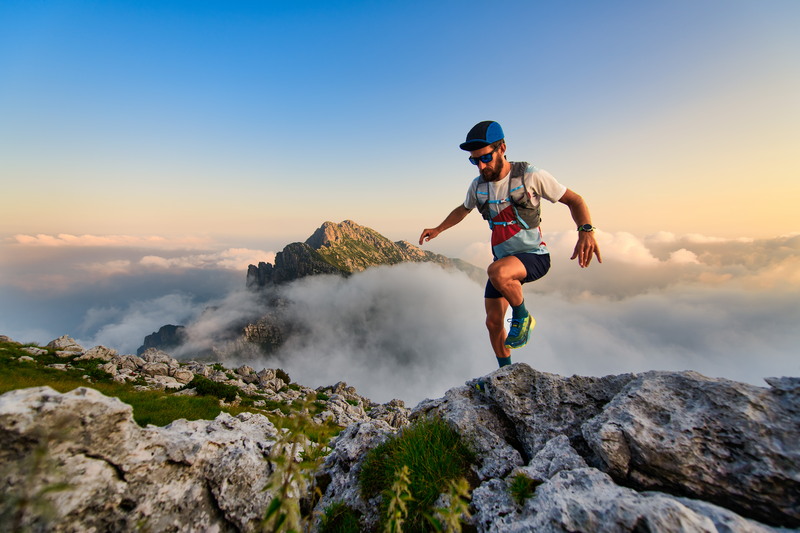
95% of researchers rate our articles as excellent or good
Learn more about the work of our research integrity team to safeguard the quality of each article we publish.
Find out more
ORIGINAL RESEARCH article
Front. Energy Res. , 17 November 2022
Sec. Advanced Clean Fuel Technologies
Volume 10 - 2022 | https://doi.org/10.3389/fenrg.2022.1053576
This article is part of the Research Topic Outcomes from ICFEE 2023 - Waste Valorization and Waste to Energy: A Pathway to Zero-waste Industries View all 4 articles
This paper analyzes the environmental and economic impact of switching fuel in industrial boilers and furnaces. This analysis, performed over 5 years, reveals that the total emissions thus avoided are 85,069 tons of CO2, 17,240 kg of CH4, 4,310 tons of N2O, and 6,630 tons of SOx. The total equivalent CO2 emissions avoided is around 87,802 tons over the decade 2012–2021. Switching results in a significant reduction in greenhouse gases: 17.8% of CO2 emissions, 66.7% of CH4 emissions, and 83.3% of N2O emissions. Analysis conducted at the boiler level shows that CO2 and CO emissions would decrease, respectively, by 2.5% points and 1.05 ppm points when natural gas is used. The same observation is made for SOx and NOx emissions, for which decreases of 188.3 and 236.7 ppm points are recorded. Additionally, the substitution of heavy fuel oil for natural gas enables an increase in thermal efficiency by 3.3% points.
Both household tasks and industrial activities are driven by economic and environmental constraints. Due to increasing greenhouse gas emissions, the limiting of global warming to below a 2°C increase is widely regarded as an imperative policy intervention. Industry has found affordable sources of electricity and heat generation in boilers, furnaces, and internal combustion engines. In order to reduce greenhouse gas emissions using a sector-by-sector regulatory approach, policymakers have generally recommended phasing out heavy fuel oil and coal boilers and furnaces (Heslin and Hobbs, 1989; De Almeida et al., 2004; Lopez and Mandujano, 2005; Zhang et al., 2016; Wilson and Staffell, 2018). There are several studies which have focused on the economic, technical, and environmental analysis of switching or substituting energy sources (Kaewboonsong et al., 2006; Ahmad and Puppim de Oliveira, 2015; Han et al., 2017; Fleiter et al., 2018; Gilbert et al., 2018; Rehfeldt et al., 2019; Moya et al., 2020; Shen et al., 2021).
Park et al. (2019) investigated the substitution of heavy fuel oil with bioliquid fuel in a large furnace and boiler, and reported a significant decrease in nitro oxide (NOx) and sulfur oxide (Sox) emissions. Wilson and Staffell (2018) found that switching fuel from coal to natural gas with an appropriate incentives framework avoided 1 GtCO2 per year. RehfeldtFleiter et al. (2020) also reported that fuel switching is a valuable option for medium and long-term emissions reduction in German industrial.
