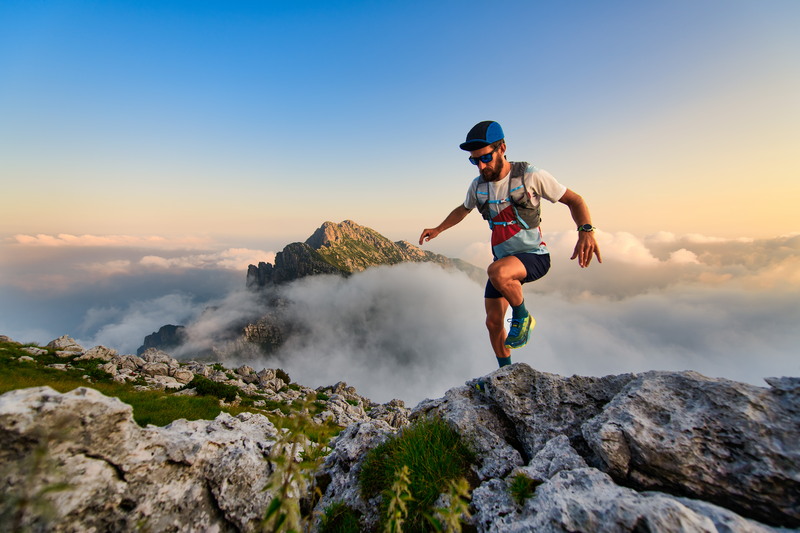
95% of researchers rate our articles as excellent or good
Learn more about the work of our research integrity team to safeguard the quality of each article we publish.
Find out more
ORIGINAL RESEARCH article
Front. Energy Res. , 26 November 2018
Sec. Nuclear Energy
Volume 6 - 2018 | https://doi.org/10.3389/fenrg.2018.00127
This article is part of the Research Topic Nuclear Safety Design and Innovation View all 14 articles
Supercritical-pressure light water-cooled reactors (SCWR) are the only water cooled reactor types in Generation IV nuclear energy systems. Startup systems, and their associated startup characteristic analyses, are important components of the SCWR design. To analyze the entire startup system, we propose a wall heat transfer model in a paper, based on the results from a supercritical transient analysis code named SCTRAN developed by Xi'an Jiao tong University. In this work, we propose a new heat transfer mode selection process. Additionally, the most appropriate heat transfer coefficient selection method is chosen from existing state-of-the-art methods. Within the model development section of the work, we solve the problem of discontinuous heat transfer coefficients in the logic transformation step. When the pressure is greater than 19 Mpa, a look-up table method is used to obtain the heat transfer coefficients with the best prediction accuracy across the critical region. Then, we describe a control strategy for the startup process that includes a description of the control objects for coolant flow rate, heat-exchange outlet temperature, system pressure, core thermal power, steam drum water-level and the once-through direct cycle loop inlet temperature. Different control schemes are set-up according to different control objectives of the startup phases. Based on CSR1000 reactor, an analytical model, which includes a circulation loop and once-through direct cycle loop is established, and four startup processes, with control systems, are proposed. The calculation results show that the thermal parameters of the circulation loop and the once-through direct cycle meets all expectations. The maximum cladding surface temperature remains below the limit temperature of 650°C. The feasibility of the startup scheme and the security of the startup process are verified.
