- 1Chemical Metallurgical and Materials Engineering, Faculty of Engineering and the Built Environment, Tshwane University of Technology, Pretoria, South Africa
- 2Center for Energy and Power, Electrical Engineering, Faculty of Engineering and the Built Environment, Tshwane University of Technology, Pretoria, South Africa
Recently, energy harvesting through the means of piezoelectric transducer technology has increasingly attracted the attention of engineers and scientists in producing/generating electricity for human consumption. However, understanding of piezoelectric materials for application in piezoelectric transducer devices in energy harvesting remains important in today’s energy systems engineering. Thus, the present review study is centered on piezoelectric materials for a better understanding of the properties of different piezoelectric materials (ceramic) when placed under mechanical stress or vibration and electrical field during energy harvesting using transducer devices. With the available literature, lead zirconate titanate materials showed to be the most common piezoelectric material with a high energy-generating performance but possessed more mechanical failure and also compromised in a harsh environment compared to lead-free piezoelectric materials. As such, the authors conclude that lead-free piezoelectric materials, such as zinc oxide and barium titanate, remain the best conducive piezoelectric material over lead zirconate titanate, which basically affects the human environment due to its toxicity. Thus, to widen the use of lead-free piezoelectric materials in energy harvesting, owing to their improved properties and environment-friendly nature, the authors recommend further enhancement of the lead-free piezoelectric material properties via nanodielectric filler incorporations using the spark plasma sintering technique.
Introduction
In the recent era, electricity has become a major need in almost all activities worldwide, owing to its increasing rate and demand for use in operating certain types of electrical devices. This occurs with respect to the growth of the human population, and as such, the means of energy presently has become inadequate for the demand of the users. Furthermore, energy consumption is increasing as a result of modernization, with natural resources being present at the site of extinction (Ramkrishna et al., 2016). However, to harness this problem, renewable energy harvesting has been adopted via proper means of storing energy for future use as micro energy harvesting is basically in search of conventional battery alternatives (Singh and Datta, 2011). The advances in renewable energy and sustainability have opened many doors for energy harvesting systems and research in real-world applications. Piezoelectricity is one such area under energy harvesting where electric charge is accumulated in certain solid materials in response to applied pressure. However, the word “Energy harvesting” can further be described as the process of capturing energy or obtaining energy from a source in accumulation and storing for future use (Elham, Noor, and Balbir, 2017; Adhithan, Vignesh, and Manikandan, 2015). Thus, in capturing this energy, electricity can be generated without any negative effect on human life and its surroundings. Accordingly, it was reported that using the human footprint, useful energy can be harvested and used to generate electricity, and this type of renewable energy does not depend on weather conditions (Mohd Asry et al., 2019). Hence, to achieve this, transducer technology is reportedly adopted as a means to address the high cost of energy and exponential reduction in the supply of fossil fuels and nuclear power instability in the current era. The type of transducer applied here is known as the piezoelectric transducer (Mohd Asry et al., 2019). Piezoelectric/piezoelectricity for transducers can be defined as the property potential of a certain material to generate electric voltage when they are subjected or exposed to mechanical stress and vibration, or vibrate when affected by an AC voltage, or both (Curie and Curie, 1880; Mitcheson et al., 2008; Kanani, 2014). The piezoelectric energy harvester on a sub-micron scale has limitless scope for research and application in the near future technology (Beeby, Tudor, and White, 2006). However, using the piezoelectric properties of some materials remains an inspiring means of alternative energy harvesting techniques (Kumar and Kim, 2012; Chennault et al., 2008), owing to the fact that piezoelectric materials could be employed as a means of converting ambient vibrations into electrical energy, which can be stored and utilized to power other devices. Therefore, the aim of this review paper was to focus on piezoelectric materials, which will offer an insight into today’s energy harvesting procedure using the piezoelectric transducer mechanism as a reference point in selecting the piezoelectric material for piezo-transducer devices in energy storage/energy harvesting applications without causing any side effects on human health.
