- 1Sustainable Materials Management, VITO, Mol, Belgium
- 2RECMIX bvba, Genk, Belgium
Mineral carbonation involves the capture and storage of carbon dioxide in carbonate minerals. Mineral carbonation presents opportunities for the recycling of steel slags and other alkaline residues that are currently landfilled. The Carbstone process was initially developed to transform non-hydraulic steel slags [stainless steel (SS) slag and basic oxygen furnace (BOF) slags] in high-quality construction materials. The process makes use of accelerated mineral carbonation by treating different types of steel slags with CO2 at elevated pressure (up to 2 MPa) and temperatures (20–140°C). For SS slags, raising the temperature from 20 to 140°C had a positive effect on the CO2 uptake, strength development, and the environmental properties (i.e., leaching of Cr and Mo) of the carbonated slag compacts. For BOF slags, raising the temperature was not beneficial for the carbonation process. Elevated CO2 pressure and CO2 concentration of the feed gas had a positive effect on the CO2 uptake and strength development for both types of steel slags. In addition, the compaction force had a positive effect on the strength development. The carbonates that are produced in situ during the carbonation reaction act as a binder, cementing the slag particles together. The carbonated compacts (Carbstones) have technical properties that are equivalent to conventional concrete products. An additional advantage is that the carbonated materials sequester 100–150 g CO2/kg slag. The technology was developed on lab scale by the optimization of process parameters with regard to compressive strength development, CO2 uptake, and environmental properties of the carbonated construction materials. The Carbstone technology was validated using (semi-)industrial equipment and process conditions.
Introduction
An estimated 170–250 Mt of steel slags were generated worldwide in 2014 (U.S. Geological Survey, 2015). The recycling of these slags provides a number of environmental benefits, including the preservation of natural resources, the recovery of valuable metals, and a reduction in the volume of solid waste. In Europe, about 76% of the steel slags generated in 2010 were recycled. The main application for these slags is as aggregate replacement in construction applications, e.g., as aggregate in asphalt and waterway embankment material. The use of these slag aggregates is, however, often hampered by their volumetric instability.
In Belgium, about 0.5 Mt of stainless steel (SS) slags are processed each year to recover the enclosed metal (Van Mechelen et al., 2011). These slags contain on average ~5% of SS. To recover the metal entrained in the slags, the slags are crushed or ground to a powder. After the metal recovery, about 70% of the slag can be recycled as coarse or fine aggregate; however, 25% of the slags occur as very fine grained powder (<0.5 mm) that is difficult to reuse without treatment due to elevated leaching of chromium and molybdenum. Solutions to reduce the volumetric instability of the slag aggregates and improve the environmental quality of the fine grained powder slags are therefore necessary.
The challenge is here to convert the very fine grained steel slag powder to a product with a positive economic value. To accomplish this, both the technical and environmental properties of the manufactured product need to comply with stringent product standards and environmental legislation. Several studies have indicated that the mechanical properties and leaching behavior of steel slags can be improved by (accelerated) mineral carbonation, which also allows to store CO2 in a solid and thermodynamically stable form (Johnson et al., 2003; Bertos et al., 2004; Baciocchi et al., 2010).
Natural mineral carbonation is the reaction between alkaline silicate minerals and atmospheric CO2. The Ca and/or Mg ions from silicate minerals dissolve and react with dissolved atmospheric CO2 to form solid carbonates. The overall exothermic dissolution–precipitation reaction can be written as
Natural carbonation processes are extremely slow but can be accelerated by increasing the surface area of the silicate minerals. The acceleration of the natural carbonation reaction to a timescale of minutes to a few hours usually also involves the use of concentrated CO2 at high pressures in the presence of moisture (e.g., Lim et al., 2010). Accelerated carbonation studies have mainly focused on maximizing the capture and storage of CO2 by optimizing pressure, temperature, liquid-to-solid (L/S) ratio, particle size, and other operating conditions (Costa et al., 2007; Huntzinger et al., 2009; Haug et al., 2010; Chang et al., 2011). An overview of various accelerated carbonation processes can be found in Sanna et al. (2014).
The Carbstone process is an accelerated carbonation process that has been developed for the recycling of non-hydraulic slags in high-quality construction products (Quaghebeur et al., 2009a, 2010). The process can provide a solution for the recycling of steel slags that are difficult to reuse today. One of the innovations of the technology is that it combines slag recycling with beneficial use of CO2 at elevated pressure and temperature. The carbonates that are produced during the reaction of CO2 with moist slag particles act as a binder cementing the slag particles together. The Carbstone blocks can therefore be produced without the use of traditional binders, e.g., Portland cement, and have the advantage of sequestering up to 150 g CO2/kg slag. The technology was developed on lab scale by optimization of the process parameters, such as pressure, temperature, and pretreatment of the raw material feed. The technology was then further developed and validated using (semi-)industrial equipment and process conditions. Both the technical and environmental properties of the construction materials were tested and optimized to comply with stringent environmental and technical requirements for building products.
In this study the following results are presented:
• the influence of shaping (compaction force applied during shaping), composition and grain size of the feed, CO2 pressure, and temperature on the compressive strength development of the building blocks;
• the influence of pressure and purity of the CO2 gas stream on the efficiency of the carbonation process;
• the technical and environmental quality (leaching behavior) of large building blocks produced by the accelerated carbonation process.
Materials and Methods
Raw Materials
The SS slag used in this study was a fine slag fraction produced by the company Recmix Belgium BVBA (located in Genk, Belgium), which results from the treatment of SS slag to recover the metal. The basic oxygen furnace (BOF) steel slags (fraction 0–3 mm) were provided by ArcelorMittal Gent (Gent, Belgium). Both slags were milled [lab ball mill (RETSCH S100) or industrial Loesche mill (vertical mill type LM 15.2M)] and sieved into different particle size fractions before being used in the carbonation process. The chemical composition of the slags was examined using ICP-AES after digestion of the samples with HF/HNO3/HCl. The particle size distribution was determined by laser diffraction using a Malvern Mastersizer X laser diffraction particle size analyzer. A polydisperse mode of analysis with air as dispersant and a particle refractive index of 1.4500 with an adsorption of 0.1 were chosen. The mineralogy was determined using X-ray diffraction (Philips X’Pert), equipped with a Cu anode X-ray tube operated at 40 kV and 35 mA and using an automatic divergence slit. Specimens were scanned from 2 to 120° (2θ), with a step size of 0.04° and a dwell time of 4 s per step. Rietveld analysis was performed using HighScore Plus software. An external silicium standard was used to determine the content of the amorphous phase(s).
Carbonation Process
The carbonation process developed to produce the carbonated construction materials consists of three main steps: (1) pretreatment of the slags, (2) shaping of the building blocks by hydraulic compaction, and (3) CO2 curing of the building block in an autoclave. A schematic overview of the process is given in Figure 1. The first step (pretreatment) involves the homogenization of the slag particles and mixing with the appropriate amount of water. For the results presented here, the moisture content of the non-carbonated feed material was 10 wt%. During the second step, the slag mixture was compacted using a hydraulic press at a compaction pressure between 75 and 609 kgf/cm2. The compacted samples were subsequently placed in an autoclave and carbonated for up to 16 h in a CO2 enriched atmosphere at a feed gas pressure of 0.5–10 MPa and a temperature between 20 and 140°C. The reactor was not flushed before introducing the feed gas. The CO2 concentration of the initial feed gas was either a pure CO2 gas or a CO2–N2 gas mixture to simulate the use of diluted CO2 streams. The CO2 concentration and pressure in the autoclave were held constant during the experiments by automatically replenishing the consumed CO2 gas with new CO2 gas.