Supercritical Water Reactor (SCWR) is the only water cooled reactor type in Generation IV nuclear energy systems. SCWR is an innovative system which is aimed for high thermal efficiency and economy. SCWR works at a high pressure, 25 MPa, with a core outlet temperature up to 500°C. Moreover, Canada's pressure vessel-type reactor outlet temperature even up to 625°C. So the cladding temperature can reach 650°C, far beyond the current pressurized water reactor. Supercritical water properties rapid changes at the trans-critical region, and neutron moderating ability would be weakened. The University of Tokyo was the first to study the startup procedure of SCWR. Since the startup procedure involves the process of cooling a reactor from a subcritical to supercritical state, analyzing SCWR-based startup thermo-hydraulic characteristics becomes an important consideration (Oka and Koshizuka, 2001). There exist two main startup strategies for SCWRs. One is constant pressure startup, and the other one is sliding pressure startup (Yi et al., 2004). During constant pressure startup procedure, the reactor starts at a supercritical pressure. This procedure is that there is no need to concern about critical heat flux or two-phase instability in two-phase flow. The disadvantage is that large pumping power is needed to make the system operate. During sliding pressure startup procedure, the reactor starts at a subcritical pressure. Using the traditional variable pressure startup system, it must be assured that the maximum cladding surface temperature is below the criterion and flow instability is avoided during startup at subcritical pressures. To avoid the above issues, Ishiwatari et al proposed e recirculation system, instead of a bypass system (Oka, 2013). The recirculation system was separated from the main line of once-through direct-cycle. Compared with the constant pressure startup procedure, the advantage of the sliding pressure startup system is that the pumping power consumption is decreased, which results in a higher efficiency during low load operations. Therefore, the recirculation system startup procedure is applied in this paper. The past investigation of startup was carried out by several researchers. Yi et al analyzed detailed thermal behavior for a high-temperature supercritical-pressure light water-cooled thermal reactor Super LWR (SCLWR-H) (Yi et al., 2004) and a Super FR with downward-upward two-pass coolant flow (Cai et al., 2009). A sliding pressure startup scheme of recirculation system for SCWRs was proposed to provide a pressurization system which was raised independently from the power (Yamada and Ishiwatari, 2009). With the modified ATHLET-SC code, which realizes the simulation of trans-critical transients using two-phase model the thermal-hydraulic dynamic behavior of the mixed SCWR core during the startup process is simulated (Fu et al., 2011). It can be concluded that the focus of previous work are mainly on the thermal hydraulics behavior of SCWR during startup to validate the limiting criteria, but there are few work on the control system design to achieve startup procedure.
The SCWR coolant loop is a once-through direct cycle that is very sensitive to disturbances. The startup procedure needs to be operated by the control system. Yuki et al. designed a control system of the SCLWR-H under steady state. The turbine inlet pressure is controlled by the turbine control valves. The main steam temperature is controlled by the feedwater flow rate. The core power is controlled by the control rods (Ishiwatari et al., 2003). Wang et al. sing FORTRAN program to make code, when perturbation happens such as pressure set-point changes, feed-water temperature drop, reactor parameters changes with time were researched at the control rod, steam turbine control valves and there actor coolant pumps as the plant control system (Wang et al., 2012). To analyze the control characteristics of SCWRs, Ishiwatari et al. (2003); (Ishwatari et al., 2010) optimized the SCR control parameters, modified the feed water control system of Super LWRs and improved the delay problem of the temperature control system. Sun and Jiang (2012) studied the control system of Canadian SCWRs and obtained the control system linearization equations via the solution of a complete nonlinear dynamic equations. Dong et al. (2016) proposed a Moving Boundary Method to control the steam temperature. To meet the startup requirements of the entire system, and based on the three typical PID control systems designed by Nakatsuka et al. (1997), control systems are proposed that have controls for coolant flow rate, heat exchanger outlet temperature, system pressure, core thermal power, steam drum water level and the once-through direct cycle loop inlet temperature. By adjusting the control parameters, the startup procedure of the SCWR can be operated according to the starting curve.
The SCWR startup procedure must ensure that the Maximum fuel cladding surface temperature (MCST) does not exceed the limit 650°C. Accordingly, the heat transfer coefficient value is very important for the calculation of the cladding temperature. A complete set of heat transfer coefficients is needed to meet the wall heat transfer requirements for a smooth transition between the subcritical and supercritical heat transfer coefficients. Ishiwatari et al. (2005) used the “oka-koshizuka correlation” (or “Kitoh correlation”) to calculate the heat transfer deterioration under supercritical region of SCWR. oka-koshizuka correlation was developed on the basis of the typical single-phase turbulence model, which is in good agreement with the experimental data of Yamagata (Yamagata et al., 1972; Koshizuka et al., 1995). However, the calculated values of heat transfer coefficient of oka-koshizuka correlation is larger than Watts correlation and Bishop correlation in the deteriorating area (Ishiwatari et al., 2005). SPRAT-DOWN code which is developed by Ishiwatrai adopts oka-koshizuka correlation in rated, transient and accident conditions. Thermophysical properties and transport properties of coolant change greatly during subcritical pressure to supercritical pressure under SCWR startup procedure. It needs a wall heat transfer model with wide-scope parameter which can satisfy the heat transfer coefficient smooth transition requirements from subcritical and supercritical region. By summarizing a large number of supercritical regional databases and literature, Zahlan et al. (2015) proposed a look-up table to calculate trans-critical heat transfer in water-cooled tubes. The SCTRAN code is chosen to analyze the SCWR startup control characteristics. This choice is made because SCTRAN (Wu et al., 2013) can smoothly calculate the physical properties of water in the cross-critical region. The wall heat transfer model of the existing SCTRAN code has a heat transfer coefficient that changes drastically near the critical point and the heat transfer coefficient jump in supercritical regions. The paper puts forward the new wall heat transfer model. The new wall heat transfer model proposes a new logic for the selection of the heat transfer modes and the most appropriate model from the literature is chosen to determine the heat transfer coefficient. Moreover, the discontinuous heat transfer coefficients in the logic transformation are removed. The purpose of this paper is to design a control system for the SCWR's circulation sliding pressure startup process based on an improved SCTRAN code. This work is the foundation of a complete and reliable startup analysis system.
