- 1Technische Universität Braunschweig, Institute for Chemical and Thermal Process Engineering, Braunschweig, Germany
- 2Technische Universität Braunschweig, Institute of Environmental and Sustainable Chemistry, Braunschweig, Germany
- 3Technische Universität Braunschweig, Cluster of Excellence SE2A—Sustainable and Energy-Efficient Aviation, Braunschweig, Germany
Aiming toward a scalable continuous electrochemical production of valeric acid, the mutual insolubility of valeric acid with the aqueous reaction medium of levulinic acid and the aqueous electrolyte are investigated in order to assess the possibility for an integrated product separation based on the liquid–liquid equilibrium of the system. The influence of the electrolyte concentration in the mixture and the mixture temperature on the liquid–liquid equilibrium is studied. Based on these results, the possibility for a batch and a continuous product separation process is developed and discussed.
Introduction
The increasing scarcity of fossil resources and associated climate change force society to shift from fossil-based to renewable energy sources and sustainable raw materials for the production of platform chemicals and fuel components (Corma et al., 2007). Hereby, organic electrosynthesis that is based on the electrochemical conversion of biogenic feedstocks into high-value products and fuels by using renewable electricity represents a promising approach (Frontana-Uribe et al., 2010). A major benefit of electrochemical syntheses results from the compliance with the rules of green chemistry. Corresponding reactions exploit electrons as an immaterial agent, avoiding the use of additional chemicals. Hereby, waste generation is minimized, leading to high atom efficiency. Additionally, electrochemical transformations can be performed at ambient temperature and pressure, avoiding the need of expensive equipment such as pressurized reactors and reducing energy consumption compared to traditional chemical methods. Furthermore, electrochemical reactions can be performed using water as an environmentally friendly solvent, and electrochemical reactors can be operated dynamically, making them an interesting possibility to store electrical energy from fluctuating renewable energy sources (Frontana-Uribe et al., 2010; Schäfer, 2011; Goldmann et al., 2018).
Levulinic acid (LA) is an interesting biomass-based feedstock, which is being produced in high yields from carbohydrates by acid-catalyzed hydrolysis (van de Vyver et al., 2011; Kamm et al., 2012; Teong et al., 2014). The presence of a keto and a carboxyl functionality, and its simple accessibility make LA a versatile chemical. Therefore, LA is considered as one of twelve high-potential biogenic platform chemicals (Werpy and Petersen, 2004; Gallezot, 2012; Kamm et al., 2012; Filiciotto et al., 2018). In the future, LA could be involved in many industrial processes because the conversion of LA enables the fabrication of industrially relevant products such as polymers, solvents, antifreeze agents, biofuels, pharmaceuticals, and herbicides (Leonard, 1956; Kamm et al., 2005; Huber et al., 2006). Besides the diverse traditional uses, LA can also be reduced to valeric acid (VA) via an electrochemical reduction, see Figure 1. By employing indium as an electrode material, it is possible to reach a selectivity for VA of > 99 % (Bisselink et al., 2019).
VA is utilized as a precursor for odor materials and synthetic lubricants or as an intermediate product for the electrocatalytic production of biofuels via Kolbe electrolysis (Nilges et al., 2012; Xin et al., 2013). Despite being first published as early as 1911 by Tafel and Emmert (1911), there is still great interest in the investigation of this reaction to develop novel sustainable industrial products and processes (Xin et al., 2013; Qiu et al., 2014; Isikgor and Becer, 2015; Pileidis and Titirici, 2016; Bisselink et al., 2019).
In our previous work, we examined the electrochemical conversion of LA to VA as a route to regenerative chemicals and fuel components (dos Santos et al., 2015). We determined that an increase of the initial educt concentration not only leads to improved Coulombic efficiency (CE) as well as a higher reaction rate of VA but also enables an elegant product separation due to the lower solubility of the product VA in the aqueous electrolyte than the starting material. This effect of a lower product solubility is applicable for a number of electrochemical reactions and was also shown during the Kolbe coupling of VA to n-octane (Nilges et al., 2012).
