the literature, the term “bipolar” can sometimes be used to refer to active materials that can be used as the cathode or the anode (Guo et al., 2015; Li et al., 2019); however, we think that such materials (or batteries using the same cathode and anode active materials) should be called “symmetric,” since the term “bipolar” has been well-established in the rechargeable battery field for over a century.
To design a 48 V battery system, for example, several individually-sealed cells have to be connected in series: this arrangement results in two important disadvantages. The first is that there is more “dead weight and volume” within the finalized battery pack, due to greater amount of electrochemically-inactive components such as cell packaging/casing, electrical connecting wires, connecting tabs and the power electronics associated with the battery management system of the pack. The second important disadvantage is that the greater amount of connecting wires and tabs, which are all typically designed to be as thin as possible to enhance a battery’s energy density, is a significant source of heat generation (via Joule heating) especially at moderate-to-high discharge (Linden and Reddy, 2002; Huggins, 2008). Thus, such batteries have higher internal resistance and due to this, enhanced heat generation—these factors can significantly negatively affect performance at the system-level and necessitate a need for more effecting cooling systems (Xu and He, 2014; Choudhari et al., 2020). Using bipolar electrodes conveniently circumvents both of the above problems. Firstly, if the battery pack consists of bipolar batteries with each entity having a much higher voltage than that of a single electrochemical cell, fewer individual bipolar batteries would be required to meet the system requirements (assuming the capacity can be met). Secondly, internal heat generation within each battery will be much lower, as the direction of current flow within one battery will be perpendicular to that of the cathode//anode stack (the cross-sectional surface area of current collectors used in most batteries for such applications is typically high), along with the fact that lower current rates would be needed for a particular power output, engendered by the high voltage of the batteries (Linden and Reddy, 2002; Liu et al., 2020). Lastly, it is a straightforward task to fabricate large-capacity electrochemical cells, by simply increasing the footprint of the cathode and anode: thus, it is possible, in theory, to fabricate large capacity (such as 10 or 50 Ah) and high voltage (20 or 48 V) systems, within one sealed battery enclosure, without associated pack electronics. This engineering challenge if solved, has the potential to revolutionize the battery systems of several applications. As mentioned in prior publications, batteries utilizing bipolar electrodes can ultimately show several advantages over conventional batteries such as reductions in battery weight, size and cost; capabilities for high power performance due to reduced internal resistance in the battery; and possibilities for simplification of battery pack design and manufacturing due to reduction/elimination of components such as pack electronics and/or cooling systems; all of which would ultimately improve the battery pack’s specific energy (Wh/kg) or power (W/kg), energy or power density (Wh/l or W/l, respectively) and cost ($/kWh) (Bullock, 1995; Wiesener et al., 1999; Linden and Reddy, 2002; Kim et al., 2018; Liu et al., 2020; Pradhan and Chakraborty, 2020).
Despite such immense promise, bipolar Li-ion or Na-ion batteries have not been commercialized yet due to an important engineering issue. Since commercial Li-ion and Na-ion batteries use liquid electrolytes, use of bipolar electrodes can lead to electrolyte leakage between adjacent series-connected cells in these bipolar batteries: electrolyte leakage typically results in rapid capacity fade, a commercially infeasible proposition. This problem has been known for decades and also seen in other battery technologies, such as the rechargeable lead-acid bipolar battery, where researchers have resorted to complicated cell designs with sealing gaskets to enable successful operation (Einstein, 1980; Kaun, 1992; Ginatta and Rossetti, 1994; Hossain, 1995; Ogg et al., 2010). To avoid the liquid electrolyte leakage concerns, bipolar Li-ion or Na-ion batteries have been historically designed with solid electrolytes or gel polymer electrolytes (Hu, 2016; Liu et al., 2020), where restrictions on the movement of Li+ or Na+ between adjacent electrochemical cells is quite easy to control from an engineering perspective. However, solid-state Li-ion or Na-ion batteries have still not been commercialized at scale yet, despite intense research focus over the last decade (Faraday, 2020; Pasta et al., 2020). In 2009, Chami et al. demonstrated a viable Li-ion battery using bipolar electrodes comprised of LiFePO4 (LFP) cathode and Li4Ti5O12 (LTO) anode where both active materials were coated on either side of Al current collector (Chami et al., 2009). Since LTO’s redox potential is high, around 1.5 V vs. Li/Li+ (allowing use of Al current collector for the anode), the resultant voltage of a single LFP//LTO cell is quite low, around 1.9 V. Thus, though bipolar batteries based on n LFP//LTO bipolar electrodes can deliver n × 1.9 V within a sealed enclosure, such a voltage value is not significantly high and actually lower than the ∼2.1 V deliverable by the rechargeable lead-acid battery (though LFP//LTO batteries have other benefits such as much longer cycle lives, higher energy density and high-power performance) (Linden and Reddy, 2002). The lower voltage of the bipolar LFP//LTO Li-ion battery was evidently not enough to convince the Li-ion industry to move towards this direction over the last decade. Bipolar Na-ion batteries, in principle, will not suffer the same limitations as LTO-based bipolar Li-ion batteries, due to the prospects of achieving high voltages (such as 3–3.7 V) from a single electrochemical cell (Barker et al., 2003; Tripathi et al., 2019; Monconduit and Croguennec, 2020; Subasinghe et al., 2020; Rudola et al., 2021a). Despite this promise, to the best of our knowledge, there has only been one report in the literature on bipolar Na-ion batteries using liquid electrolytes, but this was shown at a very small-scale (in coin cells) (Liu et al., 2019). The issue of electrolyte leakage can be controlled by workarounds at such small-scales (such as coin-cells typically used in first-stage laboratory research), but these will not be translatable to larger scales (such as cylindrical, pouch or prismatic cells typically used in most commercial applications), where a different design strategy would be needed.
