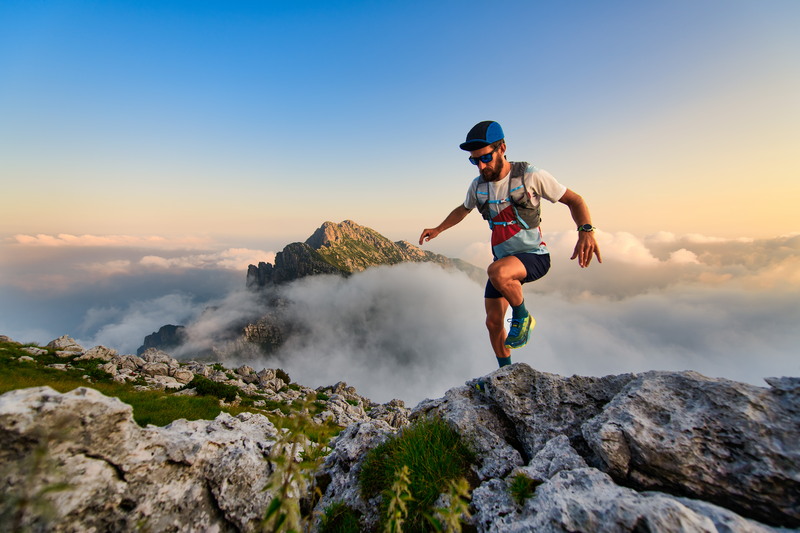
94% of researchers rate our articles as excellent or good
Learn more about the work of our research integrity team to safeguard the quality of each article we publish.
Find out more
ORIGINAL RESEARCH article
Front. Energy Res. , 18 February 2022
Sec. Bioenergy and Biofuels
Volume 10 - 2022 | https://doi.org/10.3389/fenrg.2022.837875
This article is part of the Research Topic High-performance Catalytic Processes for Biofuel Production View all 6 articles
In this work, Camellia oleifera Abel shell was used as a feedstock to prepare biochar by HNO3 impregnation and pyrolysis. The biochar was used for the catalytic pyrolysis of waste vegetable oil to prepare bio-oil. Experimental results showed that HNO3 solution treatment had an important effect on the groups and structure of the biochar catalyst. When the solid/liquid ratio of pretreatment was 1:3, the Brunauer–Emmett–Teller specific surface area of the 1:3–600°C biochar is 392.65 m2/g, which is approximately 677 times higher than that of untreated biochar. Moreover, the biochar catalyst had a remarkable catalytic performance. The selectivity of the monocyclic aromatic hydrocarbon in the bio-oil was up to 78.82%, and the oxy-compound could be completely removed at the catalytic temperature of 600°C. However, the increase of the catalyst-to-waste vegetable oil ratio and catalytic temperature decreased the bio-oil yield.
Fossil fuel depletion and the sustained growth of energy consumption result in the huge impact of the rise in energy prices on the global economy. In 2020, the combined consumption of oil, natural gas, and coal accounted for 83.10% of total primary energy consumption worldwide. Greenhouse effect aggravation and the improvement of people’s awareness of environmental problems have prompted people to begin searching for alternative energy sources, and the demand for energy has led to great prospects to utilize renewable resources and their biorefinery (Ouyang and Lin, 2014; Hsiao et al., 2020; Khodadadi et al., 2020; BP, 2021).
Waste oil can be divided into soapstock, acidified oil from refineries, nonedible woody oil, and waste catering oil (Wang et al., 2021). Edible oil is widely used in commercial activities, catering industry, and home cooking worldwide. More than 15 million tons of waste vegetable oil (WVO) are produced each year worldwide (Mahari et al., 2018; Fan et al., 2021). The disposal or incineration of WVO brings about environmental problems such as greenhouse gas emissions. Recycling and reuse of WVO can be converted into value-added products, reducing greenhouse gas emissions, and bringing about environmental, financial, and social benefits (Loizides et al., 2019). The main component of WVO is fatty acids, and its effective hydrogen-to-carbon ratio is approximately 1.50; thus, it belongs to materials with a high hydrogen-to-carbon ratio (Zhang et al., 2013). At present, WVO is mainly used to prepare biodiesel through transesterification technology. Biodiesel is one of the most recognized alternative fuels because of its potential as an ecological fuel; however, the high content of free fatty acids in WVO inhibits transesterification and reduces biodiesel yield (Hsiao et al., 2020). Therefore, effective use of WVO must be determined.
Last few years, researchers have focused on converting waste into hydrocarbon fuels through thermochemical pathways, such as pyrolysis. This endothermic decomposition process occurs in high-temperature environments and anoxic conditions to produce biochar, bio-oil, and syngas. Pyrolysis is mainly divided into four types, including flash pyrolysis, fast pyrolysis, medium pyrolysis, and slow pyrolysis. Fast pyrolysis, well known for having bio-oil as its main product, is considered the most feasible and economical way to produce bio-oil. The use of traditional heating methods for pyrolysis has not only low-heating efficiency, but also heat loss. Compared with traditional heating methods, microwave heating has the advantages of easy operation, uniform heating of materials, and rapid temperature rise, and the treatment time of microwave heating can usually be reduced to 1% of the time required to use in the electric heating method. Due to its fast heating speed, it may increase production speed, reduce power consumption, and reduce production costs (Hou et al., 2018; Putra et al., 2022). In addition, the aromatic hydrocarbons in the pyrolysis product produced by microwave-assisted catalytic pyrolysis of biomass are greater than those produced via traditional heating methods. Moreover, the coking rate of the catalyst decreases. Microwave-assisted pyrolysis is considered to be a promising technology for efficiently converting waste into clean energy (Mahari et al., 2018; Foong et al., 2020; Ryu et al., 2020; Li et al., 2021; Wang et al., 2021).
