- 1Institute of Water Resources and Electric Power, Xi’an University of Technology, Xi’an, China
- 2State Key Laboratory of Eco-Hydraulics in Northwest Arid Region, Xi’an University of Technology, Xi’an, China
Integrated systems required for renewable energy use are under development. These systems impose more stringent control requirements. It is quite challenging to control a pumped storage system (PSS), which is a key component of such power systems. Because of the S-characteristic area of the PSS pump turbine, traditional proportional-integral-derivative (PID) control induces considerable speed oscillation under medium and low water heads. PSSs are difficult to model because of their nonlinear characteristics. Therefore, we propose a machine learning (ML)-based model predictive control (MPC) method. The ML algorithm is based on Koopman theory and experimental data that includes PSS state variables, and is used to establish linear relationships between the variables in high-dimensional space. Subsequently, a simple, accurate mathematical PSS model is obtained. This mathematical model is used via the MPC method to obtain the predicted control quantity value quickly and accurately. The feasibility and effectiveness of this method are simulated and tested under various operating conditions. The results demonstrate that the proposed MPC method is feasible. The MPC method can reduce the speed oscillation amplitude and improve the system response speed more effectively than PID control.
Introduction
Sustainable energy has become increasingly important due to the present-day shortage of and pollution from fossil fuels (Albuyeh, 2013; Menon, 2013; Bozchalui, 2015; Brahman and Jadid, 2015; Zhang et al., 2015; Güney, 2019; Hasan Mehrjerdi, 2021; Rajvikram Madurai Elavarasan et al., 2021; Thomas Sattich et al., 2021). Consequently, renewable power generation technologies such as wind, solar, hydro, and biomass are used widely (Rajkumar, 2011; Francesco Calise and Piacentino, 2014; Pazouki, 2014; Zhaoyang Dong and Wen, 2014; Pazouki, 2016; Elena Smirnova et al., 2021; Eric O Shaughnessy et al., 2021; Olusola Bamisile et al., 2021; Pradhan et al., 2021). Simultaneously, energy storage technologies such as fuel cells, hydrogen storage, supercapacitors, and pumped storage systems (PSSs) have attracted increasing attention (Yves Pannatier et al., 2010; Pazouki, 2014; Brahman and Jadid, 2015; Zhang et al., 2015; Pazouki, 2016; Li et al., 2017a; Schmidt et al., 2017). PSSs are an early form of modern energy storage and are important to the development of sustainable power systems. A PSS operates economically by generating electricity during peak demand periods and pumping water to storage tanks during off-peak periods; it thus plays an important role in the economical operation of conventional power systems and facilitates the efficient use of renewable energy (Gurung et al., 2016; van Meerwijk et al., 2016; Kocaman and Modi, 2017; Min and Kim, 2017; Ruppert et al., 2017; Sam and Gounden, 2017; Julian David Hunt et al., 2020).
As the scale of PSSs and the extent to which they are utilized in the development of sustainable power systems increase, their precise control has gradually emerged as an important area of research. Existing PSS control methods can be divided into two main categories. The methods within the first category use proportional-integral-derivative (PID) control. These methods are based mainly on parametric design of each link within the PID controller. Some representative studies follow.
Shi et al. used the d-q axis vector of a generator to design PI parameters with the aim of achieving highly efficient peak regulation and frequency suppression within a power grid (Yifeng Shi et al., 2020). Zhao et al. used the power priority control and speed priority control strategies to design PID parameters, in addition to simulating and verifying the superior control effect of the power control strategy (Yves Pannatier et al., 2010; Guopeng Zhao and Ren, 2021). Several other advanced algorithms and theories have been applied as well. Xu et al. designed a fuzzy PID controller based on the F fractional-order integrator and differentiator (FOPID) (Podlubny, 1999) by using a search algorithm. This controller optimizes the FOPID method parameters, increases the convergence speed, and yields superior results (Xu et al., 2016; Xu et al., 2018). Gao et al. used Hopf bifurcation theory to determine the algebraic stability criterion of a PSS in order to obtain ideal PID controller parameters that correspond to a stable system state (Chunyang Gao et al., 2021a).
The control methods under the second category use optimization algorithms to determine the best approach to coping with the nonlinear behaviors of hydraulic systems. Schmidt et al. used a nonlinear optimization algorithm to determine the best stationary operating point of a PSS in order to minimize loss across the entire system and consider operating constraints systematically (Schmidt et al., 2017). Hou et al. used a multiobjective optimization algorithm to design a control strategy for starting a PSS in addition to establishing a simulation model based on a real system to verify the feasibility of the optimized control strategy (Hou et al., 2018; Hou et al., 2019). Pan et al. modeled a new stability criterion by using the particle swarm algorithm to optimize the parameters of a PSS controller; this criterion enhanced the independent response of the PSS significantly (Pan et al., 2021).
Among the various optimization control methods, the model predictive control (MPC) method has a robust theoretical foundation and substantial promise for practical applications. The most famous explanation is called “Open Loop Optimal Feedback” (Alamir and Allgöwer, 2008; Diego and Carrasco, 2011; Forbes MG et al., 2015). It richly illustrates the four layers of modeling, control, optimization, and logistics in the MPC control method and their relationship (Mayne, 2016; Shiliang Zhang et al., 2017; Sopasakis and Sarimveis, 2017; Ye et al., 2017). In recent years, the application of MPC to PSSs has gradually attracted the attention of scholars. Li et al. used the generalized nonlinear predictive control method to design a PSS controller and simulated start-up and speed disturbance processes under no-load conditions to verify controller robustness and efficiency (Li et al., 2017b). Liang et al. proposed an MPC strategy based on enumeration to determine the optimal switching time of a PSS with the objectives of increasing operational flexibility and promoting frequency regulation (Liang et al., 2019). Feng et al. proposed a new adaptive MPC strategy and conducted a simulation experiment to verify the superiority of this strategy in terms of adjusting the voltage and load and suppressing frequency oscillation (Chen Feng et al., 2021). Although MPC has the above advantages, it still has certain disadvantages when compared to traditional control methods. For instance, MPC modeling requires more expert knowledge and is time-consuming to perform using traditional methods (De Souza et al., 2010; Max Schwenzer et al., 2021. Fortunately, the continuous development of hardware equipment and control algorithms has decreased the MPC control time. If the control effect is particularly important, MPC is much better than traditional control methods.
