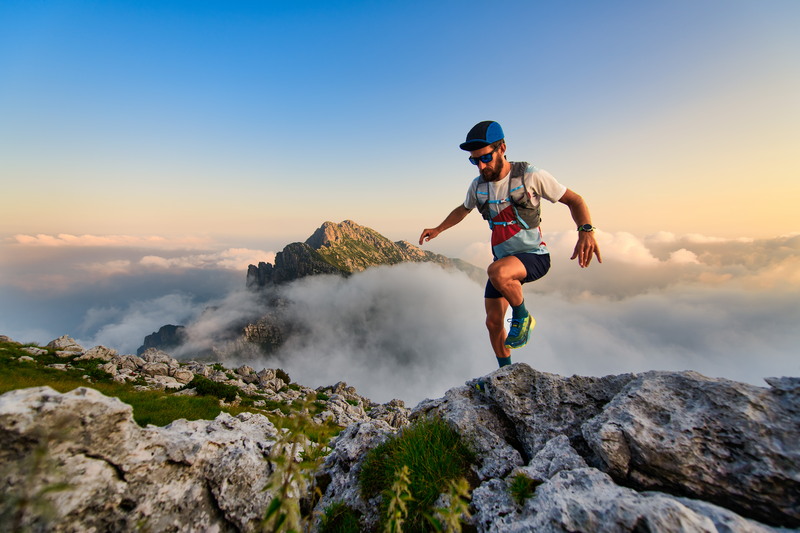
94% of researchers rate our articles as excellent or good
Learn more about the work of our research integrity team to safeguard the quality of each article we publish.
Find out more
ORIGINAL RESEARCH article
Front. Energy Res. , 27 April 2015
Sec. Bioenergy and Biofuels
Volume 3 - 2015 | https://doi.org/10.3389/fenrg.2015.00016
Poplar NE222 (Populus deltoides Bartr. ex Marsh × P. nigra L.) wood chips were pretreated in a 390 L pilot-scale rotating wood-pulping digester using a dilute sulfite solution of approximately pH 1.8 at 160°C for 40 min for bioconversion to ethanol and lignosulfonate (LS). An estimated combined hydrolysis factor (CHF) of 3.3 was used to scale the sulfite pretreatment temperature and time from laboratory bench scale experiments, which balanced sugar yield and inhibitor formation to facilitate high titer ethanol production through fermentation using S. cerevisiae YRH400 without detoxification. A terminal ethanol titer of 43.6 g L-1 with a yield of 247 L tonne wood-1 was achieved at total solids loading of 20%. The relatively low ethanol yield compared with yield from Sulfite pretreatment to overcome the recalcitrance of lignocelluloses (SPORL)-pretreated softwoods was due to inefficient utilization of xylose. The LS from SPORL has a substantially higher phenolic group (Ph-OH) content, though it was less sulfonated and had a lower molecular weight than a purified commercial softwood LS, and therefore has potential for certain commercial markets and future novel applications through further processing. The conversion efficiency achieved through process integration and simplification, demonstrated here, has significant importance to the entire supply chain of biofuel production from woody biomass.
Biomass from short rotation woody crops has been considered a viable feedstock for producing biofuels and bioproducts using the forest biorefinery concept to reduce our reliance on fossil fuel, mitigate climate change, and stimulate rural economic development (Zhu and Pan, 2010; Zalesny et al., 2011). Poplar woods can grow on marginal lands to conserve water, recycle nutrients, and sequester carbon (Vance et al., 2010) and therefore are especially attractive as a feedstock. Many efforts, from transgenic plant and plantation research (Zalesny et al., 2012; Acker et al., 2014), to pretreatment (Wyman et al., 2009; Wang et al., 2012), engineering microorganism for xylose fermentation (Ho et al., 1998; Jeffries and Jin, 2004; Wei et al., 2013), and economic analysis (Littlewood et al., 2014) have been made for efficient bioconversion of poplar woods. However, achieving high titer biofuel production from poplar woods remains a challenge; because, the chemical pretreatment step required for removing the recalcitrance of poplars for efficient enzymatic saccharification often produces inhibitors that cause difficulties in downstream processing. Unlike softwoods, the cell wall of poplar woods are highly acetylated (Gille and Pauly, 2012) to result in high concentration of acetic acid in the pretreatment hydrolyzate to substantially inhibit yeast fermentation (Palmqvist and Hahn-Hagerdal, 2000; Klinke et al., 2004; Tian et al., 2011). The compounding inhibition effect of acetic acid with furans and aromatics (Palmqvist et al., 1999) made fermentative cellulosic ethanol production from poplar woods more challenging than from softwoods. Reported studies were limited to using washed solids alone or at low solid loadings when pretreatment hydrolyzate (spent liquor) was used to avoid fermentation difficulties without detoxification (Zhu et al., 2011; Kim et al., 2013; Kundu et al., 2014).
Sulfite pretreatment to overcome the recalcitrance of lignocelluloses (SPORL) (Zhu et al., 2009) has demonstrated robust performance for high titer and high yield ethanol production from softwood biomass without detoxification (Zhou et al., 2013b, 2015; Zhu et al., 2015). Building upon the success of SPORL, we demonstrated SPORL optimization for bioconversion of a poplar wood in laboratory bench scale (1 L) experiments using a combined hydrolysis factor (CHF) to control pretreatment severity at CHF ≈ 2, which allowed us to successfully achieve high titer (>40 g L−1) ethanol production without detoxification using an engineered Saccharomyces cerevisiae (Zhang et al., 2015). The objectives of the present study were to: (1) demonstrate SPORL at a pilot scale for high titer ethanol production from poplar NE222 without detoxification, (2) further validate the approach of using CHF to optimize high titer ethanol production from poplars, and (3) analyze the properties of lignosulfonate (LS) as a potential lignin coproduct. The goal of the study is to demonstrate an efficient conversion system with respect to optimizing pretreatment and simplifying downstream processing, important to the entire supply chain of bioethanol production from woody biomass.
