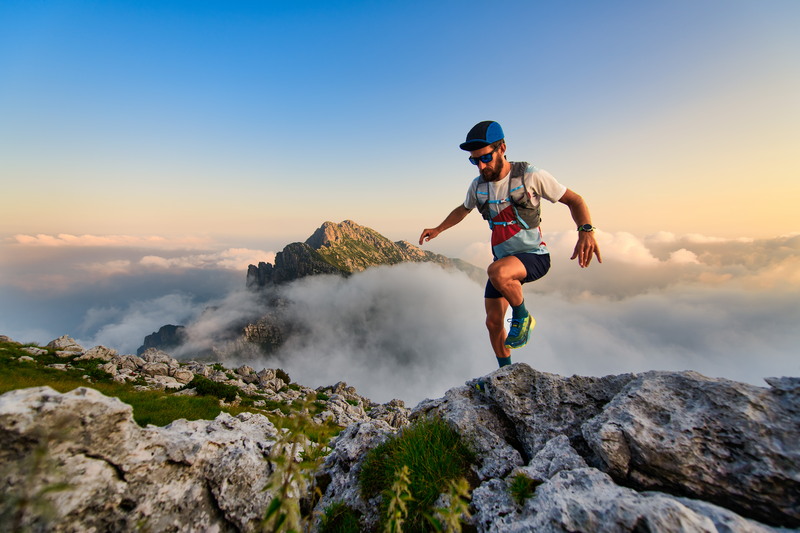
95% of researchers rate our articles as excellent or good
Learn more about the work of our research integrity team to safeguard the quality of each article we publish.
Find out more
ORIGINAL RESEARCH article
Front. Energy Res. , 27 May 2022
Sec. Fuel Cells, Electrolyzers and Membrane Reactors
Volume 10 - 2022 | https://doi.org/10.3389/fenrg.2022.827763
It is critical and challenging to start direct methanol fuel cells (DMFCs) from various environmental states to an ideal operating state by a sensor-less method. This paper presents a novel methanol sensor-less startup control (SLSC) algorithm based on the unimodal relationship of current vs. methanol concentration at a constant cell voltage during DMFC startup. A series of experiments indicate that the SLSC algorithm is capable of starting a DMFC under various initial concentrations and initial temperatures and can be easily adjusted to reduce the startup time or improve the energy efficiency. The wide applicability and easy adjustment characteristics give the SLSC algorithm a potential prospect in the DMFC system.
The direct methanol fuel cell (DMFC) is a promising portable power supply with advantages of high fuel energy density, quick refueling, and safe fuel storage (Alias, et al., 2020). For portable applications, energy density and power density are two key characteristics. Generally, a DMFC is operated in a proper methanol concentration range (0.3 mol L−1 ∼ 0.9 mol L−1) and temperature range (60–90°C) to achieve a satisfactory power density. Operating at low methanol concentration reduces output power due to methanol mass transfer limitation, while high methanol concentration causes higher mixed potential due to methanol crossover (Zenith and Krewer, 2011). Meanwhile, a DMFC needs to be heated to the specified operating temperature when starting up. A quick method to heat up is operating the DMFC at a higher methanol concentration in the early stage of the startup, and then the methanol concentration is adjusted to the proper range at the end of the startup. The adjustment process of methanol concentration is complicated in practical applications because each startup may suffer a different initial temperature and concentration. Therefore, the control of methanol concentration during startup needs elaborate attention.
