- 1Robert Frederick Smith School of Chemical and Biomolecular Engineering, Cornell University, Ithaca, NY, United States
- 2School of Civil and Environmental Engineering, Cornell University, Ithaca, NY, United States
- 3Department of Earth and Environmental Engineering, Columbia University, New York, NY, United States
Rational integration of chemical pathways at the molecular scale to direct thermodynamically favorable enhanced H2 production with inherent carbon removal from low-value substrates can be guided by exploring the thermodynamic limits of feasibility. The substrates of interest are biomass oxygenates that are water-soluble and uneconomical for separation from water. In this study, we investigate the thermodynamic feasibility of recovering H2 with inherent carbon removal from biomass oxygenates such as ethanol, methanol, glycerol, ethylene glycol, acetone, and acetic acid. The influence of biomass oxygenate-to-water ratios, reaction temperature of 150°C–325°C, and CaO or Ca(OH)2 as the alkalinity source on the yields of H2, CH4, CO2, and Ca-carbonate are investigated. By maintaining the fluids in the aqueous phase under pressure, energy needs associated with vaporization are circumvented. The hypothesis that enhanced alkalinity favors the preferential formation of CO (precursor for CO2 formation) over CH4 and aids the formation of calcium carbonate is investigated. The findings from these studies inform the feasibility, design of experiments, and the tuning of reaction conditions for enhanced H2 recovery with inherent carbon removal from biomass oxygenate sources.
Introduction
Decarbonizing energy carriers such as H2 while upcycling abundant low value resources is crucial for a sustainable energy, environmental, and climate future. This approach addresses our societal mission of lifting millions of people out of energy poverty globally (WHO, 2009) while limiting detrimental environmental impacts including the rise of global temperatures (Masson-Delmotte et al., 2018). Currently, more than 85% of H2 is produced via steam methane reforming (SMR) and the water gas shift reaction (WGSR) as represented by the following reactions: CH4 + H2O → CO + 3H2 (SMR) and CO + H2O → CO2 + H2 (WGSR). Producing H2 from renewable natural gas (e.g., biogas) and removing CO2 is one approach to produce decarbonized fuels (Gadikota, 2020, 2021).
Conventional approaches to capture CO2 using adsorption, (Sayari et al., 2011) absorption, (Rochelle, 2009), and membrane separations (Khalilpour et al., 2015) are being realized at the commercial scale. Once CO2 is captured, it is compressed and stored in geologic formations (Benson and Surles, 2006). However, the availability of appropriate reservoirs for geologic storage of CO2 is essential. In places that do not have access to appropriate geologic formations, alternative technologies are needed for storing CO2 as inorganic carbonates. Further, energy carriers such as H2 can be produced from distributed bio-based feedstocks with inherent carbon removal.
Significant advancements have been made in harnessing hydrogen from bio-based sources. Technologies to harness H2 from gaseous and solid biomass-based feedstocks include steam reforming (SR) in which light hydrocarbons are reacted with steam to produce H2 and CO2, usually in the presence of a catalyst (Ross, 1984; Ming et al., 2002), partial oxidation in which biomass is partial combusted with limited amount of O2 to produce synthetic gas (a mixture of CO and H2) (Dissanayake et al., 1991; Hohn and Schmidt, 2001), and autothermal reforming (ATR) in which biomass is mixed with steam, and a limited amount of O2 to produce synthetic gas and CO2 (Dissanayake et al., 1991; Joensen and Rostrup-Nielsen, 2002; Deluga et al., 2004). Alkaline hydrothermal treatment (ATT) of wet biomass has been extensively reported to enhance H2 generation from wet biomass with inherent CO2 capture to produce inorganic carbonates (Stonor et al., 2017a; Zhang et al., 2020). However, few approaches have addressed strategies to harness H2 from aqueous biomass oxygenate streams.
Biomass oxygenates soluble in water are important because they can be readily obtained from low value biomass feedstocks such as food or municipal waste generated in urban or rural environments, algal sources, and industrial wastewater polluted streams as shown in Table 1. These feedstocks are also available in large quantities. For example, more than 40% of the food produced in the United States, and 44 million m3/day of wastewater generated in India, eventually returns to the environment as waste (Ranade and Bhandari, 2014; NRDC, 2021). Novel conversion pathways that can be easily adapted to accommodate a wide range of aqueous feedstocks are required, given the increasing scientific viability of producing simpler biomass oxygenates from waste streams, (Badawi et al., 1992; Thompson and He, 2006; Abanoz et al., 2012; Ellis et al., 2012; Yan et al., 2012; Li et al., 2015; Uçkun Kiran and Liu, 2015; Mincer and Aicher, 2016; Kim et al., 2018; Ajao et al., 2019; Qi et al., 2020; Arora et al., 2021) and from the chemical deconstruction of biomass (Brandt et al., 2013).
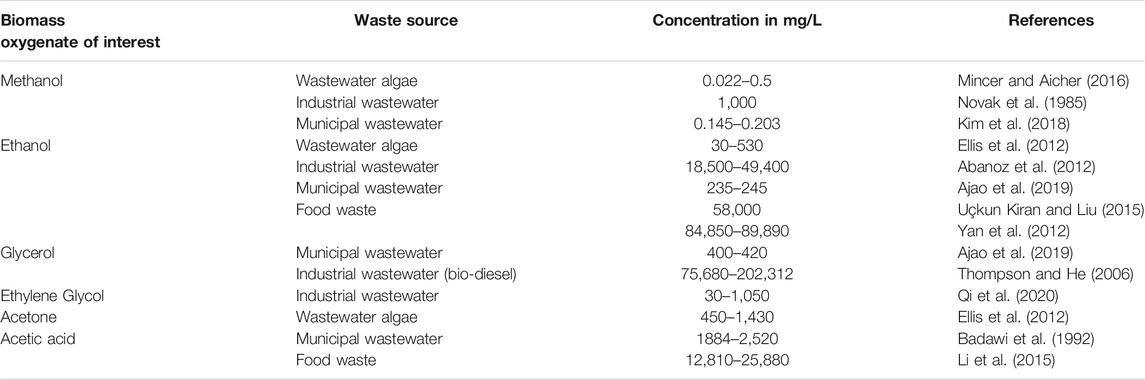
TABLE 1. Concentration of methanol, ethanol, glycerol, ethylene glycol, acetone, and acetic acid in waste streams.
One such approach is aqueous phase reforming (APR) in which bio-derived aqueous feedstocks can be converted to H2 in a pressurized environment. (Shabaker et al., 2003; Wen et al., 2008; Cortright et al., 2010). Compared to the other energy conversion approaches, APR occurs at 200–250°C which is significantly lower than temperatures >500°C for other biomass conversion approaches. The water gas shift reaction (WGSR) is integral to APR and catalysts are harnessed to direct the conversion of biomass oxygenates into H2. APR reactions are represented as follows: CnH2yOn + nH2O → nCO2 + (y + n)H2 (Davda et al., 2005). The approach of maintaining water in the aqueous phase as opposed to in the gas phase enables the scientific possibility of integrating with carbon mineralization reaction to remove CO2 with H2 recovery from biomass oxygenates (see Figure 1). The reaction representing H2 recovery with inherent carbon removal is shown as follows:
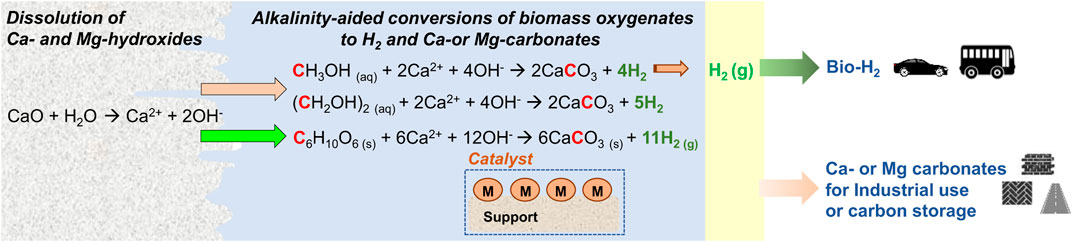
FIGURE 1. Schematic representation of the multiphase chemical interactions involved in the co-generation of bio-hydrogen and inorganic carbonates from biomass, and alkaline industrial residues or minerals.
