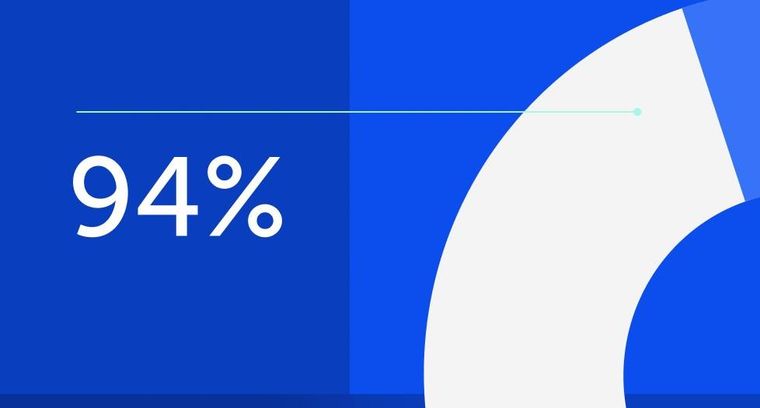
94% of researchers rate our articles as excellent or good
Learn more about the work of our research integrity team to safeguard the quality of each article we publish.
Find out more
ORIGINAL RESEARCH article
Front. Earth Sci., 04 August 2022
Sec. Structural Geology and Tectonics
Volume 10 - 2022 | https://doi.org/10.3389/feart.2022.948932
This article is part of the Research TopicUnconventional Reservoir GeomechanicsView all 16 articles
There exists a large horizontal principal stress difference (11–38 MPa) in the tight conglomerates in the Mahu oil area, China. It is difficult to form a complex fracture network via hydraulic fracturing under these conditions. To improve reservoir stimulation, the fracture formation mechanism of the complex conglomerate fracture networks was explored. Based on the geomechanics theory of fracture formation, the mechanism of the “stress wall” formed by fracturing in horizontal wells was analyzed in this paper. The inhibitory effect of the stress wall on the formation of tensile and shear fractures was studied. The reason for the decrease in the stress difference coefficient caused by fracturing fluid was analyzed through numerical simulation, which suggested that the complexity of a fracturing network is mainly controlled by the interference of externally applied stress and the reduction in the coefficient of internal stress difference. In this paper, innovative technologies were developed by proactively introducing stress interference in the application of the Ma131 small-well-spacing pilot area. The core technologies include optimization of the 3-D staggered small-well-spacing pattern, and synergetic optimization of multiple elements and zipper fracturing. The positive effects of proactive stress interference on improving fracturing volume, reserve utilization rate and recovery were discussed. Based on the concept of proactive stress interference, the “serial fracturing mode” of horizontal wells was proposed to reduce drilling and fracturing interference and improve the development effect.
An extremely large integrated conglomerate reservoir with reserves up to a billion tons has been discovered in the Mahu Sag, Junggar Basin, western China (Cao et al., 2015; Feng et al., 2020; Zhang et al., 2020). Ten oil-bearing series have been found longitudinally. The main oil-bearing strata are the Baikouquan Formation and the overlying Wuerhe Formation (Figure 1). After 8 years of continuous development since the exploration breakthrough of the M131 well in 2012, the main development model of horizontal well fracturing was established, which improves the efficiency of oil and gas exploration and development in the Mahu area (Jia et al., 2016; Li et al., 2018; Huang et al., 2019).
FIGURE 1. (A) Location of the Mahu; (B) stratigraphic column of the study area; (C) cross-section through the Mahu sag.
Due to unique sedimentary and accumulation conditions, The Mahu tight conglomerate has a unique lithology. This deposition is significantly different from the widespread deposition in North American. Its efficient development has the following difficulties. First, due to the strong heterogeneity of the reservoir, the sweet spot was difficult to identify. The conglomerate has a multimodal structure, which is similar to concrete with a large difference in particle size and composition. With the sudden lateral changes in the reservoir and relatively dispersed vertical stacking of the hydrocarbon-rich layers, the superior sweet spot is difficult to target. Second, the reservoir has relatively poor quality, the horizontal well output decreases rapidly, and it is difficult to maintain stable production. The reservoir has a porosity of (7.6%–11.8%). The permeability under overburden pressure is (0.02–0.45) ×10−3 μm (Cao et al., 2015). The reservoir has a low abundance of (22.3–47.1) × 104 m3/km2. A horizontal well targeting this reservoir has a risk of low primary recovery and production. Third, it is difficult to form a complex fracture network due to the large horizontal principal stress difference and lack of natural fractures. The horizontal principal stress difference of the Mahu tight conglomerate is 11–38.2 MPa. Based on the experience of unconventional oil and gas development in North America and the research results of commercial simulators, hydraulic fractures have the characteristic of long bilateral wings under a large principal stress difference (Adachi et al., 2007; Jin and Roy, 2017; Lecampion et al., 2018; Gao and Ghassemi, 2020a). Fourth, the reservoir is deeply buried, the conglomerate has poor drillability, and the drilling cycle is too long, which leads to a high investment required to drill a single horizontal well and increases the difficulty of economic development under the scenario of a low oil price. The unique geological conditions bring great challenges to the efficient development of the tight conglomerate reservoir in Mahu. Due to the limited ability of fluids to percolate through tight conglomerates, the concept of “fracture-controlled development” has gradually formed. The contact area between the fracture surface and the matrix can be expanded by the method of large-scale pumping and high-density fracturing. The difference in percolation pressure will decrease, and the distance of fracturing fluid percolation will be shortened, which can increase the estimated ultimate recovery (EUR) of a horizontal well. In addition, optimizing the fracturing sequence between wells and using the local high-stress field formed by the earlier fracturing of wells to proactively interfere with the fractures stimulated by subsequently completed hydraulic fracturing wells aims at enhancing the complexity of the fracture network, which is an effective method to enhance the production of horizontal wells. The process does not need to increase the cost of drilling and completion and is easy to implement, so it is a significant development strategy to improve economic efficiency. This technique has gradually been considered more seriously by reservoir engineers.