Piezoelectric material for energy storage/harvesting
In 1880, Pierre and Jacques Curie discovered the direct piezoelectric effect in crystal quartz, which generated electrical charge and/or voltage under pressure. The word piezo stands for pressure in Greek; thus, the original meaning of the word piezoelectricity means pressure electricity; in other words, materials exhibiting this phenomenon depict a geometric strain proportional to the applied electric field known as the converse piezoelectric performance, as revealed by Gabriel Lippmann in 1880 (Uchino, 2010). After these studies on quartz material for energy harvesting that produces electricity when subjected to a mechanical stress, low outcome was reported for quartz as a result of its brittleness and poor electrical conductivity. However, observing the drawbacks of quartz as a piezoelectric material in energy scavenging, another piezoelectric material known as lead zirconate titanate (PZT) was developed, which has become the most commonly used material for energy harvesting (Raghu, Sastry, and Mohammed, 2015). Piezoelectric ceramic material, used in the design of transducer devices for energy harvesting, has been adopted for the mechanism of transferring ambient vibration (mechanical energy) into electrical energy that could be stored in energy devices and later utilized in powering other devices. Today, lead zirconate titanate power generation is used as a conventional alternative over traditional power sources used in the operation of some kinds of sensors or micro electro–mechanical system devices. The processes of self-power generation using the vibration loads of structures and human motions have all received attention. Therefore, the importance of this technology being used as the power supply for electrodevices and as sensors for monitoring the vibration status of buildings, bridges, and machine equipment has been a welcome development for researchers (Shohei et al., 2013). Moreover, studies on the analysis of vibration power generation using piezoelectric elements as a power supply to drive micro devices have greatly been reported in the literature (Glynne-Jones, Beeby, and White, 2001; Arms et al., 2005). However, the outcome of the studies on vibration power generation was found in different ways, for example, the human motion (Gorlatova et al., 2014), ocean wave (Lewis, 2011), and the gathering of strain from beam particles in structures (Pfeifer, Leming, and Rumpf, 2001). Also, energy captured from mechanical loading generated from the ground in the form of compressive forces as human beings move toward the floor of a building is noted to be another sustainable means to generate electrical energy (Bischur and Schwesinger, 2012). However, along this line, Umeda et al. (1996) developed an electrical model of lead zirconate titanate in converting mechanical impact energy to electrical power. Furthermore, another experiment was carried out on generating electricity using piezoelectric materials by Dayou et al. (2009). In their finding, it was reported that lead zirconate titanate as a piezoelectric material showed a better outcome adopting the Euler–Bernoulli method. Hailu et al. (2018), on the other hand, carried out a study on the highway piezoelectric power supply system. In their study, a piezoelectric energy harvester was manufactured in advance and embedded in the pavement along the roadway of the test site, considering the contact point of vehicle tires. However, it was reported that the PZT–5H piezoelectric material used exhibited a better result in terms of excellent power-generating performance. The open circuit voltage generated from the piezoelectric energy harvester in the actual road traffic conditions was higher than 250 V. The output voltage was reportedly sensitive to the vehicle speed and increased with the increase in speed. The study deduced that energy generated by the piezoelectric energy harvester would be supplied to the light-emitting diode (LED) lamp, which could solve the challenge of the high cost of the power supply system for the mountain highway in line with the notion of sustainable energy development. Paradiso et al. (2005) also reported that PZT piezoelectric material has been the most commonly used piezoelectric material for vibration energy harvesting. However, lead zirconate titanate as a piezoelectric material for a transducer in terms of energy capturing has been recommended over the years but still faces some limitations like brittleness. This remains a major issue that was discovered in quartz as a piezoelectric material during application, although PZT still remains more efficient than quartz (Adnan, Mahmoud, and Mohamed (2017). Apart from PZT brittleness, other imperfections have also been reported by many researchers, such as the toxicity effect, greenhouse effect, and contamination of seas and rivers. With respect to this observation, the European community pointed out the restrictions over the utilization of hazardous substances, and this clearly reduced the application of lead (Pb)-based piezoelectric material in electronic devices. Furthermore, another drawback of conventional piezoelectric PZT ceramics was as a result of incessant behavior in