- 1Faculty of Engineering Science, University of Greenwich, Chatham, United Kingdom
- 2Carbon8 Systems Ltd., Chatham, United Kingdom
Carbon capture, utilization, and storage (CCUS) is a technology approach to the management of anthropogenic carbon dioxide gas emissions to the atmosphere. By injecting CO2 into host rocks, or by employing a an ex situ application step, geological formations can react with and store huge volumes of CO2 as carbonate minerals. An alternative mineral feedstock material is the Gt of industrial process wastes that are often disposed to landfill. By applying an accelerated carbonation step to solid waste, there is potential to sequestrate meaningful quantities of CO2 in carbonate-cemented products that have reuse potential. The manufacture of carbonated aggregates is commercially established in Europe, and recent advances in technology include a mobile plant that directly utilizes flue-gas derived CO2 in the mineralisation process. The present work discusses the basis for mineralization in geologically derived minerals and industrial wastes, with a focus being on the manufacture of products with value. An assessment of mineralized construction aggregates suggests that carbon capture, utilization, and storage technology can manage significant quantities of this CO2.
Introduction
As carbon dioxide (CO2) in the atmosphere increases due to anthropogenic activities, natural ecosystems are losing their ability to absorb this greenhouse gas (GHG). The major contributor of CO2 to the atmosphere is generated from burning fossil fuels, biofuels, and wood. By way of context, a large thermal power station can easily emit more than 20 Mt of CO2 each year (Armstrong et al., 2019).
The IPCC (2014) predicts that if GHG emissions continue, the global temperature will rise between 3.7 and 4.8°C by 2100. To reach the limit of 1.5°C, CO2 emissions need to be reduced by 45% from 2010 levels by 2030 and net-zero emissions by 2050. The special IPCC (2018) report gives a revised target of <1.5°C temperature rise and emphasizes the need for further emission reductions1 (IPCC, 2018).
The prospect of mitigating anthropogenic CO2 emissions by carbon capture and storage (CCS) is attractive. By injecting CO2, as a supercritical fluid, into porous rock strata in the geosphere, it is predicted that large amounts (Gt) of carbon can be managed this way. Injection into the deep ocean water column (>1,000 m), where CO2 will remain dissolved for centuries, is also being suggested (UNESCO-IOC/SCOR, 2007). However, these processes are not yet commercially or technically viable, and alternative options for sequestrating CO2 are required. Discussed later is an approach based on nature.
Reaction of Carbon Dioxide With Mineral Systems
Mineralization is nature’s way to sequester CO2, but it is a slow process. The hydrolysis of CO2 in moist air or water is a major driver of rock chemical weathering. The geological record indicates that tectonic forcing exposes large rock masses to the atmosphere and subsequent weathering occurs at a rate that can markedly reduce atmospheric CO2 levels (Raymo and Ruddiman, 1992). Notwithstanding that natural weathering can remove some 30 Gt of CO2 from the atmosphere each century, it is this natural process that has the potential to be accelerated and, therefore, industrialized. In this way, anthropogenic CO2 can combine with a reactive substrate to form a mineralized product—carbonate salts, for ultimate disposal or conversion into valorized products. Mineralized products have the potential to be beneficially utilized in quantities that can ultimately reduce the effects of global warming. The common rock types and their reaction with CO2 gas are discussed by Penner (2004) and Zevenhoven (2004).
Carbon Capture, Utilization, and Storage
The concept of managed mineralization offers an environmentally sustainable opportunity that can work in synergy with carbon capture and storage. By incorporating a “utilization” option within a “storage” concept, captured CO2 can be used as a feedstock for making products, products in which CO2 gas is sequestered permanently. This unison is known as carbon capture, utilization, and storage (CCUS).
It is not widely appreciated that CO2 gas has been used for centuries as a feedstock in industrial processes. Uses extend from carbonating beverages (18th Century) to the application of supercritical CO2 in the manufacture of instant coffee, pharmaceuticals (20th Century), or construction materials (21st Century).
CO2 gas-enhanced curing chambers have been utilized for conditioning and accelerating the hardening of cementitious materials since the 19th century (e.g., Rowland, 1870), as alkaline materials tend to be very CO2 reactive. The tendency of minerals to react with CO2 under the right conditions can be harnessed for CCUS, using both in situ and ex situ processing methods. By way of example of the former, Kelemen et al. (2019) report the application of CO2-rich fluid rather than natural water, in the in situ treatment of peridotite. In this approach, the dissolution of peridotite (and hence its carbonate-ability) can be increased by five orders of magnitude.
Rock masses found in the geosphere that are materially suitable for managed carbonation are ubiquitous, and the carbonated reaction products are stable in the geosphere. The National Academies of Sciences Engineering Medicine [NASEM] (2019) states that significant health and environmental benefits can arise from carbon mineralization, as the formation of carbonate is the safest carbon “storage” mechanism (Zhang and DePaolo, 2017).
The application of in situ mineralization technology has been described as mineral trapping or managed weathering and is simply an accelerated weathering step. Silicate rocks are the most suitable host rock formations for mineralized carbon, with the rate of carbonate mineral production being kinetically controlled. Huijgen and Comans (2003) and Zevenhoven and Fagerlund (2010) have reviewed the mineralization of CO2. As mineral carbonation is an analog of natural weathering, the reaction between CO2 and suitable silicate rocks can be summarized as (Equation 1):
If we consider the course of natural weathering of olivine (Mg2SiO4) or serpentine [Mg3Si2O5(OH4)], it is the dissolution and ionization of CO2 in the rain or groundwater that produces carbonic acid. This, in turn, dissociates into H+ and HCO or bicarbonate. As bicarbonate is conjugate acidic, it can chemically degrade susceptible minerals, liberating calcium and magnesium, which then bind with the bicarbonate to form solid carbonates. Beaulieu et al. (2012) estimate that 300 Mt of CO2 gas is removed from the atmosphere via weathering and carbonate formation each year.
Potential geological storage “reservoirs” for mineralized CO2 involve igneous (flood basalts, pillow lavas, and ultramafic rocks, such as peridotite), metamorphic (serpentinites and ophiolites), and perhaps, surprisingly, sedimentary rock formations, such as glauconitic and hematite-cemented sandstones. In respect of the latter, hematite has the potential to form siderite (FeCO3) or ankerite (CaCO3, MgCO3, and FeCO3), when Fe3+ is reduced to Fe2+. Arkosic sandstones, containing feldspar, are also a potential target host rock formation. Plagioclase (anorthite) found in igneous rocks and arkose may be a mineral suitable for carbonation; its reaction with CO2 gas is summarized below (Equation 2):
Of particular interest are flood basalts with high porosity and a linked vesicular structure. These potential host rocks extend to thousands of cubic kilometers but can be geographically isolated, as are pillow lavas. Where basalt formations are saline, stable carbonates, including calcite, magnesite, and siderite, may be expected to form on contact with H2CO. Groundwater permeation through ultramafic rocks, such as dunite, is accompanied by the dissolution of alkali and precipitation of carbonate (Canovas et al., 2017; Vankeuren et al., 2019).
The reaction rate of rock-forming minerals varies considerably, with wollastonite being one of the “fastest” and, hence, most reactive to CO2. The dissolution of some common minerals at 25 and 180°C is discussed by National Academies of Sciences Engineering Medicine [NASEM] (2019). It should be noted that at higher temperatures, the rate of dissolution of minerals increases. By way of example, albite dissolution increases from an approximate log dissolution rate of between −11.5 and −12.5 at 25°C to −7.6 and −8.5 at 180°C. For olivine, a similar trend is observed, as the log dissolution rate increases from −8.2 and −10.1 to −4.2 and −5.7, at 25 and 180°C, respectively. The effect of small changes in pH can also be significant as exemplified for anorthite at 25°C, when the log dissolution of this phase decreases from −11.11 to −10.82, between pH of 8.1 and 8.4, respectively. Figure 1 gives the solubility of different rock-forming mineral groups at 25°C between pH 5.1 and 7.7 (Palandri and Kharaka, 2004). It should be noted that not all the mineral groups shown are suitable for processing by carbonation.