At present, a large number of studies and field tests have been carried out to improve the complexity of fracture networks by using stress interference (Jin and Roy, 2017). In the 1980s, researchers found that earlier formed hydraulic fractures can increase the stress of subsequent fractures, and that the geometry of the hydraulic fractures and the elastic effect of the pores can affect the growth of nearby hydraulic fractures (Adachi et al., 2007; Pan et al., 2014; Lecampion et al., 2018; Gao and Ghassemi, 2020a). Bunger et al. (2011) further verified this phenomenon in their research of Barnet shale gas in 2010 and defined it as a stress shadow (Zhou et al., 2017; Ju et al., 2020; Wang et al., 2022; Bunger et al., 2011). With the innovation and progress of hydraulic fracturing methods, the stress shadow effect can be used to improve the effect of reservoir stimulation through zipper fracturing or simultaneous fracturing methods. However, the technique is mainly applied to clusters of parallel fractures in adjacent wells. With the transformation of the development mode from conventional single-layer sequential fracturing to three-dimensional development, the interference value of stress should be further explored and fully applied to platforms or wells to improve the effect of reservoir stimulation.
To solve the problem that a complex fracture network is difficult to form under a large horizontal stress difference in the Mahu tight conglomerate reservoir, the geomechanics mechanism of proactive stress interference between wells and its application in a pilot area with a small well spacing are expounded, and the characterization method of increasing complexity of the fracture network is analyzed. Second, based on proactive stress interference, the serial fracturing mode of horizontal wells is proposed to reduce drilling and fracturing interference and improve the development effect.
Due to the unique characteristics of the tight conglomerate reservoir and a lack of development experience, the advanced development theories applied in North America cannot be fully applied to the Mahu Oilfield. In the early stage of the development of the Mahu tight conglomerate reservoir, a series of tests were carried out, such as advanced water injection tests in vertical wells, depletion development tests in vertical wells, water injection tests in vertical wells, conventional development tests in horizontal wells and stereo development tests with a small well spacing. Our exploration of efficient development technologies has led to the following summary of the related theories on the mechanical mechanism of the formation of a complex fracture network.
Based on the development process of horizontal wells and the practice of small well spacing in the Mahu Oilfield, Guoxin Li (Li et al., 2020) innovatively proposed the “steered-by-edge” fracturing mechanism (SBEFM) and the “proactive fracturing interference” mechanism (PFIM). However, the theory of PFIM is not further discussed. Based on previous studies, the concept of a stress wall (or “pressure wall”) is innovatively proposed in this paper. The mechanical mechanism of the formation of a complex fracture network by proactive stress interference is expounded in detail, and the proactive stress interference theory is enriched and developed.
Laboratory experiments on tight conglomerate cores show that the difference in horizontal stress has an essential effect on the propagation of hydraulic fractures (Meng et al., 2013; Zhang et al., 2018; Zhao et al., 2018). Due to the large horizontal stress difference of the tight conglomerate in the Mahu Oilfield, it is difficult to form a complex hydraulic fracture network with the conventional fracturing method there. The fracturing scale of the Mahu tight conglomerate horizontal well is very large. The initial formation pressure and in-situ stress are increased by injecting a large amount of fracturing fluid into the formation. In this paper, we define the stress wall as the reservoir pressure, which is higher than the initial formation pressure after fracturing. Affected by the stress wall of the fracturing well, it is difficult for the fracturing fluid in the hydraulic fractures of adjacent wells to penetrate the high-pressure area, which leads to the resistance of the fracture propagation. The backflow of fracturing fluid results in increasing pressure, which reduces the effective stress, and promotes the Mohr stress circle to move toward the failure envelope and enter the shear failure state, causing hydraulic fracture diversion. The method of promoting the diversion of hydraulic fractures by setting up a stress wall between horizontal wells is called proactive stress interference.
Hydraulic fracture propagation is a very complex process that is affected by the heterogeneity of rocks and the uncertainty of in-situ stress. In addition, complex physical processes are involved. The conglomerate has a multimodal structure, which consists of gravel, matrix, and planes of weakness are also present. Hydraulic fractures have complex propagation mechanisms, such as SBEFM, conglomerate-piercing mechanism, and conglomerate-ending mechanism. The classical theory of two-dimensional fracture propagation cannot meet the requirement of hydraulic fracturing of tight conglomerate reservoirs. The mechanism of fracture propagation needs to be further studied to provide theoretical guidance for the design of complex fracture networks.
In the process of oilfield development, the pore pressure of the formation decreases due to production. The fractures will asymmetrically propagate in the direction of the adjacent older wells. This phenomenon is widely observed in unconventional reservoirs during hydraulic fracturing. The change in pore pressure during hydraulic fracturing is regarded as the inverse of that during production.
During hydraulic fracturing, the pore pressure of the rock increases because a large amount of fluid is injected into the formation, which changes the state of the in-situ stress (Thiercelin and Plumb, 1994; Yi et al., 2018). It is assumed that the mechanical parameters (Young’s modulus E, Poisson’ ratio μ) and structural stress coefficients (εh, εH) remain constant during fracturing (0 < μ < 0.5), and that the maximum and minimum horizontal principal stresses increase with increasing pore pressure, which is the mechanical basis for the formation of a stress wall (Liu et al., 2017; Liu et al., 2021; Liu et al., 2022a; Liu et al., 2022b)
In these equations, σv is the stress of the overlying strata; σH and σh are the maximum and minimum horizontal principal stresses, respectively; µ and E are Poisson’s ratio and Young’s modulus, respectively; Pp is the pore pressure; α is the Biot coefficient; ρ0 and ρ are the average formation density determined without density logging and the formation density from density logging, respectively; and H0 and H are the starting and reference depths of density logging, respectively.
