- 1Department of Applied Chemistry, Graduate School of Engineering, Osaka Prefecture University, Sakai, Osaka, Japan
- 2Department of Energy and Environment, Research Institute of Electrochemical Energy, National Institute of Advanced Industrial Science and Technology (AIST), Ikeda, Osaka, Japan
All-solid-state batteries with inorganic solid electrolytes (SEs) are recognized as an ultimate goal of rechargeable batteries because of their high safety, versatile geometry, and good cycle life. Compared with thin-film batteries, increasing the reversible capacity of bulk-type all-solid-state batteries using electrode active material particles is difficult because contact areas at solid–solid interfaces between the electrode and electrolyte particles are limited. Sulfide SEs have several advantages of high conductivity, wide electrochemical window, and appropriate mechanical properties, such as formability, processability, and elastic modulus. Sulfide electrolyte with Li7P3S11 crystal has a high Li+ ion conductivity of 1.7 × 10−2 S cm−1 at 25°C. It is far beyond the Li+ ion conductivity of conventional organic liquid electrolytes. The Na+ ion conductivity of 7.4 × 10−4 S cm−1 is achieved for Na3.06P0.94Si0.06S4 with cubic structure. Moreover, formation of favorable solid–solid interfaces between electrode and electrolyte is important for realizing solid-state batteries. Sulfide electrolytes have better formability than oxide electrolytes. Consequently, a dense electrolyte separator and closely attached interfaces with active material particles are achieved via “room-temperature sintering” of sulfides merely by cold pressing without heat treatment. Elastic moduli for sulfide electrolytes are smaller than that of oxide electrolytes, and Na2S–P2S5 glass electrolytes have smaller Young’s modulus than Li2S–P2S5 electrolytes. Cross-sectional SEM observations for a positive electrode layer reveal that sulfide electrolyte coating on active material particles increases interface areas even with a minimum volume of electrolyte, indicating that the energy density of bulk-type solid-state batteries is enhanced. Both surface coating of electrode particles and preparation of nanocomposite are effective for increasing the reversible capacity of the batteries. Our approaches to form solid–solid interfaces are demonstrated.
Introduction
All-solid-state batteries using inorganic solid electrolytes (SEs), used in place of conventional organic liquid electrolytes, have been studied because of their high safety (non-flammability with no liquid leakage), long cycle life, and versatile geometries (Takada, 2013; Tatsumisago et al., 2013; Tatsumisago and Hayashi, 2014). These features are important for large rechargeable lithium batteries with high energy density for application to eco-cars, such as electric vehicles and plug-in hybrid vehicles. Rechargeable sodium batteries are also attractive for large-scale applications for stationary load-leveling because sodium is expected to be the next targeted element after lithium based on its atomic weight, standard potential, and natural abundance (Yabuchi et al., 2015b; Yamada, 2014).
A key material to realize all-solid-state rechargeable batteries is a superior SE. In lithium ion conductors, sulfide electrolytes of Li10GeP2S12 and Li7P3S11 have high room-temperature conductivity of more than 10−2 S cm−1, which is as high as the conductivity of conventional organic liquid electrolytes (Kamaya et al., 2011; Seino et al., 2014). The lithium ion transport number of liquid electrolytes is below 0.5, whereas that of SE is 1. It is noteworthy that the conductivity of lithium ions of sulfide SEs already exceeds that of organic liquid electrolytes. Very recently, Li9.54Si1.74P1.44S11.7Cl0.3 has been reported to show the highest conductivity of 2.5 × 10−2 S cm−1. Using this superior electrolyte, high power competing with that of supercapacitors can be achieved in all-solid-state rechargeable lithium batteries (Kato et al., 2016b). Sulfide SEs have several important benefits of high conductivity, wide electrochemical window, and appropriate mechanical properties, such as formability and elastic modulus. A shortcoming of sulfide electrolytes is its low air stability. To realize bulk-type all-solid-state batteries, the formation of favorable solid–solid interfaces between electrode and electrolyte is important in addition to the development of superior sulfide electrolytes. Direct coating of sulfide electrolytes on active material particles instead of adding electrolyte particle is effective for forming a close solid–solid interface with large contact area. Insulative active materials, such as sulfur and Li2S, should be blended not only with SE but also with carbon-conductive additive to form ion and electron conduction paths to active materials. Nanocomposites of the three components are useful by preparation with high-energy ball milling, which pulverizes and combines them. Transition metal sulfides (MSx) with high conductivity have good compatibility with sulfide SEs having the same sulfide anions. Especially, sulfur-rich compounds, such as TiS3, are attractive active materials with high reversible capacity. Lithium metal is a supremely negative electrode, but issues related to lithium dendrites prevent its commercialization. Combination with a SE is a promising solution. Interface modification between Li metal and the SE is important.
As described in this paper, the recent development of sulfide SEs and interface formation processes for bulk-type all-solid-state Li and Na batteries are reviewed. Significant properties as SEs of conductivity, chemical stability, and mechanical property for Li+ or Na+ ion conducting sulfides are reported. Procedures for preparing sulfide electrolytes, such as mechanical milling and liquid-phase synthesis, are also described. Several approaches to form favorable solid–solid interfaces developed by our research group are demonstrated. Processes for the coating of sulfide electrolytes via gas-phase or liquid-phase process on LiCoO2 or graphite particles have been developed. Preparation of nanocomposite electrodes with sulfur, Li2S, and Li3PS4 (as a bifunctional material of electrolyte and electrode) particles is described, along with the use of MSx active materials. Formation of a solid–solid interface for using lithium metal negative electrodes is also discussed.
Development of Sulfide Solid Electrolytes
Sulfide SEs with Li+ or Na+ ion conductivity have been developed during the past three decades. Recently, chemical stability and mechanical properties as well as conductivity for sulfide electrolytes have attracted much attention. Sulfide electrolytes are prepared using several techniques with solid-phase reaction, melt-quenching, mechanical milling, crystallization of mother glasses, and liquid-phase reaction. Detailed information related to electrolyte properties will be presented in the following sections of this report.
Conductivity
Inorganic sulfide SEs with high Li+ or Na+ ion conductivities have been developed. Sulfide electrolytes with high conductivities are presented in Table 1. In Li+ ion conducting sulfide electrolytes, crystalline Li10GeP2S12 (LGPS; Kamaya et al., 2011) and glass–ceramic Li7P3S11 (Seino et al., 2014) have considerably high conductivity of more than 10−2 S cm−1 at 25°C, which is beyond the Li+ ion conductivity of conventional organic liquid electrolytes. Very recently, Li9.54Si1.74P1.44S11.7Cl0.3 with LGPS structure has been reported to show the highest conductivity of 2.5 × 10−2 S cm−1 (Kato et al., 2016b). Studies investigating new electrolytes with much higher conductivity are in progress. Several crystals, such as Li10SnP2S12 (Boron et al., 2013) and Li6PS5Cl (Boulineau et al., 2012), have high conductivity of more than 10−3 S cm−1. This conductivity is also achieved by the addition of lithium halides to sulfide glass and glass–ceramic electrolytes (Wada et al., 1983; Ujiie et al., 2014).
The Na+ ion conductivity is lower than Li+ ion conductivity in glassy electrolytes. Ionic conduction of Na+ ion with ionic radius larger than Li+ ion is unfavorable in glasses (Souquet et al., 1981). For sodium ion conductors, sulfides with high conductivity had not been found since this report described Na3PS4 glass–ceramic electrolytes in 2012. A cubic Na3PS4 phase is precipitated by crystallization of a mother Na3PS4 glass. The prepared glass–ceramic electrolyte shows Na+ ion conductivity of greater than 10−4 S cm−1 at 25°C (Hayashi et al., 2012b). Furthermore, partial substitution of Si for P in Na3PS4 is useful for increasing conductivity (Tanibata et al., 2014). Figure 1 presents the composition dependence of conductivities at 25°C for Na3PS4–Na4SiS4 glass–ceramic electrolytes. The replacement of 6 mol% Na3PS4 by Na4SiS4 increases the conductivity from 4.6 × 10−4 to 7.4 × 10−4 S cm−1. The electron density distribution of the cubic Na3PS4 structure obtained using the maximum entropy method is shown in the inset of Figure 1. Na3PS4 has three-dimensional Na+ ion conduction paths along Na1 and Na2 sites. Increased Na+ ion concentration is presumed as the reason for the enhancement of conductivity. Very recently, high conductivity of more than 10−3 S cm−1 has been reported in crystalline Na3PSe4 (Zhang et al., 2015). However, studies of new sulfide Na+ ion conductors are few. A first-principles calculation indicates that Sn-doped cubic Na3PS4 is predicted to have a higher Na+ ion conductivity of 10−2 S cm−1 (Zhu et al., 2015). Synthesis of SEs with a favorable structure for Na+ ion conduction based on calculation results is important for finding new Na+ ion conducting SEs.
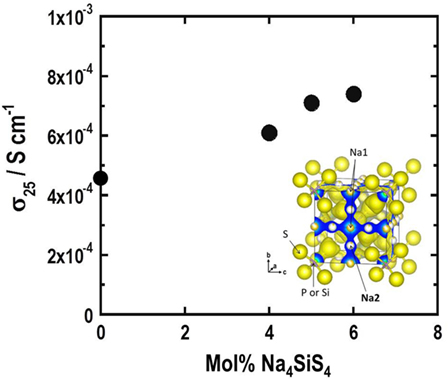
Figure 1. Composition dependence of conductivity at 25°C for (100-x)Na3PS4·xNa4SiS4 (mol%) glass–ceramic electrolytes. The inset shows the electron density distribution of the cubic Na3PS4 structure.