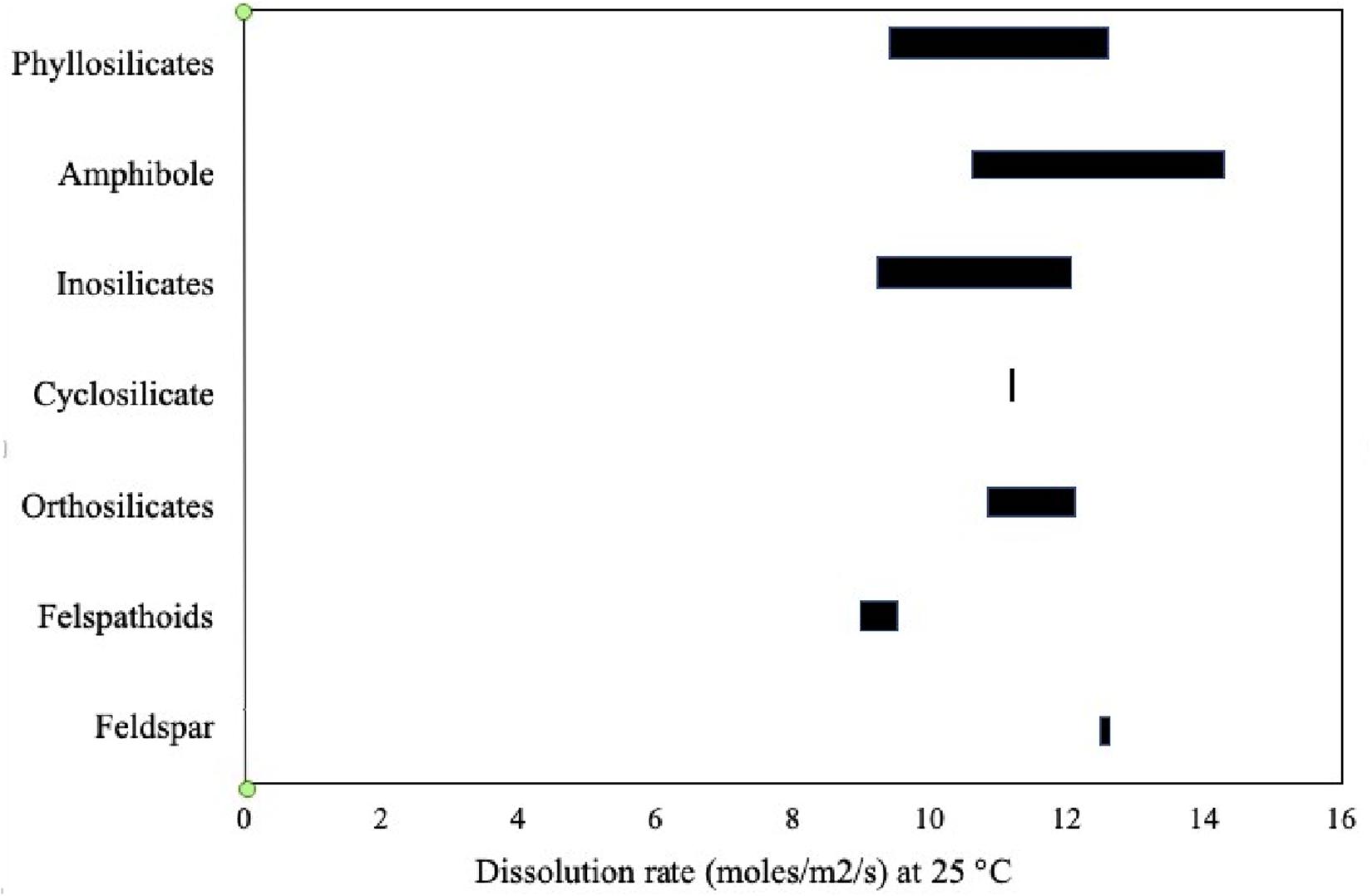
Figure 1. Dissolution rates for major rock-forming minerals at 25°C and pH 5.1–7.7 (Palandri and Kharaka, 2004).
The injection of CO2 into the vicinity of active spreading ridges, where new oceanic crust is being formed, has been suggested as suitable host rocks, as they are characterized by saline hydraulic gradients (O’Connor et al., 2005). Seawater flows into pelagic sediments towards the spreading ridge itself, and injection of CO2 would promote the formation of Mg and Ca carbonates. O’Connor et al. (2005) estimate that there is a capacity to store 8–40,000 Gt of CO2 worldwide in the vicinity of spreading ridges. Olajire (2013) discusses several in situ mineralization projects in basic and ultrabasic rock formations, including into basalts in Iceland (Carbfix, 2020).
The role of heterogeneities in potential host rock formations is of importance. Peuble et al. (2018) discussed the role of discontinuities in ultramafic rocks and their effect on chemical gradients, along preferential fluid pathways, with carbonate formation orientated normal to the hydraulic gradient.
Wherever suitable rock formations exist, their physical and chemical characteristics, including interlinked void space, pore solution chemistry, and temperature are key considerations for suitability for large-scale mineralization. There are several relevant reviews and reports on CO2 mineralization, including IPCC (2005), Renforth et al. (2011), Romanov et al. (2015), and Kelemen et al. (2019). A further potential significant consideration is the role of iron-oxidizing bacteria on the degradation of silicate rocks, which is described by Daval (2018). This study reports the biologically induced formation of a passivating Fe3+-Si-rich layer on the surface of silicate minerals found in basic and ultrabasic rocks can, for example, reduce the dissolution rate of olivine by two orders of magnitude.
As such, one of the issues to be faced is the reaction yield, that is, how much CO2 is mineralized per unit of mass of target mineral. Rarely is a target mineral reacted with CO2 as predicted on stoichiometry grounds, meaning that in ex situ applications, high temperatures and pressures and the use of chemical reagents are required to achieve an acceptable yield in a short time. This will inevitably have an impact on cost, as the amount of target mineral required to trap 1 t of CO2 (the RCO_2) already varies widely; for example, the feedstock requirement for olivine, wollastonite, basalt, and magnetite is 1.6, 2.6, 4.9, and 5.3 t, respectively (Penner, 2004; Zevenhoven, 2004; Sanna et al., 2014). Olajire (2013) reports that rocks comprising olivine and serpentinite normally have an RCO_2 ranging between 1.97 and 2.51.
The reaction of CO2 with olivine and serpentine in the presence of water is given in Table 1, together with other common minerals of interest (O’Connor et al., 2000; Renforth et al., 2011; Alexander and Maroto-Valer, 2018). The amount of CO2 that is reacted (with the yield), on a percentage w/w basis, is calculated from the equation given. As can be seen, this varies widely and is dependent on the chemistry of the mineral in question and is further impacted by reaction kinetics, purity of the mineral system, and other considerations. Thus, a 100% reaction condition is rarely achieved.
As the rate of reaction between rock and bicarbonate is slow, a managed mineralization step requires a high-energy environment and complex reaction conditions to overcome kinetic constraints (Balucan et al., 2013; Eikeland et al., 2015; Ebrahini et al., 2018). Thus, until mineralization technology advances, the in situ injection of CO2 into a rock for storage (as opposed to the utilization of sedimentary formations found in depleted oil wells) is unlikely to be widely adopted. Wang J. et al., 2018; Wang F. et al., 2018 discuss some of the economic considerations involved, whereas Verduyn et al. (2011) review the options for CO2 mineralization in rock. Majumdar and Deutch (2018) provide a context for mineralization and other CCUS options that may be deployed at scale. Kelemen et al. (2019) have most recently overviewed the status and challenges of mineralization in the geosphere.
Accelerated Carbonation of Mineral Systems
The mining and fine grinding of basaltic or other rocks have been investigated for ameliorating soil to enhance mineral weathering and produce bicarbonate (Kohler et al., 2010; Wilson et al., 2014; Renforth et al., 2015; Sackler Forum, 2017). Notwithstanding, the impacts on the chemistry of the oceans, the logistics involved in mining, processing, transporting, and widely applying this technology are likely to be prohibitive. Studies on accelerating mineralization by, for example, raised temperatures and pressures, controlling moisture content, and the partial pressure of CO2 include those of Gerdemann et al. (2007), Dri et al. (2014), and Gadikota and Park (2015).
It is often assumed that the use of ex situ treatments may overcome many of the issues associated with the costs and technical complexity of the in situ mineralization of CO2 in host rocks. An advantage of ex situ processing is the ease of auditing and confirming the permanence of carbon stored in the mineralized product(s). The drawbacks in respect of the energy requirement associated with processing and subsequent carbonation are augmented by one issue not receiving much attention to date, and that is the disposal of the mineralized media back into the geosphere. As mineralized products occupy significantly more volume than the originally excavated rock as it now contains carbonate, the environmental impacts associated with “landfilling” more rock that was excavated must be fully costed, as environmental harm will undoubtedly arise.
Geologically derived feedstock materials for mineralization, such as olivine and serpentine, are abundant, and mining technologies are mature enough to handle appropriate quantities of processed mineral media for carbonation. The high costs of intensive reaction conditions can, to a certain extent, be mitigated if commercially attractive mineral products, such as silica or magnesia, can be made available for sale. Teir et al. (2007) and Zevenhoven et al. (2017) have described processing of serpentinite by dissolution followed by carbonation and the recovery of mineral products.
For the industry to apply mineralization technology, changes in commercial and regulatory operating environments are needed. This is particularly important if the mineralization processes used manufacturing products that are suitable for reuse or sale into the market. Unless facilitating tax regimes are in place to support processing and the disposal of mineralized products to land, the cost involved can only be mitigated by the manufacture of products for sale, such as silica or finely divided calcium carbonate.
That said, there are commercial opportunities involving the mineralization of wastes to divert them from landfill into products with value. Residues are subject to waste management regulations in many countries and have a significant negative value. Furthermore, because of the waste hierarchy, there are options to apply “end of waste” via the manufacture of products that are fit for purpose, providing the wastes are risk-managed. In Europe, the Waste Framework Directive provides a pathway to “end of waste” and product status (European Commission, 2019). Products can be a substitute for virgin stone, a mineral filler, or another commercially attractive material/product. Wastes suitable for processing are often found close to market, relatively consistent, alkaline and have a high surface area, properties that facilitate further processing by mineralization.
Within the last decade, the use of CO2 to treat industrial waste via an accelerated carbonation step to make carbonate-cemented products has become established in Europe. There are several estimates of the global quantities of suitable industrial wastes for mineral carbonation (e.g., Gomes et al., 2016), and suitable arisings are likely to be ≥2 Gt each year. As such, there is mounting interest in potential carbonate-able wastes to sequestrate mineralized CO2 but also to valorize the waste and reduce the risks associated with disposal to land.
There are newly commercially available and emerging CCUS technologies involving mineralization, and these have been summarized in Hills et al. (2019). Although it is not yet possible to be certain of the potential total global amount of CO2 that can be mineralized in waste, estimates in the 1–5 Gt range are available. The GCI (2016) estimates that with the right commercial incentives/government support, 3.6 Gt/year of CO2 could be mineralized in construction aggregates by 2030. As the annual world demand for aggregate is currently in the order of 50 Gt and rising, a market for manufactured carbonated aggregates is well established.