The pore pressure plays an important role in forming tensile and shear fractures during hydraulic fracturing. We discuss the mechanism of the stress wall, which inhibits fracture propagation and promotes fracture diversion, in detail.
A tensile fracture in rock is formed when the normal stress acting on the fracture surfaces and the tensile strength of the rock are overcome (Tong and Yin, 2011; Sone and Zoback, 2013; Tong et al., 2014; Tong et al., 2021). During the fracturing process, the pore pressure at the fracture tip is increased by pumping fracturing fluid into the formation. When the pore pressure at the fracture tip is greater than the sum of the normal stress on the fracture and the tensile strength of the rock, tensile fractures form in the rock. Due to the high pore pressure formed at the end of the secondary fractures generated around the earlier fractured horizontal wells, the fracture has to overcome the additional pore pressure difference during the propagation process. The maximum tensile stress criterion is used as the basis for judging the tensile fracture of rock, and the tensile fracture factor σT is introduced, whose expression is as follows:
where P is the pressure transmitted by the fracturing fluid to the fracture surface; ΔP is the difference between the pore pressure outside the fracture and the original formation pressure inside the fracture; and T0 is the tensile strength of the rock.
In essence, whether the fracture can expand is determined by a comparison of P − ΔP and σh + T0: ① when P − ΔP > σh + T0, fracture extension occurs, and ② when P − ΔP ≤ σh + T0, the fracture is in the critical or inhibited state of propagation. As the secondary fracture expands in the direction of the rock where the stress wall has been formed in the earlier stage of hydraulic fracturing, ΔP gradually increases, and P − ΔP gradually decreases, resulting in a weaker ability to overcome the normal stress at the fracture and the tensile strength of the rock. Therefore, the tensile extension of the artificially formed fractures to the zone with high pore pressure is inhibited.
Porous elastic theory is used to predict the stress changes with reservoir depletion (Zoback, 2007). In isotropic, linear elastic, and porous media, the change in horizontal stress relative to pore pressure may be written as:
where χ is the theoretical change in horizontal stress with depletion, generally in the range of 0.5–0.7.
In this paper, the classical Mohr–Coulomb criterion is used to describe rock failure, expressed as: (Hubbert and Rubey, 1959)
where
To better understand the effect of pore pressure on shear fracture, the Mohr stress circle is introduced (Figure 2). The vertical and horizontal principal stresses are defined as σ1, σ2, and σ3. According to the core experimental results of in-situ stress, the true stress state in the Mahu Oilfield is σ3 < σ2 < σ1.
FIGURE 2. Mohr–Coulomb plot of the stress state change during fracturing liquid injection. σ1′ and σ3′ are the initial effective stresses, σ1ʺ and σ3ʺ are the effective stresses changed by pore pressure, and D1 and D2 are the failure margin distances.
Assuming that the formation pore pressure changes by ΔP during hydraulic fracturing, the gravity of the overlying rock is constant. The new maximum effective stress is given as:
The new minimum effective stress is given as:
Before and after the change in pore pressure, the distance between the Mohr–Coulomb circle and the failure envelope is given as:
Combining Eqs 5–8, the difference between the two failure margin distances is given as:
According to Eqs 3, 9, to calculate the difference between D1 and D2, the Poisson’s ratio, internal frictional angle, and Biot coefficient of the rock in the Mahu Oilfield need to be determined. Therefore, three cores from the Ma131 oilfield are selected to carry out the triaxial rock mechanical experiment. The samples are machined into a cylindrical shape with a diameter of 25 mm and a height of 50 mm. The average Young’s modulus of the conglomerate in the Ma131 oilfield is 27.0 GPa, the average Poisson’s ratio is 0.18, and the average internal frictional angle is 31.5° (Table 1).
According to the conglomerate test results (Table 2), the Biot coefficient is 0.89, and the increasing coefficient χ is 0.69. The difference between the two failure margin distances is calculated as −0.0066ΔP, which is consistent with the literature published by Dohmen (Dohmen et al., 2014; Wang et al., 2019), Norbeck and Horne (Norbeck and Horne, 2016).
TABLE 2. Published geomechanical data and Ma131 oilfield data related to the failure margin coefficient (Dohmen et al., 2017).
Under the effects of diagenesis, hydrocarbon expulsion and the mechanical property differences between the gravel and matrix, a large number of gravel margin fractures are observed in the microscopic thin sections of this conglomerate rock.
Influenced by the natural weak surface of the conglomerate, three types of fractures are mainly developed in the process of artificial fracture propagation: extensional fractures, shear fractures, and gravel margin fractures. According to the relationship between the fluid pressure, the in-situ stress, and the tensile strength of the rock, the stress mechanism controlling the formation of fractures with different properties is established, and the corresponding stress chart is formulated (Figure 3). ① If the fluid pressure is greater than the sum of the normal stress and the tensile strength of the rock surface, a tensile fracture will form. ② If the fluid pressure is smaller than the sum of the normal stress and the tensile strength of the rock surface, and the shear stress is greater than the rock cohesion, a tensile fracture will be form.③ If the fluid pressure is smaller than the sum of the normal stress and the tensile strength of the rock surface, and the shear stress is smaller than the rock cohesion, a gravel margin fracture will be form.
FIGURE 3. The stress mechanism controlling the formation of multiple types of fractures in tight conglomerates.
