- CSIRO Energy, Mayfield West, NSW, Australia
In this study, the process of carbon dioxide (CO2) capture directly from ambient air in a conventional monoethanolamine (MEA) absorption process was simulated and optimized using a rate-based model in Aspen Plus. The process aimed to capture a specific amount (148.25 Nm3/h) of CO2 from the air, which was determined by a potential application aiming to produce synthetic methane from the output of a 2.7 MW electrolyser (593 Nm3/h H2). We investigated the technical performance of the process by conducting a sensitivity analysis around different parameters such as air humidity, capture rate defined as a ratio of moles of CO2 captured during the process to the total mole of CO2 in the feed stream, CO2 loading of lean and rich absorption liquids and reboiler temperature, and evaluated the energy consumption and overall cost in this system. In order to meet the design requirement for standard packed columns, the rich absorption liquid was circulated to the top of the absorber. A capture rate of 50% was selected in this process as a baseline. At higher capture rates, the required energy per ton of captured CO2 increases due to a higher steam stripping rate, required in the desorber, and at lower capture rates, the size of equipment, in particular, absorber and blowers increases due to the need for processing a significantly larger volume of air at the given CO2 production volume. At the base case scenario, a reboiler duty of 10.7 GJ/tCO2 and an electrical energy requirement of 1.4 MWh/tCO2 were obtained. The absorber diameter and height obtained were 10.4 and 4.4 m, respectively. The desorber is found to be relatively small at 0.54 m in diameter and 3.0 m in height. A wash water section installed at top of the absorber decreased the MEA loss to 0.28 kg/ton CO2. However, this increased capital cost by around 60% resulting in CO2 capture costs of $1,691 per ton CO2 for the MEA base scenario. Based on the techno-economic analysis, assuming a non-volatile absorbent rather than MEA thereby avoiding a wash water section, and using an absorption column built from cheaper materials, the estimated cost per ton of CO2 produced was reduced to $676/tCO2. The overall cost range was between $273 and $1,227 per ton of CO2 depending on different economic parameters such as electricity ($20–$200/MWh) and heat price ($2–$20/GJ), plant life (15–25 years) and capital expenditure (±30%). In order to reduce the cost further, the use of innovative cheap gas-liquid contactors that operate at lower liquid to gas ratios is crucial.
Introduction
Ongoing use of fossil fuel over the past one and half century led to an increase in the concentration of CO2 in atmosphere from around 280 ppm to just above 400 ppm (Lindsey, 2019). Concerns about the effect of this increase on the global climate resulted in increasing efforts for the development of technologies that enable to remove CO2 directly from atmosphere referred to as Negative Emissions Technologies (McGlashan et al., 2012; McLaren, 2012; Pritchard et al., 2015). Recent studies indicate that in order to prevent the increase of global temperature to about 2°C above the pre-industrial era by the end of this century, the large scale deployment of negative emission technologies is probably required (Gasser et al., 2015).
Among all proposed negative emission technologies (McLaren, 2012; Gasser et al., 2015), the direct capture of CO2 from air (DAC) by physical or chemical processes attracted more attention due to the advantages that this method offers. For instance, DAC technology requires a relatively small area of land and can be located close to the storage/utilization sites or even can be deployed in remote areas where the land is unusable, or on the roofs of buildings in populated cities. It can also provide a larger removal capacity compared to other methods of CO2 removal from atmosphere (Baciocchi et al., 2006). Moreover, DAC was claimed to provide a means for a permanent decrease of CO2 concentration in atmosphere (in fact it can capture 100% of CO2 emission to the atmosphere), for capturing dispersed fugitive emissions, and for direct use in different industries such as beverage, greenhouse, and synthetic fuels production industries (Lackner et al., 1999; Keith, 2009; Lackner, 2009; Krekel et al., 2018).
Several technologies are proposed and investigated in the literature for the direct capture of CO2 from ambient air. Carbon Engineering, Climeworks and Global Thermostat are the three major companies that developed technologies for the large scale capturing of CO2 from air. Carbon Engineering uses a potassium hydroxide solution to capture CO2 and the energy intensive calcination process to regenerate the solvent. On the other hand, the other two companies, Climeworks and Global Thermostat use solid sorbents to capture CO2. They use high temperature and low pressure to regenerate the sorbent. A summary of these studies is shown in Table 1. Based on these studies, DAC is currently considered as an energy-intensive and costly approach for removing CO2 from the atmosphere. However, researchers believe that the high cost and energy consumption in such systems are mostly due to the immaturity of the technology, and hence DAC may be eventually considered as a viable option for removing CO2 from the atmosphere (Field and Mach, 2017; Senftle and Carter, 2017). Further research is under way on different aspects of the process such as the chemistry and stability of liquid and solid sorbents, their effective contact with gas and process modifications in order to reduce the energy requirements and cost of such systems.
The use of aqueous alkaline sorbents such as NaOH, Ca(OH)2, and KOH, based on the concepts of the conventional MEA absorption process, for the DAC application, was claimed to provide a simpler contact between air and sorbents. It was also anticipated that the system can operate continuously with a very long contactor's lifetime as the absorbing liquid in such systems is not subject to degradation reactions. The high cost for the regeneration of the aqueous solutions and water loss are the main disadvantages of such liquid-based absorption systems (Lackner, 2009; Wang et al., 2011; Keith et al., 2018).
While testing CO2 capture systems at large scale is expensive, process simulation programs such as Aspen Plus have been widely used to evaluate the process configurations and identify the optimum operating conditions. There are a number of studies that used Aspen Plus to model CO2 capture from flue gases in MEA-based absorption processes (Desideri and Paolucci, 1999; Freguia and Rochelle, 2003; Alie et al., 2005; Svendsen and Hoff, 2005; Øi, 2007). However to the best of our knowledge, no such simulation study has been conducted for CO2 capture from air. Such a study is believed to be important as it provides a baseline for the technical and economic performance of DAC technologies that use chemical absorption processes.
In this work, using a rate-based model in Aspen Plus, we conducted a comprehensive analysis on the performance of a conventional MEA-based absorption process for capturing CO2 from air, with particular focus on reducing the thermal and electrical energy consumption and, ultimately, the overall cost. The process performance is evaluated against the various parameters such as air humidity, the CO2 loadings of lean and rich solutions, capture rate and reboiler temperature. As a result, a benchmark condition for DAC technologies that use a chemical absorption process is determined and a parametric techno-economic assessment is conducted for this baseline case study. Further analysis of the study results has resulted in the identification of areas for efficiency improvement and cost reduction.
Methodology
Process Description
An MEA-based air capture process was designed to capture CO2 from air. Figure 1 shows the representation of the air capture process using a standard stripping process (a) and a cold rich-split process (b).
