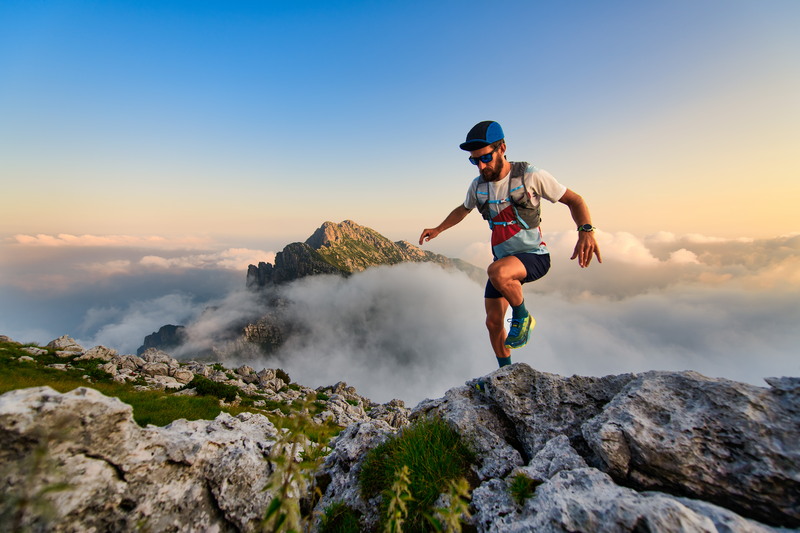
95% of researchers rate our articles as excellent or good
Learn more about the work of our research integrity team to safeguard the quality of each article we publish.
Find out more
ORIGINAL RESEARCH article
Front. Energy Res. , 04 June 2019
Sec. Electrochemical Energy Storage
Volume 7 - 2019 | https://doi.org/10.3389/fenrg.2019.00053
This article is part of the Research Topic Surface Chemistry and Materials Design in Lithium-Sulfur Batteries View all 4 articles
Pre-lithiated sulfur materials are promising cathode for lithium-sulfur batteries. The synthesis of lithium sulfide-carbon (Li2S-C) composite by carbothermic reduction of lithium sulfate (Li2SO4) is investigated in this study. The relationship between reaction temperature and the consumption of carbon in the carbothermic reduction of Li2SO4 is first investigated to precisely control the carbon content in the resultant Li2S-C composites. To understand the relationship between the material structure and the electrochemical properties, Li2S-C composites with the same carbon content are subsequently synthesized by controlling the mass ratio of Li2SO4/carbon and the reaction temperature. Systematic electrochemical analyses and microscopic characterizations demonstrate that the size of the Li2S particles dispersed in the carbon matrix is the key parameter determining the electrochemical performance. A reversible capacity of 600 mAh g−1 is achieved under lean electrolyte condition with high Li2S areal loading.
Lithium-sulfur (Li-S) batteries have received intensive investigations over the past decade due to its great potential as a high-capacity rechargeable battery technology (Ma et al., 2015; Manthiram et al., 2015; Wild et al., 2015; Fang et al., 2017; Peng et al., 2017; Zheng et al., 2017; Chen et al., 2018). To eliminate the potential safety hazard induced by the Li metal anode, high-capacity non-Li anodes, particularly silicon-based materials, have been sought as the alternative (Yang et al., 2010; Agostini et al., 2014; Cao et al., 2015; Jha et al., 2015; Guo et al., 2017). Utilizing non-Li anodes requires lithium sulfide (Li2S) cathode materials, which have been produced by a number of methods reported in literature. The most common method is to physically mix Li2S and carbon materials with high-energy ball milling (Cai et al., 2012; Jeong et al., 2013; Chen et al., 2014; Liu et al., 2015a; Lee et al., 2016; Liang et al., 2016). Li2S solution in ethanol was used to deposit Li2S on various carbon structures (Wu et al., 2014a,b,c, 2015, 2016; Wang et al., 2015; Han et al., 2016; Zhou et al., 2016). Other solvent such as anhydrous methyl acetate was also used to disperse Li2S in carbon (Seh et al., 2014). A number of chemical methods were also reported: Li2S-C composite could be produced from sulfurization of lithium carbonate with H2S (Dressel et al., 2016; Hart et al., 2018). Li2S-C composite was also synthesized via the reaction between lithium polysulfides and the nitrile group in polyacrylonitrile (Guo et al., 2013). A recently reported novel method utilized the thermal reaction between metallic Li and gaseous carbon disulfide (CS2) to form carbon coated Li2S in one step (Tan et al., 2017). Another chemical method to produce Li2S-C composites is to convert lithium sulfate (Li2SO4) to Li2S via carbothermic reduction (Yang et al., 2013; Kohl et al., 2015; Li et al., 2015; Liu et al., 2015b; Wang et al., 2016; Yu et al., 2017; Zhang et al., 2017; Ye et al., 2018). Comparing to all other methods mentioned above, carbothermic reduction of Li2SO4 involves neither hazardous gas such as gaseous CS2 or H2S, nor air sensitive reactants such as Li2S or Li metal. Furthermore, Li2S-C composites can be produced in one-step reaction in carbothermic reduction of Li2SO4. In this study, we focus on understanding the effect of reaction temperature on stoichiometric ratio of C/Li2SO4 in the carbothermic reduction and the structure-property relationship of the obtained Li2S-C composites as the cathode materials for Li-S batteries.
