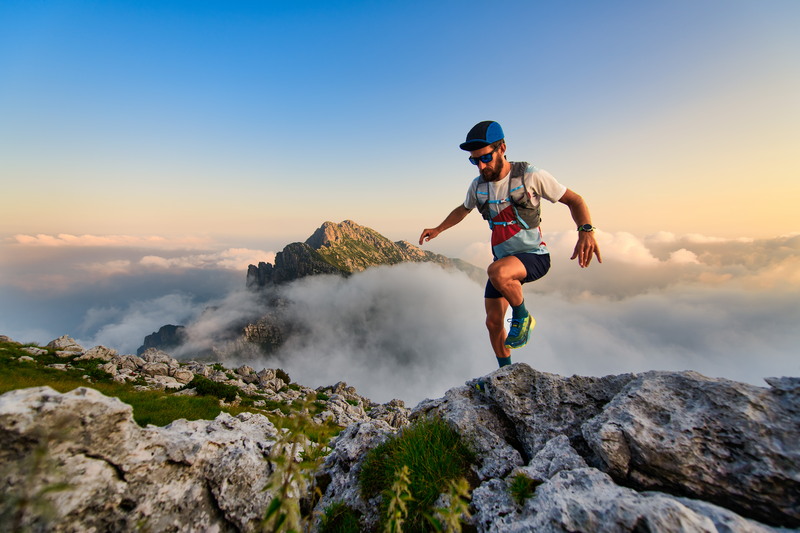
94% of researchers rate our articles as excellent or good
Learn more about the work of our research integrity team to safeguard the quality of each article we publish.
Find out more
ORIGINAL RESEARCH article
Front. Energy Res. , 02 February 2021
Sec. Bioenergy and Biofuels
Volume 8 - 2020 | https://doi.org/10.3389/fenrg.2020.608756
This article is part of the Research Topic Emerging Technologies for Waste Biomass to Energy: Innovations and Research Challenges View all 8 articles
Agricultural residues have been traditionally used as energy resources for many years. In light of current environmental and fossil fuel supplies for energy applications, agricultural residues are regarded as sustainable supplies for energy production. However, the suitability to be renewable fuel and as a co-fuel in coal combustion facilities has to be investigated. A thermal analysis was conducted to investigate the effect of the blending and heating rate of the thermal behavior of Malaysian bituminous coal (Silantek), oil palm biomass (empty fruit bunch), and their blends using thermogravimetric analysis. The investigation was done in an inert atmosphere at the heating rate of 10, 20, and 40°C/min. Characteristics including proximate, ultimate, and calorific analyses were also examined. Six different mass ratios were selected from both samples to study the effect of blending of the two materials. The results showed that thermal degradation of empty fruit bunch (EFB) occurred in three stages while Silantek coal (SC) only involved two regions due to their different fuel properties. The blending of both SC/EFB did not follow their individual samples, which showed non-additive behavior suggesting that there is an interaction between coal and biomass. The outcome of this research provides insight on the behavior of Malaysian bituminous coal and oil palm biomass, which enhances knowledge for the future of energy generation.
Concerns over the environment associated with emissions due to the use of fossil fuels as a main energy resource has been the main agenda in most countries around the world. The combustion of fossil fuels has contributed to the emission of greenhouse gases such as carbon dioxide. From 2010 to 2017, the combustion of fossil fuels has released carbon dioxide emission of about 4,188.5 million tonnes recorded in Asia alone, but the amount is increasing in 2018 due to an increase in energy demand, in line with the robust economy growth plus (IEA, 2020). The emissions have caused global warming and are indirectly increasing the need of either heating or cooling requirements globally. Currently, natural gas is the main energy source for power production in Malaysia. In 2018, about 73,352 GW Wh of the electricity generation from the total of 168,897 G Wh energy produced was fueled by coal followed by natural gas (Energy Commission, 2019). However, the depletion of petroleum energy reserves over the years has called for the industry to increase the share of coal in the total energy mix for power production. Alternative solutions to replace fossil fuels have been sought after to ensure a reduction in emission, particularly in electricity generation. This situation has led the Malaysian government to introduce the use of other energy resources to meet the increasing energy demand.
