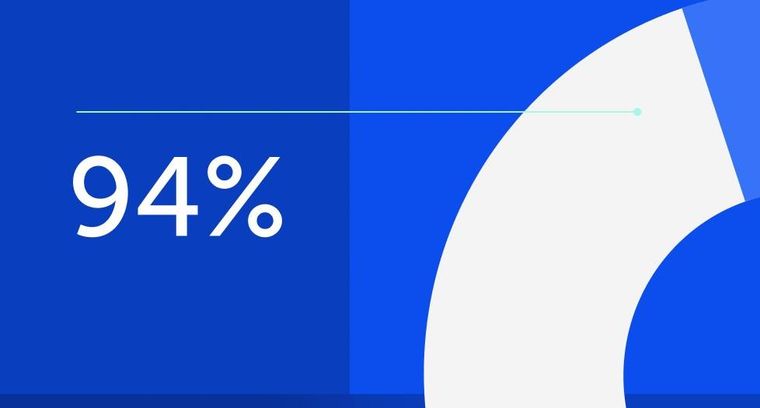
94% of researchers rate our articles as excellent or good
Learn more about the work of our research integrity team to safeguard the quality of each article we publish.
Find out more
ORIGINAL RESEARCH article
Front. Earth Sci., 26 March 2025
Sec. Solid Earth Geophysics
Volume 13 - 2025 | https://doi.org/10.3389/feart.2025.1549906
This article is part of the Research TopicAdvanced Materials and Technologies for Sustainable Development of Underground ResourcesView all 44 articles
In the process of coal mining, pressure will be induced in the working face, resulting in the stress concentration of surrounding rock, which will affect the safety and orderly normal operation of coal energy mining. The all-fiber optic micro-seismic monitoring technology offers advantages such as high sensitivity, wide dynamic range, and passive front-end intrinsic safety, resolving the conflict between high sensitivity and broadband frequency response. This technology enhances both the sensitivity and frequency response range of micro-seismic monitoring, enabling effective real-time monitoring of pressure-related activities in coal mines. Taking the II1012 working face of Taoyuan Coal Mine as the engineering background, the all-fiber optic micro-seismic monitoring work is carried out, and the data are analyzed by the methods of micro-seismic event detection, identification, classification and location. The characteristics of micro-seismic activity during the first weighting (the mine pressure appears before and after the primary fracture of the basic roof), periodic weighting (the mine pressure of the old roof is manifested by periodic fracture or collapse) and square pressure (the mining pressure of the working face is equivalent to the length of the cutting hole) are studied. The results show that: High-energy events in the first weighting stage play a major role in roof failure. In the periodic weighting stage, the influence of micro-seismic activity on the roof is greater than that on the floor, but the influence on the floor is increasing. The high-energy events increase significantly in the square pressure stage, which is easy to promote the frequent occurrence of high intensity and stress micro-seismic activities. The occurrence of micro-seismic events in mine pressure phases have advanced characteristics. There is a positive correlation between the intensity of micro-seismic activity and the rate of recovery, and the all-fiber optic micro-seismic has a good response to the mine pressure. The research work provides theoretical basis and technical support guidance for the safe production of the II1012 working face in Taoyuan Coal Mine and other similar working faces in other coal mines, reduces the risk of geological disasters caused by micro-seismic events during the pressure period, and further guarantees the safe and normal orderly development of the subsequent production work of the working face. It is of great significance to the safe mining of coal energy and the supply of production and life.
As a common dynamic disaster phenomenon in the process of coal mining, mine pressure often leads to roof fall, landslide, mine earthquake, rock burst and other accidents, which pose a serious threat and influence on the life safety of miners and the production efficiency of mines. The occurrence of disasters caused by mine pressure is closely related to rock mass fracture, and the abnormal mechanical response of rock mass is the precursor in-formation of disasters. Therefore, real-time monitoring of rock mass mechanical response is an important means to realize geological disaster early warning. Liu et al. (2024) developed a coal mine disaster monitoring, early warning and prevention platform based on geological support system, which effectively reduced the incidence of disaster accidents and promoted the intelligent construction of coal mines. Zheng et al. (2024), Zheng et al. (2025) studied the evolution process of rock damage by tomography, and monitored the velocity evolution of rock by acoustic emission, which provided a new way for monitoring rock activity in mines.
Monitoring mine pressure activities and taking relevant supporting measures are of great significance to control the influence of mine pressure and ensure safe production. He Y. L. et al. (2021) studied the mining pressure development law of mining roadway and optimized the width of coal pillar, which could further strengthen the optimization of roadway support parameters, improve the stability of surrounding rock, and form a “support - pressure relief” collaborative control technology system. Li J. Z. et al. (2023)used geological survey, displacement monitoring, numerical simulation and other methods to study the mining ground pressure development mechanism under the influence of geological structure. Other scholars have also studied it through traditional methods such as electrical method (He Z. Q. et al., 2021) and laser scanning (Zhu et al., 2025), but there are problems such as limited monitoring range, discontinuous data and poor real-time performance, which are difficult to meet the needs of modern coal mine safety production.
By capturing micro-fracture signals of rock mass, micro-seismic monitoring technology can provide early warning of dynamic disasters, achieve high-precision continuous monitoring, and obtain strong spatiotemporal information of micro-seismic events (Li et al., 2022). It has extensive and advanced application in tunnel rock burst (Yang et al., 2023), coal and gas outburst (Lu et al., 2012), slope instability (Srinivasan et al., 2015), water damage prevention (Zuo et al., 2022), coal mine rock burst (Cao et al., 2016) and so on. At present, the traditional electrical monitoring technology is widely used in mine safety monitoring, which is easy to be disturbed by environmental temperature and humidity, electromagnetic and so on, and has a wide limited area and is unstable. The development and application of multi-scale rock mass mechanical response sensing equipment, especially optical fiber sensing equipment, has created conditions for coordinating the relationship between production and safety. Optical fiber sensors can change the intensity, frequency and other characteristic information of incident light (Yang et al., 2020), and play an important role in road traffic (Wang et al., 2023), geological disasters (Anjana et al., 2024) and other fields. Optical fiber sensing monitoring technology has become the focus of applied research on mine safety monitoring. The application of optical fiber micro-seismic monitoring equipment in mine safety production is constantly expanding, meeting the needs of monitoring under harsh mining environment. Effective micro-seismic events can be selected from massive data (Song et al., 2020), which is of great significance for mine pressure safety monitoring and early warning. The optical fiber is used as the sensing medium to capture micro-seismic events by detecting the changes of optical signals in the optical fiber, and has the advantages of high sensitivity, wide frequency response, large dynamic range, front-end passive intrinsic safety, etc. It can monitor the pressure activity in real time and accurately record the characteristics of the surrounding rock stress changes caused by pressure in the production process. It can provide a solid foundation for mine safe and efficient production.
Taking the II1012 working face of Taoyuan Coal Mine in Suzhou City as the research object, the all-fiber optic micro-seismic monitoring system was established for the working face. Through the collection and analysis of micro-seismic signals, the failure location, energy and possible affected area of micro-cracks are accurately calculated, and the data characteristics of micro-seismic events during the mining pressure period in the process of mining at the working face are further analyzed, and the relevant laws are explored. The re-search work provides data and technical support for the safe mining of Taoyuan Coal Mine, which is conducive to the normal mining of Taoyuan Coal Mine.
