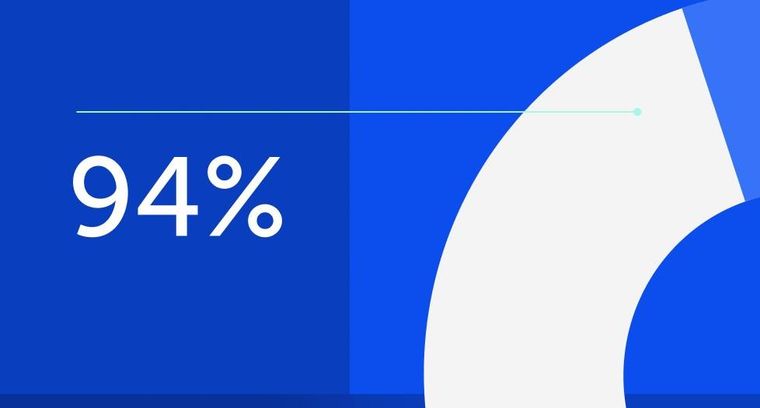
94% of researchers rate our articles as excellent or good
Learn more about the work of our research integrity team to safeguard the quality of each article we publish.
Find out more
ORIGINAL RESEARCH article
Front. Earth Sci., 29 December 2023
Sec. Geoinformatics
Volume 11 - 2023 | https://doi.org/10.3389/feart.2023.1330932
This article is part of the Research TopicSpatial Modelling and Failure Analysis of Natural and Engineering Disasters through Data-Based Methods,volume IIIView all 18 articles
The continuous development of coal science and technology has made gas and coal dust explosion disasters an important factor that restricts efficient and intelligent coal mining, which seriously threatens the safe production process of coal mines. To explore the gas and coal dust explosive overpressure and flame propagation characteristics in an actual roadway, the dynamic characteristics of gas and coal dust mixed explosion propagation and evolution laws of explosion flames were investigated using an integrated explosion test system and a high-speed image acquisition system in an engineering-level test roadway with a length of about 700 m and a cross-sectional area of 7.2 m2. Experimental results showed that the peak overpressure measured at each measuring point during the propagation process of explosion shock wave in the roadway did not rise or fall monotonously but fluctuated. The power of explosion shock wave was significantly strengthened by adding coal dust, while the flame propagation speed sharply increased in a certain zone, which generally showed a first increasing and then declining trend. In addition, the flame was blue white after the gas in the roadway was ignited, developed in an irregular shape, and ignited the surrounding combustible gas soon, which further ignited the coal dust under the combined action of pressure wave and flame front. In this case, the flame was deep yellow on the whole. The gas and coal dust explosion flame propagated along the longitudinal section above the roadway, and the flame propagated at an accelerated speed on the transverse section due to the disturbance of obstacles. The study results will provide an important theoretical basis for the R&D of technical active explosion suppression equipment in coal mines and the improvement in their installation technologies.
Gas and coal dust, which run through the whole coal mine production activity, are one of the main natural disasters in coal mines. When the gas concentration (or the concentration of coal dust suspended in the air) and oxygen concentration reach a certain limit and a high-temperature heat source is encountered, gas or coal dust explosion occurs, which not only destroys the underground ventilation network and endangers the safety of life and property but also causes a secondary explosion and brings devastating disasters to the mine. (Wang D M et al., 2021; Jia et al., 2023; Li et al., 2023). Gas and coal dust explosion includes complex physical and chemical reaction processes, and the propagation process of shock wave is a complex dynamic process of gas–solid two-phase flow coupling development. (Tousif et al., 2020). In actual coal mine production activities, gas explosion and coal dust explosion are interactive, and the mechanism of fire explosion is also complex and changeable. (Li H T et al., 2020). The generation and evolution laws of explosion flames in real roadways have not been accurately revealed to date. Therefore, exploring the gas–coal dust mixed explosive overpressure and flame propagation dynamic characteristics in engineering-level test roadways and further revealing the propagation mechanism of gas and coal dust explosion in coal mines are necessary.