In this contribution, we present our results on bipolar Na-ion batteries using liquid electrolytes in prototype pouch cells. We show, by carefully engineering a simple and scalable solution to the electrolyte leakage problem, that bipolar Na-ion batteries can actually be cycled over many cycles. We will present the universality of our approach using different Na-ion cathodes and anodes, from 1.2 V cathode//anode couples, to 3 V cathode//anode couples. We will also present the first results on nSmP bipolar Na-ion batteries, which not only demonstrate n times the voltage of a Na-ion cathode//anode couple, but can also deliver m times the capacity for a given electrode footprint, all within one sealed enclosure. Lastly, we introduce the concept of mixing different Na-ion chemistries within a single bipolar battery, to yield electrochemical curves not previously possible from one sealed battery cell: such a concept can allow battery manufacturers to propose specific solutions for a market application, which might not have necessarily existed using today’s known Na-ion storage materials.
Materials and Methods
Detailed steps on pouch cell assembly, including three-electrode cell assembly, have been reported previously (Rudola et al., 2021a; Rudola et al., 2021b; Rudola et al., 2021). Notes on fabricating bipolar cells, along with performance of initial failed experiments with imperfectly designed bipolar pouch cells, have been explained in Supplementary Note S1 and Supplementary Figure S1, in the Supplementary Information.
Details about the Faradion’s O3/P2 Oxide layered cathodes were reported in prior publications (Barker and Heap, 2020; Sayers et al., 2020; Rudola et al., 2021a). In this work, we used the same commercial hard carbon anode and the 1 M NaPF6 in carbonate-ester electrolyte as reported in our recently published article (Rudola et al., 2021b). The NVP and NTP materials used in this work were synthesized by the soft-template method described in prior publications, which also presented their material as well as electrochemical characterization experiments (Saravanan et al., 2013; Rudola et al., 2014; Rudola et al., 2018). TiS2 was purchased from Sigma Aldrich (99.9%, 200 mesh) and used as received. The electrode formulation for the NVP, NTP and TiS2 electrodes was active material:binder:conductive carbon = 80:10:10 wt/wt, for the O3/P2 Oxide cathode was 89:06:05 wt/wt and for the hard carbon anode was 88:09:03 wt/wt. The active material loadings for all electrodes ranged from 5–15 mg/cm2. All cycling experiments were conducted at 30°C, and the voltage limits along with the cathode:anode mass balance has been provided for each experiment. All other relevant experimental procedures were the same as those described in our recent publication (Rudola et al., 2021b).
Results and Discussion
Optimizing the Bipolar Cell Design With Liquid Electrolytes
Refer to Supplementary Note S1 and Supplementary Figure S1 for preliminary optimization results on the design of bipolar Na-ion cells with liquid electrolytes and commercially-available polyolefinic separators. Briefly, these optimization experiments showed that it was absolutely vital to ensure that the polyolefinic separator from one cell within a bipolar battery did not touch the separator of adjacent cells. As a consequence, the separator footprint had to be the same as the cathode footprint. Since any commercial Li-ion or Na-ion cell’s anode footprint is slightly larger than the cathode footprint, to enable successful cycling of such a cell design without internally short-circuiting the cells, it was found that the edges of the anode had to be insulated with a suitable medium to compensate for the reduced size of the separator (refer to Supplementary Note S1 for details). This insulating medium could be any material, such as commonly utilized polyimide Kapton tape (used in this work), or an appropriate resin (used by Chami et al.) (Chami et al., 2009); this process can be easily automated in manufacturing lines, with great precision, thus ensuring scalability of our cell design.
Figure 1 presents cycling results of bipolar Na-ion pouch cells using the well-known Na3V2(PO4)3 (NVP) cathode//NaTi2(PO4)3 (NTP) anode Na-ion chemistry and liquid Na-ion electrolyte, following the lessons learnt from initial optimization trials. NVP and NTP were prepared by soft-template method described previously (Saravanan et al., 2013; Rudola et al., 2014; Rudola et al., 2018), and their half-cell cycling results are displayed in Supplementary Figure S2, showing excellent rate performance with good capacity retention from slow C/5 rate to faster rates such as 1C or 2C. This popular Na-ion cathode//anode pair displays a flat plateau at an average discharge voltage of around 1.2 V. As shown in Figure 1A, the 1S1P Na-ion NVP//NTP cell indeed delivered ∼1.2 V during discharge. The bipolar Na-ion NVP//NTP cell using 2 cm × 2 cm cathodes, with two cells internally connected in series within a sealed pouch cell enclosure (2S1P configuration), could deliver double the discharge voltage at around 2.4 V, while a bipolar NVP//NTP Na-ion battery with three cells (3S1P) could show three times the voltage, at around 3.6 V. These results confirmed successful series connection within the pouch cell. As an example of cycling stability, Figure 1B shows long-term cycling of the 2S1P bipolar NVP//NTP Na-ion pouch cell at 1C rate, over 200 cycles. Such a bipolar cell retained 72% of its original discharge capacity over 200 cycles. These are the first results of bipolar Na-ion pouch cells with liquid electrolyte and commercially-available polyolefinic separators; cycle lives such as 200 cycles point to good promise for such an approach in these initial stages of this technology-type.