According to the research above, the stress wall can inhibit the propagation of tensile and shear fractures during hydraulic fracturing. During hydraulic fracturing, the pore pressure in the fracture is increased, and the effective stress on the fracture surface is reduced. At this time, the interior of the fracture during fracturing is an open space that will not be affected by the elastic effect of the pore; however, when the effective stress decreases, the Mohr stress circle shifts to the left and enters the shear state, promoting the formation of a large number of shear fractures around the main fracture. In the process of the branched fractures extending forward, as the energy decreases but does not decrease enough to form new shear fractures, the fractures will propagate along gravel edges, forming gravel margin fractures (Figure 4).
FIGURE 4. Diagram of the formation mechanism of proactive stress interference in a complex fracture network.
Through proactive stress interference, the propagation of tensile fractures is inhibited, and shear fractures and gravel margin fractures are promoted. Finally, high-density fracture networks are formed, including tensile fractures, shear fractures, and gravel margin fractures.
To form complex fractures, unique in-situ stress conditions need to be satisfied. The lower the degree of the in-situ stress anisotropy is, the higher the complexity of the hydraulic fractures. The influence of the in-situ stress on the fracture is quantitatively evaluated by the horizontal stress difference coefficient (Eq. 10). It is difficult to form complex branched fractures under a large horizontal stress difference coefficient. Compared with those in homogeneous reservoirs, the hydraulic fracture propagation paths in this conglomerate reservoir are more tortuous, and the hydraulic fracture morphology is more complex. According to the test results of the conglomerate cores, if the coefficient of the horizontal stress difference is larger than 0.2, the hydraulic fracture morphology tends to be simple; if the coefficient of the horizontal stress difference is less than 0.2, it is difficult to form complex fracture networks (Figure 5A).
where Kh is the horizontal stress difference coefficient, SH is the maximum principal stress and Sh is the minimum principal stress.
If the pore pressure increases during the fracturing process, the original horizontal principal stress changes due to the interference of induced stress, and the horizontal stress difference coefficient gradually decreases (Eq. 11).
where K′h is the coefficient of stress difference; S′H and S′h are the induced stresses of the pore elasticity effect in the direction of maximum and minimum principal stress, respectively, and Δσ and Δσ′ are the initial horizontal stress difference and the horizontal stress difference after pore pressurization, respectively.
FIGURE 5. (A) The relationship between the stress difference coefficient and the complex fracture network; (B) numerical simulation result in the difference of horizontal stress; (C) minimum principal stress before hydraulic fracturing; (D) minimum principal stress after hydraulic fracturing.
The test results of Ma131 cores show that, the horizontal stress difference is approximately 17 MPa, the minimum horizontal principal stress is 55 MPa, and the horizontal stress difference coefficient is 0.31. According to the relationship between the horizontal stress difference coefficient and the complexity of fracture networks, it is difficult to form a complex fracture network. The numerical simulation results show that the horizontal stress difference decreases during fracturing (Figure 5B), which can be reduce by 2–10 MPa in the range of 150 m. The reduction decreases with increasing distance from the wellbore (Figure 5C). With an increased pore pressure, the shut-in pressure in wells after fracturing increases significantly, and the minimum horizontal principal stress can increase by 5–10 MPa (Figure 5D). Therefore, the high pore-pressure will change the in-situ stress of later fracturing wells, and the horizontal stress difference coefficient will decrease to 0.16–0.3 (Eq. 10), which benefits the formation of complex fracture networks.
In conclusion, the complexity of hydraulic fractures is affected by multiple factors. The proactive stress interference inhibits the extension of the main fractures by changing the initial in-situ stress, and improves the complexity of the fracture network by reducing the difference in the horizontal stress coefficient. In this paper, the formation mechanism of a complex fracture network is described in detail.
Further improvements are highly desirable, such as those in the reserve utilization rate, recovery rate, drilling and completion efficiency, and investment requirements. To explore a new efficient development mode of tight conglomerates, the development test of long lateral length, tight well spacing, big well clusters, fine perforation clustering, and factory operation is carried out in the Ma131 pilot area under the guidance of proactive stress interference theory.
The pilot area is 1.2 km (Cao et al., 2015), with proven geological reserves of approximately 100.0 × 104 t. Two sets of oil reservoirs (T1b3 and T1b2) were developed with a span of 35–40 m in the longitudinal direction, and developed mudstone intercalations of 13–20 m in the middle direction. The reservoir porosity is 8.6%–10.1%, permeability is 1.1 × 10−3 μm (Cao et al., 2015), oil saturation is 50.3%–59.4%, and brittleness is 70–80. A total of 12 horizontal wells were developed, including seven wells in the T1b3 layer and five wells in the T1b2 layer. The horizontal section length is 1,200–2000 m, the sanding rates are 0.9–1.6 m3/m, and the cluster spacing is 20 m (Table 3). The fracturing mode of drilling plugs, current-limiting fracturing, and temporary plugging fracturing were adopted. Twelve wells were designed with three factory-type platforms, and four wells were drilled by one rig. Three rigs operated at the same time to improve the efficiency.
First, a 3-D staggered well pattern is adopted in the pilot area. The W-type stereo staggered mode, in which the vertical horizontal well space is designed 50 m apart, can strengthen the positive vertical interference between wells. During the fracturing progress, based on the regularity of extension, the vertical operation procedure is determined to enhance vertical interference, which is favorable (Figure 6A).
FIGURE 6. (A) The well pattern of small well spacing in the Ma131 oilfield; (B) lithofacies and design of the platform; (C) zipper fracturing sequence of the platform.
In addition, an intermittent fracturing project is designed. According to the fracture sequence of platform 1, platform 2 and platform 3, the stress wall of platform 1 and platform 3 is formed to promote the formation of a complex fracture network in the fracturing process of platform 2, which enhances the plane favorable interference (Figure 6B).
