- Department of Civil and Environmental Engineering, University of Alberta, Edmonton, AB, Canada
For the past two decades, many successful applications of microbial electrochemical technologies (METs), such as bioenergy generation, environmental monitoring, resource recovery, and platform chemicals production, have been demonstrated. Despite these tremendous potentials, the scaling-up and commercialization of METs are still quite challenging. Depending on target applications, common challenges may include expensive and tedious fabrication processes, prolonged start-up times, complex design requirements and their scalability for large-scale systems. Incorporating the three-dimensional printing (3DP) technologies have recently emerged as an effective and highly promising method for fabricating METs to demonstrate power generation and biosensing at the bench scale. Notably, low-cost and rapid fabrication of complex and miniaturized designs of METs was achieved, which is not feasible using the traditional methods. Utilizing 3DP showed tremendous potentials to aid the optimization of functional large-scale METs, which are essential for scaling-up purposes. Moreover, 3D-printed bioanode could provide rapid start-up in the current generation from METs without any time lags. Despite numerous review articles published on different scientific and applied aspects of METs, as per the authors’ knowledge, no published review articles explicitly highlighted the applicability and potential of 3DP for developing METs. Hence, this review targets to provide a current overview and status of 3DP applications for advancing METs and their future outlook.
Introduction
Microbial electrochemical technologies (METs) are unique platforms that combine microbial metabolism with electrochemistry for various value-added applications (Sravan et al., 2021). Over the last 2 decades, many different applications of METs have been demonstrated: 1) bioenergy generation, such as bio-electricity in microbial fuel cells (MFCs) (Munoz-Cupa et al., 2020; Sravan et al., 2021), bio-hydrogen in microbial electrolysis cells (MECs) (Hua et al., 2019; Rousseau et al., 2020), and bio-methane in MEC assisted anaerobic digesters (Zakaria and Dhar, 2019; Huang et al., 2020); 2) synthesis of platform chemicals, such as hydrogen peroxide (Chung et al., 2020b; Zhao et al., 2021); 3) nutrient recovery (Zou et al., 2017; Barua et al., 2019); 4) water desalination (Al-Mamun et al., 2018; Jafary et al., 2020); 5) biosensors (Do et al., 2020; Chung et al., 2020a); and many more. Despite such tremendous potential, studies emphasized the challenges in system design and fabrication, which must be addressed to improve their performance and robustness, especially for scaling-up and commercialization (Dhar et al., 2016b; Sim et al., 2018; Zakaria and Dhar, 2019). Specifically, developing a low-cost and efficient fabrication technique is imperative for advancing METs (Bian et al., 2018a; Theodosiou et al., 2020; You et al., 2020). The utilization of conventional subtractive manufacturing methods is time-consuming and highly laborious and can generate wastes from cutting materials away from larger pieces (Theodosiou et al., 2020; You et al., 2020). Moreover, the precise manufacturing of miniaturized METs for applications like biosensors is also challenging. For instance, construction defects such as widening of spacings between parts and fittings or unwanted pinholes may result in the intrusion of microbubbles, which can significantly reduce the biosensing performance (Fraiwan et al., 2013). Therefore, developing a highly functional, low-cost, and environmentally sustainable fabrication method is essential for reducing time lags toward commercialization of METs (You et al., 2017; Bian et al., 2018a; You et al., 2020).
The additive manufacturing (AM) process or three-dimensional printing (3DP) has been expanding rapidly in recent years. Briefly, 3DP generates 3D structures from computer-aided design (CAD) models by adding the material layer-by-layer, allowing rapid and precise fabrication of sophisticated structures and devices with complex geometry with minimum human interventions (Geissler and Xia, 2004; Bian et al., 2018b; You et al., 2020). Due to these promising features, 3DP has been implemented in various fields, including industrial prototype printing, aerospace (Griffiths, 2015), medical implants (Murphy and Atala, 2014; Rasperini et al., 2015), and arts (Walters and Davies, 2010). Moreover, 3DP has been applied to various energy-generating systems, such as solar cells (Angmo et al., 2013; Vak et al., 2015) and batteries (Sun et al., 2013; Izumi et al., 2014). Owing to the increased popularity and applicability, 3DP has recently been applied to fabricate different parts of METs, such as reactor bodies, electrodes, and membranes (Table 1). To the authors' knowledge, no review articles critically appraised the literature published on the application of 3DP for developing METs. Hence, this paper aims to provide a critical appraisal of the studies that utilized 3DP for METs. Furthermore, potential future developments and recommendations are outlined.