The methanol concentration can be controlled by a sensor-based scheme or a sensor-less scheme. The sensor-based scheme controls methanol concentration by concentration sensor feedback. Researchers have developed a variety of methanol concentration sensors (Akbari Elnaz et al., 2016). These sensors work based on physical characteristics (Kondoh and Nozawa, 2014; Sung, et al., 2010; Jon, 1998) or electrochemical characteristics (Yang, et al., 2010; Yan, et al., 2013; Sun, et al., 2006). Physics-based sensors are complex and expensive, and electrochemical-based sensors are unstable (Akbari, et al., 2016). These shortcomings make sensor-based schemes difficult to be widely applied in commercial DMFCs. The sensor-less scheme controls the methanol concentration by the stack operation parameters’ feedback. So far, most sensor-less schemes were developed for steady operation. One kind of scheme involves directly estimating the methanol concentration with a neural network (Aras, 2015), interpolation formula (Shen, et al., 2010), or mechanism model (Zenith and Krewer, 2010; Zenith, et al., 2015). The other kind of scheme involves indirectly controlling the methanol concentration based on the trend of the operating parameters (Chang et al., 2007; Ha, et al., 2008). Aras and Bayramoglu (2015) built up an adaptive neuro-fuzzy inference system (ANFIS) model of DMFC to predict and control methanol concentration by methanol flow rate, temperature, voltage, and current. Chiu and Lien (2006) predicted the methanol concentration using an interpolation relation between methanol concentrations and current–voltage–temperature (I–V–T) surfaces. Chang et al. (2008) and Chang et al. (2010) proposed an impulse response discrete time fuel injection (IR-DTIF) scheme to control the methanol concentration based on the power change trend, rather than the estimation value of the methanol concentration. Nevertheless, these sensor-less schemes only work well in steady-state operation due to the complexity of the non-linear relationship between the stack operation parameters and the methanol concentration.
A few sensor-less schemes are developed for startup operation, where operating parameter changes are too drastic to control the methanol concentration. The startup algorithm of the DMFC system needs to meet four goals together: 1) heat the DMFC to a proper temperature, 2) adjust the methanol concentration to an appropriate range, 3) discharge at the normal working power, and 4) start up the DMFC in a shorter time. An et al. (2014) developed a startup scheme by stepwise increasing the current based on the undershoot behavior of voltage. Their algorithm increases the power quickly during startup at a proper initial concentration, but it may take a longer time when starting under a lower initial concentration (Opu et al., 2016). The DMFC is started at a high concentration to heat the stack quickly. Their scheme adjusts the fuel feed rate by the temperature feedback. This may cause concentration oscillations because the temperature responds slowly as the concentration changes. In a word, despite the good performance of the existing startup schemes in some respects, some shortcomings still exist, such as the dependence on the initial concentration and the hysteresis of adjustment.
This work presents a new sensor-less startup control (SLSC) algorithm for the DMFC, which is constructed based on the unimodal relationship between the current and the methanol concentration at a constant cell voltage. The algorithm uses a fast response parameter (current) as a feedback signal to adjust the methanol concentration. The methanol concentration is adjusted into a specific range that matches the preset current, regardless of the initial concentration. The practicality of the SLSC algorithm is validated by a series of experiments under various initial temperatures and various initial concentrations. Finally, the SLSC algorithm is optimized for different purposes.
As shown in Figure 1, the DMFC test system contains an air compressor, two liquid pumps (circulation pump and fuel pump), two tanks (methanol fuel tank and methanol solution tank), a mixer, a DMFC stack, a temperature sensor, and a condenser.
The circulation pump feeds the methanol solution to the anode of the DMFC stack, and the anode exhaust mixture goes back to the methanol solution tank. The fuel pump feeds the methanol to the mixer to adjust the concentration of the methanol solution. The air compressor feeds the air to the cathode of the stack, and the cathode exhaust mixture goes through a condenser. Then, the condensed water goes back to the methanol solution tank. The temperature at the anode outlet is monitored and used as the stack temperature. The homemade DMFC stack contains 26 cells, and the preset normal working power is 30 W. Each MEA has an active area of 25 cm2.
The red dashed lines in Figure 1 represent the signal flow of the DMFC system. The controller (PC) collects current, voltage, and temperature data from the electronic load (IT8513C, ITECH Electronics Co.) and temperature sensor (DS18B20, Texas Instruments). Then, the controller (PC) controls the fuel pump (W0109-1B, Longer Precision Pump Co.) to adjust the fuel feed rate according to the startup control algorithm. The DMFC stack discharges in a constant voltage (CV) mode.
