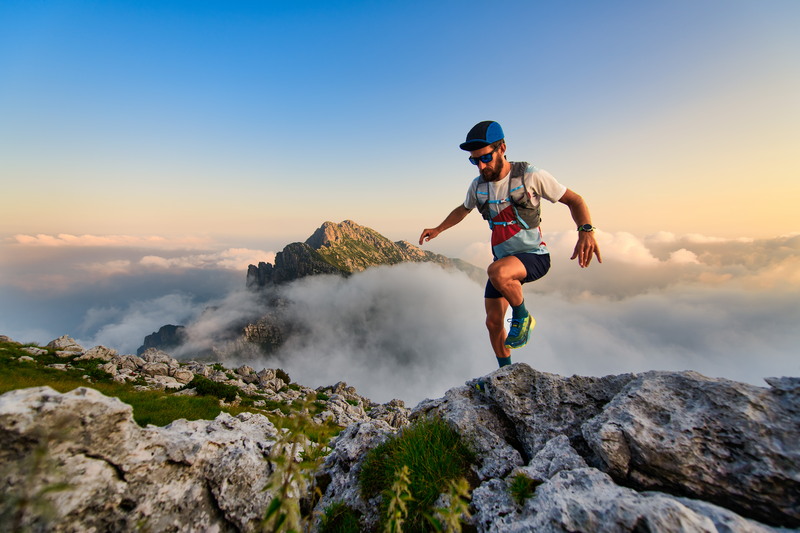
95% of researchers rate our articles as excellent or good
Learn more about the work of our research integrity team to safeguard the quality of each article we publish.
Find out more
PERSPECTIVE article
Front. Energy Res. , 09 November 2018
Sec. Bioenergy and Biofuels
Volume 6 - 2018 | https://doi.org/10.3389/fenrg.2018.00119
This article is part of the Research Topic Advancements in Biomass Feedstock Preprocessing: Conversion Ready Feedstocks View all 24 articles
Ash in biomass is believed to damage biorefinery equipment due to its abrasive properties. All biomass contains at least some ash, or inorganic content, as a result of normal physiological processes. The concentration of biogenic ash in biomass is largely species dependent; however it can also be affected by weather patterns, irrigation, soil type, and fertilizer applications. Ash concentrations in harvested biomass can also be elevated due to the incorporation of soil and dust during the harvest and collection processes. While ash concentration in biomass is important, so also is the mineral form of the ash. Certain mineral forms of ash can be much harder than the steels used to construct biorefinery equipment and cause excessive wear. In this perspective, the relative concentrations of ash elements, mineral forms of ash, and the hardness of these minerals are considered to identify ash components of concern to biorefinery operators. Strategies are suggested to remove ash from harvested biomass to reduce the risk of excessive wear on biomass processing equipment.
Based on reports from the U.S. Department of Energy supported Integrated Biorefinery projects (IBRs), biomass feedstocks such as corn stover are causing more wear to equipment than anticipated. Anecdotal information from one IBR cited grinder blade replacement every few days, less than 10% of their expected lifetime. Pneumatic conveyance systems were sustaining damage, particularly at bends where holes were worn through ducting. This excessive wear resulted in processing equipment shut-downs that could range from a few hours to days (Nguyen, 2017, pers. comm.). The problem of biomass-caused wear has been known and reported on for several years (U.S. Department of Energy, 2010; Kenney et al., 2013; Le et al., 2014); however very little research has been published that helps to determine the cause of the wear and develop mitigation strategies. Biomass-caused wear has been identified as a serious issue facing the startup of cellulosic biorefineries and needs to be mitigated for successful plant operations (U.S. Department of Energy, 2016). A more complete understanding of the physical properties of biomass is required to (1) adjust properties of the incoming biomass to result in less wear, and/or (2) design equipment that is more resistant to wear from biomass. In this perspective paper, we will discuss the poorly understood relationships between biomass feedstocks and biorefinery equipment wear. The known wear-causing properties of biomass feedstocks will be reviewed and strategies to mitigate these properties will be discussed.
