- 1Department of Civil Engineering, School of Civil and Resource Engineering, University of Science and Technology Beijing, Beijing, China
- 2State Key Laboratory of Hydroscience and Engineering, Tsinghua University, Beijing, China
- 3HUANENG Tibet Hydropower Safety Engineering Technology Research Center, Chengdu, China
- 4China Railway Engineering Equipment Group Co., Ltd., Zhengzhou, China
Existing tunnel boring machine (TBM) construction presents certain shortcomings. These include difficulty in comprehensive perception of information, poor timelines of information transmission and storage systems, significant effects of traditional data processing methods on the timeless of intelligent decision-making, and poor applicability of decision-making models and control strategies. In addition, the integration level of perception, decision-making, and control should be further improved. Therefore, a cross-platform deployable intelligent tunnelling robot system with closed-loop intelligent control functions of a “comprehensive perception, dual-driven decision-making, and composite intelligent control” is developed. Based on fieldbus, communication, database, cloud computing, and advanced exploration technologies, a multi-source information perception and integrated management platform based on a two-layer architecture is built to achieve the comprehensive perception of tunnelling information. In addition, an optimal decision-making method of the particle swarm optimisation (PSO) algorithm is simultaneously proposed for the minimum decision-making of tunnelling specific energy for scientific analyses and decision-making. A composite intelligent control strategy comprising multimodal and expert experienced learning control strategies is designed to achieve the control of conventional and unfavourable geological sections, respectively. Engineering cases verified the effectiveness and reliability of the intelligent tunnelling robot system. The research results not only provide new ideas and technical means for achieving the less-manned, unmanned, and intelligent tunnelling construction of deep-buried long tunnels but can also be promoted owing to its universality.
Introduction
The tunnel boring machine (TBM) has recently become a preferred tool for tunnel construction, mainly for long tunnels with large sections, owing to its several advantages in performance, such as the security, higher efficiency, environmental friendliness, and quality, over the new Austrian tunnelling method (NATM) and drilling-blasting methods (Armaghani et al., 2017; Li et al., 2022; Pan et al., 2022). However, the TBM is extremely sensitive to geological changes and is excessively dependent on the operator experience (Armetti et al., 2018). A manual operation relies on experience, and different operators have varying skill levels, which creates quality control issues in addition to similar accidents repeatedly occurring (Mahdevari et al., 2014; Zhang et al., 2022a). Specifically, when encountering stratum changes or complex geological conditions, manual operations may cause jamming, collapsing, and other significant consequences owing to the inability to make effective adjustments in a timely manner.
Over the past years, several techniques have been continuously proposed to solve the problems caused by completely relying on human experience to control TBM construction. These techniques can be summarised as advanced geological prospecting techniques, intelligent guidance, intelligent support, intelligent tunnelling techniques combined with sensing and fusion of information of the rock and mechanical parameters, monitoring and early-warning techniques, and modern information technologies (Mahmoodzadeh et al., 2021; Liu W L et al., 2022). An important means to ensure a safe and efficient TBM tunnel is based on geological analysis, which is a fast and reliable detection method to determine the physical characteristics of the earth, scientifically establishing an advanced geological prospecting system (Deng, 2018). It is difficult to meet the requirements of an efficient and safe TBM tunnelling process using common geological prospecting methods that are suitable for drilling-and-blasting construction, such as tunnel seismic prediction (Dastanboo et al., 2020), tunnel geological prediction (Li et al., 2014), tunnel reflection tomography (Du et al., 2022), and tunnel seismic tomography (Ba et al., 2020). New geological exploration technologies suitable for TBM and their application to TBM systems are being researched. The new geological exploration method is roughly divided into four categories: 1) differences in the medium elastic wave impedance that are used to detect geological structures, such as fault fractured zones and soft intercalated layers (Allo et al., 2022); 2) the medium temperature field, micro-seismic signal, dielectric differences, and polarisation characteristics that used for advanced geological disaster forecasting (Yu et al., 2017; Li et al., 2022); 3) intelligent classification of surrounding rock conditions based on big data and artificial intelligence (AI) technology (Liu Z B et al., 2021; Santos et al., 2021); and 4) geological disaster forecasting based on big data and AI (Mahdevari and Torabi, 2012; Sun et al., 2021).
Attitude control during TBM excavation is an important task for the TBM operator, and the degree of consistency between the excavation and design routes determines the construction quality of the tunnel (Marcher et al., 2022). Therefore, the intelligent guidance of TBM excavation is gaining popularity as a research topic, which mainly considers the following three aspects: modelling (Qiao et al., 2020), automatic control (Huang et al., 2022), and intelligent control of the tunnelling posture (Zhang and Ma, 2018; Garcia et al., 2021) A reliable design of tunnel support systems and the reasonable selection of support timing are important prerequisites to ensure the safety and long-term stability of tunnel construction (Farrokh et al., 2011; Kampas et al., 2020). Research regarding the intelligent support of tunnels includes the following three aspects: intelligent matching and optimisation of support parameters (Meschke et al., 2011), intelligent decision-making of supporting timing (Sun et al., 2007), and intelligent support structure (Liu et al., 2022c).
Owing to the lack of tunnelling evaluations and effective means to make intelligent decisions, practical tasks mainly rely on human experiences rather than scientific bases (Deng, 2018). Therefore, intelligent tunnelling research focuses on the prediction of TBM performance and intelligent decision-making of the TBM tunnelling parameters (Harandizadeh et al., 2021; Xu et al., 2021; Liu Y R et al., 2022). The prediction of TBM performance mainly includes the tunnelling speed, construction speed, operation utilisation rate, and tool wear of the TBM. More than 30 theoretical and empirical models have been developed since the 1970s (Zhang et al., 2022a). The CSM models proposed by the Colorado School of Mines include the Sanio, dimensional, and improved CSM models, which are theoretical prediction models (Goshtasbi et al., 2009; Pan et al., 2021). Regarding the empirical models, Nelson, Norwegian Institute of Technology (NTNU), QTEM, Alber, neuro-fuzzy, and Rock Mass Excavability (RME) are commonly used (Hassanpour et al., 2011; Hassanpour et al., 2016). The intelligent decision-making of the TBM tunnelling parameters is divided into prediction optimisation and decision-making. The former includes tunnelling parameter prediction and optimisation (Li et al., 2019; Gong et al., 2021; Liu W L et al., 2021). Regarding the intelligent prediction of TBM tunnelling parameters, a data-driven model is established based on the existing data of construction history to directly predict or indirectly determine reasonable TBM tunnelling parameters and then assist in adjusting and controlling these parameters (Nikakhtar et al., 2022). The optimal intelligent decision-making of the TBM tunnelling parameters is based on the different optimisation objectives and decision-making criteria within a feasible range of key control parameters. The optimisation objectives are divided into excavation efficiency, economy, energy consumption, and the excavation effect; the decision-making criteria can be single- or multi-objective optimisation.
Although scholars have actively explored TBM intelligent construction technology, the following problems remain: 1) Local area perception is unable to meet the needs of a multi-scale, comprehensive, and multi-level perception; it is difficult to strongly support decision-making and control. 2) A seamless integration between the basic automation control network and the process and management control system is lacking. 3) Insufficient real-time information retrieval, screening, and transmission, in addition to the conventional tunnelling cycle data extraction, processing, and analysis methods, make it difficult to effectively support decision-making and control. 4) The rapid expansion of data volume, dimension, and granularity makes traditional storage systems unable to meet application requirements. 5) A single mechanism or data-driven decision-making model cannot resolve the adaptive dynamic control of tunnelling parameters caused by rock mass state changes; in addition, the cost of decision-making algorithm testing is high, especially the safety risk. 6) It is difficult for the existing single control strategy to meet the diverse requirements of working conditions in conventional and unfavourable geological sections. In addition, the integration level of perception, decision-making, and control must be further improved.