It should be noted that treatment of wastes can involve high-water containing “wet” systems, where waste particles are suspended in or dissolved in aqueous solution. The addition of CO2 enables finely divided carbonated products to be produced, including precipitated calcium carbonate (PCC). PCC is used as a mineral filler in paper and plastic and has recently been recognized as a product in which CO2 is permanently bound. As such, PCC meets the requirements of emissions trading (European Union [EU], 2018), a key development that enables the benefits of CO2 sequestration to be recognized with value generation from carbon credits. Therefore, if CO2 from an Emissions Trading Scheme (ETS) installation is ultimately not released into the atmosphere, either because it is transferred for geological storage or is mineralized, that amount should be subtracted from the emissions of the originating ETS installation. Recognition of this for PCC follows the legal case initiated by Schaefer Kalk (C-460/15, EU:C:2017:29) (Curia.europa.eu, 2020).
Table 2 gives a general comparison of the strengths and weaknesses of in situ and ex situ mineralization technologies. It can be seen that there are benefits from both approaches; however, technology readiness and the investment involved are important impediments, especially where in situ technologies are concerned.
Treatment of Industrial Process Waste
The mineralization of CO2 in waste has been variously demonstrated in the laboratory and commercially, including at ambient temperature and pressure conditions. The mineralization reaction primarily involves metal/mineral oxides, hydroxides, and silicates with CO2 gas. Mineralization can be achieved (in minutes), but in reality, the reactions concerned are rarely fully completed. Calcium and magnesium carbonates, on account of the environmental impact and stability, are the favored reaction products and are simply represented as M+ (Equations 3 and 4):
The reaction pathway involved may be more complicated than shown in Equations (3) and (4), as there are options to produce more than one valuable product from a mineralization step. For example, Xie et al. (2015) used CO2 from flue gas to treat phosphogypsum waste in a reaction involving ammonia to produce ammonium carbonate, which then reacts with phosphogypsum waste in a reactor. The final products were calcium carbonate and ammonium sulfate, a source of nitrogen and sulfur for a slow release fertilizer.
A “world-first” long-term study on the sequestration of CO2 in soil via field-scale carbonate-based solidification treatment of contaminated soil in South East England was carried out in 2000. This work demonstrated the possibility of treating “problem” soils to change their physical properties and leaching behavior (Antemir et al., 2010; Hills et al., 2019). Pure CO2 was used to carbonate-solidify and granulate the soil concerned. Building on this work, flue gas extracted from a point source was used to treat locally sourced industrial solid wastes in a carbonation step. Wastes included air pollution control residues (APCr), which were mineralized with CO2 derived from a landfill flare. The aggregated products were found to comply with construction material standards, and the approach was further developed (Gunning et al., 2011) and scaled up and commercialized (see Figure 2) in the United Kingdom (see Carbon8, 2020b).
The mineralization of CO2 in waste is attractive, as it is a circular economic approach that can be achieved via direct use of available point-source CO2. Potential carbonate-able wastes and CO2 sources are generally co-located, and this provides an unique opportunity to strip the CO2 gas directly from a flue to manage both solid- and gaseous-waste streams efficiently.
The formation of carbonates is an energetically downhill process, with the chemical reactions (e.g., as shown in Equations 3 and 4) being highly exothermic. The heat generated by a managed mineralization process can be recovered and reused. Important circular economic considerations related to mineralization include:
• Availability, location, and source of both solid waste and CO2 gas;
• Optimal handling of feedstock solid and gaseous waste;
• Use of renewable energy in processing; and
• Facilitating standards for the use of the mineralized products.
Mapping sources and quantities can identify the availability of CO2 as a feedstock. In Europe, it is mandatory to publish emission data if it exceeds 0.1 Mt/year, enabling the locations of CO2 emissions to be mapped (Armstrong et al., 2019). Suitable CO2 emissions that are easy to extract arise from the paper pulp industry (31.4 Mt/year), integrated (integrated coal gasification combined cycle) thermal coal plants (3.7 Mt/year), iron and steel manufacturing (151.3 Mt/year), and cement kilns (119.4 Mt/year) (Naims, 2016; Armstrong et al., 2019).
The waste materials that have the right chemistry, mineralogy, and physical properties can react with CO2 under ambient temperature and pressure conditions (Fernandez-Bertos et al., 2004). The carbonate-cemented products can have the potential for reuse in engineering applications. However, as many industrial waste streams contain priority metals, there is a possibility of pre-processing to extract and recover the valuable metals before carbonation is carried out. By way of example, argon oxygen decarburization and basic oxygen furnace steel slags have been investigated by Gomes et al. (2016) and Ogden et al. (2017), whereas Quaghebeur et al. (2015) investigated the recovery of Cu, V, Zn, Ni, Mo, and Cr. A useful review of mineralization by Pan et al. (2012) discusses the various physico-chemical issues involved in waste mineralization. Figure 3 shows the chemistry of example process wastes within the Ca(MgO)-SiO2-AL2O3(Fe2O3) system and reflects the diversity of wastes that have or may be presented for carbonation. As with geologically derived minerals and rock, the rate of calcium “leaching” from a waste (and, hence, its ability to combine with CO2) is important. The ability of a waste to be mineralized is influenced by, for example, particle size, pH, solid-to-liquid ratio, temperature, pressure, mineralogy, etc. In reality, however, the formation of carbonate is subject to the balance between the kinetics of the reaction and the solubility of Ca or Mg in a waste feedstock (Pan et al., 2012).
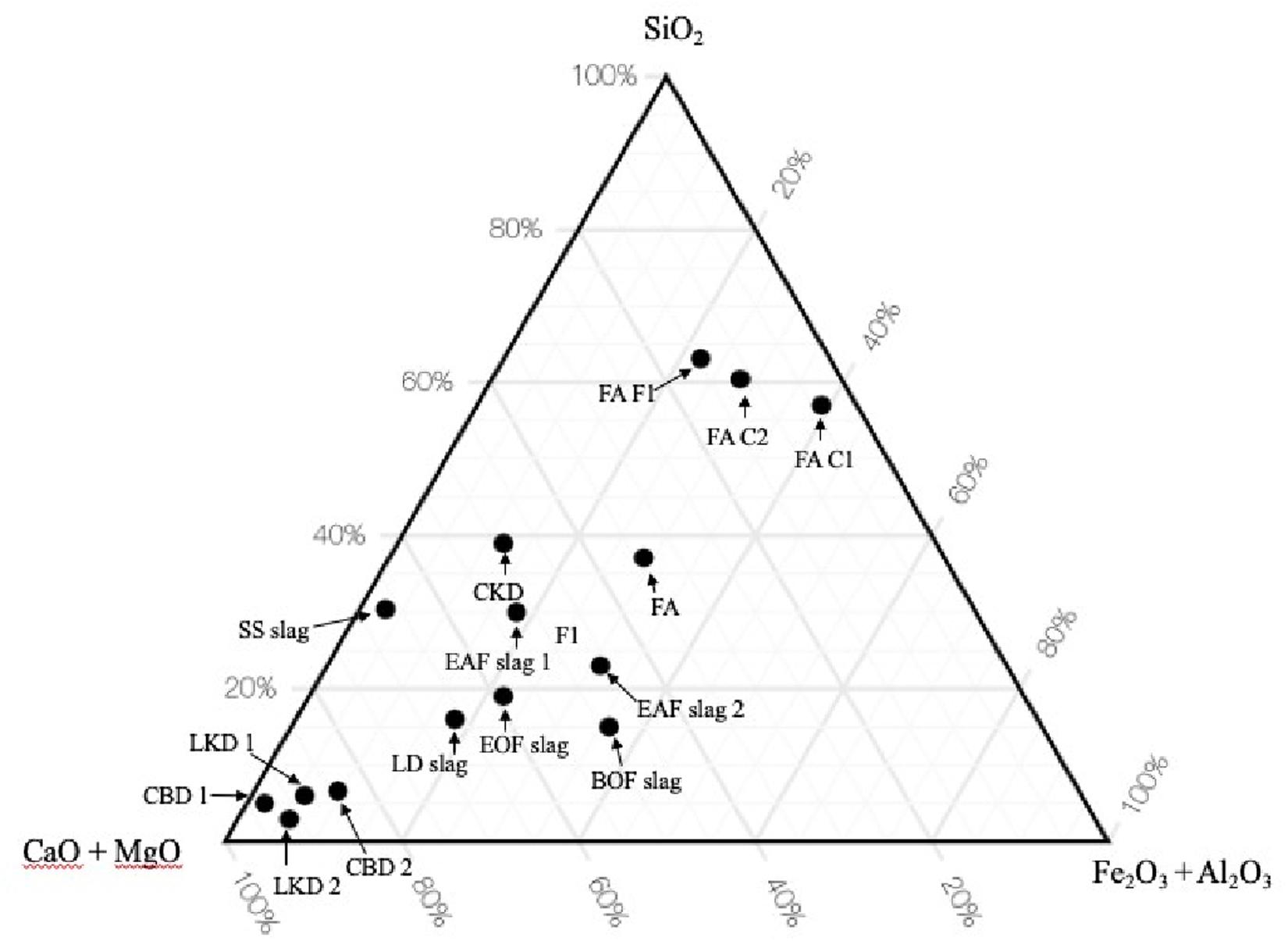
Figure 3. Normalized phase diagram showing the variability in chemistry of industrial process wastes (Chad et al., 2015; Fathy et al., 2016; Sabapathy et al., 2017; Carbon8 Systems Ltd, 2020).