A thorough review of the literature pertaining to wear properties of biomass feedstocks yielded limited information. Two studies examined wear occurring on an aluminum feed chute for an automated rice grain sorter (Camacho et al., 2007, 2009). The first study demonstrated that the main wear mechanisms were erosion and abrasion (Camacho et al., 2009). It was unclear how much rice or rice husks contributed to these wear mechanisms, but an experiment designed to simulate the presence of rice husks (which are known to be abrasive, Poudel et al., 2012) showed an order of magnitude increase in wear volume compared to rice alone. This study also examined several surface treatments (hard anodized, hard anodized with PTFE and chrome plating) that increased surface hardness. These treatments reduced wear volumes by 50% in the absence of abrasive particles and by 78–85% when abrasive particles were present. The second study demonstrated that erosive wear was predominant at the top of the chute where the grains initially impact, and abrasive wear was predominant lower on the chute in areas where the grains were sliding (Camacho et al., 2007).
Two other studies examined wear phenomena in the sugar cane industry. The first study, examining tribological aspects of shafts and bearings in sugar cane mills, found that a combination of bagasse and soil contamination entered bearing gaps and resulted in rapid abrasive wear and formation of grooves on the shaft journal (Rivas et al., 2006). Further analysis determined that both abrasion and adhesion mechanisms were responsible, with plastic deformation of grains forming laminated zones and generating debris contributing to abrasion. The second study examined wear occurring on the blades of mechanical sugarcane cutters and found that wear increased as the cane was cut closer to the ground with blades having to be replaced as often as every 20 min (Langton et al., 2007). This indicates that in addition to the wear being caused by the plant material, contaminating soil also plays a strong role in wear.
The wear of pelleting and briquetting dies has also been investigated. Sharma et al. (2016) found that the screw extruder of a briquetting system was worn out within hours when rice husks were used as a feedstock. Shrestha and Ghimire (2014) reported that it was the silica in rice husks that caused the most friction against the screw extruder and the briquette die. In their study, the screw had worn significantly within 4–5 h of processing rice husks. Reducing the silica content by blending the rice husks with lower ash biomass led to reduced wear on the dies and screw extruder. In another report, it was determined that the main cause of wear in a pellet extruder machine was due to the inclusion of sand with the biomass and high silica content of the wood being pelleted (de Wet et al., 2016).
The ash content in biomass is derived from two primary sources: introduced ash collected during harvest and processing, and biogenic ash inside of the plant tissues due to normal biological processes. The sum of these two numbers is referred to as the “ash content” of the sample and can range from 0.1% (w/w, debarked wood chips) to 26% (w/w, rice husks), or higher as introduced ash concentrations increase (Tao et al., 2012). Examination of 840 samples of wheat, miscanthus and corn stover showed that 90% of the samples had ash contents between 3 and 14% (w/w) (Kenney et al., 2013).
Introduced ash added during harvest and collection of biomass is the most likely cause of excessive wear being observed in biorefineries (U.S. Department of Energy, 2016 Nguyen, 2017, pers. comm.). The amount of introduced ash included with the biomass can be dependent upon the method of harvest (Shinners et al., 2012; Williams et al., 2016), the harvester configuration (Bonner et al., 2014b; Lizotte et al., 2015), and the skill of the equipment operator (Bonner et al., 2014b). This added material can contain rocks, sand, soil, and dust. The most common parent minerals of soil formation include quartz (SiO2, Mohs hardness = 7), calcite (CaCO3, Mohs hardness = 3), feldspar (KAlSi3O8, Mohs hardness = 7), and mica (biotite, K(Mg,Fe)3AlSi3O10(OH)2, Mohs hardness = 2.5–3; Miller and Donahue, 1990; Barthelmy, 2014). The Mohs hardness index is explained in Table 1 with higher numbers indicating harder materials. The exact chemical characteristics of soil contamination in biomass is very location specific, and can even be field and sub-field specific (Bonner et al., 2014a). Of these soil forming minerals, quartz and feldspar are of most concern as they are both harder than mild steel and are more likely to damage biomass processing equipment.
Table 1. Mohs relative hardness scale, examples of minerals of each hardness level, and common tests to determine mineral hardness.