Chemical Stability
A shortcoming of sulfide electrolytes is their lower chemical stability in air atmosphere. Sulfides tend to be decomposed by hydrolysis, generating harmful H2S. Suppression of hydrolysis of sulfides is an important task for developing sulfide electrolytes. Based on our early experiments, the selection of compositions in sulfide electrolytes gives moderate stability in air to sulfide electrolytes (Muramatsu et al., 2011). The chemical stability of sulfide glass electrolytes in the binary system Li2S–P2S5 was examined by exposing them to air atmosphere. Amounts of generated H2S from the sulfides depend on the composition of the glasses; H2S generation is minimized at the composition 75Li2S⋅25P2S5 (mol%). The glass comprises Li+ and ions. An isolated anion without bridging sulfurs is useful for high tolerance for hydrolysis. Li3PS4-based SEs with both good chemical stability and high conductivity have been prepared by the combination of oxides (Li2O or P2O5) and iodides (LiI) (Ohtomo et al., 2013a,b). The addition of metal oxides, such as ZnO, which act as an absorbent for H2S, is also effective for decreasing H2S (Hayashi et al., 2013). It is noteworthy that the use of a favorable MxOy (MxOy: Fe2O3, ZnO, and Bi2O3) with a larger negative Gibbs energy change (ΔG) for the reaction with H2S is effective for improving the chemical stability of sulfide electrolytes. Another approach is the use of sulfide compositions based on the hard and soft acids and bases theory (HSAB; Sahu et al., 2014). Lithium tin thiophosphate, Li4SnS4, has better air stability than that of Li3PS4. Actually, as-substituted Li4SnS4 has good features of both high conductivity of 10−3 S cm−1 and high air stability.
The chemical stability of SEs tends to affect battery performance. The electrochemical performance of all-solid-state C/LiCoO2 cells using Li3PS4 glass or Li7P3S11 glass–ceramic as a SE is compared. The cell with Li3PS4 glass electrolytes exhibits better cycle performance, although Li3PS4 glass has lower conductivity than Li7P3S11 electrolyte (Ohtomo et al., 2013c). High performance of the battery would be based on the higher chemical stability of Li3PS4 electrolytes. Chemical stability as well as conductivity is an important factor of SEs for developing superior solid-state batteries.
Mechanical Property
Adhesion of the solid–solid interface is a key to the utilization of electrode active materials in all-solid-state batteries. Formability or processability of SEs is examined by the molding pressure dependence of the relative density of compressed powder pellets.
Figure 2A shows the dependence of the relative density of 75Li2S⋅25P2S5 and 75Na2S⋅25P2S5 (mol%) glass electrolytes on molding pressure. The relative densities increase gradually with an increase in molding pressure in both glasses at the same alkali compositions of 75 mol% M2S (M = Li or Na), whereas the relative density for the Na2S system is higher than that for the Li2S system (Sakuda et al., 2013a,b; Nose et al., 2015). Cross-sectional SEM images of the 75 mol% M2S pellets pressed at 360 MPa are shown in the inset. Grain boundaries and voids in the pellets are more decreased in the 75Na2S⋅25P2S5 glass compared with the 75Li2S⋅25P2S5 glass. Sulfide glasses are densified by cold pressing without heat treatment, and this densification phenomenon is called “room-temperature pressure sintering” (Sakuda et al., 2013a,b). It is noteworthy that the 75Na2S⋅25P2S5 glass has better formability than the 75Li2S⋅25P2S5 glass. Both the glasses comprise Li+ or Na+ ion and ion, which are thought to diffuse at the particle boundaries on pressing at room temperature. Na+ ion with a larger ionic radius than Li+ ion has a weaker interaction with ion. Therefore, both Na+ and ions would diffuse readily by cold press, leading to better densification.
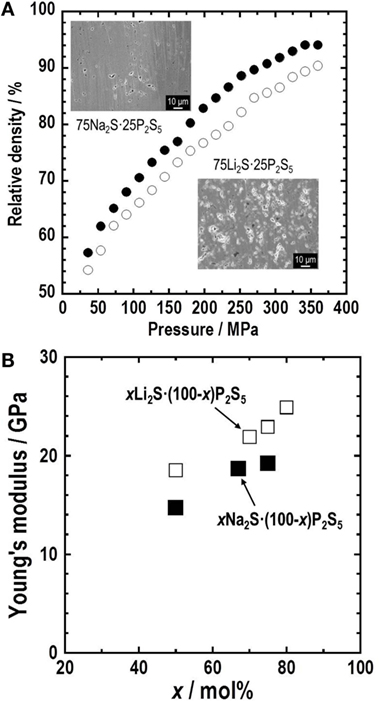
Figure 2. (A) Molding pressure dependence of relative density of 75M2S⋅25P2S5 (M = Li or Na, mol%) glass electrolyte. Cross-sectional SEM images of these glass pellets prepared by pressing at 360 MPa are also shown in the inset. (B) Composition dependence of Young’s modulus for the xM2S⋅(100-x)P2S5 glasses.
Retaining solid–solid contacts between active materials and SEs during charge–discharge processes brings about long cycle lives of all-solid-state batteries. Young’s moduli of SEs are important for keeping favorable contacts even at volume changes of active materials. Those for densified sulfide electrolytes prepared by hot-pressing are determined by an ultrasonic pulse-echo technique and the uniaxial compression tests (Sakuda et al., 2013a,b; Nose et al., 2015). Young’s moduli of the sulfide glasses in the systems Li2S–P2S5 and Na2S–P2S5 are presented in Figure 2B. They are increased gradually with the increase in the alkali content in both systems. The Na2S–P2S5 glasses have smaller Young’s moduli of 15–19 GPa than the Li2S–P2S5 glasses (18–25 GPa). The difference on Young’s modulus is understood based on the Coulomb force and the mean atomic volume of the glasses. These sulfide glasses have an intermediate Young’s modulus between oxide glasses and organic polymers. Sulfide electrolytes deforming elastically are expected to act as a buffer in response to volume changes of active materials during charge–discharge processes. In fact, most all-solid-state batteries that use sulfide SEs exhibit good cycle performance.
Preparation Process
Sulfide SEs were prepared via various techniques. Crystalline electrolytes are prepared via solid-phase reaction, whereas glass electrolytes are obtained using the melt-quenching method. In general, sulfide starting materials are sealed in a carbon-coated quartz tube under vacuum and then heat-treated because of high vapor pressure of sulfides at high temperatures. Heating temperatures and cooling rates at preparation process affect precipitated crystals. A phase diagram in ternary system Li2S–GeS2–P2S5 is complicated (Hori et al., 2015), and crystalline Li10GeP2S12 with a conductivity of 10−2 S cm−1 is prepared by selecting experimental conditions. Another preparation technique of sulfide electrolytes is mechanical milling using a high-energy planetary ball mill apparatus. This technique is fundamentally a room-temperature process. Therefore, sulfides are reacted at ordinary temperature and pressure. Electrolyte particles are obtained directly by milling. They are applicable to all-solid-state batteries without additional pulverization of electrolytes. Crystallization of glass electrolyte tends to precipitate a metastable phase, such as high-temperature phase, which generally has high ionic conductivity (Tatsumisago et al., 1991; Hayashi et al., 2003). Crystalline Li7P3S11 (a high-temperature phase at the composition) is precipitated as a primary phase by heat treatment of a corresponding mother glass, and the obtained glass–ceramic electrolytes show conductivities of 10−3–10−2 S cm−1, which depend on the degree of crystallinity and the grain boundary of Li7P3S11 (Mizuno et al., 2005, 2006; Seino et al., 2014). Cubic Na3PS4 is crystallized from the Na3PS4 glass prepared by mechanical milling. The prepared glass–ceramic electrolytes with Na3PS4 show Na+ ion conductivity of 10−4 S cm−1 at 25°C (Hayashi et al., 2012b).
Electrolyte preparation via liquid phase is a suitable process for cost-effective quantity synthesis without using a special reaction apparatus. In general, this process has benefits of lowering the reaction temperature, shortening the reaction time, and controlling the particle morphology and size. Prepared electrolyte solutions are also useful for the coating of active material particles. Very recently, liquid-phase synthesis of sulfide SEs has been reported. The reaction processes for sulfides are divided into two categories: one uses suspension and the other uses a homogeneous solution. For the former synthesis, β-Li3PS4 synthesized in tetrahydrofuran (Liu et al., 2013) or dimethyl carbonate (Phuc et al., 2016) as reaction medium and Li7P3S11 synthesized in 1,2-dimethoxyethane (Ito et al., 2014) are reported. In these reactions, precursors with precipitates are obtained. Compressed pellets of the heat-treated sulfide electrolytes show conductivity of greater than 10−4 S cm−1 at 25°C. As the latter one via homogeneous liquid, Li3PS4 is synthesized from a mixture of Li2S and P2S5 with N-methlyformamide (NMF) (Teragawa et al., 2014a). The Li3PS4 SEs can also be prepared using a dissolution–reprecipitation process in NMF from 80Li2S⋅20P2S5 (mol%) glass prepared in advance using mechanical milling (Teragawa et al., 2014b). The prepared Li3PS4 electrolyte shows low conductivity of 10−6 S cm−1 at the present stage, but conductivity can be enhanced by selecting electrolyte compositions. Argyrodide-type Li6PS5Cl is dissolved into ethanol. Then, the argyrodite phase is reprecipitated by removing ethanol at 80°C under vacuum for 3 h (Yubuchi et al., 2015a,b). A pellet of the product shows conductivity of 10−5 S cm−1 at 25°C, which is somewhat lower than that of the original Li6PS5Cl. Grain boundary resistance, which is affected by surface structure and morphology, might be greater in the prepared Li6PS5Cl. Optimization of posttreatments for the prepared powders will enhance the Li6PS5Cl conductivity. Furthermore, the combination of sulfide SEs and ionic liquids produces pseudo-SEs (Minami et al., 2010; Oh et al., 2015). The prepared electrolytes give a new category of electrolytes having both high conductivity and good formability.
