- Department of Solid State Sciences, COCOON Research Group, Ghent University, Ghent, Belgium
Transition metal oxides are promising anode materials for lithium-ion batteries thanks to their good electrochemical reversibility, high theoretical capacities, high abundance, and low cost. The mechanism of lithium insertion or deintercalation into or from these metal oxides can be different depending upon their lattice structure or chemical nature. Synergistic effects obtained from mixing different metal oxides with (dis)similar lithiation/delithiation mechanisms (intercalation, conversion and alloying) can significantly improve the device performances. In this research, we systematically investigate the impact on electrochemical properties of SnO2 thin-films upon mixing with TiO2, Fe2O3 and ZnO. In these pure thin-films, SnO2 displays conversion- as well as alloying-type lithiation and serves as the host material, whereas TiO2 represents an intercalation-type anode material, Fe2O3 exhibits conversion reactions and ZnO expresses alloying during lithiation-delithiation processes. Importantly, all the composite thin-films have an intermixed structure at the atomic scale, as they are precisely prepared by the atomic layer deposition method. The electrochemical properties demonstrate that the composite thin-films show better performance, either higher capacities or better cycling retentions, than the individual constituent material (SnO2, TiO2, Fe2O3 or ZnO). Overall cycling stability improves to a great extent along with a slight increase in capacity with the addition of TiO2. The supplement of Fe2O3 in the SnO2–Fe2O3 composite thin-films moderately improves both capacity and retention, while the SnO2–ZnO composite electrodes demonstrate a good cyclability and stabilize at a relatively high capacity. The systematic investigation of synergistic effects on the different types (intercalation, conversion and alloying) of metal oxide composites is expected to provide guidance towards the development of composite anode materials for lithium-ion batteries.
Introduction
Among different electrochemical energy storages devices, lithium-ion batteries (LIBs) are popular and widely used due to their unique virtues, such as low self-discharge rate, long cycle life, high conversion efficiency, and easy to manufacture flexible designs etc. With the growing needs for high power/energy density applications such as electric vehicles, grid storages etc., new demands for LIBs are requiring. However, traditional electrodes like graphite (anode, theoretical capacity is 372 mAh g−1) and LiCoO2 (cathode, theoretical capacity is 274 mAh g−1) are unable to satisfy anymore. Therefore, it is crucial to find new materials which can fulfill these new demands (Chen et al., 2018a; Kim et al., 2019; Pender et al., 2020).
Anode materials for LIBs can be typically divided into the categories of carbonaceous material (e.g., graphite, graphene and carbon nanotubes), silicon and metal oxides (Su et al., 2014; Qi et al., 2017; Fang et al., 2019; Roselin et al., 2019). Among others, transition metal oxides have received tremendous interests due to their high theoretical capacities, good redox reversibility and ease of synthesis (Reddy et al., 2013; Zheng et al., 2018; Fang et al., 2020). There are three mechanisms of lithium storage in transition metal oxides: intercalation, conversion and alloying. For intercalation-type anodes, the lithium ions can be reversibly inserted/removed into/from the host material without chemical deformation and slight volume deterioration. As an example, (lithium-) titanium dioxide, is a typical representative of intercalation-type materials. With the limited lithium uptake per volume and high molar mass, the intercalation-type anodes are more suitable for applications which require longer stability (Zhu et al., 2012; Yan et al., 2015; Yuan et al., 2017). For the alloying-type, metal oxide firstly irreversibly converts to metal and then reacts with lithium to form lithium-metal alloys during the charging process, the following discharging process is the reversible dealloying steps of lithium-metal to metal. Sn- and Ge-based oxides are typical belonging to the alloying-type anode (Wei et al., 2013). The lithium-metal alloying and dealloying process provides the advantage of high lithium storage capability which is certainly good for the high capacity, but the accompanying severe volume change during charge-discharge is the fatal shortcoming (Zhang, 2011; Liu et al., 2017). This issue can be solved to some extent for the conversion-type metal oxides. The formed metals during the charging process do not alloy and dealloy with lithium anymore, instead, accompanying the reduction and oxidation. The metallic nanonetwork embedded in a Li2O matrix formed after the reaction can improve the overall conductivity of the electrode (Wadewitz et al., 2013; Bruck et al., 2016; Lu et al., 2018). This essential merit can effectively elucidate the pulverization problem caused by volume changes and allow capacity improvement owing to their multiple redox reaction. However, the overall improvement in capacity and stability is limited to a certain extent. A summary of typical materials corresponding to the three types of anodes, and their advantages and drawbacks are listed in Table 1.
Even though the three types of metal oxide have their advantages, their shortcomings of either low capacity or tremendous volume changes together with the poor electronic conductivity make it hard to undertake the task of a good battery material individually. A strategy to effectively combat the bad impacts is using two different phases while react towards lithium at two different electrochemical potentials (vs. Li/Li+) in one composite electrode. Regarding this aspect, the hybrid AOx-BOy (A, B are different metal) electrodes are expected to sequentially alleviate the volume expansion and provide a highway for charge transfer in the two phases, guiding to a high reversible capacity and rate performance compared with pure phases. There are literatures reporting a synergistic effect of two different metal oxides leading to a significant improvement in cyclability and capacity (Wu et al., 2015; Zhao et al., 2016). SnO2 is a well-studied material and it exhibits a typical conversion and following alloying reaction mechanism towards lithium (Chen and Lou, 2013; Zhao et al., 2015b; Zoller et al., 2019). There are many researches on the synergistic effect between SnO2 and another metal oxide, like SnO2–CuO (Cheong et al., 2018), SnO2–TiO2 (Yi et al., 2016), SnO2–Fe2O3 (Kint et al., 2019), SnO2–ZnO (Zhao et al., 2019), SnO2–Co3O4 (Zhao et al., 2015a) and SnO2–In2O3 (Kim et al., 2007) etc. as composite anode material for LIBs.
In this report, SnO2–TiO2, SnO2–Fe2O3, and SnO2–ZnO composite thin-films intermixed at the atomic scale were precisely prepared by the atomic layer deposition (ALD), and were used as model electrodes to systematically investigate their evolved electrochemical properties. Here ALD provides the advantages of precise thickness and composition control of the thin-film electrodes, which in turn allows for the investigation of the transport process of lithium ions through the active material without the interference of polymeric binder and carbon black as used in conventional composite electrodes (Ha et al., 2012). Thin-film electrodes react with lithium fast and effectively which encourage the cyclic voltammetry curve with higher resolution and thus can be used to analyze more details of the peak and furtherly deconvolute overlapping reactions (Ferraresi et al., 2018).
Three typical representative substances which exhibit a different reaction mechanism as pure thin-films (intercalation-type TiO2, conversion-type Fe2O3 and alloying-type ZnO) have been mixed with SnO2 material. The precisely controlled compositions were verified by X-ray photoemission spectroscopy (XPS), surface morphologies measured with atomic force microscopy (AFM), synergistic effect mechanisms were mainly investigated by cyclic voltammetry (CV), electrochemical impedance spectroscopy (EIS), cycling stability and rate capability.