SCTRAN was developed in Xi′an Jiao Tong University. It is a one-dimensional safety analysis code for SCWRs (Wu et al., 2013). SCTRAN code has been verified by relap5 and other codes. Typical accidents such as LOCA, LOFA and so on of CANDU-SCWR, CGNPC-SCWR and CSR1000 are calculated (Gou et al., 2012). A homogenous equilibrium mixture model with an optional phasic slip formulation was applied in code SCTRAN. The homogenous model made the following assumptions: (1) the velocities of gas and liquid were the same; (2) gas and liquid were in thermodynamic equilibrium. Here the basic equations of homogenous equilibrium mixture model are summarized.
Mass conservation equation
where:
Momentum conservation equation
Energy conservation equation
In numerical calculation, SCTRAN code adopts the staggered grid in fluid space discretization and adopts the control volume balance method to discrete fluid basic equations.
The SCTRAN module call diagram is shown in Figure 1. SCTRAN code mainly includes the following several modules: input module, output module, conservation equation module, pressure calculation module, thermal power calculation module, structure temperature calculation module, heat transfer coefficient and heat flux calculation module, subcritical region and supercritical region fluid physical parameters calculation module. The calculation flow chart of SCTRAN is shown in Figure 2. The iterative calculation mainly determines judges whether the change speed of internal energy ΔU/U is convergent and whether it reaches the end time of calculation.
The wall heat transfer model mainly includes three parts: heat transfer modes, selection procedures of heat transfer modes (logic) and heat transfer correlations. To analyze the wall heat transfer characteristics of the SCTRAN code, a simulation of a pipe was made. The pipe fluid inlet temperature is 100°C, the outlet temperature is 500°C, the fixed flow rate per unit area is 500 kg·m−2·s−1, and the pipe is uniformly heated along the axial direction; the pressure varies from 1 to 28 MPa. The curves of the heat transfer coefficient are associated with pressure and enthalpy; they are shown in Figures 3, 4. There are some problems with the SCTRAN calculations of the heat transfer coefficient. They include: (1) SCTRAN adopts Jackson heat transfer correlation for supercritical regions, which leads to a large error. (2) The wall heat transfer model is not comprehensive for all modes. (3) The heat transfer coefficient drastically changes near the critical point and the mode transition region. To solve these problems, the project introduces a new wall heat transfer model that can be calculated from the subcritical to supercritical region. The model selects the appropriate heat transfer correlation and a lookup table (Zahlan et al., 2015) to improve the accuracy of the calculation (Table 1). In the sub-critical region, since the heat transfer coefficient of the convection term of the Chen correlation is calculated by using the DB correlation for hmac, after the heat transfer mode is converted, the DB relational expression can be smoothly transferred to the Chen correlation. Then the values of qCHF and TCHF are the results of the iterative calculation of the table and Chen correlation, so the nucleate boiling correlation can be smoothly transitioned to transition boiling. While the rest of the relations are transformed by linear interpolation. In the supercritical region, only the look-up table for trans-critical region is used.
Figure 3. Relationship between the heat transfer coefficient, enthalpy and pressure from a low-pressure to high-pressure region.
Figure 4. Relationship between the heat transfer coefficient, enthalpy and pressure in a high-pressure region.