As for the dust-raising mechanism of gas explosion-induced shock wave, gas explosion-induced deposited coal dust explosion has been investigated by most scholars through the explosion of experimental pipelines and numerical simulations, and gas-induced deposited coal dust explosion has been thought to belong to a gas–solid two-phase flow with a quite complicated formation process. Moreover, the motion trajectory of coal dust particles and the mechanism of gas-induced coal dust combustion explosion have been further determined through experiments and numerical simulations. (Cheng et al., 2020; Sha et al., 2021; Wang X T et al., 2021). Li J L et al. (2020), Li et al. (2022) discussed the diffusion characteristics of methane–coal dust in the pipeline. They found that the diffusion of coal dust particles in the vertical pipeline could be divided into four continuous stages: rapid injection, decelerated dispersion, stability, and settlement. The temporal and spatial evolution characteristics of the flow field in the process of dust diffusion were obtained, and the formation mechanism of coal dust clouds in the pipeline and the dynamic behavioral evolution characteristics of explosion flames were revealed. Liu et al. (2007) found that the combustion process of the methane–coal dust composite system could be divided into three stages: gaseous combustion reaction, multiphase combustion reaction, and carbon combustion reaction. They found that different kinds of coal samples and pulverized coal particle sizes greatly influenced the composite combustion reaction. Guo et al. (2020) argued that the gas explosion involving low-concentration coal dust was affected by many factors, among which the most important ones were the volatile fractions of coal dust and the gas concentration.
In the research on the visualization of gas and coal dust explosion flames, the formation process, flame shape characteristics, and flame propagation laws of gas and coal dust explosion flames in small-scale pipe network space have been comprehensively and deeply expounded through numerical simulations. (Nie et al., 2014; Ajrash et al., 2017a; Ajrash et al., 2017b; Zhang et al., 2021). Nie et al. (2015) established a pipeline experimental system with a length of 20 m and a cross section of 80 mm × 80 mm. They used a high-speed camera to shoot and record the propagation process of the explosion flame, and the image correlation coefficient method was adopted to calculate and analyze the dynamic variation characteristics of the flame velocity during the gas explosion. Sun and Lu. (2020) studied the dynamic behavior of gas explosion flames in pipelines and the change laws of the flame front structure. They found that the local velocity change of the flame was the direct factor that induced the change in the flame structure, and the interaction between flow and flame front was the internal reason. Song et al. (2018) numerically simulated the ignition of coal dust layers by gas explosion and discovered that the flame front showed a regular hemispherical shape in case of gas explosion with a low temperature. Subsequently, the dust cloud was ignited by explosion flames to form complex flames such that the flame temperature rose and the flame front wrinkled.
In the study on the propagation law of gas and coal dust explosion, factors such as gas volume dose, coal dust concentration, pipeline cross-sectional area, and obstacle distribution greatly influence on the overpressure evolution laws and flame propagation characteristics of shock wave (Wang et al., 2018; Niu et al., 2019; Niu et al., 2021; Jia et al., 2023). Ma et al. (2020) studied the influence of coal dust on methane–air explosion characteristics at low temperature. They found that the low-temperature environment would reduce the volatile matter in coal dust, which inhibited the flame propagation of methane–air/coal dust mixture, but the formed cracks and pores promoted the combustion of coke in coal dust. Niu et al. (2020) established a set of gas–coal dust mixed explosion experiment system in straight pipes and explored the overpressure evolution and flame propagation laws of coal dust explosion at different moisture contents. The experimental results showed that the coal dust deposited in the pipeline exploded under the induction of gas explosion when the moisture content was lower than 15.12%, and the underground environmental conditions were complex and changeable. The pipeline characteristics such as turning, bifurcation, and sudden change in the cross-sectional area would evidently influence the propagation of gas and coal dust explosion. Jing et al. (2021) comprehensively and deeply probed into the overpressure variation and distribution of the gas–coal dust coupling explosive shock wave in bifurcated pipes. They concluded that the larger bifurcation angle of the pipe resulted in the greater overpressure of the explosion shock wave, and the maximum overpressure of the explosive shock wave appeared in front of the bifurcation point.
Experiments in previous studies were usually conducted using small-scale pipe networks or through numerical simulations. The results cannot reflect the flame propagation laws and combustion forms of gas and coal dust explosion in actual roadways and also fail to visualize the meso-structural evolution of explosion flames inside actual roadways. In addition, an obvious size effect is observed in explosion, and the explosion characteristics do not simply follow the geometrical similarity law, which causes difficulty in quantitatively deducing the large-scale situation through small-scale experiments. In this study, a testing technique and the testing method were used in an engineering-level test roadway with a cross-sectional area of 7.2 m2 and a total length of about 700 m which is the largest underground engineering level tunnel test system in the Asia Pacific region and the only one in China, to explore the gas and coal dust explosive overpressure and flame propagation characteristics and their variation laws.