Experimental
The thin-film samples were prepared in a home-built high vacuum ALD system (base pressure is below 5 × 10–6 mbar) (Xie et al., 2007; Musschoot et al., 2009; Dendooven et al., 2010). Tetrakis(dimethylamino)tin(IV) (TDMASn, 99.9%, Sigma Aldrich) and H2O was used to deposit SnO2, where TDMASn bubbler heated to 45°C, and the corresponding conveyer tube to the chamber held at 50°C (Zhao et al., 2019). To deposit TiO2 and ZnO, tetrakis(dimethylamido)titanium (TDMAT, 99.99%, Sigma Aldrich) and diethyl zinc (DEZn, 95%, Strem Chemicals) were chosen as metal sources respectively, and H2O used as the co-reactant. TDMAT, DEZn and H2O were kept at room temperature and all the conveyer tubes were kept at 50°C (Deng et al., 2015). Tert-butyl ferrocene (TBF, 98%, Strem Chemicals) and oxygen plasma was used to deposit Fe2O3 (Ramachandran et al., 2014). The TBF bubbler was kept at 75°C, and the conveyer tube to the chamber was heated to 85°C. The parameters for generating oxygen plasma are as follows: the input oxygen pressure is 1 × 10–2 mbar, a radio frequency remote plasma source at a frequency of 13.56 MHz and the output power is 200 W. The substrate temperature was held at 150°C for all the depositions. The ALD of SnO2–MOx composites were conducted by using the supercycles based sequence of n × (x SnO2 + y MOx) (M = Ti, Fe or Zn), where x is the cycle number of ALD SnO2, y is the cycle number of ALD MOx, and n represents the supercycle repetition number. The value of x and y was chosen to achieve atomic scale intermixing rather than multilayer deposition, as illustrated in Figure 1A.
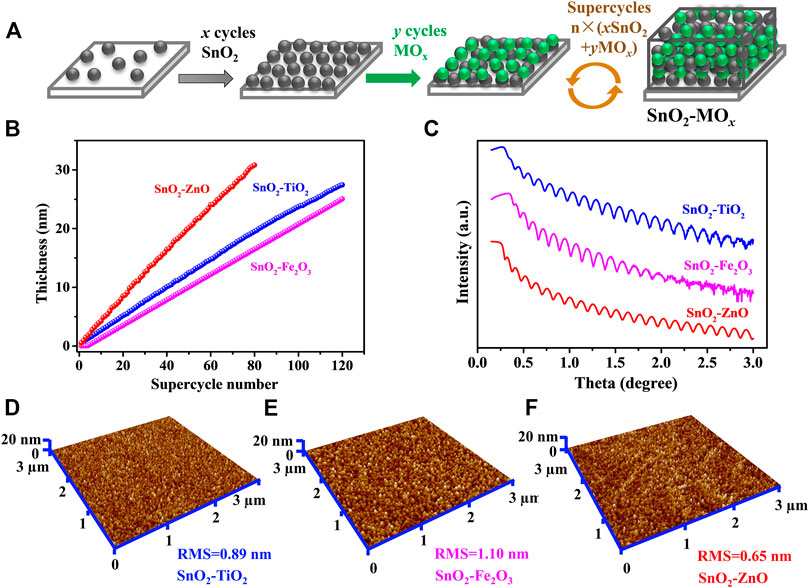
FIGURE 1. ALD of SnO2–MOx composite thin-films. (A) Scheme of the supercycles approach n × (x SnO2 + y MOx). (B) Thickness as a function of supercycle number from in-situ SE and (C) XRR curves. Three-dimensional view AFM images of the ALD (D) SnO2–TiO2, (E) SnO2–Fe2O3 and (F) SnO2–ZnO thin-films. The scale is 3 × 3 µm.
Thin-films were deposited on Si (100) substrates for growth characterizations. In-situ spectroscopic ellipsometry (SE) was used to monitor the thickness of the thin-film in between ALD cycles using a Woollam M-2000 spectrometer fitted directly onto the ALD reactor. X-ray reflectometry (XRR) was used to measure the thickness and density of the as-deposited thin-films, in which XRR was performed on a Bruker D8 diffractometer with Cu Kα (λ = 0.154 nm) radiation. Surface morphologies and roughness were characterized by atomic force microscopy (AFM, Bruker Dimension Edge system) in tapping mode and scanning electron microscopy (SEM, Quanta 200 F FEI). X-ray photoelectron spectroscopy (XPS) measurements were performed using a Thermo Scientific™ with Al Kα (λ = 0.834 nm) X-rays generated at 15 kV and 70 W. C 1 s assigned at 284.6 eV was used to calibrate the binding energy.
Electrochemical characterizations were conducted in an argon-filled glovebox (H2O < 1 ppm, O2 < 1 ppm) with a home-built potentiostat/galvanostat (Dobbelaere et al., 2017) connected to a three-electrode set (Figure 3A). The thin-films deposited on the Si-20 nm SiO2-40 nm TiN substrates were used as the electrodes for electrochemical tests. Lithium ribbon (99.9%, Sigma-Aldrich) was used as counter and reference electrode, and 1 M LiClO4 in propylene carbonate (PC, 99%, io-li-tec) was used as Li+ electrolyte. The CV was measured at a scan rate of 1 mV s−1 from 0.1–3.0 V (vs. Li/Li+). The EIS was conducted at the frequency from 100 KHz to 10 mHz m = ρ × V = ρ × s × t was used to calculate the mass (m) of active materials, where the contact area (s) is 1.05 cm2, while the density (ρ) and the thickness (t) were obtained from XRR results.
Results and Discussions
Atomic Layer Deposition Growth and Characterizations of Thin-Films
Three thin-film materials were prepared, i.e., SnO2 intermixed with TiO2, Fe2O3 and ZnO respectively, at a ratio of 1:1, labeled as SnO2–TiO2, SnO2–Fe2O3, and SnO2–ZnO. The ALD process sequence was 120 × (SnO2 + 2TiO2) for SnO2–TiO2, 120 × (SnO2 + 4Fe2O3) for SnO2–Fe2O3, and 80 × (2SnO2 + 3ZnO) for SnO2–ZnO. Figure 1B displays the thickness as a function of supercycle number from in-situ SE, and the results show that the thickness is 27.3, 25.6 and 31.1 nm for 120 cycles of SnO2–TiO2, 120 cycles of SnO2–Fe2O3 and 80 cycles of SnO2-ZnO, respectively. Figure 1C shows the recorded XRR curves of the three thin-films where no fundamental differences can be found in the thickness profile. All samples exhibit clear Kiessig fringes, which is indicating a smooth surface. The simulation results indicate thicknesses of 28, 25 and 30 nm which are in line with the in-situ SE result, roughness of 0.62, 0.97 and 0.51 nm, and densities of 5.2, 5.6 and 5.9 g cm−3 for the SnO2–TiO2, SnO2–Fe2O3 and SnO2–ZnO thin-films respectively. The surface morphologies were obtained from AFM in tapping mode. The corresponding three-dimensional surface morphologies of the as-deposited composite thin-films are shown in Figures 1D–F. The surface topography of all three thin-films were found to be smooth, homogeneous with uniform grains. The root mean square (RMS) roughness values are 0.89, 1.10 and 0.65 nm obtained for SnO2–TiO2, SnO2–Fe2O3 and SnO2–ZnO thin-film, respectively, which are well in agreement with the XRR results. Table 2 summarizes the thickness, density, and roughness values obtained from the in-situ SE and XRR data fittings.

TABLE 2. The thickness, density, roughness and XPS composition of SnO2–TiO2, SnO2–Fe2O3, and SnO2–ZnO composite thin-films by ALD.
