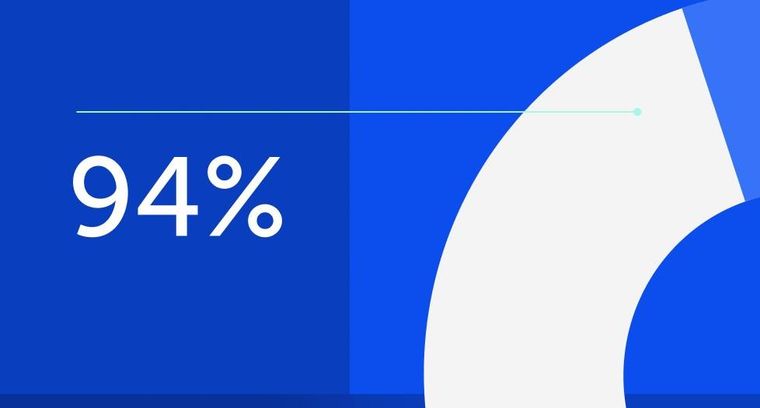
94% of researchers rate our articles as excellent or good
Learn more about the work of our research integrity team to safeguard the quality of each article we publish.
Find out more
ORIGINAL RESEARCH article
Front. Earth Sci., 08 September 2022
Sec. Marine Geoscience
Volume 10 - 2022 | https://doi.org/10.3389/feart.2022.991208
This article is part of the Research TopicGas Hydrate Appearance Accumulation, Exploration and Exploitation in Continental Margins - Volume 2View all 15 articles
With the development of economy and industry, the consumption of fossil energy is gradually increasing. Currently, natural gas hydrates (NGH) are considered to be an ideal alternative energy due to its large reserve and high energy density. However, the separation of hydrate slurry is a critical step in the exploitation of NGH. In this study, the optimization of the structural parameters based on the conventional three-phase hydrocyclone was carried out using numerical simulation and orthogonal design. At the same time, the separation efficiency criterion E was defined to evaluate the separation efficiency by calculating the sum of the discharge efficiency of water and gas. Analysis of the effect of individual structural factors on the flow field distribution characteristics inside the hydrocyclone using the single factor analysis method. The results showed that: with the combination of structural parameters of s was 2 mm2 × 12 mm2, dz was 28 mm, h was 20 mm, and li was 28 mm, the maximum E of the three-phase hydrocyclone was 1.46. The effect significance of each structural parameter on the separation efficiency from the highest to the lowest was the s, dz, h, and li. In the single-factor analysis, when the s was 2 mm2 × 12 mm2, the tangential velocity, axial velocity, and CH4 volume fraction in the flow field reached the maximum of 13.65 m/s, 4.35 m/s, and 12.4%, respectively. But the minimum water phase volume fraction was 69.9% under this structural parameter condition. When the dz was 36 mm, the maximum decrease value of axial velocity in the flow field was 3.57 m/s, the maximum CH4 volume fraction was 12.4%, and the water volume fraction reached a minimum of 66.3%. The li and the h only had significant effects on the axial velocity and the water volume fraction, respectively. The axial velocity reached a maximum of 4.75 m/s when the li was 32 mm, and the water phase volume fraction reached a maximum of 77.9% when the h was 10 mm. The study of the structural parameters and flow field characteristics of this three-phase hydrocyclone applicable to the solid fluidization exploitation of NGH provides some guidance and suggestions for the separation of hydrate slurry after solid fluidization exploitation of NGH.
With the development of economy and industry, the consumption of fossil energy is increasing year by year. According to statistics, the total global first-time energy consumption in 2018 was 14,301 million tons of oil equivalent, of which oil accounted for 31%, coal for 26%, and natural gas for 23% (Zou et al., 2016; Liang et al., 2020). The massive consumption of fossil fuels posed a great limitation to industrial and economic development and caused serious environmental pollution. Therefore, finding an alternative energy source with large reserves is the key to solving the current energy problem. Natural gas hydrates (NGH) is a kind of natural gas resource buried in the alpine permafrost and deep sea bottom, which has the characteristics of large reserve, wide distribution, high energy density, and clean combustion (Song et al., 2014; Wang et al., 2020). It is estimated that the proven reserves of NGH are 0.82 m3 × 1013 m3–2.10 m3 × 1015 m3 (at STP conditions), which is twice as much as the total reserves of fossil energy such as coal, oil, and natural gas (Li and Miao, 2014; Wei et al., 2020; Chang et al., 2021). NGH is an ice-like crystal structure composed of guest molecules under certain temperature and pressure conditions, and 1 m3 of NGH can store about 164 m3 of natural gas in the standard state (Chong et al., 2016; Chen et al., 2019). As a result, NGH is an alternative energy source with great potential.
At present, the exploitation of NGHis the focus of research in various countries. The United States, Canada, Japan, Russia, and China have all conducted test exploitation studies on NGH (Zhao et al., 2021; Chen et al., 2020). The methods applied by countries in the process of NGH test exploitation include depressurization, thermal excitation, chemical injection, and so on (Chuang et al., 2001; Song et al., 2015; Aminnaji et al., 2017; Cui et al., 2018). The depressurization method is to change the pore pressure of the hydrate reservoir, so that the reservoir pressure in the exploitation area is lower than the pressure condition for hydrate formation, thereby inducing the decomposition of NGH and releasing methane gas (Wang et al., 2018). The depressurization method does not require external energy and is considered to be the most economical method for the exploitation of NGH. However, according to the law of conservation of energy, in the process of exploiting NGH using the depressurization method, the decomposition of hydrate needs to absorb a lot of heat, which leads to the secondary generation of NGH, and then clogs the pipeline, resulting in low exploitation efficiency (Wang, 2019; Liu et al., 2021). The thermal excitation method is to inject heat into the NGH exploitation formation, so that the temperature of the formation is higher than the phase equilibrium temperature of NGH. The thermal exploitation method can control the decomposition rate of NGH by controlling the injection heat (Zhan et al., 2014; Wang et al., 2017). However, the method results in significant energy loss and high exploitation costs. The chemical injection method is to inject chemical reagents into the exploitation reservoir through special equipment, so as to change the phase equilibrium conditions of NGH in the reservoir to induce hydrate decomposition. However, this method is easy to cause environmental pollution and has the problem of high exploitation costs (Yang et al., 2019; Hou et al., 2021).
In order to solve the problems existing in the process of NGH exploitation, Zhou (Zhou et al., 2017a; Zhao et al., 2017) proposed solid fluidization exploitation method for NGH. The solid fluidization method is to crush the hydrate mineral into fine particles by means of high-pressure jet or mechanical crushing, and then mix it with seawater and transport it to the offshore platform through closed pipelines for later separation and treatment (Zhou et al., 2014). The solid fluidization method can exploit the hydrate reservoir in situ in the hydrate exploitation area and transport the hydrate particles through a closed environment. The phase equilibrium conditions of NGH are not broken during the whole exploitation process, and the uncontrollable decomposition of hydrate in shallow submarine without enclosed structure is changed to the artificially controlled decomposition of hydrate in the closed system (Zhou et al., 2017b). This method avoids the problems of formation collapse, greenhouse gas leakage, and high exploitation cost caused by traditional NGH exploitation methods, and is a highly efficient, green and controllable NGH exploitation method (Wei et al., 2018). The solid fluidization exploitation of NGH is to exploit the hydrate reservoir in a closed environment. During the exploitation process the seabed sediment is transported to the offshore platform along with the hydrate particles. Meanwhile, hydrate particles will decompose CH4 with temperature and pressure change during transport (Huang, 2018). Therefore, when the hydrate particles and sediment are moved to the offshore platform through the closed pipeline, the mixture in the pipeline is a three-phase mixture of gas-liquid-solid. So, the separation of the three-phase mixture is an important step in the solid fluidization exploitation of NGH.
At present, the main methods for separating hydrate slurry include gravity sedimentation separation (Wang et al., 2006), chemical separation (Wan, 2009), and cyclone separation (Dong et al., 2018; Qiu et al., 2019; Wang et al., 2019). The gravity sedimentation separation method relies on the density difference between different phases to make different phase in hydrate slurry settle naturally under the action of gravity, so as to realize the separation of gas, liquid, and solid phase. However, this method has the disadvantages of the large footprint and low separation efficiency. The chemical separation is to add relevant chemical reagents to the hydrate slurry and separate the needed phase by chemical reaction. But this method has high engineering application costs and is prone to environmental pollution. The cyclone separation is to inject the hydrate slurry into the hydrocyclone and the hydrate slurry do circular motion in the spin chamber, due to the density difference between different phases resulting in centrifugal force difference in the circular motion, so as to achieve the separation of different phases. With the advantages of high separation efficiency, small footprint, and no pollution to the environment, the cyclone separation is the most ideal method to separate hydrate slurry which is exploited by solid fluidization.