Considering the aforementioned problems and based on automatic control, AI, big data analysis, and other technologies, as well as the closed-loop intelligent control concept of the “perception-decision-control” (Li et al., 2022a; Li et al., 2022b), the TBM construction of deep-buried long tunnels is researched in this study to develop an intelligent tunnelling robot system, which exhibits a comprehensive perception, dual-driven decision-making, and compound intelligent control functions.
Intelligent tunnelling robot system
Overall system architecture
The intelligent tunnelling robot system (Figure 1) includes three parts: a comprehensive perception system, intelligent decision-making system, and real-time control system. The comprehensive perception system can achieve the comprehensive perception, seamless integration, and real-time fusion management of adverse geological, disastrous, and multi-source construction information in complex environments. The intelligent decision-making system considers the differences in the excavation targets of TBM construction under different geological conditions, adaptively selects the intelligent decision-making model, and provides the optimal TBM tunnelling parameters. The real-time control system receives the optimal tunnelling parameters and controls the TBM to execute the tunnelling action according to the multi-mode control strategy.
Comprehensive perception system
Data acquisition and transmission
The entire process information of TBM construction of large buried deep and long tunnels is massive, multi-dimensional, multi-granular, and strongly heterogeneous. Therefore, it is difficult to obtain and effectively collect comprehensive data. Comprehensive perception is a prerequisite for achieving intelligent decision-making and control; a more refined and time-sensitive information perception is more beneficial for TBM construction decision-making and control. Considering the aforementioned problems and the compatibility of TBM equipment manufactured by different manufacturers, as well as the requirements for a simple deployment of projects, the comprehensive perception system architecture is a two-layer architecture, including a field device layer and a field monitoring layer (Figure 2). The field device layer is the direct object of data collection, and the types of perceptual information include geological, advanced geological exploration, host vibration monitoring, cutter status monitoring, TBM guidance, PLC, rock-machine interaction, rock fragment analysis, and other types of information. The host vibration monitoring, cutter status monitoring, rock-machine interaction, and TBM guidance information are all obtained from the TBM host system and auxiliary equipment. The rock fragment analysis information is provided jointly by the TBM host system, auxiliary equipment, and continuous belt conveyor system. Geological information originates from early geological explorations. The advanced geological exploration system provides information regarding geological hazards, such as rock bursts and water inrush. Other types of information related to the field device layer is provided by the TBM rear supporting system, such as the roof bolter, concrete spraying system, and other relatively independent supporting systems. PLC information is mainly obtained by the master (slave) PLC controller of the field monitoring layer located in the TBM main control room. The communication connection between the field device layer and field monitoring layer is achieved using a fieldbus. The PLC controller of the field monitoring layer adopts a dual-machine hot standby design of the master station and master station (slave), which completes the dual-machine hot standby of the CPU through PLC hardware. The two CPU modules achieve the purpose of a hot standby through two redundant memory exchange modules, which are connected by an optical fibre. The monitoring and display module located in the field monitoring layer belongs to the Class 2 master station of the fieldbus system. It has the equipment to manage the configuration and diagnostic data of the master station PLC controller and master (slave) PLC controller, in addition to having the communication capabilities for complete data reading and writing, system configuration, monitoring, fault diagnosis, programming, parameter setting, and the online detection of each station, such as the operator monitoring, operator interface, and compiler.
The advanced geological exploration system integrated into the field device layer includes rock burst microseismic monitoring and the advanced detection of water inrush. The former achieves an all-weather, real-time, and seamless collection of microseismic signals, automatic filtering and identification of microseismic signals, automatic fine-positioning of microseismic sources, and a three-dimensional dynamic display of the positioning information and disaster risk areas. The latter is achieved by the joint interpretation and visualisation of the induced polarisation, seismic, and cross-hole radar methods. The spatial position and distribution shape of the unfavourable geological bodies are displayed based on data-driven three-dimensional visualisation. This study adopts the network communication interface to achieve the integration between the systems; that is, real-time data network communication is implemented in the standard tag length value format based on the user datagram protocol network protocol. The specific unit data is expressed in the JSON format, and the standard nested format is used for multiple fields.
The data servicer built into the computer terminal provides data management, data backup, and data communication services (Figure 3). The server begins the background real-time service program and provides an external connection interface. After the client starts, it establishes a connection with the server through a transmission control protocol. After the user verification is passed, the real-time data are read from the real-time database to the local. When the server has new data, it requests real-time data from the server. The control operation triggered by the client is written into the control data table after verification authority of the server is passed. The server starts the background history service program, provides an external connection interface, and receives historical data reported by the intelligent decision-making system. The communication module of the intelligent decision-making system establishes a message queue to store the status messages sent to the server. The background thread is started, and the real-time data in the local database are periodically scanned and uploaded to the server. Owing to the real-time requirements of the system, this thread has the highest priority. The message returned by the server indicates whether there is currently a control command. If there is a thread, the operation triggered by the client is sent to the scheduling system, and the execution result of the scheduling module is stored in the message queue. The intelligent decision-making system establishes a historical data reporting thread, connects to the historical service, regularly checks whether the historical data is consistent with that in the local database, and synchronises the local historical data to the cloud server when inconsistent. Owing to the large amount of historical data and low real-time requirements, the priority of this thread is lower than that of the real-time library thread.
Data storage
TBM construction data have the characteristics of spatiality, real-time, multi-source heterogeneity, and massiveness. It is difficult for a single relational database to satisfy the aforementioned data storage requirements, and it is necessary to build a more scientific and efficient integrated data storage system. As shown in Figure 3, the database at the management level integrates multiple types of databases, such as the relational database MySQL, non-relational database MongoDB, cache database Redis, and distributed file storage system HDFS (Yu et al., 2018). It achieves efficient storage and retrieval of data through data-adaptive storage. The semi-relational database MongoDB is responsible for storing two types of data: semi-structured and unstructured data. It is specifically used to store PLC data, file storage directories, user behaviour logs, geological data, and advanced geological exploration information of the TBM equipment. The distributed memory database Redis is responsible for storing application scenario data such as cache and highly read/write, mainly including TBM construction monitoring data, cache data, and cloud service module data to provide remote monitoring related data support. The distributed HDFS database is used for massive data storage and is responsible for storing large file data (e.g., TBM excavation process data, compressed files, and videos). The relational database MySQL is mainly used to store structured data, which is responsible for storing user registration information, TBM failure and maintenance data, expert information, and highly sensitive and secure data.
Intelligent decision-making system
Data preprocessing
By analysing the tunnelling data, a complete TBM tunnelling cycle can be divided into empty push, ascending, and stable sections. These include valid and abnormal data, as well as that of certain special tunnelling states (downtime section data). These data have a negative impact on the model establishment of the TBM intelligent decision-making system. Hence, to obtain accurate and effective input data, reduce the influence of interference samples, and dig deep into the excavation data with high quality, it is necessary to use feature engineering methods to preprocess existing data, filter abnormal data, and extract the main features. This lays the foundation for the subsequent construction and training of data-driven intelligent decision-making models using engineering data.
