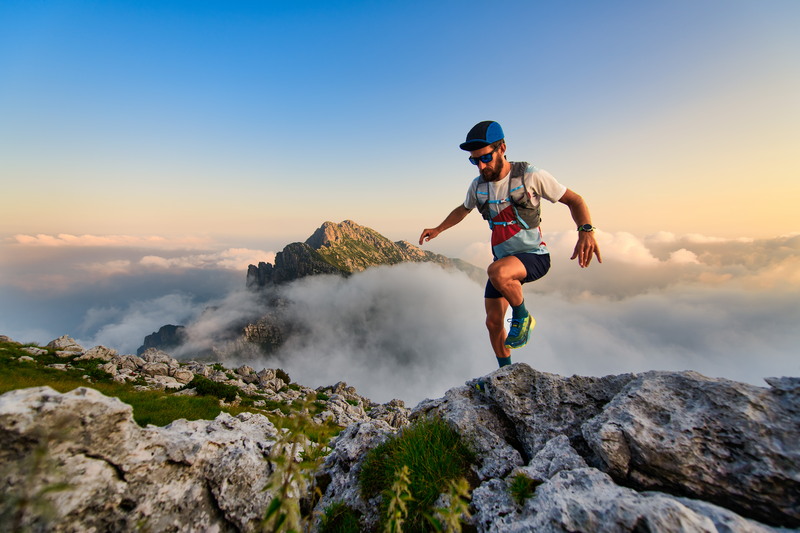
95% of researchers rate our articles as excellent or good
Learn more about the work of our research integrity team to safeguard the quality of each article we publish.
Find out more
ORIGINAL RESEARCH article
Front. Earth Sci. , 08 September 2023
Sec. Geohazards and Georisks
Volume 11 - 2023 | https://doi.org/10.3389/feart.2023.1258278
This article is part of the Research Topic Risk Assessment, Stability Monitoring, and Safe Design for Deep Rock Engineering View all 20 articles
To grasp the phase change characteristics of the filling slurry from fluid to solid state in time, conducted a study on the setting characteristics of the filling slurry with different aggregate combinations, and analyzed the law of the initial and final setting time with the change of the amount of cementation powder, filling plant tailings, tailing pond tailings, and water. The results show that the initial and final setting time of the filling slurry prepared from the tailings of the filling plant is proportional to the concentration, and is positively correlated with the slope decline of the sand-cement ratio. The filling slurry prepared from the tailings of the tailing pond shows roughly the same change trend as the above slurry, but the change law is not obvious, which cannot be expressed by one kind of functional model, and the initial setting time and final setting time are less than the above slurry, which is because the tailings of the tailing pond contain more fine particles, which play a role in delaying setting in the slurry. For example, for five kinds of filling materials with different aggregates of 4:1, 6:1, 8:1, 12:1, and 20:1 sand-to-ash ratios and concentrations of 66%–72%, the initial setting times of filling slurry prepared from tailings of filling plant and tailings of tailing pond were 75.3 h–112.3 h, 77.6 h–122.2 h, and the final setting times were 82.8 h–123.4 h, 85.5 h–133.9 h. Therefore, it shows that the use of filling plant tailings containing fewer fine particles to prepare filling slurry can obtain a better treatment effect of the mining area, and the shortening of the solidification and hardening process of filling slurry can accelerate the mining cycle operation, and increase the amount of solid waste disposal per unit time, thus creating the necessary technical conditions for the enterprise to improve production efficiency and sustainable development.