All reagents were used after purchase without further purification unless otherwise noted. Ketjen black EC-600JD (KJB, purchased from AkzoNobel) was used as the carbon source in this study. To minimize the effect of the impurity in KJB (mainly oxygen) on the carbothermic reduction of Li2SO4, KJB was treated by hydrogen reduction: In a typical experiment, approximately 400 mg KJB was heated under hydrogen/argon (5%/95%) environment at 1,000°C for 3 h. Elemental contents of KJB before and after the hydrogen treatment was analyzed as shown in Table 1.
Li2SO4 and KJB was thoroughly mixed by mechanical ball milling with different weight ratios including 2.0:1, 2.3:1, 2.5:1 and 2.9:1. The mixture was heated in a tube furnace under flowing argon (Ar) environment to form Li2S-C composite. The temperature of the tube furnace was first raised to 200°C from room temperature at 5°C min−1. The temperature was held at 200°C for 2 h, followed by further increasing to neither 700 or 750°C at 5°C min−1. The temperature was kept at 700 or 750°C for 6 h to complete the carbothermic reduction of Li2SO4. Ethanol was used to leach out the Li2S in the resultant Li2S-C composite to measure the conversion of Li2SO4 and carbon content, from which the C/Li2SO4 stoichiometric ratio in the carbothermic reduction can be calculated.
To improve the areal loading the Li2S-C composite at the cathode, micron-sized carbon particles were first synthesized with KJB as the precursor following the method reported by Lv et al. (2015). In a typical synthesis of Li2S-C composite, the micron-sized carbon particles were mixed into 5 mL aqueous solution of Li2SO4 with a specific Li2SO4/C ratio, followed by dispersion by sonication for 5 min and thorough stir for additional 24 h. One hundred milliliter ethanol was then added into the mixture and stirred for 10 min. The Li2SO4-C dispersion in the water/ethanol mixture was dried with rotary evaporator at 90°C. The obtained Li2SO4-C mixture was further dried at 80°C under vacuum overnight. To produce the Li2S-C composite, 0.5 g of Li2SO4-C mixture was heated under flowing Ar environment in a tube furnace using the same process as aforementioned.
The Li2S-C composite was characterized by powder X-Ray diffraction (XRD, PANalytical). Kapton tape was used to seal the XRD sample to prevent Li2S from reacting with moisture in the ambient environment. Nitrogen adsorption-desorption isotherms of the Li2S-C composites were measured with a surface area and porosity analyzer (Micromeritics ASAP2020). The surface area was obtained with the Brunauer-Emmett-Teller (BET) method. To avoid Li2S reacting with environmental moisture, all Li2S-C composites were transferred into the BET sample tube in the glovebox and sealed with Teflon tape. The microstructure of the Li2S-C composites was characterized with scanning electron microscopy (SEM) and elemental mapping was obtained by energy-dispersive X-ray spectroscopy (EDX). To perform the SEM characterization, the samples were carefully sealed into a stainless-steel vacuum tube in an Ar-filled glovebox. The sample tube was transferred into the SEM chamber under flowing argon protection using a glove-bag.
