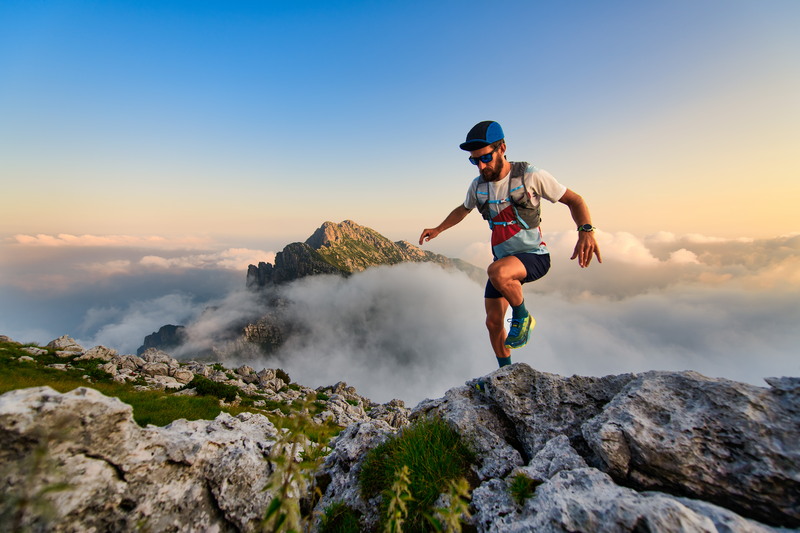
95% of researchers rate our articles as excellent or good
Learn more about the work of our research integrity team to safeguard the quality of each article we publish.
Find out more
ORIGINAL RESEARCH article
Front. Earth Sci. , 20 March 2025
Sec. Geohazards and Georisks
Volume 13 - 2025 | https://doi.org/10.3389/feart.2025.1556061
This article is part of the Research Topic Evolution Mechanism and Prevention Technology of Karst Geological Engineering Disasters View all 5 articles
Grouting technology is a crucial method for mitigating karst water inrush disasters. However, traditional grouting materials face significant limitations when addressing catastrophic karst water inrush under conditions of high-water pressure, large water inflow, and complex hydraulic environments. To overcome these challenges, this study developed a high-performance modified clay-cement grouting material. A series of indoor experiments were conducted to investigate the effects of the water-to-solid ratio, clay content, and modifier dosage on the material’s grouting performance. The optimal mix ratio was identified as water: cement: clay = 2:1:1, with an admixture dosage of 0.75%, by comparing the engineering performance of the new material against pure cement and traditional cement-clay grouting materials. The applicability and effectiveness of the developed grouting material were further validated in a practical engineering application within a water conservancy hub project in Guiping City, Guangxi Province. Results indicate that the new material not only effectively mitigates the risk of catastrophic karst water inrush but also offers advantages such as low cost, ecological benefits, and environmental sustainability. This study provides reliable technical support for emergency grouting applications and demonstrates potential for wider use.
With the rapid advancement of society and industrialization, changes in the hydrogeological environment and issues related to karst water inflow have increasingly become significant challenges in engineering construction (Zhang et al., 2018a; Li Y. et al., 2020; Cui and Tan, 2021; Cui et al., 2015; Yang and Zhang, 2016; Xu Z. et al., 2024). Karst water inflow is prevalent in regions with highly mobile groundwater, especially in fractured zones and areas with well-developed fissures in limestone and dolomite (Veress, 2020; De Waele et al., 2011; Li et al., 2016). Karst water inflow can result in sudden water and mud ingress during construction, increasing both construction difficulty and risk. Additionally, it poses long-term threats to the stability and durability of infrastructure (Gutiérrez et al., 2014; Song et al., 2012). Furthermore, dissolved minerals that are carried by inflowing water accelerate the erosion of engineering structures, potentially leading to foundation settlement, tunnel leakage, dam instability, and other serious issues (Cui et al., 2015). These hazards not only significantly increase remediation costs but also necessitate higher safety standards in engineering projects. Therefore, effectively controlling karst water inflow and mitigating its destructive impact on engineering works has become a pressing technical challenges in the field of geotechnical engineering.