This paper takes the II1012 working face of Taoyuan Coal Mine in Suzhou City, Anhui Province as the engineering background, and establishes an all-fiber optic micro-seismic monitoring system for the working face. Through on-site exploration to understand the geological conditions, the monitoring system is designed, which mainly includes determining the installation position and mode of the sensor, laying the cable, in-stalling the monitoring host, and connecting and debugging the overall equipment. The all-fiber optic micro-seismic monitoring system runs in the whole process of production work in the working face, and completes the collection and preliminary processing of micro-seismic data through micro-seismic event detection, identification and classification, and positioning. For the data collected and preliminarily processed by the monitoring system, it is necessary to further screen and process manually. The main steps include event waveform recognition, waveform first arrival picking and recalculation to obtain more ac-curate positioning, energy, magnitude and other information of event data. Finally, the data of micro-seismic events in the research period are counted, processed, analyzed and studied, and the mine pressure characteristics of the working face based on all-fiber optic micro-seismic monitoring are obtained. The overall research process is shown in Figure 1.
Taoyuan Coal Mine is located in Taoyuan Town in Yongqiao District, Suzhou City, Anhui Province, about 11 km to the north of Suzhou City, and the administrative division is under the jurisdiction of Yongqiao District, as shown in Figure 2. II1012 working face is located in the first stage of the north wing of II1 mining area, and its upper section is the goaf under 1,019 and 10,110. It is near the seven# exploration line to the northeast of the open-off cut of the working face, and near the boundary of the scour area of the ancient river bed to the southwest of the cutting line. The strike length of the working face is 1,276∼1,368 m, the inclined width is 148–161 m, and the area is 204,910 m2. The cutting length of the working face is about 150 m, and the elevation of the working face is −672∼-590 m. The II1012 mining face is shown in Figure 3.
The total thickness of the 10 coal seam in the excavation block of the II1012 working face is 0∼7.4 m, with an average of 3.8 m. Most of the coal seam contain mud and silty ton-stein, and the thickness of the tonstein is 0∼1.8 m, with an average of 0.5 m. The immediate roof of the coal seam is mudstone, and the main roof is siltstone. The immediate floor is mudstone, the hard floor is siltstone. The roof and floor of the coal seam are shown in Table 1. The dip Angle of the coal (rock) bed is 10°∼32°, with an average of 22°. The working face of II1012 in Taoyuan Coal Mine is a monoclinal structure with a strike of NNE and a tendency of SEE. The working face has wide and gentle fluctuation along the strike coal seam. According to the data of 3D seismic survey, borehole drilling and excavation, 25 faults are developed in the working face, and there is no water cut and no water diversion after excavation. The faults of F10, F14 and F20 have great influence on the mining work, and there are no abnormal geological structures such as igneous rock intrusion area, collapse column and structural window in the working face.
In this paper, the all-fiber optic micro-seismic monitoring system is mainly used to monitor the micro-seismic events occurring in the mining process of II1012 working face of Taoyuan Coal Mine. The micro-seismic events generated in the underground mining work are collected by arranging acceleration sensors on the working face, and then the collected events are transmitted to the ground data processing terminal through the micro-seismic monitoring host. The micro-seismic event data are processed by event detection, identification and classification, positioning calculation, etc., and the processed micro-seismic data are obtained, and then the characteristics and laws of micro-seismic events in mine pressure activities during the mining process are studied.
The rock is destroyed under the action of stress and micro-seismic is generated. The data are collected in real time by arranging multiple sensors. After data processing, the location of micro-seismic events can be determined. Micro-seismic is essentially a process of stress accumulation and intermittent release. With the continuous accumulation of energy, when the rock mass does not have sufficient strength conditions to bear high energy and high stress, energy will be released in the form of roof and floor cracking or breaking, resulting in the generation and expansion of micro-cracks and micro-seismic events. The micro-seismic monitoring host uses the light source generated by the fiber laser to form the optical fiber micro-seismic monitoring array through the space division, time division or wavelength division multiplexing network. The micro-vibration collected by the fiber optic sensor is converted into a digital signal through the signal acquisition and demodulation module, which is transmitted to the micro-seismic processing platform for analysis, positioning, processing and storage.
The all-fiber optic micro-seismic monitoring system includes low-noise narrow line-width fiber laser, fiber acceleration sensors, high speed fidelity demodulation, positioning interpretation module, and 3D visualization analysis system, as shown in Figure 4. All-fiber optic micro-seismic monitoring technology solves the contradiction between high sensitivity and wide frequency response, so that the sensitivity of micro-seismic monitoring is improved and the frequency band response range is increased.
The difference between the all-fiber optic micro-seismic monitoring technology and the traditional monitoring technology is shown in Table 2.
Table 2. Comparison of differences between all-fiber optic micro-seismic and traditional monitoring technology.
The all-fiber optic micro-seismic monitoring system based on the II1012 working face of Taoyuan Coal Mine adopts acceleration sensors, and the response frequency of the sensor ranges from 10 Hz to 5 kHz. The acceleration sensor is composed of passive all-optical devices, and its superior optical characteristics make the monitoring radius of a single sensor reach 200–300 m, and it can monitor micro-seismic activities for a long time in the coal mine without electrification, with strong anti-interference ability and high signal-to-noise ratio.
According to the geological condition of Taoyuan Coal Mine, in the current mining operation of II1012 working face, 16 sensors are used for data acquisition and transmission. The sensor number of transportation roadway is 1→8, and the sensor number of return-air roadway is 9→16, as shown in Figure 5. The distance between two adjacent sensors on the same roadway is about 110 m.
The monitoring system layout is designed according to the principles of all-fiber acceleration sensor installation and micro-seismic network layout, as shown in Figure 6. The all-fiber optic micro-seismic monitoring system is composed of three parts: monitoring host, optical fiber sensors and signal transmission system. During the mining process of Taoyuan Coal Mine II1012 working face, micro-seismic signals are generated due to rock fracture. These signals are received by the acceleration sensors in the mine and transmitted to the micro-seismic monitoring host through optical cable, and then transmitted to the data server on the ground through the communication optical cable. After being filtered by the data server, the data is transmitted to the engineering analysis center through the Internet, and data service engineers process and analyze the data.
Figure 6. Layout diagram of all-fiber optic micro-seismic monitoring system for II1012 working face.
The micro-seismic data processing methods used in this paper mainly include micro-seismic event detection, event recognition and classification, micro-seismic location algorithm, statistical analysis and so on.
The STA/LTA algorithm is widely used in seismic wave recognition because of its simple algorithm, fast speed and easy real-time processing (Shi H. et al., 2023). This algorithm was first proposed by Stevenson. STA is the short-time window average, which represents the change trend of signal amplitude and energy. LTA is the mean value of the long-term window, which represents the change trend of the signal background noise and energy (Yoones and Mirko, 2015). The principle is to use the ratio of STA and LTA to reflect the change in signal energy or level, when the ratio is greater than a pre-set threshold, it is considered that an event has occurred. The STA/LTA algorithm calculation equations are as shown in Equations 1-3.