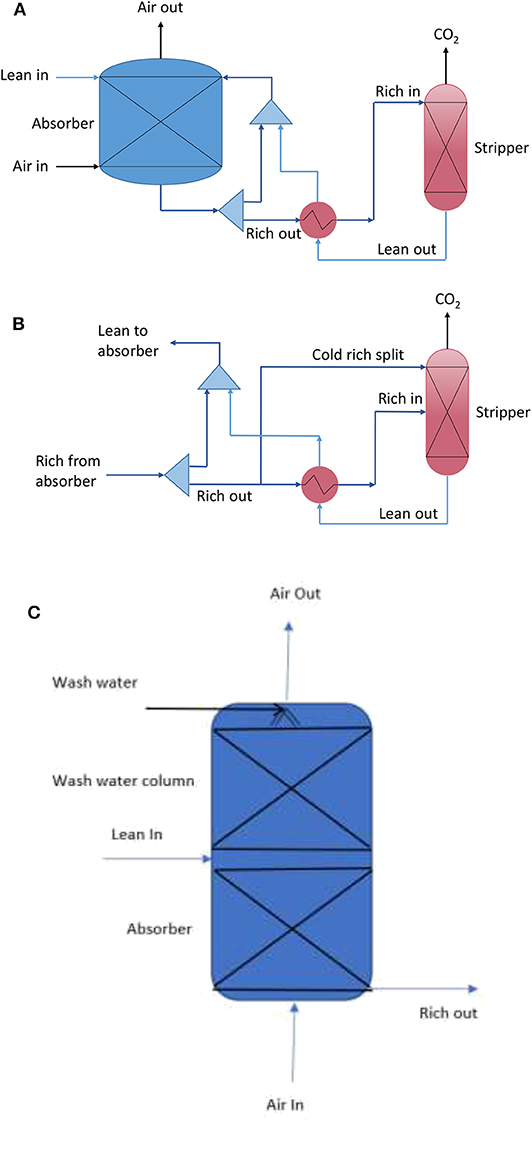
Figure 1. Representation of the MEA-based air capture process using (A) standard stripping process, (B) rich-split process (Cousins et al., 2012), and (C) a wash water column at top of the absorber.
A conventional packed column was utilized for CO2 absorption using a 30 wt% MEA solution, which is typically used for CO2 capture from flue gas. It is important to note that the CO2 concentration in air is ~300 times lower than that in the flue gas from coal-fired power station. Hence the absorption liquid flow could be much lower than that in a flue gas capture system. However, this would give rise to an extremely low liquid to gas ratio (L/G) that could not be achieved in a traditional packed column. In terms of operability, the process design used a liquid recirculation process in which most of the rich CO2 absorption liquid exiting absorber is pumped to the top of absorber in order to achieve a standard L/G of about 2.5 in the absorber, at a 70% flooding ratio. A small portion of the rich absorption liquid is sent to the desorber for CO2 removal. The regenerated lean absorption liquid from the desorber was cooled and mixed with the absorption liquid exiting the absorber, and fed back to the top of absorber for continuous CO2 absorption. The desorption process can be modified using a cold rich-split configuration, i.e., sending a small portion of cold rich absorption liquid to the top of desorber, as shown in Figure 1B, to reduce the reboiler duty.
Process Simulation
A rigorous, rate-based MEA model developed in Aspen Plus was used to simulate the air capture process. The MEA model has been well-validated in previous work at CSIRO (Li et al., 2016; Jiang et al., 2018) against the pilot plant experimental results and laboratory data and is expected to achieve reliable simulation results for the air capture process. Please refer to the Table 1 in the paper published by Li et al. (2016) for further detail about the MEA model.
A series of simulation activities were undertaken to examine the effect of various technical variables on the reboiler duty and equipment size to determine the optimized conditions for a standard MEA-based air capture process. In this optimization, the aim is to minimize the reboiler duty at any given conditions, for example different capture rates etc. The generic simulation conditions used for the CO2 absorption and desorption are provided in Table 2. Technical parameters, i.e., CO2 capture rate, rich CO2 loading, lean CO2 loading and air relative humidity were varied in the simulations, within the ranges shown in Table 2. The process was simulated based on the production of 148.25 Nm3/h of CO2 from the air (0.291 ton/h at standard conditions). This production size determined by a potential application aiming to produce synthetic methane from the output of a 2.7 MW electrolyser that has around 78% efficiency (593 Nm3/h H2).
Once the optimized conditions were determined using the standard absorbent regeneration process, the technical performance was further optimized using the rich-split configuration and the addition of a wash water column (Figure 1C) to the absorber, providing a technical basis for the economic evaluation of the MEA-based air capture process.
Economic Evaluation
With the determination of technical parameters and equipment size of the air capture process, the Aspen Capital Cost Estimator (ACCE) was utilized to estimate the direct costs for the equipment, materials and labor for construction of the air capture plant. The other costings associated with the supportive materials and labor, facilities, engineering, contractors and contingencies for plant construction were estimated based on the direct costs using multiplicative factors. These multiplicative factors were derived from a 2007 report from the Department of Energy, USA (DOE/NETL, 2007) for estimating the capital costs of an early post combustion carbon capture (PCC) plant. The assumptions for capital costs estimation and input data for the air capture process are shown in Table S1. For the costings of plant operation and maintenance, the annual maintenance cost was assumed to be 3% of total capital costs, and 30% of maintenance cost was assumed to be the labor cost (Socolow et al., 2011). The other plant and financial assumptions and economic information for the base case, such as plant capacity, plant life, discount rate, energy price etc. are also provided in Table S1.
Results and Discussion
Technical Performance
In this section, the effects of various parameters on the air capture process are reported. The heat of regeneration and the size of absorber are mainly discussed as they are often the two major costs in CO2 capture process. It should be mentioned again that this process aims to capture a specific amount of CO2 from air (around 0.291 t/h).
Capture Rate
Here it is assumed that a constant amount of CO2 was produced from ambient air using the MEA-based absorption process as the capture rate of the process varied from 20 to 90%. The simulation results revealed that at a capture rate of 90% the reboiler duty was 21.9 GJ/tCO2, almost double the one required in a process with a capture rate of 20% (Figure 2A). This is due to the fact that at lower capture rates, the rich loading is higher, and this results in a lower relative vaporization heat required in the desorber. The decrease in reboiler duty would reduce the operating cost of the air capture process.
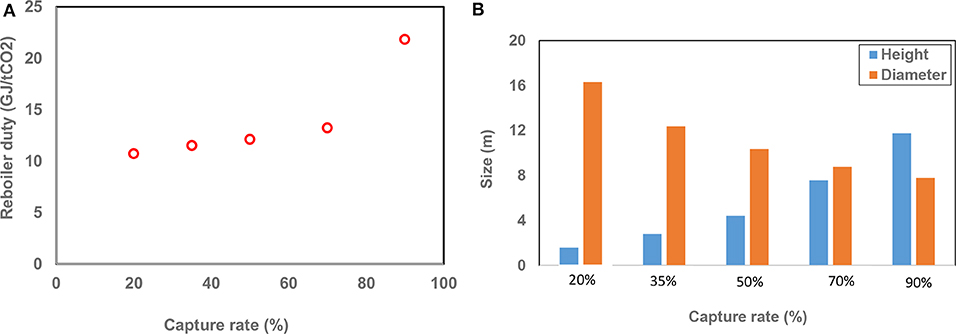
Figure 2. The variation of (A) reboiler duty and (B) the height and diameter of the absorber with capture rate.
