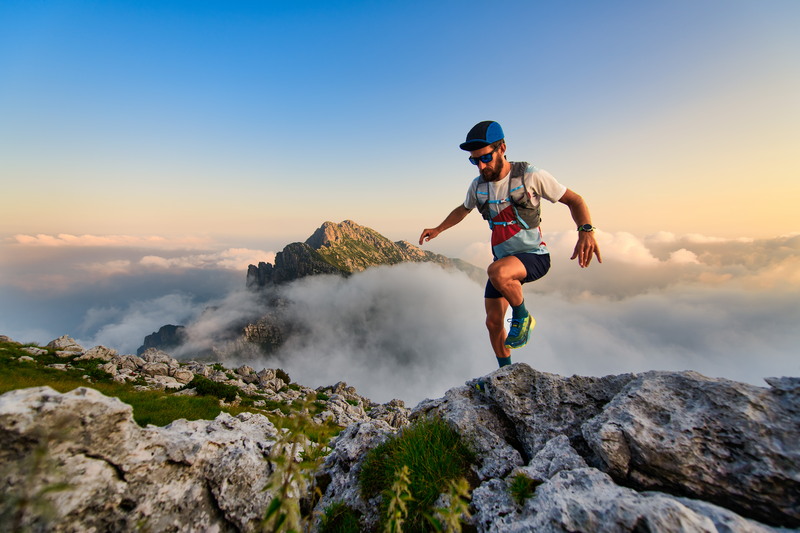
95% of researchers rate our articles as excellent or good
Learn more about the work of our research integrity team to safeguard the quality of each article we publish.
Find out more
ORIGINAL RESEARCH article
Front. Energy Res. , 15 February 2022
Sec. Process and Energy Systems Engineering
Volume 10 - 2022 | https://doi.org/10.3389/fenrg.2022.845303
This article is part of the Research Topic Advances in Microwave Energy Transmission, Conversion and Applications View all 7 articles
Most of the manganese resources in China have existed in the form of low-grade pyrolusite which is not utilized efficiently because of the high energy consumption and environmental pollution during the reduction process. Applying microwave heating to minerals reduction endows improved production efficiency and reduced production costs. In the present work, rapid preparation of manganese monoxide (MnO) was attempted through reducing low-grade pyrolusite with coal reducing agent by microwave heating, with the samples characterized by XRD, scanning electron microscopy, XPS as well as TG/DSC. The influences of the reduction reaction parameters on the reduction process of Mn in pyrolusite were comprehensively studied. The results indicated that higher temperatures and longer holding times facilitated the reduction roasting of pyrolusite, and manganese monoxide can be fabricated with a reduction ratio of 97.7% obtained at 650°C for 50 min. The mechanism of the gradual transformation of MnO2 to MnO from the macroscopic to the molecular level was also revealed in the order of MnO2 → Mn2O3 → Mn3O4 → MnO. Compared to traditional roasting, the proposed microwave-enhanced roasting process benefits from the superior kinetic conditions provided by the synergy between microwave enhancement and compact pellets, and thus reduced the roasting temperature and roasting time.
Manganese resource as a significant strategic mineral has wide industrial applications in the manufacture of iron and steel, battery, coatings, aluminum alloy, catalyst, aerospace, etc. (Yu, 1979; Pagnanelli et al., 2004; Li, 2008; Mei et al., 2011; Nayl et al., 2011). China is a major consumer of manganese resources. However, the high-grade manganese ore in China accounts for only 5% of the total available resources. A large number of low-grade pyrolusite in China is waiting to be utilized and processed efficiently (Tian et al., 2010; Zhang et al., 2013; Li et al., 2015). Meanwhile, the sustainable production of manganese products is seriously restricted by large consumption. Additionally, the high energy consumption and environmental pollution render the comprehensive utilization of pyrolusite with a grade of 20–35% using the conventional heating process is unsucessful (Su et al., 2010; Feng et al., 2013; Yang et al., 2013). Thus, the development of an environmental-friendly alternative technology for pretreatment of low-grade pyrolusite is in urgent demand.