Sodium-ion conducting sulfide electrolytes with cubic Na3PS4 are also synthesized via a liquid-phase process from the mixture of Na2S and P2S5 in NMF solvent (Yubuchi et al., 2015a). The room-temperature conductivity of the obtained electrolyte is 10−6 S cm−1, which is lower than the conductivity of the electrolyte prepared by mechanical milling. Studies investigating sulfide SEs with Na+ ion conductivity are extremely few at present. New electrolytes produced via a simple liquid-phase process will be researched widely.
Preparation of Solid–Solid Interface in All-Solid-State Batteries
Sulfide glasses are well-balanced SEs with high conductivity, good formability, appropriate Young’s modulus, and moderate chemical stability. They are therefore highly promising SEs for use in all-solid-state batteries. A schematic diagram of bulk-type all-solid-state batteries is depicted in Figure 3. A positive electrode layer is composed not only of active material particles but also of SE ones. The Li+ ion is supplied from SEs attached to active materials. Electrons are mobile through active materials. To enhance the rate of performance of the batteries, conductive additives of nanocarbons are added to the electrode layer. A lithium alloy or lithium metal is used as the negative electrode. A SE layer as a separator is sandwiched with the positive and negative electrode layers. Then, because of good formability of sulfide SEs, it can be pressed uniaxially at room temperature to fabricate bulk-type all-solid-state batteries.
An all-solid-state In/LiCoO2 or Li-In/Li4Ti5O12 cell with Li2S–P2S5 glass–ceramic electrolytes exhibits good cycle performance for hundreds of times at 25°C (Tatsumisago and Hayashi, 2008; Tatsumisago et al., 2013). These cells operate at a high temperature of 100°C, where it is difficult for a liquid electrolyte cell to be used. The all-solid-state cell with Li4Ti5O12 shows a discharge–charge capacity of about 140 mAh g−1. It retains the capacity for 700 cycles with no degradation under a high current density of more than 10 mA cm−2 (Minami et al., 2011).
Coating of Sulfide Electrolytes on LiCoO2 and Graphite Particles
Direct coating of sulfide SEs on LiCoO2 particles, instead of mixing electrolyte particles, is effective for forming good electrolyte–LiCoO2 interfaces with a wide contact area. Pulsed laser deposition (PLD) was first used as a coating technique (Sakuda et al., 2010, 2011). In this study, LiNbO3-coated LiCoO2 particles were fluidized with a vibrator to ensure uniform coating of sulfide electrolytes on the particles.
Figure 4 presents cross-sectional SEM images of positive electrodes with (a) a conventional mixture of LiCoO2 and Li2S–P2S5 SE particles with the weight ratio of 70/30 and (b) SE-coated LiCoO2 particles, where the weight ratio of LiCoO2 and SE coatings was 90/10. Figure 2A shows that solid–solid contacts between LiCoO2 and SE are formed by cold pressing of the mixture electrode because SE particles are deformed easily by pressing. Figure 4A shows that the aggregation of LiCoO2 particles engenders less utilization of LiCoO2 because many voids and less contact with SE are observed among LiCoO2 particles. A close-packed electrode layer is formed using only SE-coated LiCoO2 (Figure 4B). Its enlarged figure, which will be displayed in Figure 7D later, shows that a close solid–solid interface with fewer voids appears, and Li+ ion conduction paths are therefore formed among LiCoO2 particles. It is noteworthy that SE amounts in the electrode are decreased considerably by SE coating on LiCoO2 particles. The use of minimum amounts of SE in an electrode layer contributes to enhanced energy density of all-solid-state batteries.
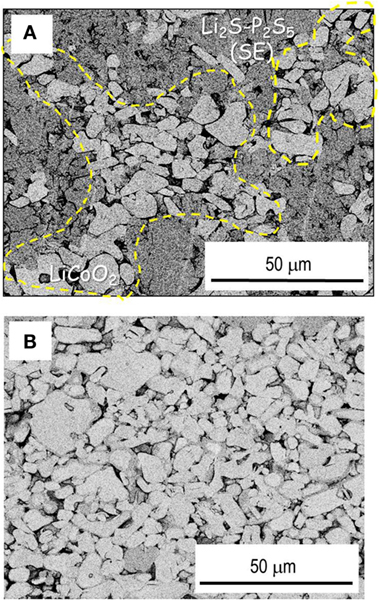
Figure 4. Cross-sectional SEM images of LiCoO2 positive electrode layers consisting of (A) mixture electrode with LiCoO2 and Li2S–P2S5 electrolyte particles and (B) electrolyte-coated LiCoO2 particles.
A cross-sectional high-angle annular dark field (HAADF)-STEM image and EDX mappings of O, P, S, Co, and Nb elements for the SE-coated LiCoO2 electrodes are presented in Figure 5. A SE coating layer is observed between two LiCoO2 particles, where one particle has several cracks. The EDX mapping of Nb element reveals that a LiNbO3 coating layer exists on the surface of LiCoO2, but the layer is missing at the cracks. The EDX mappings of P and S elements indicate that SE penetrates into the cracks as a liquid electrolyte does. Favorable formability of sulfide SE is effective for forming good contacts with the surface of active materials and using active materials even at newly formed crystal faces with cracks.
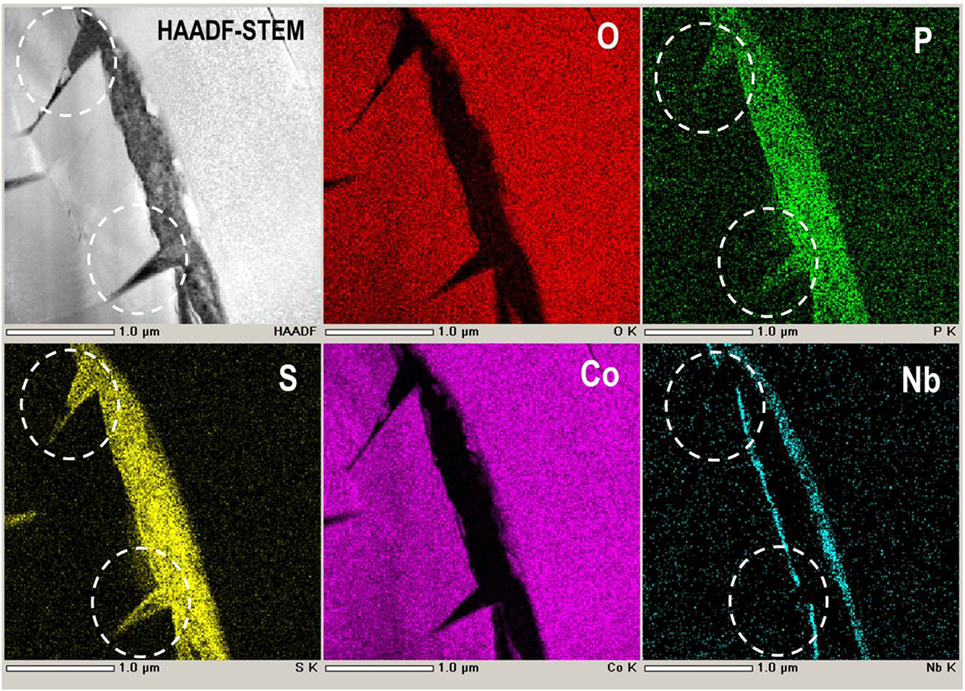
Figure 5. Cross-sectional high-angle annular dark field (HAADF)-TEM image and EDX mappings of O, P, S, Co, and Nb elements for the SE-coated LiCoO2 electrodes.
Solid electrolyte coatings were also done for graphite particles using PLD. The mixture of SE-coated graphite and SE particles was used as a negative electrode. The weight ratio of graphite and SE was 90/10. All-solid-state cells with Li2S–P2S5 SE as a separator layer were charged and discharged at a constant current density of 0.064 mA cm−2 (ca. 0.05 C) for voltages of 2.8–4.3 or 4.6 V at room temperature (Sakuda et al., 2013b). Figure 6 shows charge–discharge curves for all-solid-state SE-coated graphite/SE-coated LiCoO2 batteries. The battery with a cutoff voltage of 4.6 V at the charge process shows a higher discharge capacity than that of 4.3 V. Battery has a discharge capacity of 133 mAh g–1, as calculated from the total mass of the composite positive electrode.
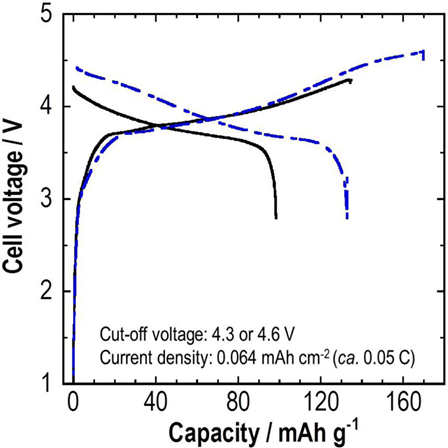
Figure 6. Initial charge–discharge curves for an all-solid-state SE-coated graphite/SE-coated LiCoO2 battery.