All these studies have concluded that fuel substitution is a promising alternative for minimizing industrial boiler emissions, particularly for waste oil, coal, or heavy fuel-oil powered boilers. A significant emissions reduction below the applicable carbon dioxide (CO2) emissions target has been recorded in the substitution of heavy fuel oil or coal by natural gas (De Almeida et al., 2004; Lopez and Mandujano, 2005).
In the case of Cameroon, a developing country, several fuel-switching or substitution alternatives are feasible for its available energy resources, including biomass, biofuels, and natural gas. Before 2012, all thermal power plants, boilers, and furnaces were fueled by heavy fuel oil and waste oil, except for two biomass cogeneration plants which were powered by sugar cane bagasse and palm oil cob agricultural waste. Such a functioning mode was imposed by Cameroon's energy sector, which lacked natural gas production until 2011. Based on the recommendations of the National Gas Development Master Plan, initiated in 1986 and updated in 2003 (Energy Sector Management Assistance Programme, 2001), the exploitation of natural gas was encouraged in 2012 by gas code legislation (Law N° 2012, 2012). Several industrials have opted for now-available natural gas due the attractive cost and environmental benefits of switching from heavy fuel oil and waste oil in industrial burners. Five years after, with fuel substitution occurring at different rates depending on the sector activity, it is essential to make an initial assessment to guide the consolidation or reorientation of ongoing fuel-switching. Can this replacement of heavy fuel and waste oil by natural gas help down drive emissions and offer a way of improving the efficiency of industrial boilers and furnaces?
The purpose of this article is to analyze the environmental and economic impact of the ongoing energy transition in industrial boilers and furnaces. It first presents the study area and the gas consumption sector. It then highlights the emissions model and resulting emissions impacts based on avoiding heavy fuel oil usage. Finally, the article analyzes substitution in steam boilers of the brewing industry using environmental and energy performance metrics.
The study was carried out in Douala (latitude 4°02′ 53.77″N, longitude 9°42′15.41″E), Cameroon’s main harbor and its most energy-hungry city, a location of economic and industrial activity. Douala is located on the western seaboard and is the most important trade hub in Central Africa. The fuel demand and consumption of the city is 70% of the country’s total. The city’s industries are in two main locations. The first is around the natural gas production unit (within 10 km) and contains 85% of the city’s industrial activity; the second is in the city’s suburbs. This study area is the only city in Cameroon where natural gas is available and is sold to industrial customers. Figure 1, depicts the study area, including the gas production and distribution network.
FIGURE 1. View of the study area and gas pipe from the gas company wellhead to customers (Victoria Oil & Gas, 2018).
The data used to perform the analysis are taken from official sources provided online by the natural gas supplier (Victoria Oil & Gas, 2018; Gaz du Cameroun, 2016; Gaz du Cameroun, 2017; Gaz du Cameroun, 2018; Gaz du Cameroun, 2021). Before the development of natural gas, boilers, furnaces, and heat production in the industrial sector were fueled by heavy fuel oil and waste oil. Figure 2 presents the evolution of heavy fuel oil consumption in the industrial sector before and after natural gas production. The substitution can be clearly observed in the decrease in fuel oil consumption since the year 2012. Some companies have opted to continue supplying burners with fuel oil due to difficulties in changing the necessary equipment.
FIGURE 2. Evolution of fuel oil consumption (Victoria Oil & Gas, 2018).
Data on natural gas consumption were collected over the decade 2012–2021. As depicted in Figure 3, natural gas consumption in industrial boilers is driven by five major applications: brewery and food processing (34%), steel manufacture (14%), dairy products (10%), and textile (10%) and salt manufacture (7%).
FIGURE 3. Repartition of natural gas consumers in the industrial sector (Victoria Oil & Gas, 2018).
The evolution of natural gas sales per day is depicted in Figure 4. The natural gas purchased is not stored by industrial customers but is directly provided to the boiler or furnace through a pipe network from the gas company wellhead. Thus, the amount of natural gas sold by the producer is equivalent to the amount consumed at the endpoint boilers and furnaces. Eq. 1 shows the assumption for estimated gas consumption.
where
In this subsection, the impact of heavy fuel oil substitution on greenhouse gas emissions is assessed on a city level based on the total volume of gas consumed. It is assumed that the combustion of fossil fuels in boilers, heaters, and furnaces results in CO2, methane (CH4), SOx, and nitrous oxide (N2O) emissions.