To prepare the electrode, Li2S-C composite was mixed with carbon black and polyvinylidene difluoride with a weight ratio of 85:5:10 in N-methyl-2-pyrrolidone. The obtained slurry was uniformly pasted on a carbon coated aluminum foil current collector and dried in the Ar-filled glovebox at 135°C for at least 15 h. The dried electrodes were assembled into 2032-type coin cells with Li foil anode (99.9%, Alfa Aesar) and Celgard® 2500 separator. The electrolyte used in this study was 1 M lithium bis(trifluoromethanesulfonyl)imide solution in a mixture of 1,3-dioxolane, dimethoxyethane and 1-butyl-1-methylpyrrolidinium bis(trifluoromethanesulfonyl)imide (1:1:2 by vol.) with 1.5 wt.% of LiNO3. The electrolyte to Li2S ratio (μL/mg) was kept at 7 in all coin cells testing. The average areal loading of Li2S on the electrode is 2 mg cm−2. The first charge (activation) was performed at a rate of C/50 (24 mA g−1) to a charge cutoff of 3.8 V vs. Li+/Li. The subsequent cycles were performed at C/10, C/5, C/2, and 1C between 2.8 and 1.7 V.
Despite the previous reports on synthesizing Li2S-C composites via carbothermic reduction of Li2SO4, the influence of reaction temperature on the stoichiometric ratio between carbon and Li2SO4 has not been investigated. As shown in Reaction 1, carbothermic reduction of Li2SO4 generally produces both carbon dioxide (CO2) and carbon monoxide (CO) (Li et al., 2015; Zhang et al., 2017). However, the ratio between CO2 and CO changes with temperature due to their different stability as the function of temperature (Zhang et al., 2017). Therefore, the carbothermic reduction of Li2SO4 can be expressed as Reaction 2, in which the stoichiometric ratio of C/Li2SO4, x, is a function of temperature. To synthesize Li2S-C composite in one-step carbothermic reduction with precise carbon content, it is critical to learn the value of x at different temperature.
With certain Li2SO4/C mass ratio (carbon in excess) and assumption of 100% conversion of Li2SO4 to Li2S, the Li2S content in the Li2S-C composite from the carbothermic reduction can be calculated as the function of the stoichiometric ratio of C/Li2SO4 as shown in Figure 1. The four solid lines represent four different Li2SO4/C mass ratio, 2.0:1, 2.3:1, 2.5:1, and 2.9:1, which all have excess of carbon. Carbothermic experiments were first performed with Li2SO4/C mass ratio of 2.0:1, 2.3:1 and 2.5:1 at 700 and 750°C. The reaction at each condition (temperature and Li2SO4/C mass ratio) was repeated at least three times to minimize experimental errors. The content of Li2S in the resultant Li2S-C composite was measured and the results demonstrated full conversion of Li2SO4 to Li2S in all experiments. Therefore, the stoichiometric ratio of C/Li2SO4, x, was calculated at all experimental conditions and the average values were marked on the theoretic curves in Figure 1. It is clear that the stoichiometric ratio of C/Li2SO4 is lower at 700°C, indicating less carbon is consumed at lower temperature with higher CO2 content in the gaseous products. The experimental results can also be linearly fitted to obtain an empirical relationship between Li2S content in Li2S-C and the stoichiometric C/Li2SO4 ratio at different temperature. The empirical relationship at 700°C is Li2S wt.% = 175.3 – 54.9x (red dotted line) and the one at 750°C is Li2S wt.% = 212.0 – 58.6x (blue dotted line).