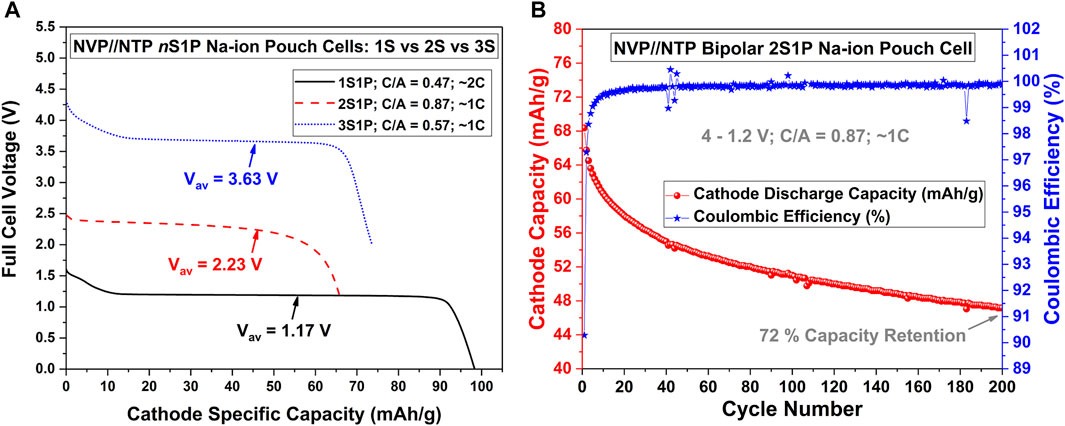
FIGURE 1. Performance of nS1P Bipolar NVP//NTP Na-ion Pouch Cells. (A) Comparison of the cycling curves of 1S1P, 2S1P and 3S1P NVP//NTP pouch cells using 2 cm × 2 cm cathodes. Note that “C/A” refers to the ratio of the active material in the cathode to that of the anode. The full cell cycling voltage limits for the three cells were as follows: 1S1P (1.9–0 V), 2S1P (4–1.2 V) and 3S1P (4.9–2 V). (B) Cycling stability over 200 cycles for the 2S1P bipolar NVP//NTP Na-ion bipolar pouch cell.
Scaling-Up Results and Concept of nSmP Bipolar Sealed Cells
We further scaled-up these results in pouch cells using cathodes with four times the surface area (4 cm × 4 cm) and in a different Na-ion chemistry, using Faradion’s patented mixed-phase O3/P2 layered oxide cathode (abbreviated as “O3/P2 Oxide”) (Barker and Heap, 2020; Sayers et al., 2020; Rudola et al., 2021a), and NTP anode. While this O3/P2 Oxide//NTP 1S1P cell could deliver an average discharge voltage of 1.08 V when cycled at C/5 rate between 2.4–0 V (see Supplementary Figure S3A), such bipolar 2S1P cells showed significantly higher mean discharge voltage of 1.7 V (refer to Figure 2A). The delivered capacity of the 2S1P cell was lower than the 1S1P cell (73 mAh/gcathode vs. 100 mAh/gcathode respectively), probably because some electrolyte leakage still occurred within this cell. The electrolyte leakage problem also resulted in a greater rate of capacity fade of the 2S1P cell vs. the 1S1P cell (see Figure 2B and compare with Supplementary Figure S3B). Since cells were hand-fabricated, it was easier to cover the anode edges with insulating tape on larger electrodes. In fact, sister cells of this chemistry fabricated using smaller footprint electrodes (2 cm × 2 cm cathodes) underperformed in terms of delivered capacity and mean discharge voltage (refer to Supplementary Figure S4). We thus believe that with larger footprint electrodes and with precision large-scale cell manufacturing lines, such hand-fabrication defects would not occur, and the electrochemical performance of large-scale bipolar Na-ion cells would be much better.
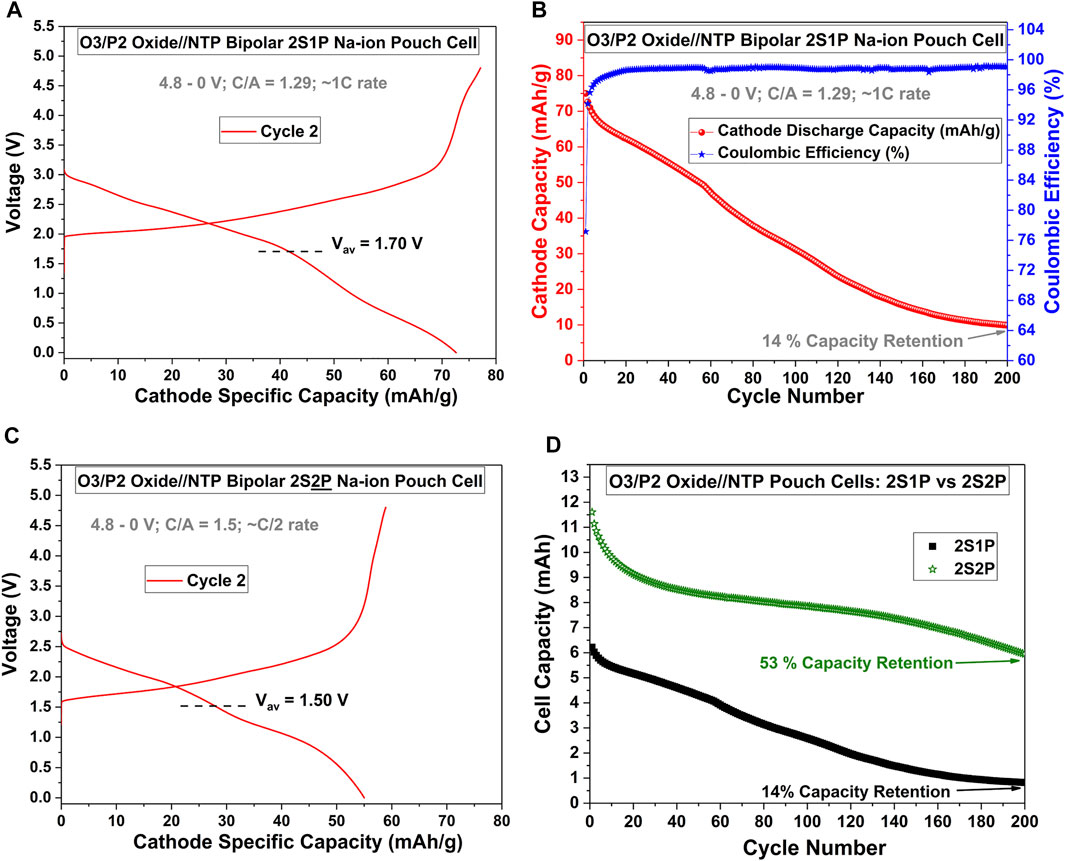
FIGURE 2. Scaling-up Bipolar Na-ion Pouch Cells to 4 cm × 4 cm Cathodes and Concept of nSmP Bipolar Cells. (A) Cycling curve of an O3/P2 Oxide//NTP 2S1P Na-ion bipolar pouch cell. (B) The corresponding cycle life of this cell. (C) Cycling curve of a 2S2P O3/P2 Oxide//NTP Na-ion bipolar pouch cell (refer to Supplementary Figure S5 for the electrode stack picture for this cell). (D) Comparison of the cycle lives of the 2S1P and the 2S2P cells: it can be seen that the cell capacity of the 2S2P cell doubles.
While the capacity of bipolar cells can be increased by increasing the footprint of the electrodes, some applications might require high voltage and high capacity within fixed dimensions. To further explore the utility of our bipolar cell design, we next investigated whether it would be possible to enhance voltage as well as capacity for a given chemistry without increasing the footprint of the cathode//anode stack, within one sealed battery enclosure. If successful, it was thought that this approach would be highly advantageous in order to give battery manufacturers the option of designing high-voltage and high-capacity batteries at any required dimensions, all within a single sealed enclosure devoid of complicated wiring and associated battery pack electronics. We fabricated a 2S2P bipolar battery with liquid electrolyte and polyolefinic separators, for the first time. Using the O3/P2 Oxide//NTP Na-ion chemistry and the 4 cm × 4 cm cathode footprint, we combined two separate 2S1P bipolar cells within a single pouch cell casing, to result in the 2S2P configuration. As illustrated in Supplementary Figure S5, to enable this concept to work, it is necessary to