Agricultural wastes are essentially a biomass resource that has the ability to be used as fuel, as its components consist of carbon, hydrogen, and oxygen, coming from the major biomass components of hemicellulose, cellulose, and lignin. The combustion of biomass has been promoted because of the net zero carbon dioxide emission due to biomass’s ability to consume carbon dioxide during its growth, while releasing carbon dioxide during combustion. Its utilization is able to reduce fossil fuel consumption because of higher fuel flexibility, higher combustion efficiency, higher heat transfer and other environmental benefits (Vuthaluru, 2004; Jayaraman et al., 2017).
From a Malaysian perspective, the tropical climate conditions that prevail around the year are favorable for oil palm plantation. This has led the country to become one of the major palm oil producers in the world (Norhidayu, et al., 2017). The palm oil milling process allows an extraction of palm oil from fresh fruit bunches. However, the processes have contributed to production of solid residues. With an increment of the residues of 5.6% from 2016 to 2017, dry solid residues (biomass) are expected to reach 85–110 million dry tonnes by 2020 (Chow, 2008; Agensi Inovasi Malaysia, 2013). It is estimated that, by the year 2020, about 8 million tonnes of empty fruit bunches (EFB) will have been produced and the amount is increasing with an increase in oil palm production every year (Agensi Inovasi Malaysia, 2013). According to Hasanuzzaman et al. (2014), based on 10 million ton/year of dry EFB, approximately 700 MW of electricity will be generated. It is predicted that the amount of EFB generated to date is sufficient to be used for electricity generation. Traditionally, empty fruit bunches have been sent to plantations for mulching, and mostly left unattended since they contain high moisture, in comparison to the palm kernel shell and palm mesocarp fiber, which are used as fuel for boilers. However, application of single biomass for energy production may lead to several problems such as low heating value, high moisture content, excess smoke during combustion and low energy density (Tumuluru et al., 2011). High ash content in these biomass materials causes major problems in a boiler furnace, as it causes slagging hence reducing heat transfer efficiency and requires frequent maintenance (Saidur et al., 2011). Nevertheless, with proper pre-treatment, and available conversion technology, such limitations can be overcome.
Much research has emerged on the co-utilization of biomass with coal for power production, which is advantageous with respect to cost, sustainability, and reduced release of CO2, SOx, and often NOx emissions (Sahu et al., 2014). Coal is available at different ranks namely, anthracite, bituminous, sub-bituminous, and lignite; whereby bituminous coal is the most widely used for the thermal industry (Grammelis et al., 2016). Although much research has been reported on the importance of the co-firing of coal and biomass, limited work has proved the synergistic effect between the utilization of raw biomass and coal. Synergistic effect between the two fuels is important as it indicates interaction between the components in both of the fuels. As coal and biomass are distinct in their properties, it is important to understand the behavior of their co-utilization, prior to commercial application during combustion.
Previously, Silantek coal’s utilization has been performed by Matali et al. (2016). However, in this work, the investigation focuses on single utilization rather than co-utilization with raw and torrefied biomass (Leucaena Leucocephala and oil palm frond). Jamaluddin et al. (2011) reported the co-combustion of the palm kernel shell (PKS) and its produced char from themicrowave pyrolysis technique. It was reported that there was a lack of synergistic effect during co-combustion of Silantek coal with PKS. Nevertheless, a synergistic effect was reported when the coal was co-combusted with PKS char. Thus far, limited work has been reported on using empty fruit bunch (EFB) with Silantek coal. Therefore, the aim of the current work is to investigate the thermal behavior of Malaysian bituminous coal which is Silantek coal blended with EFB by varying the heating rate and blending ratio. The significance of this work is that it provides an insight into the suitability of utilizing agriculture residue such as oil palm residue along with a high rank coal for a thermal application, which in turn could reduce the impact on the environment as a result of the waste disposal and combustion of fossil fuel (coal).