Finally, zipper fracturing is adopted. The two sets of reservoirs are targeted with the staggered well pattern. The staggered fracture spacing in the longitudinal direction is 10 m. The fracture network is more complicated due to the adoption of the asynchronous fracturing method, which creates cluster-to-cluster stress interference (Figure 6C).
Due to the large amount of fracturing fluid injected into the formation, the pore pressure of the formation initially increases, and the pump-off pressure of the subsequently completed fracturing wells increases. More completion energy is spent on generating fractures, which leads to complex fracture networks during subsequent completions. The shut-in pressure of platform 2 is increased by 8 MPa compared to that of platform 1, which fractured earlier (Figure 7A), indicating that platform 2 has a higher energy for fracture formation.
FIGURE 7. (A) Shut-in pressure of different platform plots; (B) reciprocal productivity index plot of the average of Ma131 small-well-spacing pilot wells compared to a typical well; (C) shut-in pressure and stimulated reservoir volume in Ma131 small-well-spacing pilot wells; (D) daily oil output of Ma131 small-well-spacing pilot wells compared to typical wells.
Production diagnosis is a reliable method of measuring the complexity of fracture networks. During the early linear flow of the horizontal well, the slope of the flow curve is equal to the reciprocal of the product of the contacted surface area of the reservoir and the square root of permeability (Eq. 12). A shallower slope equates to a greater surface area, which is indicative of more complex fracture networks. The production diagnostic result (Figure 7B) illustrates the relationship between the productivity index (∆p/q) and the square root of time. The shallower slope of the small-well-spacing data indicates that the proactive interference of stress creates a more complex fracture network than the typical hydraulic fracture technique does in the Ma131 oilfield (Figure 7C).
where T is the slope of the unit pressure drop with the square root of time, hf is the fracture height, xf is the fracture half-length, nf is the fracture number, and k is the fracture permeability.
The production law in the Mahu Oilfield shows that the horizontal wells mainly have two periods of flow: an early linear flow and a late pseudo flow. The duration of the early linear flow is generally 3 months. To reduce the influence of the single-well-controlled reserves of the single well on production, the average daily oil production and oil pressure in the first 3 months of the small-well-spacing pilot are selected as the parameters of the complex fracture network characteristics. In terms of initial production, the average daily oil output of the small-well-spacing pilot wells in the first 3 months is higher than that of other horizontal wells in the Ma131 oilfield (Figure 7D). The daily output of platform 2 is higher than those of platform 1 and platform 3. This shows that under proactive stress interference, the complexity of the fracture network near the well zone is improved, the conductivity of the formation is improved, and the initial production is significantly increased.
At present, microseismic monitoring is an effective method to evaluate the effect of reservoir stimulation in oilfield development. The microseismic monitoring results in the small-well-spacing pilot area show that compared with the 400 m spacing hydraulic fracturing well, the small-well-spacing pilot wells have a denser microseismic response (Figure 8A), larger stimulated reservoir volume and more complexity of the fracture network (Figure 8B).
FIGURE 8. (A) Ma131 early horizontal well with a well spacing of 400 m; (B) Ma131 small-well-spacing pilot area.
Considering the particularity of tight conglomerate reservoirs, the mature horizontal well development model of shale oil and tight oil reservoirs in the North American Permian basin cannot be used for reference in the Mahu Oilfield. To further improve oilfield development, conventional fracturing (Figure 9A), group fracturing (Figure 9B), and well factory fracturing modes have been explored (Ajani and Kelkar, 2012; Kurtoglu and Salman, 2015; Bommer et al., 2017; Jacobs, 2018a). However, there are still two urgent problems that need to be solved in the development process: 1) Affected by the strong heterogeneity of conglomerates, hydraulic fracture propagation is asymmetrical, resulting in fracture hits. Mahu Oilfield data show that the longest distance of fracture hits is 2 km. Fracture hits cause serious production interference, which not only affects the reservoir fracture network construction quality, but also affects the production of the adjacent well (Hao et al., 2017; Kumar et al., 2018; Thompson et al., 2018). 2) In the process of fracturing, high-density drilling muds cause irreversible damage to the artificially formed fracture of the adjacent well, resulting in a significant EUR reduction of the adjacent well.
FIGURE 9. (A) Conventional single-layer fracturing model; (B) group fracturing model; (C) serial fracturing model; (D) step-by-step implementation of the serial fracturing model.
According to the theory of proactive stress interference, this paper uses the stress wall formed by an earlier fractured well to suppress hydraulic fracture propagation and promote fracture diversion in subsequently completed wells, and the serial fracturing mode is innovatively proposed, which can reduce drilling and fracturing hits (Figures 9C,D). The advantages are as follows: 1) The stress barrier formed by the fractured well, which is not produced, can reduce the interference of the subsequently completed fracturing well to the producing well. 2) The established drilling completion buffer zone can reduce the interference of drilling hits to the fracturing well. The development efficiency of the oilfield is improved through the six steps: production, soaking, fracturing, buffering, drilling and preparation.
In the process of horizontal well fracturing, the effect of reservoir fracture network construction can be improved by reducing the well spacing and using proactive stress interference. However, in the design process of well spacing in tight conglomerate reservoirs, we should not only pursue the complexity of fracture networks but also ignore the potential negative impact of a well spacing that is too small. The production practice of horizontal well spacing in Ma131 shows that (Figure 10A), large well spacing is conducive to improving the production of single wells, but the recovery is relatively low. However, if the well spacing is too small, the geological reserves and EUR controlled by the single well decrease, which increases the benefit risk. Compared with the result of conventional horizontal wells in the same block, in less than 400 days, the Ma131 small-well-spacing pilot wells show higher production and decline rates. In more than 400 days, the production of the small-well-spacing wells is less than that of conventional horizontal wells (Figure 10B). By using the Arps decreasing method, the EUR of the small-well -spacing horizontal wells is determined to be less than 20,000 tons (Figure 10C), which is far below its economic production limit.