insulate the back face of an anode (or cathode) of cell 1, with the cathode (or anode, respectively) of cell 2. This layer can be made of any thin insulating material which is stable within the potential window of operation and in contact with the liquid electrolyte (the same polyimide Kapton tape was used herein, which was also used to insulate the edges of the anode). At large-scale, battery manufacturers can use a very thin (such as 5–10 µm) insulating material which will act as this electrode mask, only negligibly increasing the size and weight of the resultant nSmP bipolar battery. Figure 2C presents the cycling curves of cycle 2 of such a 2S2P cell at C/5 rate: the mean discharge voltage of 1.50 V was significantly higher than that of the 1S1P cell (1.08 V, see Supplementary Figure S3A), although the lower-than-expected mean discharge voltage was partly a result of the higher C/A of this cell (1.5 as opposed to the optimized ∼1.2, as shown in Supplementary Figure S3), and partly due to some inadvertent electrolyte leakage in this imperfectly fabricated bipolar cell. Of course, we expect that with precision large-scale cell manufacturing, such defects would be nullified. Importantly, as presented in Figure 2D, it can be seen that the discharge capacity of the 2S2P cell was doubled over the 1S1P cell despite using an identical footprint for the electrodes, confirming successful parallel (as well as series) connection within the sealed pouch cell. The encouraging long-term cycling stability validated this concept and points to a real promise towards future optimization with precise manufacturing controls. It should also be appreciated that the design concept outlined in this work is limited not only to Na-ion bipolar batteries, but could be applied to any alkali-ion bipolar batteries.
Beyond 5 V Na-Ion Bipolar Batteries
The real benefit of bipolar Na-ion batteries, over bipolar Li-ion batteries, is the possibility of much higher voltages for the former over the latter. To illustrate this, we fabricated bipolar Na-ion batteries using the O3/P2 Oxide//hard carbon (HC) chemistry. The performance of this Na-ion chemistry in 1SmP-type cells was described in our prior publications (Rudola et al., 2021a; Rudola et al., 2021). As an illustration, Figure 3A shows the C/10 cycling profile of cycle 1 of such a 1S2P O3/P2 Oxide//HC prototype Na-ion cell, between 4–1 V, using a larger footprint cathode (7.9 cm × 3.9 cm). It can be seen that this 1S2P cell could deliver 98 mAh/gcathode at a mean discharge voltage of 3.08 V. By utilizing the same design approach outlined in the previous sections, a 2S2P version of this Na-ion chemistry was fabricated (see Supplementary Figure S6 for the resultant 7.9 cm × 3.9 cm cathode 2S2P stack) and Figure 3B shows the cycling profile of cycle 1 at C/10 for such a bipolar cell. When cycled between 8–2 V, this 2S2P bipolar Na-ion cell could deliver 95 mAh/gcathode at a mean discharge voltage of 6.01 V. Such voltage values are not easily obtained from Li-ion bipolar batteries when using 2SmP configurations, pointing to the inherent advantages of bipolar Na-ion batteries, made possible by utilizing Al current collectors on the cathode as well as the anode. It is worth mentioning that we have already confirmed that using true bipolar electrodes (cathode and anode coated on either side of a shared Al current collector) would not have any impact on cycling. A 2S1P O3/P2 Oxide//HC Na-ion bipolar cell, using one bipolar electrode in the middle (see Supplementary Figure S7A for stack pictures), resulted in identical performance to that of the bipolar cell constructed with single sided-coated bipolar electrodes (compare cycling curves of Figure 3B and Supplementary Figure S7B). These results add further confidence to the viability of bipolar cells with liquid electrolytes using our methodology.