Logs of poplar NE222 (Populus deltoides Bartr. ex Marsh × P. nigra L.) were harvested from Hugo Sauer Nursery in Rhinelander, WI, USA, and provided by the Institute for Applied Ecosystem Studies of the USDA Forest Service Northern Research Station. The logs were hand-debarked and then chipped at USDA Forest Products Laboratory, Madison, WI, USA. The screen-accepted wood chips ranged from 6 to 38 mm in length and 1 to 5 mm in thickness. The chips were kept frozen at −16°C until used. The chemical composition of the wood chips is listed in Table 1.
Table 1. Wood component recoveries from pilot-scale SPORL pretreatment of poplar NE222 along with the chemical composition of the untreated NE222.
Folin Ciocalteau’s phenol reagent (2 N), vanillin, sodium acetate, acetic acid, sodium bisulfite, and sulfuric acid in ACS reagent grade were purchased from Sigma–Aldrich (St. Louis, MO, USA). High purity sodium LS (D-748) from acid sulfite pulping of softwoods was donated by LignoTech USA (Rothschild, WI, USA).
Commercial cellulase enzymes Cellic® CTec3 (abbreviated CTec3) was complimentary provided by Novozymes North America (Franklinton, NC, USA). The calibrated filter paper activity of CTec3 was 217 FPU mL-1 (Wood and Bhat, 1988).
Saccharomyces cerevisiae YRH400 was engineered for xylose fermentation (Hector et al., 2011) and provided by USDA Agricultural Research Service, National Center for Agriculture Utilization Research, Peoria, IL, USA. The strain was first grown on YPD agar plates and then cultured in a liquid YPD medium in a flask overnight on a shaking bed incubator (Thermo Fisher Scientific, Model 4450, Waltham, MA, USA) as described previously (Zhou et al., 2014a). The concentration of the cultured biomass was monitored by measuring the optical density at 600 nm (OD600nm) using a UV-Vis spectrometer (Model 8453, UV-visible spectroscopy system, Agilent Technologies, Palo Alto, CA, USA).
Many issues need to be taken into consideration in lignocellulose biomass pretreatment process scale-up. For example, whether or not the optimal pretreatment conditions obtained at laboratory scale be applicable at the pilot-scale? Furthermore, one also needs to consider the productivity of lignin coproduct for improving process economics. In the pulp and paper industry, the H-factor (Vroom, 1957), i.e., the integration of temperature over time, or thermal energy input, is used for controlling alkaline pulping for delignification. Similarly, we developed a CHF that can be used to describe hemicellulose yield XR (or dissolution) (Zhu et al., 2012) during pretreatment.
where CA and CB are the concentrations of chemical A (sulfuric acid) and chemical B (sodium bisulfite) used in the present study, respectively. R = 8.314 J mole-1 K-1 is the universal gas content, t is in min, T is absolute temperature (K). For poplar NE222 (Zhang et al., 2015), the adjustable parameters are α = 34.5, β = 18.6 (L mole-1), and γ = -9.7 (L mole-1), the apparent activation energy is E = 126,200 J mole-1, the initial fraction of slow reacting hemicelluloses is θ = 0.178, and the ratio of the hydrolysis reaction rate constant between the slow and fast hemicelluloses is f = 0.0784. The utility of CHF is that it can provide reasonably good predictions of sugar yield during subsequent enzymatic hydrolysis (Zhu et al., 2012; Zhang et al., 2015). This is because xylan dissolution that can be accurately predicted by CHF, dictates substrate enzymatic saccharification for lignocelluloses with low lignin content such as hardwoods and herbaceous biomass (Yang and Wyman, 2004; Moxley et al., 2012; Zhu et al., 2012; Leu and Zhu, 2013; Zhang et al., 2013).
In our previous laboratory study using the same NE222 wood chips (Zhang et al., 2015), we demonstrated that optimal sugar yield can be obtained when achieving complete dissolution of fast xylan, i.e., XR = θ, corresponding to CHF = 3.1. We recommended using a lower CHF ≈ 2 to balance sugar yield with inhibitor formation. Good ethanol yield, however, was achieved up to CHF = 2.7. Fermentation was viable even at CHF = 3.5 with a reduction in ethanol yield of approximately 25% compared with that at CHF ≈ 2.0. Based on these guidelines, we targeted a maximum threshold CHF = 2.7 for pretreatment at the pilot scale. We conducted SPORL using the same liquor to wood ratio of 3:1 (L kg-1) and sulfuric acid concentration of 2 mL L-1, but with a slightly lower sodium bisulfite charge on wood of 3.0 wt%, and at a high temperature of 160°C to reduce pretreatment duration. Based on Eq. 1, the required pretreatment time was t = 45 min.
