- 1Sino-French Institute of Nuclear Engineering and Technology Sun Yat-Sen University, Zhuhai, China
- 2Nuclear Power Institute of China, Chengdu, China
Ceramic material is one of the essential materials used in reactors. Beryllium oxide ceramics have good high-temperature radiation stability, high density, high strength, and thermal conductivity at high temperatures, and the price of beryllium oxide is relatively moderate. This makes it more suitable for use as a reflector, moderator, and dispersion phase fuel matrix in a reactor. In recent years, beryllium oxide has attracted widespread attention due to its high hardness, high resistivity, high thermal conductivity, high melting point, and high radiation resistance. Because of its excellent mechanical properties, beryllium oxide materials also have a long history in the field of nuclear energy. Reactor extreme environments have become a significant challenge for optimizing reactor operation and safety performance. The utilization of beryllium oxide can significantly alleviate extreme reactor environments. According to research, the coupling of beryllium oxide material can effectively improve nuclear fuels' thermal conductivity, such as uranium dioxide. Beryllium oxide also has good radiation resistance and neutron scattering properties, which increases its applications in nuclear energy. The article comprehensively reviews the BeO utilization approaches in reactors to improve extreme reactor environments for current reactor operation and future reactor design optimization.
Introduction
Since the beginning, the beryllium oxide (BeO) material has attracted attention because of its excellent performance, such as high thermal conductivity, high neutron reflection cross-section, low neutron capture cross-section (Manly, 1964). BeO can meet the required strength as a reactor material. It can also maintain properties' stability under the high-temperature environment and improve the nuclear system's neutron economy under the (n, 2n) reaction. These are all critical indexes to determine whether nuclear materials are excellent. BeO is extracted from beryllium minerals, and the first BeO ceramic product was made in 1939 (Hey and Livey, 1966). Much research has been performed on the performance of BeO in the extreme environment. Rothman (1962) discussed the application of BeO ceramics in space reactor (the Pluto Project). Smith et al. (1962) investigated changes in the crystal structure of BeO at high temperatures. Then Snead (2005) reviewed the utilization of BeO in space reactors. Chen and Yuan (2020) studied the neutronics of the UO2-BeO fuel with various claddings. It can be seen that the research on the BeO material has always been ongoing for its applications in the nuclear industry. However, BeO is a toxic material, and the small particles of BeO have a profound influence on the human body and the environment. The researchers are interested in finding a new material that can replace BeO ceramics entirely. For instance, Aluminum nitride (AlN) has high thermal conductivity and moderate dielectric constant, the same as BeO material. It can replace BeO sometimes in cooling parts of integrated circuits (Koba et al., 1997; Kettner et al., 2001). However, it is still challenging for other fields, such as nuclear systems. The BeO ceramics remains to play an essential role in the nuclear industry.
In 1945, the Daniels reactor's design was proposed (Manly, 1964) to use the BeO material as moderator and fuel matrix material. This was the first time in history the BeO material was proposed for reactor systems. It opened a new chapter for BeO utilization in reactor systems. Although BeO has excellent potential in terms of performance, many challenges always exist about its application in nuclear power plants, such as the BeO ceramics' cost and the technical concern of water vapor reaction (Aitken, 1960), chemical retreatment, and radiation damage.
The choice of materials for a nuclear reactor is very demanding because of the extreme nuclear reactor environments. During the reactor operation, the chain fission releases a large amount of energy continuously, resulting in a high-temperature environment, which the selected structural materials need to endure. Not only that, suitable material should not affect the process of the fission reaction. This will eliminate many alternative materials. Another aspect of selecting a moderator is that the macroscopic absorption cross-section of neutrons should be small, the macroscopic scattering cross-section should be large, and there are also high standards for thermal conductivity, density, and irradiation stability (Gao, 2006). These conditions also apply to the reflector and coolant. BeO has the potential to be an excellent material for nuclear systems. In terms of performance, it has good properties under neutron moderation. So now, it has played a significant role in many structures of the nuclear reactor system. However, there are also technical challenges to be solved for the specific applications. For example, the BeO ceramics may expand or crack due to neutron radiation, which will affect the normal operation of the reactor system. Due to its more complex fabrication process, BeO has a higher cost compared with graphite. These all need to be considered in the reactor design.
This paper summarizes the BeO ceramics' applications in nuclear reactors to improve extreme reactor environments in recent years. It gives some concrete examples for their reactor applications, and the advantages and existing problems are also discussed. The BeO material will first be introduced being moderator/reflector materials in different reactor projects, and then the BeO material’s application will be discussed as dispersion phase fuel matrix together with UO2 to promote accident-tolerant fuels (ATFs)’ development. The fabrication of BeO material and the latest application progress will also be reviewed. As moderator material competitors, the BeO material will also be compared with the graphite material regarding their benefits and drawbacks. Finally, there will be some conclusions, suggestions, and discussions on the BeO material's utilization in reactor systems to improve the extreme reactor environments.
BeO as Moderator/Reflector Materials
The moderator and reflector are essential components of a nuclear reactor system. In order to maintain the chain fission reaction in the reactor, a constant source of thermal neutrons is required, and the neutrons released by fission are fast neutrons, which cannot facilitate the fission reaction and need to be rapidly moderated to thermal neutrons by the moderator. The role of the reflector is, as the name implies, to reflect neutrons to reduce neutron leakage from the reactor. It is like an extension of the moderator to slow down and/or to retain the neutrons. The moderator and reflector should meet the requirements of a small neutron absorption cross-section and a large neutron scattering cross-section and also attain good thermal conductivity, high stability, and slight corrosion to the core structures.
Compared with other moderated materials, beryllium and beryllium oxide have excellent performance in nuclear properties, especially in the moderation capacity, as shown in Table 1. There is no doubt that BeO is an excellent refractory material too. The heavy-water properties are excellent as a neutron moderator, but it is too expensive to afford sometimes. Moreover, BeO has an excellent thermal conductivity in an environment above 1,000°C, which is more than twice that of magnesium and aluminum metal oxides. In Figure 1 [interpolated by Zhou and Zhou (2018)], the thermal conductivity of material decreases with increasing temperature and is much higher than the traditional nuclear fuel UO2.
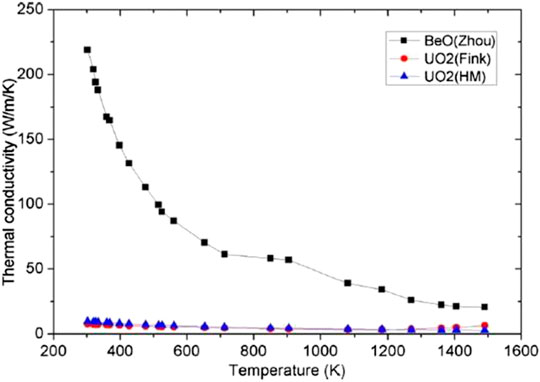
FIGURE 1. The thermal conductivity of BeO and UO2 (Zhou and Zhou, 2018).
Nevertheless, the BeO material can maintain enjoyable thermal conductivity at high temperatures. With a melting point of 2570°C (Rothman, 1962), BeO can withstand the reactor's high operational temperature and even extreme accident scenarios. The stability of physical and chemical properties is also crucial for BeO to serve as structural materials. BeO has a very stable performance with O2 and H2 even at a temperature of 2000°C.
The excellent material properties from these aspects have made BeO a top candidate for reactor moderator/reflector material. Besides, it has a high hardness as a reflector, which ensures the stability of the reactor. Excellent moderator and reflector materials can significantly improve the efficiency of the reactor. Nowadays, BeO has been chosen as moderator and/or reflector material in many reactor systems, and more details are described as follows.
Daniels Reactor Project
The history of the application of BeO to nuclear reactors can be dated back to 1945 when Farrington Daniels conceptualized and led the pioneering studies on a high-temperature pebble-bed reactor, which was envisioned to have a BeO moderator/reflector, a helium coolant, and BeO-filled graphite spherical fuel elements (Manly, 1964). This was a novel idea, the first time that BeO was proposed to combine with a nuclear reactor. Researchers were then beginning to investigate the BeO material in nuclear reactors. These efforts included the Clinton Laboratory in Oak Ridge, Tennessee, to study and push high-temperature ceramic reactors' feasibility. This project planned to build a 12 MW power plant, but eventually, it supplied only one-fifth of the planned power, i.e., 2.4 MW. The original idea was to successfully build a small power reactor at first. After demonstrating the reactor materials' performance, it would operate at a higher level of power output. The Daniels reactor had a modern appearance, as shown in Figure 2. This project planned to use a lot of hexagonal blocks to build the main body. The BeO piece's size was required to reach the maximum size producible at that time.