A fuel analysis approach is used to estimate CO2 emissions. This firstly involves determining the carbon content of fuel combusted and applying that to the amount of fuel burned to calculate CO2 emissions. The products of incomplete combustion are not taken into account. The simplified procedure used for the emissions calculation from the default fuel analysis approach is given by Eqs 2 and 3 respectively for fuel oil and natural gas (Eggleston et al., 2007).
where
The estimation of CH4 and N2O emissions from stationary combustion is performed using Eq. 4 (Rehfeldt et al., 2019).
where EF represents the emission factor, j is the pollutant type (CH4, N2O), A the activity level, and s is the source category. The appropriate factors in terms of fuel type and sector where the fuel is consumed for calculating CH4 and N2O and SOx emissions are given in the International Panel on Climate Change (IPCC) Guidelines for National Greenhouse Gas Inventories (Energy Sector Management Assistance Programme, 2001).
A comparative analysis of energy and environmental performance indicators is performed on a combustion system fired with fuel oil or natural gas in the brewing industry. The boiler used and its characteristics are presented in Table 1. The measurement was performed using an ECOM combustion analyzer apparatus for the boiler operating at different loads, ranging from 25% to 100%. The measured parameters are thermal efficiency, flue gas temperature, and losses and percentage of CO2, CO, N2O, and SOX in the flue gas. All these emissions from fuel combustion are technology-dependent. The thermal efficiency of the boiler under consideration is also determined by taking into account the lower heat value (LHV) of the fuel being considered, the useful heat power transfer to working fluid, and the fuel or gas consumption of the boiler measured using the flow meter apparatus as shown Eqs 5, 6:
Heavy-fuel-oil fired boiler efficiency:
Natural-gas fired boiler efficiency:
The losses represent the heat exiting the boiler through the flue gas and is computed using Eq. 7
where χ is a coefficient linked to the fuel type,
Despite the advantage promoted by the gas company, some industries have opted to continue supplying burners with fuel oil due to difficulties in changing the necessary equipment. The other concern to be addressed relating to some not switching from fuel oil is that the net profit margins and return on investment have not been sufficiently explained and documented. To address this concern, a price break-even line of producing a mass unit of steam at the same operational expenditure cost, using heavy fuel oil and natural gas, is constructed. The price break-even value is calculated from Eqs 8, 9 (Heslin and Hobbs, 1989):
Combining Eqs 8, 9, the relation between the fuel and gas prices is obtained and presented in Eq 10.
where:
The economic impact is determined based on the total volume of gas sold for industrial thermal usage. The current price of heavy fuel oil is about $22/mmbtu, and the natural gas price is around $16/mmbtu. As highlighted in Figure 5, fuel-oil substitution results in a reduction in expense for fuel used in boilers or furnaces. The total savings of 128 million USD realized in 10 years are quite important for low-income countries. These savings can be used to improve competitiveness or as a source for financing additional sustainable equipment. Switching a heavy fuel oil fired boiler to one fired by natural gas requires some modification and adjustment to the equipment—the main one is substituting a fuel oil burner and its auxiliary with a natural gas burner and its equipment. In the present analysis, the natural gas producer is committed to providing and installing all the additional equipment needed to ensure fuel substitution. Therefore, the cost of this equipment is not taken into account in the economic analysis. The price break-even line of producing an amount of steam at the same cost, using heavy fuel oil or natural gas, is depicted in Figure 6. It is clearly evident that, when the ratio between the heavy fuel oil and natural gas price is 1.08, steam production is achieved at the same cost. Using natural gas to fire a boiler is more profitable when the ratio is above the break-even line. In the area under the break-even line, heavy fuel oil fired boilers are more economical.
FIGURE 6. The price break-even line of producing an amount of steam at the same cost, using heavy fuel oil or natural gas.
As highlighted in the figures, switching results in a significant reduction of greenhouse gas: 17.8% in CO2 emission (Figure 7), 66.7% in CH4 (Figure 8), and 83.3% in N2O (Figure 9). These reductions are computed as the difference between the emissions recorded with a natural gas firing boiler and the emissions that would be measured if the boiler still relied on heavy fuel oil. The reductions in CO2, N2O, and CH4 emissions are mainly driven by the composition of natural gas (carbon chain length and azote content) and its more efficient combustion than heavy fuel oil.
