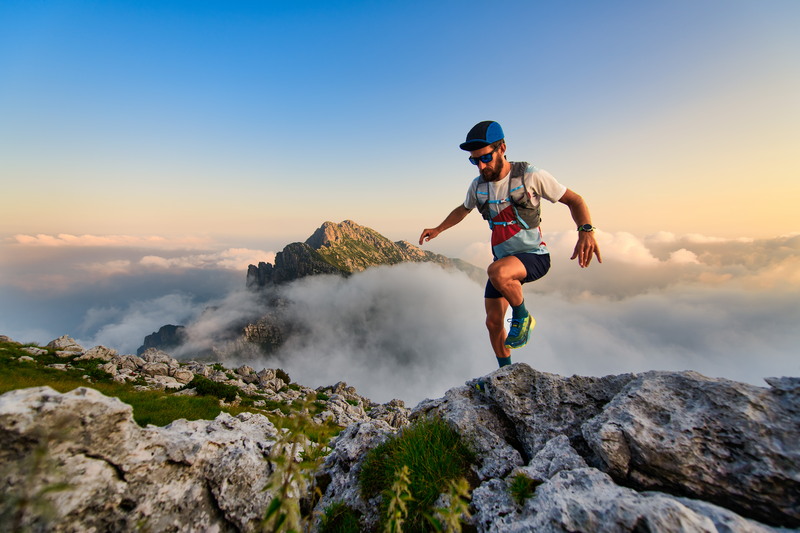
95% of researchers rate our articles as excellent or good
Learn more about the work of our research integrity team to safeguard the quality of each article we publish.
Find out more
ORIGINAL RESEARCH article
Front. Earth Sci. , 18 April 2024
Sec. Geohazards and Georisks
Volume 12 - 2024 | https://doi.org/10.3389/feart.2024.1395882
This article is part of the Research Topic Monitoring, Early Warning and Mitigation of Natural and Engineered Slopes – Volume IV View all 30 articles
Dynamic disasters seriously threaten the safety and effectiveness in deep mining. The mechanism of stick-slip instability occurrence on the deep coal-rock structure was studied in this paper through analyzing the occurrence condition of stick-slip in the weak surface and discussing the friction constitutive of the coal-rock structure. The result indicated that the grinding slip and the soft interlayer formation occurred in weak plane in the coal-rock structure in the process of diagenesis and strata movement, which is more likely to satisfy the stick-slip condition and then trigger dynamic disaster. Based on the mechanism study of coal-rock structure failure caused by stick-slip, it is proposed that the horizontal compression pulse caused by local stick-slip in coal seam could lead the layer-crack and fly out with the broken fragments. At the same time, it is pointed out that the scattering effect of the plane compression pulse in the propagation process induces the serial sliding instability of the coal-rock structure in many places, forming a large range of dynamic disasters. By means of numerical simulation of coal bump accident in a roadway in Yima Coal Mines, the dynamic process of sliding-slip instability of coal and rock mass is inverted, and the mechanism of sliding-slip instability of coal and rock structure is verified.
Coal-rock body comprises structure bodies and structure planes, and the slip and friction of structure planes in coal-rock body are its important mechanical properties (Guang-zhi et al., 2005). In seismic research, stick-slip occurrence on the friction surface is considered a mechanism of shallow-focus earthquakes, and has been introduced by scholars into the study of coal bumps. Qi et al. (Qing-xin et al., 1995) explored the mechanism of stick-slip occurrence, and introduced the mechanism of coal bump occurrence based on the stick-slip experiment of coal-rock combination. Jiang et al. (Yao-dong et al., 2005; Yao-Dong et al., 2013) established a three-dimensional model of instability of translatory coal bumps in gateways, and designed double-sided shear tests to verify the occurrence of coal-rock structural instability type coal bump induced by stick-slip. The structural instability was summarized into three stages, and the stick-slip phenomenon was attributed to the different dynamic and static friction coefficients. Yin et al. (Guang-zhi et al., 2005) drew on the two-state variable constitutive model to describe the dynamic and evolutionary behavior of coal bumps, thereby more accurately reflecting the stick-slip characteristics of coal bump systems. Li et al. (Hai-tao et al., 2018) proposed a clamping model of coal seam roof and floor to coal seam, and held that coal seams may accumulate much energy under high stress. When weak structure planes are disturbed, stick-slip will occur, inducing the release of energy accumulated, causing large-scale structural instability, then resulting in coal mine dynamic disasters. Yan et al. (Yong-gan et al., 2010) built a mechanical model for the occurrence of coal body stick-slip relative to the roof and floor, studied the conditions for coal body stick-slip, and obtained the dynamic equation of the coal body after the occurrence of stick-slip. Despite their breakthroughs, the studies described above have mainly focused on the block structure of coal-rock, without giving sufficient attention to either the properties of the coal-rock structure plane itself or the specific mechanisms of its impact on stick-slip. As a result, they have failed to obtain further details on the coal bump induced by stick-slip.