NE222 wood chips, weighing 81.9 kg with moisture content of 50.1% (40.87 kg OD weight), were pretreated in the 390 L stainless steel (317), steam jacketed pilot-scale wood-pulping digester. The pretreatment sulfite liquor was made up in 81.5 L of city water using 1.226 kg of sodium bisulfite and 0.45 kg of sulfuric acid. The digester was placed under a vacuum to approximately 635 mm mercury after the chips were loaded. The liquor was then completely injected into the bottom of the digester using atmospheric pressure and appropriate plumbing connections. The digester was then rotated at 2 rpm to provide mixing while being heated by steam in the outer jacket. The temperature of the digester reached 160°C in 30 min (ramping time) and then maintained for 40 min. The effective pretreatment time was estimated to be 40 + 0.5 × 30 (ramping time) = 55 min (because of the approximate linear temperature ramping), which resulted in an estimated pretreatment severity CHF = 3.3, slightly higher than our initial target of 2.7. As described previously (Zhang et al., 2015; Zhu et al., 2015), the digester contents were discharged into a blow tank through a stainless steel pipe at the end of pretreatment. Volatiles and non-condensable gasses including SO2 were vented to a wet scrubber (Figure 1). The pretreated materials were recovered in two fractions: the freely drainable liquor of 32.15 kg and wet solids of 110.70 kg that contained approximately two-thirds of the spent liquor. Detailed mass balance data are listed in Table 1.
Figure 1. A schematic block flow diagram shows the pilot-scale pretreatment of poplar NE222 by SPORL along with downstream enzymatic saccharification and fermentation. Process boxed by dashed lines was partially conducted.
A 1.45 kg aliquot of the freely drainable spent liquor was neutralized using lime and then disk refined along with 5.0 kg wet solids (based on the ratio of collected spent liquor and wet solids) in an atmospheric disk refiner using a disk plate gap of 1.0 mm (Andritz Sprout-Bauer Atmospheric Refiner, Springfield, OH, USA) without adding any water. The refined material, defined as whole slurry, was used for subsequent high solids enzymatic saccharification and fermentation. A sample of the milled whole slurry was washed for chemical composition analysis, yield determination, and enzymatic hydrolysis.
Enzymatic hydrolysis of the washed solids (water insoluble) was conducted at 2% (w/v) in 100 mL of 50 mM acetate buffer on a shaker/incubator (Thermo Fisher Scientific, Model 4450, Waltham, MA, USA) at 50°C and 200 rpm at an elevated pH of 5.5 as described previously (Lan et al., 2013; Lou et al., 2013; Wang et al., 2013; Zhu et al., 2015). The CTec3 enzyme loading was 10 FPU g glucan-1. Replicate hydrolysis runs were conducted. Each sample was analyzed twice. The mean values were reported and SDs were used as error bars in plots.
Q-SSF of the un-detoxified NE222 whole slurry was carried out in 125-mL Ehrlenmeyer flasks using the same shaker/incubator described above. As described previously (Lan et al., 2013; Lou et al., 2013; Wang et al., 2013; Zhu et al., 2015), fermentation was buffered at pH 5.5 using sodium acetate (50 mM) to reduce non-productive cellulase binding to lignin. At CTec3 loading of 26 mL kg untreated wood-1 liquefaction of solids was observed in about 24–26 h at 50°C and 200 rpm. The mixture was then inoculated with Saccharomyces cerevisiae YRH400 yeast seed after cooling down to 35°C. Varied yeast seed loadings of 0.1, 0.4, and 0.6 mg dry cell g substrate-1 (abbreviated as mg g-1 in the following discussions), which are equivalent to calculated optical densities OD600nm = 1, 3.5, and 5, respectively, were used in fermentation. No nutrients were supplemented during all fermentation runs. Duplicate fermentation runs were conducted to ensure experimental repeatability. Each sample was analyzed twice. The reported data were averages of two fermentation runs. The SDs were used as error bars in plotting.
The chemical compositions of the untreated and pretreated NE222 were analyzed as described previously (Luo et al., 2010) using high performance anion exchange chromatography with pulsed amperometric detection (ICS-5000, Dionex, now Thermo Scientific, Sunnyvale, CA, USA). Klason lignin (acid insoluble) was quantified gravimetrically (Dence, 1992). For fast analysis, glucose in the enzymatic hydrolyzates was measured using a commercial glucose analyzer (YSI 2700S, YSI Inc., Yellow Springs, OH, USA).
Samples of fermentation broth were analyzed for monomeric sugars, furans, acetic acid, and ethanol using a HPLC system (Ultimate 3000, Thermo Scientific, Sunnyvale, CA, USA), equipped with an RI (RI-101) and UV (VWD-3400RS) detector, and using a BioRad Aminex HPX-87P, and a HPX-87H column operated as described previously (Zhou et al., 2013b). All samples were diluted using deionized water, and filtered by a 0.22 μm syringe filter prior to injection.
The SPORL spent liquor was first filtered using Whatman filter paper then further separated and purified by ultrafiltration (142-mm Millipore Hazardous Waste Filtration System, Millipore, Ireland) using ultrafiltration membranes (Ultracel® 1 KDa Ultrofiltration Disks, Millipore Corporation, Billerico, MA, USA). Detailed descriptions of the separation process can be found in our previous study (Zhou et al., 2015).
Aqueous GPC was conducted using an UltrahydrogelTM 250 column and measured with a multi-detector GPC system consisting of an Agilent 1100 HPLC equipped with a UV detector, an OptilabR T-rEXTM RI detector (Wyatt Technology Corp., Santa Barbara, CA, USA), and a DAWNR HELEOSTM II (Wyatt Technology Corp.) multi-angle light scattering (MALS) detector as described previously (Zhu et al., 2015).
The phenolic group (Ph-OH) content of LS was determined as described previously (Zhou et al., 2013a). The sulfur content of LS was analyzed using inductive coupled plasma (ICP) mass spectrometry as described previously (Zhou et al., 2015).