The setting time refers to the time during which the binding material in concrete forms crystals in the reaction and gradually solidifies and hardens. It plays a crucial role in the strength of concrete, the arrangement of construction progress, and the quality of construction (Hu et al., 2017; Li et al., 2007). The consolidation and hardening properties of concrete-like materials are also a reflection of their strength changes, and usually, if the consolidation and hardening process of concrete-like material slurry is normal, its strength will also develop normally with certain rules to meet the engineering application requirements (Recio-Hernández et al., 2023; Yuan et al., 2023; Gupta et al., 2022; Paul et al., 2022). In the case of mine goaf backfill, the filling materials are affected by the process technology and market price, and thus also impose special performance requirements on the filling materials. In the research of filling materials for metal mines, to meet the technical needs of comprehensive large-scale underground mining of ore bodies, researchers have carried out the study on hydration reaction and setting time and material modification of paste-like and high-concentration filling slurries, and the application of research results has met the needs of enhanced mine production (Yin et al., 2020; Yin et al., 2022; Ouyang et al., 2022). In terms of setting property modification of cemented fly ash filling materials using sodium silicate, researchers analyzed the strength behavior and microstructure response and proposed a reasonable admixture dosage, thus meeting the demand for an efficient coal mine filling design (Cavusoglu et al., 2021). For the development of filling materials in special mining areas, researchers analyzed the microstructure properties of modified coal gasification slag filling materials, prepared modified coal gasification slag (MCGS) using sodium sulfate as an exciter, and then prepared modified coal gasification slag filling materials (MCGS-CPB) by MCGS, thus providing theoretical support for the microstructure analysis and material promotion of coal gasification slag filling materials (Yang et al., 2021).
In the process of filling various types of mine goaf, binding materials usually account for 50%–75% of the filling cost, and to reduce the filling cost, the current research topics on new binding materials instead of conventional binding materials have become exceptionally active and have played a role in reducing costs and increasing efficiency to some extent in practical applications (Zhang et al., 2023; Guo et al., 2022; Haruna et al., 2022; Zhao et al., 2022). In the study of cemented filling materials, researchers analyzed the process of microstructural transformation of composite binding materials to Al-O tetrahedra and observed that CaSO4 was completely hydrated to generate Aft during the reaction phase, resulting in a binding material with high early strength (Wang et al., 2017). In the exploration of new slag-based cemented filling materials, the researchers combined the properties of classified tailings of a Pb-Zn mine and used X-ray fluorescence (XRF) and X-ray diffraction (XRD) to analyze the microscopic and macroscopic properties of new slag-based cemented filling materials, and the industrial filling of this new material provided strong support for mine environmental protection and solid waste resource utilization and also obtained an extra cost of 9,460,800 yuan due to the purchase of cement in terms of cost (Wu et al., 2020). Combined with the importance of the consolidation and hardening properties of the filling slurry, the researchers directed at the properties of large underground copper mines classified tailings, conducted the determination of the setting time of the cemented filling material, pointed out that the cement admixture and tailings size play an important role in consolidation and hardening (Deng et al., 2008).
Combined with the properties of filling tailings and new binding materials, it is usually necessary to carry out the determination of the setting time parameters of the filling slurry under the conditions of different concentrations and additions of new binding materials, analyze the characteristics of the solidification and hardening law of the filling slurry. From the statistical analysis of the measured values of the filling slurry setting time, we can intuitively understand the solidification and hardening state of the filling slurry, and then judge the material state of the filling slurry into the mine goaf, and thus make the subsequent process connection (Deng et al., 2022; Shahsavari et al., 2022; Jin et al., 2022; Mohammadamin et al., 2020). As a common index for judging the solidification and hardening performance of filling materials, the initial and final setting time of cemented filling slurry has a great influence on the performance of filling materials. In this study, tests on the initial and final setting time of filling slurry with different aggregate combinations were carried out to analyze its variation law with concentration and sand-cement ratio, which provides a perfect technical basis for guiding mine filling. Given the complexity and specificity of mine conditions, each performance of the material needs dialectical analysis to meet the safe mining conditions and comprehensive benefits of the enterprise.