There are several technical issues that potentially negatively impact the versatility of mineralization as a mechanism to carbonate wastes. One of those to avoid is the use of pure CO2, supplied as a process gas as the costs involved in compressing and transportation being relatively high. Thus, by capturing CO2 directly from a flue gas without purification and liquefaction, costs are kept to a minimum as, for example, thermal residues can be reacted readily with the CO2 released during their combustion without the need for transportation to a mineralization plant for onward processing. However, the amount of CO2 in a flue gas can be low, and 10% v/v is not untypical. A point source with a low pCO2 will necessitate extended reaction times and higher processing costs.
One approach to overcoming the kinetic constraints of flue gas with a low pCO2 is the use of accelerators, and several homogeneous catalysts are available. These include inorganic oxyanions (e.g., hypochlorite or sulfite), organic solutes (e.g., sugars and polyhydric alcohols), and amines and alkanolamines (which produce carbamates with CO2) for the solvation and hydration of CO2 in water that are available (Maries and Hills, 2013). It is important, however, to ensure that the presence of residual catalysts in the mineralized product does not affect reuse as might happen with enhanced sulfate or chloride leaching.
Another approach has been the biological catalyst, carbonic anhydrase, which is an enzyme better suited for use in higher water containing carbonation reaction environment. Power et al. (2016) reported that bovine-derived carbonic anhydrase increased the carbonation of a brucite slurry by 240%. The use of biomimetic metal–organic framework catalysts has been shown to enhance wollastonite dissolution (Lorenzo et al., 2018). Other work using a yeast-based catalyst, Saccharomyces cerevisiae, applied to coal fly ash, gave an increase in carbonation efficiency of 10% (Barbero et al., 2014).
Legacy Wastes
Legacy residues, such as mine tailing, have the potential to be passively carbonated or mined as a feedstock for CCUS. This approach is sometimes called surficial carbonation, and tailings arising from mafic and ultramafic rock sources are candidate wastes (Kelemen et al., 2019). National Academies of Sciences Engineering Medicine [NASEM] (2019) suggests that 10× Mt/year CO2 can be readily sequestered in mine tailings this way. Hamilton et al. (2018) investigated chrysotile-processing residues/tailings from ultrabasic host rocks, whereas Pan et al. (2017) and Ebrahini et al. (2018) investigated Ca-rich alkaline waste/tailings, including steel slag and electric arc furnace slag. Nickel-processing tailings, yielding serpentinite, were reported to be carbonated to a high degree by Teir et al. (2009). A review by Power et al. (2013) investigates the carbonation of alkali earth silicate and hydroxide-containing minerals.
Xie et al. (2015) reviewed the mineralization of portlandite in various alkaline residues, including carbide, steel slag, paper mill waste, cement kiln dust, and coal fly ashes using sodium chloride to produce calcium bicarbonate. Treatment of both production and legacy wastes by ex situ processing has the potential to sequestrate Gt quantities of CO2 each year (Renforth et al., 2011; Sanna et al., 2014). The relative costs involved in in situ and ex situ carbonation are discussed by Kelemen et al. (2019).
Carbon Dioxide Mineralization in the Construction Industry
As mentioned, CO2 has been long used to accelerate the curing of concrete and mortar. However, this application has rarely, if at all, been used to achieve a high degree of carbonation (i.e., where carbonate phases are responsible for hardening, rather than “normal” hydrated phases).
In the 1970–1980s, Berger and others investigated the reaction of CO2 gas with cements, including individual calcium silicate phases (e.g., Klemm and Berger, 1972; Young et al., 1974). It was established that a rapid hardening of cement occurs at low water–solid contents via the decalcification of silicate phases leading to the precipitation of solid calcium carbonate. In largely unpublished work, Maries and Hills (1983) established a process for the rapid carbonate hardening of roof tiles, thereby omitting the need for steam curing. Shi et al. (2012) investigated the kinetics of concrete carbonation and demonstrated that strength and dimensional stability are comparable with steam-cured articles.
The carbonate hardening of wastes arising from a mineralization step produces materials that can be used in engineering applications. Gunning et al. (2009) reported that lightweight carbonated aggregates with a bulk density of <1,000 kg/m3 and compressive strength >0.10 MPa could be manufactured from alkaline residues. Further developed by Gunning et al. (2011) for use with APCr, the carbonation process for manufacturing construction aggregates is now commercially established. Similar work was reported by Morone et al. (2014), with bonded aggregates made from basic oxygen furnace steel slags, which capture <10% CO2 w/w. Salman et al. (2014) investigated monolithic products made from argon oxygen decarburization slag with strengths of 34 MPa after 3 weeks curing in 5% CO2 and 60 MPa at 8 bar CO2 and 80°C for 15 min. Similar results for stainless steel slag were reported by Quaghebeur et al. (2010) and Nielsen et al. (2017). Example CCUS processes delivering construction materials that are under development or commercially available are given in Table 3, together with their reported technical readiness level.
A notable recent development is a mobile carbonation plant producing construction aggregates, which is a flexible alternative to fixed plants using liquid CO2 supplied by a road tanker. The mobile plant has a capacity of approximately 12 kt/year of manufactured carbonated aggregates using CO2 directly stripped from a point source. This enables both gaseous and solid-waste streams to be economically captured and combined at relatively small emission locations or industrial plants with limited access. Figure 4 shows the “CO2ntainer” (Carbon8, 2020a, b), which has been deployed at two cement plants, one in the United Kingdom and another in Ontario, the latter as a demonstration project funded under the Ontario Centres of Excellence Solutions 2030 initiative.
The capacity of the plant is designed to match the quantity of reactive waste residues generated by an industrial plant (e.g., 6–7,000 t for cement plants and 10–12,000 t for energy from wastes), removing the need to transport the waste residues for treatment at a central site and also removing the need to purify the CO2 for transport for use elsewhere. The containerized plant can be rapidly deployed and directly connected into the flue stack to extract the CO2, with the remaining flue gas being returned to the stack.
Life Cycle and Techno-Economic Assessments of Carbon Dioxide Mineralized Products
As we move to a circular economy as part of our wider sustainability efforts, the potential of mineralized CO2-based products entering the marketplace mean the accounting of carbon is required. The key considerations concern the net carbon emissions of the process, materials processing/handling and transport, and energy requirements. At a system/sectoral level, the mineralization of CO2 in wastes allows for the application of CCUS across a range of different industrial settings within an economy, making sure the varied inputs into the process are considered.
New technologies for CCUS are emerging, and their economic and environmental viability, and economic and environmental trade-offs have to be carefully analyzed. This involves a combination of life cycle assessment (LCA) and techno-economic assessment (TEA) and is key to informed decision-making and a standardized assessment. Several regulatory bodies of the European Commission (e.g., the Scientific Advice Mechanism, EIT Climate-KIC) have recognized the need of a common assessment guidelines involving LCA and TEA to enhance reliability, transparency, and compatibility of CCUS technologies and their technology readiness levels (Buchner et al., 2018).
An LCA can be used to assess the environmental impacts of products or services, being not limited to climate change only but also the other impacts, such as resource depletion (Bui et al., 2018). According to the International Organization for Standardization (ISO 14040, 2006), an LCA consists of the four interdependent phases, as shown in Figure 5 (Armstrong et al., 2019). Artz et al. (2018) state that LCA studies for identical CCU technologies can also vary, so standardization of an LCA assessment is important under a general framework structured by ISO. Comprehensive guidance on LCAs has been produced for CCUS by the Global CO2 Initiative (Deepblue, 2020) and the National Energy Technology Laboratory [NETL] (2019)2. Both follow ISO 14040 (2006) (Environmental Management–Life Cycle Assessment–Principles and Framework) and ISO 14044 (2006) (Environmental Management–Life Cycle Assessment–Requirements and Guidelines) and provide additional guidance specific to CCUS projects. Further comprehensive guidance (arising from the same work) lists the needs for a standard methodology for LCA (Müller et al., 2020), as the choices made can differ widely and can significantly impact decision-making. Predefined assumptions on feedstock materials and utilities coupled with guidance on reporting enable standardization and a comparison between different CCUS technologies to be achieved.
