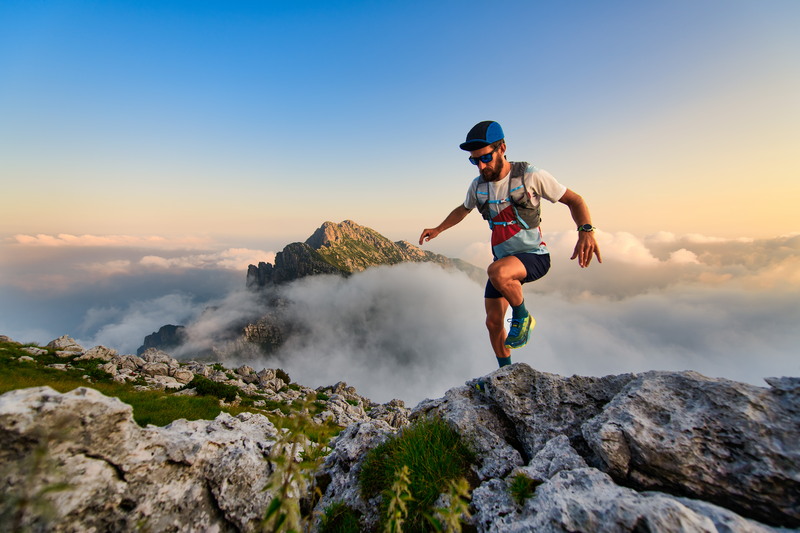
94% of researchers rate our articles as excellent or good
Learn more about the work of our research integrity team to safeguard the quality of each article we publish.
Find out more
ORIGINAL RESEARCH article
Front. Earth Sci. , 04 July 2024
Sec. Sedimentology, Stratigraphy and Diagenesis
Volume 12 - 2024 | https://doi.org/10.3389/feart.2024.1433517
This article is part of the Research Topic Fine-Grained Sedimentary Rocks: Sedimentary Processes, Diagenesis, Geochemistry and Their Relationship with Critical Geological Events View all 10 articles
Diagenetic physical simulation is a reliable means to study patterns of pore evolution and variations of physical properties, however, the current compaction model is mostly based on sandstone, and there is a lack of quantitative compaction and porosity reduction studies for more complex rock fabrics. In order to simulate the continuous change of intergranular porosity in the reservoir under compaction during the diagenesis of buried sedimentary strata, a self-designed diagenesis simulation experimental system was adopted. Using different modern sediment samples, the simulation experiment of mechanical compaction of glutenite was carried out. The experiment shows that during the process of mechanical compaction of glutenite, the change of porosity with depth is segmented, and there is a good logarithmic relationship between depth and porosity in the process of diagenetic compaction. The larger the grain size in the reservoir rock, the better the pore preservation capacity; When the sand particles fill the pores among gravel, stable secondary support structure formed by gravel and sand grades can effectively take over the bearing pressure, and when the sand-grade particle content is about 30%, the pressure-bearing capacity is the strongest; Intergranular heterobase filling is greater in samples with high heterobase content, high heterobasic content is not favourable to the preservation of primary pores. This study provides favorable experimental support for the preservation mechanism of deep clastic reservoir pores, and has important theoretical and practical significance for oil and gas exploration in the study area. The use of simulation experiment provides a useful idea for the evaluation and prediction of reservoirs and the search for favorable reservoir development zones in the future.
The abundant oil and gas resources contained in the gravel reservoirs in the deep field have attracted much attention, showing great succession potential for the next step in energy development and deployment, and gradually becoming an important source of oil and gas reserves and production (Pang X. J. et al, 2020; Li et al., 2020). Reservoir quality is one of the key factors constraining oil and gas exploration in deep reservoirs (Taylor et al., 2010; Sun et al., 2013; Wang, 2020), mechanical compaction is an important cause of pore permeability reduction in glutenite reservoirs, controlling both the preservation of intergranular pore and the evolution of physical properties (Carvalho and Ros, 2015; Yuan et al., 2017; Pang X. et al, 2020; Li et al., 2021). As the systematic study of reservoir diagenesis is becoming more and more mature, qualitative descriptions and semi-quantitative analyses of mechanical compaction can no longer provide favourable theoretical support for reservoir pore retention mechanisms. Diagenetic physical simulation has emerged as an innovative experimental method for simulating diagenesis indoors, by establishing a compaction model with compaction physical simulation experimental data and setting up temperature, pressure and fluid property conditions in line with the geological situation, it studies pore evolution patterns and physical property variations of reservoir caused by compaction.