Where,
Combined with the above formula and the geological conditions of the working face, the duration of micro-seismic events and other realistic conditions, in order to reduce noise interference and ensure that high-frequency and low-frequency micro-seismic events are detected, the short window duration selected in this paper is 0.02 s, and the long window duration is 0.05 s. It can effectively distinguish micro-seismic signals from noise, and can improve the efficiency and accuracy of event detection and ensure the accuracy of monitoring results (Liu and Zhang, 2014).
In Taoyuan Coal Mine II1012 working face monitoring area, the geological conditions and interference signals are complex and changeable, and the recognition of various events is more difficult than that of natural earthquakes. In this study, all-fiber acceleration sensors are used to collect micro-seismic signals, and a new network structure, called T_CNN model (Jin et al., 2024), is obtained by combining CNN(convolutional neural network) with transformer, which is used for automatic classification and recognition of micro-seismic events. The CNN in the model is used for feature extraction, and the key information is focused based on transformer, and the final multi-classification results are obtained by multi-layer perceptron. T_CNN model uses attention mechanism instead of the traditional de-noising algorithm, so that the network can effectively process multi-channel signal processing and estimate micro-seismic energy.
T_CNN model combines the advantages of CNN and Transformer. Compared with the CNN model, T_CNN model has stronger modeling and data capture capabilities. Compared with the Transformer model, T_CNN model adopts advanced convolution technology to optimize the data calculation efficiency, which can extract the local features of the data more efficiently and improve the operation efficiency of the model.
The number of data trained by T_CNN model is 9,180, including 4,469 noise data, 3,493 micro-seismic data, 1,218 data such as blasting and knocking,etc. The data set is randomly 80% as the training set and 20% as the test set. Different models are used to identify and classify them. The results are shown in Table 3. The results show that the classification accuracy based on T_CNN model is 98%.
The location accuracy of micro-seismic source is the key to micro-seismic monitoring technology, and the accuracy of micro-seismic source location is related to the application effect of micro-seismic technology (Feng et al., 2022). Assuming that the propagation medium of micro-seismic waves is uniform and isotropic, the travel time equation of micro-seismicwaves is as shown in Equation 4.
Where,
Micro-seismic location is the minimum value of Equation 6.
The specific description of each parameter in the above formula is as follows: ①Source parameters: source location coordinates of micro-seismic events
The specific parameters of the all-fiber optic micro-seismic monitoring system in the II1012 working face of Taoyuan Coal Mine are shown in Table 4.
Table 4. Parameter table of all-fiber optic micro-seismic monitoring system in II1012 working face of Taoyuan Coal Mine.
Since the initial mining of the II1012 working face in Taoyuan Coal Mine on 12 January 2024, the all-fiber optic micro-seismic monitoring system has been operating and recording data since the initial mining of the II1012 working face, and the mining of the II1012 working face has advanced by about 200 m in total until 20 March 2024. From January 20 to March 20, the micro-seismic system detected a total of 974 effective micro-seismic events, including 585 roof micro-seismic events and 389 floor micro-seismic events, with an average of about 16 micro-seismic events recorded every day. The total energy of micro-seismic events is 117,360.87 J, and the average energy of each event is about 120.50 J. The histogram of the data distribution of the number of micro-seismic events, the energy of the day, and the maximum energy of the day within the research period is shown in Figure 7. And the three views of the spatial distribution of micro-seismic events are shown in Figure 8. The top, front and side views represent the plane distribution map, the dip distribution map and the strike distribution map respectively.
The micro-seismic data generated by the mining work of the II1012 working face in Taoyuan Coal Mine during the study period have typical pressure characteristics, including first weighting, periodic weighting, and square pressure. Based on the site mining situation and micro-seismic data of Taoyuan Coal Mine, the following information is preliminarily known: the first weighting occurred on the II1012 working face on January 28, periodic weighting occurred in the working face from February 1 to March 5, square pressure occurred on the working face from March 6 to March 17. Table 5 shows the distribution of roof and floor micro-seismic events. According to Figure 8, during the study period, micro-seismic events mainly occur at the roof position, events with large energy and large magnitude are distributed in the coal seam and roof position, and events with small energy and small magnitude mainly occur at the floor position.
In this paper, the study period of pressure activity in the II1012 working face of Taoyuan Coal Mine is from January 20 to 20 March 2024, and the study results are discussed and analyzed based on the data of micro-seismic events in the coal seam roof and floor during the mining process and the mining footage.
The position of mining line of II1012 working face (part) during the research period is shown in Figure 9. Combined with Table 5, the location of the mining line corresponding to the date marked in Figure 9 is the location of the mining line at the key time in the research period of this paper. Jan.26th∼Jan.31st is the first weighting stage of the working face, and Jan.28th is the time of the first weighting. Feb.first∼Feb.11th, Feb.12th∼Feb.26th and Feb.27th∼Mar.fifth are the three stages of periodic weighting of working face, Mar.sixth∼Mar.17th is the stage of square pressure of working face, and Mar.seventh, Mar.11th, Mar.15th are the three time points of energy peak of micro-seismic events. The time points corresponding to each mining line in the figure will be elaborated in the subsequent chapters of this paper.
During the period from open-off cut position to 200 m, the mining speed of II1012 working face was maintained at 3∼4 m per day. The number of micro-seismic events and energy sum were counted every 10 m of mining at the self-open-off cut position of the working face, and the results were shown in Figure 10.
During the footage period of 0∼20 m, it is in the initial mining stage, and the daily number of micro-seismic events at the working face is maintained within 5. There is a small range of fluctuation in the energy and the number of micro-seismic events. The number of micro-seismic events is small, the energy is low, and the stress level is low. During the 20∼140 m mining footage period, the change of energy sum per 10 m footage is slow, within 7500 J.The number of micro-seismic events increased more during the period of 20∼30 m footage, and the first weighting stage was in this footage period. During the footage period of 30∼140 m, the indexes of the number of events and energy sum per 10 m showed an overall trend of in-creasing fluctuation, and the number of events was less than 90. The fluctuation of the indexes indirectly reflected that the surrounding rock activities of the working face showed a periodic change law under the influence of mining, and the corresponding pressure stage was periodic weighting. During the footage period of 140∼180 m, the indexes of the number of events and energy sum increase rapidly, reaching the peak state, and the corresponding pressure stage is the square pressure; compared with the 20∼30 m footage stage, the number of micro-seismic events increased by 692.68%, and the energy sum increased by 4,122.94%; compared with the 30∼140 m footage stage, although the number of micro-seismic events decreased by 35.26%, the energy and growth increased by 139.86%. This shows that the energy intensity of micro-seismic events in the 140∼180 m footage stage is greater, indicating that the activity in-tensity of surrounding rock in the working face under the influence of mining is greatly in-creased, and the failure range of roof and floor also reaches the peak. The energy sum and the number of events in the 180∼200 m footage stage is greatly reduced, which is in the later stage of pressure, and the influence of square pressure is weakened and tends to end.
It can be seen from Figure 10 that the slope of the curve in the periodic weighting stage is significantly smaller than that in the square pressure stage, so the micro-seismic activity in the square pressure stage is more intense.