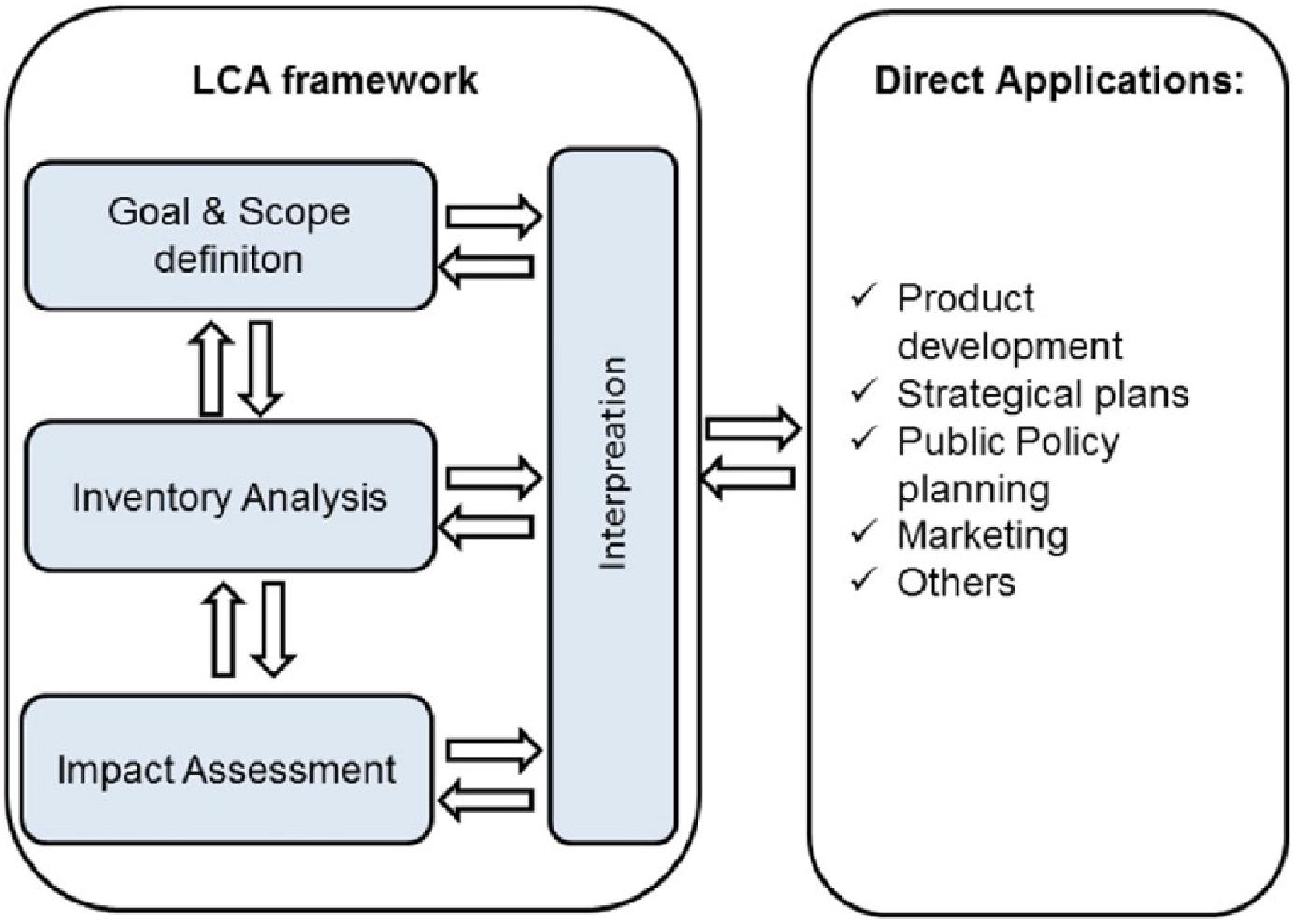
Figure 5. General framework for life cycle assessment (ISO 14040, 2006).
It is worth noting that LCA has been applied to phosphogypsum recovery, both from wastewater and simulated solid-waste processing (Amann et al., 2018; Pell et al., 2019, respectively), showing that trade-offs between emissions and energy demand are required, further strengthening the need for a consistent approach, like that described by Müller et al. (2020). An LCA-based quantification of emissions re-use in the manufacture of different mineralized products is given by Zevenhoven (2020).
The TEA is a methodological framework that analyses the technical and economic performance of a process, product, or service (Armstrong et al., 2019). The major components of this framework involve the economic impact of research, development, demonstration, and implementation/deployment of technologies (Zimmermann et al., 2020). This is all incorporated in quantifying the cost of manufacturing and market opportunities with a particular technology.
The TEA is a widely used tool that considers several perspectives (e.g., research and development, corporate, and market) and varying guidelines according to application, technology development, and stakeholder needs (Zimmermann et al., 2020).
In the case of an LCA for CO2 mineralization, the calculation mainly incorporates the emissions and turnover time of captured carbon (i.e., the duration of carbon storage in products). In a TEA for CO2 mineralization, the CO2 avoidance for product applications can be exemplified by lowering CO2 emissions of another process (e.g., cement or steel) by waste treatment for industrial ashes. In market segments, CO2 avoidance can be explained via an example of large-scale steel plants by making low-quality aggregates for low-cost concrete (Zimmermann et al., 2020).
Zimmermann et al. (2020) describe LCA and TEA of CCUS technologies and suggest that as a substitute of natural aggregates/concrete, 1 t of CO2-mineralized concrete can be produced in a 50-kt/year plant with an output of over 20 years. The use and disposal of these products are likely to be the same as for benchmark (natural) products, and a gate-to-gate approach can be applied. However, to follow the cradle-to-grave approach, the integrated life cycle costing and LCA along with a TEA are suggested (Miah et al., 2017; Dong et al., 2018). The scope of TEA and LCA in the product life cycle is given by von der Assen (2016) and modified by Zimmermann et al. (2020), as given in Table 4.
The McCord et al., 2018 interpretation of TEA for CCUS-based production of secondary aggregates from APCr concludes that the production cost is high for a fixed plant producing 4,500 metric tons per year. However, the plant is profitable due to payment of gate fees for APCr treatment. The process inputs of this cradle-to-gate process are APCr, sand, cement, water, and CO2 (flue gas). The process outputs are secondary aggregates, water, and flue gas (that is returned to stack), and the technology readiness level is 9.
In another interpretation of a cradle-to-grave approach incorporating CO2-mineralized APCr blocks composed of carbonated material (lighter blocks than conventional), McCord et al., 2018 depicts that the blocks using the Carbon8 process (using substitution to remove the energy from waste impacts form the system boundary) result in a reduction of 22–34% of GHG emissions. This is evaluated considering the impacts arising from the APCr treatment and block production process.
Future Developments for Carbon Dioxide Mineralization
Within the United Kingdom, the right commercial environment exists for the production of manufactured accelerated carbonated aggregates that are cost-competitive to natural stone and are market accepted. Acknowledging that the United Kingdom situation may be fortunate, in which aggregate sources are dwindling, landfilling of waste is subject to rising prices, and the market is amenable to new products.
However, as it currently stands, the general development of mineralization processes is largely held back by a mix of technical and economic reasons. As discussed in Chapter 7 of the IPCC special report on CCS (IPCC, 2005), although there has been some progress in the past 15 years, significant progress remains to be made (Kheshgi et al., 2012). Current hurdles to overcome and their likely solutions are given in Table 5.

Table 5. Problems and solutions for the development of mineralization technologies (Kheshgi et al., 2012).
The mineralization of CO2 in geologically derived and solid process wastes is attractive, not least that the quantities of mineral feedstock available are suitable for sequestering Gt of carbon each year. As the technology and infrastructure required develop, the associated costs will decrease. How this will be paid for and by whom is a matter of current debate. In the meantime, efficiency measures, renewable energy sources, and other measures will go some way to limit emissions to the atmosphere.
The appeal of wastes as a feedstock for mineralization is promising, as the technology for manufacturing mineralized products is already commercially established and is being further developed (e.g., mobile carbonation plant directly using CO2 from point-source emissions). In addition, the following advantages may also apply:
• Solid waste and point-source CO2 are commonly co-located,
• Many solid process wastes are alkaline in nature, and
• Being often located close to the market is an added advantage, as proximity to the market is critical if valorized products are to be cost-competitive with virgin products.
An important implication of mineralization of CO2 in waste for the production of construction materials is the environmental and economic benefits accrued via direct and indirect CO2 emissions offset. The direct offset is achieved via permanently sequestering CO2 in waste-based products, whereas indirect offsets can be realized by:
• Direct replacement of cement with carbonated materials made from waste,
• Replacement of hydraulic cement by carbonate-able binders,
• Reduction of transport involved in landfilling of waste,
• Replacement of quarried virgin stone,
• Reduced transport/materials handling, where solid waste and point-source CO2 are co-located close to the market.
As the emphasis moves further towards low-carbon construction and wider certification of products becomes firmly established, the carbon offsets achieved by the manufacture and use of mineralized construction products will become more important.
The requirements for entering the “market” with a mineralized waste-based product involve complying with relevant regulatory instruments. In the European Union, this is governed by the Waste Framework Directive (European Commission, 2019). However, the laws of a particular territory sometimes preclude compliance, as the framework cannot be enacted. Furthermore, the needs and perceptions of the market and the supply chain in place may be an issue. In the United Kingdom, the Environment Agency is receptive to landfill avoidance strategies through the “end of waste” process and provides objective guidance. Thus, there are several technical and non-technical challenges involved, not least securing long-term contracts for waste feedstock and product offtake and the impact these “hurdles” have on investment confidence.
A consideration not widely reported is the public perception of using wastes in products, including those for construction. Industrial by-products have been widely used in construction, such as coal fly ash (pulverized fuel ash) and steel slag (ground-granulated blast-furnace slag). These materials are wastes but have legal status as by-products. With many alkaline wastes falling under waste management regulations and remaining as wastes until they are sold to the market, a contradiction based on labeling emerges. As such, there is a need to address this either by legally changing the “label” or by educating stakeholders that mineralized products meeting “end of waste” are indeed products and not wastes by another name.
There are many considerations involved, and one might be to focus on:
• the embodied carbon within the mineralized product,
• its fitness for purpose including meeting internationally accepted material standards, and
• an accentuation of the sustainability gains, including protection of virgin resources.
Also, the move by the construction industry to carbon neutrality was an important consideration to the successful entry of manufactured carbonated aggregates into the United Kingdom market. With competitive pricing and technical advantages, such as lighter weight, augmented by carbon negativity, the United Kingdom construction block industry has been receptive. Furthermore, these benefits have also been somewhat recognized by the wider stakeholder community. Thus, inward investment supporting innovation and rising industry buy-in of the sustainability gains add strength to this CCUS approach.