The experimental system (Figure 1) mainly consisted of five parts: large-scale test roadway, comprehensive explosion test system, gas distribution circulation system, ignition system, and ventilation system. It could realize the simulation test of gas and coal dust explosion propagation with an actual scale under different conditions. The total length of the explosion test roadway was about 700 m, which was composed of drift and inclined roadway. The front drift was 400 m long, and the end of the drift was connected to an inclined roadway with a length of 300 m and an inclination angle of 24°. The cross section of the roadway was a semicircular arch with an area of 7.2 m2. Niche boxes were arranged in the walls on both sides of the roadway, and sensors (e.g., pressure and flame sensors) for testing explosion information could be installed in the niche boxes. The high-speed image acquisition system was mainly composed of explosion-proof high-speed camera, explosion-proof camera, signal receiving equipment, and display components. Among them, the high-speed camera was the main component to collect the explosion flame image, which was characterized by high definition and speed. The full-frame resolution was ≥1,280×800 pixels, the full-frame shooting rate was ≥5,000 frames per second, and the highest shooting rate was ≥600,000 frames per second. The explosion-proof camera was designed to bear pressure of 2.0 MPa with the maximum resolution of 1,280×960, which could realize 20 × optical zoom, and the focal length was 4.3–86 mm. In addition, the installation position of the high-speed camera in the roadway corresponded to the installation positions of sensors such as explosion pressure and flame sensors, which were located 0, 10, 20, 40, 60, 80, 100, and 120 m at the closed end of the roadway.
From the starting end of tunnel explosion (the position of the explosion door), a niche box was arranged at intervals of 0 m within 40 m; beyond 40 m, a niche box was arranged every 20 m. During the experiment, the sensors were arranged from 10 m to 160 m, and the position of the sensor from the ignition source is shown in Figure 2. In the experiment, three ignition heads of No.8 industrial electric detonators were used as trigger sources to detonate the gas mixture, and the gas explosive shock wave lifted coal dust up, which formed a secondary explosion of gas and coal dust.
Coal dust was provided by Wulunshan Coal Mine in Guizhou, China. The approximate analysis of coal dust is listed in Table 1. Test coal dust was evenly arranged in the coal dust explosion propagation interval of the roadway at 15–120 m away from the explosion door by a length of 105 m. The volatile matter content in the used coal dust was >40%, the particle size was 85%≤0.075 mm, and the dose of coal dust was about 150 g/m3 according to the roadway space.
Before the test, the test sensors were first arranged in the niche boxes at different measuring points in the test roadway, and the communication lines were ensured to be smooth through the test. The high-speed camera was installed in the corresponding position of the roadway, the shooting angle was adjusted, and the smooth video transmission was guaranteed through the test. The ignition head was laid in the ignition position. Second, the roadway was sealed with plastic film, and the hydraulic explosion door was closed such that a sealed initiation chamber was formed between the sealing film and the explosion door. A certain amount of gas was filled into the initiation chamber through the gas distribution circulation system, and the gas and air were circulated and stirred such that they were fully and evenly mixed. The gas concentration was accurately measured with a gas detector, and the gas concentration in the initiation chamber was appropriately adjusted through the gas distribution circulation system. Then, the gas and coal dust were ignited by the ignition system. In this way, the gas and coal dust exploded and spread in the roadway. At the same time of ignition, the comprehensive explosion test system and the high-speed image acquisition system were triggered, and the explosion pressure and flame information of each measuring point in the propagation direction of the roadway were collected by the comprehensive explosion test system. The high-speed image acquisition system was used to collect the explosion propagation image. After the experiment was completed, the test roadway was finally ventilated by the ventilation system for at least 20 min. Thereafter, the tester could enter the test roadway to prepare for the next experiment.
The gas explosion propagation test was performed via the engineering-level roadway test system, and the high-definition flame images in the process of gas ignition, detonation, and propagation were captured with the help of the image acquisition system. The volume of gas–air mixture was set to 100 m3, and the volume fraction was controlled between 8.5% and 10.0%. During the gas-induced explosion test of deposited coal dust, moreover, coal dust racks had to be hung at different positions in the roadway before sealing with the film, and coal dust had to be laid on the roadway floor and coal dust racks. Then, the high-definition flame images of deposited coal dust in the process of winding, ignition, detonation, and propagation were captured using the image acquisition system.
