- 1Institute of Energy and Climate Research - Systems Analysis and Technology Evaluation (IEK-STE), Forschungszentrum Jülich, Jülich, Germany
- 2Research & Development - Process Development (RDP), Linde Aktiengesellschaft, Linde Engineering, Pullach, Germany
To achieve the European Union’s ambitious climate targets, not only the energy system must be transformed, but also other sectors such as industry or transport. Power-to-X (PtX) technologies enable the production of synthetic chemicals and energy carriers using renewable electricity, thus contributing to defossilization of economy. Additionally, they provide storage capacity for renewable energy. Detailed life cycle assessments (LCA) of PtX is required, to prove the environmental advantages to fossil-based benchmark technologies. An emerging PtX technology for syngas production is the high temperature co-electrolysis (HT-co-electrolysis), which produces syngas. Aim of this LCA is the evaluation of syngas production by HT-co-electrolysis at its early stage of development to derive incentives for further research. For comparison, a small-scale steam methane reforming process (SMR) serves as today’s fossil-based benchmark. The required CO2 is obtained via direct air capture. The by-far most important input for the HT-co-electrolysis is electricity. Hence, several future electricity mixes are considered, representing two different climate protection targets (CPT80, CPT95) for the energy system in 2050. For each CPT, an additional distinction is made regarding full load hours, which depend on the availability of renewable energy. The results show lower global warming potential (GWP) and fossil fuel depletion for HT-co-electrolysis compared to SMR if mostly renewable power is used. Exclusively renewable operated HT-co-electrolysis even achieve negative net GWPs in cradle-to-gate LCA without considering syngas use. If HT-co-electrolysis shall operate continuously (8,760 h) additional fossil electricity production is needed. For CPT80, the share of fossil electricity is too high to achieve negative net GWP in contrast to CPT95. Other environmental impacts such as human toxicity, acidification, particulate matter or metal depletion are worse in comparison to SMR. The share of direct air capture on the total environmental impacts is quite noticeable. Main reasons are high electricity and heat demands. Although plant construction contributes to a minor extent to most impact categories, a considerable decrease of cell lifetime due to higher degradation caused by flexible operation, would change that. Nevertheless, flexibility is one of the most important factors to apply PtX for defossilization successfully and reinforce detailed research to understand its impacts.
Introduction
In most countries, climate change is at the top of today’s political and technological agenda. The challenge of climate change can only be met by a fundamental transformation of the energy system. The aim is to transform the current system, which is highly dependent on fossil fuels, into a mostly greenhouse gas neutral energy system based on renewable energies. The European Union has established three key targets for 2030 already in 2014: 1) reducing greenhouse gas (GHG) emissions at least by 40% compared to 1990 levels, 2) increasing the share of renewable energy at least to 32%, and 3) improving energy efficiency at least by 32.5% (European Council, 2014).
Currently, the European Commission has proposed a European climate law (the green deal) to reduce GHG emissions even by 50–55% compared to 1990 levels by 2030 and to achieve climate neutrality by 2050 (European Commission, 2020).
To reach these not only the energy system must be transformed, but also other sectors, like industry or transport. All the same, carbon-based energy carriers and raw materials will still be needed in the future, especially for the chemical industry. Hence, a full decarbonization of all sectors is very unlikely. Even more, defossilization of sectors by substitution of fossil fuels with renewables is mandatory. Power-to-X (PtX) technologies allow the production of synthetic chemicals and energy carriers using renewable electricity. By coupling sectors, PtX contributes to the overall defossilization (Heinemann et al., 2019; Bauer and Sterner, 2020). However, renewable electricity will continue to be a limited resource in the near future, since it can be used for competing PtX technologies such as Power-to-Heat, Power-to-Gas, Power-to-Fuels or Power-to-Chemicals. Processes with highest environmental benefits per kWh renewable electricity must be identified. In the past years specific efforts were taken to promote the development of PtX technologies, driving low technology readiness levels (TRL) of one to three toward demonstration plants (TRL 6–7) (Wulf et al., 2018; Chehade et al., 2019; RWE, 2019; Thema et al., 2019; Uniper SE, 2019).
The German Kopernikus project “P2X,” funded by the German Federal Ministry of Education and Research, meets the challenge to improve PtX competitiveness (Ausfelder et al., 2019). In an emerging PtX technology, known as high temperature solid oxide co-electrolysis (HT-co-electrolysis; HT-SOEC), water is split and simultaneously CO2 is activated to form syngas (Foit et al., 2016). Syngas is a mixture of carbon monoxide (CO) and hydrogen (H2) in various compositions and therefore an important intermediate product of numerous chemical synthesis such as methanol synthesis, Fischer-Tropsch synthesis, and hydroformylation. The annual production of syngas is estimated to approx. 598 million tons for 2018 (Khan, 2018). Coal (48.3%) and natural gas (46.5%) are the two dominant feedstocks. Petcoke, refinery residue and coke oven gas serve as 4.3% syngas feedstock. Biomass and waste constitute less than 1% (Khan, 2018). HT-co-electrolysis is able to generate tailor-made syngas of variable compositions, which are relevant for industrial applications in the range of H2/CO ratio of one–three by variation of operating parameters (temperature, current, feed gas composition). HT-co-electrolysis takes place at temperatures around 800°C. Syngas can be produced with current densities up to 2 A/cm2 (Zheng et al., 2017), although they are often lower in practice, and with high cell efficiencies (Foit et al., 2016).
Detailed analyses are already required at a very low TRL, since PtX products are not a priori more sustainable than their well-established fossil benchmarks. The overall performance depends on various criteria, e.g., expenditures for electricity, water and CO2 supply, efficiencies of the new synthesis routes as well as costs (Bracker, 2017). Comprehensive reviews on HT-co-electrolysis including basic principles, required materials, cell and stack design, fabrication and scale up, performance measurements, degradation issues, and economic feasibility were given by Zheng et al. (2017) and Foit et al. (2016). An in-depth insight into optimal energy system layout and conditions for economic feasibility was provided by Morgenthaler et al. (2020). Syngas, as an important intermediate of the chemical industry, is neither transported nor directly sold as a final product, in contrast to H2 (Peschel, 2020). This might be the reason that only one life cycle assessment (LCA) study was found analyzing solely the production of syngas so far (Sternberg and Bardow, 2016). The authors analyzed Power-to-Gas processes to synthetic natural gas (Power-to-SNG) by Sabatier reaction in comparison to Power-to-syngas by reverse water gas shift (rWGS) and dry reforming of methane (DRM). They pointed out that both Power-to-Syngas pathways have a higher environmental benefit than Power-to-SNG. Syngas production by DRM has lower GHG emissions than by rWGS. Some other LCA studies are available that analyze processes using CO2-based syngas as intermediate feedstock for chemicals (Anicic et al., 2014; Luu et al., 2015; Al-Kalbani et al., 2016) and fuels (van der Giesen et al., 2014; Baltrusaitis and Luyben, 2015).
Several LCA studies have been conducted for different PtX pathways. In a recent review Koj et al. (2019) compared 32 LCA studies analyzing environmental, technological, as well as methodological aspects of PtX systems. The electricity source and the methodological concept of CO2 consideration are crucial drivers of environmental impacts. Sternberg and Bardow (2015) presented an environmental comparison of Power-to-Power, -to-Mobility, -to-Heat, -to-Fuel, and -to-Chemical feedstock. Reiter and Lindorfer (2015) compared H2 and methane (CH4) production from renewable electricity via Power-to-Gas technology to conventional natural gas supply. A study from van der Giesen et al. (2014) examined rWGS process as intermediate step for the production of liquid hydrocarbon fuels (Power-to-Fuel) as an alternative to diesel. In the study from Liu et al. (2020) CO2 emissions from direct air capture (DAC) and Fischer-Tropsch fuel production were assessed by LCA. CO2 based C1-chemicals (e.g. formic acid, CO, methanol, CH4) by hydrogenation (Power-to-Chemical feedstock) are focus of the study from Sternberg et al. (2017). The environmental comparison of different CO2 sources (e.g., captured CO2 from chemical plants, natural gas processing, paper mills, power plants, iron and steel plants) for Power-to-Chemicals processes is the focus of the study by von der Assen et al. (2016). Zhang et al. (2017) discussed many system variations of Power-to-Gas technologies. Power-to-Gas can reduce GHG emissions, depending on the electricity supply and CO2 source, compared to conventional gas production technologies. A global assessment of the climate change mitigation potential of carbon capture and utilization (CCU) in the chemical industry is provided in studies by Artz et al. (2018) and Kätelhön et al. (2019).
Aim of this LCA study is to evaluate the environmental competitiveness of syngas production by HT-co-electrolysis at an early stage of development, to derive incentives for further research and development directions. For the electrolysis process, different electricity supply mixes representing various future energy scenarios are considered. The required CO2 is captured by DAC. Coal gasification (Khan, 2018) and steam methane reforming (SMR) of natural gas (Rostrup-Nielson, 2005) can be regarded as today’s most utilized fossil benchmark technologies. However, gasification is used for very large scales (>10 kNm3/h often even >100 kNm3/h syngas) and is not built on a small scale for technical and economic reasons. As HT-co-electrolysis is still at an early developing stage and will be employed only on small scale and in a decentralized way in the near future, a small-scale SMR with an output of just 330 m3/h syngas is used as fossil reference for a meaningful comparison. However, since not all measures of heat integration are economically useful for small scale, its efficiency is lower than that for large-scale SMRs usually used.
Method
LCA is a comprehensive method to assess environmental impacts of products and processes (International Organization for Standardization, 2006a; International Organization for Standardization, 2006b). According to the ISO standards, LCA is subdivided into four steps. First, in the goal and scope definition the object, the system boundaries, and the functional unit (FU) of the analysis are described. Second, in the life cycle inventory (LCI), material and energy inputs and their subsequent outputs are compiled along the process chains considered. Third, in the life cycle impact assessment (LCIA), the potential environmental impacts are evaluated. Fourth, the results are summarized and conclusions are drawn to give recommendations for improvement in the final interpretation step.