For this reason, by taking the properties of coal-rock structure planes and their related influencing factors as the research object, and introducing the friction constitutive equation, this paper discusses the influence of structure plane properties on stick-slip and establishes the motion equation of horizontal compression pulse that it induces, so as to obtain the mechanism of coal-rock structure failure and instability caused by it. In addition, this paper also establishes a numerical calculation model based on on-site conditions for fitting and verification, thereby restoring the process of coal mine dynamic disasters.
The rock body structure controls the deformation mechanism, failure mechanism, and mechanical properties of the rock body, and is composed of structure planes and structure bodies. Specifically, various complex geological interfaces within the rock body are collectively referred to as structure planes. The coal-rock body formed by sedimentation has obvious bedding structure, and structure planes are naturally formed between coal seams and rock layers. Meanwhile, the coal-rock body is connected together through cementation and compaction during the sedimentation process, forming a cohesive coal-rock body structure.
When the coal-rock body is in its original state, it is subjected to the combined action of overlying loads and horizontal tectonic stresses. The deformation of the coal-rock body is mainly elastic compression deformation. Microelements of the coal-rock body near the structure plane are selected, and their stress is shown in Figure 1A.
In the horizontal direction, the strain at a certain point of the structure plane is simultaneously affected by both coal and rock. However, due to the high strength of the rock body, it is assumed that the displacement of the structure plane varies with the strain of the rock body. If the structure plane is ideally smooth and the coal-rock body only undergoes compression deformation (Figure 1B), the black and gray areas represent the stress deformation of the coal-rock body, and their deformation amounts are as follows:
Where
The strain of coal body can be expressed as follows:
Based on the assumption of smooth structure planes, the strain of coal body is greater than that of the rock body, and deformation incompatibility occurs between the structure planes of the coal-rock structure. However, the coal-rock body shows an apparent unity, and the displacement of the coal-rock body at the same point on the structure plane is consistent. The deformation of the coal body is shown as the sum of the black area and the dashed area in Figure 1B. It can be inferred from this that there must be a shear force (friction force) on the structure plane of the coal-rock body in the original rock state, which causes the displacement of the structure plane of the coal-rock body to be the same at the same point. As a result, shear deformation occurs in the coal body, leading to an increase in the elastic energy accumulated inside the coal body, and the stronger this constraint is, the more elastic energy accumulates. Considering the different properties of coal-rock, the coal body in the coal-rock combination has a larger deformation and thus becomes the carrier of energy storage. When the coal-rock body is excavated or disturbed, the structure plane is destroyed and unstable, and the constraint effect of the structure plane is either reduced or disappears completely. The elastic energy accumulated in the coal body will consequently be released, likely resulting in coal mine dynamic disasters. It can be seen that the key links in the formation of dynamic disasters are all directly related to the properties of structure planes. Therefore, it is necessary to study the stress situation and inherent properties of structure planes.
In underground excavation engineering, the coal-rock body on the free face is subjected to an unloading effect, and the original stable coal-rock structure tends to slip toward the free face. From the free face to the inside, the coal body can be divided into the plastic zone and elastic zone (Yao-dong et al., 2005). As suggested in the above discussion, the stick-slip that may cause coal bump only occurs in the elastic zone (Yong-gan et al., 2010). Therefore, the interface between the elastic and plastic zones is taken as the Y-axis, with the upward side as the positive direction, while the interface between the coal seam and the floor is taken as the X-axis, with the positive direction deviating from the free face. The coal body with a length of dx in the elastic zone is taken as the research object, and the stress analysis is shown in Figure 2.
