- 1Guangdong Key Laboratory of Battery Safety, Guangzhou Institute of Energy Testing, Guangzhou, China
- 2School of Materials and Energy, Guangdong University of Technology, Guangzhou, China
This study aims toward the application of composite phase-change material (CPCM) in electric vehicles, which suffers from leakage, high rigidity, and low thermal conductivity. In this study, a novel flexible composite phase-change material (CPCM) with high thermal conductivity and low leakage has been proposed, presented, and utilized in a battery module. Among these, polyethylene glycol (PEG), as a phase-change component, styrene–butadiene–styrene (SBS) as support material, and ethylene–propylene–diene monomer (EPDM) as assisted packaging material could greatly enhance the flexibility and deformability of CPCM. Besides, boron nitride (BN) was adopted to enhance the heat-dissipating capacity and reduce the temperature difference in the module. In addition, compared with other cooling methods, the battery module with compact and efficient advantages are analyzed at different discharge rates. The results revealed that the flexible CPCM was controlled below 44.8°C, and the temperature difference was maintained within 5.6°C at 3C discharge rate. Even during the charge–discharge cycles, it displayed lower temperature fluctuation within the acceptable range. These outstanding shape recovery and antileakage performances of BN-based flexible CPCM would provide insights into battery modules with desirable assembly methods and process flexibility.
Introduction
In order to alleviate the environment and energy crisis, electric vehicles (EVs) and hybrid electric vehicles (HEVs) have attracted much attention in recent years. Lithium batteries, with their high energy density and without memory effect, have been widely utilized in EVs and HEVs. Nevertheless, a Li-ion battery displays much sensitivity to temperature, which would greatly affect the delivered capacity and power capability. Besides, battery failure could cause thermal hazard, and the thermal safety problem of battery module becomes the focus of the public (Nanthagopal et al., 2020; Turksoy et al., 2020; Zhao et al., 2021). Therefore, many investigators have concentrated on exploring various battery thermal management (BTM) systems to control the temperature and temperature difference (ΔT) of the power battery modules (Qin et al., 2021; Wang et al., 2021; Zhuang et al., 2021).
Among the different BTM technologies, the phase-change material (PCM) cooling method has many advantages, such as simple installation, temperature homogenizing capability, and outstanding cooling effect, become an efficient cooling solution for a battery module (Chen et al., 2020; Ding et al., 2020), which cannot only absorb and release large amounts of latent heat during the phase-transition process but also without additional energy consumption and equipment in the application of battery module (Safdari et al., 2020; Xiao et al., 2021).
There are some organic solid–liquid PCMs utilized in various areas owing to higher latent heat, crystalline materials, such as paraffins (Wu et al., 2015), poly(ethylene glycol) (PEG) (Sundararajan et al., 2017), fatty acids (Yuan et al., 2014; Luan et al., 2016; Sang et al., 2019), and fatty alcohol (Atinafu et al., 2018). Among these, PEG has many advantages, such as easy preparation, low cost, and high latent, which had been utilized in buildings, solar energy storage, and temperature-conditioning system fields. Besides, it could be applied in the BTM system. The main reason is that the appropriate temperature range and thermal performance of PEG can be obtained by regulating the size of molecular weight. Nevertheless, some drawbacks to restrict the PEG application range still existed, such as inferior dissipating heat capacity, easy leakage, and strong rigidity, especially when utilized in EVs and HEVs.
In order to overcome these serious problems, it is very necessary to explore the composite PCM with excellent flexibility and thermal properties, which could be applied in many thermal storage fields. PEG can be compounded with polymers, such as polyurethane (Tang et al., 2016) and epoxy (Lu et al., 2019) and polyethylene, which would not only exhibit a higher melting temperature but also sustain the stability during the phase-change process, so as to avoid the leakage of PCMs efficiently. Wang et al. (2017) introduced the PCMs supporting large-scale manufacture of 3D porous structures, which could be applied in the CNC hydrogel based on UV-induced click chemistry. Uemura et al. (2010) proposed the porous coordination polymers combined with PEG to improve the effect on the energy storage and phase-change temperatures. Ling Zhou et al. (2020) investigated the cross-linked polymer as a supporting material to be combined with PEG as templates. The result revealed that the self-template method has a higher PEG loading value. Nevertheless, the CPCM with traditional materials still exhibited a relatively high rigidity and fracture easily under external force conditions. Thus, it is very essential to explore a form-stable CPCM with good elastic flexibility.
In surveying the literature, the styrene–butadiene–styrene (SBS) polymer with a thermoplastic elastic supporting skeleton can improve the flexible CPCM performance, which could build three-dimensional network structures with polybutadiene segments, thus, decreasing the volume change in CPCM. Li et al. (2019) prepared petroleum asphalt with an SBS composite material to improve the wider temperature range so as to resist the fatigue crack. Chriaa et al. (2020) investigated a shape-stabilized PCM based on hexadecane/LDPE/SEBS, which could be beneficial in strengthening the stability of deformation. Our group had investigated the SBS@PA/EG that exhibited an obviously flexible performance and is utilized in a battery module to regulate the temperature distribution. However, it is still needed to improve the elastic and antileakage performances of the SBS-based CPCM. Considering that the ethylene propylene diene monomer rubber (EPDM) blends with the hard segment composed of a crystalline zone and a soft segment, which can form an amorphous zone, it can display good flexibility and high resilience at room temperature, which had been applied in the rubber industry to enhance the flexibility and aging resistance performance (Huang et al., 2021). Considering these optimum properties, it has the potential possibility to improve the mechanical properties of CPCM. Recently, there are many researchers that have already focused on battery thermal management system with flexible phase-change materials. Huang et al. (2020) had prepared SBS@PA@AlN flexible CPCM, which exhibited an excellent flexibility and could be easily bent to 180° at 70°C. Zhang et al. (2021) had proposed a SR@PW@EG@BN flexible CPCM battery thermal management system, which could not only control the temperature of the battery but also exhibit an excellent impact buffer capacity. Wu et al. (2022) presented a flexible phase-change material with polyether soft chain segments as the support material, which achieved good flexibility at low temperature and exhibited excellent thermal management effect. However, in order to satisfy the dissipating heat efficiency requirements of CPCM in EVs and HEVs, the thermal conductivity still needs to be improved further.