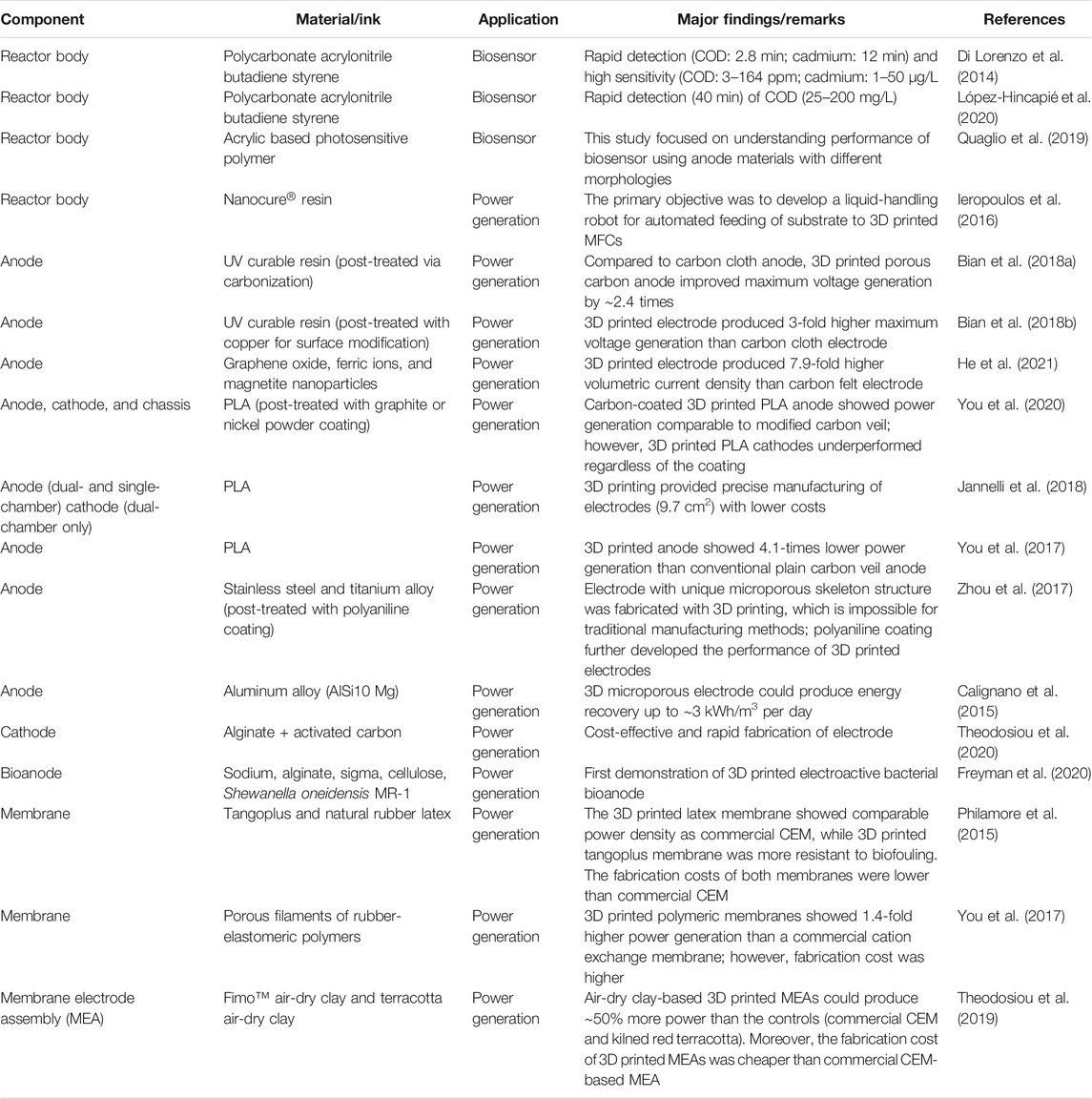
TABLE 1. Summary of studies used 3D printing for the fabrication of key components in microbial fuel cells.
Application of 3D Printing for Microbial Electrochemical Technologies
Reactor Body
The majority of METs are primarily developed for water/wastewater applications; thus, different types of reactor architectures can significantly influence the effective flow and hydrodynamics (e.g., mass transfer within biofilms) and thereby influence their performance (Kim et al., 2014; Jiang et al., 2015; Yi et al., 2020). Hence, optimizing the shape of the system, working volumes, fluid inlet/outlet settings are critical (Logan et al., 2015; Massaglia et al., 2017; Yi et al., 2020). For instance, a drop-like-shaped MFC could perform better than a square-shaped one due to the larger effective exposed area (Massaglia et al., 2017). Moreover, the addition of baffles in the anode chamber could result in higher voltage output in MFCs due to reduced dead zones where the flow velocity is <5% of the maximum velocity (Yi et al., 2020). However, fabrication of such designs and configurations can be extremely challenging using the traditional manufacturing technique, especially for the miniaturized METs. Several studies have reported successful utilization of 3DP for precise fabrication of reactor bodies for METs (see Table 1).
Di Lorenzo et al. (2014) applied 3DP for rapid fabrication of a miniaturized (2 cm3) air-cathode MFC biosensor. Their fabricated MFC biosensor exhibited a good detection range (3–164 ppm), high sensitivity (0.5 μA mM−1 cm−2), a fast response time (2.8 min), and fast recovery time (12 min) while detecting cadmium ions in water samples. Moreover, Quaglio et al. (2019) developed 3D-printed a MFC biosensor (12.5 ml), which allowed optimizing hydrodynamics (optimal fluid motion) and morphology of anode electrode (porosity) via computational fluid dynamics (CFD) modeling for quantification of sodium acetate in water samples. Although 3DP can allow bulk production of small-scale reactors for applications like biosensing within reasonable timeframes and costs, direct 3D printing of large-scale systems is not yet feasible. Nonetheless, approaches like combining 3DP and CFD modeling can enable low-cost advanced reactor engineering for large-scale field applications (e.g., wastewater treatment) of METs. For instance, governing equations for mass, momentum, and energy conservation to find numerical solutions in CFD modeling are not scale-dependent (Parra-Cabrera et al., 2018). Thus, when combined with CFD, 3D printed lab-scale prototypes can still be used for the design and optimization of large-scale systems.
Electrodes
The development of electrodes that possess highly porous structures for optimal bacterial adhesion and excellent electrochemical performance for high current output has been of great interest to the MET research communities (Zhou et al., 2017; Bian et al., 2018a; Bian et al., 2018b). Notably, complex macro-porous 3D electrode materials have been found suitable for providing a larger surface area for the biofilm developments and thereby improve the electrochemical performance of METs (Hindatu et al., 2017; Zhou et al., 2017). However, the major hurdle is in the precise construction of electrodes with geometrical complexities (e.g., porous electrodes) using the traditional manufacturing method (Zhou et al., 2017; Bian et al., 2018a; Bian et al., 2018b). Recently, researchers have explored 3DP for rapid prototyping of such ideal electrodes METs.
Zhou et al. (2017) reported that 3DP could allow the precise design of porous 3D structured X-shape skeleton electrodes with titanium and stainless steel as printing materials. The further modification of 3D-printed metal electrodes with polyaniline could provide a crumpled and biocompatible surface. Notably, the polyaniline coating of the 3D-printed titanium electrode could increase power density up to 400 times than the uncoated one. Calignano et al. (2015) developed an aluminum alloy (AlSi10 Mg) anode using 3DP, which could enable energy output of up to 3 kWh/m3 per day from an MFC. The authors suggested that the 3D microporous coral skeletal structure could provide surface roughness and excellent biocompatibility to electroactive microbes. However, metal 3D printing is still extremely expensive (Pumera, 2019). Moreover, some metal alloys used for 3DP (e.g., AlSi10 Mg) alloy are prone to corrosion (You et al., 2017; Revilla et al., 2020). Previous studies also demonstrated the feasibility of utilizing polymeric materials, such as polylactic acid (PLA), UV curable resin, for 3D printing of electrodes for METs (see Table 1). However, the electrochemical performance of 3D-printed polymeric electrodes is not always satisfactory. For instance, power generation from the PLA electrode developed by You et al. (2017) was ∼4 times lower than the control (plain carbon veil) with the same geometric structures. Despite conductive properties, thin protective polymer layers on the surface of 3D-printed polymeric electrodes can restrict electrochemical performance, which can be removed by surface modification (Pumera, 2019). Bian et al. (2018a) proposed carbonization of the 3D-printed anode from polymer resin to enhance the biocompatibility, which could produce significantly higher power density than a traditional carbon cloth anode (233.5 vs. 69 mW/m2). Similarly, surface modification of a 3D-printed polymeric electrode with copper could produce 12.3-fold higher power than copper mesh electrodes (Bian et al., 2018b). Most recently, He et al. (2021) developed a 3D-printed graphene oxide (GO) aerogel anode with a customized printing ink combining GO, ferric ions, and magnetite nanoparticles. The hierarchical pores in their GO aerogel electrode could provide effective mass transfer of substrates, leading to 7.9 folds higher volumetric current output than carbon felt anode. Thus, utilizing 3DP for electrode fabrication has shown promising results. While cost and performance are often the primary aspects considered by researchers, ensuring the long-term stability (chemical stability, corrosion resistance, etc.) of 3D-printed electrodes would be critical.