The XRD patterns of the composite thin-films and binary oxide reference thin-films are shown in Figure 2A. All the patterns clearly reveal (although with the existence of Si background) the amorphous structure except for the ZnO reference film which shows diffractions of (002) and (101) indicating a polycrystalline wurtzite structure (PDF card No. 01-074-9940). In order to evaluate the chemical composition and gain insight into the chemical bonding environment of the composite thin-films, XPS was employed. The full survey spectra presented in Figure 2B show the peaks of Sn, Ti, Fe, Zn and O elements, while no other impurities are observed. The calculated atomic concentration values indicate a nearly 1:1 atomic ratio between SnO2 and MOx in the SnO2–MOx composite thin-films, as shown in Table 2. From the XPS depth profiles in Figure 2C, the Ti content in SnO2–TiO2, Fe content in SnO2–Fe2O3 and Zn content in SnO2–ZnO are almost unchanged throughout the respective thin-film, indicating there is no bilayer or laminate structure and uniform mixing between SnO2 and MOx has been achieved. The binding energy of the Ti 2p1/2 and Ti 2p3/2 peaks for SnO2–TiO2 are centered at 465.5 and 459.7 eV, as displayed in Figure 2D, where the splitting between Ti 2p1/2 and Ti 2p3/2 was 5.8 eV indicating the presence of Ti4+ (Li et al., 2015a). In Figure 2E, Fe 2p3/2 and Fe 2p1/2 are centered at 710.3 and 723.5 eV demonstrating the trivalent state of iron present in SnO2–Fe2O3 thin-films (Gu et al., 2017). Figure 2F shows peaks aligned at 1020.8 and 1043.9 eV which corresponding to the Zn 2p3/2 and Zn 2p1/2 of Zn2+ (Zhao et al., 2019). Based on the above results, it can be summarized that 25–30 nm thick, uniform, smooth and atomically intermixed SnO2–TiO2, SnO2–Fe2O3 and SnO2–ZnO composite thin-films were grown successfully with an atomic ratio of SnO2/MOx at ∼1:1.
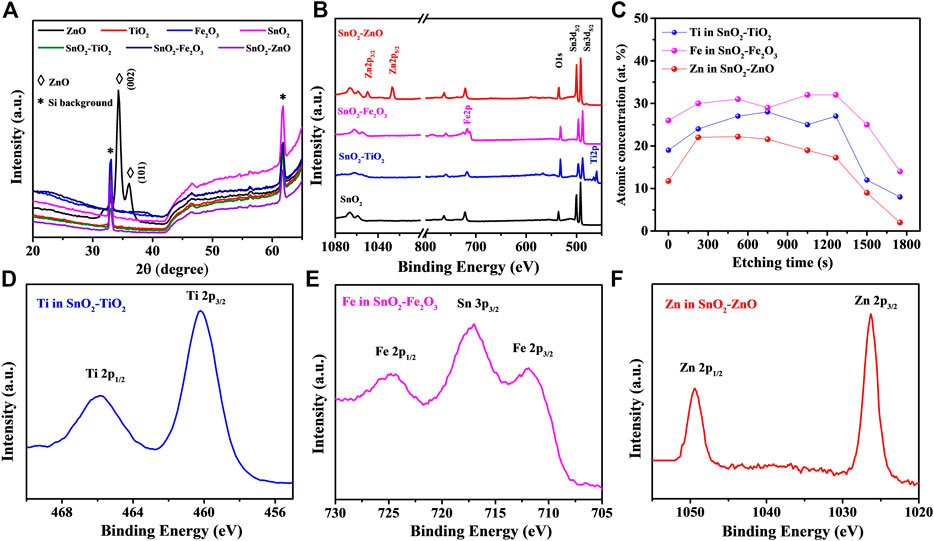
FIGURE 2. (A) XRD patterns of SnO2–MOx composite and MOx reference. XPS spectra of SnO2–MOx: (B) survey scans, (C) atomic concentration (at%) depth profiles and high-resolution scan of (D) Ti 2p in SnO2–TiO2, (E) Fe 2p in SnO2–Fe2O3 and (F) Zn 2p in SnO2–ZnO.
Electrochemical Characterization of SnO2
To evaluate the synergistic effect between SnO2 and MOx, the electrochemical studies of a pure SnO2 thin-film was performed as a reference. Figure 3B shows the initial three cycle CV curves where five distinct cathodic peaks can be observed during lithiation and three anodic peaks during delithiation. In the early stage of lithiation from 1.5 to 0.8 V, multiple reactions lead to the formation of intermediate Li2SnO3 and metallic Sn phases (corresponding to Eqs 1 and 2). Further lithiation to the range between 0.6 and 0.4 V results in another intermediate Li8SnO6 and metallic Sn phases (Eqs 3 and 4). At the potential of ∼0.25 V, the accumulated metallic Sn alloyed to LixSn phases (Eq. 5). Above 1.5 V, Sn is partially re-oxidized to SnOx, and then repeats in the following cycle. Two intermediate phases, Li2SnO3 and Li8SnO6, were detected during lithiation of the thin-film SnO2 electrode. These results match very well with the reported SnO2 thin-film model electrodes (Ferraresi et al., 2018).
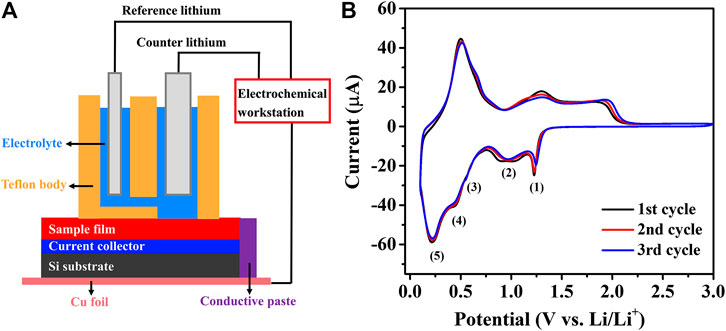
FIGURE 3. (A) The configuration of battery evaluation setup used in this research. (B) Initial three cycle CV curves of ALD SnO2 thin-film electrode.
It is worth mentioning that the reaction mechanisms of SnO2 with Li+ usually differ between the thin-film based electrodes and the slurry-based conventional electrodes. This is mainly because of the existence of conductive additives and binders in the latter (Wen et al., 2007; He et al., 2013; Jahel et al., 2014; Xie et al., 2015). Conventional SnO2 slurry electrodes exhibit two obvious cathodic peaks around 0.87 and 1.18 V, attributed to the Li2O formation and electrolyte decomposition, and other redox peaks appear at 0.15 and 0.56 V are linked to the multistep LixSn formation. The multistep conversion and alloying mechanism of the SnO2 thin-film electrode makes it obtain a theoretical capacity of 1,491 mAh g−1, in which 711 mAh g−1 comes from the irreversible conversion reaction and 783 mAh g−1 from the reversible alloying step. The evolution of SnO2 thin-films during lithiation can be summarized as follows (Kim et al., 2014; Ferraresi et al., 2018):
Synergistic Effect Between SnO2 and TiO2
To unveil the influence of TiO2 anode material, which belongs to intercalation-type in its bulk form, intermixed into the SnO2 matrix on the lithiation/delithiation process, the electrochemical performance of SnO2–TiO2 composite thin-films were investigated. Figure 4A shows the CV curves of a pure TiO2 reference thin-film in the initial three cycles where redox pair peaks assigned at 1.6 and 2.2 V corresponding to the Li+ insertion and extraction into or from TiO2 (Eq. 6). The overlap of the CV curves show the excellent Ti+4/Ti+(4−x) reversibility during the charge-discharge process (Ban et al., 2013).