Carbon-neutral fuels can replace fossil fuels to produce chemicals, electricity, heat, and fuels. The bio-oil produced by pyrolysis contains more oxy-compounds than diesel and gasoline, and the high oxy-compound content leads to low calorific value, high viscosity, and unstable properties of bio-oil (Ryu et al., 2020; Gupta et al., 2021). Adding catalysts to the pyrolysis system can effectively improve the bio-oil quality; compared with catalysts such as metal oxides, inorganic salts, and zeolite, which are expensive or prone to deactivation, biochar as a catalyst provides added value by potentially reducing waste disposal cost (Feng et al., 2020; Qiu et al., 2020). Biochar exhibits high modification and good stability in acidic and alkaline media; however, untreated biochar has a limited surface area and porosity and relatively poor catalytic ability (Huang et al., 2020a; Shan et al., 2020). Therefore, using biochar after further treatment as a catalyst or catalyst carrier in the catalytic pyrolysis of waste oil has been studied, and its use for the catalytic reforming of bio-oil has presented good results (Lam et al., 2016; Duan et al., 2020).
Alkali metals and alkaline earth metals, functional groups and pore structure, abundant O-containing functional groups on the surface, and adsorption are the reasons why biochar is used as a bio-oil-reforming catalyst (Qiu et al., 2020). Compared with the modification of biochar, the pretreatment of raw materials before pyrolysis has the advantages of low cost, simple operation, and being suitable for large-scale production (Rizwan et al., 2020). Studies have shown that washing pretreatment is a promising pre-hydrolysis method, which is particularly effective for lignocellulosic biomass. It can destroy the structure of biomass before pyrolysis, remove part of inorganic matter, and improve the carbon content of biochar (Diao et al., 2021). Dilute acid pretreatment is a widely used chemical pretreatment method for biomass, and the commonly used acid solutions are H2SO4, HCl, HNO3, and so on. Studies have shown that acid solution pretreatment of biomass can change the form of biochar and increase biochar porosity (Nikkhah et al., 2020). As a cheap and easy-to-obtain raw material, agricultural and forestry waste has become the main raw material for preparing biochar. Camellia oleifera Abel shell (COAs) is a by-product of the processing of Camellia oleifera, and more than 3 million tons are produced every year (Zhang et al., 2018). Therefore, COAs is a kind of abundant biomass energy, and the valorization of nonfood residues could have a positive impact to some extent as long as the Camelia oleifera cultivation is sustainable. Biomass wastes with high lignin content and low water content are suitable as raw materials for preparing biochar. Compared with ryegrass, corn pericarp, miscanthus, rice husk, and millet husk, etc., the lignin content of COAs is higher, about 31.35–44.8%, and it is more suitable as a raw material for preparing biochar (Huang et al., 2020b; Li and Zhang, 2020).
However, studies on the application of biochar prepared after pretreatment of biomass in the catalytic pyrolysis of WVO are few. Therefore, in this study, the effects of the solid-to-liquid ratio of COAs pretreatment by HNO3, carbonization temperature of COAs, the ratio of the feedstock to catalyst, and catalytic temperature on the composition and yield of bio-oil from microwave-assisted fast pyrolysis of WVO have been investigated.
COAs was obtained from Jinshu Ecological Camellia Professional Cooperative, Shangyou County, Ganzhou City, Jiangxi Province. HNO3, of domestic analytical pure, was obtained from Xilong Scientific Co., Ltd. SiC spheres with a diameter of 5 mm were purchased from Xinli Wear-Resistant Materials Co., Ltd. The WVO from a fried shop was filtered and then stored in a 4-°C refrigerator with shading for further experiments. The WVO was 1.0 ml, and n-hexane 5 ml and NaOH–methanol solution (0.5M) 2.5 ml were added, and the solution was refluxed in a 70°C water bath for 10 min. Then, the solution was cooled to room temperature. Then, it was transferred to a graduated test tube, and deionized water was added to make it 20 ml for ultrasonic extraction for 10 min, and the supernatant was taken for GC–MS analysis after centrifugation. The predominant fatty acid composition of WVO is shown in Table 1.
The COAs was dried in a WF-22G drying oven (WIGGENS, United States, 2019) at 105°C for 24 h, then crushed using a small grinder, and screened through a 40-mesh sieve for use. The COAs powder and HNO3 (0.2 mol/L) solution were thoroughly mixed according to M/V (1:1, 1:2, and 1:3) and underwent impregnation for 12 h. Then, the impregnated COAs powder was washed with deionization water until neutral and dried in the drying oven at 105°C. After drying, the material was crushed using the grinder and stored through a 40-mesh sieve for standby. Then, it was calcined in a tubular furnace (OFT-1200X, Hefei Keijing material technology Co., Ltd., China, 2019) at different temperatures (800, 700, 600, and 500°C) for 0.5 h. The carbon was finally collected and stored for the next experiment. The catalyst was named X-T (X: pretreatment M/V; T: carbonization temperature).