Although the CPCM with EG (Tian et al., 2016; Dongyi Zhou et al., 2020), carbon fiber (Gao et al., 2020), and metal (Drissi et al., 2019; Gulfam et al., 2019) has been widely applied in EVs and energy storage fields, due to their thermal conductivity and absorbability properties, it only focused on strengthening the heat transferring capacity. Whereas the chemical stability of CPCM could be directly affected by the thermal safety performance of the battery module, it was always neglected in the application. Boron nitride (BN) is become a promising material to obtain these objects because it has excellent insulation performance and high thermal conductivity. Yang et al. (2017) prepared a CPCM of PEG, graphene nanosheets, and BN. It has excellent light absorption ability while maintaining a high latent heat of 133.5 J/g. Jia et al. (2020) prepared a chitosan-coated PEG composite phase-change material, which was able to increase its thermal conductivity to 2.77 W/m·K with the addition of BN, and also had a latent heat of 136 J/g. To sum up, there are numerous investigators that have just concentrated on optimizing the various performances of CPCM. A few researchers deeply analyzed the requirements of CPCM, applying them in the large-format lithium-ion battery modules. Herein, a novel flexible CPCM, with different mass fractions of BN as thermal conductive addition mixed with EPDM and SBS, has been proposed. The SBS and EPDM could strengthen the mechanism performance with a synergistic effect. Besides, there are various parameters in CPCM, such as thermal conductivity, thermal stability, and mechanical strength, that needs to be analyzed. In addition, the 25 ternary batteries that were assembled in a battery module with various BTM systems were discussed. Compared with air cooling and rigid CPCM-based thermal management approaches, the battery module with flexible CPCM and the thermal management effect during the long cycles at different discharge rates were was further investigated.
Experimental Section
Materials
SBS with excellent bending and stretching properties, which plays the role of a supporting material, was purchased from Guangzhou Yongzheng Chemical Co., Ltd. EPDM (Anhui Lixin Rubber Technology Co., Ltd.), as a cross-linking agent, can play a role in improving the flexibility of composite phase-change materials. PEG2000 with a melting point of 46°C was purchased from Jiangsu Haian Petrochemical Plant. Hexagonal boron nitride, with a thermal conductivity of 33 W/m·K, was obtained from Liaoning Borda Technology Co.
Preparation
In order to investigate the effects of EPDM and BN on the mechanical and thermomechanical properties of the composite phase-change materials, different mass ratios of EPDM and BN were added to the samples, as shown in Table 1. The composite phase-change materials were prepared by the solvent volatilization method, which is not only simple but also has a low-energy consumption compared with the conventional melt blending method. The details of the preparation process of CPCM are shown in Figure 1. In addition, different proportions of BN in the composite were defined using SPEB1, SPEB3, SPEB5, SPEB7, and SPEB9, corresponding to 1%, 3%, 5%, 7%, and 9% of BN in the CPCM, respectively.
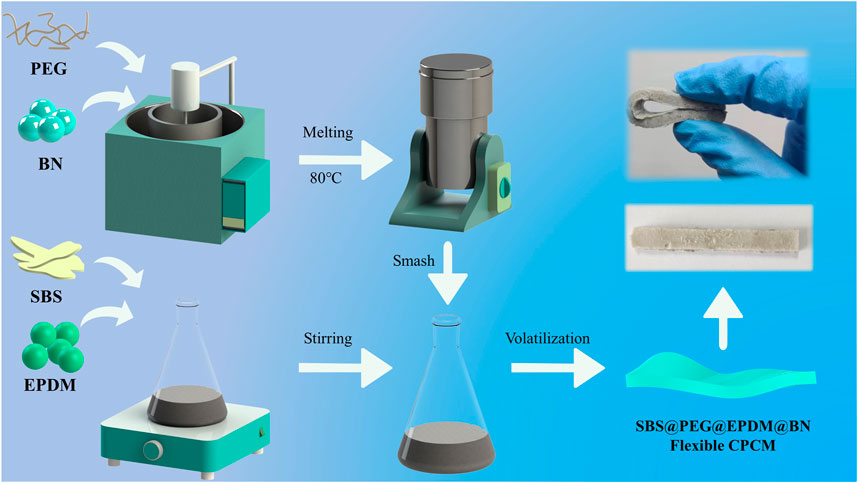
FIGURE 1. The preparation process of SBS@PEG@EPDM@BN flexible composite phase-change material (CPCM).
Figure 1 shows the specific preparation method of the CPCM. The preparation method of CPCM is solvent volatilization, which is simpler and less energy intensive than the traditional melt blending method for preparing phase-change materials.
The preparation process of CPCM is divided into five steps. First, PEG and BN are poured into an oil bath at 80°C and heated, and then stirred for 30 min using a stirrer after complete melting. In the second step, the liquid mixture of PEG and BN was solidified at room temperature and smashed into powder form by a pulverizer. Then the solid SBS and EPDM were dissolved into a gel-like mixture of SBS and EPDM with the aid of a magnetic stirrer using a CCl4 solvent. Subsequently, the PEG and BN mixture powder was mixed with the gel-like SBS and EPDM mixture, and poured into a mold. It is worth mentioning that during the mixing process of PEG and BN powders with SBS and EPDM gel-like blends, it is necessary to reduce the pore space inside the material by repeated extrusion. Finally, while waiting for the CCl4 solvent in the SBS@PEG@EPDM@BN material to volatilize completely at room temperature, the flexible CPCM was prepared.
The Characterizations of Different samples
The Microstructure Analysis and Chemical Characterization
Fourier transform infrared spectroscopy (FT-IR, Bruker Tensor-27) was utilized to characterize the different samples, which ranged from 500 to 4,000 cm−1 at 2 cm−1 resolutions with a KBr disk.
Besides, the X-ray diffractometer (Rigaku D/max-2550) using Cu Kα radiation (0.154056 nm) was applied to test the chemical structures. The 2θ range of the XRD is from 10 to 80° with a scanning speed of 10°/min.
The Morphology and the Mechanical Characterization
The samples of various CPCMs were described through the SEM (Hitachi S-3400 N, Japan), which was under the condition of 20-kV accelerating voltage. The mechanical strength was described with bending and tensile strength. The measurement samples were fabricated as long strips with a size of 12 * 6 * 2 mm and were tested with a universal tension machine (CTM8000 Xie Qiang Instrument Manufacturing Co., Ltd., China).
The digital display thermostat heating platform (GermayHeater STC803-II, China) and electronic balance (SheYanYiQi JA1003, China, accuracy is 0.001 g) were utilized to measure the shape stability of CPCM. The Qn each hour using the electronic balance was adopted to evaluate the quality of the different samples.