FIGURE 10. (A) The production difference between small-spacing wells and conventional wells in the Ma131 oilfield; (B) the daily output and predicted cumulative oil production of small-well-spacing pilot wells; (C) the relationships between recovery and cumulative oil production with well space; (D) the relationships between NPV and recovery with well space.
The net present value (NPV) is the factor used to optimize the well spacing in this work. With the investment data of horizontal wells in the Ma131 oilfield, a chart of the relationship between well spacing and NPV of different oil prices is developed. Figure 10D indicates that when the oil price is $60 BBL, the limit for economic well spacing is 200 m. Therefore, in the process of developing and designing horizontal wells in tight conglomerate reservoirs, it is important to optimize the economic well spacing.
(1) In this paper, we put forward proactive stress interference theory in a tight conglomerate oilfield and reveal its geo-mechanical mechanism. The mechanism of the stress wall and its inhibitory effect on tensile and shear fracture propagation in subsequently completed hydraulic fracturing wells are analyzed in detail. It is proposed that the formation of complex fracture networks with a small well spacing is the result of proactive stress interference and the reduction in the difference in the horizontal stress coefficient.
(2) Based on the application of proactive stress interference of staggered cube pads with a small well spacing at Ma131, the technical method and steps required to implement proactive stress interference are introduced in detail, and the characterization method of judging fracture complexity by means of shut-in pressure, linear flow characteristics, initial production characteristics and microseismic monitoring is proposed.
(3) A sequence development mode based on proactive stress interference is proposed. In view of the contradiction between drilling and fracturing interference and efficient production in the Mahu Oilfield, the stress wall formed by previously completed fracturing wells is used to reduce the interference of later fracturing wells. At the same time, the drilling buffer zone is designed to reduce the interference between the fracturing well and the production well. The development sequence is as follows: production, closing in, fracturing, buffering, drilling, and preparation.
The original contributions presented in the study are included in the article/Supplementary Material, further inquiries can be directed to the corresponding author.
SW: Conceptualization, data curation, formal analysis, Writing—original draft, Writing—review and editing. XL: Validation, resources. LH: Formal analysis, investigation. XZ: Resources, validation. LZ: Resources, validation. JS: Methodology. RL: Methodology. PH: investigation. KG:Resources. TL: Methodology. GL: Methodology. XW: Resources. SL: Resources.
This research was supported by the Fund from the Major Project of National Science and Technology (PLC2017ZX05070), Scientific Research and Technology Development Project of CNPC (KT 2018-13-02).
All authors were employed by PetroChina Xinjiang Oilfield.
All claims expressed in this article are solely those of the authors and do not necessarily represent those of their affiliated organizations, or those of the publisher, the editors and the reviewers. Any product that may be evaluated in this article, or claim that may be made by its manufacturer, is not guaranteed or endorsed by the publisher.
The Supplementary Material for this article can be found online at: https://www.frontiersin.org/articles/10.3389/feart.2022.948932/full#supplementary-material
Adachi, J., Siebrits, E., Peirce, A., and Desroches, J. (2007). Computer Simulation of Hydraulic Fractures[J]. Int. J. Rock Mech. Min. Sci. 44 (5), 739–757. doi:10.1016/j.ijrmms.2006
Ajani, A. A., and Kelkar, M. G. (2012). “Interference study in shale plays.” in Paper presented at the SPE Hydraulic Fracturing Technology Conference (Texas: The Woodlands). SPE-151045-MS. 6–8. doi:10.2118/151045-MS
Bommer, P., Bayne, M., Mayerhofer, M., Machovoe, M., and Staron, M. (2017). “Re-designing from scratch and defending offset wells: case study of a six-well bakken zipper project, McKenzie county, ND.” in Paper presented at the SPE Hydraulic Fracturing Technology Conference and Exhibition. Texas: The Woodlands. SPE-184851-MS. doi:10.2118/184851-MS
Bunger, A. P., Zhang, X., and Jeffrey, R. G. (2011). “Parameter affecting the interaction among closely spaced hydraulic fractures[C].” in paper 140426 presented at the SPE Hydraulic Fracturing Technology Conference, 24-26 January, the Woodlands (Texas, New York: The Woodlands). doi:10.2118/140426-PA
Cao, J., Lei, D. W., Li, Y. W., Tang, Y., Abulimit, , Chang, Q. S., et al. (2015). Ancient high-quality alkaline lacustrine source rocks discovered in the lower permian fengcheng formation, junggar basin. Acta Pet. Sin. 36 (7), 781–790. doi:10.7623/syxb201507002
Dohmen, T., Blangy, J. P., and Zhang, J. (2014). Microseismic depletion delineation. Interpretation 2 (3), SG1–SG13. doi:10.1190/int-2013-0164.1