Over the past several decades, using microwave energy as a heat method in metallurgical applications and processes has become increasingly more frequent (Li et al., 2019a; Zhang et al., 2019; Kang et al., 2020; Lin et al., 2020). Microwave heating has the unique advantages of selective heating, enhanced kinetics, rapid extraction, energy saving, environmental protection, and pollution-free (Hua et al., 1998; Omran et al., 2017; Li et al., 2019b; Zhang et al., 2019; Omran et al., 2020). Under sufficient intensity of microwave energy density, the in-situ energy conversion method enables rapid accumulation of energy in the material micro-areas and makes it preferentially heat the valuable minerals rather than the gangue in the ore by utilizing the difference of electromagnetic properties for minerals and gangue (Chen et al., 2012; Li et al., 2017a; Li et al., 2019b). Moreover, microwave energy is a green and environmental-friendly heating method with the characteristics of pollution-free, high energy utilization, easy to control (Chen et al., 2015; Omran et al., 2019; Chen et al., 2020). The advantages of microwave heating can be utilized to improve manganese manufacturing efficiency and achieve the purpose of saving energy and reducing production costs.
Recently, some efforts have been made on studied laboratory experiments about the conventional and microwave carbothermal reduction of low-grade pyrolusite; such information is urgently required if microwaves are to be used as an energy source for industrial application systems. Ye et al. (Li et al., 2020) have investigated the application of microwave heating on the reaction kinetics and solid surface topography of carbothermal reduction of pyrolusite ore achieved a maximum reduction ratio of low-grade pyrolusite of 97.2% at 800°C for 40 min without Fe2+ produced. At the same time, the reduction temperature was still too high. Although microwave heating has apparent advantages, it is difficult to apply in industrial production, especially in the pyrometallurgical process (Chen et al., 2007; Luo and Liang, 2012). Most microwave carbothermal reduction studies focused on the pure mineral phases. A few studies have been reported on the microwave reduction of complex low-grade minerals, especially low-grade pyrolusite (Fan et al., 2013; Ye et al., 2018a; Xiong et al., 2018). Hua et al. (1998) studied the influence of the application of microwave energy on the decomposition of MnO2, and results indicated that MnO2 was decomposed through two steps: MnO2 →Mn2O3 →Mn3O4, wherein the energy transfer through the product layer was controlling the 1st step, and the chemical kinetics controlled the 2nd step; and also highlighted applying microwave heating to replace conventional heating rendered the significantly enhanced decomposition rate and the reduced energy consumption.
In this work, microwave-assisted reduction of complex low-grade pyrolusite was analyzed, using X-ray photoelectron spectroscopy (XRF), also known as clarification of the chemical analysis on the surface of the sample, X-ray diffraction (XRD), as known as identification of compounds with differing crystalline structures, even though they have the same chemical composition, scanning electron microscopy (SEM), can be used to provide information about size and morphology of the sample, all with extremely high spatial resolution, and obtain a qualitative and quantitative elemental analysis, thermogravimetry (TG) and differential scanning calorimetry (DSC), as well known as understanding the thermal behavior of materials that are exposed to temperature increase. A typical mechanism of microwave-assisted reduction of pyrolusite was also analytically deduced. This research can provide a theoretical basis for promoting the industrialization of microwave pre-treatment of low-grade minerals.
In the present study, the as-received pyrolusite samples were received from Guangxi province, P.R. China, and the reduction agent was coal. The main manganese oxides in the pyrolusite ore mainly consisted of manganese oxides, including 42.2% of MnO2, 3.1% of Mn2O3, and 1.2% of MnO, and other components such as SiO2, Fe2O3, Al2O3, and MgO. The coal contained 78.72% of C, 8.93% of volatiles, and 11.67% of ash. The median particle diameters (D50) of low-grade pyrolusite and coal powders were 23.416 and 22.760 µm, respectively. The XRD pattern and microstructure of the pyrolusite were presented in Figure 1. The result reveals that the dominant mineral phases in pyrolusite were SiO2, MnO2, (Fe, Mn)2SiO4, which were agreed with the titrimetric analysis results. SEM image indicated that the surface structures of low-grade pyrolusite had a tighter and smoother surface morphology; therefore, it can be predicted that the reduction behavior of the as-received pyrolusite would be difficult to process with the bad kinetics condition (Salem and Jamshidi, 2012; Chubukov et al., 2016; Gunnewiek and Kiminami, 2017).