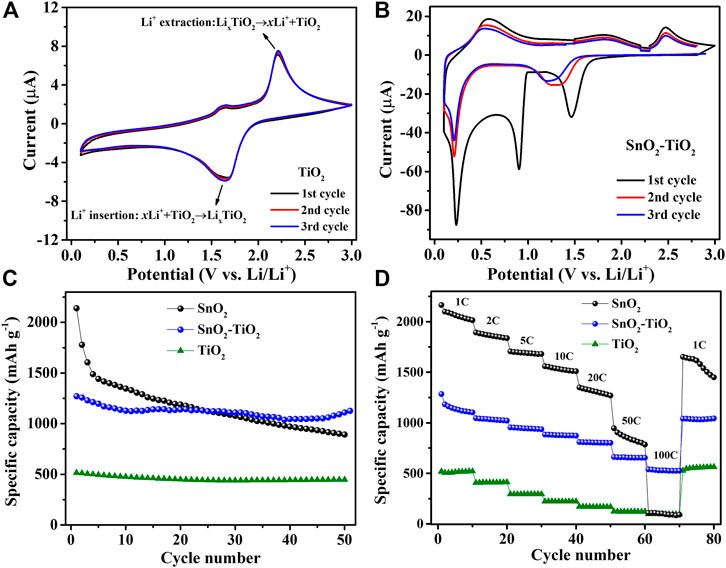
FIGURE 4. CV curves of (A) TiO2 and (B) SnO2–TiO2 composite electrodes. The comparison of SnO2, TiO2 and SnO2–TiO2 composite electrode: (C) cycling performance at 1C and (D) rate performance from 1 to 100 C.
Figure 4B displays the CV curves of the SnO2–TiO2 composite thin-film electrodes. In the first cathodic sweep, the first sharp peak around 1.6 V can be assigned to the lithium insertion into TiO2. The huge peak around 0.9 V is probably related to the reductive transformation of SnO2 to Sn/SnO (corresponding to Eqs 1–3). At very low potential, the peak located at 0.2 V is believed due to the formation of LixSn alloys (Eq. 5). During the anodic process, the broad peaks centered around 0.6 and 1.7 V correspond to the multi-step dealloying reactions from LixSn to Sn followed by oxidation of Sn to SnOx, respectively. Furthermore, the anodic peak at 2.45 V is most likely linked to the Li+ extraction from LixTiO2. Notably, both sharp cathodic peaks around 0.9 and 1.6 V disappeared from the second cycle and a new broad peak appeared at around 1.3 V instead. The broad peak possibly resulted from the combination of LixTiO2 and LiySnO2 formation. Those differences between SnO2 and SnO2–TiO2 suggest the obvious influence of TiO2 intermixing with SnO2, which would certainly affect the cycling performance. As expected, in Figure 4C the SnO2 reference electrode displayed an initial capacity as high as 2,260 mAh g−1, but it continuously and rapidly declined to 879 mAh g−1 after 50 cycles. On the other hand, the TiO2 reference thin-film electrode delivered an initial capacity of 516 and 468 mAh g−1 after 50 cycles, exhibiting a capacity retention of 90.7%, which reflects the advantages of its cycling stability due to the insertion/extraction reaction mechanism. For the SnO2–TiO2 composite electrode, the first discharge capacity is 1,270 mAh g−1, followed by capacity fading during the initial cycles, yielding a capacity of 1,177 mAh g−1 that remained stable until the 50th cycle almost without any decay. In addition, in terms of rate performance (Figure 4D), as expected, the SnO2 electrode showed worst capacity retention followed by SnO2–TiO2 and TiO2. There is an obvious synergistic effect between SnO2 and TiO2, as the incorporation of TiO2 avoids the dramatic capacity fading observed for the SnO2 reference, while the presence of SnO2 in the intermixed layer enhanced the capacity with respect to the TiO2 reference (Chen et al., 2018b).
Synergistic Effect Between SnO2 and Fe2O3
In the next attempt, we investigated the effects of atomically intermixing conversion-type Fe2O3 into a SnO2 matrix. The CV curves of a pure Fe2O3 reference thin-film electrode are presented in Figure 5A. During the first lithiation process, three cathodic peaks are observed at 1.62, 0.98 and 0.76 V, respectively, corresponding to the following three lithiation steps (Wang et al., 2017):
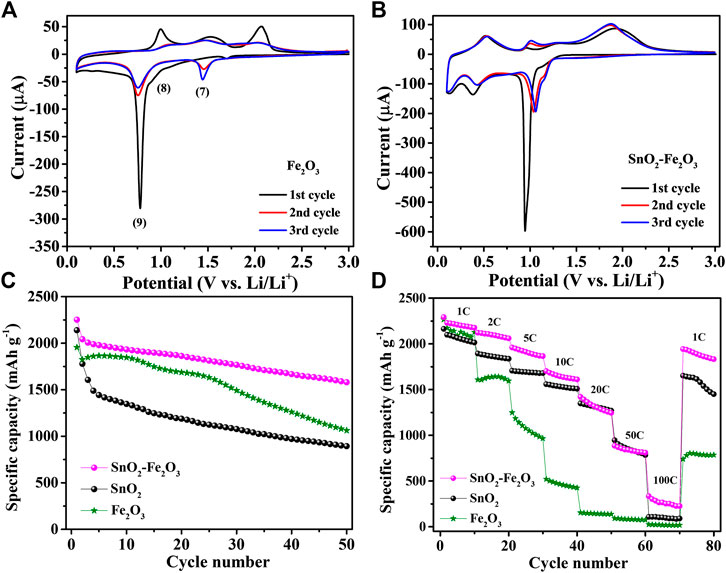
FIGURE 5. CV curves of (A) conversion-type Fe2O3 and (B) SnO2–Fe2O3 composite electrodes. The comparison of SnO2, Fe2O3 and SnO2–Fe2O3 electrode: (C) cycling performance at 1 C and (D) rate performance from 1 to 100 C.
At the initial stage of lithiation at 1.62 V, a small amount of lithium can react with Fe2O3 to form LixFe2O3 (Eq. 7). With further lithiation to 0.98 V, LixFe2O3 transformed to Li2Fe2O3 (Eq. 8). At around 0.76 V, the sharp and intense peak corresponds to the complete conversion to metallic Fe (Eq. 9). In the anodic polarization process, several broad overlapping peaks are observed corresponding to the progressing oxidation of metallic Fe to Fe2+ and further to Fe3+. Figure 5B shows the CV behavior of the SnO2–Fe2O3 composite thin-film electrode, which is closely analogous to a combination of the CV behaviors of pure Fe2O3 (Figure 5A) and pure SnO2 (Figure 3B). In the first cycle, there are three reduction peaks at 1.15, 0.93 and 0.31 V, and three oxidation peaks at 0.46, 1.05, and 1.97 V, respectively. The rather weak reaction peak at 1.15 V is assigned to the refoundation of LixFe2O3 and further reaction to Li2Fe2O3 (Eqs 7 and 8). The sharp reduction peak around 0.93 V is attributed to the coinciding reduction reactions of SnO2 to Sn/SnO and Fe2+ to Fe, and the formation of Li2O. The peak at 0.31 V ascribes to the formation of a series of LixSn alloys. The delithiation reactions can be described by the following: the oxidation peaks at 0.46 and 1.05 V during the initial charge process can be attributed to the multi-step conversion of the LixSn alloy to Sn, the oxidation peak at 1.97 V can be attributed to the oxidation of Fe to Fe3+ (Li et al., 2015b). From the cycling performance, we can see that the SnO2–Fe2O3 composite thin-film electrode achieves a discharge capacity of 1,580 mAh g−1, while pure Fe2O3 shows a discharge capacity of 1,062 mAh g−1 after 50 cycles at 1 C (Figure 5C). The composite electrode holds 70.2% of the initial capacity after 50 cycles outperforming both the pure SnO2 (38.9%) and Fe2O3 (54.3%) electrode. Figure 5D shows the further investigations of rate capabilities of all three electrodes. Among all, the pure Fe2O3 has the worst rate capability, while for the SnO2–Fe2O3 composite electrode, although the specific capacity gradually decreases with the increase in current density, the capacity is always maintained higher than both SnO2 and Fe2O3 at every delivered rate from 1 to 100 C, especially significantly superior to Fe2O3. The obtained capacity from the SnO2–Fe2O3 composite electrode is significantly higher than that of the pure SnO2 or Fe2O3 reference electrode.