Dohmen, T., Zhang, J., Barker, L., and Blangy, J. P. (2017). Microseismic magnitudes and b-Values for delineating hydraulic fracturing and depletion. SPE J. 22 (05), 1–624. doi:10.2118/186096-pa
Feng, C., Li, T., He, W., and Zheng, M. (2020). Organic geochemical traits and paleo-depositional conditions of source rocks from the carboniferous to permian sediments of the northern mahu sag, junggar basin, china. J. Petroleum Sci. Eng. 191, 107117. doi:10.1016/j.petrol.2020.107117
Gao, Q., and Ghassemi, A. (2020a). Finite element simulations of 3D planar hydraulic fracture propagation using a coupled hydro-mechanical interface element. Int. J. Numer. Anal. Methods Geomech. 44 (15), 1999–2024. doi:10.1002/nag.3116
Hao, S., Dengen, Z., Adwait, C., and Baosheng, L. (2017). “Understanding the ‘frac-hits’ impact on a midland basin tight-oil well production,” in in Paper presented at the SPE Unconventional Resources Technology Conference, Austin, Texas, July 24. doi:10.15530/urtec-2017-2662893
Huang, L., Cao, J., Guo, J., Ma, Y., Wang, G., and Zhang, H. (2019). The forming mechanism of high quality glutenite reservoirs in Baikouquan formation at the eastern slope of mahu sag of the Junggar basin,c. Petroleum Sci. Technol. 37 (14), 1665–1674. doi:10.1080/10916466.2019.1602638
Hubbert, M. K., and Rubey, W. W. (1959). Role of fluid pressure in mechanics of overthrust faulting: I. Mechanics of fluid-filled porous solids and its application to overthrust faulting. Geol. Soc. Am. Bull. 70 (2), 115–166. doi:10.1130/0016-7606(1959)70[115:rofpim]2.0.co;2
Jacobs, T. (2018a). In the battle against frac hits, shale producers go to new extremes. J. Pet. Technol. 70 (8), 35–38. SPE-0818-0035-JPT. doi:10.2118/0818-0035-JPT
Jia, H., Ji, H., Li, X., Zhou, H., Wang, L., and Gao, Y. (2016). A retreating fan-delta system in the Northwestern Junggar Basin, northwestern China-Characteristics, evolution and controlling factors. J. Asian Earth Sci. 123, 162–177. doi:10.1016/j.jseaes.2016.04.004
Jin, G., and Roy, B. (2017). Hydraulic-fracture geometry characterization using low-frequency DAS signal [J]. Lead. Edge 36 (12), 975–980. doi:10.1190/tle36120975.1
Ju, Y., Li, Y., Wang, Y. L., and Yang, Y. M. (2020). Stress shadow effects and microseismic events during hydrofracturing of multiple vertical wells in tight reservoirs: A three-dimensional numerical model. J. Nat. Gas Sci. Eng. 84, 2020. doi:10.1016/j.jngse.2020.103684
Kumar, D., Masouleh, S. F., Gassami, A., Riley, S., and Elliott, B. (2018). “A 3D geomechanical analysis of horizontal well refracturing and “frac” its.” in paper presented at the 52nd U.S. Rock Mechanics/Geomechanics Symposium ARMA-2018-729. 17–20 June. Seattle, WA.
Kurtoglu, B., and Salman, A. (2015). “How to utilize hydraulic fracture interference to improve unconventional development” in Paper presented at the AbuDhabi International Petroleum Exhibition and Conference (Abu Dhabi: UAE). SPE-177953-MS. doi:10.2118/177953-MS
Lecampion, B., Bunger, A. P., and Zhang, X. (2018). Numerical methods for hydraulic fracture propagation: a review of recent trends [J]. J. Nat. Gas Sci. Eng. 49, 66–83. doi:10.1016/j.jngse.2017.10.012
Li, G. X., Qin, J. H., Xian, C. G., Fan, X. B., Zhang, J., and Ding, Y. (2020). Theoretical understandings, key technologies and practices of tight conglomerate oilfield efficient development: a case study of the mahu oilfield, junggar basin, NW china[J]. Petroleum Explor. Dev. 47 (6), 1185–1197. doi:10.1016/s1876-3804(20)60135-0
Li, H., Tang, H.-m., Qin, Q.-r., Fan, C.-h., Han, S., Yang, C., et al. (2018). Reservoir characteristics and hydrocarbon accumulation of carboniferous volcanic weathered crust of zhongguai high area in the western junggar basin, china. J. Cent. South Univ. 25 (11), 2785–2801. doi:10.1007/s11771-018-3953-y
Liu, J., Ding, W., Yang, H., and Liu, Y. (2021). Quantitative multiparameter prediction of fractured tight sandstone reservoirs: a case study of the yanchang formation of the ordos basin, central china. SPE J., 1–32. doi:10.2118/205495-pa
Liu, J., Ding, W., Yang, H., Wang, R., Yin, S., Li, A., et al. (2017). 3D geomechanical modeling and numerical simulation of in-situ stress fields in shale reservoirs: a case study of the lower cambrian niutitang formation in the cen'gong block, south cChina. Tectonophysics 712, 663–683. doi:10.1016/j.tecto.2017.06.030
Liu, J., Mei, L., Ding, W., Xu, K., Yang, H., and Liu, Y. (2022b). Asymmetric propagation mechanism of hydraulic fracture networks in continental reservoirs. GSA Bull. doi:10.1130/B36358.1
Liu, J. S., Yang, H. M., Xu, K., Wang, Z. M., Liu, X. Y., Cui, L. J., et al. (2022a). Genetic mechanism of transfer zones in rift basins: insights from geomechanical models. GSA Bull. doi:10.1130/b36151.1
Meng, C., Maerten, F., and Pollard, D. D. (2013). Modeling mixed-mode fracture propagation in isotropic elastic three dimensional solid. Int. J. Fract. 179, 45–57. doi:10.1007/s10704-012-9771-6
Norbeck, J. H., and Horne, R. N. (2016). Physical mechanisms related to microseismic-depletion-delineation field tests with application to reservoir surveillance. SPE J. 21 (04), 1–279. doi:10.2118/178926-pa