As shown in Figure 4, the preprocessing of tunnelling data includes constructing datasets, parameter dimensionality reduction, extracting tunnelling parameters, special value processing, outlier value processing, and standardisation processing. The data include stake number information, geological condition information, and TBM tunnelling parameter data, such as the propulsion speed, cutterhead torque, and cutterhead power. Meanwhile, the geological data are divided according to the range of the stake number, and each stake number corresponds to a set of geological parameters. Thus, the construction method of the dataset matches the geological data with the TBM tunnelling parameters through the stake number. Through parameter dimensionality reduction, the prediction error and learning cost caused by redundant information are reduced, essential structural features are found, and data visualisation is facilitated. Based on previous studies (Hou et al., 2020; Zhang et al., 2022b), the Pearson correlation analysis was used to identify the 100- and 99-dimensional input parameters of the decision-making model. Based on the identification results, the key parameters with a high correlation with the predicted parameters were extracted from the tunnelling parameters of the complete tunnelling cycle as the model input. Owing to the large amount of tunnelling data in the shutdown section and the useless data of the special tunnelling state, the method of constructing a binary state discriminant function (Zhang et al., 2022b) is used to eliminate the tunnelling data in the shutdown section. The discriminant function is expressed as follows:
where
Outliers in the TBM tunnelling data were corrected using the triple standard deviation method (Zhou et al., 2020). Traditional studies regarding TBM tunnelling parameter prediction (Hou et al., 2020) generally use the data of the ascending section to predict the parameters of the stable section. However, this requires a significant amount of time to efficiently identify and extract the data of the ascending section and cannot fully reflect the geological information. Therefore, in the standardisation processing stage, the complete tunnelling cycle data are selected to predict the TBM tunnelling parameters to effectively reduce the data processing time and reflect the complex geological conditions in the tunnelling process. Considering the tunnelling data of a certain day as an example, the TBM tunnelling data after abnormal value processing are first read, and each piece of data is judged based on the cutterhead torque. The first data with non-zero cutterhead torque are recorded as P1. The next data are read line-by-line and the second data with zero cutterhead torque is determined and recorded as P2. It is then determined whether the data between P1 and P2 are between 500 and 5,000 s. If it is not within this range of time, the section of data is discarded; if it is within the range, the P1 and P2 data are output to the specified file, and a model file is generated until all the data is extracted.
Intelligent decision-making method driven by physics and data
According to previous studies (Zhang et al., 2022a; Zhang et al., 2022b), six key parameters were selected for the optimisation of decision-making: the cutterhead speed, cutterhead torque, cutterhead power, penetration, propulsion speed, and total propulsion force. Most of these parameters describe the relationship between them through the rock-mechanical interaction model. The internationally recognised theoretical model CSM (Liu et al., 2016) is selected to illustrate the relationship between the aforementioned six parameters:
where
The relationship between the cutterhead speed
The equation above indicates that the control of the six key parameters above can be directly or indirectly achieved only by controlling the cutterhead and propulsion speeds. Accordingly, the cutterhead and propulsion speeds can be selected as the main tunnelling control parameters for decision-making control. To improve the main performance indicators (e.g., the tunnelling efficiency, energy consumption, and cost), the laws of large-sample historical data and the physical and mechanical characteristics of TBM tunnelling can be comprehensively considered to clearly construct a mapping relationship model with the performance indicators and optimise the objective function. Thus, optimal decision-making can be achieved to principally improve the scientific features and reliability. Based on the aforementioned understanding and previous research (Zhang Y. K. et al., 2022; Ma et al., 2022), this paper proposes an intelligent decision-making method for TBM tunnelling parameters based on physical laws and data mining; that is, the optimal decision-making method of the particle swarm optimisation (PSO) algorithm for the minimum decision-making of tunnelling specific energy. Multivariate information that affects the TBM tunnelling performance is introduced, such as the parameters including the lithology and cutterhead vibration signals, and a TBM rock-machine mapping model is constructed by studying the rock-breaking laws and large-sample data mining. Subsequently, the main control parameters are used as constraints (e.g., the cutterhead and propulsion speeds), and the minimum specific energy of tunnelling is aimed for to achieve optimisation and decision-making.
The TBM energy consumption is a critical parameter in the process of TBM excavation, which determines the direct cost of the project (Yang et al., 2021). Reducing the TBM energy consumption during long-distance tunnel excavation is extremely significant for reducing engineering costs. The TBM energy consumption is usually described by the tunnelling specific energy
Here,
Substituting Eqs 9, 10 into Eq. 8, the specific energy decision function of TBM tunnelling can be constructed as follows:
The PSO algorithm is introduced, and the decision function represented by Eq. 11 is used as the fitness function. When the specific energy
The PSO and tunnelling parameter prediction models are combined to obtain the tunnelling specific energy as the fitness function, minimum specific energy as the decision-making strategy, and propulsion and cutterhead speeds as the optimisation goals. The process of the PSO algorithm optimisation decision-making method for the minimum tunnelling specific energy is shown in Figure 5. Here,
Real-time control system
Real-time control system
Based on the comprehensive perception system, the real-time control system adopts the mode of ‘centralized management, centralized monitoring, and decentralized control’ to achieve the interaction and control of information. The field equipment layer executes the control commands of the TBM operator or remote manager, drives the TBM subsystem and its auxiliary equipment to perform various actions, and feeds back the real-time status information to the field monitoring layer. The field monitoring layer monitors the running status of the TBM subsystem and its auxiliary equipment and interacts with the remote management layer to control the commands and related data. The remote management layer allows remote users to monitor on-site tunnelling operations in real time and remotely control the TBM. As shown in Figure 2, the TBM host system and auxiliary equipment, as well as the TBM rear supporting system, use a large PLC as the control core to complete the electrical control tasks; the PLCs communicate through the network communication interface. Other relatively independent supporting equipment use a small PLC to complete the control tasks of the actuators of each independent supporting equipment, connect with the field bus through the network communication interface, and exchange data with the field monitoring layer through the data conversion interface.
Composite intelligent control strategy
TBM composite intelligent control strategies include multimodal control strategies for conventional geological sections and expert experience learning control strategies for unfavourable geological sections (Figure 6). Considering that there are differences in the excavation goals of TBM construction under different geological conditions, the method of using the same control strategy in different working conditions cannot meet the diverse needs of working conditions (Zhang and Ma, 2018; Liu W L et al., 2022). This study adopts multimodal control ideas and expert experience to solve the problem. The basic method of multi-mode control in conventional geological sections is to divide the complex working conditions into several sub-intervals according to different lithology or surrounding rock grades and then establish a local mathematical model in each sub-interval. The internal logic is expressed as follows:
where
Combined with the rock mass parameter prediction model (Zhang and ma, 2018) and the clustering classification method (Yu et al., 2018) constructed by the multivariate algorithm fusion constructed in a previous study, the multi-modal control strategy selects the appropriate physical and data dual-drive intelligent decision-making model. With the conversion between different decision-making models, the tunnelling parameters are adaptively determined; the most suitable control strategy is selected according to different working conditions, and the advantages of various control strategies are introduced. The controller controls the TBM subsystem to execute the excavation action according to the tunnelling parameters to enable the control performance of the intelligent tunnelling robot system in the conventional stratum to meet the diverse requirements of the working conditions.
Combined with previous research (Zhang and Ma, 2018), the control method of unfavourable geological sections adopts the expert experience control strategy. That is, the excavation tasks of unfavourable geological excavation sections are mainly completed according to the experience of TBM operators.