The standard heats of reaction (
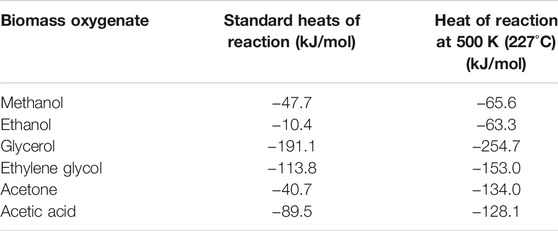
TABLE 2. Standard heats of reaction (kJ/mol) for H2 recovery from aqueous biomass oxygenates with inherent carbon removal:
Despite the simplicity of this stoichiometric representation, this reaction pathways are complex and involve several multiphase chemical interactions including: (i) cleavage of biomass oxygenate molecules, (ii) competitive formation of CO versus CH4, and (iii) conversion of CO to CO2 followed by the subsequent dissolution of CO2 to produce inorganic carbonates. These reactions are sensitive to temperature, pH, and solid and water compositions (in addition to catalyst compositions and uses). Further the anomalous solubility of calcium carbonate which decreases with increase in temperature and the dissolution behavior of the alkaline sources (e.g., Ca- or Mg-rich residues and minerals) in these multiphase chemical environments needs to be considered. The thermodynamic basis for these experimental investigations needs to be developed prior to demonstrating experimental feasibility. Therefore, the aim of this study is to develop the thermodynamic limits for enhanced H2 recovery with inherent carbon removal from aqueous biomass oxygenates and alkaline sources such as calcium oxide (CaO). CaO is abundant in ash, slags, and kiln dusts recovered from industrial processes (Gadikota et al., 2015). The biomass oxygenates of interest are methanol (CH3OH), ethanol (C2H5OH), glycerol [C3H5(OH)3], ethylene glycol [C2H4(OH)2], acetone (CH3COCH3), and acetic acid (CH3COOH), because these oxygenates have been frequently used as model compounds, during aqueous phase reforming at low temperatures (< 500°C) (Davda et al., 2005; Cortright et al., 2010; Coronado et al., 2016; NRDC, 2021). Also, these oxygenates are readily available in low value aqueous streams such as wastewater from biomass processing as shown in Table 1.
Prior studies focused on enhanced H2 conversion from biomass feedstocks at high temperature and low pressure conditions in which steam is the dominant reacting phase as opposed to water. Temperatures in the range of 427°C–627°C and steam-to-biomass ratios greater than five resulted in highly selective H2 production over CH4 formation. However, this approach is accompanied by significant evolution of CO2 and CO in the product stream (Cohce et al., 2010). H2 with purity of 99.97% or higher is needed for fuel cell applications. Even low concentrations of CO to the order of 100 ppm can inhibit the use of fuel cells (Baschuk and Li, 2001; U.S. Department of Energy et al., 2016).
Thermodynamic analyses of methanol reforming found that temperatures of 246°C and steam-to-methanol ratio of 5.6 resulted in a maximized H2 yield of 4.28% with methanation CH4 and 99.7% without methanation reactions. Further, CO product formation at atmospheric pressure was minimized (Özcan and Akın, 2019). Coupling these reactions with CO2 capture can ensure high purity H2 yields for use in fuel cell applications. To investigate the influence of inherent CO2 capture during H2 recovery from biomass oxygenates, sorption-enhanced steam methane reforming was investigated. Equilibrium H2 concentrations of over 97% were observed for reforming with water-to-oxygenate ratio of 6, 9, 4, and 12 for ethanol, glycerol, methanol, and n-butanol respectively, in the presence of CaO at 500°C, and at an elevated pressure of 5 bar (Lima Da Silva and Müller, 2011).
Furthermore, experimental studies building on similar conditions have reported better H2 yields using catalysts that suppress CH4 formation and favor more H2 production. For example, H2 yield of 63% was noted using 10 wt% aqueous glycerol in the presence of CaO and Pt-Ni catalyst at 230°C and initial N2 pressure of 30 bar (He et al., 2015). Maintaining the fluid in the aqueous phase favors accelerated carbon mineralization via enhanced dissolution and carbonate formation. Extensive studies reported the use of appropriate catalysts for aqueous phase reforming (Davda et al., 2005; Luo et al., 2008; Menezes et al., 2011; De Vlieger et al., 2012; Roy et al., 2012). Catalysts that preferentially direct the formation of CO over CH4 in aqueous phase reforming were reported. However, comprehensive analyses exploring the thermodynamic limits of enhanced H2 recovery with CO2 capture from biomass oxygenates and the corresponding physico-chemical parameters have not been reported in prior literature. This information is essential for developing the rational basis for enhanced H2 recovery from biomass oxygenates with inherent carbon removal while maintaining the fluid in the aqueous phase.
In this study, the compositions of H2, CO, CO2, and CH4 in the gas phase are determined as a function of temperature, water-to-oxygenate ratios, and CaO compositions for various biomass oxygenates such as ethanol, methanol, glycerol, ethylene glycol, acetic acid, and acetone. Specifically, the enhancement in H2 yield due to inherent carbon removal via calcium carbonate formation is the focus of these investigations. These studies provide the basis for experimental studies for probing enhanced H2 yield from biomass oxygenates with inherent carbonate formation.
Methods
Reactions Involved in Enhanced H2 Recovery With Inherent Carbon Removal From Aqueous Biomass Oxygenates
Several reactions and intermediate steps are involved in the recovery of H2 from biomass oxygenates with the inherent removal of CO2. These reactions are incorporated into the models for exploring thermodynamic limits for enhanced H2 recovery with carbon removal via mineralization. Reaction 2 represents the deconstruction of biomass oxygenates to produce CO2 and H2. This reaction represents the overall pathway for biomass oxygenate refining without CO2 capture.
Standard heat of reaction (
a, b, c, d, e, f corresponds to methanol, ethanol, glycerol, ethylene glycol, acetone, and acetic acid, respectively.
Reaction 2 involves several intermediate steps as described below. The first step in this pathway is the preferential formation of CO through bio-oxygenate decomposition as shown in Eq. 3a for C:O molar ratio of 1:1, and hydrolysis as shown in Eq. 3b for C:O molar ratios greater than 1:1. The CO produced then undergoes an exothermic water gas shift reaction (WGSR) to produce H2 and CO2.
Competing reactions that result in CH4 formation as opposed to H2 formation need to be incorporated (see reactions 5 and 6). Compared to WGS reactions, methanation reactions are more exothermic which make them favorable at low temperatures.
Furthermore, bio-derived oxygenates and their intermediate products can undergo dehydration, cracking, decomposition, and reduction to produce more undesired products such as CH4, CO, solid C, and C2H4, as shown by reactions 7–11 below.
Bio-oxygenate reforming reactions can be endothermic. Therefore, coupling these with exothermic carbon mineralization reactions (Eq. 12) enhances the overall spontaneity of these reactions. The overall exothermicity resulting from the coupling of these reaction is shown in Eq. 1, and the heat of reactions at 500 K for methanol, ethanol, glycerol, ethylene glycol, acetone, and acetic acid is presented in Table 2.
Thermodynamic Modelling and Simulation Methodology
The equilibrium compositions of various reacting processes are determined using the Gibbs energy minimization method. A more detailed description of this methodology was described by Lima et al. (Lima da Silva et al., 2009; Lima Da Silva and Müller, 2011). The advantage of this approach is that it addresses systems with potential for simultaneous reactions. The objective function shown in Eq. 14 is minimized subject to the elemental balance constraint in Eq. 15,
Where G,
Minimizing the objective function of the system indicates that a mixture of chemical species approaches an equilibrium state. These equilibrium calculations were performed and simulated using ASPEN® Plus V8.6 process simulation software. The Gibbs reactor (see Figure 2A,B) was modelled as an Isothermal equilibrium reactor, which calculates the equilibrium composition of product species using the Gibbs energy minimization method at various operating conditions, keeping our reaction temperature constant, while accounting for the heat of reactions. The Peng-Robinson (Peng-Rob) equations of state were used to model the property parameter (Peng and Robinson, 1976). This property method has been widely used for processes containing oxygenates, water, and combustion gases (Fateen et al., 2013; Ali et al., 2014; Jimmy et al., 2017).
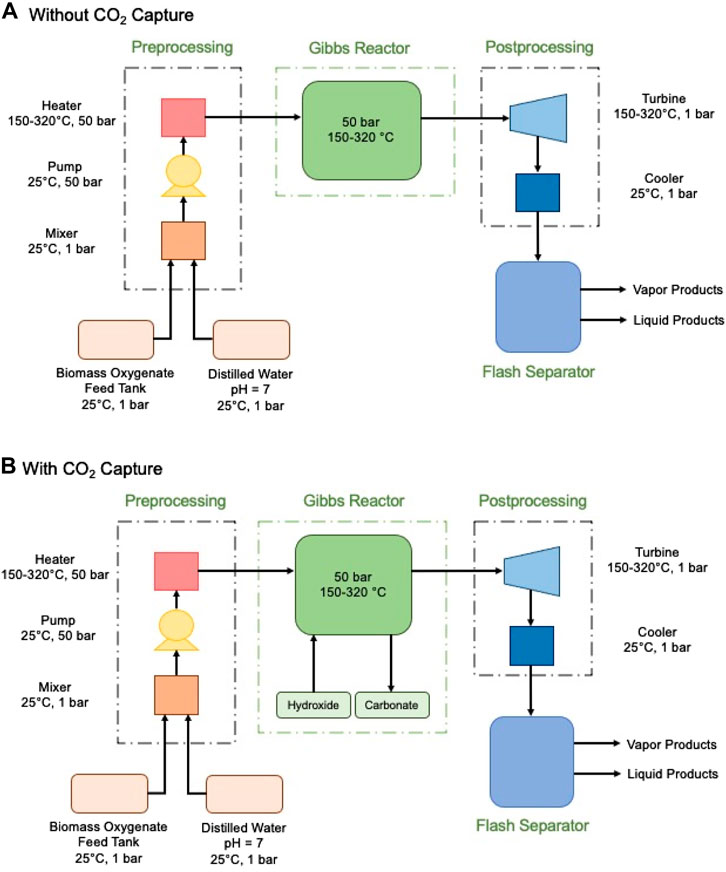
FIGURE 2. Process flow diagram of simulation environment (A) without in-situ CO2 capture, (B) with in-situ CO2 capture. The thermodynamic feasibility of enhancing H2 recovery with inherent carbon removal using aqueous biomass oxygenate sources are based on the reactions taking place in the Gibbs reactor.