The carbonation experiments were performed in an automated 3.25 or 104 L SS Premex autoclave. The autoclaves can be heated or cooled using a heating/cooling jacket (3000 W) controlled by a set of Eurotherm control units. The amount of CO2 delivered to the autoclave during the carbonation experiment was measured. The various process parameters were controlled and monitored using an Eurotherm Suite SCADA system. The CO2 uptake was automatically monitored as a function of time during each carbonation experiment. A detailed description of the method to monitor and measure the CO2 uptake is described by Quaghebeur et al. (2009b).
Characterization of the Slags and Carbonated Products
The technical properties of the carbonated blocks (100 mm × 100 mm × 250 mm) were tested by a certified laboratory using standard procedures developed for concrete paving blocks, i.e., compressive strength (NBN EN 772-1:2011), freeze-thaw resistance (NBN EN 1338, annex D), water absorption (NBN EN 1338, annex E), tensile splitting strength (NBN EN 1338, annex F), abrasion resistance (NBN EN 1338, annex G), and slip resistance (NBN EN 1338 annex I).
The leaching characteristics of the fresh and carbonated SS slag compacts were determined using a batch leaching test (EN 12457-4) on size reduced granular material (<10 mm), at a L/S ratio of 10 and 24 h contact time. To assess the environmental quality of the carbonated compacts with regard to the Dutch regulations for construction materials, the maximum availability test (NEN 7371) and static diffusion test (NEN 7375) (monolithic material, duration 64 days with renewal of solution) were carried out on the carbonated compacts.
Results and Discussion
Characterization of Raw Materials
Both slag types are rich in Ca (Table 1) and have a high alkalinity (pH > 12). The calculated maximum theoretical CO2 sequestration capacity based on the total Ca and Mg concentrations of the slags is ~460 g CO2/kg for the steel slags and 360 g CO2/kg for the BOF steel slags (with the amount of CO2 expressed as weight of the non-carbonated steel slag).
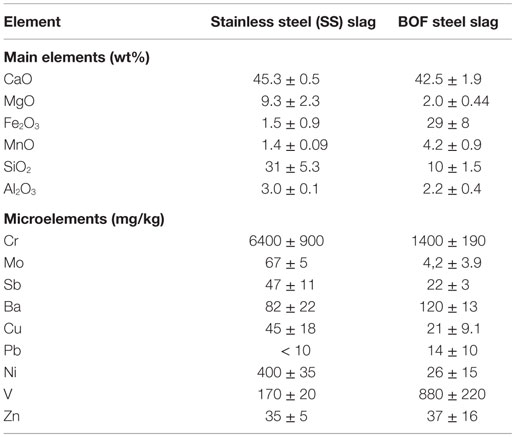
Table 1. Average chemical composition of the fresh slags used in the carbonation process (based on ICP-AES analysis).
The mineral phases of a representative fresh and non-carbonated steel slag sample were determined using XRD (Figure 2). The main minerals identified in the SS slag were merwinite [Ca3Mg(SiO4)2], bredigite [Ca7Mg(SiO4)4], gehlenite–akermanite [Ca2Al(Al,Si)O7–Ca2Mg(Si2O7)], cuspidine [Ca4(Si2O7)(F,OH)2], portlandite [Ca(OH)2], periclase (MgO), and donathite [(Fe,Mg)(Cr,Fe)2O4] (Table 2). The basic oxygen steel slag consisted mainly of amorphous Ca silicates, larnite (β-Ca2SiO4), portlandite [Ca(OH)2], srebrodolskite (Ca2Fe2O5), free lime (CaO), and wüstite (FeO) (Table 2).
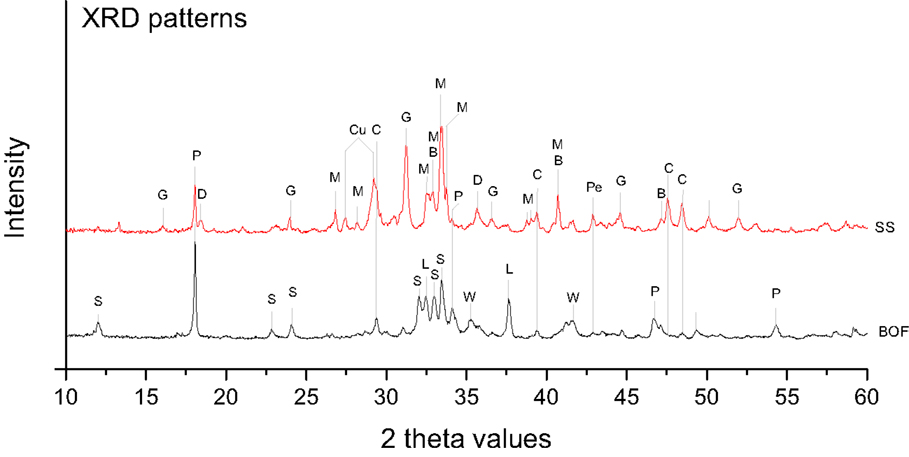
Figure 2. XRD patterns of the slags before accelerated carbonation. Abbreviations: B, bredigite; C, calcite; Cu, cuspidine; D, donathite; G, gehlenite; L, free lime; M, merwinite; P, portlandite; Pe, periclase; S, srebrodolskite; W, wüstite; SS, stainless steel slag; BOF, basic oxygen furnace slag.

Table 2. Average mineralogical composition of the fresh stainless steel slag and basic oxygen furnace slag (<125 μm) based on quantitative XRD analysis.
Carbonation Process
Various parameters that are known to affect the CO2 uptake during mineral carbonation, such as the operational conditions (temperature, pressure, and CO2 concentration), particle size, and mineralogy of the steel slags (e.g., Baciocchi et al., 2009; Baciocchi et al., 2015a) were examined.
Effect of Particle Size
The CO2 uptake can be enhanced by milling or grinding of the steel slags to smaller particle sizes (Figure 3). This is ascribed to the larger specific surface areas of the smaller slag particles. Based on the mineralogical composition of the different particle sizes of the slags before and after carbonation, it can be deduced that carbonation of slag particles <125 μm shows near complete conversion of free lime (CaO) to carbonate (or portlandite) under the applied reaction conditions, while the carbonation of larger particles (>125 μm) always displays persisting free lime (Figure 4). This is probably caused by the precipitation of carbonate minerals on the free lime particles forming a carbonate layer that hampers the access of fluids to the unreacted core of the free lime particles.
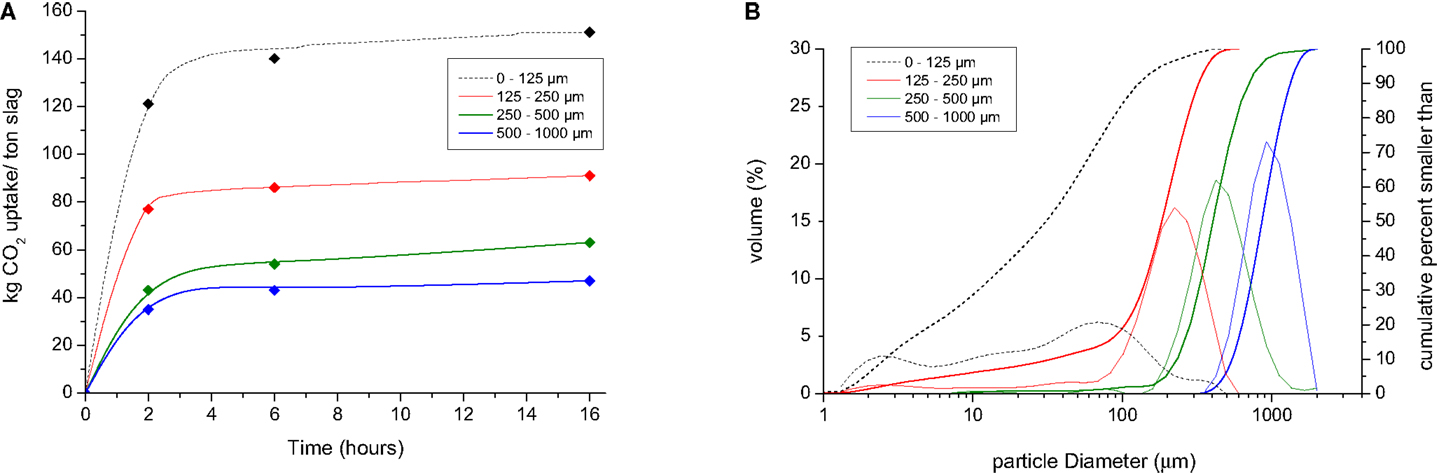
Figure 3. (A) CO2 uptake during carbonation of powders of stainless steel slag as a function of particle size (reaction conditions 2.0 MPa, 80°C) and (B) particle size distribution of the different powders.