Synergistic Effect Between SnO2 and ZnO
ZnO is known for exhibiting an alloying-type reaction mechanism towards lithium. Hence, ZnO-incorporated SnO2 composite thin-films were prepared subsequently to explore the synergistic effect of two atomically intermixed anode materials with similar alloying-based mechanism. Figure 6A shows CV curves of pure ZnO thin-film electrode. The peak at 0.6 V in the first cathodic sweep aligned to the reduction of ZnO to Zn (Eq. 10), and the peaks at 0.4 and 0.12 V correspond to the multi-phase formation of LixZn alloys (Eq. 11). In the anodic sweep, several small peaks at 0.3, 0.47 and 0.61 V can be linked to the multi-dealloying steps from LixZn to Zn, the peak at 1.4 V is most probably due to the re-oxidation of Zn (Lu et al., 2017; Zhao et al., 2019).
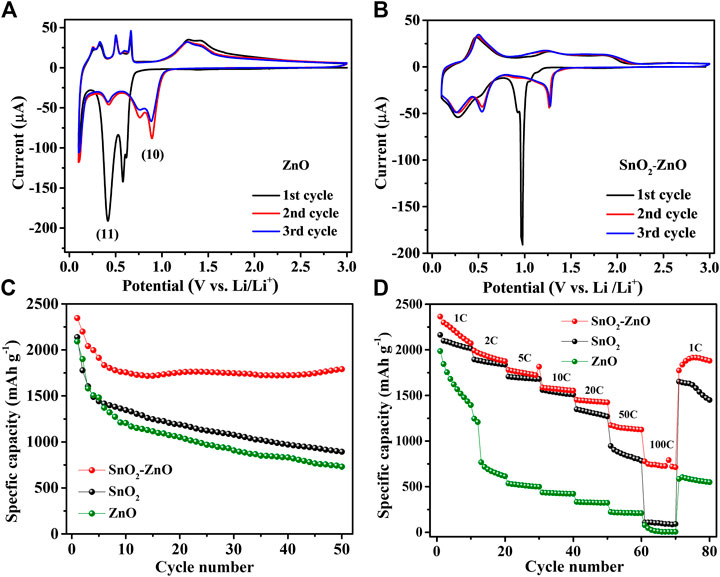
FIGURE 6. CV curves of (A) alloying-type ZnO and (B) SnO2–ZnO composite electrodes. The comparison of SnO2, ZnO and SnO2–ZnO composite electrode: (C) cycling performance at 1 C and (D) rate performance from 1 to 100 C.
The CV curves of the SnO2–ZnO composite thin-film electrode are shown in Figure 6B. During the first cathodic scan, a sharp reduction peak around 0.98 V is observed which could be explained as the combination of the reduction of SnO2 and ZnO to Sn and Zn, respectively. The peaks at 0.55 and 0.22 V probably correspond to the formations of LixSn and LixZn, respectively. During the first anodic scan, a peak at 0.54 V and a broad peak around 1.12 V are clearly distinguishable which could be attributed to multi-step dealloying reactions. The other two peaks at higher voltages (1.30 and ∼2 V) are probably due to stepwise re-oxidation from Sn to SnOx and Zn to ZnO. As observed in the cycling performance in Figure 6C, both the pure ZnO and SnO2 thin-film electrodes suffer from significant capacity decay. However, the SnO2–ZnO composite anode delivers a reversible capacity of 1,795 mAh g−1 after 50 cycles and exhibits 75.2% capacity retention with respect to the first cycle, which is much superior than that of 38.9% and 34.9% obtained from pure SnO2 and ZnO respectively. The SnO2–ZnO composite electrodes also exhibit an impressive rate capability. Figure 6D shows the rate capability behavior over 80 cycles from 1 to 100 C. The discharge capacities reach to 2,325, 1,992, 1,847, 1,642, 1,504, 1,209, and 743 mAh g−1 at 1, 2, 5, 10, 20, 50, and 100 C, respectively. Even after cycling at high rate of 100 C the capacity could return to 2,089 mAh g−1 when the current density returned back to 1 C. The SnO2–ZnO composite electrodes offer a higher capacity than that of pure SnO2 and Fe2O3 at every rate condition. Apparently, composite thin-film electrodes not only improve the capacity but also help in achieving improved cycling stability and rate performance.
Discussion on the Lithium Storage Mechanism
Table 3 lists a comparison of the details of capacities, Coulombic efficiencies and retention rates of all the investigated thin-film electrodes (pure references and composites). The charge capacity achieved in all the cases are higher than the theoretical capacity, which is due to the extremely thin films of active materials achieved by ALD (Mattelaer et al., 2015; Kint et al., 2019; Zhao et al., 2019; Li et al., 2020). The composite thin-films (SnO2–TiO2, SnO2–Fe2O3 and SnO2–ZnO) show better electrochemical properties, either higher capacity or better retention rate than their individual counter parts (SnO2 and TiO2, Fe2O3 or ZnO). With the addition of TiO2, although the SnO2 obtained smaller capacity, a significant improvement in cycling stability is observed in SnO2–TiO2 composite thin-film electrode. As for the SnO2–Fe2O3 composite thin-film electrode, both the capacity and stability are moderately improved. In the case of SnO2–ZnO composite thin-film electrode, notably, after few initial cycles of dropping, the capacity stabilizes and after 50 cycles it eventually offers the highest capacity among all the electrodes.
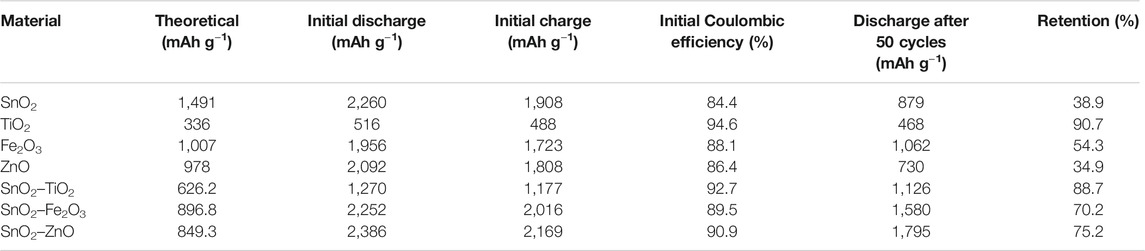
TABLE 3. The theoretical, initial charge-discharge capacity, Coulombic efficiency, the discharge capacity after 50 cycles at 1°C and the retention rate of all the investigated thin-film electrodes.