Support is provided according to the suggestions given by the system. The tunnelling is started after the excavation operation conditions are satisfied, the cutterhead is started under the mode of the escape torque, and the speed is slowly increased to the given speed. If the torque is near 80% of the maximum value or the slag output of the belt is in line with the expectations, then tunnelling is proceeded at these cutterhead and propulsion speeds; otherwise, adjustments are made. If the further measured torque value is stable, the speed can be slowly increased to a certain extent. If the measured torque value significantly fluctuates or exceeds the limit value, the tunnelling speed will be reduced, and the tunnelling operation will be conducted after the torque is stabilised after adjustment. The transitional section between conventional and unfavourable geological sections (i.e., when the surrounding rock quality transitions from good to poor) remains to be controlled according to expert experience. First, the propulsion speed is stopped, and the speed is reduced to keep the slag out. After the torque is stable, the propulsion speed is slowly increased while observing the change in the torque value. If the torque value fluctuates within the set range, it can be regarded as a stable state. After waiting for it to stabilise after a certain period of time, it continues to increase to the original set value state for the tunnelling operations.
Engineering cases
To construct and verify the effectiveness of the comprehensive perception and adaptive decision-making functions, this study chose the TBM3 bidding section of the Water Supply Project in the Central City of Jilin Province as an engineering case. The total length of the bidding section is 17.488 km, and the buried depth is 85–260 m. The data of this project not only include the TBM tunnelling parameters but also the preliminary survey and advanced geological exploration information.
Moreover, to verify the effectiveness of the entire intelligent tunnelling robot system developed, especially the composite intelligent control function, the Water Diversion Project in Xinjiang Province was selected as another engineering case. This is a pressure-free tunnel. A circular section is constructed using the TBM method. Considering the TBM2 tender section as one of the engineering examples, it has a stake number of 24 + 740∼44 + 687 m and a total length of 19.947 km. According to this example, the perception, decision-making, and control functions, especially the real-time control system, can be tested and verified.
System implementation and verification
The intelligent tunnelling robot system mainly includes functional modules such as geological forecasts, geological profiles, intelligent TBM tunnelling parameters, intelligent support, and remote monitoring (Figure 7). The main interface of the robot system summarises the common information of the rock mass, equipment, support, intelligent decision-making, remote monitoring, and real-time control, assisting operators in making scientific decisions and ensuring a safe and efficient TBM construction. The geological perception unit and intelligent support composed of the geological forecast and geological section are the mapping of the geological state. Geological prediction is a module that displays the results of an advanced geological exploration system. The two functional modules of the geological perception unit and intelligent support provide strong support for an experienced control of unfavourable geological sections. The TBM state perception unit is built into the remote monitoring module, which maps the equipment state. The intelligent tunnelling parameters achieve dual-driven and independent decision-making of the tunnelling parameters and the composite intelligent control function of tunnelling with the remote monitoring module. The remote monitoring module includes two functions: TBM equipment information perception and monitoring and TBM control.
The geological perception unit is composed of a geological section and geological forecast (Figure 7). The geological profile is digitally imported into the preliminary engineering geological survey report, and the geological profile information of the current excavation section and the entire excavation project is dynamically and intuitively displayed. The current digging position of the tunnel face can be displayed in real time. Geological prediction is divided into conventional and unfavourable geological segments. The geological forecast of the conventional geological section presents the real-time perception of the state of the rock mass at the face and the statistical information regarding lithology; the unfavourable geological section presents the advanced detection information of unfavourable geological conditions, such as a rockburst and water inrush (Figures 7, 8). The system obtains the forecast information data provided by the advanced exploration system of adverse geology through the interface in real time, displays adverse geological conditions graphically and intuitively in real time, and provides comprehensive evaluation and corresponding support suggestions accordingly.
The intelligent decision-making module senses the tunnelling information in real time, optimises the decision-making tunnelling parameters according to the geological conditions, and provides the optimal tunnelling parameters for a compound intelligent control and automatic tunnelling. Details regarding the intelligent decision-making module are shown in Figure 9. The left side of the figure presents a comparison curve between the real-time perception value of the tunnelling parameters and the optimised decision-making value. The table on the right side presents the optimal recommended values, decision algorithm library, optimisation algorithm, whether it is self-adaptive, and the monitoring diagnosis and suggestions for the surrounding rock. The monitoring, diagnosis, and suggestions of the surrounding rock enable the statistical analysis of events such as rockbursts, water gushes, and fault fracture zones that occur in unfavourable geological sections. If the self-adaptive function is checked, the intelligent decision-making module can adapt to different rock mass states based on the proposed optimal decision-making method and provide the optimal tunnelling parameters. If the PSO algorithm option is checked, the original eight decision-making algorithms can be optimised by particle swarm optimization. Table 1 presents a comparison of the accuracy of intelligent decision-making algorithms for the different rock mass states and the optimal tunnelling parameters with the minimum specific energy. Under the granite IV deviation at stake number 52,047.125, the tunnelling specific energy corresponding to the PSO-GRU decision-making algorithm is 1,422.2 kJ/m3, which is the smallest specific energy compared to the other seven algorithms. The tunnelling parameters predicted by it are optimal. Under the granite IV preference at stake number 51,998.980, the tunnelling specific energy corresponding to the PSO-GRU decision-making algorithm is 2,115.8 kJ/m3, the tunnelling specific energy is the smallest, and the tunnelling parameters predicted by it are optimal. Under granite IIIb at stake number 51,987.859, the tunnelling specific energy corresponding to the PSO-RNN decision-making algorithm is 1,441.1 kJ/m3, the tunnelling specific energy is the smallest, and the tunnelling parameters predicted by it are optimal.
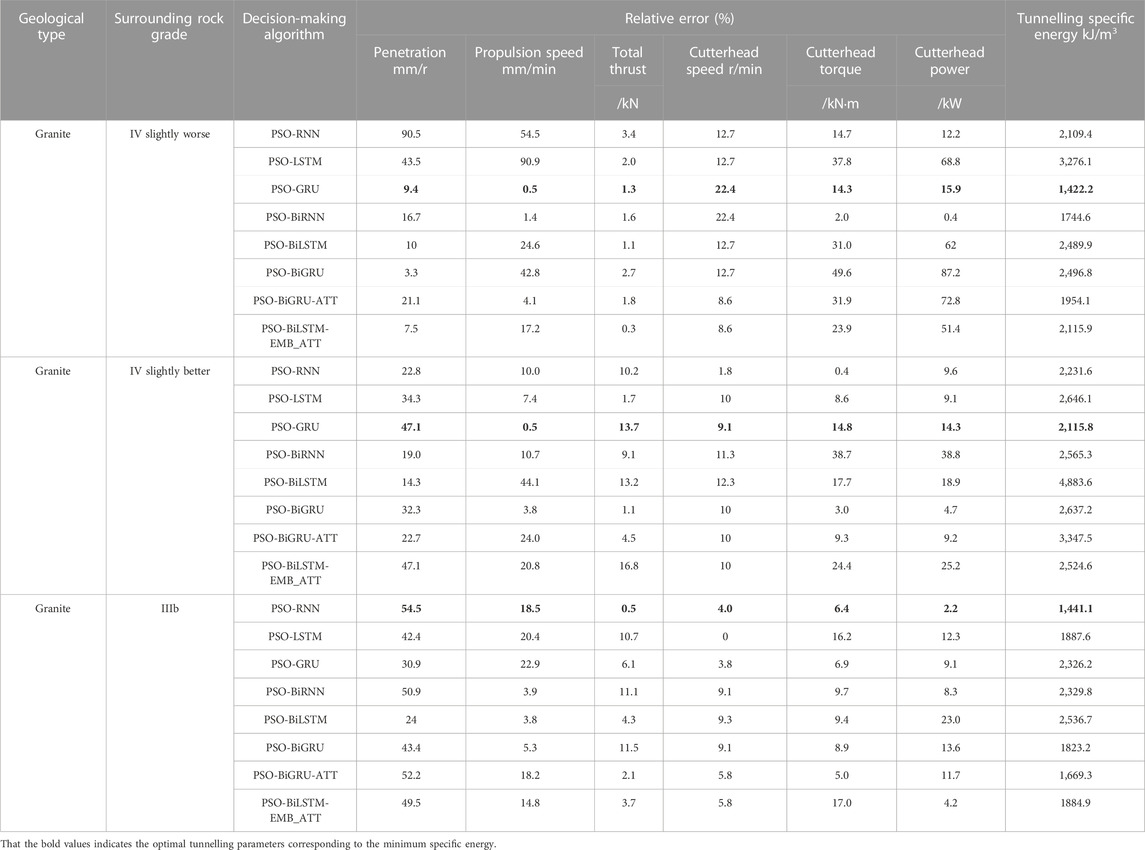
TABLE 1. Comparison of the accuracy of intelligent decision-making algorithms in different rock mass states and the optimal tunnelling parameters with the minimum specific energy.
