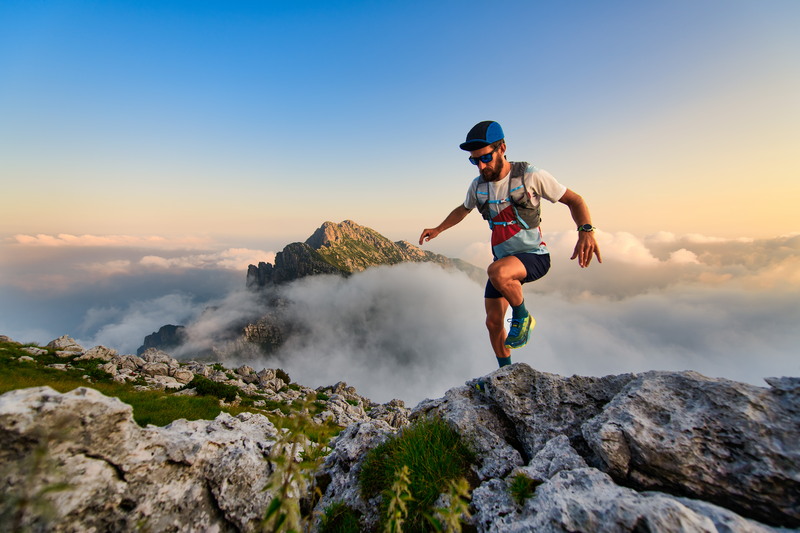
95% of researchers rate our articles as excellent or good
Learn more about the work of our research integrity team to safeguard the quality of each article we publish.
Find out more
BRIEF RESEARCH REPORT article
Front. Energy Effic. , 17 July 2024
Sec. Energy Efficiency Technologies
Volume 2 - 2024 | https://doi.org/10.3389/fenef.2024.1437214
This article is part of the Research Topic Technologies and Applications of Digital Twins to Enable Efficient Energy Systems View all articles
The expected increase in green hydrogen demand in the near future necessitates scaling-up the hydrogen production plants with the goal of reducing the hydrogen production costs. Nevertheless, a quick scale-up limits the time to test new designs, optimize operation schedules and build up knowledge for production parameters. The Digital Twin concept applied on a fleet of electrolysers is proposed as a digitization tool to contribute to this scale-up process by providing a comprehensive view of the entire electrolysers fleet as well as constructing the feedback connection to the electrolysers manufacturing process. Such Fleet Digital Twin approach can improve the efficiency and scalability of green hydrogen production using water electrolysis. This paper presents a concept of a Fleet Digital Twin and discusses its architecture requirements and design. By applying the Digital Twin concept at different levels of the system, fleet knowledge services are enabled by leveraging the availability of fleet-wide data. The proposed architecture design provides a solid foundation for future development and implementation of Fleet Digital Twins in industrial applications.
The transition towards energy sources with lower carbon emissions has intensified the necessity to establish a robust hydrogen economy as a fundamental alternative to fossil fuels. This brings several challenges, one of which pertains to the swift scaling-up of hydrogen production and the evolution of manufacturing processes towards automated mass production (BMWi, 2020; BMBF, 2022; BMWK, 2023). In parallel, researchers are actively investigating the structure and materials used within electrolysers, with long-term testing proving difficult to perform within a short timeframe, given that most electrolysers have not yet reached their end-of-life stage (BMBF, 2022). Utilizing Digital Twins as virtual representations of physical entities or assets such as electrolysers represents a promising approach. With Digital Twins, operational data can be accessed throughout the entire life cycle of the electrolysers, enabling analysis of performance characteristics (Semeraro et al., 2021).
The Digital Twins are in most cases more than virtual representations of physical entities. Digital Twins enable a live remote monitoring and control with an automated bi-directional data connection to the physical entity (Liu et al., 2021). In addition, a distinction can be made between a Digital Twin, a Digital Shadow, and a Digital Model. A Digital Twin is characterized by an automated bi-directional data connection to the physical entity, while a Digital Shadow only has an automated data connection from the physical entity to the shadow, in the read direction. A Digital Model does not have any automated data connection (Kritzinger et al., 2018).