In recent years, scholars have introduced simulation experiments of compaction to study the multiple factors affecting compaction and the dynamic response mechanism. The factors affecting sandstone compaction can be categorised into internal factors such as mineral composition, filler, grain size and sortability, and external factors such as pressure, temperature, fluid and time. Liu et al. found that the pore penetration changes in the compaction simulation process have obvious segmentation, and have good linear and exponential relationship with bearing pressure, respectively (Liu et al., 2006). In terms of experimental studies of compaction for endogenous factors such as rock fabric, Fawad and Bjørlykke found that the evolution of reservoir porosity vary with different grain sizes and mineralogical compositions, and that coarser sands with a high content of clasts are more susceptible to compaction than finer quartz-rich sands (Chuhan et al., 2002; Chuhan et al., 2003; Bjørlykke, 2014). Cao et al. and Ji et al. analysed the variation patterns of porosity and permeability in sandstone reservoirs with different grain sizes and sorting under pure compaction conditions, and found that the two showed a good positive correlation with physical properties (Cao et al., 2011; Ji et al., 2017). Gao et al. found that there is a significant negative correlation between matrix content and porosity through the simulation of compaction of sandstone, and the rate of porosity attenuation is larger in sandstone with high matrix content (Gao et al., 2015). In addition, the quantitative impact of the above external factors on the simulation of compaction evolution has also been elaborated. You et al. applied physical simulation experiments to analyse the pore evolution characteristics in the setting of different temperature and pressure fields, and clarified that the protection of primary pores by overpressure is the most constructive role in reservoirs in the setting of high temperature overpressure and strong overpressure (You et al., 2019). Gao et al. carried out physical simulation experiments on the mechanism of the role of overpressure on the physical properties of deep reservoirs, and found that the reduction value of the remaining primary pores by mechanical compaction under overpressure is only one-half of that under hydrostatic pressure, and that overpressure can effectively inhibit the role of mechanical compaction, so that a large number of intergranular primary pores can be preserved (Gao et al., 2023). Hou et al. investigated the varying rules of porosity and permeability of sandstone reservoirs under different ground temperature conditions and different burial ways under compaction by physical simulation, and found that the ground temperature and pore permeability parameters were all in a logarithmic negative correlation, whereas the burial time was in a logarithmic relationship with the pore permeability parameters (Hou et al., 2017).
The deep glutenite of Fukang Sag in Junggar Basin have a large potential of oil and gas resources (He et al., 2021), the stratigraphy of the Upper Urho Formation in this area has a large span of burial depth, and vertical burial compaction dominates, which facilitates comparative studies in the vertical direction, and provides a good example for the study of mechanical compaction response of deep glutenite. With the continuous updating of the petrogenetic physics simulation experimental device, high temperature and high pressure and even ultra-high temperature and ultra-high pressure experimental equipment have been developed successively, which provide the necessary experimental conditions for the study of deep physical and chemical diagenesis. However, most of the current compaction models are based on sandstones, and there is a lack of quantitative compaction and pore reduction studies for glutenite, which are more complex in rock fabric. Previous studies have found that glutenite is more resistant to compaction than sandstone (Xie et al., 2018; Liu et al., 2020), and that particle morphology, grain size and arrangement can have a significant effect on mechanical compaction (De Cola et al., 2018). The structure of gravel is different from that of pure sandstone. If a skeleton is built between gravel particles, it can play a supporting role, and the gravel skeleton can withstand the pressure during the compaction process, which can resist the destruction of sandy debris pores by mechanical compaction (Wei et al., 2015; Mahmic et al., 2018; Kang et al., 2019; Yue, 2019). Therefore, this paper takes the deep Permian glutenite reservoir in Fukang Sag of Junggar Basin as an example, applies the compaction physics simulation experiment to investigate the physical evolution patterns in the process of mechanical compaction of deep glutenite, quantitatively analyses the preservation of intergranular pores by rock fabric, with a goal of providing guidance for the evaluation and prediction of the deep gravel reservoirs and searching for favourable reservoir development zones.
The experiment adopts the compaction physics simulation experiment system independently designed and developed by the National Key Laboratory of Deep Oil and Gas (China University of Petroleum (East China)), which is able to complete the compaction simulation experiments with the maximum temperature of 500 °C, the maximum static rock pressure of 300 MPa, and the maximum fluid pressure of 100 MPa. It is the experimental device that can simulate the higher temperature and pressure in China, which can meet the high temperature and high pressure environment of deep- and ultra-deep strata under the actual geological conditions. It can simulate the diagenesis and pore evolution process of the reservoir under different temperature, pressure and fluid medium conditions.