Empty fruit bunch (EFB) was collected from Malaysia Palm Oil Board (MPOB), Palm Mill Technology, located in Labu, Negeri Sembilan, Malaysia and Silantek coal (SC) used in this study was originated from Silantek, Sarawak. Both coal and biomass were air dried for 2–3 days to remove moisture. The samples were ground and sieved to a size of <212 µm and further dried in a vacuum oven at 105°C for 24 h to remove excess moisture before being stored in screw-capped bottle. For chemical characteristics, proximate analyses of SC and EFB were done based on the standard method of ASTM D 5142–02a using a thermogravimetric analyzer model TGA/SDTA51e (Mettler Toledo, United States) (ASTM 5142–02a). As for ultimate analysis, data on percentage of nitrogen, carbon, hydrogen, and sulfur were obtained using a Thermo Finnigan Flashed 1,112 analyzer which followed ASTM 5373–02 (ASTM D5373–02). For calorific data, both SC and EFB was analyzed using a bomb calorimeter model IKAWORKS calorimeter System C500 Control. The methodology is summarized in a process flow as in Figure 1. The result of the characterization of the raw sample is presented in Table 1.
Thermal analyses of SC, EFB, and their blends were evaluated by a thermogravimetric analyzer TGA/SDRA51e (Mettler Toledo, United States). TGA provides simultaneous thermogravimetric (TG) and derivative thermogravimetric (DTG) data of raw and blending sample. In this experiment, approximately 20 mg of sample was placed in 150 µL alumina crucible and heated under nitrogen atmosphere of flowrate 50 ml/min, at temperatures from 25 to 900°C. All samples were heated at three different heating rates which were 10, 20, and 40°C/min. To study the effect of blending, biomass and coal were blended, at five different weight ratios which were 0:100, 20:80, 50:50, 80:20, and 100:0. Each pyrolysis was run at least twice, but more repetitions were carried out in case some inconsistencies were observed.
Synergistic investigation between SC and EFB was analyzed using a summation of the weighted average of the two fuels present in the blends given by Eq. 1 (Vuthaluru, 2004; Vamvuka et al., 2003; Xie et al., 2018; Merdun and Laougé, 2021):
where xSC and xEFB are mass fractions of SC coal and EFB in the blend, respectively and WSC and WEFB are normalized weight loss of SC and EFB, respectively, which were obtained from individual experiment data under the same process conditions.
In a similar manner, the same equation is applied on the thermogram as shown on Eq. 2
where xSC and xEFB are mass fractions of SC coal and EFB in the blend, respectively and TGSC and TGEFB are thermogram curve of pure SC and EFB, respectively, which were obtained from individual experiment data under the same process conditions.
Generally, coal and biomass characteristics differ widely due to their individual characteristics. From Table 1, it can be observed that Silantek coal (SC) contains high fixed carbon (FC), low volatile matter (VM), unlike EFB which has high VM and low fixed carbon. As for elemental characteristics, SC has a carbon content of 74.7%, while EFB only contained 42.7% of carbon. Accordingly, the calorific value of SC was observed to be almost double that of EFB. In terms of thermal behavior, Figure 2 shows thermograms (TG) and derivative thermograms (DTG) for both individual samples of SC and EFB at a heating rate of 10°C/min. Thermal activity on a thermogram can be observed based on changes in the gradient. The changes are depicted as peaks on a derivative thermogram (DTG). It can be observed that the thermal degradation of EFB occurred in three different stages where the first stage was due to the moisture drying process followed by main devolatilization and end with a slight devolatilization process. During the moisture removal region, EFB experienced a loss of excessive moisture from 25°C to 109°C. The devolatilization stage started at a temperature range of 131°C up to 478°C. A shoulder peak at around 200°C prior to the main peak (at peak temperature 320°C) indicates the degradation of hemicellulose, while the main peak was attributed to the decomposition of cellulose (Carrier et al., 2011). The proceeding non-observable peak (curve) at about 360°C–500°C can be regarded due to degradation of lignin. This finding was evident by a work reported by Wu et al. (2014). The last stage also involved the charring of the remaining solid char of the EFB until the end of the pyrolysis (Toptas et al., 2015; Wang et al., 2017). A similar study of EFB done by Omar et al. (2011) also reported the same thermal degradation profile which consists of the moisture drying region, cellulose and hemicellulose decomposition, and lastly lignin decomposition. As for the SC, the degradation only involved two major stages where the first stage corresponds to moisture removal, followed by volatile matter released at much a higher temperature as compared to that of EFB. Similar findings were also reported by other researchers on the pyrolysis of bituminous coal (Othman and Boosroh, 2009; Vhathvarothai et al., 2014).
FIGURE 2. (A) TG curves and (B) DTG curve for Silantek coal and EFB material at heating rate of 10°C/min.