Different 30 mm diameter circular samples were heated on a digital display heating platform at 50°C for 7 h. The quality of samples was recorded as Qn each hour using an electronic balance. The quality maintenance rate (R) could be calculated by Formula 1. Q0 indicates the initial quality of samples in Formula. 1.
Thermodynamic Characterization
The differential scanning calorimeter (DSC, Q20, TA Instruments Inc.) was characterized by the latent heat of CPCM. Every sample weighing 5 mg was heated from 20°C to 80°C, which was under the condition of nitrogen atmosphere at a rate of 5°C/min. Through discussion of the heat flow versus time curves among these samples, the corresponding latent heat values were measured. Besides, various CPCM samples were prepared to smoothen the circular blocks to test the corresponding thermal conductivity with the hot-disk thermal conductivity meter.
Battery Thermal Management System Evaluation
In order to investigate the cooling effect of CPCM-based thermal management for a battery module, as seen in Figure 2, serials of charge/discharge temperature measurement experiments were set up. The battery modules under the 26°C thermostat (CK408G, Dongguan Qinzhuo Environmental Test Co., Ltd., China) were built, which were tested with an equipment (BTS-4000, Shenzhen NEWARE Co., Ltd., China) during the charge and discharge process. In order to evaluate the temperatures of the battery module in this process, some special position batteries were connected to the temperature collector by thermocouples (OMEGA type, accuracy of ±0.1°C, Tqidec Co., Ltd., China). The measuring equipment and temperature collector measured the dates and were recorded in the corresponding test system of the computer.
Results and Discussion
Chemical Characterization
The crystal structures of different materials were characterized by XRD. Figure 3A shows the XRD curves of SPEB7, SPE4, SP, PEG, and BN. The XRD curves of the three CPCMs of SPEB7, SPE4, and SP display two sharp derived peaks at 2θ of 19.32° and 23.56°, which are the characteristic peaks of PEG. In addition, toward the XRD curve of SPEB7, there are also derivative peaks at 2θ of 28.96°, 36.58°, and 60.88°. They could be ascribed to the 7% BN addition. Besides, it can be clearly observed that the intensity of the characteristic peaks of PEG at 2θ of 19.32° and 23.56° are significantly higher than the intensity of the derived peaks of SP, SPE4, and SPEB7. The main reason was that PEG content in the three CPCMs is a considerable limitation, respectively. Besides, the SBS, EPDM, and BN in the CPCM restricted the crystallization of PEG. In addition, compared with the XRD curves of SPEB7 and BN, it could be observed that no new derivative peaks appeared, which indicates that the BN added into CPCM could not bring about extra chemical reactions.
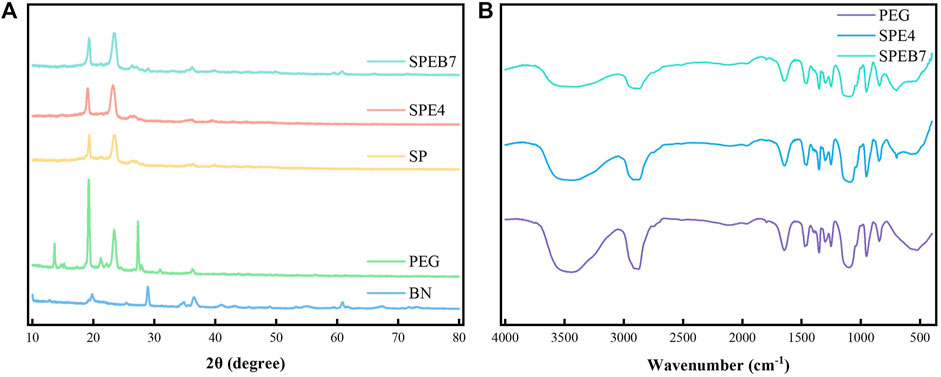
FIGURE 3. (A) XRD curves of the different samples. (B) Fourier transform infrared spectroscopy (FT-IR) spectra of the different samples.
The chemical structures of the different samples were characterized by FT-IR spectroscopy. Figure 3B shows the comparison of FT-IR spectra among PEG, SPE4, and SPEB7 samples. The maximum absorption peaks at 3,447, 2,921, 1,101, and 950 cm−1 correspond to hydroxyl (–OH) stretching, alkyl (–CH2) stretching, –C–O–C– symmetric stretching, and crystal peaks, respectively. As for the FT-IR spectrums of SPE4 and SPEB7, the corresponding absorption peaks with PEG is at 698 cm−1, which is caused by the –CH vibration in EPDM. In addition, compared with the FT-IR spectra of SPE4 and SPEB7, it reveals that no absorption peaks were generated or flattened after the addition of BN to the CPCM. It could also be demonstrated that there is only physical mixing between BN and CPCM. No chemical reaction was produced during the synthesis process of CPCM.
Micromorphology Analysis
In order to analyze the CPCM from the microscopic perspective, the morphology of the different samples was characterized by SEM. As shown in Figure 4A, the PEG displays a compact long strip shape. As shown in Figure 4B, the pure SBS exhibits a smooth and continuous morphology, but it lacks sufficient cross-linking points among the CPCM. The SEM images of EPDM and BN are shown in Supplementary Figure S1, which shows that EPDM has a rough and irregular surface. As displayed in Figure 4C, when EPDM was added into the PEG/SBS, a distinct cross-linked network could be built among the composite materials, which exhibits excellent elastic performance. In sample SPEB7, the three-dimensional cross-linked structures of EPDM and SBS can be beneficial in improving the encapsulation of PEG and granular BN with synergistic effect. Besides, it could be observed that the BN can distribute uniformly in the composite material, which can greatly improve the thermal conductivity of CPCM. Therefore, it should be concluded that the three-dimensional cross-linked structures can support CPCM with deformation stress, so as to strengthen the bending strength and tensile strength of the CPCM performances.