The functional groups were analyzed by Fourier transform-infrared spectroscopy (FTIR) (Thermo Fisher Nicolet iS5, United States, 2007). The recording range of each sample was 400–4,000 cm−1, and the resolution was 4 cm−1. A total of 64 scans were performed. The morphology of biochar samples was determined by scanning electron microscopy (SEM) (JEOL JSM-6701F, Japan, 2012). Before the determination, the samples were precoated with gold. N2 adsorption/desorption isotherms were measured using a specific surface analyzer (Micromeritics ASAP2460, United States, 2018) to evaluate the structural characteristics of biochar. The pore volume and specific surface area were calculated using the t-plot method and Brunauer–Emmett–Teller (BET) theory, respectively.
As shown in Figure 1, the experimental device was a refitted MAS-Ⅱ microwave oven (SINEO Microwave Chemical Technology Co. Ltd., China, 2015). The microwave absorbent used was 5-mm-diameter SiC spheres (200 g). High-purity nitrogen was added to the system as a carrier gas and protective gas at a flow rate of 5 ml/min. Then, the microwave oven and electric heating belt began to work after nitrogen was introduced into the quartz reactor for 5 min. The catalytic bed temperature reached the set value. The entire heating program of the refitted MAS-Ⅱ microwave oven was set at 800 W for 5 min and then to 300 W until the end of the reaction process. The heating curve of the microwave absorbent bed and SiC temperature measurement method diagram are shown in Supplementary Figures S1, S2 (Supplementary material). After the refitted MAS-Ⅱ microwave oven was heated for 5 min, WVO (4 g) was added to the reactor. During the reaction, condensable gas was collected in two U-tubes placed in a mixture of ice and water for subsequent product analysis. According to the quality difference before and after the system, the bio-oil yield was calculated, and the yield of char was negligible. Therefore, the char yield is not discussed in this article.
FIGURE 1. Experimental device diagram: (1) nitrogen; (2) microwave oven; (3) quartz reaction bottle; (4) separation funnel; (5) electric heating belt; (6) catalytic bed; (7) U-tubes; (8) condenser; (9) gas-washing bottle; (10) alkaline solution; (11) water tank; and (12) ice water.
In this study, the effects of the carbonization temperature of COAs (800, 700, 600, and 500°C), the solid-to-liquid ratio (M/V) (untreated, 1:1, 1:2, and 1:3) in the pretreatment process, the ratio of the feedstock and catalyst (without catalyst, 8:1, 4:1, 2:1, and 1:1), and the catalytic temperature (600, 550, 500, 450, and 400°C) on the chemical composition and yield of bio-oil were studied.
Gas chromatography–mass spectrometry (7890B-7000D, Agilent Technologies, United States, 2017) was used to analyze the bio-oil obtained from the pyrolysis of WVO. The analytical conditions were consistent with the previous study (Wu et al., 2020). The GC–MS conditions are as follows: Column: HP-PONA (50 m × 0.200 mm × 0.50 μm); Carrier gas: helium; Vaporizer temperature: 280°C; Ion source temperature: 230°C; Injection mode: split (50:1); Target temperature: 180°C, Heating rate: 5°C/min, and Hold time: 2 min; Target temperature: 280°C, Heating rate: 8°C/min, and Hold time: 3 min.
The FTIR results of untreated COAs biochar and pretreated COAs biochar are shown in Figure 2. Untreated COAs biochar and pretreated COAs biochar show a similar peak shape. In particular, 790, 830, and 870 cm−1 are caused by aromatic C–H bending. C–H around 1,419 cm−1, C=C around 1,577 cm−1, and the C=O bond at 2,346 cm−1 may be caused by the presence of the aldehyde or ketone. The band strength at 3,446 cm−1 is related to the tensile vibration of the O–H group. The increase of the liquid-to-solid ratio results in a slight increase of the group peak, and its peak value decreases with the increase of carbonization temperature (Wang et al., 2020; Zhang et al., 2021). The group signal peak in biochar after HNO3 treatment is clearer than that in untreated biochar. However, C=C, C=O, O-H, and other groups were obviously missing when the carbonization temperature reaches 800°C; thus, high temperature promotes the decomposition of functional groups (Zhang et al., 2021). This scenario indicates that the high temperature is harmful to the groups. This result is consistent with the study of Zhang et al. (2020).
FIGURE 2. Comparison of the FTIR of COAs biochar. (A) Different solid-to-liquid ratios at same carbonization temperature (600°C); (B) same solid-to-liquid ratio (1:3) at different carbonization temperatures.
The COAs biochar has a lamellar structure and rough surface, as shown in Figure 3. This feature is caused by the COAs structure itself and the devolatilization and breakdown of biomass during carbonization (Shi, 2018; Duan et al., 2020). The increase of the liquid-to-solid ratio and carbonization temperature results in the increase of the lamellar structure and appearance of pore structure. This result is consistent with the N2 adsorption/desorption isotherm. Acid solution has a corrosive effect. It can destroy and dissolve the cellulose and other substances in the biomass and remove some metals. The removal of metals creates new pores, which is conducive to the volatilization analysis. Moreover, the evaporation degree of volatile substances increases with the increase in carbonization temperature, resulting in the increase in surface area and pore structure formation (Nikkhah et al., 2020).
FIGURE 3. SEM images of biochar treated under different conditions. (A) Untreated–600°C; (B) 1:1–600°C; (C) 1:2–600°C; and (D) 1:3–600°C.