The product insolubility opens the door for continuous and easy product removal by liquid–liquid phase separation. Consequently, this could allow for a completely continuous production process of VA, including continuous reaction and product separation. Continuous processes are in general assumed to provide increased process safety and control and ultimately better product quality (Kirschning, 2009; Kirschning, 2011; Movsisyan et al., 2016). Only few studies deal with the product separation of LA and VA. Bisselink et al. and Tafel suggest an extraction of VA; however, introducing additional extraction agents like hexane or ether will require subsequent separation of the latter—adding additional downstream effort (Tafel and Emmert, 1911; Bisselink et al., 2019).
In order to design continuous product separation based on mutual insolubility, this work aims toward the characterization of the ternary liquid–liquid equilibrium (LLE) of the substances involved, namely, LA, VA, and the aqueous electrolyte (EL). In the first section, the influence of electrolyte concentration (sulfuric acid) and temperature on the LLE is examined, while the second part discusses the possibility to develop a continuous production process with integrated phase separation, aiming for high product purity.
Experimental Section
Chemicals
All chemicals used in this study were of analytical grade. For qualitative and quantitative analyses, reference materials and solvents were used as purchased (Sigma Aldrich), without further purification. LA was used in 98% purity, and VA was used in 99% purity.
Liquid–Liquid Equilibrium Measurement
Mixtures of VA, LA, and H2SO4 (0.5, 1, 2, and 4 M in deionized water) of defined composition in the 2-phase region were prepared and equilibrated using a shaking incubator (model 3032, GFL, Gesellschaft für Labortechnik mbH, Burgwedel, Germany) at n = 200 rpm and the desired temperature for at least 12 h. Phases were allowed to settle for at least 1 h before phase separation. The separated organic and aqueous phases were kept in separate vials for at least 1 h at the given temperature before sample preparation for high-performance liquid chromatography (HPLC) analysis. An appropriate volume of the organic and the aqueous phase was weighted to determine the mass of the sample,
where
Mass fractions of the components are defined as
Analysis
Routine substance quantification was obtained by HPLC, with a refractive index detector (Agilent 1260 Infinity II LC system) equipped with a BioRad Aminex HPX 87-H (9 μm, 7.8 mm × 300 mm) column. Sulfuric acid (2.5 mM, flow rate 0.6 ml min−1) served as the eluent. The column was operated at 60°C and the refractory index at 40°C.
Discussion
Liquid–Liquid Equilibrium
In order to evaluate the possibility of an integrated product separation via the formation of a second organic phase, LLE data of the system VA/LA/aqueous H2SO4 (EL) for different H2SO4 concentrations (0.5–4 M) are determined and displayed in Figure 2. As a general trend, the size of the 2-phase region increases with increasing H2SO4 concentration. This might be due to the increase in the H+ concentration in the aqueous phase, which results in a shift of the protonation/deprotonation equilibria of VA and LA toward their neutral, non-dissociated state, reducing their water solubility. Furthermore, the reduced water solubility could be explained by a salting-out effect, in which the VA is displaced from the aqueous phase. This results in a lower organic acid content in the aqueous phase and, therefore, in a broadened 2-phase region. Regarding product separation via LLE, a high EL concentration would therefore be beneficial.