Grouting technology is considered an effective solution for controlling karst water inflow. Its primary mechanism involves filling karst fractures and cavities with grouting materials to block the formation of water inflow channels and enhance rock mass stability (Zhang et al., 2018b; Li H. et al., 2020). Researchers have developed various grouting materials that are tailored to address karst water inflow issues (Cui et al., 2017; Shi et al., 2017; Zhenjun et al., 2024). Among these materials, cement-based grouting materials are widely used due to their high strength, broad availability, and adaptability. However, these materials also have several disadvantages, including high material consumption, difficulties in controlling diffusion, and poor environmental adaptability. These challenges are particularly evident in highly erosive karst water environments, where maintaining the long-term effectiveness of cement-based grouting is often challenging (Li Y. et al., 2020; Xu C. et al., 2024; Li et al., 2021). Additionally, the high carbon emissions that are associated with traditional cement-based materials conflict with current objectives of green and low-carbon development in the engineering sector (Zhang et al., 2019; Zhang et al., 2024). In recent years, modified cement materials have emerged as an important class of green building materials, and they are widely applied in underground engineering due to their low cost, ease of construction, high mechanical strength, and superior durability. In particular, the combination of cement and clay significantly improves grout fluidity and setting performance while enhancing filling capacity and compactness. However, traditional cement‒clay grouts still exhibit limitations in erosion resistance and impermeability under high water pressure and fast-flowing water conditions, making them insufficient for effectively managing karst water inflow.
This study aims to optimize the performance of cement‒clay grouting materials by incorporating modifiers to increase their adaptability under complex hydrogeological conditions. Based on the practical requirements of karst water inflow management, a novel high-performance modified cement‒clay grouting material was developed. The research systematically analyzed the effects of the water‒solid ratio, clay content, and modifier dosage on grouting material performance, and its effectiveness and feasibility were validated through practical engineering applications. This study not only introduces an innovative, efficient, economical, and environmentally friendly solution for managing karst water inflow but also provides theoretical and technical support for addressing engineering challenges under complex geological conditions.
The Datengxia Water Conservancy Project (Figure 1), approved by the State Council, is a flood control hub project for the Pearl River Basin and a landmark infrastructure project for the Pearl River–Xijiang Economic Belt and the “Xijiang Hundred-Million-Ton Golden Waterway.” It is a significant cooperative effort between Guangdong and Guangxi provinces and between Guangxi and Macao. Located at the outlet of the Datengxia Gorge on the Qianjiang River section of the Xijiang River system in the Pearl River Basin, approximately 6.6 km from the Qianjiang Bridge in Guiping, the Datengxia Water Conservancy Project is a large-scale multifunctional water conservancy project. Its functions include flood control, navigation, power generation, freshwater replenishment to combat saltwater intrusion, and irrigation, with the ship lock being one of its primary structures.
The ship lock foundation primarily comprises an upper Quaternary overburden layer and a lower bedrock layer. The bedrock consists of limestone and dolomite from the lower and middle sections of the Yujing Formation (D1y1-3 and D1y2 layers). The strata strike northeast, dip southeast, and have dip angles ranging from 20° to 22°, with interbedded formations as the dominant structure, along with minor thick-bedded and thin-bedded formations. Karst development is prominent in the limestone and dolomite of the Yujing Formation, characterized as a broad-valley-type buried karst system.
As the excavation of the ship lock foundation approached the designed foundation level, the volume of karst water inflow within the foundation pit showed a continuous increase. Three major water inflows were observed at the left slope toe of the pit, while one significant inflow occurred at the right slope toe, with a combined water inflow rate of approximately 3,800 m3/h. The high drainage volume required for the foundation pit led to elevated pumping costs and posed a risk of catastrophic karst water inflow. To prevent catastrophic water inflow that could flood the foundation pit and ensure construction safety, it was essential to implement emergency rescue measures and comprehensive karst water seepage management.
Cement primarily serves as a binder in grouting materials, generating strength and enhancing material stability through hydration reactions. The cement used in this study is Grade 42.5 ordinary Portland cement produced by the Hunan Biluo Cement Plant, meeting the national standards for Portland cement. The main performance indicators are shown in Table 1.