The results in Table 2 show that HNO3 pretreatment significantly affects the specific surface area of the COAs biochar catalyst. The untreated biochar has a very low BET surface area (0.58 m2/g). However, the BET surface area increases significantly with the decrease of the solid-to-liquid ratio. Moreover, the specific surface area of the 1:3–600°C biochar is as high as 392.65 m2/g, which is approximately 677 times larger than that of the untreated biochar. Furthermore, 1:3–600°C biochar has a relatively high micropore area of 323.34 m2/g. These findings may be caused by the removal of alkali and alkaline earth metals and some inorganic substances in biomass by HNO3 pretreatment (Wang et al., 2020). The larger the specific surface area of the biochar, the more the contact surface area and active sites can be provided in the catalytic system (Yang et al., 2020).
The effects of the solid-to-liquid ratio (M/V) (untreated, 1:1, 1:2, and 1:3) and carbonization temperature (800, 700, 600, and 500°C) on bio-oil constituents were studied. The feedstock-to-catalyst ratio was 8:1, and the catalytic temperature was kept at 450°C.
The distribution of pyrolysis products under different biochar catalyst conditions is shown in Figure 4. The main components of bio-oils were divided into five categories, as shown in Figure 4B: C20+ hydrocarbons, green diesel (C13–C20), green gasoline (C10–C12), green naphtha (C5–C9), and oxy-compound (Khodadadi et al., 2020). The content of green naphtha was significantly higher than that of untreated COAs biochar with the increase of the liquid-to-solid ratio. Compared with that obtained under the untreated biochar catalyzed condition, the selectivity of green naphtha in the liquid product obtained under the catalyzed condition of 1:3–600°C biochar greatly increased from 36.01 to 67.17%. The reason is that the active groups, surface structure levels, and BET surface area of biochar prepared from COAs pretreated with HNO3 were increased, which was beneficial to the catalytic performance of biochar; this scenario enhanced catalytic cracking of decarboxylation and decarbonylation of long-chain fatty acids, alcohols, and esters in the process of catalytic pyrolysis and accelerated the Diels–Alder reaction to convert alkenes to aromatics (Duan et al., 2020). Moreover, the content of aromatics was increased, and the content of oxy-compound in bio-oil was decreased. The presence of oxy-compound in bio-oil can cause it to be chemically unstable and corrosive and reduce its calorific value (Nikkhah et al., 2020). As shown in Figure 4A, compared with those under untreated biochar condition, the content of the monocyclic aromatic hydrocarbon (MAH) in the bio-oil under the catalyzed condition of 1:3–600°C biochar increased significantly, and the selectivity of MAH increased from 46.08 to 66.86%. Moreover, the content of polycyclic aromatic hydrocarbon (PAH) was reduced, and the selectivity dropped from 37.26 to 15.90%. When the solid-to-liquid ratio was 1:2 and 1:3, the MAH content first increased and then decreased with the increase of carbonization temperature, and the PAH content first decreased and then increased. The increase of carbonization temperature resulted in the increase of the release of volatile substances in biomass, formation of the pore structure, and increase in the specific surface area. Moreover, the microporous structure inhibited the formation of high molecular weight aromatic hydrocarbons. However, the pore structure of biochar was destroyed when the carbonization temperature was excessively high, and the inhibitory effect was reduced (Zhang et al., 2021). Increasing MAH content and reducing PAH content can be considered the advantages of HNO3 pretreatment for biochar preparation. According to the results of catalytic pyrolysis experiments, when 1:3–600°C COAs biochar was used as a catalyst, the content of MAH is the highest, and the content of PAH is the lowest, and the content of green naphtha is also the highest in terms of carbon number classification. Therefore, 1:3–600°C COAs biochar was used in the following experiments.
FIGURE 4. Distribution of pyrolysis products of WVO at different biochar catalysts. (A) Area percentages of PAH, MAH, hydrocarbon (alkene and alkane), and oxy-compound of bio-oil; (B) area percentage of oxy-compound, C20+ hydrocarbons, green diesel (C13–C20), green gasoline (C10–C12), and green naphtha (C5–C9) in bio-oil.
The solid-to-liquid ratio of the pretreatment was 1:3, the catalytic temperature was fixed at 450°C, and the carbonization temperature was 600°C to study the effects of the feedstock-to-catalyst ratio (catalyst free, 8:1, 4:1, 2:1, and 1:1) on the bio-oil composition and yield. The bio-oil yields at different feedstock-to-catalyst ratios are shown in Figure 5A. The pyrolysis of WVO without catalyst had the highest bio-oil yield (82.50%). The bio-oil yield decreased with the increase of catalyst amount. Therefore, the increase of catalyst amount provides abundant catalytic active sites, prolongs the catalytic reaction time, promotes the secondary fracture of pyrolysis steam, and forms considerable noncondensable vapor, leading to the decline of bio-oil yield from 82.50 to 41.25% (Jin et al., 2018).
FIGURE 5. Effect of the feedstock-to-catalyst ratio on bio-oil. (A) Area percentage of the bio-oil containing oxy-compound, hydrocarbon (alkene and alkane), MAH, PAH, the total aromatics, and the bio-oil yield; (B) area percentage of oxy-compound, C20+ hydrocarbons, green diesel (C13–C20), green gasoline (C10–C12), and green naphtha (C5–C9) in bio-oil.