Figure 7 shows cross-sectional SEM images of SE-coated LiCoO2 positive electrodes; Figure 7A as-prepared, Figure 7B after the initial charge-discharge (cutoff voltage: 4.3 V), and Figure 7C after the initial charge–discharge (cutoff voltage: 4.6 V). Figures 7D–F, respectively, portray enlarged images of Figures 7A–C. Closely attached SE–LiCoO2 interfaces with large contact area are achieved by PLD coating, as shown in Figures 7A,D. The electrode morphology (Figure 7B) does not change greatly after the initial charge–discharge process at the cutoff of 4.3 V. SE coatings still attach on the LiCoO2 particles (Figure 7E), and empty spaces among particles observed in panel (Figure 7B) are similar to those observed in the as-prepared electrode (Figure 7A). Figure 7C shows that voids among LiCoO2 particles increase after the charge–discharge process at a higher cutoff voltage of 4.6 V. A LiCoO2 particle charged to 4.6 V suffers from deterioration. Many cracks are formed in the particle, as shown in the magnified image of panel (Figure 7F). This morphological change is attributable to (1) reduction of mechanical strength and (2) excess strain at the solid–solid interfaces among LiCoO2 particles during their large volume expansion and/or phase transition.
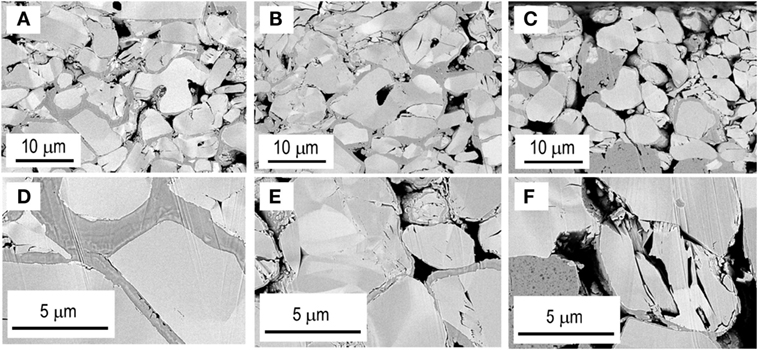
Figure 7. Cross-sectional SEM images of SE-coated LiCoO2 positive electrodes (A) as-prepared, (B) after the initial charge–discharge (cutoff voltage: 4.3 V), and (C) after the initial charge–discharge (cutoff voltage: 4.6 V). Images of (D–F), respectively, depict enlarged images of (A–C).
Figure 8 shows cross-sectional SEM images of SE-coated graphite negative electrodes; Figure 8A as-prepared and Figure 8B after the initial charge–discharge (cutoff voltage: 4.3 V). Graphite particles are close-packed in a negative electrode layer. SE coatings are observed around graphite particles. They form Li+ ion conduction paths through the electrode layer. After the initial charge–discharge, no obvious void is observed in the negative electrode. The close-packed electrode is present. Good solid–solid interfaces are also retained between the graphite layer and an electrolyte separator layer.
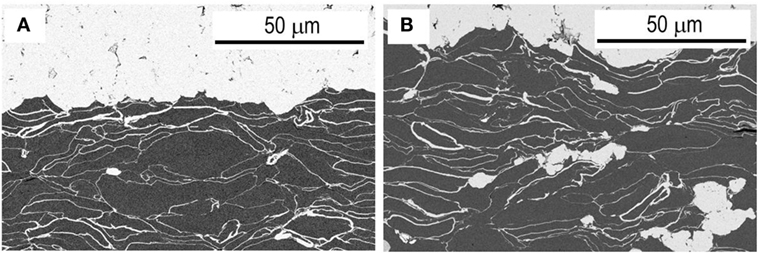
Figure 8. Cross-sectional SEM images of SE-coated graphite negative electrodes (A) as-prepared and (B) after the initial charge–discharge (cutoff voltage: 4.3 V).
As described in Section “Preparation Process,” liquid-phase synthesis of sulfide electrolytes is also useful for forming favorable electrode–electrolyte solid–solid interfaces, which can be achieved by removing solvents from electrolyte solutions. An all-solid-state cell using LiCoO2 coated with Li3PS4 electrolyte via an NMF solution operates as rechargeable batteries without the addition of SE and carbon-conductive additive particles to the positive electrodes (Teragawa et al., 2014a,b). However, the cell capacities are lower than those of the cells using LiCoO2 coated with Li3PS4 electrolytes by PLD, because the electrolytes synthesized via the liquid-phase has lower ionic conductivities than those prepared by PLD. The LiCoO2 particles coated with Li6PS5Cl electrolytes via ethanol solution with a higher conductivity than Li3PS4 were therefore applied to all-solid-state cells. The weight ratio of LiCoO2/SE layer was 92.5/7.5 in SE-coated LiCoO2 particles. An all-solid-state cell using the electrolyte-coated LiCoO2 shows an initial discharge capacity of 45mAh g−1, which is greater than that of cells using Li3PS4-coated LiCoO2 (Yubuchi et al., 2015b). SE coating via electrolyte liquids is a simple and cost-effective process. Increasing conductivity of SE at lower temperatures is necessary to improve battery performance.
Sulfur-Based Nanocomposite Positive Electrodes
Sulfur is a fascinating positive electrode with high energy density because it is an abundant resource with high theoretical capacity of 1672 mAh g−1 and environmental friendliness. Lithium polysulfides (Li2Sx), which are formed during discharge (lithiation process), are readily dissolved in organic liquid electrolytes, leading to lack of a sulfur positive electrode. Dissolution of lithium polysulfides is suppressed by absorbing sulfurs in nanocarbon pores. This approach has been studied extensively (Ji and Nazar, 2010). The use of inorganic SEs fundamentally resolves the problem.
Composite sulfur electrodes consisting of S, acetylene black (AB), and Li2S–P2S5 SE powders with a weight ratio of 25/25/50 were prepared using high-energy planetary ball milling to produce favorable contacts among the three components (Nagao et al., 2011). The Li-In/S cell exhibits a large reversible capacity of greater than 1500 mAh g−1 of sulfur with average potential of ca. 2.1 V (vs. Li+/Li). The cell with sulfur electrode shows 15 times higher capacity than the cell with LiCoO2, although the operating potential of the former cell is almost half that of the latter cell.
Application of Li2S as a discharge product of sulfur active material offers the important benefits of high theoretical capacity of 1167 mAh g−1 and versatility of negative electrode materials without lithium sources. Because of the insulative nature of Li2S, composite electrodes, Li2S mixed with conductive additives, such as nanocarbons and SEs, should be prepared for the use of Li2S as an active material. Composite Li2S electrodes were prepared by mechanical milling. A typical weight ratio of Li2S/AB/Li2S–P2S5 SE is 25/25/50. The prepared composite gives broad peaks attributable to Li2S in X-ray diffraction patterns. An all-solid-state cell of In/Li2S composites is charged and then discharged at 25°C. The initial reversible capacity is 800 mAh g−1 at the current density of 0.064 mA cm−2 (Nagao et al., 2012b). The cell retained 750 mAh g−1 for 10 cycles. Charge–discharge reaction mechanisms were examined using high-resolution TEM observation (Nagao et al., 2015). Figure 9 shows TEM images for the Li2S electrodes; Figure 9A before charge–discharge test, Figure 9B after the initial charge, and Figure 9C after the initial discharge. Figure 9A shows that nanoparticles of ca. 5 nm in size with different crystal orientations are distributed randomly in the matrix consisting of amorphous SE and AB. Those nanoparticles are attributable to crystalline Li2S. Figure 9B shows that no lattice fringes because of the crystalline Li2S are apparent, and there exists the characteristic contrast attributable to amorphous structure in the whole region after the initial charge process. As shown in Figure 9C, lattice fringes with spacing of about 3.9 Å are clearly apparent after the initial discharge, suggesting that amorphous sulfur is converted into crystalline nanoparticles during discharge reaction. Reversible transformation between crystallization and amorphization of sulfur-based active nanoparticles is responsible for the high capacity and its retention.
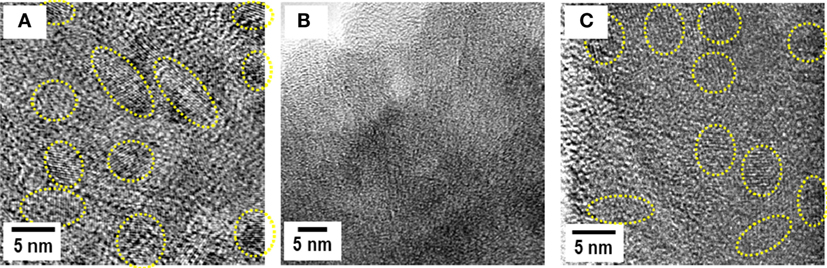
Figure 9. TEM images for the Li2S electrodes (A) before charge–discharge test, (B) after the initial charge, and (C) after the initial discharge.