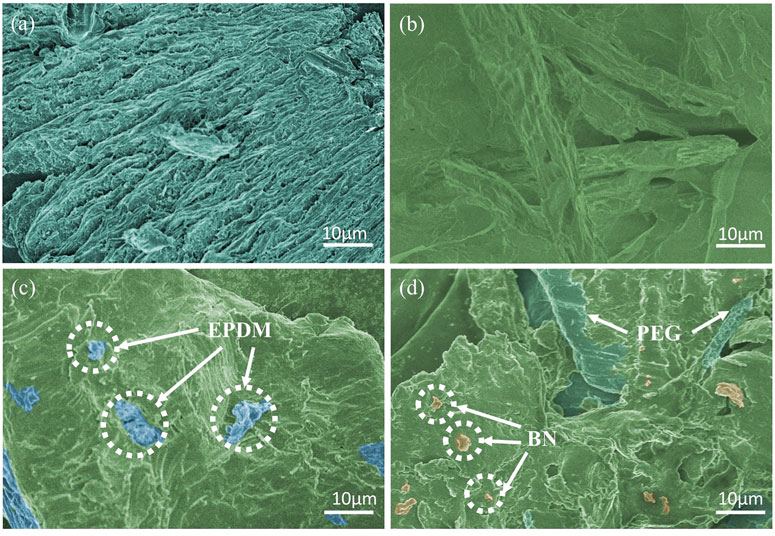
FIGURE 4. SEM images of (A) polyethylene glycol (PEG), (B) styrene–butadiene–styrene (SBS), (C) SPE4, and (D) SPEB7.
Shape Stability and Mechanism Performance
In order to investigate the flexible performance of the different CPCMs, twist tests were carried out in the samples, such as PEG, SP, SPE4 and SPEB7, as shown in Figure 5A. It can be observed that PEG is a rigid material, which could not be twisted under external force conditions. On the basis of the experiment results, the SP is slightly twisted under external force owing to the SBS wrapping. Besides, SPE4 with EPDM added is able to be twisted by 540° under external force, which is more significant than that of SP. The results indicate that EPDM can greatly improve the flexible performance of SBS-coated PEG materials. In addition, after adding the SBS/EPDM/PEG with 7% BN, it could be observed that the flexible performance was able to be twisted by 1,080° under a similar external force condition.
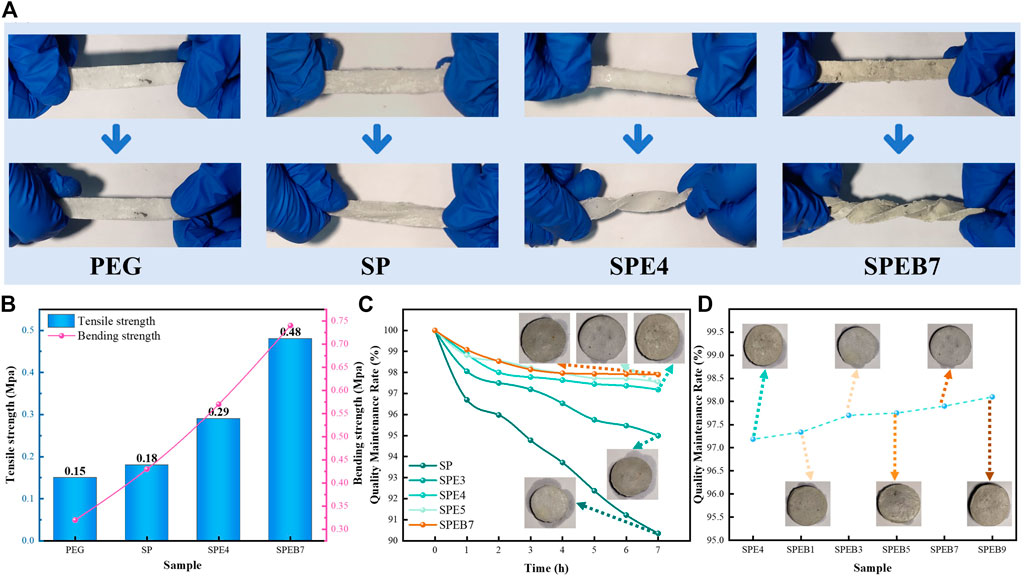
FIGURE 5. (A) Twist test results of the different samples. (B) Tensile strength and bending strength curves of the different samples. (C) The quality maintenance rate curves of the different samples. (D) The quality maintenance rate curves of the different samples with boron nitride (BN).
To illustrate the mechanical characterization of the different samples clearly, the bending and tensile strength among PEG, SP, SPE4, and SPEB7are analyzed, and the results are shown in Figure 5B. It can be observed that the tensile strength of the samples increased from 0.15 to 0.48 Mpa. It is concluded that the SBS/EPDM exerted a positive effect to improve the mechanism effect, which formed a tight three-dimensional structure to restrict the PEG to fracture. In Supplementary Figure S2, when the BN proportion in CPCM surpassed 7%, the bending strength had a decreasing tendency. It was observed that the flexible property of PSEB decreased as the BN correspondingly increased. The excessive BN affected the continuity of the SBS among the composite material, which could cause the decreasing flexibility of CPCM.
Besides, the quality maintenance of CPCM could directly affect the servicing lifespan of CPCM, especially utilized in the battery module. If the CPCM incurred severe liquid leakage, it would decrease the enthalpy of CPCM and seriously affect the safety of the battery module. The quality maintenance rate curves of thte different samples, as shown in Figure 5C, could indicate that the EPDM and SBS could be beneficial in improving quality maintenance. The main reason was that the EPDM with three-dimensional cross-link assisted SBS to prevent PEG leakage.
In further analyzing the influence of BN on the composite material, as shown in Figure 5D, it could be obtained that the quality maintenance rates among SPEB9 are from 97.2% to 98.1%, so it can be concluded that BN played a little effect on the leakage of CPCM. In order to visually describe the shape stability of different shapes, the samples on the filter paper were photographed to analyze the wetting range of various samples. When the various BNs were added to the CPCM, the shape stability almost remained invariable.
In addition, the thermal conductivity is very important as it affects the rate of heat storage release and absorption during the phase-change process, especially in the battery module. Figure 6C exhibits the thermal conductivity of various samples with the mass ratio of BN. The thermal conductivity of CPCM without BN is only 0.21 W/m·K. By adding different proportions of BN in CPCM, the thermal conductivity of SPEB1, SPEB3, SPEB5, SPEB7, and SPEB9 are 0.37, 0.56, 0.69, 0.77, and 0.83 W/m·K, respectively. Nevertheless, the increase in the value of thermal conductivity incurred a decreasing tendency after the BN surpassed 7%. The main reason was that among the CPCM, BN filling was sufficient, so as to restrict the SBS/EPDM distribution uniformly. Thus, it should be concluded that the thermal conductivity obtained the optimum value when BN proportion was 7% in the CPCM.