Figure 3 is the gas was ignited using the ignition head of an industrial detonator as the trigger. The gas flame was blue white in the initiation zone within 0–1 ms, developed in an irregular state, and quickly ignited the surrounding combustible gas. When the explosive pressure wave propagation along the roadway, the wave front surface pressure rises sharply and produces rapid flow, and the pressure wave passed through the coal dust deposition zone before the flame front. At this time, the airflow would generate a large velocity along the transverse direction of the roadway and a velocity gradient along the longitudinal direction of the roadway, and the coal dust deposited on the coal dust rack would fluctuate. Once the lifting power of the coal dust was greater than the required minimum power, the coal dust would float away from the bottom of the coal dust rack. (Liu et al., 2021).
Figure 4 is a high-definition flame image captured from the place where the laid coal dust (10 m) was ignited by explosion from the initiation point (0 m) in the roadway. After the gas explosion, the shock wave propagated forward and ignited the deposited coal dust on the coal dust rack. After the coal dust particles were raised, the trajectories became different, and a certain concentration of coal dust cloud was formed under the action of pressure wave. Then, the turbulent flame reached the dusty zone and ignited the coal dust cloud such that the coal dust participated in the deflagration reaction and the flame front is beginning to extend above the roadway, while the flame is slowly increasing in luminous intensity. Under the action of pressure wave and flame front, the flame was obviously layered, where the outer flame was dark yellow and the inner flame was bright yellow. Compared with the single-gas deflagration reaction, the coal dust-ignited flame was dark yellow. In addition, some of the coal dust clouds lifted outward were ignited by gas and then spread along the propagation direction of deflagration wave.
Figure 5 shows the flame propagation of gas and coal dust explosion in the early-medium stage. In the early stage (t=2.6 m), due to the uneven concentration distribution of gas in the roadway and the nature of the fire source, (Wu et al., 2022; Zheng et al., 2022), some methane volume fractions were too high or too low to form bright premixed combustion, which led to the darkening of the flame with a “V” structure, and the tip of the “V” pointed to the source of the flame. In the medium stage (t=55 m), a thin flame surface was formed after the ignition head above the roadway was detonated, and the generated heat heated the adjacent gas, which resulted in gas ignition and burning. At the same time the tendency of flame propagation in the transverse section of the roadway is obvious, and it is found that the effect of turbulence is enhanced in the transverse section by the presence of pedestrian handrails, frames and other facilities in the actual roadway itself, which stretches the flame front and enlarges the burning area. The fold degree of the flame front was enhanced and the shape of flames are extremely irregular due to the participation of the coal dust in the reaction (t=112 m), and oxygen was continuously added in the roadway, which led to more violent diffusion combustion. The explosion flame continued to spread in a more violent turbulent state, which caused the flame to fill the whole roadway. At t=156 m, a bright yellow flame fills the entire alleyway, and the flame is bright and blinding.
Figure 6 shows the flame propagation of gas and coal dust explosion in the later-last stage. In the later stage (t=209 m), the fire has begun to decay due to the exhaustion of combustible gases in the roadway. In the last stage (t=367 m), the entire tunnel space is filled with dark red flames, and the explosion flame structure was irregular due to the exhaustion of combustible gas in the roadway until the flame was gradually extinguished in t=662 m.
Figure 7 shows the flame propagation velocity measured at each measuring point in the process of gas and coal dust explosion propagation. In the forward propagation process of explosion shock wave in the roadway, the explosion flame was detected within 0–140 m of the roadway with gas and coal dust explosion, while the length of the gas explosion flame zone was only 70 m. With the increase in the propagation distance, the flame propagation speed rose first and then decreased. The gas and coal dust explosion flame showed a uniform rising trend in the first 70 m, and the flame propagation speed increased suddenly after 70 m, reached the maximum at 90 m, and then decreased slowly in the interval of 100–120 m. However, the flame propagation speed of gas explosion was relatively small, and the decline rate was faster after 50 m. The reason is that the pressure starting time in the process of coal dust explosion induced by gas explosion was always longer than the flame starting time. Therefore, at the front end of the explosion, the flame front was ahead of the pressure propagation, and the flame propagation speed rose slowly. When coal dust participated in the explosion, the pressure wave caught up with and exceeded the flame front at 70 m in the roadway, the flame front was affected by the reflected pressure wave, and a large amount of unburnt gas and coal dust mixture reacts with the high temperature burning mixture, which results in a significant increase in the reaction rate, leading to an accelerated forward propagation of the flame. The accelerated flame speed further increases the degree of turbulence, which in turn increases the travelling speed of the gas and coal dust mixture, leading to stronger folding of the flame front, creating positive feedback between the gas flow and the propagation of the flaming combustion, which dramatically increases the propagation speed of the flame front.