The composition of bio-oil collected at different feedstock-to-catalyst ratios are shown in Figure 5B. The area percentage of oxy-compound decreased significantly from 66.00% (catalyst-free) to 2.96% (8:1). The oxy-compound in the bio-oil produced without catalysis mainly consists of acids, alcohols, esters, and ketones. The selectivity of green naphtha, green gasoline, and green diesel was all lower than 15.00%, which limits its use in industry. The small amount of oxy-compound in the bio-oil produced by the catalyst was mainly alcohols, esters, and ketones. The area percentage of acids, alcohols, and esters decreased obviously with catalysis. The contents of green naphtha and gasoline were significantly increased with the use of the catalyst. However, the selectivity of C5–C9 was significantly inhibited, and the selectivity of C13–C20, C20+ hydrocarbons, and oxy-compound increased with the increase of catalyst dosage (more than 1 g). Long-chain fatty acids, alcohols, and esters were catalyzed to decarboxylation and decarbonylation and dehydrogenation/hydrogenation to form short-chain hydrocarbons, which then formed olefins or further cyclization and aromatization to alicyclic compounds and aromatic hydrocarbons (Lam et al., 2016). As a result, the area percentage of oxy-compound and hydrocarbons decreased considerably, whereas the area percentage of PAH and MAH increased considerably. The area percentage of hydrocarbons decreased and reached the lowest of 9.76% at 4:1 with the decrease of the feedstock-to-catalyst ratio. The further decrease of the feedstock-to-catalyst ratio slightly increased the hydrocarbon content. Olefins can be converted to aromatic hydrocarbons by the Diels–Alder reaction, a kind of a cycloaddition reaction (Lam et al., 2016). The area percentage of MAH increased from 5.10% (catalyst-free) to 69.21% (4:1). The area percentage of PAH increased from 0.00% (without catalyst) to 20.30% (2:1). High catalyst usage can hinder the passage rate of volatile substances, thus prolonging the catalytic reaction time. This scenario leads to the secondary fracture reaction and repolymerization reaction. As a result, the hydrocarbon content decreased, and the contents of MAH and PAH increased (Balasundram et al., 2018). PAHs have harmful biological effects, such as toxicity, mutagenicity, carcinogenicity, and adverse environmental effects. They are also precursors of carbon deposits, which greatly affect catalyst activity, and the high oxygen content of bio-oil affects the bio-oil quality (Zhang et al., 2014; Sun et al., 2021). It is worth noting that when the feedstock-to-catalyst ratio was 8:1 to 4:1, the increase rate of MAH and total aromatics was lower than that of the catalyst (Ding et al., 2018). Therefore, it is not economically feasible to increase the aromatics content by simply increasing the amount of the catalyst. Therefore, by analyzing the yield and composition of bio-oil, the feedstock-to-catalyst ratio of 8:1 was chosen for subsequent experiments.
The effects of catalytic temperature (600, 550, 500, 450, and 400°C) on the composition and yield of bio-oil were studied. The catalyst was 1:3–600°C biochar, and the feedstock-to-catalyst ratio was 8:1. The bio-oil components and yield distributions at different catalytic temperatures are shown in Figure 6.
FIGURE 6. Effect of catalytic temperature on bio-oil. (A) Area percentage of the bio-oil containing oxy-compound, hydrocarbon (alkene and alkane), MAH, PAH, the total aromatics, and the bio-oil yield; (B) area percentage of oxy-compound, C20+ hydrocarbons, green diesel (C13–C20), green gasoline (C10–C12), and green naphtha (C5–C9) in bio-oil.
As shown in Figure 6A, the yield of bio-oil decreased with the increase of catalytic temperature, and the maximum yield was 50.00 wt% at 400°C. Pyrolysis is an endothermic reaction, which can be promoted by a high temperature. High catalytic temperature (the temperature in the current study exceeded 400°C) can provide much energy, promoting long-chain compound fracture and small molecule compound formation. The condensable part of the small molecule compounds after condensation formed bio-oil. However, the secondary pyrolysis of the pyrolysis vapor was promoted when the catalytic temperature was further increased, and considerable noncondensable vapor was generated, leading to the bio-oil yield decrease (Wang et al., 2018). This scenario was also the main reason for the decrease of bio-oil yield as the catalytic temperature increased from 400 to 600°C.
The results showed that when the catalytic temperature increased from 400 to 600°C, the oxy-compound content decreased from 2.63 to 0.00%. The high catalytic temperature promoted the deoxidation reaction and reduced the oxy-compound content. The area percentage of the hydrocarbon decreased from 15.15% (400°C) to 6.03% (550°C). The area percentage of the MAH increased from 66.86% (450°C) to 78.82% (600°C). The high catalytic temperature also promoted PAH formation, and the area percentage of PAH increased from 10.15% (400°C) to 16.07% (550°C); the total aromatics content was up to 93.27% when the catalytic temperature was 550°C. This occurrence was due to the increase of temperature, which caused short-chain alkene oligomerization to produce mixtures of long-chain alkenes and alkanes; aromatic hydrocarbons were produced by aromatization, alkylation, and isomerization of long-chain alkenes and alkanes (Wu et al., 2020). Therefore, high temperature promotes deoxidation and aromatization at the expense of oxy-compound and olefins, and this finding is consistent with the results of Duan et al. (2020). However, the area percentage of MAH and hydrocarbons showed an opposite trend to PAH when the catalytic temperature was further increased to 600°C, indicating that the high catalytic temperature reduced PAH production. As shown in Figure 6B, the green naphtha content increased from 67.17 to 76.32% when the catalytic temperature was increased from 450 to 600°C, and the area percentage of C10+ hydrocarbons decreased significantly. This result was attributed to the catalytic fast pyrolysis process. The high catalytic temperature promoted the cracking reaction of long-chain fractions (C10+ hydrocarbons) (Duan et al., 2020). When the catalytic temperature was 600°C, the area percentage of MAH was up to 78.82%, and the area percentage of green naphtha was 76.32%, and also the oxy-compound content was the lowest, so the best catalytic temperature was 600°C.
