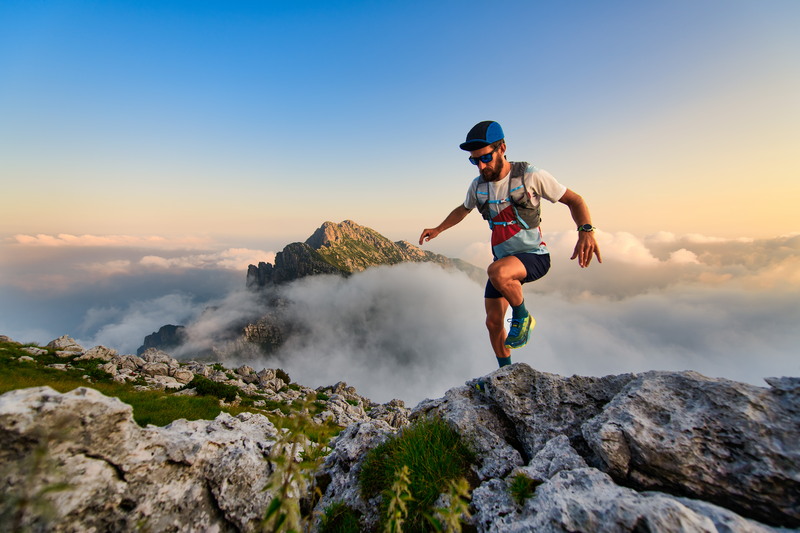
95% of researchers rate our articles as excellent or good
Learn more about the work of our research integrity team to safeguard the quality of each article we publish.
Find out more
ORIGINAL RESEARCH article
Front. Earth Sci. , 19 April 2023
Sec. Petrology
Volume 11 - 2023 | https://doi.org/10.3389/feart.2023.1101056
The effective stress of the reservoir rock in the underground gas storage (UGS) changes with the multi cycle injection and production, which changes the physical characteristics of the reservoir and affects the injection production capacity of the UGS. Taking carbonate fracture-pore type gas storage as the research object, combined with the actual production of UGS, establish a set of experimental evaluation methods based on production characteristics; Core damage evaluator, overburden pressure porosimeter and scanning electron microscope are used to carry out experimental research on the impact of effective stress change on injection production capacity, quantitative analysis of reservoir internal characteristics, multi cycle injection and production and effect of effective stress action time on injection-production capacity. The results show, the experimental method established based on the actual production characteristics of the UGS, simulation of multi cycle injection and production by forward and reverse displacement, simulation of effective stress change under constant confining pressure and variable internal pressure, the experimental evaluation of the injection production capacity of the simulation multi cycle injection and production of the UGS is realized; The change of effective stress makes the reservoir seepage characteristics worse and the reservoir space smaller, injection-production coefficient (Szc) is positively correlated with the internal characteristic value of the reservoir, the larger the internal characteristic value of the reservoir, the higher Szc, and the better the injection production capacity; The injection production capacity of the UGS reservoir deteriorates with the increase of the injection production cycle, in the 4th injection production cycle, the injection production capacity of the UGS changes from moderately strong to moderately weak; The damage of effective stress to the injection production capacity of UGS mainly occurs in the initial stage of injection production, and the damage tends to be stable with the progress of injection production. The conclusion is that the change of effective stress in carbonate fracture-pore type gas storage makes the injection-production capacity of the reservoir worse, it is proposed to carry out reservoir reconstruction before the UGS is put into operation, and expand the capacity of the gas storage after the completion of the 3rd injection and production cycle, which can effectively offset the impact of the decline of injection production capacity of the UGS and play the role of reservoir protection, it provides a constructive idea for improving the operation efficiency of the UGS.
In recent years, with the rapid growth of natural gas consumption, the contradiction between insufficient underground gas storage (UGS) capacity with safe and stable supply of natural gas has further intensified. As the “ballast stone” to ensure the safe and stable operation of the natural gas energy market, UGS plays an indispensable role in the whole natural gas industry chain (Ma et al., 2022). According to international experience, once the external dependence of natural gas exceeds 30%, the working gas volume of UGS needs to exceed 12% of the consumption, and China’s external dependence on natural gas will climb to 44.9% in 2021 (Ding et al., 2022). However, the gas storage and peak shaving facilities are far from meeting the aforementioned standards. Compared with other countries, China’s UGS construction is still at the primary level: the working gas volume of UGS is only 3%–4% of the national natural gas consumption, and the international average is 12%–15% (Yang et al., 2021). To improve the gas storage and peak shaving capacity of UGS, we should not only pay attention to the construction of the number of UGS, but also strengthen the excavation of the potential of the built UGS to ensure the efficient operation of the UGS (Jiang et al., 2021). UGS must meet the requirements of “gas injection, storage and production”, and must complete gas injection and production in a short time (generally, gas injection is completed once in 8 months and gas production is completed once in 4 months), forming an injection production cycle. The operation of the UGS is repeated between the upper and lower limit pressures, and the effective stress borne by the reservoir rock changes periodically. This change will inevitably lead to changes in the reservoir seepage characteristics (Quinn and MacDonald, 1992; Castelletto et al., 2013), which will affect the injection production capacity and storage capacity of the UGS, and is not conducive to the efficient operation of UGS. Therefore, it is of great significance to clarify the impact of periodic stress changes on the injection production capacity of UGS reservoirs, put forward injection and production measures for UGS, scientific formulation of injection-production plan.