The SLSC algorithm is constructed based on the unimodal relationship of current vs. methanol concentration at a constant cell voltage, as shown in Figure 2. At lower methanol concentrations, the stack has poor performance due to methanol mass transfer loss, and the current increases with the increment of methanol concentration. When the methanol concentration is excessive (higher than a certain one), the cathodic polarization loss becomes larger due to the intense crossover methanol, and the current decreases with the increment of methanol concentration. This unimodal relationship brings on a peak current (Imax). Normally, we can define a “normal range” around Imax to operate the DMFC for a good performance. However, during startup, it is better to define a “startup range” to operate the DMFC for a higher temperature rising rate. Although higher methanol concentration operation can rapidly raise the temperature, it may also cause local overheating and irreversible damage to the stack. The maximum concentration to ensure the safe operation is determined by many factors, e.g., the stack structure and the MEA type (Ru, et al., 2019; Feng et al., 2017). Here, the acceptable maximum concentration is 2 mol L−1 for our homemade stack.
FIGURE 2. Relationship of the current, temperature rising rate, vs. methanol concentration of our test system. Stack state: 26 units of MEAs with 25 cm2 active area per unit. Discharge voltage: 0.4 V cell−1. Temperature: 60°C. Green area: concentration control range for normal operation. Red area: concentration control range for startup operation.
Based on the normal range and startup range, the SLSC algorithm divides the startup process into two stages: heat-up stage and transition stage. In the heat-up stage, the SLSC algorithm operates the DMFC in the startup range. Then in the transition stage, the SLSC algorithm reduces the concentration to the normal range. The methanol concentration is adjusted by current feedback because the current responds quickly when the concentration changes. Therefore, in the heat-up stage, in order to operate the DMFC in the startup range, the SLSC algorithm adjusts the fuel feed rate to achieve the following two goals: 1) the current is below the peak current and 2) the current is negatively related to the methanol concentration. ΔIset is defined as the difference between the peak current (Imax) and the current at the reference control point for startup. It is a critical control parameter of SLSC algorithm, and we will discuss it in detail in Section 3.3.1. According to Figure 2, increasing ΔIset can increase the operation concentration during startup. Since the acceptable maximum concentration is 2 mol L−1, ΔIset should be set below 0.75°A.
In addition, due to the wide temperature span in the startup process, a temperature-compensated equation is needed to reduce the effect of temperature on the feedback current. The temperature-compensated equation is constructed by pre-experiment and discussed in Supplementary Material 1.
The startup control program is created according to the operation strategy mentioned above, as shown in Figure 3. Parameters in the program are listed in Appendix Table A1. When a DMFC starts, it switches on the air compressor and circulation pump, discharges at a constant voltage (Vset), and goes to the heat-up stage. Vset is defined as the initial discharge voltage. It is also a critical control parameter of SLSC algorithm, and we will discuss it in detail in Section 3.3.2.
In the heat-up stage, the SLSC algorithm firstly finds the peak current (Imax) and then adjusts the concentration to the startup range. At first, the algorithm empirically sets Imax in the database. Next, it gradually increases the fuel feed rate and continuously monitors the current and temperature. If the current grows up, Imax is updated in the database by it. If the current drops down, the latest Imax in the database is obtained. Then, the SLSC algorithm adopts a positive feedback equation to control the fuel feed rate and adjust the methanol concentration to the startup range, as expressed in Equation 1. Parameters of Equation 1 are listed in Appendix Table A1. At the same time, the SLSC algorithm sets a maximum fuel feed rate (Nm_max) in order to prevent the local concentration from being too high. The SLSC algorithm keeps the DMFC running in the startup range until the DMFC stack reaches a proper temperature (Tmid). Here, we empirically set Tmid to 45°C. After that, the SLSC algorithm turns to the transition stage:
In the transition stage, the SLSC algorithm needs to reduce methanol concentration to the normal range. To this end, the SLSC algorithm shuts down the fuel pump in order to interrupt methanol feed and reduces the discharge voltage in order to accelerate methanol consumption. At the same time, the SLSC algorithm sets a minimum discharge voltage (Vmin: 0.4 V cell−1) in order to safely operate the stack.