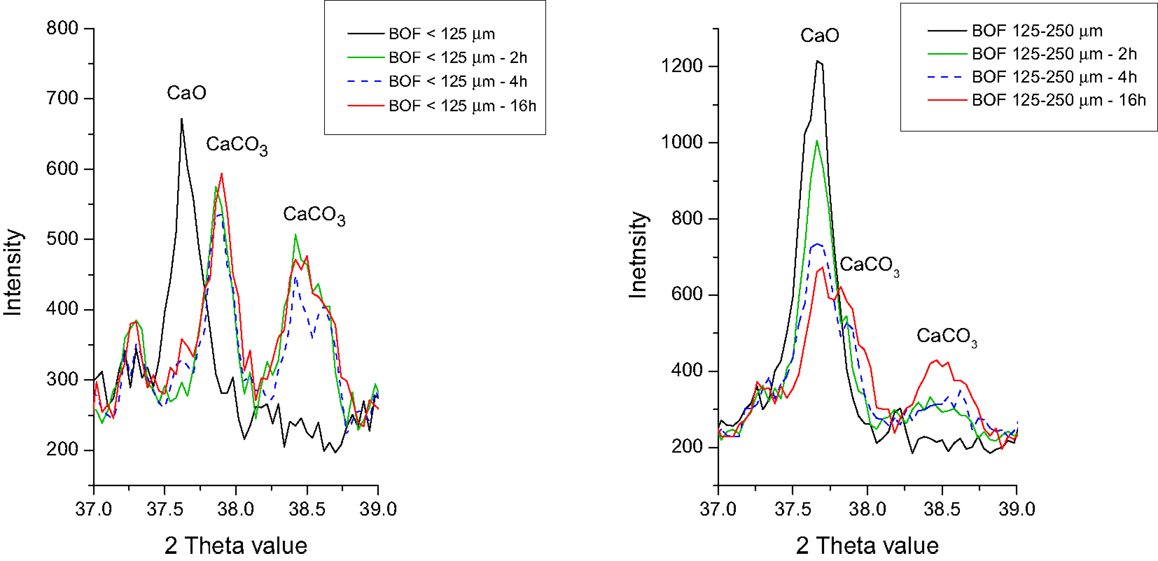
Figure 4. Excerpts of the XRD patterns of the BOF slag particles before and after 2 to 16 h of carbonation. Note the almost complete disappearance of CaO in the BOF particles <125 μm (left) and the persistence of CaO in the BOF particles >125 μm (right).
Effect of Temperature and Mineralogy
The effect of temperature is complex because raising the temperature can affect the carbonation reaction in wet and semi-wet conditions in different ways: (1) the solubility of carbon dioxide decreases with increasing temperature resulting in less CO2 available in solution for the carbonation reactions and (2) the solubility of calcium- and magnesium-bearing minerals may either increase or decrease with increasing temperature.
The solubility of silicates and most mineral groups increases with increasing temperature. For these minerals, an increase in temperature is more likely to have a positive effect on the carbonation reaction, although the increased temperature would lower the dissolution of CO2 in water. For the carbonation of serpentine and olivine, optimum temperatures of, respectively, 155 and 185°C have been reported (O’Connor et al., 2001). As the silicate minerals present in steel slags are less stable [e.g., amorphous phases and unstable (high-temperature) silicates], less energy-intensive carbonation conditions may be required for carbonation of these silicates.
The solubility of many carbonates and hydroxides [Ca(OH)2, Mg(OH)2] decreases with increasing temperature. These minerals have a retrograde solubility and are therefore thermodynamically more stable at elevated temperatures. For the carbonation of hydroxides, an increase in temperature may therefore have a negative effect, as demonstrated by Park et al. (2003). These authors reported Mg(OH)2 conversion rates of 90% in an hour at a temperature of 20°C, and when the temperature was increased to 90°C the conversion rate dropped to 32%. An optimum temperature for the carbonation reactions will thus clearly depend on the minerals involved.
For the carbonation of the BOF and SS slags, increasing the temperature had opposite effects with regard to the uptake of CO2 (Figure 5), which can be explained by their respective mineralogy [i.e., the BOF slag contains a large amount of Ca(OH)2 that can be carbonated while the SS slag mainly contains Ca–Mg silicates that can be carbonated]. In Figure 6, it can be seen that the dissolution of the silicates (merwinite, bredigite and cuspidine) increases significantly by increasing the temperature from 100 to 140°C for the SS slags. In Figure 7, it can be seen that raising the temperature leads to less conversion of portlandite for the BOF slags (probably due to the retrograde solubility of this mineral). This was also the case for portlandite present in the SS slags (not shown).
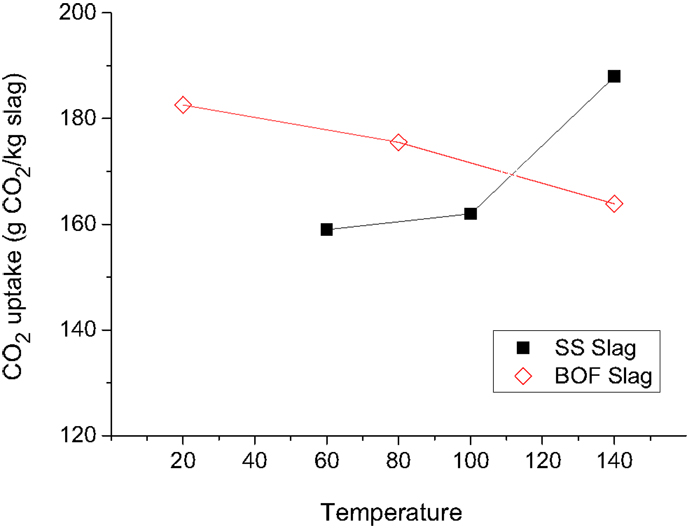
Figure 5. The CO2 uptake of BOF and SS slag particles as a function of temperature. The CO2 uptake is based on TC measurements and includes CO2 uptake prior to the accelerated carbonation experiments. The particles had a moisture content of 8% (BOF) and 12% (SS) and were carbonated at a feed pressure of 2.0 MPa with pure CO2 during 16 h. The grain size of both slags was comparable [SS slags with D(v,0.1) = 5 μm, D(v,0.5) = 40 μm, and D(v,0.9) = 190 μm and BOF slag with D(v,0.1) = 4 μm, D(v,0.5) = 60 μm, and D(v,0.9) = 160 μm].