Bioelectrode
Besides electrodes and other physical components of METs, electroactive microorganisms are vital components affecting METs performance (Koch and Harnisch, 2016). The selection and enrichment of kinetically efficient electroactive bacteria (EAB) are often challenging (Torres et al., 2009; Dhar et al., 2016a). Due to slow growth kinetics, the time required for complete enrichment of anode or cathode biofilms can be significant (e.g., months-years), ultimately prolonging the reactor start-up time (Zakaria and Dhar, 2019). Several studies have utilized the effluent from MET reactors as an inoculum source (Zakaria et al., 2018; Barua et al., 2019; Chung et al., 2020a), which can expedite the enrichment process of electroactive biofilms. However, an innovative approach for the rapid establishment of electroactive biofilms is still required. A recent study by Freyman et al. (2020) suggested that 3DP can provide an attractive solution to such time-consuming biofilms development procedures. They investigated 3DP for constructing a bioanode with Shewanella oneidensis MR-1 as living inks. More importantly, Shewanella oneidensis MR-1 survived during the 3D printing process, and their MFC produced a stable current for almost 93 h. Of note, prior to their study, 3DP was applied to engineer 3D objects and structures with microorganisms, such as Escherichia coli, Pseudomonas putida, Acetobacter xylinum, yeast cells (Lehner et al., 2017; Schaffner et al., 2017; Qian et al., 2019). Particularly, due to the adhesion of cells during the process, objects 3D-printed with microbes could potentially achieve a high cell density. Nonetheless, based on the authors’ knowledge, Freyman et al. (2020) first demonstrated the feasibility of 3D-printed bioanode, potentially opening up new possibilities for high-performance METs.
Ion-Exchange Membranes
Ion-exchange membranes (IEM) are imperative, especially for the dual-chamber METs, to facilitate the ion transport between anode and cathode, governing the electroneutrality (Dhar and Lee, 2013; Leong et al., 2013). The IEMs can alter the current output, depending on their relative surface area, which is associated with ionic conductivity and internal resistance of METs (Zuo et al., 2007; Philamore et al., 2015). Hence, increasing the specific ion-exchange area of IEM is great of interest, but it is often a major challenge (Philamore et al., 2015). Notably, commercially available IEMs can be costly (e.g., >700 USD/m2 for Nafion) due to the complex manufacturing process (Yee et al., 2012; Dhar and Lee, 2013). Besides, IEMs require pre-treatment processes (Ghasemi et al., 2013; Rahimnejad et al., 2014), which can be time-consuming. Therefore, an efficient and low-cost membrane manufacturing method is greatly needed.
Several studies implemented 3DP as an alternative fabrication method for IEMs (Philamore et al., 2015; You et al., 2017; Theodosiou et al., 2019). Philamore et al. (2015) have manufactured IEMs for METs utilizing 3DP at a much lower cost than commercial CEM ($0.00112–0.00357 for latex and $0.16 for Tangoplus resin vs. $0.22–40 for commercial CEM, per 20 cm2, USD). The power generation from an MFC with a 3D-printed latex membrane was comparable to commercial CEM (10.51 vs. 11.39 µW). In contrast, maximum power generation was much lower in the MFC with a 3D-printed Tangoplus membrane (0.92 µW). Nonetheless, the latex membrane was more prone to fouling and almost damaged after 210 days of operation, while the Tangoplus membrane was more resistant to biofouling. In contrast, 3D printed membrane using rubber-elastomeric polymers developed by You et al. (2017) could increase maximum power output up to 1.4 times than commercial CEM; however, the fabrication cost of the 3D-printed membrane was higher than commercial CEM. Thus, these results suggested that selecting low-cost and durable polymeric materials would be necessary for fabricating economic and technically sustainable 3D-printed IEMs. However, previous studies primarily focused on the performance of 3D-printed IEMs in terms of current output and biofouling potential, while limited information provided on other critical features, such as proton permeability, membrane resistance, substrate loss, and oxygen diffusion (in MFCs) (Dhar and Lee, 2013).
Membrane Electrode Assembly (MEA)
The spacing between electrodes is critical for minimizing internal energy losses in METs (Moon et al., 2015b). Therefore, MEA (membrane sandwiched between electrodes) has been considered by many researchers to reduce internal energy losses and thereby improve the performance of METs (Moon et al., 2015b). Typically, MEAs are prepared by pressing membrane and electrodes with or without heat treatment (Theodosiou et al., 2019), which has multiple drawbacks. For instance, a high degree of hydrophilicity can often cause anolyte leakage from the surface of MEA (Mashkour et al., 2021). Furthermore, uneven physical contact between membrane and electrode resulting from the conventional fabrication method can increase internal resistance and ultimately lower the current output (Moon et al., 2015a; Vilela et al., 2020). Therefore, precise fabrication methods for MEA are required. Recently, Theodosiou et al. (2019) compared 3D-printed MEAs with a commercial CEM. The 3D-printed MEAs from air-dry clay materials exhibited up to 50% higher power output (130 vs. 66 µW) for >70 days and provided 34–51 times cheaper production cost. Although the results were promising, future studies should focus on a comprehensive investigation of underlying mechanisms that can provide a superior performance of 3D-printed MEAs over the conventional ones.