Figures 7A–D shows the surface morphology of SnO2, SnO2–TiO2, SnO2–Fe2O3 and SnO2–ZnO electrode before and after cycling (after 50 charging-discharging cycles at 1 C). Before cycling, the as-prepared films are uniform and smooth with low roughness (as confirmed by AFM in Figures1D–F). After cycling, all the investigated films became much rougher, but in general, the morphology changes of the composite electrodes are less than that of pure SnO2 reference. The SnO2 electrode surface with large amounts of needle-like dendrites formed a porous structure after cycling which demonstrated the distortion by the lithiation and delithiation process. The SnO2–TiO2 surface kept relative smooth compared with others, indicating that there are mild volume changes when charged/discharged. While for the SnO2–Fe2O3 and SnO2–ZnO composite electrode, many islands surrounded by cracks are formed on the surface. The situation for SnO2–Fe2O3 is worse than for SnO2–ZnO. EIS before and after cycling was also conducted to gain further insight into the composite electrodes. As shown in Figure 7E, by comparing the size of the arcs, the diameters of the semicircles greatly increased after cycling, indicating an increase of the charge-transfer resistance. SnO2–TiO2, SnO2–Fe2O3 and SnO2–ZnO composite electrodes increased less than pure SnO2, suggesting that the composite electrodes improved the electronic conductivity and among the composites SnO2–ZnO is the most remarkable. Based on the results of morphology and EIS before and after cycling, we proposed a schematic diagram, as shown in Figure7F, to explain the lithium storage mechanism. In the SnO2–TiO2 composite thin-film electrodes, there is no conversion reaction or alloying reaction between TiO2 and lithium. The (Lix)TiO2 may act as a stable membrane during charge-discharge processes regardless of the drastic volume change of LixSn, possibly causing the enhanced cyclability. For the SnO2–Fe2O3 thin-film electrode, the addition of an extra conversion component Fe2O3, not only provides new Li+ hosts but also increases the conductivity of the electrode by introducing metallic Fe from the conversion reaction between lithium and Fe2O3 after full discharge. For the SnO2–ZnO composite thin-film electrode, the improved performance can be attributed to the combined advantages of large capacity of SnO2 and ZnO. The obvious synergistic effect between ZnO and SnO2 is that during discharging process, SnO2 reacts with Li at a higher potential (∼0.76 V) than ZnO (∼0.61 V), forming metallic Sn nanograins surrounding ZnO particles before they get lithiated, which may help to suppress the ZnO volume expansion and in return preventing the Sn nanograins from aggregation in the following lithiation of ZnO. In this way, the capacity fading of SnO2–ZnO composite can be relieved and cycling life can be extended.
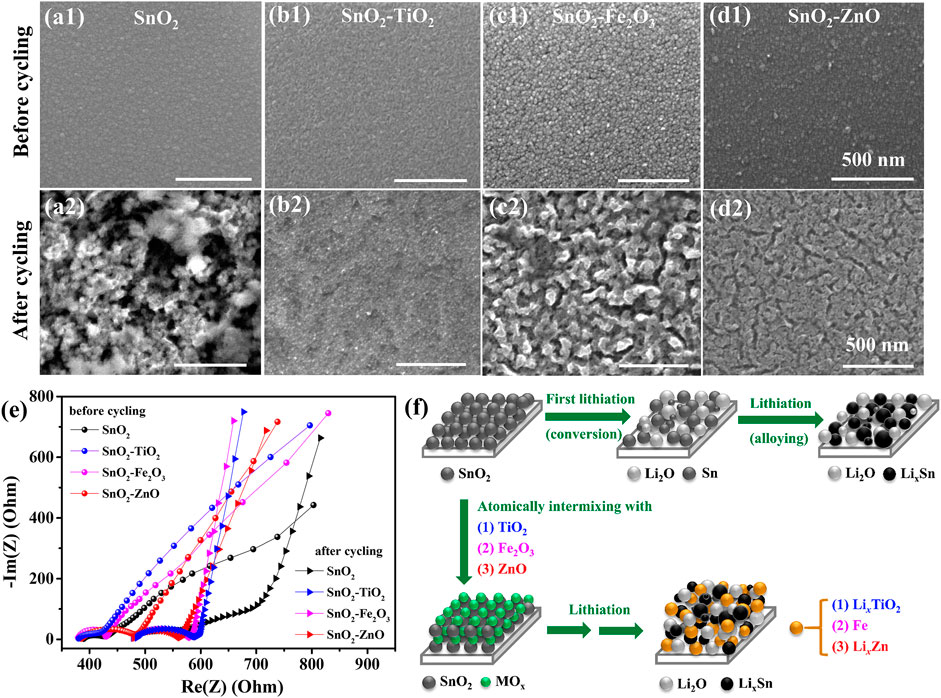
FIGURE 7. SEM images of the morphology before and after cycling for the (A1,A2) SnO2, (B1,B2) SnO2–TiO2, (C1,C2) SnO2–Fe2O3 and (D1,D2) SnO2–ZnO electrode. (E) EIS of the electrodes before and after cycling. (F) Schematic illustration of SnO2 and the effect of atomically intermixing SnO2 with MOx on the lithiation mechanism.
Conclusions
We have exploited the benefits of ALD to fabricate uniform, smooth and well atomically intermixed SnO2–TiO2, SnO2–Fe2O3 and SnO2–ZnO composite thin-film model electrodes to evaluate their electrochemical performance as anode materials for LIBs. Cycling stability discloses the effect of synergy on battery capacity performance. All the composite thin-films (SnO2–TiO2, SnO2–Fe2O3 and SnO2–ZnO) show better electrochemical properties, either higher capacity, better retention or improved rate capability as compared to the individual components (SnO2, TiO2, Fe2O3 and ZnO). With the addition of TiO2, the composite thin-films achieve lower overall capacity but obtain excellent cyclability. With incorporation of Fe2O3 in the composite thin-films, both the capacity and retention are improved, but both have moderate effect. With regards to the addition of ZnO, the composite thin-films can be stabilized at higher capacity than the bare components after a capacity drop in the few initial cycles. The SnO2–ZnO composite thin-film electrodes eventually obtain the best comprehensive performance amongst the tested materials. This work reports a systematic study of the synergistic effects between two different types of metal oxide and can hopefully provide a useful guidance for the development of better composite anode materials for thin-film rechargeable batteries.
Data Availability Statement
The original contributions presented in the study are included in the article/Supplementary Material, further inquiries can be directed to the corresponding author.
Author Contributions
CD conceived the original idea and supervised the writing. BZ did all the experiments and data analysis, plotted the figures, wrote the original draft. AD and JD revised the manuscript.
Funding
The authors acknowledge FWO-Vlaanderen (Nos. GO87418N and 1S68518N), and BOF-UGent (Nos. 01G01513 and 01G01019) for financial support.
Conflict of Interest
The authors declare that the research was conducted in the absence of any commercial or financial relationships that could be construed as a potential conflict of interest.
Acknowledgments
The authors also acknowledge Dr. Matthias Minjauw for assistance with the XPS measurements and analysis, and thank Olivier Janssens for SEM measurements.