The total solids recovery from SPORL was 97.9% with 89.2% from the wet solids based on initial OD wood chips and without taking into account of the chemicals applied (Table 1). The amount of freely drainable spent liquor collected was 32.15 kg with additional 74.25 kg spent liquor remaining in the wet solids; or the wet solids contained 69.8% of the spent liquor. The amount of lignin dissolved as LS was 29.8% and was determined based on the balance of the measured Klason lignin in washed solids. Glucan loss was minimal with a total recovery of 95.1% with 87.3% from the washed solids. Xylan recovery was 81.5%. The production of furfural was 6.7% expressed as the percent of xylan in untreated NE222. The furfural and acetic acid concentrations in the spent liquor were 2.4 and 13.4 g L-1, respectively, in agreement with those from our laboratory study reported previously (Zhang et al., 2015). These levels of inhibitors can support viable fermentation using YRH400.
The washed solid substrate enzymatic digestibility (SED), defined as the percentage of glucan in the washed solids, enzymatically saccharified to glucose reached 88% in 72 h as shown in Figure 2 at a low CTec3 loading of 10 FPU g glucan-1 or 19 mL kg untreated wood-1. This indicated that the pretreatment was effective.
Figure 2. Time-dependent enzymatic saccharification efficiency of the washed solids of SPORL pretreated NE222 at a low CTec3 loading of 10 FPU g glucan-1.
Q-SSF of the whole slurry of SPORL pretreated NE222 was conducted at 20% total solids loading without detoxification using S. cerevisiae YRH400. Enzymatic liquefaction (or pre-hydrolysis) produced a hydrolyzate with initial glucose concentration of approximately 70 g L-1 (Figure 3A, yeast added at t = 0). The initial xylose concentration in the hydrolyzate was approximately 30 g L-1 (Figure 3B) along with 7 g L-1 mannose (Figure 3C). Glucose was completely consumed in 120 h and 72 h by YRH400 at yeast loadings of 0.4 mg g-1 (OD600nm = 3.5) and 0.6 mg g-1 (OD600nm = 5.0), respectively. However, glucose consumption was delayed for approximately 20 h at yeast loading = 0.1 mg g-1 (OD600nm = 1.0) as shown in Figure 3A. Furthermore, glucose consumption rate was substantially reduced. The average glucose consumption in the first 48 h was reduced from -0.89 g L-1 h-1 at yeast loading = 0.4 mg g-1 to -0.33 g L-1 h-1 at 0.1 mg g-1 (Table 2), or by 63%. Only approximately 25% of the xylose was consumed in 120 h fermentation (Figure 3B). This low xylose consumption was also observed in our previous study (Zhou et al., 2014a), especially with the presence of fermentation inhibitors. S. cerevisiae relies on hexose transporters with a low affinity for xylose (Kotter and Ciriacy, 1993). Both xylose and mannose consumptions were slower at lower yeast loadings (Figures 3B,C). Ethanol productivity was 0.35 g L-1 h-1 in the first 48 h at yeast loading of 0.4 mg g-1 with terminal ethanol concentration of 43.6 g L-1, compared with 0.11 g L-1 h-1 and 23.1 g L-1 at 0.1 mg g-1 yeast loading (Table 2). Further increase in yeast loading from 0.4 to 0.6 mg g-1 did not significantly improve terminal ethanol titer and yield, though it did improve ethanol productivity to 0.59 g L-1 in the first 48 h (Table 2).
Figure 3. Time-dependent ethanol production and sugar consumptions during Q-SSF of the whole slurry of SPORL pretreated NE222 at 20% total solids loading without detoxification. (A) Ethanol and glucose; (B) Xylose; (C) Mannose.
Table 2. Performance of Q-SSF of the SPORL pretreated NE222 whole slurry at 20% total solids without detoxification at three yeast loadings.
Acetic acid is the major inhibitor in hydrolyzates derived from hardwoods or herbaceous biomass. Acetic acid concentration was approximately 10 g L-1 in the SPORL pretreated NE222 fermentation broth throughout the fermentation process (Figure 4A) as S. cerevisiae does not metabolize acetic acid (Wei et al., 2013). However, YRH400 quickly metabolized furans even at the lower yeast loading of 0.1 mg g-1 (Figures 4B,C). Furfural was completely metabolized within the first 20 h at yeast loading of 0.4 mg g-1. However, complete metabolization of hydroxylmethyl furfural (HMF) required 72 h at the same yeast loading because HMF has a lower membrane permeability (Palmqvist and Hahn-Hägerdal, 2000). The results in Figures 3A–C and 4A–C suggested that fermentation by YRH400 was fairly robust even at acetic acid concentration of 10 g L-1 and furan concentration of approximately 2 g L-1.
Figure 4. Time-dependent inhibitor concentrations during Q-SSF of the whole slurry of SPORL pretreated NE222 at 20% total solids loading without detoxification. (A) Acetic acid; (B) Furfural; (C) HMF.
To demonstrate the effectiveness of using CHF for SPORL process scale-up, the present ethanol yield and productivity vs pretreatment severity CHF were compared with those obtained at the lab bench-scale under different temperatures and a slightly higher sulfite loading of 4 wt% in a previous study (Zhang et al., 2015). Both ethanol productivity and yield from the pilot scale showed good agreement with the lab-bench scale data (Figure 5), indicating CHF is a good scaling factor for ethanol production when using SPORL.
Figure 5. Comparisons of ethanol productivity and yield from the present pilot-scale study (40 kg) with those from a lab-bench scale study (150 g) plotted against pretreatment severity CHF.