Figure 2B shows that the absorption column height required for capturing the specific amount of CO2 in a system with 90% capture rate was almost 6 times greater than that required in a system with 20% capture rate. This is due to the longer contact time between liquid and air required in the system with 90% capture rate. It should be considered that in order to produce a specific amount of CO2 with an air capture system at low capture rate, a significantly larger volume of air needs to be processed. This results in a larger diameter absorption column (Figure 2). This suggests that considering a capture rate of around 50% may be more feasible in terms of cost effectiveness of the air capture process. It should be noted that the optimum capture rate can vary with the economic parameters such as electricity and heat prices. For example, if electricity and heat are available at low cost, the optimum capture rate can be >50%. A summary of operating conditions and results at different capture rates are indicated in Table S2.
An air capture system operating at a low capture rate can also result in an extra number of energy and cost components, such as much higher MEA loss, a more significant circulation rate of rich absorption liquid to the absorber, and a significantly high energy requirement for air movement through the absorption column.
CO2 Loading
The effect of the CO2 loading of lean and rich absorption liquids on the reboiler duty and the size of the absorber were examined at a 50% capture rate. Figure 3A shows that the reboiler duty decreased by about 50% with increasing the lean loading from 0.15 to 0.25. With increasing lean loading, the loading in the recirculation of the absorber increased as well, leading to a lower regeneration duty. Higher rich loadings led to a lower ratio for water vapor to CO2 in the desorber, hence it reduces the heat requirement for vaporization in the desorber. However, as the lean loading and consequently the liquid loading in the absorber recirculation increased, the lower mass transfer driving force led to a taller absorption column. Figure 3B also shows that the column diameter which is mainly dependent on the hydrodynamics of the system expectedly remained unchanged with lean loading. Again, the loss of MEA was significantly higher at higher loadings due to the large volume of air processed. Table S3 lists the simulation's parameter and results for this case study. It is noted that the air humidity of 90% considered in this case changed the results slightly compared to the case when air humidity is 100%.
The effects of CO2 loading of rich absorption liquid on the performance of the process were also investigated. In this set of conditions, a lean loading of 0.2 and a humidity of 100% were used. As evident in Figure 4, the heat of regeneration in the reboiler decreased from 24.1 GJ/tCO2 to about 12.1 GJ/t CO2 with increasing the rich loading from 0.26 to 0.35 mol CO2/mol MEA, which is due to the lower relative vaporization in the desorber at higher rich loadings. As expected, the height of the absorber increased with increasing rich loading.
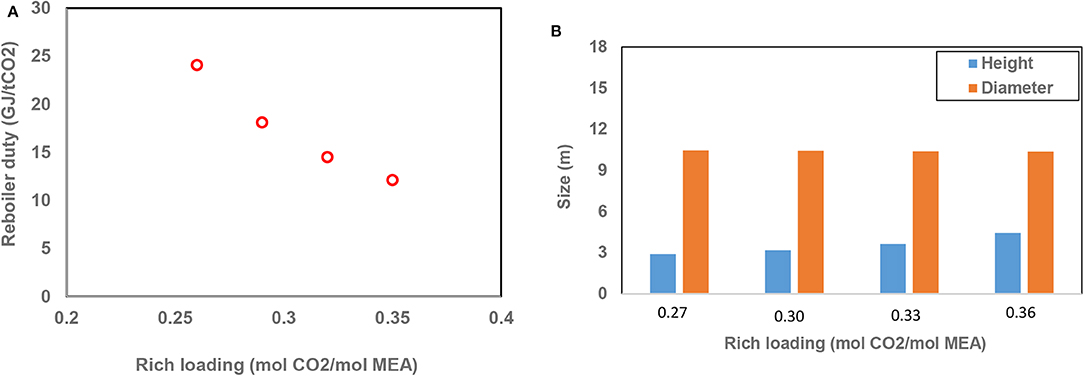
Figure 4. (A) Reboiler duty and (B) absorber size variations with CO2 loading of rich absorption liquid.
Air Humidity
The effect of humidity of inlet air on the air capture process was also evaluated. This is important as the very large volumes of air that pass through the absorber may lead to high rates of water vaporization, depending on humidity of the inlet air. The results indicate that the reboiler duty decreased from 14.4 GJ/tCO2 to around 9.9 GJ/tCO2 when the relative humidity of air increased from 30 to 90% (Figure 5). In the low humidity cases, a massive amount of water was evaporated, which resulted in an absorption liquid containing a higher concentration of MEA. At the fixed pressure in the desorber, the reboiler temperature and the required heat of regeneration consequently increased. Figure 5 also shows that the water loss was around 13 t/tCO2 when the air relative humidity was 30% while it decreased to 2.5 t/tCO2 when a 90% humid air was used. This suggests that preventing water losses would be beneficial when processing relatively dry air. This could be done by applying appropriate water separation system to recover the lost water. Otherwise, there would be a substantial water supplement for the air capture system, in turn increasing the costs of the air capture process.
The humidity of the inlet air had no effect on the height and diameter of the absorber.
Reboiler Temperature
Next, the effect of reboiler temperature on the performance of the air capture process was examined. A lean loading of 0.2, a rich loading of 0.35 and a capture rate of 50% were considered for this case. Figure 6 shows that the reboiler duty decreased significantly with increasing the reboiler temperature. By increasing the reboiler temperature from 123 to 150°C, the reboiler duty decreased by more than 50%, to around 4.0 GJ/tCO2. The operating conditions and results are given in Table S4. The results indicate the importance of alternative absorption liquids to have a higher resistance to thermal degradation. MEA does not lend itself for regenerator temperatures much higher than higher than 120°C. However, there are other amines and amine formulations such as piperazine that could be used at temperature up to 160°C (Rochelle, 2016).
Benchmark Conditions for the Capture Process
According to the results obtained from the sensitivity analysis shown above, a benchmark condition was selected for the capture of CO2 from air using the MEA absorption process. This point was based on a capture efficiency of 50%, a lean loading and a rich loading of 0.2 and 0.35, respectively, and a reboiler temperature of 123°C. The rich split configuration was used in this case study due to its superior energy performance. A detailed analysis was conducted for this base case scenario, which included determination of thermal and electrical energy requirements in this system. The total electricity consumption for air blowers and liquid pumps was calculated to be 1.452 MWh/tCO2, and the reboiler duty was calculated to be 10.7 GJ/tCO2. The absorber height and diameter were calculated to be 6.3 and 10.4 m, respectively. A wash water section, 10.4 m in diameter and 5 m high, was also added to decrease the evaporative loss of MEA to around 0.28 kg/tCO2 (0.04 ppm in exhaust air) during the absorption process. The desorber dimensions are significantly smaller than the absorber dimensions which reflects the large difference in gas and liquid flow rates. The final simulation results for this base case scenario is indicated in Table 3. The break-down of required electrical energy in this process are also indicated in Table 3.