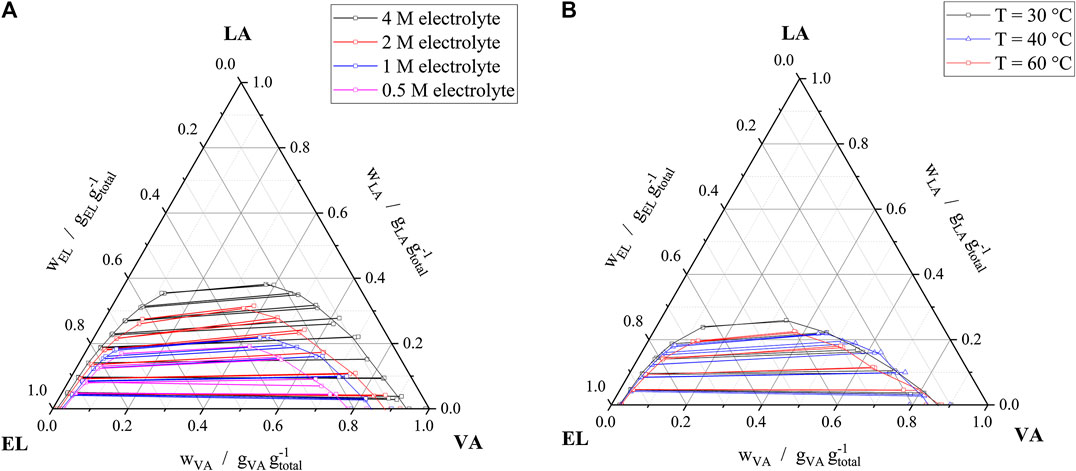
FIGURE 2. Liquid–liquid equilibrium data of the system valeric acid (VA), levulinic acid (LA), and aqueous H2SO4 (EL) at (A) different molar concentrations of the electrolyte (T = 40°C) and (B) at T = 30, 40, and 60°C for an EL concentration of 1 M.
Increasing temperature typically increases the mutual solubility of liquids, resulting in a narrower 2-phase region. This behavior can also be observed for the system under investigation; however, temperature influence is small. In Figure 2B, this trend is clearly visible for the aqueous phase in the system, where the area of the 2-phase region decreases with increasing temperature. For the organic phase, the EL solubility in VA seems to slightly increase with temperature and maximizes at 60 °C. However, differences between 30 and 40°C may be masked by measurement uncertainty. Compared to the influence of the electrolyte concentration, temperature has only a minor influence on the phase equilibrium of the system under investigation.
Process Concept
In the following, the determined LLE data shall be examined in the light of a potential continuous production process with integrated product separation. Different process concepts and their applicability to an efficient production of VA are discussed, also taking into account the electrolyte concentration and starting concentration of the educt of LA. Information on methods and equations used for the unit conversions can be found in the Supplementary Material.
Batch Processing
Typically, in lab experiments, batch processes are employed, where a given starting concentration of the reactant is processed for a given time. In Figure 3, the progression of such a reaction is displayed for different starting concentrations of LA (0.1–2 M) and for an EL concentration of 0.5 M. The reactant mixture only consists of LA and EL, so the starting points are situated on the EL–LA axis. In an ideal case, assuming full conversion of LA and 100% selectivity to VA, the final reaction mixture only consists of EL and VA, and thus rests on the EL–VA axis. Red lines connect the start and end points and therefore depict the reaction path for this ideal case. As one molecule of LA converts to one molecule of VA, the reaction path is a straight line.
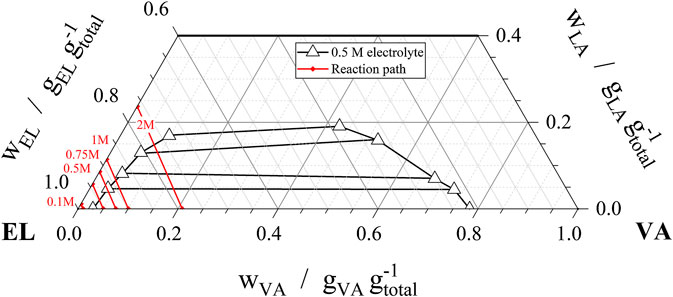
FIGURE 3. Reaction path for batch reactions with different starting concentrations of the reactant (0.1–2 M) in 0.5 M electrolyte.