Figure 2. Force analyses of coal-rock slip (Yong-gan et al., 2010). (A) Loading, (B) stress state.
One of the most important mechanical properties of a structure plane is its shear strength, which is related to rock strength, structure plane roughness, and structure plane cohesion. According to Banton’s formula, the shear strength of the coal-rock structure plane is as follows:
Where JCS is the compressive strength of the structure plane;
For coal-rock composite rock bodies, there are significant differences in their mechanical properties, due to differences in their diagenetic composition, cementing substances, and diagenetic environment. However, the strength and stiffness of coal body are generally less than those of the rock body, while the strength of JCS is similar to that of the coal body. The geometric shape of the structure plane of the coal-rock body is generally flat and wavy, with very few serration and step shapes, and its JRC value does not exceed 10.
On the premise of not considering the coal body failure, when the horizontal structural stress is greater than the sum of the cohesive force and static friction force of weak structure plane, the coal body will slip. The critical conditions for coal body slip are as follows:
Where
When the coal-rock body satisfies Eq. 4, the coal body will slip, and the friction force it bears will change from static to dynamic friction force. However, the rock slip can be further divided into stable slip and stick slip, and not all slip will cause dynamic disasters in coal mines: only stick-slip instability may cause stress drop in the coal-rock body, after which elastic energy stored will be quickly release and dynamic changes will occur in the state of the coal-rock body. According to previous research, the slip friction force of rocks is related to their velocity, and the velocity-state friction constitutive law can be used to successfully predict the friction behavior of rocks, a method which has been widely applied in theoretical analysis and practical engineering (Dieterich, 1978; Chang-rong, 1999). Assuming that stress conditions are constant and normal, the velocity-state friction constitutive relation can be described as follows (Linker and Dieterich, 1992):
Where
Where
The deep mining of coal bodies is characterized by great burial depth and overlying load. If displacement occurs during the formation of coal-rock layers along the strata movement and when the structure plane is sheared, the surface of the coal body with lesser strength is more likely to have a breaking effect of the friction surface under the action of higher stress, due to the different strength of coal and rock in coal-rock combination. In addition, the bumps of the coal-rock body are sheared or smoothed, greatly reducing the overall strength of the shear surface and increasing the possibility of stick-slip occurrence, as shown in Figure 2A. This also explains the mechanism of higher stick-slip occurrence possibility under high stress conditions. Meanwhile, during the process of coal-rock body sedimentation or structure plane breaking, a weak plane interlayer composed of clast and debris is formed in the coal-rock structure plane, which weakens the strength of coal-rock contact surface to a certain extent, and large-scale dynamic disasters will also occur under low-stress conditions. It is worth noting that the mudded intercalation or fractured zone within the weak plane exhibits certain rheological behavior, and the long-term shear strength of the structure plane is 15%–20% lower than the instantaneous strength. As a consequence, the critical condition for stick-slip in the coal seam is reduced and the risk of dynamic disasters increases.
If the stress state of the coal-rock body meets the condition of stick-slip occurrence on the weak structure plane, then when disturbed the roof and coal seam in the dx range (
Assuming it is a linearly decaying pulse waveform, the stress amplitude at any distance x from the wavefront is expressed as follows (Qi, 1996):
Where
Where
Assuming that the time for the pulse wavefront to reach the free reflection surface is the starting point (t=0) and the stress wave velocity is
The peak intensity is generally smaller than the compressive strength of the rock, and the horizontal stress on the free face is smaller than the internal horizontal stress of the coal body, which will not cause destruction to the coal body. When the compression wave reaches the free face, it is reflected as a tensile wave of equal intensity, leading to destruction near the end face. Assuming that the pulse wave decays linearly, the maximum tensile stress occurs at half-wavelength from the free face. When the tensile stress of the section reaches or exceeds the dynamic tensile strength of the rock
Assuming that the distance between the wavefront of the reflected tensile wave and the free face is
Where when
According to the law of conservation of energy, the momentum
The velocity of fractured fragments is then obtained by combining Eq. 8 and Eqs. 11 and 12:
Eq. 13 above explains the disaster process caused by layered cracking and collapse of the coal-rock body on the free face after the occurrence of stick-slip instability in a single local area. The strength of the compression pulse and the dynamic tensile strength of the rock body determine if the coal body is destroyed, and also determine the corresponding extruding speed of the fractured coal body. The larger the overlying load is, the greater the difference between the static and stick-slip friction force, the higher the energy of the compression pulse, and the faster the rock body extruding speed will be.