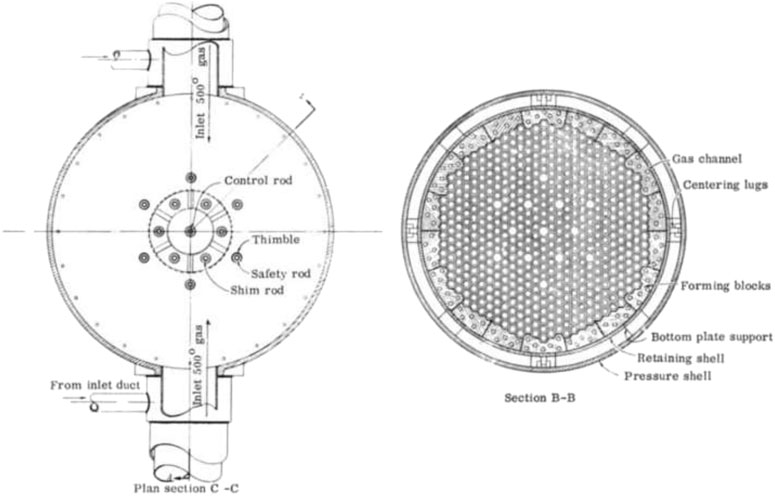
FIGURE 2. The view of the Daniels reactor and its core layout (Manly, 1964).
Meanwhile, the central core program consisted of 228 fuel lines and 12 control rods, and the BeO piece should be fabricated in a unique shape to use. However, it was too expensive to execute at that time. Besides, not much information is available on BeO and the behavior of BeO in a reactor at that time. The high reactor operating temperature, as well as the temperature span of the helium coolant, made core material selection more difficult. So, there was much uncertainty in practice.
Additionally, considering the irradiation environments in reactors, people cannot solve the problems and design the core structure correctly without sufficient experimental validations. There is no doubt that the project's idea was advanced, which confirmed the BeO material's excellent properties as a moderator. However, as mentioned above, people only knew that BeO has an excellent ability to moderate neutron but did not have enough experience solving possible problems under extreme reactor environments. The complex structure of nuclear reactors also made the design more complicated. The lack of sufficient experience in reactor design, the uncertainty of helium coolant properties, and more attention to the other projects led to this project's termination. Until 1950, a new project about the use of BeO in reactors continued (McCullough, 1947).
Aircraft Reactor Experiment/Test (ARE/ART) Projects
In 1954, a new project was operated by Oak Ridge National Laboratory (ORNL). The Aircraft Reactor Experiment (ARE) used molten salt as fuel, BeO as moderator, liquid sodium and liquid fuel as a coolant at the same time (Bettis et al., 1957). Several BeO blocks procured for the Daniels Reactor were used in the materials investigations supporting the ARE (Slaughter et al., 1957). This was the world's first experimental prototype of a molten salt reactor, as shown in Figure 3 (Robertson, 1965). The core's height is 90.93 cm (cm), the diameter around 84.60 cm, and the thermal power is 2.5 MWt. The ARE reached its critical mass on November 3, 1954. It operated for ten days. During the ARE experimental reactor operation, a series of experiments, such as critical experiment, high power experiment, and low power experiment, were carried out. Based on the ARE's design and operational experience, ORNL also designed and built spherical space reactors - Aircraft Reactor Test (ART). The ART is a 60-MW reflector-moderated circulating-fuel type whose basic design is suitable for aircraft use. Its thermal power is higher than ARE (Cottrell et al., 1955). It also had a more sophisticated and more stable system. However, the military ended their cooperation because of the concession of Aircraft Nuclear Propulsion (ANP) (James, 2000). Of course, the project of ART also expired. Although the ART and ARE projects did not finish successfully, these projects' experimental results have significantly contributed to nuclear power development. The ARE project's research had given a boost to the development of molten salt reactors. This established the applicability of the BeO material to molten salt reactors and promoted molten salt reactor research. Until now, the molten salt reactor has not only been selected as one of the six candidates for the fourth generation reactor but has also developed several different designs based on the traditional molten salt reactor for different purposes. Besides, the ART project demonstrated the potential of BeO for nuclear propulsion in space.
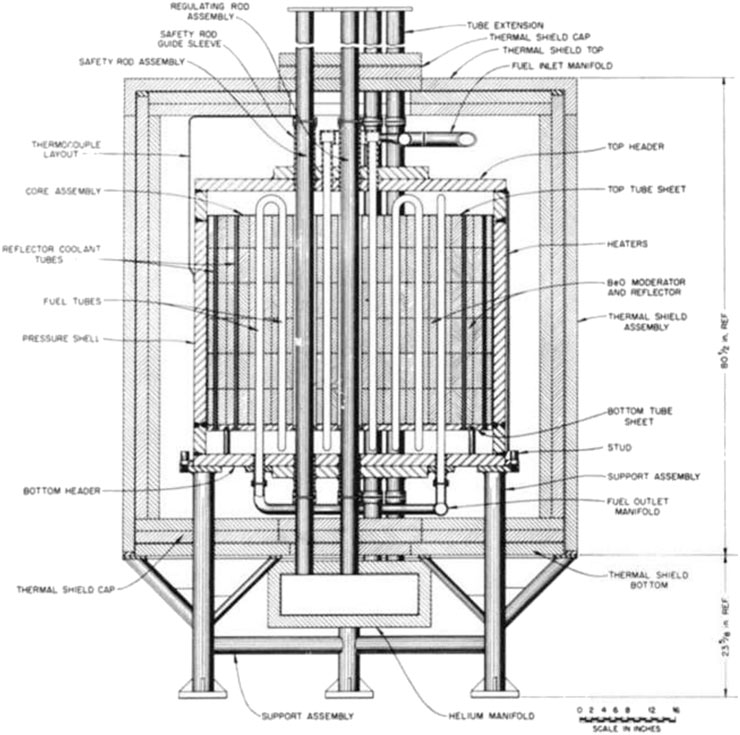
FIGURE 3. The elevation section of the Aircraft Reactor Experiment (Slaughter et al., 1957).
Meanwhile, space reactors are operated under more complex and extreme environments. So, the selection of materials is more stringent than other reactors. In these extreme environments, the BeO material, as a solid, is easier to be carried into space than heavy water; and it is more reliable than graphite, which may catch fire in accident scenarios. So, the BeO material is still employable because of its excellent performance. From the ARE operation experience, the material properties of coolant and moderator were stable, and no compatibility problems existed. However, some erosion occurred in the dynamic tests. Interestingly, the structure of BeO was not appreciably changed and was intact (Slaughter et al., 1957). However, more research is needed for the BeO material to be applied in these reactors.
Pluto Project
On January 1, 1957, the U.S. Air Force and the U.S. Atomic Energy Commission (AEC) selected the Lawrence Radiation Laboratory to study the feasibility of applying heat from nuclear reactors to ramjet engines, which was called the Pluto Project. The designers came up with a ramjet engine concept (Merkle, 1961), intending to develop nuclear-powered missiles. They planned to build a 513 MW unshielded nuclear reactor and to fully utilize the combination of the ramjet engine and air heating to provide the missile's power. Considerably, the maximum temperature of this project operating environment reached a temperature of 1,600°C. The heavy-water properties are excellent as a neutron moderator, but it is too expensive for this project. The designers should find a unique ceramic for the reactor's structural components to ensure normal operation at high temperatures. Likewise, in the selection of moderators, the materials have also to be resistant to high temperature. The BeO was an outstanding choice due to its excellent high-temperature resistance, extraordinary performance in thermal conductivity, large neutron macroscopic scattering cross-section, and small macroscopic absorption cross-section.
However, the utilization of BeO was not as successful as expected in this project. Firstly, the material's thermal stress was too considerable with the temperature increase, easily causing damage to the material (Lillie, 1961). So, it is necessary to maximize the strength or creep as much as possible at high temperatures. Moreover, BeO reacts with water vapor at high temperatures (Van Houten et al., 1961). These problems can affect reactor efficiency. Another limitation is a disruptive transformation at a temperature above 2050°C. In the single crystal of BeO above 2050°C, several domains have formed within the crystal, with some fracturing at domain boundaries (Smith et al., 1962). The researchers tried to develop coating materials to solve the problems of the BeO reacting with water vapor. However, some technical difficulties arose when using UO2 as fuel. Besides, improvements in radar technology led to the termination of the project.
Experimental Beryllium Oxide Reactor (EBOR) Project
The Experimental Beryllium Oxide Reactor (EBOR) (Moore, 1961) was a 10 MWt helium-cooled beryllium moderated nuclear reactor at Idaho National Laboratory. The project started on February 17, 1958, as the United States Atomic Energy Commission portion of the Joint Maritime Administration - AEC Maritime Gas-Cooled Reactor Program. The project started with a contract between the U.S. Atomic Energy Commission and General Dynamics. The project's goal was to create a small nuclear reactor for merchant shipping or a medium-sized power plant. The reactor's main goals were a simple design, low maintenance costs, and maximum efficiency over a wide range of power settings. In December 1960, the project was authorized to construct a 10-MWt test reactor to determine the Beryllium Oxide gas-cooled system's characteristics. The EBOR was designed to test the fundamental fuel element and moderator designs for the final reactor. The EBOR used a Helium cooling system and was an intermediate step toward a prototype power plant. The plan was to use a closed-cycle turbine or a steam cycle with the reactor to make a small land-based or maritime power plant. This plan was abandoned as the reactor never achieved criticality.