Prior to been fed into the reactor, biomass oxygenate, and water is mixed, pressurized, and heated using a mixer, pump, and heater, respectively. In cases where the effect of alkalinity was investigated, the alkaline source was fed directly into the reactor at its specified temperature and pressure. It was found that the temperature of the input feed stream does not affect the thermodynamic results, because fixing the reactor parameters produces the equilibrium effect determined by the set temperature and pressure. However, the configuration was still used to ensure proper representation of the real batch reformer, as it would account for the energy required to heat the feedstock to the desired temperature and cool the products before analysis. Using this setup, H2 evolution with varying biomass oxygenate-to-water ratios in the range of 5–95%, a low temperature range of 150–325°C, and varying alkaline sources, was studied at 50 bar. Prior studies have shown that methanation reactions can also be effectively suppressed using catalysts (Davda et al., 2005; Coronado et al., 2016). We also investigated the influence of 1) methanation and 2) suppressed methanation. Both cases were also investigated with and without CO2 capture via carbon mineralization. This approach provides the optimal and sub-optimal scenarios that are dependent on the activity of the catalysts.
The equilibrium conversions of biomass oxygenates to products and associated product yields were defined as follows:
Results and Discussion
Effect of Water-to-Biomass Oxygenate Ratio on H2 Recovery With Carbon Removal
Water plays a synergistic role in enhanced H2 recovery with inherent carbon removal from biomass oxygenates. Water facilitates the dissolution of calcium oxide to release calcium ions that can readily react with the evolved CO2 to produce inorganic carbonates, as opposed to steam. The enhanced ion transport in gas-liquid-solid environments as opposed to in gas-solid environments favors accelerated formation of carbonates at lower temperatures as opposed to sorption-enhanced stream methane reforming that occurs at higher temperatures (Wang et al., 2008; Lindén et al., 2011). Further, the need for additional energy input in the form of latent heat of vaporization is avoided by maintaining water in the aqueous phase. To harness these advantages and resolve the compositions of the product stream, simulations were performed at 227°C, N2 pressure of 50 bar, with and without stoichiometric amounts of CaO as defined by reaction 1 and 13. H2, CH4, and CO2 yields with and without CaO are shown in Figures 3–8 for methanol, ethanol, glycerol, ethylene glycol, acetone, and acetic acid, respectively.
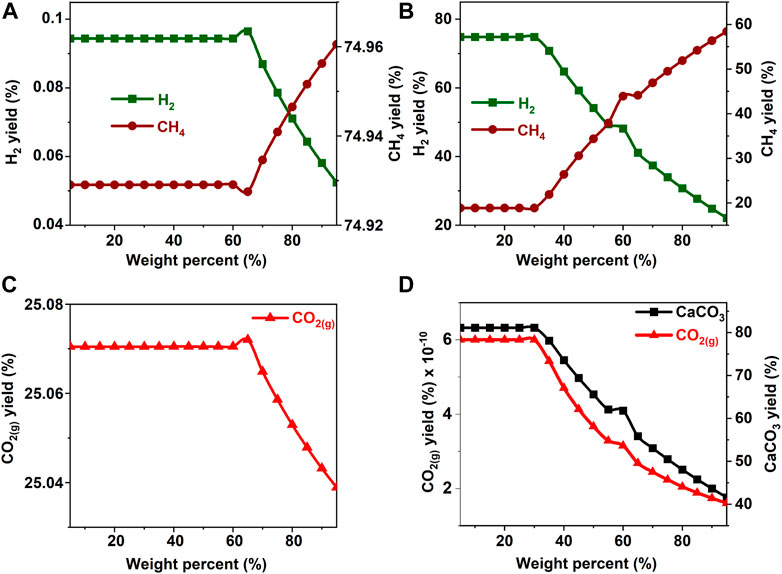
FIGURE 3. Effect of methanol concentration on the product yield (A, C) in the absence and (B) in the presence of calcium oxide. The yield of CO2 post capture to produce calcium carbonate is represented in 1(D). These calculations are performed with temperatures of 227°C and pressures of 50 bar.

FIGURE 4. Effect of ethanol concentration on the product yield (A, C) in the absence and (B) in the presence of calcium oxide. The yield of CO2 post capture to produce calcium carbonate is represented in 2(D). These calculations are performed with temperatures of 227°C and pressures of 50 bar.
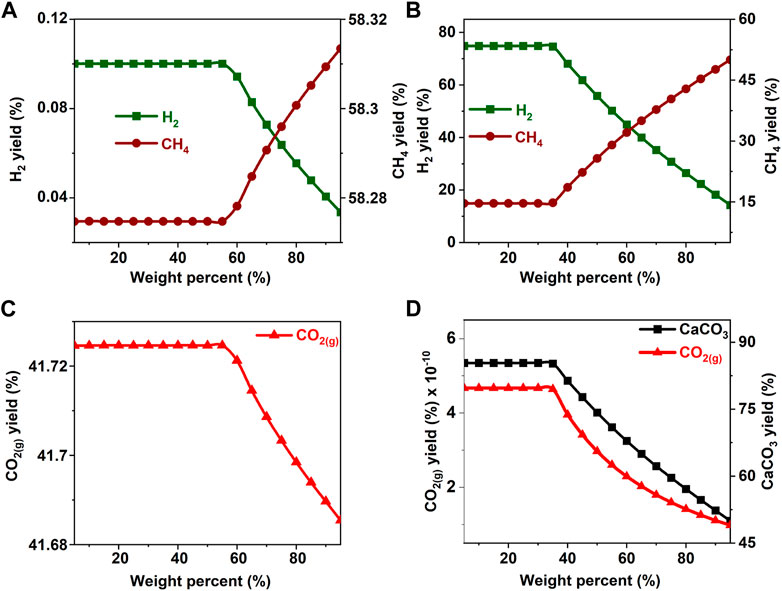
FIGURE 5. Effect of glycerol concentration on the product yield (A, C) in the absence and (B) in the presence of calcium oxide. The yield of CO2 post capture to produce calcium carbonate is represented in 3(D). These calculations are performed with temperatures of 227°C and pressures of 50 bar.
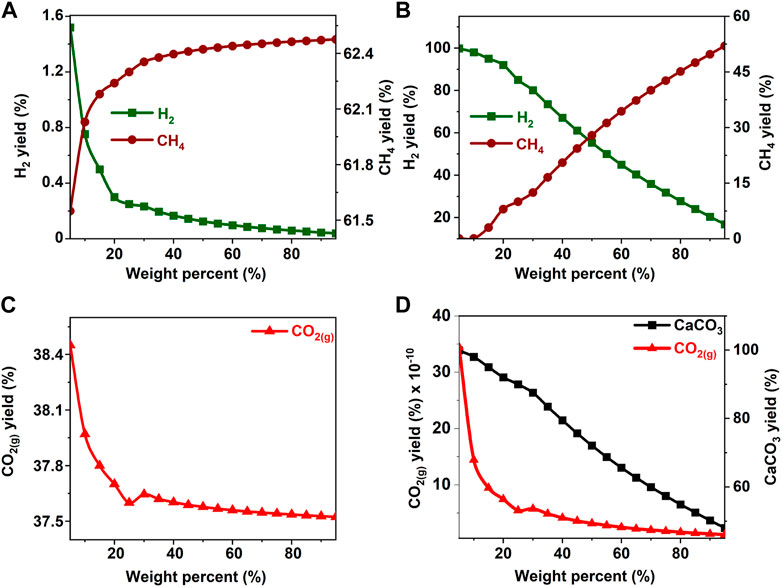
FIGURE 6. Effect of ethylene glycol concentration on the product yield (A, C) in the absence and (B) in the presence of calcium oxide. The yield of CO2 post capture to produce calcium carbonate is represented in 4(D). These calculations are performed with temperatures of 227°C and pressures of 50 bar.