The hydrocyclone as the main technical equipment of cyclone separation was widely used in petroleum and petrochemical, environmental protection, chemical, and other fields of multi-phase separation because of the advantages of high efficiency, small size, and fast separation (Liu et al., 2018; Gao, 2021; Song et al., 2021). Up to now, many experts and scholars have done a lot of research on three-phase hydrocyclone. Zhao et al. (2008) studied the separation characteristics of hydrocyclone for fine particles under circulating flow conditions by experiment. The experimental results showed that the separation efficiency was maximum at a cycle period rate of 0.68 and a cyclical flow amplitude rate of 2%. Wu and Liu (2019) studied the effect of the inner cone structure on the separation efficiency of a three-phase hydrocyclone by computational fluid dynamics method, and obtained the optimal combination of inner cone structure. Jiang et al. (2014) used numerical simulation to study the effect of three-phase hydrocyclone overflow tube on the separation performance, which provided implications for the optimization of three-phase hydrocyclone structures. Zheng (2005) proposed a hydrocyclone for gas-water-sand three-phase separation by connecting solid-liquid cyclone and gas-liquid cyclone in series, and analyzed the flow field distribution characteristics by experiment. The experimental results verified the separation performance of the three-phase hydrocyclone. Chang et al. (2021) designed a hydrocyclone for desanding of NGH in the wellbore. The effect of structural parameters on the flow field distribution inside the device was verified by a combination of numerical simulation and experiments, and the optimal flow rate of this desanding hydrocyclone was obtained. However, up to now, there are few studies on gas-liquid-solid three-phase hydrocyclone applicable to solid fluidization exploitation of NGH.
In this paper, the numerical simulation method was used to study the structural parameters and internal flow field characteristics of the three-phase hydrocyclone which is applicable to solid fluidization exploitation of NGH. In order to ensure the universality and accuracy of the research, the structural parameters of the conventional three-phase hydrocyclone were optimized by the orthogonal design, and the structural parameters of the three-phase hydrocyclone applicable to the solid fluidization extraction of NGH were obtained. The effects of the gas outlet depth length (li), tangential inlet area (s), drain hole height (h), and inverted cone diameter (dz) on the separation efficiency of the hydrocyclone were also studied. The separation efficiency criterion of the three-phase hydrocyclone for NGH was defined based on the gas output and sand output of the optimized three-phase hydrocyclone. At the same time, the effect of single-factor change on the internal flow field distribution characteristics of the three-phase hydrocyclone was investigated by changing the individual structural parameters of the hydrocyclone. This study has some engineering guidance on hydrate slurry separation in the solid fluidization exploitation of NGH.
In this paper, based on the three-phase hydrocyclone designed by Xu et al. (2017), the optimization of structural parameters and flow field analysis of the three-phase hydrocyclone applicable to the solid fluidization exploitation of NGH were carried out. The structure of the gas-water-sand three-phase hydrocyclone was shown in Supplementary Figure S1.
Hydrate mineral becomes hydrate particles with sediment after solid fluidization exploitation. In the process of transporting hydrate particles from the seabed to the sea surface through a closed pipeline, as the pressure decreases and the temperature increases, the hydrate particles decompose into a three-phase mixture of gas, water, and sand. The mixture is injected into the spin chamber from the tangential inlets at a certain initial velocity, and makes a circular motion along the inner wall of the spin chamber to form a strong vortex. Due to the different densities among different phases, the centrifugal force generated by the three phases of air, water, and sand in the process of circular motion is different. Among them, the density of the sand is the largest, and the centrifugal force generated during the circular motion is the largest, so the sand is distributed on the side wall of the spin chamber, and finally discharged from the sand outlet, an annulus between the outer wall of the spin chamber and the water outlet. The density of the gas is the smallest, and the centrifugal force generated during the circular motion is the smallest, so the gas is distributed at the axis of the spin chamber. However, due to the inverted cone at the axis of the spin chamber, the gas is pushed into the gas outlet and finally discharged from the hydrocyclone under the action of the inverted cone. The density of water is between gas and sand, which is distributed between them in the spin chamber, and enters the interior of the inverted cone through the drain hole and is finally discharged from the hydrocyclone by the water outlet.
In this paper, a three-dimensional model was used to study the structural parameters and flow field characteristics of three-phase hydrocyclone applicable to solid fluidization exploitation of NGH. In the study of swirl flow field, compared with the two-dimensional model, the three-dimensional model can express the velocity change in three directions, thus showing the separation among different phases, and the flow field characteristics can be expressed more accurately. The structural parameters of the three-phase hydrocyclone were shown in Supplementary Table S1.
The fluid in the three-phase hydrocyclone can be regarded as a viscous incompressible fluid, which follows the basic governing equation. Continuity equation, momentum conservation equation and energy conservation equation, as shown in the following Eqs 1–3 (Elsayed and Lacor, 2011; Wang et al., 2015; Zhang et al., 2019; Bu et al., 2021):
Continuity equation
Momentum conservation equation
Energy conservation equation
In this paper, the numerical simulation was performed via commercial software Ansys Fluent 2020. The internal flow field of the hydrocyclone is regarded to be a strong complex swirl field, so the choice of turbulence model has an important effect on the accuracy of numerical simulation results. Among the turbulence models, the Reynolds stress model (RSM) is considered to be suitable for the simulation of turbulent flow fields such as anisotropic flow and three-dimensional flow, taking into account the additional stress caused by streamline curvature and the anisotropy and three-dimensional effect of turbulence. Therefore, the RSM is used to simulate the internal flow field of the three-phase hydrocyclone.
The RSM is based on the average Reynolds number theory, and the governing equations as is shown in the following Eqs 4–10 (Xu, 2012; Wang, 2020):
Reynolds stress transport equation:
Turbulent kinetic energy diffusion term equation:
Molecular viscous diffusion term equation:
Shear stress equation:
Buoyancy generation term equation:
Pressure strain term equation:
Viscous dissipative term equation:
The finite volume method was used to solve the problem, and the control equation was discretized based on the pressure-based solver. The Mixture model was selected to study the internal flow field characteristics of the three-phase hydrocyclone and the Semi-Implicit Method for Pressure-Linked Equations (SIMPLE) algorithm was used to solve the discrete equation. SIMPLE algorithm is one of the most widely used flow field calculation methods for solving incompressible flow field in engineering. The core of this method is to use a “prediction-correction” process to solve the Navier-Stokes equations by calculating the pressure field on the basis of an interleaved grid. Considering the effect of gravity on the separation, the gravity acceleration was set as 9.81 m/s−2. Set 1,000 steps per iteration to be saved as a data file in the calculation activity, and the total number of steps for the iteration was 10,000 steps. At the same time, in order to ensure the calculation accuracy, the convergence residual error was set as 10−6.
Meshing the 3D model of three-phase hydrocyclone. In order to ensure the accuracy of the numerical simulation and reduce the calculation time, four grid levels were divided and the grid independence test was carried out.
In this study, water and CH4 were set as continuous phases and sand as discrete phases. The density of water was 998.2 kg/m3, and the viscosity was 0.001 pa·s, the density of methane was 0.68 kg/m3. In order to avoid the particle diameter has an influence on the separation of each phase, the density of sand was 2,700 kg/m3, and the particle diameter was 50 μm. The volume fractions of water, CH4 and sand were 0.7, 0.1, and 0.2 respectively. The boundary condition of the tangential inlets of the three-phase hydrocyclone was set as the velocity inlet, and the incident velocity of the gas, water, and sand was consistent under the same structural parameters. The gas outlet, water outlet, and sand outlet were all set as outflow, and the flow ratios were set as 0.6, 0.2, and 0.2, respectively. The wall of the three-phase hydrocyclone was set as wall, the wall roughness was 0, and there was no slip wall boundary.
In this paper, the numerical simulation method was used to optimize the structural parameters and analyze the internal flow field of the three-phase hydrocyclone applicable to solid fluidization exploitation of NGH. Firstly, taking the actual working conditions of the solid fluidization exploitation process of NGH as the standard, based on the conventional three-phase hydrocyclone, the orthogonal design was used to optimize the structural parameters. Through investigation, it was known that the structural parameters of the gas outlet tube, tangential inlets, and inverted cone structure have a significant effect on the separation efficiency of hydrocyclone. Therefore, the optimization parameters mainly include five factors in this study: gas outlet depth length (li), inverted cone length (lz), tangential inlet area (s), drain hole height (h), and inverted cone diameter (dz), and each factor were set at five levels. If all five factors and five levels are combined with each other for a full-scale test, the number of tests is 55=3,125. In order to reduce the number of tests and ensure the accuracy and scientifically in the statistical analysis process, the orthogonal design was used to calculate and analyze the optimization test process of the structural parameters of the three-phase hydrocyclone. The orthogonal design is an efficient, fast, and concise mathematical statistical method that adopts standardized orthogonal table and scientifically arranges and analyzes multi-factor problems according to the equilibrium discrete orthogonal principle (Zhong et al., 2019; Chen, 2020).