Currently, in Europe, there is pressure for mineralization technologies to be included in the European Union ETS along with the generation of e-fuels, to avoid the release of fossil carbon. The mechanism being proposed is via the Emissions Monitoring and Reporting Regulation (European Union [EU], 2018) and relates to the ability of industrial flue gas to be transformed into useful materials, including mineralized building products. Changes to emission trading regulations, as proposed, will be a significant stimulus to help meet innovation challenges for the circular economy, the avoidance of CO2, protection of natural resources, and the creation of wealth.
The world market for construction aggregates is in the order of 50 Gt/year and rising, so it is well placed to receive manufactured carbonated aggregate products. The total value of aggregate sales is projected to be US$547 Bn by 2025 (Research and Markets, 2020), highlighting that value-added mineralized products can benefit from a growing global market. With the right incentives within emerging circular economies, such as those anticipated in Europe and Asia, sustainable mineralized products can play an increasingly important role in the building materials supply chain.
Author Contributions
This work was conceived and primarily written by CH and NT. PC provided practical advice, guidance, and text, primarily to the commercially related aspects described in the manuscript, including the recent development of mobile carbonation plant and also elsewhere. All authors played a substantive role in the production and completion of the present work.
Conflict of Interest
The work reported is a review of technological advances involved in the mineralization of CO2. Research is undertaken at the University of Greenwich, which has, in part, been successfully commercialized by its spin-out company, Carbon8 Systems Ltd. (C8S). It is explicitly recognized that PC is an executive director of C8S and CH is a full-time professor at the University of Greenwich but retains a non-executive technical role, in fulfillment of the Universities responsibility to its licensee spin-out company.
The remaining author declares that the research was conducted in the absence of any commercial or financial relationships that could be construed as a potential conflict of interest.
Footnotes
References
Alexander, G., and Maroto-Valer, M. M. (2018). Serpentine and Single Stage Mineral Carbonation for the Storage of Carbon Dioxide. Available online at: https://pdfs.semanticscholar.org/1b97/91c844cdc5b7031734442244515fcac3bb69.pdf (accessed March 2020).
Amann, A., Zoboli, O., Krampe, J., Rechberger, H., Zessner, N., and Egle, L. (2018). Environmental impacts of phosphorus recovery from municipal waste water. Resour. Conserv. Recycl. 130, 127–139. doi: 10.1016/j.resconrec.2017.11.002
Antemir, A., Hills, C. D., Carey, P. J., Magnié, M.-C., and Polettini, A. (2010). Investigation of 4-year-old stabilised/solidified and accelerated carbonated contaminated soil. J. Hazard. Mater. 118, 543–555. doi: 10.1016/j.jhazmat.2010.05.048
Armstrong, K., Zimmermann, A., Müller, Wunderlich, J., Bucher, G., Marxen, A., et al. (2019). “Techno-economic assessment and life cycle assessment for CO2 utilisation,” in Carbon Dioxide Utilisation: Fundamentals, Vol. 1, eds M. North and P. Styring (Berlin: De Gruyter Publications), 63–78. doi: 10.1515/9783110563191-005
Artz, J., Müller, T. E., Thenert, K., Kleinekorte, J., Meys, R., Sternberg, A., et al. (2018). Sustainable conversion of carbon dioxide: an integrated review of catalysis and life cycle assessment. Chem. Rev. 118, 434–504. doi: 10.1021/acs.chemrev.7b00435
Balucan, R. D., Dluggogorski, B. Z., Kennedy, E. M., Belova, I. V., and Murch, G. E. (2013). Energy cost of heat activating serpentinites for CO2 storage by mineralisation. Int. J. Greenhouse Gas Control 17, 225–239. doi: 10.1016/j.ijggc.2013.05.004
Barbero, R., Carnelli, L., Simon, A., Kao, A., Monforte, A. A., Riccò, M., et al. (2014). Engineered yeast for enhanced CO2 mineralization. Energy Environ. Sci. 6, 660–674.
Beaulieu, E., Godd́eris, Y., Donnadieu, Y., Labat, D., and Roelandt, C. (2012). High sensitivity of the continental-weathering carbon dioxide sink to future climate change. Nat. Clim. Change 2, 346–349. doi: 10.1038/nclimate1419
Blue Planet (2020). Available online at: www.blueplanet-ltd.com/ (accessed April 2020).
Buchner, G. A., Schomäcker, R., Meys, R., and Bardow, A. (2018). Guiding Innovation with Integrated Life-Cycle Assessment (LCA) and Techno-Economic Assessment (TEA)- the Case of CO2-Containing Polyurethane Elastomers. Climate-KIC Technical Report, 12/2018. Aachen: RWTH Aachen University.
Bui, M., Adjiman, C. S., Bardow, A., Anthony, E. J., Boston, A., Brown, S., et al. (2018). Carbon capture and storage (CCS: the way forward. Energy Environ. Sci. 11:1062.
Canovas, P. A., Hoehler, T., and Shock, E. L. (2017). Geochemical bioenergetics during low-temperature serpentinization: an example from the Samail ophiolite, Sultanate of Oman. J. Geophys. Res. Biogeosci. 122, 1821–1847. doi: 10.1002/2017JG003825
Carbfix (2020). Available online at: www.carbfix.com (accessed April, 2020).
Carbicrete (2020). Available online at: http://www.carbicrete.com/ (accessed March, 2020).
Carboclave (2020). Available online at: http://www.carboclave.com/ (accessed March, 2020).
Carbon8 (2020a). Technology-Adding Carbon Dioxide to Waste to Give it Commercial Value. Available online at: http://c8s.co.uk/technology/ (accessed March, 2020).
Carbon8 (2020b). Available online at: www.c8s.co.uk (accessed April, 2020).
Carbon8 Systems Ltd (2020). Available online at: http://pers.com/en
Chad, S. P., Paul, B., and Kumar, M. (2015). An overview of the use of Linz-Donawitz (LD) steel slag in agriculture. Curr. World Environ. 10, 975–984. doi: 10.12944/cwe.10.3.29
Curia.europa.eu (2020). Case Number C-460/15. Available online at: http://curia.europa.eu/juris/documents.jsf;jsessionid=32407B6EE359B2D47A582FB14BB34F8D?oqp=&for=&mat=or&lgrec=en&jge=&td=%3BALL&jur=C%2CT%2CF&num=C-460%252F15&page=1&dates=&pcs=Oor&lg=&pro= &nat=or&cit=none%252CC%252CCJ%252CR%252C2008E%252C%252C%252C%252C%252C%252C%252C%252C%252C%252Ctrue%252Cfalse%252Cfalse&language=en&avg=&cid=2136616 (accessed April 2020).
Daval, D. (2018). Carbon dioxide sequestration through silicate degradation and carbon mineralisation:promises and uncertainties. NPJ Mater. Degrad. 2:11. doi: 10.1038/s41529-018-0035-4
Deepblue (2020). Available online at: https://deepblue.lib.umich.edu/handle/2027.42/147467 (accessed March 2020).
Dong, Y., Miraglia, S., Mazo, S., Georgiadis, S., Sørup, H. J. D., Borian, E., et al. (2018). Environmental sustainable decision making- The need and obstacles for integration of LCA into decision analysis. Environ. Sci. Policy 87, 33–44. doi: 10.1016/j.envsci.2018.05.018
Dri, M., Sanna, A., and Maroto-valer, M. (2014). Mineral carbonation from metal wastes: Effect of solid to liquid ratio on the efficiency and characterization of carbonated products. Appl. Energy 113, 515–523. doi: 10.1016/j.apenergy.2013.07.064
Ebrahini, A., Saffari, M., Hong, Y., Miliani, D., Montoya, A., Valix, M., et al. (2018). Mineral sequestration of CO2 using saprolite mine tailings in the presence of alkaline industrial wastes. J. Clean. Prod. 188, 686–697. doi: 10.1016/j.jclepro.2018.04.046
Eikeland, E., Blichfield, A. B., Tyrsted, C., Jensen, A. P., and Iversen, B. B. (2015). Optimized carbonation of magnesium silicate mineral for CO2 storage. ACS Appl. Mater. Interfaces 7, 5258–5264. doi: 10.1021/am508432w
European Commission (2019). Directive 2008/98/EC on waste (Waste Framework Directive). Brussels: European Commission.
European Union [EU] (2018). Commission Implementing Regulation, 2018/2066, Monitoring and Reporting of Greenhouse Gas Emissions. Regulation, 19th December 2018. Available online at: https://eur-lex.europa.eu/legal-content/EN/TXT/?uri=CELEX%3A32018R2066 (accessed March, 2020).
Fathy, S., Liping, G., Rui, M., Wei, S., and Gu, C. (2016). “Chemistry, mineralogy and morphology of steel slag and stainless steel slag: A comparative study,” in Proceedings of the International Conference on Mining, Materials and Metallurgical Engineering, Cairo.
Fernandez-Bertos, M., Simons, S. J., Hills, C. D., and Carey, P. J. (2004). A review of accelerated carbonation technology in the treatment of cement-based materials and sequestration of CO2. J. Hazard. Mater. 112, 193–205. doi: 10.1016/j.jhazmat.2004.04.019
Gadikota, G., and Park, A.-H. A. (2015). “Chapter 8 - accelerated carbonation of Ca- and Mg-bearing minerals and industrial wastes using CO2,” in Carbon Dioxide Utilisation, eds P. Styring, E. A. Quadrelli, and K. Armstrong (Amsterdam: Elsevier).