Biomass is never ash-free as plants require inorganic elements and minerals for normal growth and physiological functions (Epstein, 1994, 1999; Kochian, 2000). Essential elements include the macronutrients nitrogen, potassium, calcium, magnesium, phosphorous, and sulfur, and the micronutrients chlorine, boron, iron, manganese, zinc, copper, molybdenum, and nickel. Cobalt is required for all plants that fix nitrogen. Silicon and sodium are required by very few plants; however their presence in the soil can be beneficial as they are absorbed by the plant and incorporated into plant tissue. Aluminum can be present in low quantities in plants complexed with other elements such as silicon (Vassilev et al., 2013).
The presence of these elements is not necessarily predictive of wear, but rather the wear properties are defined by the type of mineral in which the element is present. As an example, elevated concentrations of silicon in biomass, if present as quartz (SiO2), could be quite damaging to processing equipment due to the hardness of the mineral (Mohs hardness = 7; Barthelmy, 2014). However, the same concentrations of silicon present in the biomass as the mineral kaolinite (Al2Si2O5(OH)4, Mohs hardness = 1.5–2) would be unlikely to cause damage to the processing equipment. The mineral content found in the plants is dependent upon several variables, including plant species, soil type, soil amendments and weather. There are several chemical and physical forms that inorganic minerals can take in the biomass, including amorphous crystals, precipitated salts, integrated structures, or complexed with other organic molecules within the lignocellulosic matrix.
For these minerals to cause damage to equipment, the mineral must be present in sufficient quantities and must be at least as hard as steel to cause rapid damage to biorefinery equipment. Softer minerals may also cause wear to steel through long term exposure and high speed impacts; however only minerals at least as hard as mild steel were considered due to their potential to cause wear at an accelerated rate. Table 2 shows plant and soil minerals with observed concentrations above 1% shaded green and minerals with Mohs hardness of 5 (mild steel) or above shaded blue. The names of minerals with both these properties have been shaded red. It is hypothesized that these red-shaded minerals are the most likely to cause damage to biomass processing equipment, and all but three are silicates. As a basic example, in some biomass feedstocks 10% of the mass is ash, and over 50% of that ash can be silicon-based minerals. Thus, five percent of the material that is being handled in a refinery could be hard silicates that are damaging equipment.
Table 2. Mineral compounds found in biomass [Adapted from (Vassilev et al., 2013), hardness values obtained from the “Minerology Database (10) (http://webmineral.com/)].
Prior to introducing the material into the conversion reactors, there is an opportunity to improve the quality of the biomass by removing ash. Effective mechanical and chemical methods have been developed that can reduce the ash content of the biomass; however it is likely not economically feasible to remove all of the ash from the biomass. An understanding of the advantages and limits of these approaches will enable the selective removal of the most abrasive ash components found in the biomass using the most cost effective technologies.
Introduced ash can be efficiently removed via mechanical separations including size separations and air classification. Air classification of forest residues was shown to concentrate 40% of the total ash into a small fraction that represented about 7% of the total biomass (Lacey et al., 2015). The concentrated ash was primarily introduced ash (enriched in silicon, aluminum, and iron); however the mineral compositions of this ash fraction were not determined. A similar study using a variety of feedstocks including corn stover, switchgrass, and grass clippings, and a combination of air classification and size fractionation was used to isolate fractions with high ash content. An effective separation of soil elements was evidenced by elevated concentrations of aluminum and iron in the lightest air classified fractions and smallest size fractions (Thompson et al., 2016). Others have also shown ash to be concentrated in the smallest size fractions (Smith et al., 2012; Zhang et al., 2012). Using both sieving (Liu and Bi, 2011; Lacey et al., 2016; Thompson et al., 2016) and trommel screens (Smith et al., 2012; Dukes et al., 2013; Greene et al., 2014), concentrations of introduced ash could be effectively reduced from biomass feedstocks.