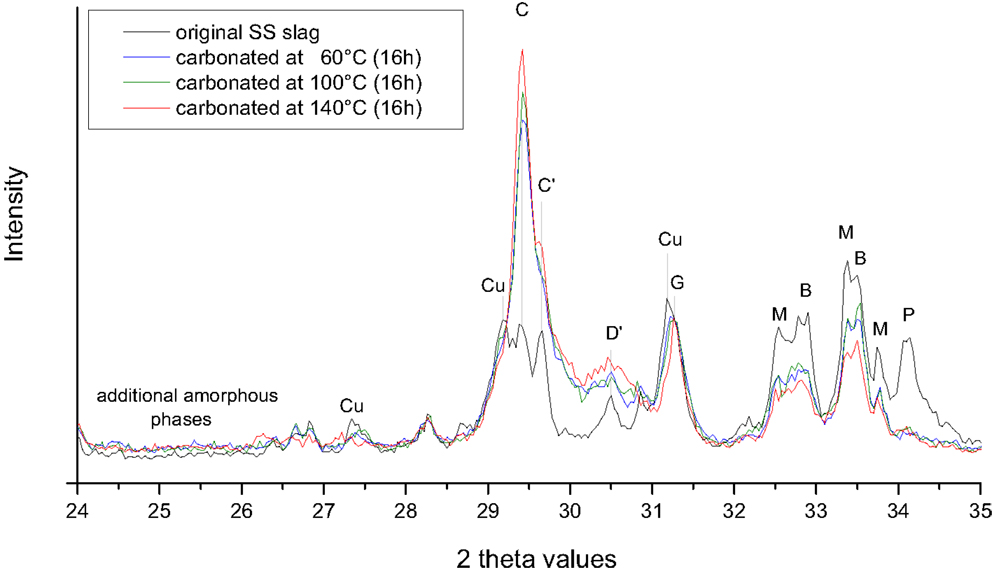
Figure 6. XRD patterns of the stainless steel slag particles before and after 16 h carbonation at a feed pressure of 2.0 MPa CO2, 12% moisture, and temperatures of 60, 100 and 140°C. Note the lower intensities of the diffraction peaks of the Ca–Mg silicates (merwinite and bredigite) carbonated at 140°C. Note also the increased background values between the 2θ values of 24 and 26, indicating an increase in amorphous phases after carbonation. Abbreviations: B, bredigite; C, calcite; C′, Mg calcite; D′, dolomite or protodolomite [CaMg(CO3)2]; Cu, cuspidine; G, gehlenite; M, merwinite; P, portlandite.
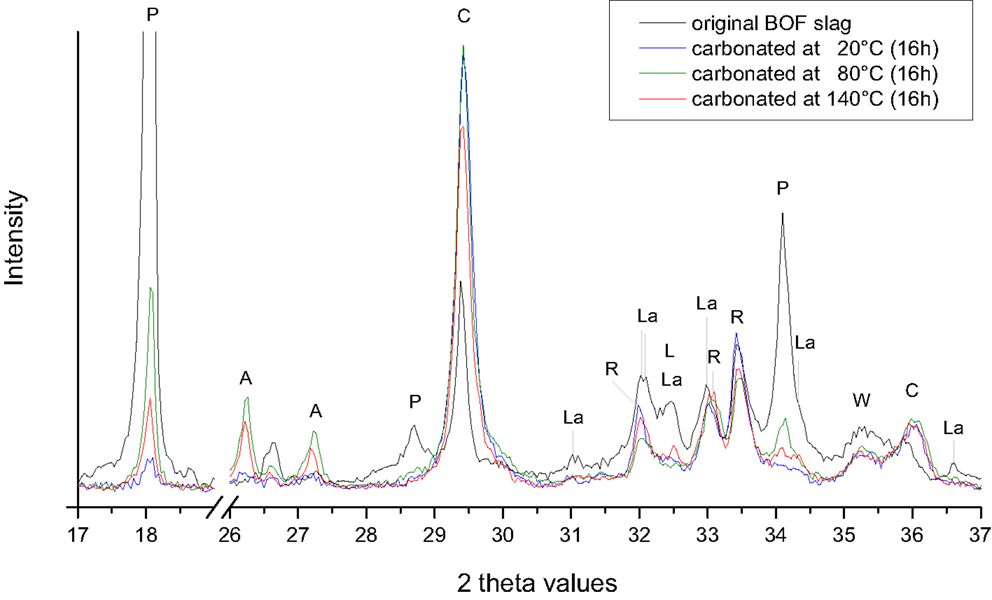
Figure 7. XRD patterns of the BOF slag particles before and after 16 h carbonation at a feed pressure of 2.0 MPa CO2, 8% moisture, and temperatures of 20, 80, and 140°C. Abbreviations: A, aragonite (CaCO3); C, calcite (CaCO3); L, free lime (CaO); La, larnite (β-Ca2SiO4); R, srebrodolskite (Ca2Fe2O5); W, wusite (FeO).
In addition, other carbonates may form during carbonation at higher temperatures. For the SS slags, an increase in calcite and Mg-bearing carbonates (Mg calcite and dolomite) is observed at 140°C (Figure 6). For the BOF slags, the formation of aragonite was observed when the carbonation temperature was raised to 80 and 140°C (Figure 7). The calcite content, however, decreased at the higher temperatures.
Carbonates as Binder
The objective of the carbonation process in this study is to produce construction materials using steel slags and CO2 as raw materials without the addition of hydraulic or pozzolanic binders. Strength is developed by the precipitation of carbonate minerals that bind the slag particles together and fill the porosity between the slag particles. This is here illustrated in Figure 8 where particles of BOF slag (no compaction was applied, hence the very large pores) are bonded by carbonate minerals during the carbonation process. In compacts, the carbonates form both around the slag particles as well as in pores in and between the slag particles, making it more difficult to observe the carbonation products. A detailed description of the effect of carbonation on the porosity of the compacts can be found in Boone et al. (2014). Boone et al. monitored the carbonation of SS slag compacts in real time using high-resolution X-ray computed microtomography. The authors showed that carbonates mainly precipitate at grain contacts and in capillary pores and that this precipitation has little effect on the connectivity of the pore spaces (Boone et al., 2014).
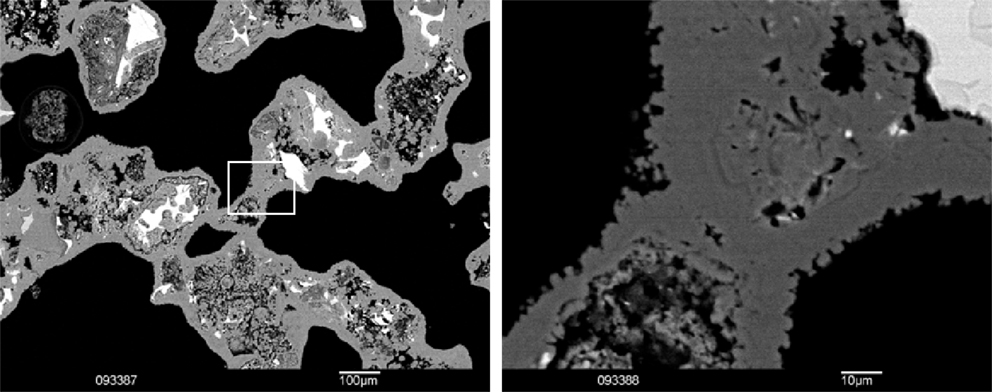
Figure 8. SEM backscatter electron image of carbonated loose (uncompacted) BOF slag particles. Note the carbonate (gray) cementing the loose slag particles together and forming a carbonate layer of about 10 μm thick around the slag particles. Right detail of white rectangular showing small calcite rhombohedra of ~1–3 μm in diameter. Black is pore between the slag particles.
The initial porosity of the compacts, this is the porosity prior to the carbonation step, is a function of the grain size distribution of the slag particles, and the compaction force applied during shaping of the compacts. The compaction force should be high enough to develop the necessary green strength to handle the compacts, yet low enough to maintain the required porosity to allow for CO2 and water diffusivity within the blocks during the carbonation process. The latter is important as it allows for continuous transport of reactants and keeps the carbonation process going. The diffusion of CO2 through the compact is typically controlled by the permeability, the pore network, the water content, as well as the applied total gas pressure.
