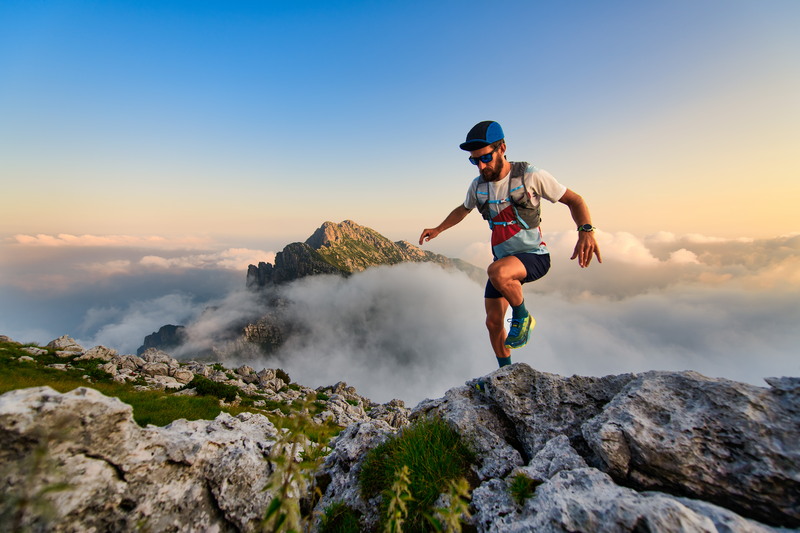
95% of researchers rate our articles as excellent or good
Learn more about the work of our research integrity team to safeguard the quality of each article we publish.
Find out more
ORIGINAL RESEARCH article
Front. Energy Res. , 17 January 2020
Sec. Nuclear Energy
Volume 7 - 2019 | https://doi.org/10.3389/fenrg.2019.00167
This article is part of the Research Topic Safety Analysis of Nuclear Reactor Thermal-Hydraulics View all 12 articles
Thermoelectric conversion system, as one of the keys of space nuclear power supply system, is of great significance to the development and application of space nuclear power source. Thermion thermoelectric conversion system is a kind of thermoelectric conversion technology with potential for development, it has simple equipment and compact structure, but its conversion efficiency is limited by the inherent characteristics of the heat ion Energy converter, in order to improve the conversion efficiency of the thermionic energy converter, the thermionic energy converter and thermoelectric generator are coupled. In this paper, the thermionic-thermoelectric generator is taken as the research object, and the thermodynamic analysis and calculation of the thermionic-thermoelectric generator model is carried out by using the existing formula, on the basis of which the appropriate parameters are selected to optimize the system performance.
Space nuclear power is very important for deep space exploration, and the thermoelectric conversion efficiency of space nuclear power devices has a very important impact on the whole system. Thermoelectric conversion is divided into static conversion and dynamic conversion. Dynamic conversion mainly includes Stirling cycle, Rankine cycle, and Brayton cycle. Static conversion includes thermionic conversion, alkali metal conversion, temperature difference conversion, and MHD power generation.
Thermion thermoelectric conversion is a kind of static thermoelectric convention device that can conveniently convert the heat energy at relatively high temperatures into electricity (Yarygin, 2012). At present, only thermionic conversion and temperature difference conversion are used in nuclear power plants. Thermionic conversion has the advantages of small system volume and light weight, but short service life and low efficiency (Albertoni et al., 2013). Since the beginning of the last century, research on space nuclear thermionic thermoelectric conversion has been carried out. The thermoelectric conversion method adopted by the power supply of the two TOPAZ space nuclear reactors successfully launched by Russia is thermionic thermoelectric conversion. TOPAZ-I was in orbit for 6 months until cesium was consumed. TOPAZ-II uses a single section of thermionic original, and can be electrically heated on the test bench before launching. But its efficiency is not ideal. In order to improve the efficiency of thermoelectric conversion, the energy conversion efficiency of thermion conversion is closely dependent on the materials of the cathode working at higher temperatures and the space charge effect (Bellucci et al., 2016). El-Genk et al. established a thermionic transient analysis model (TITAM) to analyze the steady state and transient state of the power system of a thermionic nuclear reactor. The research has reference value for space nuclear power thermionic conversion (El-Genk et al., 1993). Covas Nickoff proved that adding barium vapor to cesium vapor can ensure the emitter to reach the best work function, thus improving the conversion efficiency. NASA developed program code to analyze flowing fluid in space radiators (Hainley, 1991). GRC has developed LERCHP code, which can determine the operating temperature of radiator under specific conditions (Tower et al., 1992). El-Genk proposed that micro-nano technology can be used to reduce the work function on the emitter surface, thus improving the conversion efficiency (Paramonov and El-Genk, 1997). Jensen proposed a micro-ridge arrangement of electrodes, which is beneficial for electrons to face the receiving electrode and can improve the overall current density (Jensen et al., 2006). Mannhart suggests that graphene or related 2D materials can be treated as gate electrodes because electrons with energies between 2 and 40 eV have a transparency of up to 60% (Hassink et al., 2015; Wanke et al., 2016). Koeck and Nemanich have developed nitrogen doped nano diamond films with effective work function as low as 1.99eV (Koeck and Nemanich, 2006). Zhang et al. have done a lot of work on the design and performance analysis of liquid metal heat pipe radiators for space nuclear energy systems (Zhang et al., 2016a,b). Wang et al. modified and applied the system analysis code RELAP5 to provide more detailed transient thermal-hydraulic characteristics of space nuclear energy systems (Tang et al., 2019).