Biogenic ash is often precipitated inside the cell walls or contained in water transport elements, but can also be incorporated into the cell walls as part of the physical support structure. Because of this, typical mechanical fractionation methods cannot effectively separate it from the bulk of the feedstock. If it is necessary to remove this type of ash, chemical preprocessing that solubilizes the ash would be required. The exact location and chemical state of the ash will determine the most effective removal methods. Physiological cations involved in nutrient transport and enzyme catalysis may be leached out via diffusion if an acid is added as a counter ion to facilitate ion-ion exchange (Schell et al., 2003; Li et al., 2010; Liu and Bi, 2011; Aston et al., 2016). Hot water “washes” cause auto catalysis of acetyl acid groups producing acetic acid (Lu et al., 2016). This has been observed to result in over 90% removal of alkaline earth and alkali metals at temperatures as low as 90°C (Aston et al., 2016). Although dilute acid leaches or hot water washes are effective at removing specific cations, alkaline extractions will likely be required to remove both entrained and physiological silica since it causes structural changes that liberate this element (Hsieh et al., 2009; Cheng et al., 2011; Bazargan et al., 2015). Such an approach combined with mechanical separations and blending with lower ash materials may improve the economic feasibility within the feedstock supply chain (Lacey et al., 2015, 2016; Thompson et al., 2016).
While little is known about the specific wear properties of biomass, much is known about the minerals that can be present in biomass, and methods have been developed that are capable of efficiently removing introduced and biogenic ash. Additional work is needed to better characterize the minerals present in biomass feedstocks that are causing the most wear. With this understanding, biomass could be modified to alter its wear properties, or equipment could be selected that will be more compatible with the specific mineral content found in the biomass being processed.
JL is the primary author and contributed text on the literature review and on mitigation methods for ash removal. JA contributed text on mitigation methods for ash removal. VT is the corresponding author and contributed text on the literature review.
The research was supported by the U.S. Department of Energy (DOE), Office of Energy Efficiency and Renewable Energy (EERE), Bioenergy Technologies Office (BETO), under DOE Idaho Operations Office Contract DE-AC07-05ID14517.
The authors declare that the research was conducted in the absence of any commercial or financial relationships that could be construed as a potential conflict of interest.
Aston, J. E., Thompson, D. N., and Westover, T. L. (2016). Performance assessment of dilute-acid leaching to improve corn stover quality for thermochemical conversion. Fuel 186, 311–319. doi: 10.1016/j.fuel.2016.08.056
Barthelmy, D. (2014). Mineralogy Database. Available online at: http://webmineral.com (Accessed Mar 25, 2017).
Bazargan, A., Bazargan, M., and McKay, G. (2015). Optimization of rice husk pretreatment for energy production. Renew. Energy 77, 512–520. doi: 10.1016/j.renene.2014.11.072
Bonner, I., Cafferty, K., Muth, D., Tomer, M., James, D., Porter, S., et al. (2014a). Opportunities for energy crop production based on subfield scale distribution of profitability. Energies 7:6509. doi: 10.3390/en7106509
Bonner, I. J., Smith, W. A., Einerson, J. J., and Kenney, K. L. (2014b). Impact of harvest equipment on ash variability of baled corn stover biomass for bioenergy. Bioenergy Res. 7, 845–855. doi: 10.1007/s12155-014-9432-x
Camacho, J., Lewis, R., and Dwyer-Joyce, R. S. (2007). Wear of a chute in a rice sorting machine. Wear 263, 65–73. doi: 10.1016/j.wear.2006.11.052
Camacho, J., Lewis, R., and Dwyer-Joyce, R. S. (2009). Solid particle erosion caused by rice grains. Wear 267, 223–232. doi: 10.1016/j.wear.2008.12.034
Cheng, H. L., Zhan, H. Y., Fu, S. Y., and Lucia, L. A. (2011). Alkali extraction of hemicellulose from depithed corn stover and effects on soda-AQ pulping. Bioresources 6, 196–206. doi: 10.15376/biores.6.1.196-206
de Wet, M., de Lange, L., and du Toit, D. (2016). Study to Minimise Abrasion Caused by Sand and Minerals From Harvested Encroacher Bush Biomass With Possible Alternative Technologies and Improvements for Manufacturing a Selection of Compressed Wood Products in Namibia: Milestone V: Final Report. Report completed by GIZ, NRGen Advisors (PTY) Ltd., and WML Consulting Engineers (PTY) Ltd.