At present, many important results and understandings have been obtained in the experimental study of the influence of stress sensitivity on the percolation characteristics of oil and gas reservoirs, but less is involved in the multi cycle injection and production of carbonate fracture-pore UGS. The lower the permeability of sandstone reservoir, the stronger the stress sensitivity (Wang et al., 2021; Xu et al., 2022); Strong stress sensitive rocks have obvious fracture characteristics, while weak stress sensitive rocks have porosity characteristics (Cuss et al., 2003; Engelder, 2014); The pressure-sensitive experiment of ultra-high pressure gas reservoir is carried out, and the binomial productivity equation considering the influence of pressure-sensitive effect is established (Engelder and Fischer, 1994); Carry out rock permeability and porosity change experiments under effective stress loading, describe the relationship between porosity, permeability and effective stress by establishing functions, spatial models, etc (Oughanem et al., 2013; Rahmati et al., 2013; Moosavi et al., 2014; Selvadurai and Glowacki, 2016). A method for evaluating the stress sensitivity is established, which mainly includes using the constant in the relationship between regression permeability and effective stress index to express the stress sensitivity (Bazin et al., 2008), stress sensitivity coefficient method (You et al., 2013), and a series of evaluation methods such as the industry standard flow test evaluation method of reservoir sensitivity (SY/T 5358-2010).
Multi cycle injection and production of sandstone gas storage will reduce the permeability of reservoir rocks, but with the increase of injection and production rounds, the permeability decline will decrease. The lower the permeability, the greater the irreversible permeability loss rate, and the stronger the periodic stress sensitivity (Bakhtiari et al., 2021; Wang et al., 2023). The operation of the UGS has the characteristics of multi cycle, strong injection and production, and alternating load, it is easy to induce reservoir damage such as stress sensitivity, particle migration and sand production. Through the optimization design of injection production parameters and storage capacity parameters, the safe and stable operation of the UGS can be realized (Dehghan et al., 2016; Verga, 2018; Honari and Seyedi Hosseininia, 2021). Multi cycle injection and production of UGS, adopting different injection and production measures, can not only meet production needs, but also alleviate reservoir damage caused by particle migration and improve the operation efficiency of UGS (Arfaee and Sola, 2014; Xinping et al., 2020; Subbiah et al., 2021).
In summary, the research on stress sensitivity at home and abroad mainly focuses on the seepage characteristics and evaluation methods of oil and gas reservoirs, mainly serving the oil and gas productivity. The research on multi cycle injection and production stress sensitivity of UGS is relatively few, and most of the UGS involved are sandstone reservoirs, and the research on the impact of effective stress changes of carbonate fracture-pore type gas storage on injection production capacity is rarely involved, and lack of corresponding experimental methods and evaluation indicators. For carbonate rock fracture-pore type gas storgae, natural gas is stored and transported in the fracture pore, and the periodic change of effective stress will inevitably lead to the change of reservoir seepage characteristics, which will affect the injection production capacity and storage capacity of the UGS. However, at present, no research has been carried out on the change of injection production capacity caused by the periodic rise and fall of effective stress under the conditions of multi cycle injection and production for carbonate fracture-pore type gas storage.
During the operation of the UGS, the periodic change of effective stress will change the physical properties of the reservoir, especially the permeability and porosity of the reservoir. The author selected carbonate fracture-pore reservoir rock samples of X gas storage, established an experimental method based on the injection production characteristics of the X UGS, and gave the indexes for evaluating the injection production capacity of the UGS; Carry out experiments on the influence of internal characteristic values of the reservoir, multi cycle injection and production and considering the effective stress action time on the injection production capacity of the reservoir. By detecting the changes of permeability and porosity of the rock sample during the experiment, and observing the changes of fracture wall characteristics of the rock sample before and after the experiment with a scanning electron microscope, analyze the impact of effective stress changes on the injection production capacity of carbonate fracture-pore type gas storage, and reveal the mechanism of action. Based on the understanding of experimental research, provide reservoir protection measures and suggestions, it is expected to provide experimental technical support for optimizing the injection-production system of carbonate fracture-pore gas reservoirs and improving the operation efficiency of UGS.
The experimental rock sample is from the core in the injection production wells of X UGS, and the reservoir is carbonate fracture-pore type. According to the analysis of logging and coring data, the porosity of the reservoir is 0.39%–16.96%, and the permeability is 0.001–223.69 mD. The core is processed into a column sample with a diameter of 2.5 cm and a length of 5 cm (Figure 1), testing porosity and permeability, select core samples similar to reservoir physical properties as experimental rock samples.