Summary and Outlook
With the recent advancement in 3D printing technologies, their application in METs has been gaining attention. Previous studies demonstrated the potential as a precise and rapid fabrication method for different components of METs. Notably, 3DP could control complex geometric structures of electrodes with customized properties (e.g., porosity, roughness, etc.) to improve efficiency over traditional electrodes (discussed earlier). Although outcomes have been promising, several drawbacks, such as high cost, low durability, biocompatibility, and electrochemical properties of 3D printed components (Angmo et al., 2013; Wei et al., 2015; You et al., 2017), may limit the application of 3DP for METs (Bian et al., 2018a). Therefore, future research should continue to seek low-cost but well-performing 3D-printable materials for MET components.
While polymeric materials would be a better choice for keeping the cost low (You et al., 2017), activation or post-treatment would be necessary to achieve desired performance from 3D-printed electrodes (Baran and Erbil, 2019; Pumera, 2019). It is expected that activation steps will increase the fabrication time and cost. Recently, various simple and low-cost activation methods for 3D-printed polymer electrodes have been developed for improving conductive properties for various electrochemical applications (Browne et al., 2018; Pumera, 2019). For instance, dimethylformamide (DMF) immersion and electrochemical activation by applying constant potential have recently been demonstrated as simple and cost-effective methods for activating 3D printed polymer/graphene by removing the insulating polymer layer (Browne et al., 2018; Pumera, 2019). These methods should be explored for developing highly conductive 3D-printed polymer electrodes for METs. Moreover, strategies for improving biocompatibility would be an additional aspect that needs to be addressed by the METs research community. Likewise, there have been significant developments toward developing advanced 3D-printed membranes for various industrial applications (Lee et al., 2016; Lv et al., 2017). Thus, multidisciplinary collaborations in these areas can promote rapid development.
As an emerging concept, the feasibility of 3D-printed bioelectrode could still be questionable. However, EAB can rapidly recover from extreme and harsh environments, such as extremely low-temperature settings below freezing point (Winfield et al., 2015; Cho et al., 2020), long-term (5–10 days) starvation (Ruiz et al., 2015; Dhar et al., 2018). The digital printing of electroactive cyanobacterium onto the paper electrode was also successful in the past (Sawa et al., 2017). Thus, the concept of 3D-printed bioelectrode should be highly feasible with further developments, which can undoubtedly shorten the start-up time of METs. Additionally, there are still many other possibilities to utilize such an innovative approach to further advance METs. In METs, energy recovery from complex organic substrates requires a partnership between EAB and their syntrophic partners (e.g., fermentative bacteria), as complex substrates (e.g., fermentable organics) can not be directly oxidized by EAB (Parameswaran et al., 2009; Dhar et al., 2019; Zakaria and Dhar, 2020). However, existing literature provides limited information on how to manipulate or develop a well-balanced syntrophic community for high-performance METs. It can be envisioned that the application of 3DP can offer a pragmatic solution to develop living bioelectrode with a designer syntrophic co-culture with target functionality (e.g., electron recovery from a specific complex electron donor). Thus, it will be interesting to see the feasibility and sustainability (i.e., long-term reliable operation) of such new opportunities.
Moreover, the broader impact of 3DP can be facilitated by incorporating other research tools, such as CFD and machine learning (ML) modeling tools (Figure 1). As discussed earlier, the combination of CFD and 3DP bears immense potential as a design optimization tool for large-scale METs. Particularly, the CFD model can provide critical information on the crucial parameters, such as maximum flow locations and dead zones with different designs for METs (Kim et al., 2014; Yi et al., 2020). The information can be adopted to rethink and redesign METs that can be rapidly prototyped with 3DP and tested for further validation. Moreover, incorporating ML techniques with 3DP can also be useful. For instance, previous studies substantiated the significance of printing inks on the performance and sustainability of 3D-printed components of METs (Philamore et al., 2015; You et al., 2017; Theodosiou et al., 2019). ML can be utilized to select efficient printing materials for achieving specific characteristics, such as conductivity, porosity, and surface roughness required for 3D-printed components of METs. The lack of METs-specific training data and data source variability could be barriers to such developments. However, there have been developments toward ML algorithm validation with a small amount of training data (Vabalas et al., 2019). Therefore, future studies should explore these options for optimal design and fabrication of 3D-printed components, especially for larger-scale METs, in which, the current challenges and limitations were discussed earlier.
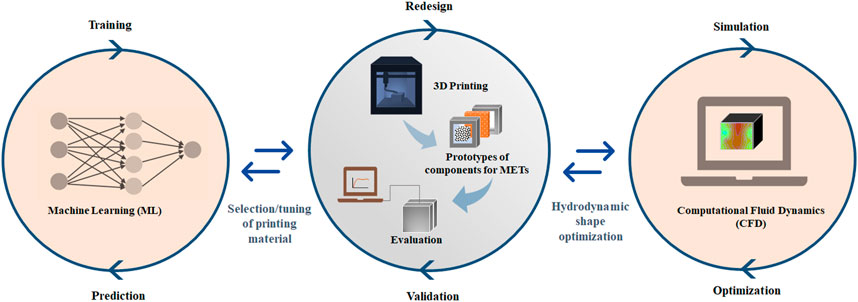
FIGURE 1. A proposed framework combining 3D printing with machine learning (ML) and computational fluid dynamics (CFD) modeling for design, optimization, and fabrication of systems for METs.
Author Contributions
TC: Conceptualization, Investigation, Writing-original draft, Writing-review & editing BD: Conceptualization, Funding acquisition, Supervision, Writing-original draft, Writing-review & editing.
Conflict of Interest
The authors declare that the research was conducted in the absence of any commercial or financial relationships that could be construed as a potential conflict of interest.
Acknowledgments
This work was supported by the Discovery Grant (#2017–05608) from the Natural Sciences and Engineering Research Council of Canada (NSERC). The first author of this article (TC) acknowledges support from Alberta Innovates Graduate Student Scholarship and NSERC Alexander Graham Bell Canada Graduate Scholarship-Doctoral programs.