Clay primarily serves as a thickening agent in grouting materials, enhancing slurry viscosity, stability, and water retention while improving rheological properties. This contributes to better workability and filling performance of the slurry (Cui and Tan, 2021; Zhang et al., 2017). The clay used in this study was sourced from Changsha, Hunan Province, and its chemical composition is shown in Table 2.
The modifier in grouting materials enhances the compatibility between cement and clay, ensuring uniformity of the slurry. This effectively improves grouting performance and soil stability (Zhang et al., 2018b; He et al., 2020). The primary component of the modifier is meta-aluminate, and its dosage complies with relevant Chinese regulations. Due to its hygroscopic nature, the modifier must be stored in a dry environment.
The water-to-solid ratio, clay content, and modifier dosage are the primary factors influencing the rheological properties of grouting materials. In this study, the water-to-solid ratio (by mass) was set at 0.6, 1.0, and 1.5 (see Table 3), while the clay content was selected as 0%, 10%, 30%, and 45% of the cement mass. Based on prior laboratory experiments and field engineering practices (Güllü, 2015; Anagnostopoulos, 2014), the modifier dosage was set between 0.5% and 3.0% of the cement mass. Accordingly, in Table 4 the modifier dosages in this study were 0.25%, 0.5%, 0.75%, 1.0%, and 1.25% of the cement mass. To minimize experimental error, each scheme was tested three times, and the median value of the three results was used for final analysis. Where cement grouting material (CGM) was used as a control experiment.
Figure 2 shows the experimental testing. The rheological testing of grouting materials is used to evaluate their fluidity and injectability, providing a basis for optimizing construction parameters and predicting the material’s diffusion and coverage performance in soil. This helps improve grouting effectiveness and ensures construction quality. The rheological tests were conducted using an RSX SST rheometer (Brookfield Engineering, United States of America), which operates in controlled shear rate (RPM) and controlled shear stress (torque) modes. It characterizes the creep behavior, yield stress, and viscosity distribution of slurries, muds, and particulate materials. The accompanying Rheo3000 software supports PC control, enabling data acquisition and analysis, and allows for the processing of multiple test files.
Grouting materials applied to karst water inflows must possess anti-erosion capabilities to resist the scouring or dilution caused by high water flow velocities and quickly solidify in dynamic water environments to maintain stability. To evaluate the anti-erosion performance, the grouting materials were subjected to experiments under varying flow velocities in a water tank. The flow velocity was controlled using a water pump and set to 0.3 m/s, 0.6 m/s, 0.9 m/s, and 1.2 m/s, with a scouring duration of 60 s. The experimental procedure was as follows: first, the flow velocity was adjusted to the target value. Once the flow stabilized, the grouting material was placed in the water tank to begin the anti-erosion test. After 60 s, the experiment was stopped, and the remaining slurry was weighed to calculate the erosion retention rate.
Consistency and setting time are key parameters that affect grouting activities. Consistency is an important indicator for evaluating the fluidity of the slurry during the pumping process, while setting time directly influences the control of the grouting process. By assessing the consistency and setting time of the slurry, the diffusion radius can be effectively controlled. In this study, the consistency and setting time of the slurry were measured using a mortar consistency tester. The initial setting time of the slurry was determined by pouring the slurry into a beaker inclined at 45° and recording the time required for the slurry to stop flowing.
The mechanical properties of the hardened slurry, including compressive strength and permeability coefficient, are important indicators for evaluating grouting quality. In this experiment, a concrete compression testing machine was used to test the compressive strength of cubic samples with a side length of 70.7 mm. The hardened slurry was tested at three different curing periods: 3 days, 7 days, and 28 days, under standard curing conditions.
Figure 3 shows the rheological curves of the cement‒clay slurry at different water‒solid ratios. The results indicate that when the water‒solid ratio is 0.6:1, the cement‒clay slurry behaves as a Bingham fluid, with yield stress gradually increasing as clay content increases (Choi et al., 2016). When the water-solid ratio is 1:1, the rheological behavior of slurries with 0% and 15% clay content is similar, and both exhibited shear-thinning characteristics typical of a power-law fluid (expanding fluid), where shear stress increases with shear rate. As the clay content increases to 30% and 45%, the slurry transitions to a Bingham fluid, with shear-thinning behavior observed only when the clay content is 30%. At a water-to-solid ratio of 1.5:1, the cement‒clay slurry continues to exhibit Bingham fluid behavior. Although clay content significantly influences the slurry’s rheological curve, its overall rheological behavior remains consistent with the Bingham fluid model. When the shear rate is below 15 s–1, the slurry’s initial viscosity approaches that of water (0 Pas) due to the higher water-solid ratio, resulting in a shear stress of 0 Pa. As the slurry begins to set, both viscosity and shear stress gradually increase.