The utilization of Li2S is ca. 50% in the composite electrode. To increase the utilization of Li2S, one strategy is the fundamental enhancement of ionic conductivity in Li2S. A partial substitution of more polarizable iodide anion with larger ionic radii for sulfide anion in Li2S is expected to increase conductivity by introducing lithium vacancies and by increasing the lattice constant. Solid solutions in the system Li2S-LiI are therefore prepared using mechanical milling (Hakari et al., 2015a). Only the XRD peaks attributable to Li2S are observed; LiI peaks disappear completely in the composition range of 0 < LiI (mol%) < 20. Figure 10A presents the composition dependence of lattice constant and conductivity at 25°C for the prepared Li2S-LiI materials. The lattice constant increases monotonically with increased LiI content, suggesting that Li2S-based solid solutions are prepared using a mechanical milling process. Conductivity is also enhanced by increasing the LiI content. The solid solution with 20 mol% LiI has conductivity of 2.2 × 10−6 S cm−1, which is two orders of magnitude higher than that for Li2S itself without the addition of LiI. A composite positive electrode with the 80Li2S⋅20LiI (mol%) solid solution, vapor-grown carbon fiber (VGCF), and Li3PS4 glass electrolyte with a weight ratio of 50/10/40 is applied to all-solid-state cells. Figure 10B shows that an all-solid-state cell (Li-In/Li3PS4/80Li2S⋅20LiI) is charged and discharged at a current density of 0.13 mA cm−2 (0.07 C) at 25°C. The cell shows a reversible capacity of 930 mAh g−1 for 50 cycles. The capacity corresponds to 80% utilization of Li2S. It is noteworthy that the enhancement of conductivity of Li2S is effective for increasing the utilization of the active material. This strategy is beneficial for the development of all-solid-state cells with a higher energy density.
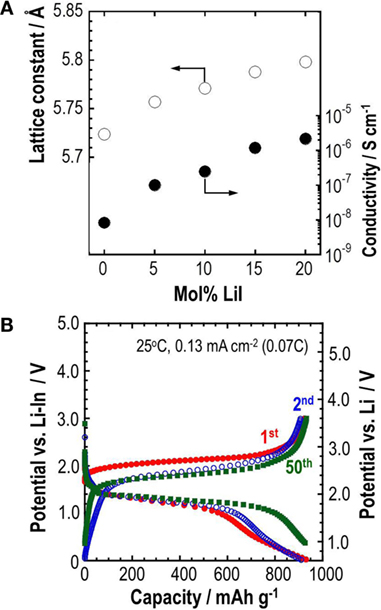
Figure 10. (A) Composition dependence of lattice constant and conductivity at 25°C for prepared Li2S-LiI solid solutions and (B) charge–discharge curves of an all-solid-state cell (Li-In/Li3PS4/80Li2S⋅20LiI).
A SE Li3PS4 is ball-milled with nanocarbon, such as AB. The prepared Li3PS4–AB materials as a mixed conductor are useful as positive electrode acting not only as a SE but also as an active material. An all-solid-state cell with the Li3PS4–AB composite positive electrode is charged and discharged. Its operation voltage of ca. 2.6 V vs. Li+/Li is somewhat higher than that of Li2S (Hakari et al., 2015b). Redox-active electrolytes, such as CuCl2-dissolved solution in porous carbons, are also reported to apply to supercapacitors (Mai et al., 2013). The use of the SEs as an active material in electrode layers is effective at increasing the reversible capacity per gram of the total mass of positive electrodes.
Transition Metal Sulfide Positive Electrodes
Typical MSx, such as TiS2, are used as active materials in all-solid-state Li and Na batteries with sulfide SEs. Decreasing the particle size of MSx and forming a wide contact area with both SEs and conductive additives are important for increasing the MSx utilization.
Monodispersed MSx nanoparticles are prepared using a so-called “hot-soap” technique using high-boiling point solvents as a reaction medium. Particle morphology and size can be controlled by choosing the reaction conditions and combinations of coordinating or non-coordinating solvents. NiS particles of 50 nm size were prepared using thermal decomposition of nickel acetylacetonate in a mixed solution of 1-dodecanethiol as a sulfur source and 1-octadecene as a non-coordinating solvent at 280°C for 5 h (Aso et al., 2011). The NiS nanoparticles are crystallized directly on a carbon fiber (VGCF) by adding VGCF to a liquid medium. Good adhesion between NiS and carbon is achieved (Aso et al., 2012). Sulfide electrolyte coating on NiS–VGCF was produced using the PLD method. All-solid-state cells with the prepared NiS composite electrode operate as a secondary battery at 25°C, suggesting that electron and Li+ ion conduction paths are formed in the composite electrodes (Aso et al., 2013).
To increase the positive electrode capacity, sulfur-rich MSx are desired. For example, titanium trisulfide TiS3 shows a higher capacity than that of TiS2, because additional sulfurs in TiS3 contribute to the redox reaction that occurs during charge–discharge processes (Hayashi et al., 2012a). Amorphous NbSx (x = 3, 4, 5) are prepared mechanochemically. Electrochemical cells with an organic liquid electrolyte using the amorphous NbSx (x = 3, 4, 5) show higher discharge capacities with an increase in the sulfur content of NbSx (Sakuda et al., 2014). Amorphous TiS3 (a-TiS3) retains a higher capacity than crystalline TiS3 in all-solid-state lithium cells. The crystal structure of TiS3 is partially deteriorated at the initial cycle, leading to an irreversible capacity in the cell with crystalline TiS3 (Matsuyama et al., 2016a,b). It is noteworthy that sulfur-rich amorphous MSx with electrical conductivity are promising for use as positive electrodes instead of sulfur active materials.
Figure 11A shows the first and tenth charge–discharge curves of all-solid-state lithium cell Li-In/a-TiS3 at 0.013 mA cm−2 at 25°C. The right side ordinate axis represents the electrode potential vs. Li+/Li, as calculated based on the potential difference between the Li-In and Li electrode (0.62 V). The cell with a-TiS3 positive electrode including no carbon-conductive additives and SEs shows a reversible capacity for 10 cycles of about 510 mAh g−1 of a-TiS3, which equals the weight of the total positive electrode. The capacity corresponds to storage of about 3M Li to a-TiS3. Electronic structural analyses using S2p XPS and S K-edge XANES reveal that a reversible sulfur redox in a-TiS3 appears mainly during charge–discharge processes and contributes to its good capacity retention (Matsuyama et al., 2016a,b).
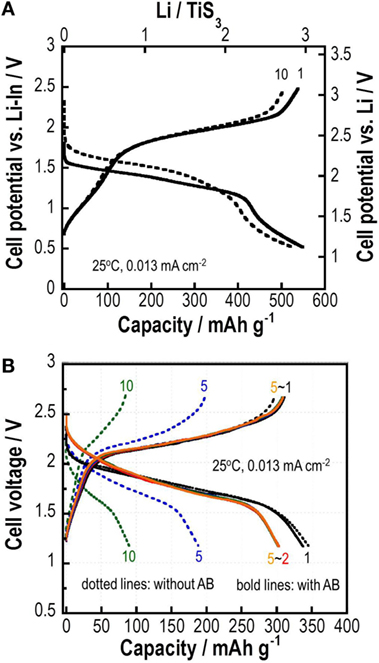
Figure 11. (A) Charge–discharge curves of all-solid-state lithium cell Li-In/amorphous TiS3 and (B) charge–discharge curves of all-solid-state sodium cell Na15Sn4/amorphous TiS3 with or without AB.
Amorphous TiS3 is also applicable to all-solid-state sodium batteries. An all-solid-state sodium cell using a-TiS3 shows capacity higher than 300 mAh g−1 at the first discharge process, as presented in Figure 11B (Tanibata et al., 2015a). The composite positive electrode consisting of a-TiS3 and the cubic Na3PS4 electrolyte with a weight ratio of 40/60 is used. Na15Sn4 alloy and the cubic Na3PS4 electrolyte are used, respectively, as a negative electrode and a separator layer. The cell capacity decreases gradually during discharge–charge cycles. SEM–EDX analysis reveals that the a-TiS3 particles aggregate after the cycles, and that resistance in the a-TiS3 composite electrode increases during cycles. To secure electron conduction paths to a-TiS3, 6 wt% AB is added to the positive electrode. Good capacity retention is achieved in the cell using a-TiS3 electrode with AB. The added AB particles might prevent the shutoff of electron conduction paths in the composite electrode and give a buffer space for the volume change of a-TiS3 particles for preserving adhesion among the particles. The addition of AB to the Na15Sn4 electrode also suppresses cell resistance after charge–discharge. In addition, the replacement of Na3PS4 glass–ceramic by 94Na3PS4⋅6Na4SiS4 (mol%) glass–ceramic with higher conductivity decreases cell resistance and increases the rate performance of all-solid-state cells (Tanibata et al., 2015b). Reversible capacity in all-solid-state Na cells is less than that in all-solid-state Li cells, as shown in Figures 11A,B. The lower conductivity of SEs and loss of particle contacts because of the larger volume change are responsible for a smaller capacity for the Na cells. Approaches that are used to prepare composite positive electrodes suitable for insertion/de-insertion of Na+ ion with larger ionic radius must be developed to improve battery performance in all-solid-state Na batteries.
Interface Modification for Li Metal Negative Electrode
To achieve high energy density of all-solid-state Li batteries, the final goal is the use of lithium metal as a negative electrode. Lithium metal is an ultimate negative electrode because of a large theoretical capacity of 3861 mAh g−1 and the lowest electrochemical potential of −3.04 V vs. SHE. However, a possibility of fatal problems emerged by short-circuit with dendrite formation prevent the practical use of Li metal negative electrode in lithium cells with conventional liquid and polymer electrolytes. Combination with inorganic SEs is expected to resolve the problem. In fact, thin-film solid-state batteries with Li negative electrode have excellent cycle life without capacity fading (Bates et al., 1993). The rate of utilization of Li electrodes is not high in thin-film batteries because positive electrodes such as LiCoO2 have lithium sources, which are mainly used for a charge–discharge process.
