- 1The Seventh Engineering Co., LTD. of CFHEC, Zhengzhou, China
- 2School of Civil Engineering, Chang’ an University, Xi’an, China
Loess is often not suitable for direct use as a roadbed or building foundation due to its collapsibility, and it needs to be improved by adding curing agents. Taking the loess in Xi’an area as the research object, the reinforcement of loess was carried out using waste tire rubber particles and Enzyme Induced Carbonate Precipitation (EICP) technology. The change of shear strength and shear strength index of improved soil with rubber content and rubber particle size under different strengthening conditions was analyzed, and the strengthening mechanism was also expounded. The results show that rubber powder can improve the shear strength of loess to a certain extent, and the combination of EICP technology can increase the strength of improved loess by nearly 50%. In addition, rubber particles have a certain inhibitory effect on EICP, and the shear strength growth rate decreases with the increase of rubber content. When the rubber particle size is 1–2 mm, the shear strength growth rate is the highest. It is suggested that when adding rubber particles or adding rubber particles combined with EICP technology is used to improve loess, the rubber particle size should be selected as 1–2 mm, and the content is about 10%. The test results can provide a scientific basis for the reduction of geologic disasters in loess areas, and at the same time can provide a non-polluting way for the disposal of waste tires.
1 Introduction
Loess in China is widely distributed and thick, accounting for 6.6% of China’s land area (Zhao and Huang, 2004). The loess has a loose structure and is prone to shear failure under water and external loads (Derbyshire, 2001). Therefore, untreated loess is highly susceptible to geological disasters such as subsidence, landslides and collapses, and cannot be used directly in engineering practice (Yang and Wen, 2013; Zhang and Yang, 2021; Zhang et al., 2023), and cannot be used directly in engineering practice. Hence, it is necessary to improve the mechanical properties of loess. At present, the improvement means is mainly to improve the mechanical properties of loess by mixing high-strength materials into the soil. For example, lignosulfonate (Xu et al., 2022), permeable polymer materials (Mu et al., 2022), cement materials (Chen et al., 2021), cement and fly ash (Zhang et al., 2019) are added to improve the mechanical properties of loess. However, the high-strength materials are often expensive, and in actual engineering practice, it is generally necessary to improve loess on a large scale, which is not conducive to economic benefits. In addition, some curing agents have certain environmental pollution characteristics, which will decompose and produce harmful substances (Ding et al., 2022). Therefore, it is necessary to study a green and environmentally friendly improvement method with excellent economic benefit.
Due to the rapid development of the automotive industry, the number of used tires has increased dramatically, and the disposal of used tires has become an urgent problem to be solved (Falak et al., 2011). In the natural state, waste tires are difficult to degrade, and if burned, it will produce a lot of harmful gases, affecting human health (Pierce and Blackwell, 2003). Considering that waste tire rubber particles have advantages such as lightweight, high strength, good deformation coordination, and low cost (Moo-Young et al., 2003), it can be widely used in engineering practice. For example, rubber particles have been incorporated into sand as reinforcing walls (Youwai and Bergado, 2004; Hartman et al., 2013), replaced fine aggregate as light concrete (Reza et al., 2023), and incorporated foundation soil layer as structural damping layer (Tsang, 2008), and so on. Therefore, a series of studies on rubberized mixed soil have been carried out. For example,: Lee et al. (1999) studied the stress-strain relationship and strength of rubber sand mixed soil through Triaxial shear test, and found that the peak Shear stress of rubber sand mixed soil is greater than that of pure sand. Ghazavi. (2004) found that the bulk density and rubber content of rubber sand mixed soil with different rubber mass ratios were the main factors affecting the shear strength of the mixed soil. Cetin et al. (2006) found that the shear strength of rubber debris sandy clay mixed soil increased when the rubber content was between 20% and 30%. Anastasiadis et al. (2011) and Anastasiadis et al. (2012) studied the elastic modulus and damping ratio of rubber improved soil under the conditions of different gravel particle size and rubber mix ratio through dynamic Triaxial shear test, and obtained the theoretical formula of elastic modulus and damping ratio of rubber improved soil through function fitting. At present, the researches on rubber improvement of sandy soil are quite sufficient, but the researches on structural loess improvement are few.
Since the strength and stiffness of rubber particles are lower than that of soil particles, when rubber particles replace soil particles, the original skeleton bearing capacity of soil samples is weakened, and the compressive strength of specimens will be reduced. Because the strength and stiffness of rubber particles are lower than that of soil particles, when rubber particles replace soil particles, the skeleton bearing capacity of the original soil sample is weakened, and the compressive strength of the sample will be reduced. Therefore, the effect of simply using rubber particles to improve the structural soil is not ideal. In order to make up for the lack of compressive strength, the sample can be further strengthened by microorganism-induced calcium carbonate precipitation (MICP) technology. This technique utilizes urease to decompose urea to generate ammonium ions and carbonate ions, which combine with calcium ions in the environment to generate calcium carbonate crystals. Calcium carbonate crystals can fill soil pores and bond soil particles, thereby improving soil strength (Liang et al., 2020; Laurynas et al., 2023; Liu et al., 2023). At present, there have been many related researches. For example, Whiffin (2004) studied the pH environment and the effect of culture medium on the urease activity produced by Bacillus subtilis. The experiment showed that bacteria can tolerate high concentrations of urea and calcium ions, and produce urease through reproductive metabolism. Ng et al. (2012) studied the influencing factors of MICP reinforcement through experiments, including bacterial concentration, calcium source selection, cementation fluid concentration, solution acidity and alkalinity, and temperature. Paassen and Andreas. (2009) conducted grouting treatment on sandy soil and found that after 1 day of microbial grouting treatment, the stiffness of the sandy soil was significantly improved.
Considering the complicated extraction steps of microbial urease, in recent years, some scholars have directly used urease extracted from common plants to reinforce soil, that is, Enzyme Induced Carbonate Precipitation (EICP) technology (Dilrukshi and Satoru, 2016). EICP technology eliminates the need for bacterial cultivation, eliminates the process of producing urease, and avoids the impact of external environment on bacterial growth (Wen et al., 2020). Nam et al. (2015) extracted urease from jack beans and found that the urease could be used for crack repair with similar results as biurease, but with lower costs. Cuccurullo et al. (2020) studied that calcium carbonate precipitation induced by soybean urease can improve the permeability resistance of silty clay soil. Neupane et al. (2013) used EICP technology to strengthen sand samples in PVC pipes, and found that the porosity of the samples was reduced and the mechanical performance was improved. Ossai et al. (2020) conducted research on reinforced sand based on EICP technology, and found that the anti-erosion ability of treated sand was enhanced.