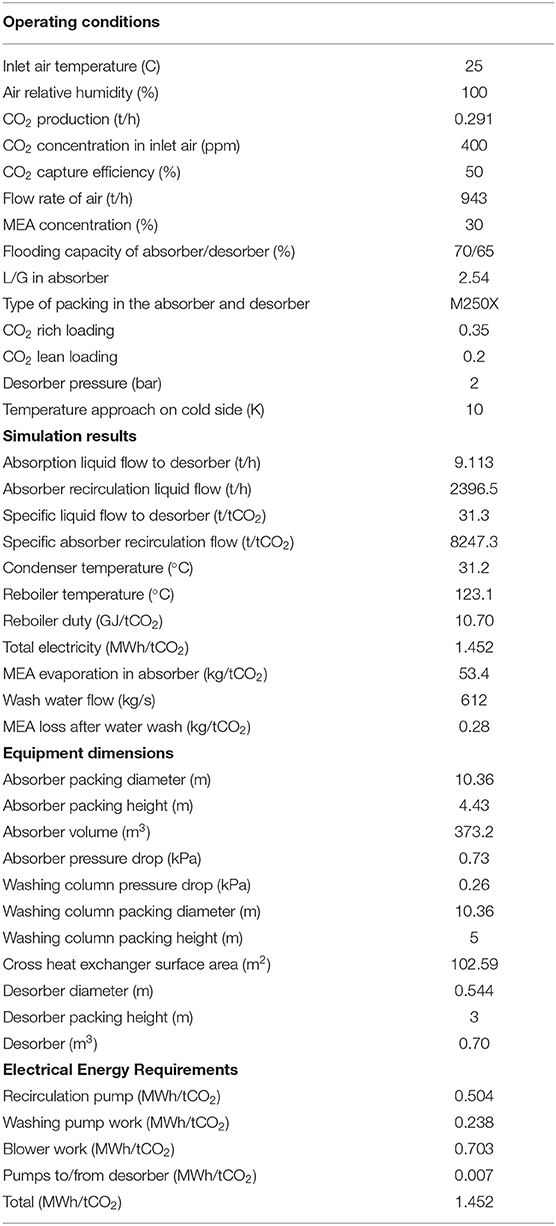
Table 3. The operating conditions and process simulation results for a base case scenario in the air capture process.
Economic Performance of the Base Air Capture Process
CO2 Capture Cost—Standard Chemical Engineering Design
Using the Aspen Capital Cost Estimator with the base case design specified in Table 3 and standard chemical engineering design specifications, the CO2 capture cost was calculated to be $1,691/ton CO2 for the MEA-based air capture. It should be noted here that this estimation is based on particular capture amount of 0.291 tCO2/h (~2,300 tCO2/year). Considering the economy of scale (Blok and Nieuwlaar, 2017), the cost per ton of CO2 captured will be lower for larger scale systems. Table 4 provides the specific costs of major equipment and total investment costs, the operating expenses and the break-down of CO2-capture costs. Figure 7A provides the distribution of capture costs over capital, operating expenses and energy expenses. The capital constitutes 61% of the CO2 capture cost, followed by 23% for O&M, 9% for electricity consumption with heat consumption being the smallest contribution at 7%. The contribution of electricity and heat to the total cost can be significantly reduced if there would be cheaper sources of electricity and heat available for the process. The sensitivity analysis around different economic parameters including the heat and electricity price will be discussed in the next section.
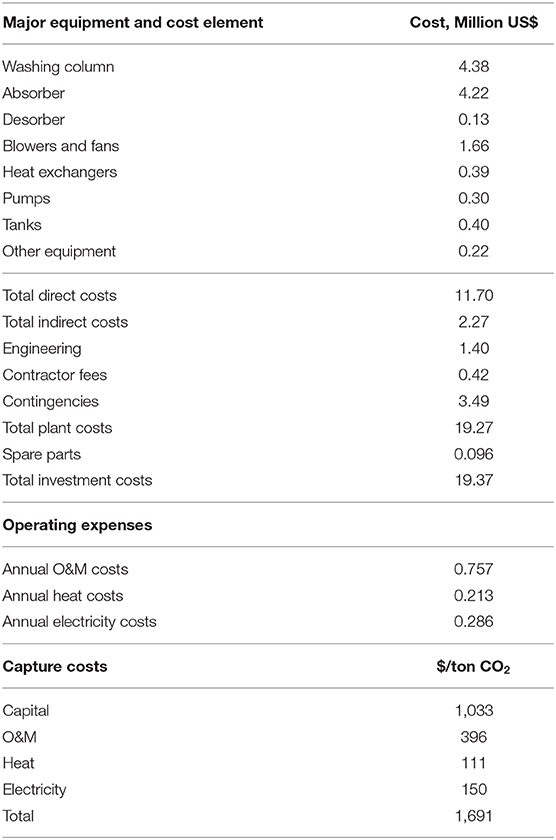
Table 4. Economic performance of MEA-based air capture. All the costs are on a basis of 1st Qtr 2016 US$.
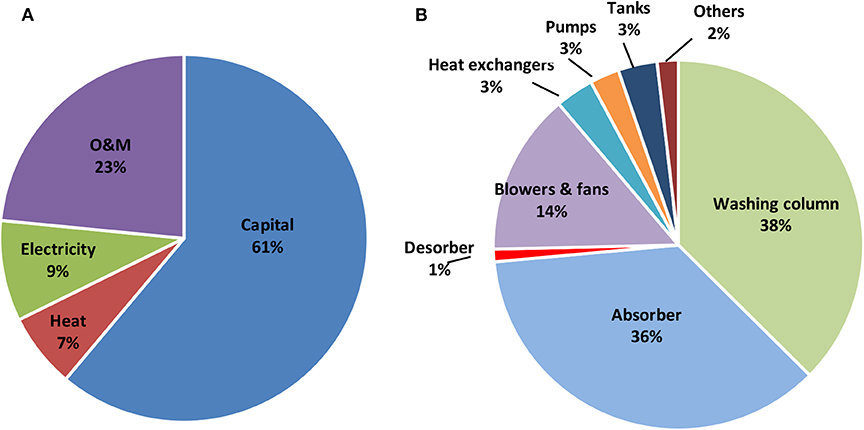
Figure 7. (A) CO2 capture cost distributions on capital, O&M, electricity and heat, and (B) capital cost distributions of major equipment in the MEA-based air capture.
The total capital costs of the MEA-based air capture process were estimated to be $19.37 million for our benchmark MEA-based air capture process. The washing column ($4.38 million) and absorber ($4.22 million) constituted the largest and the second largest capital item among the total capital investment and accounted for 74% of total capital costs, as shown in Figure 7B. Considering that a water cooling system could be difficult to implement on locations with shortage of water, air cooling was used in the present study for the cooling requirement. Due to the large amount of air requirement to meet the high cooling duty of stripper condenser and the large air flow through absorber for CO2 absorption, the costs of blowers and fans accounted for 14% of total capital costs, being the third largest contribution.