The crystalline phases of the as-received pyrolusite sample and the products were investigated by XRD (D/Max 2,200, Rigaku, Japan). The XRD patterns were recorded at the voltage of 20–40 kA, anode current of 15 mA–25 mA, 2θ from 5° to 100°, and a scanning rate of 0.25°/min. The morphological characteristics of the as-received samples were examined using SEM (Nova Nano SEM 450, FEI, United States). The Thermo gravimetric-Differential scanning calorimetry (TG/DSC) analysis for the pyrolusite-coal mixture was studied using a thermal gravimetric analyzer (STA 409, NETZSCH, Germany) with a heating rate of 5°C/min in an argon-protected environment. The particle size distributions and the volume average of the particle diameter of the as-received pyrolusite and coal powder were determined by a Laser Particle Sizer commercially available from Chengdu Jingxin Powder Analyse Instrument Co., Ltd., China (JL-1177). The surface elemental compositions of the samples were examined by XPS (Kratos Axis Ultra DLD, Thermo Fisher Scientific) using a monochromatic Al Kα X-ray (1,486.6 eV) source, operated at 6 mA and 12 kV, with the survey scans performed at a step size of 0.1 eV.
A microwave heating reactor was used in the reduction experiment. The microwave reactor consisted mainly of a computer control system, microwave reactor, vacuum pump, motor, rotation, flowmeter, gas generator, barometer, infrared thermocouple, and insulating brick, with a power ranging from 0 to 3 kW and a frequency of 2.45 GHz. The temperature was measured using an infrared thermocouple, with infrared radiation passed through the insulating brick and down to the sample’s surface. A vacuum pump extracted the off-gas vapours from the microwave heating experiments. The mass change of the samples during experiments was tracked by the weight measurement system connected to the sample.
The experimental flow-process diagram for the microwave assistant reduction process was exhibited in Figure 2. The as-received pyrolusite was homogenously mixed with coal powder at a mass ratio of 1.2, with 20.0 g of pyrolusite and 2.4 g of coal powder. This ratio can ensure the complete reduction of Mn4+ and Mn3+ to Mn2+. Then, 1.5 ml of distilled water and 0.4 g of methylcellulose were added to the pyrolusite-coal mixture as the organic binder. Afterward, the mixture was pressed into spheroidal pellets using pellets makers. The pellet diameter of the pellets was approximately 30 mm, weighing around 23 g. The pellet was prepared to make the reduction effect of coal powder more efficient, mainly rendering the gas can have better contact with low-grade pyrolusite and react with it, produced by the thermal decomposition behavior of coal powder, mainly carbon monoxide (CO). Before the reduction experiments, the pellets were dried at 110°C for 12 h.
The reactor was evacuated and then filled with nitrogen lasting for 10 min to provide an inert atmosphere before the test. The carbothermal reduction experiments were conducted at various temperatures regimes. After the experiments, the sample was transferred to an airtight container for cooling at room temperature. After grinding the residue, the manganese monoxide powder was prepared.
The reduction ratio of pyrolusite ore is calculated as the following information,
where
The reduction behavior of pyrolusite-coal mixture was studied by the TG-DTG-DSC techniques (25–1,000°C), with a heating rate of 5°C/min under an argon atmosphere (Ar), and the results were shown in Figure 3.
The TG-DTG-DSC curves showed three distinct mass loss regimes, which were attributed to different reaction behavior during three stages of the reduction process of the pyrolusite-coal mixture. The 1st stage corresponds to the temperatures below 368°C, wherein the mass decreased by 2.89%, which could be ascribed to the evaporation and release of water and volatiles in the pyrolusite-coal mixture. The 2nd stage corresponded to the temperature range of 368–716°C, associated with mass decreased by 6.14%. This weight loss was attributed to the reduction reactions of 2MnO2+C=Mn2O3+CO (g) and 3Mn2O3+C = 2Mn3O4+CO (g). Both of the mentioned two stages are associated with endothermic reactions. During the 3rd stage (716–1000°C), the mass decreased by 6.98%, attributed to the reduction reaction of Mn3O4+C = 3MnO + CO (g). The third stage reaction was exothermic.
The morphology and crystal structure of the microwave-treated samples were investigated by XRD analysis and SEM analysis, and the results are shown in Figure 4, respectively. Figures 4A,B displayed the XRD patterns and SEM images for the pyrolusite treated at 450°C for 10 min, Figures 4C,D showed the XRD and SEM patterns for the pyrolusite treated at 650°C for 50 min.
FIGURE 4. XRD and SEM patterns of the microwave treated pyrolusite, (A) XRD for the pyrolusite treated at 450°C for 10 min; (B) SEM, 700,00×; (C) XRD for the pyrolusite treated at 650°C for 50 min; (D) SEM, 700,00×.