Modeling is a key component of MPC but almost all systems used in relevant contexts are nonlinear; for example, the water pump turbine of a PSS has an S-characteristic area (Yin et al., 2014; Li et al., 2017a; Anilkumar et al., 2017; Zeng et al., 2017; Zhang et al., 2017). This increases the difficulty of modeling. A variety of modeling methods have been developed in response.
Huang et al. proposed a method of predicting the complete characteristics of a Francis pump turbine. Based on Euler’s equation and the velocity triangle at the runner, their method derives a mathematical model that completely describes the characteristics of the Francis pump turbine. The results of a simulation experiment indicated that their method was suitable for performing a priori simulations before measuring device characteristics (Huang et al., 2018). Gao et al. established a high-precision, variable-speed control model for a pump turbine based on the complete characteristic curve of the turbine in order to describe the characteristics of the variable speed units more effectively (Chunyang Gao et al., 2021b). Zhou et al. proposed a real-time accurate equivalent circuit model of a PSS via error compensation. This model reconciles the conflict between real-time online simulation and simulation accuracy under various operating conditions (Jianzhong Zhou et al., 2018).
In recent years, with the continual development of artificial intelligence technology, a few machine learning (ML) algorithms have yielded outstanding nonlinear system modeling results (R. Martin et al., 2015; J. Sánchez Oro et al., 2016; Li et al., 2016; Idowu et al., 2016; Robinson et al., 2017; Yong Ping Zhao et al., 2018; Kiely et al., 2019; Ayush Thada et al., 2021). The application of ML algorithms to PSS has emerged as an innovative idea. In this regard, Feng et al. established a PSS model by optimizing the initial learning parameters via prior knowledge learning and subsequently adopting a stepped control strategy and an artificial-sheep-algorithm-based rolling optimization mechanism. This model can replace the existing differential geometry model (Chen Feng et al., 2021). Zhao et al. introduced an improved Suter transformation-backpropagation (BP) neural network interpolation model and used it to establish a PSS model. This model can be divided into three parts: characteristic curve processing, data prediction, and interpolation. It can correct the characteristic curve of a pump turbine effectively (Zhigao Zhao et al., 2019). These modeling methods are innovative and represent meaningful research directions. However, the model machines and BP neural networks used in the aforementioned modeling methods have extremely complex structures and use large numbers of parameters. This increases the complexity of PSS control.
For these reasons, we propose using a MPC method based on an ML algorithm to model PSS control. This method can convert a nonlinear model into a linear model in high-dimensional space. The form of the obtained model is simple and few parameters are required. Thus, it is suitable for fast, accurate control processes. Our paper makes the following contributions to PSS development: 1) The pump-turbine partition model that we establish effectively solves the common problem of difficult modeling in the S-region and provides a feasible direction for research on pump turbines in the s-region. 2) The machine-learning algorithm that we propose makes full use of the data generated in the PSS; it is an effective way of combining experimental data with the actual system and improves the accuracy of the actual system model. 3) We use the proposed model within the MPC method; this solves the problem of large control errors in the PSS at low water heads. 4) Compared to traditional control methods, our proposed method can reduce the shock of the pumped storage system and reduce the control process adjustment time.
PSS Modeling
The overall MPC structure is illustrated in Figure 1. It comprises three parts: a controlled system (a PSS), a data collection component, and a control component. The PSS is composed of a pump turbine, servo mechanism, penstock, and generator. The function of the data acquisition component is to collect the data in the PSS and provide it to the control system. It includes a flow sensor, a torque sensor, a speed sensor, an opening sensor, and a pressure gauge, and is responsible for collecting five variables: the flow, torque, speed, guide vane opening, and water head. The control system includes model generators for pumps, turbines, servo systems, pipelines, and generators. Their task is to generate PSS component models that the controller can use. The control system also includes a predictor that generates a predictive model. In addition, the controller generates control instructions according to the optimized algorithm in order to manipulate the PSS control variables.
Five important state variables are used in the PSS:
ML Algorithm
To establish a simple, accurate PSS model, we propose an ML algorithm that can determine the linear relationships among state variables in high-dimensional space using the given data.
Related Principles
1) Assume that the set of all state variables
where
where
where
For nonlinear relationships, Koopman proposed the Koopman operator (KO), expressed in Eq. 4, in 1931. The KO can be used to represent the complete nonlinear relationship using a linear function. Notably, no universal method is available for selecting the observation function; it is usually selected based on the characteristics of the system and the analyst’s experience.
where
2) For each value of
where
We apply the KO to matrix
where
where
According to the Koopman principle, under a suitable observation function set,
where
where
The error is the deviation between the real value
where
3) When
where
ML Algorithm Flow
The ML algorithm flow is depicted in Figure 2. It consists of the following parts: data preprocessing, KO, establishment of the objective equation, estimation of the state variable value, error calculation, parameter determination, and determination of the fit model. The details follow:
Data Preprocessing
Experimental data are generated using the experimental platform. All
KO
The observation function set is selected according to theoretical principles and practical experience and applied to matrix
Establishing the Objective Equation
We establish the objective equation given in Eq. 9 and transform it into the form presented in Eq. 13.
where
Calculation of the Estimated Value
We perform singular value decomposition on
where
Next, matrix A can be expressed using Eq. 15. Its eigenvalue decomposition form is given in Eq. 16.
where
where
By substituting Eq. 15 into Eq. 16, we can obtain the linear model given in Eq. 17. The value of
where
Error Calculation and Parameter Determination
The error between the real and estimated values is expressed in the form given in Eq. 19. This expression is related to the parameter
Fit Model Determination
As previously mentioned, the form of the fitted model is given in Eq. 12. We use the least squares method to determine the coefficient
PSS Models
Pump Turbine Modeling Using an ML Algorithm
The pump-turbine model contains s-shaped regions and is a complex, nonlinear model. We use machine learning algorithms to model the pump-turbine by partition. The process is shown in the Figure 3. A detailed description of the modeling process is provided below.