References
Ban, C. M., Xie, M., Sun, X., Travis, J. J., Wang, G. K., Sun, H. T., et al. (2013). Atomic layer deposition of amorphous TiO2 on graphene as an anode for Li-ion batteries. Nanotechnology 24 (42), 424002. doi:10.1088/0957-4484/24/42/424002
Bruck, A. M., Cama, C. A., Gannett, C. N., Marschilok, A. C., Takeuchi, E. S., and Takeuchi, K. J. (2016). Nanocrystalline iron oxide based electroactive materials in lithium ion batteries: the critical role of crystallite size, morphology, and electrode heterostructure on battery relevant electrochemistry. Inorg. Chem. Front. 3 (1), 26–40. doi:10.1039/c5qi00247h
Chen, J. S., and Lou, X. W. (2013). SnO2-based nanomaterials: synthesis and application in lithium-ion batteries. Small 9 (11), 1877–1893. doi:10.1002/smll.201202601
Chen, D., Lou, Z., Jiang, K., and Shen, G. Z. (2018a). Device configurations and future prospects of flexible/stretchable lithium-ion batteries. Adv. Funct. Mater. 28 (51), 1805596. doi:10.1002/adfm.201805596
Chen, X. F., Huang, Y., Zhang, K. C., Feng, X. S., and Wang, M. Y. (2018b). Porous TiO2 nanobelts coated with mixed transition-metal oxides Sn3O4 nanosheets core-shell composites as high-performance anode materials of lithium ion batteries. Electrochim. Acta 259, 131–142. doi:10.1016/j.electacta.2017.10.180
Cheong, J. Y., Kim, C., Jung, J. W., Yoon, K. R., and Kim, I. D. (2018). Porous SnO2-CuO nanotubes for highly reversible lithium storage. J. Power Sources 373, 11–19. doi:10.1016/j.jpowsour.2017.10.090
Dendooven, J., Deduytsche, D., Musschoot, J., Vanmeirhaeghe, R. L., and Detavernier, C. (2010). Conformality of Al2O3 and AlN deposited by plasma-enhanced atomic layer deposition. J. Electrochem. Soc. 157 (4), G111–G116. doi:10.1149/1.3301664
Deng, S., Kurttepeli, M., Cott, D. J., Bals, S., and Detavernier, C. (2015). Porous nanostructured metal oxides synthesized through atomic layer deposition on a carbonaceous template followed by calcination. J. Mater. Chem. A 3 (6), 2642–2649. doi:10.1039/C4TA05165C
Dobbelaere, T., Vereecken, P. M., and Detavernier, C. (2017). A USB-controlled potentiostat/galvanostat for thin-film battery characterization. HardwareX 2, 34–49. doi:10.1016/j.ohx.2017.08.001
Fang, R. P., Chen, K., Yin, L. C., Sun, Z. H., Li, F., and Cheng, H. M. (2019). The regulating role of carbon nanotubes and graphene in lithium-ion and lithium-sulfur batteries. Adv. Mater. 31 (9), 1800863. doi:10.1002/adma.201800863
Fang, S., Bresser, D., and Passerini, S. (2020). Transition metal oxide anodes for electrochemical energy storage in lithium‐and sodium‐ion batteries. Adv. Energy Mater. 10 (1), 1902485. doi:10.1002/aenm.201902485
Ferraresi, G., Villevieille, C., Czekaj, I., Horisberger, M., Novak, P., and El Kazzi, M. (2018). SnO2 model electrode cycled in Li-ion battery reveals the formation of Li2SnO3 and Li8SnO6 phases through conversion reactions. ACS Appl. Mater. Interfaces 10 (10), 8712–8720. doi:10.1021/acsami.7b19481
Gu, Y., Jiao, Z., Wu, M. H., Luo, B., Lei, Y., Wang, Y., et al. (2017). Construction of point-line-plane (0-1-2 dimensional) Fe2O3-SnO2/graphene hybrids as the anodes with excellent lithium storage capability. Nano Res. 10 (1), 121–133. doi:10.1007/s12274-016-1271-y
Ha, D. H., Islam, M. A., and Robinson, R. D. (2012). Binder-free and carbon-free nanoparticle batteries: a method for nanoparticle electrodes without polymeric binders or carbon black. Nano Lett. 12 (10), 5122–5130. doi:10.1021/nl3019559
He, M., Yuan, L. X., Hu, X. L., Zhang, W. X., Shu, J., and Huang, Y. H. (2013). A SnO2@carbon nanocluster anode material with superior cyclability and rate capability for lithium-ion batteries. Nanoscale 5 (8), 3298–3305. doi:10.1039/c3nr34133j
Jahel, A., Ghimbeu, C. M., Monconduit, L., and Vix-Guterl, C. (2014). Confined ultrasmall SnO2 particles in micro/mesoporous carbon as an extremely long cycle-life anode material for Li-ion batteries. Adv. Energy Mater. 4 (11), 1400025. doi:10.1002/aenm.201400025
Kim, D. W., Hwang, I. S., Kwon, S. J., Kang, H. Y., Park, K. S., Choi, Y. J., et al. (2007). Highly conductive coaxial SnO2-In2O3 heterostructured nanowires for li ion battery electrodes. Nano Lett. 7 (10), 3041–3045. doi:10.1021/nl0715037
Kim, H., Park, G. O., Kim, Y., Muhammad, S., Yoo, J., Balasubramanian, M., et al. (2014). New insight into the reaction mechanism for exceptional capacity of ordered mesoporous SnO2 electrodes via synchrotron-based X-ray analysis. Chem. Mater. 26 (22), 6361–6370. doi:10.1021/cm5025603
Kim, T., Song, W. T., Son, D. Y., Ono, L. K., and Qi, Y. B. (2019). Lithium-ion batteries: outlook on present, future, and hybridized technologies. J. Mater. Chem. A 7 (7), 2942–2964. doi:10.1039/c8ta10513h
Kint, J., Mattelaer, F., Minjauw, M., Zhao, B., and Detavernier, C. (2019). Atomic layer deposition of thin films as model electrodes: a case study of the synergistic effect in Fe2O3-SnO2. J. Vac. Sci. Technol. A 37 (5), 050904. doi:10.1116/1.5115987
Li, Q., Li, H., Xia, Q., Hu, Z., Zhu, Y., Yan, S., et al. (2020). Extra storage capacity in transition metal oxide lithium-ion batteries revealed by in situ magnetometry. Nat. Mater. doi:10.1038/s41563-020-0756-y
Li, S., Ling, M., Qiu, J. X., Han, J. S., and Zhang, S. Q. (2015a). Anchoring ultra-fine TiO2-SnO2 solid solution particles onto graphene by one-pot ball-milling for long-life lithium-ion batteries. J. Mater. Chem. A 3 (18), 9700–9706. doi:10.1039/c5ta01350j
Li, Y., Yu, S. L., Yuan, T. Z., Yan, M., and Jiang, Y. Z. (2015b). Rational design of metal oxide nanocomposite anodes for advanced lithium ion batteries. J. Power Sources 282, 1–8. doi:10.1016/j.jpowsour.2015.02.016
Liu, D. Q., Liu, Z. J., Li, X. W., Xie, W. H., Wang, Q., Liu, Q. M., et al. (2017). Group IVA element (Si, Ge, Sn)-Based alloying/dealloying anodes as negative electrodes for full-cell lithium-ion batteries. Small 13 (45), 1702000. doi:10.1002/smll.201702000
Lu, S. T., Wang, H. H., Zhou, J., Wu, X. H., and Qin, W. (2017). Atomic layer deposition of ZnO on carbon black as nanostructured anode materials for high-performance lithium-ion batteries. Nanoscale 9 (3), 1184–1192. doi:10.1039/c6nr07868k
Lu, Y., Yu, Y., and Lou, X. W. (2018). Nanostructured conversion-type anode materials for advanced lithium-ion batteries. Chem 4 (5), 972–996. doi:10.1016/j.chempr.2018.01.003
Mattelaer, F., Vereecken, P. M., Dendooven, J., and Detavernier, C. (2015). Deposition of MnO anode and MnO2 cathode thin films by plasma enhanced atomic layer deposition using the Mn(thd)3 precursor. Chem. Mater. 27 (10), 3628–3635. doi:10.1021/acs.chemmater.5b00255