hysteresis and aging effects when it comes to huge electric fields (Uchino, 2010). All these aforementioned imperfections of PZT, however, lead to the development of lead-free piezoelectric materials in designing piezoelectric transducers for energy harvesting. The effectiveness and potential of any energy conversion depend on the size, material properties, load or pressure, and vibration, affecting the piezoelectric material. It was also noted that high thickness and higher forces do generate suitable surface charge (Elham et al., 2017a). In enhancing the potential of PZT after its restriction, other studies were carried out on PZT for improving its performance. However, PZT as an inorganic ceramic was found to be brittle with low expansion characteristics. Again, a study revealed that PZT required maximum protection in a harsh environment (Bischur and Schesinger, 2012), such as salt water, moisture, noxious gases, mechanical stress, and even an acidic environment, hence resulting in more limitations to its application. In addition, it is worth noting that this brittleness, which is characteristic of PZT material, actually contributes to the rapid failure of a piezoelectric transducer made of PZT in service when a load or vibration is applied in the cyclic form. Yao et al. (2014) provided evidence about the presence of internal stress on the domain of lead zirconate titanate piezoelectric material after mechanical cyclic loading during their study on the fatigue behavior of PZT material. This internal stress in the structure of the PZT material results in inhomogeneity strain and, as such, reduces the property potential of the piezoelectric transducer in energy harvesting when it comes to the piezoelectric strain coefficient, as noted by the author. Another problem of a PZT material is that when a pressure load greater than 50 kbar is applied to PZT, a rapid decrease in output current occurs (Sastry, Mohammed, and Raghu, 2015). This makes the electromechanical coupling of PZT material low because Kumar et al. (2013) stated that for a higher output voltage to occur, there must be a high coupling coefficient of piezoelectric material. Again, considering heel-strike generators using piezoelectric material as a result of high impact forces generated during walking (Starner and Paradisco, 2004), the benefits of piezoelectric materials are mostly used for heel-strike devices, based on little effort of incorporating them into shoes, meaning that a material with a superior power to weight ratio is needed (Riemer, 2011). Herein, PZT as a piezoelectric material might not be accepted as a result of its density. Furthermore, another issue with PZT is the volatility of lead oxide (PbO) during sintering at about 800°C (Jordan and Ounaies, 2001). With this volatility, there might be hazardous effects of lead on human health within such an environment, and it was also reported that PZT elastic properties can vary as much as 5%, and dielectric properties, 20% within the same batch of production. This is as a result of the rapid volatility of lead oxide (Jordan and Ounaies, 2001). In addition, it was noted that PZT-0 with a high lead content cracked during sintering due to large spontaneous strains and thermal expansion anisotropy accompanied with lead titanate materials at the point of cooling from the sintering temperature (Karapuzha et al., 2016). According to Bermejo et al. (2012), in the mechanical characterization of PZT ceramics for the multilayer piezoelectric, it was observed that during poling, a crack occurred in the pole multilayer metal PZT ceramic composite, as can be seen in Figure 1, hence its limitation.
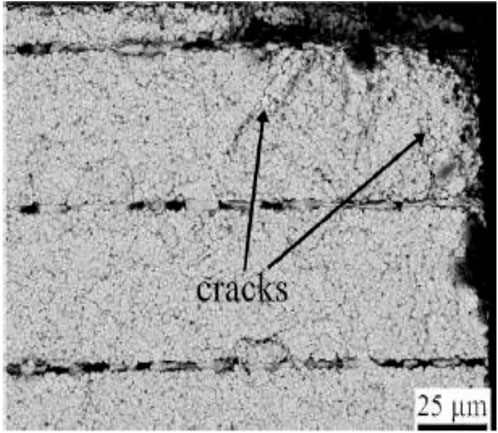
FIGURE 1. Scanning electron microscopic view of the fractured surface of the poled multilayer PZT ceramic composite reproduced from the study by Bermejo et al. (2012).
With all these limitations to PZT piezoelectric material, lead-free piezoelectric material was found to be a promising material and was employed in order to meet up in energy harvesting using a piezoelectric transducer. Lead-free piezoceramics were actually developed after 1999 (Uchino, 2010). Figure 2 shows the statistics of lead-free piezoelectric ceramic materials, and this came into existence after a patent statistical study. Although the application of lead-free piezoelectric material was not actually adopted until more percentage of lead on PZT was noticed in creating hazards during processing, it is greatly toxic to the environment when disposed; however, this outcome of PZT material as a hazardous material led to the attention of regulatory agencies worldwide in putting strict restrictions on the use of lead (Elena and Jacob, 2010). Table 1 lists the chemical composition of bulk PZT, as revealed in EDAX analysis, during characterization of porous PZT piezoelectric ceramics. The results of the EDAX analysis showed that there was a reduction in the weight concentration of the elements, and this could be from lead and oxygen as a result of their volatile behavior, hence causing a problem with lead (Pb) side effects on human health.
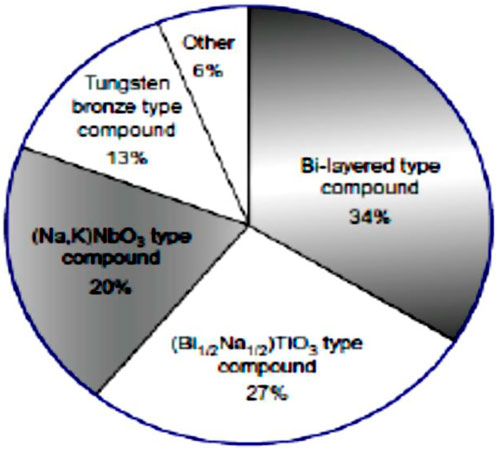
FIGURE 2. Patent statistics for the lead-free piezoelectric (Uchino, 2010).