Compared with thin-film batteries fabricated by gas-phase deposition, insufficient Li–SE interfaces in bulk-type all-solid-state batteries prepared by cold pressing are important issues that must be resolved. It has been revealed by in situ SEM observation that lithium is deposited through grain boundaries and voids in the SE (Nagao et al., 2013). Insertion of a Li-alloy thin layer at the interface between the Li electrode and SE layers brought about stable Li dissolution and deposition in the all-solid-state Li metal cells (Hiratani et al., 1988; Okita et al., 2011; Nagao et al., 2012a). These interface modifications are effective at establishing homogeneous interfaces between the Li metal and SEs.
Intensive utilization of Li is important for achieving high energy density of all-solid-state lithium metal batteries. Insertion of a Au thin film at the Li–SE interface is effective for increasing Li utilization (Kato et al., 2016a). Li and Au thin films were formed on a pelletized Li3PS4 glass electrolyte by vacuum evaporation. Galvanostatic cycling tests for the Li/Li3PS4/Li cell are presented in Figure 12A. At the initial cycle, the utilization of Li metal is about 40%, which is a higher rate of utilization of Li metal for thin-film batteries (about 20%). However, utilization of Li metal for the cell decreases rapidly after five cycles. The Li thin-film morphology is rough after galvanostatic cycling tests, as shown in the SEM image (Figure 12C), indicating that inhomogeneous Li dissolution–deposition reactions occur. The cell Li/Au/Li3PS4/Au/Li has about 35% Li utilization at the initial cycle and retains about 25% after the fifth cycle, as presented in Figure 12B. The morphology of Li metal after Li dissolution–deposition reaction became more uniform, as shown in the SEM image of panel (Figure 12D), compared with the cell without Au thin films. The insertion of Au film to a Li–SE interface is a first step for improving the cyclability of Li deposition–dissolution reactions with high Li utilization in all-solid-state lithium metal batteries. Intensive studies are in progress.
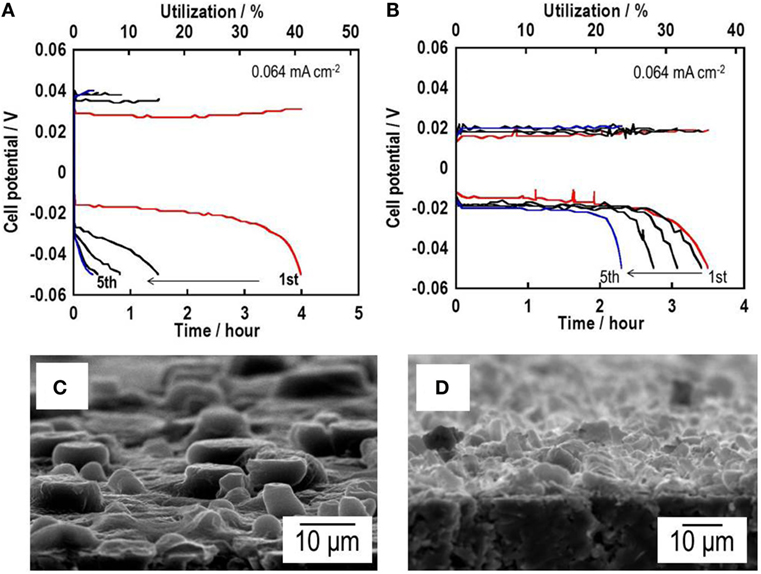
Figure 12. Galvanostatic cycling tests for (A) a Li symmetric Li/Li3PS4/Li cell and (B) a Li/Au/Li3PS4/Au/Li cell. SEM images of the surface of (C) a Li/Li3PS4/Li cell and (D) a Li/Au/Li3PS4/Au/Li cell after galvanostatic cycling tests.
Concluding Remarks
We have reviewed recent developments related to sulfide SEs and interface formation processes for all-solid-state rechargeable batteries. The conductivity of sulfide Li+ ion conductors, such as Li10GeP2S12, Li7P3S11, and Li9.54Si1.74P1.44S11.7Cl0.3, has already reached 10−2 S cm−1 at room temperature. Conductivities of sulfide Na+ ion conductors are lower than those of Li+ ion conductors at the present stage. The highest conductivity of 10−3 S cm−1 was obtained for Na3PSe4. Sulfide glass electrolytes with high alkali content were prepared by high-energy ball milling process. Metastable phases, such as Li7P3S11 and cubic Na3PS4, with high conductivity were formed by careful crystallization of the prepared glasses. Sulfide electrolytes can be synthesized via liquid-phase processing, which is useful for coating application. Sulfide glass electrolytes have favorable formability, and Young’s modulus for forming good electrode–electrolyte interfaces achieving rapid charge transfer in bulk-type all-solid-state batteries. Chemical stability in air is a great shortcoming of using a sulfide electrolyte. The composition of Li3PS4 has superior chemical stability in the Li2S–P2S5 binary system. The higher chemical stability is achieved by partial substitution of oxygen for sulfur. Selecting composition and designing structure for sulfide electrolytes is expected to improve conductivity, mechanical properties, and chemical stability further. As Na+ ion conductors, higher conductivity of more than 10−2 S cm−1 is predicted for Sn-substituted cubic Na3PS4, but the conductivity has not been achieved experimentally. Further studies seeking new electrolytes and suitable preparation processes must be undertaken.
Coating of SE and preparation of nanocomposites are useful for forming favorable solid–solid interface in an electrode layer for bulk-type all-solid-state batteries. Coating of sulfide electrolytes on LiCoO2 or graphite particles using gas-phase or liquid-phase techniques is effective for increasing solid–solid contact area using extremely small amounts of electrolytes. Preparation of nanocomposites using high-energy ball milling is useful for sulfur or Li2S active materials with an insulative nature. Conductivity enhancement of Li2S by combination with LiI contributes to the improvement of Li2S utilization. Amorphous MSx, such as amorphous TiS3, are attractive as mixed conductors with large capacity in all-solid-state batteries. Interface modification for Li metal negative electrode with Au thin film improves the cycle performance of Li dissolution–deposition while maintaining a high rate of utilization. For further improvement of electrochemical performance of the batteries, facile approaches achieving favorable electrode–electrolyte interfaces with large contact area will be developed. Controlling the size, morphology, and dispersibility of both electrolyte and electrode particles and selecting suitable electrolytes for maintaining close solid–solid contacts during charge–discharge processes will be assessed in future studies.
Author Contributions
AH contributed to the preparation of the manuscript. AS and MT contributed to the discussions about research results.
Conflict of Interest Statement
The authors declare that the research was conducted in the absence of any commercial or financial relationships that could be construed as a potential conflict of interest.
Acknowledgments
This research is supported by a Grant-in-Aid for Scientific Research from the Ministry of Education, Culture, Sports, Science and Technology (MEXT) of Japan. In particular, the research about all-solid-state Li batteries was financially supported by the Japan Science and Technology Agency (JST), Advanced Low Carbon Technology Research and Development Program (ALCA), Specially Promoted Research for Innovative Next Generation Batteries (SPRING) Project, while the research about all-solid-state Na batteries was supported by the MEXT program “Elements Strategy Initiative for Catalysts and Batteries (ESICB).”