By comparison, the annual costs of O&M and energy, i.e., electricity for blowers and pumps and heat for absorbent regeneration, are lower than the capital costs. The electricity costs ($0.286 million/year) were higher than the heating costs ($0.213 million/year) owing to the large electricity consumption for air transfer through the columns and solution pumping and the high circulation for CO2-absorption and washing. It should be noted here that, in the base case, if less humid air than 100% was used, the added cost due to water evaporation in this process would be up to $4/tCO2, which is still negligible in comparison with other cost components shown in Table 4.
For the base case, a plant life of 20 years, a discount rate of 8%, a capacity factor of 90%, heat price of $10/GJ and electricity price of $100/MWh were considered. A sensitivity analysis shows that with variation of equipment costs in the range of 30%, the CO2 capture cost varied between $1,262 and $2,120/ton CO2, a 34% decrease/increase with the 30% decrease/increase in capital costs. This again suggests that decreasing the process equipment costs would significantly reduce the cost of CO2 capture from air. This can be achieved by three aspects: (1) enhancing mass transfer between absorbent and CO2 through more efficient gas-liquid contacting in order to reduce the equipment size of CO2 absorption, (2) absorbents that have lower evaporation of absorbent (water and amine) to the air in order to minimize the size of equipment for emission control, and (3) seeking cheaper materials for equipment manufacture in order to reduce the equipment costs. In the following section, these elements for reducing the cost of the air capture process will be explored qualitatively.
CO2 Capture Cost—New Design
As described, the wash water section and absorber constitute 45% of total cost in the process, hence using an alternative absorption liquid with low vapor pressure and replacing the packings and absorber materials with cheaper materials can drastically reduce the total cost of the process.
– Use of alternative absorption liquid
Owing to the contact between the large volume of air and the small amount of liquid in the air capture process, MEA is evaporated during the absorption process. As discussed in section Benchmark Conditions for the Capture Process, this necessitates the use of a large wash water section after the CO2 absorber, and hence creates an additional cost to the process. As shown in Figure 7B, 38% of capital cost is related to this wash water section, which in fact constitutes around 25% of total cost of the process.
Amino acid salts solutions have been proven to have a potential for absorbing CO2 with an effectiveness that matches that of MEA (Aronu et al., 2010; Jockenhövel and Schneider, 2011; Ciftja et al., 2013; Guo et al., 2013; Wei et al., 2014; He et al., 2017). These salts do not impose any amine vapor. Based on the assumption that they show the same performance as MEA in the CO2 capture process, if they are used in the air capture process, the need for the wash water section can be eliminated from the process. This will reduce the capital cost of the CO2 capture process from $1,033 to around $640 per ton of CO2. This will also decrease the electrical energy requirement from 1.452 MWh/tCO2 to around 1.03 MWh/tCO2, as the washing water pump is no longer required, and less energy will be required for blowing the air into the absorber. This will reduce the electricity cost from $150 to around $126 per ton of CO2.
– Use of cheap plastic packings
Based on the techno-economic analysis in APS report (Socolow et al., 2011) and details by Carbon Engineering (Holmes and Keith, 2012; Keith et al., 2018), cost of packing materials can be up to one third of the total cost of major equipment. Using the cheap plastic packings as proposed by Carbon Engineering, the cost was reported to be 1/6 of standard stainless steel packings such as Sulzer Mellachevron 250X. Assuming the same cost for Mellapak 250X and Sulzer Mellachevron 250X, this reduces the cost of packings in this process from $1,190,000 to around $198,000. The absorber cost reduction is around 23% from $372/ton of CO2 to around $285/ton of CO2 (another $87 reduction in capital cost to $554 per ton of CO2).
– Use of cheap materials in absorber structure
The cost of the absorber structure was reported to be around $2,300 and $3,700 per inlet area of absorbers (m2) for cooling tower and contactors used in Carbon Engineering's process (Holmes and Keith, 2012), respectively, while based on the APS report (Socolow et al., 2011), the cost for a conventional absorption tower is around $15,800 per inlet area of absorber (m2). This shows that the cost of the absorber using a standard chemical engineering design specification is around 6 times more than the structure used in the cooling towers/Carbon Engineering systems. This means that if the absorption column used in this work is replaced by a cooling tower system, the cost of absorber structure will be reduced by 83% from $30,32,800 to around $505,460. This reduces the absorber cost by another 60% to $62 per ton of CO2 which is close to the number reported by Carbon Engineering. The total capital cost contribution of capturing CO2 from air will be decreased to $317 per ton of CO2. It is assumed that the cheaper absorber equipment materials used are resistant toward to the amino-acid based absorption liquids.
The details of techno economic result based on the new design are given in Table 5. The final cost of capturing CO2 from air is $676/ton of CO2, which is close to the cost reported by Climeworks (Climeworks press release, 2017; Marshall, 2017) ($600/ton of CO2) and in the APS report (Socolow et al., 2011) ($610/ton of CO2).
Figure 8 shows different cost components of the new liquid-based absorption process that was designed based on new absorption liquids, packings and absorber materials. In this new design, capital investment is still the main contributor to the total cost of the process. Among the major equipment, the cost of blowers and fans for moving the massive amount of air has now become the major part in the capital investment.
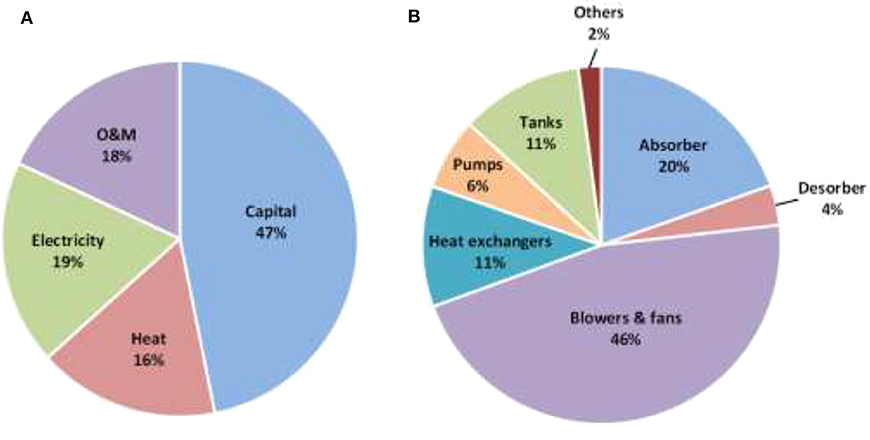
Figure 8. (A) CO2 capture cost distributions on capital, O&M, electricity and heat, and (B) capital cost distributions of major equipment in the MEA-based air capture.
Sensitivity Analysis
The parameters used for the base case economic analysis are: 20 year plant life, 8% discount rate, 90% availability factor, $10/GJ heat cost and $100/MWh electricity cost. The effects of various economic parameters, such as plant life, heat and electricity unit cost, discount rate and equipment costs for the air capture process, on the economic performance were analyzed, with the results summarized in Figure 9. With variation of equipment costs in the range of 30%, the CO2 capture cost varied between $545 and $808/ton CO2. The discount rate also has a significant impact on the CO2 capture cost. With a discount rate ranging from 4 to 12%, the cost of CO2 capture ranged from $588 and $876/ton CO2. Here, increasing plant life from 15 to 25 years, the cost of CO2 captured varied by 10%, from $655 to $723/ton CO2.