Goal and Scope Definition
Goal of this paper is the comparison of environmental impacts of syngas production by HT-co-electrolysis and by the corresponding small-scale SMR process. Therefore, LCIs of syngas production by HT-co-electrolysis and small-scale SMR as well as CO2 supply by DAC are compiled In addition, detailed LCIs of construction of HT-co-electrolysis and small-scale SMR and their environmental impacts is carried out in order to sensitize the technology developers to critical materials at an early stage and to derive further research incentives. In case of HT-co-electrolysis, balance-of-plant (BoP) components, stack materials and single cells are published for the first time and can serve as a basis for further analyses in the PtX field.
System Boundaries and Functional Unit
Figure 1 presents the system boundaries of the two syngas production pathways considered in an attributional cradle-to-gate LCA. The functional unit (FU) is 1 kg of syngas produced, with a molar H2/CO ratio of 2, at 20 bar, 40°C and a CO2 molar fraction below 0.1 mol%. The molar ratio of two is chosen, since many chemical processes and synthetic fuels require such a syngas feed. Syngas use is not included in this analysis.
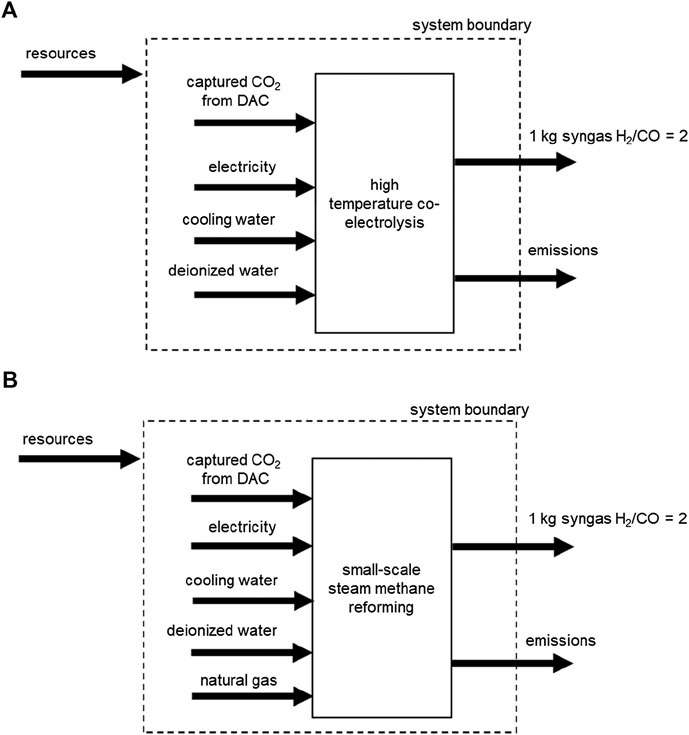
FIGURE 1. System boundaries of cradle-to-gate syngas production pathways considered: (A) syngas production by HT-co-electrolysis, (B) conventional syngas production by small-scale SMR.
Tables 2-4 present the LCI data of HT-co-electrolysis, small-scale SMR, and DAC construction and operation. Detailed information about construction is provided in the Supplementary Material.
For electricity as the most important input of the HT-co-electrolysis, four different electricity supply mixes are used for the year 2050, which are specified in detail in the background system “Electricity Supply Mixes.” The electricity mixes take into account two different climate protection targets (CPT) based on 80% and 95% CO2 reduction (CPT80, CPT95). For each CPT, an additional distinction is made regarding full load hours, which depend on the availability of renewable energy. The availability represents hours of exclusively renewable generated electricity (Bareiß et al., 2018; Bareiß et al., 2019). This results in four scenarios: 1) CPT80, 8,760 h; 2) CPT80, 3,000 h; 3) CPT95, 8,760 h; 4) CPT95, 6,500 h) (Table 5). The lower the number of full load hours, the lower the quantities of syngas produced per year. While for 8,760 h, 147 t of syngas are produced per year, for 3,000 h (CPT80) and 6,500 h (CPT95), 50.3 and 109 t of syngas are produced, respectively (Table 2). For small-scale SMR as today’s conventional technology of syngas production, an 8,760 h operation with the German electricity mix 2014 is considered.
Data Sources
For process chain modeling, the LCA software GaBi version 9.2.0.58 (thinkstep, 2018) was used. Background LCI data are taken from both the ecoinvent 3.5 database (Ecoinvent, 2016) and the GaBi Professional 9.2 database. Most of the LCI data of the syngas production technologies (so called foreground data) are provided by Kopernikus project partners:
(1) cell and stack construction of HT-co-electrolysis: Forschungszentrum Jülich GmbH - Institute of Energy and Climate Research (IEK-1, IEK-3), - Central Institute of Engineering, Electronics and Analytics (ZEA)
(2) small-scale SMR process design and simulation, HT-co-electrolysis overall system design and process simulation: Linde Aktiengesellschaft (AG), Linde Engineering, Research & Development, Process Development
(3) DAC: Climeworks AG
(4) electricity supply models: Technical University Munich - Institute for Renewable and Sustainable Energy Systems.
Limitations
The construction of the syngas production units as well as of the DAC unit is considered. The lifetime is 20 years. Components with lower lifetime (e.g., cells) are replaced. Decommissioning of the production units or other end-of-life processes are neglected. To simplify the calculation it was assumed, that the intermittent renewable electricity is provided continuously to HT-co-electrolysis. This is, of course, not the case. However, a consequential ramp up and shut down of the HT-co-electrolysis most likely would affect the performance and life time of the unit. This effects have not been investigated yet and are topic of further research. Processing and use of syngas for a specific industrial application is out of the presented scope. Nevertheless, results can be taken for LCAs of further products based on syngas with H2/CO ratio of 2.
Allocation
If more than one product is produced in a process, it is necessary to divide the environmental impacts between the products according to ISO 14040 (International Organization for Standardization (ISO), 2006a; b). Although syngas and oxygen are produced during the HT-co-electrolysis, no allocation was carried out between the two products. Oxygen is neither purified, nor stored or used. Before the oxygen is released from the system, it is diluted with air to mitigate safety concerns. Therefore, it is considered as waste and no allocation is necessary.
The assessment of the various impacts of CO2 supply as well as the best way to account for expenditures for the capture process has been topic of several controversial studies and lies beyond the scope of this study (Müller et al., 2020). In case of DAC it is not necessary to consider the primary CO2 emitter (air). CO2 is considered as an elementary flow (see Life Cycle Inventory of High Temperature Co-Electrolysis). We completely allocate all expenditures for DAC (e.g., electricity, heat) and emissions to the both syngas production systems. Additionally, the amount of CO2 removed from the atmosphere is credited to the syngas production via HT-co-electrolysis and via small-scale SMR process.
Environmental Impact Categories
The environmental impacts are determined according to the ReCiPe methodology for LCIA version 2016 v1.1 Midpoint (Hierarchist) (Goedkoop, 2009) with one exception considering abiotic resource depletion. The two considered syngas production pathways are compared based on the following eight impact categories:
(1) Climate change (GWP) (kg CO2 eq.),
(2) Fossil depletion (FD) (kg oil eq.),
(3) Fine Particulate Matter Formation (PM) (kg PM2.5 eq.),
(4) Terrestrial Acidification (AP) (kg SO2 eq.),
(5) Photochemical Ozone Formation, Ecosystems (POCPeco) (kg NOx eq.),
(6) Photochemical Ozone Formation, Human Health (POCPhuman) (kg NOx eq.), and
(7) Human toxicity, cancer (HTP) (kg 1,4-DB eq.)
(8) Abiotic resource depletion (ADP) (kg Sb eq.).
The first seven categories are chosen because they reflect electricity driven impact categories and thus represent the motivation for PtX. Due to the use of rare earth elements (REEs) for the single cells in the HT-co-electrolysis unit, the impact category “Abiotic Depletion (ADP elements)” (kg Sb eq.) supplied by CML method version CML2001 - Jan. 2016 is used additionally. For this method, Adibi et al. (2019) estimated new characterization factors (CFs) for 15 REEs. Despite the high criticality, individual REEs are not covered appropriately by any LCIA methods so far. To develop the CFs, the authors collected a wide range of data from U.S. Geological Survey (USGS) and other mining reports for 11 large REE deposits. For this study, we integrated the new CFs of the REEs in the ADP category of CML. ADP and HTP are often important for the supply of steel, nickel, copper and other metals like REEs or chromium.
Specification of Foreground Systems
High Temperature Co-Electrolysis
Technical Description of High Temperature Co-Electrolysis
HT-co-electrolysis is a further development of HT-solid oxide electrolysis (HT-SOEC) for H2 production. In the HT-co-electrolysis, the two reactions of electrolytic H2 production and CO production by rWGS run simultaneously in one reactor. Operation at high temperatures offers thermodynamic advantages. On stack level, this results in lower energy requirements combined with increased efficiency by better kinetics compared to low temperature electrolysis. A complex fully heat integrated HT-co-electrolysis process at commercial scale, however, has not been built so far. This results in a lower system efficiency compared to the stack efficiency. The simulated 150 kW HT-co-electrolysis analyzed in this study operates at 800°C with an efficiency of approx. 75% (Figure 2). The process design was done by Linde AG deriving a fully heat integrated process, so that no steam input and export is required. Since CO2 and steam are not fully converted in the electrolyzer, CO2 needs to be separated from the syngas and recycled. CO2 separation is carried out by pressure swing adsorption (PSA). The syngas output has the same composition and properties as the one from the small-scale SMR described below. The output amounts to 16.8 kg/h and is therefore only 10% of the syngas output supplied by the small-scale SMR (159 kg/h). Additional losses in efficiency caused by transformer, rectifier and power electronics are not yet included in the HT-co-electrolysis analysis. These losses usually are below 5%.
Currently, a degradation of 1%/1,000 h in contrast to the much lower degradation of solid oxide fuel cells (SOFC) (0.3%/1,000 h) is taken into account. This results in a total cell replacement after 10 years. It is assumed that most of the stack material (Crofer22APU) can be reused. However, system efficiency losses due to lower cell efficiency over time is not considered in power demand. It should be noted that the current degradation of 1%/1,000 h will probably result in overcharged maintenance and replacement costs which makes industrial applications rather unrealistic. Although it can be assumed that degradation will decrease when the TRL increases, degradation remains a major development task for HT-co-electrolysis. It is still uncertain whether lower degradation can be achieved.
Table 1 presents the main cell, stack and operating parameters. The numbers of cell levels and single cells for a 150 kW unit are calculated to 227 and 908, respectively. For simplification, two stacks with 120 levels each and 960 single cells are assumed.