The pump turbine model is based on two relational expressions. That is,
where
We use the preceding ML algorithm to establish the relationship between
The Relationship Between , , and
To analyze the relationship between
The error obtained using the proposed ML algorithm is depicted in Figure 4 (1-A). In all ranges, the vane opening satisfies the requirements outlined in this observation function set.
We use the observation function set given in Eq. 23 to analyze the relationship between
The ML parameter N is determined using the algorithmic flow shown in Figure 2. In actual operation, we continue to increase the value of N and calculate the error as shown in Eq. 19. When this error increases significantly, the prediction model does not match reality. The error at this point is the threshold. We use this N as the boundary of the segmented model. The technical details are as follows:
As
• The error corresponding to
• When
• When
Based on the aforementioned three scenarios, the ML algorithm divides the relationship between
The Relationship Between , , and
Much like
Based on the relationship between the torque and speed of a pump turbine, the observation function set given in Eq. 26 is used.
Much like the process used in step 1, we use the ML process in Figure 2 to determine the segment boundary. The technical details are as follows:
• The error corresponding to
• When
where
•For
The ML algorithm divides the relationship between
Fit Model
After obtaining the partitions, the principles described in Related Principles are used to establish polynomial models of
·P1 of
·P2 of
·P3 of
·P1 of
·P2 of
·P3 of
Comprehensive Area Model
Notably, the partition model is chosen because the device model includes multiple expressions, each of which is divided into multiple segments. Since these segments are related directly to differences and coverage, we divide them into multiple regions so that they can accurately represent the device model in a detailed manner. Herein, the partitions
· Area 1
Condition:
Model:
· Area 2
Condition:
Model:
· Area 3
Condition:
Model:
· Area 4
Condition:
Model:
· Area 5
Condition:
Model:
· Area 6
Condition:
Model:
Other Models
In the description of the pump turbine model, it is necessary to point out the relationship between unit and non-unit quantities, which is expressed using Eqs 34–36.
where
Servo Mechanism Model
The servo mechanism model is nonlinear; it considers the speed limit, position limit, position saturation limit, and suppression governor, as depicted in Figure 7. In this model,
Penstock System Model
The approximate elastic water hammer model is used to model the penstock system. Its expression is given in Eq. 37.
where
Motion Equation Model
When the generator is connected to the pump turbine, the torque of the turbine and the load torque generated by the generator must satisfy the motion equation (Eq. 38).
where
MPC Process
Model Prediction
After obtaining the model by using the method introduced in the preceding section, we can predict the value of the state variable. The process is depicted in Figure 8. The details of each module are introduced as follows.
1. Calculate the model calculation value
2. Subtract the model-calculated value
3. Calculate the model calculation value
4. Add the deviation value
5. Calculate the error
6. Judge whether the error is lower than the limit. If the error is lower than the limit, the prediction level meets the requirements and the prediction model is obtained directly. If the error exceeds the limit, return to step 2 and continue the model prediction process.
The predicted values of each of the PSS variables are as follows. Prediction using the pump turbine model:
Prediction using the conversion relationship between unit and non-unit quantities:
Prediction obtained using the penstock system model:
Prediction using the motion equation model:
Optimizer
In this study, we use optimization algorithms as the MPC strategy. The corresponding set of state variables is given in Eq. 46.
The goal of PSS control is to regulate the vane opening such that the turbine operates at the required speed and the system achieves the highest efficiency. Therefore, the objective function is the reciprocal of the turbine efficiency, as shown in Eq. 47.
The optimization constraints include equality and inequality constraints. The equality constraints are represented by the model predictions established in Eqs 39–45. The inequality constraints include the upper and lower limits of each state variable, as described in Eqs 48–52.
The optimization process uses the interior point algorithm, which works well in practice. It has been proven that in some cases, this method can solve a problem to a specified accuracy by performing operations on various polynomials that do not exceed the dimension of the problem.
Numerical Experiments and Analysis
To verify the effectiveness of MPC, we measured and collected data from a PSS in China and conducted simulation experiments using the MATLAB software environment (Mathworks, 2017). The experiment proceeded in three parts, each of which corresponded to no-load start up, frequency disturbance, or speed disturbance. The experiment was performed under medium and low water heads because the PSS easily enters the S-characteristic area under these head levels. We set the water head
No-Load Start-Up Condition
In this part of the experiment, the PSS was in the no-load condition and the pump turbine was started from a standstill. MPC and PID control were implemented when the startup speed reached 90% of the rated speed. The experiment was performed for 120 cycles, each of which ran for approximately 0.2 s. The speed results are depicted in Figure 9. The pump turbine state variable results are depicted in Figure 10. The results indicate that MPC performs better than PID control of PSSs because MPC provides a smaller overshoot and faster response speed.
Frequency Disturbance Condition
In this part of the experiment, the PSS was operated under no load. For the system frequency to be disturbed at the 10th cycle, the PSS speed needed to be increased to 1.02 times the rated speed. The experimental results obtained under MPC and PID control are depicted in Figure 11 and Figure 12. Both control methods can fulfill the frequency disturbance requirements. Under PID control, the speed overshoots the threshold and the response time is longer. In contrast, the speed overshoot is smaller and the new speed requirements are reached quickly under MPC control.