The system device includes axial pressure monitoring equipment, flow pressure monitoring equipment, heating furnace and temperature control device, temperature monitoring equipment, automatic control system and other components. During the experimental process, the configured experimental samples were put into the sample tubes in the reactor, and the warming and pressurisation experiments were carried out under the set temperature and static rock pressure. The overlying formation pressure is simulated by the axial pressure, the pore fluid pressure is regulated by the backpressure booster pump, the constant flow pressure is slowly increased by the constant flow pressure pump to fill the fluid and make it slowly flow through the samples, the strata temperature is simulated by the heater and the temperature control device on the core gripper of the reactor, and the compaction displacement is recorded by the high-precision precision displacement sensors on the two ends of the core gripper (Figure 1).
Figure 1. Schematic diagram of compaction physical simulation experiment device (modified from Zhou et al., 2011).
The samples used in this experiment were modern sediments taken from the surface layers of the sedimentary areas of Golden Beach and Silver Beach in Qingdao, Liansan Island, and Lingshan Island. The compaction physics simulation experiments were carried out by means of artificial natural sampling, and the composition of the experimental samples was referred to the actual clastic group distribution ratio of the deep Permian sandstone and conglomerate reservoir cores in Fukang Sag. The rock type of the reservoir is dominated by clastic sand (conglomerate), and the distribution of quartz content in the grains ranges from 2% to 12%, with an average of 7.5%; the distribution of feldspar content ranges from 3% to 17%, with an average of 8.4%; the distribution of clastic content ranges from 67% to 93%, with an average of 84.1%. In view of this, the seashore glutenite of Qingdao, which is close to the source of this area, was selected as the physical simulation source sample for the experiment, taking 10% quartz particles content, 10% feldspar particles content and 80% rock debris particles content. The source samples were sieved into different particle size groups by sieve analysis and rounded into sub-angular and sub-rounded samples. Accordingly, artificial samples under the corresponding experimental conditions were prepared for physical modelling.
The Junggar Basin is a typical low-temperature cold basin in the west (Cao et al., 2022), and the Fukang Sag is located in the southeastern part of the central depression of the Junggar Basin, the Upper Urho Formation develops a thick layer-scale glutenite reservoir, with the depth of burial ranging from 4,500 to 6,000 m. According to the actual geological situation of the basin, the strata density of 2.5 g/cm3, the ground temperature gradient of 2.4 °C/hm. The present formation water of Upper Urho Formation in Fukang Sag is CaCl2 type. The density of strata water of 1.01 g/cm3, and the pressure coefficient under the normal compaction condition are set to be 1.0. Combining the above parameters and setting the temperature and pressure conditions of each depth, the simulated maximum burial depth of the study area is set to be 7,000 m (Table 1).
The rock structure of glutenite reservoir of the Upper Urho Formation in the Fukang Sag is complex, with low maturity of composition and structure, and the fraction of clastic particles is dominated by plastic clasts, with an average content of more than 80%, and the average content of quartz, feldspar and other rigid particles is less than 10%, with a wide range of particle size, poor sorting as a whole, and the gravel particles are filled with both sand-scale particles and muddy matrix. Based on the actual geological analysis of the study area, there is little variation in the mineralogical components of the rock, and there is a difference between sand and mud in the support structure and fill material characteristic of the glutenite. Therefore, three sets of variables, grain size, sand content and mud matrix content, were selected and introduced into the compaction physics simulation experiment to investigate the effect of each single factor on the preservation of intergranular porosity in glutenite reservoirs. The experiment was divided into a total of 11 control groups, of which 4 were grain size controls, four were sand content controls, and three were mud matrix tcontent controls, and were analysed and compared within the groups (Table 2). After the physical simulation experiments, the compacted samples were removed after natural cooling to room temperature and pressure unloading to atmospheric pressure (Figure 2) for subsequent cast thin section preparation and microscopic observation.
Figure 2. Sample effect diagram before and after compaction physical simulation experiment (A) Compacted samples with 10% sand content; (B) Compacted samples with 20% sand content; (C) Compacted samples with 30% sand content.
During the experiment, the computer monitors and records the changes in temperature, pressure, fluid flow rate, compaction displacement and other relevant experimental conditions and parameters. When the corresponding depth point reached and the pressure was confirmed to be stable, the data were collected to gather and analyse the results at different depths. The calculation method of porosity during the simulation experiment is as follows (Formulas 1–4) (Cao et al., 2011):
where r is the radius of the sample cross-section, cm; L0 is the length of the sample, cm; S0 is the cross-sectional area of the sample, cm2; V0 is the original volume of the sample, cm3; Vϕ is the original volume of the pore, cm3; Vg is the volume of the skeleton of the sample, cm3; ϕ0 is the original porosity.