References
Al-Mamun, A., Ahmad, W., Baawain, M. S., Khadem, M., and Dhar, B. R. (2018). A Review of Microbial Desalination Cell Technology: Configurations, Optimization and Applications. J. Clean. Prod. 183, 458–480. doi:10.1016/j.jclepro.2018.02.054
Angmo, D., Larsen-Olsen, T. T., Jørgensen, M., Søndergaard, R. R., and Krebs, F. C. (2013). Roll-to-roll Inkjet Printing and Photonic Sintering of Electrodes for ITO Free Polymer Solar Cell Modules and Facile Product Integration. Adv. Energy Mater. 3 (2), 172–175. doi:10.1002/aenm.201200520
Baran, E., and Erbil, H. (2019). Surface Modification of 3D Printed PLA Objects by Fused Deposition Modeling: A Review. Colloids Inter. 3 (2), 43. doi:10.3390/colloids3020043
Barua, S., Zakaria, B. S., Chung, T., Hai, F. I., Haile, T., Al-Mamun, A., et al. (2019). Microbial Electrolysis Followed by Chemical Precipitation for Effective Nutrients Recovery from Digested Sludge Centrate in WWTPs. Chem. Eng. J. 361, 256–265. doi:10.1016/j.cej.2018.12.067
Bian, B., Shi, D., Cai, X., Hu, M., Guo, Q., Zhang, C., et al. (2018a). 3D Printed Porous Carbon Anode for Enhanced Power Generation in Microbial Fuel Cell. Nano Energy 44, 174–180. doi:10.1016/j.nanoen.2017.11.070
Bian, B., Wang, C., Hu, M., Yang, Z., Cai, X., Shi, D., et al. (2018b). Application of 3D Printed Porous Copper Anode in Microbial Fuel Cells. Front. Energ. Res. 6, 50. doi:10.3389/fenrg.2018.00050
Browne, M. P., Novotný, F., Sofer, Z., and Pumera, M. (2018). 3D Printed Graphene Electrodes' Electrochemical Activation3D Printed Graphene Electrodes’ Electrochemical Activation. ACS Appl. Mater. Inter. 10 (46), 40294–40301. doi:10.1021/acsami.8b14701
Calignano, F., Tommasi, T., Manfredi, D., and Chiolerio, A. (2015). Additive Manufacturing of a Microbial Fuel Cell—A Detailed Study. Scientific Rep. 5 (1), 1–10. doi:10.1038/srep17373
Cho, J. H., Gao, Y., Ryu, J., and Choi, S. (2020). Portable, Disposable, Paper-Based Microbial Fuel Cell Sensor Utilizing Freeze-Dried Bacteria for In Situ Water Quality Monitoring. ACS omega 5 (23), 13940–13947. doi:10.1021/acsomega.0c01333
Chung, T. H., Meshref, M. N., and Dhar, B. R. (2020a). Microbial Electrochemical Biosensor for Rapid Detection of Naphthenic Acid in Aqueous Solution. J. Electroanal. Chem. 873, 114405. doi:10.1016/j.jelechem.2020.114405
Chung, T. H., Meshref, M. N., Hai, F. I., Al-Mamun, A., and Dhar, B. R. (2020b). Microbial Electrochemical Systems for Hydrogen Peroxide Synthesis: Critical Review of Process Optimization, Prospective Environmental Applications, and Challenges. Bioresour. Technol. 313, 123727. doi:10.1016/j.biortech.2020.123727
Dhar, B. R., and Lee, H.-S. (2013). Membranes for Bioelectrochemical Systems: Challenges and Research Advances. Environ. Technol. 34 (13-16), 1751–1764. doi:10.1080/09593330.2013.822007
Dhar, B. R., Park, J.-H., Park, H.-D., and Lee, H.-S. (2019). Hydrogen-based Syntrophy in an Electrically Conductive Biofilm Anode. Chem. Eng. J. 359, 208–216. doi:10.1016/j.cej.2018.11.138
Dhar, B. R., Ren, H., Chae, J., and Lee, H.-S. (2018). Recoverability of Electrical Conductivity of a Geobacter-Enriched Biofilm. J. Power Sourc. 402, 198–202. doi:10.1016/j.jpowsour.2018.09.039
Dhar, B. R., Ryu, H., Ren, H., Domingo, J. W. S., Chae, J., and Lee, H.-S. (2016a). High Biofilm Conductivity Maintained Despite Anode Potential Changes in a Geobacter-Enriched Biofilm. ChemSusChem. 9 (24), 3485–3491. doi:10.1002/cssc.201601007
Dhar, B. R., Ryu, H., Santo Domingo, J. W., and Lee, H.-S. (2016b). Ohmic Resistance Affects Microbial Community and Electrochemical Kinetics in a Multi-Anode Microbial Electrochemical Cell. J. Power Sourc. 331, 315–321. doi:10.1016/j.jpowsour.2016.09.055
Di Lorenzo, M., Thomson, A. R., Schneider, K., Cameron, P. J., and Ieropoulos, I. (2014). A Small-Scale Air-Cathode Microbial Fuel Cell for On-Line Monitoring of Water Quality. Biosens. Bioelectron. 62, 182–188. doi:10.1016/j.bios.2014.06.050
Do, M. H., Ngo, H. H., Guo, W., Chang, S. W., Nguyen, D. D., Liu, Y., et al. (2020). Microbial Fuel Cell-Based Biosensor for Online Monitoring Wastewater Quality: A Critical Review. Sci. Total Environ. 712, 135612. doi:10.1016/j.scitotenv.2019.135612
Fraiwan, A., Sundermier, S., Han, D., Steckl, A. J., Hassett, D. J., and Choi, S. (2013). Enhanced Performance of Micro-electro-mechanical-systems (MEMS) Microbial Fuel Cells Using Electrospun Microfibrous Anode and Optimizing Operation. Fuel Cells 13 (3), 336–341. doi:10.1002/fuce.201200225
Freyman, M. C., Kou, T., Wang, S., and Li, Y. (2020). 3D Printing of Living Bacteria Electrode. Nano Res. 13 (5), 1318–1323. doi:10.1007/s12274-019-2534-1
Geissler, M., and Xia, Y. (2004). Patterning: Principles and Some New Developments. Adv. Mater. 16 (15), 1249–1269. doi:10.1002/adma.200400835
Ghasemi, M., Wan Daud, W. R., Ismail, M., Rahimnejad, M., Ismail, A. F., Leong, J. X., et al. (2013). Effect of Pre-treatment and Biofouling of Proton Exchange Membrane on Microbial Fuel Cell Performance. Int. J. Hydrogen Energ. 38 (13), 5480–5484. doi:10.1016/j.ijhydene.2012.09.148
Griffiths, L. (2015). 3D Printing for Aerospace:‘‘additive Manufacturing Will Change the Game Forever”. TCT Magazine, July (2015).