A crucial performance characteristic of electrolysers is their degradation and estimated remaining useful life. By automatically assessing the state of health of electrolysers throughout their lifespan, Digital Twins can provide valuable insights about their degradation (BMBF, 2022). In addition, it supports establishing a feedback loop from the field into production as well as into development and engineering of electrolysers, leading to possible improvements in the development, production, and maintenance process (Kritzinger et al., 2018).
Furthermore, with the scale-up plan for electrolysis capacity set to reach several gigawatts, numerous electrolyser plants are expected to operate in the near to mid-term future (BMBF, 2022). Managing such a large fleet of electrolysers will require a robust Prognostic and Health Management (PHM) system. Digital Twin driven PHM can be advantageous over traditional PHM, given that vast amounts of operating data can be collected from the numerous electrolysers within the fleet (Tao et al., 2019a).
However, to fully leverage the benefits of a Digital Twin of an electrolyser fleet, it should not be limited to analyzing degeneration and PHM. A Fleet Digital Twin should also be designed to facilitate the development and implementation of various high-level applications, including those that may not have been initially considered during the development of the Fleet Digital Twin. Therefore, a Fleet Digital Twin should be designed with modularity and flexibility in mind, to allow for the accommodation of different objectives and to enable the addition of new applications as needed (Huxoll et al., 2022; Alsharif et al., 2023).
Despite the potential benefits, the application of Digital Twins to large scale electrolysers at a fleet level, remains underexplored. Current research predominantly focuses on individual Digital Twins, overlooking the synergies and enhanced insights that can be derived from a fleet-level perspective.
This paper presents a concept and an architecture design for a Digital Twin of a fleet of electrolysers, towards a framework that integrates individual Digital Twins into a cohesive Fleet Twin, enabling better data management, predictive maintenance, and overall optimization of the electrolysers. The paper discusses the requirements for such an architecture and the architectural pattern chosen to meet these requirements. Complementary to previous architectures for Digital Twins of single electrolysers as in (Huxoll et al., 2022; Alsharif et al., 2023), a modular and flexible architecture for a fleet of physical entities, i.e., electrolysers, is presented. The design focuses on the integration of different technologies and facilitates the development of different applications. This paper also discusses the various technologies used in different components of the architecture and their advantages.
Several studies have investigated the development of Digital Twins for industrial equipment and processes, including electrolysers. For instance, the work by Shin et al. (2022) proposes a Digital Twin for a 500 kW alkaline water electrolyser. The authors developed a simulation model as a base of the Digital Twin using Python and gPROMS. They analyse the system efficiency and found out the optimum operating pressure. The study by Meraghni et al. (2021) constructs a data-driven Digital Twin to integrate the physical knowledge of the system and used a deep transfer learning model based on stacked denoising autoencoder to update the Digital Twin with online measurements. They present a case study with experimental PEM fuel cell degradation data where the proposed data-driven Digital Twin prognostics method has been applied and reached a high prediction accuracy. The authors implement the Digital Twin in a layered architecture comprising of a physical, a connection and a digital layer. The study focuses on the accuracy of the suggested models but not on the architecture of the Digital Twin.
Another work by Folgado et al. (2022) describes the design and implementation of a MATLAB-based application that embeds a digital replica of a PEM water electrolyser and a GUI dedicated to its control. The implementation focuses on providing a user-friendly environment that visualises the evolution of the operation of an experimental electrolyser by reading the data in real-time.
The work by Glaessgen and Stargel (2012) identifies deficiencies in the conventional methods used by the US Air Force to achieve real-time monitoring and precise prediction. As a result, they proposed the development of Digital Twins that could integrate historical, fleet and sensor data. The authors also outline key characteristics of Digital Twins such as ultrahigh-fidelity models, robust computational and data processing capabilities, and vehicle health management systems. Furthermore, they highlight the benefits of Digital Twins for PHM, including increased reliability and timely evaluation of mission parameters.
In a previous work, the authors of this paper present a short summary of an architecture design for a Digital Twin for single electrolysers (Huxoll et al., 2022). The authors elaborate more on the design and its requirements in Alsharif et al. (2023). As an extension to that work, this paper provides the requirements and the design for a Digital Twin from the fleet perspective.