Figure 1. Mass ratio of Li2S in the Li2S-C composite as the function of stoichiometry ratio of C/Li2SO4 with different Li2SO4/C mass ratio at 2.0:1, 2.3:1, 2.5:1, and 2.9:1 at 700 and 750°C.
To study the structure-property relationship of the Li2S-C composites, we need to select a composite from each reaction temperature with same Li2S content. One selected Li2S-C composite is produced at 750°C with Li2SO4/C mass ratio of 2.5:1, which contains 72 wt.% of Li2S. The same Li2S content was projected on the empirical linear fitting of Li2S content vs. stoichiometric C/Li2SO4 ratio at 700°C, from which the required Li2SO4/C mass ratio was calculated to be 2.9:1. The carbothermic reduction of Li2SO4 at 700°C with Li2SO4/C mass ratio of 2.9:1 yielded Li2S-C with 71 wt.% Li2S content, which agreed very well with the prediction.
The two Li2S-C composites with the same Li2S content are denoted as Li2S-C700 and Li2S-C750 according to the reaction temperature. The XRD patterns of these two composites in Figure 2A indicate well-crystallized Li2S formed from the carbothermic reduction of Li2SO4. The broad peak around 20° is due to the Kapton tape protecting Li2S from reacting to the ambient moisture. Based on the full-width at half-maximum of the XRD peaks, Li2S-C750 has smaller crystal grain size than that of Li2S-C700. The BET surface areas of these two Li2S-C composites from the N2 adsorption-desorption isotherms (Figure 2B) are very close: 350.8 m2 g−1 for Li2S-C750 and 326.8 m2 g−1 for Li2S-C700. We believe the higher carbon content in the Li2SO4-C mixture at the 750°C reaction alleviated the particle aggregation thus leading to smaller Li2S particles.
Figure 2. (A) XRD patterns and (B) N2 adsorption-desorption isotherms of the Li2S-C composites synthesized at different temperature.
SEM was used to characterize the microstructure of the Li2S-C composites. Figure 3a shows the structure of the Li2SO4/C mixture before carbothermic reduction for Li2S-C750. Li2SO4 exhibited typical monoclinic crystal structure as hexagonal plate with crystal size around 10 μm. Interestingly, the carbothermic reduction of Li2SO4 yielded spherical Li2S particles dispersed in carbon matrix as displayed in the SEM image in Figure 3b and the EDX elemental mapping in Figures 3c,d. The SEM characterization of the Li2S-C700 demonstrated very similar microstructure with Li2S-C750 as displayed in Figures 3f–i. The particle size of Li2S was measured by ImageJ software and the average particle size was analyzed by Gaussian distribution over 700 particles. As the particle size distribution shown in Figures 3e,j, the Li2S particle size in Li2S-C750 was smaller than that in Li2S-C700: The average Li2S particle size was 4.4 μm in Li2S-C750 and 6.4 μm in Li2S-C700.
Figure 3. (a) SEM image of Li2SO4-C mixture with Li2SO4/C mass ratio of 2.5:1, (b) SEM image, (c,d) EDX elemental mapping, and (e) Li2S size distribution of Li2S-C750; (f) SEM image of Li2SO4-C mixture with Li2SO4/C mass ratio of 2.9:1, (g) SEM image, (h,i) EDX elemental mapping and (j) Li2S size distribution of Li2S-C700.