The so-called Jülich FY10 is a robust stack design based on 2.5–5 mm thick interconnectors (IC) consisting of Crofer22APU (Fang et al., 2015; Frey et al., 2018). This vacuum-cast alloy has a composition of 22% chromium, 0.4% manganese, 0.07% titanium, 0.08% lanthanum, and 77.45% iron and was developed by Quadakkers et al. (2004). The major stack components are shown in Figure 3 (Fang et al., 2015). Each repeating unit consists of one IC, one frame, together with the cell and a nickel mesh. The anode side of the IC is coated with a 100 µm chromium poisoning protection layer consisting of Mn1.0Co1.9Fe0.1O4 (MCF). The coating is performed by atmospheric plasma spraying (APS). The glass-cermet used as sealant is discussed in Groß-Barsnick et al. (2018). The slurry contains glass powder, yttrium stabilized zirconia (YSZ) fibers, and organics.
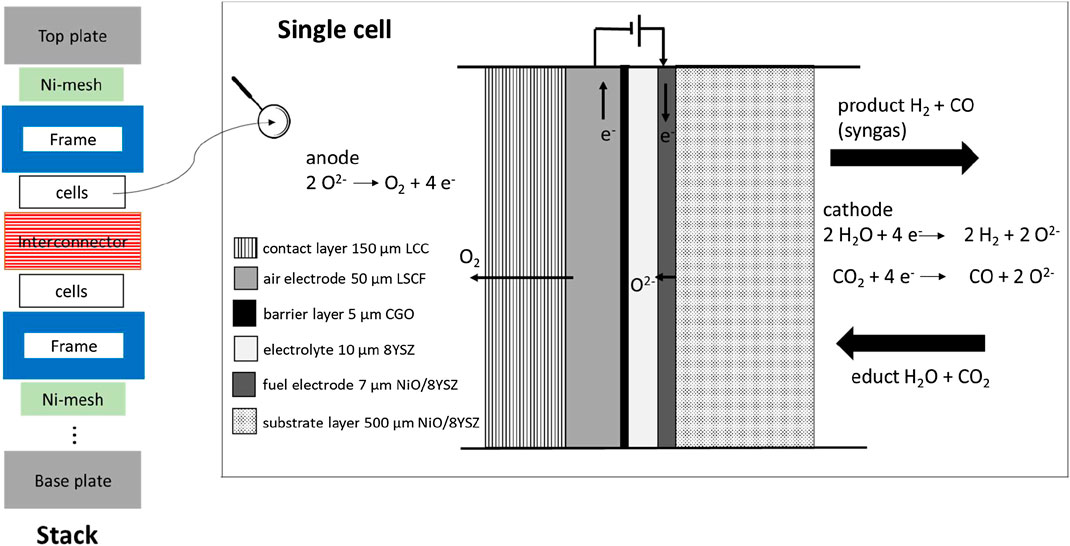
FIGURE 3. Schematic illustration of the Jülich FY10 stack design based on Fang et al. (2015) and an included single cell (Menzler et al., 2014; Harboe et al., 2020).
Figure 3 shows a schematic illustration of an anode-supported cell (ASC in SOFC mode) which is considered here, in contrast to the other main concept of electrolyte-supported cells (ESC). The cell and stack concept analyzed in this study is mainly based on activities at Forschungszentrum Jülich (Menzler et al., 2014; Schafbauer et al., 2014; Frey et al., 2018), but using a thinner IC (2.5 mm) as described in Harboe et al. (2020). Due to its mechanical strength, 8 mol% YSZ (8YSZ) is used as an electrolyte. The anode consists of (La, Sr) (Co, Fe)O3 perovskite (LSCF) and the contact layer consist of La1Mn0.45Co0.35Cu0.2O3 (LCC10). The cathode is a nickel cermet (NiO/8YSZ). Gadolinium doped ceria (CGO) is used as barrier layer and is screen printed between electrolyte and anode. Typical cell manufacturing processes are tape casting (for the substrate layer), screen printing (for all other layers) and various sintering processes for each layer at optimized temperature (Menzler et al., 2014). The production route of these cells is discussed in detail in Menzler et al. (2014).
Life Cycle Inventory of High Temperature Co-Electrolysis
For the production of 1 kg of syngas, 1.38 kg of CO2, 1.13 kg of deionized H2O and 8.82 kWh of electricity are required. The separated oxygen leaves the plant without any ecological impact (see “Goal and Scope Definition”). Depending on the full load hours, various shares of single cells, stacks, and BoP pieces are assigned to the process. The smaller the number of full load hours due to the assumed electricity supply mix, the smaller the amounts of syngas produced per year. This results in larger shares of single cells, stacks, and BoP pieces assigned to 1 kg of syngas (Table 2). The amount of syngas reduces from 147 t/y to 109 t/y (CPT95) and finally to 50 t/y (CPT80) when the full load hours drop from 8,760 to 6,500 and 3,000 (Table 2).
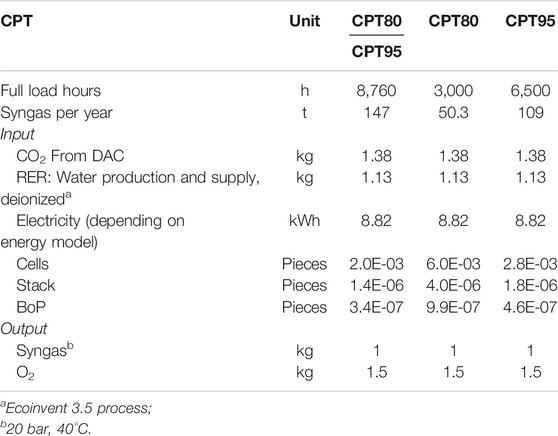
TABLE 2. Operation of HT-co-electrolysis to produce 1 kg of syngas (molar ratio H2/CO = 2) under consideration of different electricity mixes.
For stack production approx. 530 of kg Crofer22APU, 20 kg of nickel mesh, 20 kg of glass-ceramic sealant, and 3 kg of MCF are required for one stack. Further material processing such as form-shaping steps (e.g., milling of fuel gas and air manifolds, creep-feed grinding of the air channels, laser-cutting of outline), application of the chromium protecting layer MCF by APS and annealing of the stack at high-temperature are also considered in terms of their energy demand (Harboe et al., 2020). Argon and H2 needed for annealing are not considered due to missing data on gas consumption. In case of cells, materials and energy required for the sintering steps are included in the LCI. Further information about cell and stack construction as well as BoP can be found in Supplementary Tables S4–S7.
According to the BoP of a 100 kWel SOFC plant in Pehnt (2002) and data from Primas (2007), the BoP for the 150 kW HT-co-electrolysis was calculated. Approx. 1.9 t of steel are required for water evaporator, compressor, heat exchanger and piping. Moreover, an inverter, electricity and fuels for heating were used (Supplementary Table S7). The construction material for the PSA could not be taken into account because no data was available.
Small-Scale Steam Methane Reforming
Technical Description of Small-Scale Steam Methane Reforming
The process design of the small-scale SMR was carried out by Linde AG within the Kopernikus P2X project. For a meaningful comparability to the HT-co-electrolysis, a small-scale SMR process is modeled with typical heat integration and process set-up for small-scale. The syngas output is 330 Nm3/h (with 0.481 kg/m3 for a syngas with a molar ratio of H2/CO of 2) and therefore considerably lower than the usual industrial SMR processes between 20,000 and 200,000 Nm3/h. The process design is adapted to obtain syngas in a H2/CO ratio of two from a small-scale SMR for H2 production (Linde AG, 2019). The process performance is obtained from process simulations using UniSim Design® and physical property data. Such a small-scale SMR differs significantly from large-scale reformers in terms of process design and hence process efficiency. In case of large-scale reformers, a tailored heat recovery is economically reasonable. For small scale this would increase the specific investment costs per Nm3 product. Therefore, a simpler heat integration is used. By reason of small scale, the process is designed without steam export. Excess thermal energy is dissipated via cooling water. The efficiency of the small-scale SMR process is about 63% related to the lower heating value (LHV) of used natural gas (49.085 MJ/kg). Thus, the energy efficiency is more than 10%-points lower than for large-scale SMR plants.
The German natural gas mix from the GaBi Professional database (thinkstep, 2018) was selected for suppling the small-scale SMR. Because data for natural gas supply from the GaBi database stand for a LHV of 45.5 MJ/kg, the required quantity is converted by the LHV used for SMR modeling. The produced syngas consists of 66.4 mol% H2, 33.2 mol% CO and traces of CO2, nitrogen, H2O and hydrocarbons and has a LHV of 23.59 MJ/kg. The modeling data and process design of the small-scale SMR process supplied by Linde AG is confidential and cannot be presented in detail.
Life Cycle Inventory of Small-Scale Steam Methane Reforming
Table 3 specifies the inputs and outputs of 1 kg of syngas production by small-scale SMR. For SMR operation, 8,760 full load hours are assumed. Approx. 25% of the natural gas input serves as fuel for the burner. The calculation of the natural gas combustion emissions in the burner is based on the ecoinvent report 06.V (Faist-Emmenegger et al., 2007).
For the construction of the small-scale SMR including BoP material, 100 t of concrete, approx. 31 t of various steel types and 0.5 t of nickel are required (Supplementary Table S8). It should be noted that these values are only a first rough estimation. Furthermore, these values cannot be used to calculate the construction materials for a large-scale plant due to a significantly different design. In contrast to HT-co-electrolysis, no metalworking steps for the reformer components could be included due to missing information. As the results of the HT-co-electrolysis show, the metalworking steps have only a marginal impact on the results.
Specification of Background Systems
For the comparison of the HT-co-electrolysis and the small-scale SMR process, the background processes considered are identical. Both pathways need CO2, electricity, deionized water, and cooling water. Cooling water consumption is neglected because it is usually circulated and has only minor effects.
Supply of CO2 by Direct Air Capture
Technical Description of Direct Air Capture
The required CO2 can be supplied from different sources. Larger point sources, for example from CO2 wash systems as employed in chemical processes (e.g., ethylene oxide production), have the advantage of high CO2 concentrations and often high flow rates. In the long term, CO2 from biomass, waste gasification or obtained via DAC are favorable sources for a defossilization of the entire system. Keeping this long-term perspective in mind and to be as independent as possible from local conditions, DAC is considered as CO2 source in this study.