Per the SCWR startup sequence (Table 2), the startup procedure is divided into four phases: raising of feed water temperature, pressurization, switching from recirculation line to once-through line and power-raising. The control of the SCWR circulation startup system should be able to meet the control requirements needed for the pressure, thermal power, temperature, steam drum water level and coolant flow rate. Therefore, we designed six different control systems for the SCWR startup procedure (Table 3). The basic control methods and equations can be introduced by reference (Nakatsuka et al., 1997; Ishiwatari et al., 2003). Based on the HPLWR thermal cycle, SCWR circulation loop, CSR1000 design parameters and the control method proposed in this paper, a complete CSR1000 control system (Figure 5) is designed.
Bailey experiment and Subbotin experiment (Wu et al., 2016) were selected to validate the calculation accuracy of the wall heat transfer model with wide-scope parameter. The inner diameter and wall thickness of Bailey and Subbotin experiment are 12.7762 mm and 2.3368 mm, respectively. The heated length of the test section of Bailey and Subbotin experiment are 3.048 and 6.000 m, respectively. The experimental conditions are shown in Table 4. By comparing the wall temperature obtained by the codes with the experiment data, we can verify the modified model.
The CHF calculation correlation used in the new wall heat transfer model is the Groeneveld CHF look-up table developed in 2006 (Groeneveld et al., 2007). From the validation results of Bailey experiment (Figure 6) and Subbotin experiment (Figure 7), we can see that the modified model better predicted the wall temperature during film boiling under all cases, and it got the relatively good results of the locations where CHF occurred in most cases. In the prediction of the CHF occurrence location, the SCTRAN new calculation results were early, which was caused by the inherent error of the CHF look-up table. The low heat transfer coefficient value obtained from the look-up table leads to a higher wall temperature and makes the CHF occurrence location in advance.
Based on the various disturbances, this part demonstrates the steady ability of control system. The introduced linear perturbations include main steam temperature, system pressure, core power, coolant flow, and so on (Table 5).
When subjected to various disturbances, under the control of the control system, each control system can effectively controls the control target quickly and steadily (Figure 8). It shows that the control system designed in this thesis is fast and effective. Response of the main steam temperature control system.
Typical startup schemes use a sliding startup system that includes a circulation loop for startup and a once-through direct loop (Figure 5). The whole startup procedure needs to be completed in approximately 61.59 h. The variation of thermodynamic parameters is shown in Figure 9. During the startup procedure, with the thermal power control system and the flow control system controlling, the core power and the flow rate operates according to the requirements (Figures 9A,B). The doppler reactivity, void fraction reactivity and reactivity inserted by the control rod can be seen in Figure 9B. At the beginning of the fourth stage, the flow rate of the water rod in the second process is negative, and the coolant is counter-current. At about 41.2 h, the flow rate of the water rod in the second process becomes positive, and the coolant flows normally. At this time, the power and flow rate is about 59%.With the rise of the coolant flow, the buoyancy resistance is not enough to resist the pressure drop increase with the driving force, caused the second process water rod flow rate from the larger negative value changes into larger positive value. It makes the value of void fraction reactivity dramatic changes in this place. The water level can be controlled, up to a height of about 3 m (Figure 9C), via the steam drum water level control system. The steam drum water level control system is deactivated at 20 MPa (15.6 h). Under the control of the once-through direct-cycle loop-inlet control system, the core-inlet coolant temperature can be maintained at 280°C. The outlet coolant temperature gradually increases with time until the rated operating temperature is 500°C (Figure 9D). The MCST does not exceed the limit temperature of 650°C throughout the startup procedure (Figure 9E). The lower plenum will not generate steam during the entire startup procedure and the supercritical steam occurs only in the lower plenum after the supercritical pressure has been achieved. Thus, the coolant remains in a single-phase state and there is no boiling crisis or flow instability problem within the core (Figure 9F). Because the buoyancy is greater than the driving force, during the lowering of the water in the second process, the coolant reverses from the subcritical region to the supercritical region (Figures 9G,H). The mass flow rate greatly affects the surface temperature of the cladding and the value of the reactivity feedback. The abrupt flow generally causes avoid reactivity great changes (Figure 9A).
Figure 9. Transient performance of the startup procedure. (A) Transient performance of thermal power and feed water flow rate. (B) Transient performance of the core reactivity. (C) Transient performance of the steam drum water level and its average quality. (D) Transient performance of the coolant temperature and pressure. (E) Transient performance of the maximum cladding surface temperature for SCWR. (F) Transient performance of core average quality. (G) Transient performance of the first process flow rate. (H) Transient performance of the second process flow rate.