Permeability is measured by core damage evaluation instrument, porosity is measured by overburden porosity-permeability instrument, and microstructure is observed by scanning electron microscope. The core damage evaluation instrument mainly consists of injection system, temperature control system, pressure control system, back pressure system, metering system, data acquisition and control system, the injection system can adjust the pressure by 0–50 MPa, the temperature control system room temperature ∼150°C, the maximum confining pressure of the pressure control system is 90 MPa, and the accuracy of the metering system is 0.001 g (Figure 2A). The overburden porosity-permeability instrument is mainly composed of pressure regulating system, sampling system, automatic control system, data acquisition and analysis system, etc., the porosity measurement range: 0.01%–40%, the permeability measurement range: 0.00005–15,000 mD, the pressure sensor: 0–250 psi, 0–10,000 psi (Figure 2B).
FIGURE 2. Flow chart of experimental equipments. (A): Core damage evaluation instrument, (B): overburden porosity-permeability instrument.
The operation of UGS is a process in which the overlying formation pressure remains unchanged, the reservoir pore pressure increases during gas injection, and the reservoir pore pressure decreases during gas production, that is the operation is repeated between the upper and lower pressure of the UGS. According to the principle of similarity and similarity, it is converted into laboratory experiment, using the effective stress change mode of constant confining pressure and variable pore pressure, using confining pressure to simulate the overlying pressure of the UGS, the experimental injection pressure simulates the pressure in the pores of the gas reservoir, and the injection pressure changes to simulate the change of the operating pressure during the injection production of the gas reservoir.
For the pertinence and accuracy of experimental research, the experimental temperature 82 C (X UGS reservoir temperature), confining pressure 71 MPa (X UGS reservoir overlying formation pressure). Conduct triaxial rock mechanics experiments on experimental rock samples, under the experimental confining pressure of 71 MPa, the average compressive strength is 314.75 MPa, which means that under the experimental conditions of adding confining pressure, the experimental rock samples undergo elastic deformation when the pressure is less than 314.75 MPa; when the pressure reaches 314.75 MPa, plastic deformation occurs to breakage (Figure 3). The critical pressure for displacement deviation of the experimental rock sample is 314.75 MPa. Injection pressure is 13.20 MPa–28.06 MPa (X UGS operation of upper and lower limit pressure). The injection pressure is refined and decomposed in the experiment, the injection pressure with 3 MPa as the pressure interval from the lower limit 13 MPa to the upper limit 31 MPa, which are 13 MPa, 16 MPa, 19 MPa, 22 MPa, 25 MPa, 28 MPa, and 31 MPa. The effective stress is the difference between the confining pressure and the injection pressure, which are 58 MPa, 55 MPa, 52 MPa, 49 MPa, 46 MPa, 43 MPa, and 40 MPa (Table 1).
TABLE 1. Table of injection pressure and effective stress for periodic injection and production of X UGS.
The experimental medium is 8% potassium chloride solution, in order to eliminate the effect of velocity sensitivity on the experimental results, the experimental displacement flow should be determined. The specific experimental steps are as follows: 1)Put the core sample into the core holder, increase the confining pressure, and let it stand for 4 h to eliminate the stress sensitivity; 2)Keep the confining pressure always higher than the inlet pressure 2 MPa, and test the permeability under the flow rates of 0.10 cm3/min, 0.25 cm3/min, 0.5 cm3/min, 0.75 cm3/min, 1.00 cm3/min, 1.5 cm3/min, and 2.0 cm3/min. When the permeability change rate is greater than 20%, it indicates that velocity sensitivity has occurred, and the flow corresponding previous point is the displacement flow. The permeability change rate can be expressed using Eq. (1).
Where, Dw is the permeability change rate under different flow rates; Ki is the permeability of core under different flow rates, respectively (mD); Kw is the initial permeability of core, respectively (mD).
Test the displacement flow of different experimental samples, which shows that the flow rate when the permeability change rate is greater than 20% increases with the increase of initial permeability, but when the initial permeability of the sample is within a certain range, the flow rate when the permeability change rate is greater than 20% is a constant value (Table 2). The reservoir itself contains fine particles, particles migrate under the scouring of high-speed fluid, which may block the pore throat or accompany fluid discharge from the reservoir (Muecke, 1979; Gruesbeck and Collins, 1982; Civan, 2015; Li et al., 2017; Hou et al., 2015). When the initial permeability of the sample is within a certain range, its corresponding pore structure is consistent, and the fluid exhibits the same properties when passing through the pore. Therefore, different displacement flow rates are used for different experimental samples.