DAC is a geo-engineering method that separates CO2 from air. The concept was first introduced by Klaus Lackner in 1999 (Sanz-Pérez et al., 2016). Since that time, DAC caused many pro and cons analyses whether it is (or is not) an important and viable option for reducing greenhouse gases. In the last 10 years DAC is a rapidly growing environmental technology with several start-ups pushing this technology from lab scale to demonstration and pilot scale (Sanz-Pérez et al., 2016), although the second-law thermodynamic efficiency is likely to be significantly below 10% (House et al., 2011). In contrast, efficiency for amine based flue gas scrubbing reaches 20–25% (House et al., 2011). During the DAC process, ambient air flows through a filter where either adsorption, absorption or mineralization removes CO2 from air. In this study, the DAC technology of Climeworks AG is considered. This technology uses an adsorption-desorption process with a special cellulose-based filter material. Amine based solid sorbents are often proposed for DAC. The CO2 is chemically bound to the filter material along with air moisture (Fasihi et al., 2019). When the filter is saturated with CO2, it is heated up to around 100°C mainly by low-grade heat as an energy source. The CO2 is released from the filter and collected as concentrated CO2 gas to supply customers. The process is operated in continuous cycles. The filter is reused and lasts several thousand cycles (Climeworks, 2017). A full cycle takes 4–6 h with an output of >99% pure CO2 flow (Lozanovski, 2019). Data of this process represents the Climeworks DAC plant in Hinwil (Switzerland). It started operation in 2017 and is situated on top of a waste incineration plant. Eighteen air filter modules extract 900 t of CO2 per year, which is sold to a nearby fruit and vegetable grower for use in its greenhouse. The waste incineration plant provides the low-grade heat for stripping the CO2. This accounts for approx. 80% of the DAC’s total energy requirements (Fasihi et al., 2019). Climeworks seeks to reduce the current energy demand of 500 kWh of electricity and 1,500 kWh of heat per ton of CO2 by 40% in the future (Evans, 2017).
Life Cycle Inventory of Direct Air Capture
Table 4 shows the required inputs to produce 1 t of CO2 by DAC. Main inputs for the process are electricity, heat and amine based sorbents. We assumed the ecoinvent process “RER: market for anionic resin” for the production of the amine based solid sorbents. Although the low-grade heat for the DAC plant in Hinwil is provided by the waste incineration plant, we considered a more general heat supply, using the ecoinvent process “CH: market for heat, district or industrial, natural gas.” This constitutes a worse case due to the heat supply from natural gas. Ecological improvements can be achieved by an advantageous heat supply instead of natural gas (e.g., waste heat from waste incineration as in Hinwil or from industrial processes).
To calculate the expenditures to build a DAC plant, 900 t of CO2 produced per year and a lifetime of 12 years were assumed. For construction 52 t of concrete, 93 t of gravel, 90 t of sand, 66.6 t of steel, 26.2 t of aluminum, 1.7 t of copper, 8.7 t of isolation material, and 1.1 t of sealing compound were considered (Lozanovski, 2019). Recycling of aluminum and steel was taken into account with recycling rates of 92% and 90%, respectively. We applied the usual avoided burden approach by giving the system a credit for possible metal recycling and thus avoiding the production of virgin metal. Further detailed LCI data regarding construction can be found in Supplementary Table S3.
Electricity Supply Mixes
The main energy input for the HT-co-electrolysis is electricity, which plays an important role. Hence, several future electricity supply mixes are considered, representing different assumptions for a future energy system. For the year 2050, four different electricity supply mixes were assumed, elaborated by the project partner TUM (Table 5). The electricity supply mixes base on two different CO2 reduction scenarios taken from the German Climate Action Plan 2050 (BMU, 2016). The calculations consider the specified target corridors of 80 and 95% greenhouse gas reduction up to 2050 compared to 1990 (climate protection target: CPT80, CPT95) (Repenning et al., 2015). A power plant deployment model is applied with spatial and hourly resolution for the German federal states. An economic optimization of the overall system is carried out to determine the power generation capacity (fossil power plants, expansion of renewable energies). The entire derivation of the electricity supply mixes as well as all assumptions and parameters are listed in the studies from TUM (Bareiß et al., 2018; Bareiß et al., 2019). Furthermore, for each CPT, an additional distinction is made regarding full load hours, which depend on the availability of renewable energy. The hours of generation of renewable electricity was calculated using the model of TUM (Table 5). The CPT with higher reduction targets results in a higher share of renewables and consequentially in higher operation hours of renewable technologies, 6,500 h (CPT95) compared to 3,000 h (CPT80). An operation of 8,760 h allows maximum capacity utilization of the HT-co-electrolysis. In case of the small-scale SMR, the German electricity mix 2014 is considered, because it represents today’s conventional technology. Thus, the LCA of the small-scale SMR represents the worst case in terms of the electricity supply mix.
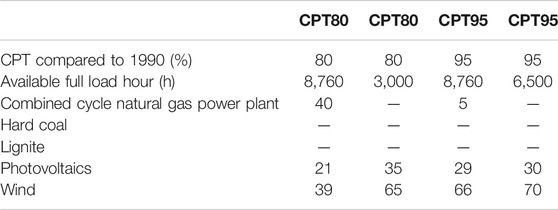
TABLE 5. Electricity supply mixes assumed for 2050 based on data from TUM (Bareiß et al., 2018; Bareiß et al., 2019).
More detailed information about LCI and LCIA of the electricity supply mixes are listed in Supplementary Tables S1 ans S2.
Results and Discussion of the Life Cycle Impact Assessment
Comparison of Syngas Production by High-Temperature Co-electrolysis and Small-Scale Steam Methane Reforming
The comparison of the environmental categories between small-scale SMR and HT-co-electrolysis per kg of syngas produced is shown in Figure 4 (see Supplementary Table S9 for raw data). The figure visualizes the main process segments including expenditures for CO2 provision by DAC, energy and water supply as well as the construction of the unit to show their contribution to the impacts. Additionally, for HT-co-electrolysis, the differences regarding the four electricity supply mixes, described above, are presented. In case of the small-scale SMR, natural gas supply as well as direct emissions during syngas production were considered supplementary. To display all impacts (unit: kg-eq.) in a single diagram, some of them had to be multiplied or divided by factors (e.g., 10, 100, 1,000; this procedure is applied for Figures 4, 6, and 10). The results show lower impacts for HT-co-electrolysis in terms of FD and GWP (Figure 4), while all other impacts are higher. For HT-co-electrolysis the electricity supply of approx. 9 kWh/kg syngas (Table 2) is the crucial segment regardless of the electricity supply mix. The emissions most contributing due to electricity supply are chromium (+VI) emissions into water (HTP), SO2 and NOx into air (AP), NOx into air (both POCPs), SO2 and particles (<2.5 µm) into air (PM) as well as indium (60%), silver (14%), cadmium (7%) and copper (4.5%) as resources (ADP). The ADP impacts occur during mining of raw materials and construction of power plants (fossil and renewable) and not during electricity generation. ADP for photovoltaics is highest followed by wind turbines and natural gas combined cycle power plants. The share of construction is higher for HT-co-electrolysis than for small-scale SMR, especially for ADP and HTP. The DAC is also clearly visible while the deionized water supply is negligible.
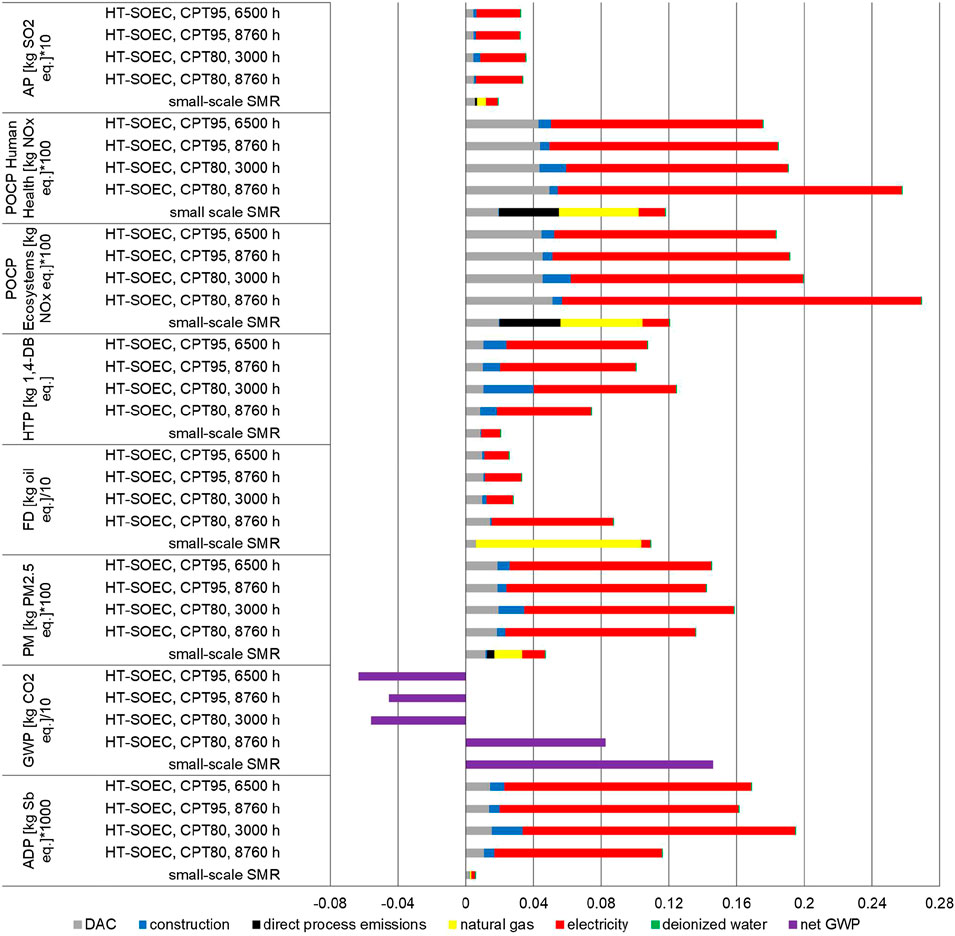
FIGURE 4. Environmental impacts of small-scale SMR and HT-co-electrolysis for 1 kg of syngas (molar ratio H2/CO = 2).