In addition, when excavating gateways in deep mines, the coal-rock structure planes scattered in the mining space are likely in a critical state of slip due to the natural high stress state of the coal-rock body. In this case, the plane compression pulse induced by local stick-slip will not only cause destruction to the nearby coal-rock body, but will also form a larger range of interference due to the scattering effect of the pulse wave during the propagation process, inducing slip or even stick-slip of structure planes in critical state in other areas. Furthermore, multiple elastic stress waves will superimpose on each other in the mining space, thus triggering multiple chain reactions, in turn resulting in large-scale coal bumps. This complex multiple elastic wave action mechanism is difficult to accurately describe using mathematical expressions. However, it is clear that the damage and losses caused by such coal-rock dynamic disasters would be incalculable, and should be given sufficient attention in the actual production process.
During the excavation of the transportation roadway in the working face of a coal mine in Yima, Henan province, a coal bump accident occurred. Based on relevant data, FLAC3D was used to perform numerical simulation, and the model is shown in Figure 4A. The model is a unit thickness plate model of 50*50 m, with the top and bottom layers as the top and bottom plates, which have high strength and dimensions of 23.5*50 m. After simplification, their mechanical properties are the same. The intermediate modelled coal seam has a relatively low strength, and a thickness of 3 m. A 3*5 m rectangular coal roadway is excavated in the middle of the model, and the physical and mechanical parameters of the model are shown in Table 1. The depth of the coal seam reaches
According to the mechanism of stick-slip instability occurrence described above, when stick-slip occurs at a weak plane of the coal-rock body, a dynamic chain reaction will occur in the coal seam. The elastic energy accumulated by compression in the coal-rock layer will be transmitted to the gateway edge at an extremely high speed, and the coal body in the edge will be extruded out at high speed, thus resulting in dynamic disasters. For this reason, the loose coal body extruding out of the gateway edge was simplified as a block attached to the gateway wall, with a length of 2 m and height of 2.6 m, and without any contact with the roof and floor, as shown in Figure 4B.
To study the dynamic disasters caused by sudden stick-slip instability of coal-rock body, after the model reached equilibrium, the slip properties of the structure planes of coal-rock body were assigned by writing FISH language and referring to the stick-slip experiment results (Eq. (14)) described in Qi et al. [24]. When the shear force on the structure plane of the coal-rock layer reached its maximum friction force, it was suddenly initialized as residual friction force to simulate the occurrence of stick-slip instability.
Where
When the structure of the coal-rock body becomes unstable, the loose coal body will be extruded out. Figure 5 shows the entire dynamic process of the stick-slip instability in the coal body. The friction force on the structure surface was reduced to zero, and the corresponding displacement and velocity of the coal body in each time period were displayed at intervals of 0.02 s, respectively represented by colors and arrows.
Figure 5. Dynamic process of coal-rock structure stick-slip instability. (A) 0.01s, (B) 0.03s, (C) 0.05s, (D) 0.07s.
The velocity variation of the coal body on the free face and the right side of the extruded coal body over time is shown in Figure 6. After about 0.002 s of coal-rock structure stick-slip, the coal body transferred kinetic energy to the external extruded coal body through collision. After 0.007 s of coal-rock structure stick-slip, the velocity of the coal body was transmitted to the extruded coal body in the form of kinetic energy, and the velocity of the extruded coal body reached its maximum value, being pushed out at a maximum rate of approximately 2 m/s. At this time, the velocity of the coal body was reduced by half of the maximum value. Subsequently, the velocity of the coal body showed a fluctuating downward trend. After about 0.05 s, the velocity of the coal body decreased to 0. At this time, the displacement of the coal body reached its maximum value, and the displacement nephogram exhibited a distribution of elliptical envelope lines.