The paper presents an exprimental study on the mechanical properties of loess reinforced by rubber particles and urease-induced calcium carbonate precipitation (EICP). Firstly, the approximate range of rubber doping and the optimal concentration of urease and cementing solution are determined by preliminary experiment. Secondly, the change rule of shear strength and shear strength indexes of loess under only rubber particles and rubber particles combined with EICP are analyzed, and its mechanism is explained. Finally, the optimal reinforcement conditions are comprehensively selected according to the test results. This study can provide a reliable scientific basis for soil reinforcement in loess area, and at the same time, it can provide a non-polluting way for the treatment of rubber particles.
2 Introduction to the experiment
2.1 Test materials
The loess used in the experiment (Figure 1A) was taken from the loess of a project in Xi’an City, Shaanxi Province, 10 m from the excavation of the foundation pit. The soil sample is yellowish brown. The basic physical properties of the soil have been measured, and the results are shown in Table 1. The particle size grading curve is shown in Figure 2. The selected rubber particles (Figure 1B) are obtained from the shredding and screening of waste tires, with particle sizes of 0–1 mm, 1–2 mm, and 2–3 mm, and a rubber particle density of 1.03 g/cm3. Urease and cementation fluid material (Figure 1C) are provided by Ica Biological Reagents, in which urease is derived from cana bean, the activity is 1 U/mg, and generally stored at 2°C–8 °C; The cementation fluid materials are calcium chloride and urea, which are stored at room temperature and away from light, and urea is ultra-pure urea.
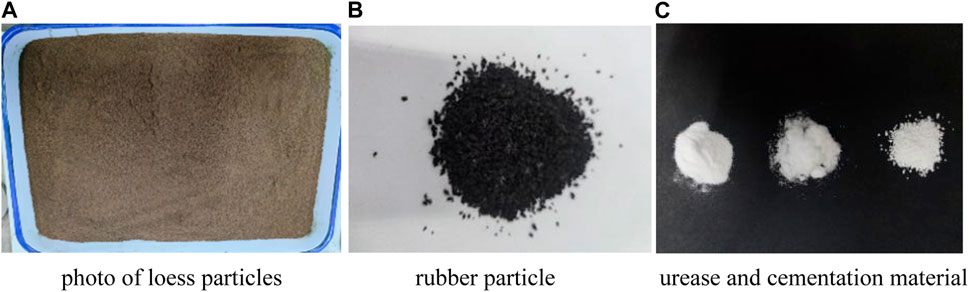
FIGURE 1. Experimental material: (A) loess; (B) rubber particle; (C) urease and cementation material.
Urease is derived from concanavalin beans with an activity of 1U/mg and is generally stored at 2°C–8 °C. The cementation fluid material is calcium chloride and urea, which are stored at room temperature and protected from light.
2.2 Specimen preparation
The improved loess in this experiment is divided into two categories: rubber particles improved loess and rubber particles combined with EICP improved loess. The rubber particles mixed in the test are determined according to the volume ratio between rubber particles and loess, and the water content of the prepared sample was 15%.
When preparing rubber particle improved soil, the dried loess is first ground and screened by 2 mm. According to the proportion of rubber particles, the corresponding quality of loess and rubber particles are weighed and mixed. Then add an appropriate amount of pure water to the mixed soil and stir it evenly, load the mixed soil into the ring knife sample press, and use a jack to compact the sample. After the standard direct shear sample with a size of 61.8 mm×20 mm is made, it is sealed with plastic wrap, and the prepared sample is placed in a constant temperature curing box for 72 h. The curing temperature is 25°C–30 °C and the curing humidity is 95%. When preparing rubber particles combined with EICP to improve loess, it is only necessary to change the pure water in the above steps to urease solution and cementation fluid, with a ratio of 1:1. The two are added to the mixed soil in sequence and stirred evenly. The cementation fluid is calcium chloride and urea solution, with a volume ratio of 1:1, and the pH of the cementation fluid is adjusted to 7.4. The sample preparation process diagram is shown in Figure 3.
2.3 EICP working principle
The main chemicals involved in the EICP process are urease, urea, and calcium chloride. Among them, urease decomposes urea solution to produce carbonate ions, which combine with calcium ions in the solution to form calcium carbonate precipitates. The reaction equations involved are as follows (1)–(5) (Ahenkorah et al., 2021). Calcium carbonate can fill the internal pores of loess, increase the strength of loess skeleton, and then improve the shear strength of the sample. The reinforcement diagram is shown in Figure 4.
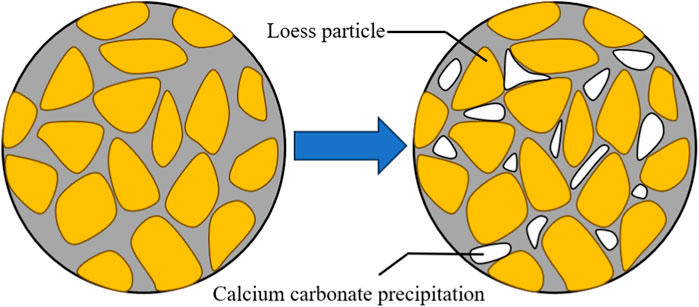
FIGURE 4. Schematic diagram of the basic principle of soil reinforcement by urease induced calcium carbonate precipitation.
2.4 Testing instrument and testing scheme
The testing instrument used in this paper is a ZJ strain controlled direct shear instrument, as shown in Figure 5. The direct shear rate ranges from 0.8 mm/min to 1.2 mm/min. The test data are automatically recorded by the computer. First, each soil sample is placed on the shear boxes with an impervious stone above and below, and then the sample is pressed into the shear box with a top cap. After applying vertical pressure, the bolt is removed, and the shear rate is adjusted to 0.8 mm/min, then the rapid shear test will be started. When the dial indicator reading no longer moves forward but backward, continue to shear until the shear displacement is 4mm, and read the peak strength as the shear strength of the soil sample. When the dial indicator reading has no peak value, stop the test when the shear displacement is 6 mm, and read the corresponding value when the shear displacement is 4 mm as the Shear strength of the soil sample.
This experiment is divided into two parts: preliminary experiment and shear characteristic experiment. The proportion range of rubber particles added and the optimal concentration of urease and cementation fluid are determined through preliminary experiments. Then, the reinforcement effect of loess improved by only adding rubber particles and loess improved by combining rubber particles with EICP is evaluated through shear characteristic tests, and its reinforcement mechanism is explained accordingly.
A part of the preliminary experiment is to conduct a fast shear test on the improved loess with only rubber particles added. The content of rubber particles is 0%, 5%, 7%, 10%, 13%, 15%, 20%, 25% and 30% respectively, and the optimal mixing range is selected according to the shear strength of the samples. A total of 10 groups are presented in Table 2. The other part is the rapid shear test of the sample containing urease and cementation fluid based on the above test content. The optimal concentration of urease and cementing fluid (mixed liquid with a volume ratio of calcium chloride to urea of 1:1) was determined by orthogonal test results, in which the concentration of urease solution is 100 g/L, 200 g/L, 300 g/L and 400 g/L, and the concentration of cementing fluid was 0.5 mol/L, 1 mol/L and 2 mol/L, respectively, in 12 groups. The test scheme is shown in Table 3.