In this study, COAs biochar was proposed for microwave-assisted catalytic pyrolysis of WVO to produce aromatic-rich bio-oil. The micropore area and BET surface area of 1:3–600°C biochar were 323.34 and 392.65 m2/g, respectively. The high carbonization temperature caused the loss of O–H and C–O groups. High catalytic temperature and catalyst dosage could promote deoxidation but also reduce the bio-oil yield. The oxy-compound significantly decreased by 63.04% from no catalysis to the feedstock-to-catalyst ratio of 8:1, thus showing significant deoxygenation capacity. The total aromatics content was up to 93.27% when the catalytic temperature was 550°C.
The original contributions presented in the study are included in the article/Supplementary Material; further inquiries can be directed to the corresponding author.
MX: conceptualization, methodology, data curation, and writing–original draft; YW: resources, supervision, project administration, and funding acquisition; QW: writing–review and editing; YZ: investigation and visualization; SZ: validation; LD: software; RZ: formal analysis; YL: project administration; and RR: funding acquisition.
This project was financially supported by the National Natural Science Foundation of China (No. 21766019 and No. 22166026), The Centrally Guided Local Science Technology Special Project (20202ZDB01012), the Major Discipline Academic and Technical Leaders Training Program of Jiangxi Province (20204BCJ23011), and the Jiangxi Provincial Natural Science Foundation (20212ACB215007).
The authors declare that the research was conducted in the absence of any commercial or financial relationships that could be construed as a potential conflict of interest.
All claims expressed in this article are solely those of the authors and do not necessarily represent those of their affiliated organizations, or those of the publisher, the editors, and the reviewers. Any product that may be evaluated in this article, or claim that may be made by its manufacturer, is not guaranteed or endorsed by the publisher.
The Supplementary Material for this article can be found online at: https://www.frontiersin.org/articles/10.3389/fenrg.2022.837875/full#supplementary-material
Balasundram, V., Ibrahim, N., Kasmani, R. M., Isha, R., Hamid, M. K. A., Hasbullah, H., et al. (2018). Catalytic Upgrading of Sugarcane Bagasse Pyrolysis Vapours over Rare Earth Metal (Ce) Loaded HZSM-5: Effect of Catalyst to Biomass Ratio on the Organic Compounds in Pyrolysis Oil. Appl. Energ. 220, 787–799. doi:10.1016/j.apenergy.2018.03.141
BP (2021). BP Statistical Review of World Energy 2021. Available at: https://www.bp.com (Accessed January 26, 2022).
Diao, R., Sun, M., Huang, Y., and Zhu, X. (2021). Synergistic Effect of Washing Pretreatment and Co-pyrolysis on Physicochemical Property Evolution of Biochar Derived from Bio-Oil Distillation Residue and walnut Shell. J. Anal. Appl. Pyrolysis 155, 105034. doi:10.1016/j.jaap.2021.105034
Ding, K., He, A., Zhong, D., Fan, L., Liu, S., Wang, Y., et al. (2018). Improving Hydrocarbon Yield via Catalytic Fast Co-pyrolysis of Biomass and Plastic over Ceria and HZSM-5: An Analytical Pyrolyzer Analysis. Bioresour. Tech. 268, 1–8. doi:10.1016/j.biortech.2018.07.108
Duan, D., Zhang, Y., Wang, Y., Lei, H., Wang, Q., and Ruan, R. (2020). Production of Renewable Jet Fuel and Gasoline Range Hydrocarbons from Catalytic Pyrolysis of Soapstock over Corn Cob-Derived Activated Carbons. Energy 209, 118454. doi:10.1016/j.energy.2020.118454
Fangfang, F., Alagumalai, A., and Mahian, O. (2021). Sustainable Biodiesel Production from Waste Cooking Oil: ANN Modeling and Environmental Factor Assessment. Sustainable Energ. Tech. Assessments 46, 101265. doi:10.1016/j.seta.2021.101265
Feng, D., Zhang, Y., Zhao, Y., Sun, S., Wu, J., and Tan, H. (2020). Mechanism of In-Situ Dynamic Catalysis and Selective Deactivation of H2O-Activated Biochar for Biomass Tar Reforming. Fuel 279, 118450. doi:10.1016/j.fuel.2020.118450
Foong, S. Y., Liew, R. K., Yang, Y., Cheng, Y. W., Yek, P. N. Y., Wan Mahari, W. A., et al. (2020). Valorization of Biomass Waste to Engineered Activated Biochar by Microwave Pyrolysis: Progress, Challenges, and Future Directions. Chem. Eng. J. 389, 124401. doi:10.1016/j.cej.2020.124401