Throughout the impact process, the entire coal body moved toward the side of the adjacent gateway, and the loose coal body was extruded out at a high speed. There was strong friction between the coal seam and roof, along with obvious slip scratch and separation between the coal seam and the roof and floor. However, no obvious displacement between the roof and floor of the coal seam was observed. As shown in Figure 7, the arrows in the figure represent the displacement of the nodes. Depending on the different positions of loose blocks scattered in the gateway, the displacement of loose blocks decreased in a gradient from top to bottom, better corresponding to the form of coal body destruction in the gateway after coal bumps. The numerical simulation results are consistent with the previous description of coal bump (QI et al., 2003).
The stick-slip mechanism has opened up new avenues for the prevention of dynamic disasters. The stick-slip mechanism indicates that stick-slip instability is a dynamic phenomenon under certain conditions. Therefore, the prediction of disaster events can be achieved through the prediction of disaster occurrence conditions, and the comprehensive effects of disaster inducement factors can be determined to achieve the goal of disaster prediction. The process of preventing and controlling disasters is also a process of changing the conditions under which disasters occur. Through in-depth research on the conditions for disaster occurrence, effective measures can be taken to avoid such disasters and achieve effective prevention and control.
(1) There are natural joint faces in the structure planes of coal-rock bodies, but they generally show an apparent unity. Due to the constraint effect of the structure plane, uncoordinated deformation occurs near the structure plane of the coal-rock body, causing a certain amount of elastic energy to accumulate within the coal body. After being disturbed by stress, the constraint effect of the structure plane decreases, and the elastic energy is released.
(2) After the excavation of the coal-rock body, the occurrence of stick-slip instability must meet the critical condition of coal body slip, that is, the horizontal tectonic stress is greater than or equal to the friction force between the coal body and the roof and floor, and there is a trend of slipping towards the gateway. In addition, it must also satisfy the conditions for stick-slip occurrence.
(3) By introducing the rock friction constitutive equation, it is believed that there are many penetrating cracks in the layered structure of the coal-rock body. After slip and migration in the diagenesis process, the coal-rock structure planes undergo running-in or form weak interlayers, thus increasing the possibility of stick-slip.
(4) The application of elastic mechanics and elastic dynamics theory suggests that, due to the stick-slip between the coal seam and the roof and floor, horizontal compression pulses are formed in the coal body, and the energy accumulated in the coal seam is released, resulting in the fracturing and extruding of the coal-rock body on the free face. Due to the scattering effect of pulse propagation, large-scale disturbances are formed and lead to large-scale structural instability of coal-rock bodies, in turn causing serious dynamic disasters.
(5) A numerical simulation method was used to reproduce the coal bumps in the gateway of a mine in Yima. By assigning the structure plane with stick-slip characteristics, the stick-slip instability of coal-rock body was simulated. The results show that after 0.002 s of stick-slide, the coal body transferred kinetic energy to the loose coal body on the free face through collision and threw it out at a high speed, and after 0.05 s of stick-slide, the displacement of the coal body reached its maximum value and overall slip occurred toward the side of the adjacent gateway.
The original contributions presented in the study are included in the article/Supplementary Material, further inquiries can be directed to the corresponding authors.
ZZ: Writing–original draft. G Y: Conceptualization, Investigation, Methodology, Writing–original draft. YL: Writing–original draft. YC: Investigation, Writing–original draft, Writing–review and editing. CY: Writing–original draft. JZ: Writing–original draft.
The author(s) declare that financial support was received for the research, authorship, and/or publication of this article. This study was supported by Key Research and Development Program of China National Coal Group Corporation (20211BY001).
Authors ZZ, YL, and CY were employed by China National Coal Group Corporation. Author ZZ was employed by Coal Northwest Energy Co., Ltd. Author YL was employed by Inner Mongolia Coal Manda New Energy Chemical Co., Ltd. Author CY was employed by Ordos Branch of China Coal Energy Co. Ltd.
The remaining authors declare that the research was conducted in the absence of any commercial or financial relationships that could be construed as a potential conflict of interest.
All claims expressed in this article are solely those of the authors and do not necessarily represent those of their affiliated organizations, or those of the publisher, the editors and the reviewers. Any product that may be evaluated in this article, or claim that may be made by its manufacturer, is not guaranteed or endorsed by the publisher.
Biegel, R. L., Sammis, C. G., and Dieterich, J. H. (1989). The frictional properties of a simulated gouge having a fractal particle distribution. J. Struct. Geol. 11, 827–846. doi:10.1016/0191-8141(89)90101-6
Chang-rong, H. E. (1999). Comparing two types of rate and state dependent friction laws. Seismol. Geol. 21 (2), 137–146.