Figure 3. Rheological curves of CCGM with different water-solid ratios. (A) Water-solid ratio of 0.6:1. (B) Water/solid ratio of 1:1.(C) water-solid ratio of 1.5:1.
Figure 4 presents the rheological curves of modified cement‒clay slurry with different amounts of modifier. When the modifier content is 0.25% and 0.50%, the slurry exhibits Bingham fluid characteristics. As the modifier content increases to 0.75%, 1.0%, and 1.25%, the slurry transitions to a pseudoplastic fluid (Herschel-Bulkley fluid) (Rahman et al., 2017), with an initial shear yield value exceeding 20 Pa. When the modifier content exceeds 0.75%, the shear stress of the slurry first decreases before stabilizing as the shear rate increases. This phenomenon may be attributed to the disruption of the internal structure of the slurry at higher shear rates, which reduces structural resistance and ultimately leads to a decrease in viscosity. As structural breakdown continues, shear stress stabilizes at a constant value. A comparison of static yield stress and dynamic yield stress can further clarify this mechanism. When the modifier content exceeds 0.75%, the stable shear stress of the slurry tends to become consistent. At a specific shear rate, increasing the modifier content initially increases shear stress, but further increases result in little significant change.
Figure 5 illustrates the viscosity curves of cement‒clay slurry at different water‒solid ratios. When the water‒solid ratio is 0.6:1 and the clay content is 0% or 15%, the slurry viscosity shows minimal variation over time. However, as the clay content increases to 30% and 45%, viscosity increases rapidly before stabilizing at approximately 40 min. At a water‒solid ratio of 1:1, viscosity initially decreases before increasing, with higher initial viscosity observed with higher clay contents. For a water‒solid ratio of 1.5:1, the viscosity of the slurry with 0% clay remains at zero initially but gradually increases over time. Other slurries follow a trend of decreasing viscosity followed by increased viscosity. Except for the slurry with 45% clay content, all the others exhibit an initial viscosity of zero.
Figure 5. Viscosity of CCGM with different water-solid ratios. (A) Water-solid ratio of 0.6:1. (B) Water-solid ratio of 1:1. (C) Water-solid ratio of 1.5:1.
The observed trend of viscosity decreasing and then increasing over time can be attributed to the instability of slurries with higher water‒solid ratios, which promote rapid separation of water from the slurry. During this segregation process, slurry viscosity decreases. Once water segregation is complete, the slurry begins to coagulate, leading to a subsequent increase in viscosity.
Figure 6 shows the effect of different modifier dosages on the viscosity changes of modified clay-cement slurry over time. The viscosity of the modified slurry initially increases before gradually stabilizing. The trend indicates that the continuous generation of hydration products leads to a progressive increase in viscosity throughout the hydration process, with a sustained increase as the hydration time extends. Additionally, the time required for viscosity stabilization is delayed with increasing modifier dosage.
The results indicate that viscosity stabilization time is closely related to hydration duration. Additionally, slurries with the same clay content but varying modifier dosages exhibit similar viscosity trends, suggesting that clay content is the primary factor influencing slurry viscosity.
When a suspension is at rest, particles collide due to shear forces and Brownian motion, eventually forming flocs. However, under shear stress, these flocs break apart, decreasing in size as shear rate increases, leading to a reduction in viscosity. This phenomenon, known as thixotropy, has also been observed in other fluids (Wallevik, 2009; Mardani-Aghabaglou et al., 2021). Figure 7 illustrates the thixotropic behavior of modified clay-cement slurries prepared with different dosages of modifiers. The modifier dosage significantly affects the slurry’s thixotropy, resulting in complex changes.