Figures 4A,B show the CV cycles of Li2S-C750 and Li2S-C700 electrodes. The Li2S-C750 electrode demonstrated slightly lower delithiation potential than Li2S-C700 in the first cycle (3.5 vs. 3.6 V for the cathodic peak, respectively). This observation is consistent with the first galvanostatic delithiation (charge) curves of these two composites shown in Figures 4C,D. Li2S-C750 clearly demonstrated a lower activation potential at approximately 3.2 V vs. Li+/Li in the first two third of the charge process. On the contrary, Li2S-C700 showed much higher activation potential at 3.5 V vs. Li+/Li, which led to a lower first charge capacity. We speculate that the lower delithiation overpotential of Li2S-C750 is attributed to its structural advantage, mainly smaller Li2S particle size. Previous studies also reported that larger Li2S particle size could result to higher activation potential in the first charge process (Yang et al., 2012; Kohl et al., 2015; Liu et al., 2015a; Wang et al., 2016; Ye et al., 2018). In addition to the effect from particle size, activation potential of Li2S can also be affected by surface impurities such as Li2SO4, Li2CO3, and Li2O (Jung and Kang, 2016; Vizintin et al., 2017). The better microstructure of Li2S-C750 is also evidenced by the lower charge-discharge potential hysteresis (Figures 4C,D), better cycle stability and rate capability shown in Figures 4E,F. The average initial discharge capacity of Li2S-C750 is 600 mAh g−1 (average of 3 electrodes), and 400 mAh g−1 capacity was retained after 200 cycles at C/5. The specific capacity of Li2S-C750 at C/2 only slightly decreased from C/10 and C/5, indicating good rate capability. On the other hand, Li2S-C700 suffered from not only lower specific capacity at C/10, but also inferior rate capability as indicated by the low capacity at C/5, C/2, and 1C. It is clear that particle size of Li2S is the critical parameter for rate performance of the Li2S-C composites. It is also worth noting that the initial specific capacity of Li2S-C700 started with slight increase during cycling at C/10, which can be attributed to its inferior activation process due to larger Li2S particle size.
Figure 4. CV curves of (A) Li2S-C750 and (B) Li2S-C700; the 1st, 2nd, 10th, and 50th cycles of charge-discharge of (C) Li2S-C750 and (D) Li2S-C700 at C/5; the cycle stability at C/10, C/5, C/2, and 1C of (E) Li2S-C750 and (F) Li2S-C700.
In summary, the synthetic route of Li2S-C from carbothermic reduction of Li2SO4 was investigated in this study. Particularly the relationship between reaction temperature and stoichiometric ratio of C/Li2SO4 in the carbothermic reduction was obtained for the first time. Through investigations on microstructures and electrochemical properties, we speculated that smaller Li2S particle size dispersed in carbon matrix is the key parameter to improve the electrochemical performance. Methods to further reduce particle size of Li2S via carbothermic reduction of Li2SO4 will be investigated in future studies.
All datasets generated for this study are included in the manuscript and/or the supplementary files.
JS performed the majority of the experiments. JZ performed SEM and EDX. YZ and ZY synthesized the micron-sized carbon particles used in Li2S-C synthesis. NH and JG designed the experiments. All authors co-wrote the manuscript.
The authors declare that the research was conducted in the absence of any commercial or financial relationships that could be construed as a potential conflict of interest.
We acknowledge the National Science Foundation for financial support under grant no. CBET-1604908.