Compared the pyrolusite treated at 450°C for 10 min with raw pyrolusite, combined with Figures 1, 4, it can be concluded that after microwave heating, the fine and smooth surface morphology of the raw material was replaced by an irregular surface with numerous pits, holes, and cracks, as shown in Figure 4B, which was because of the characteristics of unique selective heating and enhanced reaction kinetics under microwave heating. With the significant difference in dielectric properties of mineral components, large thermal stresses would occur between different mineral phases, resulting in cracks and irregular pits (Ye et al., 2018b; Ye et al., 2018c; Li et al., 2019c). The MnO2 phase endows excellent microwave absorbing properties and discharge between particles; therefore, the heating efficiency of the MnO2 phase was higher than components that have weak microwave-absorbing properties, which even exceeded the set temperature by more than slight dozen degrees Celsius. Consequently, melted granules were observed in Figure 4A. The XRD pattern supported these findings. A comparison with the observations in Figure 1 indicated that new phases were detected in the microwave-treated sample, which was due to the transformation behavior of MnO2 into MnO (JCPDS: 07-0230) and Mn3O4 (JCPDS: 18-0803). Moreover, the strongest preferential orientation of (111), (200), and (220) plane of the peak intensity of MnO phase was appeared at 2θ values of 34.910°, 40.547°, and 58.722°, respectively. However, the peaks of MnO and Mn3O4 were weak, caused by the transformation process that occurred at a relatively low temperature and without prolonged heat treatment.
The XRD pattern of the sample after further microwave treatment was shown in Figure 4C, and the corresponding SEM patterns are shown in Figure 4D, treated at 650°C for 50 min. From Figure 4D, the molten granules grew further and became interconnected and stacked. Because of the loss of oxygen during pyrolusite reduction and the release of gas from the pyrolusite-coal mixture, the whole surface of the pyrolusite sample became loose and porous (Ren et al., 2015; Li et al., 2017b). The peaks in the XRD pattern were smooth, indicating the improvement in the crystalline structure of the MnO phase. With the increasing heating time and reduction temperature, the intensity of the MnO peaks increased significantly. Meanwhile, the MnO2 peaks disappeared, resulting from the complete reduction of MnO2. Moreover, attributed to the decomposition behavior of (Mn, Fe)2SiO4 phase, traces of Mn2SiO4 and Fe3O4 phases were detected.
The chemical composition and surface electronic state of the as-received sample and the microwave-treated samples were presented in Figure 5. In Figure 5A, A, B, and C were the Mn spectra of the as-received sample, the sample treated by microwave irradiation at 450°C for 10 min, and the sample heated by microwave energy at 650°C for 50 min, respectively. The binding energies (BEs) of Mn 2p1/2 and Mn 2p3/2 were 653.68 and 641.88 eV, respectively. The characteristic satellite peak of Mn2+ appeared, hence, the presence of MnO in the microwave-treated samples can be confirmed. The characteristic satellite peak became obvious with the increase of duration time and reduction temperature, implying that more Mn2+ was produced.
FIGURE 5. XPS spectra of low-grade pyrolusite before and after microwave heating (A) and the best fit of Mn2p in raw pyrolusite (B); the best fit of Mn2p in microwave treated pyrolusite at 450°C for 10 min (C); the best fit of Mn2p in microwave treated pyrolusite at 650°C for 50 min (D).
Figures 5B–D presented the XPS spectra of MnOx, where the three Mn species, Mn2+, Mn3+, and Mn4+ coexisted during the microwave-enhanced carbothermal reduction process. The Mn 2p spectra were deconvolved into the three components at BEs of 640.34, 641.31, and 642.82 eV, assigned to Mn2+, Mn3+, and Mn4+, respectively. The species of the surface elements of the raw material and the microwave-treated samples were calculated by a quantitative analysis method and were summarised in Table 1. The bulk of the Mn species in the raw material was Mn4+. By contrast, after microwave treatment, the Mn species were mainly Mn2+. Therefore, it can be concluded that Mn4+ was mostly reduced to Mn2+ by microwave heating at 650°C for 50 min.
According to chemical titration analysis, the reduction ratio was 33% at 450°C for 10 min, which the low reduction ratio was ascribed to the terrible thermodynamic conditions caused by the low reduction temperature. However, a much higher reduction ratio reached 97.7%, achieved at 650°C within a heating time of 50 min. This result was higher than that from the fitted XPS spectra. The XPS analysis of the sample surface indicated that despite the antioxidant treatment, a small portion of MnO was oxidized to high-valence MnOx, wherein MnO is easily oxidized at high temperatures.