The effect of modifier dosage on the thixotropy of modified cement‒clay slurry is evident in several aspects. When the modifier dosage is relatively high (≥1.25%), the slurry exhibits coagulation behavior and transitions into a plastic state. Under external forces, such as sustained shear stress, intermolecular forces weaken or disappear, leading to structural degradation within the slurry. This structural degradation reduces strength and consistency. When the external force is removed, molecular recombination occurs, but the slurry strength does not fully recover to its original state, demonstrating typical thixotropic behavior. In contrast, when the modifier dosage is relatively low (<0.75%), intermolecular bonding forces within the slurry are weaker, and Brownian motion is more pronounced. As the cement hydration reaction progresses, the consistency of the slurry gradually increases. At the same shear rate, the shear stress of the upward flow curve is consistently lower than that of the downward flow curve, reflecting the rheological characteristics of the slurry.
The results of the erosion resistance experiments are shown in Figure 8. As shown in the figure, cement slurry exhibits the poorest erosion resistance, with a retention rate of only 32% at a flow velocity of 1.2 m/s. In contrast, the retention rate of cement‒clay slurry is 22% higher than that of cement slurry, which can be attributed to clay particles filling the voids within the slurry. Additionally, the water absorption and slight swelling of clay particles reduce the porosity and enhance the compactness of the hardened material, thereby improving erosion resistance. The modified cement‒clay slurry, with the addition of modifiers, demonstrates superior erosion resistance across all flow velocities compared to the other two slurries. This improvement is attributed to the modifier reducing slurry dispersibility, thereby minimizing particle loss and peeling in erosive environments. Furthermore, the modifier optimizes the internal microstructure of the slurry, resulting in a more compact and uniform hardened material, significantly enhancing its erosion resistance. Based on this analysis, modified cement‒clay slurry is well-suited for high-flow velocity conditions, such as karst water inrush conditions.
Table 5 presents the setting times of various grouting materials. The results indicate that cement‒clay slurry has the longest setting time, followed by pure cement slurry, while the modified cement‒clay slurry exhibits a significantly reduced setting time compared to the other two materials. Specifically, the setting time of CCGM increased by 16.2%, whereas that of MCCGM decreased by 50.7% compared to CGM. The prolonged setting time of cement‒clay slurry is primarily due to its lower cementitious material content and the strong water absorption capacity of clay. Clay particles absorb free water, slowing the hydration rate of cement particles and extending the setting time. In contrast, the modifier in the modified cement‒clay slurry rapidly stimulates the hydration reactions of both cement and clay, accelerating the formation of C‒S‒H gel. This promotes the rapid development of a stable gel network within the slurry, thereby significantly shortening its setting time.
Table 5 presents the bleeding rates of various grouting materials, showing that the incorporation of clay and modifiers significantly reduces the bleeding rate. Compared to pure cement grouting material, the bleeding rates of cement‒clay grouting material and modified cement‒clay grouting material decreased by 50.6% and 84.7%, respectively. This reduction can be attributed to the properties of clay, including pore-filling and water-absorbing expansion. The fine clay particles fill microvoids within the grouting material and swell upon water absorption, sealing channels and enhancing the material’s compactness. Furthermore, the modifier accelerates cement hydration, generating denser hydration products that further reduce the bleeding rate. Table 5 also presents the volumetric shrinkage rates of the grouting materials, which follow a trend consistent with the bleeding rates. The modified cement‒clay grouting material exhibits a significantly lower volumetric shrinkage rate than the other two materials. This is because the modifier not only promotes the generation of additional cementitious materials but also enhances the uniformity and anti-segregation properties of the slurry, thereby minimizing volumetric shrinkage. In conclusion, the modified cement‒clay grouting material offers significant advantages for engineering applications, particularly in managing karst water inflow environments.
Figure 9 shows the compressive strength of the solidified bodies of each slurry at different curing ages. As shown in the figure, the compressive strength of the cement slurry solidified bodies is significantly higher than that of the other two slurries at all curing ages. Additionally, the solidified bodies of the modified cement‒clay slurry exhibit higher early compressive strength than those of the cement‒clay slurry. The decrease in compressive strength of the cement‒clay slurry solidified bodies can be attributed to the partial replacement of cement with clay, which reduces the effective cement content in the paste. This leads to a lower generation of hydration products, thereby decreasing compressive strength. However, the addition of the modifier accelerates early hydration reactions, enabling the modified cement‒clay slurry to achieve a compressive strength of 1.4 MPa at the 3-day curing age, surpassing the cement‒clay slurry, which has a strength of 2.1 MPa. Thus, the modified cement‒clay slurry exhibits a higher early strength gain.