Research has proved that there is not much room to improve the efficiency of thermionic conversion due to its working principle. However, the electrode still has a high temperature after thermionic thermoelectric conversion. These energies are directly discharged into space and are not well-utilized. In this paper, thermionic conversion and thermoelectric generation are combined to utilize waste heat after thermionic conversion and improve conversion efficiency.
The direct conversion of heat energy into electrical energy is called thermion conversion by the phenomenon of transmitting electrons at high temperature of metal. At a non-0 temperature, when the metal is immersed in rare gas vapor, charged particles, such as electrons, ions, emitted from the metal surface like vapor are called thermion emission (Hatsopoulos and Gyftopoulos, 1973).
Thermoelectric conversion devices based on the principle of thermion emission are called thermionic energy converters. The thermionic energy converter consists of a emitter that emits electrons, a receiving stage that receives electrons, and a metal ceramic seal that separates two electrodes. The thermionic energy converter is insulated and sealed (Liao et al., 2016; Chen et al., 2017). At work, the emitter is heated to a very high temperature. The free electrons on the metal surface get enough energy and leap the electrode clearance, then reach the receiving stage. The electrons work on the load through the outer circuit connected to two electrodes, then return to the emitter, forming an electrical circuit. The residual heat is discharged through the receiving stage. The principle of thermionic energy converter is shown in Figure 1.
In order to use the temperature of the anode discharge of the thermion thermoelectric conversion, the thermion thermoelectric conversion, and the thermoelectric generator are coupled. Without significantly affecting the performance of thermion thermoelectric conversion, the thermoelectric generator is driven by a large temperature difference between the anode temperature and the room temperature to generate additional power (Meng et al., 2014). Model of thermionic-thermoelectric generator is shown in Figure 2.
Thermionic generator consists of two components: emitter and collector, which are separated by a small space (Zhang et al., 2014). After the emitter of the thermionic generator is heated by the heat source, part of the electrons in the interior of the thermionic generator will have kinetic energy greater than the work function. The electrons escape from the surface of the emitter to form thermionic ions and they are accelerated by the collector. Then run to the collector and create the formation of current. When the current flows through the load, part of the emitter′s heat energy is consumed by the load. The current density from the emitter and collector can be approximated by the Richardson equation:
The heat flow rate away from the emitter due to the transmission of electrons is Q1, the heat flow rate received of the receiver due to the transmission of electrons is Q2. The radiant current from emitter to receiver is QR.
The total heat flow away from the emitter is QC, the total heat flow received of the receiver is QA.
Finally, the power density of the thermionic convertor can be calculated:
The heat absorbed from hot junction is QH, the heat released by cold junction is QL.
In the equation: α, I, R, K is the Bessel coefficient, current, resistance, heat transfer coefficient of the semi-conductor.
In the equation, the lower mark means whether it is n side or the p side of the semi-conductor. And then get the thermoelectric conductor power formula:
The final efficiency formula is:
For the whole thermoelectric conversion device, the optimization coefficient Z is an important parameter of the thermoelectric conversion device, and the value of the optimization coefficient Z needs to be determined first. Therefore, it is necessary to find the relationship between efficiency and optimization coefficient Z, as shown in Figure 3.