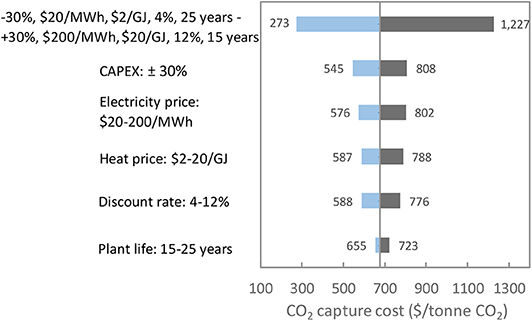
Figure 9. Effect of economic variables on the CO2 capture cost. The parameters used for the base case are: 20-year plant life, 8% discount rate, 90% capacity factor, $10/GJ heat price and $100/MWh electricity price.
A wide range of electricity prices from $20 to $200/MWh and heat prices from $2 to $20/GJ were considered in this study, providing various possibilities of electricity and heat sources applicable to the air capture process. The CO2 capture cost varied by 39% from $576 to $802/ton CO2 and 34% from $587 to $788/ton CO2, as the prices of electricity ($20-$200/MWh) and heat ($2–$20/GJ) varied by a factor of 10, respectively. The use of zero-carbon energy, e.g., renewables or nuclear, in the air capture process is most likely required to avoid any additional CO2 emission to air due to the energy consumption for the capture process.
Based on a sensitivity analysis on all variables, considering the most desirable and the most undesirable values for various economic parameters, the overall cost of capturing a ton of CO2 ranges from $273 to $1227.
Energy and Cost in Comparison With Other Air Capture Studies
There are only a few studies that reported the required energy and cost for the capture of CO2 from air. Using different technologies such as absorption and adsorption, the required thermal energy for the direct capture of CO2 from air was reported to be almost 4–8 times larger than the required electrical energy. The cost of capturing one ton of CO2 was reported to be between $100–1,000 (Keith et al., 2005, 2018; Heidel et al., 2011; House et al., 2011; Kulkarni and Sholl, 2012). The difference between the ranges reported for capture cost in this study and in literature originates from the fact that both were estimated using different technologies and economic assumptions around interest rates, plant life, electricity price and heat price etc. Figure 10 shows the required electrical and thermal energy and total cost estimated in this work in comparison with the other air capture systems. It should be noted that there is insufficient detail on the energy consumption and cost of the other technologies that are still under development (shown in Table 1).
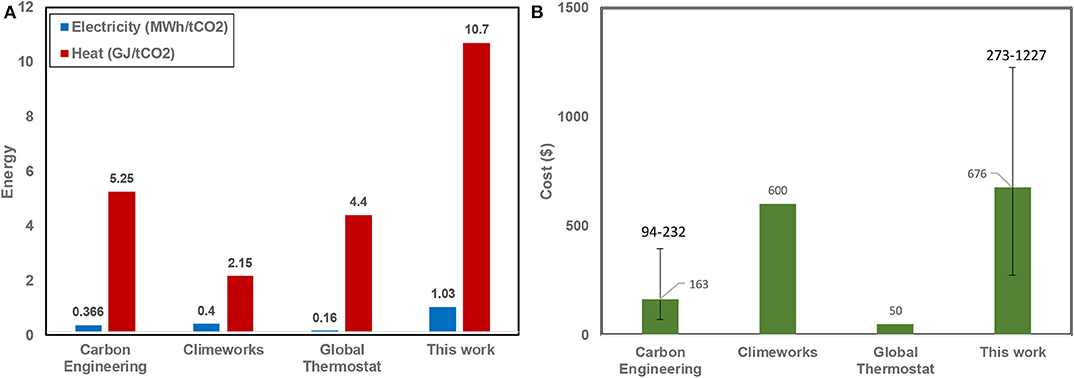
Figure 10. (A) Energy consumption and (B) total cost reported in different studies for direct air capture processes. Note that $50/tCO2 reported by Global Thermostat was the cost that they anticipated to achieve. No information whether they have achieved this. Also, this work and Carbon Engineering's study reported a range for the cost of the process, based on various economic parameters.
For the baseline case chosen in this study, the thermal energy required is 10.7 GJ/t CO2 which is almost 3 times greater than the required electricity (~1.03 MWh/tCO2). These are significantly larger than those reported in other studies. This is mainly due to different characteristics of this technology compared to others, for example the large recirculation of rich solvent is required here to prevent loading/flooding in the absorption column (it constitutes around 50% of total electricity requirement). Figure 10 also shows that the total cost for capturing one ton of CO2 from air using the new liquid absorption process was estimated to be around $676, in compared with the cost reported by the other researchers using their technologies ($93–232 in CE, $600 in CW, and $50 in GT). This includes $317 and $359 related to capital cost and operating cost, respectively.
As previously indicated in Table 1, the only technology in the market that uses a liquid sorbent for air capture is the one developed and demonstrated by Carbon Engineering, based on sodium hydroxide, with subsequent transfer of CO2 from sodium carbonate to calcium carbonate and CO2 recovery via a calcination process. To compare, our estimated CO2 capture cost is higher than the reported results of $94–232/tCO2 from Carbon Engineering. This is attributed both to the higher capital costs ($255–379/tCO2) and operating cost ($290–$430/tCO2) in our system compared to the costs for Carbon Engineering one (capital: $64-$120/tCO2, the operating cost: $30-$110/tCO2).
The design of the Carbon Engineering gas-liquid contactor reduces the energy requirement and capital costs of blowers and fans. They use a horizontally oriented crossflow cooling tower, resulting in a low pressure drop, while in our study, we considered a vertically counter-current flow packed tower, significantly increasing the energy and capital costs of air movement in our system.
Based on the cost analysis described above, the other areas that can be improved in order to further reduce the capital and operating cost in the air capture system are:
1. If new air-liquid contactor is designed to optimize the contact between the large volume of air and small amount of liquid, this will eliminate the necessity for the large circulation rate/pumping of absorption liquids which consumes 0.54 MWh/tCO2 electricity (around 50% of total electricity requirement) and hence reduce the capital and operating cost. In this case, the electricity cost reported in Table 5 can be reduced by 50% to around $63.
2. Development of new liquid absorbents and applying process modifications. If the reboiler temperature can be increased to 150°C, the absorbent heat requirement will be reduced by 60% to around 4 GJ/tCO2. The cost for heat reported in Table 5 will be therefore reduced by 60% to around $44. This in fact necessitates new absorption liquids that are more stable at high temperature compared with MEA.