In case of the small-scale SMR, construction of the SMR plant and deionized water supply are negligible and are even lower in case of steel and nickel recycling. Direct process emissions are considerable for both POCPs and GWP. In case of POCP, direct NOx emissions account for 30% and NOx emissions caused by natural gas supply contribute to approx. 40% of the total POCP. Direct NOx emissions can be further reduced by enhanced burner technology and use of a DeNOx unit. It should be mentioned again that the LCIA is based on emission calculation and not on measured plant data. The share of CO2 supply by DAC on the total environmental impacts is quite noticeable and reaches approx. 40% for ADP and HTP, 30% for AP and still 26% for PM. The main reasons are the high electricity (0.5 kWh/kg CO2) and heat demands (1.5 kWh/kg CO2) for DAC (Table 4). Natural gas supply is the main cause for FD (approx. 90%) and contributes significantly to the other impacts too. It should be kept in mind that almost all values will be lower by more than 10% in case of large-scale reformer due to enhanced efficiency. In addition, FD and GWP will be significantly lower in case of biogas instead of natural gas as feed. As mentioned before, power supply is calculated with today’s electricity mix in case of the small-scale SMR. Hence, GWP and FD will become lower in case of applying a greener electricity mix.
For the 80% and 95% reduction scenarios, the energy supply mixes result in a reduction of conventional CHP from 40% to 5% and a considerable increase of wind (27%-points) and a smaller increase of photovoltaics (8%-points) (Table 5). This leads to an improvement of most environmental impacts. Only HTP, PM and ADP worsen, as gas supply has much lower impacts here than wind and photovoltaic electricity production. For CPT80, 8,760 h, 75% of the total ADP is caused by photovoltaics supply chain, 54% of HTP by wind power supply chain, an equal contribution of all to PM, and 61% of both POCPs by the natural gas-fired CHP. These contributions change for CPT95, 8,760 h to 73% photovoltaic to ADP, 64% wind to HTP, 50% photovoltaics to PM, and 48% photovoltaics and 41% wind, respectively, to both POCPs.
Differences between the full load hours are more prominent for CPT80. In case of CPT95, the differences in terms of environmental impacts are only marginal. The most obvious difference can be found in the share of plant construction, which increases for lower full load hours.
In summary, CPT95, 6,500 h shows the lowest environmental impacts in most categories, except for HTP, PM and ADP, where the change to more renewables has higher impacts. From a technical point of view, however, operation with less operation hours for HT-co-electrolysis is questionable, due to less syngas production, higher degradation and a shorter lifetime of cells and stacks. These aspects have not been considered in the calculation so far. In addition, operating the HT-co-electrolysis in dynamic mode results in severe technical challenges on plant operation, such as keeping temperature gradients low during ramp up and shut-down, which have not been solved by far. Nevertheless, flexibility of the HT-co-electrolysis is one of the most important factors to apply this technology for GWP reduction successfully, so further detailed assessment of fluctuation effects is mandatory. In order to bridge the fluctuations of renewable energies to achieve a high capacity utilization of HT-co-electrolysis, the use of temporary electricity storage is necessary. This is again associated with higher costs (Morgenthaler et al., 2020) and additional environmental impacts.
The discussion above shows the strong dependence of HT-co-electrolysis from the future electricity supply mix deployed, which depends on the CPT agreed upon. Using today's German electricity mix with approx. 0.48 kg CO2 eq. per kWh in 2017 (Juhrich, 2017) means that HT-co-electrolysis would not be competitive compared to the SMR. The GWP of HT-co-electrolysis would be 6.5 kg CO2 eq./kg syngas in contrast to 1.5 kg CO2 eq./kg syngas for small-scale SMR. In addition, all other impact categories would be worse than for small-scale SMR. This analysis underlines the necessity to switch to sustainable power production and also to produce additional green power for PtX processes.
The GWP due to the production of the syngas is reduced by the amount of CO2 separated from the atmosphere by DAC. In some cases the net GWP even becomes negative if the credit for CO2 capture from DAC is higher than the CO2 emissions from syngas production. To visualize this effect, Figure 5 focusses on GWP. The lowest GWP achieves HT-co-electrolysis using exclusively renewables in the CPT95 scenario. This is followed by the CPT80, 3,000 h, the CPT95, 8,760 h scenario and the small-scale SMR. Last is operation in the CPT80, 8,760 h scenario due to a high share of natural gas (40%) in this electricity supply mix. The share of natural gas in the electricity supply mix CPT95, 8,760 h amounts only to 5%. This low natural gas utilization is the reason for the low GWP, which is comparable to exclusively renewable operation (Supplementary Table S2).
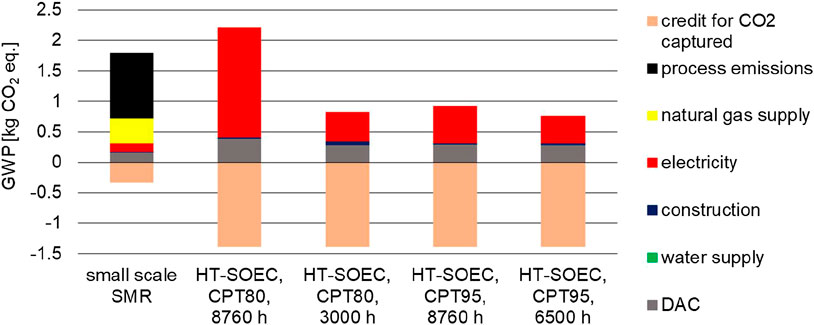
FIGURE 5. Share of process chain stages on the total GWP of 1 kg syngas (molar ratio H2/CO = 2) production by small-scale SMR and HT-co-electrolysis.
In Figure 5, GWP is divided into the individual process chain segments like plant construction as well as electricity, natural gas, and water supply. Also the expenditures to capture CO2 as well as the credit for the captured CO2 are displayed. The share of construction is hardly noticeable, and the supply of deionized water is not identifiable at all. In case of the small-scale SMR, the direct CO2 emissions caused by natural gas burning during syngas production have the highest share on the total GWP, followed by emissions caused by natural gas supply. The credit given for CO2 capture from atmosphere by DAC is higher for HT-co-electrolysis than for the small-scale SMR, due to the higher CO2 demand for producing 1 kg of syngas by HT-co-electrolysis (1.38 kg of CO2/kg syngas) than by small-scale SMR (0.33 kg of CO2/kg syngas) (Tables 2, 3). Incorporating the credit given for CO2 capture from atmosphere by DAC, the exclusively renewable operation (CPT80 and CPT95) and the HT-co-electrolysis operated by the CPT95, 8,760 mix achieve negative net GWP’s (purple bar in Figure 4).
Operating 8,760 h for CPT95 is the most favored scenario due to high syngas production capacity and acceptable environmental impacts.
Results Regarding Construction
Construction of both plants plays only a minor role in the overall environmental performance of syngas production (Figure 4). Nevertheless, it is necessary for developers of new technologies to be aware of possible risks posed by materials used. Details of material use for HT-co-electrolysis (Figure 6) and small-scale SMR (Figure 10) are presented. Figure 7 represents separated HT-co-electrolysis details for BoP components, Figure 8 for stack materials, and Figure 9 for single cells.
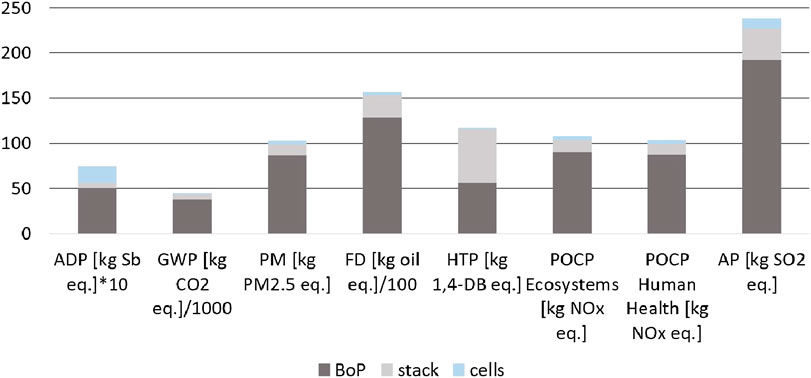
FIGURE 6. Environmental impacts of the HT-co-electrolysis subdivided in BoP, stack and single cells.
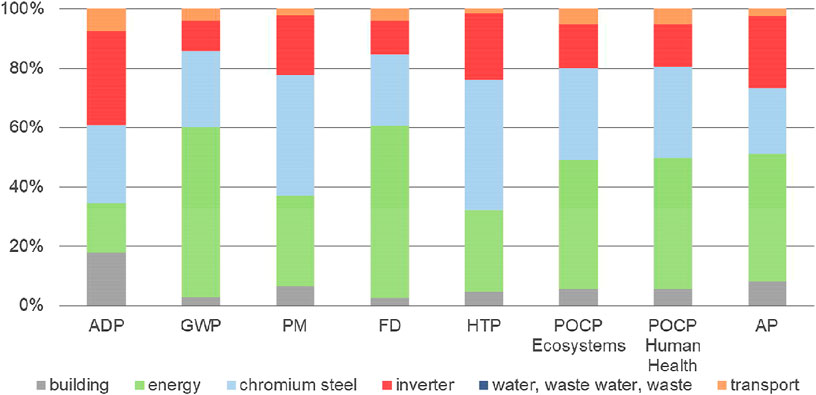
FIGURE 7. Share of materials and energy demand on the total environmental impacts of the BoP construction for HT-co-electrolysis.