From the DTG curve, reactivity of both SC and EFB can be determined based on maximum peak temperature and peak height. Reactivity is important as it indicates how reactive the fuel is or vice versa (Miranda et al., 2008). It appears that the peak temperature of EFB is lower than SC at 320°C with the peak height of 1.73 mg/min indicating that EFB is more reactive than SC. Similar findings from other researchers on comparison of biomass and coal reactivity were observed (Kastanaki et al., 2002; Omar et al., 2011; Jayaraman et al., 2017). This is because EFB contains more volatile matter than that of SC, thus reducing the reactivity of SC. The two fuels have distinct properties; hence it is important to understand the behavior during co-utilization.
Pyrolysis parameters such as temperature, residence time, and heating rate are among the important factors that affect yield and desired product quality (de Jong et al., 2007). Figure 3 shows trends of pyrolysis of EFB and SC at three different heating rates of 10, 20, and 40°C/min. It can be observed that derivative curves show similar profiles as heating rate increases for both samples. Parameters of initial, peak, and final temperatures during pyrolysis of EFB at different heating rates are shown in Table 2. Initial reaction temperatures of EFB at a heating rate of 10, 20, and 40°C/min are 131.31, 164.75, and 189.24°C, respectively. It is observed that the peak temperature increases with increasing heating rate. Corresponding peak temperatures for heating rates at 10, 20, and 40°C/min are 318.28, 331.29, and 335.31°C, respectively.
FIGURE 3. DTG profiles of (A) EFB and (B) Silantek coal (SC) at heating rates of 10, 20, and 40°C/min under pyrolysis condition.
TABLE 2. The characteristic temperatures of EFB and SC pyrolysis at heating rate of 10, 20, and 40°C/min.
Final reaction temperature for a heating rate of 10°C/min is lower as compared to a heating rate of 20 and 40°C/min. Temperature shifts as heating rate is increased can be explained by ineffective heat transfer when fast heating rates was applied. In heating the same sample mass, with higher heating rates, heat transfer inside inner portion and particle of biomass is reduced, hence more time is needed to achieve the same heating, which can be achieved at a later time, hence at a much higher temperature (El-Sayed and Khairy, 2015). This data agrees reasonably well with the work carried out by other researchers on effect of heating rate on thermal degradation of EFB in inert atmosphere (Mohammed et al., 2013; Idris et al., 2010). However, it can be observed that, for SC, characteristic temperatures (Ti, Tp and Tf) were not affected as much as that of biomass.
It is important to understand the thermal degradation behavior of the two fuels by performing thermal analysis under inert conditions. Thermal degradation of EFB blended with SC at ratio of 100:0, 80:20, 50:50, 20:80, and 0:100 is shown in Figure 4. Three decomposition profiles are observed for SC/EFB blends where the first peak (TEP 1) appears at a temperature below 150°C, second peak (TEP 2) between temperatures of 274 and 400°C, and third peak (TEP 3) is between 434 and 566°C. The first peak can be associated with water removal from both samples, while the second peak indicates the devolatilization of biomass and the last were assigned to decomposition of SC. As can be seen, both samples followed the same thermal evolution profile as their parent fuel. Maximum rate of devolatilization (also known as peak height) gradually increases with an increasing amount of biomass in the blends due to high volatile quantities released (Idris et al., 2010; Vamvuka et al., 2003; Panwar et al., 2020)). This also shows improved reactivity of the sample where biomass increment will increase the maximum rate of mass loss (Jayaraman et al., 2017). Moreover, the position of the maximum peak was shifted to a lower temperature as the biomass percentage increased, while the peak temperature was also found to be at a lower temperature as compared to SC. From Table 1, char yield of SC and EFB is 76.47% and 34.01%, respectively. This indicates the remaining solid particles in the main body mass upon devolatilization. Apparently, the char yield of the blends decreases with increasing biomass. This can be seen on the TG curve of the EFB:SC at the mixture of 20:80, 50:50, and 80:20 where the final residues are 55.35%, 45.85%, and 33.9%, respectively. The main reason for this finding is because of the differences in the coal and biomass chemical structures. Coal is known to have a strong C=C bond energy structure of 1,000 kJ/mol that makes it difficult to rupture under thermal treatment as compared to a weak energy bond of 380–420 kJ/mol for biomass. Thus, it is easier for the biomass to decompose when subjected to heating (Quan & Gao, 2016). Similar findings have also been reported by Vuthaluru (2004) on pyrolysis of wood waste and wheat straw, He et al. (2018) on co-pyrolysis of bituminous coal and fermented cornstalk, and (Panwar et al., 2020) on co-pyrolysis of raw/torrefied biomass and coal blends, and (Quan et al., 2014) on white pine and bituminous coal using thermogravimetric analysis.