The average mining speed equation of each pressure stage is as shown in Equation 7.
Among them, v represents the average mining speed, l represents the mining distance, t represents the mining time.
According to the 10 m standard statistics, the mining footage shows that the mining distance of the first weighting, periodic weighting and square pressure stage is 10 m, 110 m and 40 m respectively, and the mining time is 4 days, 34 days and 12 days respectively. According to Equation 7, the average mining speed of the first weighting, periodic weighting and square pressure stage is about 2.5 m/day, 3.24 m/day and 3.33 m/day respectively. The first weighting stage of the average mining speed of the working face is less than the periodic weighting stage, and the periodic weighting stage is less than the square pressure stage. It can be speculated that the indexes of the number of micro-seismic events and energy sum are positively correlated with the mining speed. In the current mining work, the change of mining speed will affect the occurrence of micro-seismic events and the release of energy in the working face to an extent. The faster the mining speed, the more likely it is to aggravate the stress and energy release caused by the change of in-situ stress in the working face space. On the contrary, the micro-seismic activity is more moderate. Similarly, the more intense the micro-seismic activity, the greater the impact on the roof and floor of the working face. The mining work of the working face and the micro-seismic activity interact with each other, which also shows the necessity of maintaining the uniform speed of the mining speed of the working face from the side. To an extent, it can reduce the pressure of the working face and the occurrence of micro-seismic events, and ensure the safe and orderly operation of mining production.
In the first weighting stage, the number of micro-seismic events began to increase on January 26, and the number of micro-seismic events and energy reached the peak on January 27. The first weighting occurred on January 28, and the first weighting step was 25.10 m. During the period to January 31, there was a small amount of reduction and fluctuation, and the micro-seismic energy did not change much. The impact of the first weighting on the working face basically ended.
There are 60 micro-seismic events during the whole first weighting period, including 42 roof micro-seismic events and 18 floor micro-seismic events. The three views of the spatial distribution of micro-seismic events are shown in Figure 11. The red mining line in the figure is the mining position of the first weighting on January 28. The number of micro-seismic events is small, the magnitude is small, and the spatial distribution is relatively scattered. The micro-seismic events along the mining direction of the working face are basically in front of the current mining position. The distance between the maximum energy event position and the mining line on the day is about 68 m. The average distance between the location of all events and the mining line is about 69 m. The occurrence of micro-seismic events is advanced, and the coal seam and floor are mainly small energy events. The large energy event is distributed in the roof position, which plays a major role in the roof collapse caused by the first weighting.
The periodic weighting of II1012 working face in Taoyuan Coal Mine occurred from February 1 to March 5. A total of 481 effective micro-seismic events were monitored by the all-fiber optic micro-seismic monitoring system, including 268 roof micro-seismic events and 213 floor micro-seismic events. The mining footage of the working face was 28.61 m–132.96 m, and the mining distance was about 104.35 m. The whole periodic weighting period was divided into three stages, and the corresponding time periods were Feb.01st∼Feb.11th, Feb.12th∼Feb.26th and Feb.27th∼Mar.05th, respectively. The three views of the spatial distribution of micro-seismic events are shown in Figure 12. A small number of large-energy and large-magnitude events are distributed above the roof, and most of the small-energy and small-magnitude events are concentrated in the floor and the middle and lower parts of the roof.
After the first weighting of the II1012 working face, the mining footage of the first stage from February 1 to February 11 was 28.61∼58.34 m, and the mining distance was about 29.73 m. During the period, the number of micro-seismic events fluctuated greatly, and the number of events remained at about 5∼20, but the energy of micro-seismic events did not change much, which was basically the same as that during the first weighting. The three views of the spatial distribution of micro-seismic events are shown in Figure 13. During this period, the number of roof events is 84, and the number of floor events is 48. The location of the daily maximum energy events is mostly in the roof position. The disturbance of micro-seismic events to the roof during the mining process of the working face is more severe than that of the floor, but the micro-seismic events are mostly small energy events, and the degree of damage to the roof is not large. During the period, the number and energy sum of events on February 3 and February 6 reached a new small peak at the same time. The micro-seismic events before and after the period showed the characteristics of small number and small energy. The energy and surrounding rock stress were accumulated and released on the peak day. Due to the shutdown of the II1012 working face of Taoyuan Coal Mine during the Spring Festival from February 9 to February 11, the number and energy of micro-seismic events decreased sharply.
After the end of the Spring Festival holiday on February 11, the II1012 working face of Taoyuan Coal Mine began to continue the mining production work. In the second stage, the number of micro-seismic events began to increase and the energy began to rise. On February 14, February 16 and February 19, the maximum energy events were about 1162 J, 728 J and 1462 J respectively, and the energy sum was also rising. On February 19, the number of micro-seismic events, maximum energy and energy sum all reached the peak, the stress of surrounding rock continued to accumulate and release, and the pressure of roof and floor continued to increase. From then to February 26, the micro-seismic activity began to slow down, the number of events was small, the energy was small, and the pressure of the roof and floor began to decrease. The influence of periodic weighting tends to end, the mining footage reaches 105.74 m, and the second stage mining distance is about 47.40 m. The three views of the spatial distribution of micro-seismic events are shown in Figure 14. The red mining line in the figure is the mining position on February 19. The micro-seismic events along the mining direction of the working face are basically in front of the current mining position. The maximum energy event position on the day is about −12 m away from the mining line. The average distance between the location of all events and the mining line is about 70 m. The occurrence of micro-seismic events is advanced. In the second stage, the number of roof events is 87 and the number of floor events is 72. Compared with the first stage, the number of floor micro-seismic events begins to increase, and the daily maximum energy events occur at the floor position. The micro-seismic activity caused by periodic weighting has a significant degree of damage to the floor.
In the third stage, the micro-seismic activity was severe from February 27 to March 5, and the indexes of micro-seismic events changed significantly. The number of micro-seismic events generally showed an increasing trend, reaching three peaks on February 27, February 29, and March 5, with 19, 26, and 37, respectively. On February 29, the number and energy sum of micro-seismic events reached the peak. At this stage, the mining footage of the working face reached 132.96 m, and the mining distance was about 27.22 m. It began to approach the length of the open-off cut of the working face. It had begun to be affected by the early stage of the square pressure, mainly with small energy and small magnitude events, and began to accumulate stress and energy for the later square pressure activities. The three views of the spatial distribution of micro-seismic events are shown in Figure 15. The red mining line in the figure is the location of the mining line on February 29. The micro-seismic events along the mining direction of the working face are basically in front of the current mining position. The location of the maximum energy event on the day is −50 m away from the mining line. The average distance between the location of all events and the mining line is about 44 m. The occurrence of micro-seismic events is advanced. In the third stage, the number of micro-seismic events in the roof and floor reached 100 and 93, respectively. The stress of surrounding rock and energy accumulation and release intensity were large. The damage degree of micro-seismic activity to the roof and floor was more severe, and the pressure of the roof and floor was increasing. During the periodic weighting period, the mining work disturbed and destroyed the equilibrium state of the in-situ high stress field of the working face, the structure of the surrounding rock of the working face was adjusted, and the stress of the surrounding rock was repeatedly accumulated and released, which promoted the fracture, migration and even collapse of the roof strata, and induced the increase of large energy and large magnitude events and distributed in the roof position.