The treatment of karst groundwater inflow was influenced by geological conditions and the overall project schedule. The treatment was carried out using methods that involved blocking inflow points and reverse grouting. The grouting process was carried out as follows: First, loose debris and silt at each inflow point were removed to expose the karst water channels or fractures as much as possible. The removal area was determined based on the actual conditions at each inflow point on-site. Next, a diversion (grouting) pipe was inserted into the karst water channel. The diversion (grouting) pipe was selected, and different diameters of steel pipes were used depending on the channel size. The length of the steel pipe was adjusted based on the inflow volume and burial depth of each inflow point. The underground section of the steel pipe and its mouth were wrapped with two layers of nonwoven geotextile to maximize water redirection into the pipe. A gate valve was installed at the exposed outlet of the steel pipe. Subsequently, as can be seen in Figure 10, concrete was applied to add weight, while a setting accelerator and dispersant were incorporated to minimize slurry loss. As shown in Figure 11, during the initial grouting phase, cement slurry was used to establish a channel for subsequent grouting, preventing excessive plugging pressure in later stages that could lead to the lifting of the sealing concrete.
It can be seen from Figure 12, after backfilling the centralized seepage points, the gushing water in the pit was reduced from 4,200 m3/h to 1,400 m3/h. Additionally, the quality of the gushing water improved, becoming clearer. The reduction in total water inflow by more than two-thirds resulted in the distribution of water entry points no longer being centralized, significantly lowering the risk of catastrophic water inflow and ensuring that the lock pits remained under control. Through this counter-irrigation treatment, the water surge problem was effectively solved. Following the completion of the construction, excavation in the treated area resumed without any recurrence of sudden water influx, confirming that the counter-irrigation treatment effectively sealed the water influx channel. This construction method offers an effective approach for addressing similar water influx issues, especially in cases of sudden water influx during pit excavation. By effectively reducing water inflow, the method can ensure pit construction safety. The pit karst surge water backfilling treatment method is especially suitable for managing sudden groundwater surges in projects of a similar engineering nature.
To address challenging issues such as sudden karst water influx, which is common in engineering, this paper develops a kind of inexpensive, low-carbon, and environmentally friendly modified clay-cement grouting material using cement, clay, and a modifier. The main conclusions are as follows:
1. Experimental research determined that the optimal ratio for the modified clay-cement grouting materials is water:cement:clay = 2:1:1, with a modifier dosage of 0.75%. This ratio improves the fluidity and compressive strength of the material, making it suitable for grouting under high water pressure and complex hydraulic conditions.
2. The modified cement‒clay slurry exhibited better scour resistance than traditional cement-based materials under varying water flow rates. The addition of the modifier effectively reduces slurry dispersion, thereby enhancing scour resistance. This characteristic makes it particularly suitable for rapid water flow scenarios, such as karst surges.
3. The study shows that the percolation rate of the modified cement‒clay grouting material is significantly lower than that of traditional cement grouting material, by 50.6% and 84.7%, respectively. This indicates that the modified material exhibits superior densification and durability in karst water surge management, effectively preventing water infiltration and improving the durability and stability of the grouting material.
4. In the actual application of the project, the modified cement-clay grouting material shows good applicability and effectiveness, providing an efficient, economical, and environmentally friendly solution for controlling karst water influx. Moreover, this material has a wide range of potential applications.
The raw data supporting the conclusions of this article will be made available by the authors, without undue reservation.
JL: Conceptualization, Investigation, Methodology, Writing–original draft. ZS: Conceptualization, Methodology, Writing–review and editing. ZF: Data curation, Writing–review and editing. XW: Data curation, Writing–review and editing.
The author(s) declare that no financial support was received for the research, authorship, and/or publication of this article.
The authors declare that the research was conducted in the absence of any commercial or financial relationships that could be construed as a potential conflict of interest.
The author(s) declare that no Generative AI was used in the creation of this manuscript.