Moreover, referred to the previous work studied by Ye et al. (Li et al., 2020), effects of heating technologies (conventional or microwave) on manganese reduction ratio for carbothermal reduced low-grade pyrolusite were comparatively investigated, and the experimental results of conventional heating on manganese reduction ratio were provided in Table 2. A reduction ratio of 97.7% was achieved at 650°C for 50 min with a more/mcoal of 10:1.2 by microwave heating, while a reduction ratio reached 95.81 at 900°C for 30 min with a more/mcoal of 10:1.0 by conventional heating. Therefore, it can be summarised that replacing conventional heating with microwave heating to process low-grade pyrolusite renders excellent advantages, including a decrease in reduction temperature required and an increase in reduction efficiency, even with environmental-friendly, low energy consumption and high working efficiency.
A concise diagram of the mechanism of microwave carbothermal reduction of pyrolusite from the macroscopic to the molecular level was presented in Figure 6. Compared to the original material with the smooth and fine surface, SEM images of samples before and after microwave treatment showed that the specimen became rough and porous (Figure 5). The advantages of microwave heating characteristics are rapid and selective heating. Based on the distinguished microwave-absorbing properties of MnO2 phase, the MnO2 phase was heated to a higher temperature, while gangue components such as SiO2 were difficult to heat, forming a large temperature gradient and causing thermal stress at the interface, further to open the inclusions and produce structural cracks (Li et al., 2019c; He et al., 2019). Therefore, the temperature gradient increased the specific surface area of the particles, meanwhile providing kinetic conditions suitable for gaseous diffusion and accelerating the reduction reaction.
The mechanism of pyrolusite reduction by microwave heating can be summarised as follows: when the temperature rose to the reaction temperature, pyrolusite (MnO2) and coal (C) underwent direct solid-phase reduction, with MnOx and CO produced. The reductive CO reacted with nearby MnO2 or MnOx to generate CO2. The generated CO2 reached the external environment through the porous product layers and gas film in turn. After diffusion in the external environment, the CO2 reached the carbon surface, and CO began to form by the boudouard reaction of carbon (gasification of carbon). Followed by the CO arrived at the chemical reaction interface through the gas film layer and porous product layer in turn. Then CO and MnOx underwent the indirect reduction reaction to form CO2, which the cycle continued until the completion of the reaction (Li et al., 2021).
Results from the experiment data, manganese monoxide can be obtained from low-grade pyrolusite by using microwave-enhanced carbothermal reduction roasting. The influences of the reduction reaction parameters on the reduction process of Mn in pyrolusite were comprehensively studied, and the following sequence can summarise the reduction transformation: MnO2 → Mn2O3 → Mn3O4 → MnO. Higher temperatures and longer holding times facilitated the reduction roasting of pyrolusite. Roasted the sample at 650°C for 50 min, a reduction ratio of 97.7% was obtained, and the iron oxides were mostly converted to Fe3O4. The mechanism of microwave carbothermal reduction of pyrolusite from the macroscopic to the molecular level was presented, and the mechanism of gradual conversion of MnO2 to MnO was also revealed. Compared to traditional roasting, the proposed microwave-enhanced roasting process can be applied to reduce the roasting temperature and roasting time, which can be attributed to superior kinetic conditions provided by synergy between microwave enhancement and compact pellets.
The original contributions presented in the study are included in the article/Supplementary Material, further inquiries can be directed to the corresponding authors.
JC: Conceptualization, Investigation, Writing-original draft. FH: Conceptualization, Investigation, Writing-original draft. LG: Writing-review and editing. SG: Supervision, Project administration, Writing-review and editing. MO: Conceptualization, Writing review and editing. GC: Writing-review and editing.
The authors declare that the research was conducted in the absence of any commercial or financial relationships that could be construed as a potential conflict of interest.
All claims expressed in this article are solely those of the authors and do not necessarily represent those of their affiliated organizations, or those of the publisher, the editors, and the reviewers. Any product that may be evaluated in this article, or claim that may be made by its manufacturer, is not guaranteed or endorsed by the publisher.
The authors would like to acknowledge the National Natural Science Foundation of China (Grant Nos. U1802255), the Hunan Provincial Science and Technology Plan Project, China (No. 2016TP1007), and the Innovative Research Team (in Science and Technology) at the University of Yunnan province for the financial support.
Chen, J., Pan, X., Zhang, M., Zhao, J., and Lin, Y. (2007). Heating Characteristics of Manganese Oxide Ore Fines Containing Coal under Microwave Irradiation. Mat. Rev. A2, 81–84.