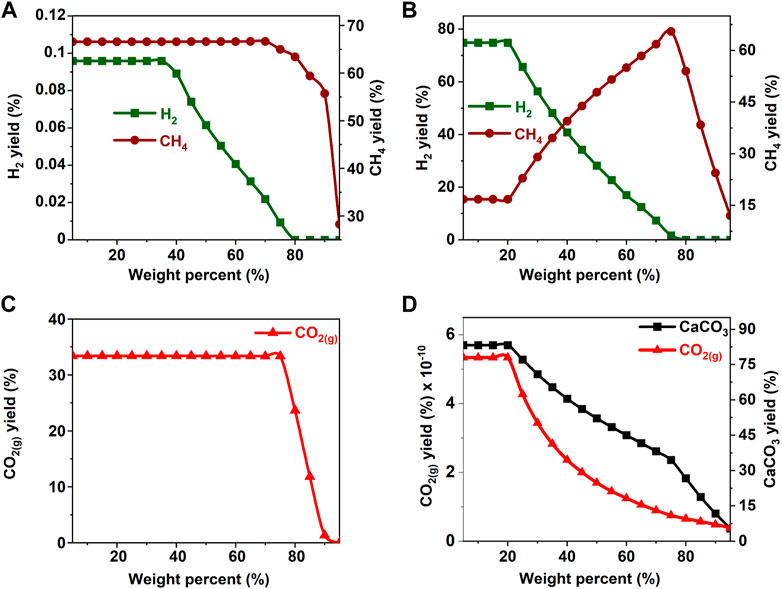
FIGURE 7. Effect of acetone concentration on the product yield (A, C) in the absence and (B) in the presence of calcium oxide. The yield of CO2 post capture to produce calcium carbonate is represented in 5(D). These calculations are performed with temperatures of 227°C and pressures of 50 bar.
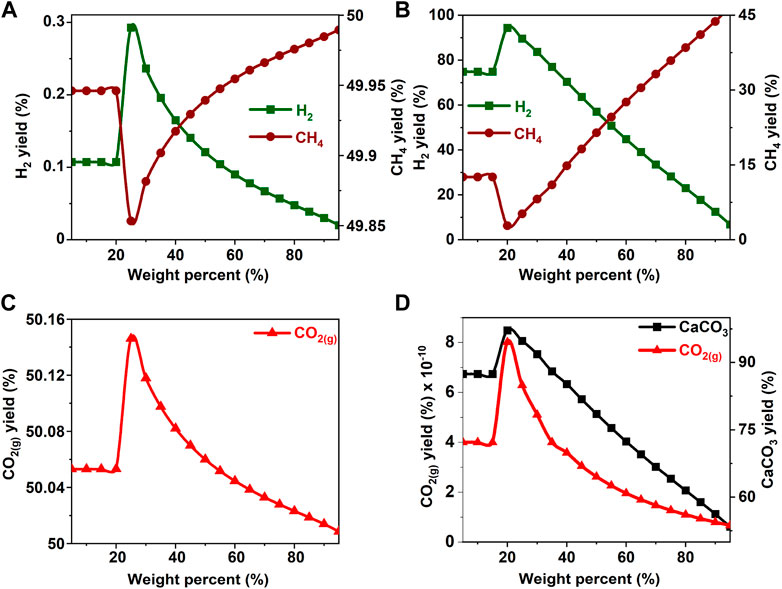
FIGURE 8. Effect of acetic acid concentration on the product yield (A, C) in the absence and (B) in the presence of calcium oxide. The yield of CO2 post capture to produce calcium carbonate is represented in 6(D). These calculations are performed with temperatures of 227°C and pressures of 50 bar.
In the absence of CaO for CO2 capture, the yields of H2 and CH4 remain unaffected by an increase in the concentration of methanol and ethanol up to 40 wt% (See Figures 3A,C, 4A,C). Further increases in the concentrations of methanol and ethanol led to an increase in CH4 yield and a simultaneous decrease in the production of hydrogen. Decrease in H2 yield is accompanied by a decrease in the production of gaseous CO2 gas, which can be attributed to the limited amount of H2O available to undergo a water gas shift reaction as shown in Eq. 4. Limited water concentration cause a thermodynamic shift to favor CH4 production via CO methanation reaction at equilibrium. When CaO was introduced to capture CO2, H2 concentrations decreased after methanol and ethanol concentrations exceeded 20 wt% (See Figures 3B,D, 4B,D). This change is attributed to the use of water for the water gas shift reaction and the dissolution of CaO to produce calcium carbonate.
The hypothesis that CaO significantly enhances H2 yields and suppresses CH4 yields was shown to be true since H2 yields exceeding 75% were achieved around 20 wt% for all the biomass oxygenates reported in this study (Figures 3B–8B). In the absence of CaO, less than 2% yield of H2 was noted (Figures 3A–8A). However, methane yields either remained unchanged at low biomass oxygenate concentrations or increased in most cases except for acetone. At acetone concentrations of 80 wt% or higher, H2 yields approached zero and methane yields decreased significantly. Also, the concentration of unreacted acetone in the product stream rapidly increased indicating low conversions of acetone (19–81%) at concentrations of 80wt% or higher, elsewhere the conversion was 100%. The observed anomaly could imply a different reaction mechanism caused by inadequate amounts of water leading to acetone decomposition to produce unstable radicals described as (CH3COCH3 → 2CH3* + CO) (Spence and Wild, 1936; Smith and Hinshelwood, 1944). Further, the absence of H2O or H2 for the CO produced during this reaction to undergo WGS reactions or methanation reaction as described in reactions 4) and 5) shifts the equilibrium back to acetone production at room temperature, leading to low conversions. With all the biomass oxygenates investigated, non-monotonic relationships between the concentrations of biomass oxygenates and the yields of H2 and CH4 were noted.
It was interesting to note a significantly lower yield of H2 at biomass oxygenate concentrations exceeding 60% for all the biomass oxygenates reported in this study which are methanol, ethanol, glycerol, ethylene glycol, acetone, and acetic acid. However, the trends in the concentrations of H2 and CH4 at biomass oxygenate concentrations below 60 wt% differ. The effectiveness of using stoichiometric amounts of CaO is evident from the negligibly low concentrations of CO2 in the gas phase to the order of 10–12 mol of CO2 per mole of biomass oxygenate fed after CO2 capture (Figures 3D–8D). At biomass oxygenate concentrations of 20 wt% or less, near complete conversions of CaO to CaCO3 are noted (Figures 3D–9D). In addition to aiding the separation of CO2, the heat generated during carbon mineralization aids the water gas shift reaction for enhanced H2 conversion.
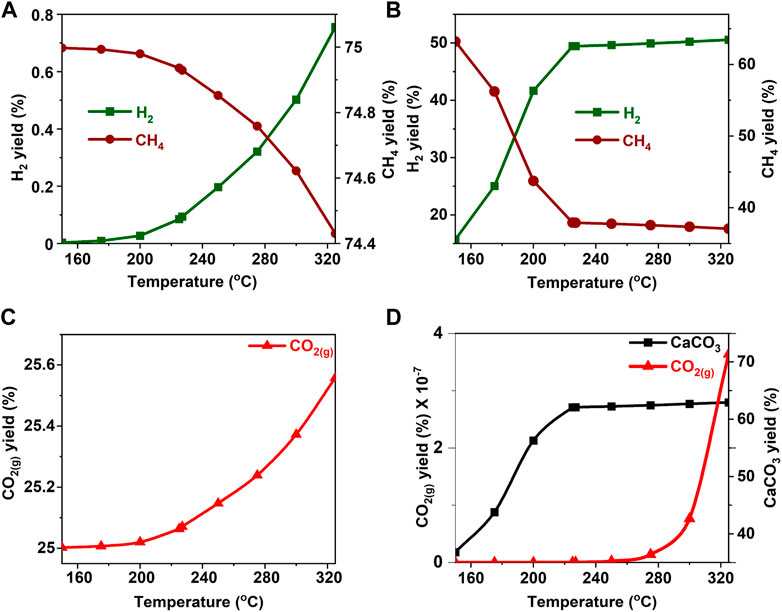
FIGURE 9. Effect of temperature on the product yield from methanol (A, C) in the absence and (B) in the presence of calcium oxide. The yield of CO2 post capture to produce calcium carbonate is represented in 7(D). These calculations are performed with temperatures of 227°C and pressures of 50 bar.
Effect of Temperature on H2 Recovery With Carbon Removal
Temperature has a significant effect on coupled multiphase chemical interactions involved in enhanced H2 recovery with inherent CO2 removal from biomass oxygenate precursors. Increase in temperature favors product and reactant formation in endothermic and exothermic reactions, respectively. Further, the solubility of calcium carbonate decreases with temperature which favors the removal of CO2. Aqueous biomass oxygenate decomposition is an endothermic reaction (see Reaction 3) and higher temperatures are expected to aid the decomposition behavior. In contrast, the conversion of CO and H2 to CH4 is exothermic (and higher temperatures may shift the equilibrium towards the reactants, which favors H2 yield. Coupling the exothermic water-gas-shift reaction (see Reaction 4) with the carbon mineralization reaction removes CO2 from the product stream and pushes the equilibrium to the products. This coupling of reactions counterbalances the effect of temperature which is to push the equilibrium towards the products. To investigate the hypothesis that the reaction temperature has a significant effect on enhanced H2 formation with inherent carbon removal, the gas compositions were determined at temperatures in the range of 150°C–325°C, while all other conditions such as the biomass oxygenate composition and the N2 pressure were held constant at 50 wt% and 50 bar.