FIGURE 11. Speed variation in the presence of a frequency disturbance under 413 and 418 m of water head.
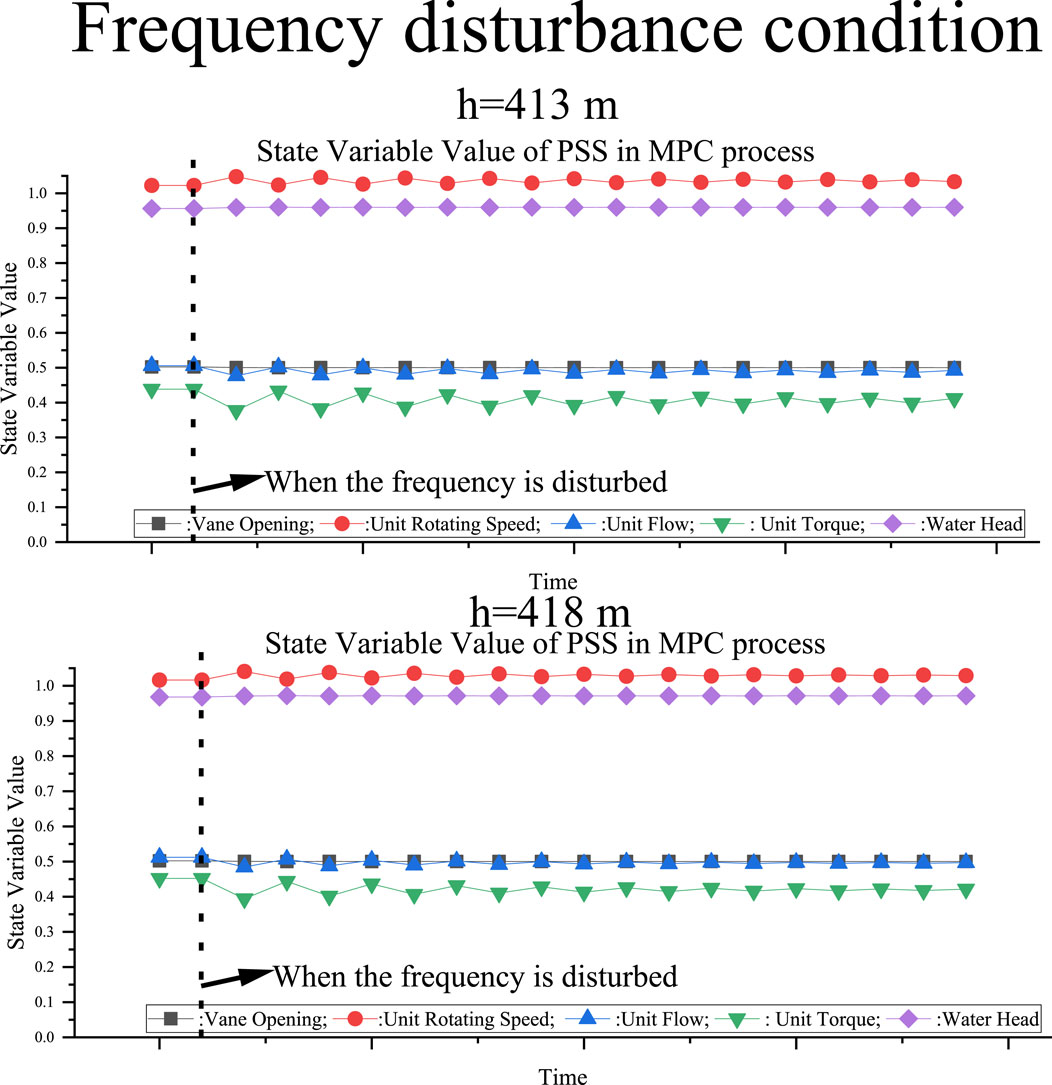
FIGURE 12. PSS MPC state variables in the presence of a frequency disturbance under 413 and 418 m of water head.
Speed Disturbance Condition
In this part of the experiment, the load generator was activated at the 10th cycle and the load torque was increased in steps. At this point, the speed of the pump turbine was disturbed such that it decreased abruptly. The experimental results obtained under MPC and PID control are depicted in Figure 13 and Figure 14. Under PID control, the speed is disturbed in the S-characteristic region. This produces strong oscillation and the speed takes substantial time to stabilize. In contrast, the speed oscillation amplitude is smaller and the speed stabilizes within a short time under MPC control.