The remote monitoring module mainly includes the main monitoring page, parameter setting, and cutterhead drive; the TBM status sensing unit is built into the remote monitoring module. The main monitoring page, including the remote-control function, is shown in Figure 10. The main monitoring page not only monitors the core components, such as the TBM top shield, right shield, right shoe, left shield, left shoe, cutterhead, propulsion system, oil cylinder, left and right rear supports, and main beam in real time but also the footage data in real time. The parameter setting includes the temperature warning value, grease frequency, speed, oil pressure, penetration warning, mileage, and other TBM equipment status parameters, as well as the tunnelling target parameters, in addition to adjusting the saddle frame. The cutter head drive monitors key parameters such as the motor current and torque of the cutter head drive system, in addition to the interlocking conditions and running time of the cutter head drive. As shown in the red box in Figure 10, remote control can be achieved through the ‘upper computer + lower computer’ mode.
Any control system with a decision-making algorithm must undergo several experimental tests, verifications, and assessments (Ge et al., 2022). However, the heavy excavation tasks, complex and changeable geological conditions, and extremely high safety requirements of deep-buried long tunnels make it difficult to systematically conduct the testing, verification, and improvement of the control system with a decision-making algorithm. Currently, the method testing cost, especially the safety risk, is significantly high owing to the many actual excavation inspections and perfect methods. Furthermore, the tunnel ceased to exist after excavation, and the improved control algorithm could not obtain the same test conditions again, resulting in a failure to verify the system improvement effect. Therefore, the decision-making level is faced with major technical problems, including the control algorithm completeness, robustness testing, and continuous improvement and upgrading. Therefore, this study first relies on the Water Supply Project in the Central City of the Jilin Province to build an intelligent tunnelling robot system. The preliminary verification of its perception, decision-making, and control functions is conducted. Thereafter, a small number of on-site excavation tests of the water diversion project in the Xinjiang Province were used to verify the real-time control function.
A statistical analysis was conducted on the data of the cutterhead and propulsion speeds, the results of which are shown in Figures 11, 12; Table 2. The relative error between the measured and set values of the cutterhead speed of the biotite schist is small, and the average relative error under the condition of surrounding rock IIIb is slightly higher than that of surrounding rock IV. The relative error between the measured and set values of the cutterhead speed under the condition of the granite porphyry-surrounding rock grade II is higher than that under the condition of the surrounding rock grade IV. The relative error between the measured and set values of the cutterhead speed of the granite porphyry was generally higher than that of the biotite quartz schist. Compared to the cutterhead speed, the relative error between the measured and set values of the propulsion speed of the biotite quartz schist and granite porphyry was significantly larger; the relative error was higher under the granite porphyry than that of the biotite quartz schist. By comparison, it was found that the relative error between the measured and set values of the propulsion speed was an order of magnitude higher than that of the cutterhead speed, and the relative error was relatively large. The results demonstrate that the control accuracy of the cutterhead speed is higher, and the effect of precise control is apparently better than that of the propulsion speed.
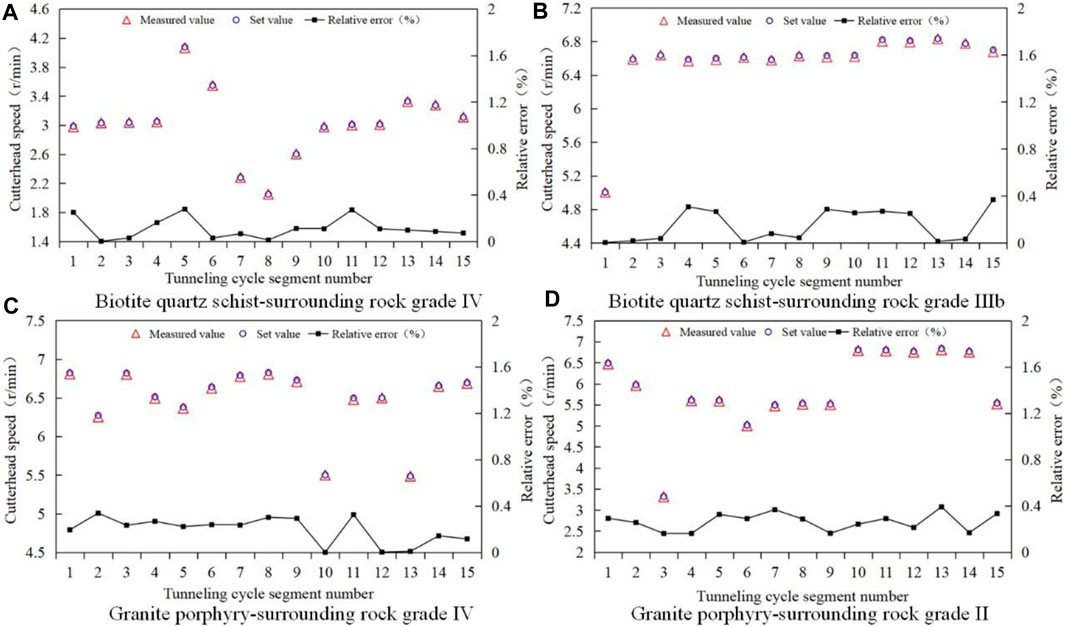
FIGURE 11. Comparison between the measured and set values of the cutterhead speed. (A) Biotite quartz schist-surrounding rock grade IV; (B) Biotite quartz schist-surrounding rock grade IIIb; (C) Granite porphyry-surrounding rock grade IV; (D) Granite porphyry-surrounding rock grade II.