Conclusion
The technical and economic aspects of a conventional MEA-based absorption process for capturing CO2 directly from air was simulated using a rate-base model in Aspen Plus. A benchmark condition was defined and further explored through a sensitivity analysis involving different parameters. It is concluded that:
– In an air capture system with a low capture rate, the heat required for the regeneration of absorption liquid per ton of captured CO2 is significantly lower. However, a large volume of air needs to be processed and this results in a larger unit and hence a higher capital cost.
– Owing to the very low concentration of CO2 in air, the amount of liquid required for the contact with air would be extremely low. To meet the operational requirement of a conventional packed column, a large liquid circulation around the absorber is required, resulting in a large electricity requirement.
– At the base case scenario, a capture rate of 50% was selected. The reboiler duty was 10.7 GJ/tCO2 and the electrical energy requirement was 1.4 MWh/tCO2. The absorber diameter and height were 10.4 and 4.4 m, respectively and the wash water section was 5 m in height.
– Owing to the large volume of air used in the air capture process, water and MEA losses due to evaporation were quite high. The addition of a wash water section to the absorber can reduce the MEA evaporation significantly down to 0.28 kg/ton of CO2 (0.04 ppm), at the expense of increased capital costs.
– Using the standard chemical engineering design which may not necessarily required for the air capture process, the total estimated cost for this process was around $1,690/ton CO2. The capital cost and operating cost were $1031/ton CO2 and $659/ton CO2, respectively.
– The wash water section and absorber accounted for around 74% of total capital cost of this process. Using an alternative absorption liquid with negligible vapor pressure which allows for the removal of the wash water section, the capital cost will be reduced by $393 per ton of CO2.
– The replacement of stainless steel packing and absorption column materials by cheaper materials like those used in cooling towers reduced the capital cost by another $323 per ton of CO2.
– The techno-economic analysis of the air capture process designed based on the cooling tower technology and non-volatile liquid absorbent showed that the cost for CO2 capture from air was, in the range of US$273 to US$1,227. Around 45% and 55% of this were attributed to the capital cost and operating cost, respectively.
In summary, this study provides an economic baseline for the air capture technologies that aim to use liquid-based capture process. Even though the energy requirement and cost of the baseline for such processes are still high with respect to the current CO2-price, even for the CO2-price in the framework of the Californian Low Carbon Fuel Standard (Low Carbon Fuel Standard, 2020), it is believed that the energy and equipment cost of the liquid-based air capture processes can be significantly reduced when this technology further matures and is scaled up to larger plant sizes. The use of cheap materials and more effective ways of contacting air and absorption liquids, using more robust and economical absorption liquids and innovative process modifications is required to further reduce the cost of this process. Also, if the CO2 captured from atmosphere is utilized to produce synthetic fuels, then the process can be considered more economically favorable.
Data Availability Statement
The datasets for this article are not publicly available because the data ownership and control must stay with CSIRO for propriety reasons. Requests to access the datasets should be directed to Paul Feron (cGF1bC5mZXJvbkBjc2lyby5hdQ==).
Author Contributions
AK drafted the manuscript and analyzed and integrated the research results. KJ performed the process modeling and did the techno-economic analysis. PF conceived and designed the research work and analyzed research results. All authors contributed to the review and editing of the manuscript.
Conflict of Interest
The authors declare that the research was conducted in the absence of any commercial or financial relationships that could be construed as a potential conflict of interest.
Acknowledgments
This activity received funding from ARENA (Australian Renewable Energy Agency) as part of ARENA's Research and Development Program—Renewable Hydrogen for Export. The views expressed here are not necessarily the views of the Australian Government and the Australian Government does not accept responsibility for any information and advice contained herein.
Supplementary Material
The Supplementary Material for this article can be found online at: https://www.frontiersin.org/articles/10.3389/fenrg.2020.00092/full#supplementary-material
References
Alie, C., Backham, L., Croiset, E., and Douglas, P. L. (2005). Simulation of CO2 capture using MEA scrubbing: a flowsheet decomposition method. Energy Conv. Manag. 46, 475–487. doi: 10.1016/j.enconman.2004.03.003
Aronu, U. E., Svendsen, H. F., and Hoff, K. A. (2010). Investigation of amine amino acid salts for carbon dioxide absorption. Int. J. Greenh. Gas Control 4, 771–775. doi: 10.1016/j.ijggc.2010.04.003
Baciocchi, R., Storti, G., and Mazzotti, M. (2006). Process design and energy requirements for the capture of carbon dioxide from air. Chem. Eng. Process. Process Intensif. 45, 1047–1058. doi: 10.1016/j.cep.2006.03.015
Blok, K., and Nieuwlaar, E. (2017). Introduction to Energy Analysis. London: Routledge. doi: 10.4324/9781315617213
Chichilniski, G. (2018). Global Thermostat. Available onine at: https://www.usea.org/event/global-thermostats-flexible-co2-capture-technology
Ciftja, A. F., Hartono, A., and Svendsen, H. F. (2013). Selection of amine amino acids salt systems for CO2 capture. Energy Proc. 37, 1597–1604. doi: 10.1016/j.egypro.2013.06.035
Climeworks press release (2017). World-First Climeworks Plant: Capturing CO2 From Air to Boost Growing Vegetables. Available online at: http://www.climeworks.com/wp-content/uploads/2017/05/02_PR-Climeworks-DAC-Plant-Case-Study.pdf
Cousins, A., Cottrell, A., Lawson, A., Huang, S., and Feron, P. H. M. (2012). Model verification and evaluation of the rich-split process modification at an Australian-based post combustion CO2 capture pilot plant. Greenh. Gas. Sci. Technol. 2, 329–345. doi: 10.1002/ghg.1295
Desideri, U., and Paolucci, A. (1999). Performance modelling of a carbon dioxide removal system for power plants. Energy Conv. Manag. 40, 1899–1915. doi: 10.1016/S.0196-8904(99)00074-6
Field, C. B., and Mach, K. J. (2017). Rightsizing carbon dioxide removal. Science 356, 706–707. doi: 10.1126/science.aam9726
Freguia, S., and Rochelle, G. T. (2003). Modeling of CO2 capture by aqueous monoethanolamine. AIChE J. 49, 1676–1686. doi: 10.1002/aic.690490708