Based on the preliminary experimental results, the range of rubber particle dosage and the concentration of urease and cementation fluid were determined. A total of 124 sets of direct shear specimens were prepared with rubber particle dosage of 0%, 5%, 7%, 10%, 13%, and 15%, rubber particle sizes of 0–1 mm, 1–2 mm, and 2–3 mm, urease concentration of 200 g/L, and cementation fluid concentration of 1 mol/L. The experimental plan is shown in Table 4.
3 Analysis of test results
3.1 Analysis of preliminary experimental results
(1) Determination of rubber particle content
As can be seen from Figure 6, with the increase of rubber content under different rubber particle sizes, the variation trend of the specimen shear strength has a certain similarity, all showing a pattern of first increasing and then decreasing. Compared to the test results of soil samples without the addition of rubber particles, the range of rubber content corresponding to the increase in shear strength of improved soil with different particle sizes of rubber is not entirely the same, but the peak shear strength occurs between about 7% and 13% of rubber content. Although the shear strength of the sample is lower than 0% when the rubber content is between 7% and 13% for some particle sizes, considering that EICP technology will continue to improve the shear strength of the sample, a rubber content range of 5%–15% is selected for subsequent shear characteristic tests.
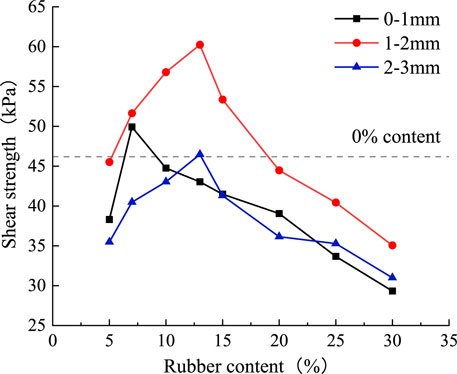
FIGURE 6. Shear strength-rubber particles content relationship curve of samples with different particle sizes (100 kPa).
Loess itself is a kind of loose material, while rubber particles are a kind of surface roughness and internal dense material. When a small amount of rubber particles is added to loess, the internal pore defects of the sample will be reduced, and the development of cracks in the sample during the shear failure process will be inhibited, so the shear strength of the sample will be increased. However, the strength of rubber particles is lower than that of soil particles. When replacing soil particles with equal volume of rubber particles, the overall strength of the soil is reduced. Moreover, with an increase in rubber content, rubber particles are prone to aggregation and floating during the mixing process with loess. The aggregation of rubber particles actually increases the pores of the sample, creating a weak interface, and the sample is more prone to damage during shear, resulting in a decrease in shear strength. Thus, when the rubber content exceeds the critical value, the shear strength shows a decreasing trend.
(2) Determination of the urease and cementation fluid concentration
From Figure 7, it can be seen that under different concentrations of cementation fluid, the shear strength of the sample shows a unified trend with the variation of urease concentration. As the concentration of urease increases, the shear strength of the sample first increases and then decreases, and the peak shear strength corresponds to a urease concentration of 200 g/L. Under different urease concentrations, the variation of the shear strength of the sample with the concentration of the adhesive solution is approximately consistent, showing a pattern of first increasing and then decreasing. The peak shear strength corresponds to a concentration of 1 mol/L of the adhesive solution. Therefore, through this orthogonal experiment, it can be determined that the urease concentration for subsequent shear characteristic tests is 200 g/L, and the concentration of the cementation fluid is 1 mol/L.
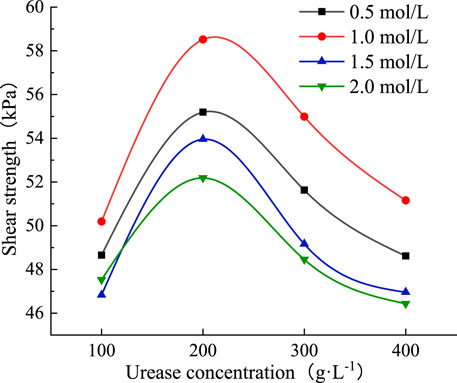
FIGURE 7. Curve of relationship between shear strength and urease concentration in improved soil in different cementation fluid concentration.
Based on the working principle of EICP, when the concentration of the cementation fluid is fixed and different concentrations of urease solutions are added, the shear strength of the sample is enhanced to varying degrees, and the urease concentration corresponding to the peak shear strength is 200 g/L. The reasons for this phenomenon can be explained as follows. When the concentration of urease is low, the ability of urease to decompose urea is limited, resulting in a smaller amount of calcium carbonate generated and a lower rate of improvement in the shear strength of the sample. When the concentration of urease is high, the amount of cementation fluid is fixed, urease completely decomposes urea, and the yield of calcium carbonate is fixed. However, considering that the distribution of cementation fluid is not completely uniform during the sample production process, during the sample curing process, the cementation fluid has already been decomposed and utilized by urease before completing migration. Therefore, the filling of the sample skeleton is not uniform, resulting in a low growth rate of shear strength. Therefore, there is a critical value for urease concentration. When the concentration of urease is fixed, as the concentration of the cementation fluid increases, the concentration of calcium ions also increases. When the concentration of the cementitious solution is less than the critical value, the calcium carbonate produced by urease decomposing urea binds with calcium ions, resulting in an increase in calcium carbonate production. However, excessive concentration of calcium ions can inhibit urease activity, reduce urea decomposition, and thus reduce the concentration of carbonate ions, resulting in a decrease in calcium carbonate production. Therefore, there is a critical value for the concentration of the cementation fluid.
3.2 Analysis of shear characteristics test results
(1) Improvement of loess by mixing rubber granules only
By comparing and analyzing the deformation development law of specimens under different rubber content and rubber particle size during shear failure, the strain characteristics and shear strength of each specimen are obtained. According to the Mohr-Coulomb shear strength criterion, the shear strength of each single specimen under different vertical pressures is linearly fitted, and the variation law of cohesion and internal friction angle with rubber content and rubber particle size can be accordingly obtained.
Figure 8 shows the shear stress-displacement relationship curve of improved soil samples with different rubber content when the rubber particle size is 1–2 mm under the vertical pressure of 50 kPa and 100 kPa respectively. It can be seen from Figure 8 that the change rule of shear stress-displacement curve of samples under different rubber content is similar. When the vertical pressure is 50 kPa, the samples with different rubber content show the strain softening characteristics, that is, after the shear stress reaches the maximum value, the shear stress gradually decreases with the increase of shear displacement. When the vertical pressure is 100 kPa, the specimen shows strain hardening characteristics, that is, after the shear stress reaches the maximum value, the shear stress remains unchanged or continues to increase with the increase of shear displacement.