In the progress of determining the initial and final setting time of cemented filling slurry, combined with the filling process of mining enterprises, the tailings of filling plants and tailing ponds are regarded as filling aggregates, cementation powder is regarded as binding material, and the filling slurry was formed with different concentrations after adding a certain amount of water, and then the setting time parameters were determined by manual Vicatometer after filling into stainless steel round mold with the specifications of 65×75×40 mm. When preparing a stainless-steel circular mold, attention should be paid to applying a layer of oil on the inner wall of the mold to facilitate mold removal; The slurry needs to fill the mold and spill a little to avoid experimental errors caused by sedimentation during the solidification process.
As the aggregate used in the setting time test, the unclassified tailings appear as a grayish-brown powder, the tailings of the filling plant were obtained by sampling on-site at the filling slurry preparation station, and the tailing pond tailings were obtained by sampling on-site at the tailing pond in the south area during normal production. After drying and crushing these tailings into the original granular state, the basic physical property index parameters were measured, and the results obtained are shown in Table 1. The particle size was tested by laser particle size meter to obtain the particle gradation characteristic parameters of the unclassified tailings, and the particle size curve of the unclassified tailings in the filling plant was obtained after analyzing and processing the data as shown in Figure 1, and the particle size curve of the unclassified tailings in the south tailing pond as shown in Figure 2, from the nonuniformity coefficients and curvature coefficients analyzed in these two graphs, both of the two tailings belong to well-graded soils. The content of different chemical components in the tailings was determined by chemical experimental analysis, as shown in Figure 3.
As the binding material used in the setting time test, the cementation powder appears as a gray-white powder, after on-site sampling at the site of the binding material mixing station, an uniformly mixed finished cementation powder was obtained, and transported to the laboratory to determine its basic physical properties index parameters, the results obtained are shown in Table 2. The particle size was tested by laser particle size meter to obtain the particle gradation characteristic parameters of the cementation powder, and the particle size curve of the cementation powder was obtained after analyzing and processing the data as shown in Figure 4, from the nonuniformity coefficients and curvature coefficients analyzed in the figure, the cementation powder is well-graded.
The water used for mixing the filling materials in the test is ordinary tap water, which is a colorless and odorless transparent liquid at room temperature, with a specific gravity of 1, a density at room temperature of 0.996 t/m³, a weight of 9.8 kN/m³ at room temperature, and a pH value of about 7.0–7.4.
The filling materials were mixed by a portable agitator and, after mixing uniformly, poured into a stainless steel round mold placed on a 10×10 cm glass plate. During operation, it should be handled gently to prevent excessive force from damaging the glass sheet. There was not vibration throughout the entire process, and a Vicat apparatus was used to test the setting time of each group of filling slurry at certain intervals. The corresponding sinking depth and intervals of the test pin were recorded, and the test pin was held by hand during the initial setting time test, then let fall slowly under its own weight, avoiding bending and deformation from hitting the glass plate. The Vicat apparatus used for the determination of the setting time index is shown in Figure 5, and the filling slurry setting time test samples are shown in Figure 6.
Combining the properties of the tailings and the new binding material for filling, this study was carried out to determine the setting time under different concentrations and additions of the new binding material, and to analyze the characteristics of the solidification and hardening law from them. Through the experimental tests, the setting time parameters of each group of filling slurry with filling plant tailings and tailing pond tailings as the filling aggregate and sand-cement ratios of 4:1, 6:1, 8:1, 12:1, and 20:1 and concentrations of 66, 68, 70, and 72% were obtained, and then the change law of the initial setting time, the final setting time, the interval between the initial and final setting with different formulations of filling slurry was analyzed in depth.
The characteristics of the setting time of the filling materials were measured through multiple groups of proportioning tests, and the variation law of the setting time of the filling slurry prepared by filling plant tailings and tailing pond tailings with the concentration and sand-cement ratio are shown in Figures 7, 8. From the three-dimensional scatter diagram, it can be seen that the setting time of the filling slurry prepared from the tailings of the filling plant gradually shortens as the concentration increases, and the higher the sand-cement ratio, the longer the setting time of the slurry, and the filling slurry prepared from the tailing pond tailings also reflects this law.