The initial temperature (Tini) varies with the season and region of application. Starting in summer may confront a higher initial temperature. Starting in winter may confront a frozen stack, which requires some extra work to bring the DMFC stack out from the frozen state (Park, et al., 2010), and it is beyond the scope of the SLSC algorithm. Here, we focus on starting at higher temperatures and carrying out startup tests under the initial temperatures of 23°C, 30°C, and 35°C.
Figure 4 shows the power, the temperature, the fuel feed rate, and the temperature rising rate during DMFC startup at various initial temperatures. As shown in Figure 4, the DMFC can be stepwise started by the SLSC program. In the heat-up stage (solid line), the fuel feed rate increases from zero to the maximum (Nm,max) and lasts for tens of seconds at Nm,max and then decreases rapidly. It leads to a gradual increase of methanol concentration. The temperature rising rate increases continuously (Figure 4D) because more and more methanol transports to the cathode and reacts with oxygen. Then, in the transition stage (dotted line), the fuel feed rate drops to zero (Figure 4C), resulting in a gradual decrease of methanol concentration. The temperature rising rate gradually decreases (Figure 4D), the temperature tends to be stable (Figure 4B), and the power increases rapidly (Figure 4A). In addition, when starting at a low initial temperature, the algorithm can keep the DMFC running at a high temperature rising rate for a longer time. For example, the algorithm keeps the DMFC running above 3°C min−1 for 8.5 min with the initial temperature of 23°C, while 5.6°min with 35°C. These results indicate that the SLSC algorithm is effective at various initial temperatures.
FIGURE 4. Profiles of the (A) power, (B) temperature, (C) fuel feed rate, and (D) temperature rising rate of the DMFC during startups at various initial temperatures. Cini: 0.5 mol L−1.
On the contrary, according to Figure 4A, the power grows up slowly in the heat-up stage and grows up faster in the transition stage. In the heat-up stage, the SLSC algorithm operates the DMFC at high methanol concentration, which is slightly similar to Opu’s algorithm (Opu et al., 2016). The temperature increases rapidly because of the intense reaction rate of crossover methanol with oxygen. The rising temperature improves the power, but the high methanol concentration limits the power by severe mixed potential. Thus, the power increases slowly in the heat-up stage. In the transition stage, the SLSC algorithm reduces methanol concentration by interrupting methanol feed and rising discharge current (by reducing voltage), which is slightly similar to An’s algorithm (An et al., 2014). The temperature still rises and the temperature rising rate drops as the concentration recovers to the normal range. Both the rising temperature and the recovered concentration can improve the power. Therefore, the output power rises faster in the transition stage than the heat-up stage. To some extent, the SLSC algorithm combines the advantages of Opu’s algorithm and An’s algorithm and shows stronger applicability.
The initial methanol concentration for DMFC startups is influenced by many factors. After the DMFC shutdown, the methanol and water in the methanol solution will gradually evaporate and deplete, which causes an uncertain initial concentration for the next startup. In order to verify the effectiveness of the SLSC algorithm at various initial concentrations, we carry out startup tests under the initial concentrations of 0.3 mol L−1, 0.5 mol L−1, and 0.7 mol L−1. The results are shown in Figure 5.
FIGURE 5. Profiles of the (A) power, (B) temperature, (C) fuel feed rate, and (D) temperature rising rate of the DMFC during startups at various initial concentrations. Tini: 23°C.
The profiles of the temperatures, powers, and fuel feed rates in Figures 5A-C are similar to those in Figurse 4A-C, indicating that startup processes under different initial concentrations are similar to those under different initial temperatures. In addition, when the initial concentration increases from 0.3 mol L−1 to 0.7 mol L−1, the average temperature rising rate increases from 3.8°C min−1 to 5.3°C min−1 (Figure 5D), and the feeding amount of methanol decreases from 0.25 to 0.23 mol (Figure 5C). It can be seen that the temperature rises rapidly under high initial concentration although less methanol is injected. The rapid increase in temperature accelerates methanol consumption, which means that more methanol in methanol solution is consumed when starting at a high initial concentration. These results indicate that the SLSC algorithm is also effective at various initial concentrations below 0.7 mol L−1.