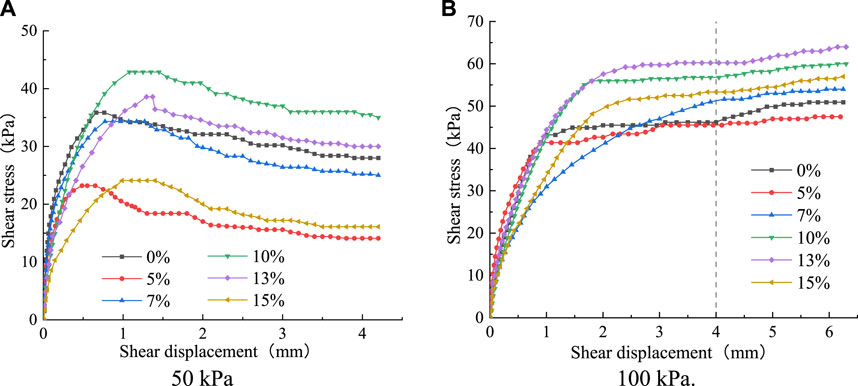
FIGURE 8. Shear stress-shear displacement curves of samples under different vertical pressures (Rubber particle size: 1–2 mm): (A) 50 kPa; (B) 100 kPa.
Statistical analysis has been conducted on the strain characteristics and shear strength of the samples mixed only with rubber particles in Table 4. The results of the strain characteristics are shown in Table 5, and the shear strength results are shown in Table 6.

TABLE 5. Statistical results of strain characteristics of samples under different working conditions (soil samples mixed with rubber particles only).
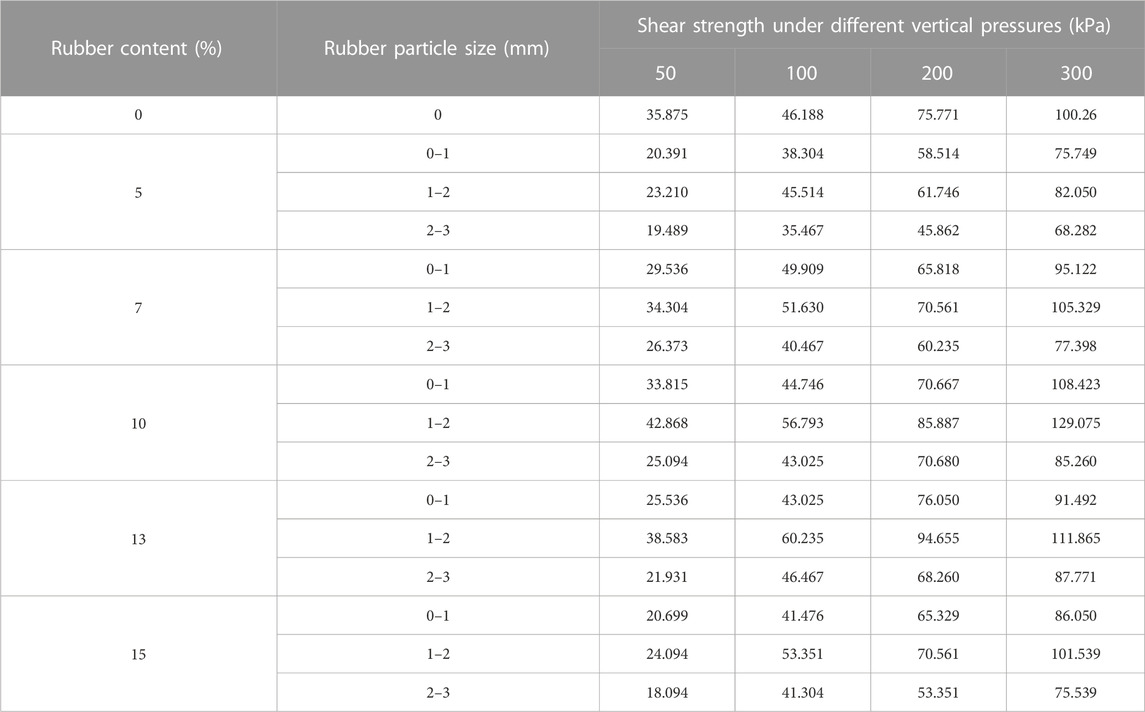
TABLE 6. Statistical results of the shear strength of the sample under different working conditions (soil sample mixed with rubber particles only).
It can be seen from the results in Table 5 that the strain characteristics of the samples under different rubber content and different rubber particle size are similar. The strain characteristics of the samples show a softening rule under lower pressure. When the vertical pressure increases, the strain characteristics change from softening to hardening, and all of them show strain hardening characteristics under high pressure.
According to the shear strength results of the samples mixed only with rubber particles in Table 6, it can be seen that under the same vertical pressure and different rubber particle sizes, the changes in shear strength of the samples are similar with the increase of rubber content, showing a trend of first increasing and then decreasing. And the shear strength of the corresponding samples when the rubber particle size is 1–2 mm is higher than that of the corresponding samples when the rubber particle size is 0–1mm and 2–3 mm. Under different vertical pressures, compared with the control group without the addition of rubber particles, the range of rubber content corresponding to the increase in shear strength of the sample is roughly between 7% and 13%. Under different vertical pressures, the maximum increase in shear strength of the sample is 19.49%, 30.41%, 24.92%, and 28.74%, respectively.
Linear fitting has been performed on the shear strength results of the samples under different vertical pressures shown in Table 6, and the curves of the cohesion and internal friction angle of the samples under different rubber dosages and rubber particle sizes are obtained, as shown in Figure 9. Under different rubber particle sizes, the cohesion and internal friction angle of the sample show a trend of first increasing and then decreasing with the change of rubber content. When the rubber particle size is 1–2mm, the corresponding cohesion and internal friction angle of the sample are the highest. Compared with the control group with 0% rubber content, when the rubber particle size is 1–2 mm and the rubber content is 10%–13%, the cohesion and internal friction angle of the sample increase, with the maximum increase in cohesion being 31.57% and the maximum increase in internal friction angle being 27.89%.
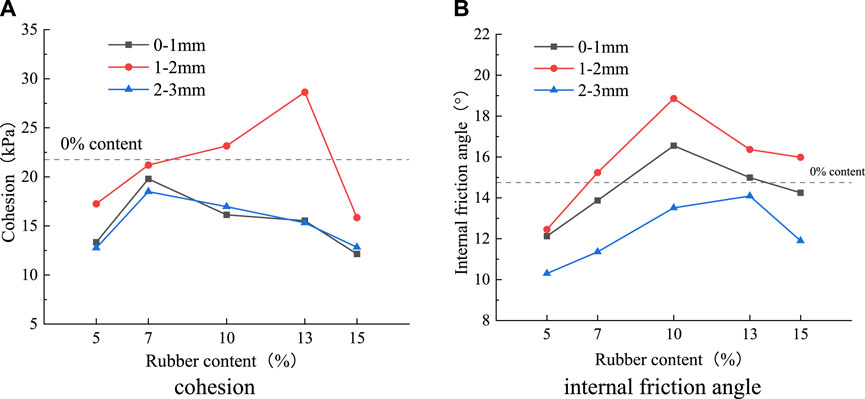
FIGURE 9. Cohesion and internal friction Angle of improved soil samples under different working conditions (soil sample mixed with rubber particles only): (A) cohesion; (B) internal friction angle.