He, Y.-T., Fu, Q., Pang, Y., Li, Q., Li, J., Zhu, X., et al. (2021). Customizable Design Strategies for High-Performance Bioanodes in Bioelectrochemical Systems. Iscience 24 (3), 102163. doi:10.1016/j.isci.2021.102163
Hindatu, Y., Annuar, M. S. M., and Gumel, A. M. (2017). Mini-review: Anode Modification for Improved Performance of Microbial Fuel Cell. Renew. Sust. Energ. Rev. 73, 236–248. doi:10.1016/j.rser.2017.01.138
Hua, T., Li, S., Li, F., Zhou, Q., and Ondon, B. S. (2019). Microbial Electrolysis Cell as an Emerging Versatile Technology: a Review on its Potential Application, Advance and Challenge. J. Chem. Technol. Biotechnol. 94 (6), 1697–1711. doi:10.1002/jctb.5898
Huang, Q., Liu, Y., and Dhar, B. R. (2020). A Critical Review of Microbial Electrolysis Cells Coupled with Anaerobic Digester for Enhanced Biomethane Recovery from High-Strength Feedstocks. Crit. Rev. Environ. Sci. Tech. 2020, 1–40. doi:10.1080/10643389.2020.1813065
Ieropoulos, I., Taylor, B., Theodosiou, P., Stoy, K., Nejatimoharrami, F., and Faíña, A. (2016). “EvoBot: an Open-Source, Modular Liquid Handling Robot for Nurturing Microbial Fuel Cells,” in Proceedings of the Artificial Life Conference 2016 13, Cancun, Mexico, July 04, 2016 (Cambridge, MA: MIT Press), 626–633.
Izumi, A., Sanada, M., Furuichi, K., Teraki, K., Matsuda, T., Hiramatsu, K., et al. (2014). Rapid Charge and Discharge Property of High Capacity Lithium Ion Battery Applying Three-Dimensionally Patterned Electrode. J. Power Sourc. 256, 244–249. doi:10.1016/j.jpowsour.2014.01.067
Jafary, T., Al-Mamun, A., Alhimali, H., Baawain, M. S., Rahman, M. S., Rahman, S., et al. (2020). Enhanced Power Generation and Desalination Rate in a Novel Quadruple Microbial Desalination Cell with a Single Desalination Chamber. Renew. Sust. Energ. Rev. 127, 109855. doi:10.1016/j.rser.2020.109855
Jannelli, E., Di Trolio, P., Flagiello, F., and Minutillo, M. (2018). Development and Performance Analysis of Biowaste Based Microbial Fuel Cells Fabricated Employing Additive Manufacturing Technologies. Energ. Proced. 148, 1135–1142. doi:10.1016/j.egypro.2018.08.029
Jiang, Y., Liang, P., Zhang, C., Bian, Y., Yang, X., Huang, X., et al. (2015). Enhancing the Response of Microbial Fuel Cell Based Toxicity Sensors to Cu(II) with the Applying of Flow-Through Electrodes and Controlled Anode Potentials. Bioresour. Tech. 190, 367–372. doi:10.1016/j.biortech.2015.04.127
Kim, J., Kim, H., Kim, B., and Yu, J. (2014). Computational Fluid Dynamics Analysis in Microbial Fuel Cells with Different Anode Configurations. Water Sci. Technol. 69 (7), 1447–1452. doi:10.2166/wst.2014.041
Koch, C., and Harnisch, F. (2016). Is There a Specific Ecological Niche for Electroactive Microorganisms? ChemElectroChem. 3 (9), 1282–1295. doi:10.1002/celc.201600079
Lee, J.-Y., Tan, W. S., An, J., Chua, C. K., Tang, C. Y., Fane, A. G., et al. (2016). The Potential to Enhance Membrane Module Design with 3D Printing Technology. J. Membr. Sci. 499, 480–490. doi:10.1016/j.memsci.2015.11.008
Lehner, B. A. E., Schmieden, D. T., and Meyer, A. S. (2017). A Straightforward Approach for 3D Bacterial Printing. ACS Synth. Biol. 6 (7), 1124–1130. doi:10.1021/acssynbio.6b00395
Leong, J. X., Daud, W. R. W., Ghasemi, M., Liew, K. B., and Ismail, M. (2013). Ion Exchange Membranes as Separators in Microbial Fuel Cells for Bioenergy Conversion: a Comprehensive Review. Renew. Sust. Energ. Rev. 28, 575–587. doi:10.1016/j.rser.2013.08.052
Logan, B. E., Wallack, M. J., Kim, K.-Y., He, W., Feng, Y., and Saikaly, P. E. (2015). Assessment of Microbial Fuel Cell Configurations and Power Densities. Environ. Sci. Technol. Lett. 2 (8), 206–214. doi:10.1021/acs.estlett.5b00180
López-Hincapié, J. D., Picos-Benítez, A. R., Cercado, B., Rodríguez, F., and Rodríguez-García, A. (2020). Improving the Configuration and Architecture of a Small-Scale Air-Cathode Single Chamber Microbial Fuel Cell (MFC) for Biosensing Organic Matter in Wastewater Samples. J. Water Process Eng. 38, 101671. doi:10.1016/j.jwpe.2020.101671
Lv, J., Gong, Z., He, Z., Yang, J., Chen, Y., Tang, C., et al. (2017). 3D Printing of a Mechanically Durable Superhydrophobic Porous Membrane for Oil-Water Separation. J. Mater. Chem. A. 5 (24), 12435–12444. doi:10.1039/c7ta02202f
Mashkour, M., Rahimnejad, M., Mashkour, M., and Soavi, F. (2021). Increasing Bioelectricity Generation in Microbial Fuel Cells by a High-Performance Cellulose-Based Membrane Electrode Assembly. Appl. Energ. 282, 116150. doi:10.1016/j.apenergy.2020.116150
Massaglia, G., Gerosa, M., Agostino, V., Cingolani, A., Sacco, A., Saracco, G., et al. (2017). Fluid Dynamic Modeling for Microbial Fuel Cell Based Biosensor Optimization. Fuel Cells 17 (5), 627–634. doi:10.1002/fuce.201700026
Moon, J. M., Kondaveeti, S., Lee, T. H., Song, Y. C., and Min, B. (2015a). Minimum Interspatial Electrode Spacing to Optimize Air-Cathode Microbial Fuel Cell Operation with a Membrane Electrode Assembly. Bioelectrochemistry 106, 263–267. doi:10.1016/j.bioelechem.2015.07.011
Moon, J. M., Kondaveeti, S., and Min, B. (2015b). Evaluation of Low-Cost Separators for Increased Power Generation in Single Chamber Microbial Fuel Cells with Membrane Electrode Assembly. Fuel Cells 15 (1), 230–238. doi:10.1002/fuce.201400036
Munoz-Cupa, C., Hu, Y., Xu, C. C., and Bassi, A. (2020). An Overview of Microbial Fuel Cell Usage in Wastewater Treatment, Resource Recovery and Energy Production. Sci. Total Environ. 754, 142429. doi:10.1016/j.scitotenv.2020.142429