The process data were used to produce the overall mass balance for the fermentation run with yeast loading of 0.4 mg g-1 (or OD600nm = 3.5). As shown in Figure 6, ethanol yield was 247 ± 1 L (195 kg) tonne wood-1, or equivalent to 54.7% theoretical based on the sum of wood glucan, mannan, and xylan content. The terminal titer was 43.6 ± 0.2 g L-1 (Table 2). These numbers are in agreement with those produced from lab scale (150 g) pretreatment (Zhang et al., 2015) using the same NE222 with CHF = 1.87–2.68. The low ethanol yield of 54.7% theoretical compared with approximately 70% using SPORL on softwood species (Zhou et al., 2013b; Zhu et al., 2015) was mainly due to the low xylose fermentation yield. Poplar NE222 has 12.7% xylan content, only approximately 25% of the xylose was fermented as discussed previously (Figure 3B). A better xylose fermentation strain may be able to improve overall ethanol yield.
Figure 6. A block diagram shows overall process mass balance for the pilot-scale pretreatment of poplar NE222 with subsequent enzymatic saccharification and fermentation. Process boxed by dashed lines was partially conducted.
Approximately 67 kg wood lignin tonne wood-1 can be recovered as LS as a coproduct (Figure 6). The actual LS yield will be higher because sodium and sulfur on LS was not in the mass balance calculation. LS has a variety of commercial applications (Gargulak and Lebo, 1999). To ensure the utility of the LS produced from poplar NE222 (LS-SP-NE222) in the present study, the molecular weight (MW), sulfonic acid group, and Ph-OH contents were compared with a commercial LS (D-748) produced from acid sulfite pulping of softwoods. As shown in Table 3, LS-SP-NE222 had a low MW of 16560 Da compared with 43110 Da for D-748. LS-SP-NE222 was also less sulfonated with sulfur content of 42.5 mg g-1 vs 61.7 mg g-1 for D-748. However, the Ph-OH content in LS-SP-NE222 is approximately two times of that in D-748.
Table 3. Comparisons of MWs and sulfur and Ph-OH contents of the LS from SPORL pretreated NE222 at the pilot scale with sulfuric acid and sodium bisulfite loading on wood 1.1 and 3.0 wt%, respectively, for 40 min at 160°C with those of a commercial LS from sulfite pulping of softwoods.
Typically, LSs with higher sulfur content were found to be better than those of low sulfur content as a dispersant for coal–water slurry and cement (Yang et al., 2007; Ouyang et al., 2009). A similar finding was obtained in applying LS as a dispersant to gypsum paste (Matsushita and Yasuda, 2005). This suggests the low sulfite loading used in the present SPORL pretreatment does not produce a favorable lignin coproduct for the above mentioned applications. Previous studies using high sulfite loading for softwoods produced LS with a sulfur content equivalent to as D-748 (Zhou et al., 2014b; Zhu et al., 2015). Ph-OH content affects both LS physical and chemical properties (Adler, 1977). The high content of Ph-OH indicates the potential of LS to produce phenolic, isocyanate, and epoxy resins (Olivares et al., 1988; Lora and Glasser, 2002). In addition, Ph-OH provides opportunities for chemical and biological modifications for developing novel applications of LS. This suggests that the LS-SP-NE222 may be more suitable for these applications.
This study demonstrated pilot-scale SPORL pretreatment of a poplar wood for high titer ethanol production without detoxification. The compounding effect of fermentation inhibition from acetic acid and furans was managed by balancing sugar yield with inhibitor formation using a CHF as a pretreatment severity measure. A good ethanol yield of 247 L tonne wood-1 at titer of 43.6 g L-1 was achieved at a CTec3 loading of only 15 FPU g glucan-1 or 26 mL kg wood-1 and yeast loading of 0.4 mg g substrate-1. LS from SPORL pretreatment had high Ph-OH content that may be suitable for special applications to improve the economics of biofuel production. No competing technology has demonstrated the results presented in this study. SPORL was developed based on sulfite pulping with proven commercial scalability and has potential for commercialization. The study demonstrated an efficient conversion system at pilot scale, especially with respect to optimizing pretreatment by using a simple scale factor and eliminating detoxification in downstream processing. Therefore, this study is important to both the research community and industry in the entire supply chain of bioethanol production from woody biomass.
Haifeng Zhou and Roland Gleisner are co-inventors of a US patent application on SPORL. The other co-authors declare that the research was conducted in the absence of any commercial or financial relationships that could be construed as a potential conflict of interest.
This work was supported by a USDA Small Business Innovative Research (SBIR) Phase II project (Contract Number: 2010-33610-21589) to Biopulping International, the Chinese Scholarship Council (CSC), and the International Science and Technology Cooperation Program of China (ISTCP):2013DFA41670. The funding from these programs made the visiting appointment of HZ at the USDA Forest Products Laboratory (FPL) possible. We would like to acknowledge Jerry Gargulak of LignoTech for providing us the D-748 Lignosulfonate, Fred Matt for conducting carbohydrate measurements, Linda Lorenz for assisting GPC measurements of lignosulfonate, Kolby Hirth for ICP analysis of sulfur, and Ron Zalesny of the USDA Forest Service Northern Research Station for providing the wood material. This work was conducted on official government time of JYZ and RG while HZ was a visiting student at the USDA Forest Service, Forest Products Laboratory, Madison, WI, USA.
Acker, R. V., Leple, J. C., Aerts, D., Storme, V., Goeminne, G., Ivens, B., et al. (2014). Improved saccharification and ethanol yield from field-grown transgenic poplar deficient in cinnamoyl-CoA reductase. Proc. Natl. Acad. Sci. USA. 111, 845–850. doi: 10.1073/pnas.1321673111
Pubmed Abstract | Pubmed Full Text | CrossRef Full Text | Google Scholar
Adler, E. (1977). Lignin chemistry – past, present and future. Wood Sci. Technol. 11, 169–218. doi:10.1007/BF00365615
Dence, C. W. (1992). “The determination of lignin,” in Methods in Lignin Chemistry, eds S. Y. Lin and C. W. Dence (Berlin: Springer-Verlag), 33–61.
