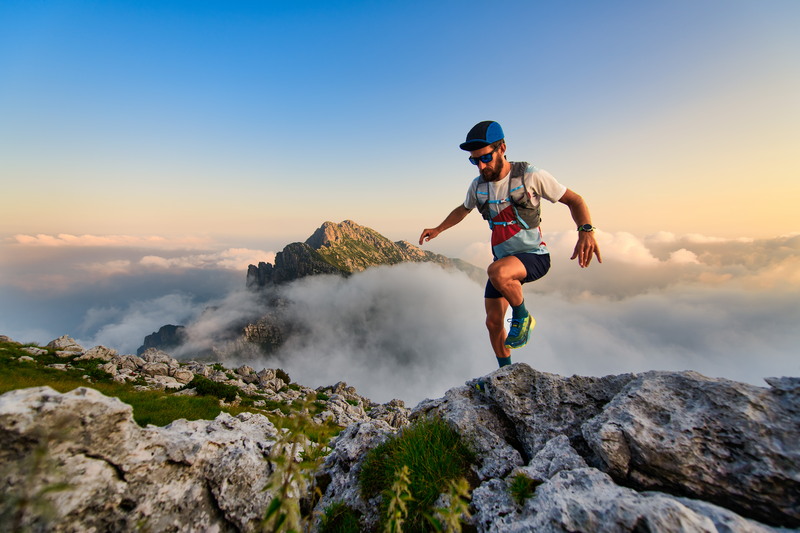
94% of researchers rate our articles as excellent or good
Learn more about the work of our research integrity team to safeguard the quality of each article we publish.
Find out more
ORIGINAL RESEARCH article
Front. Energy Res. , 02 March 2022
Sec. Advanced Clean Fuel Technologies
Volume 10 - 2022 | https://doi.org/10.3389/fenrg.2022.826469
The challenges associated with unconventional reservoirs are related to their intrinsic nature: extremely low porosity and permeability. Combinations of horizontal wells and multistage hydraulic fracturing techniques have been developed to overcome the production obstacles and unlock the vast amount of oil in place in such formations. However, oil production still exhibits a sharp decline within the first 2 years after the stimulation, leading to an oil recovery of less than 15%. Thus, enhanced oil recovery methods need to be investigated to further increase the production rates and the recovery. In this study, laboratory experiments and numerical simulations were conducted to evaluate the performance of the CO2 foam huff and puff process and its impacts on oil recovery in tight oil formations. More specifically, the foam half-life was measured as a function of surfactant concentration and followed by the foam drainage ratio and its rheological properties in the subsequent tests. Reservoir simulations were conducted using the lab data and the field data collected from Cardium formation. Sensitivity analyses were finally carried out to investigate the effects of controlling variables on the CO2 foam performance. Experimental results revealed that the optimal surfactant concentration was found to be 0.2%, which is the critical micelle concentration point. Simulation results show that CO2 foam huff and puff can increase the oil recovery by more than 11% compared to that of the primary production. Moreover, sensitivity analyses show that the production time, injection time, and soaking time are the main effecting parameters, while the injection rate and the incremental injection rate are less important.
Worldwide oil demand and decline in the well production rate has led to the implementation of improved oil recovery (IOR) and enhanced oil recovery (EOR) methods to sustain oil production (Golabi et al., 2012; Shabib-Asl et al., 2014; Ayoub et al., 2015; Hosseini et al., 2015a; Hosseini et al., 2015b; Shabib-Asl et al., 2015a; Shabib-Asl et al., 2015b; Dianatnasab et al., 2016; Shabib-AsL et al., 2019a; Shabib-Asl et al., 2019b). Tight oil reservoirs provide 45% of total oil production in the U.S. and 9% of world oil production (Wang et al., 2016; Shabib-Asl and Plaksina, 2019; Shabib-Asl et al., 2020), yet the oil recovery from the primary production and waterflooding of such formations is as low as 10–15%, compared to 40% from conventional reservoirs (Hosseini et al., 2015a). Due to the low injectivity in the tight oil reservoirs, gas injection is preferred as the potential EOR techniques, such as huff and puff gas injection. In this technique, gas is primarily injected into the reservoir (huff process), and then time is given for the gas to improve the physical properties of the oil (soaking time). After an optimum soaking time, the well will return to production (puff process) (Zhou et al., 2018). Using the huff and puff EOR process can activate production mechanisms such as viscosity reduction (Sayegh and Maini, 1984), oil swelling (Hoffman and Reichhardt, 2019), reservoir re-pressurization (Zhang et al., 2004), and solution gas drive (Monger et al., 1991). There are many parameters that can affect the huff and puff performance, including soaking time, injection rate, injection pressure, number of cycles, and injection fluid composition, which need to be optimized for its field application to achieve maximum oil recovery or profits.