In summary, previous studies have investigated the development of Digital Twins for various types of machines, including electrolysers and related equipment. These studies have utilized various modeling approaches and data sources to enable predictive maintenance, optimize performance, and improve the overall reliability of the equipment. However, to the best of our knowledge, there has only been limited research on the development of a Digital Twin for a fleet of electrolysers with focus on the architecture and its requirements. This paper aims to fill this research gap by proposing an architecture for a Digital Twin of an electrolyser fleet and presenting the requirements and the design of the proposed architecture.
This section explains the concept of a Fleet Digital Twin (short: Fleet Twin). It includes a definition of the term “Fleet Twin” and explores different model types. The section also provides examples of Fleet Twins in action, namely, in the field of hydrogen electrolysers.
In the context of this work, a Digital Twin is defined as the virtual representation of a physical object or an asset with a bi-directional automated data connection (Liu et al., 2021). When considering a fleet of physical objects, e.g., a fleet of electrolysers, a Fleet Twin refers to a digital representation of the entire fleet of electrolysers, assets or equipment, rather than just a single unit. From the application perspective, Digital Twins can be classified into unit-level, system-level and system of systems (SoS) level Digital Twins (Tao et al., 2019b).
We define a Fleet Twin as the representation of a group of similar objects (units, systems or SoS), in one digital replica that is able to represent the status of the set of objects, analyse the data and infer knowledge useful to make operation, maintenance and production decisions. This basic concept for a Fleet Twin is a special case of the SoS Digital Twin from Tao et al. (2019b). The main differentiation is that while in the SoS Digital Twin every subsystem can be very different to the other, the objects within a fleet have similar technical characteristics and functional principles (Braig and Zeiler, 2023). The advantage of this specialization of the SoS approach is that it allows for use-cases based on the similarity of the objects, such as anomaly detection by comparing the behavior of different, but similar objects.
In the example of electrolysers, Digital Twins could be used to represent single cells, an integral part of PEM electrolysers. These cell twins are combined to build the first level of the Fleet Twin, so-called stacks. The stacks in turn are combined again by a Fleet Twin to a whole electrolyser. This concept can be applied recursively, as multiple of these electrolysers could be combined again in another Fleet Twin, for example, to represent all electrolysers on one hydrogen production site.
This can be illustrated with the example of electrolysers, as shown in Figure 1. In a first step, Digital Twins represent single physical objects. Once multiple twins are combined, a Fleet Twin is applied to represent the group of twins. Fleet Twins themselves in turn can also be combined again. The concept of a Fleet Twin can be advantageous in several ways. It provides a holistic view of the entire fleet for better understanding of the overall health and performance of the fleet. Furthermore, a Fleet Twin can serve as a shared platform for different unit owners to collaborate and increase efficiency without compromising the property of data. In addition, real-time monitoring on the fleet level can improve the operation and maintenance when it is combined with fleet-based knowledge for predictive maintenance and PHM.
Figure 1. Digital twin concept applied for physical objects on different levels: single object, fleet of objects and a group of fleets.
Different models can be applied on different levels of the fleet hierarchy shown in Figure 1. Typical types of models are physics-based models on the one hand and data-driven models on the other hand. While physics-based models may account for a higher accuracy, for complex systems they may lack of efficiency, whereas for data-driven models it may be the other way around (Willard et al., 2022). As shown in Figure 1, the complexity and possible amount of data grows from left to right, wherefore data-driven models are more likely to be used on the aggregated Fleet Twins.
Combining both types of models can help to reduce the complexity of the overall system, as data-driven models can be used to substitute some of the more computationally expensive physics-based models. This can help to create faster and more efficient models that can be used in real-time applications. In electrolysers, for example, this can be temperature control or optimizing operation according to the available renewable energy and electricity prices.
To make architecture decisions, requirements for the architecture are needed. We derive the requirements based on a use case specification. First, the use case is presented, from which the requirements are derived.
One key use case for Fleet Twins for electrolysers is centered on addressing the challenge of predicting maintenance accurately for individual electrolysers within the fleet, with the goal of reducing maintenance costs, improving asset availability, and optimizing process performance (Liu et al., 2018). By analyzing fleet-wide data, the Fleet Twin can construct a degradation model that can estimate the maintenance time for a particular electrolyser that does not have sufficient data or models. The operator of the electrolysers can interact with the Digital Twin to select which electrolyser within the fleet needs a maintenance schedule. The Digital Twin should be able to provide the current health state of the electrolyser, along with a recommended maintenance time. This information can help the operator to plan for maintenance activities proactively, reducing the risk of unscheduled downtime and associated costs. Such service can also be used to monitor the fleet’s overall health and identify trends or patterns that may signal an issue with the electrolysers’ performance. By analyzing this data, the fleet operator can identify opportunities for process optimization, improving efficiency, and reducing costs.