Startup time and energy efficiency are two key factors that affect the competitiveness of the SLSC algorithm. When using the SLSC algorithm, a shorter startup time or a higher energy efficiency can be achieved by adjusting two parameters: ΔIset and Vset. To this end, we investigated the effect of ΔIset and Vset on startup time and energy efficiency.
As mentioned in Section 3.1, ΔIset affects the startup time and energy efficiency by changing the operation concentration during startup. It should be set below 0.75 A to prevent irreversible damage from local overheating. Meanwhile, if ΔIset is too low, the methanol concentration cannot increase to the startup range. Therefore, a range of 0.3–0.7°A is chosen to investigate the effect of ΔIset on startup time and energy efficiency. The results are shown in Figure 6 and Table 1. The startup time is recorded when the output power reaches the normal working power of 30 W. In addition, the average methanol consumption rate and the energy efficiency are estimated by an energy balance model (Supplementary Material 2) according to the experimental data.
FIGURE 6. Profiles of the (A) power, (B) temperature, (C) fuel feed rate, and (D) temperature rising rate of the DMFC during startups at various ΔIset. Cini: 0.3 mol L−1; Tini: 23°C; Vset: 0.45 V cell−1.
TABLE 1. Parameters of DMFC startup at various ΔIset. Cini: 0.3 mol L−1, Tini: 23°C, and Vset: 0.45 V cell−1.
The results show that the startup time reduces 34% as ΔIset rises from 0.3 to 0.5°A, while increases 17% as ΔIset rises from 0.5 to 0.7°A. When ΔIset increases from 0.3 to 0.5°A, the feeding amount of methanol increases by 28% (Figure 6C), and the average temperature rising rate increases by 54% (Figure 6D). The higher temperature rising rate has two effects: 1) reducing the time cost of the heat-up stage from 7.3 to 5.1 min and 2) increasing the average methanol consumption rate by 44%. It can be seen that the average methanol consumption rate increases more significantly than the feeding amount of methanol. Consequently, a shorter time is needed to recover the methanol concentration, which reduces the time cost of the transition stage from 7.3 to 4.5 min. When ΔIset increases from 0.5 to 0.7°A, the feeding amount of methanol increases by 25% (Figure 6C), and the average temperature rising rate increases by 9% (Figure 6D). The higher temperature rising rate also has two effects: 1) reducing the time cost of the heat-up stage from 5.1 to 4.8 min and 2) increasing the average methanol consumption rate by 6%. In this case, the feeding amount of methanol increases more significantly than the methanol consumption rate, which increases the time cost of the transition stage from 4.5 to 6.5 min. These results indicate that ΔIset needs to be carefully set to reduce the startup time.
The energy efficiency increases with the decrease of ΔIset. When ΔIset decreases from 0.7 to 0.3°A, the feeding amount of methanol decreases by 37% (Figure 6C). It results in a low operation concentration during startup. Consequently, the temperature rising rate decreases by 41%, and the average methanol consumption rate decreases by 34%. Meanwhile, the average power increases by 5% even at the lower temperature rising rate. It may be caused by the low operation concentration because reducing the methanol concentration within the startup range can improve the stack performance, as shown in Figure 2. These results indicate that the improved energy efficiency at low ΔIset is caused by the reduced average methanol consumption rate and the increased average power. Therefore, higher energy efficiency can be achieved by reducing ΔIset within our test scope.
Vset is another key parameter to improve the startup process. It also needs to be limited within a certain range to safely operate the stack (Slepski et al., 2014). Here, a voltage range of 0.4–0.5 V cell−1 is chosen to investigate the effect of Vset on startup time and energy efficiency. The results are shown in Figure 7 and Table 2.
FIGURE 7. Profiles of the (A) power, (B) temperature, (C) fuel feed rate, and (D) temperature rising rate of the DMFC during startups at various Vset. Cini: 0.3 mol L−1; Tini: 23°C; ΔIset: 0.5 A.