FIGURE 7. Variation law of the setting time of the filling slurry prepared by filling plant tailings with concentration and sand-cement ratio.
FIGURE 8. Variation law of the setting time of the filling slurry prepared by tailing pond tailings with concentration and sand-cement ratio.
Through statistical analysis of the test data, the characteristic functions of the setting time of the filling slurry prepared from the tailings of the filling plant and the tailings of the tailings pond with the concentration and the sand-cement ratio are shown in Tables 3, 4, 5, 6, respectively. From the data in the table, it can be seen that the initial and final setting time of the filling slurry prepared from the tailings of the filling plant is proportional to the concentration, and shows a positive correlation with the slope decrease of sand-cement ratio, while the setting time of the filling slurry prepared from the tailings of the tailing pond is slower than that of the filling slurry prepared from the tailings of the filling plant, and the change law is not stable and cannot be expressed by one kind of function model, and there is no obvious law for the difference of the initial and final setting time.
TABLE 3. Variation characteristic function of setting time of filling slurry with different aggregate with concentration.
TABLE 4. Variation characteristic function of setting time of filling slurry with different aggregate with concentration.
TABLE 5. Variation characteristic function of setting time of filling slurry with different aggregate with a sand-cement ratio.
TABLE 6. Variation characteristic function of setting time of filling slurry with different aggregate with a sand-cement ratio.
Among the various underground mining methods, the filling mining method is the mining method with the highest ore recovery, the best sustainability, and the safest construction, and its outstanding contribution to the environment as well as to the improvement of economic benefits has been mentioned in a large number of papers (Choudhary et al., 2013; Zhang et al., 2023). The new binding material prepared in this study for filling the underground goaf, not only saves the company a lot of production and operation costs but also greatly improves the surrounding rock conditions of the underground goaf. The continuous flow of filling slurry into the extraction area will produce hydrostatic pressure on the surrounding rock and retaining wall, and after 3–5 days of solidification and hardening, a cemented backfill with high strength will be formed gradually, which makes part of the exposed mineral rock body transform from uniaxial to the triaxial compressed state, thus improving the stress conditions of the surrounding rock.
From the compositional analysis of the tailings and the cementation powder, it can be seen that the component content of SiO₂ far exceeds that of other inorganic compounds, which will result in a large number of silicate ions in the slurry, which reacts with Ca ions in the slurry to produce calcium silicate hydrate (CSH) leading to a denser microstructure and much higher strength of the resulting backfill (Zheng et al., 2022). It can be seen from the law of setting time evolution that the use of different filling aggregates will cause the same concentration and the same ratio of the filling slurry setting time differences, the initial setting time and final setting time of the cemented filling slurry with the increase in concentration and show a certain trend of shortening, while the difference between the initial and final setting time is not a significant trend followed. Through particle size analysis of two types of tailings materials, the median particle size of the filling plant tailings is 175.95um, and the median particle size of the tailing pond tailings is 74.39um. It is obvious that the tailing pond tailings contain many fine particle tailings, which play a role in delaying the setting of the slurry (Hsu et al., 1998). Given the specificity of the physical and chemical properties of mine filling aggregates and filling binding materials, the setting time of cemented filling slurry takes a long time, but the ultimate purpose of cemented filling in each mine is to obtain a relatively high-strength filling material, thus requiring a certain amount of comprehensive consideration between various properties.