Gargulak, J. D., and Lebo, S. E. (1999). “Commercial use of lignin-based materials,” in Lignin: Historical, Biological, and Materials Perspectives, Vol. 742, eds W. G. Glasser, R. A. Northey, and T. P. Schultz (Washington, DC: American Chemical Society), 304–320.
Gille, S., and Pauly, M. (2012). O-acetylation of plant cell wall polysaccharides. Front. Plant Sci. 3:12. doi:10.3389/fpls.2012.00012
Pubmed Abstract | Pubmed Full Text | CrossRef Full Text | Google Scholar
Hector, R. E., Dien, B. S., Cotta, M. A., and Qureshi, N. (2011). Engineering industrial Saccharomyces cerevisiae strains for xylose fermentation and comparison for switchgrass conversion. J. Ind. Microbiol. Biotechnol. 38, 1193–1202. doi:10.1007/s10295-010-0896-1
Pubmed Abstract | Pubmed Full Text | CrossRef Full Text | Google Scholar
Ho, N. W. Y., Chen, Z., and Brainard, A. P. (1998). Genetically engineered Saccharomyces yeast capable of effective cofermentation of glucose and xylose. Appl. Environ. Microbiol 64, 1852–1859.
Jeffries, T. W., and Jin, Y.-S. (2004). Metabolic engineering for improved fermentation of xylose by yeasts. Appl. Microbiol. Biotechnol. 63, 495–509. doi:10.1007/s00253-003-1450-0
Pubmed Abstract | Pubmed Full Text | CrossRef Full Text | Google Scholar
Kim, T. H., Choi, C. H., and Oh, K. K. (2013). Bioconversion of sawdust into ethanol using dilute sulfuric acid-assisted continuous twin screw-driven reactor pretreatment and fed-batch simultaneous saccharification and fermentation. Bioresour. Technol. 130, 306–313. doi:10.1016/j.biortech.2012.11.125
Pubmed Abstract | Pubmed Full Text | CrossRef Full Text | Google Scholar
Klinke, H. B., Thomsen, A. B., and Ahring, B. K. (2004). Inhibition of ethanol-producing yeast and bacteria by degradation products produced during pre-treatment of biomass. Appl. Microbiol. Biotechnol. 66, 10–26. doi:10.1007/s00253-004-1642-2
Pubmed Abstract | Pubmed Full Text | CrossRef Full Text | Google Scholar
Kotter, P., and Ciriacy, M. (1993). Xylose fermentation by Saccharomyces cerevisiae. Appl. Microbiol. Biotechnol. 38, 776–783. doi:10.1007/BF00167144
Kundu, C., Lee, H. J., and Lee, J. W. (2014). Enhanced bioethanol production from yellow poplar by deacetylation and oxalic acid pretreatment without detoxification. Bioresour. Technol. 178, 28–35. doi:10.1016/j.biortech.2014.08.082
Pubmed Abstract | Pubmed Full Text | CrossRef Full Text | Google Scholar
Lan, T., Lou, H., and Zhu, J. (2013). Enzymatic saccharification of lignocelluloses should be conducted at elevated pH 5.2–6.2. Bioenerg. Res. 6, 476–485. doi:10.1007/s12155-012-9273-4
Leu, S. Y., and Zhu, J. Y. (2013). Substrate-related factors affecting enzymatic saccharification of lignocelluloses: our recent understanding. Bioenerg. Res. 6, 405–415. doi:10.1007/s12155-012-9276-1
Littlewood, J., Guo, M., Boerjan, W., and Murphy, R. J. (2014). Bioethanol from poplar: a commercially viable alternative to fossil fuel in the European Union. Biotechnol. Biofuels 7, 113. doi:10.1186/1754-6834-7-113
Pubmed Abstract | Pubmed Full Text | CrossRef Full Text | Google Scholar
Lora, J. H., and Glasser, W. G. (2002). Recent industrial applications of lignin: a sustainable alternative to nonrenewable materials. J. Polym. Environ. 10, 39–48. doi:10.1023/A:1021070006895
Lou, H., Zhu, J., Lan, T. Q., Lai, H., and Qiu, X. (2013). pH-Induced lignin surface modification to reduce nonspecific cellulase binding and enhance enzymatic saccharification of lignocelluloses. ChemSusChem 6, 919–927. doi:10.1002/cssc.201200859
Pubmed Abstract | Pubmed Full Text | CrossRef Full Text | Google Scholar
Luo, X., Gleisner, R., Tian, S., Negron, J., Zhu, W., Horn, E., et al. (2010). Evaluation of mountain beetle-infested lodgepole pine for cellulosic ethanol production by sulfite pretreatment to overcome recalcitrance of lignocellulose. Ind. Eng. Chem. Res. 49, 8258–8266. doi:10.1021/ie1003202
Matsushita, Y., and Yasuda, S. (2005). Preparation and evaluation of lignosulfonates as a dispersant for gypsum paste from acid hydrolysis lignin. Bioresour. Technol. 96, 465–470. doi:10.1016/j.biortech.2004.05.023
Pubmed Abstract | Pubmed Full Text | CrossRef Full Text | Google Scholar
Moxley, G., Gaspar, A. R., Higgins, D., and Xu, H. (2012). Structural changes of corn stover lignin during acid pretreatment. J. Ind. Microbiol. Biotechnol. 39, 1289–1299. doi:10.1007/s10295-012-1131-z