In the absence of a catalyst and CaO for CO2 capture, H2 yields are less than 1% for all the biomass oxygenates and CH4 yields exceed 49% in the temperature range of 150°C–325°C (Figures 9A–14A). H2 and CO2 yields increase monotonically with temperature (Figures 9A,C–14A,C). The yields of CH4 decrease monotonically with temperature at these conditions (Figures 9A–14A). In the presence of CaO for CO2 capture, H2 yields of 46–65% or higher are achieved at temperatures exceeding 220°C. At these conditions, CH4 yields are 30% or lower at temperatures exceeding 220°C (Figures 9B–14B). These data suggest that alkaline environments (bearing CaO in this case) favor alkaline hydrolysis that contributes to the cleavage of C-C bonds as opposed to acid hydrolysis that results in C-O cleavage which promotes alkane formation. (Davda et al., 2005). Further, CO yields to the order of 10–3% and 10–9% were noted in the absence and presence of CaO, suggesting that the removal of CO2 from the gas phase accelerates the conversion of CO to CO2 (See Supplementary Figure S2A–F).
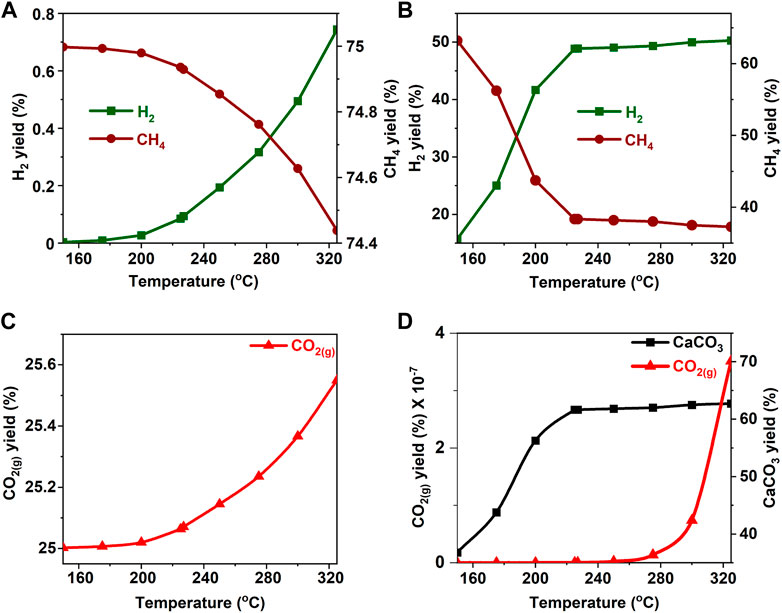
FIGURE 10. Effect of temperature on the product yield from ethanol (A, C) in the absence and (B) in the presence of calcium oxide. The yield of CO2 post capture to produce calcium carbonate is represented in 8(D). These calculations are performed with temperatures of 227°C and pressures of 50 bar.
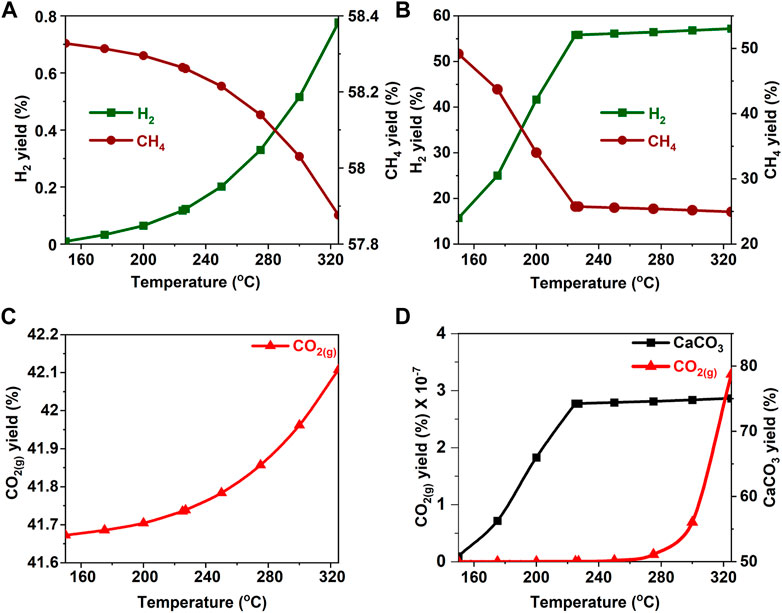
FIGURE 11. Effect of temperature on the product yield from glycerol (A, C) in the absence and (B) in the presence of calcium oxide. The yield of CO2 post capture to produce calcium carbonate is represented in 9(D). These calculations are performed with temperatures of 227°C and pressures of 50 bar.
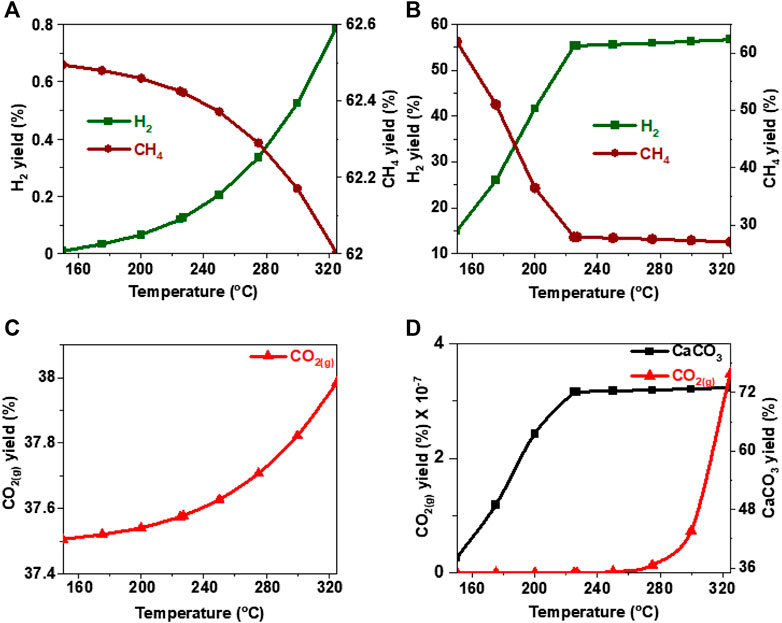
FIGURE 12. Effect of temperature on the product yield from ethylene glycol (A, C) in the absence and (B) in the presence of calcium oxide. The yield of CO2 post capture to produce calcium carbonate is represented in 10(D). These calculations are performed with temperatures of 227°C and pressures of 50 bar.
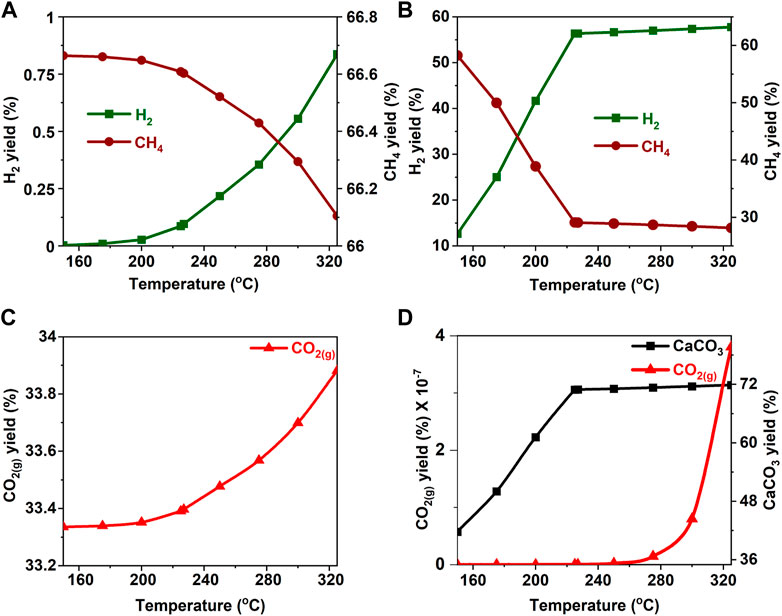
FIGURE 13. Effect of temperature on the product yield from acetone (A, C) in the absence and (B) in the presence of calcium oxide. The yield of CO2 post capture to produce calcium carbonate is represented in 11(D). These calculations are performed with temperatures of 227°C and pressures of 50 bar.
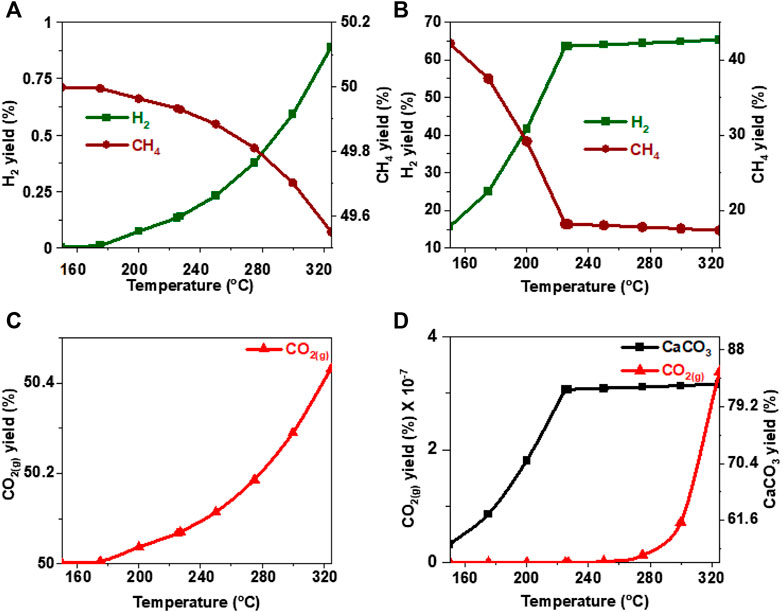
FIGURE 14. Effect of temperature on the product yield from acetic acid (A, C) in the absence and (B) in the presence of calcium oxide. The yield of CO2 post capture to produce calcium carbonate is represented in 13(D). These calculations are performed with temperatures of 227°C and pressures of 50 bar.