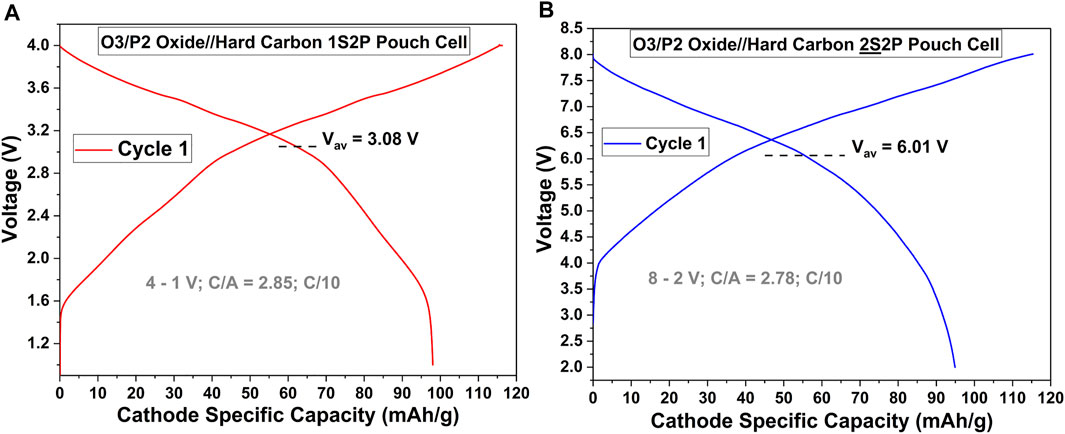
FIGURE 3. Beyond 5 V Bipolar Na-ion Pouch Cells using 7.9 cm × 3.9 cm Cathodes. (A) Cycling curve of an O3/P2 Oxide//HC 1S2P Na-ion pouch cell. (B) Cycling curve of a 2S2P O3/P2 Oxide//HC Na-ion bipolar cell demonstrating double the voltage and the same capacity, within a single sealed cell.
Designing Custom Cell Voltage Profiles for Specific Applications
The concept of nSmP bipolar cells opens the door for designing bespoke electrochemical curves from a single sealed alkali-ion cell, which might not be possible based on currently known Li-ion, Na-ion or even K-ion storage materials. As an illustration, consider the cycling curves shown in Figure 4. This kind of an electrochemical cycling curve, between 4.9–0 V, is not possible for any known Na-ion cathode//anode coupling. The cycling curves shown in Figure 4 was made possible by combining a 1S1P NVP//NTP cell and a 1S1P O3/P2 Oxide//HC cell, to result in a 2S1P mixed Na-ion chemistry bipolar cell. The correct voltage window for such a 2S1P mixed chemistry Na-ion cell would have been 5.9–0 V, as the NVP//NTP chemistry was designed to be cycled between 1.9–0 V (see Figure 1A) and the O3/P2 Oxide//HC chemistry was designed to be cycled between 4–1 V (see Figure 3A). Due to hardware limitations, we cycled this 2S1P mixed-chemistry bipolar cell up to 4.9 V and thus, the O3/P2 Oxide//HC cell in particular was not charged to completion. However, the example illustrates what might be possible with such an approach. Perhaps an easier example to grasp might be the following. Say for a particular application, it might be desired to have a single Na-ion cell of 5 Ah capacity, delivering its capacity with a mostly flat voltage with the plateau around 5.4 V, to result in a 27 Wh battery. There is no known Na-ion cathode//anode couple that can meet this task within one sealed cell. However, by combining 2S1P NVP//NTP Na-ion chemistry as cells 1 and 2 (flat plateau output voltage ∼2.4 V) and Rhombohedral-Na2Fe2(CN)6 cathode//HC anode chemistry as cell 3 (flat plateau output voltage ∼3 V) (Rudola et al., 2017; Subasinghe et al., 2020) within a sealed bipolar 3S1P Na-ion cell, the appropriate cycling profile at the correct discharge voltage and capacity can be easily designed. This approach, extendable to other types of alkali-ion batteries as well, will offer an alternate solution to manufacturers to provide more appropriate and tailored battery solutions to their clients.
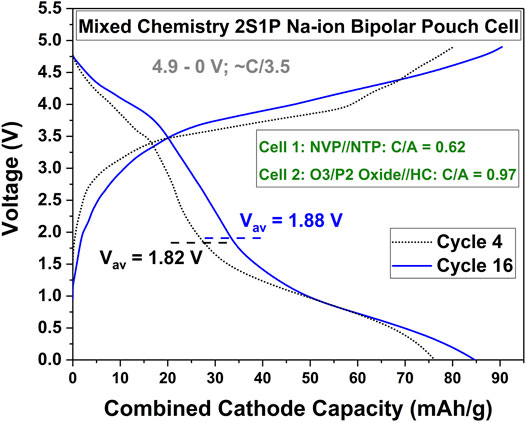
FIGURE 4. Concept of Mixed Chemistry Bipolar nSmP Cells. Cycling curves of an NVP//NTP and O3/P2 Oxide//HC mixed-chemistry 2S1P bipolar Na-ion cell demonstrating a completely unique cycling profile not possible from a single cathode//anode chemistry within a sealed cell.