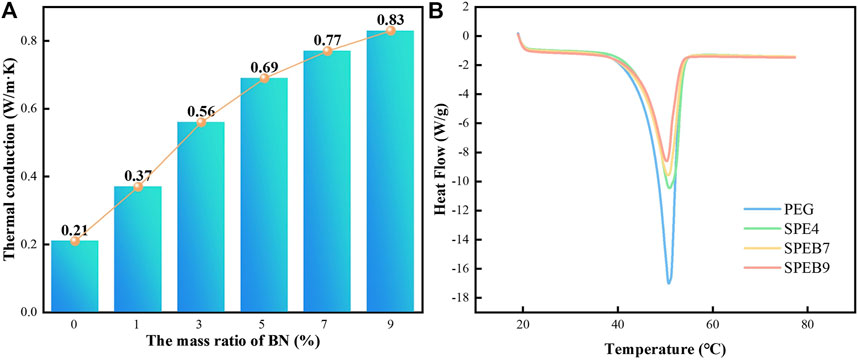
FIGURE 6. (A) Thermal conductivity curves of the different samples. (B) Differential scanning calorimeter (DSC) test curves of the different samples.
As we know, the absorbed heat degree of CPCM was very essential to affect temperature distribution in the battery module. Figure 6D displays the DSC of the different samples, such as PEG, SPE4, SPEB7, and SPEB9. The latent heat value (H) and melting temperature relationship could be obtained, which is calculated in the Table 2. The latent value of SPEB7 was obviously lower than pure PEG. This is ascribed to the latent heat that was contributed by the PEG. The content of PEG was obviously reduced, so H decreased. Besides, with the increase in the CPCM, H has a decreasing tendency. The reason for this is that the BN with high thermal conductivity could transfer the heat absorbed by PEG timely and quickly.
The Evaluation of Battery Thermal Management
To clearly analyze the cooling effect of battery modules with various thermal management systems, three battery modules, such as air cooling, rigid CPCM, and flexible CPCM, were investigated, as described in Figures 7A–C. From the aforementioned analyzed results, the flexible CPCM with PSEB7 was applied in the battery module. In contrast with that, a similar mass ratio of PEG and BN was utilized to prepare the rigid CPCM.
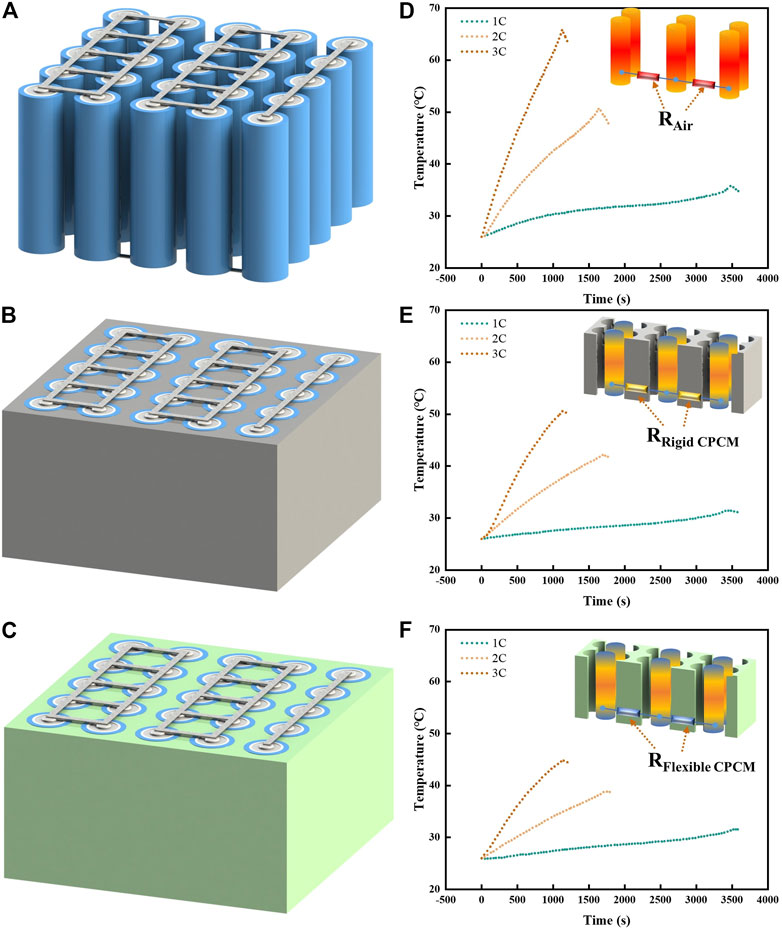
FIGURE 7. Three battery modules with various cooling systems: (A) Air cooling, (B) rigid CPCM, and (C) flexible CPCM. Temperature curves of the three battery modules with different cooling systems: (D) Air cooling, (E) rigid CPCM, and (F) flexible CPCM at 1C, 2C, and 3C discharge rates.
Compared with air cooling and rigid CPCM, flexible CPCM, in Figures 7D–F, shows the temperature curves of the battery modules at different discharge rates. The maximum temperatures of the battery module with rigid PCM and flexible CPCM are 32.2°C and 31.5°C, respectively, which are obviously lower than the air cooling effect at a discharge rate of 1 C. This is primarily due to the thermal conductivity of air, which was markedly lower than CPCM. The maximum temperature of the battery module with rigid PCM is close to that of the module with flexible CPCM.
However, the maximum temperature of air-based and rigid CPCM battery module at 3C discharge rate could reach 65.8°C and 50.6°C, respectively, as shown in Figure 7F. In contrast, the flexible CPCM for a battery module could control the maximum temperature to 44.8°C, which is lower than air cooling and rigid CPCM. This is probably due to the flexible CPCM, which could make a tight contact fitting with batteries and further decrease the contact thermal resistance. The corresponding mechanism diagram is shown in the inset figure in Figures 7D–F.
In addition, the temperature difference (ΔT) has been recognized as the vital parameter to indicate the thermal behavior of the battery module. Figure 8A displays the temperature difference curve among battery modules with various cooling approaches. The maximum ΔT values of these battery modules at different discharge rates are summarized in Figure 8C. Especially at 3C discharge rate, the maximum ΔT of the battery module with air cooling was severely inconsistent, which could easily cause thermal runway. Compared with that, the maximum ΔT of the battery module with flexible CPCM is just 5.7°C. It reveals that the temperature difference could significantly decrease during the discharge rate, especially at a high discharge rate. Therefore, it could lead to the conclusion that the flexible CPCM for battery module demonstrates the optimum temperature capacity, which could be in a much closer contact with batteries than rigid CPCM and, thus, improve the transferring heat efficiency.