In the process of orthogonal design, the orthogonal table with six factors and five levels was selected according to the number of factors and levels. Each factor was set as a single column, and an empty column was set as reflect the error caused by random factors. Therefore, L25(56) orthogonal table was selected, as shown in Supplementary Table S2. Numerical simulations were carried out for a total of 25 combinations of structural parameters from OD1 to OD25 according to Supplementary Table S2. Defined the dimensionless parameter E as the criterion for evaluating the separation efficiency of different combinations of structural parameters, and E is the sum of the ratio of gas outlet discharge to inlet gas injection and the ratio of sand outlet discharge to inlet sand injection, as shown in Eq. 11.
The results of orthogonal design were analyzed by direct analysis and analysis of variance, and the effect degree of different factors on orthogonal design results and the optimal factor combination case were obtained. Meanwhile, by calculating the mean square of each factor and the mean square of the empty column respectively, and comparing the mean square of each factor with the mean square of the empty column, a factor that was less than the mean square of the empty column was classified as an error column. Finally, the optimal structure parameters combination was obtained, and the effect degree of each factor on the results of the orthogonal design was evaluated.
Secondly, taking the three-phase hydrocyclone with the optimal parameters combination as the basic case. The control variable method based on single factor analysis was used to study the effect of single structural parameter change on the internal flow field characteristics of three-phase hydrocyclone. In this study, the numerical simulation was also used to study the effects of the four structural parameters which included gas outlet depth length (li), tangential inlet area (s), drain hole height (h), and inverted cone diameter (dz) on the internal flow field characteristics of three-phase hydrocyclone. In order to ensure the universality and accuracy of the research, the level changes of each structural parameter were evenly distributed, as shown in Supplementary Table S3.
In the process of using numerical simulation to study the effect of structural parameters change on flow field characteristics, Case 1 was set as the basic case. Among all 13 Cases, the tangential inlet area (s) of Case2–Case4 range from 2 mm2 × 12 mm2–8 mm2 × 18 mm2, and the inverted cone diameter (dz) of Case5–Case7 range from 24 to 36 mm. The gas outlet depth length (li) of Case8–Case10 range from 20 to 32 mm, and the drain hole height (h) of Case11–Case13 range from 10 to 15 mm. These cases were used to study the effects of the tangential inlet area (s), the inverted cone diameter (dz), gas outlet depth length (li), and the drain hole height (h) on the distribution characteristics of the internal flow field of three-phase hydrocyclone.
According to the principle of cyclone separation, the mixture is injected into the three-phase hydrocyclone from the tangential inlets and makes a circular motion in the spin chamber. And in this study, the numerical simulation was carried out base on a three-dimensional physical model, so the characteristics of the flow field on any axial section were consistent. In the analysis of the internal flow field, the X-Y section was selected as the analysis section. The mixture formed a strong swirl in the spin chamber, and the gas was discharged under the action of the inverted cone and the depth section of the gas outlet. Meanwhile, the density difference between the liquid and the solid leads to the centrifugal force difference in the circular motion, thus realizing the preliminary separation of the solid and liquid in the spin chamber. According to the orthogonal design in Supplementary Table S2, the maximum of gas outlet depth length (li) and inverted cone length (lz) were 32 mm and 108 mm, respectively. Therefore, in order to analyze the flow field distribution characteristics of different phases between the end of the gas outlet tube and the tip of the inverted cone, the monitoring line LAm, LBm, LCm was set at an equal distance of 43, 63, and 83 mm from the top of the spin chamber. In the process of separation, the liquid entered the inverted cone through the drain hole and was discharged through the water outlet at the bottom of hydrocyclone. The sand moved downward along the outer surface of the inverted cone and was discharged through the sand outlet at the bottom of the spin chamber. In order to monitor the separation results of liquid and sand, a monitoring line LDm was set up at the bottom of the spin chamber. The position of the analysis section and the monitoring lines was shown in Supplementary Figure S2.
Finally, by analyzing the distribution and changing trend of velocity field, CH4 volume fraction and water volume fraction on the analysis section and the monitoring line, thus the effect of the change of structural parameters on flow field distribution and separation efficiency were obtained. In this study, in order to ensure the accuracy of the visibility of the numerical simulation results, the Ansys’s post-processing software was used to process the simulation results, and the ratio of chart processing size to model size was 1:1.
During the meshing process, the physical model was meshed with four levels of 549618, 670520, 782246, and 869326 respectively. The static pressure distribution on monitoring line LAm was analyzed under different grid levels, as shown in Supplementary Figure S3. The static pressure distribution curve with grid levels of 549618, 670520, 782264 was polynomial fitted, and the correlation coefficient R2 was 0.9954. It is proved that the number of grids has little effect on the numerical simulation results under these levels of grid number. When the number of grids is 869326, the static pressure distribution on monitoring line LAm changes greatly. In order to reduce calculation time and ensure the accuracy of numerical simulation, the fluid domain of three-phase hydrocyclone was divided into about 670000 grid elements, and the grid generation results is shown in Supplementary Figure S4.
The experimental results of Xu were used to verify the accuracy of the numerical simulation. The experimental platform was designed according to the actual situation of the construction site, so the numerical calculation model reestablished according to Xu’s experimental situation in this paper. The spin chamber length of the three-phase hydrocyclone is 238 mm, the main diameter is 45 mm, the inverted cone length is 96 mm, the drain hole height is 10 mm, and the tangential inlet area is 4 mm2 × 14 mm2. Other structural parameters are consistent as those of the experimental device. In the experiment, the flow rate was set as 4.83 m3/h, and the pressure drop distribution was studied when the flow ratio of the gas outlet varies in the range of 56%–64%. Therefore, the Reynold stress model and the Mixture model were used in the numerical simulation and the same physical model and boundary conditions were established as in the experiment. The distribution of the experimental results and numerical simulation results of the gas outlet pressure drop under the condition of the gas outlet flow ratio varies from 56% to 64% is shown in Supplementary Figure S5. As shown in Supplementary Figure S5, the overall smaller numerical simulation results compared to the experimental results were due to the simplification of the real process of separation in the numerical simulation. A polynomial fit between the experimental results and numerical simulation was carried out, the correlation coefficient R2 was 0.942. This verified the accuracy of the numerical simulation results.
The separation efficiency criterion E of OD1-OD25 was calculated by Eq. 11, and the E of 25 groups was obtained as shown in Supplementary Figure S6. As shown in Supplementary Figure S6, the maximum value of E for OD20 is 1.46 and the minimum value of E for OD24 is 1.1. According to the distribution results of E, when the combination of factors is A4B5C1D4E2, that is when the gas outlet depth length is 28 mm, the tangential inlet area is 2 mm2 × 12 mm2, the inverted cone diameter is 28 mm, the inverted cone length is 108 mm, and the drain hole height is 20 mm, the sum of the ratio of gas outlet discharge to inlet gas injection and the ratio of sand outlet discharge to inlet sand injection is the largest of three-phase hydrocyclone. The separation efficiency of the hydrocyclone is the largest under this structure factors combination.
In order to verify the distribution results of the above E and study the effect of a certain level of a single factor on the test results, Kx was defined as the sum of the test results of the level number is x which belongs to a certain factor column. For example, K1 represents the sum of the E of all the test results with the level number 1 in a single factor column. In order to study the effect of the level change of various factors on the test results, R was defined as the range. Where a larger R for a factor indicates that the level of that factor has a greater effect on the test results. R can be expressed as Eq. 12.
The Kx and R of each factors of OD1-OD25 were calculated, and the results as shown in Supplementary Table S4.
In the orthogonal design of this paper, the separation efficiency of the three-phase hydrocyclone was evaluated by the E. The larger the E is, the higher the comprehensive efficiency of the gas and water discharge of the hydrocyclone is, that is, the higher the separation efficiency is. As shown in Supplementary Table S4, the distribution of Kx in A (li) factor column is K4> K3> K1> K2> K5, in B (lz) factor column is K5> K1> K2> K3> K4, in C(s) factor column is K1> K3> K2> K4> K5, in D (h) factor column is K4> K3> K2> K5> K1, in E (dz) factor column is K2> K1> K3> K4> K5. According to the calculation results of Kx, the optimal factor combination can be obtained as A4B5C1D4E2. The calculation results of Kx is consistent as that of Eq. 11, which shows that the separation efficiency is the highest when the gas outlet depth length is 28 mm, the tangential inlet area is 2 mm2 × 12 mm2, the inverted cone diameter is 28 mm, the inverted cone length is 108 mm, and the drain hole height is 20 mm. The calculation accuracy of Eq. 11 is also verified.
The R of each factors in Supplementary Table S4 was analyzed. The R of factor B (lz) is less than that of empty column, indicating that the effect of factor B (lz) on the orthogonal design results is less than that of the test error, and the change of level cannot have a significant effect on the orthogonal design results. Therefore, factor B (lz) is classified as error. The R of factor A(li), C(s), D(h), and E(dz) are larger than that of empty column, indicating that these four factors have a significant effect on the orthogonal design results. Among them, RC>RE>RD>RA, it is proved that the tangential inlet area has the most significant effect on the separation efficiency, and gas outlet depth length has the least effect on the separation efficiency of the three-phase hydrocyclone.