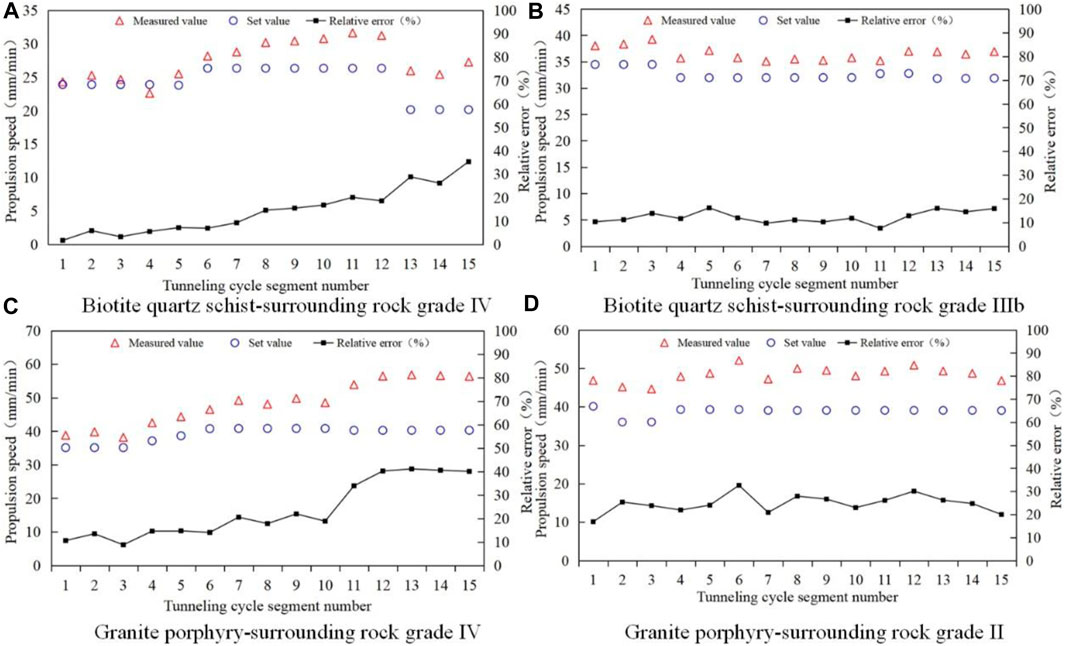
FIGURE 12. Comparison between the measured and set values of the propulsion speed. (A) Biotite quartz schist-surrounding rock grade IV; (B) Biotite quartz schist-surrounding rock grade IIIb; (C) Granite porphyry-surrounding rock grade IV; (D) Granite porphyry-surrounding rock grade II.
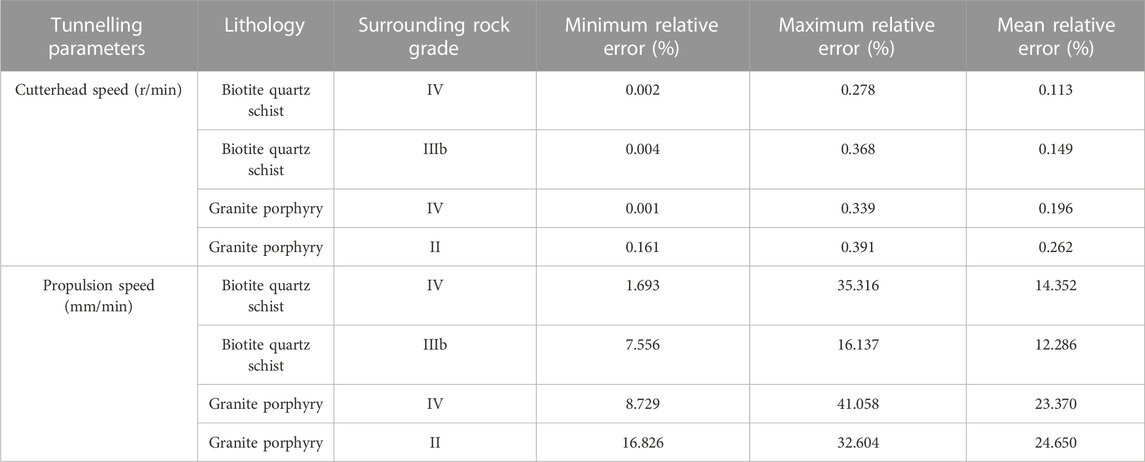
TABLE 2. Relative error between the measured and set values of the tunnelling parameters under different lithology and surrounding rock grades.
Conclusion
Based on the closed-loop intelligent control concept of ‘perception-decision-control’, an intelligent tunnelling robot system was developed, verified by different projects. The following results were obtained.
(1) The multi-source information comprehensive perception and integrated management platform of a fieldbus is constructed; an integrated data storage system is formed based on the non-relational database MongoDB, combined with MySQL, Redis, HDFS, and other systems. This can effectively solve the problem of a seamless integration between the basic automation control network and the process and management control system, improve the timeliness of perceptual information transmission, enable the storage system to meet the application requirements, and achieve a comprehensive perception of TBM tunnelling information.
(2) The optimal decision-making method of the PSO algorithm for minimum tunnelling specific energy that satisfies the complete tunnelling cycle data and adaptive rock mass state is proposed; subsequently a TBM intelligent decision-making system driven by physical laws and data mining is constructed. This can effectively improve the timeliness of intelligent decision-making, solve the problem of poor matching between the tunnelling and rock mass state parameters, and achieve the dual-driven decision-making of tunnelling parameters.
(3) A multimodal and expert-experience composite intelligent control strategy is designed for diverse working conditions. The verification results of the decision-making algorithm of the control system demonstrate that the average relative error between the measured and set values of the cutterhead speed is between 0.1113% and 0.262%. The average relative error between the measured and set values of the propulsion speed is between 14.352% and 24.650%, which can meet the safe and efficient construction requirements of TBM under complex geological conditions.
(4) An intelligent tunnelling robot system with closed-loop intelligent control functions of ‘comprehensive perception, dual-driven decision-making, and composite intelligent control’ that can be deployed across platforms has been developed. Its effectiveness and reliability were verified through engineering cases. This provides new technical means for the construction of deep-buried long tunnels, especially for the less-manned, unmanned, and intelligent excavation construction of TBM in high-cold areas. Moreover, it can be extended and applied to other types of tunnel engineering and has a certain universality. Further research is required to improve the performance of the intelligent tunnelling robot system to meet the construction requirements of an uncertain environment and to incorporate more factors for intelligent decision-making (e.g., the equipment condition management, maintenance, and spare parts receipt).
Data availability statement
The original contributions presented in the study are included in the article/supplementary material, further inquiries can be directed to the corresponding author.
Author contributions
All authors listed have made a substantial, direct, and intellectual contribution to the work and approved it for publication.
Funding
Fundamental Research Funds for the Central Universities (Project No: FRF-TP-20-043A1), and Open Research Fund Program of the State Key Laboratory of Hydroscience and Engineering (Project No: sklhse-2021-C-04) are gratefully acknowledged.
Conflict of interest
Authors YoZ and LJ were employed by the company China Railway Engineering Equipment Group Co., Ltd. Authors SD and KS were employed by HUANENG Tibet Hydropower Safety Engineering Technology Research Center.
The remaining authors declare that the research was conducted in the absence of any commercial or financial relationships that could be construed as a potential conflict of interest.
The authors declare that this study received funding from the Science and Technology Project of Huaneng Group Headquarters (Project No: HNKJ19-H15). The funder had the following involvement in the study: data collection and decision to publish.
Publisher’s note
All claims expressed in this article are solely those of the authors and do not necessarily represent those of their affiliated organizations, or those of the publisher, the editors and the reviewers. Any product that may be evaluated in this article, or claim that may be made by its manufacturer, is not guaranteed or endorsed by the publisher.