To control the green strength and permeability of the compacts, sample preparation and process conditions should be adapted to avoid water saturation of the pores. The effect of compaction force and grain size distribution can be demonstrated by the reaction kinetics of the carbonation reaction (Figure 9), and the compressive strengths obtained for compacts made with different particle size distributions (Table 3). The results show that the reaction rate is significantly affected by the compaction force used during shaping of the compacts (cylinders of 10 mm diameter and ~40 mm height). For a compaction force of 75–389 kgf/cm2, a comparable CO2 uptake is achieved after 16 h of reaction (Figure 9). The compressive strength, however, increases from 12 MPa (75 kgf/cm2) to 31 MPa (389 kgf/cm2) as there is less pore space to be filled in the compacts made with higher compaction forces. The reaction rates are comparable for compaction forces of 75 and 150 kgf/cm2 while at higher compaction forces (389 and 609 kgf/cm2) the CO2 uptake rate is significantly slower (Figure 9). The compaction force of 609 kgf/cm2 resulted in a compact with a non-carbonated core after 16 h of reaction. The total CO2 uptake after 16 h was also significantly lower than for the compacts produced with lower compaction forces (Figure 9; Table 3). High compaction forces result in low porosity, which after a certain threshold impedes CO2 diffusion between particles and through the compact (Bertos et al., 2004).
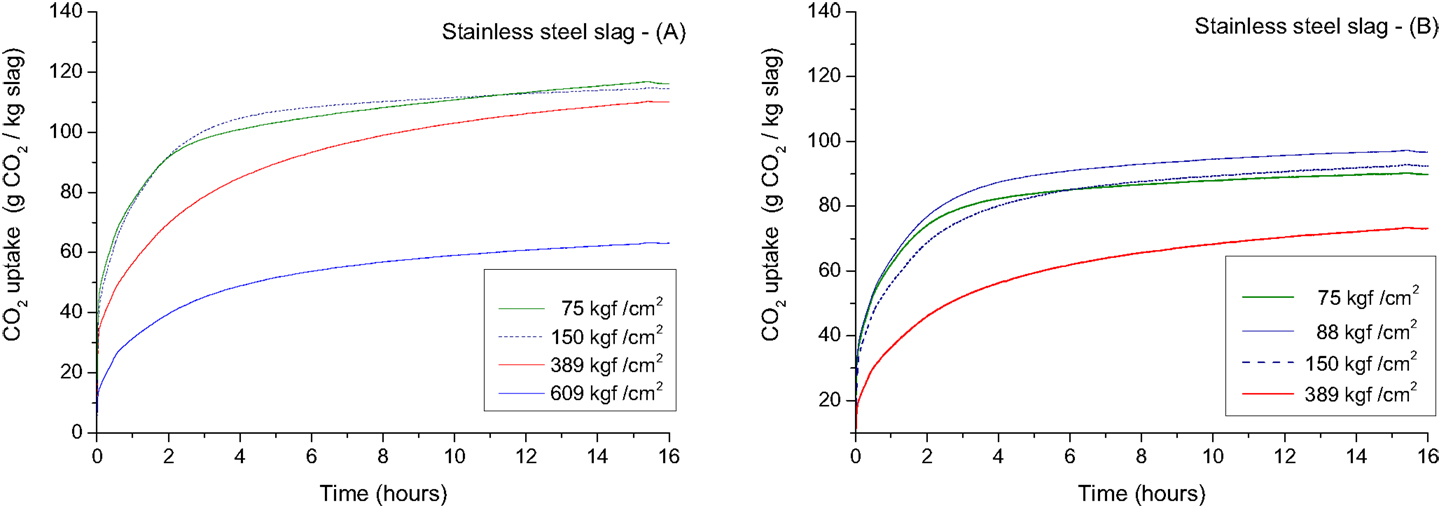
Figure 9. CO2 uptake as a function of time for compacted stainless steel slag compacts carbonated at 2.0 MPa with 100% CO2 at a temperature of 140°C. The particle size distribution of the slags used to make the compacts and the obtained compressive strengths of the respective compacts are given in Table 3.
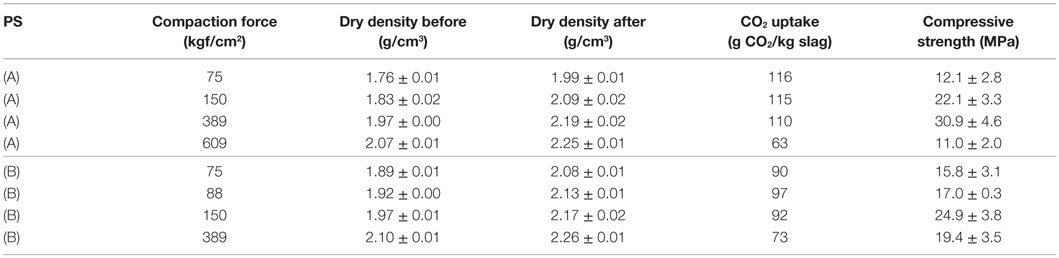
Table 3. CO2 uptake, bulk dry density, and compressive strengths of compacts in function of particle size (PS) and compaction force used to make the compacts (A) = 80% (0–2 mm) + 10% (2–8 mm) + 10% (8–16 mm), (B) = 60% (0–2 mm) + 20% (2–8 mm) + 20% (8–16 mm).
When compacts are fully carbonated, a clear linear correlation can be observed between the density of the compact before carbonation and the compressive strength after carbonation (Figure 10). However, when a compaction force of 600 kgf/cm2 was applied, the core of the compact was not fully carbonated, as a result the compressive strength was lower than anticipated based on the linear correlation (Figure 9). The compressive strength also correlates with the amount of carbonates formed during the carbonation process of the compacts (Figure 11).
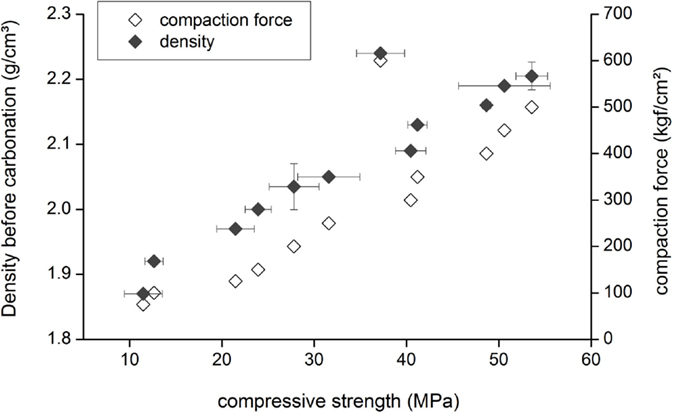
Figure 10. Graph showing the correlation between compaction force and density on the one hand and the compressive strength of carbonated BOF slag compacts on the other hand. The carbonation conditions were always the same, i.e., 20°C, 2.0 MPa pCO2, and a moisture content of 10 wt%. Horizontal and vertical error bars present 1 SD. The PSD of the BOF samples was: D(v,0.1) = 4 μm, D(v,0.5) = 35 μm, and D(v,0.9) = 120 μm for compacts made with compaction forces of 200–600 kgf/cm2 and D(v,0.1) = 10 μm, D(v,0.5) = 90 μm, and D(v,0.9) = 240 μm for compacts made with compaction forces of 75–200 kgf/cm2.
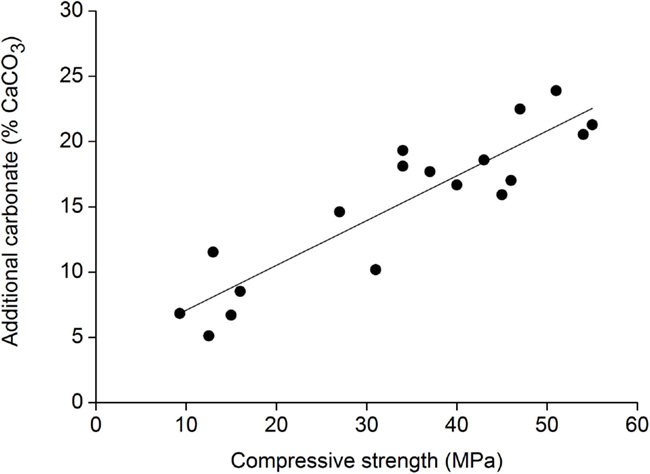
Figure 11. Correlation between carbonate formation and compressive strength development. Measurements are for stainless steel slag compacts exposed to different carbonation conditions.