While these could also be implemented on the Digital Twin level, doing it on a fleet level provides some advances. By utilizing transfer learning approaches, degradation models can be enhanced with knowledge from other electrolyzers and the maintenance scheduling can consider maintenance times from other electrolysers to do maintenance together or reduce the number of devices which are maintained at the same time.
Based on the described use case, the Fleet Twin aims to enable live monitoring and control of multiple of remote physical entities through other instances of Digital Twins. It also aims to provide fleet knowledge services for the operation and production processes by leveraging data-driven methods and the availability of fleet-wide historical data.
Our concept for Fleet Twins is based on the idea that a Fleet Twin is an extension of Digital Twins, wherefore the requirements are similar to the ones for the Digital Twins. Hence, the requirements which are provided in Alsharif et al. (2023) for the Digital Twins also apply for the Fleet Twin concept. Nevertheless, the weights for the requirements shift: the scalability, modularity and interoperability are increasingly important with a distributed set of different twins connected to a Fleet Twin. Reliability is especially important as single failing units in a fleet may not disturb the whole Fleet Twin. The most important non-functional requirements are listed in Table 1.
Table 1. Fleet Twin related Non-Functional requirements based on (Alsharif et al., 2023).
Next to the non-functional requirements, the use case above provides functional requirements. Among others, these include data aggregation of Digital Twin data for degradation modeling to predict possible failures. Additionally, the Fleet Twin needs the functionality of maintenance scheduling to schedule maintenance actions together.
An important consideration when adding the concept of a fleet to Digital Twins is the question of how to organize the data handling between the physical entities and the Fleet Twin. In the following we consider three types to establish a Fleet Twin, ranging from a centralized Data Lake approach over a separated Digital Twin and Fleet Twin approach to an approach where Digital Twins and Fleet Twin manage their data and capabilities in a federated manner.
Figure 2A shows an approach where all the data from the different physical objects reside on one big data lake. Data analysis is performed in this one entity by processing single units’ data and fleet data directly from the data lake. This represents a solution that does not require complex communication between individual twins and the Fleet Twin since they are the same digital entity. However, this approach is not optimal if different physical entities have different ownerships and may not be willing to share all of the collected data. Nevertheless, if the data is collected in a single Data Lake, the analysis of all the data may be simplified. Reliability-wise, the Data Lake represents a single point of failure. If this data lake is compromised, the individual as well as the Fleet Digital Twins are affected.
Figure 2. Comparison of different Configurations of Digital Twins and Fleet Twin. (A) Digital Twin and Fleet Twin as same entity. (B) Digital Twins and Fleet Twin as separate entities, connecting. (C) Digital Twins and Fleet Twin as separate entities, connecting.
Figure 2B shows an approach where the Digital Twins and Fleet Twin are considered different entities. This approach is more suitable if the physical entities have different ownerships, as each individual can be set up and operated by its respective owner. Data owners can choose which data to share with the fleet and can partially solve the data ownership problem. In addition, this improves the reliability of the whole system: if one Digital Twin fails, the system can still work, and even the Fleet Twin can substitute the single Digital Twin affected.
Furthermore, there are several ways to collect the data streams that are generated from the individual machines. One way is to connect the Fleet Twin directly to each individual physical entity as shown in Figure 2B. This way has the advantage of increased redundancy for the system of Digital Twins and decouples the Fleet Twin from the Digital Twins of the units. This might entail duplicates in data preparation, pre-processing and state estimation as it needs to be performed both in the Digital Twins and the Fleet Twin. The interface with the physical object also needs to be implemented twice.
Another way is to connect the Fleet Twin to the individual Digital Twins instead of the physical units as shown in Figure 2C. In this case, pre-processing and preparation of data happens only once, saving resources. However, redundancy of the whole system is reduced, as only the Digital Twin is connected to the physical entity. Additionally, in the perspective of data ownership, this type offers the option to only share data pre-aggregated by a Digital Twin with the Fleet Twin, improving the data privacy for the owner of a physical entity by keeping the option to profit from a shard Fleet Twin with other device owners.