Conclusion
In this article, we have revealed a simple strategy to enable fabrication of bipolar Na-ion pouch cells, using commercially-feasible materials and fabrication steps. We demonstrated various types of nSmP bipolar Na-ion cells using polyolefinic separators and liquid Na-ion electrolytes in a single sealed cell, offering output voltages in multiples of 1.1 V (for the O3/P2 Oxide//NTP chemistry), 1.2 V (for the NVP//NTP chemistry), 1.3 V (for the O3/P2 Oxide//TiS2 chemistry) or 3 V (for the O3/P2 Oxide//HC chemistry), as illustrative examples, the last of which is not easily possible for bipolar Li-ion cells. By circumventing the electrolyte leakage issue using a convenient and scalable engineering solution, we were able to demonstrate cycle lives such as 100 or 200 cycles for such bipolar Na-ion pouch cells at different stack dimensions, from 2 cm × 2 cm–7.9 cm × 3.9 cm cathode dimensions, for the very first time. Furthermore, herein we introduce the concept of nSmP mixed-chemistry alkali-ion bipolar cells, which can offer battery manufacturers the option of designing bespoke electrochemical cycling curves for different applications which would not otherwise have been possible within a single sealed cell enclosure.
These preliminary results on bipolar Na-ion cells, using similar manufacturing methodologies and materials existing currently for commercial alkali-ion cells, point to a realistic promise for realizing cost-effective and high voltage Na-ion bipolar cells. Upon further development of this type of technology for rechargeable batteries, we anticipate significant improvements to the design of existing battery systems for various commercial applications in several industry sectors, helping to lower costs, and enhance energy densities and system efficiencies.
Data Availability Statement
The original contributions presented in the study are included in the article/Supplementary Material, further inquiries can be directed to the corresponding authors.
Author Contributions
AR conceived the engineering design, performed most experiments and wrote the manuscript. JB supervised the work, performed some experiments and edited the manuscript. CW edited the manuscript. All authors participated in discussions of the results and their significance.
Conflict of Interest
AR, CW, and JB are employed by Faradion Limited.
Publisher’s Note
All claims expressed in this article are solely those of the authors and do not necessarily represent those of their affiliated organizations, or those of the publisher, the editors and the reviewers. Any product that may be evaluated in this article, or claim that may be made by its manufacturer, is not guaranteed or endorsed by the publisher.
Acknowledgments
The authors thank all Faradion staff and commercial partners for helping to achieve the results contained herein. AR thanks Ryan Malcolmson for coating bipolar electrodes, and Francesco Mazzali for coating NVP, NTP, and TiS2 electrodes.
Supplementary Material
The Supplementary Material for this article can be found online at: https://www.frontiersin.org/articles/10.3389/fenrg.2022.852630/full#supplementary-material
References
Barker, J., and Heap, R. (2020). O3/P2 Mixed Phase Sodium-Containing Doped Layered Oxide Materials WO Application. WO patent 2019197812A1.
Barker, J., Saidi, M. Y., and Swoyer, J. L. (2003). A Sodium-Ion Cell Based on the Fluorophosphate Compound NaVPO[sub 4]F. Electrochem. Solid-state Lett. 6, A1. doi:10.1149/1.1523691
Bullock, K. R. (1995). Progress and Challenges in Bipolar Lead‐Acid Battery Development. J. Electrochem. Soc. 142, 1726–1731. doi:10.1149/1.2048646
Canon (2022). Canon LP-E10 Battery Pack. Available at: https://store.canon.co.uk/canon-lp-e10-battery-pack/5108B002/(Accessed January 7, 2022).
Chami, M., Mailley, S., Reynier, Y., Masse, F., Martinet, S., and Fusalba, F. (2009). Safe Li-Ion Technology for Micro and Mild Hybrid Application Based on CEA Bipolar LiFePO4/Li4Ti5O12 Technology. Wevj 3, 735–739. doi:10.3390/wevj3040735
Choudhari, V. G., Dhoble, D. A. S., and Sathe, T. M. (2020). A Review on Effect of Heat Generation and Various thermal Management Systems for Lithium Ion Battery Used for Electric Vehicle. J. Energ. Storage 32, 101729. doi:10.1016/j.est.2020.101729
Ellis, K., Hill, A., Hill, J., Loyns, A., and Partington, T. (2004). The Performance of Ebonex Electrodes in Bipolar lead-acid Batteries. J. Power Sourc. 136, 366–371. doi:10.1016/j.jpowsour.2004.03.025
The Faraday Institution (2020). Faraday Report - January 2020. High-Energy Battery Technologies. The Faraday Institution. Available at: https://faraday.ac.uk/wp-content/uploads/2020/01/High-Energy-battery-technologies-FINAL.pdf (Accessed January 7, 2022).