Researchers have conducted both experimental and numerical studies on CO2 injection performance under different conditions (Rahmanifard et al., 2014). Wan et al. (2018) used nuclear magnetic resonance (NMR) technology to investigate pore-scale recovery mechanisms of cyclic nitrogen injection and revealed that the first few cycles provided the most accessible oil (Wan et al., 2018). Santiago and Kantzas (2020) performed a huff and puff gas injection simulation for an unconventional gas condensate reservoir (Santiago and Kantzas, 2020). They discovered that the higher number of cycles yields more efficient contact between the injected fluid and reservoir oil; nevertheless, they emphasized that extra cycles do not constantly enhance oil production. Li and Sheng (2017) also reported that the incremental produced oil decreased while the number of cycles increased (Li and Sheng, 2017). On the other hand, the incremental oil produced is not a direct function of soaking time in all cases. Yu et al. (2016) reported that increasing soaking time from 0.25 to 12 h in the laboratory could increase recovery by about 7%, but expanding soaking time from 12 to 48 h only increases recovery by 1% (Yu et al., 2016). Furthermore, (Meng and Sheng, 2016) observed that the best recovery case was the one that had no soaking time. Plus, increasing the number of cycles when the soaking time was large can decrease the produced oil for a limited time owing to the increased non-productive period (Meng and Sheng, 2016). There is a notable difference in the oil production rate after the first or second cycle. Moreover, the role of the injection rate and pressure has also been investigated in numerous research studies (Monger and Coma, 1988; Monger et al., 1991; Shayegi et al., 1996; Song and Yang, 2013; Wang et al., 2013; Yu et al., 2014; Sanchez-Rivera et al., 2015; Wan et al., 2015; Sun et al., 2016; Zhang et al., 2018). Wan et al. (2018) and Kerr et al. (2020) both showed that higher injection pressure and larger slug size would lead to an increase in the recovery factor (Wan et al., 2018; Kerr et al., 2020). Field and laboratory data indicated that the larger slug size improves oil production (Monger and Coma, 1988; Monger et al., 1991; Cronin et al., 2019). Evaluation of huff and puff CO2 injection into Texas Gulf Coast Miocene reservoirs reveals a weak correlation between slug size and incremental oil produced, but the larger slugs appear to be better. A study by Haskin and Alston, (1989) showed that the optimum soaking time was confirmed to be between 14 and 21 days, and the larger or shorter soaking time was considered uneconomical (Haskin and Alston, 1989).
The limitations associated with the gas injection are well understood so far (Farajzadeh et al., 2016; Hematpur et al., 2016; Moortgat, 2016; Zaker et al., 2020; Khan and Mandal, 2021). Gas fingering and channeling are shown to be destructive to overall operation performance (Navarro-Brull and Gómez, 2018; Yang and Hou, 2020; Zhao et al., 2020), and the mobility control methods are developed to reduce the negative effects of injection of weightless, low-viscosity fluid (Kovscek and Bertin, 2003; Li et al., 2010; Yu et al., 2012; Sabet et al., 2016). The addition of surfactant solution to the injection stream could effectively reduce surface tension between liquid and gas phases, thus forming stable bubbles and trapping the gas phase that prevents the gas phase from bypassing the oil bank (Zhao et al., 2015; Afifi et al., 2021). The CO2 foam properties such as stability, foam quality, and rheological behavior are investigated in numerous studies (Rafati et al., 2016; Yekeen et al., 2017; AlYousef et al., 2018; Phukan et al., 2020) to increase foam half-life and the apparent viscosity. Xu et al. (2017) conducted a series of experimental tests on CO2 foam huff and puff injection and showed the beneficial aspects of this method (Xu et al., 2017). Moreover, their findings showed that the ultimate oil recovery can provide 13% more than CO2 injection in the case of CO2 foam injection, and the observations suggest that the CO2 foam was capable of increasing sweep efficiency by 16.7%. However, the fundamentals and main controlling factors of the CO2 foam huff and puff process in the tight oil reservoirs are still not clear, and more work needs to be conducted to understand the potential field performance of such a process.
In this work, a series of experimental tests were conducted to analyze the foam stability, foam quality, and foam rheological properties, and then numerical simulation was used to model the effects of injection, soaking, and production times on the final oil recovery factor. The Taguchi method was finally conducted to optimize the performance of the CO2 foam huff and puff in the Cardium formation.
In the study, a commercial surfactant known as sodium dodecyl sulfate (SDS) (purity>99.0%) was used as the foaming agent. The rheological characteristics of CO2 foam were identified by the capillary tube experiment and the power-law model selected to represent its behavior. An illustration of the experimental setup is shown in Figure 1. CO2 gas and SDS solution mixed in the “foam generator” located in the inlet of the capillary tube. The pressure drop in the capillary tube can be carried out using the pressure transmitters installed in the inlet and outlet of the tube and then collected using a digital system. In our setup, the foam texture is visualized using a see-through window located in the outlet of the capillary tube. The foam quality, which can be controlled by the CO2/SDS solution ratio, was set to be variable in each run. In each experiment, the injection of SDS solution-CO2 gas continues to find the steady-state pressure drop along the capillary tube. The steady-state pressure drop was recorded to calculate the foam rheological properties, which were then used in the subsequent history matching processes.
The foam stability tests were conducted on a foam column apparatus at ambient temperature, and the concept of foam half-life was used as an indicator of foam enduring. The half-life is calculated by reading the initial foam height and stepwise measurement of foam height decline by time. The required time for the decay in foam height by 50% is recorded as its half-life. The foam stability test may have been subjected to error due to changes in environmental conditions such as temperature variation. To reduce the error in our data, the foam stability measurements were repeated three times, and the reported values on results are the arithmetic average of the listed values. After each stability test, the foaming equipment was carefully cleaned to remove any residuals.