For 0.1 M, the reaction system cannot reach the 2-phase region since the concentration of VA, even after complete conversion of LA, is below the solubility limit. For 0.5 M and higher initial LA concentrations, the reaction path reaches the 2-phase region and, dependent on the overall LA conversion, an organic product phase is formed eventually, which can be separated and used for further workup.
Examining the LLE data for different EL concentrations together with the respective reaction pathways, the required conversion of LA to VA that is necessary to form a second phase may be determined, depending on the starting concentration of LA and the molarity of the electrolyte. The resulting curves are given in Figure 4. Here, the minimum conversion required for a phase separation is plotted over the initial LA concentration for the four EL concentrations, 0.5–4 M. Phase separation is only achieved above the respective curve, opening the window for direct product removal.
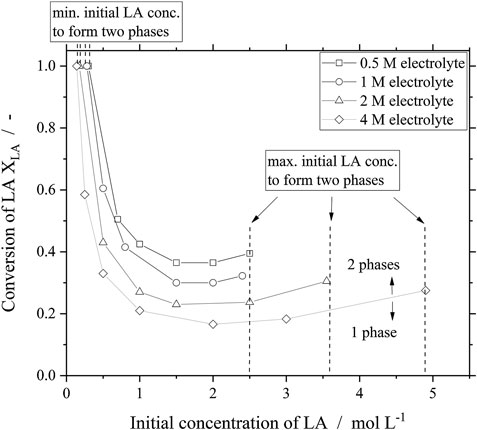
FIGURE 4. Operating range of the electrochemical conversion process derived from liquid–liquid equilibrium measurements and range of initial Levulinic acid (LA) concentration where a second organic product phase is formed upon reaction.
It becomes apparent that a lower and an upper initial LA concentration for the formation of a second organic phase exist. The second phase forms earlier, that is, at lower conversions of LA, with increasing EL concentration. The minimal initial LA concentration is between 0.115 M for 4 M EL and 0.3 M LA for 0.5 M EL. For concentrations below these limits, the product VA cannot be removed via LL separation. The upper limit represents the area near the critical point of the binodal curve, where the composition of organic and aqueous phases approaches each other and separation becomes more difficult or inefficient, respectively, due to the high content of EL and LA in the product phase.
Considering the different EL concentrations, the respective curves exhibit a similar trend; however, with increasing EL concentration, the phase separation occurs for lower conversions. This behavior represents the width of the 2-phase region in Figure 2. A minimum for the required conversion can be observed around 1.5 M initial LA concentration.
Taking the reaction data of our previous work into consideration, it becomes obvious that such an electrochemical production process is ideally operated at elevated reactant concentrations, to maintain high conversion rates and CE and to also enable phase separation (dos Santos et al., 2015). Thereby, the CE describes the charge efficiency by which electrons are transferred in the reaction products. However, such conditions are only the case for the starting phase of a batch process where overall conversion is low. With increasing conversion, reactant concentration decreases, slowing down rate and diminishing CE. It would thus be beneficial to continuously replenish the consumed educt and electrolyte to maintain high concentrations and to also continuously remove the product phase in order to keep driving forces up. A respective process concept is discussed in the following.
Continuous Process Concept
To aim for a feasible continuous production process that exploits the above findings, the following concept, based on batch reaction data and LLE data, is suggested (see Figure 5).
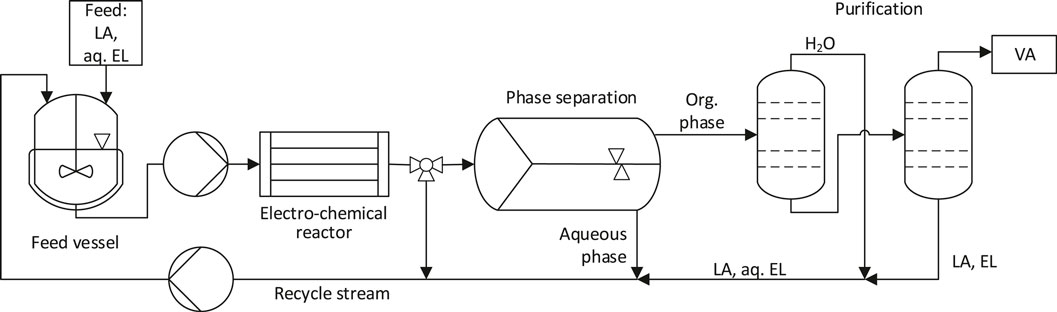
FIGURE 5. Concept for the continuous production of valeric acid (VA) in an electrochemical flow reactor with integrated product separation and reactant recycle.