Gambe, Y., Sun, Y., and Honma, I. (2015). Development of Bipolar All-Solid-State Lithium Battery Based on Quasi-Solid-State Electrolyte Containing Tetraglyme-LiTFSA Equimolar Complex. Sci. Rep. 5, 8869. doi:10.1038/srep08869
Guo, S., Yu, H., Liu, P., Ren, Y., Zhang, T., Chen, M., et al. (2015). High-performance Symmetric Sodium-Ion Batteries Using a New, Bipolar O3-type Material, Na0.8Ni0.4Ti0.6O2. Energy Environ. Sci. 8, 1237–1244. doi:10.1039/c4ee03361b
Ha, J. H., and Park, P. (2018). Product Specification: Rechargeable Lithium Ion Battery Model : INR21700 M50T 18.2Wh. Available at: https://www.batteryspace.com/prod-specs/11514.pdf (Accessed January 7, 2022).
Hpjc04, (2022). HP JC04 Rechargeable Battery Specifications. Available at: https://support.hp.com/in-en/document/c05735862 (Accessed January 7, 2022).
Huggins, R. (2008). Advanced Batteries: Materials Science Aspects. Springer Science & Business Media.
Karami, H., Shamsipur, M., Ghasemi, S., and Mousavi, M. F. (2007). Lead-acid Bipolar Battery Assembled with Primary Chemically Formed Positive Pasted Electrode. J. Power Sourc. 164, 896–904. doi:10.1016/j.jpowsour.2006.11.034
Kim, S.-H., Choi, K.-H., Cho, S.-J., Yoo, J., Lee, S.-S., and Lee, S.-Y. (2018). Flexible/shape-versatile, Bipolar All-Solid-State Lithium-Ion Batteries Prepared by Multistage Printing. Energ. Environ. Sci. 11, 321–330. doi:10.1039/c7ee01630a
Lain, M. J., Brandon, J., and Kendrick, E. (2019). Design Strategies for High Power vs. High Energy Lithium Ion Cells. Batteries 5, 64. doi:10.3390/batteries5040064
Li, X., Zhou, S., Wu, Q., Wang, X., Yao, T., Zhang, Y., et al. (2019). Na0.9Ni0.45Ti0.55O2 as Novel Bipolar Material for Sodium Ion Batteries. Solid State Ionics 334, 14–20. doi:10.1016/j.ssi.2019.01.033
Lilley, S. (2021). Sodium-ion Batteries: Inexpensive and Sustainable Energy StorageFaraday Insights- Issue 11 (The Faraday Institution). Available at: https://www.faraday.ac.uk/wp-content/uploads/2021/06/Faraday_Insights_11_FINAL.pdf (Accessed November 22, 2021).
Liu, T., Yuan, Y., Tao, X., Lin, Z., and Lu, J. (2020). Bipolar Electrodes for Next‐Generation Rechargeable Batteries. Adv. Sci. 7, 2001207. doi:10.1002/advs.202001207
Liu, T., Zhang, Y., Chen, C., Lin, Z., Zhang, S., and Lu, J. (2019). Sustainability-inspired Cell Design for a Fully Recyclable Sodium Ion Battery. Nat. Commun. 10, 1965. doi:10.1038/s41467-019-09933-0
Marsh, R. A., Russell, P. G., and Reddy, T. B. (1997). Bipolar Lithium-Ion Battery Development. J. Power Sourc. 65, 133–141. doi:10.1016/s0378-7753(96)02615-8
Nguyen, C. T. P., Nguyễn, B. H., Trovão, J. P. F., and Ta, M. C. (2020). Effect of Battery Voltage Variation on Electric Vehicle Performance Driven by Induction Machine with Optimal Flux‐weakening Strategy. IET Electr. Syst. Transportation 10, 351–359. doi:10.1049/iet-est.2020.0013
Ogg, R., Smith, D. R., and Park, D. F. (2010). Bi-polar Rechargeable Electrochemical Battery. US Patent, 7794877.
Ogihara, N., Yasuda, T., Kishida, Y., Ohsuna, T., Miyamoto, K., and Ohba, N. (2014). Organic Dicarboxylate Negative Electrode Materials with Remarkably Small Strain for High-Voltage Bipolar Batteries. Angew. Chem. Int. Ed. 53, 11467–11472. doi:10.1002/anie.201405139
Pasta, M., Armstrong, D., Brown, Z. L., Bu, J., Castell, M. R., Chen, P., et al. (2020). 2020 Roadmap on Solid-State Batteries. J. Phys. Energ. 2, 032008. doi:10.1088/2515-7655/ab95f4
Pradhan, S. K., and Chakraborty, B. (2020). Substrate Materials and Novel Designs for Bipolar lead-acid Batteries: A Review. J. Energ. Storage 32, 101764. doi:10.1016/j.est.2020.101764
Rudola, A., Aurbach, D., and Balaya, P. (2014). A New Phenomenon in Sodium Batteries: Voltage Step Due to Solvent Interaction. Electrochemistry Commun. 46, 56–59. doi:10.1016/j.elecom.2014.06.008
Rudola, A., Azmansah, S. A. B., and Balaya, P. (2018). Communication-Mg(TFSI)2-Based Hybrid Magnesium-Sodium Electrolyte: Case Study with NaTi2(PO4)3//Mg Cell. J. Electrochem. Soc. 165, A1092–A1094. doi:10.1149/2.1091805jes
Rudola, A., Coowar, F., Heap, R., and Barker, J. (2021). “The Design, Performance and Commercialization of Faradion's Non‐aqueous Na‐ion Battery Technology,” in Na‐ion Batteries. Editors L. Monconduit, and L. Croguennec, 313–344. doi:10.1002/9781119818069.ch8
Rudola, A., Du, K., and Balaya, P. (2017). Monoclinic Sodium Iron Hexacyanoferrate Cathode and Non-flammable Glyme-Based Electrolyte for Inexpensive Sodium-Ion Batteries. J. Electrochem. Soc. 164, A1098–A1109. doi:10.1149/2.0701706jes
Rudola, A., Rennie, A. J. R., Heap, R., Meysami, S. S., Lowbridge, A., Mazzali, F., et al. (2021a). Commercialisation of High Energy Density Sodium-Ion Batteries: Faradion's Journey and Outlook. J. Mater. Chem. A. 9, 8279–8302. doi:10.1039/d1ta00376c
Rudola, A., Wright, C. J., and Barker, J. (2021b). Communication-Surprisingly High Fast Charge Volumetric Capacities of Hard Carbon Electrodes in Sodium-Ion Batteries. J. Electrochem. Soc. 168, 110534. doi:10.1149/1945-7111/ac377a
Rudola, A., Wright, C. J., and Barker, J. (2021c). Reviewing the Safe Shipping of Lithium-Ion and Sodium-Ion Cells: A Materials Chemistry Perspective. Energ. Mater. Adv. 2021, 9798460. doi:10.34133/2021/9798460
Saravanan, K., Mason, C. W., Rudola, A., Wong, K. H., and Balaya, P. (2013). The First Report on Excellent Cycling Stability and Superior Rate Capability of Na3V2(PO4)3for Sodium Ion Batteries. Adv. Energ. Mater. 3, 444–450. doi:10.1002/aenm.201200803
Sayers, R., Barker, J., and Heap, R. (2020). Compositions Containing Doped Nickelate Compounds. US Patent, 10550007.