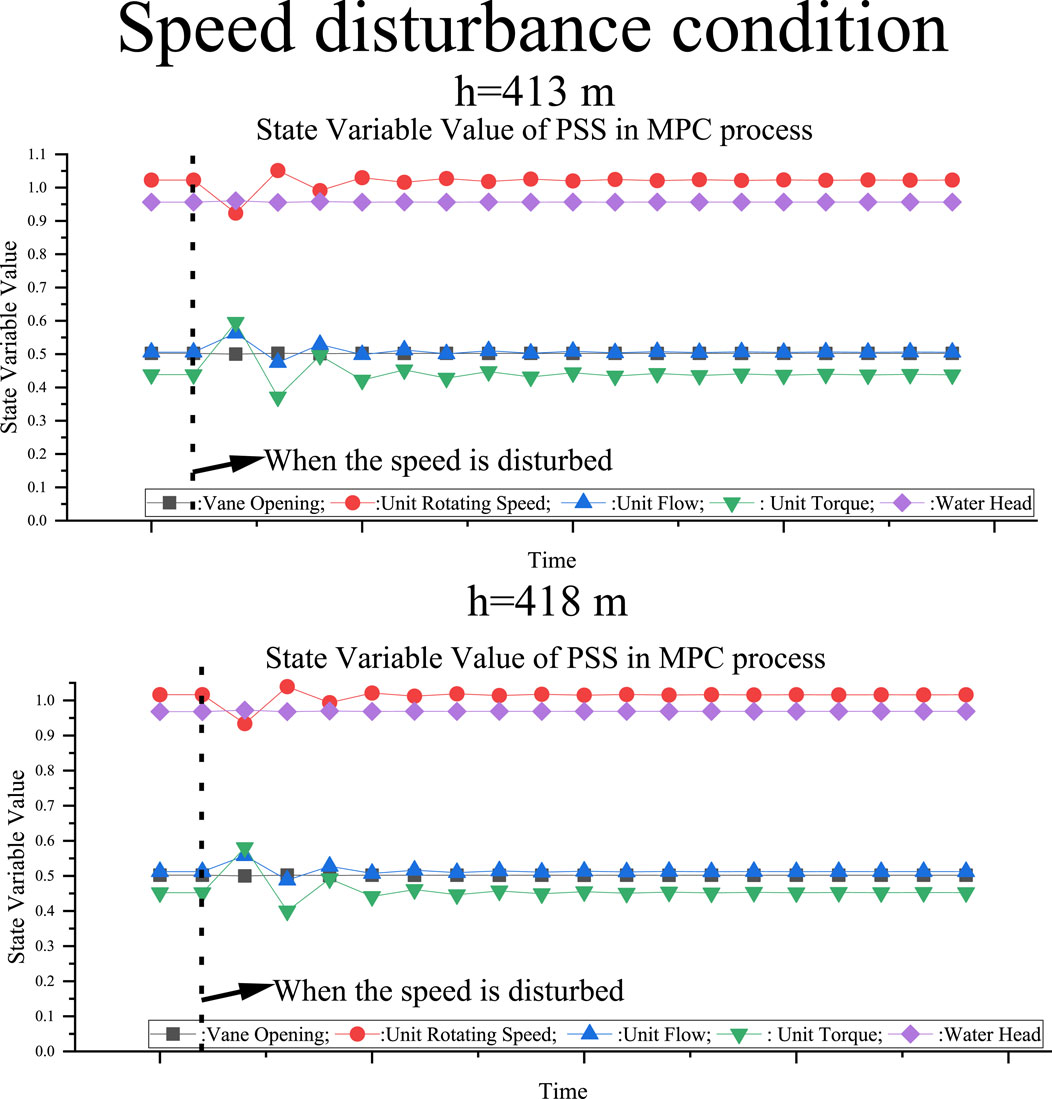
FIGURE 14. PSS MPC state variables in the presence of speed disturbances under 413 and 418 m of water head.
Advantages of MPC
The results described in the preceding section indicate that the MPC and PID control methods can fulfill PSS S-characteristic area control requirements that are otherwise difficult to meet. However, the MPC method offers the following advantages:
• The MPC method can achieve effective control under the conditions of no-load start-up, frequency disturbance, and speed disturbance.
• The model built using ML can accurately represent the PSS. The control program calculation time can be reduced because the established model is simple.
• Since the MPC method uses a global optimization algorithm, the optimal solution within the partition can be calculated directly. Therefore, PSS oscillation in the S feature area can be reduced effectively.
• Under the MPC method, the change of state variable is gentle. Thus, it is substantially conducive to reducing PSS equipment loss.
Conclusion
We proposed an MPC method for PSSs. A ML algorithm based on the Koopman theory was proposed for PSS modeling. A partition model of the pump turbine used in PSSs was established. This allowed us to express the complex nonlinearity of the S-characteristic region using a simple polynomial model. The experimental results indicated that the MPC method quickly reached the control target under conditions of no-load start-up, frequency disturbance, and speed disturbance. This method can more effectively suppress oscillation of the turbine rotation speed in the S-characteristic region than existing control methods and has a faster response speed. The proposed method has practical promise because it learns device characteristics from experimental data and is not limited by device type. In the future, we will improve the accuracy of ML to improve the effect of MPC and study the performance of the proposed method under other working conditions.
Data Availability Statement
The datasets presented in this article are not readily available because Data set for pumped storage system. Requests to access the datasets should be directed to b2RkbmV3bGlmZUAxMjYuY29t.
Author Contributions
QC and XL; methodology, QC; software, QC and SY; validation, XL; data curation, PZ; writing—original draft preparation, SY; writing—review and editing, QC; visualization, CG; supervision, XL; project administration, XL; All authors have read and agreed to the published version of the manuscript.
Conflict of Interest
The authors declare that the research was conducted in the absence of any commercial or financial relationships that could be construed as a potential conflict of interest.
Publisher’s Note
All claims expressed in this article are solely those of the authors and do not necessarily represent those of their affiliated organizations, or those of the publisher, the editors and the reviewers. Any product that may be evaluated in this article, or claim that may be made by its manufacturer, is not guaranteed or endorsed by the publisher.