Gasser, T., Guivarch, C., Tachiiri, K., Jones, C. D., and Ciais, P. (2015). Negative emissions physically needed to keep global warming below 2 °C. Nat. Commun. 6:7958. doi: 10.1038/ncomms8958
Guo, D., Thee, H., Tan, C. Y., Chen, J., Fei, W., Kentish, S., et al. (2013). Amino acids as carbon capture solvents: chemical kinetics and mechanism of the glycine + CO2 reaction. Energy Fuels 27, 3898–3904. doi: 10.1021/ef400413r
He, F., Wang, T., Fang, M., Wang, Z., Yu, H., and Ma, Q. (2017). Screening test of amino acid salts for CO2 absorption at flue gas temperature in a membrane contactor. Energy Fuels 31, 770–777. doi: 10.1021/acs.energyfuels.6b02578
Heidel, K., Keith, D., Singh, A., and Holmes, G. (2011). Process design and costing of an air-contactor for air-capture. Energy Proc. 4, 2861–2868. doi: 10.1016/j.egypro.2011.02.192
Holmes, G., and Keith, D. W. (2012). An air-liquid contactor for large-scale capture of CO2 from air. Philos. Trans. A Math. Phys. Eng. Sci. 370, 4380–4403. doi: 10.1098/rsta.2012.0137
House, K. Z., Baclig, A. C., Ranjan, M., van Nierop, E. A., Wilcox, J., and Herzog, H. J. (2011). Economic and energetic analysis of capturing CO2 from ambient air. Proc. Natl. Acad. Sci.U.S.A. 108, 20428–20433. doi: 10.1073/pnas.1012253108
Jiang, K., Li, K., Puxty, G., Yu, H., and Feron, P. H. (2018). Information derivation from vapour-liquid equilibria data: a simple shortcut to evaluate the energy performance in an amine-based post-combustion CO2 capture. Environ. Sci. Technol. 52, 10893–10901. doi: 10.1021/acs.est.8b03512
Jockenhövel, T., and Schneider, R. (2011). Towards commercial application of a second-generation post-combustion capture technology - pilot plant validation of the siemens capture process and implementation of a first demonstration case. Energy Proc. 4, 1451–1458. doi: 10.1016/j.egypro.2011.02.011
Keith, D. W. (2009). Why capture CO2 from the atmosphere? Science 325, 1654–1655. doi: 10.1126/science.1175680
Keith, D. W., Ha-Duong, M., and Stolaroff, J. K. (2005). Climate strategy with CO2 capture from the air. Clim. Change 74, 17–45. doi: 10.1007/s10584-005-9026-x
Keith, D. W., Holmes, G., St. Angelo, D., and Heidel, K. (2018). A process for capturing CO2 from the atmosphere. Joule 2, 1573–1594. doi: 10.1016/j.joule.2018.05.006
Krekel, D., Samsun, R. C., Peters, R., and Stolten, D. (2018). The separation of CO2 from ambient air - a techno-economic assessment. Appl. Energy 218, 361–381. doi: 10.1016/j.apenergy.2018.02.144
Kulkarni, A. R., and Sholl, D. S. (2012). Analysis of equilibrium-based TSA processes for direct capture of CO2 from air. Ind. Eng. Chem. Res. 51, 8631–8645. doi: 10.1021/ie300691c
Lackner, K., Ziock, H.-J., and Grimes, P. (1999). “Carbon dioxide extraction from air: is it an option?,” Paper Presented at the 24th Annual Technical Conference on Coal Utilization and Fuel Systems (Clearwater, FL).
Lackner, K. S. (2009). Capture of carbon dioxide from ambient air. Eur. Phys. J. Spec. Top. 176, 93–106. doi: 10.1140/epjst/e2009-01150-3
Li, K., Cousins, A., Yu, H., Feron, P., Tade, M., Luo, W., et al. (2016). Systematic study of aqueous monoethanolamine-based CO2 capture process: model development and process improvement. Energy Sci. Eng. 4, 23–39. doi: 10.1002/ese3.101
Low Carbon Fuel Standard (2020). 2011–2018 Performance of the Low Carbon Fuel Standard. Available online at: https://ww3.arb.ca.gov/fuels/lcfs/dashboard/dashboard.htm (accessed March 18, 2020).
Marshall, C. (2017). “In Switzerland, a giant new machine is sucking carbon directly from the air,” in Science. Available online at: https://www.sciencemag.org/news/2017/06/switzerland-giant-new-machine-sucking-carbondirectly-air
McGlashan, N., Shah, N., Caldecott, B., and Workman, M. (2012). High-level techno-economic assessment of negative emissions technologies. Process Saf. Environ. Protect. 90, 501–510. doi: 10.1016/j.psep.2012.10.004
McLaren, D. (2012). A comparative global assessment of potential negative emissions technologies. Process Saf. Environ. Protect. 90, 489–500. doi: 10.1016/j.psep.2012.10.005
Øi, L. (2007). “Aspen HYSYS simulation of CO2 removal by amine absorption from a gas based power plant,” Paper Presented at the SIMS2007 Conference (Gothenburg).
Pritchard, C., Yang, A., Holmes, P., and Wilkinson, M. (2015). Thermodynamics, economics and systems thinking: what role for air capture of CO2? Process Saf. Environ. Protect. 94, 188–195. doi: 10.1016/j.psep.2014.06.011
Rochelle, G. T. (2016). “Conventional amine scrubbing for CO2 capture,” in Absorption-Based Post-Combustion Capture of Carbon Dioxide, ed P. H. M. Feron (Woodhead Publishing Series in Energy), 35–67.
Sandalow, D., Friedmann, J., McCormick, C., and McCoy, S. (2018). “Direct Capture of Carbon Dioxide: ICEF Roadmap,” in Innovation for Cool Earth Forum. Available online at: https://www.icef-forum.org/pdf2018/roadmap/ICEF2018_DAC_Roadmap_20181210.pdf
Senftle, T. P., and Carter, E. A. (2017). The holy grail: chemistry enabling an economically viable CO2 capture, utilization, and storage strategy. Acc. Chem. Res. 50, 472–475. doi: 10.1021/acs.accounts.6b00479
Socolow, R., Desmond, M., Aines, R., Blackstock, J., Bolland, O., Kaarsberg, T., et al. (2011). Direct Air Capture of CO2 With Chemicals: A Technology Assessment for the APS Panel on Public Affairs. American Physical Society.
Svendsen, H. F., and Hoff, K. A. (2005). Desorber energy consumption amine based absorption plants AU - tobiesen, finn andrew. Int. J. Green Energy 2, 201–215. doi: 10.1081/GE-200058981
Wang, T., Lackner, K. S., and Wright, A. (2011). Moisture swing sorbent for carbon dioxide capture from ambient air. Environ. Sci. Technol. 45, 6670–6675. doi: 10.1021/es201180v
Keywords: CO2 capture, techno—economical assessment, chemical absorbents, amine, air capture
Citation: Kiani A, Jiang K and Feron P (2020) Techno-Economic Assessment for CO2 Capture From Air Using a Conventional Liquid-Based Absorption Process. Front. Energy Res. 8:92. doi: 10.3389/fenrg.2020.00092
Received: 06 December 2019; Accepted: 29 April 2020;
Published: 29 May 2020.
Edited by:
Mai Bui, Imperial College London, United KingdomReviewed by:
Joan Ramón Morante, Institut de Recerca de l'Energia de Catalunya, SpainStefano Stendardo, Italian National Agency for New Technologies, Energy and Sustainable Economic Development (ENEA), Italy
Copyright © 2020 Kiani, Jiang and Feron. This is an open-access article distributed under the terms of the Creative Commons Attribution License (CC BY). The use, distribution or reproduction in other forums is permitted, provided the original author(s) and the copyright owner(s) are credited and that the original publication in this journal is cited, in accordance with accepted academic practice. No use, distribution or reproduction is permitted which does not comply with these terms.
*Correspondence: Paul Feron, cGF1bC5mZXJvbkBjc2lyby5hdQ==