From a storage vessel, the feed solution, containing LA and the aqueous electrolyte, is passed through the electrochemical reactor. The reactor is designed to only partially convert LA to the desired product VA at a typical conversion of XLA = 10–20%. The high reactant concentration and partial conversion assure high reaction rates and a high CE, as well as a high selectivity to the desired product VA. However, in the start-up phase, conversion in a single pass through the reactor will not be sufficient to form the organic product phase. An immediate recycle to the feed vessel will be required to enrich VA concentration after multiple reactor passages. Upon sufficient formation of VA, the organic product phase appears according to the measured LLE data (see Figure 2), which can be separated from the aqueous reactant phase in the following LL separator. For the formation of an organic phase with a high VA concentration resulting in minimized effort for further workup and purification of VA, a high electrolyte concentration in the aqueous reaction phase is beneficial. The remaining aqueous reactant phase with the unreacted LA is recycled, ensuring high resource efficiency regarding LA. Since LA concentration in the recycle loop will decrease over time due to the electrochemical reaction, fresh feed solution containing a high concentration of LA or even pure LA has to be dosed constantly in the feed vessel to maintain a sufficiently high and also constant LA concentration in the process.
The separated organic product phase can then be further purified, for example, via rectification to obtain pure VA. The organic phase will consist of mainly VA and LA with the addition of water and a small amount of the electrolyte H2SO4. For the purification of VA, a strategy using two rectification columns should be sufficient (see Figure 5). In the first column, light boiling constituents (such as water) in the organic product phase will be separated via the head product stream and recycled into the reaction process. Employing the second column, VA is obtained as the head product, while high-boiling LA and H2SO4 remain in the bottom stream and can be recycled as well. Due to the high normal boiling points of VA (184–186°C), LA (244–246°C), and H2SO4 (290°C), this should be conducted at reduced pressure to limit thermal stress to the components and corrosivity of the sulfuric acid containing the bottom product.
Figure 6, left, displays the expected reaction pathway and operation points for the continuous process concept for initial LA concentrations of 0.5, 1, and 2 M, and an EL concentration of 0.5 M. Starting with the two-component mixture LA/EL, the reaction first proceeds in the single-phase region (red arrows). When a sufficient amount of LA is reacted to VA, the reaction mixtures becomes saturated with VA, and its composition is represented by the intersection of the reaction path and the binodal curve (red circles). From now on, every pass through the electrochemical reactor will produce additional VA molecules, which will separate according to the LLE, resulting in the formation the organic phase (red squares).