References
Alamir, M., and Allgöwer, F. (2008). Model Predictive Control. Int. J. Robust Nonlinear Control. 18, 799. doi:10.1002/rnc.1266
Albuyeh, A. I. F. (2013). Grid of the Future. IEEE Power Energ. Mag. 11 (4), 20. doi:10.1109/MPE.2008.931384
Anilkumar, T. T., and Padhy, N. P. (2017). Residential Electricity Cost Minimization Model through Open Well-Pico Turbine Pumped Storage System. Appl. Energ. 195, 23–35. doi:10.1016/j.apenergy.2017.03.020
Ayush Thada, S. P., Dubey, A., and Bhaskara Rao, L. (2021). Machine Learning Based Frequency Modelling. Mech. Syst. Signal Process. 160, 107951. doi:10.1016/j.ymssp.2021.107915
Bozchalui, M. C. (2015). Optimal Energy Management of Greenhouses in Smart Grids. IEEE TRANSACTIONS SMART GRID 6 (2), 827–835. doi:10.1109/tsg.2014.2372812
Brahman, F. H. M., and Jadid, S. (2015). Optimal Electrical and thermal Energy Management of a Residential Energy Hub, Integrating Demand Response and Energy Storage System. Amsterdam: Elsevier. doi:10.1016/j.enbuild.2014.12.039
Chen Feng, C. L., Chang, Li., Mai, Z., and Wu, C. (2021). Nonlinear Model Predictive Control for Pumped Storage Plants Based on Online Sequential Extreme Learning Machine with Forgetting FactorComplexity. doi:10.1155/2021/5692621
Chunyang Gao, X., Nan, Hg., Men, C., and Fu, J. (2021a). Stability and Dynamic Analysis of Doubly-Fed Variable Speed Pump Turbine Governing System Based on Hopf Bifurcation Theory. Renew. Energ. 175, 568–579.
Chunyang Gao, X. Y., Nan, H., Men, C., and Fu, J. (2021b). A Fast High-Precision Model of the Doubly-Fed Pumped Storage Unit. New York, NY: Journal of Electrical Engineering & Technology, 16, 797–808. doi:10.1007/s42835-020-00641-0
De Souza, G., and Zanin, A. C. (2010). Real Time Optimization (RTO) with Model Predictive Control (MPC). Comput. Chem. Eng. 34 (12), 1999–2006. doi:10.1016/j.compchemeng.2010.07.001
Diego, S., and Carrasco, G. C. G. (2011). Feedforward Model Predictive Control. Annu. Rev. Control. 35, 199–206. doi:10.1016/j.arcontrol.2011.10.007
Elena Smirnova, S. K., Kolpak, E., and Shestak, V. (2021). Governmental Support and Renewable Energy Production: A Crosscountry Review. Energy 230. doi:10.1016/j.energy.2021.120903
Eric O’Shaughnessy, J. H., Shah, C., and Koebrich, S. (2021). Corporate Acceleration of the Renewable Energy Transition and Implications for Electric Grids. Renew. Sust. Energ. Rev. 146, 111160. doi:10.1016/j.rser.2021.111160
Forbes, M. G., Patwardhan, R. S., Hamadah, H., and Gopaluni, R. B. (2015). Model Predictive Control in Industry: Challenges and Opportunities. IFAC-PapersOnLine 48 (8), 531–538. doi:10.1016/j.ifacol.2015.09.022
Francesco Calise, M. D. d. A., and Piacentino, A. (2014). A Novel Solar Trigeneration System Integrating PVT (Photovoltaic/thermal Collectors) and SW (Seawater) Desalination. Amsterdam: Dynamic simulation and economic assessment. Energy 67, 129–148. doi:10.1016/j.energy.2013.12.060
Güney, T. (2019). Renewable Energy, Non-renewable Energy and Sustainable Development. Int. J. Sust. Develop. World Ecol.. doi:10.1080/13504509.2019.1595214
Guopeng Zhao, Y. Z., and Ren, J. (2021). Analysis of Control Characteristics and Design of Control System Based on Internal Parameters in Doubly Fed Variable-Speed Pumped Storage Unit. New Jersey, NY: Complexity. doi:10.1155/2021/6697311
Gurung, A. B., Borsdorf, A., Füreder, L., Kienast, F., Matt, P., Scheidegger, C., et al. (2016). Rethinking Pumped Storage Hydropower in the European Alps. Mountain Res. Develop. 36 (2), 222–232. doi:10.1659/mrd-journal-d-15-00069.1
Hasan Mehrjerdi, A. A. M. A. (2021). Modeling and Optimal Planning of an Energy–Water–Carbon Nexus System for Sustainable Development of Local CommunitiesAdvanced Sustainable Systems.
Hou, C. L., Tian, Z., Xu, Ye., Lai, X., Zhang, N., Zheng, T., et al. (2018). Multi-Objective Optimization of Start-Up Strategy for Pumped Storage Units. Energies 1 (5), 1141. doi:10.3390/en11051141
Hou, J., Li, W., Guo, W., and Fu, W. (2019). Optimal Successive Start-Up Strategy of Two Hydraulic Coupling Pumped Storage Units Based on Multi-Objective Control. Int. J. Electr. Power Energ. Syst. 111, 398–410. doi:10.1016/j.ijepes.2019.04.033
Huang, W., Guo, X., Wang, J., Li, J., and Li, J. (2018). Prediction Method for the Complete Characteristic Curves of a Francis Pump-Turbine. Water 10 (2), 205. doi:10.3390/w10020205
Idowu, S., Saguna, S., Åhlund, C., and Schelén, O. (2016). Applied Machine Learning: Forecasting Heat Load in District Heating System. Energy and Buildings 133, 478–488. doi:10.1016/j.enbuild.2016.09.068
Jianzhong Zhou, Z. Z., Zhang, Chu., Li, C., and Xu, Y. (2018). A Real-Time Accurate Model and its Predictive Fuzzy PID Controller for Pumped Storage Unit via Error Compensation. Energies 11 (1), 35. doi:10.3390/en11010035