Sulfur dioxide (SO2) emissions are completely avoided when burners are supplied with gas, as highlighted in Figure 10. Since natural gas contains no sulfur, emissions of substances formed from this atom are completely avoided in the natural-gas-fired mode. The sulfur content of heavy fuel oil (around 2 parts per million) is the source of the SOx released into the atmosphere. The reduction in emissions observed in the third calendar quarter (July-September) is linked to the reduced gas consumption due to economic slowdown in the rainy season. The decrease in gas consumption is sometimes linked to the rise in the dollar exchange rate. Thanks to the dollarization of the gas market, the level of industrial commitment to fire boilers with natural gas depends on the local currency exchange rate. The cost for acquiring natural gas is sometimes less competitive than that for heavy fuel oil due to the weaker exchange rate of the local FCFA against the USD.
Figure 11 gives an overview of the avoided emissions for each sera gas after 10 years. The total avoided emission is respectively 85,069 tons of CO2, 17,240 kg of CH4, 4,310 tons of N2O, and 6,630 tons of SOx. The total equivalent of avoided CO2 emissions is around 87,802 tons over a 10-year period.
The analysis uses case study information from boilers in the important brewing industry. The measured parameters are grouped for a better graphical representation into two groups. The first group includes thermal losses, the air factor, and the percentage of CO2, O2, and CO in the flue gas. The second group includes thermal efficiency, the flue gas temperature, and the percentage of N2O and SOX in the flue gas. For a boiler working at loads ranging from 25% to 100%, Figures 12A–F serve as proof that, in a fuel oil firing mode, emissions of CO2 and CO are greater. It is also observed that losses are minimized in natural gas firing mode due to the lower flue gas temperature, depicted in Figures 13A–F. The lower flue gas temperature results in better efficiency in gas firing mode regardless of the load factor. The same figure shows that the SOX and N2O emissions are respectively 0 and minimal in a gas firing mode. Concerning emissions, Figure 14A highlights that the CO2 and CO emissions decrease respectively by 2.5% and 1.05 ppm. The same observation is made for SO2 and NOx emissions, for which respective decreases of 188.3 ppm and 236.7 ppm were recorded (Figure 14B). Figure 14C shows that the substitution of heavy fuel oil for natural gas enables an increase in thermal efficiency by 3.3% points. With natural gas fired boilers, the flue gas temperature decreases by 34.33°C and induces a 3.55% drop in thermal losses. The analysis performed at the boiler steam level confirms the results obtained using the fuel analysis approach. Additionally, carbonaceous deposit and calamine are substantially reduced in natural gas fired boilers. The related fire tubes and burner cleaning costs are minimal in natural gas fired mode. The capital and operational expenditure incurred from preheating heavy fuel oil are also avoided in natural gas fueled burners.
FIGURE 12. Comparison of carbon dioxide, carbon monoxide, oxygen, air factor, and losses in fuel firing or gas firing mode: (A) boiler load of 25%, (B) boiler load of 37.5%, (C) boiler load of 50%, (D) boiler load of 65%, (E) boiler load of 75%, (F) boiler load of 100%.
FIGURE 13. Comparison of nitrous oxide, sulfur dioxide, thermal efficiency, and flue gas temperature in fuel firing or gas firing mode: (A) boiler load of 25%, (B) boiler load of 37.5%, (C) boiler load of 50%, (D) boiler load of 65%, (E) boiler load of 75%, (F) boiler load of 100%.
FIGURE 14. Amelioration of environmental and energetic parameters in natural gas fired mode: (A) carbon dioxide and carbon monoxide emission, (B) sulfur dioxide and nitrous oxide emission, (C) thermal efficiency, heat losses, flue gas temperature.
The substitution of heavy fuel oil for natural gas in industrial burners gradually leads to the decarbonisation of the energy mix. Switching from heavy fuel oil results in reductions of CO2, N2O, and CH4 emissions. The evaluation of the energy parameter, including thermal efficiency and the flue gas temperature, clearly demonstrates that a natural gas firing mode results in a better parameter. Due to the difference in fuel price, natural gas fueled boilers present an advantage in terms of operational costs. Both industry and research have shown that deploying natural gas technology has been mostly driven by supporting policies. It is thus clear that the consolidation of ongoing energy transition requires the government to adopt both coercive and incentive measures to promote the acquisition of appropriate combustion equipment and the application of greenhouse gas limitation directives. It is also important for the government to encourage a market deployment of alternative solutions to heavy fuel oil in the industrial sector and to avoid creating an energy infrastructure that depends on heavy fuel oil. The detailed responsibilities of stakeholders in the process of fuel switching need to be studied and documented. Finally, to facilitate stakeholders' understanding of the significance of ongoing energy transition, awareness and understanding by national stakeholders will need to be intensified.