Sehil, K., Darwish, M., Marouchos, C. C., and Jeans, W. C. (2020). “Comparative Analysis of High Voltage Battery Pack Cells for Electric Vehicle,” in 2020 55th International Universities Power Engineering Conference, Turin, Italy (UPEC), 1–6. https://ieeexplore.ieee.org/document/9209870
Sonnen GmbH (2019). Technical Data sonnenBatterie Hybrid 9.53. Available online: https://sonnenbatterie.co.uk/ (Accessed January 7, 2022).
Subasinghe, L. U., Satyanarayana Reddy, G., Rudola, A., and Balaya, P. (2020). Analysis of Heat Generation and Impedance Characteristics of Prussian Blue Analogue Cathode-Based 18650-type Sodium-Ion Cells. J. Electrochem. Soc. 167, 110504. doi:10.1149/1945-7111/ab9ee9
Tapia-Ruiz, N., Armstrong, A. R., Alptekin, H., Amores, M. A., Au, H., Barker, J., et al. (2021). 2021 Roadmap for Sodium-Ion Batteries. J. Phys. Energ. 3, 031503. doi:10.1088/2515-7655/ac01ef
Tripathi, A., Rudola, A., Gajjela, S. R., Xi, S., and Balaya, P. (2019). Developing an O3 Type Layered Oxide Cathode and its Application in 18650 Commercial Type Na-Ion Batteries. J. Mater. Chem. A. 7, 25944–25960. doi:10.1039/c9ta08991h
Vynakov, O., Savolova, E., and Skrynnyk, A. (2016). Modern Electric Cars of Tesla Motors Company. Odessa, 9–18. https://oaji.net/articles/2017/1004-1484517992.pdf, https://journals.onaft.edu.ua/index.php/atbp/article/view/162.
Wiesener, K., Ohms, D., Benczúr-Ürmössy, G., Berthold, M., and Haschka, F. (1999). High Power Metal Hydride Bipolar Battery. J. Power Sourc. 84, 248–258. doi:10.1016/s0378-7753(99)00325-0
Xu, X. M., and He, R. (2014). Review on the Heat Dissipation Performance of Battery Pack with Different Structures and Operation Conditions. Renew. Sustain. Energ. Rev. 29, 301–315. doi:10.1016/j.rser.2013.08.057
ZVEI - German Electrical and Electronic Manufacturers’Association (2013). Frankfurt Am Main, Germany: ZVEI - German Electrical and Electronic Manufacturers’ Association Voltage Classes for Electric Mobility. Available at: https://www.zvei.org/fileadmin/user_upload/Presse_und_Medien/Publikationen/2014/april/Voltage_Classes_for_Electric_Mobility/Voltage_Classes_for_Electric_Mobility.pdf (accessed November 22, 2021).
Keywords: bipolar battery, sodium-ion battery, bipolar Na-ion battery, high voltage batteries, bipolar electrodes, beyond 5 V battery, mixed-chemistry batteries
Citation: Rudola A, Wright CJ and Barker J (2022) Explorations Into the Viability of High Voltage Bipolar Na-Ion Cells Using Liquid Electrolytes. Front. Energy Res. 10:852630. doi: 10.3389/fenrg.2022.852630
Received: 11 January 2022; Accepted: 03 March 2022;
Published: 11 April 2022.
Edited by:
Ivana Hasa, University of Warwick, United KingdomReviewed by:
Giuseppe Antonio Elia, Politecnico di Torino, ItalyShinichi Komaba, Tokyo University of Science, Japan
Copyright © 2022 Rudola, Wright and Barker. This is an open-access article distributed under the terms of the Creative Commons Attribution License (CC BY). The use, distribution or reproduction in other forums is permitted, provided the original author(s) and the copyright owner(s) are credited and that the original publication in this journal is cited, in accordance with accepted academic practice. No use, distribution or reproduction is permitted which does not comply with these terms.
*Correspondence: Ashish Rudola, YXNoaXNoLnJ1ZG9sYUBmYXJhZGlvbi5jby51aw==; Jerry Barker, amVycnkuYmFya2VyQGZhcmFkaW9uLmNvLnVr