Chen, G., Chen, J., Li, J., Guo, S., Srinivasakannan, C., and Peng, J. (2012). Optimization of Combined Microwave Pretreatment-Magnetic Separation Parameters of Ilmenite Using Response Surface Methodology. Powder Technol. 232, 58–63. doi:10.1016/j.powtec.2012.08.009
Chen, G., Chen, J., and Peng, J. (2015). Effects of Mechanical Activation on Structural and Microwave Absorbing Characteristics of High Titanium Slag. Powder Technol. 286, 218–222. doi:10.1016/j.powtec.2015.08.021
Chen, G., Li, K., Jiang, Q., Li, X., Peng, J., Omran, M., et al. (2020). Microstructure and Enhanced Volume Density Properties of FeMn78C8.0 alloy Prepared via a Cleaner Microwave Sintering Approach. J. Clean. Prod. 262, 121364. doi:10.1016/j.jclepro.2020.121364
Chubukov, B. A., Palumbo, A. W., Rowe, S. C., Hischier, I., Groehn, A. J., and Weimer, A. W. (2016). Pressure Dependent Kinetics of Magnesium Oxide Carbothermal Reduction. Thermochim. Acta 636, 23–32. doi:10.1016/j.tca.2016.03.035
Fan, L., Chen, J., Guo, J., Jiang, X., and Jiang, W. (2013). Influence of Manganese, Iron and Pyrolusite Blending on the Physiochemical Properties and Desulfurization Activities of Activated Carbons from walnut Shell. J. Anal. Appl. Pyrolysis 104, 353–360. doi:10.1016/j.jaap.2013.06.014
Feng, Y., Cai, Z., Li, H., Du, Z., and Liu, X. (2013). Response Surface Optimization of Fluidized Roasting Reduction of Low-Grade Pyrolusite Coupling with Pretreatment of Stone Coal. J. Min Metall. B Metall. 49, 33–41. doi:10.2298/jmmb120525040f
Gunnewiek, R. F. K., and Kiminami, R. H. G. A. (2017). Fast Synthesis of Porous Chromium Carbide by Microwave-Assisted Carbothermal Reduction. Ceramics Int. 43, 10614–10618. doi:10.1016/j.ceramint.2017.05.062
He, F., Chen, J., Chen, G., Peng, J., Srinivasakannan, C., and Ruan, R. (2019). Microwave Dielectric Properties and Reduction Behavior of Low-Grade Pyrolusite. JOM 71, 3909–3914. doi:10.1007/s11837-019-03522-8
Hua, Y., Liu, C., and Li, L. (1998). Microwave-Assisted Decomposition Kinetics of MnO2. Chin. J. Nonferrous. 3, 497–501.
Kang, J., Gao, L., Zhang, M., Pu, J., He, L., Ruan, R., et al. (2020). Synthesis of Rutile TiO2 Powder by Microwave-Enhanced Roasting Followed by Hydrochloric Acid Leaching. Adv. Powder Technol. 31 (3), 1140–1147. doi:10.1016/j.apt.2019.12.042
Li, B., Feng, Y., and Li, H. (2015). Gas-Solid Fludized Two-Stage Roasting of Pyrolusite for Preparation of Potassium Manganite. J. Cent. South. U. Sci. T. 46 (2), 379–385. doi:10.11817/j.issn.1672-7207.2015.02.001
Li, Y., Chen, G., Peng, J., Srinivasakannan, C., and Ruan, R. (2017). Study of the Oxygen Reduction of Low Valent Titanium in High Titanium Slag by Microwave Rapid Heating. Powder Technol. 315, 318–321. doi:10.1016/j.powtec.2017.04.027
Li, B., Cheng, Y., Dong, L., Wang, Y., Chen, J., Huang, C., et al. (2017). Nitrogen Doped and Hierarchically Porous Carbons Derived from Chitosan Hydrogel via Rapid Microwave Carbonization for High-Performance Supercapacitors. Carbon 122, 592–603. doi:10.1016/j.carbon.2017.07.009
Li, K., Chen, J., Peng, J., Ruan, R., Omran, M., and Chen, G. (2019). Dielectric Properties and thermal Behavior of Electrolytic Manganese Anode Mud in Microwave Field. J. Hazard. Mater. 384, 121227. doi:10.1016/j.jhazmat.2019.121227
Li, K., Chen, J., Chen, G., Peng, J., Ruan, R., and Srinivasakannan, C. (2019). Microwave Dielectric Properties and Thermochemical Characteristics of the Mixtures of Walnut Shell and Manganese Ore. Bioresour. Technol. 286, 121381. doi:10.1016/j.biortech.2019.121381