Kilopower Space Reactor Project
Along with the aerospace development, there are also some BeO utilization examples in space reactors, such as Kilopower space reactor, in recent years. On May 2, 2018, the National Aeronautics and Space Administration (NASA) announced the completion of the Kilopower space reactor test at the Nevada National Safety Test Site. The Kilopower is a kilowatt reactor (Poston et al., 2019). The space reactor is much smaller and produces much less power than the traditional one due to the need to fit it with the spacecraft and space travel. The prototypic nuclear power of Kilopower was a 5-KWt space reactor (Gibson et al., 2017). The conception of the space reactor is shown in Figure 4. It used the BeO material as a reflector. At present, the reactor has completed its first step of testing. It included simulating unexpected conditions, such as power reduction, generator failure, and heat pipe failure, to test the reactor system's practicality. The test results showed that the prototype reactor could run continuously and cope with various fault conditions successfully, proving the BeO system's stability.
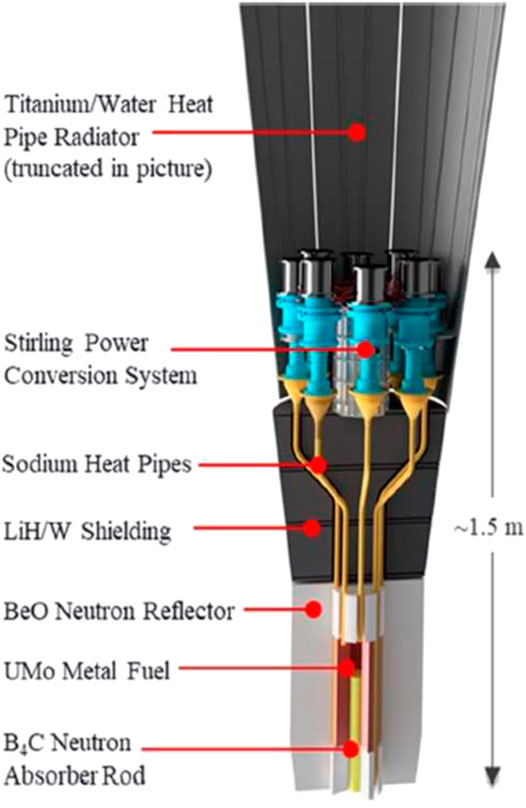
FIGURE 4. The conception of Kilopower space reactor (Gibson et al., 2017).
Interestingly, the Kilopower reactor uses lots of heat pipes rather than conventional water coolant to transfer heat, considering the high heat transfer efficiency and inherent safety of heat pipes. The successful test of Kilopower is only a first step toward harnessing fission power in space. The technology is still conceptual and has a long way to go before being applied to space systems.
UO2-BeO as Reactor Fuel Candidates
The BeO material has attracted significant attention as dispersion phase fuel matrix together with UO2 to promote Accident-Tolerant Fuels (ATFs)’ development. There are three points in how to optimize the ATF: 1) Replacement or improvement of the current UO2 ceramic fuel; 2) Improvement of the oxidation resistance for the cladding by modifying the current zircaloy alloy; 3) Utilization of new high oxidation resistance cladding materials (Ott et al., 2014). Since Fukushima Daiichi nuclear accident in 2011, many potential ATFs and claddings have been proposed and investigated by the U.S. Department of Energy (DOE) Office of Nuclear Energy Advanced Fuels Campaign and governmental agencies of other countries, such as France, Japan, Korea, and China. Of course, replacement or optimization of the current UO2 ceramic fuel appeared in early projects due to its promising feasibility in the near future.
Aerojet-General Nucleonics Army Gas-Cooled Reactor
In the Aerojet-General Nucleonics Army Gas-Cooled Reactor, the BeO has been selected as a diluent for the UO2 fuel (Aerojet-General Corporation, 1962). Besides, it used pure BeO insulators to disperse the heat from the top pellets to reduce the peak temperature gradient. This time researchers made a difference in the utilization of BeO from the previous projects to establish a mobile, low-powered nuclear power plant to furnish electrical power in remote locations (Manly, 1964). The reactor that used BeO as diluent had great benefits. There is no doubt that the fuel inventory is low, and also, because of its outstanding thermal conductivity, BeO can provide a better environment for the core. In terms of fission-gas retention, the composite fuel may have better performance than UO2. However, the cost of BeO should not be neglected, and thus it failed to spread to other projects. In this era, there are several other nuclear programs involve the use of BeO. However, many projects belong to the military. So, very little detailed information is available. We hope more advantages of the BeO material can become accessible in the future.
Annular Core Research Reactor (ACRR)
The Annular Core Research Reactor (ACRR) (Pelfrey, 2019) was developed in the 1970s and became operational in 1978. The ACRR is a TRIGA-type reactor that consists of 236 fuel elements with UO2-BeO fuel pellets. The fuel elements are arranged in an annulus around a 9″ dry central cavity. The ACRR is operated by adjusting its 11 moveable elements to control the reactivity of the reactor. The 11 moveable rods consist of six control rods, three transient rods, and two safety rods. The moveable rods all contain a boron carbide upper portion that absorbs neutrons, and both the safety and control rods have fuel in the lower half. The safety rods are moved to the up position to operate the reactor, and the control rods are adjusted depending on the desired steady-state power or pulse size. In pulse operations, the transient rods are ejected using pressurized nitrogen, causing the ACRR to prompt supercritical. During pulses, the ACRR shuts itself down due to Doppler broadening effects in the fuel. The ACRR can operate at a 4 MW steady-state and reach pulse powers up to 50,000 MWth with total energy yields over 300 MJ. The schematic of an ACRR fuel element and the cross-sectional view of the ACRR's fuel element are shown in Figures 5A,B.
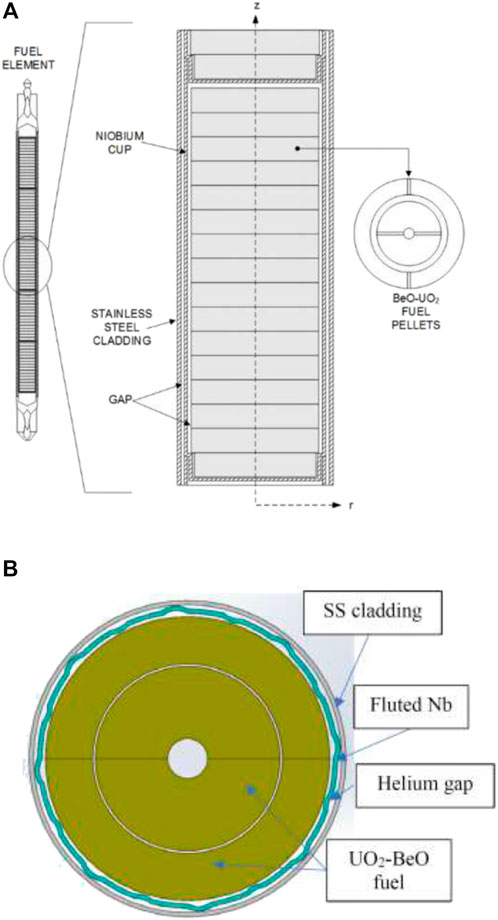
FIGURE 5. (A) Schematic of an ACRR fuel element; (B) Cross-sectional view of the ACRR’s fuel element (Pelfrey, 2019).
A Brief Overview on UO2-BeO Fuel Development
In the 1960s, Nishigaki and Maekawa evaluated beryllium's additions in UO2-BeO fuel and obtained the results to compare with pure UO2. It is found that thermal conductivity could be enhanced by 10–20 times after adding 20 wt% BeO (Nishigaki and Maekawa, 1964). At almost the same time, the United States Atomic Energy Commission (Mills et al., 1964) studied 70%BeO-30%UO2 fuel used in Experiment Beryllium Oxide Reactor (EBOR). A coarse dispersion (100–200 micron fuel particles) and a fine dispersion (50-micron fuel particles) were used in this program. The results showed that swelling in most of these tests was very small, and there was little change in the microstructure. Wells and Cline (1963) had researched the resistance of thermal stress of BeO and BeO-UO2 in early time. They put the experimental apparatus in one water-cooled cylinder, which maintained an inert gas atmosphere to prevent graphite oxidation. The thermal stress test was performed by controlling the power within a specified time to reach a specified temperature. Under these experimental conditions, they obtained the relationship of these factors. Ishimoto et al. (Ishimoto et al., 1996) evaluated the effects of BeO precipitate shape and content (0.3, 0.6, 0.9, 1.2, and 13.6 wt%) on thermal conductivity.