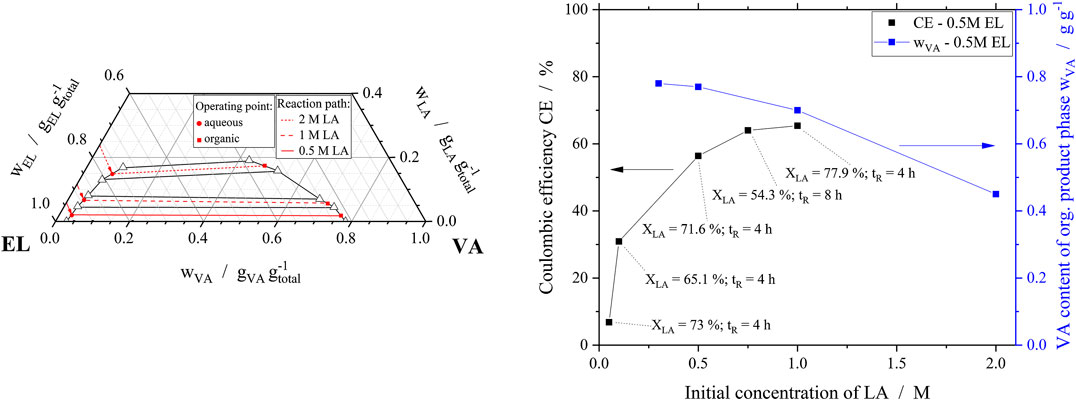
FIGURE 6. Left: hypothetical process pathways and resulting organic and aqueous phase composition in steady-state continuous operation for different initial levulinic acid (LA) concentrations. Right: purity of the obtained organic product phase by means of valeric acid (VA) mass fraction and coulombic efficiency of the electrochemical conversion (CE data from dos Santos et al., 2015) as a function of the initial LA concentration in a 0.5 M EL solution.
Since the reactor is operated under low partial conversion, the amount of organic phase produced per cycle is relatively low. Consequently, the respective composition of the 2-phase mixture before separation is close to the binodal curve inside the 2-phase region, and it can be concluded that the flow rate of the organic product stream will be much smaller than that of the aqueous recycle stream.
Keeping the composition of the aqueous recycle phase constant at the respective operating point (red circles) by dosing a feed solution consisting of LA and EL to replenish the consumed LA is essential for a stable operation over the course of the process with a constant composition and flow rate of the organic product phase.
By employing different initial LA concentrations, different operating points can be selected. As seen from Figure 6, right, the mass fraction of the desired product VA in the organic product phase decreases with increasing LA starting concentration. This will increase the effort for further purification, for example, by distillation, to gain pure VA. In contrast, CE benefits from a higher initial LA concentration (dos Santos et al., 2015). Consequently, LA concentration for the operation of the reaction and separation step in a continuous process requires optimization, which will be addressed in future investigations.
Higher concentrations of EL increase the purity of the organic product phase. The 2-phase region is becoming wider with increased EL content (see Liquid-Liquid Equilibrium), which will result in a better separation and therefore in a higher purity of the organic product phase. The impact of a higher EL concentration on selectivity, conversion, and CE will also be investigated in further experimental studies.
Conclusion
Aiming for a continuous electrochemical synthesis process with the integrated separation of VA from the aqueous reaction medium based on the mutual insolubility of the species involved, the liquid–liquid phase equilibrium of the LA/VA/EL system has been studied in detail. The VA content of the organic product phase after phase separation benefits from increased electrolyte concentrations in the aqueous phase, while temperature has only a minor effect in the range considered. As a result of the investigations, a continuous production concept with partial conversion, recycle of the unreacted educt, and continuous product removal via liquid–liquid phase separation based on the LLE data is designed and hypothetically assessed. Operating the continuous process at partial conversion and with a high electrolyte concentration is beneficial both for the selectivity and CE of the reaction as well as for the liquid–liquid phase separation. Regarding the reactant concentration, an optimization problem between CE and purity of the organic product phase is present, which will be investigated in future experiments.
The principle of integrated product separation for continuous electrochemical production was shown for the system LA/VA in this work. However, many interesting systems exhibit similar characteristics, where product solubility is reduced due to the electrochemical conversion compared to the starting materials. Therefore, the presented approach is generalizable and might also be used for the continuous electrochemical production of octane from VA or 2-methylfuran from furfural in the future.
Data Availability Statement
The original contributions presented in the study are included in the article/Supplementary Material.
Author Contributions
MR and MG conceptualized the research work, analyzed the data, and wrote the manuscript. WS and JK conducted the LLE measurements. US and SS reviewed the manuscript and supervised the project. All authors contributed to the article and approved the submitted version.