In order to analyze the error of the orthogonal design and accurately estimate the significance of each factor on the orthogonal design, the analysis of variance of the orthogonal design results was carried out.
In the process of carrying out the orthogonal design, the change of the factor level and the test error is the main reason for the difference between the orthogonal design results. In order to reflect the overall difference of the orthogonal design results, SST was defined as the total sum of squares of deviation. The larger the SST is, the greater the difference of each orthogonal design results. SST can be expressed as Eq. 13.
The sum of the squares of the deviations of each factor was defined as SSj (j = A, B, C, D, E, and Empty column). SSj can be expressed as Eq. 14.
In Eqs 13, 14,
The total sum of squares of deviation was calculated by using Eq. 13, and SST was obtained of 0.1567, and the sum of squares of deviation of each factors were calculated by using Eq. 14, the SSA, SSB, SSC, SSD, SSE, SSEmpty column were obtained of 0.0156, 0.0079, 0.0571, 0.0148, 0.0473, and 0.014, respectively.
Because the empty column was set as reflect the error caused by random factors in the orthogonal design process. In the aforementioned direct analysis, the R of factor B was 0.217, which was smaller than that of the empty column of 0.294. In the calculation of sum of squares of deviation, the SSB was 0.0079 which was smaller than SSEmpty column of 0.014. It indicates that the effect of factor B on the results of orthogonal design is less than that of error on the results of orthogonal design, so factor B is classified as error. The sum of squares of deviation of the test error was defined as SSerror, and it was calculated as shown in Eq. 19.
The total freedom degree of the sum of total deviation square was defined as dfT, the freedom degree of the deviations square sum of each factor was defined as dfj, and the freedom degree of error was defined as dferror. The dfT, dfj, dferror can be expressed as Eqs 20–22.
The total freedom degree was calculated by using Eq. 20, and dfT was obtained of 24. The freedom degree of each factors were calculated by using Eq. 21, and dfA, dfB, dfC, dfD, dfE, dfEmpty column were obtained of 4. The freedom degree of error was calculated by using Eq. 22, and dferror was obtained of 8.
The mean square of each factor was defined as MSj (j = A, B, C, D, E, Empty column). The mean square of error was defined as MSerror. MSj, and MSerror can be expressed as Eqs 23, 24.
The mean square of each factor were calculated by using Eq. 23, and MSA, MSB, MSC, MSD, MSE, MSEmpty column were obtained of 0.0039, 0.0020, 0.0143, 0.0037, 0.0118, 0.0027, respectively. According to the calculation results of Eq. 23, MSB = 0.0020 is less than MSEmpty column = 0.0035. Therefore, factor B is classified as error, which is consistent as the result of intuitive analysis and the result of sum of squares of deviations calculation.
The mean square of error was calculated by using Eq. 24, the MSerror was obtained of 0.0027.
The F of each factors was defined as Fj (j = A, C, D, E), Fj can be expressed as Eq. 25.
Calculated from Eq. 25, FA = 1.4261, FC = 5.2085, FD = 1.3536, FE = 4.3135.
For the given significance level α, the significance of each factor was tested by comparing the Fj and F. If the Fj is greater than Fα (dfj, dfe), it is proved that this factor has a significant effect on the results of orthogonal design. Therefore, in this paper four levels of α = 0.025, α = 0.05, 0.95, and α = 0.975 were chosen to carry out the significance test. By querying the F distribution table, it was found that F0.025 (4,8) = 5.05, F0.05(4,8) = 3.84, F0.95(4,8) = 0.166, F0.975(4,8) = 0.111. The significance test results were compared, as shown in Supplementary Table S5.
As shown in Supplementary Table S5, FA, FC, FD, FE are all greater than Fα. According to the principle of significance test, A(li), C(s), D(h), E(dz) all have significant effect on the results of orthogonal design. Among them, the factor C(s) has the most significant effect on the results of the orthogonal design, and the results of the analysis of variance are consistent with the results of the direct analysis.
The structural parameters of the three-phase hydrocyclone applicable to solid fluidization exploitation of NGH were optimized by the orthogonal design, and the results of orthogonal design were verified by the direct analysis and the analysis of variance. The test results showed that the gas outlet depth length, the tangential inlet area, the drain hole height, and the inverted cone diameter all had a significant effect on the separation efficiency of the three-phase hydrocyclone. Among them, the effect significance of each factor on the separation efficiency of three-phase hydrocyclone was s>dz>h>li. At the same time, the dimensionless parameter E for evaluating the separation efficiency was defined by synthesizing the efficiency of water and sand discharge of the three-phase hydrocyclone. Taking E as the evaluation criterion, it was obtained that when the gas outlet depth length was 28 mm, the tangential inlet area was 2 mm2 × 12 mm2, the inverted cone diameter was 28 mm, the inverted cone length was 108 mm, and the drain hole height was 20 mm, the separation efficiency of hydrocyclone separator was the optimal.
In the aforementioned study, the orthogonal design was used to optimize the structural parameters based on the conventional three-phase hydrocyclone, and the optimal combination of structural parameters of three-phase hydrocyclone applicable to solid fluidization exploitation of NGH was obtained. In order to study the effect of the individual structural parameters changes on the separation performance. Based on the significance of the effects of different structural parameters on the separation efficiency obtained from the orthogonal design results, the effect of four structural parameters of s, dz, li, and h on the velocity field, CH4 volume fraction and water volume fraction distribution law in the flow field were investigated by numerical simulation.
When the s of the three-phase hydrocyclone changes, the tangential velocity distribution in the flow field is shown in Supplementary Figure S7. In Supplementary Figures S7A,B,C show the results of tangential velocity distribution at monitoring line LAm, LBm, LCm, respectively. As shown in Supplementary Figure S7A, the tangential velocity distribution of Case1–Case4 on monitoring line LAm shows a symmetrical distribution law that increases gradually from the axis to the sidewall with the axial position x = 0 as the symmetrical center. It indicates that the NGH slurry makes a circular motion around the axis after entering the spin chamber of hydrocyclone from the tangential inlets. However, due to the wall surface roughness of spin chamber was set as 0 and the wall surface had no slip during the numerical simulation, the tangential velocity decreases sharply near the radial position of ±22.5 mm. The maximum tangential velocity of Case 1 in circular motion is 13.65 m, and the maximum tangential velocity of Case 4 in circular motion is 4.80 m/s. The difference between the maximum tangential velocity of Case 1 and that of Case 4 is 8.85 m/s. It is proved that the circular motion of hydrate slurry is the fastest in the spin chamber when s is 2 mm2 × 12 mm2, which leads to greater difference of centrifugal force between different phases and better precision of separation. Meanwhile, according to the distribution law shown in Supplementary Figure S7A, under the same flow rate, the incident velocity of the hydrate slurry at the tangential inlets decrease gradually with the increase of s, which leads to the decrease of the maximum tangential velocity of each case on monitoring line LAm. However, the maximum tangential velocity appears near the radial position of ±21.3 mm, which proves that the increase of s has no significant effect on the distribution position of the tangential velocity.
Supplementary Figure S7B shows the distribution of tangential velocity on monitoring line LBm with different s of hydrocyclone. Compared with the distribution of the tangential velocity on monitoring line LAm, the positional distribution of the tangential velocity on monitoring line LBm does not change, but the maximum tangential velocity in each case has decreased. The maximum tangential velocity of Case1–Case4 decreases 11.72, 7.31, 5.46, and 4.27 m/s respectively. Among them, the tangential velocity reduction of Case 1 is maximum of 1.93 m/s, and the tangential velocity reduction of Case 4 is minimum of 0.53 m/s.
The distribution of tangential velocity on monitoring line LCm under different s conditions is shown in Supplementary Figure S7C. The maximum tangential velocity of Case1–Case4 on monitoring line LCm is 9.99, 6.41, 4.88, and 3.90 m/s, respectively. Compared with the tangential velocity distribution on monitoring line LAm, 3.66, 2.08, 1.27, and 0.9 m/s are decreased respectively. Within the axial range of 43–83 mm from the top of the three-phase hydrocyclone, the tangential velocity decrease of Case1 is the largest, and the tangential velocity decrease of Case4 is the least. The maximum tangential velocity is distributed near the radial position of ±21.3 mm, which proves that the position of the maximum tangential velocity distribution is not affected by s in the axial distance.