In recent years, more researchers devote themselves to better utilizing BeO to improve the performance of the UO2 fuel. In pursuing the nuclear fuel initiative to improve efficiency and safety, IBC Advanced Alloys (IBC) has been dedicated to research and sponsored the projects conducted at Purdue University and Texas A&M University. The high temperature can also increase the cladding pressure due to fission gas build-up, even breaking the claddings (Jernkvist et al., 2002). So, the addition of another element together with UO2 is used to enhance nuclear fuel's thermal conductivity. There is no doubt that BeO is an ideal material for this purpose. The good news was that this research proved the fuel thermal conductivity could be improved and put forward a viable solution for the industry. The improvement of thermal conductivity does lead to improved reactor safety performance. Sarma et al. (2006) developed unique granulation and mixing techniques to obtain UO2-BeO fuel. Latta et al. (2008) carried out green granule and slug-bisque processes to produce UO2-BeO fuel.
Smith (2012) has researched UO2-BeO nuclear fuel about its thermal properties and analyzed the relationship between neutronic performance and economy. Smith concluded the addition of BeO brought positive effects. The thermal conductivity of UO2 varies from 4 to 3 W/m-K for temperatures between 500 and 900°C, is low for the core heat transport purpose, and is temperature-dependent (Fink, 2000). UO2-BeO fuel has considerable potential because the BeO material can improve the thermal conductivity of UO2 fuel. The increased thermal conductivity can provide a decreased fuel temperature. Thus the reductions in temperature affect reactivity. So, it is a significant benefit for the fuel performance. Although some penalties increased in some areas, they were compensated by the positive temperature effect.
Ferreira et al. (2013) studied BeO mixed UO2 microspheres with contents ranging from 1 wt% up to 14 wt%. Besides, an epithermal pool-type research reactor Annular Core Research Reactor (ACRR), at Sandia National Laboratories (SNL), had used UO2-BeO as core fuel for many years (Lyoussi et al., 2016). Russia also considered using UO2-BeO fuel in VVER type reactor (Kovalishin et al., 2014). Garcia et al. (2017) fabricated ceramic-ceramic composite forms of UO2 containing a continuous BeO matrix to increase the thermal conductivity of UO2. BeO's Additions were made to UO2 fuel pellets in 2.5, 5, 7.5, and 10 vol pct concentrations with the goals of establishing reliable lab-scale processing procedures, minimizing porosity, and maximizing thermal conductivity. The microstructure was characterized with electron probe microanalysis, and the thermal properties were assessed by light flash analysis and differential scanning calorimetry. Reliable, high-density samples were prepared using compaction pressure between 200 and 225 MPa and sintering times between 4 and 6 h. It was found that the thermal conductivity of UO2 improved approximately 10 pct for each 1 vol pct BeO added over the measured temperature range 298.15–523.15 K (25–250°C) with the maximum observed improvement being ∼100 pct, or doubled, at 10 vol pct BeO. Li et al. (2018) reported coefficient of thermal expansion and thermal conductivity evolutions of SPS fabricated UO2-10 vol% BeO fuel against temperature from room temperature to 1,600°C and found that the coefficient of thermal expansion increases flatly while the thermal conductivity is significantly improved, which demonstrated UO2-BeO composite fuel is one of the most effective thermal enhanced candidates for high-temperature operation. Camarano et al. (2019) investigated the influence of the beryllium oxide addition to increase the thermal conductivity in uranium dioxide fuel pellets containing gadolinium oxide as the burnable poison was investigated. Fuel pellets of UO2, UO2–BeO–Gd2O3, and UO2–Gd2O3 were obtained in concentrations of 2–3 wt% of BeO and 6 wt% of Gd2O3. The results showed an increase in the thermal diffusivity and conductivity of the UO2 pellets with additions of BeO compared to the values obtained with UO2 and UO2–Gd2O3 pellets. Gao et al. (2020) optimized the UO2-BeO composite pellets' fabrication process for improving thermal conductivity based on multi-parameter theoretical analyses and experimental investigations. It was found that the density of BeO and UO2/BeO interfacial thermal resistance (ITR) are crucial parameters that affect the thermal conductivity of UO2-BeO. To effectively increase BeO density and decrease UO2/BeO ITR, the fabrication method of pressureless sintering with a spheroidizing process was proposed. Through this method, a UO2-BeO composite with high thermal conductivity was obtained. 89.2 and 71.4% enhancements of the thermal conductivity over UO2 were achieved at room temperature and 673 K, respectively. This enhancement is higher than all the reported results in the previous literature that fabricated UO2-BeO using normal sintering temperatures (<2023 K). The finite element modeling results showed that our fabricated pellets' centerline temperatures in the reactor decreased remarkably compared with UO2 fuel, which would significantly improve reactor safety. Zhu et al. (2021) calculated the UO2/BeO interfacial thermal resistance (ITR) by diffuse mismatch model (DMM) and investigated the effects of ITR on UO2-BeO thermal conductivity. DMM can predict UO2/dispersed-BeO ITR within the accuracy of orders of magnitude. However, UO2/continuous-BeO ITR is three to four orders of magnitude larger than DMM predictions. This indicates that UO2/dispersed-BeO ITR is mainly induced by the vibrational mismatch, while UO2/continuous-BeO ITR may be attributed to the contact resistance. The thermal conductivity of UO2 containing dispersed BeO decreases with the decrease in BeO size, and the thermal conductivity of UO2 containing continuous BeO decreases with the decrease in the size of UO2 granule surrounded by BeO. The conditions for achieving the targeted enhancement of UO2 thermal conductivity by doping with BeO are derived. These conditions can be used to design and optimize the distribution, content, size of BeO, and the size of the UO2 granule.
Chandramouli and Revankar (2014) conducted a simulation of UO2-BeO composite under a loss of coolant accident (LOCA) condition by using FRAPTRAN code. Revankar et al. (2015) studied UO2 fueled core and UO2-BeO fueled core for a small break LOCA in a pressurized water reactor (PWR) RELAP5 code. Neutronic pin cell simulations for a typical PWR were performed using the lattice physics code DRAGON by McDeavitt et al. (2011). The mass equivalence studies compared two scenarios with an equal amount of uranium-235 atoms: a fuel with the BeO additive and fuel without the BeO additive. By holding an effective temperature constant (527°C) and increasing the BeO content from 0 to 10 volume percent, it was observed that BeO increased the BOC reactivity by ∼80 pcm per vol% BeO. By then accounting for the differences in Teff, it was found that the ∼100°C difference introduces another ∼350 pcm of reactivity. It was also determined that the beginning-of-cycle reactivity might increase by approximately 2900% milliRho, resulting in an increase in cycle length of approximately 20 days with a potential increase in end-of-cycle burnup to approximately 4000 MW d/tHM.
The temperature difference profile across a nuclear fuel pellet was calculated for the enhanced thermal conductivity of oxide nuclear fuels by Kim et al. (2010), Kim et al. (2011), Kim et al. (2012). The SB-BeO-UO2 fuel had the least decrease in the centerline temperature, followed by the green granule BeO-UO2 fuel. The green granule BeO-UO2 fuel had a more considerable decrease in centerline temperatures. According to the cost-benefit analysis results, the optimized BeO content was about 4.8 wt% when the BeO and uranium oxide prices were assumed to be $317/kg and $64/kg, respectively. Zahrádka and Škoda (2014) calculated the fuel temperature with a computational fluid dynamics software Fluent 14.0 using the WWER-1000 fuel geometry. The maximum fuel temperature for standard UO2 fuel was 1,175°C. Adding 5%, BeO reduced the maximum temperature by 145–1,030°C, a decrease of 12.4%. The increasing volume fraction of BeO resulted in decreased peak fuel temperature. Liu et al. (2015) presented the development of modeling and simulation for enhanced thermal conductivity UO2-BeO fuel behavior in a light water reactor with a 2D axisymmetric geometry using CAMPUS code. The modeling results showed that the fuel temperature could be significantly lowered using the enhanced thermal conductivity UO2-BeO fuel. Liu and Zhou (2017) proposed and analyzed a novel sandwich fuel. The performance of UO2 fuel, UO2-BeO composite fuel, and three types of UO2-BeO sandwich fuel were modeled in a light water reactor using CAMPUS code (Liu et al., 2016).
Li et al. (2009) presented simulation results for thermal conductivity of UO2-BeO composites using statistical continuum mechanics. Simulated micrographs of two UO2/BeO composites with 30% BeO were presented. The sample with less anisotropic microstructure showed that the thermal conductivity along the z-direction was 4.2% greater than that along the x-direction. In contrast, another sample with more anisotropic microstructure showed that the thermal conductivity in the z-direction is 6.1% greater than that in the x-direction. A methodology to generate ANSYS FEM thermal models of enhanced thermal conductivity oxide nuclear fuels was developed to study UO2-BeO composite nuclear fuel's enhanced thermal conductivity by Zhou et al. (2014), Zhou et al. (2015), Zhou et al. (2018). The modeling results successfully demonstrated the models' potential to accurately predict an enhanced thermal conductivity oxide nuclear fuel's effective thermal conductivity.