References
Allo, O. J., Ayolabi, E. A., Adeoti, L., Akinmosin, A., and Oladele, S. (2022). Reservoir characterization for hydrocarbon detection using amplitude variation with angles constrained by localized rock physics template. J. Afr. Earth. Sci. 192, 104548. doi:10.1016/j.jafrearsci.2022.104548
Armaghani, D. J., Mohamad, E. T., Narayanasamy, M. S., Narita, N., and Yagiz, S. (2017). Development of hybrid intelligent models for predicting TBM penetration rate in hard rock condition. Tunn. Undergr. Sp. Tech. 63, 29–43. doi:10.1016/j.tust.2016.12.009
Armetti, G., Migliazza, M. R., Ferrari, F., Berti, A., and Padovese, P. (2018). Geological and mechanical rock mass conditions for TBM performance prediction. The case of “La Maddalena” exploratory tunnel, Chiomonte (Italy). Tunn. Undergr. Sp. Tech. 77, 115–126. doi:10.1016/j.tust.2018.02.012
Ba, E. V. N., Noble, M., Gelis, C., Cabrera, J., and Gesret, A. (2020). Potential of surface-to-tunnel seismic tomography to detect vertical faults: Application to the tournemire underground research laboratory, France. Pure Appl. Geophys. 177, 4143–4159. doi:10.1007/s00024-020-02505-0
Dastanboo, N., Li, X. Q., and Gharibdoost, H. (2020). Comparison between electrical resistivity tomography and tunnel seismic prediction 303 methods for detecting the water zone ahead of the tunnel face: A case study. Open. Geosci. 12, 1094–1104. doi:10.1515/geo-2020-0193
Deng, M. J. (2018). Challenges and thoughts on risk management and control for the group construction of a super-long tunnel by TBM. Engineering 4, 112–122. doi:10.1016/j.eng.2017.07.001
Du, C. L., Pan, Y. C., Liu, Q. S., Huang, X., and Yin, X. (2022). Rockburst inoculation process at different structural planes and microseismic warning technology: A case study. B. Eng. Geol. Environ. 81 (499), 499–518. doi:10.1007/s10064-022-02980-w
Farrokh, E., Rostami, J., and Laughton, C. (2011). Analysis of unit supporting time and support installation time for open TBMs. Rock. Mech. Rock. Eng. 44 (4), 431–445. doi:10.1007/s00603-011-0135-8
Garcia, G. R., Michau, G., Einstein, H. H., and Fink, O. (2021). Decision support system for an intelligent operator of utility tunnel boring machines. Autom. Constr. 131, 103880. doi:10.1016/j.autcon.2021.103880
Ge, S. R., Wang, S. B., Guan, Z. H., Wang, X. S., An, W. L., Lyu, Y. B., et al. (2022). Digital twin: Meeting the technical challenges of intelligent fully mechanized working face. J. Mine Automation 48 (7), 1–12. doi:10.13272/j.issn.1671-251x.17959
Gong, Q. M., Zhou, X. X., Liu, Y. Q., Liu, Y. Q., Han, B., and Yin, L. J. (2021). Development of a real-time muck analysis system for assistant intelligence TBM tunnelling. Tunn. Undergr. Sp. Tech. 107, 103655. doi:10.1016/j.tust.2020.103655
Goshtasbi, K., Monjezi, M., and Tourgoli, P. (2009). Evaluation of boring machine performance with special reference to geomechanical characteristics. Int. J. Min. Mater. Mat. 16 (6), 615–619. doi:10.1016/S1674-4799(10)60001-5
Harandizadeh, H., Armaghani, D. J., Asteris, P. G., and Gandomi, A. H. (2021). TBM performance prediction developing a hybrid ANFIS-PNN predictive model optimized by imperialism competitive algorithm. Neural. comput. Appl. 33, 16149–16179. doi:10.1007/s00521-021-06217-x
Hassanpour, J., Rostami, J., and Zhao, J. (2011). A new hard rock TBM performance prediction model for project planning. Tunn. Undergr. Sp. Tech. 26 (5), 595–603. doi:10.1016/j.tust.2011.04.004
Hassanpour, J., Vanani, A. A. G., Rostami, J., and Cheshomi, A. (2016). Evaluation of common TBM performance prediction models based on field data from the second lot of Zagros water conveyance tunnel (ZWCT2). Tunn. Undergr. Sp. Tech. 52, 147–156. doi:10.1016/j.tust.2015.12.006
Hou, S. K., Liu, Y. R., and Zhang, K. (2020). Prediction of TBM tunneling parameters based on IPSO-BP hybrid model. Chin. J. Rock Mech. Eng. 39 (8), 1648–1657. doi:10.13722/j.cnki.jrme.2019.1084
Huang, Z., Xu, Y. Q., Du, W. Y., Cheng, E. J., Yan, Q. D., and Shen, X. L. (2022). A noncontact cutterhead dynamic coordinate measurement method for double-shield TBM guidance based on photographic imaging. Ieee. Trans. Instrum. Meas. 71, 1–16. doi:10.1109/TIM.2021.3128688
Kampas, G., Knappett, J. A., Brown, M. J., Anastasopoulos, I., Nikitas, N., and Fuentes, R. (2020). Implications of volume loss on the seismic response of tunnels in coarse-grained soils. Tunn. Undergr. Sp. Tech. 95, 103127. doi:10.1016/j.tust.2019.103127
Li, G., Yu, T. B., Fei, X. T., and Wang, W. S. (2012). A method to predict cutterhead specific energy for TBM based on CSM model. J. Northeast. Univ. Nat. Sci. 33 (12), 103097–111769.
Li, J. B., Jing, L. J., Zheng, X. F., Li, P. Y., and Yang, C. (2019). Application and outlook of information and intelligence technology for safe and efficient TBM construction. Tunn. Undergr. Sp. Tech. 93, 103097. doi:10.1016/j.tust.2019.103097
Li, Q. B., Ma, R., Hu, Y., Huangfu, Z. H., Shen, Y. Y., Zhou, S. W., et al. (2022a). A review of intelligent dam construction techniques. J. Tsinghua. Univ (Sci Technol). 62 (8), 1252–1269. doi:10.16511/j.cnki.qhdxxb.2022.25.018
Li, Q. B., Ma, R., Hu, Y., Huangfu, Z. H., Shen, Y. Y., Zhou, S. W., et al. (2022b). Theory of intelligent dam construction. J. Hydroel. Eng. 41 (1), 1–13. doi:10.11660/slfdxb.20220101
Li, S. C., Bu, L., Shi, S. S., Li, L. P., and Zhou, Z. Q. (2022). Prediction for water inrush disaster source and CFD-based design of evacuation routes in Karst tunnel. Int. J. Geomech. 22 (5), 05022001. doi:10.1061/(ASCE)GM.1943-5622.0002305
Li, S. C., Liu, B., Sun, H. F., Nie, L. C., Zhong, S. H., Su, M. X., et al. (2014). State of art and trends of advanced geological prediction in tunnel construction. Chin. J. Rock Mech. Eng. 33 (6), 1090–1113. doi:10.13722/j.cnki.jrme.2014.06.003
Liu, B., Wang, Y. X., Zhao, G. Z., Yang, B., Wang, R. R., Huang, D. X., et al. (2021). Intelligent decision method for main control parameters of tunnel boring machine based on multi-objective optimization of excavation efficiency and cost. Tunn. Undergr. Sp. Tech. 116, 104054. doi:10.1016/j.tust.2021.104054
Liu, Q. S., Liu, J. P., Pan, Y. C., Kong, X. X., Cui, X. Z., Huang, S. B., et al. (2016). Research advances of tunnel boring machine performance prediction models for hard rock. Chin. J. Rock Mech. Eng. 35 (1), 2766–2786. doi:10.13722/j.cnki.jrme.2014.1601
Liu, W. L., Li, A., and Liu, C. J. (2022). Multi-objective optimization control for tunnel boring machine performance improvement under uncertainty. Autom. Contr. 139, 104310. doi:10.1016/j.autcon.2022.104310