The axial velocity distribution in the flow field is shown in Supplementary Figure S8. As shown in Supplementary Figure S8A, the axial velocity on monitoring line LAm shows a distribution law from increasing to decreasing to increasing again from the edge to the axial center of the flow field. The rapid increase of the axial velocity near the edge of the flow field from 0 m/s is due to the fact that the boundary conditions of the spin chamber wall was set to be no wall slip and the roughness is 0 during the numerical simulation. In Case1–Case4, the maximum axial velocity appears at the radial position of 0 mm, and the maximum axial velocity of Case1 is 4.35 m/s. It shows that the axial velocity of the fluid in the flow field is the fastest at the axis of the spin chamber of the three-phase hydrocyclone. As shown in Supplementary Figure S8A, the Case1–Case4 appears a “reverse flow” moving toward the gas outlet near the axis of the flow field with the zero axial velocity line as the dividing line. The “reverse flow” of Case1–Case4 is distributed in the range of the radial position of ±15.3, ±14.2, ±13.5, and ±12.7 mm, respectively. Because the fluid domain in the spin chamber is cylindrical, the position where the Case1–Case4 “reverse flow” occurs can be regarded as a circle with a radius of 15.3, 14.2, 13.5, and 12.7 mm, respectively. On monitoring line LAm, the distribution range of the “reverse flow” of Case1 is the largest in the radial position, and that of Case4 is the smallest in the radial position.
The axial velocity distribution on monitoring line LBm is shown in Supplementary Figure S8B. Because the inverted cone is fixed in the axial position of the flow field of the three-phase hydrocyclone. The axial velocity of Case1 and Case2 is affected by the inverted cone, which shows a small decrease near the radial position of 0 mm. The axial velocity distribution of Case3 and Case4 is not affected by the inverted cone. However, compared with monitoring line LAm, the maximum axial velocity of each case on monitoring line LBm decreases 0.92, 0.92, 1.19, and 1.14 m/s respectively. Similarly, the “reverse flow” of Case1–Case4 is distributed in the circular flow field with a radius of 13.3 mm with the zero axial velocity line as the dividing line. Compared with the axial velocity distribution on monitoring line LAm, the “reverse flow” radius of Case1–Case3 distribute on monitoring line LBm decrease 2, 0.9 and 0.2 mm, respectively. And the “reverse flow” radius of Case4 distributes on monitoring line LBm increases 0.6 mm.
Supplementary Figure S8C shows the axial velocity distribution curve on monitoring line LCm. The axial velocity distribution of Case1–Case4 at the axis is decreased by the effect of inverted cone, and the position of the maximum axial velocity in each case tends to approach the radial center with the increase of s. The maximum axial velocities of Case1 and Case4 at radial positions of 5.4 mm and 4.69 mm are 3.11 m/s and 1.27 m/s, respectively, which decreases 0.5 m/s and 0.59 m/s compared with monitoring line LAm. As shown in Supplementary Figure S8C, although the axial velocity of the “reverse flow” at the axis of each case has decreased, its minimum value is still greater than that of the 0 m/s, indicating that the “reverse flow” still exists in the position of monitoring line LCm. At this time, the radius of “reverse flow” in each case is roughly the same, but it is decreased compared with that in the position of monitoring line LAm. It indicates that the axial velocity decreases and the distribution range decreases gradually with the increase of axial distance.
As shown in Supplementary Figures S9A,B,C, in order to study the effect of hydrocyclone with different s on the distribution of CH4 in the flow field, the volume fraction distribution of CH4 on monitoring lines LAm, LBm, and LCm were analyzed. On monitoring line LAm, the volume fraction of CH4 of Case1 is maximum of 12.4%, and the volume fraction of CH4 of case 4 is minimum of 11.9%. The CH4 volume fraction of case1 in the radial range of ±22 mm is higher than 10%, which proves that CH4 accumulates in the axial position of 43 mm and radial range of ±22 mm. The volume fraction of CH4 in the radial range of ±20.1 mm, ±19.2 mm, ±18.5 mm of Case2–Case4 is higher than 10%, and the radial accumulation range is smaller than that of Case1. That is, with the increase of s from 2 mm2 × 12 mm2 to 8 mm2 × 18 mm2, the tangential velocity and axial velocity gradually decrease, and the volume fraction of CH4 at monitoring line LAm gradually decreases, but the CH4 accumulation position is closer to the axis.
The CH4 volume fraction distribution on monitoring line LBm under different s conditions is shown in Supplementary Figure S9B. The distribution of CH4 volume fraction at monitoring line LBm is roughly the same as that at monitoring line LAm. The volume fraction of CH4 in the radial range of ±21.4 mm of Case 1 is more than 10%, and this distribution range is larger than that of Case 2–Case 4. At the same time, the minimum CH4 volume fraction of Case 1 at the edge is 9.23%, which is higher than that of other cases at the edge. It is proved that when s is 2 mm2 × 12 mm2, it has the most significant effect on the distribution of CH4 in the flow field at the axial position of 63 mm.
Supplementary Figure S9C shows the CH4 volume fraction distribution on monitoring line LCm under different s conditions. On monitoring line LCm, the maximum CH4 volume fraction of Case 1–Case 4 are all 12.5% and are all located at the radial position of 0 mm. Compared with monitoring lines LAm and LBm, the maximum CH4 volume fraction of Case 2–Case 4 increase by 0.2%, 0.3%, and 0.6%, respectively. It indicates that as the axial distance from the top of the three-phase hydrocyclone increases from 43 to 83 mm, the accumulation of CH4 in Case2–Case4 also increases gradually. However, the CH4 volume fraction in the radial range of ±20.4 mm of Case1 is more than 10%, and the distribution range is still larger than that of Case2–Case4. It shows that at monitoring line LCm, when s is 2 mm2 × 12 mm2, it has the most significant effect on the distribution of CH4 in the flow field.
The water volume fraction distribution on monitoring line LDm under different s conditions is shown in Supplementary Figure S10. In Case1–Case4, in order to compare with Case2–Case4, taking Case1 as basic case according to the results of orthogonal design. It can be seen from Supplementary Figure S10 that the water volume fraction distribution of Case3 and Case1 on monitoring line LDm is roughly the same, indicating that the separation efficiency of the three-phase hydrocyclone is the same when the other structural parameters are the same and the tangential inlet area is 2 mm2 × 12 mm2 and 6 mm2 × 16 mm2, respectively. The water volume fraction of Case1 on monitoring line LDm is 69.9%. Compared with the water volume fraction of Case1, the water volume fraction of Case4 increased by 5.5% with a maximum of 75.4% at monitoring line LDm. It indicates that the distribution of water is the most concentrated and the water volume fraction is the largest when the tangential inlet area is 8 mm2 × 18 mm2.
The curves of the effect of three-phase hydrocyclone with different dz on the tangential velocity distribution in the flow field are shown in Supplementary Figure S11. Case1 is set as the basic case and Case5–Case7 is set as the variation group. The tangential velocity changes on monitoring lines LAm, LBm, and LCm were analyzed. As shown in Supplementary Figure S9, the maximum tangential velocity of each case at different monitoring line positions all appear at the edge of the flow field and shows the characteristics of central symmetrical distribution with the radial position of 0 mm as the symmetry center. From the local enlargement, we can see that the tangential velocity of different cases on the same monitoring line is roughly the same, but the tangential velocity of the same case is different on different monitoring lines, and the maximum tangential velocity shows the distribution law of decreasing from monitoring line LAm to LCm. In each case, the tangential velocity is distributed about 13.6 m/s at monitoring line LAm and about 9.98 m/s at monitoring line LCm, and the maximum tangential velocity decreases 3.62 m/s. It indicates that the decrease of tangential velocity is due to the increase of axial distance, and dz has no significant effect on tangential velocity in the flow field.
The axial velocity distribution of Case1 and Case5–Case7 on each monitoring line under different dz conditions is shown in Supplementary Figure S12. When the axial velocity is greater than 0 m/s and the axial position is within the range of monitoring line LAm to LCm, the axial velocity at the edge of the flow field of each case decreases gradually under different dz conditions, but the axial velocity distribution is the same in other positions. It shows that when the axial velocity is greater than 0 m/s, the axial position will affect the axial velocity distribution, but dz will not affect the axial velocity. It indicates that when the axial velocity is greater than 0 m/s, the axial velocity distribution will be affected by the change of axial position, but the axial velocity will not be affected by dz. When the axial velocity is less than 0 m/s, the axial velocity at the center of the flow field decreases gradually as the axial distance from the top of the three-phase hydrocyclone increases from 43 to 83 mm within the axial range of monitoring line LAm to LCm. The maximum axial velocities of Case1 and Case5–Case7 at monitoring line LAm are 4.35, 3.55, 4.0, and 3.91 m/s, respectively, and at monitoring line LCm, the axial velocities of each case at the radial position of 0 mm are 1.13, 1.15, 0.54, and 0.34 m/s respectively. Among them, the axial velocity decrease of Case7 is the largest, indicating that the axial velocity in the flow field is affected most when dz is 36 mm.