Agostini, M., Hassoun, J., Liu, J., Jeong, M., Nara, H., Momma, T., et al. (2014). A lithium-ion sulfur battery based on a carbon-coated lithium-sulfide cathode and an electrodeposited silicon-based anode. ACS Appl. Mater. Interfaces 6, 10924–10928. doi: 10.1021/am4057166
Cai, K., Song, M., Cairns, E., and Zhang, Y. (2012). Nanostructured Li2S-C composites as cathode material for high-energy lithium/sulfur batteries. Nano Lett. 12, 6474–6479. doi: 10.1021/nl303965a
Cao, R., Xu, W., Lv, D., Xiao, J., and Zhang, J. (2015). Anodes for rechargeable lithium-sulfur batteries. Adv. Energy Mater. 5:1402273. doi: 10.1002/aenm.201402273
Chen, L., Guo, X., Lu, W., Chen, M., Li, Q., Xue, H., et al. (2018). Manganese monoxide-based materials for advanced batteries. Coordination Chem. Rev. 368, 13–34. doi: 10.1016/j.ccr.2018.04.015
Chen, L., Liu, Y., Ashuri, M., Liu, C., and Shaw, L. L. (2014). Li2S encapsulated by nitrogen-doped carbon for lithium sulfur batteries. J. Mater. Chem. A 2:18026. doi: 10.1039/C4TA04103H
Dressel, B. C., Jha, H., Eberle, A., Gasteiger, A. H., and Fassler, F. T. (2016). Electrochemical performance of lithium-sulfur batteries based on a sulfur cathode obtained by H2S gas treatment of a lithium salt. J. Power Sources 307, 844–848. doi: 10.1016/j.jpowsour.2015.12.140
Fang, R., Zhao, S., Sun, Z., Wang, D. W., Cheng, H. M., et al. (2017). More reliable lithium-sulfur batteries: status, solutions and prospects. Adv. Mater. 29:1606823. doi: 10.1002/adma.201606823
Guo, J., Yang, Z., Yu, Y., Abruña, H. D., and Archer, L. A. (2013). Lithium-sulfur battery cathode enabled by lithium-nitrile interaction. J. Am. Chem. Soc. 135, 763–767. doi: 10.1021/ja309435f
Guo, X., Zheng, S., Zhang, G., Xiao, X., Li, X., Xu, Y., et al. (2017). Nanostructured graphene-based materials for flexible energy storage. Energy Storage Mater. 9, 150–169. doi: 10.1016/j.ensm.2017.07.006
Han, F., Yue, J., Fan, X., Gao, T., Luo, C., Ma, Z., et al. (2016). High-performance all-solid-state lithium-sulfur battery enabled by a mixed-conductive Li2S nanocomposite. Nano Lett. 16, 4521–4527. doi: 10.1021/acs.nanolett.6b01754
Hart, N., Shi, J., Zhang, J., Fu, C., and Guo, J. (2018). Lithium sulfide-carbon composites via aerosol spray pyrolysis as cathode materials for lithium-sulfur batteries. Front. Chem. 6:674. doi: 10.3389/fchem.2018.00476
Jeong, S., Bresser, D., Buchholz, D., Winter, M., and Passerini, S. (2013). Carbon coated lithium sulfide particles for lithium battery cathodes. J. Power Sources 235, 220–225. doi: 10.1016/j.jpowsour.2013.01.084
Jha, H., Buchberger, I., Cui, X., Meini, S., and Gasteiger, H. A. (2015). Li-S batteries with Li2S cathodes and Si/C anodes. J. Electrochem. Soc. 162, A1829–A1835. doi: 10.1149/2.0681509jes
Jung, Y., and Kang, B. (2016). Understanding abnormal potential behaviors at the 1st charge in Li2S cathode material for rechargeable Li-S batteries. Phys. Chem. Chem. Phys. 18:21500. doi: 10.1039/C6CP03146C
Kohl, M., Bruckner, J., Bauer, I., Althues, H., and Kaskel, S. (2015). Synthesis of highly electrochemically active Li2S nanoparticles for lithium–sulfur-batteries. J. Mater. Chem. A 3, 16307–16312. doi: 10.1039/C5TA04504E
Lee, S., Lee, Y. J., and Sun, Y. (2016). Nanostructured lithium sulfide materials for lithium-sulfur batteries. J. Power Sources 323, 174–188. doi: 10.1016/j.jpowsour.2016.05.037
Li, Z., Zhang, S., Zhang, C., Ueno, K., Yasuda, T., Tatara, R., et al. (2015). One-pot pyrolysis of lithium sulfate and graphene nanoplatelet aggregates: in situ formed Li2S/graphene composite for lithium-sulfur batteries. Nanoscale 7, 14385–14392. doi: 10.1039/C5NR03201F