The Cardium formation was discovered in the Western Canada Sedimentary Basin and has been important in Alberta since the discovery of oil in the Pembina area in 1953. The Cardium Formation was formed around 86 million years ago in primarily marginal and shallow marine settings during the late Cretaceous period. This formation is subdivided into two parts in the Pembina field: the Pembina River and the overlaying Cardium Zone. The lower Pembina River component is an offshore shale deposit. The upper Pembina River grades into sandier lithologies that were deposited on a shallow shelf and shoreface settings. Depth to formation top for the West Pembina assessment area ranges from 1,500 m in the northeast to 2,200 m in the southwest. The bulk of horizontal drilling in the Cardium Formation has occurred in the more restricted sections of the West Pembina assessment area.
The numerical model has a dimension of 2500 ft × 1200 ft × 100 ft, which is described by 50 × 30 × 10 grids in X, Y, and Z coordinates, respectively. There are eight hydraulic fracture treatments in the well with a half-length of 300 ft and a fracture spacing of 200 ft in between. The side view and top view of the reservoir model are shown in Figure 2. Figure 3 represents the phase diagram, and the relative permeability curves are described in Figure 4. Local grid refinement has been applied to better simulate fluid flow in the fractures. Reservoir simulations and sensitivity analyses were conducted to examine the performance of the CO2 foam huff and puff process and the effects of the main controlling variables. Local grid refinement has been applied to better simulate fluid flow in the fractures. Table 1 shows the simulation input data, and Table 2 represents the oil compositions.
FIGURE 4. Relative permeability curves for Cardium formation. (B) Gas-oil relative permeability. (A) Water-oil relative permeability.
The Taguchi method is a statistical approach for enhancing experimental result quality and has been successfully applied in many engineering fields (Karna and Sahai, 2012). This experimental design procedure adjusts the design parameters, while uncontrollable factors such as noise are canceled in this manner (Phadke, 1989). Table 3 shows the experimental design. In this work, the Taguchi method was used to effectively investigate the effects of the main variables on the performance of the CO2 foam huff and puff process, including the injection time, soaking time, production time, injection rate, and incremental injection rate.
The incremental injection rate was investigated in each cycle of some scenarios to increase the efficiency of the huff and puff process. As more cycles are conducted on a well, oil in the area close to the wellbore and fractures will be produced, leaving a void space growing from the wellbore and further into the formations. Such void space will then need to be filled by the injected CO2 in the next huff period. Hence, a fixed injection rate may not be sufficient after several cycles as it cannot cover the entire drainage area and sometimes cannot reach the undeveloped oil zone. So, the incremental injection rate ratio is proposed here to overcome this problem. For instance, an incremental injection rate ratio of 1.1 means that the first cycle injection rate is 10,000 scf/d, the second cycle is 11,000 scf/d, the third cycle is 12,100 scf/d, and so on.
Experiments have been conducted to examine the foam stability at various sodium dodecyl sulfonate (SDS) concentrations. Figure 5 shows an image of the CO2 foam generated using the sand pack-type foam generator in this study. The milky foam with fine bubbles has been observed, indicating that the foam generator can effectively produce CO2 when the SDS and CO2 are simultaneously injected into the generator. The half-life of foams with different SDS concentrations is presented in Figure 6. It can be seen that foam stability is significantly enhanced with the increase in SDS concentration until it reaches 0.2 wt%, after which the half-life of foam almost levels off. This is because the critical micelle concentration (CMC) of SDS in deionized water under room conditions is about 0.23 wt%, and the absorption of the surfactant on the interface is almost saturated when surfactant concentration increases up to the CMC (Afifi et al., 2021). There is no noticeable enhancement for foam stability when SDS concentration is higher than 0.2 wt%. As a result, 0.2 wt% is the optimal concentration of SDS for foam stability, and the foam rheological properties are also quantified at this concentration.
The volume of liquid drained out of foam versus time has been recorded to examine the foam decay. The drainage ratio is defined as the volume of drained liquid to the total liquid used to generate foam. A slow increase in the drainage ratio means that the liquid drains slowly out of the foam, indicating a stable foam system. As shown in Figure 7, liquid drains faster when the drainage ratio is less than 0.6, and a straight line can well fit the drainage ratio during this period. It demonstrates that foam decays at a constant rate before 60% of the liquid is drained out of foam. Then, the change in the drainage ratio is slow. In other words, the foam system decays fast at the initial stage but can sustain at a lower rate after 60% of the liquid has drained out of the foam.
The foam quality is a crucial parameter affecting the properties of CO2 foam. It is the ratio of CO2 volume to foam volume (i.e., CO2 + SDS solution). In general, when foam quality is between 52% and 96%, the gas bubbles are in contact with each other, and as a result, an increase in viscosity will occur (Belyadi et al., 2019). In field operations, the shear rates are generally high; thus, the rheological properties of the foam are determined at three different foam qualities of 50%, 75%, and 90% based on five injection rates of 1.2, 3.0, 6.0, 9.0, and 12.0 cm3/min corresponding to shear rates of 1091, 2728, 5,456, 8185, and 10,913 s−1, respectively.