The instability, movement and rupture of the overlying roof strata during the mining process of the working face are the main reasons for the mine pressure appearance of the working face, and the stress change of the overlying strata is the strongest in the square stage of the working face goaf. When the mining length of the working face is equal to the distance of the working open-off cut, the pressure activity is the square pressure, which is a special case of mining pressure. At this time, the activity intensity of the roof in the goaf reaches the peak, the dynamic load caused by the roof fracture is large, the ground pressure appears violently, and the risk of dynamic pressure on the working face increases.
The length of open-off cut of II1012 working face in Taoyuan Coal Mine is 150 m, so the mining footage is accumulated to about 150 m which is considered to be the square of the working face. The influence period of the working face is from March 6 to 17 March 2024. A total of 346 effective micro-seismic events were monitored by the all-fiber optic micro-seismic monitoring system, including 204 roof micro-seismic events and 142 floor micro-seismic events. The maximum energy events occurred in the roof position of the working face. As shown in Figure 16, during the influence of the square pressure on the II1012 working face, with the continuous mining work, the energy and average energy have three peaks. The time is March 7, March 11, and March 15, respectively. The first peak energy is much higher than the latter two peak energies. The energy and average energy of other times show an upward and downward trend before and after the peak time. It can be seen that the three peak times are the most intense time period for the influence of the square pressure on the working face, and as the follow-up mining work progresses, the influence of the square pressure gradually weakens.
On 6 March 2024, when II1012 working face was mined to 138.80 m, the influence of square pressure began to appear. The number of micro-seismic events decreased, mainly small energy events. On March 6, the total energy released was not large, and the stress accumulation began to develop rapidly, resulting in small strain and small energy micro-seismic events.
When the working face is mined to 142.12 m on March 7, the influence of square pressure is the most severe, the stress concentration, the strength is close to the peak, the maximum energy event appears, and the energy of micro-seismic event reaches the maximum peak. The micro-seismic events are concentrated in the position of 0∼20 m of the coal floor and 0∼60 m of the coal roof. The micro-seismic events are mainly low-frequency large energy events and concentrated in the roof position. The number of micro-seismic events is 17, the total energy is 12,765 J, the average energy is 750 J, and the maximum energy event is 4624 J, which belongs to the typical stress accumulation and release process. The frequency of stress change in some areas is low and the strength is large. At this time, the stress of the surrounding rock of the working face is highly concentrated, the risk of instability and failure is high, and the in-tensity of mining disturbance is large. After comprehensively evaluating the production situation, the mine side of Taoyuan Coal Mine took timely safety countermeasures such as safety support and drilling pressure relief.
After the release of the peak stress on March 7, the footage of the working face from March 8 to March 10 was 145.80∼153.19 m. The micro-seismic activity was relatively gentle during the new equilibrium process of stress, mainly small energy and small magnitude micro-seismic events. On March 11, the working face was mined to 155.73 m. The micro-seismic events were concentrated in the position of 0∼20 m of coal floor and 0∼60 m of coal roof. The micro-seismic events were mainly small energy and small magnitude events, and a few large energy events occurred in the roof position. The number of micro-seismic events was 33, the total energy was 10,868 J, the average energy was 329 J, and the maximum energy event was 2509 J. The stress of surrounding rock reached a new accumulation state, but the release of total energy was more moderate than that on March 7, but it still reached a new peak. At this time, the stress accumulation intensity of surrounding rock was strong, so it was necessary to pay close attention to it and take pressure relief measures in time.
After the release of the peak stress on March 11, the process of reaching a new balance on March 12, 13, and 14 was dominated by small-energy and small-magnitude micro-seismic events. On March 15, the working face was mined to 172.43 m. The distribution of micro-seismic events was relatively scattered, and the number of large and small energy events was relatively balanced. The number of micro-seismic events was 34, the total energy was 11,025 J, the average energy was 324 J, and the maximum energy event was 2469 J. The stress of surrounding rock reached a new peak, but the total energy released was still lower than the first peak. After March 16, the number of micro-seismic events decreased, the sum of energy decreased, and the current mining work was at the end of the influence of the pressure. On March 17, when the working face was mined to 181.68 m, the number and energy of micro-seismic events decreased to a low point. The micro-seismic events were mainly small energy events within a week after the release of the stress concentration. Combined with the analysis of the mining footage and the ground pressure phenomenon feedback from the Taoyuan Coal Mine, it can be seen that the influence period of the pressure has basically ended.
The spatial distribution of micro-seismic events corresponding to the above analysis results is shown in Figure 17. In the figure, the red mining line is the mining position on March 7,11 and 15 along the mining direction. The micro-seismic events along the mining direction of the working face are basically in front of the current mining position, and the occurrence of micro-seismic events is advanced. On March 7, the location of the maximum energy event is 7 m away from the mining line, and the average distance between the location of all events and the mining line is about 37 m. On March 11, the location of the maximum energy event is 66 m away from the mining line, and the average distance between the location of all events and the mining line is about 14 m. On March 15, the location of the maximum energy event is −12 m away from the mining line, and the average distance between the location of all events and the mining line is about 24 m. The large energy events are mainly distributed in the roof of the working face, with a large number. There are some large energy events in the right wing adjacent to the 1,019 goaf. It is speculated that the disturbance response of the working face mining work to the adjacent old mining area, and the floor is still dominated by small energy events, with a small number.
Combined with Figures 3, 5, 7–9, 11–13, it can be seen that in the initial stage of mining, the advancing abutment pressure period, the first weighting, and the first stage of periodic weighting, there are some small faults that have some impacts on the mining work of the working face, but the impact is small, resulting in a few micro-seismic events and small energy. It is analyzed and judged that the initial mining work leads to the crushing and fracture of small faults, which is the main reason for the first weighting of the working face, and has some impacts on the first stage of periodic weighting, but the overall impact on the mining work of the working face is limited, and the subsequent mining production work of the working face is carried out normally and orderly.
In this paper, the research period is from January 20 to 20 March 2024, the research time is about 2 months, and the cumulative mining footage of the working face is 200 m.According to the mining progress of about 3∼4 m per day, more than ten times of pressure activities occur in the working face, which are divided into first weighting, periodic weighting, square pressure and other specific pressure activities, so as to explore the micro-seismic variation law of mine pressure in the mining process of the working face (Li X. P. et al., 2023).
There are some relationships between the energy of micro-seismic events and the risk of mine pressure disasters (Cheng et al., 2023). Discussion on this can better predict disaster risk and guide mine production. Combined with the micro-seismic data in the research period of this paper and Figure 7, it can be seen that when the mining work of the working face enters the pressure state, the number of micro-seismic events and the energy of micro-seismic events increase, and the change trend of the number of micro-seismic events and energy is basically the same, showing a positive correlation. In the periodic weighting and the middle and late stages of square pressure, when the energy of micro-seismic events reaches the peak, the number of micro-seismic events also reaches the peak state. However, in the initial period of square pressure, the number of micro-seismic events is negatively correlated with energy. The energy of micro-seismic events increases greatly, but the number of events decreases, indicating that the pressure stage is more likely to promote the occurrence of large energy events, which means that there is greater potential destructive power in the working face. As shown in Table 6, for the study period of energy threshold classification and disaster risk.