Dieterich, J. H. (1978). Time-dependent friction and the mechanics of stick-slip. Pure Appl. Geophys. 116, 790–806. doi:10.1007/bf00876539
Guang-zhi, Y. I. N., Gao-fei, D. A. I., Wen-li, P. I., et al. (2005). Study on rock burst using stick slip model. Rock Soil Mech. (3), 359.
Hai-tao, L. I., Jun, L. I. U., and Shan-kun, ZHAO (2018). Experimental study on the development mechanism of coal bump considering the clamping effect of roof and floor. J. China Coal Soc. 43 (11), 2951.
Linker, M. F., and Dieterich, J. H. (1992). Effects of variable normal stress on rock friction: observations and constitutive equations. J. Geophys. Res. 97, 4923–4940. doi:10.1029/92jb00017
Qi, Q.-xin (1996). The study on its theory and practice of rockburst led by the structure failure of bedded coal-rock mass. Beijing: China Coal Research Institute.
Qing-xin, Q. I., Tian-quan, L. I. U., and Yuan-wei, S. H. I. (1995). Mechanism of friction sliding destability of rock burst. Ground Press. Strata Control (Z1), 174–177+200.
Qi, Q., Mao, D., and Wang, Y. (2003). A study of nonlinear and discontinuous characters of rock burst. Rock Soil Mech. (S2), 575–579.
Ruina, A. L. (1983). Slip instability and state variable friction laws. J. Geophys. Res. 83 (10), 10359–10370. doi:10.1029/jb088ib12p10359
Wen-bin, T. A. N., and Chang-rong, H. E. (2007). Friction constitutive parameters of mafic rock and possibility of earthquake nucleation in the lower crust. Seismol. Geol. (01), 161–171.
Yao-Dong, JIANG, Wang, T., Yi-Min, SONG, Wang, X., and Zhang, W. (2013). Experimental study on the stick-slip process of coal-rock composite samples. J. China Coal Soc. 38 (2), 177–182.
Yao-dong, JIANG, Yi-xin, ZHAO, Wen-gang, L. I. U., and Zhu, J. (2005). Investigation on three-dimensional model of instability of translatory coal bumps in deep mining. Chin. J. Rock Mech. Eng., 24 (16) :2864 -2869.
Yong-gan, Y. A. N., Guo-rui, FENG, Ying-da, ZHAI, et al. (2010). Stick-slip conditions and dynamics analysis of coal rock burst. J. China Coal Soc. 35 (S1), 19–21.
Keywords: dynamic disaster, coal bump, stick-slip failure, layered structure weak plane, friction constitutive
Citation: Zhang Z, Yang G, Lü Y, Chen Y, Yang C and Zheng J (2024) Theoretical study on the mechanism of stick-slip instability occurrence on deep coal-rock structure. Front. Earth Sci. 12:1395882. doi: 10.3389/feart.2024.1395882
Received: 04 March 2024; Accepted: 04 April 2024;
Published: 18 April 2024.
Edited by:
Wen Nie, Jiangxi University of Science and Technology, ChinaReviewed by:
Xiaofei Jing, Chongqing University of Science and Technology, ChinaCopyright © 2024 Zhang, Yang, Lü, Chen, Yang and Zheng. This is an open-access article distributed under the terms of the Creative Commons Attribution License (CC BY). The use, distribution or reproduction in other forums is permitted, provided the original author(s) and the copyright owner(s) are credited and that the original publication in this journal is cited, in accordance with accepted academic practice. No use, distribution or reproduction is permitted which does not comply with these terms.
*Correspondence: Guanyu Yang, eWFuZ2d1YW55dW1pbmluZ0AxMjYuY29t; Yulong Chen, NjczMDU0Mzk5QHFxLmNvbQ==
†These authors have contributed equally to this work
Disclaimer: All claims expressed in this article are solely those of the authors and do not necessarily represent those of their affiliated organizations, or those of the publisher, the editors and the reviewers. Any product that may be evaluated in this article or claim that may be made by its manufacturer is not guaranteed or endorsed by the publisher.
Research integrity at Frontiers
Learn more about the work of our research integrity team to safeguard the quality of each article we publish.