The synergistic interaction between the SC and EFB can be observed from the additive or non-additive behavior based on the sum of weighted average of the mass loss profile, as indicated in Eq. 1 (Vamvuka et al., 2003; Merdun and Laougé, 2021; Xie et al., 2018). An equation was applied on the char yield of the blends as shown in Figure 5. The trend line represents data as calculated by using Eq. 1, while experimental data were represented by the data points. It appears that the char yield profile does not show an additive behavior as the data point for the experimental result lies away from the summation of weighted average line (trendline). Such a behavior is indicative of synergistic effect between fuels in the blend. Similar observation was reported by Quan et al. (2014) on the co-pyrolysis of white pine with bituminous coal using TGA. It was reported that the interaction exists due to the formation of volatiles and residues of biomass that took place at a much lower temperature than that of coal, and could easily be deposited on the coal surface. At a low heating rate, there is a longer release time of volatiles from both materials, hence allowing secondary reaction of intraparticle volatiles.
FIGURE 4. EFB blended with SC at ratio of 100:0, 80:20, 50:50, 20:80, and 0:100 under pyrolysis condition at heating rate of 10°C/min.
Using Eq. 2, an additional plot was made for calculated and experimental thermograms (TG) of the blends as shown in Figure 6 (Xie et al., 2018). It appears that the calculated data are not able to represent the experimental data by a simple weighted average, indicating the existence of interaction between the fuels (Vuthaluru, 2004; Quan and Gao, 2016). It is also observed at the beginning of the process up to 300°C, the experimental data for the blends appear to be much lower than that of the parent fuels. This is also evidence of the synergistic effect of the two fuels. This could be due to lignocellulosic materials being primarily transformed into laevoglucose with the breakdown of glycosidic bonds, which can provide a hydrogenous donor for bituminous coal pyrolysis (Wu et al., 2014). Interaction between coal and biomass during co-pyrolysis, although uncommon, has been reported by some researchers involving different ranks of coal and various types of biomass (Haykiri-Acma and Yaman, 2008; Aboyade et al., 2013; Xie et al., 2018)). Similar work performed but on different coal by Idris et al. (2010), however, showed the additive behavior when Mukah Balingian coal (lower rank coal) and EFB were co-utilized during pyrolysis.
It has been demonstrated that, synergistic effect exists for the two fuels during co-pyrolysis. Its application for co-combustion is much influenced by the understanding of both behaviors in this condition i.e., in the absence of oxidative gas. Ideally, the best ratio could be selected so as to overcome limitations of both fuels during combustion. It is already highlighted that biomass has high volatile matter and low characteristic temperature, meaning its reactivity is high as compared to coal which has a high initial temperature. A high char yield would translate into a char combustion phase at a much higher temperature and longer duration could be maintained and is desirable (Sotannde et al., 2010; Jamaluddin et al., 2011; Matali et al., 2016; Abdullah et al., 2019) Thus it can be said that the blend of 50% coal and biomass, has an ignition temperature of about 172°C, intermediate reactivity, with a long reaction time. Nevertheless, further combustion analysis of the co-blend materials shall be carried out in our future research.
As a conclusion, thermal decomposition of Silantik Coal (SC), Empty Fruit Bunches (EFB), and their blends under inert conditions has been determined using a thermogravimetric analysis technique. Degradation of EFB occurred at a lower temperature compared to SC and reactivity of the EFB is higher than SC. Heating rate has an effect on the thermal behavior of the fuel causing temperature shifts to higher temperatures as the heating rate increases. Blended fuels showed a degree of interactions during co-pyrolysis, observed from the sum of the weighted average of the thermograms. The interactions between the biomass and coal are of paramount importance with the hope to further reduce NOx or SOx during combustion, hence sustaining the environment. Outcomes from this work provide an insight and prompts further research into reducing utilization of coal by increasing the share of biomass materials as fuel toward obtaining energy for the benefit of future generations.