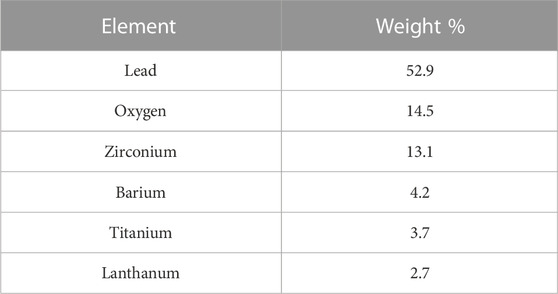
TABLE 1. Chemical composition of PZT using EDAX analysis reproduced from the study by Praveen et al. (2018).
In a nutshell, the piezoelectricity of any material can be determined by its piezoelectric coefficient and/or piezoelectric modulus (G). The piezoelectric modulus can be described as a change in volume that occurs in a piezoelectric material when subjected to an electric field (Indrani and Nitin, 2013), and it has been reported in the literature that the piezoelectric coefficient depends on crystal orientation (Damjanovic, 1998). With this, piezoelectricity in zinc oxide (ZnO) was noted because of its versatility as a metal oxide semiconductor material. In addition, zinc oxide nanostructures depict anisotropic piezoelectric properties as a result of their structural non-central symmetry (Kong and Wang, 2003; Kwon et al., 2008). In noticing the properties of zinc metal oxide, which happened to be lead-free, Lee et al. (2011) examined ZnO nanowires as a piezoelectric material for energy harvesting, and results showed that a higher output voltage suitable for driving small commercial electronic devices was generated. In addition, in previous research works on zinc oxide, better properties were recorded compared to PZT; for example, the density of zinc oxide was found to be lower than that of lead zirconate titanate. Another lead-free piezoelectric material developed was barium titanate (BaTiO3). Barium titanate (BaTiO3) was the first discovered ferroelectric oxide with a perovskite structure (Robert, 1947). This ceramic material was found to exhibit a relatively high electromechanical coupling factor of about 0.50 and a good piezoelectric strain constant mode, which is incompletely adopted for piezoelectric applications, for example, sonars. Although, the working temperature range of barium titanate was reported to be small for real applications because barium titanate has a low Curie temperature of about 120–135°C (Takahashi et al., 2006). Therefore, to enhance the Curie temperature of barium titanate, the doping process was adopted, and potassium as the doping agent, hence the bismuth potassium titanate, which happened to be a typical lead-free ferroelectric with a perovskite structure of tetragonal symmetry at ambient temperature and a higher temperature of about 380°C (Buhrer, 1962). Seeing the properties of some lead-free piezoelectric materials, like barium titanate, it is a welcome development in using it to produce piezoelectric transducers for energy harvesting when doped. However, in doing so, it results in the reduction of environmental damage when disposing piezoelectric product waste (Tadashi, 2013) than lead zirconate titanate (PZT) mentioned previously in this review paper. In addition, barium titanate as a piezoelectric material continues to serve as a model system for more fundamental investigations for technological applications (Rogan et al., 2003). Thus, as lead-free piezoelectric materials are reportedly an alternative to piezoelectric materials, owing to the growing environmental concerns about the toxicity of lead-based piezoelectric materials, Zhao et al. (2018) investigated the high piezoelectricity in BaTiO3 using multiphase convergence with broad structural flexibility. In their study, an ultrahigh piezoelectric constant of 700 pC/N in BaTiO3 ceramic over a wide composition range was recorded. It was deduced that the lead-free piezoelectric material exceeds the performance of the majority of lead-based piezoelectric systems, including PZT-5H, in the temperature range of 10–40°C. Moreover, Dogrusoz et al. (2021) reported on the PZT-5H and PZT-8 type piezoelectric effects on the cycling stability of multiwall carbon nanotubes containing anode materials. In characterizing the resultant composites, results show that the addition of the PZT material in the composites improved its capacity value (420 mA/hg), which is about a 300% improvement in comparison with the pure composite without PZT. In another study, Yang et al. (2021) improved the piezoelectric output capability of a piezoelectric mechanical energy harvester via the development of a 3D porous structure of polyvinylidene fluoride/BaTiO3 by the assisted selective laser sintering process. From the experimental results under the synergistic influence of BaTiO3, a high output with an output voltage of 20.9 V and a current density of about 0.371 nA/mm2 were recorded. In the study, it was concluded that the developed piezoelectric energy harvester can directly light up 11 green LEDs and charge a 1-μF commercial capacitor to 4.9 V within 180 s, establishing that the BaTiO3 solid solution with the pseudo-cubic phase has received much attention based on their large strains for potential piezoelectric multilayer actuator applications. Yuan et al. (2021), on the other hand, examined the strain and electrical properties of Li2CO3 sintering aid modified 0.64BiFeO3–0.36BaTiO3 ceramics produced by the high-temperature sintering method. The experimental results indicate that the dielectric loss and strain hysteresis of BiFeO3–BaTiO3 