According to micro-seismic data and Table 6, the higher the energy threshold of micro-seismic events, the greater the risk of mine pressure-induced disasters, and large energy events and high risks mainly occur in the square pressure stage (Lai et al., 2022). The relevant situation has been communicated with Taoyuan Coal mine in time, and relevant supporting measures have been taken in time, which has effectively reduced the occurrence of mining pressure disasters on the working face.
Based on the all-fiber optic micro-seismic monitoring technology, this paper analyzes and studies the characteristics of the first weighting, periodic weighting and square pressure stage generated in the II1012 working face of Taoyuan Coal Mine during the research period. There is a positive correlation between the intensity of micro-seismic activity and the mining speed of the working face. Generally speaking, the faster the mining distance of the working face in the same time, the more the number of micro-seismic events produced by the mining work, the greater the energy of micro-seismic events, the more intense the micro-seismic activity, the deeper the damage to the surrounding rock, and the greater the pressure on the working face. Therefore, the mining work of the working face needs to maintain a fixed mining speed, and take safety measures such as support in time to ensure the safety, normal and orderly progress of the mining work.
Through the analysis and research on the micro-seismic data of the three stages of the first weighting, periodic weighting and square pressure of the working face, the three stages have the same characteristics. Along the mining direction of the working face, the location of micro-seismic events is basically distributed in the front of the current mining position, and the micro-seismic events are scattered in a small amount behind the current mining position, indicating that the mining work has a great impact on the unmined area in front of it. The occurrence of micro-seismic events has significant advance characteristics, and its hysteresis characteristics are not obvious (Figures 11, 14, 15, 17). This law is of great significance for predicting the occurrence of micro-seismic activity. The micro-seismic activity based on all-fiber optic micro-seismic monitoring technology has a good response effect on mining pressure.
Mine pressure refers to the force generated by the rock movement caused by the mining process on the surrounding rock of the support, which often leads to a series of mechanical phenomena such as roof subsidence and collapse, floor heave, rib spalling, support deformation and damage, filling subsidence and compression, rock strata and surface movement, rock burst, water and gas outburst, and even safety accidents. Therefore, the real-time monitoring and early warning of mine pressure plays a vital role in mine production safety and prevention of mining accidents (Xu et al., 2022). Some scholars predict the pressure disaster of coal mine through Logistic regression model and Adagrad optimization algorithm, which provides a reliable guarantee for coal mine safety production (Zhu et al., 2023). At present, the depth of coal mining is increasing, the geological situation is more complicated, and the pressure of coal mine is becoming more and more prominent. An evaluation method for the implementation of pressure relief in the dangerous area of rock-burst in deep mining area is based on the frequency change rate of micro-seismic high-energy interval events and the change rate of blasting strain energy, which provides a reference for the monitoring and prevention of mining pressure (Li Y. et al., 2023).
In this paper, all-fiber optic micro-seismic monitoring technology is used to monitor the micro-seismic activities generated during coal mining, and then the characteristics and laws of micro-seismic events in mine pressure activities are studied. As an emerging monitoring technology, all-fiber optic micro-seismic monitoring technology is based on the principle of optical fiber interference. It uses a narrow line-width and low noise laser light source. It has the advantages of high sensitivity, wide response frequency and large dynamic range, and can realize the detection of weak signals. In recent years, all-fiber optic micro-seismic monitoring technology has developed rapidly, and its application in coal and gas outburst, mine dynamic disaster (Guo, 2022; Zhang et al., 2023), coal mine water inrush, tunnel rock burst (Jin et al., 2024) and other fields has been continuously expanded (Wu et al., 2024). Previously, all-fiber optic micro-seismic monitoring technology has a good application effect in the monitoring of floor water inrush in the 11,023 working face of Pan ‘er Coal Mine. The relationship between floor failure and micro-seismic activity in the fault anomaly area of the 11,023 working face was analyzed and studied. It reflects the advantages of all-fiber optic micro-seismic monitoring technology system, such as high signal-to-noise ratio and wide monitoring range, and is suitable for monitoring work in different coal mine working faces. In the future, all-fiber optic micro-seismic monitoring technology can be combined with other Frontier technologies to jointly assist the monitoring work in mines, tunnels, slopes and other fields, further promote the sustainable development of the industry, and ensure the safe and efficient mining and supply of coal energy and other resources (Shi Y. N. et al., 2023; Wu et al., 2022; Shi et al., 2024; Wu et al., 2020; Wu et al., 2025).
As an emerging monitoring technology, the all-fiber optic micro-seismic monitoring technology is not particularly mature compared with the traditional monitoring technology. The monitoring system may produce errors in the process of micro-seismic data acquisition and preliminary processing. Therefore, after the system uploads the preliminary processed data to the engineering analysis center, it is necessary to manually screen and process the data to reduce the error of the data and further improve the accuracy of the micro-seismic data. In view of this deficiency, in the future, we can strengthen the system‘s data processing ability through cutting-edge technologies such as artificial intelligence to reduce data errors and improve work efficiency.
In the equipment installation work of the all-fiber optic micro-seismic monitoring system, the follow-up equipment failure investigation work and the dismantling and moving work of the equipment, the construction personnel need to go deep into the underground mine, the tunnel and other harsh environment construction sites to work. In these places, safety accidents such as gas leakage, water inrush accidents and rock collapse may occur, which poses potential threat to the safety of construction personnel. In response to this problem, future construction personnel can command robots on the ground to work on the spot, which can not only reduce the security threat to construction personnel, but also improve work efficiency.
In addition, in the micro-seismic location algorithm, it is assumed that the medium is homogeneous and isotropic, which may be different from the actual geological conditions of Taoyuan Coal Mine. There are differences in different lithology, density and porosity in the actual situation of the coal mine, which leads to different propagation speeds of seismic waves in different regions. There are faults, folds and other structures in coal mine geology, which will change the propagation direction of seismic waves. The above factors may have some impacts on the positioning accuracy of micro-seismic, resulting in positioning deviation.
This paper studies the use of all-fiber optic micro-seismic monitoring technology, which has excellent characteristics such as strong anti-interference ability, large dynamic range continuous monitoring, intrinsic safety, low loss and large capacity transmission, and can better reduce the impact of coal mine geological conditions on seismic wave propagation and positioning. Based on this, in the future research work, detailed information such as stratum distribution and lithology in the coal mine area can be obtained. Combined with the physical parameters of different rock strata, considering the velocity changes of different rock strata, the micro-seismic positioning algorithm is introduced to establish a more accurate velocity model. In addition, seismic tomography technology can also be used to image the velocity structure of the coal mine area to obtain the velocity distribution details of the underground medium, so as to update the velocity model in the micro-seismic positioning algorithm and improve the positioning accuracy.
This paper refers to a large number of international journal literature, including optical fiber sensor technology, micro-seismic monitoring, coal mine pressure research, etc. The research work of coal mine pressure based on all-fiber micro-seismic monitoring is of great significance to related research work at home and abroad. All-fiber optic micro-seismic monitoring technology has attracted more and more attention from international researchers. In the future, researchers around the world can conduct in-depth research on various fields such as mines, tunnels, highways, and railways based on all-fiber optic micro-seismic monitoring technology, and jointly promote international academic development in related research fields.