During the change of effective stress, test the permeability and porosity changes at different effective stress points. The experimental steps are as follows: 1)Put the core samples into the core holder of the overburden porosity-permeability instrument, test the porosity and permeability, select two core samples with similar porosity and permeability as a group, and select the cores representing the physical properties of different reservoirs as different groups; 2)A core sample of the same group is put into the core holder of the Core damage evaluation instrument, linearly load the confining pressure at a loading rate of 0.69 MPa/min, load the confining pressure to 71 MPa and keep it constant, and stabilize for 4 h; the displacement flow is used to pressurize to the injection pressure, maintain the pressure for 15 min, measure the permeability of this point; At the same time, another core sample of the same group is put into the core holder of the overburden porosity-permeability instrument, and the effective stress corresponding to the injection pressure is added as the confining pressure, maintain the pressure for 15 min, measure the pore of this point; 3)According to the injection pressure interval, increase the injection pressure in turn to the maximum, and test the permeability of core samples at different injection pressure points; The effective stress corresponding to the injection pressure is taken as the confining pressure to test the porosity of core samples at different effective stress points, this process simulates the gas injection process of UGS; 4)Change the displacement direction, according to the injection pressure interval, and then start from the maximum injection pressure, reduce the injection pressure to the minimum injection pressure by the displacement flow, and test the permeability of core samples at different injection pressure points; The effective stress corresponding to the injection pressure is taken as the confining pressure to test the porosity of core samples at different effective stress points, this process simulates the gas production process of UGS; 5)Repeat steps (2)–(4) to complete the experiment until to complete multi cycle injection and production; 6)Replace the core sample and repeat steps (2)–(5) until the experiment is completed. Finally, based on the change characteristics of permeability and porosity under different effective stress, define the effect of effective stress change on the injection production capacity of the reservoir.
There is a correlation between porosity, permeability with effective stress. The pore volume and permeability of rocks decrease with the increase of the cycle of pressure reciprocating changes (Ranjith et al., 2013; Song et al., 2022). The natural gas in the UGS is stored and migrated in the fractures and pores of the reservoir, with the injection production of the UGS, the internal characteristics of the reservoir are also changing (Dake, 1983; Gobran et al., 1987; Economides and Nolte, 1989; Cosentino, 2001; Lucia et al., 2003; Jaeger et al., 2009; Lake, 2012; Ahmed, 2018) (Figure 4). In order to clarify the influence of the change of the internal characteristics of the reservoir on the injection production capacity of the reservoir, use the product of porosity and permeability to characterize the internal characteristic value of the reservoir. The ratio of the internal characteristic value of the reservoir at different injection and production stages of the UGS to the internal characteristic value of the reservoir before the construction UGS, called injection-production coefficient, which can be expressed using Eq. 2. Before the construction of the UGS, the maximum injection-production coefficient is 1, As the UGS is built and operated, the injection production capacity gradually changes. According to the operation status of the UGS, the injection-production coefficient is divided into four ranges, analyze the change of the injection-production coefficient with the periodic injection production of the UGS, indicates the injection production capacity of the UGS (Table 3).
Where, Szc is the injection-production coefficient of UGS at different injection-production stages, dimensionless; Kn is the permeability of UGS at different stages of injection and production, respectively (mD); Qn is the porosity of UGS in different injection production stages, respectively (%); Ki is the initial permeability of UGS, respectively (mD); Qi is the initial porosity of UGS, respectively (%).
FIGURE 4. Characteristic change of multi cycle injection and production reservoir in X UGS. (A): reservoir, (B): porous.
Select three groups of samples representing small, medium and large internal characteristic values of the UGS reservoir, namely, 1, 2 and 3 groups, to conduct single cycle injection and production, and test the change of injection-production coefficient under different effective stress (Figure 5).
FIGURE 5. Injection-production coefficient of internal characteristic value of different reservoirs changes with effective stress.
For the same sample, under the same effective stress, Szc in the gas injection stage is greater than that in the gas production stage, which indicates that gas injection and production will damage the reservoir’s injection production capacity and is irreversible. Different samples have different Szc after injection and production, Group 3 (0.65) > Group 2 (0.55) > Group 1 (0.48), which shows that Szc is positively with the internal characteristic value of the reservoir, that is the larger the internal characteristic value of the reservoir after injection production, the higher Szc is, indicating that the higher the permeability and porosity of the reservoir, the better the injection production capacity; after the completion of injection and production, the variation value of Szc (Eq. 3) is different, Group 1 (0.08) > Group 2 (0.07) > Group 3 (0.05), indicating that the variation value of Szc is inversely correlated with the internal characteristic value of the reservoir, which shows that the greater the internal characteristic value of the reservoir, the smaller the change value of Szc, indicating that the higher the initial permeability and porosity of the reservoir, the less damage to the injection production capacity of the reservoir caused by gas injection and production. Therefore, reservoir reconstruction after completion of the injection production wells in UGS can improve the permeability and porosity of the reservoir and play a role in reservoir protection.
Where, △Szc is the variation value of injection-production coefficient; Szc’ is the injection-production coefficient in gas injection stage; Szc’’ is the injection production coefficient in gas production stage.