Due to the large number of fine-grained tailings in the test material, its specific surface area is large, which is reflected in the apparent state as a very viscous slurry. The excessive specific surface area makes the surface of the tailings particles almost all in contact with water, making it difficult to adhere, and the filling slurry used for filling the mining area needs great fluidity to achieve self-flow transport, so the water content is oversaturated, resulting in very weak adsorption between the particles and difficult to coagulate. For five kinds of filling materials with different aggregates of 4:1, 6:1, 8:1, 12:1, and 20:1 sand-to-ash ratios and concentrations of 66%–72%, the initial setting times of filling slurry prepared from tailings of filling plant and tailings of tailing pond were 75.3 h–112.3h, 77.6 h–122.2 h, and the final setting times were 82.8 h–123.4 h and 85.5 h–133.9 h. The binding material in this study is a cement substitute specially developed by special treatment of tailings. In this experimental study, compared with cement, cementation powder as a new binding material far exceeds the setting time of cement by 5 h, however, in terms of economic benefits, cementation powder instead of cement can greatly save costs, and in terms of mechanical properties, the strength of the backfill formed by cementation powder instead of cement as a binding material has been greatly improved. In summary, to solve the demand of mine filling management engineering, this study carried out the setting time test experiment of filling slurry, and proved that the properties of filling slurry prepared from tailings in different position states of the same mine will produce certain differences, and obtained the characteristic law of material setting, the obtained test results all meet the demand of mine filling, and provide strong data support for the promotion and application of mine filling method.
(1) The initial and final setting time of the filling slurry prepared from the tailings of the filling plant is proportional to the concentration and is positively correlated with the slope decline of the sand-cement ratio. The filling slurry prepared from the tailings of the tailing pond roughly follows this trend, but the change law is not obvious, which cannot be expressed by one kind of functional model. There is no obvious change law in the interval between the initial and final setting of different aggregate filling slurrys.
(2) For the filling slurry with different filling aggregates, the setting speed decreases with the increase of slurry concentration. Compared with the conventional concrete used in the construction field, the filling slurry used in the goaf backfill has a higher water content, which far exceeds its critical saturation state water content. Excessive water reduces the cohesion between the particles, so the setting time of the filling slurry is much longer than that of normal concrete, and has a negative correlation with the concentration of the filling slurry.
(3) From the setting test results, it can be seen that the filling slurry with tailing pond tailings as filling aggregate is slower to solidify and harden than the filling slurry with filling plant tailings as filling aggregate, and it varies with the sand-cement ratio, which is mainly because the tailing pond tailings contain more fine particles, and under the same sand-cement ratio and the same concentration, the equivalent amount of cementation powder particles need to be dispersed into more tailings particles, Therefore, the cementing effect is negatively affected.
The original contributions presented in the study are included in the article/Supplementary material, further inquiries can be directed to the corresponding author.
DD: Funding acquisition, Investigation, Writing–original draft, Writing–review and editing. YW: Data curation, Investigation, Writing–review and editing. WL: Data curation, Writing–review and editing. JF: nvestigation, Writing–review and editing.
The author(s) declare financial support was received for the research, authorship, and/or publication of this article. This work was supported by the NSFC projects of China (51764009), the Provincial Natural Science Foundation of Hunan (2023JJ50041), the Doctoral Research Project of Xiangtan University (22QDZ28, 22QDZ35), the Guizhou Institute of Technology High-level Talent Research Start-up Funding Project—Research on Optimization of Particle grading of Modified filling Materials (Project Approval Number/Contract Number: XJGC20190652), the Guizhou Province Science and Technology Projects (Grant No.QKHZC(2021) General407). The authors are grateful for the financial support for this research.
The authors declare that the research was conducted in the absence of any commercial or financial relationships that could be construed as a potential conflict of interest.
All claims expressed in this article are solely those of the authors and do not necessarily represent those of their affiliated organizations, or those of the publisher, the editors and the reviewers. Any product that may be evaluated in this article, or claim that may be made by its manufacturer, is not guaranteed or endorsed by the publisher.