Murphy, S. V., and Atala, A. (2014). 3D Bioprinting of Tissues and Organs. Nat. Biotechnol. 32 (8), 773–785. doi:10.1038/nbt.2958
Parameswaran, P., Torres, C. I., Lee, H.-S., Krajmalnik-Brown, R., and Rittmann, B. E. (2009). Syntrophic Interactions Among Anode Respiring Bacteria (ARB) and Non-ARB in a Biofilm Anode: Electron Balances. Biotechnol. Bioeng. 103 (3), 513–523. doi:10.1002/bit.22267
Parra-Cabrera, C., Achille, C., Kuhn, S., and Ameloot, R. (2018). 3D Printing in Chemical Engineering and Catalytic Technology: Structured Catalysts, Mixers and Reactors. Chem. Soc. Rev. 47 (1), 209–230. doi:10.1039/c7cs00631d
Philamore, H., Rossiter, J., Walters, P., Winfield, J., and Ieropoulos, I. (2015). Cast and 3D Printed Ion Exchange Membranes for Monolithic Microbial Fuel Cell Fabrication. J. Power Sourc. 289, 91–99. doi:10.1016/j.jpowsour.2015.04.113
Pumera, M. (2019). Three-dimensionally Printed Electrochemical Systems for Biomedical Analytical Applications. Curr. Opin. Electrochemistry 14, 133–137. doi:10.1016/j.coelec.2019.02.001
Qian, F., Zhu, C., Knipe, J. M., Ruelas, S., Stolaroff, J. K., DeOtte, J. R., et al. (2019). Direct Writing of Tunable Living Inks for Bioprocess Intensification. Nano Lett. 19 (9), 5829–5835. doi:10.1021/acs.nanolett.9b00066
Quaglio, M., Massaglia, G., Vasile, N., Margaria, V., Chiodoni, A., Salvador, G. P., et al. (2019). A Fluid Dynamics Perspective on Material Selection in Microbial Fuel Cell-Based Biosensors. Int. J. Hydrogen Energ. 44 (9), 4533–4542. doi:10.1016/j.ijhydene.2018.11.087
Rahimnejad, M., Bakeri, G., Najafpour, G., Ghasemi, M., and Oh, S.-E. (2014). A Review on the Effect of Proton Exchange Membranes in Microbial Fuel Cells. Biofuel Res. J. 01 (1), 7–15. doi:10.18331/brj2015.1.1.4
Rasperini, G., Pilipchuk, S., Flanagan, C., Park, C., Pagni, G., Hollister, S., et al. (2015). 3D-printed Bioresorbable Scaffold for Periodontal Repair. J. dental Res. 94 (9_Suppl. l), 153S–157S. doi:10.1177/0022034515588303
Revilla, R., Verkens, D., Rubben, T., and De Graeve, I. (2020). Corrosion and Corrosion Protection of Additively Manufactured Aluminium Alloys-A Critical Review. Materials 13 (21), 4804. doi:10.3390/ma13214804
Rousseau, R., Etcheverry, L., Roubaud, E., Basséguy, R., Délia, M.-L., and Bergel, A. (2020). Microbial Electrolysis Cell (MEC): Strengths, Weaknesses and Research Needs from Electrochemical Engineering Standpoint. Appl. Energ. 257, 113938. doi:10.1016/j.apenergy.2019.113938
Ruiz, Y., Ribot-Llobet, E., Baeza, J. A., and Guisasola, A. (2015). Conditions for High Resistance to Starvation Periods in Bioelectrochemical Systems. Bioelectrochemistry 106, 328–334. doi:10.1016/j.bioelechem.2015.06.010
Sawa, M., Fantuzzi, A., Bombelli, P., Howe, C. J., Hellgardt, K., and Nixon, P. J. (2017). Electricity Generation from Digitally Printed Cyanobacteria. Nat. Commun. 8 (1), 1–10. doi:10.1038/s41467-017-01084-4
Schaffner, M., Rühs, P. A., Coulter, F., Kilcher, S., and Studart, A. R. (2017). 3D Printing of Bacteria into Functional Complex Materials. Sci. Adv. 3 (12), eaao6804. doi:10.1126/sciadv.aao6804
Sim, J., Reid, R., Hussain, A., An, J., and Lee, H.-S. (2018). Hydrogen Peroxide Production in a Pilot-Scale Microbial Electrolysis Cell. Biotechnol. Rep. 19, e00276. doi:10.1016/j.btre.2018.e00276
Sravan, J. S., Tharak, A., Modestra, J. A., Chang, I. S., and Mohan, S. V. (2021). Emerging Trends in Microbial Fuel Cell Diversification-Critical Analysis. Bioresour. Tech. 326, 124676. doi:10.1016/j.biortech.2021.124676
Sun, K., Wei, T.-S., Ahn, B. Y., Seo, J. Y., Dillon, S. J., and Lewis, J. A. (2013). 3D Printing of Interdigitated Li-Ion Microbattery Architectures. Adv. Mater. 25 (33), 4539–4543. doi:10.1002/adma.201301036
Theodosiou, P., Greenman, J., and Ieropoulos, I. A. (2020). Developing 3D-Printable Cathode Electrode for Monolithically Printed Microbial Fuel Cells (MFCs). Molecules 25 (16), 3635. doi:10.3390/molecules25163635
Theodosiou, P., Greenman, J., and Ieropoulos, I. (2019). Towards Monolithically Printed Mfcs: Development of a 3d-Printable Membrane Electrode Assembly (Mea). Int. J. Hydrogen Energ. 44 (9), 4450–4462. doi:10.1016/j.ijhydene.2018.12.163
Torres, C. I., Krajmalnik-Brown, R., Parameswaran, P., Marcus, A. K., Wanger, G., Gorby, Y. A., et al. (2009). Selecting Anode-Respiring Bacteria Based on Anode Potential: Phylogenetic, Electrochemical, and Microscopic Characterization. Environ. Sci. Technol. 43 (24), 9519–9524. doi:10.1021/es902165y
Vabalas, A., Gowen, E., Poliakoff, E., and Casson, A. J. (2019). Machine Learning Algorithm Validation with a Limited Sample Size. PloS one 14 (11), e0224365. doi:10.1109/embc.2019.8857307
Vak, D., Hwang, K., Faulks, A., Jung, Y.-S., Clark, N., Kim, D.-Y., et al. (2015). 3D Printer Based Slot-Die Coater as a Lab-To-Fab Translation Tool for Solution-Processed Solar Cells. Adv. Energ. Mater. 5 (4), 1401539. doi:10.1002/aenm.201401539
Vilela, C., Cordeiro, D. M., Boas, J. V., Barbosa, P., Nolasco, M., Vaz, P. D., et al. (2020). Poly(4-styrene Sulfonic Acid)/bacterial Cellulose Membranes: Electrochemical Performance in a Single-Chamber Microbial Fuel Cell. Bioresour. Tech. Rep. 9, 100376. doi:10.1016/j.biteb.2019.100376
Walters, P., and Davies, K. (2010). 3D Printing for Artists: Research and Creative Practice. Rapport: J. Norwegian Print Assoc. 1, 12–15.