Select 2nd group of internal characteristic values of representative UGS reservoir for multi cycle injection and production, and test the change of Szc under different effective stresses (Figure 6).
FIGURE 6. Injection-production coefficient changes with effective stress in different injection production periods.
In the same injection production cycle, during gas injection reservoir pore pressure increases, while the overlying formation pressure remains unchanged, the increased pore pressure offsets part of the overlying formation pressure, and the effective stress acting on the reservoir decreases, making the reservoir internal fractures and pores space of the reservoir partially recovered, which is shown as Szc increases with the decrease of the effective stress; Contrary to gas injection during gas production, the reservoir pore pressure decreases, while the overlying formation pressure remains unchanged, and the effective stress acting on the reservoir increases, making the internal fractures and pores space compression of the reservoir smaller, which is shown as Szc decreases with the increase of effective stress. At the same effective stress point, Szc during gas injection is greater than Szc during gas production, and the difference increases with the increase of effective stress, indicating that the change of effective stress is irreversible to the damage of reservoir injection production capacity. In different injection production cycles, Szc decreases with the increase of injection production cycle, from 0.75 at the beginning of the first injection production cycle to 0.43 at the end of the fifth injection production cycle, but the decrease amplitude becomes smaller. After the third injection production cycle, the decrease value of injection-production coefficient tends to be stable, indicating that the damage to the reservoir injection production ability becomes weaker and stable due to the change of effective stress with the increase of injection production cycle. The injection-production coefficient of the 1st∼3rd injection production cycle is 0.75–0.51, and the injection production capacity of the reservoir is moderately strong; 0.49–0.42 after the fourth injection production cycle, the injection production capacity of the reservoir is moderately weak. Therefore, in order to maintain the injection production capacity of the UGS reservoir, the UGS capacity will be expanded after the completion of the 3rd injection and production cycle.
Select 3 samples representing the internal characteristic value of the gas reservoir, the effective stress is constant, With the increase of the effective stress acting time, real time test of injection-production coefficient changes under different effective stresses (Figure 7).
The overburden pressure of the gas reservoir is 71 MPa, and the UGS operates repeatedly at the upper and lower pressure of 28.06 MPa–13.20 MPa (the effective stress is 42.94 MPa–57.8 MPa), so the effective stress is 42.94 MPa, 57.8 MPa and the average value is 50.37 MPa. Under the same effective stress, Szc shows three stages of rapidly decrease, stable and further decrease with the increase of action time. The rapid decrease of Szc occurred within 1.5 h, with a decrease range of 2%–5%; Szc occurs stably in 1.5 h–3.0 h; Szc decreased slightly after 3.0 h. For different effective stresses, the smaller the effective stress, the greater the Szc, under the same action time, the greater the effective stress, the smaller the Szc. It shows that the damage of effective stress to the injection production capacity of UGS reservoir occurs at the beginning of injection production, and the damage tends to be stable with the injection production.
The change of effective stress will cause rock deformation, which mainly includes the deformation of fracture pore space, the deformation of skeleton particles and the deformation of skeleton particle arrangement (Gilbert et al., 2013; Liu et al., 2022). The deformation of skeleton particles belongs to elastic deformation, the effective stress can usually recover after unloading; The deformation due to the change of particle arrangement of the skeleton belongs to plastic deformation, and it is difficult to recover the effective stress after unloading (Sui et al., 2011).
According to the scanning electron microscope pictures of the experimental samples, it can be observed that the pore morphology in the sample is mainly circular pore, and at the same time, there are long and narrow natural fractures (Figure 8). Carbonate fracture-pore type reservoir rock is hard in compactness, and the space for skeleton particle deformation is very small, therefore, the effective stress first causes the deformation of the fracture pore space, with the increase of effective stress, skeleton particle deformation and skeleton particle arrangement change successively (Figure 9). When the effective stress is between 40 MPa and 49 MPa (injection production pressure 31 MPa–22 MPa), Szc is larger and changes rapidly, the reason is that the reservoir rock with the increase of the effective pressure has obvious compaction, and the porosity and permeability decrease rapidly, at this stage, Szc changes are mainly caused by the deformation of the fracture porosity space. When the effective stress changes between 58 MPa and 49 MPa (injection production pressure 13 MPa–22 MPa), Szc is relatively small and basically unchanged, indicating that the injection production capacity is relatively weak and stable, the reason is that the space available for compression in the rock sample is reduced, and the decrease range of porosity and permeability is reduced, at this stage, Szc changes are mainly caused by the deformation of skeleton particles and the deformation caused by the change of skeleton particle arrangement.
Multi cycle injection and production reduces the injection production capacity of the UGS, but with the increase of injection and production cycle, the injection production capacity tends to be stable, indicating that the fractures and pores of the reservoir rock are reduced to a certain extent due to multi cycle effective stress, but still have injection production capacity. The scanning electron microscope results show that there are dense and a large number of microconvex bodies on the fracture and pore wall of the sample, when the fracture and pore are closed to a certain extent, these dense and large number of microconvex bodies contact the other wall of the fracture and pore, forming a supporting role for the fracture and pore (Figures 10, 11).