Liang, S., Liang, C., Xia, Y., Xu, H., Huang, H., Tao, X., et al. (2016). Facile synthesis of porous Li2S@C composites as cathode materials for lithium-sulfur batteries. J. Power Sources 306, 200–207. doi: 10.1016/j.jpowsour.2015.12.030
Liu, J., Nara, H., Yokoshima, T., Momma, T., and Osaka, T. (2015a). Li2S cathode modified with polyvinylpyrrolidone and mechanical milling with carbon. J. Power Sources 273, 1136–1141. doi: 10.1016/j.jpowsour.2014.09.179
Liu, J., Nara, H., Yokoshima, T., Momma, T., and Osaka, T. (2015b). Micro-scale Li2S-C composite preparation from Li2SO4 for cathode of lithium ion battery. Electrochim. Acta 183, 70–77. doi: 10.1016/j.electacta.2015.07.116
Lv, D., Zheng, J., Li, Q., Xie, X., Ferrara, S., Nie, Z., et al. (2015). High energy density lithium–sulfur batteries: challenges of thick sulfur cathodes. Adv. Energy Mater. 5:1402290. doi: 10.1002/aenm.201402290
Ma, L., Hendrickson, K. E., Wei, S., and Archer, L. A. (2015). Nanomaterials: science and applications in the lithium-sulfur battery. Nano Today 10, 315–338. doi: 10.1016/j.nantod.2015.04.011
Manthiram, A., Chung, S. H., and Zu, C. (2015). Lithium-sulfur batteries: progress and prospects. Adv. Mater. 27, 1980–2006. doi: 10.1002/adma.201405115
Peng, H., Huang, J., Cheng, X., and Zhang, Q. (2017). Review on high-loading and high-energy lithium-sulfur batteries. Adv. Energy Mater. 7:1700260. doi: 10.1002/aenm.201700260
Seh, Z. W., Wang, H., Hsu, P., Zhang, Q., Li, W., Zheng, G., et al. (2014). Facile synthesis of Li2S-polypyrrole composite structures for high-performance Li2S cathodes. Energy Environ. Sci. 7, 672–676. doi: 10.1039/c3ee43395a
Tan, G., Xu, R., Xing, Z., Yuan, Y., Lu, J., Wen, J., et al. (2017). Burning lithium in CS2 for high-performing compact Li2S-graphene nanocapsules for Li-S batteries. Nat. Energy. 2:17090. doi: 10.1038/nenergy.2017.90
Vizintin, A., Chabanne, L., Tchernychova, E., Arcon, I., Stievano, L., Aquilanti, G., et al. (2017). The mechanism of Li2S activation in lithium-sulfur batteries: can we avoid the polysulfide formation? J. Power Sources 344, 208–217. doi: 10.1016/j.jpowsour.2017.01.112
Wang, C., Wang, X., Yang, Y., Kushima, A., Chen, J., Huang, Y., et al. (2015). Slurryless Li2S/reduced graphene oxide cathode paper for high-performance lithium sulfur battery. Nano Lett. 15, 1796–1802. doi: 10.1021/acs.nanolett.5b00112
Wang, D., Xie, D., Yang, T., Zhang, Y., Wang, X., Xia, X., et al. (2016). Conversion from Li2SO4 to Li2S@C on carbon paper matrix: a novel integrated cathode for lithium-sulfur batteries. J. Power Sources 331, 475–480. doi: 10.1016/j.jpowsour.2016.09.033
Wild, M., O'Neill, L., Zhang, T., Purkayastha, R., Minton, G., Marinescu, M., et al. (2015). Lithium sulfur batteries, a mechanistic review. Energy Environ. Sci. 8:3477. doi: 10.1039/C5EE01388G
Wu, F., Kim, H., Magasinski, A., Lee, J., Lin, H., and Yushin, G. (2014a). Harnessing steric separation of freshly nucleated Li2S nanoparticles for bottom-up assembly of high-performance cathodes for lithium-sulfur and lithium-ion batteries. Adv. Energy Mater. 4:1400196. doi: 10.1002/aenm.201400196
Wu, F., Lee, J., Magasinski, A., Kim, H., and Yushin, G. (2014b). Solution-based processing of graphene-Li2S composite cathodes for lithium-ion and lithium-sulfur batteries. Part. Part. Syst. Charact. 31, 639–644. doi: 10.1002/ppsc.201300358
Wu, F., Lee, J. T., Fan, F., Nitta, N., Kim, H., Zhu, J., et al. (2015). A hierarchical particle-shell architecture for long-term cycle stability of Li2S cathodes. Adv. Mater. 27, 5579–5586. doi: 10.1002/adma.201502289