After measuring its original volume, the samples were dried and then the skeleton volume was measured by the drainage method to find the original porosity ϕ0.
From the recorded compaction displacements, the volume of the rock sample at each depth point during compaction can be derived (Formula 5):
where L1 is the experimentally recorded compaction displacement, cm; V is the volume of the rock sample at each point during compaction, cm3.
During the experiment, it is assumed that the volume of the skeleton remains essentially constant. Then there is (Formula 6):
where ϕ is the porosity at each depth point during compaction.
(1) Preservation of intergranular pores by different grain sizes
By preparing and observing cast thin sections of the compacted samples, it is possible to qualitatively describe the degree of compaction hole reduction and the mode of compaction deformation during the simulated experiments. It is worth noting that, in the cast thin sections obtained from the compaction experiments, the particles were found to be loose under microscopic observation, partly due to the outward expansion of the samples after the release of the compaction, and partly due to the lack of systematic diagenesis in the physical simulation experiments, but the microscopic observation can still obtain more effective information on the contact relationship between the particles, the arrangement characteristics, and the fracture information of the compression under force. It was found that the sandstone particles with smaller grain size were adjusted by sliding, rotation, displacement and other positional adjustments, and the particles were rearranged, presenting certain directional arrangement characteristics, and the rupture degree of the particles was smaller. For gravel particles with larger grain size, positional adjustment occurs, the arrangement tends to stabilise, the particles tend to contact the long axis more closely, and the particle skeleton reaches the compressive limit of the rupture phenomenon is more obvious (Figure 3).
Figure 3. Compaction characteristics of samples with different grain size (A) Sample with grain size 0.25–0.5 mm, partially orientated arrangement of particles (−); (B) Sample with grain size 0.5–1.0 mm, obvious orientated arrangement of particles (−); (C) Sample with grain size 2.0–3.0 mm, particles supported, low degree of rupture (−); (D) Sample with grain size 2.0–3.0 mm, particles orientated arrangement (−); (E) Sample with grain size 3.0–4.0 mm, particles orientated and tightly arranged (−); (F) Sample with grain size 3.0–4.0 mm, particles supported, visible rupture (−).
The results of physical simulation experiments on mechanical compaction of samples with different grain sizes show that the porosity evolution has a segmented characteristic (Figure 4). In the early stage of mechanical compaction, with the increase of pressure, the debris particles slide, misalign and rotate, rearranging and adjusting their positions so as to reach the state of compact accumulation, i.e., the rapid compaction stage; after this stage, the debris particles reach a stable stacking state, and with the increase of pressure, the degree of compact stacking increases and the porosity decreases slowly, this is the slow compaction stage. Meanwhile, it was found that with the gradual increase of the sample grain size, the stage of rapid change gradually became shorter, and it was analysed that the gravel scale formed the support structure faster than the sand scale particles, and the adjustment of particles in the later stage was smaller, the reservoir was more resistant to pressure. In addition, based on the results of physical simulation experiments, the relationship between porosity and depth of the four groups of samples was obtained by fitting curves, and the results showed that porosity and depth were basically in a logarithmic relationship (Table 3).
Figure 4. Physical simulation experiment results of mechanical compaction of samples with different grain size (A) Porosity-pressure correlation; (B) Porosity-depth correlation.
Through the quantitative analysis of the test data, in the rapid compaction stage, the rate of pore reduction was 11.8%/km for samples with grain sizes of 0.25–0.5 mm, 11.5%/km for samples with grain sizes of 0.5–1.0 mm, 10.5%/km for samples with grain sizes of 2.0–3.0 mm, 11.2%/km for samples with grain sizes of 3.0–4.0 mm, it shows that the rate of pore reduction is larger for samples with smaller grain size in this stage. During the slow compaction stage, the rate of pore reduction was 1.16%/km for samples with grain sizes of 0.25–0.5 mm, 1.17%/km for samples with grain sizes of 0.5–1.0 mm, 0.94%/km for samples with grain sizes of 2.0–3.0 mm, and 0.68%/km for samples with grain sizes of 3.0–4.0 mm (Figure 5). Therefore, the preservation of pore space by grain size is mainly in the slow-change compaction stage. It was analysed that, with the increase of burial depth and overlying pressure, the finer-grained samples have less force per unit area, and their overlying pressure is mainly used to squeeze the pore space, while the coarser-grained samples have more force per unit area, and the support structure formed earlier carries part of the pressure and reduces part of the force to squeeze the pore space. Therefore, the coarser grain size samples have better pore preservation ability.