It can be seen from the figure that with the increase of the Z, the efficiency of the thermoelectric is higher, so it is better to choose a higher Z. The part makes a choice between the price and the mass, and finally find a semi-conductor that is relative high optimized coefficient. And the final Z is 0.00336. The parameters of the semi-conductor are listed in Table 1.
After determining the optimized coefficient Z and the parameters of the semi-conductor, we need to find the relationships between efficiency, power and high temperature zone Tc. The output voltage is U. The relationships between efficiency, power and high temperature zone Tc are shown in Figures 4, 5.
From the figures, it can be seen that with the increase of the high temperature zone, the peak power and the efficiency are all higher. Here choose Tc = 1,500 K. The relationships between efficiency, power and rare vapor pressure are shown in Figures 6, 7.
It can be seen that if the rare vapor pressure is smaller, the efficiency and the power will be higher. The pressure is related with the material properties. Cs is chosen of which the pressure is 1.4 eV.
The items of the thermoelectric convertor have been gotten. It is needed to determine the relationships between efficiency, power, and low temperature zone. As are shown in Figures 8, 9.
As can be seen from Figures 8, 9, when the output voltage is constant, the higher the temperature in the low temperature zone, the higher the corresponding efficiency and power. There is little difference in peak efficiency when the temperature is different. As the output voltage increases, both the output power and efficiency first increase and then decrease. Under actual conditions, the temperature in the low temperature zone is generally not higher than 800 K. When the output voltage is constant, the peak power at 800 K in the low temperature zone is about 15–20% higher than that at other temperatures. The temperature in the low temperature zone is 800 K. The parameters of the whole model are listed in Table 2.
In the paper, the performance analysis and optimization of thermionic-thermoelectric generators are mainly studied. Combined with actual working conditions, appropriate constraint parameters are selected, and the following conclusions are drawn. The efficiency of the thermionic-thermoelectric generator is 12% higher than that of the thermoelectric generator alone. According to past experience, the temperature of the transmitting stage is not higher than 1,800 K, and the temperature of the receiving stage is not higher than 800 K. In this range increasing the temperature of emitter and receiver can improve the output power and efficiency of the system. In fact, when the quality factor Z is about 0.00336, the economy and efficiency of the whole system is the best. Comparing several common rare vapor pressure, the lower the rare vapor pressure, the greater the efficiency of the system.
All datasets generated for this study are included in the article/supplementary material.
HZ conceived and designed the research. DY analyzed the data. XC, BK, and XL made the assistance.
This work was supported by the Key Laboratory of Reactor System Design Technology (Grant Nos. SQKFKT-02-2016005 and HT-KFKT-10-2018004).
The authors declare that the research was conducted in the absence of any commercial or financial relationships that could be construed as a potential conflict of interest.
Albertoni, R., Pedrini, D., Paganucci, F., and Andrenucci, M. (2013). A reduced-order model for thermionic hollow cathodes. IEEE Trans. Plasma. Sci. 41, 1731–1745. doi: 10.1109/TPS.2013.2266512
Bellucci, A., Girolami, M., and Calvani, P. (2016). Buried boron doped layer for CVD diamond photo-thermionic cathodes. IEEE Trans. Nanotechnol. 15, 862–866. doi: 10.1109/TNANO.2016.2566674
Chen, L., Ding, Z., Zhou, J., Wang, W., and Sun, F. (2017). Thermodynamic performance optimization for an irreversible vacuum thermionic generator. Eur. Phys. J. Plus. 132:293. doi: 10.1140/epjp/i2017-11561-2
El-Genk, M. S., Xue, H., and Paramonov, D. (1993). Start-up simulation of a thermionic space nuclear reactor system. AIP Conf. Proc. 271:935. doi: 10.1063/1.43119
Hainley, D. C. (1991). User's Manual for the Heat Pipe Space Radiator Design and Analysis Code (HEPSPARC). Report No. NASA-CR-187067. Brook Park, OH: Sverdrup Technology, Inc.
Hassink, G., Wanke, R., Rastegar, I., Braun, W., Stephanos, C., Herlinger, P., et al. (2015). Transparency of graphene for low-energy electrons measured in a vacuum-triode setup. APL Mater. 3:076106. doi: 10.1063/1.4927406
Hatsopoulos, G. N., and Gyftopoulos, E. P. (1973). Thermionic energy conversion. Process. Devices 1:4362–4366.