Abdalla et al. (2012) conducted a sensitivity analysis to determine the factors affecting the fuel centerline temperature. In this process, steady-state one-dimensional heat transfer analysis was conducted using MATLAB programming, and UO2-BeO fuels were examined enclosed in a 54 element fuel bundle. It presented that the fuel centerline temperature was lowered by 780°C for UO2-BeO. Wei et al. (2019) developed Modified Embedding Atom Method (MEAM) potential parameters of the beryllium oxide, which can well reproduce the thermodynamic properties of beryllium oxide.
Chen and Yuan (2020) discussed the neutronic properties of UO2-BeO fuel with various claddings such as zircaloy, FeCrAl, and SiC claddings. They investigated neutronic properties through the Monte Carlo method (Wang et al., 2014) and the Linear Reactivity Model. They suggested the relationship between the difference of reactivity at the End of the Cycle and two factors included the uranium enrichment and the volume fraction of BeO in the composite fuel. They also found an essential feature because the production of 4He in BeO-UO2 fuel is much more than 4He produced in the UO2 fuel. The composite fuel has a large (n,α) cross-section in the neutron's different energy spectrum. The zircaloy alloy cladding and SiC cladding have similar infinite multiplication factors kinf, also at low burnup, the kinf of SiC claddings act a little bit higher (Chen and Yuan, 2020). The SiC has lower neutron absorption cross-sections, while the FeCrAl claddings have a larger thermal neutron absorption cross-section, inducing a lower kinf. The FeCrAl and composite UO2-BeO system has less production of Kr and Xe than the UO2 systems. These data can provide a reliable reference for the research of optimization and replacement of current UO2 fuel. As mentioned above, developing a better fuel for nuclear systems is an inevitable trend.
Conventional energy sources are secure because they can be controlled quickly. Likely generator can be turned off effectively. However, nuclear fuel systems take a long time to close. The reactants in the fuel pellets will produce heat for some time continually. Thus, the cooler is the fuel, the better is the reactor system controlled. Also, reducing the temperature difference between the centerline and the pellet surface can decrease the fission gases produced. We can see the temperature difference between the two different fuel pellets in Figure 6 (Chen and Yuan, 2020). The UO2-BeO fuel pellet can transfer heat better than the UO2 one, and the fewer fission gases mean less damage to the fuel and claddings. Moreover, the addition of BeO can replace 238U in the fuel,so that increased resonance escape probability induces a positive reactivity effect because 238U is a strong absorber. As a whole, the addition of BeO is a positive effect on reactor reactivity.
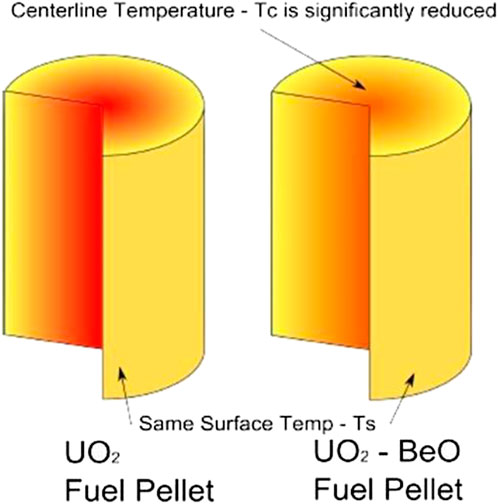
FIGURE 6. The temperature distribution in UO2 and UO2-BeO fuel pellets (Chen and Yuan, 2020).
However, in comparing UO2 and composite UO2 fuel economy, some problems emerge, and we should carefully consider them. If we only consider the 238U replaced by the addition of BeO, maybe the required amount of uranium will be reduced. However, the UO2-BeO needs more Uranium-235 to satisfy the requirement of higher enrichment (Smith, 2012) so that the costs associated with the UO2-BeO fabrication will increase. So, in terms of increasing enrichment, we should spend more effort to reduce its costs. The extra fuel processing costs could be compensated in other ways, such as the extension of cycle length, reduced operational costs, and the benefits of reactor safety.
The addition of beryllium material can increase nuclear fuel's burnup and life due to thermal conductivity improvement. We need to find a balance between the cost and two factors, i.e., the burnup and the operational lifetime. The fuel cost-benefit analysis (Kim et al., 2010) demonstrated that if the burnup is more than 60 MWD/kg, the BeO-UO2 fuel may have a positive economic sense. We can find the optimal ratio of beryllium and UO2 to make economic sense for composite fuel under certain conditions. Besides, if we can decrease the price gap between the beryllium material and uranium, it will increase the economic benefit. So, it is necessary to estimate the fuel cost of BeO-UO2 associated with the unstable market price of beryllium.
BeO Fabrication Overview
BeO’s receiving much attention can be traced back to the 1950s. Not only the combination of a low thermal neutron absorption cross-section with a high neutron scattering cross-section makes it an ideal material to use as a moderator or reflector (Rich et al., 1961), but also it has good performance in high-temperature such as thermal conductivity, stability, and radiation resistance relatively (Simnad et al., 1966). The preparation of BeO ceramic substrate material is mainly divided into five stages: powder preparation, powder pretreatment, shaping, sintering, and metallization.
BeO is the only alkaline-earth oxide crystallizing in the wurtzite structure instead of the NaCl-type structure (Morell et al., 1996). In its industrial production, BeO powder is extracted from beryllium minerals. Usually, Be(OH)2 is made first, then obtained BeO by calcining it. The BeO powder is processed either through the fluoride or sulfuric acid routes (Dong and Yi, 2005). The industrial-grade beryllium oxide contains a variety of impurities, such as magnesium oxide (MgO), aluminum oxide (Al2O3), and ferric oxide (Fe2O3). So, we should purify the powder by precipitating it with ammonium sulfate to remove aluminum. Each country has its purification method. The Soviet Union purified BeO by essential beryllium acetate distillation; some American companies obtained high-purity BeO by beryllium sulfate recrystallization. These ways all can achieve a purity level of above 99.9% for the purified powder. The conventional ceramic processing pathways can manufacture the monolithic BeO. Many binder materials should be used in the pre-firing process to obtain resins and starches. If we want to machine sintered products, we should pre-fire them at 1,200–1,500°C, then process them with appropriate tools, and finally, heat treats them at 1700–2000°C.
Sintering plays a vital role in the preparation of beryllium oxide ceramics. The main factors affecting sintering are temperature, atmosphere, and sintering time. Such materials' critical application property is their thermal conductivity, and purity is an essential factor affecting BeO ceramics' thermal conductivity. The higher purity of BeO powders, the better is the thermal conductivity of BeO ceramics. Proper sintering temperature and sintering time can contribute to the improvement of the ceramics thermal properties. In the initial sintering kinetics of BeO, we found that added a small amount of MgO could significantly improve the sintering rate of BeO (Carniglia and Hove, 1961), and the water vapor also can affect the shrinkage of BeO (Quirk et al., 1957; Quirk, 1959). Aitken (Aitken, 1960) investigated the shrinkage behavior of BeO calcined at different temperatures as well as the effect of water vapor on high-temperature sintering. It indicates that the density decreases even if the temperature is high enough under the influence of water vapor. In the research of hot pressing technology and density of ceramics, the BeO density can be increased by hot pressing to improve the thermal conductivity. At the temperature of 1700°C, the hot pressing powders' density is close to the theoretical value of 3.03 g/cc. However, above 1800°C, the repaid crystal growth has enormous effects on the ceramics strength. So, the temperature range of the best hot pressing is generally in 1700–1800°C (Snead, 2005). Of course, the density and thermophysical properties have a strong correlation with the fabrication conditions. The fabrication standards for nuclear-grade BeO have become more stringent, and the cost of production has increased significantly. Attempts to find more efficient methods in quantitative production can help solve the current cost concerns.
Comparison With Graphite Materials
The graphite material is mainly used in high-temperature gas-cooled reactors. Graphite gas-cooled reactors once played a crucial part in the development of nuclear reactors. Later on, it was gradually replaced by light water reactors and retired from the stage of history. However, the research into Gas-cooled Fast Reactor (GFR) is booming. The GFR system features a high-temperature helium-cooled fast spectrum reactor (Anzieu et al., 2009). The advantage of GFR is still worth exploring. The Gen-IV International Forum (GIF) Technology Roadmap indicated that GFR could combine a fast spectrum system with the sustainable development of uranium utilization resources (Gen IV, 2002). If we consider the BeO's use with gas-cooled reactors, we should compare its effect with graphite. Objectively, if we neglect the problems induced by irradiation, BeO has better compatibility with coolants. We can have wider choices for coolants. Graphite materials perform better at high temperatures regarding thermal conductivity, as shown in Figure 7 (Manly, 1964). However, the BeO exceeds other metallic oxides in thermal conductivity greatly.
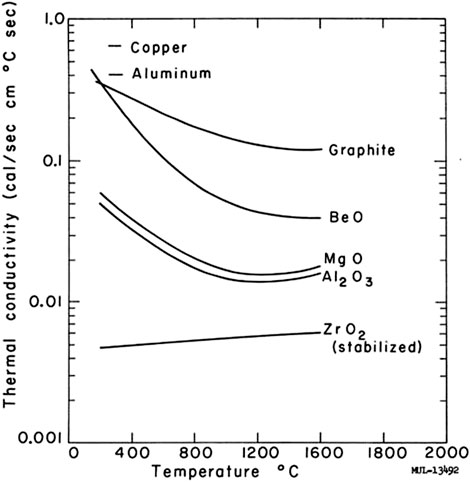
FIGURE 7. The comparison of thermal conductivities in different materials (Manly, 1964).