The CH4 distribution on each monitoring line in the flow field under different dz conditions is shown in Supplementary Figure S13. The CH4 volume fraction of Case1 and Case5–Case7 decreases gradually from the radial center to the edge on each monitoring line. It indicates that during the circular motion of the hydrate slurry in the spin chamber, the centrifugal force is the smallest due to the smallest density of CH4, so that the CH4 is distributed at the center of the axis. From the local enlargement, it is known that in the axial range between monitoring line LAm and LCm, with the increase of the axial distance, the CH4 volume fraction increases gradually at the radial position of 0 mm, and the CH4 volume fraction of each case reaches the maximum at monitoring line LCm. On monitoring line LCm, the CH4 volume fraction of Case5 is minimum of 12.46%, the CH4 volume fraction of case 7 is maximum of 12.49%. The CH4 volume fraction distribution increases with the increase of dz. It indicates that under the condition that other structural parameters are the same, the increase of the inverted cone diameter reduces the fluid domain between the spin chamber side wall and the inverted cone, and causes the hydrate slurry to move along the surface of the inverted cone, thus increasing its circular motion radius, and then increasing the centrifugal force to promote the separation efficiency of the CH4.
In order to study the effect of the change of structural parameters dz on water separation, the water volume fraction distribution curves on monitoring line LDm under different dz conditions as shown in Supplementary Figure S14. In Case1 and Case5–Case7, the dz of Case5 is minimum of 24 mm and the dz of case 7 is maximum of 36 mm. As shown in Supplementary Figure S14, with the increase of dz from 24 to 36 mm, the water volume fraction at a radial position of 0 mm on monitoring line LDm decrease from 70.7% to 66.3%. It indicates that with the increase of the inverted cone diameter, the annular area between the inverted cone and the side wall of the spin chamber gradually decreases, and there is not enough space to separate the water and sand, resulting in the larger the dz, the lower the water separation efficiency.
The tangential velocity distribution curves in the flow field under different li conditions are shown in Supplementary Figure S15. As shown in Supplementary Figure S15, compared to Case1, there is no significant difference in the tangential velocity distribution of Case8–Case10 on the same monitoring line. It indicates that the change of li has no significant effect on the distribution of tangential velocity in the flow field. The maximum tangential velocity of each case appears near the radial position of ±21.2 mm. As shown in local enlargement, the maximum tangential velocity of Case8–Case10 on monitoring lines LAm, LBm, and LCm are 14.2, 11.9, and 10.2 m/s respectively, which is not significantly different from that of Case1. It also indicates that the change of li has no significant effect on the tangential velocity.
The axial velocity distribution of Case1 and Case8–Case10 on monitoring lines LAm, LBm, and LCm under different li conditions is shown in Supplementary Figures S16A,B,C, respectively. According to the results of orthogonal design and the setting of structural parameters, the li of each case is distributed evenly within 20–32 mm. As shown in Supplementary Figure S16A, as li increases from 20 to 32 mm, the maximum axial velocity on monitoring line LAm increases from 3.46 to 4.75 m/s. It shows that the increase of the gas outlet depth length is beneficial to the movement of the gas to the gas outlet. When the axial velocity is greater than 0 m/s, the axial velocity distribution of each case is the same. It is proved that the change of li only has a significant effect on the axis.
As shown in Supplementary Figure S16B. As the axial distance from the top of the three-phase hydrocyclone increases from 43 to 83 mm, the effect of the change of the structural parameter li on the axial velocity distribution in the flow field is gradually decreased. On monitoring line LBm, the axial velocity of Case1 and Case9-Case10 is about 3.30 m/s at the radial position of 0 mm, but the axial velocity of Case8 is the smallest of 2.69 m/s at the radial position of 0 mm. It indicates that when li is 20 mm, its effect on the axial motion of the gas in the flow field is weakened obviously.
The axial velocity distribution on monitoring line LCm is shown in Supplementary Figure S16C. With the increase of axial distance, the effect of gas outlet depth length on the flow field gradually disappears. On monitoring line LCm, under the condition of the same other structural parameters of Case1 and Case8–Case10, the effect of li on the flow field is weakened, and there is no significant difference in the axial velocity distribution of each case.
The CH4 distribution on monitoring line under different li conditions is shown in Supplementary Figure S17. On each monitoring line, CH4 shows the distribution law of accumulation in the radial center, and the CH4 volume fraction is more than 10% in the radial range of ±20.9 mm. However, there is no significant difference in the CH4 volume fraction distribution under different li conditions on the same monitoring line, indicating that the change of structural parameters li has no significant effect on the CH4 volume fraction distribution in the flow field.
Supplementary Figure S18 shows the water volume fraction distribution curves on monitoring line LDm under different li conditions. As shown in Supplementary Figure S18, the water volume fraction distribution of Case1 and Case8–Case10 on monitoring line LDm is the same, showing the distribution characteristics of increasing gradually from the edge to the axis. The maximum water volume fraction is 70.2% at the radial position of 0 mm. It shows that the change of the structural parameter li has no significant effect on the separation of the water phase.
Supplementary Figure S19 shows the tangential velocity distribution under different h conditions. From the local enlargement in Supplementary Figure S19, it can be seen that the maximum tangential velocity shows a gradual decrease in the axial distance of 40 mm from monitoring line LAm to monitoring line LCm. However, the tangential velocity also shows the distribution characteristic that is not affected by h on the same monitoring line. It indicates that the change of h has no significant effect on the radial separation of gas-liquid-solid mixture.
The axial velocity distribution of Case1 and Case11–Case13 on different monitoring lines under different h conditions is shown in Supplementary Figure S20. When the axial velocity is less than 0 m/s, the axial velocity at the edge of the same monitoring line is the same in different cases, but with the increase of the axial position, the axial velocity at the edge decreases gradually. When the axial velocity is less than 0 m/s, in the axial range between monitoring line LAm and LCm, as the axial distance from the top of the three-phase hydrocyclone increases from 43 to 83 mm, the axial velocity decreases gradually at the radial center. However, the axial velocity distribution on the same monitoring line is not affected by the change of the structural parameter h. It indicates that the drain hole height only affects the transport of the separated phase, but it has no effect on the velocity distribution in the flow field and the separation process of multiphase.
Supplementary Figure S21 shows the CH4 distribution curve on monitoring line under different h conditions. Because the parameter h is the height of the drain hole, and the drain hole is the tangential inlets arranged on the inverted cone structure. According to the structural characteristics of the drain hole, it will not affect the circular motion of the fluid in the flow field. Therefore, when other structural parameters are the same, the change of h has no significant effect on the CH4 distribution in the flow field. However, due to the centrifugal force difference caused by the density difference between different phases in the circular motion, the CH4 still moves toward the radial center, and the maximum CH4 volume fraction appears at the radial position of 0 mm at different monitoring lines.
The water volume fraction distribution on monitoring line LDm under different h conditions is shown in Supplementary Figure S22. Among Case1 and Case11–Case13, Case11 has the largest water volume fraction on monitoring line LDm, and the maximum water volume fraction of Case11 is 77.9% at the radial position of 0 mm. Compared with Case1, the water volume fraction of Case12 and Case13 has no obvious change, and the maximum water volume fraction distribution are all about 70.5%. It shows that h = 10 mm is the optimal structure parameter for the separated water to enter the drain hole, and the hydrate slurry is separated completely at this position. When h is greater than 10 mm, the position of the drain hole is close to the top of the three-phase hydrocyclone, where the hydrate slurry has not been completely separated, and the water will carry part of the sand phase into the drain hole, so that the mixture discharged from the water outlet contains sand.
In this paper, the optimal structural parameter combination of the three-phase hydrocyclone applicable to solid fluidization exploitation of NGH was obtained. The effect of the optimized structural parameters on the internal flow field characteristics of the three-phase hydrocyclone was studied. Based on the above results and discussion, the following conclusions were drawn.
(1) By using the orthogonal design, the structure optimization was carried out based on the conventional three-phase hydrocyclone and defined the dimensionless parameter E as the criterion of separation efficiency. The effect significance of different structural parameters on separation efficiency from high to low was: s>dz>h>li. When the maximum E was 1.46, the optimal structural parameters combination was that the tangential inlet area(s) was 2 mm2 × 12 mm2, the inverted cone diameter (dz) was 28 mm, the drain hole height (h) was 20 mm and the gas outlet depth length (li) was 28 mm. A new structure of hydrocyclone applicable to solid fluidization exploitation of NGH was obtained, which provides a reference for the engineering practice of hydrate slurry separation.
(2) When the s was in the range from 2 mm2 × 12 mm2 to 8 mm2 × 18 mm2, the tangential velocity, axial velocity and CH4 volume fraction in the flow field were all negatively correlated with the s. The three parameters all reached the maximum when the s was 2 mm2 × 12 mm2, in which the tangential velocity was 13.65 m/s, the axial velocity was 4.35 m and the CH4 volume fraction was 12.4%. The water volume fraction distribution was positively correlated with s. When the s was 8 mm2 × 18 mm2, the water volume fraction at the water outlet was 75.4%. Therefore, if the water separation efficiency is improved, it is suggested that the s should be set as 8 mm2 × 18 mm2.
(3) When the dz was 36 mm, the maximum attenuation of axial velocity was 3.57 m/s, the maximum CH4 volume fraction was 12.46% and the minimum water volume fraction was 66.3%. The change of dz has no significant effect on tangential velocity. Therefore, when the flow rate is constant in engineering practice, the separation efficiency of water and CH4 can be adjusted by changing the dz.