TABLE 2. Parameters of DMFC startup at various initial discharge voltages. Cini: 0.3 mol L−1; Tini: 23°C; ΔIset: 0.5 A.
The results show that as Vset decreases, the startup time decreases and the energy efficiency increases. When Vset decreases from 0.5 V cell−1 to 0.4 V cell−1, the total feeding amount of methanol changes slightly (less than 7%, Figure 7C), the average power increases by 54% (Figure 7A), the average temperature rising rate increases by 23% (Figure 7D), and the average methanol consumption rate increases by 25% (Table 2). The rapid increment of temperature reduces the time cost of the heat-up stage, which decreases from 6.2 to 4.3 min. In addition, thanks to the similar total feeding amount of methanol under different Vset, the higher methanol consumption rate reduces the time cost of the transition stage, which decreases from 5.5 to 4.5 min. Thus, a lower Vset can reduce the startup time by reducing the time cost of both the heat-up stage and the transition stage. More luckily, when Vset decreases to 0.4 V cell−1, the startup time of the SLSC algorithm is shorter than that in the literature under similar initial conditions, which are 8.8 min (SLSC algorithm in this paper), 14 min (An et al., 2014), and 25 min (Chen, et al., 2007). On the contrary, focusing on energy efficiency, it can be seen that the power increases more significantly than the methanol consumption rate as Vset decreases, which means that reducing Vset can improve the energy efficiency. Therefore, both a shorter startup time and a higher energy efficiency can be achieved by reducing Vset within our test scope.
A novel sensor-less startup control (SLSC) algorithm is proposed to solve the problem of starting a DMFC in various application scenarios. The SLSC algorithm is constructed based on the unimodal relationship between the current and the concentration at a constant cell voltage during startup. It firstly operates the DMFC at a higher concentration to heat up quickly and then recovers the concentration to the normal range at the end of the startup. Systematic experiments show that the SLSC algorithm is effective under different initial temperatures and concentrations and can be easily adjusted to improve the energy efficiency or startup time. In our experiment, even under a low initial concentration of 0.3 mol L−1 and temperature of 23°C, the optimized SLSC algorithm can start a DMFC within 8.8 min. The adaptability for various initial conditions and startup goals gives the SLSC algorithm a wide application prospect in commercial DMFCs.
The raw data supporting the conclusions of this article will be made available by the authors, without undue reservation.
HG conceived the presented idea, carried out the experiment, and wrote the manuscript with support from HS. HS helped supervise the project. All authors discussed the results and contributed to the final manuscript.
The authors declare that the research was conducted in the absence of any commercial or financial relationships that could be construed as a potential conflict of interest.
All claims expressed in this article are solely those of the authors and do not necessarily represent those of their affiliated organizations, or those of the publisher, the editors, and the reviewers. Any product that may be evaluated in this article, or claim that may be made by its manufacturer, is not guaranteed or endorsed by the publisher.
The Supplementary Material for this article can be foundonline at: https://www.frontiersin.org/articles/10.3389/fenrg.2022.827763/full#supplementary-material
Akbari, E., Buntat, Z., Nikoukar, A., Kheirandish, A., and Afroozeh, M. A. (2016). Sensor Application in Direct Methanol Fuel Cells (DMFCs). Renew. Sustain. Energ. Rev. 60, 1125–1139. doi:10.1016/j.rser.2016.02.001
Akbari, E., Buntat, Z., Nikoukar, A., Kheirandish, A., Khaledian, M., and Afroozeh, A. (2016). Sensor Application in Direct Methanol Fuel Cells (DMFCs). Renew. Sustain. Energ. Rev. 60, 1125–1139. doi:10.1016/j.rser.2016.02.001
Alias, M. S., Kamarudin, S. K., Zainoodin, A. M., and Masdar, M. S. (2020). Active Direct Methanol Fuel Cell: An Overview. Int. J. Hydrogen Energ. 45, 19620–19641. doi:10.1016/j.ijhydene.2020.04.202
An, M.-G., Mehmood, A., and Ha, H. Y. (2014). A Sensor-Less Methanol Concentration Control System Based on Feedback from the Stack Temperature. Appl. Energ. 131, 257–266. doi:10.1016/j.apenergy.2014.06.017
Aras, Ö., and Bayramoglu, M. (2015). Employing Direct Methanol Fuel Cell Yielded In Situ Methanol Concentrations under Varying Operating Conditions: A Comparative Optimal Search Study. J. Electrochem. Soc. 163, F230–F237. doi:10.1149/2.0941603jes
Aras, Ö. (2015). Control Applications (ANFIS/Fuzzy/PID) over Mathematical Model of DMFC System: Experimental and Simulation Studies. Int. J. Electrochem. Sci. 10, 8013–8023.