Interestingly, if we use the BeO material to design the reactor core, we should try our best to develop a smaller core than the system of graphite. In terms of power density requirements, the BeO reactor should have a higher power density because of its high capital cost of the reactor core. In contrast, the graphite systems are in no need to obtain power densities above 10 W/cm3 because the graphite plays a small portion in all power density associated costs. So, it is a necessity to obtain high power densities for the BeO systems.
In terms of the reactor core design, the ratio of the beryllium atoms to fissile atoms is about 2000, and the ratio of graphite systems is about 4000. Under this criterion, the cost per Gram of fissile material for the BeO system reactor is about 15 times that of the graphite system. So, we need to prolong the BeO system's reaction cycle length and increase its fuel recovery. An investigation has indicated that the benefit of increasing the thermal conductivity of BeO-UO2 fuel was more significant than the burden of high BeO material cost if the BeO content was 4.8 wt% (Kim et al., 2010). This is a valuable aspect for us to consider in the future. It is convenient to compare the two systems' parameters in a pebble-bed reactor because it can eliminate many unnecessary core parameters. Figure 8 shows the variation of power densities vs. different sphere diameters for both the BeO and graphite systems (Rothman, 1962).
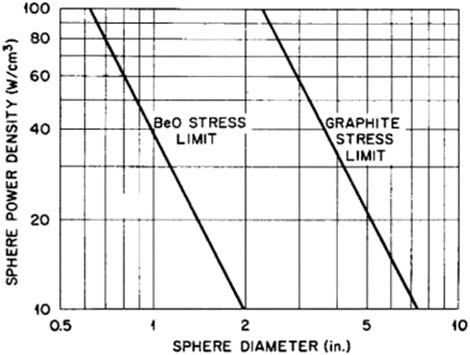
FIGURE 8. The relation of sphere diameter and power density (Rothman, 1962).
Meanwhile, thermal stress is limited to some extent. The BeO thermal stress is 10 times that of graphite. The BeO systems also reduce the core power density to satisfy the void fraction requirement in the core. Moreover, under the specific thermal stress limits, the average power density needs to be further reduced. This conflicts with the necessity to enhance the BeO reactor's power density. So, it is a serious technical problem, which needs further investigation in the future. Table 2 shows the difference between the BeO-helium, BeO-CO2, and Graphite-helium systems. The advantage of the BeO systems is that the cost of CO2.
On the other hand, if we want to achieve the same standards as the graphite systems, the BeO fuel pellets should be as small as possible. This means the BeO system uses the number of fuel elements over 50 times the graphite system. These constraints make the cost and equipment requirements of BeO systems significantly increased. Of course, the BeO material has advantages in terms of compatibility with coolant.
Conclusion
It is necessary to find a suitable material to improve the safety and effectiveness of nuclear reactors. There is no doubt that the BeO is an excellent potential material due to its properties of high conductivity and excellent neutron moderation. All of these are necessary to develop and enhance nuclear reactor safety and performance. Even though the graphite systems also have good performance and meet the nuclear industry requirements, some BeO utilization in reactor systems is still worth investigation to improve the reactor safety and performance. In terms of moderate neutron performance, the BeO material has more excellent performance and better compatibility with coolants. It can improve the ratio of energy conversion to some extent. This material brings improved performance for reactors, while the costs associated with material manufacturing and fuel reprocessing need further investigation and compensation. The problems on reprocessing fuel and the fabrication of nuclear grade BeO still need further exploration. There are still some challenges to overcome if we choose to use BeO mixed with the graphite material, such as whether BeO can be compatible with the graphite material, the expansion difference between two materials, and the fission gas release.
We can conclude from the previous research that the BeO material will be more widely used in reactor systems. The presentation of the Daniels reactor project had led to new applications for BeO. The choice of moderator materials is no longer limited to particular materials, such as graphite and heavy water. Some metal oxide materials can provide even better performance. BeO has superior moderation properties compared to graphite and lower cost compared to heavy water. In the subsequent ARE and ART projects, researchers also attempted to apply the BeO material to space and molten salt reactors, and some experimental results also proved the feasibility of the BeO material. The high-temperature resistance of the BeO material made it a preferred choice of moderator material for the Pluto Project. In some extreme environments, such as space reactors, stable metal oxide materials offer a more suitable option. The BeO material's application in the Kilopower project is an excellent example for this purpose.
Nevertheless, the BeO implementation still encountered some challenges and difficulties. The Daniels Reactor project's termination was due to insufficient experimental data for the BeO behavior in a reactor, which would lead to much uncertainty. The military's termination of cooperation also brought about the failure of the ART and other projects. The Kilopower Project just completed the first step of exploration. There is still much work ahead. So, further investigation on the BeO material becomes necessary.
In specific design considerations for the BeO cores, the first thing to distinguish is whether the core's design is homogeneous or heterogeneous. For the heterogeneous reactors, the irradiation stability of BeO and the release characteristics of tritium and lithium are beneficial. For the homogeneous reactors, it is noticed that how to recycle the BeO moderator material and fuel as far as possible and the proper methods of material preservation are also relatively critical. Therefore a reliable reprocessing and manufacturing process is required. For two different systems, the volume of BeO is always small due to its relatively high capital cost in the reactor core. It may complicate more the core design. It is not easy to select suitable channels of coolant and control rod holes. Even though the pebble-bed design can partly simplify the core design, it would also bring many difficulties such as pressure drop and fuel processing.
The research should focus on developing accident-tolerant fuels, which can modify nuclear fuel using the BeO material. The high thermal conductivity of BeO material should be utilized as far as possible. Researchers have been evaluating the BeO-UO2 composite fuel for a long time. Its properties are accorded with the direction of the development of next-generation nuclear reactors perfectly. The combination of the BeO material and fuel can significantly improve fuel performance safely and economically. It will broadly promote the development of nuclear reactors. The combination of a considerable volume of BeO and UO2 fuel can improve the fuel's conductivity. The thermal conductivity could be enhanced by 10–20 times after adding 20 wt% BeO compared with pure UO2.
Moreover, it has an impact on the release of fission gases. All of these ways are critical indicators to improve the performance of nuclear fuel. However, there are still many challenging problems to be solved. The BeO is a toxic material. In the manufacturing process, it is possible to cause harm to people's health and the environment. The perfect protection and treatment measures can effectively avoid damages. However, in some countries, the use of BeO material is limited. More attention should be paid to the reactor operating temperature range when designing the BeO cores. The excessive temperature would affect the stability of the BeO material. The large temperature gradient has damage to the material structure. So, it is better to enhance the plasticity of UO2-BeO to resist the thermal stress deformation at the specific temperature range. The minimum temperature should be kept above 800°C, and the maximum temperature should not exceed 1,375°C. The high temperature (1,100°C) would also increase the reaction between BeO and the vapor, inducing the moderator's failure. These conditions define the temperature range of each area for the reactors. It will significantly limit the choice of heat exchangers and piping systems in the reactor design. At present, the BeO reactor has been under development for a long time. It exactly proved the importance of BeO in nuclear systems. However, there are many limitations to BeO utilization in reactors until now. Perhaps we can take the following measures to improve our ability to solve problems:
(1) Looking for a more economical manufacturing process for nuclear-grade BeO and how to improve the recovery of BeO as far as possible.
(2) Focusing on the best combination of UO2 and BeO to improve the performance of the fuel.
(3) Expanding knowledge reserves about the BeO utilization under the extreme environment employing computer simulation technology.
(4) Trying to modify the BeO structure to eliminate the effect of thermal stress-strain cycling on the BeO properties.
(5) Researching on irradiation mechanism of BeO to solve the BeO irradiation deformation problem.
Although there is no doubt that BeO has excellent reactor performance, it can play its role to a large extent only after we solve the associated manufacturing technology and cost concerns. Seeking and developing mature technology methods to reduce the cost is an important direction. Further attention should be paid to the exploration of the BeO material and its compatibility with other materials. The computer simulation technology can be appropriately used to get more reference data about the BeO utilization under the extreme environment to provide theoretical support for reactors' practical applications. If it can correctly solve the cost and compatibility problems, it will bring about a revolution for reactors' BeO utilization.
Author Contributions
The work is mainly done by KL and WZ. LQ, XL, and YM all contributed to the accomplishment of this work, and WZ is the advisor of KL.
Funding
The financial support from Nuclear Power Technology Innovation Center of China (No. 45000–41020012), the Fundamental Research Funds for the Central Universities of China (No. 45000–18841210), the International Sci and Tech Cooperation Program of Guangdong Province (No. 2019A050510022), and Guangdong Major Project of Basic and Applied Basic Research (No. 2019B030302011) is highly appreciated.