Global CCS Institute (2011). Accelerating the Uptake of CCS: Industrial use of Captured Carbon Dioxide. Available online at: https://www.globalccsinstitute.com/archive/hub/publications/14026/accelerating-uptake-ccs-industrial-use-captured-carbon-dioxide.pdf
McCord, S., Zaragoza, V., Sanderson, P., Armstrong, K., Styring, P., Hills, C., et al. (2018). Global CO2 Initiative: Complete Mineralization Study. Available online at: http://hdl.handle.net/2027.42/145436
Gerdemann, S. J., O’Connor, W. K., Dahlin, D. C., Penner, L. R., and Rush, H. (2007). Ex situ aqueous mineral carbonation. Environ. Sci. Technol. 41, 2587–2593. doi: 10.102/es0619253
Gomes, H. I., Mayes, W., Rogerson, M., Stewart, D. I., and Burke, I. T. (2016). Alkaline residues and the environment: a review of impacts, management practices and opportunities. J. Clean. Prod. 112, 3571–3582. doi: 10.1016/j.jclepro.2015.09.111
Gunning, P., Hills, C., Antemir, A., and Carey, P. (2011). “Novel approaches to the valorisation of ashes using aggregation by carbonation,” in Proceedings of the 2nd International Slag Valorisation Symposium, Leuven, 18–20.
Gunning, P. J., Hills, C. D., and Carey, P. J. (2009). Production of lightweight aggregate from industrial waste and carbon dioxide. Waste Manage. 29, 2722–2728. doi: 10.1016/j.wasman.2009.05.021
Hamilton, J. L., Wilson, S. A., Morgan, B., Turvey, C. C., Paterson, D. J., Jowitt, S. M., et al. (2018). Fate of transition metals during passive carbonation of ultramafic mine tailings via air capture with potential for metal resource recovery. Int. J. Greenhouse Gas Control 71, 155–167. doi: 10.1016/j.ijggc.2018.02.008
Hills, C. D., Tripathi, N., Lake, C., Carey, P. J., Heap, D., and Hills, A. T. (2019). “General Mineralisation of CO2 in solid waste,” in Carbon Dioxide Utilisation: Fundamentals, Vol. 1, eds M. North and P. Styring (Berlin: De Gruyter Publications), 165–187.
Huijgen, W. J. J., and Comans, R. N. J. (2003). Carbon Dioxide Sequestration by Mineral Carbonation. Report Number ECN-C-03-016. Petten: Energy Research Centre of the Netherlands (ECN).
IPCC (2005). “IPCC special report on carbon dioxide capture and storage,” in Prepared by Working Group III of the Intergovernmental Panel on Climate Change, eds B. Metz, O. Davidson, H. C. de Coninck, M. Loos, and L. A. Meyer (Cambridge: Cambridge University Press), 442.
IPCC (2014). Climate Change 2014 Synthesis Report Summary for Policymakers. Available online at: http://www.ipcc.ch2018/02 (accessed April, 2020).
IPCC (2018). Summary for Policymakers of IPCC Special Report On Global Warming of 1.5° C Approved by Governments. Available online at: https://www.ipcc.ch/sr15 (accessed April, 2020).
ISO 14040 (2006). Environmental Management – Life Cycle Assessment – Principles and Framework, Vol. 3. (Geneva: International Organisation Standardisation), 20.
ISO 14044 (2006). Environmental Management – Life Cycle Assessment – Requirements and Guidelines. Int. j. Life Cycle Assessment, 652–668.
Kelemen, P., Benson, S. M., Pilorgé, H., Psarras, P., and Wilcox, J. (2019). An overview of the status and challenges of CO2 storage in minerals and geological formations. Front. Clim. 1:9. doi: 10.3389/fclim.2019.00009
Kheshgi, H., de Coninck, H., and Kessels, J. (2012). Carbon dioxide capture and storage: seven years after the IPCC special report. Mitig. Adapt. Strateg. Glob. Change 17, 563–567. doi: 10.1007/s11027-012-9391-5
Klemm, W. A., and Berger, R. L. (1972). Accelerated Curing of Cementitious Systems by carbon Dioxide: Part 1, Portland cement. Cem. Concr. Res. 2, 567–576. doi: 10.1016/0008-8846(72)90111-1
Kohler, P., Hartmann, J., and Wolf-Gladrow, D. A. (2010). Geoengineering Potential of Artificially Enhanced Silicate Weathering of Olivine. Proc. Natl. Acad. Sci. U.S.A. 107, 20228–20233. doi: 10.1073/pnas.1000545107
Lorenzo, F. D., Ruiz-Agudo, C., Ibañez-Velasco, A., Millán, R. G., Navarro, J. A. R., Ruiz-Agudo, E., et al. (2018). The carbonation of wollastonite: a model reaction to test natural and biomimetic catalysts for enhanced CO2 sequestration. Minerals 8:209. doi: 10.3390/min8050209
Majumdar, A., and Deutch, J. (2018). Research opportunities for CO2 utilisation and negative emissions at the gigatonne scale. Joule 2, 801–809. doi: 10.1016/j.joule.2018.04.018
Maries, A., and Hills, C. (2013). “Homogeneous catalysis of the accelerated carbonation of Portland cement,” in Proceedings of the 4th International Conference on Accelerated Carbonation for Environmental and Materials Engineering (Leuven: ACEME).
Miah, J. H., Koh, S. C. L., and Stone, D. (2017). A hybridised framework combining integrated methods for environmental Life Cycle Assessment and Life Cycle Costing. J. Clean. Prod. 168, 846–866. doi: 10.1016/j.jclepro.2017.08.187
Morone, M., Costa, G., Polettini, A., Pomi, R., and Baciocchi, R. (2014). Valorization of steel slag by a combined carbonation and granulation treatment. Minerals Eng. 59, 82–90. doi: 10.1016/j.mineng.2013.08.009
Müller, L. J., Kätelhön, A., Bachmann, M., Zimmermann, A., Sternberg, A., and Bardow, A. (2020). A guideline for life cycle assessment of carbon capture and utilization. Front. Energy Res. 8:15. doi: 10.3389/fenrg.2020.00015
Naims, H. (2016). Economics of carbon dioxide capture and utilization- a supply and demand perspective. Environ. Sci. Pollut. Res. 23, 22226–22241. doi: 10.1007/s11356-016-6810-2
Nation Energy Technology Laboratory [NETL] (2019). Available online at: www.netl.doe.gov/LCA/CO2U (accessed March, 2020).
National Academies of Sciences Engineering Medicine [NASEM] (2019). Negative Emissions Technologies and Reliable Sequestration: A Research Agenda. Washington, DC: The National Academies Press.
National Energy Technology Laboratory [NETL] (2019). Timothy J. S. P. E., Mutchek, M., Krynock, M., Cooney, G., Pegallapati, A., Rai, S., et al. Carbon Dioxide Utilisation : Life Cycle Analysis Guidance for the U.S. DOE Office of Fossil Energy. DOE/NETL-2019/2069, eds Available online at: https://www.netl.doe.gov/energy-analysis/details?id=3737 (accessed April, 2020).
Nielsen, P., Baciocchi, R., Costa, G., Quaghebeur, M., and Snellingsa, R. (2017). Carbonate-bonded construction materials from alkaline residues. RILEM Tech. Lett. 2, 53–58. doi: 10.21809/rilemtechlett.2017.50
O’Connor, W. K., Dahlin, D. C., Nilsen, D. N., Walters, R. P., and Turner, P. C. (2000). “Carbon Dioxide Sequestration by Direct Mineral Carbonation with Carbonic Acid,” in Proceedings of the 25th International Technical Conf. On Coal Utilization & Fuel Systems, Coal Technology Assoc, (Clear Water, FL: U.S. Department of Energy).
O’Connor, W. K., Dahlin, D. C., Rush, G. E., Gerdemann, S. J., Penner, L. R., and Nilsen, D. N. (2005). Aqueous.mineral Carbonation: Mineral Availability, Pretreatment, Reaction Parametrics and Process Studies. DOE/ARC-TR-04-002. Albany, OR: Albany Research Centre.
Ogden, M. D., Moon, E. M., Wilson, A., and Pepper, S. E. (2017). Application of chelating weak base resin Dowex M4195 to the recovery of uranium from mixed sulfate/chloride media. Chem. Eng. J. 317, 80–89. doi: 10.1016/j.cej.2017.02.041
Olajire, A. A. (2013). A review of mineral carbonation technology in sequestration of CO2. J. Petrol. Sci. Eng. 109, 364–392. doi: 10.1016/j.petrol.2013.03.013
On-Site (2020). Available online at: www.on-sitemag.com/features/1003957345 (accessed April, 2020).
Palandri, J. L., and Kharaka, Y. K. (2004). A Compilation of Rate Parameters of Water-Mineral Interaction Kinetics for Application to Geochemical Modeling. US Geological Survey Open File Report 2004-1068. Available online at: http://www.dtic.mil/cgi-bin/GetTRDoc?Location=U2&doc=GetTRDoc.pdf&AD=ADA440035 (accessed April, 2020).
Pan, S., Chang, E., and Chiang, P. (2012). CO2 capture by accelerated carbonation of alkaline wastes: a review on its principles and applications. Aerosol and Air Qual. Res. 12, 770–791.