Table 2 summarizes the three architecture types. Type 1 (data lake) might be suitable for setups where all the entities belong to one data owner and sharing the data of different entities is not a problem. The architecture is simpler, but presents a single point of failure which may not be an option in every use case. Type 2 (separated twins) is more suitable for critical systems where redundant representation is required. Here, loosing a Digital Twin does not disrupt the operation of the other physical units nor of the entire fleet. Type 3 (federated twins) can be used in case a compromise can be made between redundancy and resources with the additional upside of the option of high data privacy while sharing data with the Fleet Twin.
More details of the architecture of the Fleet Twin for electrolysers are described in the next section.
To demonstrate the architecture design on a more detailed level, we took the application example of a fleet of electrolyzers to decide for and design a Fleet Twin architecture. In this use case, we aim for high flexibility regarding the composition of fleets to be able to add electrolyzers when the fleet grows over time. Additionally, data ownership questions have a high priority, as owners of electrolyzers may want to share some data with a fleet to gain better insights, e.g., for predictive maintenance, but also want to limit the amount of shared data to avoid other device owners to gain unnecessary insights into others’ owners devices. Due to these considerations, we decide for a Fleet Twin architecture of Type 3.
The construction of the Fleet Twin is similar to the Digital Twin presented in Huxoll et al. (2022). Figure 3 depicts the components of the Fleet Twin with the core functionalities in the blue box. The message orchestrator component is responsible for connecting different components within the twin and to distribute the messages. The connection framework’s task is to establish the bi-directional data connection with the physical/digital entities in (nearly) real-time. The state estimation component is responsible for proving the state of the physical entities based on the live measurements retrieved from their respective Digital Twins, mainly based on data-driven approaches. Data management is handled by the data storage component, which may consist of several different databases.
Figure 3. Fleet Twin context diagram, showing the relationship between different actors and the high level component diagram of the Fleet Twin.
Instead of a direct connection to every physical device as in Type 1 and 2, here, the Fleet Twin connects to the Digital Twins of the electrolysers. As depicted in Figure 3, the Digital Twin provides aggregated data to the connection framework and may accept certain control signals. Due to this setup, the Digital Twin has the final control on what data is shared and which control can be done by the Fleet Twin.
Higher functionalities are enabled using these core components via the message orchestrator and are connected to the Fleet Twin using the service framework. The service framework uses a generic API to be able to add functionalities written in different environments such as programming languages. Such a modular design with a thin core and an extensible service ecosystem ensures modularity, extensibility, and interoperability (Huxoll et al., 2022). In our example for an electrolyzer fleet, this may be a service for improving the manufacturing process, which processes aging data from the state estimation component to correlate these to manufacturing properties.
When considering multiple electrolysers, multiple streams of data for plant sensors as well as states are expected to be aggregated by the Fleet Twin. The data streams might have different resolutions and different formats. Thus, during a pre-processing step in the data stream system, the data is converted to a predefined format. With this data, the state estimation can run and estimate parameters of the electrolysers. This may be done additionally to a Digital Twins’ estimation, as the fleet data may allow other insights. This is done in near real-time using stream processing (Alsharif et al., 2023). Next, the electrolysers’ data is made available for the services via a publish-subscribe system and saved in a time-series database. Within the use case of a fleet of hydrogen electrolyzers, the number of electrolysers in the fleet is expected to increase, leading to significant growth in the generated data volume. Hence, effective scalability represents a serious challenge in this field. The publish-subscribe system suggested has proven to be a robust solution for managing large-scale data streams efficiently Bellavista et al. (2014). It decouples data producers (such as sensors and electrolysers) from consumers (Twins), enabling scalability without compromising performance.
The Services within the Twin can access the live data as well as the stored data to provide their functionality (Alsharif et al., 2023). The service framework can include services such as predictive maintenance or optimized operation of the fleet. The results of the services are again made available on the publish-subscribe system, as other services might rely on those results. Since the architecture is service-based, with the components and services are containerized, the architecture can handle the addition, removal or update of services easily. The service must only be able to access the publish-subscribe system and read or write data in a suitable format (Alsharif et al., 2023).