CO2 foam is a typical non-Newtonian fluid system. The power-law model is adopted to describe the rheological properties of CO2 foam in this study.
where
As for fluid flow in the pipe, the pressure drop and wall shear stress can be described as follows:
The Newtonian wall shear rate can be determined using the flow rate and pipe diameter (Faroughi et al., 2018), as follows:
Correspondingly, the non-Newtonian wall shear rate can be quantified based on the Newtonian shear rate. The slope of the log–log plot of the flow curve (wall shear stress,
where Δp is pressure drop, Pa; D is the inner diameter of the pipe, m; L is the length of the pipe, m;
The Newtonian shear rate and apparent wall shear stress for CO2 foam with three different foam qualities are plotted in Figure 8. The correlations for the linear relation of log–log plots with high R-squared values have been obtained through regression. The flow index n for foam qualities of 50%, 75%, and 90% are 0.9784, 0.9768, and 1.7119, respectively. The plots for CO2 foam systems with foam quality of 50% and 75% are almost parallel, and the values of n are less than 1. Such CO2 foams are shear-thinning fluids. By contrast, the CO2 foam with a foam quality of 90% is a shear-thickening fluid because the flow index value is larger than 1. The values of K are 1.773 × 10–3, 3.336 × 10–3, and 2.065 × 10–3 for CO2 foams with foam qualities of 50%, 75%, and 90%, respectively. Consequently, the apparent CO2 foam with different foam qualities can be quantified using the power-law model. As shown in Figure 9, foam quality is a critical factor for the rheological properties of CO2 foam. The flow index values for CO2 foams with foam qualities of 50% and 75% are close to but less than 1. The apparent viscosities of these two foam systems are decreased slightly with the increase in the shear rate, that is, a shear-thinning behavior. Meanwhile, the apparent viscosity of CO2 foam with a foam quality of 90% increases with the increasing shear rate, that is, a shear-thickening behavior.
FIGURE 8. Newtonian shear rate and apparent wall shear stress for CO2 foam at different foam qualities.
The apparent viscosity of CO2 foam increases when the foam quality is increased from 50% to 75% due to the presence of a higher number of bubbles and regular interaction among the bubbles (Blauer et al., 1974). Nevertheless, the apparent viscosity is decreased when the foam quality is increased to 90%. That is mainly because the bubbles become denser, and thus the energy dissipation among these bubbles due to the collision and viscous friction decreases at high foam quality (Jing et al., 2017). In addition, the surfactant solution phase is transformed from the external phase into the internal phase when the CO2 proportion is significant for high foam quality, resulting in apparent viscosity reduction and weak stability (Luo et al., 2014).
Simulation runs were conducted based on the Taguchi theorem via a compositional reservoir simulator, and the final recoveries are recorded in Table 4. The impact of injection time was determined through a series of simulations by setting the injection time to 1, 3, 6, 9, and 12 months. In this regard, the minimum oil recovery was gained in the lowest injection time, and the highest oil recovery was achieved when injection time increased. However, the optimum huff time of 6 months and more extended foam injection can inversely affect the reservoir performance. In a 1-month injection, the volume of injected fluid is small and cannot cover all the drainage area. Hence, longer huff time provides enough EOR agents to contribute to reservoir depletion. On the other hand, only a certain amount of injected fluid would change oil PVT properties, and an extra injection of the foam would result in the occupation of reservoir pores with the useless fluid; thus, the oil relative permeability is reduced as a negative parameter. Figure 10 illustrates oil recovery comparison among different scenarios; as is obvious in the figure, the highest oil recovery was achieved in the case of 6-month injection, 3-month soaking, and 12-month production. The results showed that longer production is the key parameter to increase oil recovery, but longer soaking time is not guaranteed for more oil recovery. The lowest oil recovery is represented by the case of 1-month injection, 1-month soaking, and 1-month production.
FIGURE 10. Oil recovery comparison among different scenarios (run number 1, 6, 13, and 21 from Table 4).
Figure 11 demonstrates the influence of the main parameters on the oil recovery factor. The change in soaking time also has a considerable impact on the final amount of produced oil. The increase in soaking time from 1 to 3 months can raise the recovery factor by 6%, and the additional increase in soaking time has an inverse effect on the oil recovery. The injected gas reached the equilibrium state with the reservoir fluid at a particular time and added soaking times would not change oil viscosity and volume anymore. For a limited timeframe, extra waiting times equal shorter production time; accordingly, the oils that have enough potential to be produced would not produce appropriately due to lack of production time.
The puff process time was determined to have the most significant influence on the CO2 foam huff and puff, and the longer production times yielded higher oil recovery. In the CO2 foam huff and puff, the injection of the EOR agent has already increased reservoir pressure, and the reservoir fluids properties also have enhanced to some extent, based on the soaking time. Hence, the more productive time of the well increases the recovery factor. However, the reservoir performance shrinks after the 6 months of production owing to decreased reservoir pressure. The longer soaking time results in a shorter production time; thus, a lower amount of oil is produced and the reservoir pressure is maintained at higher levels. Increasing the injection rate would bring more foam to the reservoir, and the oil with a long distance from the injection well has a higher chance of getting in touch with the injected fluid and being positively altered for production. However, further increasing the injection rate would diverge oil from the well and reduce oil recovery after a specific rate. In this regard, the incremental injection rate in the subsequent huff processes has negligible oil recovery effects.
Affecting parameters on the recovery change were analyzed by the binary interaction plots. Based on the Pareto chart shown in Figure 12., it can be seen that the main affecting parameters of the CO2 foam huff and puff are determined to be production time and the synergic effects of soaking time and production time (BC), followed by the synergic effects of injection time and soaking time. The letters on the vertical axis in Figure describe the affecting parameters, and the two-lettered vertical axis shows the synergism between those parameters. However, the other four main parameters are less significant, which reveals that a huff and puff process cannot be optimized based on a single parameter, and their synergic effects should be considered. The optimum value of each parameter thus can be calculated through a set of optimization algorithms to obtain the best systematic performance.