The shear strength index of soil is composed of cohesion and internal friction angle. According to the results in Table 6 and Figure 9, although the maximum increase of cohesion is higher than the maximum increase of internal friction angle for the improved loess with only rubber particles, the increase range of cohesion is only in the interval when the rubber particle size is 1–2 mm and the content is 10%–13%. The internal friction Angle increases in the rubber particle size of 0∼1mm, the content of 10%–13% and the rubber particle size of 1∼2mm, the content of 7%–15%, and the increase range of internal friction angle is wider. Therefore, the internal friction angle plays a major role in the increase of the shear strength of the improved loess mixed only with rubber particles.
The mechanism analysis of the above phenomenon is as follows. After adding rubber particles to the loess, the contact between the particles changes. When adding a small amount of rubber particles with the same particle size, the mixed soil changes from a single soil-soil contact to soil-soil contact with a small amount of soil-rubber contact and rubber-rubber contact. In this case, rubber particles are covered by loess, and the bonding effect is enhanced, thus increasing the cohesion. Rubber particles have irregular shapes and many angles, which can provide greater friction resistance, so the internal friction Angle increases with the increase of rubber content. However, considering that the density of rubber particles is only 1.03 g/cm3, while the density of loess is 1.72 g/cm3, when replacing soil particles with equal volume of rubber particles, the mass of the two is not equal, which reduces the friction between soil particles and the bonding effect between soil particles. Two factors jointly affect the strength of the improved soil. Therefore, compared to the control group without the addition of rubber particles, the shear strength of the improved soil sample may increase or decrease, which is directly related to the size of rubber particles. As the rubber content continues to increase, the soil-rubber contact and rubber-rubber contact increase, and the degree of “granulation” of the mixed soil increases, so the cohesion of the sample decreases. Considering that the sample is still dominated by the contact of soil particles, the friction between soil particles decreases to a greater extent than the increase of soil-rubber and rubber-rubber friction, so the internal friction Angle of the mixed soil gradually decreases. The overall shear strength of the sample also decreased.
In the case of the same rubber content, when the rubber particle size is small, the number of rubber particles in the same volume is too large, resulting in the reduction of cohesion between soil particles, and although the soil-rubber contact and rubber-rubber contact increase, the internal friction angle is lower than that of the whole rubber particles, so the shear strength of the sample decreases. When the size of rubber particles is large, the number of rubber particles in the same volume is too small, resulting in uneven distribution of rubber particles in the sample. In addition, in the process of sample production, jack is used to compact the sample. Due to the good elasticity of rubber particles, when the jack is unloaded, the large-particle rubber will rebound, resulting in the fracture of soil-soil contact and soil-rubber contact, and then the cohesion and internal friction Angle of the sample are reduced, so the shear strength of the sample is reduced.
(2) Improvement of loess by rubber particles combined with EICP
The deformation development curve of the loess sample improved by rubber particles combined with EICP technology during shear failure is similar to that in Figure 8, and the strain characteristics of each sample are consistent with the results of the loess sample improved by only mixing rubber particles in Figure 8. Detailed analysis will not be made in this section. The test results of the shear strength of loess improved by rubber particles combined with EICP are shown in Table 7. Obviously, under the same confining pressure, the shear strength obtained by the combined improvement method is higher than that obtained by using only rubber particle improvement. The calculation results under different confining pressures are shown in Figure 10.
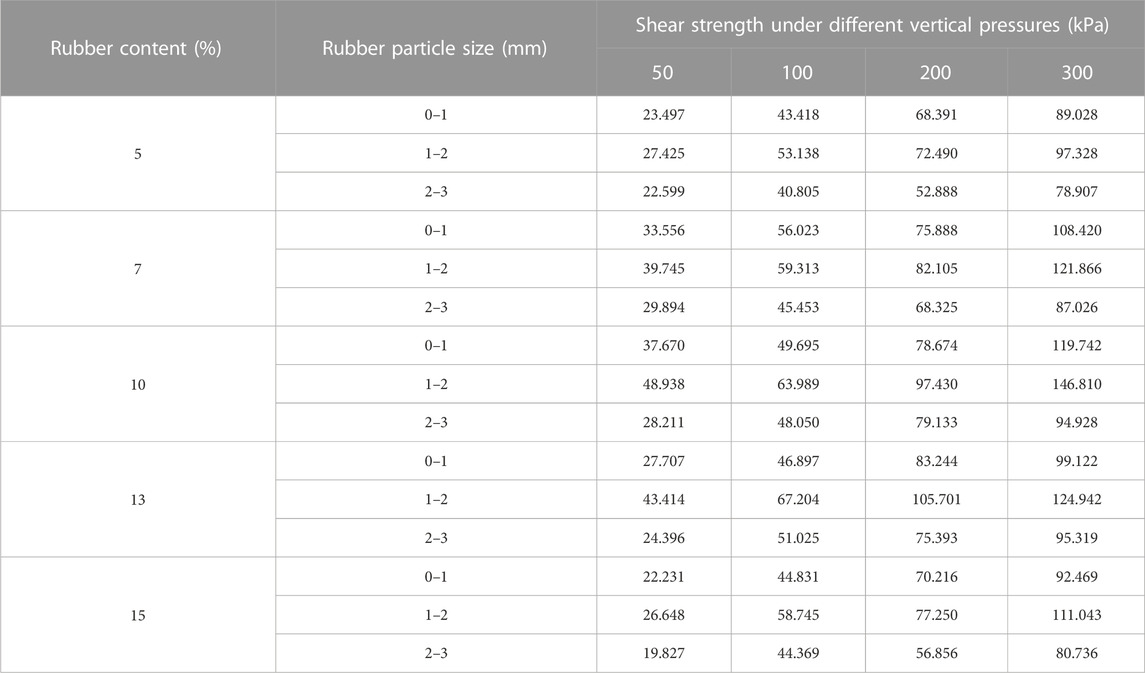
TABLE 7. Statistical results of the shear strength of the sample under different working conditions (soil sample mixed with rubber particles combined with EICP).