were reduced by 40% and 47%, respectively, with a large strain of 0.3% (dielectric strength of 60 kV/cm). The reduced dielectric loss and strain hysteresis attributed from the improved relative density decreased the concentration of defects and partial phase transition from partial pseudo-cubic to rhombohedral symmetry by Li2CO3 incorporations. The observed low dielectric loss and reduced strain hysteresis of the ceramics demonstrate that they are promising candidate materials for high-temperature and lead-free piezoelectric actuator applications. Wang et al. (2018) also reported on the piezoelectric property enhancement of BiFeO3–BaTiO3 on calcium-doped BiFeO3–BaTiO3 ceramics fabricated by the solid-state reaction process. The results revealed that calcium doping has little effect on the crystal structure of the resultant ceramic material, while notable grain growth occurred. Enhanced piezoelectric characteristics with a piezoelectric coefficient of 168 pC/N, a planar electromechanical coupling factor of 0.28, a maximum strain of 0.146%, and high thermal stability are recorded at 0.75% calcium-doped ceramics. The mechanism, which attributes to the improved piezoelectric properties, could be the stability of the long-range ferroelectric state at the high-temperature and high-degree poling-induced domain structure of the doped ceramic. The results, in other words, evidence the use of lead-free piezoceramics for energy applications.
Energy generation by different piezoelectric materials
Piezoelectric material in generating electricity has been a major material used in the design and fabrication of piezoelectric transducer devices for energy capturing. However, Table 2 shows generated power values by different company technology methods using a transducer device manufactured with piezoelectric material. In addition, there are other technologies or models in energy harvesting apart from the floor which can be found in Zhang, Li, and Yu (2016).
Conclusion
In this review article, an attempt has been made to discuss piezoelectric material on transducer technology for energy harvesting. This was actually achieved with little available literature. In the review study, it was noted that lead zirconate titanate was commonly used for piezoelectric transducers, but because of its shortcomings, such as mechanical failure, the aging effect when subjected to an electric field, and the hazardous effect within the human environment during disposal resulted in its restriction. However, lead-free piezoelectric material was developed and started being used in the fabrication of transducer devices. From the literature reviewed, it was noted that better properties were observed in lead-free piezoelectric material without hazardous effects than in lead zirconate titanate (PZT). This review article also demonstrated that electricity could be generated with no negative impact on human life and surroundings when a lead-free piezoelectric material is employed fully in the design and manufacturing of piezoelectric transducer devices for energy harvesting. However, there is a need for future study in the improvement of piezoelectric properties of lead-free piezoelectric materials, for example, BaTiO3, for better performance during service. As such, the authors recommend the incorporation of nanoparticles with a high strain output, high strain (charge) constant and permittivity, low mechanical quality factor, and excellent thermal stability in lead-free piezoceramics in the design of piezoelectric transducer components using the Taguchi design of experiment and spark plasma sintering processing methods.
Author contributions
Study conception and design: VO and AP; draft manuscript preparation: VO, OM, and AP. All authors proofread the manuscript and approved the final version of the manuscript.
Acknowledgments
The authors appreciate the Tshwane University of Technology for granting access to their e-library.
Conflict of interest
The authors declare that the research was conducted in the absence of any commercial or financial relationships that could be construed as a potential conflict of interest.
Publisher’s note
All claims expressed in this article are solely those of the authors and do not necessarily represent those of their affiliated organizations, or those of the publisher, the editors, and the reviewers. Any product that may be evaluated in this article, or claim that may be made by its manufacturer, is not guaranteed or endorsed by the publisher.
References
Adhithan, A., Vignesh, K., and Manikandan, M. (2015). Proposed method of foot step power generation using piezo electric sensor. Int. Adv. Res. J. Sci. Eng. Technol. 2, 25–29. doi:10.17148/1ARJSET.2015.2406
Adnan, M. E., Mahmoud, Y. M. G., and Mohamed, E. (2017). Feasibility study for using piezoelectric energy harvesting floor in buildings’ interior space. Energy Procedia 115, 114–126. doi:10.1016/j.egypro.2017.05.012
Ariel, S. (2016). Electricity generating dance floors and other miracles of piezoelectricity. https://www.good.is/articles/electricty-generating-dance-floors-and-other miracles-of-piezoelectricity.