This paper presents a definition and concept for a Digital Twin for a fleet of similar units, namely, a Fleet Twin, and discusses several options for its design. This is done with the example of hydrogen electrolysers. A fundamental use case for a Fleet Twin was explained and the functional and non-functional requirements of the architecture design were deduced based on it. Three architecture design options for a Fleet Twin are discussed. Based on the presented use case of electrolyzers, one of the three design options for a Fleet Twin was adopted. The choice was made for a Fleet Twin comprising of the connection to the electrolysers’ Digital Twins. This enables applying the fleet concept recursively on different levels. The main components and data management design choices were discussed in more detail.
Currently, a first implementation of the designed architecture with the essential components is being developed and tested based on simulated data. Future work will focus on extending the current implementation to include all components of the suggested architecture, such as fleet-level anomaly detection and transfer learning. Field data originating from actual electrolysers will be incorporated to evaluate the architecture and the selected technologies.
Furthermore, future development should focus on validating the Fleet Twin concept through case studies reflecting real operation conditions. This can help to identify potential issues and further improve the architecture. Afterward, address the projected scalability and computation challenges by implementing advanced data handling techniques, such as edge computing and data aggregation, and then leveraging high-performance computing solutions. Additionally, ensuring integration with existing industrial systems through standardized protocols and interfaces is crucial. Real-world applications include predictive maintenance to reduce downtime, operational optimization for improved efficiency, and informing the design of next-generation electrolysers.
The original contributions presented in the study are included in the article/Supplementary Material, further inquiries can be directed to the corresponding author.
SA: Conceptualization, Software, Writing–original draft. NH: Conceptualization, Software, Writing–original draft. JW: Writing–review and editing, TG: Conceptualization, Writing–original draft, Writing–review and editing. MB: Conceptualization, Writing–review and editing. SL: Supervision, Writing–review and editing.
The author(s) declare that financial support was received for the research, authorship, and/or publication of this article. This work is part of the project SEGIWA (Serienproduktion von Elektrolyseuren im Gigawatt-Bereich) funded by the BMBF under reference number 03HY121F.
The authors declare that the research was conducted in the absence of any commercial or financial relationships that could be construed as a potential conflict of interest.
All claims expressed in this article are solely those of the authors and do not necessarily represent those of their affiliated organizations, or those of the publisher, the editors and the reviewers. Any product that may be evaluated in this article, or claim that may be made by its manufacturer, is not guaranteed or endorsed by the publisher.
Alsharif, S., Huxoll, N., Raeiszadeh, A., Brandt, T., Brand, M., and Lehnhoff, S. (2023). “Digital twins for scaling up hydrogen electrolysis,” in ETG Congress 2023, 1–7.
Bellavista, P., Corradi, A., and Reale, A. (2014). Quality of service in wide scale publish—subscribe systems. IEEE Commun. Surv. Tutorials 16, 1591–1616. doi:10.1109/SURV.2014.031914.00192
BMBF (2022). Wasserstoff leitprojekte: H2giga: Serienfertigung, bundesministerium für bildung und forschung. Available at: https://www.wasserstoff-leitprojekte.de/leitprojekte/h2giga.
BMWi (2020). Die nationale wasserstoffstrategie 2020, bundesministerium für wirtschaft und energie. Available at: https://www.bmwk.de/Redaktion/DE/Publikationen/Energie/die-nationale-wasserstoffstrategie.html.
BMWK (2023). National hydrogen strategy update, federal ministry for economic affairs and climate action. Available at: https://www.bmwk.de/Redaktion/EN/Publikationen/Energie/national-hydrogen-strategy-update.pdf.
Braig, M., and Zeiler, P. (2023). Using data from similar systems for data-driven condition diagnosis and prognosis of engineering systems: a review and an outline of future research challenges. IEEE Access 11, 1506–1554. doi:10.1109/access.2022.3233220
Folgado, F. J., González, I., and Calderón, A. J. (2022). Pem electrolyser digital twin embedded within matlab-based graphical user interface. Eng. Proc. 19. doi:10.3390/ECP2022-12676
Glaessgen, E., and Stargel, D. (2012). The digital twin paradigm for future nasa and u.s. air force vehicles,” in 53rd AIAA/ASME/ASCE/AHS/ASC Struct. Struct. Dyn. Mater. Conference;lt;BR;gt;20th AIAA/ASME/AHS Adapt. Struct. Conference<BR>14th AIAA. doi:10.2514/6.2012-1818
Huxoll, N., Alsharif, S., and Diettrich, J. C., (2022). “Digital twin architecture and technologies for hydrogen electrolyser applications,” in Abstracts of the 11th DACH+ Conference on energy Informatics - volume 5, supplement 2 (Springer open), DACH+ Conference on energy Informatics, 6–8.