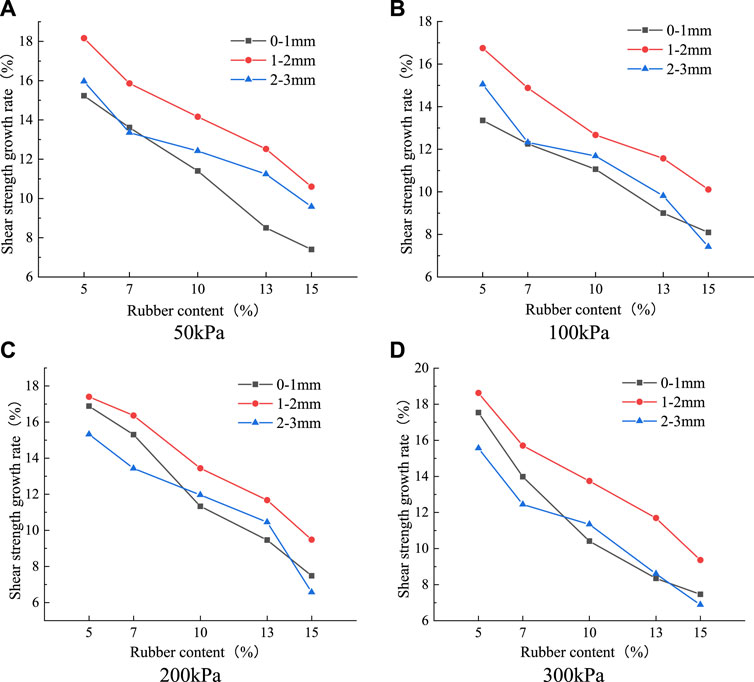
FIGURE 10. Curves of shear strength growth rate with rubber content under different vertical pressures: (A) 50 kPa; (B) 100 kPa; (C) 200kPa; (D) 300 kPa.
In order to compare and analyze the strength changes of loess modified by rubber particles combined with EICP and that modified by rubber particles only, the shear strength growth rate is defined as the percentage increase of the shear strength of loess modified by rubber particles combined with EICP compared with that of rubber particles only under the same conditions. Based on the experimental results in Table 7 and Figure 10, it can be seen that the variation pattern of shear strength of loess samples improved by rubber particles combined with EICP is consistent with that of loess samples improved by only adding rubber particles. After being treated with EICP technology, the shear strength of the samples increased to varying degrees. Under the same vertical pressure and different rubber particle sizes, with the increase of rubber content, the shear strength of the sample shows a trend of first increasing and then decreasing. The growth rate of shear strength of the sample shows a gradually decreasing trend. The shear strength and shear strength growth rate of the corresponding samples with a rubber particle size of 1–2 mm are higher than the results of the corresponding samples with a rubber particle size of 0–1 mm and 2–3 mm.
The results in Figure 10 show that under different vertical pressures, the maximum shear strength growth rates of the specimens obtained by the combined improvement method are 18.16%, 16.75%, 17.4%, and 18.62%, which significantly improves the improvement effect of rubber particles on loess. Comparing this result with the shear strength of the unmodified loess sample, it can be concluded that the maximum increase in shear strength of the sample is 36.41%, 45.5%, 39.5%, and 46.43%, respectively. It can be seen that the combination of rubber particles and EICP technology has a good effect on improving loess.
The shear strength parameters of loess samples improved by rubber particles combined with EICP technology under different working conditions are summarized in Figure 11. By comparing Figure 9, it can be seen that under different reinforcement conditions, the variation patterns of specimen cohesion and internal friction angle are relatively consistent, and the results have increased to varying degrees after EICP technology treatment. Compared with the results of only adding rubber particles, the maximum increases in cohesion and internal friction angle of the sample are 15.19% and 28.56%, respectively. Compared with the 0% dosage control group, the maximum increases in sample cohesion and internal friction angle are 47.87% and 64.42%, respectively. The soil sample with increased cohesion corresponds to a rubber particle size of 0–1 mm with a content of 7% and a rubber particle size of 1–2 mm with a content of 7%–13%. The soil sample with increased internal friction angle corresponds to the rubber particle size of 0–1 mm and 1–2 mm, with a content of 5%–15%; The rubber particle size is 2–3 mm, and the content is 10%–13%. Therefore, under the condition of the joint improvement, when the shear strength of the sample increases, the internal friction angle still plays a major role.
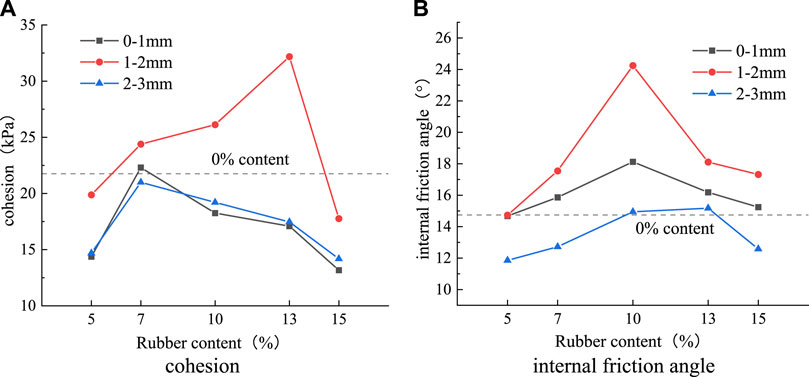
FIGURE 11. Curves of cohesion and internal friction angle of samples with different dosage and particle size (Rubber particles combined with EICP): (A) cohesion; (B) internal friction angle.
The mechanism analysis of the above results is as follows. Based on the principle of EICP technology, the generated calcium carbonate precipitation is the main factor leading to the increase of the shear strength of the sample. Generally speaking, the more calcium carbonate precipitation is generated in the soil, the more obvious the shear strength of the sample is improved, but the influencing factors are also related to the distribution form of calcium carbonate in the soil. Considering the non-hydrophilic properties of rubber particles, the water content in the sample preparation process is mainly determined by the content of soil particles, while the concentration of urease and cementing fluid is constent. Therefore, when the sample is mixed by mixing method, the amount of urease and cementing fluid in the sample decreases with the increase of the content of rubber particles, so the calcium carbonate precipitation generated in the sample decreases. Therefore, although the test shear strength increases, the growth rate of shear strength decreases with the increase of rubber content.
When the content of rubber added is the same but the particle size is different, for soil samples with smaller rubber particles added, the pore size in the soil is too small, which limits the migration of urease. The uneven distribution of urease and cementation fluid in the soil during sample preparation leads to the accumulation of calcium carbonate precipitates at a certain point or the reduction of calcium carbonate precipitates generated, resulting in poor solidification effect of the sample. When the particle size of rubber particles is large, the deformation of the rubber particles is significant during the compaction process using a jack. After the jack is unloaded, the rubber particles undergo deformation and rebound, leading to an increase in sample pores. However, the size of calcium carbonate crystals generated by EICP technology is about 2-150 um, and the crystal particles are small. The generated calcium carbonate precipitation cannot effectively bond the soil rubber together, resulting in poor solidification effect of the sample. Therefore, when rubber particles with smaller and larger particle sizes are added, although the shear strength increases, the growth rate of shear strength decreases.