Julian David Hunt, B. Z., Rafael Lopes, P. S. Fo. B., and Andreas, N. (2020). Existing and New Arrangements of Pumped-Hydro Storage Plants. Renew. Sust. Energ. Rev. 129, 109914. doi:10.1016/j.rser.2020.109914
Kiely, T. J., Kiely, N. D. B., and Bastian, N. D. (2019). The Spatially Conscious Machine Learning Model. Stat. Anal. Data Min: ASA Data Sci. J. 13 (1), 31–49. doi:10.1002/sam.11440
Kocaman, A. S., and Modi, V. (2017). Value of Pumped Hydro Storage in a Hybrid Energy Generation and Allocation System. Appl. Energ. 205, 1202–1215. doi:10.1016/j.apenergy.2017.08.129
Li, C., Mao, Y., Yang, J., and Xu, Y. (2017b). A Nonlinear Generalized Predictive Control for Pumped Storage Unit. Renew. Energ. 114, 945–959. doi:10.1016/j.renene.2017.07.055
Li, J.-w., ZhangXian, H-z., Xian, H.-z., and Yu, J.-x. (2017a). Numerical Simulation of Hydraulic Force on the Impeller of Reversible Pump Turbines in Generating Mode. J. Hydrodyn 29, 603–609. doi:10.1016/s1001-6058(16)60773-4
Li, J., Ward, J. K., Tong, J., and Platt, G. (2016). Machine Learning for Solar Irradiance Forecasting of Photovoltaic System. Renew. Energ. 90, 542–553. doi:10.1016/j.renene.2015.12.069
Liang, L., and Hou, D. J. (2019). GPU-based Enumeration Model Predictive Control of Pumped Storage to Enhance Operational Flexibility. IEEE Trans. Smart Grid 10 (5), 5223–5233. doi:10.1109/tsg.2018.2879226
Martin, R., Aler, R., and Galvan, I. M. (2015). Machine Learning Techniques for Daily Solar Energy Prediction and Interpolation Using Numerical Weather Models. Concurrency Computat.: Pract. Exper. 28, 1261–1274. doi:10.1002/cpe.3631
Max Schwenzer, M. A., Bergs, T., and Abel, D. (2021). Review on Model Predictive Control: an Engineering Perspective. Int. J. Adv. Manufacturing Tech.. doi:10.1007/s00170-021-07682-3
Mayne, D. (2016). Robust and Stochastic Model Predictive Control: Are We Going in the Right Direction?. Annu. Rev. Control. 41, 184–192. doi:10.1016/j.arcontrol.2016.04.006
Menon, R. P. (2013). Study of Optimal Design of Polygeneration Systems in Optimal Control Strategies. Amsterdam: Energy 55, 134–141. doi:10.1016/j.energy.2013.03.070
Min, C.-G., and Kim, M.-K. (2017). Flexibility-Based Reserve Scheduling of Pumped Hydroelectric Energy Storage in Korea. Energies 10 (10), 1478. doi:10.3390/en10101478
Olusola Bamisile, A. B., Humphrey, A., Nasser, Y., Mukhtar, M., Huang, Qi., and Hu, W. (2021). Electrification and Renewable Energy Nexus in Developing Countries; an Overarching Analysis of Hydrogen Production and Electric Vehicles Integrality in Renewable Energy Penetration. Energ. Convers. Manage. 235, 114023. doi:10.1016/j.enconman.2021.114023
Pan, W., Zhu, Z., Liu, T., and Tian, W. (2021). Optimal Control for Speed Governing System of On-Grid Adjustable-Speed Pumped Storage Unit Aimed at Transient Performance Improvement. IEEE Access 9, 40445–40457. doi:10.1109/access.2021.3063434
Pannatier, Y., Kawkabani, B., Nicolet, C., Schwery, A., and Allenbach, P. (2010). Investigation of Control Strategies for Variable-Speed Pump-Turbine Units by Using a Simplified Model of the Converters. IEEE Trans. Ind. Electron. 57, 3039–3049. doi:10.1109/tie.2009.2037101
Pazouki, S. H. M.-R. (2016). Optimal Planning and Scheduling of Energy Hub in Presence of Wind, Storage and Demand Response under Uncertainty. Int. J. Electr. Power Energ. Syst. doi:10.1016/j.ijepes.2016.01.044
Pazouki, S. (2014). Uncertainty Modeling in Optimal Operation of Energy Hub in Presence of Wind, Storage and Demand Response. Amsterdam: International Journal of Electrical Power and Energy Systems, 61, 33–345. doi:10.1016/j.ijepes.2014.03.038
Podlubny, I. (1999). Fractional-order Systems and PI/sup/spl lambda//D/sup/spl Mu//-Controllers. IEEE Trans. Automat. Contr. 44 (1), 208–214. doi:10.1109/9.739144
Pradhan, A., and Franca, M. J. (2021). The Adoption of Seawater Pump Storage Hydropower Systems Increases the Share of Renewable Energy Production in Small Island Developing States. Renew. Energ. 177, 448–460. doi:10.1016/j.renene.2021.05.151
Rajkumar, R. K. (2011). Techno-economical Optimization of Hybrid Pv/wind/battery System Using Neuro-Fuzzy. Energy 36 (8), 5148–5153. doi:10.1016/j.energy.2011.06.017
Rajvikram Madurai Elavarasan, R. P., Jamal, T., Dyduch, Ja., Arif, M. T., Shafiullah, G. M., Chopra, St. S., et al. (2021). Envisioning the UN Sustainable Development Goals (SDGs) through the Lens of Energy Sustainability (SDG 7) in the post-COVID-19 World. Appl. Energ. 292. doi:10.1016/j.apenergy.2021.116665
Robinson, C., Dilkina, B., Hubbs, J., Zhang, W., Guhathakurta, S., and Pendyala, R. M. (2017). Machine Learning Approaches for Estimating Commercial Building Energy Consumption. Appl. Energ. 208, 889–904. doi:10.1016/j.apenergy.2017.09.060