The datasets presented in this study can be found in online repositories. The names of the repository/repositories and accession number(s) can be found below: www.gazducameroun.com/q4-2018-operations-update/, https://www.gazducameroun.com/160120-rns-q4-operations-update-2, https://www.gazducameroun.com/q4-2016-operations-update/, https://www.gazducameroun.com/q1-2017-operations-update/, https://www.snh.cm/index.php/en/hydrocarbons-in-cameroon/key-data, https://www.gazducameroun.com/q2-2017-operations-update/, https://www.victoriaoilandgas.com/wp-content/uploads/2017/07/VOGAR16_Web.pdf.
Conception and design of study: SN; Acquisition of data: SN, SM, and IM; Analysis and/or interpretation of data: SN, IM, and SM; Drafting the manuscript: SN, SM, and IM; Revising the manuscript critically for important intellectual content: SN; Approval of the version of the manuscript to be published: SN, IM, and SM.
The authors declare that the research was conducted in the absence of any commercial or financial relationships that could be construed as a potential conflict of interest.
All claims expressed in this article are solely those of the authors and do not necessarily represent those of their affiliated organizations, or those of the publisher, the editors, and the reviewers. Any product that may be evaluated in this article, or claim that may be made by its manufacturer, is not guaranteed or endorsed by the publisher.
Ahmad, S, and Puppim de Oliveira, J. A. (2015). Fuel switching in slum and non-slum households in urban India. J. Clean. Prod. 94, 130–136. doi:10.1016/j.jclepro.2015.01.072
De Almeida, A T., Lopes, A, Carvalho, A, Mariano, J, and Nunes, C (2004). Evaluation of fuel-switching opportunities in the residential sector. Energy Build. 36, 195–203. doi:10.1016/j.enbuild.2003.11.003
Eggleston, H. S., Buendia, L., Miwa, K., Ngara, T., and Tanabe, K. (2007). IPCC 2006, 2006 IPCC Guidelines for national greenhouse gas Inventories, prepared by the national greenhouse gas inventories Programme. Avaliable At: https://www.ipcc-nggip.iges.or.jp/public/2006gl/.
Energy Sector Management Assistance Programme (ESMAP) (2001). Africa gas initiative Cameroon volume ill. Avaliable At: https://esmap.org/node/873.
Fleiter, T., Rehfeldt, M., Herbst, A., Elsland, R., Klingler, A.-L., Manz, P., et al. (2018). A methodology for bottom-up modelling of energy transitions in the industry sector: The FORECAST model. Energy Strategy Rev. 22, 237–254. doi:10.1016/j.esr.2018.09.005
Gaz du Cameroun (2016). Quarter 4 2016 operations update. Avaliable At: www.gazducameroun.com/q4-2016-operations-update/ (Accessed: November 15, 2019).
Gaz du Cameroun (2017). Quarter 4 2017 operations update. Avaliable At: www.gazducameroun.com/q4-2017-operations-update/ (Accessed: November 15, 2019).
Gaz du Cameroun (2018). Quarter 4 2018 operations update. Avaliable At: www.gazducameroun.com/q4-2018-operations-update/ (Accessed: November 15, 2019).
Gaz du Cameroun (2021). Quarter 4 2021 operations update. Avaliable At: www.gazducameroun.com/q4-2021-operations-update/ (Accessed: November 16, 2022).
Gilbert, P, Walsh, C, Traut, M, Kesieme, U, Pazouki, K, and Murphy, A (2018). Assessment of full life cycle air emissions of alternative shipping fuels. J. Clean. Prod. 172, 855–866. doi:10.1016/j.jclepro.2017.10.165
Han, Y, Shen, B, and Zhang, T (2017). A techno-economic assessment of fuel switching options of addressing environmental challenges of coal-fired industrial boilers: An analytical work for China. Energy Procedia 142, 3083–3087. doi:10.1016/j.egypro.2017.12.448
Heslin, J S., and Hobbs, B F. (1989). A multiobjective production costing model for analyzing emissions dispatching and fuel switching (of power stations). IEEE Trans. Power Syst. 4 (3), 836–842. doi:10.1109/59.32569
Kaewboonsong, W., I Kuprianov, V., and Chovichien, N. (2006). Minimizing fuel and environmental costs for a variable-load power plant (co-)firing fuel oil and natural gas. Fuel Process. Technol. 87, 1085–1094. doi:10.1016/j.fuproc.2006.08.003
Law N° 2012 (2012). Law N° 2012/006 of 19 April 2012 that institute gas code. Avaliable At: https://minepded.gov.cm/wp-content/uploads/2020/01/LAW-NO.-2012006-OF-19-APRIL-2012-TO-INSTITUTE-THE-GAS-CODE.pdf.