Funding
WS and MR were supported by the Ministry for Science and Culture of Lower Saxony as part of the research program MOBILISE (Mobility in Science and Engineering), grant number ZN3247. MG acknowledges the funding by the Deutsche Forschungsgemeinschaft (DFG, German Research Foundation) under Germany’s Excellence Strategy EXC 2163/C2.1 Sustainable and Energy Efficient Aviation, Project ID 390881007. We acknowledge support by the German Research Foundation and the Open Access Publication Funds of the Technische Universität Braunschweig.
Conflict of Interest
The authors declare that the research was conducted in the absence of any commercial or financial relationships that could be construed as a potential conflict of interest.
Supplementary Material
The Supplementary Material for this article can be found online at: https://www.frontiersin.org/articles/10.3389/fenrg.2020.565570/full#supplementary-material
Abbreviations
ci (molL−1), concentration of component i; CE (%), Coulombic efficiency; DF, dilution factor; EL, aqueous electrolyte solution; LA, levulinic acid; LLE, liquid–liquid phase equilibrium; mi (kg), mass of component i in the sample; Mi (gmol−1), molar mass of component i; VS (mL), volume of the sample; VA, valeric acid; wi
References
Bisselink, R. J. M., Crockatt, M., Zijlstra, M., Bakker, L. J., Goetheer, E., Slaghek, T. M., et al. (2019). Identification of more benign cathode materials for the electrochemical reduction of levulinic acid to valeric acid. ChemElectroChem 6, 3285. doi:10.1002/celc.201900734
Corma, A., Iborra, S., and Velty, A. (2007). Chemical routes for the transformation of biomass into chemicals. Chem. Rev. 107, 2411. doi:10.1021/cr050989d
dos Santos, T. R., Nilges, P., Sauter, W., Harnisch, F., and Schröder, U. (2015). Electrochemistry for the generation of renewable chemicals: electrochemical conversion of levulinic acid. RSC Adv. 5, 26634. doi:10.1039/c4ra16303f
Filiciotto, L., Balu, A. M., van der Waal, and J. C., and Luque, R. (2018). Catalytic insights into the production of biomass-derived side products methyl levulinate, furfural and humins. Catal. Today 302, 2. doi:10.1016/j.cattod.2017.03.008
Frontana-Uribe, B. A., Little, R. D., Ibanez, J. G., Palma, A., and Vasquez-Medrano, R. (2010). Organic electrosynthesis: a promising green methodology in organic chemistry. Green Chem. 12, 2099. doi:10.1039/c0gc00382d
Gallezot, P. (2012). Conversion of biomass to selected chemical products. Chem. Soc. Rev. 41, 1538. doi:10.1039/C1CS15147A
Goldmann, A., Sauter, W., Oettinger, M., Kluge, T., Schröder, U., Seume, J., et al. (2018). A study on electrofuels in aviation. Energies 11, 392. doi:10.3390/en11020392
Huber, G. W., Iborra, S., and Corma, A. (2006). Synthesis of transportation fuels from biomass: chemistry, catalysts, and engineering. Chem. Rev. 106, 4044. doi:10.1021/cr068360d
Isikgor, F. H., and Becer, C. R. (2015). Lignocellulosic biomass: a sustainable platform for the production of bio-based chemicals and polymers. Polym. Chem. 6, 4497. doi:10.1039/C5PY00263J
Kamm, B., Gruber, P. R., and Kamm, M. (2005). Biorefineries-industrial processes and products. Weinheim, Germany: Wiley-VCH Verlag GmbH. doi:10.1002/14356007.l04_l01.pub2
Kamm, B., Gruber, P. R., and Kamm, M. (2012). “Biorefineries—industrial processes and products,” in Ullmann’s encyclopedia of industrial chemistry, 659–683. doi:10.1002/14356007.l04_l01