A new wall heat transfer model is developed for SCTRAN applications to analyze the SCWR startup characteristics. In the model, drastic changes to the heat transfer coefficient (calculated by the SCTRAN) near the critical region is resolved and the heat transfer coefficient from a subcritical to supercritical pressure is forecast precisely and smoothly.
Because the thermo-physical properties and transport properties of coolant change significantly from a subcritical to supercritical pressure, a control system is required to adjust the parameter changes during the startup procedure. Under the control strategy of the startup procedure, the system pressure, temperature, thermal power and flow rate can be regulated according to the startup objectives. The calculation results show that the thermal parameters of the circulation loop and the once-through direct cycle meet the requirement and the MCST remains below the limit temperature of 650°C.
YY wrote the manuscript. JS guided this research. LW, DW, and XZ critical revised the article.
The authors declare that the research was conducted in the absence of any commercial or financial relationships that could be construed as a potential conflict of interest.
Cai, J., Ishiwatari, Y., Ikejiri, S., and Oka, Y. (2009). Thermal and stability considerations for a supercritical water-cooled fast reactor with downward-flow channels during power-raising phase of plant startup. Nuclear Eng. Desig. 239, 665–679. doi: 10.1016/j.nucengdes.2008.12.010
Dong, H., Lu, J., Chen, P., and Sun, P. (2016). Fuzzy Adaptive PI Control of Steam Temperature in a Canadian SCWR. Nuclear Power Eng. 37, 66–70. doi: 10.13832/j.jnpe.2016.06.0066
Fu, S.-W., Xu, Z.-H., and Yang, Y.-H. (2011). Thermal hydraulic behavior of SCWR sliding pressure startup. Nuclear Power Eng. 32, 69–74. doi: 10.1111/j.1759-6831.2010.00113.x
Gou, J., Wu, P., Shan, J., Zhang, B., and Yang, J. (2012). “Development of a safety analysis code SCTRAN for SCWR,” in American Society of Mechanical Engineers (Anaheim, CA), 431–438. doi: 10.1115/ICONE20-POWER2012-54847
Groeneveld, D. C., Shan, J. Q., Vasić, A. Z., Leung, L. K. H., Durmayaz, A., Yang, J., et al. (2007). The 2006 CHF look-up table. Nuclear Eng. Design 237, 1909–1922. doi: 10.1016/j.nucengdes.2007.02.014
Ishiwatari, Y., Oka, Y., and Koshizuka, S. (2003). Control of a high temperature supercritical pressure light water cooled and moderated reactor with water rods. J. Nuclear Sci. Technol. 40, 298–306. doi: 10.1080/18811248.2003.9715359
Ishiwatari, Y., Oka, Y., Koshizuka, S., Yamaji, A., and Liu, J. (2005). Safety of Super, LWR,(II) safety analysis at supercritical pressure. J. Nuclear Sci. Technol. 42, 935–948. doi: 10.1080/18811248.2005.9711045
Ishwatari, Y., Peng, C., Ikejiri, S., and Oka, Y. (2010). Improvements of feedwater controller for the super fast reactor. J. Nuclear Sci. Technol. 47, 1155–1164. doi: 10.1080/18811248.2010.9720982
Koshizuka, S., Takano, N., and Oka, Y. (1995). Numerical analysis of deterioration phenomena in heat transfer to supercritical water. Trans. Jpn. Soc. Mech. Eng. 60, 3077–3084. doi: 10.1016/0017-9310(95)00008-W
Nakatsuka, T., Oka, Y., and Koshizuka, S. (1997). Control of a fast reactor cooled by supercritical light water. Nuclear Technol. 121, 81–91. doi: 10.13182/NT98-A2821
Oka, Y. (2013). Time dependent start-up thermal analysis of a super fast reactor. Nuclear Eng. Design 263, 129–137. doi: 10.1016/j.nucengdes.2013.04.014
Oka, Y., and Koshizuka, S. (2001). Supercritical-pressure, once-through cycle light water cooled reactor concept. J. Nuclear Sci. Technol. 38, 1081–1089. doi: 10.1080/18811248.2001.9715139
Sun, P., and Jiang, J. (2012). Construction and analysis of a dynamic model for a Canadian direct-cycle SCWR for control system studies. Nuclear Technol. 180, 399–421. doi: 10.13182/NT12-A15352
Wang, H.-D., Zhou, T., Chen, J., and Fan, Y.-N. (2012). Perturbation characteristics analysis of supercritical cooling-water reactor under control condition. Atomic Ener. Sci. Technol. 46, 555–560. doi: 10.1007/s11783-011-0280-z
Wu, P., Gou, J., Shan, J., and Zhang, B. (2013). Safety analysis code SCTRAN development for SCWR and its application to CGNPC SCWR. Ann. Nuclear Ener. 56, 122–135. doi: 10.1016/j.anucene.2013.01.028
Wu, P., Xiong, X., Shan, J., and Junli, G. (2016). Improvement and validation of the wall heat transfer package of RELAP5/MOD3.3. Nuclear Eng. Design 310, 418–428. doi: 10.1016/j.nucengdes.2016.10.049
Yamada, S., and Ishiwatari, Y. (2009). “Design and analysis of procedures for system pressurization and line-switching to once-through mode in plant startup of SCWR,” in The 13th International Topical Meeting on Nuclear Reactor Thermal Hydraulic, Ishikawa, Paper N13P1435.