A detailed view of the interactions is given in Figure 13. The interaction of soaking time and production time was ranked as the second influencing factor in our study. The results showed that the final recovery is a direct function of soaking time and production time, and the higher soaking times require more production times. In this case, the optimum recovery was obtained when the soaking time was 3 months and production time was maximized. For the low soak times, the increased injection time was favorable in recovering more oils. However, in the higher soaking times, the increased injection time can reduce project efficiency.
In this work, CO2 foam was first generated on the laboratory scale, and its stability and rheological properties were measured through several tests. Then the performance of huff and puff foam injection into tight oil reservoirs was investigated using a compositional model, which was optimized using the Taguchi method to reduce costs of computation. Outcomes showed the feasibility of this oil recovery method, and the combination of affecting parameters can be used to maximize the oil recovery. The final conclusions are as follows:
The foam stability increases with the increase in surfactant concentration, and then reaches a plateau after its CMC. The optimum surfactant concentration was measured to be 0.2 wt%. The foam rheological properties showed that in foam qualities of 50% and 75%, the generated foam acts as shear-thinning fluids, and the increase in foam quality changes its behavior to shear-thickening fluid.
The puff process time was determined to have the most significant influence on the CO2 foam huff and puff, and the longer production times yielded higher oil recovery.
The simulation results showed that the production time is the most significant factor followed by the soaking time and injection time. Simulation results also demonstrated that the injection rate and incremental injection rate ratio have lower impact on the final oil recovery. Further analysis showed that combination of soaking time–production time and soaking time–injection time have higher impact than individual soaking and injection time. Using the optimum parameters, huff and puff foam injection can return 13.61% more oil than the base case.
The raw data supporting the conclusion of this article will be made available by the authors, without undue reservation.
AS-A is a Postdoctoral Research Fellow at the University of Calgary, Canada under the supervision of SC. AS-A’s contribution is around 40%, SC’s is around 30%, and SZ’s is around 30%.
Author SZ was employed by the company Exceed Canada Oilfield Equipment.
The remaining authors declare that the research was conducted in the absence of any commercial or financial relationships that could be construed as a potential conflict of interest.
All claims expressed in this article are solely those of the authors and do not necessarily represent those of their affiliated organizations, or those of the publisher, the editors, and the reviewers. Any product that may be evaluated in this article, or claim that may be made by its manufacturer, is not guaranteed or endorsed by the publisher.
This research was undertaken thanks in part to funding from the University of Calgary and the Canada First Research Excellence Fund. The authors would also like to acknowledge the support received from the University of Calgary.
Afifi, H. R., Mohammadi, S., Derazi, A. M., Alemi, F. M., and Abad, K. F. H. (2021). A Comprehensive Review on Critical Affecting Parameters on Foam Stability and Recent Advancements for Foam-Based EOR Scenario. J. Mol. Liquids. doi:10.1016/j.molliq.2021.116808
Alyousef, Z. A., Almobarky, M. A., and Schechter, D. S. (2018). The Effect of Nanoparticle Aggregation on Surfactant Foam Stability. J. Colloid Interf. Sci. 511, 365–373. doi:10.1016/j.jcis.2017.09.051
Ayoub, M. A., Shabib-Asl, A., Abdellahizein, A. M., Elraies, K. A., and Bin MohdSaaid, I. (2015). Recovery Optimization of an Oil Reservoir by Water Flooding under Different Scenarios; a Simulation Approach. Rjaset 10, 357–372. doi:10.19026/rjaset.10.2499
Belyadi, H., Fathi, E., and Belyadi, F. (2019). Hydraulic Fracturing in Unconventional Reservoirs. Elsevier.
Blauer, R., Mitchell, B., and Kohlhaas, C. (1974). "Determination of Laminar, Turbulent, and Transitional Foam Flow Losses in Pipes", in: SPE California Regional Meeting: OnePetro).
Cronin, M., Emami-Meybodi, H., and Johns, R. (2019). “Multicomponent Diffusion Modeling of Cyclic Solvent Injection in Ultratight Reservoirs,” in SPE Annual Technical Conference and Exhibition (Calgary, Alberta, Canada: Society of Petroleum Engineers). doi:10.2118/196008-ms
Dianatnasab, F., Nikookar, M., Hosseini, S., and Sabeti, M. (2016). Study of Reservoir Properties and Operational Parameters Influencing in the Steam Assisted Gravity Drainage Process in Heavy Oil Reservoirs by Numerical Simulation. Petroleum 2, 236–251. doi:10.1016/j.petlm.2016.06.002
Farajzadeh, R., Eftekhari, A. A., Hajibeygi, H., Kahrobaei, S., Van Der Meer, J. M., Vincent-Bonnieu, S., et al. (2016). Simulation of Instabilities and Fingering in Surfactant Alternating Gas (SAG) Foam Enhanced Oil Recovery. J. Nat. Gas Sci. Eng. 34, 1191–1204. doi:10.1016/j.jngse.2016.08.008
Faroughi, S. A., Pruvot, A. J.-C. J., and Mcandrew, J. (2018). The Rheological Behavior of Energized Fluids and Foams with Application to Hydraulic Fracturing: Review. J. Pet. Sci. Eng. 163, 243–263. doi:10.1016/j.petrol.2017.12.051
Golabi, E., Azad, F. S., Ayatollahi, S. S., Hosseini, S. N., and Akhlaghi, N. (2012). “Experimental Study of Wettability Alteration of Limestone Rock from Oil-Wet to Water-Wet Using Various Surfactants,” in SPE Heavy Oil Conference Canada. SPE-157801-MS.()
Haskin, H. K., and Alston, R. B. (1989). An Evaluation of CO2 Huff 'n' Puff Tests in Texas. J. Pet. Tech. 41, 177–184. doi:10.2118/15502-pa
Hematpur, H., Mahmood, S., Akb, S., and Shabib-Asl, A. (2016). Foam Modeling Approaches in Enhanced Oil Recovery: A Review. Indian J. Sci. Tech. 9.