(4) The change of li had no effect on the tangential velocity, CH4 volume fraction distribution and water volume fraction distribution in the flow field. The axial velocity increases with the increase of li and reaches the maximum of 4.75 m/s when the li was 32 mm. The li had a significant effect on the axial migration of CH4. In engineering practice, the li should be appropriately increased to improve the separation efficiency of CH4.
(5) The h had on effect on the tangential velocity, axial velocity and CH4 volume fraction distribution in the flow field. With the increase of the h, the water volume fraction of the water outlet decreased gradually. When the h was 10 mm, the water volume fraction of the water outlet was maximum of 77.9%. The h had no significant effect on the flow field distribution, but different h had a significant effect on monitoring the separation position and separation efficiency of the water in engineering practice.
The original contributions presented in the study are included in the article/Supplementary Material, further inquiries can be directed to the corresponding author.
NW: Resources, project administration, funding acquisition. YQ: Conceptualization, methodology, software, formal analysis, data curation, writing-original draft, writing-review and editing. AL: Investigation. JZ: Project administration, funding acquisition. LZ: Project administration, funding acquisition. JX: Investigation, visualization.
The research is funded by National Natural Science Foundation of China (No. U20B6005-05), National Key Research and Development Program (No. 2021YFC2800903), 111 Project (No. D21025), Open Fund Project of State Key Laboratory of Oil and Gas Reservoir Geology and Exploitation (No. PLN2021-01, PLN2021-02, PLN2021-03), High-end Foreign Expert Introduction Program (No. G2021036005L), National Natural Science Foundation of China (No. 51874252).
Author AL is employed by Geological Explorations and Development Institute, Chuan Qing Drilling Engineering Company Limited.
The remaining authors declare that the research was conducted in the absence of any commercial or financial relationships that could be construed as a potential conflict of interest.
All claims expressed in this article are solely those of the authors and do not necessarily represent those of their affiliated organizations, or those of the publisher, the editors and the reviewers. Any product that may be evaluated in this article, or claim that may be made by its manufacturer, is not guaranteed or endorsed by the publisher.
The Supplementary Material for this article can be found online at: https://www.frontiersin.org/articles/10.3389/feart.2022.991208/full#supplementary-material
Aminnaji, M., Tohidi, B., Burgass, R., and Atilhan, M. (2017). Gas hydrate blockage removal using chemical injection in vertical pipes. J. Nat. Gas Sci. Eng. 40, 17–23. doi:10.1016/j.jngse.2017.02.003
Bu, F. X., Liu, Y., Liu, Y. B., Xu, Z., Chen, S. Q., Jiang, M. H., et al. (2021). Leakage diffusion characteristics and harmful boundary analysis of buried natural gas pipeline under multiple working conditions. J. Nat. Gas Sci. Eng. 94, 104047. doi:10.1016/j.jngse.2021.104047
Chang, Y. L., Ti, W. Q., Wang, H. L., Zhou, S. W., Li, J. P., Wang, G. R., et al. (2021). Hydrocyclone used for in-situ sand removal of natural gas-hydrate in the subsea. Fuel 285, 119075. doi:10.1016/j.fuel.2020.119075
Chen, B. B., Sun, H. R., Li, K. H., Wang, D. Y., and Yang, M. J. (2019). Experimental investigation of natural gas hydrate production characteristics via novel combination modes of depressurization with water flow erosion. Fuel 252, 295–303. doi:10.1016/j.fuel.2019.04.120
Chen, X. P., Shen, Q., Ma, X. C., Li, A., and Zhan, M. (2020). Overview of natural gas hydrate test mining at domestic and Foreign. Guangdong Chem. Ind. 47, 95–96.
Chen, Z. (2020). Design and simulation research of wellhead oil-water-sand cyclone. dissertation/master's thesis. Jingzhou: Yangtze University.
Chong, Z. R., Yang, S. H. B., Babu, P., Linga, P., and Li, X. S. (2016). Review of natural gas hydrates as an energy resource: Prospects and challenges. Appl. Energy 162, 1633–1652. doi:10.1016/j.apenergy.2014.12.061
Chuang, J., Ahmadi, G., and Smith, D. H. (2001). Natural gas production from hydrate decomposition by depressurization. Chem. Eng. Sci. 56, 5801–5814. doi:10.1016/s0009-2509(01)00265-2
Cui, Y. D., Lu, C., Wu, M. T., Peng, Y., Yao, Y. B., and Luo, W. J. (2018). Review of exploration and production technology of natural gas hydrate. Adv. Geo-Energy Res. 2, 53–62. doi:10.26804/ager.2018.01.05
Dong, H., Wu, K. S., Kuang, Y. C., and Dai, M. L. (2018). Study on separation law of hydrate slurry in hydrocyclone based on CFD-DEM. J. Zhejiang Univ. Eng. Sci. 52, 11811–11820. doi:10.3785/j.issn.1008-973X.2018.09.023
Elsayed, K., and Lacor, C. (2011). The effect of cyclone inlet dimensions on the flow pattern and performance. Appl. Math. Model. 35, 1952–1968. doi:10.1016/j.apm.2010.11.007
Gao, J. M. (2021). Research on coalescence and breakage characteristics of oil droplets in hydrocyclone under the condition of gas-containing. dissertation/master's thesis. Daqing: Northeast Petroleum University.
Hou, L., Yang, J. H., Liu, Z. X., and Jiao, J. (2021). Current status and suggestions on development of marine gas hydrate technologies in China. World Pet. Ind. 28, 17–22.
Huang, T. (2018). Fundamental theory study on gas-liquid-solid three-phase flow in natural gas hydrate transportation pipelines in deep water. dissertation/doctor's thesis. Chengdu: Southwest Petroleum University.
Jiang, M. H., Li, Y. S., Zhao, L. X., Xu, B. R., and Cheng, Q. L. (2014). Numerical simulation on overflow pipe structure of a degassing/desanding three-phase separation hydrocyclone. Petro-Chemical Equip. 43, 10–13. doi:10.3969/j.issn.1000-7466.2014.05.003
Li, L. S., and Miao, Q. (2014). Review on natural gas hydrate exploration and development technology. Oil Gas Field Dev. 32, 66–71. doi:10.3969/j.issn.1006-553932014.01.018
Liang, L., Sun, J., Yue, M. J., and Geng, H. L. (2020). Comparative analysis of global energy consumption mix in recent ten years. World Pet. Ind. 27, 41–47.
Liu, H., Gao, Y., Pei, X. H., Zheng, G. X., and Zheng, L. C. (2018). Progress and prospect of downhole cyclone oil-water separation with single-well injection-production technology. Acta Pet. Sin. 39, 463–471. doi:10.7623/syxb201804010
Liu, L. L., Li, Y. L., Zhang, X. H., Luo, D. S. H., and Liu, C. L. (2021). Experimental study on gas hydrate system state evolving during depressurization. J. Eng. Geol. 29, 916–1925. doi:10.13544/j.cnki.jep.2021-0695
Qiu, S. Z., Wang, G. R., Wang, G. S., Zhou, S. W., Liu, Q. Y., Zhong, L., et al. (2019). Effects of hydrocyclone separation on purification of natural gas-hydrate slurry and sand remove. Chin. J. Process Eng. 19, 64–72. doi:10.12034/j.issn.1009-606X.218154
Song, M. H., Zhao, L. X., Xu, B. R., Liu, L., and Zhang, S. (2021). Discussion on technology of improving separation efficiency of liquid-liquid hydrocyclone. Chem. Industry Eng. Prog. 40, 6590–6603. doi:10.16085/j.issn.1000-6613.2020-2545
Song, Y. C., Chen, C. X., Zhao, J. F., Zhu, Z. H., Liu, W. G., Yang, M. J., et al. (2015). Evaluation of gas production from methane hydrates using depressurization, thermal stimulation and combined methods. Appl. Energy 145, 265–277. doi:10.1016/j.apenergy.2015.02.040
Song, Y. C., Yang, L., Zhao, J. F., Liu, W. G., Yang, M. J., Li, Y. H., et al. (2014). The status of natural gas hydrate research in China: A review. Renew. Sustain. Energy Rev. 31, 778–791. doi:10.1016/j.rser.2013.12.025
Wan, L. H. (2009). Study on dissociation features of gas hydrate in the presence of chemicals. dissertation/doctor's thesis. Guangzhou: Guangzhou Institute of Energy Conversion, Chinese Academy of Science.
Wang, A., Yan, X. K., Wang, L. J., Cao, Y. J., and Liu, J. T. (2015). Effect of cone angles on single-phase flow of a laboratory cyclonic-static microbubble flotation column: PIV measurement and CFD simulations. Sep. Purif. Technol. 149, 308–314. doi:10.1016/j.seppur.2015.06.004
Wang, B., Fan, Z., Wang, P. F., Liu, Y., Zhao, J. F., and Song, Y. C. (2018). Analysis of depressurization mode on gas recovery from methane hydrate deposits and the concomitant ice generation. Appl. Energy 227, 624–633. doi:10.1016/j.apenergy.2017.09.109
Wang, B. (2019). Study on mining characteristics and effiiciency optimization of naturel gas hydrate resources via depressurization. dissertation/doctor's thesis. Dalian: Dalian University of Technology.