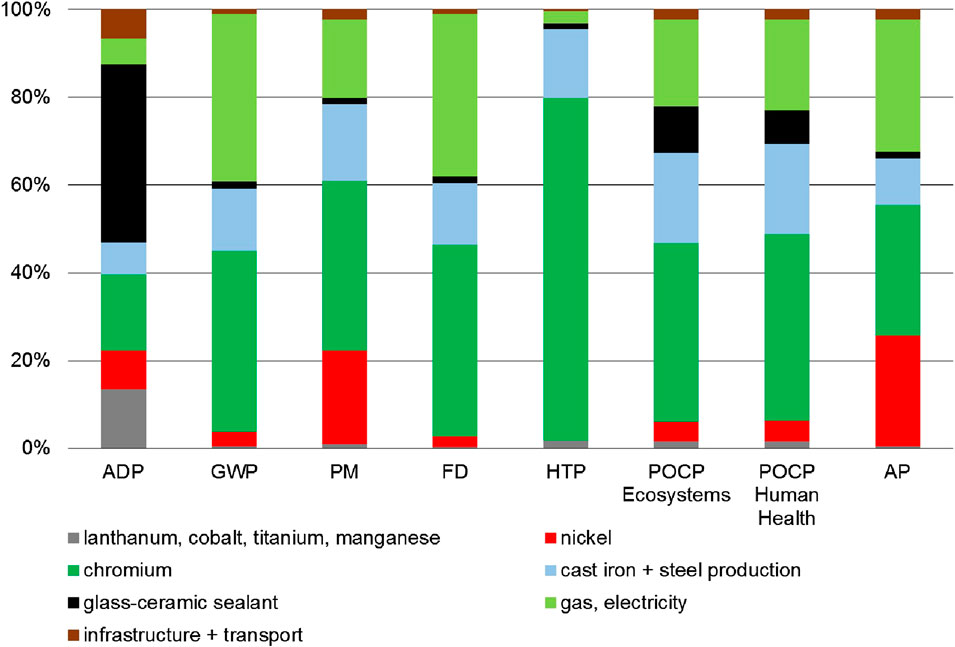
FIGURE 8. Share of stack materials, energy demand and others on the total environmental impacts of the stack construction for HT-co-electrolysis.
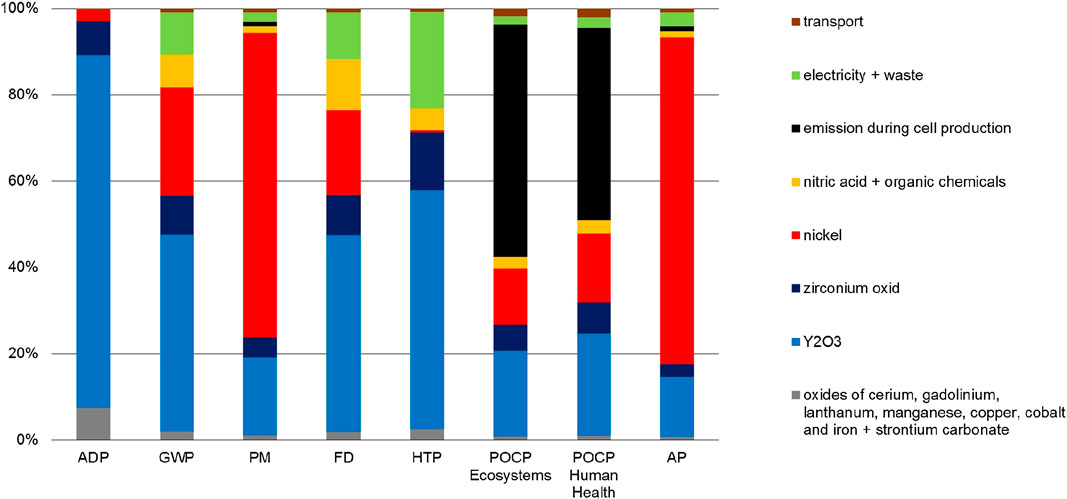
FIGURE 9. Share of cell materials, energy demand and others on the total environmental impacts of single cell construction for HT-co-electrolysis.
Construction of High-Temperature Co-Electrolysis
In case of HT-co-electrolysis, the BoP has almost always a share of more than 80% on the total environmental effects of plant construction with the exception of ADP (70%) and HTP (50%) (Figure 6).
For BoP construction, 17% (ADP) up to 58% (GWP and FD) of all impacts are due to energy supply (Figure 7). Chromium steel causes 22% (AP)–44% (HTP) of the total impacts of BoP and 10–32% are caused by the inverter (Figure 7). The impacts associated with the building are low and only noticeable in the case of ADP (20%).
On the overall plant construction the stacks cause 8–16% on the total impacts with the exception of HTP (50%) (Figure 6). Reason for the latter is the high chromium content in the stack material Crofer22APU (Figure 8). Within the stack, approx. 40% of the resource depletion (ADP) are allotted to the glass-ceramic sealant due to the use of yttrium oxide (67%), barium oxide (25.5%) and 6% zirconium oxide (Figure 8). Gas and electricity demand required for stack construction (e.g., laser cutting, annealing, grinding of gas channels, sand blasting, ultrasonic cleaning, APS-coating, spot welding, assembly) accounts to 20–40% except for ADP (6%) and HTP (3%). Nickel, which is required for the nickel meshes, is responsible for approx. 20% of AP and PM. The chromium content in the Crofer22APU is the main causer of almost all impact categories.
The single cells are only responsible for less than 5% of each impact on the total construction impacts with the exception of ADP (23%) (Figure 6). The main contributor for this is yttrium oxide used in 8YSZ for substrate, electrolyte, and cathode material (Figures 3, 9). The other REE’s (cerium, gadolinium, lanthanum) and metal oxides of strontium, zirconium, cobalt and iron account for only 7% of the ADP and 1–2% of the other impacts. During cell production, NMVOC and NOx are emitted due to losses of solvent and nitric acid, respectively. These emissions are responsible for both POCP impacts. Again, the nickel supply chain is the main contributor to AP (75%) and PM (70%). Nickel is required for the nickel cermet NiO/8YSZ used as substrate and cathode material. Although some sintering processes at high temperature are required for single cell production, the electricity demand is hardly visible for almost all impact categories.
Summarizing, a significant reduction of environmental impacts regarding construction can be achieved by reducing the quantity of steel. Here other stack concepts, for example with thinner interconnectors, and material recycling could be helpful.
Construction of Small-Scale Steam Methane Reformer
In case of small-scale SMR construction, the main part of the environmental impacts are caused by 34.5 tons of low-alloyed and unalloyed steel. Five hundred kg of nickel causes 30% of PM and ADP, and even 45% of AP. One thousand four hundred kg of chromium steel are responsible for 6% AP, 10% PM and HTP, and 20% ADP. One hundred tons of concrete have a considerable effect on GWP (10%) (Figure 10). In case of steel and nickel recycling, the small impacts of construction (Figure 4) can be reduced even further.
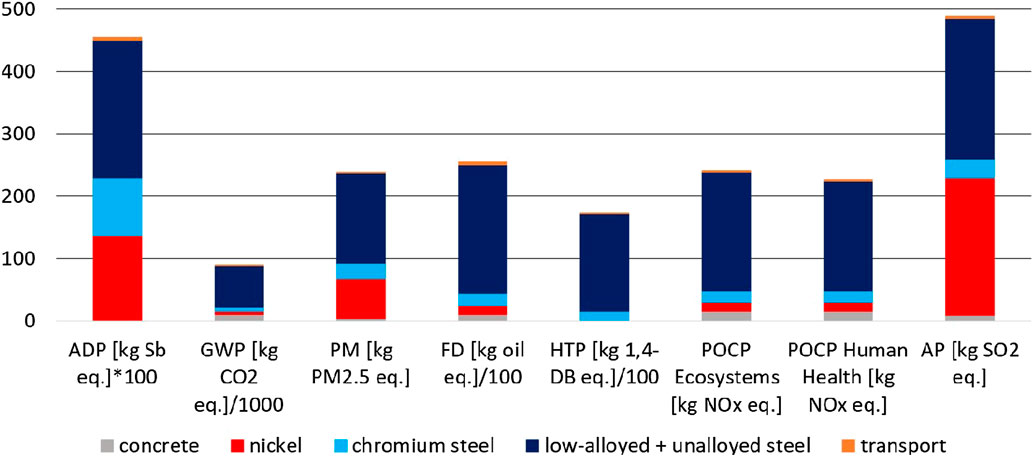
FIGURE 10. Environmental impacts of the small-scale SMR plant subdivided according to the materials used.
Conclusion
In this paper, we analyzed the following two Power-to-syngas production pathways: HT-co-electrolysis as a new PtX technology with a low TRL and SMR as their well-established fossil-based counterpart designed as a small-scale system for decentralized operation. This smaller type of SMR has a lower efficiency than the large SMR plants, because it is less energetically optimized for economic and technical reasons. The evaluation of the environmental performance of HT-co-electrolysis at an early stage of development was used to derive incentives for further research. In a HT-co-electrolysis, syngas is synthesized from conversion of CO2 and steam. As CO2 source, we considered DAC as a future capture technology to keep the long-term perspective of PtX in mind and be independent of local CO2 sources. Due to the high importance of electricity as main input for HT-co-electrolysis, we included various future electricity supply mixes taking into account different CO2 reduction targets and different full load hours due to the availability of renewable energies. This resulted in four different electricity supply scenarios.
The results of cradle-to-gate LCA without considering syngas use indicate advantages of HT-co-electrolysis compared to the small-scale SMR in terms of GWP and FD if mostly renewable energy is used. Exclusively renewable operated HT-co-electrolysis achieves negative specific net GWPs, however resulting in lower operation hours and therefore less syngas production per year. In case of CPT80, only 3,000 h operation hours are achieved, which would hinder market penetration of a novel technology. In addition, the investment costs would be high and too many load changes would make operation difficult, which would have a negative effect on the lifetime of cell and plant. Subsequent syngas using processes such us Fischer-Tropsch require higher and continuous amounts of syngas. If HT-co-electrolysis shall operate continuously (8,760 h) additional fossil-based electricity is needed. For CPT80, the share of fossil electricity is still high, so that negative net GWPs cannot be achieved. Targeting CPT95 requires a higher share of renewable electricity, which results in negative net GWP also for 8,760 h. Using today's German electricity mix, HT-co-electrolysis would be far from competitive with respect to GWP of 6.5 kg CO2 eq./kg syngas compared to that of the SMR even at small-scale (1.5 kg CO2 eq./kg syngas All other environmental impacts are lower for small-scale SMR, particularly due to the high electricity demand of the HT-co-electrolysis and the associated renewable electricity supply chains. While wind and PV technologies produce no emissions during electricity generation, they are associated with impacts during construction.
Besides electricity supply, the CO2 supply is also crucial for the environmental performance of Power-to-syngas pathways. The syngas production can achieve lower global warming impacts if, e.g., CO2 is captured from flue gases or from chemical process, which would emit the CO2 otherwise. Using existing capture technologies, the energy demand for separation at industrial sites is lower than for DAC. The contribution of the CO2 supply would be reduced accordingly. This holds true for both HT-co-electrolysis and SMR.