Hoffman, B. T., and Reichhardt, D. (2019). "Quantitative Evaluation of Recovery Mechanisms for Huff-N-Puff Gas Injection in Unconventional Reservoirs", in: SPE/AAPG/SEG Unconventional Resources Technology Conference, (D033S060R002).
Hosseini, S. N., Shuker, M. T., Hosseini, Z., Joao Tomocene, T., Shabib-Asl, A., and Sabet, M. (2015a). The Role of Salinity and Brine Ions in Interfacial Tension Reduction while Using Surfactant for Enhanced Oil Recovery. Rjaset 9, 722–726. doi:10.19026/rjaset.9.2617
Hosseini, S. N., Shuker, M. T., Sabet, M., Zamani, A., Hosseini, Z., and Shabib-Asl, A. (2015b). Brine Ions and Mechanism of Low Salinity Water Injection in Enhanced Oil Recovery: A Review. Rjaset 11, 1257–1264. doi:10.19026/rjaset.11.2233
Jing, Z., Feng, C., Wang, S., Xu, D., and Xu, G. (2017). Effect of Foam Quality on Flow Behavior of Liquid CO2-based Foam Fracturing Fluid Stabilized by Hydrofluoroether. J. Pet. Sci. Eng. 159, 710–716. doi:10.1016/j.petrol.2017.10.017
Kerr, E., Venepalli, K. K., Patel, K., Ambrose, R., and Erdle, J. (2020). “Use of Reservoir Simulation to Forecast Field EOR Response - an Eagle Ford Gas Injection Huff-N-Puff Application,” in SPE Hydraulic Fracturing Technology Conference and Exhibition (The Woodlands, Texas, USA: Society of Petroleum Engineers). doi:10.2118/199722-ms
Khan, M. Y., and Mandal, A. (2021). Improvement of Buckley-Leverett Equation and its Solution for Gas Displacement with Viscous Fingering and Gravity Effects at Constant Pressure for Inclined Stratified Heterogeneous Reservoir. Fuel 285, 119172. doi:10.1016/j.fuel.2020.119172
Kovscek, A. R., and Bertin, H. J. (2003). Foam Mobility in Heterogeneous Porous media. Transport in porous media 52, 17–35. doi:10.1023/a:1022312225868
Li, L., and Sheng, J. J. (2017). Numerical Analysis of Cyclic CH4 Injection in Liquid-Rich Shale Reservoirs Based on the Experiments Using Different-Diameter Shale Cores and Crude Oil. J. Nat. Gas Sci. Eng. 39, 1–14. doi:10.1016/j.jngse.2017.01.017
Li, R. F., Yan, W., Liu, S., Hirasaki, G. J., and Miller, C. A. (2010). Foam Mobility Control for Surfactant Enhanced Oil Recovery. SPE J. 15, 928–942. doi:10.2118/113910-pa
Luo, X., Wang, S., Wang, Z., Jing, Z., and Lv, M. (2014). Experimental Research on Rheological Properties and Proppant Transport Performance of GRF-CO2 Fracturing Fluid. J. Pet. Sci. Eng. 120, 154–162. doi:10.1016/j.petrol.2014.06.009
Meng, X., and Sheng, J. J. (2016). Optimization of Huff-N-Puff Gas Injection in a Shale Gas Condensate Reservoir. J. Unconventional Oil Gas Resour. 16, 34–44. doi:10.1016/j.juogr.2016.09.003
Monger, T. G., and Coma, J. M. (1988). A Laboratory and Field Evaluation of the CO2 Huff 'n' Puff Process for Light-Oil Recovery. SPE Reservoir Eng. 3, 1168–1176. doi:10.2118/15501-pa
Monger, T. G., Ramos, J. C., and Thomas, J. (1991). Light Oil Recovery from Cyclic CO2 Injection: Influence of Low Pressures Impure CO2, and Reservoir Gas. SPE Reservoir Eng. 6, 25–32. doi:10.2118/18084-pa
Moortgat, J. (2016). Viscous and Gravitational Fingering in Multiphase Compositional and Compressible Flow. Adv. Water Resour. 89, 53–66. doi:10.1016/j.advwatres.2016.01.002
Navarro-Brull, F. J., and Gómez, R. (2018). Modeling Pore-Scale Two-phase Flow: How to Avoid Gas-Channeling Phenomena in Micropacked-Bed Reactors via Catalyst Wettability Modification. Ind. Eng. Chem. Res. 57, 84–92. doi:10.1021/acs.iecr.7b02493
Phukan, R., Gogoi, S. B., and Tiwari, P. (2020). Effects of CO2-foam Stability, Interfacial Tension and Surfactant Adsorption on Oil Recovery by alkaline-surfactant-alternated-gas/CO2 Flooding. Colloids Surf. A: Physicochemical Eng. Aspects 597, 124799. doi:10.1016/j.colsurfa.2020.124799
Rafati, R., Haddad, A. S., and Hamidi, H. (2016). Experimental Study on Stability and Rheological Properties of Aqueous Foam in the Presence of Reservoir Natural Solid Particles. Colloids Surf. A: Physicochemical Eng. Aspects 509, 19–31. doi:10.1016/j.colsurfa.2016.08.087
Rahmanifard, H., Helalizadeh, A., Ebrahimi, M., Shabibasl, A. M., and Mayahi, N. (2014). Field Scale and Economical Analysis of Carbon Dioxide, Nitrogen, and Lean Gas Injection Scenarios in Pazanan Gas Condensate Reservoir. Ijpe 1, 62–91. doi:10.1504/ijpe.2014.059422
Sabet, M., Hosseini, S. N., Zamani, A., Hosseini, Z., and Soleimani, H. (2016). Application of Nanotechnology for Enhanced Oil Recovery: A Review. Ddf 367, 149–156. doi:10.4028/www.scientific.net/ddf.367.149
Sanchez-Rivera, D., Mohanty, K., and Balhoff, M. (2015). Reservoir Simulation and Optimization of Huff-And-Puff Operations in the Bakken Shale. Fuel 147, 82–94. doi:10.1016/j.fuel.2014.12.062
Santiago, C. J., and Kantzas, A. (2020). “Investigation of Cyclic Gas Injection in the Gas Condensate Window of Unconventional Reservoirs,” in SPE Canada Unconventional Resources Conference. D043S008R005.