All claims expressed in this article are solely those of the authors and do not necessarily represent those of their affiliated organizations, or those of the publisher, the editors and the reviewers. Any product that may be evaluated in this article, or claim that may be made by its manufacturer, is not guaranteed or endorsed by the publisher.
Anagnostopoulos, C. A. (2014). Effect of different superplasticisers on the physical and mechanical properties of cement grouts. Constr. Build. Mater 50, 162–168. doi:10.1016/j.conbuildmat.2013.09.050
Choi, M., Park, K., and Oh, T. (2016). Viscoelastic properties of fresh cement paste to study the flow behavior. Int. J. Concr. Struct. M. 10, 65–74. doi:10.1007/s40069-016-0158-3
Cui, Q., Wu, H., Shen, S., Xu, Y., and Ye, G. (2015). Chinese karst geology and measures to prevent geohazards during shield tunnelling in karst region with caves. Nat. Hazards 77, 129–152. doi:10.1007/s11069-014-1585-6
Cui, W., Huang, J., Song, H., and Xiao, M. (2017). Development of two new anti-washout grouting materials using multi-way ANOVA in conjunction with grey relational analysis. Constr. Build. Mater 156, 184–198. doi:10.1016/j.conbuildmat.2017.08.126
Cui, Y., and Tan, Z. (2021). Experimental study of high performance synchronous grouting materials prepared with clay. Materials 14, 1362. doi:10.3390/ma14061362
De Waele, J., Gutiérrez, F., Parise, M., and Plan, L. (2011). Geomorphology and natural hazards in karst areas: a review. Geomorphology 134, 1–8. doi:10.1016/j.geomorph.2011.08.001
Güllü, H. (2015). On the viscous behavior of cement mixtures with clay, sand, lime and bottom ash for jet grouting. Constr. Build. Mater 93, 891–910. doi:10.1016/j.conbuildmat.2015.05.072
Gutiérrez, F., Parise, M., De Waele, J., and Jourde, H. (2014). A review on natural and human-induced geohazards and impacts in karst. Earth-Sci Rev. 138, 61–88. doi:10.1016/j.earscirev.2014.08.002
He, S., Lai, J., Wang, L., and Wang, K. (2020). A literature review on properties and applications of grouts for shield tunnel. Constr. Build. Mater 239, 117782. doi:10.1016/j.conbuildmat.2019.117782
Li, H., Zhang, Y., Wu, J., Zhang, X., Zhang, L., and Li, Z. (2020b). Grouting sealing mechanism of water gushing in karst pipelines and engineering application. Constr. Build. Mater 254, 119250. doi:10.1016/j.conbuildmat.2020.119250
Li, S., Liu, R., Zhang, Q., and Zhang, X. (2016). Protection against water or mud inrush in tunnels by grouting: a review. J. Rock Mech. Geotech. 8, 753–766. doi:10.1016/j.jrmge.2016.05.002
Li, S., Ma, C., Liu, R., Chen, M., Yan, J., Wang, Z., et al. (2021). Super-absorbent swellable polymer as grouting material for treatment of karst water inrush. Int. J. Min. Sci. Techno 31, 753–763. doi:10.1016/j.ijmst.2021.06.004
Li, Y., Zhang, G., Jiang, H., Liu, Y., and Kuang, C. (2020a). Performance assessment of a newly developed and highly stable sandy cementitious grout for karst aquifers in China. Environ. Earth Sci. 79, 153–211. doi:10.1007/s12665-020-8894-8
Mardani-Aghabaglou, A., Kankal, M., Nacar, S., Felekoğlu, B., and Ramyar, K. (2021). Assessment of cement characteristics affecting rheological properties of cement pastes. Neural Comput. Appl. 33, 12805–12826. doi:10.1007/s00521-021-05925-8
Rahman, M., Wiklund, J., Kotzé, R., and Håkansson, U. (2017). Yield stress of cement grouts. Tunn. Undergr. Sp. Tech. 61, 50–60. doi:10.1016/j.tust.2016.09.009
Shi, H., Bai, M., and Xing, S. (2017). Mechanics parameter optimization and evaluation of curtain grouting material in deep, water-rich karst tunnels. Adv. Mater Sci. Eng. 2017, 1853951–1854012. doi:10.1155/2017/1853951
Song, K., Cho, G., and Chang, S. (2012). Identification, remediation, and analysis of karst sinkholes in the longest railroad tunnel in South Korea. Eng. Geol. 135, 92–105. doi:10.1016/j.enggeo.2012.02.018