Based on the above all-fiber optic micro-seismic monitoring results and discussions, the following conclusions are drawn:
(1) In the first weighting stage, a small number of large-energy and large-magnitude micro-seismic events have a major impact on roof collapse, and the first weighting interval is 25.10 m.
(2) In the periodic weighting stage, the influence of micro-seismic activity on the roof is greater than that on the floor, but the influence on the floor failure is increasing significantly.
(3) In the square pressure stage, the high-energy micro-seismic events are significantly more than those in the previous mining stage, and the square pressure is easy to promote the frequent occurrence of high-strength and high-stress micro-seismic activities.
(4) The occurrence of micro-seismic events in the stages of first weighting, periodic weighting and square pressure has the characteristics of advance, and has a great in-fluence on the front area along the mining direction, which is of great significance to predict the occurrence of micro-seismic activities in the working face.
(5) The mining work of the working face is related to the micro-seismic activity. There is a positive correlation between the intensity of micro-seismic activity and the mining speed. The faster the mining speed, the more intense the micro-seismic activity. The micro-seismic activity based on all-fiber monitoring has a good response to mine pressure.
The original contributions presented in the study are included in the article/supplementary material, further inquiries can be directed to the corresponding author.
SW: Conceptualization, Data curation, Formal Analysis, Investigation, Methodology, Software, Validation, Visualization, Writing–original draft, Writing–review and editing. KW: Investigation, Methodology, Project administration, Resources, Supervision, Validation, Visualization, Writing–review and editing. ZZ: Conceptualization, Funding acquisition, Investigation, Resources, Supervision, Validation, Writing–review and editing. YM: Conceptualization, Data curation, Formal Analysis, Methodology, Project administration, Writing–original draft. TC: Data curation, Project administration, Software, Writing–review and editing.
The author(s) declare that financial support was received for the research and/or publication of this article. This research was funded by the National Natural Science Foundation of China, grant number U23A20601.
Authors YM and TC were employed by IDETECK CO., LTD.
The remaining authors declare that the research was conducted in the absence of any commercial or financial relationships that could be construed as a potential conflict of interest.
The author(s) declare that no Generative AI was used in the creation of this manuscript.
All claims expressed in this article are solely those of the authors and do not necessarily represent those of their affiliated organizations, or those of the publisher, the editors and the reviewers. Any product that may be evaluated in this article, or claim that may be made by its manufacturer, is not guaranteed or endorsed by the publisher.
Anjana, K., Herath, M., and Epaarachchi, J. (2024). Optical fibre sensors for geohazard monitoring – a review. Measurement 235, 114846. doi:10.1016/j.measurement.2024.114846
Cao, A. Y., Dou, L. M., Wang, C. B., Yao, X. X., Dong, J. Y., and Gu, Y. (2016). Microseismic precursory characteristics of rock burst hazard in mining areas near a large residual coal pillar: a case study from Xuzhuang coal mine, Xuzhou, China. Rock Mech. Rock Eng. 49 (11), 4407–4422. doi:10.1007/s00603-016-1036-7
Cheng, X., Qiao, W., and He, H. (2023). Study on deep learning methods for coal burst risk prediction based on mining-induced seismicity quantification. Geomech. Geophys. Geo-energ. Geo-resour. 9 (1), 145. doi:10.1007/s40948-023-00684-3
Feng, Q., Han, L. G., and Zhao, B. H. (2022). Localizing microseismic events using semi-supervised generative adversarial networks. Ieee Trans. Geosci. Remote Sens. 60, 1–8. doi:10.1109/tgrs.2022.3225415
Guo, Q. H. (2022). Development and application of precursory information sensing technology in coal mine dynamic disaster. Coal Sci. Technol. 50 (11), 76–83. doi:10.13199/j.cnki.cst.2021-0415
He, Y. L., Gao, M. S., Xu, D., and Yu, X. (2021). Investigation of the evolution and control of fractures in surrounding rock under different pressure relief and support measures in mine roadways prone to rockburst events. R. Soc. open Sci. 8 (3), 202044. doi:10.1098/rsos.202044
He, Z. Q., Ju, F., Xiao, M., Ning, P., and Zhou, C. (2021). An experimental investigation on the compaction characteristic of coal waste rock backfilling material using electrical resistivity method. Environ. Earth Sci. 80, 450. doi:10.1007/s12665-021-09701-8
Jin, S., Luo, J. T., Gao, Y., Yu, B. L., Zhang, S. J., and Zhen, S. L. (2024). Deep learning-based classification and identification of fiber optic microseismic signals. J. Electron. Meas. Instrum. 38 (6), 135–142. doi:10.13382/j.jemi.B2307104
Lai, X. P., Jia, C., Cui, F., Zhou, Y. P., Feng, G. G., Gao, Y. J., et al. (2022). Microseismic energy distribution and impact risk analysis of complex heterogeneous spatial evolution of extra-thick layered strata. Sci. Rep. 12 (1), 10832. doi:10.1038/s41598-022-14538-7
Li, J. Z., Liu, S., Ren, W. T., Liu, H., Li, S. Y., and Yan, K. X. (2023). Research on engineering practice and effect evaluation method of pressure relief in deep rock burst danger area of coal mine. Minerals 13 (4), 570. doi:10.3390/min13040570
Li, S. L., Ni, Y., Wang, Y., Shi, J. H., Zhang, S. C., Ge, Q., et al. (2022). Highly sensitive fiber optic micro-seismic monitoring system for tunnel rock burst. Measurement 189, 110449. doi:10.1016/j.measurement.2021.110449
Liu, F., Wang, Y., Kou, M. M., and Liang, C. H. (2024). Applications of microseismic monitoring technique in coal mines: a state-of-the-art review. Appl. Sci. 14 (4), 1509. doi:10.3390/app14041509
Liu, H., and Zhang, J. Z. (2014). STA/LTA algorithm analysis and improvement of Microseismic signal automatic detection. Prog. Geophys. 29 (4), 1708–1714. doi:10.6038/pg20140429
Li, X. P., Liu, Y. Q., Ren, X. P., Wu, X. Y., and Zhou, C. H. (2023). Roof breaking characteristics and mining pressure APPEARANCE laws in close distance COAL seams. Energy explor. Exploit. 41 (2), 728–744. doi:10.1177/01445987221120888
Li, Y., Zheng, J., Wang, F. N., Ma, X. G., Zhang, R. X., Sun, Y. Y., et al. (2023). Experimental study on the movement law of overlying rock non-pillar coal overhead mining. J. Mt. Sci. 20 (6), 1759–1773. doi:10.1007/s11629-023-7915-y