The original contributions presented in the study are included in the article, further inquiries can be directed to the corresponding author.
NH: Writing-Original Draft, methodology, data curation SI: Corresponding author, supervision, conceptualization, grant acquisition and administration, review and editing NA: Review and editing SM: Data curation NA: Supervision, review and editing.
FRGS research grant (600-RMI/FRGS 5/3 (127/2015)) from Ministry of Education Malaysia.
The authors declare that the research was conducted in the absence of any commercial or financial relationships that could be construed as a potential conflict of interest.
The authors are grateful for the FRGS research grant (600-RMI/FRGS 5/3 (127/2015)) from Ministry of Education Malaysia and also facilities and constant encouragement provided by Faculty of Chemical Engineering, University Teknologi MARA.
Abdullah, N., Town, G., and Zangina, T. (2019). A comparative study on the heat release during the combustion of coal and oil palm biomass charcoal briquette via thermogravimetric analysis. Int. J. Biomass Renew. 8 (2), 1–8.
Aboyade, A. O., Görgens, J. F., Carrier, M., Meyer, E. L., and Knoetze, J. H. (2013). Thermogravimetric study of the pyrolysis characteristics and kinetics of coal blends with corn and sugarcane residues. Fuel Process. Technol. 106, 310–320. doi:10.1016/j.fuproc.2012.08.014
Agensi Inovasi Malaysia (2013). National biomass strategy 2020. New Wealth Creation for Malaysia’s Goverment Agency Report Biomass Industry, 34.
ASTM D5142-02a (2002). Standard test methods for proximate analysis of the analysis sample of coal and coke by instrumental procedures. West Conshohocken, PA: ASTM International, 5.
ASTM D5373-02 (2002). Standard test methods for instrumental determination of carbon, hydrogen, and nitrogen in laboratory samples of coal and coke. West Conshohocken, PA: ASTM International, 5.
Carrier, M., Loppinet-Serani, A., Denux, D., Lasnier, J. M., Ham-Pichavant, F., Cansell, F., et al. (2011). Thermogravimetric analysis as a new method to determine the lignocellulosic composition of biomass. Biomass Bioenergy. 35 (1), 298–307. doi:10.1016/j.biombioe.2010.08.067
Chow, M. C., Wahid, M. B., and Chan, K. W. (2008). Availability and potential of biomass resources from the Malaysian palm oil industry for generating renewable energy. Oil Palm Bull 56, 23–28.
de Jong, W., Di Nola, G., VennekerSpliethoff, B. C. H. H., and Wójtowicz, M. A. (2007). TG-FTIR pyrolysis of coal and secondary biomass fuels: determination of pyrolysis kinetic parameters for main species and NOx precursors. Fuel 86 (15), 2367–2376. doi:10.1016/j.fuel.2007.01.032
El-Sayed, S. A., and Khairy, M. (2015). Effect of heating rate on the chemical kinetics of different biomass pyrolysis materials. Biofuels 6, 157–170. doi:10.1080/17597269.2015.1065590
Energy Comission (2019). Malaysia energy statistic handbook. Available at: http://www.seda.gov.my/ (Accessed 01 03 2019).
Grammelis, P., Margaritis, N., and Karampinis, E. (2016). Solid Fuel Types for Energy Generation: Coal and Fossil Carbon-Derivative Solid Fuels. Elsevier Ltd doi:10.1016/B978-1-78242-378-2.00002-X
Hasanuzzaman, M., Farhad Hossain, M., and Abd. Rahim, N. (2014). Palm oil EFB: green energy source in Malaysia. Appl. Mech. Mater 619, 376–380. doi:10.4028/www.scientific.net/AMM.619.376
Haykiri-Acma, H., and Yaman, S. (2008). Effect of co-combustion on the burnout of lignite/biomass blends: a Turkish case study. Waste Manag 28, 2077–8410. doi:1016/j.wasman.2007.08.028
He, Y., Chang, C., Li, P., Han, X., Li, H., Fang, S., et al. (2018). Thermal decomposition and kinetics of coal and fermented cornstalk using thermogravimetric analysis. Bioresour. Technol 259, 294–303. doi:10.1016/j.biortech.2018.03.043
Idris, S. S., Abd Rahman, N., Ismail, K., Alias, A. B., Abd Rashid, Z., and Aris, M. J. (2010). Investigation on thermochemical behaviour of low rank Malaysian coal, oil palm biomass and their blends during pyrolysis via thermogravimetric analysis (TGA). Bioresour. Technol 101 (12), 4584–4592. doi:10.1016/j.biortech.2010.01.059
Jamaluddin, M. A., Ismail, K., Ghani, Z. A., Ishak, M. A. M., Idris, S. S., Abdullah, M. F., et al. (2011). Thermogravimetric analysis of Silantek coal, palm kernel shell, palm kernel shell char and their blends during combustion. 3rd international symposium and exhibition in sustainable energy and environment (ISESEE), Melaka, Malaysia, June 1–3, 2011 (IEEE), 48–50.