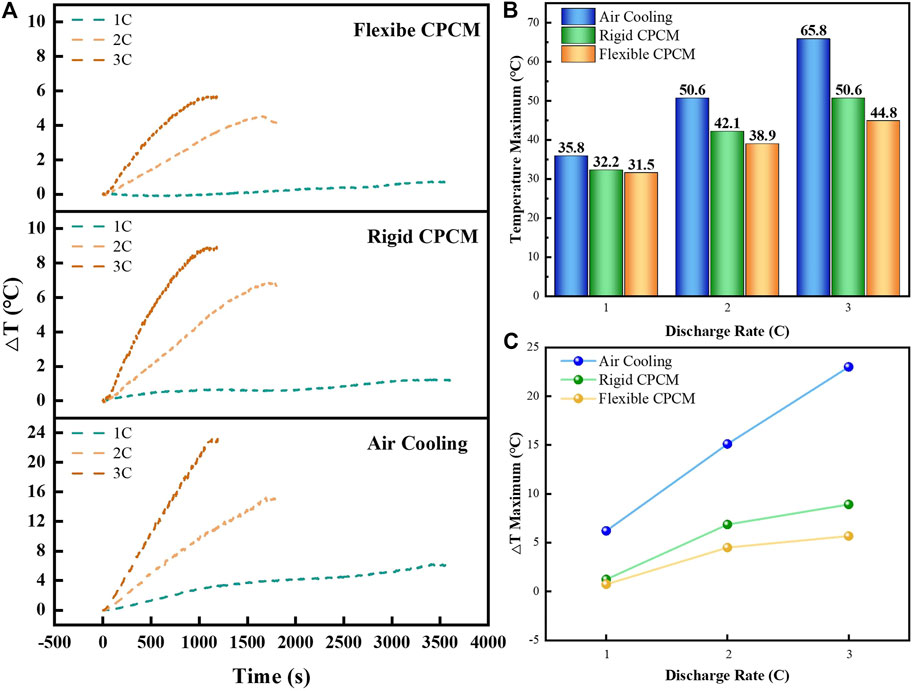
FIGURE 8. (A) Temperature difference curves during the discharge process of the three battery modules with different cooling methods. (B) Maximum temperature values during discharge of the battery modules with three different cooling methods. (C) Maximum temperature difference values during discharge of the battery modules with three different cooling methods.
The temperature stability of the battery module is an important indicator in evaluating thermal management effect during the charge and discharge process. In evaluating the capacity of the battery module with various BTM systems, 10 cycles were carried out at 1C, 2C, and 3 C discharge rates. The temperature curves of the different battery modules are displayed in Figure 9. It could be seen that the temperature of the flexible CPCM-based battery module is only 44.8°C, which is markedly smaller than the value of air cooling system, and is also lower than the temperature of the battery module with rigid CPCM. Therefore, it can be induced that the battery module assembled with flexible CPCM could obtain an optimum controlling temperature effect during long multicycle operating conditions, which would enhance the thermal safety of the battery module.
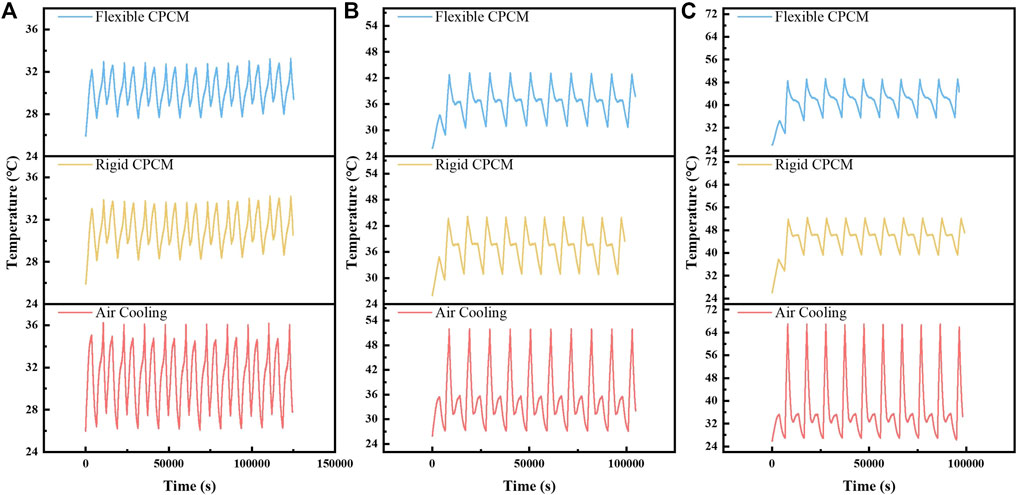
FIGURE 9. Temperature curves of the three battery modules in 10 cycles of charge/discharge tests at different discharge rates: (A) 1C, (B) 2C, and (C) 3 C.
Conclusion
In this study, a passive battery module management system with flexible composite PCM has been proposed and experimentally researched. Initially, the structure, thermal property, and morphology of composites were investigated in detail. Then, the battery modules with various cooling systems were designed and carried out at different discharge rates during 10 charge and discharge cycling processes. The main results are summarized as follows:
1) A good compatibility of the PEG/SBS/EPDM/BN composite material is exhibited. The quality maintenance rate of the flexible CPCM is maintained at 98.1%, surpassing by 7.7%, under 50°C heating condition for 7 h, the 90.4% SBS/EPDM in the composite material.
2) BN with its high thermal conductivity could enhance the heat transferring capacity of CPCM, which could reach up to 0.83 W/m·K when the BN proportion was 9%.
3) Compared with air cooling and rigid CPCM, the shape recovery of the flexible CPCM can effectively reduce thermal contact resistance, so as to increase the thermal stability of the battery module. The maximum temperature could be controlled below 44.8°C at 3C discharge rate.
In summary, this research reveals that the flexible CPCM can provide excellent thermal management effect and have great promising prospects in the application of energy storage fields.
Data Availability Statement
The original contributions presented in the study are included in the article/Supplementary Material. Further inquiries can be directed to the corresponding author.
Author Contributions
XT and JD: Conceptualization, methodology, investigation, formal analysis, visualization, validation, data curation, writing—original draft, and writing—reviewing and editing. ZW: Methodology, investigation, supervision, and writing—reviewing and editing. XL and CW: Methodology, data curation, validation, supervision, writing—reviewing and editing, and project administration.