Conflict of Interest
Author LQ was employed by company Nuclear Power Institute of China.
The remaining authors declare that the research was conducted in the absence of any commercial or financial relationships that could be construed as a potential conflict of interest.
References
Abdalla, A., Peiman, W., Pioro, I., and Gabriel, K. (2012). “Sensitivity Analysis of Fuel Centerline Temperature in SCWRs,” in Proceedings of the 2012 20th International Conference on Nuclear Engineering and the ASME 2012 Power Conference. The American Society of Mechanical Engineers, New York, NY, July 30–August 3, 2012, 1–18. doi:10.1115/icone20-power2012-54530
Aerojet-General Corporation (1962). Army Gas-Cooled Reactor Systems Program Semiannual Progress Report, IDO-28590. San Ramon, CA: Aerojet-General Corporation.
Aitken, E. A. (1960). Initial Sintering Kinetics of Beryllium Oxide. J. Am. Ceram. Soc. 43 (12), 627–633. doi:10.1111/j.1151-2916.1960.tb13631.x
Anzieu, P., Stainsby, R., and Mikityuk, K. (2009). Gas-cooled Fast Reactor (GFR): Overview and Perspectives, in “Proceedings of GIF (Gen-IV International Forum) Symposium 2009”, Paris, France.
Bettis, E. S., Cottrell, W. B., Mann, E. R., Meem, J. L., and Whitman, G. D. (1957). The Aircraft Reactor Experiment-Operation. Nucl. Sci. Eng. 2 (6), 841–853. doi:10.13182/nse57-a35497
Camarano, D. M., Mansur, F. A., Santos, A. M. M., Ribeiro, L. S., and Santos, A. (2019). Thermal Conductivity of UO2–BeO–Gd2O3 Nuclear Fuel Pellets. Int. J. Thermophys. 40, 110. doi:10.1007/s10765-019-2574-5
Carniglia, S., and Hove, J. (1961). Fabrication and Properties of Dense Beryllium Oxide. J. Nucl. Mater. 4 (2), 165–176. doi:10.1016/0022-3115(61)90125-8
Chandramouli, D., and Revankar, S. T. (2014). Development of Thermal Models and Analysis of UO2-BeO Fuel during a Loss of Coolant Accident. Int. J. Nucl. Energ 2014 (4), 1–9. doi:10.1155/2014/751070
Chen, S., and Yuan, C. (2020). Neutronic Study of UO2-BeO Fuel with Various Claddings. Nucl. Mater. Energ. 22, 100728. doi:10.1016/j.nme.2020.100728
Cottrell, W., Ergen, W., Fraas, A., McQuilkin, F., and Meem, J. (1955). Aircraft Reactor Test Hazards Summary Report. Oak Ridge, TN: Oak Ridge National Lab (ORNL). doi:10.2172/4204557
Dong, C., D., and Yi, J. (2005). Prospect of Beryllium Copper Alloy′ S Market and Application. Chin. J. Rare Met. 2005 (3), 350–356. doi:10.3969/j.issn.0258-7076.2005.03.019
Ferreira, R. A. N., Camarano, D. D. M., Miranda, O., Grossi, P. A., Andrade, A. S., Queiroz, C. M., et al. (2013). Beryllium Project: Developing in CDTN of Uranium Dioxide Fuel Pellets with Addition of Beryllium Oxide to Increase the Thermal Conductivity. INAC 2013: International Nuclear Atlantic Conference
Fink, J. K. (2000). Thermophysical Properties of Uranium Dioxide. J. Nucl. Mater. 279 (1), 1–18. doi:10.1016/s0022-3115(99)00273-1
Gao, R., Yang, Z., Li, B., Yan, B., Cheng, L., Wang, Y., et al. (2020). Fabrication of UO2-BeO Composite Pellets with Superior Thermal Conductivity Based on Multi-Parameter Theoretical Analyses. J. Nucl. Mater. 542, 152533. doi:10.1016/j.jnucmat.2020.152533
Garcia, C. B., Brito, R. A., Ortega, L. H., Malone, J. P., and McDeavitt, S. M. (2017). Manufacture of a UO2-Based Nuclear Fuel with Improved Thermal Conductivity with the Addition of BeO. Metallurgical Mater. Trans. E 4, 70–76. doi:10.1007/s40553-017-0108-2
Gen IV, R. (2002). A Technology Roadmap for Generation IV Nuclear Energy Systems. Washington DC: US DOE nuclear energy research advisory committee and the Generation IV international forum, GIF002-00.
Gibson, M. A., Oleson, S. R., Poston, D. I., and McClure, P. (2017). NASA's Kilopower Reactor Development and the Path to Higher Power Missions. IEEE Aerospace Conference. IEEE, 1–14.
Hey, A. W., and Livey, D. T. (1966). The Calcination of Two BeO Powders. Trans. Br. Ceram. Soc. 65, 627–642. doi:10.1039/TF9676302316
Ishimoto, S., Hirai, M., Ito, K., and Korei, Y. (1996). Thermal Conductivity of UO2-BeO Pellet. J. Nucl. Sci. Technol. 33, 134–140. doi:10.1080/18811248.1996.9731875
James, C. C. (2000). The Politics of Extravagance: The Aircraft Nuclear Propulsion Project. Naval War Coll. Rev. 53, 158–190.
Jernkvist, L., Massih, A., and de Betou, J. I. (2002). Evaluation of Fission Product Gas Release and the Impact of Fuel Microstructure at High Burnup. Enlarged Halden Programme Group Meeting, September 8–13, 2002. Norway: Storefjell, Gol.
Kettner, M., Biebersmith, P., Roldan, N., and Sharma, B. K. (2001). Aluminum Nitride vs. Beryllium Oxide for High Power Resistor Products (Technical Feature). Microwave J. 44 (11), 104–111.
Kim, S. K., Ko, W. I., Kim, H. D., Chung, Y. H., Bang, S. S., and Revankar, S. T. (2011). Economic Viability to BeO-UO2 Fuel Burnup Extension. Nucl. Eng. Technol. 43, 141–148. doi:10.5516/net.2011.43.2.141
Kim, S. K., Ko, W. I., Kim, H. D., Revankar, S. T., Zhou, W., and Jo, D. (2010). Cost-benefit Analysis of BeO–UO2 Nuclear Fuel. Prog. Nucl. Energ. 52, 813–821. doi:10.1016/j.pnucene.2010.07.008
Kim, S., Ko, W., Zhou, W., Revankar, S. T., Chung, Y., and Bang, S. (2012). The Credit Analysis of Recycling Beryllium and Uranium in BeO-UO2 Nuclear Fuel. J. Nucl. Sci. Technol. 49, 298–309. doi:10.1080/00223131.2012.660020
Koba, R., Harris, J., Youngman, R., Mallinger, M., and Max, L. (1997). Aluminum-nitride Packages Provide Consistent Performance. Microwaves & RF 36 (10), 156–166.
Kovalishin, A. A., Prosyolkov, V. N., Sidorenko, V. D., and Stogov, Y. V. (2014). On the Possibility of Using Uranium-Beryllium Oxide Fuel in a VVER Reactor. Phys. Atom. Nucl. 77, 1661–1663. doi:10.1134/s1063778814140063
Latta, R., Revankar, S. T., and Solomon, A. A. (2008). Modeling and Measurement of Thermal Properties of Ceramic Composite Fuel for Light Water Reactors. Heat Transf. Eng. 29, 357–365. doi:10.1080/01457630701825390
Li, B., Yang, Z., Jia, J., Zhong, Y., Liu, X., Zhang, P., et al. (2018). High Temperature Thermal Physical Performance of BeO/UO2 Composites Prepared by Spark Plasma Sintering (SPS). Script. Mater. 142, 70–73. doi:10.1016/j.scriptamat.2017.08.031
Li, D. S., Garmestani, H., and Schwartz, J. (2009). Modeling Thermal Conductivity in UO2 with BeO Additions as a Function of Microstructure. J. Nucl. Mater. 392, 22–27. doi:10.1016/j.jnucmat.2009.03.048
Lillie, J. (1961). Some Properties of Beryllium Oxide. Livermore, USA: Univ., Lawrence Radiation Lab.
Liu, R., Prudil, A., Zhou, W., and Chan, P. K. (2016). Multiphysics Coupled Modeling of Light Water Reactor Fuel Performance. Prog. Nucl. Energ. 91, 38–48. doi:10.1016/j.pnucene.2016.03.030
Liu, R., and Zhou, W. (2017). Multiphysics Modeling of Novel UO2-BeO Sandwich Fuel Performance in a Light Water Reactor. Ann. Nucl. Energ. 109, 298–309. doi:10.1016/j.anucene.2017.05.037
Liu, R., Zhou, W., Shen, P., Prudil, A., and Chan, P. K. (2015). Fully Coupled Multiphysics Modeling of Enhanced Thermal Conductivity UO2–BeO Fuel Performance in a Light Water Reactor. Nucl. Eng. Des. 295, 511–523. doi:10.1016/j.nucengdes.2015.10.019
Lyoussi, A., Kaiser, K., Nowlen, K. C., and DePriest, K. R. (2016). Characterization of the Annular Core Research Reactor (ACRR) Neutron Radiography System Imaging Plane. EPJ Web of Conferences 106, 01005. 10.1051/epjconf/201610601005.