Arms, S. W., Townsend, C. P., Churchill, D. L., Galberath, J. H., and Mundll, S. W. (2005). “Power management for energy harvesting wireless sensor,” in Smart structures and meterials, smart electronics, MEMS, bio-MEMS and nanotechnology. Editor V. K. Varadan (Proc. SPIE), 5763, 267. New York.
Beeby, S. P., Tudor, M. J., and White, N. M. (2006). Energy harvesting vibration sources for microsystems applications. Meas. Sci. Technol. 17, 175–195. doi:10.1088/0957-0233/17/12/r01
Bermejo, R., and Deluca, M. (2012). Mechanical characterization of PZT ceramics for multilayer piezoelectric actuators. J. Ceram. Sci. Technol. 3 (4), 159–168.
Bischur, E., and Schwesinger, N. (2012a). “Energy harvesting from floor using organic piezoelectric modules,” in Power Engineering and Automation Conference (PEAM) (IEEE). Wuhan, China.
Buhrer, C. F. (1962). Some properties of bismuth perovskites. J. Chem. Phys. 36 (3), 798–803. doi:10.1063/1.1732613
Chennault, K. A. C., Thambi, N., and Sastry, A. M. (2008). Powering micro electromechanical system (MEMS) portable devices - a review of non regenerative and regenerative power supply systems with special emphasis on piezoelectric energy. Smart Mater. Struct. 17 (4), 1–33. doi:10.1088/0964-1726/17/4/043001
Curie, J., and Curie, P. (1880). Development via compression of electric polarization in hemihedral crystals with inclined faces. bulmi. 3, 90–93. doi:10.3406/bulmi.1880.1564
Dayou, J., Man-Sang, C., Dalimin, M. N., and Wang, S. (2009). Generating electricity using piezoelectric material. Borneo Sci. 24, 47–51.
Damjanovic, D. (1998). Ferroelectric, dielectric and piezoelectric properties of ferroelectric thin films and ceramics. Rep. Prog. Phys. 61 (9), 1267–1324. doi:10.1088/0034-4885/61/9/002
Doğrusöz, M., Demirkan, M. T., and Çakan, R. D. (2021). Investigation of PZT-5H and PZT-8 type piezoelectric effect on cycling stability on Si-MWCNT containing anode materials. Turk. J. Chem. 45 (5), 1551–1558. doi:10.3906/kim-2102-62
Elena, A., and Jacob, L. J. (2010). Advances in lead-free piezoelectric materials for sensors and actuators. Sensors 10, 1935–1954. doi:10.3390/s100301935
Elham, M. N., Noor Amila, W. Z., and Balbir Singh, M. (2017b). A review of walking energy harvesting using piezoelectric materials. IOP Conf. Ser. Mat. Sci. Eng. 291, 012026–012028. doi:10.1088/1757-899x/291/1/012026
Elham, M. N., ZawawiAmila Wan Abdullah, N., and Singh Mahinder Singh, B. (2017a). A review of walking energy harvesting using piezoelectric materials. IOP Conf. Ser. Mat. Sci. Eng. 291 (1), 012026. doi:10.1088/1757-899x/291/1/012026
Glynne-Jones, P., Beeby, S. P., and White, N. M. (2001). Towards a piezoelectric vibration-powered microgenerator. IEE Proc. Sci. Meas. Technol. 148 (2), 68. doi:10.1049/ip-smt:20010323
Gorlatova, M., Sarik, J., Grebla, G., Cong, M., Kymissis, I., and Zussman, G. (2014). Movers and shakers: Kinetic energy harvesting for the internet of things. SIGMETRICS Perform. Eval. Rev. 42, 407–419. doi:10.1145/2637364.2591986
Hailu, Y., Linbing, W., Bin, Z., Ya, W., and Qian, Z. (2018). A preliminary study on the highway piezoelectric power supply system. Int. J. Pavement Res. Technol. 11, 168–175. doi:10.1016/j.ijprt.2017.08.006
Indrani, D., and Nitin, A. (2013). Piezoelectric energy generation and harvesting at the nano-scale: Materials and devices. Nanomater. Nanotechnol. 3, 21. doi:10.5772/56941
Jordan, T. L., and Ounaies, Z. (2001). Piezoelectric ceramics characterisation. Virginia, VA, USA: ICASE, NASA Langley research center hampton.
Kanani, B. D. (2015). Electrical measurements and measuring instruments. Vasan Gandhinagar: Institute of engineering and technology.