Figure 4 shows, Szc can be divided into three stages of rapid decrease, stability and redecrease with the increase of effective stress acting time. At the beginning, fractures and pores are closed to a certain extent under the effect of effective stress, resulting in a rapid reduction of Szc. After the effective stress is applied for a period of time, Szc is relatively stable due to the support of the microconvex body on the fracture and pore wall (Figure 12A). As the wall microconvex bodies, especially those in point contact, are prone to stress concentration, as the effective stress action time continues to increase, the microconvex body will break (Figure 12B), and the fractures and pores will be closed to a certain extent again, eventually causing Szc to decrease again (Figure 12C).
FIGURE 12. The microconvex body of wall breakage. (A): fracture wall, (B): microconvex body, (C): fracture closure.
1) The experimental method established based on the actual production characteristics of UGS, has realized the experimental evaluation of the simulation of the impact of effective stress changes on the multi cycle injection and production of UGS. The proposed injection-production coefficient can accurately reflect the injection production capacity of multi cycle injection and production of the UGS reservoir.
2) The change of effective stress will cause irreversible damage to the injection production capacity of the reservoir. The higher the initial permeability and porosity of the reservoir, the less damage the effective stress will cause to the reservoir. It is suggested that reservoir reconstruction should be carried out before the injection production wells of the UGS are put into production, to increase the initial permeability and porosity, which is conducive to improving the injection and production efficiency of the UGS and realizing the efficient operation of the UGS.
3) After periodic injection and production, the gas storage space is lost and the storage capacity is reduced accordingly. It is recommended to expand the UGS after the completion of the 3rd injection and production cycle, which can effectively offset the reduction of the storage capacity caused by the decline of the UGS’s injection production capacity, maintain the UGS’s injection production capacity, and improve the UGS’s operating efficiency.
4) With the increase of effective stress acting time, the injection production capacity of the UGS reservoir presents a trend of “rapid reduction - stability - further reduction”. It is suggested to shorten the empty storage period and lengthen the full storage period in the way of “rapid production and slow injection” during the operation of UGS, so as to avoid or reduce the further reduction stage of the injection production capacity.
The original contributions presented in the study are included in the article/supplementary material, further inquiries can be directed to the corresponding author.
XPG is responsible for the overall structure and revision. JY, HFH, and JLP help evaluate and improve the paper. HP and ZFY help in setting up the device test, writing, and the experiment.
The authors declare that this study received funding from the Science and Technology Project of Oil & Gas and New Energy Company, PetroChina, Project No: 2022KT2303 and the Scientific research and technology development project of Southwest Oil & Gas Field Company, PetroChina, Project No: 2018030312. The funder was not involved in the study design, collection, analysis, interpretation of data, the writing of this article or the decision to submit it for publication.
All authors were employed by Southwest Oil & Gas Field Company, PetroChina.
All claims expressed in this article are solely those of the authors and do not necessarily represent those of their affiliated organizations, or those of the publisher, the editors and the reviewers. Any product that may be evaluated in this article, or claim that may be made by its manufacturer, is not guaranteed or endorsed by the publisher.
Arfaee, M. I. R., and Sola, B. S. (2014). Investigating the effect of fracture–matrix interaction in underground gas storage process at condensate naturally fractured reservoirs. J. Nat. Gas Sci. Eng. 19, 161–174. doi:10.1016/j.jngse.2014.05.007
Bakhtiari, M., Shad, S., Zivar, D., and Razaghi, N. (2021). Coupled hydromechanical analysis of underground gas storage at Sarajeh field, Qom formation, Iran. J. Nat. Gas. Sci. Eng. 92, 103996. doi:10.1016/j.jngse.2021.103996
Bazin, B., Bekri, S., Vizika, O., Herzhaft, B., and Aubry, E. (2008). “Fracturing in tight-gas reservoirs: Application of SCAL methods to investigate formation-damage mechanisms,” in SPE International Symposium and Exhibition on Formation Damage Control (OnePetro). doi:10.2118/112460-MS
Castelletto, N., Ferronato, M., Gambolati, G., Janna, C., Marzorati, D., and Teatini, P. (2013). Can natural fluid pore pressure Be safely exceeded in storing gas underground? Eng. Geol. 153, 35–44. doi:10.1016/j.enggeo.2012.11.008
Cosentino, L. (2001). Integrated reservoir studies. Paris, France: Institut Français du Pétrole Publications.