Pan, L. H., Zhang, S. C., Cheng, L. J., Lu, Z. H., and Lliu, K. Y. (2014). A numerical simulation of the inter-cluster interference in multi-cluster staged fracking for horizontal wells [J]. Nat. Gas. Ind. 34 (1), 74–79. doi:10.3787/j.issn.1000-0976.2014.01.011
Sone, H., and Zoback, M. D. (2013). Mechanical properties of shale-gas reservoir rocks—Part 1: static and dynamic elastic properties and anisotropy. Geophysics 78 (5), D381–D392. doi:10.1190/geo2013-0050.1
Thiercelin, M. J., and Plumb, R. A. (1994). A core-based prediction of lithologic stress contrasts in east texas formations [J]. SPE Form. Eval. 9 (4), 251–258. doi:10.2118/21847-pa
Thompson, J., Franciose, N., Schutt, M., Hartig, K., and Mckenna, J. (2018). “Tank development in the midland basin, texas: a case study of super-charging a reservoir to optimize production and increase horizontal well densities.” in SPE -2902895 presented at the Unconventional Resources Technology Conference held in Houston, 23. doi:10.15530/urtec-2018-2902895
Tong, H. M., Zhang, P., Zhang, H. X., Liu, Z. P., Ren, X. H., Xiao, K. Z., et al. (2021). Geomechanical mechanisms and prevention countermeasures of casing deformation in shale gas horizontal wells[J]. Nat. Gas. Ind. 41 (1), 189–197. doi:10.3787/j.issn.1000-0976.2021.01.017
Tong, H. M., and Yin, A. (2011). Reactivation tendency analysis: a theory for predicting the temporal evolution of pre-existing weakness under uniform stress state. Tectonophysics 503, 195–200. doi:10.1016/j.tecto.2011.02.012
Tong, H. M., Wang, J. J., Zhao, H. T., Li, B., Hao, H. H., and Wang, M. Y. (2014). Mohr space and its application to the activation prediction of pre-existing weakness. Sci. China Earth Sci. 57, 1595–1604. doi:10.1007/s11430-014-4860-1
Wang, L. C., Duan, K., Zhang, Q. Y., Li, X. Y., and Jiang, R. H. (2022). Study of the dynamic fracturing process and stress shadowing effect in granite sample with two holes based on SCDA fracturing method. Rock Mech. Rock Eng. 55, 1537–1553. doi:10.1007/s00603-021-02728-0
Wang, S. G., Tan, Y. H., Sangnimnuan, An., Khan, S., Liang, B. S., and Rijken, P. (2019). “Learnings from the hydraulic fracturing test site (hfts) #1, midland basin, west Texas - a geomechanics perspective,” in in Paper presented at the SPE Unconventional Resources Technology Conference. URTEC-2019-1570-MS., Denver, Colorado, July 22. doi:10.15530/urtec-2019-1570
Yi, C., Johansson, D., and Greberg, J. (2018). Effects of in-situ stresses on the fracturing of rock by blasting. Comput. Geotechnics 104, 321–330. doi:10.1016/j.compgeo.2017.12.004.9
Zhang, B., Ji, B., and Liu, W. (2018). The study on mechanics of hydraulic fracture propagation direction in shale and numerical simulation. Geomech. Geophys. Geo-energ. Geo-resour. 4, 119–127. doi:10.1007/s40948-017-0077-z
Zhang, C. M., Song, X. M., Wang, X. J., Wang, X. L., Zhao, K., and Shuang, Q. (2020). Origin and depositional characteristics of supported conglomerates [J]. Petroleum Explor. Dev. 47 (2), 272–285. doi:10.1016/s1876-3804(20)60047-7
Zhao, J. Z., Ren, L., Shen, C., and Li, Y. M. (2018). Latest research progresses in network fracturing theories and technologies for shale gas reservoirs [J]. Nat. Gas. Ind. 38 (3), 1–14. doi:10.3787/j.issn.1000-0976.2018.03.001
Zhou, L., Chen, J., Gou, Y., and Feng, W. (2017). Numerical investigation of the time-dependent and the proppant dominated stress shadow effects in a transverse multiple fracture system and optimization. Energies 10 (1), 83. doi:10.3390/en10010083
Keywords: Mahu tight conglomerate, stress wall, proactive stress interference, complex fracture network, sequence of fracturing
Citation: Wang S, Li X, Hao L, Zhang X, Zhang L, Song J, Liu R, Pan H, Gu K, Li T, Luo G, Wang X and Li S (2022) Proactive stress interference mechanism and its application in the Mahu oil area, Junggar basin. Front. Earth Sci. 10:948932. doi: 10.3389/feart.2022.948932
Received: 20 May 2022; Accepted: 27 June 2022;
Published: 04 August 2022.
Edited by:
Jingshou Liu, China University of Geosciences Wuhan, ChinaReviewed by:
Shuai Yin, Xi’an Shiyou University, ChinaCopyright © 2022 Wang, Li, Hao, Zhang, Zhang, Song, Liu, Pan, Gu, Li, Luo, Wang and Li. This is an open-access article distributed under the terms of the Creative Commons Attribution License (CC BY). The use, distribution or reproduction in other forums is permitted, provided the original author(s) and the copyright owner(s) are credited and that the original publication in this journal is cited, in accordance with accepted academic practice. No use, distribution or reproduction is permitted which does not comply with these terms.
*Correspondence: Shuo Wang, MTA4NTcwNDkwMUBxcS5jb20=
Disclaimer: All claims expressed in this article are solely those of the authors and do not necessarily represent those of their affiliated organizations, or those of the publisher, the editors and the reviewers. Any product that may be evaluated in this article or claim that may be made by its manufacturer is not guaranteed or endorsed by the publisher.
Research integrity at Frontiers
Learn more about the work of our research integrity team to safeguard the quality of each article we publish.