Dukes, C. C., Baker, S. A., and Greene, W. D. (2013). In-wood grinding and screening of forest residues for biomass feedstock applications. Biomass Bioenergy 54, 18–26. doi: 10.1016/j.biombioe.2013.02.032
Epstein, E. (1994). The anomaly of silicon in plant biology. Proc. Natl. Acad. Sci. U. S. A. 91, 11–17. doi: 10.1073/pnas.91.1.11
Epstein, E. (1999). Silicon. Ann. Rev. Plant Physiol. Plant Mol. Biol. 50, 641–664. doi: 10.1146/annurev.arplant.50.1.641
Greene, W. D., Cutshall, J. B., Dukes, C. C., and Baker, S. A. (2014). Improving woody biomass feedstock logistics by reducing ash and moisture content. Bioenergy Res. 7, 816–823. doi: 10.1007/s12155-013-9404-6
Hsieh, Y., Du, Y., Jin, F., Zhou, Z., and Enomoto, H. (2009). Alkaline pre-treatment of rice hulls for hydrothermal production of acetic acid. Chem. Eng. Res. Design 87, 13–18. doi: 10.1016/j.cherd.2008.07.001
Kenney, K. L., Smith, W. A., Gresham, G. L., and Westover, T. L. (2013). Understanding biomass feedstock variability. Biofuels 4, 111–127. doi: 10.4155/bfs.12.83
Kochian, L. V. (2000). “Molecular physiology of mineral nutrient acquisition, transport, and Utilization,” in Biochemistry & Molecular Biology of Plants, ed W. G. R. J. B. Buchanan (Rockville, MD: American Society of Plant Physiologists), 1204–1249.
Lacey, J., Aston, J., Westover, T., Cherry, R., and Thompson, D. (2015). Removal of introduced inorganic content from chipped forest residues via air classification. Fuel 160, 265–273. doi: 10.1016/j.fuel.2015.07.100
Lacey, J. A., Emerson, R. M., Thompson, D. N., and Westover, T. L. (2016). Ash reduction strategies in corn stover facilitated by anatomical and size fractionation. Biomass Bioenergy 90, 173–180. doi: 10.1016/j.biombioe.2016.04.006
Langton, M. I., Smithers, J. C., Bezuidenhout, C. N., and Lyne, P. W. L. (2007). Evaluation of the Illovo mechanical cane cutter. Int. Sugar J. 109, 118–120.
Le, D. M., Sørensen, H. R., Knudsen, N. O., Schjoerring, J. K., and Meyer, A. S. (2014). Biorefining of wheat straw: accounting for the distribution of mineral elements in pretreated biomass by an extended pretreatment–severity equation. Biotech Biofuels 7:141. doi: 10.1186/s13068-014-0141-7
Li, C., Knierim, B., Manisseri, C., Arora, R., Scheller, H. V., Auer, M., et al. (2010). Comparison of dilute acid and ionic liquid pretreatment of switchgrass: biomass recalcitrance, delignification and enzymatic saccharification. Bioresour. Tech. 101, 4900–4906. doi: 10.1016/j.biortech.2009.10.066
Liu, X., and Bi, X. T. (2011). Removal of inorganic constituents from pine barks and switchgrass. Fuel Proc. Tech. 92, 1273–1279. doi: 10.1016/j.fuproc.2011.01.016
Lizotte, P-L., Savoie, P., and De Champlain, A. (2015). Ash content and calorific energy of corn stover components in Eastern Canada. Energies 8, 4827–4838. doi: 10.3390/en8064827
Lu, H. S., Liu, S. Y., Zhang, M. H., Meng, F. M., Shi, X. F., and Yan, L. (2016). Investigation of the strengthening process for liquid hot water pretreatments. Energy Fuels 30, 1103–1108. doi: 10.1021/acs.energyfuels.5b02658
Miller, R. W., and Donahue, R. L. (1990). Soils: An Introduction to Soils and Plant Growth. Upper Saddle River, NJ: Prentice Hall.
Poudel, M. S., Shrestha, K. R., and Singh, R. M. (2012). “Screw extruder biomass briquetting,” in Rentech Symposium Compendium (Dhulikhel).