Cavusoglu, I., Yilmaz, E., and Yilmaz, A. O. (2021). Sodium silicate effect on setting properties, strength behavior, and microstructure of cemented coal fly ash backfill. Powder Technol. 384, 17–28. doi:10.1016/j.powtec.2021.02.013
Choudhary, B. S., and Kumar, S. (2013). Underground void filling by cemented mill tailings. Int. J. Min. Sci. Technol. 8 (6), 893–900. doi:10.1016/j.ijmst.2013.11.003
Deng, D., Yao, Z., Yang, Y., and Meng, W. (2008). Setting properties of cement-classified tailings filling slurry. Nonferrous Met. 2008 (03), 112–115. doi:10.3969/j.issn.2095-1744.2008.03.030
Deng, X., Li, Y., Wang, F., Shi, X., Yang, Y., Xu, X., et al. (2022). Experimental study on the mechanical properties and consolidation mechanism of microbial grouted backfill. Int. J. Min. Sci. Technol. 32 (2), 271–282. doi:10.1016/j.ijmst.2022.01.010
Guo, L., Peng, X., Zhao, Y., Liu, G., Tang, G., and Pan, A. (2022). Experimental study on direct tensile properties of cemented paste backfill. Front. Mater. 9, 2022. doi:10.3389/fmats.2022.864264
Gupta, R., Mahajan, M., Sharma, P., Bhardwaj, S., Gupta, V., and Mahajan, A. (2022). Application of vesical imaging-reporting and data system in evaluation of urinary bladder cancer using multiparametric magnetic resonance imaging: A hospital-based cross-sectional study. Cem. Concr. Res. 2022, 162–168. doi:10.1055/s-0042-1755334
Haruna, S., and Fall, M. (2022). Reactivity of cemented paste backfill containing polycarboxylate-based superplasticizer. Miner. Eng. 2022, 188. doi:10.1016/j.mineng.2022.107856
Hsu, J. P., and Liu, B. T. (1998). Effect of particle size on critical coagulation concentration. J. colloid interface Sci. 198 (1), 186–189. doi:10.1006/jcis.1997.5275
Hu, X., Jiang, X., and Pan, P. (2017). Effect of sample setting time on experimental evaluation of hot mix asphalt. Constr. Build. Mater. 152, 375–385. doi:10.1016/j.conbuildmat.2017.07.012
Jin, J., Qin, Z., Lu, X., Liu, T., Zhang, G., and Shi, J. (2022). Rheology control of self-consolidating cement-tailings grout for the feasible use in coal gangue-filled backfill[J]. Constr. Build. Mater. 2022, 316. doi:10.1016/j.conbuildmat.2021.125836
Li, Z., Xiao, L., and Wei, X. (2007). Determination of concrete setting time using electrical resistivity measurement. J. Mater Civ. Eng. 19 (5), 423–427. doi:10.1061/(asce)0899-1561(2007)19:5(423)
Mohammadamin, J., Mohammad, S., and Murray, G. (2020). Experimental study of the behavior of cemented paste backfill under high isotropic compression. J. Geotechnical Geoenvironmental Eng. 146 (11). doi:10.1061/(asce)gt.1943-5606.0002383
Ouyang, S., Huang, Y., Wu, L., Yin, W., Yang, X., Wang, J., et al. (2022). Effects of chlorides on setting time, hydration heat and hydration products of fresh slurry of cemented paste backfill. Case Stud. Constr. Mater. 17, e01462. doi:10.1016/j.cscm.2022.e01462
Paul, S. C., Babafemi, A. J., Miah, M. J., Basit, M. A., Hasan, N. M. S., and Kong, S. Y. (2022). Role of sugarcane juice as a natural admixture on setting time and hardened properties of cementitious materials. Infrastructures 7 (10), 145. doi:10.3390/infrastructures7100145
Recio-Hernández, J. A., Landa, A. E., Fajardo San Miguel, G., Mejía-Sánchez, E., López Huerta, F., Orozco Cruz, R., et al. (2023). Electrochemical noise study of the passivation of AISI 1018 carbon steel as reinforcements embedded in ternary concretes during the setting process. Electrochem. Soc. Trans. 110 (1), 159–167. doi:10.1149/11001.0159ecst
Shahsavari, M., Jafari, M., and Grabinsky, M. (2022). Influence of load path and effective stress on one-dimensional deformation of cemented paste backfill (CPB) during deposition and curing. Geotechnical Geol. Eng. 2022, 2319–2338. doi:10.1007/s10706-021-02030-4
Wang, Z., Xia, H., and Wang, H. (2017). Analysis of hydration mechanism and microstructure of composite cementitious materials for filling mining. J. Wuhan Univ. Technol. Mater. Sci. 32 (04), 910–913. doi:10.1007/s11595-017-1689-4
Wu, G. (2020). Application and research of new slag-based binding materials in industrial trials for mine backfill. Guangzhou, China: Guangzhou University.