(2) Preservation of intergranular pores by different sand contents
Figure 5. Mechanical compaction pore reduction characteristics of samples with different grain size.
Microscopic observation revealed that with the increase of sand content, the sand-scale particles gradually occupied the intergranular pore space, and the gravel-scale particles gradually transitioned from point contact to floating, while the long-axis contact of the particles gradually weakened (Figure 6). By analysing the pore evolution of the compaction simulation with different sand contents, the porosity evolution with depth was also segmented (Figure 7), and the results of the fitted curves yielded a logarithmic relationship between porosity and depth for samples with different sand contents (Table 4).
Figure 6. Compaction characteristics of samples with different sand content (A) Samples with 20% sand content (−); (B) Samples with 30% sand content (−); (C) Samples with 50% sand content (−).
Figure 7. Physical simulation experiment results of mechanical compaction of samples with different sand content. (A) Porosity-pressure correlation; (B) Porosity-depth correlation.
During the fast compaction stage, the samples show similar trends in porosity evolution and insignificant differences in pore reduction. After entering the slow compaction stage, with the increase of overburden pressure, the evolution process of the samples began to show a non-monotonic pattern, i.e., the pore reduction rate showed a tendency of decreasing and then increasing with the increase of sand-scale particle content. Further quantitative analysis of the test data showed that in the fast compaction stage, the rate of pore reduction was 8.15%/km for samples of 20% sand content, 8.44%/km for samples of 30% sand content, 7.94%/km for samples of 40% sand content, and 6.75%/km for samples of 50% sand content. During the slow compaction stage, the rate of pore reduction was 0.68%/km for samples of 20% sand content, 0.55%/km for samples of 30% sand content, 0.67%/km for 40% samples of sand content, and 0.97%/km for samples of 50% sand content, which shows that the pore preservation effect of the samples with different sand contents is mainly reflected in this stage (Figure 8).
Figure 8. Mechanical compaction pore reduction characteristics of samples with different sand content (A) Characteristics of total pore reduction rate for samples with different sand content; (B) Characteristics of different stages of pore reduction rate for samples with different sand content.
It was analysed that in the rapid compaction stage, when the position of particles of different grain sizes was adjusted and rearranged, the finer particles were forced to squeeze and fill in the pore space formed by the arrangement of coarse particles, resulting in a rapid loss of porosity. However, after entering the slow compaction stage, the particles have a stable stacking state, and compaction further increases the tightness of the particles and the degree of compaction. At this time, the content of sand particles is not enough to completely fill the pore between gravel particles, the pressure increase will be further extrusion caused by the loss of the pore, and when the sand particle content exceeds the limit of filling the pore between gravel particles, the gravel particles show incomplete contact, which makes it difficult to form a stable mechanical structure between the gravel particles, and the pressure increase will be turned to extrusion of sand particles caused by the loss of the pore. Therefore, only when the sand-scale particles can just fill the pore between gravel-scale particles, the external gravel bridges the pressure, and the internal sand particles take over the pressure, which makes the best preservation of the intergranular pore space. It was found by the experiment that when the sand particles can just fill the pore space between gravels, the content of sand particles is about 30%.
(3) Preservation of intergranular pores by different mud matrix contents
Through microscopic observation, it was found that the particles of the sample with matrix content of 5% were mainly in point contact, with only a small amount of line contact. With the gradual increase of compaction effect, the particles tend to be tight contact with each other, and a small number of micro-cracks begin to appear on the surface of the particles. For loose gravel particles with 10% matrix, the intergranular space was filled with matrix, and the intergranular pore was further reduced. Loose gravel grade particles with 15% matrix radicals, the contact degree of the particles is increasing, the position between the particles is adjusted, and the matrix radicals are squeezed and filled into the remaining intergranular pore, which makes the pore decrease significantly and the intergranular pore reduce (Figure 9).
Figure 9. Characteristics of samples with different mud content (A) Samples with 5% mud content (−); (B) Samples with 10% mud content (−); (C) Samples with 15% mud content (−).
By analysing the pore evolution of the compaction simulation for different mud contents, the porosity evolution with depth is also segmented, and the results of the fitted curves yielded a logarithmic relationship between porosity and depth for the samples with different clay contents (Table 5). In addition, it was found that the rate of pore reduction gradually increases with the increase of matrix content (Figure 10).