Lu, C. P., Dou, L. M., Liu, H., Liu, H. S., Liu, B., and Du, B. B. (2012). Case study on microseismic effect of coal and gas outburst process. Int. J. Rock Mech. Min. Sci. 53, 101–110. doi:10.1016/j.ijrmms.2012.05.009
Shi, H., Chen, W. L., Zhang, H. Q., Song, L., Li, M., Wang, M. J., et al. (2023). Dynamic strength characteristics of fractured rock mass. Eng. Fract. Mech. 292, 109678. doi:10.1016/j.engfracmech.2023.109678
Shi, H., Zhang, H. Q., Chen, W. L., Song, L., and Li, M. (2024). Pull-out debonding characteristics of rockbolt with prefabricated cracks in rock: a numerical study based on particle flow code. Comput. Part. Mech. 11, 29–53. doi:10.1007/s40571-023-00607-9
Shi, Y. N., Qi, P. L., Wang, Y., Wang, Y. Y., and Zhang, C. C. (2023). Micro-seismic signal denoising algorithm based on CEEMD-SVD and STA/LTA. J. Vib. Shock 42 (5), 113–121. doi:10.13465/j.cnki.jvs.2023.05.014
Song, G. D., Hu, B. X., Zhu, F., Zhang, H., and Liu, T. Y. (2020). Identification of effective events recorded by optical fiber micro-seismic monitoring system. J. Phys. Conf. Ser. 1621, 012004. doi:10.1088/1742-6596/1621/1/012004
Srinivasan, V., Kumar, L. A., and Erraiyan, K. (2015). Slope stability monitoring by quantification and behavior of microseismic events in an opencast coal mine. J. Geol. Soc. India 85 (4), 450–456. doi:10.1007/s12594-015-0236-1
Wang, J. W., Han, Y. F., Cao, Z. L., Xu, X. Y., Zhang, J. K., and Xiao, F. P. (2023). Applications of optical fiber sensor in pavement Engineering: a review. Constr. Build. Mater. 400, 132713. doi:10.1016/j.conbuildmat.2023.132713
Wu, J. Y., Jing, H. W., Gao, Y., Meng, Q. B., Yin, Q., and Du, Y. (2022). Effects of carbon nanotube dosage and aggregate size distribution on mechanical property and microstructure of cemented rockfill. Cem. Concr. Compos. 127, 104408. doi:10.1016/j.cemconcomp.2022.104408
Wu, J. Y., Jing, H. W., Yin, Q., Yu, L. Y., Meng, B., and Li, S. C. (2020). Strength prediction model considering material, ultrasonic and stress of cemented waste rock backfill for recycling gangue. J. Clean. Prod. 276, 123189. doi:10.1016/j.jclepro.2020.123189
Wu, J. Y., Wong, H. S., Zhang, H., Yin, Q., Jing, H. W., and Ma, D. (2024). Improvement of cemented rockfill by premixing low-alkalinity activator and fly ash for recycling gangue and partially replacing cement. Cem. Concr. Compos. 145, 105345. doi:10.1016/j.cemconcomp.2023.105345
Wu, J. Y., Yang, S., Williamson, M., Wong, H. S., Bhudia, T., Pu, H., et al. (2025). Microscopic mechanism of cellulose nanofibers modified cemented gangue backfill materials. Adv. Compos. Hybrid. Mater. 8 (2), 177. doi:10.1007/s42114-025-01270-9
Yang, M. H., Lewis, E., and Matias, I. R. (2020). Guest editorial special issue on advances in fiber optic sensing technologies. IEEE Sens. J. 21 (1), 16. doi:10.1109/jsen.2020.3033913
Yang, Y. L., Du, L. J., Li, Q. W., Zhao, X. B., Zhang, W. F., and Liu, Z. Y. (2023). Predicting the accuracy and applicability of micro-seismic monitoring of rock burst in TBM tunneling using the data from two case studies in China. Sustainability 15 (5), 4232. doi:10.3390/su15054232
Yoones, V., and Mirko, V. D. B. (2015). Comparison of the STA/LTA and power spectral density methods for microseismic event detection. Geophys. J. Int. 203 (3), 1896–1908. doi:10.1093/gji/ggv419
Zhang, D. D., Huang, Z. M., Ma, Z., Yang, J. F., and Chai, J. (2023). Research on similarity simulation experiment of mine pressure appearance in surface gully working face based on BOTDA. Sensors 23 (22), 9063. doi:10.3390/s23229063
Zheng, Q. Q., Li, P. F., Xu, Y., Cheng, B., Hu, H., Shi, H., et al. (2025). Crack propagation and CT imaging of internal cracks in rocks damaged by pre-compression under explosive loading. Ain Shams Eng. J. 16 (3), 103302. doi:10.1016/j.asej.2025.103302
Zheng, Q. Q., Qian, J. W., Zhang, H. J., Chen, Y. K., and Zhang, S. H. (2024). Velocity tomography of cross-sectional damage evolution along rock longitudinal direction under uniaxial loading. Tunn. Undergr. Space Technol. 143, 105503. doi:10.1016/j.tust.2023.105503
Zhu, B. B., Shi, Y. K., Hao, J., and Fu, G. Q. (2023). Prediction of coal mine pressure hazard based on logistic regression and Adagrad algorithm—a case study of C coal mine. Appl. Sci. 13 (22), 12227. doi:10.3390/app132212227
Zhu, H., Ju, M. H., Cao, A. Y., Yu, L. Y., Cai, W., and Dou, L. M. (2025). Unloading-induced acoustic and fracturing behavior of a fault interface at various depths: relevance to faulting-affected coal burst in deep mining. Bull. Eng. Geol. Environ. 84 (1), 7. doi:10.1007/s10064-024-03920-6
Zuo, J. P., Wu, G. S., Du, J., Lei, B., and Li, Y. B. (2022). Rock strata failure behavior of deep ordovician limestone aquifer and multi-level control technology of water inrush based on microseismic monitoring and numerical methods. Rock Mech. Rock Eng. 55, 4591–4614. doi:10.1007/s00603-022-02891-y
Keywords: all-fiber optic micro-seismic, first weighting, periodic weighting, square pressure, micro-seismic response
Citation: Wang S, Wang K, Zhao Z, Miao Y and Cai T (2025) Research on coal mine pressure characteristics based on all-fiber optic micro-seismic monitoring. Front. Earth Sci. 13:1549906. doi: 10.3389/feart.2025.1549906
Received: 22 December 2024; Accepted: 14 March 2025;
Published: 26 March 2025.
Edited by:
Jiangyu Wu, China University of Mining and Technology, ChinaReviewed by:
Zhengzheng Cao, Henan Polytechnic University, ChinaCopyright © 2025 Wang, Wang, Zhao, Miao and Cai. This is an open-access article distributed under the terms of the Creative Commons Attribution License (CC BY). The use, distribution or reproduction in other forums is permitted, provided the original author(s) and the copyright owner(s) are credited and that the original publication in this journal is cited, in accordance with accepted academic practice. No use, distribution or reproduction is permitted which does not comply with these terms.
*Correspondence: Kangdong Wang, d2tkQHVzdGMuZWR1LmNu
†ORCID: Zhigen Zhao, orcid.org/0000-0003-4413-8688
Disclaimer: All claims expressed in this article are solely those of the authors and do not necessarily represent those of their affiliated organizations, or those of the publisher, the editors and the reviewers. Any product that may be evaluated in this article or claim that may be made by its manufacturer is not guaranteed or endorsed by the publisher.
Research integrity at Frontiers
Learn more about the work of our research integrity team to safeguard the quality of each article we publish.