References
Aotani, N., Iwamoto, K., Takada, K., and Kondo, S. (1994). Synthesis and electrochemical properties of lithium ion conductive glass, Li3PO4-Li2S-SiS2. Solid State Ionics. 68, 35–39. doi:10.1016/0167-2738(94)90232-1
Aso, K., Hayashi, A., and Tatsumisago, M. (2012). Synthesis of NiS-carbon fiber composites in high-boiling solvent to improve electrochemical performance in all-solid-state lithium secondary batteries. Electrochim. Acta 83, 448–453. doi:10.1016/j.electacta.2012.07.088
Aso, K., Kitaura, H., Hayashi, A., and Tatsumisago, M. (2011). Synthesis of nanosized nickel sulfide in high-boiling solvent for all-solid-state lithium secondary batteries. J. Mater. Chem. 21, 2987–2990. doi:10.1039/c0jm02639e
Aso, K., Sakuda, A., Hayashi, A., and Tatsumisago, M. (2013). All-solid-state lithium secondary batteries using NiS-carbon fiber composite electrodes coated with Li2S-P2S5 solid electrolytes by pulsed laser deposition. ACS Appl. Mater. Interfaces 5, 686–690. doi:10.1021/am302164e
Bates, J., Dudney, N., Gruzalski, G., Zuhr, R., Choudhury, A., and Luck, C. (1993). Fabrication and characterization of amorphous lithium electrolyte thin films and rechargeable thin-film batteries. J. Power Sources 4, 103–110. doi:10.1016/0378-7753(93)80106-Y
Boron, P., Johansson, S., Zick, K., Gunne, J., Dehnen, S., and Roling, B. (2013). Li10SnP2S12: an affordable lithium superionic conductor. J. Am. Chem. Soc. 135, 15694–15697. doi:10.1021/ja407393y
Boulineau, S., Courty, M., Tarascon, J. M., and Viallet, V. (2012). Mechanochemical synthesis of Li-argyrodite Li6PS5X (X=Cl, Br, I) as sulfur-based solid electrolytes for all solid state batteries application. Solid State Ionics. 221, 1–5. doi:10.1016/j.ssi.2012.06.008
Hakari, T., Hayashi, A., and Tatsumisago, M. (2015a). Highly utilized lithium sulfide active material by enhancing conductivity in all-solid-state batteries. Chem. Lett. 44, 1664–1666. doi:10.1246/cl.150758
Hakari, T., Nagao, M., Hayashi, A., and Tatsumisago, M. (2015b). All-solid-state lithium batteries with Li3PS4 glass as active material. J. Power Sources 293, 721–725. doi:10.1016/j.jpowsour.2015.05.073
Hayashi, A., Hama, S., Minami, T., and Tatsumisago, M. (2003). Formation of superionic crystals from mechanically milled Li2S-P2S5 glasses. Electrochem. Commun. 5, 111–114. doi:10.1016/S1388-2481(02)00555-6
Hayashi, A., Matsuyama, T., Sakuda, A., and Tatsumisago, M. (2012a). Amorphous titanium sulfide electrode for all-solid-state rechargeable lithium batteries with high capacity. Chem. Lett. 41, 886–888. doi:10.1246/cl.2012.886
Hayashi, A., Noi, K., Sakuda, A., and Tatsumisago, M. (2012b). Superionic glass-ceramic electrolytes for room-temperature rechargeable sodium batteries. Nat. Commun. 3, 1–5. doi:10.1038/ncomms1843
Hayashi, A., Muramatsu, H., Ohtomo, T., Hama, S., and Tatsumisago, M. (2013). Improvement of chemical stability of Li3PS4 glass electrolytes by adding MxOy (M=Fe, Zn, and Bi) nanoparticles. J. Mater. Chem. A 1, 6320–6326. doi:10.1039/c3ta10247e
Hiratani, M., Miyauchi, K., and Kudo, T. (1988). Effect of a lithium alloy layer inserted between a lithium anode and a solid electrolyte. Solid State Ionics. 2, 1406–1410. doi:10.1016/0167-2738(88)90394-3
Hori, S., Kato, M., Suzuki, K., Hirayama, M., Kato, Y., and Kanno, R. (2015). Phase diagram of the Li4GeS4-Li3PS4 quasi-binary system containing the superionic conductor Li10GeP2S12. J. Am. Ceram. Soc. 98, 3352–3360. doi:10.1111/jace.13694
Ito, S., Nakakita, M., Aihara, Y., Uehara, T., and Machida, N. (2014). A synthesis of crystalline Li7P3S11 solid electrolyte from 1, 2-dimethoxyethane solvent. J. Power Sources 271, 342–345. doi:10.1016/j.jpowsour.2014.08.024
Jansen, M., and Henseler, U. (1992). Synthesis, structure determination, and ionic conductivity of sodium tetrathiophosphate. J. Solid State Chem. 99, 110–119. doi:10.1016/0022-4596(92)90295-7
Ji, X., and Nazar, L. (2010). Advances in Li-S batteries. J. Mater. Chem. 20, 9821–9826. doi:10.1039/b925751a
Kamaya, N., Homma, K., Yamakawa, Y., Hirayama, M., Kanno, R., Yonemura, M., et al. (2011). A lithium superionic conductor. Nat. Mater 10, 682–686. doi:10.1038/nmat3066
Kato, A., Hayashi, A., and Tatsumisago, M. (2016a). Enhancing utilization of lithium metal electrodes in all-solid-state batteries by interface modification with gold thin films. J. Power Sources 309, 27–32. doi:10.1016/j.jpowsour.2016.01.068
Kato, Y., Hori, S., Saito, T., Suzuki, K., Hirayama, M., Mitsui, A., et al. (2016b). High-power all-solid-state batteries using sulfide superionic conductors. Nat. Energy 1, 16030. doi:10.1038/nenergy.2016.30
Liu, Z., Fu, W., Payzant, E., Yu, X., Wu, Z., Dudney, N., et al. (2013). Anomalous high ionic conductivity of nanoporous β-Li3PS4. J. Am. Chem. Soc. 135, 975–978. doi:10.1021/ja3110895
Mai, L. Q., Minhas-Khan, A., Tian, X., Hercule, K. M., Zhao, Y. L., Lin, X., et al. (2013). Synergistic interaction between redox-active electrolyte and binder-free functionalized carbon for ultrahigh supercapacitor performance. Nat. Commun. 4, 2923. doi:10.1038/ncomms3923
Matsuyama, T., Deguchi, M., Mitsuhara, K., Ohta, T., Mori, T., Orikasa, Y., et al. (2016a). Structure analyses using X-ray photoelectron spectroscopy and X-ray absorption near edge structure for amorphous MS3 (M: Ti, Mo) electrodes in all-solid-state lithium batteries. J. Power Sources 313, 104–111. doi:10.1016/j.jpowsour.2016.02.044
Matsuyama, T., Hayashi, A., Ozaki, T., Mori, S., and Tatsumisago, M. (2016b). Improved electrochemical performance of amorphous TiS3 electrodes compared to its crystal for all-solid-state rechargeable lithium batteries. J. Ceram. Soc. Jpn. 124, 242–246. doi:10.2109/jcersj2.15299
Minami, K., Hayashi, A., and Tatsumisago, M. (2010). Characterization of solid electrolytes prepared from Li2S-P2S5 glass and ionic liquids. J. Electrochem. Soc. 157, A1296–A1301. doi:10.1149/1.3489352
Minami, K., Hayashi, A., Ujiie, S., and Tatsumisago, M. (2011). Electrical and electrochemical properties of glass–ceramic electrolytes in the systems Li2S-P2S5-P2S3 and Li2S-P2S5-P2O5. Solid State Ionics. 192, 122–125. doi:10.1016/j.ssi.2010.06.018
Mizuno, F., Hayashi, A., Tadanaga, K., and Tatsumisago, M. (2005). New, highly ion-conductive crystals precipitated from Li2S-P2S5 glasses. Adv. Mater. 17, 918–921. doi:10.1002/adma.200401286
Mizuno, F., Hayashi, A., Tadanaga, K., and Tatsumisago, M. (2006). High lithium ion conducting glass-ceramics in the system Li2S-P2S5. Solid State Ionics. 177, 2721–2725. doi:10.1016/j.ssi.2006.04.017
Muramatsu, H., Hayashi, A., Ohtomo, T., Hama, S., and Tatsumisago, M. (2011). Structural change of Li2S-P2S5 sulfide solid electrolytes in the atmosphere. Solid State Ionics. 182, 116–119. doi:10.1016/j.ssi.2010.10.013
Nagao, M., Hayashi, A., and Tatsumisago, M. (2011). Sulfur-carbon composite electrode for all-solid-state Li/S battery with Li2S-P2S5 solid electrolyte. Electrochim. Acta 56, 6055–6059. doi:10.1016/j.electacta.2011.04.084
Nagao, M., Hayashi, A., and Tatsumisago, M. (2012a). Bulk-type lithium metal secondary battery with indium thin layer at interface between Li electrode and Li2S-P2S5 solid electrolyte. Electrochem. 80, 734–736. doi:10.5796/electrochemistry.80.734
Nagao, M., Hayashi, A., and Tatsumisago, M. (2012b). High-capacity Li2S-nanocarbon composite electrode for all-solid-state rechargeable lithium batteries. J. Mater. Chem 22, 10015–10020. doi:10.1039/c2jm16802b
Nagao, M., Hayashi, A., Tatsumisago, M., Ichinose, T., Ozaki, T., Togawa, Y., et al. (2015). Li2S nanocomposites underlying high-capacity and cycling stability in all-solid-state lithium-sulfur batteries. J. Power Sources 274, 471–476. doi:10.1016/j.jpowsour.2014.10.043
Nagao, M., Hayashi, A., Tatsumisago, M., Kanetsuku, T., Tsuda, T., and Kuwabata, S. (2013). In situ SEM study of a lithium deposition and dissolution mechanism in a bulk-type solid-state cell with a Li2S-P2S5 solid electrolyte. Phys. Chem. Chem. Phys. 15, 18600–18606. doi:10.1039/c3cp51059j
Nose, M., Kato, A., Sakuda, A., Hayashi, A., and Tatsumisago, M. (2015). Evaluation of mechanical properties of Na2S-P2S5 sulfide glass electrolytes. J. Mater. Chem. A 3, 22061–22065. doi:10.1039/C5TA05590C