Yamagata, K., Nishikawa, K., Hasegawa, S., and Fujii, T. (1972). Forced convective heat transfer to supercritical water flowing in tubes. Int. J. Heat Mass Transf. 15, 2575–2593. doi: 10.1016/0017-9310(72)90148-2
Yi, T. T., Ishiwatari, Y., Koshizuka, S., and Oka, Y. (2004). Startup thermal analysis of a high-temperature supercritical-pressure light water reactor. J. Nuclear Sci. Technol. 41, 790–801. doi: 10.1080/18811248.2004.9715548
Zahlan, H., Tavoularis, S., and Groeneveld, D. (2015). A look-up table for trans-critical heat transfer in water-cooled tubes. Nuclear Eng. Design 285, 109–125. doi: 10.1016/j.nucengdes.2014.12.027
A: flow area/m2
e(t): main steam temperature deviation from set point, %
Dh: Hydraulic equivalent diameter, m
ftp: friction coefficient
g: gravitational acceleration, m·s–2
h: enthalpy, J·kg–1
K1: lead-lag coefficient
K2: integral coefficient
KP: proportional gain
KI: integral gain
L: length, m
T1: lead time, s
T2: lag time, s
Tmean: measured temperature by the thermometer,°C
Tset: main steam temperature set point,°C
Tstream: main steam real temperature,°C
t: time, t
U: internal energy, J·kg–1
u(t): feed water flow rate signal, kg/s
ΔV: valve opening relative to initial time
v: fluid velocity, m·s–1
W: flow rate, kg·s–1
z: distance, m
vρ: insertion reactivity speed, cent/s
vρmax: the maximum insertion reactivity speed, cent/s
ρmix: mixture density, kg/m3
Keywords: Supercritical Water Reactor, SCTRAN, heat transfer coefficient, control system, startup
Citation: Yuan Y, Shan J, Wang L, Wang D and Zhang X (2018) Startup Thermal Analysis of a Supercritical-Pressure Light Water-Cooled Reactor CSR1000. Front. Energy Res. 6:127. doi: 10.3389/fenrg.2018.00127
Received: 08 September 2018; Accepted: 07 November 2018;
Published: 26 November 2018.
Edited by:
Jun Wang, University of Wisconsin-Madison, United StatesReviewed by:
Yacine Addad, Khalifa University, United Arab EmiratesCopyright © 2018 Yuan, Shan, Wang, Wang and Zhang. This is an open-access article distributed under the terms of the Creative Commons Attribution License (CC BY). The use, distribution or reproduction in other forums is permitted, provided the original author(s) and the copyright owner(s) are credited and that the original publication in this journal is cited, in accordance with accepted academic practice. No use, distribution or reproduction is permitted which does not comply with these terms.
*Correspondence: Yuan Yuan, eXVhbnl1YW41QG1haWwuc3lzdS5lZHUuY24=
Disclaimer: All claims expressed in this article are solely those of the authors and do not necessarily represent those of their affiliated organizations, or those of the publisher, the editors and the reviewers. Any product that may be evaluated in this article or claim that may be made by its manufacturer is not guaranteed or endorsed by the publisher.
Research integrity at Frontiers
Learn more about the work of our research integrity team to safeguard the quality of each article we publish.