Manly, W. D. (1964). Utilization of BeO in Reactors. J. Nucl. Mater. 14, 3–18. doi:10.1016/0022-3115(64)90158-8
McCullough, C. R. (1947). Summary Report on Design and Development of High Temperature Gas-Cooled Power Pile. Oak Ridge, TN (United States): Clinton Labs. doi:10.2172/4359623
McDeavitt, S. M., Ragusa, J., Revankar, S. T., Solomon, A. A., and Malone, J. (2011). A High-Conductivity Oxide Fuel Concept. Nucl. Eng. Int., 40–42.
Merkle, T. C. (1961). The Nuclear Ramjet Propulsion System. Berkeley, USA: University of California Radiation Laboratory.
Mills, R. G., Barner, J. O., Johnson, D. E., and Simnad, M. T. (1964). Irradiation Effects on Dispersion Type BeO-UO2 Fuels for Ebor. J. Nucl. Mater. 14, 482–486. doi:10.1016/0022-3115(64)90215-6
Moore, W. C. (1961). The Experimental Beryllium Oxide Reactor. Maritime Gas-cooled Reactor Program. United States: Maritime Gas-Cooled Reactor Program. doi:10.2172/4826933
Morell, G., Perez, W., Ching-Prado, E., and Katiyar, R. (1996). Anharmonic Interactions in Beryllium Oxide. Phys. Rev. B 53 (9), 5388. doi:10.1103/physrevb.53.5388
Nishigaki, S., and Maekawa, K. (1964). Fabrication of BeO-UO2-Be Fuel Pellets. J. Nucl. Mater. 14, 453–458. doi:10.1016/0022-3115(64)90211-9
Ott, L. J., Robb, K. R., and Wang, D. (2014). Preliminary Assessment of Accident-Tolerant Fuels on LWR Performance during Normal Operation and under DB and BDB Accident Conditions. J. Nucl. Mater. 448 (1-3), 520–533. doi:10.1016/j.jnucmat.2013.09.052
Pelfrey, E. (2019). A Transient Thermal and Structural Analysis of Fuel in the Annular Core Research Reactor. Albuquerque, Mexico USA: Master thesis, University of New Mexico.
Poston, D. I., Gibson, M., and McClure, P. (2019). “Kilopower Reactors for Potential Space Exploration Missions,” in Nuclear and Emerging Technologies for Space (ANS: American Nuclear Society Topical Meeting).
Quirk, J. F. (1959). Factors Affecting Sinterability of Oxide Powders: BeO and MgO. J. Am. Ceram. Soc. 42 (4), 178–181. doi:10.1111/j.1151-2916.1959.tb12943.x
Quirk, J. F., Mosley, N. B., and Duckworth, W. H. (1957). Characterization of Sinterable Oxide Powders: I, BeO. J. Am. Ceram. Soc. 40 (12), 416–419. doi:10.1111/j.1151-2916.1957.tb12565.x
Revankar, S. T., Zhou, W., and Chandramouli, D. (2015). Thermal Performance of UO2-BeO Fuel during a Loss of Coolant Accident. Int. J. Nucl. Energ. Sci. Eng. 5 (0), 1–8.
Rich, J., Walters, G., and Barnes, R. (1961). The Mechanical Properties of Some Highly Irradiated Beryllium. J. Nucl. Mater. 4 (3), 287–294. doi:10.1016/0022-3115(61)90079-4
Robertson, R. (1965). MSRE Design and Operations Report. Part I. Description of Reactor Design. Tennessee, USA: Oak Ridge National Lab. doi:10.2172/4654707
Rothman, A. J. (1962). Properties of BeO Ceramics and Their Application in a Nuclear Propulsion Systems (PLUTO). USA: University of California Lawrence Radiation Laboratory.
Sarma, K. H., Fourcade, J., Lee, S.-G., and Solomon, A. A. (2006). New Processing Methods to Produce Silicon Carbide and Beryllium Oxide Inert Matrix and Enhanced Thermal Conductivity Oxide Fuels. J. Nucl. Mater. 352, 324–333. doi:10.1016/j.jnucmat.2006.02.090
Simnad, M., Meyer, R., and Zumwalt, L. (1966). Beryllium Oxide - a Review in Nuclear Applications. Westerville, OH: American Ceramic Society, 469.
Slaughter, G., Leitten, C., Patriarca, P., Hoffman, E., and Manly, W. (1957). Sodium Corrosion and Oxidation Resistance of High-Temperature Brazing Alloys. (NY: Welding J.). 36.
Smith, D. K., Cline, C. F., and Frechette, V. D. (1962). A High Temperature Crystallographic Phase Inversion in BeO. J. Nucl. Mater. 6 (3), 265–270. doi:10.1016/0022-3115(62)90003-x
Smith, J. (2012). Enhanced Thermal Conductivity UO2-BeO Nuclear Fuel: Neutronic Performance Studies and Economic Analyses. College Station, TX: Master thesis, Texas A&M University.
Snead, L. L., (2005). Use of Beryllium and Beryllium Oxide in Space Reactors. In AIP Conference Proceedings, 768–775.
Van Houten, G., White, J., and Botje, J. (1961). Formation of Alumina Coatings on BeO by a Vapor Deposition Process. USA: General Electric Company Report, Apex-699. doi:10.2172/12474963
Wang, K., Li, Z., She, D., Xu, Q., Qiu, Y., Yu, J., et al. (2014). RMC-A Monte Carlo Code for Reactor Core Analysis. SNA+ MC 2013-Joint International Conference on Supercomputing in Nuclear Applications+ Monte Carlo. Les Ulis, France: EDP Sciences, 06020. doi:10.1051/snamc/201406020
Wei, J., Zhou, W., Li, S., Shen, P., Ren, S., Hu, A., et al. (2019). Modified Embedded Atom Method Potential for Modeling the Thermodynamic Properties of High Thermal Conductivity Beryllium Oxide, ACS Omega, 4, 6339–6346. doi:10.1021/acsomega.9b00174
Wells, W., and Cline, C. (1963). Thermal Stress Fracture Characteristics of BeO. Livermore, USA: California. Univ., Lawrence Radiation Lab.
Zahrádka, T., and Škoda, R. (2014). Cost Saving when Using Enhanced Conductivity Nuclear Fuel Containing BeO in WWER-1000 Reactors, in “2014 22nd International Conference on Nuclear Engineering”, American Society of Mechanical Engineers (ASME), V001T01A019.
Zhou, W., Liu, R., and Revankar, S. T. (2015). Fabrication Methods and Thermal Hydraulics Analysis of Enhanced Thermal Conductivity UO2-BeO Fuel in Light Water Reactors. Ann. Nucl. Energ. 81, 240–248. doi:10.1016/j.anucene.2015.02.044
Zhou, W., Liu, R., and Revankar, S. T. (2014). UO2-BeO Composite Fuel Thermal Property and Performance Modeling. J. Energ. Power Eng. 8 (7), 234. doi:10.17265/1934-8975/2014.07.003
Zhou, W., Revankar, S. T., Liu, R., and Shahmohammadi Beni, M. (2018). Microstructure Based Thermal Conductivity and Thermal Behavior Modeling of Nuclear Fuel UO2-BeO. Heat Transfer Eng. 39 (9), 760–774. doi:10.1080/01457632.2017.1341216
Zhou, W., and Zhou, W. (2018). Thermophysical and Mechanical Analyses of UO2-36.4 Vol% BeO Fuel Pellets with Zircaloy, SiC, and FeCrAl Claddings. Metals 8 (1), 65. 10.3390/met8010065.
Keywords: beryllium oxide, moderator, reflector, accident tolerant fuel (ATF), extreme reactor environment
Citation: Li K, Qian L, Li X, Ma Y and Zhou W (2021) BeO Utilization in Reactors for the Improvement of Extreme Reactor Environments - A Review. Front. Energy Res. 9:669832. doi: 10.3389/fenrg.2021.669832
Received: 19 February 2021; Accepted: 26 April 2021;
Published: 10 May 2021.
Edited by:
Shoaib Usman, Missouri University of Science and Technology, United StatesReviewed by:
Claudio Tenreiro, University of Talca, ChileJie Cheng, Harbin Engineering University, China
Copyright © 2021 Li, Qian, Li, Ma and Zhou. This is an open-access article distributed under the terms of the Creative Commons Attribution License (CC BY). The use, distribution or reproduction in other forums is permitted, provided the original author(s) and the copyright owner(s) are credited and that the original publication in this journal is cited, in accordance with accepted academic practice. No use, distribution or reproduction is permitted which does not comply with these terms.
*Correspondence: Wenzhong Zhou, emhvdXd6aDNAbWFpbC5zeXN1LmVkdS5jbg==