Karapuzha, A. S., James, N. K., Khanbareh, H., Van der Zwaag, S., and Groen, W. A. (2016). Structure, dielectric and piezoelectric properties of donor doped pzt ceramics across the phase diagram. Ferroelectrics 504 (1), 160–171. doi:10.1080/00150193.2016.1240571
Kim, H. S., Kim, J. H., and Kim, J. (2011). A review of piezoelectric energy harvesting based on vibration. Int. J. Precis. Eng. Manuf. 12 (6), 1129–1141. doi:10.1007/s12541-011-0151-3
Kong, X. Y., and Wang, Z. L. (2003). Spontaneous polarization-induced nanohelixes, nanosprings, and nanorings of piezoelectric nanobelts. Nano Lett. 3 (12), 1625–1631. doi:10.1021/nl034463p
Kumar, B., and Kim, S. (2012). Energy harvesting based on semiconducting piezoelectric ZnO nanostructures. Nano Energy. Kanpur, India 1 (3), 342–355. doi:10.1016/j.nanoen.2012.02.001
Kumar, D., and Chaturvedi, P. (2013). IIT Kanpur.Piezoelectric energy harvesting from vibration induced deformation of floor tilesSixth National Power Electronics Conference (NPEC). 2013, Kanpur, India.
Kwon, S., Hong, W., Jo, G., Maeng, J., Kim, T., Song, S., et al. (2008). Piezoelectric effect on the electronic transport characteristics of ZnO nanowire field-effect transistors on bent flexible substrates. Adv. Mat. 20 (23), 4557–4562. doi:10.1002/adma.200800691
Lee, M., Lee, J., Lee, C. S., Hong, S., and Wang, Z. L. (2011). Self-powered environmental sensor system driven by nanogenerators. Energy Environ. Sci. 4, 3359–3363. doi:10.1039/c1ee01558c
Lewis, A. (2011). “Ocean energy,” in IPCC special report on renewable energy sources and climate change mitigation. Editors O. Edenhofer, R. Pichs-Madruga, Y. Sokona, K. Seyboth, P. Matschoss, S. Kadneret al. (Cambridge, United Kingdom and New York, NY, USA.
Mitcheson, P. D., Yeatman, E. M., Rao, G. K., Holmes, A. S., and Green, T. C. (2008). Energy harvesting from human and machine motion for wireless electronic devices. Proc. IEEE 96 (9), 1457–1486. doi:10.1109/jproc.2008.927494
Mohd Asry, A. M., Mustafa, F., Ishak, M., and Ahmad, A. (2019). Power generation by using piezoelectric transducer with bending mechanism support. Int. J. Power Electron. Drive Syst. (IJPEDS) 10, 562–567. doi:10.11591/ijpeds.v10.i1.pp562-567
Paradiso, J. A., and Starner, T. (2005). Energy scavenging for mobile and wireless electronics. IEEE Pervasive Comput. 4, 18–27. doi:10.1109/mprv.2005.9
Pfeifer, K. B., Leming, S., and Rumpf, A. (2001). Embedded self-powered micro sensors for monitoring the surety of critical buildings and infrastructures. SAND2001-3619 Unltd. Release Print. 3, 3–6.
Praveen, K. B., Bhupender, R., and Rajan, K. M. (2018). Characterization of high porous PZT piezoelectric ceramics by different techniques. Def. Sci. J. 68 (5), 500–504. doi:10.14429/dsj.68.12315
Raghu, C. G., Sastry, V. R., and Mohammed, S. M. (2015). Piezo-gen - an approach to generate electricity from vibrations. Procedia earth Planet. Sci. 11, 445–456. doi:10.1016/j.proeps.2015.06.044
Ramkrishnaa, S. N., Nikesha, C., Allamrajub, V. K., and Korlac, S. (2016). Comparative study between tapping and straining for effective energy harvesting using piezoelectirc disc actuators. National conference on MEMS, smart materials, structures and systems. Kanpur, India: IIT Kanpur.