One frequently used argument pro PtX is the potential to balance the power production and consumption in case of a large share of renewable power production. Intermittent renewable electricity could be directly used by HT-co-electrolysis, especially when more renewables have to be fed into the grid. However, offering flexibility must be carefully examined and decided on a case-by-case basis (Ausfelder et al., 2019). The advantage of flexible operation can turn into a disadvantage, as it results in higher cell and plant degradation and a shorter lifetime as well as more complicated operation and difficult integration with downstream production. Although degradation was not further analyzed in this paper, the need to focus further research on materials and processing which lower degradation potentials can be pointed out.
To use our results in a discussion about potentials of defossilization of the economy, the syngas production needs to be integrated into a wider picture. The subsequent processing of syngas to chemicals and fuels should be considered in further analysis in order to assess the full potential of HT-co-electrolysis. In addition, alternative PtX pathways need to be analyzed on the same basis and compared to each other.
Overall, the results show that HT-co-electrolysis is a promising technology to integrate renewable electricity into the chemistry and transport sector and to decrease dependence on fossil feedstock. Together with changes in the electricity sector, HT-co-electrolysis can contribute to the overall defossilization of the economy. Other technology options using captured CO2 for syngas production such as rWGS or dry reforming with additional H2 import produced from renewable power may also contribute to the defossilization. Hence, HT-co-electrolysis is one technological option for defossilization of the economy among others. Further sustainability assessments of various PtX technologies need to follow.
Data Availability Statement
All datasets generated for this study are included in the manuscript/Supplementary Material.
Author Contributions
AS: conceptualization, life cycle assessment and writing. AP and BH: technical calculation. PZ: project administration and validation.
Funding
The authors gratefully acknowledge funding by the German Federal Ministry of Education and Research (BMBF) within the Kopernikus Project P2X: Flexible use of renewable resources–exploration, validation and implementation of “Power-to-X” concepts.
Conflict of Interest
The authors AP and BH were employed by the company Linde AG.The remaining authors declare that the research was conducted in the absence of any commercial or financial relationships that could be construed as a potential conflict of interest.
Acknowledgments
The information and advice applied from L. Blum (Institute of Energy and Climate Research, IEK-3, Electrochemical Process Engineering), N.H. Menzler (Institute of Energy and Climate Research, IEK-1, Materials Synthesis and Processing) and N. Margaritis (Central Institute for Engineering, Electronics and Analytics, ZEA-1, Engineering and Technology) from Forschungszentrum Jülich are gratefully acknowledged.
Supplementary Material
The Supplementary Material for this article can be found online at: https://www.frontiersin.org/articles/10.3389/fenrg.2020.533850/full#supplementary-material
References
Adibi, N., Lafhaj, Z., and Payet, J. (2019). New resource assessment characterization factors for rare earth elements: applied in NdFeB permanent magnet case study. Int. J. Life Cycle Assess. 24, 712–724. doi:10.1007/s11367-018-1489-x.
Al-Kalbani, H., Xuan, J., García, S., and Wang, H. (2016). Comparative energetic assessment of methanol production from CO2: chemical versus electrochemical process. Appl. Energy 165, 1–13. doi:10.1016/j.apenergy.2015.12.027.
Anicic, B., Trop, P., and Goricanec, D. (2014). Comparison between two methods of methanol production from carbon dioxide. Energy 77, 279–289. doi:10.1016/j.energy.2014.09.069.
Artz, J., Müller, T. E., Thenert, K., Kleinekorte, J., Meys, R., Sternberg, A., et al. (2018). Sustainable conversion of carbon dioxide: an integrated review of catalysis and life cycle assessment. Chem. Rev. 118 (2), 434–504. doi:10.1021/acs.chemrev.7b00435.
Ausfelder, F., Bareiß, K., Deutz, S., Dura, H., Forster, S., Fröhlich, T., et al. (2019). “Roadmap des Kopernikus-Projekts “Power-to-X”: flexible Nutzung erneuerbarer Ressourcen (P2X),” in Optionen für ein nachhaltiges Energiesystem mit Power-to-X Technologien. Nachhaltigkeitseffekte – potenziale Entwicklungsmöglichkeiten. F. Ausfelder and H. Dura (Editors) (Frankfurt am Main: DECHEMA Gesellschaft für Chemische).
Baltrusaitis, J., and Luyben, W. L. (2015). Methane conversion to syngas for gas-to-liquids (GTL): is sustainable CO2 reuse via dry methane reforming (DMR) cost competitive with SMR and ATR processes? ACS Sustain. Chem. Eng. 3 (9), 2100–2111. doi:10.1021/acssuschemeng.5b00368.
Bareiß, K., de la Rua, C., Möckl, M., and Hamacher, T. (2019). Life cycle assessment of hydrogen from proton exchange membrane water electrolysis in future energy systems. Appl. Energy 237, 862–872. doi:10.1016/j.apenergy.2019.01.001.
Bareiß, K., Schönleber, K., and Hamacher, T. (2018). Szenarien für den Strommix zukünftiger, flexibler Verbraucher am Beispiel von P2X-Technologien. Munich: Technische Universität München, Lehrstuhl für Erneuerbare und Nachhaltige Energiesysteme).
Bauer, F., and Sterner, M. (2020). Power-to-X im Kontext der Energiewende und des Klimaschutzes in Deutschland. Chem. Ing. Tech. 92 (1–2), 85–90. doi:10.1002/cite.201900167.
BMU (2016). Klimaschutzplan 2050 – klimaschutzpolitische Grundsätze und Ziele der Bundesregierung". Bundesministerium für Umwelt, Naturschutz, Bau und Reaktorsicherheit. Available at: https://www.bmu.de/fileadmin/Daten_BMU/Download_PDF/Klimaschutz/klimaschutzplan_2050_bf.pdf.
Bracker, J. (2017). An outline of sustainability criteria for synthetic fuels used in transport - policy paper for Transport & Environment. Freiburg, Germany: Öko-Institut e.V.
Chehade, Z., Mansilla, C., Lucchese, P., Hilliard, S., and Proost, J. (2019). Review and analysis of demonstration projects on power-to-X pathways in the world. Int. J. Hydrogen Energy 44 (51), 27637–27655. doi:10.1016/j.ijhydene.2019.08.260.
Climeworks (2017). Available at: http://www.climeworks.com/. (Accessed April 04, 2019) (Online).
Ecoinvent (2016). Life cycle inventory database Version 3.3 (St. Gallen (Switzerland): Swiss Center for Life Cycle Inventory).
European Commission (2020). Proposal for a regulation of the European Parliament and of the Council establishing the framework for achieving climate neutrality and amending Regulation (EU) 2018/1999 (European climate law) (Brussels: COM). (Accessed April 03, 2020). COM(2020) 80 final.
European Council (2014). Agreement on climate framework until 2030. Available at: https://www.bundeskanzlerin.de/bkin-de/angela-merkel/terminkalender/reiseberichte/einigung-auf-klimarahmen-bis-2030-426584. (Accessed April 10, 2019) (Online).
Evans, S. (2017). Available at: https://www.carbonbrief.org/swiss-company-hoping-capture-1-global-co2-emissions-2025. (Accessed June 22, 2020) (Online).
Faist-Emmenegger, M., Heck, T., Jungbluth, N., and Tuchschmid, M. (2007). “Erdgas,” in Sachbilanzen von Energiesystemen: grundlagen für den ökologischen Vergleich von Energiesystemen und den Einbezug von Energiesystemen in Ökobilanzen für die Schweiz. Final report ecoinvent No. 6-V. R. Dones (Editor) (Dübendorf, Switzerland: Paul Scherrer Institut Villigen, Swiss Centre for Life Cycle Inventories).
Fang, Q., Blum, L., Peters, R., Peksen, M., Batfalsky, P., and Stolten, D. (2015). SOFC stack performance under high fuel utilization. Int. J. Hydrogen Energy 40 (2), 1128–1136. doi:10.1016/j.ijhydene.2014.11.094.
Fasihi, M., Efimova, O., and Breyer, C. (2019). Techno-economic assessment of CO2 direct air capture plants. J. Clean. Prod. 224, 957–980. doi:10.1016/j.jclepro.2019.03.086.
Foit, S. R., Vinke, I. C., de Haart, L. G. J., and Eichel, R.-A. (2016). Power-to-Syngas – an enabling technology for the transition of the energy system? Angew. Chem. Int. Ed. 56 (20), 5402–5411. doi:10.1002/anie.201607552.
Frey, C. E., Fang, Q., Sebold, D., Blum, L., and Menzler, N. H. (2018). A detailed post mortem analysis of solid oxide electrolyzer cells after long-term stack operation. J. Electrochem. Soc. 165 (5), F357–F364. doi:10.1149/2.0961805jes.
Goedkoop, M., Heijungs, R., Huijbregts, M. A. J., De Schryver, A., Struijs, J., and Van Zelm, R. (2009). “ReCiPe 2008. A life cycle impact assessment method which comprises harmonised category indicators at the midpoint and the endpoint level,” in Report I: characterisation factors. 1st Edn. (Den Haag, Netherlands: Ministerie van Volkshuisvesting, Ruimtelijke Ordening en Milieubeheer (VROM)). Available at: www.vrom.nl
Groß-Barsnick, S.-M., Margaritis, N., Haart, U. d., Huczkowski, P., and Quadakkers, W. J. (2018). “Interaction of a barium-calcium-silicate glass composite sealant with Sanergy HT 441,” in Proceedings of the 13th European SOFC & SOE forum. E. Ivers-Tiffée, C. Endler-Schuck, A. Leonide, A. Weber, A. Häffelin, J.-C. Njodzefon, et al. ( s). (Lucerne, Switzerland: European Fuel Cell Forum AG), 9–18.
Harboe, S., Schreiber, A., Margaritis, N., Blum, L., Guillon, O., and Menzler, N. H. (2020). Manufacturing cost model for planar 5 kWel SOFC stacks at Forschungszentrum Jülich. Int. J. Hydrogen Energy 45 (15), 8015–8030. doi:10.1016/j.ijhydene.2020.01.082.