Gupta, S., Mondal, P., Borugadda, V. B., and Dalai, A. K. (2021). Advances in Upgradation of Pyrolysis Bio-Oil and Biochar towards Improvement in Bio-Refinery Economics: A Comprehensive Review. Environ. Tech. Innovation 21, 101276. doi:10.1016/j.eti.2020.101276
Hou, Y., Qi, S., You, H., Huang, Z., and Niu, Q. (2018). The Study on Pyrolysis of Oil-Based Drilling Cuttings by Microwave and Electric Heating. J. Environ. Manage. 228, 312–318. doi:10.1016/j.jenvman.2018.09.040
Hsiao, M.-C., Kuo, J.-Y., Hsieh, S.-A., Hsieh, P.-H., and Hou, S.-S. (2020). Optimized Conversion of Waste Cooking Oil to Biodiesel Using Modified Calcium Oxide as Catalyst via a Microwave Heating System. Fuel 266, 117114. doi:10.1016/j.fuel.2020.117114
Huang, D., Li, R., Xu, P., Li, T., Deng, R., Chen, S., et al. (2020b). The Cornerstone of Realizing Lignin Value-Addition: Exploiting the Native Structure and Properties of Lignin by Extraction Methods. Chem. Eng. J. 402, 126237. doi:10.1016/j.cej.2020.126237
Huang, W.-H., Lee, D.-J., and Huang, C. (2021a). Modification on Biochars for Applications: A Research Update. Bioresour. Tech. 319, 124100. doi:10.1016/j.biortech.2020.124100
Jin, J., Li, S., Peng, X., Liu, W., Zhang, C., Yang, Y., et al. (2018). HNO3 Modified Biochars for Uranium (VI) Removal from Aqueous Solution. Bioresour. Tech. 256, 247–253. doi:10.1016/j.biortech.2018.02.022
Khodadadi, M. R., Malpartida, I., Tsang, C.-W., Lin, C. S. K., and Len, C. (2020). Recent Advances on the Catalytic Conversion of Waste Cooking Oil. Mol. Catal. 494, 111128. doi:10.1016/j.mcat.2020.111128
Lam, S. S., Wan Mahari, W. A., Cheng, C. K., Omar, R., Chong, C. T., and Chase, H. A. (2016). Recovery of Diesel-like Fuel from Waste palm Oil by Pyrolysis Using a Microwave Heated Bed of Activated Carbon. Energy 115, 791–799. doi:10.1016/j.energy.2016.09.076
Li, H., Wang, Y., Zhou, N., Dai, L., Deng, W., Liu, C., et al. (2021). Applications of Calcium Oxide-Based Catalysts in Biomass Pyrolysis/gasification - A Review. J. Clean. Prod. 291, 125826. doi:10.1016/j.jclepro.2021.125826
Li, X., and Zhang, J. (2020). Progress on Biochar Preparation through Pyrolysis Process. Acta Pet. Sin., (Pet. Process. Sect.) 36, 1101–1110. doi:10.1007/s10114-020-9499-6
Loizides, M., Loizidou, X., Orthodoxou, D., and Petsa, D. (2019). Circular Bioeconomy in Action: Collection and Recycling of Domestic Used Cooking Oil through a Social, Reverse Logistics System. Recycling 4, 16. doi:10.3390/recycling4020016
Nikkhah, H., Tavasoli, A., and Jafarian, S. (2020). Investigating the Influence of Acid Washing Pretreatment and Zn/activated Biochar Catalyst on thermal Conversion of Cladophora Glomerata to Value-Added Bio-Products. Energ. Convers. Manag. 225, 113392. doi:10.1016/j.enconman.2020.113392
Ouyang, X., and Lin, B. (2014). Impacts of Increasing Renewable Energy Subsidies and Phasing Out Fossil Fuel Subsidies in China. Renew. Sust. Energ. Rev. 37, 933–942. doi:10.1016/j.rser.2014.05.013
Putra, P. H. M., Rozali, S., Patah, M. F. A., and Idris, A. (2022). A Review of Microwave Pyrolysis as a Sustainable Plastic Waste Management Technique. J. Environ. Manage. 303, 114240. doi:10.1016/j.jenvman.2021.114240
Qiu, Z., Zhai, Y., Li, S., Liu, X., Liu, X., Wang, B., et al. (2020). Catalytic Co-pyrolysis of Sewage Sludge and rice Husk over Biochar Catalyst: Bio-Oil Upgrading and Catalytic Mechanism. Waste Manag. 114, 225–233. doi:10.1016/j.wasman.2020.07.013
Rizwan, M., Lin, Q., Chen, X., Li, Y., Li, G., Zhao, X., et al. (2020). Synthesis, Characterization and Application of Magnetic and Acid Modified Biochars Following Alkaline Pretreatment of rice and Cotton Straws. Sci. Total Environ. 714, 136532. doi:10.1016/j.scitotenv.2020.136532
Ryu, H. W., Kim, D. H., Jae, J., Lam, S. S., Park, E. D., and Park, Y.-K. (2020). Recent Advances in Catalytic Co-pyrolysis of Biomass and Plastic Waste for the Production of Petroleum-like Hydrocarbons. Bioresour. Tech. 310, 123473. doi:10.1016/j.biortech.2020.123473
Shan, R., Han, J., Gu, J., Yuan, H., Luo, B., and Chen, Y. (2020). A Review of Recent Developments in Catalytic Applications of Biochar-Based Materials. Resour. Conservation Recycling 162, 105036. doi:10.1016/j.resconrec.2020.105036
Shi, Y. (2018). The Research on Microanatomical Structure and Pore Distribution Characteristic of C. oleifera Abel., Vol. master, Central South University of Forestry and Technology.