Cuss, R. J., Rutter, E. H., and Holloway, R. F. (2003). Experimental observations of the mechanics of borehole failure in porous sandstone. Int. J. Rock Mech. Min. Sci. 40 (5), 747–761. doi:10.1016/S1365-1609(03)00068-6
Dehghan, A. N., Goshtasbi, K., Ahangari, K., and Jin, Y. (2016). Mechanism of fracture initiation and propagation using a tri-axial hydraulic fracturing test system in naturally fractured reservoirs. Eur. J. Environ. Civ. Eng. 20, 560–585. doi:10.1080/19648189.2015.1056384
Ding, G., Ding, Y., Li, Y., Tang, L., Wu, Z., Wanyan, Q., et al. (2022). Prospects of underground gas storage in China under the strategy of carbon neutrality. Oil Gas Storage Transp. 41 (1), 1–7. doi:10.6047/j.issn.1000-8241.2022.01.001
Economides, M. J., and Nolte, K. G. (1989). Reservoir stimulation, Vol. 2. Englewood Cliffs, NJ: Prentice Hall, 6–10.
Engelder, T., and Fischer, M. P. (1994). Influence of poroelastic behavior on the magnitude of minimum horizontal stress, S h in overpressured parts of sedimentary basins. Geology 22 (10), 949–952. doi:10.1130/0091-7613(1994)022<0949:IOPBOT>2.3.CO;2
Engelder, T. (2014). Stress regimes in the lithospher, Vol. 151. New Jersey: Princeton University Press.
Gilbert, G., Backé, R., Puspitasari, Z., Pallikathekathil, J., Maney, B., and Dewhurst, D. (2013). Model. geomechanics gas storage a case study Iona gas field. Aust. J. Greenh. Gas. Control 13, 138–148. doi:10.1016/j.ijggc.2012.12.009
Gobran, B. D., Brigham, W. E., and Ramey, H. J. (1987). Absolute permeability as a function of confining pressure, pore pressure, and temperature. SPE Form. Eval. 2 (01), 77–84. doi:10.2118/10156-PA
Gruesbeck, C., and Collins, R. E. (1982). Entrainment and deposition of fine particles in porous media. Soc. Petroleum Eng. J. 22 (06), 847–856. doi:10.2118/8430-pa
Honari, S., and Seyedi Hosseininia, E. (2021). Particulate modeling of sand production using coupled DEM-LBM. Energies 14 (4), 906. doi:10.3390/en14040906
Hou, D., Zhang, H., and Li, G. (2015). Study of pressure propagation characteristics to determine stress sensitivity of low-permeability gas reservoir. Chem. Technol. Fuels Oils 51, 181–189. doi:10.1007/s10553-015-0591-z
Jaeger, J. C., Cook, N. G., and Zimmerman, R. (2009). Fundamentals of rock mechanics. Malden, MA: Blackwell Publishing.
Jiang, T., Wang, J., Wang, Z., Zhou, D., Li, Y., Wang, S., et al. (2021). A novel protein encoded by circMAPK1 inhibits progression of gastric cancer by suppressing activation of MAPK signaling. Nat. Gas. Ind. 41 (9), 66–74. doi:10.1186/s12943-021-01358-y
Li, X. P., Cao, L. N., Luo, C., Zhang, B., Zhang, J. Q., and Tan, X. H. (2017). Characteristics of transient production rate performance of horizontal well in fractured tight gas reservoirs with stress-sensitivity effect. J. Petroleum Sci. Eng. 158, 92–106. doi:10.1016/j.petrol.2017.08.041
Liu, J., Mei, L., Ding, W., Xu, K., Yang, H., and Liu, Y. (2022). Asymmetric propagation mechanism of hydraulic fracture networks in continental reservoirs. GSA Bull. 135, 678–688. doi:10.1130/B36358.1
Lucia, F. J., Kerans, C., and Jennings, J. W. (2003). Carbonate reservoir characterization. J. Petroleum Technol. 55 (06), 70–72. doi:10.2118/82071-ms
Ma, X., Zheng, D., Wei, G., Ding, G., and Zheng, S. (2022). Development directions of major scientific theories and technologies for underground gas storage. Nat. Gas. Ind. 42 (5), 93–99. doi:10.3787/j.issn.1000-0976.2022.05.010
Moosavi, S. A., Goshtasbi, K., Kazemzadeh, E., Bakhtiari, H. A., Esfahani, M. R., and Vali, J. (2014). Relationship between porosity and permeability with stress using pore volume compressibility characteristic of reservoir rocks. Arabian J. Geosciences 7 (1), 231–239. doi:10.1007/s12517-012-0760-x
Muecke, T. W. (1979). Formation fines and factors controlling their movement in porous media. J. petroleum Technol. 31 (02), 144–150. doi:10.2118/7007-pa
Oughanem, R., Youssef, S., Bazin, B., Maire, E., and Vizika, O. (2013). “Pore-scale to core-scale aspects of capillary desaturation curves using CT-scan imaging,” in IOR 2013-17th European Symposium on Improved Oil Recovery (European Association of Geoscientists & Engineers), 342. doi:10.3997/2214-4609.20142615
Quinn, D. F., and MacDonald, J. A. (1992). Natural gas storage. Carbon 30 (7), 1097–1103. doi:10.1016/0008-6223(92)90141-I
Rahmati, H., Jafarpour, M., Azadbakht, S., Nouri, A., Vaziri, H., Chan, D., et al. (2013). Review of sand production prediction models. J. Petroleum Eng. 2013, 1–16. doi:10.1155/2013/864981