Chang, C. L., Chen, C. C., Liou, D. H., Chang, C. Y., and Cha, H. C. (2010). Fuel Sensor-Less Control of a Liquid Feed Fuel Cell under Dynamic Loading Conditions for Portable Power Sources (II). J. Power Sourc. 195, 1427–1434. doi:10.1016/j.jpowsour.2009.09.012
Chang, C. L., Chen, C. C., and Liou, D. H. (2007). Fuel Sensor-Less Control of a Liquid Feed Fuel Cell System under Steady Load for Portable Applications. J. Power Sourc. 164, 606–613. doi:10.1016/j.jpowsour.2006.10.092
Chang, C. L., Chen, C. C., and Liou, D. H. (2008). Fuel Sensor-Less Control of a Liquid Feed Fuel Cell under Dynamic Loading Conditions for Portable Power Sources (I). J. Power Sourc. 182, 133–140. doi:10.1016/j.jpowsour.2008.04.026
Chen, C. Y., Liu, D. H., Huang, C. L., and Chang, C. L. (2007). Portable DMFC System with Methanol Sensor-Less Control. J. Power Sourc. 167, 442–449. doi:10.1016/j.jpowsour.2007.02.056
Chiu, Y.-J., and Lien, H.-C. (2006). A Strategy of Estimating Fuel Concentration in a Direct Liquid-Feed Fuel Cell System. J. Power Sourc. 159, 1162–1168. doi:10.1016/j.jpowsour.2005.12.099
Feng, Y., Liu, H., and Yang, J. (2017). A Selective Electrocatalyst-Based Direct Methanol Fuel Cell Operated at High Concentrations of Methanol. Sci. Adv. 3, 8. doi:10.1126/sciadv.1700580
Ha, T., Kim, J., Joh, H., Kim, S., Moon, G., Lim, T., et al. (2008). Sensor-less Control of Methanol Concentration Based on Estimation of Methanol Consumption Rates for Direct Methanol Fuel Cell Systems. Int. J. Hydrogen Energ. 33, 7163–7171. doi:10.1016/j.ijhydene.2008.09.019
Jon, P. (1998). Precision Laser-Based Concentration and Refractive Index Measurement of Liquids. Microscale Thermophysical Eng. 2, 261–272. doi:10.1080/108939598199900
Kondoh, J., and Nozawa, T. (2014). Online Real-Time Monitoring Method of Methanol Concentration for Direct Methanol Fuel Cell Using Shear Horizontal Surface Acoustic Wave. IEEE Int. Ultrason. Symp., 1509–1512. doi:10.1109/ULTSYM.2014.0373
Opu, M., Singh, R., Korparkar, A., and Henderson, J. (2016). Method for Measuring and Controlling Methanol Concentration in a Methanol Fuel Cell Oorja Protionics. inc.. Fremont, California, US.