Unlike the cases without CaO, where we obtained a constant increase in H2 yield, an asymptotic pattern was observed in cases with in-situ CO2 capture for temperatures greater than 225°C. Furthermore, despite the low amounts of CO being produced, there was a sharp increase CO formation with increasing temperature between 225°C and 320°C. These observations imply that biomass oxygenate decomposition is aided at higher temperatures to produce CO. However, the low concentrations of CO and higher temperatures do not favor product formation in the exothermic water-gas-shift and methanation reactions. These factors contribute to the asymptotic behavior of H2 above 225°C which also corresponds to the near complete uptake of CO2 to produce CaCO3 (Figures 9D–14D). Negligible concentrations of CO2 to the order 10–7–10–10% were found in the product gas stream for all cases of biomass oxygenates studied after CO2 capture using CaO (See Figures 9D–14D).
Effect of Methanation on H2 Recovery With Carbon Removal
The key limiting factor in accelerating H2 recovery from biomass oxygenates is the formation of CH4. CH4 is produced from CO or CO2 and H2 as building blocks via exothermic reaction pathways (see Reactions 5 and 6). One approach to limit CH4 formation is to use catalysts that favor C-C bond cleavage and the water gas shift (WGS) reaction over C-O bond cleavage and methanation reactions (Davda et al., 2003; Davda et al., 2005; Coronado et al., 2016). Some examples of these catalysts include rare earth metals supported catalysts such as Pt/SiO2, Pd/Al2O3, and Ru/C. Further, catalysts that have a basic character or operate in alkaline environments such as earth abundant Ni catalysts have also been shown to be effective in aiding H2 evolution (Stonor et al., 2017b).
In this study, we build on these observations to investigate the influence of methanation and its suppression on H2, CH4, CO, CO2, and CaCO3 yields. In the suppressed methanation case, the reactions associated with CH4 formation from CO and CO2 precursors are not included in the model. The studies are conducted at 227°C, N2 pressure of 50 bar, and biomass oxygenate concentrations of 20 wt%, with and without CO2 capture. For cases with CO2 capture, we used a stoichiometric amounts of CaO as defined by (reaction 13). In this study, we consider four scenarios for hydrothermal biomass oxygenate reactions: 1) with methanation, 2) without methanation, 3) alkaline treatment with methanation, and 4) alkaline treatment without methanation reactions (Figure 15).
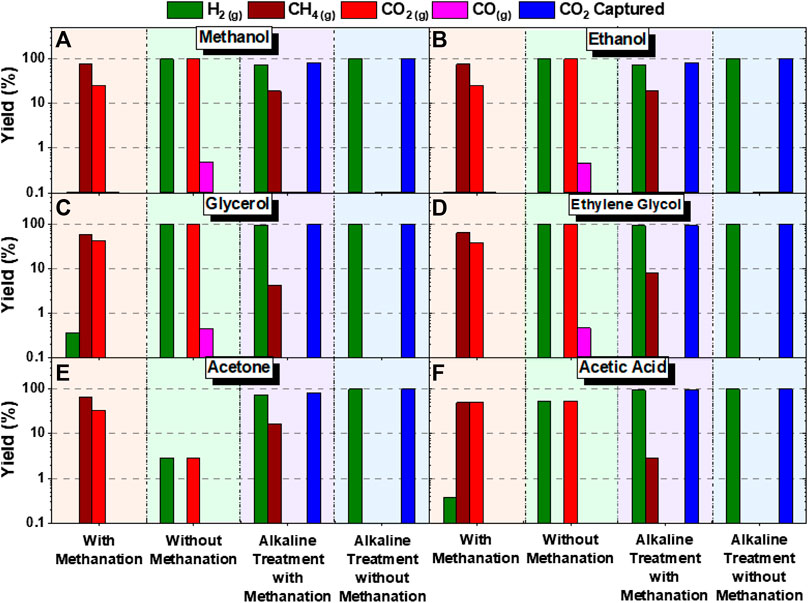
FIGURE 15. Comparison of theoretical product yields with 20 wt% of (A) methanol, (B) ethanol, (C) glycerol, (D) ethylene glycol, (E) acetone, (F) acetic acid. Thermodynamic product yield was computed for cases with methanation, catalytic effect (without methanation reactions), alkaline treatment with methanation, and alkaline treatment with catalytic effect (without methanation reactions). These calculations are performed with temperatures of 227°C and pressures of 50 bar.
In the scenario with methanation and without a catalyst, CH4 and CO2 compositions are dominant and H2 yields are less than 0.3%. In the scenario where methanation is suppressed by using a catalyst, H2 and CO2 yields are dominant, while CO formation is suppressed and there is no CH4 observed. For alkaline treatment with methanation, more than 70% conversion of H2 and CaCO3, and substantial CH4 yields are noted. No CO formation is noted in this case. For alkaline treatment without methanation, H2 and CaCO3 are the dominant phases. These results demonstrate that strategies to harness biomass oxygenates for H2 recovery with CO2 removal need to incorporate catalysts to suppress methane formation and alkaline sources for in-situ CO2 capture.
Analysis of the product streams provided further insights into the reactivities of various biomass oxygenates. The reactivities of the functional groups proceed in the descending order of OH > COOH > COR. This trend was similar with experimental results obtained by Fu and co-workers (Fu et al., 2020) who investigated the steam reforming of bio-oil and its derivatives and reported the highest H2 yield from reforming of ethylene glycol, followed by acetic acid, and acetone. Additionally, the separation of CO2 from the gas phase in the alkaline environment greatly limits methanation kinetically at low and moderate temperatures (less than 227°C) and enhances H2 production. The lower temperatures are potentially beneficial to catalyst life, and they significantly reduce cost. Furthermore, trace amounts of CO(10−12 %) were evident in all cases studied, implying that these processes are effective for generating hydrogen with CO content within the 20 ppm limit for fuel cell applications.
Conclusion
In this study, the thermodynamic limits for enhanced H2 recovery with inherent CO2 removal from various biomass oxygenate sources such as methanol, ethanol, glycerol, ethylene glycol, acetone, and acetic acid are reported. The effects of biomass oxygenate-to-water ratio, temperature, and suppression of the limiting methanation reactions on the yields of H2 and other associated compositions are investigated. As opposed to conventional high temperature reforming processes (> 500°C) at atmospheric pressure, we investigated the effect of maintaining fluids in the aqueous phase on under N2 pressure of 50 bar and at significantly lower temperatures <325°C. The effect of coupling thermodynamically downhill carbon mineralization reactions for in-situ CO2 capture to enhance H2 evolution was also studied. Higher H2 yields with in-situ CO2 capture were achieved with biomass oxygenate concentrations lower than 30 wt%. Water is needed as a reactant for the water gas shift reaction and to facilitate the dissolution of CaO for carbon mineralization. Temperatures around 220–230°C yielded high H2 conversion with in-situ CO2 capture. Further increases in temperature did not contribute to a significant enhancement in CO2 capture. The suppression of methanation reactions and in-situ CO2 capture to produce inorganic carbonates is crucial for producing high purity H2 that can be used in a fuel cell. The thermodynamic feasibility of these reaction pathways demonstrates that low value residues such as Ca-rich alkaline residues and wastewater streams bearing biomass oxygenates can be successfully upcycled to produce high value H2 with inherent CO2 removal.
Data Availability Statement
The original contributions presented in the study are included in the article/Supplementary Material, further inquiries can be directed to the corresponding author.
Author Contributions
PO conducted the analyses and completed the initial draft. CB and RK contributed to the resource assessments. GG conceptualized the study and contributed towards writing and editing.
Funding
This work was supported as part of the Cornell Atkinson Small Grant Program through the Reducing Climate Risk initiative funded by the Cornell Atkinson Center for Sustainability, Cornell University.
Conflict of Interest
The authors declare that the research was conducted in the absence of any commercial or financial relationships that could be construed as a potential conflict of interest.
Publisher’s Note
All claims expressed in this article are solely those of the authors and do not necessarily represent those of their affiliated organizations, or those of the publisher, the editors and the reviewers. Any product that may be evaluated in this article, or claim that may be made by its manufacturer, is not guaranteed or endorsed by the publisher.