Pan, S. Y., Chung, T. C., Ho, C. C., Hou, C. J., Chen, Y. H., and Chiang, P. C. (2017). CO2 mineralization and utilization using steel slag for establishing a waste-to-resource supply chain. Sci Rep. 7:17227. doi: 10.1038/s41598-017-17648-9
Pell, R., Wall, F., Yan, X., Li, J., and Zeng, X. (2019). Mineral processing simulation based-environmental life cycle assessment for rare earth project development: a case study on the Songwe Hill project. J. Environ. Manage 249:109353. doi: 10.1016/j.jenvman.2019.109353
Penner, L. O. W. (2004). “Mineral carbonation: energy costs of pre-treatment options and insights gained from flow loop reaction studies,” in Proceedings of the 3rd Annual Conference on Carbon Capture and Sequestration, Dublin.
Peuble, S., Andreani, M., Gouze, P., Pollet-Villard, M., Reynard, B., and Van de Moortele, B. (2018). Multi-scale characterisation of the incipient carbonation of peridotite. Chem. Geol. 476, 150–160. doi: 10.1016/j.chemgeo.2017.11.013
Power, I. M., Harrison, A. L., Dipple, D. M., Wilson, S. A., Kelemen, P. B., Hitch, M., et al. (2013). Carbon mineralization: from natural analogues to engineered systems. Rev. Mineral. Geochem. 77, 305–360. doi: 10.2138/rmg.2013.77.9
Power, I. M., Harrison, A. L., and Dipple, G. M. (2016). Accelerating mineral carbonation using carbonic anhydrase. Environ. Sci. Technol. 50, 2610–2618. doi: 10.1021/acs.est.5b04779
Quaghebeur, M., Nielsen, P., Horckmans, L., and Mechelen, D. V. (2015). Accelerated carbonation of steel slag compacts: development of high strength construction materials. Front. Energy Res. 3:52. doi: 10.3389/fenrg.2015.00052
Quaghebeur, M., Nielsen, P., Laenen, B., Nguyen, E., and Van Mechelen, D. (2010). Carbstone : sustainable valorisation technology for fine grained steel slags and CO2. Refract. World Forum 2, 75–79.
Raymo, M. E., and Ruddiman, W. F. (1992). Tectonic forcing of late cenozoic climate. Nature 359, 117–122. doi: 10.1038/359117a0
Renforth, P., Pogg von Strandmann, P. A. E., and Henderson, G. M. (2015). The dissolution of olivine added to soil: implications for enhanced weathering. Appl. Geochem. 61, 109–118. doi: 10.1016/j.apgeochem.2015.05.016
Renforth, P., Washbourne, C.-L., Taylder, J., and Manning, D. (2011). Silicate production and availability for mineral carbonation. Environ. Sci. Technol. 45, 2035–2041. doi: 10.1021/es103241w
Research and Markets (2020). Available online at: www.researchandmarkets.com (accessed April, 2020).
Romanov, V. N., Soong, Y., Carney, C., and Rush, G. E. (2015). Mineralisation of carbon dioxide: a literature review. ChemBioEng Rev. 2, 231–256. doi: 10.1002/cben.201500002
Rowland, J. L. (1870). Improvement in the manufacture of artificial stone. U.S. Patent No. 109669. Washington, DC: U.S. Patent and Trademark Office.
Sabapathy, Y. K., Balasubramanian, V. B., Shankari, N., Kumar, A., and Ravichandar, D. (2017). Experimental investigation of surface modified EOF slag as coarse aggregate in concrete. J. King Saud. Univ. Eng. Sci. 29, 388–393. doi: 10.1616/j-jksues.2016.07.002
Sackler Forum (2017). Dealing with Carbon Dioxide at Scale. Available online at: www.royalsociety.org/sackler-forum (accessed April, 2020).
Salman, M., Cizer, Ö., Pontikes, Y., Santos, R. M., Snellings, R., Vandewalle, L., et al. (2014). Effect of accelerated carbonation on AOD stainless steel slag for its val- orisation as a CO2-sequestering construction material. Chem. Eng. J. 246, 39–52. doi: 10.1016/j.cej.2014.02.051
Sanna, A., Uinbu, M., Caramanna, G., Kuusik, R., and Maroto-Valer, M. M. (2014). A review of mineral carbonation technologies to sequester CO2. Chem. Soc. Rev. 43, 8049–8080. doi: 10.1039/c4cs00035h
Shi, C. J., Liu, M., He, P. P., and Ou, Z. H. (2012). Factors affecting the kinetics of CO2 curing of concrete. J. Susuain. Cement Based Mater. 24–25.
Teir, S., Eloneva, S., Fogelholm, C. J., and Zavenhoven, R. (2009). Fixation of carbon dioxide by producing hydromagnesite from serpentinite. Appl. Energy 86, 214–218. doi: 10.1016/j.apenergy.2008.03.013
Teir, S., Kuusik, R., Fogelholm, C., and Zevenhoven, R. (2007). Production of magnesium carbonates from serpentinite for long-term storage of CO2. Int. J. Mineral Process. 85, 1–15. doi: 10.1016/j.minpro.2007.08.007
UNESCO-IOC/SCOR (2007). Ocean Carbon Sequestration: A Watching Brief of the Intergovernmental Oceanographic Commission of UNESCO and the Scientific Committee on Ocean Research. Version 2. Paris: UNESCO.
Vankeuren, A. N. P., Matter, J. M., Stute, M., and Kelemen, P. B. (2019). Multitracer determination of apparent groundwater ages in peridotite aquifers within the Samail ophiolite, Sultanate of Oman. Earth Planet. Sci. Lett. 516, 37–48. doi: 10.1016/j.epsl.2019.03.007
Verduyn, M., Geerlings, H., van Mossel, G., and Jijayakumari, S. (2011). Review of the various CO2 mineralization product forms. Energy Procedia 4, 2885–2892. doi: 10.1016/j.egypro.2011.02.195
Vito (2020). Available online at: www.vito.be/en/carbstone (accessed April. 2020).
von der Assen, N. (2016). From Life-Cycle Assessment Towards Life Cycle Designof Carbon Dioxide Capture and Utilisation. Available online at: http://publications.rwth.aachen.de/record/570980 (accessed March, 2020).
Wang, F., Dreisinger, D. B., Jarvis, M., and Hitchins, T. (2018). The technology of CO2 sequestration by mineral carbonation: current status and future prospects. Can. Metall. Q. 57, 46–58. doi: 10.1080/00084433.2017.1375221
Wang, J., Wu, H., Duan, H., Zillante, G., Zuo, J., and Yuan, H. (2018). Combining life cycle assessment and building information modelling to account for carbon emission of building demolition waste: a case study. J. Clean. Prod. 172, 3154–3166. doi: 10.1016/j.jclepro.2017.11.087
Wilson, S. A., Harrison, A. L., Dipple, G. M., Power, I. M., Barker, S. L. L., Mayer, K. U., et al. (2014). Offsetting of CO2 emissions by air capture in mine tailings at the Mount Keith Nickel Mine, Western Australia: rates, controls and prospects for carbon neutral mining. Int. J. Greenhouse Gas Control 25, 121–140. doi: 10.1016/j.ijggc.2014.04.002
Xie, H., Yue, H., Zhu, J., Li, C., Wang, Y., Xie, L., et al. (2015). Scientific and engineering progress in CO2 mineralization using industrial waste and natural minerals. Engineering 1, 150–157. doi: 10.15302/j-eng-2015017
Young, J. F., Berger, P. L., and Breese, J. (1974). Accelerated curing of compacted calcium silicate mortars on exposure to CO2. J. Am. Ceram. Soc. 57, 394–397. doi: 10.1111/j.1151-2916.1974.tb11420.x
Zevenhoven, R. (2004). Mineral carbonation for long-term CO2 storage: an exergy analysis. Int. J. Appl. Thermodyn. 23, 23–31.
Zevenhoven, R. (2020). Metals Production, Mineralisation and LCA. Metals 10:342. doi: 10.3390/met10030342
Zevenhoven, R., and Fagerlund, J. (2010). “Mineralisation of CO2,” in Developments and Innovation in CCS Technology, ed. M. MarotoValer (Cambridge: Woodhead Publishing Ltd), 433–462. doi: 10.1533/9781845699581.4.433
Zevenhoven, R., Slotte, M., Koivisto, E., and Erlund, R. (2017). Serpentinite carbonation process routes using ammonium sulfate and integration in industry. Energy Technol. 5, 945–954. doi: 10.1002/ente.201600702
Zhang, S., and DePaolo, D. J. (2017). Rates of CO2 mineralisation in geological carbon storage. Acc. Chem. Res. 50, 2075–2084. doi: 10.1021/acs.accounts.7b00334
Keywords: carbon capture, utilization and storage, mineralization of carbon dioxide, calcium carbonate, flue gas, accelerated carbonation, accelerated weathering
Citation: Hills CD, Tripathi N and Carey PJ (2020) Mineralization Technology for Carbon Capture, Utilization, and Storage. Front. Energy Res. 8:142. doi: 10.3389/fenrg.2020.00142
Received: 17 April 2020; Accepted: 10 June 2020;
Published: 14 July 2020.
Edited by:
Rafael Mattos Dos Santos, University of Guelph, CanadaReviewed by:
Hannu-Petteri Mattila, Independent Researcher, Parainen, FinlandMarius Bodor, “Dunarea de Jos” University of Galati, Romania
Copyright © 2020 Hills, Tripathi and Carey. This is an open-access article distributed under the terms of the Creative Commons Attribution License (CC BY). The use, distribution or reproduction in other forums is permitted, provided the original author(s) and the copyright owner(s) are credited and that the original publication in this journal is cited, in accordance with accepted academic practice. No use, distribution or reproduction is permitted which does not comply with these terms.
*Correspondence: Colin D. Hills, Yy5kLmhpbGxzQGdyZS5hYy51aw==; aGMzNEBncmUuYWMudWs=