Musschoot, J., Xie, Q., Deduytsche, D., Van den Berghe, S., Van Meirhaeghe, R. L., and Detavernier, C. (2009). Atomic layer deposition of titanium nitride from TDMAT precursor. Microelectron. Eng. 86 (1), 72–77. doi:10.1016/j.mee.2008.09.036
Pender, J. P., Jha, G., Youn, D. H., Ziegler, J. M., Andoni, I., Choi, E. J., et al. (2020). Electrode degradation in lithium-ion batteries. ACS Nano 14 (2), 1243–1295. doi:10.1021/acsnano.9b04365
Qi, W., Shapter, J. G., Wu, Q., Yin, T., Gao, G., and Cui, D. X. (2017). Nanostructured anode materials for lithium-ion batteries: principle, recent progress and future perspectives. J. Mater. Chem. A 5 (37), 19521–19540. doi:10.1039/c7ta05283a
Ramachandran, R. K., Dendooven, J., and Detavernier, C. (2014). Plasma enhanced atomic layer deposition of Fe2O3 thin films. J. Mater. Chem. A 2 (27), 10662–10667. doi:10.1039/c4ta01486c
Reddy, M. V., Rao, G. V. S., and Chowdari, B. V. R. (2013). Metal oxides and oxysalts as anode materials for Li ion batteries. Chem. Rev. 113 (7), 5364–5457. doi:10.1021/cr3001884
Roselin, L. S., Juang, R. S., Hsieh, C. T., Sagadevan, S., Umar, A., Selvin, R., et al. (2019). Recent advances and perspectives of carbon-based nanostructures as anode materials for Li-ion batteries. Materials 12 (8), 1229. doi:10.3390/ma12081229
Su, X., Wu, Q. L., Li, J. C., Xiao, X. C., Lott, A., Lu, W. Q., et al. (2014). Silicon-based nanomaterials for lithium-ion batteries: a review. Adv. Energy Mater. 4 (1), 1300882. doi:10.1002/aenm.201300882
Wadewitz, D., Gruner, W., Herklotz, M., Klose, M., Giebeler, L., Voss, A., et al. (2013). Investigation of copper-cobalt-oxides as model systems for composite interactions in conversion-type electrodes for lithium-ion batteries. J. Electrochem. Soc. 160 (8), A1333–A1339. doi:10.1149/2.014309jes
Wang, Y. Z., Han, J. S., Gu, X. X., Dimitrijev, S., Hou, Y. L., and Zhang, S. Q. (2017). Ultrathin Fe2O3 nanoflakes using smart chemical stripping for high performance lithium storage. J. Mater. Chem. A 5 (35), 18737–18743. doi:10.1039/c7ta05798a
Wei, W., Wang, Z., Liu, Z., Liu, Y., He, L., Chen, D., et al. (2013). Metal oxide hollow nanostructures: fabrication and Li storage performance. J. Power Sources 238, 376–387. doi:10.1016/j.jpowsour.2013.03.173
Wen, Z. H., Wang, Q., Zhang, Q., and Li, J. H. (2007). In situ growth of mesoporous SnO2 on multiwalled carbon nanotubes: a novel composite with porous-tube structure as anode for lithium batteries. Adv. Funct. Mater. 17 (15), 2772–2778. doi:10.1002/adfm.200600739
Wu, F. F., Bai, J., Feng, J. K., and Xiong, S. L. (2015). Porous mixed metal oxides: design, formation mechanism, and application in lithium-ion batteries. Nanoscale 7 (41), 17211–17230. doi:10.1039/c5nr04791a
Xie, M., Sun, X., George, S. M., Zhou, C. G., Lian, J., and Zhou, Y. (2015). Amorphous ultrathin SnO2 films by atomic layer deposition on graphene network as highly stable anodes for lithium-ion batteries. ACS Appl. Mater. Interfaces 7 (50), 27735–27742. doi:10.1021/acsami.5b08719
Xie, Q., Jiang, Y. L., Detavernier, C., Deduytsche, D., Van Meirhaeghe, R. L., Ru, G. P., et al. (2007). Atomic layer deposition of TiO2 from tetrakis-dimethyl-amido titanium or Ti isopropoxide precursors and H2O. J. Appl. Phys. 102 (8), 083521. doi:10.1063/1.2798384
Yan, X. D., Wang, Z. H., He, M., Hou, Z. H., Xia, T., Liu, G., et al. (2015). TiO2 nanomaterials as anode materials for lithium-ion rechargeable batteries. Energy Technol. 3 (8), 801–814. doi:10.1002/ente.201500039
Yi, Z., Han, Q. G., Zan, P., Cheng, Y., Wu, Y. M., and Wang, L. M. (2016). Facile fabrication of SnO2@TiO2 core-shell structures as anode materials for lithium-ion batteries. J. Mater. Chem. A 4 (33), 12850–12857. doi:10.1039/c6ta03915d
Yuan, T., Tan, Z. P., Ma, C. R., Yang, J. H., Ma, Z. F., and Zheng, S. Y. (2017). Challenges of spinel Li4Ti5O12 for lithium-ion battery industrial applications. Adv. Energy Mater. 7 (12), 1601625. doi:10.1002/aenm.201601625
Zhang, W. J. (2011). Lithium insertion/extraction mechanism in alloy anodes for lithium-ion batteries. J. Power Sources 196 (3), 877–885. doi:10.1016/j.jpowsour.2010.08.114
Zhao, B., Huang, S. Y., Wang, T., Zhang, K., Yuen, M. M. F., Xu, J. B., et al. (2015a). Hollow SnO2@Co3O4 core-shell spheres encapsulated in three-dimensional graphene foams for high performance supercapacitors and lithium-ion batteries. J. Power Sources 298, 83–91. doi:10.1016/j.jpowsour.2015.08.043
Zhao, Q. Q., Ma, L. S., Zhang, Q., Wang, C. G., and Xu, X. J. (2015b). SnO2-based nanomaterials: synthesis and application in lithium-ion batteries and supercapacitors. J. Nanomater. 2015, 850147. doi:10.1155/2015/850147
Zhao, Y., Li, X. F., Yan, B., Xiong, D. B., Li, D. J., Lawes, S., et al. (2016). Recent developments and understanding of novel mixed transition-metal oxides as anodes in lithium ion batteries. Adv. Energy Mater. 6 (8), 1502175. doi:10.1002/aenm.201502175
Zhao, B., Mattelaer, F., Kint, J., Werbrouck, A., Henderick, L., Minjauw, M., et al. (2019). Atomic layer deposition of ZnO–SnO2 composite thin film: the influence of structure, composition and crystallinity on lithium-ion battery performance. Electrochim. Acta 320, 134604. doi:10.1016/j.electacta.2019.134604
Zheng, M. B., Tang, H., Li, L. L., Hu, Q., Zhang, L., Xue, H. G., et al. (2018). Hierarchically nanostructured transition metal oxides for lithium-ion batteries. Adv. Sci. 5 (3), 1700592. doi:10.1002/advs.201700592
Zhu, G. N., Wang, Y. G., and Xia, Y. Y. (2012). Ti-based compounds as anode materials for Li-ion batteries. Energy Environ. Sci. 5 (5), 6652–6667. doi:10.1039/c2ee03410g
Keywords: atomic layer deposition, synergistic effect, intercalation, conversion, alloying, thin-film, SnO2, lithium-ion battery
Citation: Zhao B, Dhara A, Dendooven J and Detavernier C (2020) Atomic Layer Deposition of SnO2-Based Composite Anodes for Thin-Film Lithium-Ion Batteries. Front. Energy Res. 8:609417. doi: 10.3389/fenrg.2020.609417
Received: 23 September 2020; Accepted: 16 November 2020;
Published: 11 December 2020.
Edited by:
Xiangbo Meng, University of Arkansas, United StatesCopyright © 2020 Zhao, Dhara, Dendooven and Detavernier. This is an open-access article distributed under the terms of the Creative Commons Attribution License (CC BY). The use, distribution or reproduction in other forums is permitted, provided the original author(s) and the copyright owner(s) are credited and that the original publication in this journal is cited, in accordance with accepted academic practice. No use, distribution or reproduction is permitted which does not comply with these terms.
*Correspondence: Christophe Detavernier, Y2hyaXN0b3BoZS5kZXRhdmVybmllckB1Z2VudC5iZQ==