Wei, X., Li, D., Jiang, W., Gu, Z., Wang, X., Zhang, Z., et al. (2015). 3D Printable Graphene Composite. Scientific Rep. 5, 11181. doi:10.1038/srep11181
Winfield, J., Chambers, L. D., Rossiter, J., Greenman, J., and Ieropoulos, I. (2015). Urine-activated Origami Microbial Fuel Cells to Signal Proof of Life. J. Mater. Chem. A. 3 (13), 7058–7065. doi:10.1039/c5ta00687b
Yee, R. S. L., Rozendal, R. A., Zhang, K., and Ladewig, B. P. (2012). Cost Effective Cation Exchange Membranes: A Review. Chem. Eng. Res. Des. 90 (7), 950–959. doi:10.1016/j.cherd.2011.10.015
Yi, Y., Xie, B., Zhao, T., Qian, Z., and Liu, H. (2020). The Effect of Anode Hydrodynamics on the Sensitivity of Microbial Fuel Cell Based Biosensors and the Biological Mechanism. Bioelectrochemistry 132, 107351. doi:10.1016/j.bioelechem.2019.107351
You, J., Fan, H., Winfield, J., and Ieropoulos, I. A. (2020). Complete Microbial Fuel Cell Fabrication Using Additive Layer Manufacturing. Molecules 25 (13), 3051. doi:10.3390/molecules25133051
You, J., Preen, R. J., Bull, L., Greenman, J., and Ieropoulos, I. (2017). 3D Printed Components of Microbial Fuel Cells: Towards Monolithic Microbial Fuel Cell Fabrication Using Additive Layer Manufacturing. Sustain. Energ. Tech. Assessments 19, 94–101. doi:10.1016/j.seta.2016.11.006
Zakaria, B. S., and Dhar, B. R. (2020). Changes in Syntrophic Microbial Communities, EPS Matrix, and Gene-Expression Patterns in Biofilm Anode in Response to Silver Nanoparticles Exposure. Sci. Total Environ. 734, 139395. doi:10.1016/j.scitotenv.2020.139395
Zakaria, B. S., Barua, S., Sharaf, A., Liu, Y., and Dhar, B. R. (2018). Impact of Antimicrobial Silver Nanoparticles on Anode Respiring Bacteria in a Microbial Electrolysis Cell. Chemosphere 213, 259–267. doi:10.1016/j.chemosphere.2018.09.060
Zakaria, B. S., and Dhar, B. R. (2019). Progress towards Catalyzing Electro-Methanogenesis in Anaerobic Digestion Process: Fundamentals, Process Optimization, Design and Scale-Up Considerations. Bioresour. Technol. 289, 121738. doi:10.1016/j.biortech.2019.121738
Zhao, Q., An, J., Wang, X., and Li, N. (2021). In-situ Hydrogen Peroxide Synthesis with Environmental Applications in Bioelectrochemical Systems: a State-Of-The-Art Review. Int. J. Hydrogen Energ. 46 (4), 3204–3219. doi:10.1016/j.ijhydene.2020.05.227
Zhou, Y., Tang, L., Liu, Z., Hou, J., Chen, W., Li, Y., et al. (2017). A Novel Anode Fabricated by Three-Dimensional Printing for Use in Urine-Powered Microbial Fuel Cell. Biochem. Eng. J. 124, 36–43. doi:10.1016/j.bej.2017.04.012
Zou, S., Qin, M., Moreau, Y., and He, Z. (2017). Nutrient-energy-water Recovery from Synthetic Sidestream Centrate Using a Microbial Electrolysis Cell - Forward Osmosis Hybrid System. J. Clean. Prod. 154, 16–25. doi:10.1016/j.jclepro.2017.03.199
Keywords: 3D printing, additive manufacturing, microbial electrochemical technologies (MET), microbial electrochemical cells (MXCs), microbial fuel cells (MFCs)
Citation: Chung TH and Dhar BR (2021) A Mini-Review on Applications of 3D Printing for Microbial Electrochemical Technologies. Front. Energy Res. 9:679061. doi: 10.3389/fenrg.2021.679061
Received: 10 March 2021; Accepted: 29 April 2021;
Published: 21 May 2021.
Edited by:
Pierangela Cristiani, Ricerca Sul Sistema Energetico, ItalyReviewed by:
Mirella Di Lorenzo, University of Bath, United KingdomMatteo Grattieri, University of Bari Aldo Moro, Italy
Copyright © 2021 Chung and Dhar. This is an open-access article distributed under the terms of the Creative Commons Attribution License (CC BY). The use, distribution or reproduction in other forums is permitted, provided the original author(s) and the copyright owner(s) are credited and that the original publication in this journal is cited, in accordance with accepted academic practice. No use, distribution or reproduction is permitted which does not comply with these terms.
*Correspondence: Bipro Ranjan Dhar, Ymlwcm9AdWFsYmVydGEuY2E=