Supplementary Material
The Supplementary Material for this article can be found online at: https://www.frontiersin.org/articles/10.3389/fenrg.2021.742323/full#supplementary-material
Abbreviations
References
Abanoz, K., Stark, B. C., and Akbas, M. Y. (2012). Enhancement of Ethanol Production from Potato-Processing Wastewater by Engineering Escherichia coli Using Vitreoscilla Haemoglobin. Lett. Appl. Microbiol. 55, 436–443. doi:10.1111/lam.12000
Ajao, V., Millah, S., Gagliano, M. C., Bruning, H., Rijnaarts, H., and Temmink, H. (2019). Valorization of Glycerol/ethanol-Rich Wastewater to Bioflocculants: Recovery, Properties, and Performance. J. Hazard. Mater. 375, 273–280. doi:10.1016/j.jhazmat.2019.05.009
Ali, E., Hadj-Kali, M. K., Mulyono, S., Alnashef, I., Fakeeha, A., Mjalli, F., et al. (2014). Solubility of CO2 in Deep Eutectic Solvents: Experiments and Modelling Using the Peng-Robinson Equation of State. Chem. Eng. Res. Des. 92, 1898–1906. doi:10.1016/j.cherd.2014.02.004
Arora, K., Kaur, P., Kumar, P., Singh, A., Patel, S. K. S., Li, X., et al. (2021). Valorization of Wastewater Resources into Biofuel and Value-Added Products Using Microalgal System. Front. Energ. Res. 9, 1–25. doi:10.3389/fenrg.2021.646571
Badawi, M. A., El-Shinnawi, M. M., Blanc, F. C., Wise, D. L., and El-Shimi, S. A. (1992). Production of Acetic Acid from Thermally Treated Sewage Sludge in an Upflow Anaerobic Reactor. Resour. Conserv. Recycl. 7, 201–212. doi:10.1016/0921-3449(92)90017-V
Baschuk, J. J., and Li, X. (2001). Carbon Monoxide Poisoning of Proton Exchange Membrane Fuel Cells. Int. J. Energ. Res. 25, 695–713. doi:10.1002/er.713
Benson, S. M., and Surles, T. (2006). Carbon Dioxide Capture and Storage: An Overview with Emphasis on Capture and Storage in Deep Geological Formations. Proc. IEEE 94, 1795–1804. doi:10.1109/JPROC.2006.883718
Brandt, A., Gräsvik, J., Hallett, J. P., and Welton, T. (2013). Deconstruction of Lignocellulosic Biomass with Ionic Liquids. Green. Chem. 15, 550–583. doi:10.1039/c2gc36364j
Cohce, M. K., Dincer, I., and Rosen, M. A. (2010). Thermodynamic Analysis of Hydrogen Production from Biomass Gasification. Int. J. Hydrogen Energ. 35, 4970–4980. doi:10.1016/j.ijhydene.2009.08.066
Coronado, I., Stekrova, M., Reinikainen, M., Simell, P., Lefferts, L., and Lehtonen, J. (2016). A Review of Catalytic Aqueous-phase Reforming of Oxygenated Hydrocarbons Derived from Biorefinery Water Fractions. Int. J. Hydrogen Energ. 41, 11003–11032. doi:10.1016/j.ijhydene.2016.05.032
Cortright, R. D., Davda, R. R., and Dumesic, J. A. (2010). Hydrogen from Catalytic Reforming of Biomass-Derived Hydrocarbons in Liquid Water. Mater. Sustain. Energ. A Collect. Peer-Reviewed Res. Rev. Artic. Nat. Publ. Gr. 418, 289–292. doi:10.1142/9789814317665_0043
Davda, R. R., Shabaker, J. W., Huber, G. W., Cortright, R. D., and Dumesic, J. A. (2003). Aqueous-phase Reforming of Ethylene Glycol on Silica-Supported Metal Catalysts. Appl. Catal. B Environ. 43, 13–26. doi:10.1016/S0926-3373(02)00277-1
Davda, R. R., Shabaker, J. W., Huber, G. W., Cortright, R. D., and Dumesic, J. A. (2005). A Review of Catalytic Issues and Process Conditions for Renewable Hydrogen and Alkanes by Aqueous-phase Reforming of Oxygenated Hydrocarbons over Supported Metal Catalysts. Appl. Catal. B Environ. 56, 171–186. doi:10.1016/j.apcatb.2004.04.027
De Vlieger, D. J. M., Mojet, B. L., Lefferts, L., and Seshan, K. (2012). Aqueous Phase Reforming of Ethylene Glycol - Role of Intermediates in Catalyst Performance. J. Catal. 292, 239–245. doi:10.1016/j.jcat.2012.05.019
Deluga, G. A., Salge, J. R., Schmidt, L. D., and Verykios, X. E. (2004). Renewable Hydrogen from Ethanol by Autothermal Reforming. Science 303, 993–997. doi:10.1126/science.1093045
Dissanayake, D., Rosynek, M. P., Kharas, K. C. C., and Lunsford, J. H. (1991). Partial Oxidation of Methane to Carbon Monoxide and Hydrogen over a Ni/Al2O3 Catalyst. J. Catal. 132, 117–127. doi:10.1016/0021-9517(91)90252-Y
Ellis, J. T., Hengge, N. N., Sims, R. C., and Miller, C. D. (2012). Acetone, Butanol, and Ethanol Production from Wastewater Algae. Bioresour. Technol. 111, 491–495. doi:10.1016/j.biortech.2012.02.002
Fateen, S. E. K., Khalil, M. M., and Elnabawy, A. O. (2013). Semi-empirical correlation for binary interaction parameters of the Peng-Robinson equation of state with the van der Waals mixing rules for the prediction of high-pressure vapor-liquid equilibrium. J. Adv. Res. 4, 137–145. doi:10.1016/j.jare.2012.03.004
Fu, P., Zhang, A., Luo, S., Yi, W., and Zhang, Y. (2020). Comparative Study on the Catalytic Steam Reforming of Biomass Pyrolysis Oil and its Derivatives for Hydrogen Production. RSC Adv. 10, 12721–12729. doi:10.1039/d0ra01409e
Gadikota, G., Park, A., and hyung, A. (2015). Accelerated Carbonation of Ca- and Mg-Bearing Minerals and Industrial Wastes Using CO2. Elsevier B.V. doi:10.1016/B978-0-444-62746-9.00008-6
Gadikota, G. (2020). Multiphase Carbon Mineralization for the Reactive Separation of CO2 and Directed Synthesis of H2. Nat. Rev. Chem. 4, 78–89. doi:10.1038/s41570-019-0158-3
Gadikota, G. (2021). Carbon Mineralization Pathways for Carbon Capture, Storage and Utilization. Commun. Chem. 4, 1–5. doi:10.1038/s42004-021-00461-x
He, C., Zheng, J., Wang, K., Lin, H., Wang, J. Y., and Yang, Y. (2015). Sorption Enhanced Aqueous Phase Reforming of Glycerol for Hydrogen Production over Pt-Ni Supported on Multi-Walled Carbon Nanotubes. Appl. Catal. B Environ. 162, 401–411. doi:10.1016/j.apcatb.2014.07.012
Hohn, K. L., and Schmidt, L. D. (2001). Partial Oxidation of Methane to Syngas at High Space Velocities over Rh-Coated Spheres. Appl. Catal. A. Gen. 211, 53–68. doi:10.1016/S0926-860X(00)00835-8
Jimmy, U., Mohamedali, M., and Ibrahim, H. (2017). Thermodynamic Analysis of Autothermal Reforming of Synthetic Crude Glycerol (Scg) for Hydrogen Production. ChemEngineering 1, 1–12. doi:10.3390/chemengineering1010004
Joensen, F., and Rostrup-Nielsen, J. R. (2002). Conversion of Hydrocarbons and Alcohols for Fuel Cells. J. Power Sourc. 105, 195–201. doi:10.1016/S0378-7753(01)00939-9
Khalilpour, R., Mumford, K., Zhai, H., Abbas, A., Stevens, G., and Rubin, E. S. (2015). Membrane-based Carbon Capture from Flue Gas: A Review. J. Clean. Prod. 103, 286–300. doi:10.1016/j.jclepro.2014.10.050
Kim, I. T., Yoo, Y. S., Yoon, Y. H., Lee, Y. E., Jo, J. H., Jeong, W., et al. (2018). Bio-Methanol Production Using Treated Domestic Wastewater with Mixed Methanotroph Species and Anaerobic Digester Biogas. Water (Switzerland) 10, 1414. doi:10.3390/w10101414
Li, Y., He, D., Niu, D., and Zhao, Y. (2015). Acetic Acid Production from Food Wastes Using Yeast and Acetic Acid Bacteria Micro-aerobic Fermentation. Bioproc. Biosyst. Eng. 38, 863–869. doi:10.1007/s00449-014-1329-8
Lima Da Silva, A., and Müller, I. L. (2011). Hydrogen Production by Sorption Enhanced Steam Reforming of Oxygenated Hydrocarbons (Ethanol, Glycerol, N-Butanol and Methanol): Thermodynamic Modelling. Int. J. Hydrogen Energ. 36, 2057–2075. doi:10.1016/j.ijhydene.2010.11.051
Lima da Silva, A., Malfatti, C. de. F., and Müller, I. L. (2009). Thermodynamic Analysis of Ethanol Steam Reforming Using Gibbs Energy Minimization Method: A Detailed Study of the Conditions of Carbon Deposition. Int. J. Hydrogen Energ. 34, 4321–4330. doi:10.1016/j.ijhydene.2009.03.029
Lindén, I., Backman, P., Brink, A., and Hupa, M. (2011). Influence of Water Vapor on Carbonation of CaO in the Temperature Range 400-550 °c. Ind. Eng. Chem. Res. 50, 14115–14120. doi:10.1021/ie2009795
Luo, N., Fu, X., Cao, F., Xiao, T., and Edwards, P. P. (2008). Glycerol Aqueous Phase Reforming for Hydrogen Generation over Pt Catalyst - Effect of Catalyst Composition and Reaction Conditions. Fuel 87, 3483–3489. doi:10.1016/j.fuel.2008.06.021
Masson-Delmotte, V., Zhai, P., Pörtner, H.-O., Roberts, D., Skea, J., Shukla, P. R., et al. (2018). IPCC Report Global Warming of 1.5°C. Ipcc - Sr15 2, 17–20. Available at: www.environmentalgraphiti.org.