Li, K., Chen, G., Li, X., Peng, J., Ruan, R., Omran, M., et al. (2019). High-Temperature Dielectric Properties and Pyrolysis Reduction Characteristics of Different Biomass-Pyrolusite Mixtures in Microwave Field. Bioresour. Technol. 294, 122217. doi:10.1016/j.biortech.2019.122217
Li, K., Chen, J., Peng, J., Ruan, R., Srinivasakannan, C., and Chen, G. (2020). Pilot-Scale Study on Enhanced Carbothermal Reduction of Low-Grade Pyrolusite Using Microwave Heating. Powder Technol. 360, 846–854. doi:10.1016/j.powtec.2019.11.015
Li, K., Jiang, Q., Chen, G., Gao, L., Peng, J., Chen, Q., et al. (2021). Kinetics Characteristics and Microwave Reduction Behavior of walnut Shell-Pyrolusite Blends. Bioresour. Technol. 319, 124172. doi:10.1016/j.biortech.2020.124172
Li, T. (2008). Technology of Low Grade Pyrolusite Ore Reduction Process and Recent Advances. Chinas. Man. Ind. 26, 4–14.
Lin, S., Gao, L., Yang, Y., Chen, J., Guo, S., Omran, M., et al. (2020). Dielectric Properties and High Temperature Thermochemical Properties of the Pyrolusite-Pyrite Mixture during Reduction Roasting. J. Mater. Res. Technol. 9 (6), 13128–13136. doi:10.1016/j.jmrt.2020.09.056
Luo, S., and Liang, Y. (2012). Research on Microwave Heating Process of Deoxygenafe Restoring Pyrolusite. Popular. Sci. Technolo. 1, 62–64.
Mei, G., Zhang, W., and Zeng, X. (2011). Technology of China Manganese Industry. Changsha: Technol. China. Man, 13–19.
Nayl, A. A., Ismail, I. M., and Aly, H. F. (2011). Recovery of Pure MnSO4∙H2O by Reductive Leaching of Manganese from Pyrolusite Ore by Sulfuric Acid and Hydrogen Peroxide. Int. J. Mineral Process. 100, 116–123. doi:10.1016/j.minpro.2011.05.003
Omran, M., Fabritius, T., Heikkinen, E.-P., and Chen, G. (2017). Dielectric Properties and Carbothermic Reduction of Zinc Oxide and Zinc Ferrite by Microwave Heating. R. Soc. Open Sci. 4, 170710. doi:10.1098/rsos.170710
Omran, M., Fabritius, T., and Heikkinen, E.-P. (2019). Selective Zinc Removal from Electric Arc Furnace (EAF) Dust by Using Microwave Heating. J. Sustain. Metall. 5, 331–340. doi:10.1007/s40831-019-00222-0
Omran, M., Fabritius, T., Heikkinen, E.-P., Vuolio, T., Yu, Y., Chen, G., et al. (2020). Microwave Catalyzed Carbothermic Reduction of Zinc Oxide and Zinc Ferrite: Effect of Microwave Energy on the Reaction Activation Energy. RSC Adv. 10, 23959–23968. doi:10.1039/d0ra04574h
Pagnanelli, F., Garavini, M., Vegliò, F., and Toro, L. (2004). Preliminary Screening of Purification Processes of Liquor Leach Solutions Obtained from Reductive Leaching of Low-Grade Manganese Ores. Hydrometallurgy 71, 319–327. doi:10.1016/s0304-386x(02)00156-1
Ren, Y., Yang, L., Wang, L., Xu, T., Wu, G., and Wu, H. (2015). Facile Synthesis, Photoluminescence Properties and Microwave Absorption Enhancement of Porous and Hollow ZnO Spheres. Powder Technol. 281, 20–27. doi:10.1016/j.powtec.2015.04.076
Salem, A., and Jamshidi, S. (2012). Effect of Paste Humidity on Kinetics of Carbothermal Reduction of Extruded Barite and Coke Mixture. Solid State. Sci. 14, 1012–1017. doi:10.1016/j.solidstatesciences.2011.10.011
Su, H., Liu, H., Wang, F., Lü, X., and Wen, Y. (2010). Kinetics of Reductive Leaching of Low-Grade Pyrolusite with Molasses Alcohol Wastewater in H2SO4. Chin. J. Chem. Eng. 18, 730–735. doi:10.1016/s1004-9541(09)60121-x