Riemer, R., and Shapiro, A. (2011). Biomechanical energy harvesting from human motion: Theory, state of the art, design guidelines, and future directions. J. Neuroengineering Rehabilitation 8 (1), 22–13. doi:10.1186/1743-0003-8-22
Robert, S. (1947). Dielectric and piezoelectric properties of barium titanate. Phys. Rev. 71, 890–895. doi:10.1103/physrev.71.890
Rogan, R. C., Tamura, N., Swift, G. A., and Ustundag, E. (2003). Direct measurement of triaxial strain fields around ferroelectric domains using X-ray microdiffraction. Nat. Mat. 2, 379–381. doi:10.1038/nmat901
Sastry, V. R., Mohammed, S. M., and Raghu, C. G. (2015). Piezo-gen - an approach to generate electricity from vibrations. Procedia Earth Planet. Sci. 11, 445–456. doi:10.1016/j.proeps.2015.06.044
Shohei, Y., Shigeru, F., Masaaki, I., Tokio, K., and Takeshi, M. (2013). Characterization of the piezoelectric power generation of pzt ceramics under mechanical force DTIP. 2013 Symposium on Design, Test, Integration and Packaging of MEMS/MOEMS (DTIP), Barcelona, Spain.
Starner, T., and Paradiso, J. A. (2004). Human generated power for mobile electronics. Low. Power Electron. Des. 45, 1–35. doi:10.1201/9781420039559.ch45
Tadashi, T. (2013). “Lead-free piezoelectric ceramics,” in Handbook of advanced ceramics applications processing, and properties. Elsevier, 429–446.
Takahashi, H., Numamoto, Y., Tani, J., and Tsurekawa, S. (2006). Piezoelectric properties of BaTiO3 ceramics with high performance fabricated by microwave sintering. Jpn. J. Appl. Phys. (2008). 45, 7405–7408. doi:10.1143/jjap.45.7405
Uchino, K. (2010). Development of piezoelectric materials and the new perspective”. State College, PA, USA, Pennsylvania State University, 1–39.
Umeda, M., Nakamura, K., and Ueha, S. (1996). Analysis of the transformation of mechanical impact energy to electric energy using piezoelectric vibrator. Jpn. J. Appl. Phys. (2008). 35 (1), 3267–3273. doi:10.1143/jjap.35.3267
Wang, J., Zhou, C., Li, Q., Yang, L., Xu, J., Chen, Q., et al. (2018). Simultaneously enhanced piezoelectric properties and depolarization temperature in calcium doped BiFeO3-BaTiO3 ceramics. J. Alloys Compd. 748, 758–765. doi:10.1016/j.jallcom.2018.03.174
Yang, C., Chen, F., Sun, J., and Chen, N. (2021). Boosted mechanical piezoelectric energy harvesting of polyvinylidene fluoride/barium titanate composite porous foam based on three-dimensional printing and foaming technology. ACS omega 6 (45), 30769–30778. doi:10.1021/acsomega.1c04998
Yao, Y., Xu-Sheng, W., Yan-Xia, L., and Xi, Y. (2014). Fatigue behaviors in PZT ceramics induced by mechanical cyclic load. Ferroelectr. Lett. Sect. 41 (4-6), 123–128. doi:10.1080/07315171.2014.956021
Yuan, H., Li, L., Hong, H., Ying, Z., Zheng, X., Zhang, L., et al. (2021). Low sintering temperature, large strain and reduced strain hysteresis of BiFeO3–BaTiO3 ceramics for piezoelectric multilayer actuator applications. Ceram. Int. 47, 31349–31356. doi:10.1016/j.ceramint.2021.08.008
Zhang, S. J., Li, F., and Yu, F. P. (2016). “Piezoelectric materials for cryogenic and high-temperature applications,” in In structural health monitoring (SHM) in Aerospace Structures. Woodhead Publishing, 59–93. doi:10.1016/B978-0-08-100148-6.00003-2
Keywords: transducer, energy harvesting, lead zirconate titanate (piezoelectric ceramic), lead-free piezoelectric materials, electromechanical coupling characteristics
Citation: Ogbonna VE, Popoola API and Popoola OM (2022) Piezoelectric ceramic materials on transducer technology for energy harvesting: A review. Front. Energy Res. 10:1051081. doi: 10.3389/fenrg.2022.1051081
Received: 22 September 2022; Accepted: 30 November 2022;
Published: 22 December 2022.
Edited by:
Iskander Tlili, National School of Engineers of Monastir, TunisiaReviewed by:
Hitesh Panchal, Government Engineering College, IndiaSami Ullah Khan, COMSATS University Islamabad, Pakistan
Copyright © 2022 Ogbonna, Popoola and Popoola. This is an open-access article distributed under the terms of the Creative Commons Attribution License (CC BY). The use, distribution or reproduction in other forums is permitted, provided the original author(s) and the copyright owner(s) are credited and that the original publication in this journal is cited, in accordance with accepted academic practice. No use, distribution or reproduction is permitted which does not comply with these terms.
*Correspondence: V. E. Ogbonna, b2dib25uYXZpY3Rvcjg3QGdtYWlsLmNvbQ==