Menezes, A. O., Rodrigues, M. T., Zimmaro, A., Borges, L. E. P., and Fraga, M. A. (2011). Production of Renewable Hydrogen from Aqueous-phase Reforming of Glycerol over Pt Catalysts Supported on Different Oxides. Renew. Energ. 36, 595–599. doi:10.1016/j.renene.2010.08.004
Mincer, T. J., and Aicher, A. C. (2016). Methanol Production by a Broad Phylogenetic Array of marine Phytoplankton. PLoS One 11, 1–17. doi:10.1371/journal.pone.0150820
Ming, Q., Healey, T., Allen, L., and Irving, P. (2002). Steam Reforming of Hydrocarbon Fuels. Catal. Today 77, 51–64. doi:10.1016/S0920-5861(02)00232-8
Novak, J. T., Goldsmith, C. D., Benoit, R. E., and O’Brien, J. H. (1985). Biodegradation of Methanol and Tertiary Butyl Alcohol in Subsurface Systems. Water Sci. Technol. 17, 71–85. doi:10.2166/wst.1985.0083
NRDC (2021). Food Waste in Cities. Available at: https://www.nrdc.org/food-matters (Accessed July 10, 2021).
Özcan, O., and Akın, A. N. (2019). Thermodynamic Analysis of Methanol Steam Reforming to Produce Hydrogen for HT-PEMFC: An Optimization Study. Int. J. Hydrogen Energ. 44, 14117–14126. doi:10.1016/j.ijhydene.2018.12.211
Peng, D. Y., and Robinson, D. B. (1976). A New Two-Constant Equation of State. Ind. Eng. Chem. Fundam. 15, 59–64. doi:10.1021/i160057a011
Qi, K., Li, Z., Zhang, C., Tan, X., Wan, C., Liu, X., et al. (2020). Biodegradation of Real Industrial Wastewater Containing Ethylene Glycol by Using Aerobic Granular Sludge in a Continuous-Flow Reactor: Performance and Resistance Mechanism. Biochem. Eng. J. 161, 107711. doi:10.1016/j.bej.2020.107711
Ranade, V. V., and Bhandari, V. M. (2014). Industrial Wastewater Treatment, Recycling, and Reuse: An Overview. Ind. Wastewater Treat. Recycl. Reuse, 1–80. doi:10.1016/B978-0-08-099968-5.00001-5
Rochelle, G. T. (2009). Amine Scrubbing for CO2 Capture. Science 325, 1652–1654. doi:10.1126/science.1176731
Roy, B., Martinez, U., Loganathan, K., Datye, A. K., and Leclerc, C. A. (2012). Effect of Preparation Methods on the Performance of Ni/Al 2O 3 Catalysts for Aqueous-phase Reforming of Ethanol: Part I-Catalytic Activity. Int. J. Hydrogen Energ. 37, 8143–8153. doi:10.1016/j.ijhydene.2012.02.056
Sayari, A., Belmabkhout, Y., and Serna-Guerrero, R. (2011). Flue Gas Treatment via CO2 Adsorption. Chem. Eng. J. 171, 760–774. doi:10.1016/j.cej.2011.02.007
Shabaker, J. W., Huber, G. W., Davda, R. R., Cortright, R. D., and Dumesic, J. A. (2003). Aqueous-phase Reforming of Ethylene Glycol over Supported Platinum Catalysts. Catal. Lett. 88, 1–8. doi:10.1023/A:1023538917186
Smith, J. R. E., and Hinshelwood, C. N. (1944). The thermal Decomposition of Acetone. Proc. R. Soc. Lond. Ser. A. Math. Phys. Sci. 183, 33–37. doi:10.1098/rspa.1944.0019
Spence, R., and Wild, W. (1936). Mechanism of the Photo-Decomposition of Acetone. Nature 138, 206. doi:10.1038/138206b0
Stonor, M. R., Chen, J. G., and Park, A. H. A. (2017a). Bio-Energy with Carbon Capture and Storage (BECCS) Potential: Production of High Purity H2 from Cellulose via Alkaline Thermal Treatment with Gas Phase Reforming of Hydrocarbons over Various Metal Catalysts. Int. J. Hydrogen Energ. 42, 25903–25913. doi:10.1016/j.ijhydene.2017.08.059
Stonor, M. R., Ouassil, N., Chen, J. G., and Park, A. H. A. (2017b). Investigation of the Role of Ca(OH)2 in the Catalytic Alkaline Thermal Treatment of Cellulose to Produce H2 with Integrated Carbon Capture. J. Energ. Chem. 26, 984–1000. doi:10.1016/j.jechem.2017.07.013
Thompson, J. C., and He, B. B. (2006). Characterization of Crude Glycerol from Biodiesel Production from Multiple Feedstocks. 22, 261–265. doi:10.13031/2013.20272
U.S. Department of Energy Ohi, J. M., Vanderborgh, N., and Voecks, G. (2016). Hydrogen Fuel Quality Specifications for Polymer Electrolyte Fuel Cells in Road Vehicles. Safety, Codes Stand. Progr, 1–72.
Uçkun Kiran, E., and Liu, Y. (2015). Bioethanol Production from Mixed Food Waste by an Effective Enzymatic Pretreatment. Fuel 159, 463–469. doi:10.1016/j.fuel.2015.06.101
Wang, C., Jia, L., Tan, Y., and Anthony, E. J. (2008). Carbonation of Fly Ash in Oxy-Fuel CFB Combustion. Fuel 87, 1108–1114. doi:10.1016/j.fuel.2007.06.024
Wen, G., Xu, Y., Ma, H., Xu, Z., and Tian, Z. (2008). Production of Hydrogen by Aqueous-phase Reforming of Glycerol. Int. J. Hydrogen Energ. 33, 6657–6666. doi:10.1016/j.ijhydene.2008.07.072
WHO (2009). The Energy Access Situation in Developing Countries. UNDP WHO New York, 142. Available at: http://www.who.int/indoorair/publications/PowerPoint_Energy_Access_paper-lr.pdf%0Ahttp://scholar.google.com/scholar?hl=en&btnG=Search&q=intitle:THE+ENERGY+ACCESS+SITUATION+IN+DEVELOPING+COUNTRIES+A+Review+Focusing+on+the#0.
Williams, M. L. (1996). CRC Handbook of Chemistry and Physics. Occup. Environ. Med. 53, 504. doi:10.1136/oem.53.7.504
Yan, S., Chen, X., Wu, J., and Wang, P. (2012). Ethanol Production from Concentrated Food Waste Hydrolysates with Yeast Cells Immobilized on Corn Stalk. Appl. Microbiol. Biotechnol. 94, 829–838. doi:10.1007/s00253-012-3990-7
Keywords: hydrogen, carbon removal, biomass oxygenates, calcium carbonate, thermodynamics
Citation: Ochonma P, Blaudeau C, Krasnoff R and Gadikota G (2021) Exploring the Thermodynamic Limits of Enhanced H2 Recovery With Inherent Carbon Removal From Low Value Aqueous Biomass Oxygenate Precursors. Front. Energy Res. 9:742323. doi: 10.3389/fenrg.2021.742323
Received: 16 July 2021; Accepted: 30 August 2021;
Published: 29 September 2021.
Edited by:
Andreas Borgschulte, Swiss Federal Laboratories for Materials Science and Technology, SwitzerlandReviewed by:
Federico Rossi, University of Siena, ItalyZaki Yamani Zakaria, University of Technology Malaysia, Malaysia
Copyright © 2021 Ochonma, Blaudeau, Krasnoff and Gadikota. This is an open-access article distributed under the terms of the Creative Commons Attribution License (CC BY). The use, distribution or reproduction in other forums is permitted, provided the original author(s) and the copyright owner(s) are credited and that the original publication in this journal is cited, in accordance with accepted academic practice. No use, distribution or reproduction is permitted which does not comply with these terms.
*Correspondence: Greeshma Gadikota, Z2c0NjRAY29ybmVsbC5lZHU=