The mineralogy of the slags determines their reactivity and also plays an important role in the compressive strength of the slag compacts. In Figure 12, this is demonstrated for the mainly silicate-based SS slags and the more (hydr)oxide-based BOF slags.
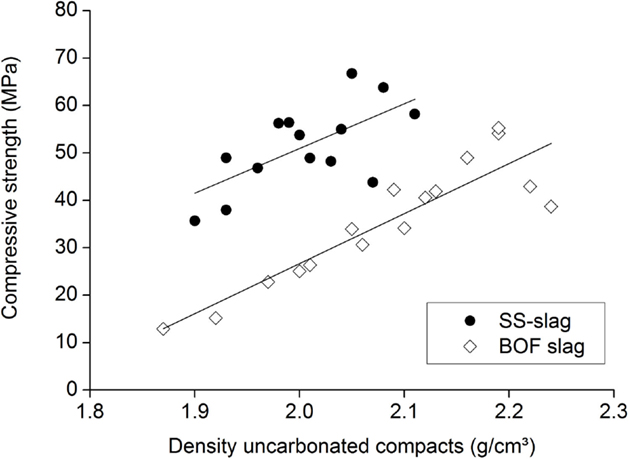
Figure 12. Compressive strengths for the BOF and SS slag compacts as a function of the density before carbonation.
Influence of the Feed Pressure and CO2 Composition
Higher CO2-feed gas pressures applied during the carbonation process resulted in higher CO2 uptakes (Figure 13) and higher compressive strengths of the carbonated compacts. Higher CO2 pressures significantly increase the solubility of CO2 in water (Takenouchi and Kennedy, 1964; Rosenbauer and Koksalan, 2002; Duan and Sun, 2003), which is beneficial for the carbonation reaction. Increasing the gas pressure will also cause CO2 and water to progressively penetrate smaller pores in the compact. Elevated CO2 pressure is, therefore, advantageous for the carbonation reaction and for the strength development of the carbonated materials. Elevated pressure, however, also results in higher production and investments costs making the process less attractive from an economic point of view. A moderate pressure of 2.0 MPa was, therefore, chosen as a standard pressure for further development of the carbonation process. The initial process development was done with pure CO2-feed gas. However, since flue gasses generally contain lower CO2 concentrations, and caption of CO2 is expensive and not yet integrated in existing processes, many companies are interested in finding a solution for using these dilute streams of CO2. Therefore, the impact of the CO2 concentration on the CO2-uptake rate and strength development was investigated. The results show that the CO2-uptake rate is lower when a less concentrated CO2 (20, 50, and 77%) atmosphere is present in the autoclave (Figure 14). The total CO2 uptake was, however, comparable. Longer process times are, therefore, needed when dilute CO2 streams are used to obtain carbonated blocks of comparable strength.
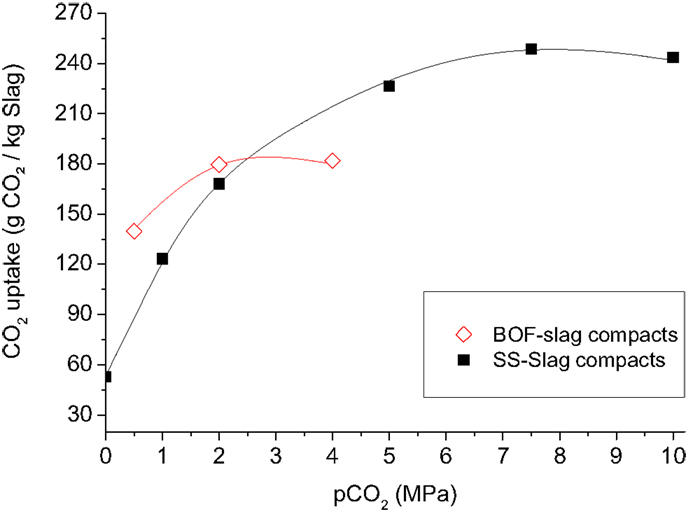
Figure 13. Influence of pCO2 pressure on the CO2 uptake of stainless steel slag and basic oxygen furnace slag compacts (compaction force 175 kgf/cm2) after 16 h of carbonation at a pCO2 of 2.0 MPa and a temperature of, respectively, 140°C and 80°C. The CO2 uptake is based on TC measurements and includes CO2 uptake prior to the accelerated carbonation experiments.
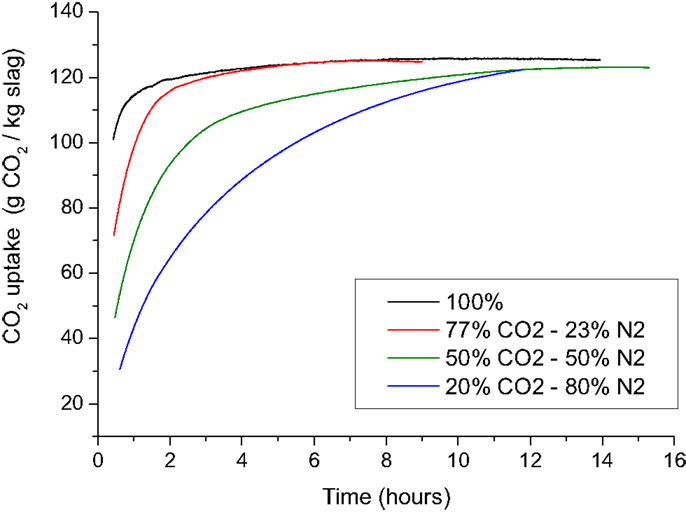
Figure 14. The CO2 uptake as a function of time for BOF slag compacts containing 10 wt% water and made with a compaction force of 175 kgf/cm2. The compacts were carbonated at 20°C at a pressure of 2.0 MPa in an atmosphere with a constant CO2 concentration of 20, 50, 77, or 100% CO2.
Technical and Environmental Quality of the Carbonated Compacts
After the lab scale optimization tests, larger compacts (300 mm × 100 mm × 50 mm) were made using (semi-)industrial equipment typically used in sand-lime brick plants. To evaluate if the carbonated blocks fulfill the requirements set for concrete paving blocks a series of technical tests (Table 4) were carried out. Each value is the average of at least 3 measurements made on different samples. For some of the tests subsamples were cut from the carbonated blocks. This was the case for the freeze-thaw resistance test, which was carried out on subsamples of 100 mm × 90 mm × 20 mm. The results of the freeze-thaw resistance tests are expressed as weight loss in kg/m2 after the test with de-icer salts. The abrasion resistance test was carried out on subsamples of 100 mm × 100 mm × 30 mm, and evaluated according to the deep abrasion resistance test using an abrasive disk.
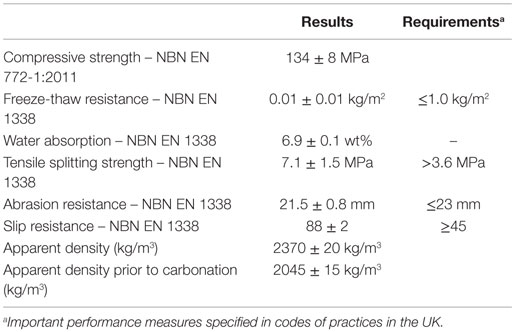
Table 4. Overview of the technical properties of carbonated stainless steel slag compacts, compared to requirements for concrete paving blocks.