Jensen, K. L., Lau, Y. Y., and Jordan, N. (2006). Emission nonuniformity due to profilimetry variation in thermionic cathodes. Appl. Phys. Lett. 88:164105. doi: 10.1063/1.2197605
Koeck, F. A., and Nemanich, R. J. (2006). Emission characterization from nitrogen-doped diamond with respect to energy conversion. Diam. Relat. Mater. 15, 217–220. doi: 10.1016/j.diamond.2005.08.045
Liao, T., Chen, X., Lin, B., and Chen, J. (2016). Performance evaluation and parametric optimum design of a vacuum thermionic solar cell. Appl. Phys. Lett. 108:39. doi: 10.1063/1.4940195
Meng, J. H., Zhang, X. X., and Wang, X. D. (2014). Multi-objective and multi-parameter optimization of a thermoelectric generator module. Energy 71, 367–376. doi: 10.1016/j.energy.2014.04.082
Paramonov, D. V., and El-Genk, M. S. (1997). A review of cesium thermionic converters with developed emitter surfaces. Energy Convers. Manag. 38, 533–549. doi: 10.1016/S0196-8904(96)00067-2
Tang, S., Sun, H., Wang, C., Tian, W., Qiu, S., Su, G. H., et al. (2019). Transient thermal-hydraulic analysis of thermionic space reactor TOPAZ-II with modified RELAP5. Prog. Nucl. Energy. 112, 209–224. doi: 10.1016/j.pnucene.2018.12.016
Tower, L. K., Baker, K. W., and Marks, T. S. (1992). Nasa Lewis Steady-State Heat Pipe Code Users Manual. Cleveland, OH: National Aeronautics and Space Administration. doi: 10.2172/10181275
Wanke, R., Hassink, G. W. J., Stephanos, C., Rastegar, I., Braun, W., and Mannhart, J. (2016). Magnetic-field-free thermoelectronic power conversion based on graphene and related two-dimensional materials. J. Appl. Phys. 119:244507. doi: 10.1063/1.4955073
Yarygin, V. I. (2012). Experimental studies of properties of excited states of cesium in the interelectrode plasma of a low-temperature thermal to electric energy thermionic converter. J. Clust. Sci. 23, 77–93. doi: 10.1007/s10876-012-0443-5
Zhang, J., Xuan, Y., and Yang, L. (2014). Performance estimation of photovoltaic-thermoelectric hybrid systems. Energy 78, 895–903. doi: 10.1016/j.energy.2014.10.087
Zhang, W., Wang, C., Chen, R., Tian, W., Qiu, S., and Su, G. H. (2016a). Preliminary design and thermal analysis of a liquid metal heat pipe radiator for TOPAZ-II power system. Ann. Nucl. Energy 97, 208–220. doi: 10.1016/j.anucene.2016.07.007
Keywords: space nuclear power source, thermionic-thermoelectric, generator system performance, quality factor, optimization
Citation: Zhang H, Yin D, Chai X, Kong B and Liu X (2020) Thermoelectric Conversion Performance of Combined Thermoions System for Space Nuclear Power Supply. Front. Energy Res. 7:167. doi: 10.3389/fenrg.2019.00167
Received: 31 October 2019; Accepted: 24 December 2019;
Published: 17 January 2020.
Edited by:
Ki-Yong Choi, Korea Atomic Energy Research Institute (KAERI), South KoreaReviewed by:
Luteng Zhang, Chongqing University, ChinaCopyright © 2020 Zhang, Yin, Chai, Kong and Liu. This is an open-access article distributed under the terms of the Creative Commons Attribution License (CC BY). The use, distribution or reproduction in other forums is permitted, provided the original author(s) and the copyright owner(s) are credited and that the original publication in this journal is cited, in accordance with accepted academic practice. No use, distribution or reproduction is permitted which does not comply with these terms.
*Correspondence: Haochun Zhang, emhjNUB2aXAuMTYzLmNvbQ==
Disclaimer: All claims expressed in this article are solely those of the authors and do not necessarily represent those of their affiliated organizations, or those of the publisher, the editors and the reviewers. Any product that may be evaluated in this article or claim that may be made by its manufacturer is not guaranteed or endorsed by the publisher.
Research integrity at Frontiers
Learn more about the work of our research integrity team to safeguard the quality of each article we publish.