Funding
This research was financially supported by the Guangdong Key Laboratory of Battery Safety (No. 2019B121203008) and the National Natural Science Foundation of China (No. 21875046).
Conflict of Interest
The authors declare that the research was conducted in the absence of any commercial or financial relationships that could be construed as a potential conflict of interest.
Publisher’s Note
All claims expressed in this article are solely those of the authors and do not necessarily represent those of their affiliated organizations, or those of the publisher, the editors, and the reviewers. Any product that may be evaluated in this article, or claim that may be made by its manufacturer, is not guaranteed or endorsed by the publisher.
Supplementary Material
The Supplementary Material for this article can be found online at: https://www.frontiersin.org/articles/10.3389/fenrg.2022.801341/full#supplementary-material
References
Atinafu, D. G., Dong, W., Wang, C., and Wang, G. (2018). Synthesis of Porous Carbon from Cotton Using an Mg(OH)2 Template for Form-Stabilized Phase Change Materials with High Encapsulation Capacity, Transition Enthalpy and Reliability. J. Mater. Chem. A 6, 8969–8977. doi:10.1039/c8ta01672k
Chen, F., Huang, R., Wang, C., Yu, X., Liu, H., Wu, Q., et al. (2020). Air and PCM Cooling for Battery Thermal Management Considering Battery Cycle Life. Appl. Therm. Eng. 173, 115154. doi:10.1016/j.applthermaleng.2020.115154
Chriaa, I., Trigui, A., Karkri, M., Jedidi, I., Abdelmouleh, M., and Boudaya, C. (2020). Thermal Properties of Shape-Stabilized Phase Change Materials Based on Low Density Polyethylene, Hexadecane and SEBS for thermal Energy Storage. Appl. Therm. Eng. 171, 115072. doi:10.1016/j.applthermaleng.2020.115072
Ding, B., Qi, Z.-H., Mao, C.-S., Gong, L., and Liu, X.-L. (2020). Numerical Investigation on Cooling Performance of PCM/cooling Plate Hybrid System for Power Battery with Variable Discharging Conditions. J. Therm. Anal. Calorim. 141, 625–633. doi:10.1007/s10973-020-09611-0
Zhou, D., Yuan, J., Zhou, Y., and Liu, Y. (2020). Preparation and Characterization of Myristic Acid/expanded Graphite Composite Phase Change Materials for thermal Energy Storage. Sci. Rep. 10, 10889. doi:10.1038/s41598-020-67849-y
Drissi, S., Ling, T.-C., and Mo, K. H. (2019). Thermal Efficiency and Durability Performances of Paraffinic Phase Change Materials with Enhanced thermal Conductivity - A Review. Thermochim. Acta 673, 198–210. doi:10.1016/j.tca.2019.01.020
Gao, L., Sun, X., Sun, B., Che, D., Li, S., Liu, Z., et al. (2020). Preparation and thermal Properties of Palmitic Acid/expanded Graphite/carbon Fiber Composite Phase Change Materials for thermal Energy Storage. J. Therm. Anal. Calorim. 141, 25–35. doi:10.1007/s10973-019-08755-y
Gulfam, R., Zhang, P., and Meng, Z. (2019). Advanced thermal Systems Driven by Paraffin-Based Phase Change Materials - A Review. Appl. Energ. 238, 582–611. doi:10.1016/j.apenergy.2019.01.114
Huang, Q., Deng, J., Li, X., Zhang, G., and Xu, F. (2020). Experimental Investigation on Thermally Induced Aluminum Nitride Based Flexible Composite Phase Change Material for Battery thermal Management. J. Energ. Storage 32, 101755. doi:10.1016/j.est.2020.101755
Huang, Q., Li, X., Zhang, G., Deng, J., and Wang, C. (2021). Thermal Management of Lithium-Ion Battery Pack through the Application of Flexible Form-Stable Composite Phase Change Materials. Appl. Therm. Eng. 183, 116151. doi:10.1016/j.applthermaleng.2020.116151
Jia, X., Li, Q., Ao, C., Hu, R., Xia, T., Xue, Z., et al. (2020). High thermal Conductive Shape-Stabilized Phase Change Materials of Polyethylene Glycol/boron Nitride@chitosan Composites for thermal Energy Storage. Compos. A Appl. Sci. Manuf. 129, 105710. doi:10.1016/j.compositesa.2019.105710
Li, J., Zhang, F., Liu, Y., Muhammad, Y., Su, Z., Meng, F., et al. (2019). Preparation and Properties of Soybean Bio-Asphalt/SBS Modified Petroleum Asphalt. Constr. Build. Mater. 201, 268–277. doi:10.1016/j.conbuildmat.2018.12.206
Zhou, L., Tang, L.-S., Tao, X.-F., Yang, J., Yang, M.-B., and Yang, W. (2020). Facile Fabrication of Shape-Stabilized Polyethylene Glycol/cellulose Nanocrystal Phase Change Materials Based on Thiol-Ene Click Chemistry and Solvent Exchange. Chem. Eng. J. 396, 125206. doi:10.1016/j.cej.2020.125206
Lu, X., Huang, J., Wong, W.-Y., and Qu, J.-p. (2019). A Novel Bio-Based Polyurethane/wood Powder Composite as Shape-Stable Phase Change Material with High Relative Enthalpy Efficiency for Solar thermal Energy Storage. Solar Energ. Mater. Solar Cell 200, 109987. doi:10.1016/j.solmat.2019.109987
Luan, Y., Yang, M., Ma, Q., Qi, Y., Gao, H., Wu, Z., et al. (2016). Introduction of an Organic Acid Phase Changing Material into Metal-Organic Frameworks and the Study of its thermal Properties. J. Mater. Chem. A 4, 7641–7649. doi:10.1039/c6ta01676f
Nanthagopal, M., Santhoshkumar, P., Shaji, N., Sim, G. S., Park, J. W., Senthil, C., et al. (2020). An Encapsulation of Nitrogen and sulphur Dual-Doped Carbon over Li[Ni0.8Co0.1Mn0.1]O2 for Lithium-Ion Battery Applications. Appl. Surf. Sci. 511, 145580. doi:10.1016/j.apsusc.2020.145580
Qin, P., Liao, M., Mei, W., Sun, J., and Wang, Q. (2021). The Experimental and Numerical Investigation on a Hybrid Battery thermal Management System Based on Forced-Air Convection and Internal Finned Structure. Appl. Therm. Eng. 195, 117212. doi:10.1016/j.applthermaleng.2021.117212