Figure 8 exhibits the maximum explosive overpressure measured at each measuring point in the propagation process of gas and coal dust explosion. The peak overpressure of each measuring point did not rise or fall monotonously but fluctuated, which could be roughly divided into three stages. In the initial stage of explosion (0–40 m), the gas was ignited near the ignition source and then impacted outward at high speed, the gas expanded rapidly to do work, and the explosion overpressure decreased after reaching a certain peak. In the development stage of explosion (40–120 m), the pressure would fluctuate in case of single-gas explosion with the continuous explosion reaction which is due to the combustible gas is compressed, a large amount of gas is involved in the reaction, combustion is accelerated, and the shockwave pressure value starts to rise with the propagation distance. As the explosion reaction continues, the constraint of the roadway space and the returning of pressure wave, the explosion of rapid reaction generated by the heat and consumption tends to balance, the explosion of the overpressure shows a trend of decreasing and then increasing, and finally due to the gradual consumption of combustible gases, the explosion energy and intensity of the final and gradually reduced. When coal dust participated in the explosion reaction, the coal dust cloud was ignited by a high-temperature flame and violently exploded, and the pressure in the roadway grew rapidly, so that the original weak explosion developed into a strong explosion. The pressure reached the highest at 120 m, which greatly enhanced the destructive power of the explosion. In the later stage of explosion (120–140 m), the overpressure gradually decreased when the combustible gas was exhausted without the influence of other conditions.
In this study, the gas and coal dust explosion test was performed in an engineering-level roadway, and the generation and evolution laws of the explosion flame and the overpressure and flame characteristics during explosion propagation were studied. The research results will provide an important theoretical basis for the development and installation of coal mine active explosion suppression technology and equipment. The main results are summarized as follows.
1. The flame was evidently layered when coal dust explosion was triggered by gas explosive shock wave, and the inner flame showed a bright yellow combustion state while the outer flame exhibited a dark yellow combustion state after the coal dust on coal dust racks was ignited.
2. The explosion flame of gas propagated forward along the upper part of the longitudinal section of the roadway. The combined effect of the pressure wave and the flame front ignites the coal dust, causing the surface of the explosion flame was rapidly stretched, and dramatically increasing the propagation speed of the flame front.
3. The propagation of explosive overpressure in the roadway was divided into three stages. The explosive overpressure fluctuated somehow in each stage, and it peaked at 120 m of the roadway. The destructive power of explosion was considerably enhanced by the participation of coal dust. The evolution of the explosion flame in the roadway was largely divided into four stages. A sharp increase zone of flame propagation velocity was observed due to the participation of coal dust, and it even reached the maximum value at 90 m.
The original contributions presented in the study are included in the article/Supplementary material, further inquiries can be directed to the corresponding author.
YN: Writing–original draft. RS: Writing–original draft. ZL: Data curation, Writing–review and editing. LW: Data curation, Formal Analysis, Writing–review and editing. ZH: Funding acquisition, Methodology, Writing–review and editing. QJ: Data curation, Formal Analysis, Writing–review and editing.
The author(s) declare financial support was received for the research, authorship, and/or publication of this article. This research was financially supported by National Natural Science Foundation of China (Nos. 52174226 and 52304207), Natural Science Foundation of Chongqing Scientific and Technological (CSTB2022NSCQ-MSX0335), The Science and Technology Research Program of Chongqing Municipal Education Commission (Grant Nos. KJQN202301525 and KJQN202101529). The Project was Supported by Engineering Technology Research Centre for Safe and Efficient Coal Mining (Anhui University of Science and Technology) (No. SECM2207).
The authors declare that the research was conducted in the absence of any commercial or financial relationships that could be construed as a potential conflict of interest.
All claims expressed in this article are solely those of the authors and do not necessarily represent those of their affiliated organizations, or those of the publisher, the editors and the reviewers. Any product that may be evaluated in this article, or claim that may be made by its manufacturer, is not guaranteed or endorsed by the publisher.