Wu, F., Lee, J. T., Zhao, E., Zhang, B., and Yushin, G. (2016). Graphene-Li2S-carbon nanocomposite for lithium-sulfur batteries. ACS Nano 10, 1333–1340. doi: 10.1021/acsnano.5b06716
Wu, F., Magasinski, A., and Yushin, G. (2014c). Nanoporous Li2S and MWCNT-linked Li2S powder cathodes for lithium-sulfur and lithium-ion battery chemistries. J. Mater. Chem. A 2, 6064–6070. doi: 10.1039/C3TA14161F
Yang, Y., McDowell, M. T., Jackson, A., Cha, J. J., Hong, S. S., and Cui, Y. (2010). New nanostructured Li2S/silicon rechargeable battery with high specific energy. Nano Lett. 10, 1486–1491. doi: 10.1021/nl100504q
Yang, Y., Zheng, G., Misra, S., Nelson, J., Toney, M. F., and Cui, Y. (2012). High-capacity micrometer-sized Li2S particles as cathode materials for advanced rechargeable lithium-ion batteries. J. Am. Chem. Soc. 134, 15387–15394. doi: 10.1021/ja3052206
Yang, Z., Guo, J., Das, K. S., Yu, Y., Zhou, Z., Abruna, D. H., et al. (2013). In situ synthesis of lithium sulfide-carbon composites as cathode materials for rechargeable lithium batteries. J. Mater. Chem. A 1, 1433–1440. doi: 10.1039/C2TA00779G
Ye, F., Noh, H., Lee, J., Lee, H., and Kim, H. (2018). Li2S/carbon nanocomposite strips from a low-temperature conversion of Li2SO4 as high-performance lithium-sulfur cathodes. J. Mater. Chem. A 6, 6617–6624. doi: 10.1039/C8TA00515J
Yu, M., Wang, Z., Wang, Y., Dong, Y., and Qiu, J. (2017). Freestanding flexible Li2S paper electrode with high mass and capacity loading for high-energy Li-S batteries. Adv. Energy Mater. 7:1700018. doi: 10.1002/aenm.201700018
Zhang, J., Shi, Y., Ding, Y., Peng, L., Zhang, W., and Yu, G. (2017). A conductive molecular framework derived Li2S/N, P-codoped carbon cathode for advanced lithium-sulfur batteries. Adv. Energy Mater. 7:1602876. doi: 10.1002/aenm.201602876
Zheng, S., Li, X., Yan, B., Hu, Q., Xu, Y., Xiao, X., et al. (2017). Transition-metal (Fe, Co, Ni) based metal-organic frameworks for electrochemical energy storage. Adv. Energy Mater. 7:1602733. doi: 10.1002/aenm.201602733
Keywords: lithium-sulfur batteries, lithium sulfide, lithium sulfate, carbothermic reaction, carbon composite
Citation: Shi J, Zhang J, Zhao Y, Yan Z, Hart N and Guo J (2019) Synthesis of Li2S-Carbon Cathode Materials via Carbothermic Reduction of Li2SO4. Front. Energy Res. 7:53. doi: 10.3389/fenrg.2019.00053
Received: 02 March 2019; Accepted: 16 May 2019;
Published: 04 June 2019.
Edited by:
Wen Liu, Beijing University of Chemical Technology, ChinaCopyright © 2019 Shi, Zhang, Zhao, Yan, Hart and Guo. This is an open-access article distributed under the terms of the Creative Commons Attribution License (CC BY). The use, distribution or reproduction in other forums is permitted, provided the original author(s) and the copyright owner(s) are credited and that the original publication in this journal is cited, in accordance with accepted academic practice. No use, distribution or reproduction is permitted which does not comply with these terms.
*Correspondence: Juchen Guo, amd1b0BlbmdyLnVjci5lZHU=
Disclaimer: All claims expressed in this article are solely those of the authors and do not necessarily represent those of their affiliated organizations, or those of the publisher, the editors and the reviewers. Any product that may be evaluated in this article or claim that may be made by its manufacturer is not guaranteed or endorsed by the publisher.
Research integrity at Frontiers
Learn more about the work of our research integrity team to safeguard the quality of each article we publish.