Figure 10. Physical simulation experiment results of mechanical compaction of samples with different mud matrix content. (A) Porosity-pressure correlation; (B) Porosity-depth correlation.
In the fast compaction stage, the rate of pore reduction was 5.4%/km for samples with 5% mud content, 6.0%/km for samples with 10% mud content, and 6.3%/km for samples with 15% mud content. In the slow compaction stage, the rate of pore reduction was 0.74%/km for samples with 5% mud content, 0.79%/km for samples with 10% mud content, 0.97%/km for samples with 15% mud content (Figure 11).
Figure 11. Mechanical compaction pore reduction characteristics of samples with different mud contents (A) Characteristics of total pore reduction rate of samples with different mud contents; (B) Characteristics of different stages of pore reduction rate of samples with different mud contents.
It is analysed that at the early stage of compaction, different contents of mud matrix were forced to squeeze into the intergranular pore, resulting in a reduction of porosity, and with the increase of overburden pressure, the samples with higher matrix content had greater intergranular matrix filling degree, resulting in a greater reduction of porosity. It shows that high matrix content will occupy intergranular pore, especially for gravel close to the source and easy to receive a large number of source area deposits, usually the storage space is not developed, and the preservation of intergranular pore is poor.
(1) In the process of mechanical compaction of glutenite, the change of porosity with depth is segmented, i.e., the fast-change phase in the early stage of compaction and the slow-change phase in the later stage. The depth of the boundary between the fast-change and slow-change phases is about 1,000 m.
(2) Regression fitting using the slow-change phase data revealed a good logarithmic relationship between depth and porosity during diagenesis compaction, with correlation coefficients of 0.90 or higher for the data fitting results of the 11 sets of experiments.
(3) In the case of only experiencing mechanical compaction, the coarser the grain size of the sample particles, the smaller the rate of compaction pore reduction during compaction, the more pores are eventually preserved, and the preservation of pores by the grain size is mainly reflected in the stage of slow-change compaction.
(4) When the sand particles fill the pore space between gravels, the stable secondary support structure formed by gravel-scale and sand-scale can effectively take over the pressure, and when the content of sand particles is about 30%, the pressure-bearing capacity is the strongest. The preservation effect of sand particles on pore is mainly reflected in the slow-change compaction stage.
(5) Samples with high mud matrix content have low initial porosity and greater intergranular matrix filling, and samples with high mud matrix content have a greater rate of pore reduction throughout all stages of the compaction process, so high matrix content is not conducive to the preservation of intergranular pores.
The original contributions presented in the study are included in the article/Supplementary material, further inquiries can be directed to the corresponding author.
HG: Writing–review and editing. DW: Writing–original draft. XS: Writing–review and editing. BP: Writing–review and editing. ZZ: Writing–review and editing. JW: Writing–review and editing. KL: Writing–review and editing.
The author(s) declare that financial support was received for the research, authorship, and/or publication of this article. PetroChina Key Research Program on Deep Petroleum System in the Tarim Basin (No. ZD 2019-183-001-003).
The authors declare that the research was conducted in the absence of any commercial or financial relationships that could be construed as a potential conflict of interest.
All claims expressed in this article are solely those of the authors and do not necessarily represent those of their affiliated organizations, or those of the publisher, the editors and the reviewers. Any product that may be evaluated in this article, or claim that may be made by its manufacturer, is not guaranteed or endorsed by the publisher.