Rivas, J. S., Coronado, J. J., and Gomez, A. L. (2006). Tribological aspects for the shafts and bearings of sugar cane mills. Wear 261, 779–784. doi: 10.1016/j.wear.2006.01.026
Schell, D. J., Farmer, J., Newman, M., and McMillan, J. D. (2003). Dilute-sulfuric acid pretreatment of corn stover in pilot-scale reactor. Appl. Biochem. Biotechnol. 105, 69–85. doi: 10.1385/abab:105:1-3:69
Sharma, S., Bajracharya, T. R., and Shrestha, K. R. (2016). “Surface treatment of screw and financial analysis of rice husk briquetting machine by using different types of hardfacing welding rods,” in 2016 IOE Graduate Conference (Pulchowk), 215–220.
Shinners, K. J., Bennett, R. G., and Hoffman, D. S. (2012). Single- and two-pass corn grain and stover harvesting. Transac. ASABE 55, 341–350. doi: 10.13031/2013.41372
Shrestha, R., and Ghimire, R. (2014). “Analysis for the financial viability of the rice husk briquette production by increasing screw life and reducing fuel cost,” in 2014 IOE Graduate Conference (Katmandu).
Smith, D., Sessions, J., Tuers, K., Way, D., and Traver, J. (2012). Characteristics of forest-derived woody biomass collected and processed in oregon. Forest Products J. 62, 520–527. doi: 10.13073/FPJ-D-12-00014.1
Tao, G. C., Geladi, P., Lestander, T. A., and Xiong, S. J. (2012). Biomass properties in association with plant species and assortments. II: a synthesis based on literature data for ash elements. Renew. Sustain. Energy Rev. 16, 3507–3522. doi: 10.1016/j.rser.2012.01.023
Thompson, V. S., Lacey, J. A., Hartley, D., Jindra, M. A., Aston, J. E., and Thompson, D. N. (2016). Application of air classification and formulation to manage feedstock cost, quality and availability for bioenergy. Fuel 180, 497–505. doi: 10.1016/j.fuel.2016.04.040
U.S. Department of Energy (2016). Biorefinery Optimization Workshop Summary Report. Washington DC: Report, Office of Energy Efficiency and Renewable Energy, Bioenergy Technologies Office, Chicago.
U.S. Department of Energy, U.S. Department of Agriculture, U.S. Department of Transportation, U.S. Environmental Protection Agency, and U.S. National Science Foundation. (2010). Biofuel Feedstock Logistics: Recommendations for Research and Commercialization. Washington, DC: F.L.I.W. Group.
Vassilev, S. V., Baxter, D., Andersen, L. K., and Vassileva, C. G. (2013). An overview of the composition and application of biomass ash. Part 1. Phase-mineral and chemical composition and classification. Fuel 105, 40–76. doi: 10.1016/j.fuel.2012.09.041
Williams, C. L., Westover, T. L., Emerson, R. M., Tumuluru, J. S., and Li, C. (2016). Sources of biomass feedstock variability and the potential impact on biofuels production. BioEnergy Res. 9, 1–14. doi: 10.1007/s12155-015-9694-y
Keywords: biomass abrasion, biogenic ash, introduced ash, ash minerals, equipment wear
Citation: Lacey JA, Aston JE and Thompson VS (2018) Wear Properties of Ash Minerals in Biomass. Front. Energy Res. 6:119. doi: 10.3389/fenrg.2018.00119
Received: 15 May 2018; Accepted: 22 October 2018;
Published: 09 November 2018.
Edited by:
Timothy G. Rials, University of Tennessee, Knoxville, United StatesReviewed by:
Ben J. Stuart, Old Dominion University, United StatesCopyright © 2018 Lacey, Aston and Thompson. This is an open-access article distributed under the terms of the Creative Commons Attribution License (CC BY). The use, distribution or reproduction in other forums is permitted, provided the original author(s) and the copyright owner(s) are credited and that the original publication in this journal is cited, in accordance with accepted academic practice. No use, distribution or reproduction is permitted which does not comply with these terms.
*Correspondence: Vicki S. Thompson, Vmlja2kuVGhvbXBzb25AaW5sLmdvdg==
Disclaimer: All claims expressed in this article are solely those of the authors and do not necessarily represent those of their affiliated organizations, or those of the publisher, the editors and the reviewers. Any product that may be evaluated in this article or claim that may be made by its manufacturer is not guaranteed or endorsed by the publisher.
Research integrity at Frontiers
Learn more about the work of our research integrity team to safeguard the quality of each article we publish.