Yang, P. (2021). Preparation of modified coal gasification slag backfill material and its hydration and microstructure evolution study. Xi'an, China: Xi'an University of Science and Technology.
Yin, S., Liu, J., Chen, W., Zhou, L., Kou, Y., and Li, X. (2020). Influence of different coarse aggregates on the setting performance of paste and ratio optimization. J. Eng. Sci. 42 (07), 829–837. doi:10.13374/j.issn2095-9389.2019.07.14.005
Yin, S., Zhou, Y., Wang, L., Pan, J., and Kou, Y. (2022). Setting, bleeding, and hardening strength properties of coarse aggregate filling slurry. Case Stud. Constr. Mater. 2022, 17. doi:10.1016/j.cscm.2022.e01667
Yuan, L., Li, T., Li, H., Wang, F., and Qi, H. (2023). An adaptive degree of freedom condensation algorithm for simulating transient temperature, applied to an asphalt-concrete core wall. Appl. Sci. 13 (3), 1456. doi:10.3390/app13031456
Zhang, S., Wang, K., Li, H., Zhang, X., and Jiang, Y. (2023a). Novel SCMs produced by the calcination of secondary aluminum dross with dolomite and their potential usage in cemented paste backfill. Constr. Build. Mater. 2023, 365. doi:10.1016/j.conbuildmat.2022.130119
Zhang, X., Wu, D., Lu, H., Liu, L., and Zheng, S. (2023b). Improvement of tailings gradation on workability and strength of cemented tailings backfill. Constr. Build. Mater. 387, 131633. doi:10.1016/j.conbuildmat.2023.131633
Zhao, Q., Huang, Y., Ren, Q., Feng, Y., Han, Y., and Qi, W. (2022). Effectiveness of soda residue-activated GGBS as an alternative binder on compressive strength and workability of cemented paste backfills: reuse of multi-source solid wastes. Constr. Build. Mater. 2022, 348. doi:10.1016/j.conbuildmat.2022.128594
Keywords: phase change characteristics, mineral processing tailings, filling slurry, setting characteristics, solid waste treatment, sustainable development
Citation: Deng D, Wang Y, Liang W and Fan J (2023) Study on the setting characteristics of filling slurry with different aggregate combinations. Front. Earth Sci. 11:1258278. doi: 10.3389/feart.2023.1258278
Received: 13 July 2023; Accepted: 24 August 2023;
Published: 08 September 2023.
Edited by:
Bin Gong, Brunel University London, United KingdomReviewed by:
Shichao Zhang, Anhui University of Science and Technology, ChinaCopyright © 2023 Deng, Wang, Liang and Fan. This is an open-access article distributed under the terms of the Creative Commons Attribution License (CC BY). The use, distribution or reproduction in other forums is permitted, provided the original author(s) and the copyright owner(s) are credited and that the original publication in this journal is cited, in accordance with accepted academic practice. No use, distribution or reproduction is permitted which does not comply with these terms.
*Correspondence: Ye Wang, MjAxNjA3MTNAZ2l0LmVkdS5jbg==
Disclaimer: All claims expressed in this article are solely those of the authors and do not necessarily represent those of their affiliated organizations, or those of the publisher, the editors and the reviewers. Any product that may be evaluated in this article or claim that may be made by its manufacturer is not guaranteed or endorsed by the publisher.
Research integrity at Frontiers
Learn more about the work of our research integrity team to safeguard the quality of each article we publish.