Bjørlykke, K. (2014). Relationships between depositional environments, burial history and rock properties. Some principal aspects of diagenetic process in sedimentary basins. Sediment. Geol. 301, 1–14. doi:10.1016/j.sedgeo.2013.12.002
Cao, Y. C., Xi, K. L., Wang, J., Yuan, G. H., and Yang, T. (2011). Preliminary study on diagenetic simulation experiment of mechanical compaction and physical property evolution of sandstone. Geoscience 25, 1152–1158. (in Chinese). doi:10.3969/j.issn.1000-8527.2011.06.014
Cao, Y. C., Yuan, G. H., Yang, H. J., Wang, Y. Z., Liu, K. Y., Zan, N. M., et al. (2022). Current situation of oil and gas exploration and research progress of the origin of high-quality reservoirs in deep-ultra-deep clastic reservoirs of petroliferous basins. Acta Petrol. Sin. 43, 112–140. (in Chinese). doi:10.7623/syxb202201010
Carvalho, A. D. S. G., and Ros, L. F. D. (2015). Diagenesis of aptian sandstones and conglomerates of the campos basin. J. Petrol. Sci. Eng. 125, 189–200. doi:10.1016/j.petrol.2014.11.019
Chuhan, F. A., Kjeldstad, A., Bjørlykke, K., and Høeg, K. (2002). Porosity loss in sand by grain crushing—experimental evidence and relevance to reservoir quality. Mar. Petrol. Geol. 19, 39–53. doi:10.1016/S0264-8172(01)00049-6
Chuhan, F. A., Kjeldstad, A., Bjørlykke, K., and Høeg, K. (2003). Experimental compression of loose sands: relevance to porosity reduction during burial in sedimentary basins. Can. Geotech. J. 40, 995–1011. doi:10.1139/t03-050
De Cola, F., Pellegrino, A., Glößner, C., Penumadu, D., and Petrinic, N. (2018). Effect of particle morphology, compaction, and confinement on the high strain rate behavior of sand. Exp. Mech. 58, 223–242. doi:10.1007/s11340-017-0331-x
Gao, Z. Y., Cui, J. G., Fan, X. R., Feng, J. R., and Shi, Y. X. (2023). The mechanism of abnormal fluid pressure on the physical properties of deep reservoirs: a case study of the Jurassic Toutunhe Formation in the southern margin of Junggar Basin. Petrol. explor. Dev. 50, 1221–1232. (in Chinese). doi:10.11698/PED.20230030
He, H. Q., Zhi, D. M., Tang, Y., Liu, C. W., Chen, H., Guo, X. G., et al. (2021). A great discovery of well kangtan 1 in the Fukang Sag in the Junggar Basin and its significance. China Petrol. Explor 26, 1–11. (in Chinese). doi:10.3969/j.issn.1672-7703.2021.02.001
Hou, G. F., Ji, Y. L., Wu, H., Li, L. L., Wang, Y. S., and Wang, W. (2017). Quantitative characterization on the influence factors of porosity and permeability characteristics of clastic reservoirs by physical experiment simulation. Geol. Sci. Technol. Inf. 36, 153–159. (in Chinese). doi:10.19509/j.cnki.dzkq.2017.0419
Ji, Y. L., Wu, H., Wang, Y. S., Zhou, Y., Wang, W., Hou, G. F., et al. (2017). Applying physical simulation to study the physical property evolution in clastic reservoirs: a case from the paleogene shahejie Formation in the shengli oil zone, bohai bay basin. Geol. J. China Univ. 23, 657–669. (in Chinese). doi:10.16108/j.issn1006-7493.2017042
Kang, X., Hu, W., Cao, J., Wu, H., Xiang, B., and Wang, J. (2019). Controls on reservoir quality in fan-deltaic conglomerates: insight from the lower triassic baikouquan formation, Junggar Basin, China. Mar. Petrol. Geol. 103, 55–75. doi:10.1016/j.marpetgeo.2019.02.004
Li, M. Q., Zhang, L. Q., Li, Z. H., Zhang, L., Mao, L. X., and Xu, X. T. (2021). Diagenetic facies division and logging identification of tight sandstone in the lower conglomerate member of Lower Jurassic Ahe Formation in Tarim Basin: case study of Yiqikelike area in Kuqa Depression. Nat. Gas. Geosci. 32, 1559–1570. (in Chinese). doi:10.11764/j.issn.1672-1926.2021.03.001
Li, Y., Xue, Z. J., Cheng, Z., Jiang, H. J., and Wang, R. Y. (2020). Progress and development directions of deep oil and gas exploration and development in China. China Petrol. Explor 25, 45–57. (in Chinese). doi:10.3969/j.issn.1672-7703.2020.01.005
Liu, B., Yang, Y., Li, J., Chi, Y., Li, J., and Fu, X. (2020). Stress sensitivity of tight reservoirs and its effect on oil saturation: a case study of Lower Cretaceous tight clastic reservoirs in the Hailar Basin, Northeast China. J. Petrol. Sci. Eng. 184, 106484. doi:10.1016/j.petrol.2019.106484
Liu, G. Y., Liu, Y., and Zhang, L. P. (2006). Experimental study on the effects of compaction on the properties of sandstone reservoir. J. Xi’an Shiyou Univ. Nat. Sci. 21, 24–28. (in Chinese). doi:10.3969/j.issn.1673-064X.2006.04.006