In addition, it can be seen from Table 8 and Table 9 that calcium-carbonate solidified soil can increase the cohesion and internal friction angle of the sample, but due to the rubber content and rubber particle size, the amount of calcium carbonate precipitation and distribution of calcium carbonate are inconsistent. Therefore, the growth rate of cohesion and internal friction angle is not obvious.
In summary, under the two reinforcement conditions, when the rubber particle size is 1∼2 mm, the cohesion force and internal friction Angle of the sample reach the maximum value, and considering that the internal friction Angle of the sample is the main factor to improve the shear strength of the sample, and the internal friction Angle of the sample reaches the maximum value when the rubber content is 10%, it is recommended to choose the rubber particle size of 1∼2 mm and the rubber content is about 10%.
4 Conclusion
In this paper, the experimental study on t the shear mechanical properties of loess samples improved by only adding rubber particles and rubber particles combined with EICP technology are carried out, and the influence of different reinforcement methods on the mechanical properties of the improved soil samples are analyzed. Then the reinforcement mechanism of different improvement methods is expounded accordingly. The main conclusions are as follows.
(1) When the concentration of urease is 200 g/L, the concentration of cementation fluid is 1 mol/L, and both are added to loess in equal volume, the shear strength of the soil sample increases most significantly, indicating the feasibility of EICP technology.
(2) The strain variation characteristics of the specimen under the two reinforcement conditions are consistent, with the strain softening characteristic when the vertical pressure is at 50 kPa and the strain hardening characteristic when the vertical pressure is greater than or equal to 100 kPa.
(3) The changes in shear strength and shear strength indicators of the sample under two reinforcement conditions are consistent. Under different vertical pressures and rubber particle sizes, as the rubber content increases, they all show an increase and then a decrease. When the rubber particle size is 1–2 mm, the shear strength is the highest, and the main role of the shear strength indicator is the internal friction angle. The shear strength, cohesion and internal friction angle of the soil improved by rubber particle combined with EICP are increased by 46.43%, 47.87% and 64.42% compared with the results of unimproved soil sample.
(4) In the combination of rubber particles and EICP to improve loess samples, rubber particles have an inhibitory effect on EICP technology. Under different vertical pressures and rubber particle sizes, the shear strength growth rate of the sample gradually decreases with the increase of rubber content. Among them, when the rubber particle size is 1–2mm, the shear strength growth rate is the highest.
(5) For the improvement of loess, such as adding rubber particles or adding rubber particles combined with EICP technology, It is advisable to choose a rubber particle size of 1–2 mm and a rubber content of about 10%.
Data availability statement
The raw data supporting the conclusion of this article will be made available by the authors, without undue reservation.
Author contributions
YC: Data curation, Formal Analysis, Writing–original draft. SC: Data curation, Formal Analysis, Investigation, Project administration, Writing–original draft. DC: Investigation, Resources, Software, Supervision, Writing–review and editing. WW: Resources, Validation, Visualization, Writing–review and editing. XL: Conceptualization, Funding acquisition, Methodology, Writing–review and editing. JL: Software, Writing–review and editing.
Funding
The author(s) declare financial support was received for the research, authorship, and/or publication of this article.The work described in this paper was supported by the Natural Science Basic Research Plan in Shaanxi Province, (No. 2020JM-235 & No. 2022JM-262) and Fundamental Research Funds for the Central Universities, CHD (No. 300102282201), and for which the authors are very thankful.
Conflict of interest
YC, SC, DC, and WW were employed by The Seventh Engineering Co., LTD. of CFHEC.
The remaining authors declare that the research was conducted in the absence of any commercial or financial relationships that could be construed as a potential conflict of interest.
Publisher’s note
All claims expressed in this article are solely those of the authors and do not necessarily represent those of their affiliated organizations, or those of the publisher, the editors and the reviewers. Any product that may be evaluated in this article, or claim that may be made by its manufacturer, is not guaranteed or endorsed by the publisher.
References
Ahenkorah, I., Rahman, M. M., Karim, M. R., Simon, B., and Christopher, S. (2021). A review of enzyme induced carbonate precipitation (EICP): the role of enzyme kinetics. Sustain. Chem. 02, 92–114. doi:10.3390/SUSCHEM2010007
Anastasiadis, A., Gargala, C., Karakasi, I., Senetakis, K., Pitilakis, K., Edil, T., et al. (2011). Dynamic behavior of sand/rubber mixtures. Part I: effect of rubber content and duration of confinement on small-strain shear modulus and damping ratio. J. ASTM Int. 09, 103680. doi:10.1520/JAI103680
Anastasiadis, A., Senetakis, K., and Pitilakis, K. (2012). Small-strain shear modulus and damping ratio of sand-rubber and gravel-rubber mixtures. Geotech. Geol. Eng. 30, 363–382. doi:10.1007/s10706-011-9473-2
Cetin, H., Fener, M., and Gunaydin, O. (2006). Geotechnical properties of tire-cohesive clayey soil mixtures as a fill material. Eng. Geol. 88, 110–120. doi:10.1016/j.enggeo.2006.09.002
Chen, X. S., Qi, L., Zha, W. X., Zhou, Y. C., Gao, F., and Zou, W. D. (2021). Experimental study on cement improved loess. Int. J. Pavement. Res. Technol. 15, 1–11. doi:10.1007/S42947-021-00028-Y
Cuccurullo, A., Gallipoli, D., Bruno, A. W., Augarde, C., Hughes, P., and Borderie, C. L. (2020). “Soil stabilization against water erosion via calcite precipitation by plant-derived urease,” in Geotechnical research for land protection and development: Proceedings of CNRIG 2019 7 (Springer International Publishing), 753–762. doi:10.1007/978-3-030-21359-6_80
Derbyshire, E. (2001). Geological hazards in loess terrain, with particular reference to the loess regions of China. Earth. Sci. Rev. 54, 231–260. doi:10.1016/S0012-8252(01)00050-2
Dilrukshi, R., and Satoru, K. (2016). Effective use of plant-derived urease in the field of geoenvironmental/geotechnical engineering. J. Civ. Environ. Eng. 06, 1–13. doi:10.4172/2165-784x.1000207
Ding, Z. Y., Liu, T., Zhang, Y., Su, X. T., and Zheng, J. G. (2022). The curing and strength properties of highly moist waste mud from slurry shield tunnel construction. Appl. Sci. 12, 3762. doi:10.3390/APP12083762
Falak, O. A., Mohammed, O. A., Raghad, O. A., and Shymaa, K. G. (2011). Improvement of soil by waste tires addition. Eng. Technol. 29, 3417–3428.