Jayaraman, K., Kok, M. V., and Gokalp, I. (2017). Thermogravimetric and mass spectrometric (TG-MS) analysis and kinetics of coal-biomass blends: IEEE Xplore. Renew. Energy 101, 293–300. doi:10.1016/j.renene.2016.08.072
Kastanaki, E., Vamvuka, D., Grammelis, P., and Kakaras, E. (2002). Thermogravimetric studies of the behavior of lignite–biomass blends during devolatilization. Fuel Process. Technol 77–78, 159–166. doi:10.1016/S0378-3820(02)00049-8
Matali, S., Rahman, A. N., Idris, S. S., and Yaacob, N. (2016). Combustion properties, water absorption and grindability of raw/torrefied biomass pellets and Silantek coal. AIP Conf. Proc 1901, 100005. doi:10.1063/1.5010527
Merdun, H., and Laougé, Z. B. (2021). Kinetic and thermodynamic analyses during co-pyrolysis of greenhouse wastes and coal by TGA. Renew. Energy 163, 453–464. doi:10.1016/j.renene.2020.08.120
Miranda, T., Esteban, A., Rojas, S., Montero, I., and Ruiz, A. (2008). Combustion analysis of different olive residues. Int. J. Mol. Sci 9, 512–525. doi:10.3390/ijms9040512
Mohamed, A. R., Hamzah, Z., Daud, M. Z. M., and Zakaria, Z. (2013). The effects of holding time and the sweeping nitrogen gas flowrates on the pyrolysis of efb using a fixed–bed reactor. Procedia Eng. 53, 185–191. doi:10.1016/j.proeng.2013.02.024
Norhidayu, A., Nursyazwani, M., Radzil, R. H. M., and Amin, I. Z. M. (2017). The production of crude palm oil in Malaysia. Int. J. Econ. Manage 11 (S3), 591–606.
Omar, R., Idris, A., Yunus, R., Khalid, K., and Aida Isma, M. I. (2011). Characterization of empty fruit bunch for microwave-assisted pyrolysis. Fuel 90 (4), 1536–1544. doi:10.1016/j.fuel.2011.01.023
Othman, N. F., and Boosroh, M. H. (2009). Pyrolysis study of Sarawak coal using thermogravimetric analysis. Int. Energy J 10, 195–200.
Panwar, N. L., Gajera, B., Jain, S., and Salvi, B. L. (2020). Thermogravimetric studies on co-pyrolysis of raw/torrefied biomass and coal blends. Waste Manag. Res 38 (11), 1259–1268. doi:10.1177/0734242X19896624
Quan, C., and Gao, N. (2016). Copyrolysis of biomass and coal: a review of effects of copyrolysis parameters, product properties, and synergistic mechanisms. BioMed Res. Int, 2016, 6197867. doi:10.1155/2016/6197867
Quan, C., Xu, S., An, Y., and Liu, X. (2014). Co-pyrolysis of biomass and coal blend by TG and in a free fall reactor. J. Therm. Anal. Calorim 117 (2), 817–823. doi:10.1007/s10973-014-3774-7
Sahu, S. G., Chakraborty, N., and Sarkar, P. (2014). Coal–biomass co-combustion: an overview. Renew. Sustain. Energy Rev 39, 575–586. doi:10.1016/j.rser.2014.07.106
Saidur, R., Abdelaziz, E. A., Demirbas, A., Hossain, M. S., and Mekhilef, S. (2011). A review on biomass as a fuel for boilers. Renew. Sustain. Energy Rev 15 (5), 2262–2289. doi:10.1016/j.rser.2011.02.015
Sotannde, O. A. a., Oluyege, A. O. b., and Abah, G. B. a. (2010). Physical and combustion properties of charcoal briquettes from neem wood residues. Int. Agrophys. 24 (August), 189–194.