Ajrash, M. J., Zanganeh, J., and Moghtaderi, B. (2017a). Impact of suspended coal dusts on methane deflagration properties in a large-scale straight duct. J. Hazard Mater 338, 334–342. doi:10.1016/j.jhazmat.2017.05.030
Ajrash, M. J., Zanganeh, J., and Moghtaderi, B. (2017b). The flame deflagration of hybrid methane coal dusts in a large-scale detonation tube (LSDT). Fuel 194, 491–502. doi:10.1016/j.fuel.2017.01.038
Cheng, F. M., Chang, Z. C., Luo, Z. M., Liu, C., Li, H., and Wang, T. (2020). Numerical study on premixing characteristics and explosion process of starch in a vertical pipe under turbulent flow. J. Loss Prev. Proc. 68, 104303. doi:10.1016/j.jlp.2020.104303
Guo, C. W., Shao, H., Jiang, S. G., Wang, Y., Wang, K., and Wu, Z. (2020). Effect of low-concentration coal dust on gas explosion propagation law. Powder Technol. 367, 243–252. doi:10.1016/j.powtec.2020.03.045
Jia, Q. S., Si, R. J., Wang, L., Li, Z., and Xue, S. (2023). Influence of initial gas concentration on methane-air mixtures explosion characteristics and implications for safety management. Sci. Rep. 13, 13519. doi:10.1038/s41598-023-40383-3
Jing, G. X., Guo, S. S., and Wu, Y. L. (2021). Investigation on the characteristics of single-phase gas explosion and gas-coal dust coupling explosion in bifurcated tubes. Therm. Sci. 25, 3595–3605. doi:10.2298/tsci200729337j
Li, H. T., Deng, J. L., Chen, X. K., Shu, C. M., Kuo, C. H., Zhai, X., et al. (2020). Transient temperature evolution of pulverized coal cloud deflagration in a methane-oxygen atmosphere. Powder Technol. 366, 294–304. doi:10.1016/j.powtec.2020.02.042
Li, H. T., Zhai, F. R., Li, S. S., Lou, R., Wang, F., Chen, X., et al. (2022). Macromorphological features and formation mechanism of particulate residues from methane/air/coal dust gas-solid two-phase hybrid explosions: an approach for material evidence analysis in accident investigation. Fuel 315, 123209. doi:10.1016/j.fuel.2022.123209
Li, J. L., Wang, X. B., Guo, J., Zhang, J., and Zhang, S. (2020). Effect of concentration and ignition position on vented methane-air explosions. J. Loss Prev. Proc. 68, 104334. doi:10.1016/j.jlp.2020.104334
Li, S. J., Jia, Z. Z., and Ye, Q. (2023). Study on dynamic response of damper under gas explosion impact. Sustainability 15, 3356. doi:10.3390/su15043356
Liu, T. Q., Cai, Z. X., Sun, R. C., Wang, N., Jia, R., and Tian, W. (2021). Effect of coal dust parameters on gas-coal dust explosions in pipe networks. JCEJ 54, 631–637. doi:10.1252/jcej.21we066
Liu, Y., Sun, J. H., and Chen, D. L. (2007). Flame propagation in hybrid mixture of coal dust and methane. J. Loss Prev. Proc. 20, 691–697. doi:10.1016/j.jlp.2007.04.029
Ma, D., Qin, B. T., Cao, Y., Jiang, J., and Feng, B. (2020). Study on the explosion characteristics of methane-air with coal dust originating from low-temperature oxidation of coal. Fuel 260, 116304. doi:10.1016/j.fuel.2019.116304
Nie, B. S., He, X. Q., Wang, C., Lu, H., and Xue, F. (2015). Computational method of the propagation velocity of methane explosion flame based on correlation coefficient of images. Combust. Sci. Technol. 187, 1157–1166. doi:10.1080/00102202.2015.1019621
Nie, B. S., He, X. Q., Zhang, C., Li, X., and Li, H. (2014). Temperature measurement of gas explosion flame based on the radiation thermometry. Int. J. Therm. Sci. 78, 132–144. doi:10.1016/j.ijthermalsci.2013.12.010
Niu, Y. H., Shi, B. M., and Jiang, B. Y. (2019). Experimental study of overpressure evolution laws and flame propagation characteristics after methane explosion in transversal pipe networks. Appl. Therm. Eng. 154, 18–23. doi:10.1016/j.applthermaleng.2019.03.059
Niu, Y. H., Zhang, L. L., and Shi, B. M. (2020). Experimental study on the explosion-propagation law of coal dust with different moisture contents induced by methane explosion. Powder Technol. 361, 507–511. doi:10.1016/j.powtec.2019.11.089