Kirschning, A. (2009). Chemistry in flow systems. Beilstein J. Org. Chem. 5, 15. doi:10.3762/bjoc.5.15
Kirschning, A. (2011). Chemistry in flow systems II. Beilstein J. Org. Chem. 7, 1046. doi:10.3762/bjoc.7.119
Leonard, R. H. (1956). Levulinic acid as a basic chemical raw material. Ind. Eng. Chem. 48, 1330. doi:10.1021/ie50560a033
Movsisyan, M., Delbeke, E. I. P., Berton, J. K. E. T., Battilocchio, C., Ley, S. V., and Stevens, C. V. (2016). Taming hazardous chemistry by continuous flow technology. Chem. Soc. Rev. 45, 4892. doi:10.1039/C5CS00902B
Nilges, P., dos Santos, T. R., Harnisch, F., and Schröder, U. (2012). Electrochemistry for biofuel generation: electrochemical conversion of levulinic acid to octane. Energy Environ. Sci. 5, 5231. doi:10.1039/c1ee02685b
Pileidis, F. D., and Titirici, M.-M. (2016). Levulinic acid biorefineries: new challenges for efficient utilization of biomass. ChemSusChem 9, 562. doi:10.1002/cssc.201501405
Qiu, Y., Xin, L., Chadderdon, D. J., Qi, J., Liang, C., and Li, W. (2014). Integrated electrocatalytic processing of levulinic acid and formic acid to produce biofuel intermediate valeric acid. Green Chem. 16, 1305. doi:10.1039/c3gc42254b
Schäfer, H. J. (2011). Contributions of organic electrosynthesis to green chemistry. C. R. Chim. 14, 745. doi:10.1016/j.crci.2011.01.002
Tafel, J., and Emmert, B. (1911). Die elektrolytische Reduktion von Lävulinsäure und α-Dimethyllävulinsäure. Z. Elektrochem. Angew. p. 17, 569. doi:10.1002/bbpc.19110171404
Teong, S. P., Yi, G., and Zhang, Y. (2014). Hydroxymethylfurfural production from bioresources: past, present and future. Green Chem. 16, 2015. doi:10.1039/C3GC42018C
van de Vyver, S., Thomas, J., Geboers, J., Keyzer, S., Smet, M., Dehaen, W., et al. (2011). Catalytic production of levulinic acid from cellulose and other biomass-derived carbohydrates with sulfonated hyperbranched poly(arylene oxindole)s. Energy Environ. Sci. 4, 3601 doi: 10.1039/C1EE01418H
Werpy, T., and Petersen, G. (2004). Top value added chemicals from biomass. Pacific Northwest National Laboratory, National Renewable Energy Laboratory, Office of Scientific and Technical Information, Oak Ridge, United States, 13–48. doi:10.2172/15008859
Keywords: valeric acid, phase separation, continuous product removal, electrochemical hydrogenation, liquid–liquid equilibrium
Citation: Rehbein MC, Guschakowski M, Sauter W, Kunz J, Schröder U and Scholl S (2020) Liquid–Liquid Equilibrium Data and Continuous Process Concept for the Electrosynthesis of Valeric Acid from Levulinic Acid. Front. Energy Res. 8:565570. doi:10.3389/fenrg.2020.565570
Received: 25 May 2020; Accepted: 26 August 2020;
Published: 22 September 2020.
Edited by:
Soorathep Kheawhom, Chulalongkorn University, ThailandReviewed by:
Roel Bisselink, Wageningen University and Research, NetherlandsHelena Lundberg, Royal Institute of Technology, Sweden
Copyright © 2020 Rehbein, Guschakowski, Sauter, Kunz, Schröder and Scholl. This is an open-access article distributed under the terms of the Creative Commons Attribution License (CC BY). The use, distribution or reproduction in other forums is permitted, provided the original author(s) and the copyright owner(s) are credited and that the original publication in this journal is cited, in accordance with accepted academic practice. No use, distribution or reproduction is permitted which does not comply with these terms.
*Correspondence: Stephan Scholl, cy5zY2hvbGxAdHUtYnJhdW5zY2h3ZWlnLmRl