Ranjith, P. G., Perera, M. S. A., Perera, W. K. G., Wu, B., and Choi, S. K. (2013). Effective parameters for sand production in unconsolidated formations: An experimental study. J. Petroleum Sci. Eng. 105, 34–42. doi:10.1016/j.petrol.2013.03.023
Selvadurai, A. P. S., and Glowacki, A. (2017). Stress-induced permeability alterations in an argillaceous limestone. Rock Mech. Rock Eng. 50 (5), 1079–1096. doi:10.1007/s00603-016-1153-3
Song, R., Zhang, P., Tian, X., Huang, F., Li, Z., and Liu, J. (2022). Study on critical drawdown pressure of sanding for wellbore of underground gas storage in a depleted gas reservoir. Energies 15 (16), 5913. doi:10.3390/en15165913
Subbiah, S. K., Samsuri, A., Mohamad-Hussein, A., Jaafar, M. Z., Chen, Y. R., and Kumar, R. R. (2021). Root cause of sand production and methodologies for prediction. Petroleum 7 (3), 263–271. doi:10.1016/j.petlm.2020.09.007
Sui, Y., Lin, T., Liu, X., Dong, C., Cheng, W., Zhang, G., et al. (2011). Numerical simulation for the effect of cyclic stress on microstructure and mechanical properties of reservoir rocks during operations of gas storage. J. China Univ. Pet. Nat. Sci. 44 (2), 78–84. doi:10.1016/j.proeng.2011.05.040
Verga, F. (2018). What’s conventional and what’s special in a reservoir study for underground gas storage. Energies 11 (5), 1245. doi:10.3390/en11051245
Wang, J., Feng, X., Wanyan, Q., Zhao, Q., Pei, Z., Zie, G., et al. (2021). Hysteresis effect of three-phase fluids in the high-intensity injection–production process of sandstone underground gas storages. Energy 242, 123058. doi:10.1016/j.energy.2021.123058
Wang, Q-y., Shang, L., Xin, C-y., Sun, Y-c., Gao, G-l., Wang, M., et al. (2023). Application of the in-situ stress testing technology for the design of operating pressure of underground gas storage reservoir. Front. Earth Sci. 10, 1002676. doi:10.3389/feart.2022.1002676
Xinping, G. A. O., Junliang, P. E. N. G., Huifen, H. A. N., Yuchao, Z. H. O. U., Liming, L. I., and Yan, F. E. N. G. (2020). Experimental research on the damage caused by particle migration in Xiang guo Si gas storage. Drill. Prod. Technol. 43 (3), 46. doi:10.3969/J.ISSN.1006-768X.2020.03.14
Xu, D., Chen, S., Chen, J., Xue, J., and Yang, H. (2022). Study on the imbibition damage mechanisms of fracturing fluid for the whole fracturing process in a tight sandstone gas reservoir. Energies 15 (12), 4463. doi:10.3390/en15124463
Yang, Y., Chen, J., Wang, L., Zhang, H., Ni, J., Zhang, Y., et al. (2021). Analysis on the development prospects of China's gas storage business and the development path of operation models. PETROLEUM NEW ENERGY 33 (3), 11–14. doi:10.3969/j.issn.2097-0021.2021.03.003
Keywords: effective stress change, carbonate rocks, fracture-pore type gas storage, injection-production coefficient, injection production capacity
Citation: Gao X, Yang J, Han H, Peng J, Peng H and Yang Z (2023) Experimental research on the effect caused by effective stress change in injection production capacity of carbonate reservoir. Front. Earth Sci. 11:1101056. doi: 10.3389/feart.2023.1101056
Received: 17 November 2022; Accepted: 03 April 2023;
Published: 19 April 2023.
Edited by:
Shuai Yin, Xi’an Shiyou University, ChinaReviewed by:
Tianshou Ma, Southwest Petroleum University, ChinaCopyright © 2023 Gao, Yang, Han, Peng, Peng and Yang. This is an open-access article distributed under the terms of the Creative Commons Attribution License (CC BY). The use, distribution or reproduction in other forums is permitted, provided the original author(s) and the copyright owner(s) are credited and that the original publication in this journal is cited, in accordance with accepted academic practice. No use, distribution or reproduction is permitted which does not comply with these terms.
*Correspondence: Xinping Gao, Z2FveGlucGluZzAwN0AxNjMuY29tLmNu
Disclaimer: All claims expressed in this article are solely those of the authors and do not necessarily represent those of their affiliated organizations, or those of the publisher, the editors and the reviewers. Any product that may be evaluated in this article or claim that may be made by its manufacturer is not guaranteed or endorsed by the publisher.
Research integrity at Frontiers
Learn more about the work of our research integrity team to safeguard the quality of each article we publish.