Mahmic, O., Dypvik, H., and Hammer, E. (2018). Diagenetic influence on reservoir quality evolution, examples from Triassic conglomerates/arenites in the Edvard Grieg field, Norwegian North Sea. Mar. Petrol. Geol. 93, 247–271. doi:10.1016/j.marpetgeo.2018.03.006
Pang, X., Jia, C., Zhang, K., Li, M., Wang, Y., Peng, J., et al. (2020b). The dead line for oil and gas and implication for fossil resource prediction. Earth Syst. Sci. Data 12, 577–590. doi:10.5194/essd-12-577-2020
Pang, X. J., Niu, C. M., Du, X. F., Wang, Q. B., and Dai, L. M. (2020a). Quantitative characterization of sandstone reservoir difference between member 1 and member 2 of shahejie Formation in northeastern margin of shijiutuo uplift, bohai sea. Acta Petrol. Sin. 41, 1073–1088. (in Chinese). doi:10.7623/syxb202009004
Sun, L. D., Zou, C. N., Zhu, R. K., Zhang, Y. H., Zhang, S. C., Zhang, B. M., et al. (2013). Formation, distribution and potential of deep hydrocarbon resources in China. Petrol. explor. Dev. 40, 687–695. (in Chinese). doi:10.1016/s1876-3804(13)60093-2
Taylor, T. R., Giles, M. R., Hathon, L. A., Diggs, T. N., Braunsdorf, N. R., Birbiglia, G. V., et al. (2010). Sandstone diagenesis and reservoir quality prediction: models, myths, and reality. AAPG Bull. 94, 1093–1132. doi:10.1306/04211009123
Wang, B. (2020). Study on formation mechanism and seismic prediction method of deep sandy conglomerate dessert reservoir in Mahu area, Junggar Basin. [dissertation]. Chengdu: Chengdu University of Technology. (in Chinese).
Wei, W., Zhu, X., Tan, M., Xue, M., Guo, D., Su, H., et al. (2015). Diagenetic and porosity evolution of conglomerate sandstones in bayingebi formation of the lower cretaceous, chagan Sag, China-Mongolia frontier area. Mar. Petrol. Geol. 66, 998–1012. doi:10.1016/j.marpetgeo.2015.08.011
Xie, Y. H., Zhang, G. C., Shen, P., Liu, L. F., and Huang, S. B. (2018). Formation conditions and exploration direction of large gas field in Bozhong Sag, Bohai Bay Basin. Acta Petrol. Sin. 39, 1199–1210. (in Chinese). doi:10.7623/syxb201811001
You, L., Qu, X. Y., Zhong, J., Li, C., Wu, S. J., Gao, Y., et al. (2019). Physical simulation experiments on pore evolution in high-temperature and overpressure reservoirs. Nat. Gas. Ind. 39, 21–30. (in Chinese). doi:10.3787/j.issn.1000-0976.2019.07.003
Yuan, G., Cao, Y., Qiu, L., and Chen, Z. (2017). Genetic mechanism of high-quality reservoirs in Permian tight fan delta conglomerates at the northwestern margin of the Junggar Basin, northwestern China. AAPG Bull. 101, 1995–2019. doi:10.1306/02071715214
Yue, Z. Q. (2019). Diagenetic characteristics of sand conglomerate in Mahu Depression, Junggar Basin and its influence on reservoir. Xi’an: Northwest University. [master’s thesis] (in Chinese).
Keywords: compaction physics simulation, clastic reservoirs, rock fabric, intergranular pore, compaction
Citation: Guo H, Wang D, Shan X, Peng B, Zou Z, Wu J and Li K (2024) Preservation of intergranular pore in deep clastic reservoirs by rock fabric based on compaction physics simulation experiments. Front. Earth Sci. 12:1433517. doi: 10.3389/feart.2024.1433517
Received: 16 May 2024; Accepted: 11 June 2024;
Published: 04 July 2024.
Edited by:
Jianguo Zhang, China University of Geosciences, ChinaReviewed by:
Changyu Fan, Northwest University, ChinaCopyright © 2024 Guo, Wang, Shan, Peng, Zou, Wu and Li. This is an open-access article distributed under the terms of the Creative Commons Attribution License (CC BY). The use, distribution or reproduction in other forums is permitted, provided the original author(s) and the copyright owner(s) are credited and that the original publication in this journal is cited, in accordance with accepted academic practice. No use, distribution or reproduction is permitted which does not comply with these terms.
*Correspondence: Daoshen Wang, d2FuZ2Rhb3NoZW4xOTk2QDE2My5jb20=
Disclaimer: All claims expressed in this article are solely those of the authors and do not necessarily represent those of their affiliated organizations, or those of the publisher, the editors and the reviewers. Any product that may be evaluated in this article or claim that may be made by its manufacturer is not guaranteed or endorsed by the publisher.
Research integrity at Frontiers
Learn more about the work of our research integrity team to safeguard the quality of each article we publish.