Veress, M. (2020). Karst types and their karstification. J. Earth Sci-China 31, 621–634. doi:10.1007/s12583-020-1306-x
Wallevik, J. E. (2009). Rheological properties of cement paste: thixotropic behavior and structural breakdown. Cem. Concr. Res. 39, 14–29. doi:10.1016/j.cemconres.2008.10.001
Xu, C., Lei, X., Han, L., Lang, L., Chen, Z., Fu, S., et al. (2024b). Investigation the engineering properties and environmental impact of electrolytic manganese residue-based grouting materials for karst application. Constr. Build. Mater 457, 139344. doi:10.1016/j.conbuildmat.2024.139344
Xu, Z., Zhang, Z., Cao, C., Wu, Z., and Dong, T. (2024a). Progressive assessment of water inrush disasters in pre-construction and construction phases based on Chinese tunnels research. Carbonate Evaporite 39, 50. doi:10.1007/s13146-024-00958-1
Yang, Z., and Zhang, J. (2016). Minimum safe thickness of rock plug in karst tunnel according to upper bound theorem. J. Cent. South Univ. 23, 2346–2353. doi:10.1007/s11771-016-3293-8
Zhang, C., Fu, J., Yang, J., Ou, X., Ye, X., and Zhang, Y. (2018b). Formulation and performance of grouting materials for underwater shield tunnel construction in karst ground. Constr. Build. Mater 187, 327–338. doi:10.1016/j.conbuildmat.2018.07.054
Zhang, C., Yang, J., Fu, J., Ou, X., Xie, Y., Dai, Y., et al. (2019). A new clay-cement composite grouting material for tunnelling in underwater karst area. J. Cent. South Univ. 26, 1863–1873. doi:10.1007/s11771-019-4140-5
Zhang, C., Yang, J., Ou, X., Fu, J., Xie, Y., and Liang, X. (2018a). Clay dosage and water/cement ratio of clay-cement grout for optimal engineering performance. Appl. Clay Sci. 163, 312–318. doi:10.1016/j.clay.2018.07.035
Zhang, C., Zhou, J., Zheng, X., Yang, J., Zhan, S., and Yang, L. (2024). A novel water-swelling grouting material formulation and its performance for water rushing in karst strata. Constr. Build. Mater 416, 135245. doi:10.1016/j.conbuildmat.2024.135245
Zhang, G., Liu, J., Li, Y., and Liang, J. (2017). A pasty clay–cement grouting material for soft and loose ground under groundwater conditions. Adv. Cem. Res. 29, 54–62. doi:10.1680/jadcr.16.00079
Keywords: grouting, karst water gushing, grouting material, admixture, rheological properties
Citation: Liang J, Song Z, Fan Z and Wang X (2025) Study and application of a novel high-performance grouting material in the management of karst water inrush disasters. Front. Earth Sci. 13:1556061. doi: 10.3389/feart.2025.1556061
Received: 06 January 2025; Accepted: 24 February 2025;
Published: 20 March 2025.
Edited by:
Pengfei Liu, CCCC Second Harbor Engineering Co., Ltd., ChinaReviewed by:
Kaiwen Liu, Southwest Jiaotong University, ChinaCopyright © 2025 Liang, Song, Fan and Wang. This is an open-access article distributed under the terms of the Creative Commons Attribution License (CC BY). The use, distribution or reproduction in other forums is permitted, provided the original author(s) and the copyright owner(s) are credited and that the original publication in this journal is cited, in accordance with accepted academic practice. No use, distribution or reproduction is permitted which does not comply with these terms.
*Correspondence: Zilong Song, NzY1ODE0MzdAcXEuY29t
Disclaimer: All claims expressed in this article are solely those of the authors and do not necessarily represent those of their affiliated organizations, or those of the publisher, the editors and the reviewers. Any product that may be evaluated in this article or claim that may be made by its manufacturer is not guaranteed or endorsed by the publisher.
Research integrity at Frontiers
Learn more about the work of our research integrity team to safeguard the quality of each article we publish.