Pubmed Abstract | Pubmed Full Text | CrossRef Full Text | Google Scholar
Olivares, M., Guzman, J. A., Natho, A., and Saavedra, A. (1988). Kraft lignin utilization in adhesives. Wood Sci. Technol. 22, 157–165. doi:10.1016/j.ultsonch.2013.05.001
Pubmed Abstract | Pubmed Full Text | CrossRef Full Text | Google Scholar
Ouyang, X., Ke, L., Qiu, X., Guo, Y., and Pang, Y. (2009). Sulfonation of alkali lignin and its potential use in dispersant for cement. J. Dispers. Sci. Technol. 30, 1–6. doi:10.1080/01932690802473560
Palmqvist, E., Grage, H., Meinander, N. Q., and Hahn-Hägerdal, B. (1999). Main and interaction effects of acetic acid, furfural, and p- hydroxybenzoic acid on growth and ethanol productivity of yeasts. Biotechnol. Bioeng. 63, 46–55. doi:10.1002/(SICI)1097-0290(19990405)63:1<46::AID-BIT5>3.3.CO;2-A
Pubmed Abstract | Pubmed Full Text | CrossRef Full Text | Google Scholar
Palmqvist, E., and Hahn-Hagerdal, B. (2000). Fermentation of lignocellulosic hydrolysate: I inhibition and detoxification. Bioresour. Technol. 74, 17–24. doi:10.1016/j.biortech.2013.03.014
Pubmed Abstract | Pubmed Full Text | CrossRef Full Text | Google Scholar
Palmqvist, E., and Hahn-Hägerdal, B. (2000). Fermentation of lignocellulosic hydrolysates. II: Inhibitors and mechanisms of inhibition. Bioresour. Technol. 74, 25–33. doi:10.1016/S0960-8524(99)00161-3
Tian, S., Zhu, W., Gleisner, R., Pan, X. J., and Zhu, J. Y. (2011). Comparisons of SPORL and dilute acid pretreatments for sugar and ethanol productions from aspen. Biotechnol. Prog. 27, 419–427. doi:10.1002/btpr.545
Pubmed Abstract | Pubmed Full Text | CrossRef Full Text | Google Scholar
Vance, E. D., Maguire, D. A., and Zalesny, R. S. J. (2010). Research strategies for increasing productivity of intensively managed forest plantations. J. For. 108, 183–192.
Vroom, K. E. (1957). A means of expressing cooking times and temperatures as a single variable. Pulp Paper Mag. Can. 58, 228–231.
Wang, Z. J., Lan, T. Q., and Zhu, J. Y. (2013). Lignosulfonate and elevated pH can enhance enzymatic saccharification of lignocelluloses. Biotechnol. Biofuels 6, 9. doi:10.1186/1754-6834-6-9
Pubmed Abstract | Pubmed Full Text | CrossRef Full Text | Google Scholar
Wang, Z. J., Zhu, J. Y., Zalesny, R. S. J., and Chen, K. F. (2012). Ethanol production form poplar wood the through enzymatic saccharification and fermentation by dilute acid and SPORL pretreatments. Fuel 95, 606–614. doi:10.1016/j.fuel.2011.12.032
Wei, N., Quarterman, J., Kim, S. R., Cate, J. H. D., and Jin, Y. S. (2013). Enhanced biofuel production through coupled acetic acid and xylose consumption by engineered yeast. Nat. Commun. 4, 2580. doi:10.1038/ncomms3580
Pubmed Abstract | Pubmed Full Text | CrossRef Full Text | Google Scholar
Wood, T. M., and Bhat, K. M. (1988). Methods for measuring cellulase activities. Meth. Enzymol. 160, 87–112. doi:10.1016/0076-6879(88)60109-1
Wyman, C. E., Dale, B. E., Elander, R. T., Holtzapple, M., Ladisch, M. R., Lee, Y. Y., et al. (2009). Comparative sugar recovery and fermentation data following pretreatment of poplar wood by leading technologies. Biotechnol. Prog. 25, 333–339. doi:10.1002/btpr.142
Pubmed Abstract | Pubmed Full Text | CrossRef Full Text | Google Scholar
Yang, B., and Wyman, C. E. (2004). Effect of xylan and lignin removal by batch and flowthrough pretreatment on the enzymatic digestibility of corn stover cellulose. Biotechnol. Bioeng. 86, 88–95. doi:10.1002/bit.20043
Pubmed Abstract | Pubmed Full Text | CrossRef Full Text | Google Scholar
Yang, D., Qiu, X., Zhou, M., and Lou, H. (2007). Properties of sodium lignosulfonate as dispersant of coal water slurry. Energy Convers. Manage. 48, 2433–2438. doi:10.1016/j.enconman.2007.04.007
Zalesny, R. S. Jr., Donner, D. M., Coyle, D. R., and Headlee, W. L. (2012). An approach for siting poplar energy production systems to increase productivity and associated ecosystem services. For. Ecol. Manage. 284, 45–58. doi:10.1016/j.foreco.2012.07.022
Zalesny, R. S. J., Cunningham, M. W., Hall, R. B., Mirck, J., Rockwood, D. L., Stanturf, J. A., et al. (2011). “Woody biomass from short rotation energy crops. 1st ed,” in Sustainable Production of Fuels, Chemicals, and Fibers from Forest Biomass, eds J. Y. Zhu, X. Zhang, and X. J. Pan (Washington, DC: American Chemical Society), 27–63.