Ghazavi, M. (2004). Shear strength characteristics of sand-mixed with granular rubber. Geotech. Geol. Eng. 22, 401–416. doi:10.1023/B:GEGE.0000025035.74092.6c
Hartman, D., Ledezma, M., Xiao, M., and Zoghi, M. (2013). Shake table test of MSE wall with tire derived aggregates(TDA) backfill. Geo-Congress, 1168–1177. doi:10.1061/9780784412787.118
Laurynas, V., Vilius, M., MarijaEgle, J. L., Martynas, T., Lina, M., Andrius, M., et al. (2023). Insights in MICP dynamics in urease-positive Staphylococcus sp. H6 and Sporosarcina pasteurii bacterium. Environ. Res. 234, 116588. doi:10.1016/J.ENVRES.2023.116588
Lee, H. J., Salgado, R., Bernal, A., and Lovell, C. W. (1999). Shredded tires and rubber-sand as lightweight backfill. J. Geotech. Geoenviron. 125, 132–141. doi:10.1061/(ASCE)1090-0241(1999)125:2(132)
Liang, S. H., Chen, J. T., Niu, J. G., Gong, X., and Feng, D. L. (2020). Using recycled calcium sources to solidify sandy soil through microbial induced carbonate precipitation. Mar. Georesources. Geotechnol. 38, 393–399. doi:10.1080/1064119X.2019.1575939
Liu, J., Li, X. A., Li, G., and Zhang, J. L. (2023). Experimental study on the mechanical behaviors of aeolian sand treated by microbially induced calcite precipitation (MICP) and basalt fiber reinforcement (BFR). Materials 16, 1949. doi:10.3390/MA16051949
Moo-Young, H., Sellasie, K., Zeroka, D., and Gajanan, S. (2003). Physical and chemical properties of recycled tire shreds for use in construction. J. Environ. Eng. 129, 921–929. doi:10.1061/(ASCE)0733-9372(2003)129:10(921)
Mu, J. Q., Zhang, J. Q., Kong, J. X., Wang, S. B., Wang, J., Zheng, J., et al. (2022). Study on improving loess properties with permeable polymer materials. Polymers 14, 2862. doi:10.3390/POLYM14142862
Nam, I., Chon, C., Jung, K., Choi, S., Choi, H., and Park, S. (2015). Calcite precipitation by ureolytic plant (Canavalia ensiformis) extracts as effective biomaterials. KSCE J. Civ. Eng. 19, 1620–1625. doi:10.1007/s12205-014-0558-3
Neupane, D., Yasuhara, H., Kinoshita, N., and Unno, T. (2013). Applicability of enzymatic calcium carbonate precipitation as a soil-strengthening technique. J. Geotech. Geoenviron. 139, 2201–2211. doi:10.1061/(ASCE)GT.1943-5606.0000959
Ng, W. S., Lee, M. L., and Hii, S. L. (2012). An overview of the factors affecting microbial-inducedCalcite precipitation and its potential application in soil improvement. Int. J. Civ. Environ. Eng. 62, 188–194.
Ossai, R., Rivera, L., and Bandini, P. (2020). “Experimental study to determine an EICP application method feasible for field treatment for soil erosion control,” in Geo-congress 2020 (Reston, VA: American Society of Civil Engineers), 205–213. doi:10.1061/9780784482834.023
Paassen, V., and Andreas, L. (2009). Biogrout ground improvementby microbial induced carbonate precipitation. Australia: Murdoch University.
Pierce, C. E., and Blackwell, M. C. (2003). Potential of scrap tire rubber as lightweight aggregate in flowable fill. Waste. Manage. 23, 197–208. doi:10.1016/S0956-053X(02)00160-5
Reza, H. K., Aliha, M. R. M., Ehsan, K., Amir, M., Salehi, S. M., Jafari, H. P., et al. (2023). Strength and cracking resistance of concrete containing different percentages and sizes of recycled tire rubber granules. J. Build. Eng. 67, 106033. doi:10.1016/J.JOBE.2023.106033
Tsang, H. H. (2008). Seismic isolation by rubber-soil mixtures for developing countries. Earthq. Eng. Struct. Dyn. 37, 283–303. doi:10.1002/eqe.756
Wen, K. J., Li, Y., Amini, F., and Li, L. (2020). Impact of bacteria and urease concentration on precipitation kinetics and crystal morphology of calcium carbonate. Acta. Geotech. 15, 17–27. doi:10.1007/s11440-019-00899-3
Whiffin, V. S. (2004). Microbial CaCO3 precipitation for the production of biocement. Murdoch University.
Xu, P., Lin, Q. W., and Fang, L. Y. (2022). Study on the mechanical properties of loess improved by lignosulfonate and its mechanism analysis and prospects. Appl. Sci. 12, 9843. doi:10.3390/APP12199843
Yang, Y., and Wen, J. Y. (2013). High fill embankment of collapsible loess settlement observation and research. Adv. Mat. Res. 838-841, 874–877. doi:10.4028/WWW.SCIENTIFIC.NET/AMR.838-841.874
Youwai, S., and Bergado, T. D. (2004). Numerical analysis of reinforced wall using rubber tire chips–sand mixtures as backfill material. Comput. Geotech. 31, 103–114. doi:10.1016/j.compgeo.2004.01.008
Zhang, Z. G., and Yang, X. M. (2021). Analysis of collapsible deformation mechanism of collapsible loess considering strain distribution characteristics of high embankment. Arab. J. Geosci. 15, 84–13. doi:10.1007/S12517-021-09358-4
Zhang, Y., Johnson, A. E., and White, D. J. (2019). Freeze-thaw performance of cement and fly ash stabilized loess. Transp. Geotech. 21, 100279. doi:10.1016/j.trgeo.2019.100279
Zhang, S., Sun, P., Li, R., and Wang, F. W. (2023). Preliminary investigation on a catastrophic loess landslide induced by heavy rainfall on 1 September 2022 in Qinghai, China. Landslidesl 20, 1553–1559. doi:10.1007/S10346-023-02086-8
Keywords: shear mechanical properties, improved loess, rubber particle incorporation, EICP technology, shear strength parameters
Citation: Chen Y, Chai S, Cai D, Wang W, Li X and Liu J (2023) Experimental study on shear mechanical properties of improved loess based on rubber particle incorporation and EICP technology. Front. Earth Sci. 11:1270102. doi: 10.3389/feart.2023.1270102
Received: 31 July 2023; Accepted: 28 August 2023;
Published: 07 September 2023.
Edited by:
Kai Liu, University of Oxford, United KingdomReviewed by:
Lv Longlong, Ningxia University, ChinaJuehao Huang, Chinese Academy of Sciences (CAS), China
Erdi Abi, Chongqing Jiaotong University, China
Copyright © 2023 Chen, Chai, Cai, Wang, Li and Liu. This is an open-access article distributed under the terms of the Creative Commons Attribution License (CC BY). The use, distribution or reproduction in other forums is permitted, provided the original author(s) and the copyright owner(s) are credited and that the original publication in this journal is cited, in accordance with accepted academic practice. No use, distribution or reproduction is permitted which does not comply with these terms.
*Correspondence: Xianpeng Li, bHhwMTgyMzUxNzEyMDBAMTYzLmNvbQ==