Sayegh, S. G., and Maini, B. B. (1984). Laboratory Evaluation of the Co2 Huff-N-Puff Process for Heavy Oil Reservoirs. J. Can. Pet. Tech. 23, 29–36. doi:10.2118/84-03-02
Shabib-Asl, A., Abdalla Ayoub, M., and Abdalla Elraies, K. (2019a). “Combined Low Salinity Water Injection and Foam Flooding in sandstone Reservoir Rock: A New Hybrid EOR: A New Hybrid EOR,” in SPE Middle East Oil and Gas Show and Conference: OnePetro.
Shabib-Asl, A., Ayoub, M. A., and Elraies, K. A. (2019b). A New Hybrid Technique Using Low Salinity Water Injection and Foam Flooding for Enhanced Oil Recovery in sandstone Rock. J. Pet. Sci. Eng. 174, 716–728. doi:10.1016/j.petrol.2018.11.035
Shabib-Asl, A., Ayoub, M. A., Saaid, I. M., and Valentim, P. P. J. (2015b). Experimental Investigation into Effects of Crude Oil Acid and Base Number on Wettability Alteration by Using Different Low Salinity Water in sandstone Rock. J. Jpn. Petrol. Inst. 58, 228–236. doi:10.1627/jpi.58.228
Shabib-Asl, A., Ayoub, M., and Elraies, K. (2015a). “Laboratory Investigation into Wettability Alteration by Different Low Salinity Water Compositions in sandstone Rock,” in SPE/IATMI Asia Pacific Oil & Gas Conference and Exhibition: OnePetro.
Shabib-Asl, A., Mohammed, M. a. A., Kermanioryani, M., and Valentim, P. P. J. (2014). Effects of Low Salinity Water Ion Composition on Wettability Alteration in sandstone Reservoir Rock: a Laboratory Investigation. J. Nat. Sci. Res. 4, 34–41.
Shabib-Asl, A., Plaksina, T., and Moradi, B. (2020). Evaluation of Nanopore Confinement during CO2 Huff and Puff Process in Liquid-Rich Shale Formations. Comput. Geosciences, 1–16. doi:10.1007/s10596-019-09932-6
Shabib-Asl, A., and Plaksina, T. (2019). Selection of Decline Curve Analysis Model Using Akaike Information Criterion for Unconventional Reservoirs. J. Pet. Sci. Eng. 182, 106327. doi:10.1016/j.petrol.2019.106327
Shayegi, S., Jin, Z., Schenewerk, P., and Wolcott, J. (1996). “Improved Cyclic Stimulation Using Gas Mixtures,” in SPE Annual Technical Conference and Exhibition (Denver, Colorado: Society of Petroleum Engineers). doi:10.2118/36687-ms
Song, C., and Yang, D. (2013). “Performance Evaluation of CO2 Huff-N-Puff Processes in Tight Oil Formations,” in SPE Unconventional Resources Conference Canada: OnePetro.
Sun, J., Zou, A., Sotelo, E., and Schechter, D. (2016). Numerical Simulation of CO2 Huff-N-Puff in Complex Fracture Networks of Unconventional Liquid Reservoirs. J. Nat. Gas Sci. Eng. 31, 481–492. doi:10.1016/j.jngse.2016.03.032
Wan, T., Wang, W., Jiang, J., and Zhang, Y. (2018). Pore-scale Analysis of Gas Huff-N-Puff Enhanced Oil Recovery and Waterflooding Process. Fuel 215, 561–571. doi:10.1016/j.fuel.2017.11.033
Wan, T., Yu, Y., and Sheng, J. J. (2015). Experimental and Numerical Study of the EOR Potential in Liquid-Rich Shales by Cyclic Gas Injection. J. Unconventional Oil Gas Resour. 12, 56–67. doi:10.1016/j.juogr.2015.08.004
Wang, H., Ma, F., Tong, X., Liu, Z., Zhang, X., Wu, Z., et al. (2016). Assessment of Global Unconventional Oil and Gas Resources. Pet. Exploration Dev. 43, 925–940. doi:10.1016/s1876-3804(16)30111-2
Wang, Z., Ma, J., Gao, R., Zeng, F., Huang, C., Tontiwachwuthikul, P., et al. (2013). “Optimizing Cyclic CO2 Injection for Low- Permeability Oil Reservoirs through Experimental Study,” in SPE Unconventional Resources Conference Canada (Calgary, Alberta, Canada: Society of Petroleum Engineers).