Zhang, D. S., Yang, Q., Zhu, J. Y., and Pan, X. J. (2013). Sulfite (SPORL) pretreatment of switchgrass for enzymatic saccharification. Bioresour. Technol. 129, 127–134. doi:10.1016/j.biortech.2012.11.031
Pubmed Abstract | Pubmed Full Text | CrossRef Full Text | Google Scholar
Zhang, J., Gu, F., Zhu, J. Y., and Zalesny, R. S. Jr. (2015). Optimizing high titer ethanol production from a SPORL pretreated poplar without detoxification using a combined hydrolysis factor (CHF). Bioresour. Technol. 186, 223–231. doi:10.1016/j.biortech.2015.03.080
Zhou, H., Lan, T., Dien, B. S., Hector, R. E., and Zhu, J. Y. (2014a). Comparisons of five Saccharomyces cerevisiae strains for ethanol production from SPORL pretreated lodgepole pine. Biotechnol. Prog. 30, 1076–1083. doi:10.1002/btpr.1937
Pubmed Abstract | Pubmed Full Text | CrossRef Full Text | Google Scholar
Zhou, H., Leu, S.-Y., Wu, X., Zhu, J. Y., Gleisner, R., Yang, D., et al. (2014b). Comparisons of high titer ethanol production and lignosulfonate properties by SPORL pretreatment of lodgepole pine at two temperatures. RSC Adv. 4, 27033–27038. doi:10.1039/c4ra03608e
Zhou, H., Yang, D., Qiu, X., Wu, X., and Li, Y. (2013a). A novel and efficient polymerization of lignosulfonates by horseradish peroxidase/H2O2 incubation. Appl. Microbiol. Biotechnol. 97, 10309–10320. doi:10.1007/s00253-013-5267-1
Pubmed Abstract | Pubmed Full Text | CrossRef Full Text | Google Scholar
Zhou, H., Zhu, J. Y., Luo, X., Leu, S.-Y., Wu, X., Gleisner, R., et al. (2013b). Bioconversion of beetle-killed lodgepole pine using SPORL: Process scale-up design, lignin coproduct, and high solids fermentation without detoxification. Ind. Eng. Chem. Res. 52, 16057–16065. doi:10.1021/ie402873y
Zhou, H., Zhu, J. Y., Gleisner, R., Qiu, X., Horn, E., and Negron, J. (2015). Pilot-scale demonstration of SPORL for bioconversion of lodgepole pine to bio-ethanol and lignosulfonate. Holzforschung doi:10.1515/hf-2014-0332
Zhu, J. Y., Chandra, M. S., Gu, F., Gleisner, R., Reiner, R., Sessions, J., et al. (2015). Using sulfite chemistry for robust bioconversion of Douglas-fir forest residue to bioethanol at high titer and lignosulfonate: a pilot-scale evaluation. Bioresour. Technol. 179, 390–397. doi:10.1016/j.biortech.2014.12.052
Pubmed Abstract | Pubmed Full Text | CrossRef Full Text | Google Scholar
Zhu, J. Y., Gleisner, R., Scott, C. T., Luo, X. L., and Tian, S. (2011). High titer ethanol production from simultaneous enzymatic saccharification and fermentation of aspen at high solids: a comparison between SPORL and dilute acid pretreatments. Bioresour. Technol. 102, 8921–8929. doi:10.1016/j.biortech.2011.07.047
Pubmed Abstract | Pubmed Full Text | CrossRef Full Text | Google Scholar
Zhu, J. Y., and Pan, X. J. (2010). Woody biomass pretreatment for cellulosic ethanol production: technology and energy consumption evaluation. Bioresour. Technol. 101, 4992–5002. doi:10.1016/j.biortech.2009.11.007
Pubmed Abstract | Pubmed Full Text | CrossRef Full Text | Google Scholar
Zhu, J. Y., Pan, X. J., Wang, G. S., and Gleisner, R. (2009). Sulfite pretreatment (SPORL) for robust enzymatic saccharification of spruce and red pine. Bioresour. Technol. 100, 2411–2418. doi:10.1016/j.biortech.2008.10.057
Pubmed Abstract | Pubmed Full Text | CrossRef Full Text | Google Scholar
Keywords: forest biorefinery, biofuel, process scale-up, high solids fermentation, enzymatic saccharification/hydrolysis, lignosulfonate, poplar wood
Citation: Zhou H, Zhu JY, Gleisner R, Qiu X and Horn E (2015) High titer ethanol and lignosulfonate production from SPORL pretreated poplar at pilot scale. Front. Energy Res. 3:16. doi: 10.3389/fenrg.2015.00016
Received: 10 February 2015; Paper pending published: 11 March 2015;
Accepted: 25 March 2015; Published online: 27 April 2015.
Edited by:
Soo-Jeong Shin, Chungbuk National University, South KoreaReviewed by:
Rajeev Kumar Sukumaran, National Institute for Interdisciplinary Science and Technology, IndiaCopyright: © 2015 Zhou, Zhu, Gleisner, Qiu and Horn. This is an open-access article distributed under the terms of the Creative Commons Attribution License (CC BY). The use, distribution or reproduction in other forums is permitted, provided the original author(s) or licensor are credited and that the original publication in this journal is cited, in accordance with accepted academic practice. No use, distribution or reproduction is permitted which does not comply with these terms.
*Correspondence: J. Y. Zhu, Forest Products Laboratory, 1 Gifford Pinchot Dr., Madison, WI, USA e-mail:anpodUBmcy5mZWQudXM=
Disclaimer: All claims expressed in this article are solely those of the authors and do not necessarily represent those of their affiliated organizations, or those of the publisher, the editors and the reviewers. Any product that may be evaluated in this article or claim that may be made by its manufacturer is not guaranteed or endorsed by the publisher.
Research integrity at Frontiers
Learn more about the work of our research integrity team to safeguard the quality of each article we publish.