Sun, K., Song, Y., He, F., Jing, M., Tang, J., and Liu, R. (2021). A Review of Human and Animals Exposure to Polycyclic Aromatic Hydrocarbons: Health Risk and Adverse Effects, Photo-Induced Toxicity and Regulating Effect of Microplastics. Sci. Total Environ. 773, 145403. doi:10.1016/j.scitotenv.2021.145403
Wan Mahari, W. A., Chong, C. T., Lam, W. H., Anuar, T. N. S. T., Ma, N. L., Ibrahim, M. D., et al. (2018). Microwave Co-pyrolysis of Waste Polyolefins and Waste Cooking Oil: Influence of N2 Atmosphere versus Vacuum Environment. Energ. Convers. Manag. 171, 1292–1301. doi:10.1016/j.enconman.2018.06.073
Wang, Y., Jiang, L., Dai, L., Yu, Z., Liu, Y., Ruan, R., et al. (2018). Microwave-assisted Catalytic Co-pyrolysis of Soybean Straw and Soapstock for Bio-Oil Production Using SiC Ceramic Foam Catalyst. J. Anal. Appl. Pyrolysis 133, 76–81. doi:10.1016/j.jaap.2018.04.018
Wang, Y., Yang, Q., Ke, L., Peng, Y., Liu, Y., Wu, Q., et al. (2021). Review on the Catalytic Pyrolysis of Waste Oil for the Production of Renewable Hydrocarbon Fuels. Fuel 283, 119170. doi:10.1016/j.fuel.2020.119170
Wang, Y., Zhang, Z., Zhang, S., Wang, Y., Hu, S., Xiang, J., et al. (2020). Steam Reforming of Acetic Acid over Ni/biochar Catalyst Treated with HNO3: Impacts of the Treatment on Surface Properties and Catalytic Behaviors. Fuel 278, 118341. doi:10.1016/j.fuel.2020.118341
Wu, Q., Wang, Y., Peng, Y., Ke, L., Yang, Q., Jiang, L., et al. (2020). Microwave-assisted Pyrolysis of Waste Cooking Oil for Hydrocarbon Bio-Oil over Metal Oxides and HZSM-5 Catalysts. Energ. Convers. Manag. 220, 113124. doi:10.1016/j.enconman.2020.113124
Yang, H., Chen, Z., Chen, W., Chen, Y., Wang, X., and Chen, H. (2020). Role of Porous Structure and Active O-Containing Groups of Activated Biochar Catalyst during Biomass Catalytic Pyrolysis. Energy 210, 118646. doi:10.1016/j.energy.2020.118646
Zhang, D., Lin, X., Zhang, Q., Ren, X., Yu, W., and Cai, H. (2020). Catalytic Pyrolysis of wood-plastic Composite Waste over Activated Carbon Catalyst for Aromatics Production: Effect of Preparation Process of Activated Carbon. Energy 212, 118983. doi:10.1016/j.energy.2020.118983
Zhang, H., Shao, S., Xiao, R., Shen, D., and Zeng, J. (2014). Characterization of Coke Deposition in the Catalytic Fast Pyrolysis of Biomass Derivates. Energy Fuels 28, 52–57. doi:10.1021/ef401458y
Zhang, H., Xiao, R., and Huber, G. W. (2013). Experimental Research on Co-catalytic Pyrolysis of Biomass and Waste Oil in a Fluidized Bed. J. Eng. Thermophys. 34, 771–774.
Zhang, L., He, Y., Zhu, Y., Liu, Y., and Wang, X. (2018). Camellia Oleifera Shell as an Alternative Feedstock for Furfural Production Using a High Surface Acidity Solid Acid Catalyst. Bioresour. Tech. 249, 536–541. doi:10.1016/j.biortech.2017.10.061
Keywords: Camellia oleifera Abel shell, biochar, waste vegetable oil, pyrolysis, aromatic hydrocarbon
Citation: Xia M, Wang Y, Wu Q, Zeng Y, Zhang S, Dai L, Zou R, Liu Y and Ruan R (2022) Microwave-Assisted Camellia oleifera Abel Shell Biochar Catalyzed Fast Pyrolysis of Waste Vegetable Oil to Produce Aromatic-Rich Bio-Oil. Front. Energy Res. 10:837875. doi: 10.3389/fenrg.2022.837875
Received: 17 December 2021; Accepted: 11 January 2022;
Published: 18 February 2022.
Edited by:
Yan Gao, Shandong Jianzhu University, ChinaReviewed by:
Feiqiang Guo, China University of Mining and Technology, ChinaCopyright © 2022 Xia, Wang, Wu, Zeng, Zhang, Dai, Zou, Liu and Ruan. This is an open-access article distributed under the terms of the Creative Commons Attribution License (CC BY). The use, distribution or reproduction in other forums is permitted, provided the original author(s) and the copyright owner(s) are credited and that the original publication in this journal is cited, in accordance with accepted academic practice. No use, distribution or reproduction is permitted which does not comply with these terms.
*Correspondence: Yunpu Wang, d2FuZ3l1bnB1QG5jdS5lZHUuY24=
Disclaimer: All claims expressed in this article are solely those of the authors and do not necessarily represent those of their affiliated organizations, or those of the publisher, the editors and the reviewers. Any product that may be evaluated in this article or claim that may be made by its manufacturer is not guaranteed or endorsed by the publisher.
Research integrity at Frontiers
Learn more about the work of our research integrity team to safeguard the quality of each article we publish.