Heinemann, C., Kasten, P., Bauknecht, D., Bracker, J. F., Bürger, V., Emele, L., et al. (2019). “Die Bedeutung strombasierter Stoffe für den Klimaschutz in Deutschland. Zusammenfassung und Einordnung des Wissenstands zur Herstellung und Nutzung strombasierter Energieträger und Grundstoffe,” in Kopernikus-Projekt: ENSURE – neue EnergieNetzStruktURen für die Energiewende (Freiburg, Berlin, Darmstadt: Öko-Insitut), Förderkennzeichnen 03SFK1TO.
House, K. Z., Baclig, A. C., Ranjan, M., van Nierop, E. A., Wilcox, J., and Herzog, H. J. (2011). Economic and energetic analysis of capturing CO2 from ambient air. Proc. Natl. Acad. Sci. Unit. States Am. 108 (51), 20428–20433. doi:10.1073/pnas.1012253108.
International Organization for Standardization (ISO) (2006a). ISO 14040: environmental management - life cycle assessment - principles and framework". Geneva, Switzerland: ISO.
International Organization for Standardization (ISO) (2006b). ISO 14044: environmental management - life cycle assessment - requirements and guidelines. Geneva, Switzerland: ISO.
Kätelhön, A., Meys, R., Deutz, S., Suh, S., and Bardow, A. (2019). Climate change mitigation potential of carbon capture and utilization in the chemical industry. Proc. Natl. Acad. Sci. Unit. States Am. 116 (23), 11187–11194. doi:10.1073/pnas.1821029116.
Koj, J. C., Wulf, C., and Zapp, P. (2019). Environmental impacts of power-to-X systems - a review of technological and methodological choices in Life Cycle Assessments. Renew. Sustain. Energy Rev. 112, 865–879. doi:10.1016/j.rser.2019.06.029.
Linde, A. G. (2019). HYDROPRIME®-Wasserstoffgeneratoren [Online]. Available at: https://www.linde-engineering.com/de/process-plants/furnaces_fired_heaters_incinerators_and_t-thermal/steam_reformer_furnaces/index/hydroprime.html (Accessed September 16, 2019).
Liu, C. M., Sandhu, N. K., McCoy, S. T., and Bergerson, J. A. (2020). A life cycle assessment of greenhouse gas emissions from direct air capture and Fischer–Tropsch fuel production. Sustain. Energy Fuels 4 (6), 3129–3142. doi:10.1039/C9SE00479C.
Lozanovski, A. (2019). Life cycle assessment of a commercial scale CO2 - direct air capture plant,” in 17th international conference on carbon dioxide utilization (ICCDU). (Aachen, Germany: DECHEMA).
Luu, M. T., Milani, D., Bahadori, A., and Abbas, A. (2015). A comparative study of CO2 utilization in methanol synthesis with various syngas production technologies. J. CO2 Util. 12, 62–76. doi:10.1016/j.jcou.2015.07.001.
Menzler, N. H., Malzbender, J., Schoderböck, P., Kauert, R., and Buchkremer, H. P. (2014). Sequential tape casting of anode-supported solid oxide fuel cells. Fuel Cells 14 (1), 96–106. doi:10.1002/fuce.201300153.
Morgenthaler, S., Kuckshinrichs, W., and Witthaut, D. (2020). Optimal system layout and locations for fully renewable high temperature co-electrolysis. Appl. Energy 260 (15). doi:10.1016/j.apenergy.2019.114218.
Müller, L. J., Kätelhön, A., Bachmann, M., Zimmermann, A., Sternberg, A., and Bardow, A. (2020). A guideline for life cycle assessment of carbon capture and utilization. Front. Energy Res. 8 (15). doi:10.3389/fenrg.2020.00015.
Pehnt, M. (2002). Ganzheitlichen Bilanzierung von Brennstoffzellen in der Energie- und Verkehrstechnik,” in Fortschrittsberichte VDI, reihe 6, energietechnik, Nr. 476 (Düsseldorf: VDI Verlag).
Peschel, A. (2020). Industrial perspective on hydrogen purification, compression, storage, and distribution. Fuel Cells 20 (4). doi:10.1002/fuce.201900235
Primas, A. (2007). Life cycle inventories of new CHP systems,” in Ecoinvent report (Basler & Hofmann AG, Dubendorf, & Zurich: Swiss Centre for Life cycle Inventories).
Quadakkers, W. J., Pirón-Abellán, J., and Shemet, V. (2004). Metallic materials in solid oxide fuel cells. Mater. Res. 7, 203–208. doi:10.1590/S1516-14392004000100027
Reiter, G., and Lindorfer, J. (2015). Global warming potential of hydrogen and methane production from renewable electricity via power-to-gas technology. Int. J. Life Cycle Assess. 20 (4), 477–489. doi:10.1007/s11367-015-0848-0.
Repenning, J., Emele, L., Blanck, R., Böttcher, H., Dehoust, G., Förster, H., et al. (2015). Klimaschutzszenario 2050 - 2. Endbericht (Berlin, Karlsruhe: Studie im Auftrag des Bundesministeriums für Umwelt, Naturschutz, Bau und Reaktorsicherheit).
Rostrup-Nielson, J. R. (2005). “Natural gas: fuel or feedstock?,” in Sustainable strategies for the upgrading of natural gas: fundamentals, challenges, and opportunities. Proceedings of the NATO advanced study Institute, Vilamoura, Portugal, July 6–18, 2003. E.G. Derouane, V. Parmon, F. Lemos, and F. R. Ribeiro (Editors) (Dordrecht, Netherlands: Springer Netherlands).
RWE (2019). Niederaußem ist Schauplatz wichtiger technologischer fortschritte [Online]. Köln, 28.05.2019. Available at: https://www.group.rwe/presse/rwe-power/2019-05-28-niederaussem-ist-schauplatz-wichtiger-technologischer-fortschritte (Accessed January 15, 2020).
Sanz-Pérez, E. S., Murdock, C. R., Didas, S. A., and Jones, C. W. (2016). Direct capture of CO2 from ambient air. Chem. Rev. 116 (19), 11840–11876. doi:10.1021/acs.chemrev.6b00173.
Schafbauer, W., Menzler, N. H., and Buchkremer, H. P. (2014). Tape casting of anode supports for solid oxide fuel cells at Forschungszentrum Jülich. Int. J. Appl. Ceram. Technol. 11 (1), 125–135. doi:10.1111/j.1744-7402.2012.02839.x.
Sternberg, A., and Bardow, A. (2016). Life cycle assessment of power-to-gas: syngas vs methane. ACS Sustain. Chem. Eng. 4 (8), 4156–4165. doi:10.1021/acssuschemeng.6b00644.
Sternberg, A., and Bardow, A. (2015). Power-to-what?–environmental assessment of energy storage systems. Energy Environ. Sci. 8 (2), 389–400. doi:10.1039/C4EE03051F.
Sternberg, A., Jens, C. M., and Bardow, A. (2017). Life cycle assessment of CO2-based C1-chemicals. Green Chem. 19 (9), 2244–2259. doi:10.1039/C6GC02852G.
Thema, M., Bauer, F., and Sterner, M. (2019). Power-to-Gas: electrolysis and methanation status review. Renew. Sustain. Energy Rev. 112, 775–787. doi:10.1016/j.rser.2019.06.030.
thinkstep (2018). GaBi (ganzheitliche bilanzierung) version 8.7.018. Available: https://www.thinkstep.com/software/gabi-lca/ [Dataset].
Uniper SE (2019). Methanisierungsanlage in Falkenhagen geht in Betrieb und liefert synthetisches Methan – weiterer Schritt für eine erfolgreiche Energiewende [Online]. Düsseldorf. Available at: https://www.uniper.energy/news/methanisierungsanlage-in-falkenhagen-geht-in-betrieb-und-liefert-synthetisches-methan--weiterer-schritt-fur-eine-erfolgreiche-energiewende/ (Accessed January 15, 2020).
van der Giesen, C., Kleijn, R., and Kramer, G. J. (2014). Energy and climate impacts of producing synthetic hydrocarbon fuels from CO2. Environ. Sci. Technol. 48 (12), 7111–7121. doi:10.1021/es500191g.
von der Assen, N., Müller, L. J., Steingrube, A., Voll, P., and Bardow, A. (2016). Selecting CO2 sources for CO2 utilization by environmental-merit-order curves. Environ. Sci. Technol. 50 (3), 1093–1101. doi:10.1021/acs.est.5b03474.
Wulf, C., Linßen, J., and Zapp, P. (2018). Review of power-to-gas projects in Europe. Energy Procedia 155, 367–378. doi:10.1016/j.egypro.2018.11.041.
Zhang, X., Bauer, C., Mutel, C. L., and Volkart, K. (2017). Life Cycle Assessment of Power-to-Gas: approaches, system variations and their environmental implications. Appl. Energy 190, 326–338. doi:10.1016/j.apenergy.2016.12.098.
Zheng, Y., Wang, J., Yu, B., Zhang, W., Chen, J., Qiao, J., et al. (2017). A review of high temperature co-electrolysis of H2O and CO2 to produce sustainable fuels using solid oxide electrolysis cells (SOECs): advanced materials and technology. Chem. Soc. Rev. 46 (5), 1427–1463. doi:10.1039/C6CS00403B.
Keywords: life cycle assessment, power-to-syngas, small-scale steam methane reforming, high-temperature co-electrolysis, solid oxide electrolysis cell, direct air capture
Citation: Schreiber A, Peschel A, Hentschel B and Zapp P (2020) Life Cycle Assessment of Power-to-Syngas: Comparing High Temperature Co-Electrolysis and Steam Methane Reforming. Front. Energy Res. 8:533850. doi: 10.3389/fenrg.2020.533850
Received: 10 February 2020; Accepted: 01 October 2020;
Published: 09 November 2020.
Edited by:
David Parra, Université de Genève, SwitzerlandReviewed by:
Xun Liao, École Polytechnique Fédérale de Lausanne, SwitzerlandJohannes Lindorfer, Energy Institute at Johannes Kepler University, Austria
Copyright © 2020 Schreiber, Peschel, Hentschel and Zapp. This is an open-access article distributed under the terms of the Creative Commons Attribution License (CC BY). The use, distribution or reproduction in other forums is permitted, provided the original author(s) and the copyright owner(s) are credited and that the original publication in this journal is cited, in accordance with accepted academic practice. No use, distribution or reproduction is permitted which does not comply with these terms.
*Correspondence: Andrea Schreiber, YS5zY2hyZWliZXJAZnotanVlbGljaC5kZQ==