Xu, X., Saeedi, A., and Liu, K. (2017). An Experimental Study of Combined Foam/surfactant Polymer (SP) Flooding for Carbone Dioxide-Enhanced Oil Recovery (CO2-EOR). J. Pet. Sci. Eng. 149, 603–611. doi:10.1016/j.petrol.2016.11.022
Yang, J., and Hou, J. (2020). Experimental Study on Gas Channeling Characteristics of Nitrogen and Foam Flooding in 2-D Visualized Fractured-Vuggy Model. J. Pet. Sci. Eng. 192, 107334. doi:10.1016/j.petrol.2020.107334
Yekeen, N., Idris, A. K., Manan, M. A., and Samin, A. M. (2017). Experimental Study of the Influence of Silica Nanoparticles on the Bulk Stability of SDS-Foam in the Presence of Oil. J. Dispersion Sci. Tech. 38, 416–424. doi:10.1080/01932691.2016.1172969
Yu, J., An, C., Mo, D., Liu, N., and Lee, R. (2012). “Foam Mobility Control for Nanoparticle-Stabilized CO2 Foam,” in SPE Improved Oil Recovery Symposium. OnePetro.
Yu, W., Lashgari, H., and Sepehrnoori, K. (2014). “Simulation Study of CO2 Huff-N-Puff Process in Bakken Tight Oil Reservoirs,” in SPE Western North American and Rocky Mountain Joint Meeting: OnePetro.
Yu, Y., Li, L., and Sheng, J. J. (2016). “Further Discuss the Roles of Soaking Time and Pressure Depletion Rate in Gas Huff-N-Puff Process in Fractured Liquid-Rich Shale Reservoirs,” in SPE Annual Technical Conference and Exhibition (Dubai: UAE: Society of Petroleum Engineers).
Zaker, S., Parvizi, R., Hosseini, S., and Ghaseminejad, E. (2020). Crude Oil Behavior during Injection of Solutions Containing MgSO4 in the Presence and Absence of CO2. Energy Sourc. A: Recovery, Utilization, Environ. Effects, 1–18. doi:10.1080/15567036.2020.1783397
Zhang, Y. P., Sayegh, S. G., Huang, S., and Dong, M. (2004). “Laboratory Investigation of Enhanced Light-Oil Recovery by CO/Flue Gas Huff-N-Puff Process,” in Canadian International Petroleum Conference (Calgary, Alberta: Petroleum Society of Canada). doi:10.2118/2004-021
Zhang, Y., Yu, W., Li, Z., and Sepehrnoori, K. (2018). Simulation Study of Factors Affecting CO2 Huff-N-Puff Process in Tight Oil Reservoirs. J. Pet. Sci. Eng. 163, 264–269. doi:10.1016/j.petrol.2017.12.075
Zhao, F., Wang, P., Huang, S., Hao, H., Zhang, M., and Lu, G. (2020). Performance and Applicable Limits of Multi-Stage Gas Channeling Control System for CO2 Flooding in Ultra-low Permeability Reservoirs. J. Pet. Sci. Eng. 192, 107336. doi:10.1016/j.petrol.2020.107336
Zhao, G., Dai, C., Zhang, Y., Chen, A., Yan, Z., and Zhao, M. (2015). Enhanced Foam Stability by Adding Comb Polymer Gel for In-Depth Profile Control in High Temperature Reservoirs. Colloids Surf. A: Physicochemical Eng. Aspects 482, 115–124. doi:10.1016/j.colsurfa.2015.04.041
Keywords: hydraulic fracturing, huff and puff, Cardium, CO2 Foam, soaking
Citation: Shabib-Asl A, Chen S( and Zheng S (2022) Performance of CO2 Foam Huff and Puff in Tight Oil Reservoirs. Front. Energy Res. 10:826469. doi: 10.3389/fenrg.2022.826469
Received: 10 December 2021; Accepted: 05 January 2022;
Published: 02 March 2022.
Edited by:
Kaiqiang Zhang, Imperial College London, United KingdomReviewed by:
Yuting Lv, Shandong University of Science and Technology, ChinaCopyright © 2022 Shabib-Asl, Chen and Zheng. This is an open-access article distributed under the terms of the Creative Commons Attribution License (CC BY). The use, distribution or reproduction in other forums is permitted, provided the original author(s) and the copyright owner(s) are credited and that the original publication in this journal is cited, in accordance with accepted academic practice. No use, distribution or reproduction is permitted which does not comply with these terms.
*Correspondence: Shengnan (Nancy) Chen, c25jaGVuQHVjYWxnYXJ5LmNh
Disclaimer: All claims expressed in this article are solely those of the authors and do not necessarily represent those of their affiliated organizations, or those of the publisher, the editors and the reviewers. Any product that may be evaluated in this article or claim that may be made by its manufacturer is not guaranteed or endorsed by the publisher.
Research integrity at Frontiers
Learn more about the work of our research integrity team to safeguard the quality of each article we publish.