An overview of the technical properties for the carbonated blocks made with SS slag containing 10 wt% water and compacted with a force of 300 kgf/cm2 (reaction conditions: 2.0 MPa pCO2 and 140°C during 16 h) is given in Table 4. Note that a compressive strength of more than 100 MPa was gained for these compacts after carbonation. The water absorption of 6.9 wt% is quite high compared to what is normally required from concrete. Water absorption of concrete is generally considered a measure for the resistance against carbonation and chloride migration. In the case of reinforced concrete, where carbonation and chloride migration may lead to corrosion of steel rebars, a low water absorption is important. For concrete paving blocks, however, water absorption is of minor importance, as long as the freeze-thaw resistance is good. The slip resistance is a measure of the coefficient of friction (or resistance to slip accidents) of flooring surfaces. The higher this value is the better, i.e., less chance of slipping. A slip resistance above 75 is considered extremely good, between 40 and 74 good, between 20 and 39 moderate, and below 19 high (guidelines recommended by the UK Slip resistance group, issue 2, RAPRA 2000).
The environmental quality was evaluated by leaching of the fresh and carbonated SS material using a batch leaching test (EN 12457-4) for granular material (<10 mm). Here, only the leaching of the potentially hazardous Cr and Mo was investigated, which are present in substantial amounts in SS slags (Proctor et al., 2000; Huijgen et al., 2005) and have been identified as critical elements in SS slag leaching (Huijgen and Comans, 2006). The leaching of these elements could be reduced by carbonation at higher temperatures (Figure 15). A reduction of the leaching of potentially hazardous heavy metals following the carbonation of steel slags has often been attributed to pH effects (Baciocchi et al., 2015b). The pH of the carbonated compacts that were exposed to different carbonation temperatures is, however, more or less comparable. The effect on the leachability can thus not be explained by pH effects only. Because the tests are performed on size reduced material the reduced leaching is more likely a chemical stabilization than a physical immobilization process. This chemical stabilization can possibly be linked to the development and the composition of the amorphous silica layers surrounding the reacting slag particles. It has been noted that under certain conditions these amorphous silica phases are affected (reduced) by restructuring/condensation processes, resulting in a densification of the structure and a closure of pores in the leached layers. This restructuring/condensation process may be enhanced by increased temperatures, and the accompanying structural changes may actually improve chemical bonding of certain metal cations such as Cr and Mo (Mollah et al., 1993) and may be responsible for a better immobilization of these metals.
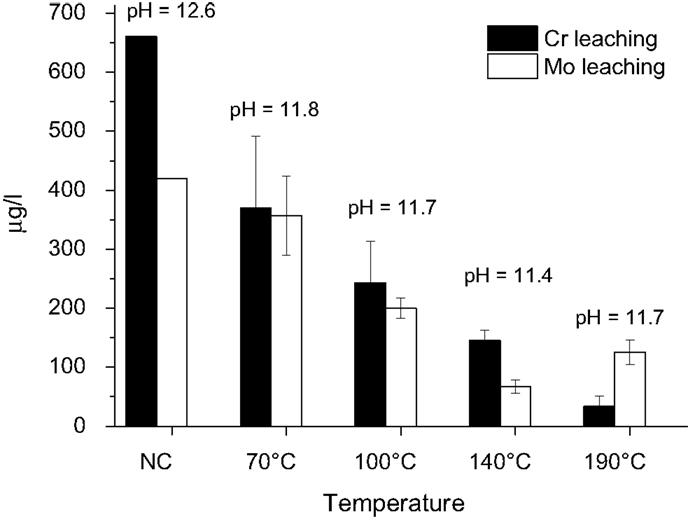
Figure 15. Batch leaching of size reduced (<10 mm) stainless steel slag compacts carbonated at a feed pressure of 2 MPa with pure CO2, 12% moisture content, and temperatures from 70 to 190°C. The error bars present 1 SD.
To assess the environmental quality, the leaching properties of the carbonated blocks were also tested using a maximum availability test (NEN 7371, 2004) and a diffusion test (NEN 7375, 2004). The leaching values are given in Table 5 and compared to the Dutch limit values for monolithic building materials. The leaching concentrations all comply with the limit values of the Dutch Soil Quality decree (Soil Quality Decree of the Netherlands, 2007).
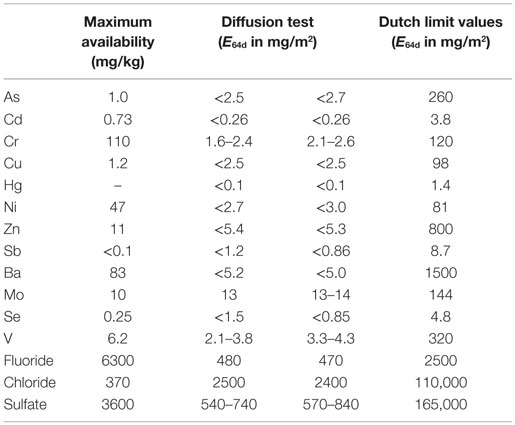
Table 5. Leaching values of the carbonated stainless steel slag compacts (maximum availability test and static diffusion test) compared to the Dutch leaching limit values for monolithic construction materials.
Conclusion
A carbonation process has been developed for the production of construction materials using slags and CO2 as raw materials without the need for any additional binder. The process operates at moderate pressure (2.0 MPa) and temperature and makes use of a unique combination of existing technologies commonly used in the construction industry. The process can be geared to make construction materials with different technical qualifications. A compressive strength of more than 100 MPa can be obtained. The carbonated blocks show good technical and environmental properties making them suitable to be used as high-quality construction materials. Understanding the factors that influence the strength development of the materials during carbonation is needed to have a flexible process with regard to product design. The compositions of raw materials, grain size distribution, shaping of materials using different compaction forces and pCO2 during carbonation all have a large influence on the carbonation rate and strength development of the carbonated materials. The purity of the CO2 gas streams used has little effect on the final strength that can be obtained, but the CO2 uptake rate will be lower when less concentrated CO2 is used.
Author Contributions
MQ and PN steered and conducted the research and were involved in the writing of this article. LH was involved in the upscaling and follow-up of lab experiments. DM was involved in the steering of research.
Conflict of Interest Statement
The authors declare that the research was conducted in the absence of any commercial or financial relationships that could be construed as a potential conflict of interest.
Acknowledgments
The authors would like to acknowledge financial support from IWT grant 100621 “CarbMAX: production of high-strength materials with mineral residues and CO2.” Bo Peeraer, Warre Van Dun, Raymond Kemps, and Myrjam Mertens are acknowledged for carrying out lab experiments, SEM and XRD analyses.