Toptas, A., Yildirim, Y., Duman, G., and Yanik, J. (2015). Combustion behavior of different kinds of torrefied biomass and their blends with lignite. Bioresour. Technol. 177, 328–336. doi:10.1016/j.biortech.2014.11.072
Tumuluru, J. S., Wright, C. T., Hess, J. R., and Kenney, K. L. (2011). A review of biomass densification systems to develop uniform feedstock commodities for bioenergy application. Biofuels, Bioprod. Bioref. 5, 683–707. doi:10.1002/bbb.324
Vamvuka, D., Kakaras, E., Kastanaki, E., and Grammelis, P. (2003). Pyrolysis characteristics and kinetics of biomass residuals mixtures with lignite. Fuel 82, (15–17), 1949–1960. doi:10.1016/s0016-2361(03)00153-4
Vhathvarothai, N., Ness, J., and Yu, J. (2014). An investigation of thermal behaviour of biomass and coal during co‐combustion using thermogravimetric analysis (TGA). Int. J. Energy Res. 38, 804–812. doi:10.1002/er.3083
Vuthaluru, H. B. (2004). Thermal behaviour of coal/biomass blends during co-pyrolysis. Fuel Process. Technol. 85 (2–3), 141–155. doi:10.1016/s0378-3820(03)00112–7
Wang, S., Dai, G., Yang, H., and Luo, Z. (2017). Lignocellulosic biomass pyrolysis mechanism: a state-of-the-art review. Prog. Energy Combust. Sci. 62, 33–86. doi:10.1016/j.pecs.2017.05.004
Wu, Z., Wang, S., Zhao, J., Chen, L., and Meng, H. (2014). Synergistic effect on thermal behavior during co-pyrolysis of lignocellulosic biomass model components blend with bituminous coal. Bioresour. Technol. 169, 220–228. doi:10.1016/j.biortech.2014.06.105
Xie, W., Wen, S., Liu, J., Xie, W., Kuo, J., Lu, X., et al. (2018). Comparative thermogravimetric analyses of co-combustion of textile dyeing sludge and sugarcane bagasse in carbon dioxide/oxygen and nitrogen/oxygen atmospheres: thermal conversion characteristics, kinetics, and thermodynamics. Bioresour. Technol. 255 (January), 88–95. doi:10.1016/j.biortech.2018.01.110
Keywords: pyrolysis, Silantek coal, empty fruit bunch, thermogravimetric analysis, co-utilization, coal/biomass blends
Citation: Hamzah NS, Idris SS, Rahman NA, Abu Bakar NF and Matali S (2021) Thermal Analysis of Co-Utilization of Empty Fruit Bunch and Silantek Coal Under Inert Atmosphere Using Thermogravimetric Analyzer (TGA). Front. Energy Res. 8:608756. doi: 10.3389/fenrg.2020.608756
Received: 21 September 2020; Accepted: 08 December 2020;
Published: 02 February 2021.
Edited by:
Eldon R. Rene, IHE Delft Institute for Water Education, NetherlandsReviewed by:
Bing Shen How, Swinburne University of Technology Sarawak Campus, MalaysiaCopyright © 2021 Hamzah, Idris, Rahman, Abu Bakar and Matali. This is an open-access article distributed under the terms of the Creative Commons Attribution License (CC BY). The use, distribution or reproduction in other forums is permitted, provided the original author(s) and the copyright owner(s) are credited and that the original publication in this journal is cited, in accordance with accepted academic practice. No use, distribution or reproduction is permitted which does not comply with these terms.
*Correspondence: Siti Shawalliah Idris, c2hhd2FsMDc1QHVpdG0uZWR1Lm15
Disclaimer: All claims expressed in this article are solely those of the authors and do not necessarily represent those of their affiliated organizations, or those of the publisher, the editors and the reviewers. Any product that may be evaluated in this article or claim that may be made by its manufacturer is not guaranteed or endorsed by the publisher.
Research integrity at Frontiers
Learn more about the work of our research integrity team to safeguard the quality of each article we publish.