Park, Y.-C., Peck, D.-H., Kim, S.-K., Lim, S., Lee, D.-Y., Ji, H., et al. (2010). Operation Characteristics of Portable Direct Methanol Fuel Cell Stack at Sub-zero Temperatures Using Hydrocarbon Membrane and High Concentration Methanol. Electrochimica Acta 55, 4512–4518. doi:10.1016/j.electacta.2010.02.096
Ru, C., Gu, Y., Duan, Y., Zhao, C., and Na, H. (2019). Enhancement in Proton Conductivity and Methanol Resistance of Nafion Membrane Induced by Blending Sulfonated Poly(arylene Ether Ketones) for Direct Methanol Fuel Cells. J. Membr. Sci. 573, 439–447. doi:10.1016/j.memsci.2018.12.030
Shen, K.-S., Wan, C.-C., Wang, Y.-Y., Yu, T. L., and Chiu, Y.-J. (2010). An Algorithm for Sensor-Less Fuel Control of Direct Methanol Fuel Cells. J. Power Sourc. 195, 4785–4795. doi:10.1016/j.jpowsour.2010.02.051
Slepski, P., Janicka, E., Darowicki, K., and Pierozynski, B. (2014). Impedance Monitoring of Fuel Cell Stacks. J. Solid State. Electrochem. 19, 929–933. doi:10.1007/s10008-014-2676-8
Sun, W., Sun, G., Yang, W., Yang, S., and Xin, Q. (2006). A Methanol Concentration Sensor Using Twin Membrane Electrode Assemblies Operated in Pulsed Mode for DMFC. J. Power Sourc. 162, 1115–1121. doi:10.1016/j.jpowsour.2006.07.033
Sung, C. C., Tseng, Y. L., Chiang, Y. F., and Chen, C. Y. (2010). Evaluation of Ultrasonic Sensing of Methanol Concentration for Direct Methanol Fuel Cell. Sensors Actuators A: Phys. 161, 101–107. doi:10.1016/j.sna.2010.04.035
Yan, L., Liao, J., Feng, L., Zhao, X., Liang, L., Xing, W., et al. (2013). Developing and Performance Measurements for a Novel Miniaturized Electrochemical Methanol Sensor. J. Electroanalytical Chem. 688, 49–52. doi:10.1016/j.jelechem.2012.09.010
Yang, J. S., Park, J. H., Kim, S.-I., Kim, Y. T., and Kim, Y. H. (2010). I-V Characteristics of a Methanol Concentration Sensor for Direct Methanol Fuel Cell (DMFC) by Using Catalyst Electrode of Pt Dots. Curr. Appl. Phys. 10, 370–372. doi:10.1016/j.cap.2009.05.012
Zenith, F., and Krewer, U. (2010). Modelling, Dynamics and Control of a Portable DMFC System. J. Process Control. 20, 630–642. doi:10.1016/j.jprocont.2010.02.014
Zenith, F., and Krewer, U. (2011). Simple and Reliable Model for Estimation of Methanol Cross-Over in Direct Methanolfuel Cells and its Application on Methanol-Concentration Control. Energy Environ. Sci. 4, 519–527. doi:10.1039/c0ee00415d
Keywords: DMFC, sensor-less, startup, unimodal relationship, various initial conditions
Citation: Gan H and Sun H (2022) Methanol Sensor-Less Control Strategy for Direct Methanol Fuel Cell Startup. Front. Energy Res. 10:827763. doi: 10.3389/fenrg.2022.827763
Received: 02 December 2021; Accepted: 11 March 2022;
Published: 27 May 2022.
Edited by:
Lei Ge, University of Southern Queensland, AustraliaReviewed by:
Kingshuk Dutta, Central Institute of Plastics Engineering and Technology, IndiaCopyright © 2022 Gan and Sun. This is an open-access article distributed under the terms of the Creative Commons Attribution License (CC BY). The use, distribution or reproduction in other forums is permitted, provided the original author(s) and the copyright owner(s) are credited and that the original publication in this journal is cited, in accordance with accepted academic practice. No use, distribution or reproduction is permitted which does not comply with these terms.
*Correspondence: Hai Sun, c3VuaGFpQGRpY3AuYWMuY24=
Disclaimer: All claims expressed in this article are solely those of the authors and do not necessarily represent those of their affiliated organizations, or those of the publisher, the editors and the reviewers. Any product that may be evaluated in this article or claim that may be made by its manufacturer is not guaranteed or endorsed by the publisher.
Research integrity at Frontiers
Learn more about the work of our research integrity team to safeguard the quality of each article we publish.