Wang, D. F., Wang, G. R., Zhong, L., and Qiu, S. Z. (2019). Effects of numbers of inlets on characteristics of flow field and separation performance of natural gas hydrate slurry in hydrocyclone. Shipbuild. China 60, 161–169. doi:10.3969/j.issn.1000-4882.2019.04.018
Wang, G. D., He, L. M., Lv, Y. L., and Chen, Z. Y. (2006). Study on oil-water separating behavior of gravity separator. Acta Pet. Sin. 27, 112–115. doi:10.7623/syxb200606025
Wang, H. (2020). Experimental study on separation performance of three-phase cyclone in underground coal mine. dissertation/master's thesis. Qingdao: Shandong University of Science and Technology.
Wang, W. C., Wang, X. Y., Li, Y. X., Liu, S., Yao, S. P., and Song, G. C. (2020). Study on the characteristics of natural gas hydrate crystal structures during decomposition process. Fuel 271, 117537. doi:10.1016/j.fuel.2020.117537
Wang, Y., Feng, J. C., Li, X. S., and Zhang, Y. (2017). Experimental investigation of optimization of well spacing for gas recovery from methane hydrate reservoir in sandy sediment by heat stimulation. Appl. Energy 207, 562–572. doi:10.1016/j.apenergy.2017.06.068
Wei, N., Zhao, J. Z., Sun, W. T., Zhou, S. W., Zhang, L. H., Li, Q. P., et al. (2018). Non-equilibrium multiphase wellbore flow characteristics in solid fluidization exploitation of marine gas hydrate reservoirs. Nat. Gas. Ind. 38, 90–99. doi:10.3787/j.issn.1000-0976.2018.10.013
Wei, N., Zhou, S. W., Cui, Z. J., Zhao, J. Z., Zhang, L. H., and Zhao, J. (2020). Evaluation of physical parameters and construction of a parameter classification system for natural gas hydrate in the northern South China Sea. Nat. Gas. Ind. 40, 59–67. doi:10.3787/j.issn.1000-0976.2020.08.004
Wu, Y. M., and Li, L. Y. (2019). Numerical simulation of inner cone structure of gas-liquid-solid three-phase cyclone separator. Jiangxi Chem. Ind., 101–103. doi:10.14127/j.cnki.jiangxihuagong.2019.02.029
Xu, B. R., Jiang, M. H., and Zhao, L. X. (2017). Effect of production fluid viscosity on the performance of three phase separation hydrocyclone. J. Mech. Eng. 53, 175–182. doi:10.3901/jme.2017.08.175
Xu, Y. X. (2012). Numerical simulation and analysis of the separation process in the hydrocyclone. dissertation/doctor's thesis. Shanghai: East China University of Science and Technology.
Yang, L., Liu, Y. L., Zhang, H. Q., Xiao, B., Guo, X. W., Wei, R. P., et al. (2019). The status of exploitation techniques of natural gas hydrate. Chin. J. Chem. Eng. 27, 2133–2147. doi:10.1016/j.cjche.2019.02.028
Zhan, M. S., Liu, S. X., Zhang, Y. M., Sun, G. G., and Weng, L. (2014). Methane hydrate formation and thermal based dissociation behavior in silica glass bead porous media. Ind. Eng. Chem. Res. 53, 6840–6854. doi:10.1021/ie4036737
Zhang, C. E., Cui, B. Y., Wei, D. Z., and Lu, S. S. (2019). Effects of underflow orifice diameter on the hydrocyclone separation performance with different feed size distributions. Powder Technol. 355, 481–494. doi:10.1016/j.powtec.2019.07.071
Zhao, J. Z., Zhou, S. W., Zhang, L. H., Wu, K. S., Guo, P., Li, Q. P., et al. (2017). The first global physical simulation experimental systems for the exploitation of marine natural gas hydrates through solid fluidization. Nat. Gas. Ind. 37, 15–22. doi:10.3787/j.issn.1000-0976.2017.09.002
Zhao, K. B., Sun, C. Q., and Wu, C. Z. (2021). Research progress of natural gas hydrate development technologies. Oil Drill. Prod. Technol. 43, 7–14. doi:10.13639/j.odpt.2021.01.002
Zhao, L. X., Jiang, M. H., and Wang, Y. (2008). Experimental study of a hydrocyclone under cyclic flow conditions for fine particle separation. Sep. Purif. Technol. 59, 183–189. doi:10.1016/j.seppur.2007.06.009
Zheng, J. (2005). Study the gas-liquid-sand three-phase hydrocyclone. dissertation/master's thesis. Dalian: Dalian University of Technology.
Zhong, L. C., Zhang, Y. S., Wang, T., Ji, Y., Norris, P., and Pan, W. P. (2019). Optimized methods for preparing activated carbon from rock asphalt using orthogonal experimental design. J. Therm. Anal. Calorim. 136, 1989–1999. doi:10.1007/s10973-018-7855-x
Zhou, S. W., Chen, W., and Li, Q. P. (2014). The green solid fluidization development principle of natural gas hydrate stored in shallow layers of deep water. China Offshore Oil Gas 26, 1–7.
Zhou, S. W., Chen, W., Li, Q. P., Zhou, J. L., and Shi, H. S. (2017a). Research on the solid fluidization well testing and production for shallow non-diagenetic natural gas hydrate in deep water area. China Offshore Oil Gas 29, 1–8. doi:10.11935/j/issn.1673-1506.2017.04.001
Zhou, S. W., Zhao, J. Z., Li, Q. P., Chen, W., Zhou, J. L., Wei, N., et al. (2017b). Optimal design of the engineering parameters for the first global trial production of marine natural gas hydrates through solid fluidization. Nat. Gas. Ind. 37, 1–14. doi:10.3787/j.issn.1000-0976.2017.09.001
Zou, C. N., Zhao, Q., Zhang, G. S., and Xiong, B. (2016). Energy revolution: From a fossil energy era to a new energy era. Nat. Gas. Ind. B 36, 1–11. doi:10.1016/j.ngib.2016.02.001
df Freedom degree
dz Inverted cone diameter (mm)
Dij Diffusion term
E Separation efficiency evaluating criterion
F F value
g Gravitational acceleration (m/s2)
Gall Gas volume injected in tangential inlets (%)
Gout Gas volume exhausted from gas outlet (%)
Gij Buoyancy generating term
h Drain hole height (mm)
kt Fluid thermal conductivity
Kx Sum of the test results of the level number is x which belongs to a certain factor column
li Gas outlet depth length (mm)
lz Inverted cone length (mm)
L Monitoring lines
MS Mean square of each factor
P Fluid pressure (Pa) Average value of the square of the sum of E
P Fluid pressure (Pa) Average value of the square of the sum of E
Pij Stress generation term
Q Sum of E2
R Range
s Tangential inlet area (mm2)
Sout Sand volume exhausted from sand outlet (%)
Sall Sand volume injected in tangential inlets (%)
SS Sum of squares of deviation
T Sum of E
u Velocity (m/s)
μ Fluid viscosity
εij Viscous dissipative term
ρ Density
Φij Pressure strain generating term
all Volume fraction of phase
i Directions
j Directions
out Volume fraction of phase at outlet
x position
Keywords: natural gas hydrate, three-phase hydrocyclone, structural parameter optimization, flow field characteristics, solid fluidization exploitation
Citation: Wei N, Qiao Y, Liu A, Zhao J, Zhang L and Xue J (2022) Study on structure optimization and applicability of hydrocyclone in natural gas hydrate exploitation. Front. Earth Sci. 10:991208. doi: 10.3389/feart.2022.991208
Received: 11 July 2022; Accepted: 28 July 2022;
Published: 08 September 2022.
Edited by:
Pibo Su, Guangzhou Marine Geological Survey, ChinaReviewed by:
Shuanshi Fan, South China University of Technology, ChinaCopyright © 2022 Wei, Qiao, Liu, Zhao, Zhang and Xue. This is an open-access article distributed under the terms of the Creative Commons Attribution License (CC BY). The use, distribution or reproduction in other forums is permitted, provided the original author(s) and the copyright owner(s) are credited and that the original publication in this journal is cited, in accordance with accepted academic practice. No use, distribution or reproduction is permitted which does not comply with these terms.
*Correspondence: Yi Qiao, cWlhb3lpc3dwdUAxNjMuY29t
Disclaimer: All claims expressed in this article are solely those of the authors and do not necessarily represent those of their affiliated organizations, or those of the publisher, the editors and the reviewers. Any product that may be evaluated in this article or claim that may be made by its manufacturer is not guaranteed or endorsed by the publisher.
Research integrity at Frontiers
Learn more about the work of our research integrity team to safeguard the quality of each article we publish.