Liu, Y. R., Hou, S. K., Cheng, L., and Huang, Y. Q. (2022). Advances and key technologies of intelligent construction of hydraulic engineering. Water Resour. Hydropower Eng. 53 (10), 1–20. doi:10.13928/j.cnki.wrahe.2022.10.001
Liu Z B, Z. B., Li, Long., Fang, X. L., Qi, W. B., Shen, J. M., Zhou, H. Y., et al. (2021). Hard-rock tunnel lithology prediction with TBM construction big data using a global-attention-mechanism-based LSTM network. Autom. Constr. 125, 103647. doi:10.1016/j.autcon.2021.103647
Ma, R., Yin, T., Li, H. X., Zhang, F. Q., Hu, Y., and Li, Q. B. (2022). Basic structure and characteristics of dam mechanism-data-driven fusion models. J. Hydr. Eng. 41 (5), 59–74. doi:10.11660/slfdxb.20220507
Mahdevari, S., Shahriar, K., Yagiz, S., and Akbarpour, S. M. (2014). A support vector regression model for predicting tunnel boring machine penetration rates. Int. J. Rock Mech. Min. Sci. 72, 214–229. doi:10.1016/j.ijrmms.2014.09.012
Mahdevari, S., and Torabi, S. R. (2012). Prediction of tunnel convergence using artificial neural networks. Tunn. Undergr. Sp. Tech. 28, 218–228. doi:10.1016/j.tust.2011.11.002
Mahmoodzadeh, A., Mohammadi, M., Ibrahim, H. H., Abdulhamid, S. N., Ali, H. F. H., Hasan, A. M., et al. (2021). Machine learning forecasting models of disc cutters life of tunnel boring machine. Autom. Const. 128, 103779. doi:10.1016/j.autcon.2021.103779
Marcher, T., Erharter, G., and Unterlass, P. (2022). “Capabilities and challenges using machine learning in tunnelling,” in Theory and Practice on Tunnel Engineering (IntechOpen), 1–15. doi:10.5772/intechopen.97695
Meschke, G., Nagel, F., and Stascheit, J. (2011). Computational simulation of mechanized tunneling as part of an integrated decision support platform. Int. J. Geomech. 11 (6), 519–528. doi:10.1061/(ASCE)GM.1943-5622.0000044
Nikakhtar, L., Zare, S., and Nasirabad, H. M. (2022). Intelligent identification of soil and operation parameters in mechanised tunnelling by a hybrid model of artificial neural network-genetic algorithm (case study: Tabriz Metro Line 2). Civ. Eng. Environ. Syst. 39 (4), 287–308. doi:10.1080/10286608.2022.2075857
Pan, Y. C., Liu, Q. S., Liu, Q., Bo, Y., Liu, J. P., Peng, X. X., et al. (2021). Comparison and correlation between the laboratory, semi-theoretical and empirical methods in predicting the field excavation performance of tunnel boring machine (TBM). Acta. Geotech. 17 (2), 653–676. doi:10.1007/s11440-021-01228-3
Pan, Y., Fu, X. L., and Zhang, L. M. (2022). Data-driven multi-output prediction for TBM performance during tunnel excavation: An attention-based graph convolutional network approach. Autom. Constr. 141, 104386. doi:10.1016/j.autcon.2022.104386
Qiao, S. F., Xu, P., Liu, R. T., and Wang, G. (2020). Study on the horizontal axis deviation of a small radius TBM tunnel based on winkler foundation model. Appl. Sci. 10 (3), 784. doi:10.3390/app10030784
Santos, A. E. M., Lana, M. S., and Pereira, T. M. (2021). Rock mass classification by multivariate statistical techniques and artificial intelligence. Geotech. Geol. Eng. 39 (3), 2409–2430. doi:10.1007/s10706-020-01635-5
Sun, H. T., Liu, D. Y., Huang, S. S., and Yang, T. B. (2007). Study of intelligent method on the tunnel supporting time. Int. J. Environ. Eng. 29 (3), 78–82. doi:10.11835/j.issn.1674-4764.2007.03.019
Sun, Y. T., Li, G. C., Zhang, J. F., and Huang, J. D. (2021). Rockburst intensity evaluation by a novel systematic and evolved approach: Machine learning booster and application. B. Eng. Geol. Environ. 80, 8385–8395. doi:10.1007/s10064-021-02460-7
Xu, C., Liu, X. L., Wang, E. Z., and Wang, S. J. (2021). Prediction of tunnel boring machine operating parameters using various machine learning algorithms. Tunn. Undergr. Sp. Tech. 109, 103699. doi:10.1016/j.tust.2020.103699
Yang, J. H., Guo, W. X., Yan, C. B., and Miao, D. (2021). Study on optimization of TBM driving parameters based on the energy consumption. Mod. Tunn. Technol. 58 (1), 54–60. doi:10.13807/j.cnki.mtt.2021.01.007
Yu, T. Z., Li, J. B., Jing, L. J., Xu, S. T., and Xu, J. A. (2018). Design and practice of cloud computing platform for TBM operation information. Mod. Tunn. Technol. 55 (6), 33–41. doi:10.13807/j.cnki.mtt.2018.06.005
Yu, Y., Feng, X. T., Chen, B. R., Xiao, Y. X., and Feng, G. L. (2017). Fractal characteristics of micro-seismic volume for different types of immediate rock-bursts in deep tunnels. Acta. Geotech. 39 (12), 2173–2179. doi:10.11779/CJGE201712004
Zhang, Q. L., Zhu, Y. W., Ma, R., Du, C. X., Du, S. L., Shao, K., et al. (2022a). Prediction method of TBM tunneling parameters based on PSO-Bi-LSTM model. Front. Earth. Sc-Switz. 10, 854807. doi:10.3389/feart.2022.854807
Zhang, Q. L., Zhu, Y. W., Ma, R., Yan, D., Yang, C. G., Cui, T. H., et al. (2022b). Prediction method of TBM tunneling parameters based on Bi-GRU-ATT model. Mod. Tunn. Technol. 59 (4), 1–16. doi:10.1155/2022/3743472
Zhang, Y. K., Gong, G. F., Yang, H. Y., Chen, Y. X., and Chen, G. L. (2022c). Towards autonomous and optimal excavation of shield machine: A deep reinforcement learning-based approach. J. Zhejiang University-SCIENCE A Appl. Phys. Eng. 23 (6), 458–478. doi:10.1631/jzus.A2100325
Zhang, Z. H., and Ma, L. H. (2018). Attitude correction system and cooperative control of tunnel boring machine. Int. J. Pattern. Recogn. 32 (11), 1859018. doi:10.1142/S0218001418590188
Keywords: deep-buried long tunnel, intelligent tunnelling robot, comprehensive perception, dual-driven decision-making, composite intelligent control
Citation: Zhang Q, Zhu Y, Ma R, Du S, Shao K, Jing L, Zhang Y and Li Q (2023) Intelligent tunnelling robot system for deep-buried long tunnels. Front. Earth Sci. 11:1135948. doi: 10.3389/feart.2023.1135948
Received: 02 January 2023; Accepted: 24 May 2023;
Published: 01 June 2023.
Edited by:
Rui Yong, Ningbo University, ChinaCopyright © 2023 Zhang, Zhu, Ma, Du, Shao, Jing, Zhang and Li. This is an open-access article distributed under the terms of the Creative Commons Attribution License (CC BY). The use, distribution or reproduction in other forums is permitted, provided the original author(s) and the copyright owner(s) are credited and that the original publication in this journal is cited, in accordance with accepted academic practice. No use, distribution or reproduction is permitted which does not comply with these terms.
*Correspondence: Qingbin Li, cWluZ2JpbmxpQHRzaW5naHVhLmVkdS5jbg==