Niu, Y. H., Zhang, L. L., Shi, B. M., Yang, Q., and Zhong, Z. (2021). Methane-coal dust mixed explosion in transversal pipe networks. Combust. Sci. Technol. 193, 1734–1746. doi:10.1080/00102202.2019.1711071
Sha, D., Li, Y. C., Zhou, X. H., Zhang, J., Zhang, H., and Yu, J. (2021). Influence of volatile content on the explosion characteristics of coal dust. ACS Omega 6, 27150–27157. doi:10.1021/acsomega.1c03803
Song, Y. F., Nassim, B., and Zhang, Q. (2018). Explosion energy of methane/deposited coal dust and inert effects of rock dust. Fuel 228, 112–122. doi:10.1016/j.fuel.2018.04.155
Sun, X., and Lu, S. (2020). On the mechanisms of flame propagation in methane-air mixtures with concentration gradient. Energy 202, 117782. doi:10.1016/j.energy.2020.117782
Tousif, M., Harish, A., Kumaran, S. M., and Raghavan, V. (2020). Numerical study of interaction of coal dust with premixed fuel-lean methane-air flames. Adv. Powder Technol. 31, 3833–3844. doi:10.1016/j.apt.2020.07.027
Wang, D. M., Shao, Z. L., and Zhu, Y. F. (2021). Several scientific issues on major thermodynamic disasters in coal mines. J. China Coal Soc. 46, 57–64. doi:10.13225/j.cnki.jccs.YG20.1798
Wang, L., Si, R. J., Li, R. Z., and Huo, Y. (2018). Experimental investigation of the propagation of deflagration flames in a horizontal underground channel containing obstacles. Tunn. Undergr. Sp. Tech. 78, 201–214. doi:10.1016/j.tust.2018.04.027
Wang, X. T., Dai, H. M., Liang, G. Q., Zhu, H., Zhang, B., et al. (2021). Flame propagation characteristics of mixed pulverized coal at the atmosphere of gasification. Fuel 300, 120954. doi:10.1016/j.fuel.2021.120954
Wu, Q. F., Yu, M. G., and Zheng, K. (2022). Experimental investigation on the effect of obstacle position on the explosion behaviors of the non-uniform methane/air mixture. Fuel 320, 123989. doi:10.1016/j.fuel.2022.123989
Zhang, L. L., Yang, Q. Y., Shi, B. M., Niu, Y., and Zhong, Z. (2021). Influences of a pipeline’s bending angle on the propagation law of coal dust explosion induced by gas explosion. Combust. Sci. Technol. 193, 798–811. doi:10.1080/00102202.2019.1673381
Keywords: mine gas, gas and coal dust explosion, explosion flame, propagation characteristics, explosion pressure
Citation: Niu Y, Si R, Li Z, Wang L, Huang Z and Jia Q (2023) Experimental study on gas and coal dust explosive overpressure and flame dynamic characteristics in an engineering-level test roadway. Front. Earth Sci. 11:1330932. doi: 10.3389/feart.2023.1330932
Received: 31 October 2023; Accepted: 06 December 2023;
Published: 29 December 2023.
Edited by:
Faming Huang, Nanchang University, ChinaReviewed by:
Runzhi Li, Shandong University of Science and Technology, ChinaCopyright © 2023 Niu, Si, Li, Wang, Huang and Jia. This is an open-access article distributed under the terms of the Creative Commons Attribution License (CC BY). The use, distribution or reproduction in other forums is permitted, provided the original author(s) and the copyright owner(s) are credited and that the original publication in this journal is cited, in accordance with accepted academic practice. No use, distribution or reproduction is permitted which does not comply with these terms.
*Correspondence: Rongjun Si, c2lyajczQDE2My5jb20=
Disclaimer: All claims expressed in this article are solely those of the authors and do not necessarily represent those of their affiliated organizations, or those of the publisher, the editors and the reviewers. Any product that may be evaluated in this article or claim that may be made by its manufacturer is not guaranteed or endorsed by the publisher.
Research integrity at Frontiers
Learn more about the work of our research integrity team to safeguard the quality of each article we publish.