References
Baciocchi, R., Costa, G., and Bartolomeo, D. (2010). Carbonation of stainless steel slag as a process for CO2 storage and slag valorization. Waste Biomass Valorization 1, 467–477. doi: 10.1007/s12649-010-9047-1
Baciocchi, R., Costa, G., Di Gianfilippo, M., Polettini, A., Pomi, R., and Stramazzo, A. (2015a). Thin-film versus slurry-phase carbonation of steel slag: CO2 uptake and effects on mineralogy. J. Hazard. Mater. 283, 302–313. doi:10.1016/j.jhazmat.2014.09.016
Baciocchi, R., Costa, G., Polettini, A., and Pomi, R. (2015b). Effects of thin-film accelerated carbonation on steel slag leaching. J. Hazard. Mater. 286, 369–378. doi:10.1016/j.jhazmat.2014.12.059
Baciocchi, R., Costa, G., Polettini, A., and Pomi, R. (2009). Influence of particle size on the carbonation of stainless steel slag for CO2 storage. Energy Proc. 1, 4859–4866. doi:10.1016/j.egypro.2009.02.314
Bertos, M. F., Simons, S. J. R., Hills, C. D., and Carey, P. J. (2004). A review of accelerated carbonation technology in the treatment of cement-based materials and sequestration of CO2. J. Hazard. Mater. B 112, 193–205. doi:10.1016/j.jhazmat.2004.04.019
Boone, M. A., Nielsen, P., De Kock, T., Boone, M. N., Quaghebeur, M., and Cnudde, V. (2014). Monitoring of stainless-steel slag carbonation using X-ray computed microtomography. Environ. Sci. Technol. 48, 674–680. doi:10.1021/es402767q
Chang, E. E., Pan, S. Y., Chen, Y. H., Chu, H. W., and Chiang, P. C. (2011). CO2 sequestration by carbonation of steelmaking slags in an autoclave reactor. J. Hazard. Mater. 195, 107–114. doi:10.1016/j.jhazmat.2011.08.006
Costa, I., Baciocchi, R., Polettini, A., Pomi, R., Hills, C. D., and Carey, P. J. (2007). Current status and perspectives of accelerated carbonation processes on municipal waste combustion residues. Environ. Monit. Assess. 135, 55–75. doi:10.1007/s10661-007-9704-4
Duan, Z. H., and Sun, R. (2003). An improved model calculating CO2 solubility in pure water and aqueous NaCl solutions from 273 to 533 K and from 0 to 2000 bar. Chem. Geol. 193, 257–271. doi:10.1016/S0009-2541(02)00263-2
Haug, T. A., Kleiv, R. A., and Munz, I. A. (2010). Investigating dissolution of mechanically activated olivine for carbonation purposes. Appl. Geochem. 25, 1547–1563. doi:10.1016/j.apgeochem.2010.08.005
Huijgen, W. J. J., and Comans, R. N. J. (2006). Carbonation of steel slag for CO2 sequestration: leaching of products and reaction mechanisms. Environ. Sci. Technol. 40, 2790–2796. doi:10.1021/es052534b
Huijgen, W. J. J., Witkamp, G. J., and Comans, R. N. J. (2005). Mineral CO2 sequestration by steel slag carbonation. Environ. Sci. Technol. 39, 9676–9682. doi:10.1021/es050795f
Huntzinger, D. N., Gierke, J. S., Kawatra, S. K., Eisele, T. C., and Sutter, L. L. (2009). Carbon dioxide sequestration in cement kiln dust through mineral carbonation. Environ. Sci. Technol. 43, 1986–1992. doi:10.1021/es802910z
Johnson, D. C., Macload, C. L., Carey, P. J., and Hills, C. D. (2003). Solidification of stainless steel slag by accelerated carbonation. Environ. Technol. 24, 671–678. doi:10.1080/09593330309385602
Lim, M., Han, G. C., Ahn, J. W., and You, K. S. (2010). Environmental remediation and conversion of carbon dioxide (CO2) into useful green products by accelerated carbonation technology. Int. J. Environ. Res. Public Health 7, 203–228. doi:10.3390/ijerph7010203
Mollah, M., Hess, T. R., Tsai, Y., and Cocke, D. L. (1993). An FTIR and XPS investigations of the effects of carbonation on the solidifications/stabilization of cement based systems-Portland type V with zinc. Cem. Concr. Res. 23, 773–784. doi:10.1016/0008-8846(93)90031-4
NEN 7371. (2004). Leaching Characteristics – Determination of the Availability of Inorganic Components for Leaching – Solid Earthy and Stony Materials. Netherlands: Dutch Normalisation Institute (NEN) in Delft.
NEN 7375. (2004). Leaching Characteristics – Determination of the Leaching of Inorganic Components from Shaped and Monolithic Material with the Diffusion Test – Solid Earthy and Stony Materials. Netherlands: Dutch Normalisation Institute (NEN) in Delft.
O’Connor, W. K., Dahlin, D. C., Dahlin, C. L., and Collins, W. K. (2001). “Carbon dioxide sequestration by direct mineral carbonation: process mineralogy of feed and products,” in Society of Mining Engineers Annual Meeting and Exhibit, Denver, Colorado, 8. Available from: http://www.osti.gov/scitech/servlets/purl/897114/
Park, A. A., Jadhav, R., and Fan, L.-S. (2003). CO2 mineral sequestration: chemically enhanced aqueous carbonation of serpentine. Can. J. Chem. Eng. 81, 885–890. doi:10.1002/cjce.5450810373
Proctor, D. M., Fehling, K. A., Shay, E. C., Wittenborn, J. L., Green, J. J., Avent, C., et al. (2000). Physical and chemical characteristics of blast furnace, basic oxygen furnace, and electric arc furnace steel industry slags. Environ. Sci. Technol. 34, 1576–1582. doi:10.1021/es9906002
Quaghebeur, M., Laenen, B., and Nielsen, P. (2009a). Production of a Mainly Carbonate Bonded Article by Carbonation of Alkaline Materials. Patent WO2009/1331202.
Quaghebeur, M., Nielsen, P., and Laenen, B. (2009b). “Accelerated carbonation to improve quality of recycling methods: a study of the real time kinetics,” in Proc. of the 7th Int. Waste Conference (WASCON) (Lyon), 14–15.
Quaghebeur, M., Nielsen, P., Laenen, B., Nguyen, E., and Van Mechelen, D. (2010). Carbstone: sustainable valorisation technology for fine grained steel slags and CO2. Refract. Worldforum 2, 75–79.
Rosenbauer, R. J., and Koksalan, T. (2002). “Experimental determination of the solubility of CO2 in electrolytes: application to CO2 sequestration in deep-saline aquifers (abs.),” in Geological Society of America Annual Meeting, Denver, Abstracts with Programs (Boulder: The Geological Society of America), Vol. 24, No. 6, 304. Available from: https://gsa.confex.com/gsa/2002AM/finalprogram/abstract_40939.htm
Sanna, A., Uibu, M., Caramanna, G., Kuusik, R., and Maroto-Valer, M. M. (2014). A review of mineral carbonation technologies to sequester CO2. Chem. Soc. Rev. 2004, 8049–8080. doi:10.1039/c4cs00035h
Soil Quality Decree of the Netherlands. (2007). (Regeling bodemkwaliteit) Staatscourant (Netherlands: The Department of Justice of the Netherlands), Vol. 247, 67. Available from: https://zoek.officielebekendmakingen.nl/stb-2007-469
Takenouchi, S., and Kennedy, G. C. (1964). The binary system H2O-CO2 at high temperatures and pressures. Am. J. Sci. 262, 1055–1074. doi:10.2475/ajs.262.9.1055
U.S. Geological Survey. (2015). Mineral Commodity Summaries 2015. Reston, VA: U.S. Geological Survey, 196.
Keywords: accelerated carbonation, steel slag recycling, sustainable building materials, CO2 sequestration, carbonation technology
Citation: Quaghebeur M, Nielsen P, Horckmans L and Van Mechelen D (2015) Accelerated Carbonation of Steel Slag Compacts: Development of High-Strength Construction Materials. Front. Energy Res. 3:52. doi: 10.3389/fenrg.2015.00052
Received: 02 October 2015; Accepted: 30 November 2015;
Published: 17 December 2015
Edited by:
Renato Baciocchi, University of Rome Tor Vergata, ItalyReviewed by:
Xuezhong He, Norwegian University of Science and Technology, NorwayMai Uibu, Tallinn University of Technology, Estonia
Copyright: © 2015 Quaghebeur, Nielsen, Horckmans and Van Mechelen. This is an open-access article distributed under the terms of the Creative Commons Attribution License (CC BY). The use, distribution or reproduction in other forums is permitted, provided the original author(s) or licensor are credited and that the original publication in this journal is cited, in accordance with accepted academic practice. No use, distribution or reproduction is permitted which does not comply with these terms.
*Correspondence: Peter Nielsen, cGV0ZXIubmllbHNlbkB2aXRvLmJl