Lopez, J. L., and Mandujano, C. (2005). Estimation of the impact in the air quality by the use of clean fuels (fuel oil versus natural gas). Catal. Today 106, 176–179. doi:10.1016/j.cattod.2005.07.173
Moya, D, Budinis, S, Giarola, S, and Adam, H (2020). Agent-based scenarios comparison for assessing fuel-switching investment in long-term energy transitions of the India’s industry sector. Appl. Energy 274, 115295–95. doi:10.1016/j.apenergy.2020.115295
Park, H. Y., Han, K., Kim, H. H., Park, S., Jang, J., Yu, G. S., et al. (2019). Comparisons of combustion characteristics between bioliquid and heavy fuel oil combustion in a 0.7 MWth pilot furnace and a 75 MWe utility boiler. Energy 192 (1), 116557. doi:10.1016/j.energy.2019.116557
Rehfeldt, M., Fleiter, T, Herbst, A, and Eidelloth, S (2020). Fuel switching as an option for medium-term emission reduction - a model-based analysis of reactions to price signals and regulatory action in German industry. Energy Policy 147, 111889. doi:10.1016/j.enpol.2020.111889
Rehfeldt, M., Globisch, J., and Fleiter, T. (2019). Fuel choice in industrial steam generation: Empirical evidence reveals technology preferences. Energy Strategy Rev. 26, 100407. doi:10.1016/j.esr.2019.100407
Shen, B, Price, L, Lu, H, Liu, X, and Tsen, K (2021). Curbing air pollution and greenhouse gas emissions from industrial boilers in China ERNEST Orl LAWRENCE BERKELEY Natl Lab. Avaliable At: https://china.lbl.gov/publications/Curbing Air Pollution and Greenhouse Gas Emissions from Industrial Boilers in China/.
Victoria Oil & Gas (2018). Annual report & accounts. Avaliable At: www.victoriaoilandgas.com (Accessed on: November 15, 2019).
Wilson, I. A. G., and Staffell, I. (2018). Rapid fuel switching from coal to natural gas through effective carbon pricing. Nat. Energy 3 (5), 365–372. doi:10.1038/s41560-018-0109-0
Keywords: fuel switching, natural gas, heavy fuel oil, greenhouse gas emissions, industrial sector
Citation: Koumi Ngoh S, Epessé Missé S and Moungnutou Mfetoum I (2022) Environmental and economic assessment of switching from heavy fuel oil to natural gas in industrial boilers and furnaces: Case of Cameroon, a low-income country. Front. Energy Res. 10:1053576. doi: 10.3389/fenrg.2022.1053576
Received: 25 September 2022; Accepted: 26 October 2022;
Published: 17 November 2022.
Edited by:
Jinlong Liu, Zhejiang University, ChinaReviewed by:
Huachao Yang, Zhejiang University, ChinaCopyright © 2022 Koumi Ngoh, Epessé Missé and Moungnutou Mfetoum. This is an open-access article distributed under the terms of the Creative Commons Attribution License (CC BY). The use, distribution or reproduction in other forums is permitted, provided the original author(s) and the copyright owner(s) are credited and that the original publication in this journal is cited, in accordance with accepted academic practice. No use, distribution or reproduction is permitted which does not comply with these terms.
*Correspondence: Simon Koumi Ngoh, c2ltb25fa291bWlAeWFob28uZnI=
Disclaimer: All claims expressed in this article are solely those of the authors and do not necessarily represent those of their affiliated organizations, or those of the publisher, the editors and the reviewers. Any product that may be evaluated in this article or claim that may be made by its manufacturer is not guaranteed or endorsed by the publisher.
Research integrity at Frontiers
Learn more about the work of our research integrity team to safeguard the quality of each article we publish.