Kritzinger, W., Karner, M., Traar, G., Henjes, J., and Sihn, W. (2018). Digital twin in manufacturing: a categorical literature review and classification. IFAC-PapersOnLine 51, 1016–1022. 16th IFAC Symposium on Information Control Problems in Manufacturing INCOM 2018. doi:10.1016/j.ifacol.2018.08.474
Liu, M., Fang, S., Dong, H., and Xu, C. (2021). Review of digital twin about concepts, technologies, and industrial applications. J. Manuf. Syst. 58, 346–361. Digital Twin towards Smart Manufacturing and Industry 4.0. doi:10.1016/j.jmsy.2020.06.017
Liu, Z., Meyendorf, N., and Mrad, N. (2018). The role of data fusion in predictive maintenance using digital twin. AIP Conf. Proc. 1949, 020023. doi:10.1063/1.5031520
Meraghni, S., Terrissa, L. S., Yue, M., Ma, J., Jemei, S., and Zerhouni, N. (2021). A data-driven digital-twin prognostics method for proton exchange membrane fuel cell remaining useful life prediction. Int. J. Hydrogen Energy 46, 2555–2564. doi:10.1016/j.ijhydene.2020.10.108
Semeraro, C., Lezoche, M., Panetto, H., and Dassisti, M. (2021). Digital twin paradigm: a systematic literature review. Comput. Industry 130, 103469. doi:10.1016/j.compind.2021.103469
Shin, Y., Oh, J., Jang, D., and Shin, D. (2022). “Digital twin of alkaline water electrolysis systems for green hydrogen production,”. 14th international symposium on process systems engineering. Editors Y. Yamashita, and M. Kano (Elsevier of Computer Aided Chemical Engineering), 1483–1488.
Tao, F., Zhang, H., Liu, A., and Nee, A. Y. C. (2019a). Digital twin in industry: state-of-the-art. IEEE Trans. Industrial Inf. 15, 2405–2415. doi:10.1109/tii.2018.2873186
Tao, F., Zhang, M., and Nee, A. (2019b). “Chapter 3 - five-dimension digital twin modeling and its key technologies,” in Digital twin driven smart manufacturing. Editors F. Tao, M. Zhang, and A. Nee (Academic Press), 63–81.
Keywords: Digital Twin, Fleet Twin, electrolysers, green hydrogen, stream processing
Citation: Alsharif S, Huxoll N, Wibbeke J, Grimm T, Brand M and Lehnhoff S (2024) Digital Twin concept and architecture for fleets of hydrogen electrolysers. Front. Energy Effic. 2:1437214. doi: 10.3389/fenef.2024.1437214
Received: 23 May 2024; Accepted: 01 July 2024;
Published: 17 July 2024.
Edited by:
Xiao Hu, Northeast Electric Power University, ChinaReviewed by:
Hongye Zhao, Dalian University of Technology, ChinaCopyright © 2024 Alsharif, Huxoll, Wibbeke, Grimm, Brand and Lehnhoff. This is an open-access article distributed under the terms of the Creative Commons Attribution License (CC BY). The use, distribution or reproduction in other forums is permitted, provided the original author(s) and the copyright owner(s) are credited and that the original publication in this journal is cited, in accordance with accepted academic practice. No use, distribution or reproduction is permitted which does not comply with these terms.
*Correspondence: Sharaf Alsharif, c2hhcmFmLmFsZGluLmFsc2hhcmlmQG9mZmlzLmRl
Disclaimer: All claims expressed in this article are solely those of the authors and do not necessarily represent those of their affiliated organizations, or those of the publisher, the editors and the reviewers. Any product that may be evaluated in this article or claim that may be made by its manufacturer is not guaranteed or endorsed by the publisher.
Research integrity at Frontiers
Learn more about the work of our research integrity team to safeguard the quality of each article we publish.