Safdari, M., Ahmadi, R., and Sadeghzadeh, S. (2020). Numerical Investigation on PCM Encapsulation Shape Used in the Passive-Active Battery thermal Management. Energy 193, 116840. doi:10.1016/j.energy.2019.116840
Sang, G., Cao, Y., Fan, M., Lu, G., Zhu, Y., Zhao, Q., et al. (2019). Development of a Novel Sulphoalumitate Cement-Based Composite Combing fine Steel Fibers and Phase Change Materials for thermal Energy Storage. Energy Build. 183, 75–85. doi:10.1016/j.enbuild.2018.10.039
Sundararajan, S., Samui, A. B., and Kulkarni, P. S. (2017). Versatility of Polyethylene Glycol (PEG) in Designing Solid–Solid Phase Change Materials (PCMs) for thermal Management and Their Application to Innovative Technologies. J. Mater. Chem. A 5, 18379–18396. doi:10.1039/C7TA04968D
Tang, B., Wang, L., Xu, Y., Xiu, J., and Zhang, S. (2016). Hexadecanol/phase Change Polyurethane Composite as Form-Stable Phase Change Material for thermal Energy Storage. Solar Energ. Mater. Solar Cell 144, 1–6. doi:10.1016/j.solmat.2015.08.012
Tian, B., Yang, W., Luo, L., Wang, J., Zhang, K., Fan, J., et al. (2016). Synergistic Enhancement of thermal Conductivity for Expanded Graphite and Carbon Fiber in Paraffin/EVA Form-Stable Phase Change Materials. Solar Energy 127, 48–55. doi:10.1016/j.solener.2016.01.011
Turksoy, A., Teke, A., and Alkaya, A. (2020). A Comprehensive Overview of the Dc-Dc Converter-Based Battery Charge Balancing Methods in Electric Vehicles. Renew. Sustain. Energ. Rev. 133, 110274. doi:10.1016/j.rser.2020.110274
Uemura, T., Yanai, N., Watanabe, S., Tanaka, H., Numaguchi, R., Miyahara, M. T., et al. (2010). Unveiling thermal Transitions of Polymers in Subnanometre Pores. Nat. Commun. 1, 83. doi:10.1038/ncomms1091
Wang, Z., Situ, W., Li, X., Zhang, G., Huang, Z., Yuan, W., et al. (2017). Novel Shape Stabilized Phase Change Material Based on Epoxy Matrix with Ultrahigh Cycle Life for thermal Energy Storage. Appl. Therm. Eng. 123, 1006–1012. doi:10.1016/j.applthermaleng.2017.05.179
Wang, Y., Liu, B., Han, P., Hao, C., Li, S., You, Z., et al. (2021). Optimization of an Air-Based thermal Management System for Lithium-Ion Battery Packs. J. Energ. Storage 44, 103314. doi:10.1016/j.est.2021.103314
Wu, D., Ni, B., Liu, Y., Chen, S., and Zhang, H. (2015). Preparation and Characterization of Side-Chain Liquid crystal Polymer/paraffin Composites as Form-Stable Phase Change Materials. J. Mater. Chem. A 3, 9645–9657. doi:10.1039/c5ta00606f
Wu, W., Ye, G., Zhang, G., and Yang, X. (2022). Composite Phase Change Material with Room-Temperature-Flexibility for Battery thermal Management. Chem. Eng. J. 428, 131116. doi:10.1016/j.cej.2021.131116
Xiao, C., Wu, X., Dong, X., Ye, G., Zhang, G., and Yang, X. (2021). Ultrareliable Composite Phase Change Material for Battery Thermal Management Derived from a Rationally Designed Phase Changeable and Hydrophobic Polymer Skeleton. ACS Appl. Energ. Mater. 4 (4), 3832–3841. doi:10.1021/acsaem.1c00235
Yang, J., Tang, L.-S., Bao, R.-Y., Bai, L., Liu, Z.-Y., Yang, W., et al. (2017). Largely Enhanced thermal Conductivity of Poly (Ethylene Glycol)/boron Nitride Composite Phase Change Materials for solar-thermal-electric Energy Conversion and Storage with Very Low Content of Graphene Nanoplatelets. Chem. Eng. J. 315, 481–490. doi:10.1016/j.cej.2017.01.045
Yuan, Y., Zhang, N., Tao, W., Cao, X., and He, Y. (2014). Fatty Acids as Phase Change Materials: A Review. Renew. Sustain. Energ. Rev. 29, 482–498. doi:10.1016/j.rser.2013.08.107
Zhang, Y., Huang, J., Cao, M., Liu, Z., and chen, Q. (2021). A Novel Flexible Phase Change Material with Well thermal and Mechanical Properties for Lithium Batteries Application. J. Energ. Storage 44, 103433. doi:10.1016/j.est.2021.103433
Zhao, G., Wang, X., Negnevitsky, M., and Zhang, H. (2021). A Review of Air-Cooling Battery thermal Management Systems for Electric and Hybrid Electric Vehicles. J. Power Sourc. 501 (1), 230001. doi:10.1016/j.jpowsour.2021.230001
Keywords: composite phase change material, thermal contact resistance, thermal-induced flexibility, battery thermal management, anti leakage property
Citation: Tang X, Deng J, Wu Z, Li X and Wang C (2022) Experimental Investigation on BN-Based Flexible Composite Phase-Change Material for Battery Module. Front. Energy Res. 10:801341. doi: 10.3389/fenrg.2022.801341
Received: 25 October 2021; Accepted: 08 February 2022;
Published: 08 April 2022.
Edited by:
Zhonghao Rao, China University of Mining and Technology, ChinaReviewed by:
Yun Huang, Institute of Process Engineering (CAS), ChinaWeixiong Wu, Jinan University, China
Copyright © 2022 Tang, Deng, Wu, Li and Wang. This is an open-access article distributed under the terms of the Creative Commons Attribution License (CC BY). The use, distribution or reproduction in other forums is permitted, provided the original author(s) and the copyright owner(s) are credited and that the original publication in this journal is cited, in accordance with accepted academic practice. No use, distribution or reproduction is permitted which does not comply with these terms.
*Correspondence: Xinxi Li, cGtkbHh4QDE2My5jb20=
†These authors share first authorship