Ruppert, L., List, B., Bauer, C., and Bauer, C. (2017). An Analysis of Different Pumped Storage Schemes from a Technological and Economic Perspective. Energy 141, 368–379. doi:10.1016/j.energy.2017.09.057
Sam, N. K., and Gounden, N. A. (2017). Wind-driven Stand-Alone DFIG with Battery and Pumped Hydro Storage System. Sādhanā 42, 173–185. doi:10.1007/s12046-017-0595-ys
Sánchez-Oro, J., and Duarte, A. (2016). Robust Total Energy Demand Estimation with a Hybrid Variable Neighborhood Search - Extreme Learning Machine Algorithm. Energ. Convers. Manage. 123, 445–452. doi:10.1016/j.enconman.2016.06.050
Schmidt, J., and Kemmetmüller, W. (2017). Modeling and Static Optimization of a Variable Speed Pumped Storage Power Plant. Renew. Energ. 111, 38–51. doi:10.1016/j.renene.2017.03.055
Shiliang Zhang, H. C., Zhang, Y., Jia, L., Ye, Z., and Hei, X. (2017). Data-Driven Optimization Framework for Nonlinear Model Predictive Control. Math. Probl. Eng. 2017, 15. doi:10.1155/2017/9402684
Sopasakis, P., and Sarimveis, H. (2017). Stabilising Model Predictive Control for Discrete-Time Fractional-Order Systems. Automatica 75, 24–31. doi:10.1016/j.automatica.2016.09.014
Thomas Sattich, D. F., Scholten, D., and Yan, S. (2021). Renewable Energy in EU-China Relations: Policy Interdependence and its Geopolitical Implications. Energy Policy 156, 112456. doi:10.1016/j.enpol.2021.112456
van Meerwijk, A. J. H., Davila-martinezBenders, A., and LaugsLAUGS, G. A. H. (2016). Swiss Pumped Hydro Storage Potential for Germany's Electricity System under High Penetration of Intermittent Renewable Energy. J. Mod. Power Syst. Clean. Energ. 4 (4), 542–553. doi:10.1007/s40565-016-0239-y
Xu, Y., Zheng, Y., Du, Y., Yang, W., and Li, C. (2018). Adaptive Condition Predictive-Fuzzy PID Optimal Control of Start-Up Process for Pumped Storage Unit at Low Head Area. Energ. Convers. Manage. 177, 592–604. doi:10.1016/j.enconman.2018.10.004
Xu, Y., Zhou, J., Xue, X., Fu, W., and Li, C. (2016). An Adaptively Fast Fuzzy Fractional Order PID Control for Pumped Storage Hydro Unit Using Improved Gravitational Search Algorithm. Energ. Convers. Manage. 111, 67–78. doi:10.1016/j.enconman.2015.12.049
Ye, B.-L., Wu, W., Gao, H., Lu, Y., and Zhu, L. (2017). Stochastic Model Predictive Control for Urban Traffic Networks. Appl. Sci. 7 (6), 588. doi:10.3390/app7060588
Yifeng Shi, X. S., Yi, C., Song, X., and Chen, X. (2020). Control of the Variable-Speed Pumped Storage Unit-Wind Integrated System Mathematical Problems In Engineering 2020. doi:10.1155/2020/3816752
Yin, J., Wang, D., and Wei, X. (2014). Investigation of the Unstable Flow Phenomenon in a Pump Turbine. Sci. China Phys. Mech. Astron. 57, 1119–1127. doi:10.1007/s11433-013-5211-5
Zeng, W., and Hu, J. (2017). Pumped Storage System Model and Experimental Investigations on S-Induced Issues during Transients. Mech. Syst. Signal Process. 90, 350–364. doi:10.1016/j.ymssp.2016.12.031
Zhang, H., Chen, D., Wu, C., Wang, X., Lee, J.-M., and Jung, K.-H. (2017). Dynamic Modeling and Dynamical Analysis of Pump-Turbines in S-Shaped Regions during Runaway Operation. Energ. Convers. Manage. 138, 375–382. doi:10.1016/j.enconman.2017.01.053
Zhang, X. S. M., Alabdulwahab, A., and Abusorrah, A. (2015). Optimal Expansion Planning of Energy Hub with Multiple Energy Infrastructures. Smart Grid IEEE Trans. 6 (5), 2302–2311. doi:10.1109/tsg.2015.2390640
Zhao, Y.-P., Hu, Q.-K., Xu, J.-G., Li, B., and Pan, Y.-T. (2018). A Robust Extreme Learning Machine for Modeling a Small-Scale Turbojet Engine. Appl. Energ. 218, 22–35. doi:10.1016/j.apenergy.2018.02.175
Zhaoyang Dong, J. Z., and Wen, F. (2014). From Smart Grid to Energy Internet: Basic Concept and Research Framework. Automat Elec Power Syst. 38 (15), 1–11.
Keywords: model predictive control, machine Learning, pumped storage system, sustainable hydropower, intelligent control
Citation: Cai Q, Luo X, Gao C, Guo P, Sun S, Yan S and Zhao P (2021) A Machine Learning-Based Model Predictive Control Method for Pumped Storage Systems. Front. Energy Res. 9:757507. doi: 10.3389/fenrg.2021.757507
Received: 12 August 2021; Accepted: 19 October 2021;
Published: 08 November 2021.
Edited by:
Biagio Fernando Giannetti, Paulista University, BrazilReviewed by:
Yi Zong, Technical University of Denmark, DenmarkAlfian Ma’Arif, Ahmad Dahlan University, Indonesia
Copyright © 2021 Cai, Luo, Gao, Guo, Sun, Yan and Zhao. This is an open-access article distributed under the terms of the Creative Commons Attribution License (CC BY). The use, distribution or reproduction in other forums is permitted, provided the original author(s) and the copyright owner(s) are credited and that the original publication in this journal is cited, in accordance with accepted academic practice. No use, distribution or reproduction is permitted which does not comply with these terms.
*Correspondence: Xingqi Luo, bHVveHFAeGF1dC5lZHUuY24=