Tian, X., Wen, X., Yang, C., Liang, Y., Pi, Z., and Wang, Y. (2010). Reductive Leaching of Manganese from Low-Grade Manganese Dioxide Ores Using Corncob as Reductant in Sulfuric Acid Solution. Hydrometallurgy 100, 157–160. doi:10.1016/j.hydromet.2009.11.008
Xiong, S., Li, X., Liu, P., Hao, S., Hao, F., Yin, Z., et al. (2018). Recovery of Manganese from Low-Grade Pyrolusite Ore by Reductively Acid Leaching Process Using Lignin as a Low Cost Reductant. Minerals Eng. 125, 126–132. doi:10.1016/j.mineng.2018.06.003
Yang, K.-D., Ye, X.-J., Su, J., Su, H.-F., Long, Y.-F., Lü, X.-Y., et al. (2013). Response Surface Optimization of Process Parameters for Reduction Roasting of Low-Grade Pyrolusite by Bagasse. Trans. Nonferrous Met. Soc. China 23, 548–555. doi:10.1016/s1003-6326(13)62498-x
Ye, Q., Zhu, H., Zhang, L., Liu, P., Chen, G., and Peng, J. (2014). Carbothermal Reduction of Low-Grade Pyrolusite by Microwave Heating. RSC Adv. 4, 58164–58170. doi:10.1039/c4ra08010f
Ye, Q., Chen, J., Chen, G., Peng, J., Srinivasakannan, C., and Ruan, R. (2018). Effect of Microwave Heating on the Microstructures and Kinetics of Carbothermal Reduction of Pyrolusite Ore. Adv. Powder Technol. 29, 1871–1878. doi:10.1016/j.apt.2018.04.025
Ye, X., Koppala, S., Qu, W., Xu, S., Zhang, L., Liu, B., et al. (2018). New Approach to the Utilization of Microwave thermal Energy: Desulfurization and Decarburization of Spent Catalyst via Microwave Treatment. Powder Technol. 338, 764–773. doi:10.1016/j.powtec.2018.07.085
Ye, X., Guo, S., Yang, L., Gao, J., Peng, J., Hu, T., et al. (2018). New Utilization Approach of Microwave thermal Energy: Preparation of Metallic Matrix diamond Tool Bit by Microwave Hot-Press Sintering. J. Alloys Compd. 748, 645–652. doi:10.1016/j.jallcom.2018.03.183
Zhang, H., Zhu, G., Yan, H., Zhao, Y., Li, T., and Feng, X. (2013). Reduction of Low-Grade Manganese Dioxide Ore Pellets by Biomass Wheat Stalk. Acta Metall. Sin. 26, 167–172. doi:10.1007/s40195-012-0250-x
Keywords: microwave assisted heating, low grade pyrolusite, manganese monoxide, reduction mechanism, pretreatment
Citation: Chen J, He F, Gao L, Guo S, Omran M and Chen G (2022) Rapid Preparation of Manganese Monoxide by Microwave-Enhanced Selective Carbothermal Reduction. Front. Energy Res. 10:845303. doi: 10.3389/fenrg.2022.845303
Received: 29 December 2021; Accepted: 25 January 2022;
Published: 15 February 2022.
Edited by:
Jing Sun, Shandong University, ChinaCopyright © 2022 Chen, He, Gao, Guo, Omran and Chen. This is an open-access article distributed under the terms of the Creative Commons Attribution License (CC BY). The use, distribution or reproduction in other forums is permitted, provided the original author(s) and the copyright owner(s) are credited and that the original publication in this journal is cited, in accordance with accepted academic practice. No use, distribution or reproduction is permitted which does not comply with these terms.
*Correspondence: Fei He, MTE1OTM0MTg3M0BxcS5jb20=; Mamdouh Omran, bWFtZG91aC5vbXJhbkBvdWx1LmZp; Guo Chen, Z3VvY2hlbkBrdXN0LmVkdS5jbg==
Disclaimer: All claims expressed in this article are solely those of the authors and do not necessarily represent those of their affiliated organizations, or those of the publisher, the editors and the reviewers. Any product that may be evaluated in this article or claim that may be made by its manufacturer is not guaranteed or endorsed by the publisher.
Research integrity at Frontiers
Learn more about the work of our research integrity team to safeguard the quality of each article we publish.