Oh, D. Y., Nam, Y. J., Park, K. H., Jung, S. H., Cho, S. J., Kim, Y. K., et al. (2015). Excellent compatibility of solvate ionic liquids with sulfide solid electrolytes: toward favorable ionic contacts in bulk-type all-solid-state lithium-ion batteries. Adv. Energy Mater. 5, 1500865. doi:10.1002/aenm.201570120
Ohtomo, T., Hayashi, A., Tatsumisago, M., and Kawamoto, K. (2013a). Glass electrolytes with high ion conductivity and high chemical stability in the system LiI-Li2O-Li2S-P2S5. Electrochemistry 81, 428–431. doi:10.5796/electrochemistry.81.428
Ohtomo, T., Hayashi, A., Tatsumisago, M., and Kawamoto, K. (2013b). All-solid-state batteries with Li2O-Li2S-P2S5 glass electrolytes synthesized by two-step mechanical milling. J. Solid State Chem. 17, 2551–2557. doi:10.1007/s10008-013-2149-5
Ohtomo, T., Hayashi, A., Tatsumisago, M., and Kawamoto, K. (2013c). All-solid-state lithium secondary batteries using the 75Li2S·25P2S5 glass and the 70Li2S·30P2S5 glass-ceramic as solid electrolytes. J. Power Sources 233, 231–235. doi:10.1016/j.jpowsour.2013.01.090
Okita, K., Ikeda, K., Sano, H., Iriyama, Y., and Sakaebe, H. (2011). Stabilizing lithium plating-stripping reaction between a lithium phosphorus oxynitride glass electrolyte and copper thin film by platinum insertion. J. Power Sources 196, 2135–2142. doi:10.1016/j.jpowsour.2010.10.014
Phuc, N., Morikawa, K., Totani, M., Muto, H., and Matsuda, A. (2016). Chemical synthesis of Li3PS4 precursor suspension by liquid-phase shaking. Solid State Ionics. 285, 2–5. doi:10.1016/j.ssi.2015.11.019
Sahu, G., Lin, Z., Li, J., Liu, Z., Dudney, N., and Liang, C. (2014). Air-stable, high-conduction solid electrolytes of arsenic-substituted Li4SnS4. Energy Environ. Sci. 7, 1053–1058. doi:10.1039/C3EE43357A
Sakuda, A., Hayashi, A., Ohtomo, T., Hama, S., and Tatsumisago, M. (2010). LiCoO2 electrode particles coated with Li2S-P2S5 solid electrolyte for all-solid-state batteries. Electrochem. Solid-State Lett. 13, A73–A75. doi:10.1149/1.3376620
Sakuda, A., Hayashi, A., Ohtomo, T., Hama, S., and Tatsumisago, M. (2011). All-solid-state lithium secondary batteries using LiCoO2 particles with pulsed laser deposition coatings of Li2S-P2S5 solid electrolytes. J. Power Sources 196, 6735–6741. doi:10.1016/j.jpowsour.2010.10.103
Sakuda, A., Hayashi, A., Takigawa, Y., Higashi, K., and Tatsumisago, M. (2013a). Evaluation of elastic modulus of Li2S-P2S5 glassy solid electrolyte by ultrasonic sound velocity measurement and compression test. J. Ceram. Soc. Jpn. 121, 946–949. doi:10.2109/jcersj2.121.946
Sakuda, A., Hayashi, A., and Tatsumisago, M. (2013b). Sulfide solid electrolyte with favorable mechanical property for all-solid-state lithium battery. Sci. Rep. 3, 2261. doi:10.1038/srep02261
Sakuda, A., Taguchi, N., Takeuchi, T., Kobayashi, H., Sakaebe, H., Tatsumi, K., et al. (2014). Amorphous niobium sulfides as novel positive-electrode materials. ECS Electrochem. Lett. 3, A79–A81. doi:10.1149/2.0091407eel
Seino, Y., Ota, T., Takada, K., Hayashi, A., and Tatsumisago, M. (2014). A sulphide lithium super ion conductor is superior to liquid ion conductors for use in rechargeable batteries. Energy Environ. Sci. 7, 627–631. doi:10.1039/C3EE41655K
Souquet, J. L., Robinel, E., Barrau, B., and Ribes, M. (1981). Glass formation and ionic conduction in the M2S-GeS2 (M=Li, Na, Ag) systems. Solid State Ionics. 3-4, 317–321. doi:10.1016/0167-2738(81)90105-3
Takada, K. (2013). Progress and prospective of solid-state lithium batteries. Acta Mater. 61, 759–770. doi:10.1016/j.actamat.2012.10.034
Tanibata, N., Hayashi, A., and Tatsumisago, M. (2015a). Improvement of rate performance for all-solid-state Na15Sn4/amorphous TiS3 cells using 94Na3PS4·6Na4SiS4 glass-ceramic electrolytes. J. Electrochem. Soc. 162, A793–A795. doi:10.1149/2.0011506jes
Tanibata, N., Matsuyama, T., Hayashi, A., and Tatsumisago, M. (2015b). Improvement of rate performance for all-solid-state Na15Sn4/amorphous TiS3 cells using 94Na3PS4·6Na4SiS4 glass-ceramic electrolytes. J. Power Sources 275, 284–287. doi:10.1016/j.jpowsour.2014.10.193
Tanibata, N., Noi, K., Hayashi, A., Kitamura, N., Idemoto, Y., and Tatsumisago, M. (2014). X-ray crystal structure analysis of sodium-ion conductivity in 94Na3PS4·6Na4SiS4 glass-ceramic electrolytes. Chem. Electro. Chem. 1, 1130–1132. doi:10.1002/celc.201402016
Tatsumisago, M., and Hayashi, A. (2008). All-solid-state lithium secondary batteries using sulfide-based glass-ceramic electrolytes. Funct. Mater. Lett. 1, 31–36. doi:10.1142/S1793604708000071
Tatsumisago, M., and Hayashi, A. (2014). Sulfide glass-ceramic electrolytes for all-solid-state lithium and sodium batteries. Int. J. Appl. Glass. Sci. 5, 226–235. doi:10.1111/ijag.12084
Tatsumisago, M., Nagao, M., and Hayashi, A. (2013). Recent development of sulfide solid electrolytes and interfacial modification for all-solid-state rechargeable lithium batteries. J. Asian. Ceram. Soc. 1, 17–25. doi:10.1016/j.jascer.2013.03.005
Tatsumisago, M., Shinkuma, Y., and Minami, T. (1991). Stabilization of superionic α-AgI at room temperature in a glass matrix. Nature 354, 217–218. doi:10.1038/354217a0
Teragawa, S., Aso, K., Tadanaga, K., Hayashi, A., and Tatsumisago, M. (2014a). Liquid-phase synthesis of a Li3PS4 solid electrolyte using N-methylformamide for all-solid-state lithium batteries. J. Mater. Chem. A 2, 5095–5099. doi:10.1039/c3ta15090a
Teragawa, S., Aso, K., Tadanaga, K., Hayashi, A., and Tatsumisago, M. (2014b). Preparation of Li2S-P2S5 solid electrolyte from N-methylformamide solution and application for all-solid-state lithium battery. J. Power Sources 248, 939–942. doi:10.1016/j.jpowsour.2013.09.117
Ujiie, S., Hayashi, A., and Tatsumisago, M. (2014). Preparation and electrochemical characterization of (100-x)(0.7Li2S·0.3P2S5)·xLiBr glass-ceramic electrolytes. Mater. Renew. Sustain. Energy 3, 1–8. doi:10.1007/s40243-013-0018-x
Wada, H., Menetrier, M., Levasseur, A., and Hagenmuller, P. (1983). Preparation and ionic conductivity of new B2S3-Li2S-LiI glasses. Mater. Res. Bull. 18, 189–193. doi:10.1016/0025-5408(83)90080-6
Yabuchi, N., Kubota, K., Dahbi, M., and Komaba, S. (2015b). Research development on sodium-ion batteries. Chem. Rev. 114, 11636–11682. doi:10.1021/cr500192f
Yamauchi, A., Sakuda, A., Hayashi, A., and Tatsumisago, M. (2013). Preparation and ionic conductivities of (100-x)(0.75Li2S·0.25P2S5)·xLiBH4 glass electrolytes. J. Power Sources 244, 707–710. doi:10.1016/j.jpowsour.2012.12.001
Yubuchi, S., Hayashi, A., and Tatsumisago, M. (2015a). Sodium-ion conducting Na3PS4 electrolyte synthesized via a liquid-phase process using N-methylformamide. Chem. Lett. 44, 884–886. doi:10.1246/cl.150195
Yubuchi, S., Teragawa, S., Aso, K., Tadanaga, K., Hayashi, A., and Tatsumisago, M. (2015b). Preparation of high lithium-ion conducting Li6PS5Cl solid electrolyte from ethanol solution for all-solid-state lithium batteries. J. Power Sources 293, 941–945. doi:10.1016/j.jpowsour.2015.05.093
Zhang, L., Yang, K., Mi, J., Lu, L., Zhao, L., Wang, L., et al. (2015). Solid electrolytes: Na3PSe4: a novel chalcogenide solid electrolyte with high ionic conductivity. Adv. Energy Mater 5, 1501294. doi:10.1002/aenm.201501294
Zhang, Z., and Kennedy, J. H. (1990). Synthesis and characterization of the B2S3-Li2S, the P2S5-Li2S and the B2S3-P2S5-Li2S glass systems. Solid State Ionics. 38, 217–224. doi:10.1016/0167-2738(90)90424-P
Keywords: all-solid-state battery, lithium battery, sodium battery, sulfide, solid electrolyte, electrode–electrolyte interface
Citation: Hayashi A, Sakuda A and Tatsumisago M (2016) Development of Sulfide Solid Electrolytes and Interface Formation Processes for Bulk-Type All-Solid-State Li and Na Batteries. Front. Energy Res. 4:25. doi: 10.3389/fenrg.2016.00025
Received: 01 March 2016; Accepted: 16 June 2016;
Published: 15 July 2016
Edited by:
Shyue Ping Ong, University of California, San Diego, USACopyright: © 2016 Hayashi, Sakuda and Tatsumisago. This is an open-access article distributed under the terms of the Creative Commons Attribution License (CC BY). The use, distribution or reproduction in other forums is permitted, provided the original author(s) or licensor are credited and that the original publication in this journal is cited, in accordance with accepted academic practice. No use, distribution or reproduction is permitted which does not comply with these terms.
*Correspondence: Akitoshi Hayashi, aGF5YXNoaUBjaGVtLm9zYWthZnUtdS5hYy5qcA==