- 1School of Water Resources and Hydropower, Hunan Polytechnic of Water Resources and Electric Power, Changsha, China
- 2Hunan Institute of Water Resources and Hydropower Research, Changsha, China
Grouting is an important and common method for fortifying water-bearing sand layers; however, this method is difficult to perform due to the poor groutability of these sand layers. This paper proposes superfine cement–bentonite-based emulsified asphalt composite grout (CACG) to infiltrate water-bearing sand layers. The grout uses superfine cement and bentonite as the base materials, while emulsified asphalt is added to achieve good pumpability, excellent fluidity, high stability and sufficient compressive strength. The effects of the composition and formulation on the performance of CACG is determined through a series of laboratory experiments, and the recommended optimal formulation of CACG is as follows: a water/superfine cement ratio of 1:1, a bentonite content of 6.5%, and an emulsified asphalt content of 20%. The effectiveness and economy of CACG is checked by a field test in which CACG is applied to the water-bearing sand layers of a river embankment. The results illustrate that CACG not only fulfills engineering requirements but is also cost effective.
Introduction
Water-bearing sand layers are widely distributed in China and easily liquefy during earthquakes (Wang et al., 2017; Asheghabadi et al., 2019; Esfeh and Kaynia, 2020; Gao et al., 2021). As a result, a large number of surface structures unevenly subside or collapse, even resulting in serious disasters (Yu et al., 2015; Huang et al., 2009; Sharp and Adalier, 2006). Therefore, it is necessary to apply an effective reinforcement treatment to improve water-bearing sands that make them more resistant to liquefaction. For this reason, a series of methods to treat water-bearing sand layers have been developed by engineers over the past 10 years, and grouting is one of the methods that is most well-known and applied (Avxhiu and NenajPanaiotov et al., 1987;2002). Engineering practices indicate that there are many factors that influence the grouting quality; among these factors, the grouting material is very important.
Currently, a series of materials have been widely used in water-bearing sand layer grouting engineering, such as cement pastes, microcement pastes, and chemical solutions (Heins, 1950; Wu et al., 2018). However, these traditional grouting materials still have some deficiencies. For example, cement grout is hardly used in water-bearing sand layers because of their poor groutability. Compared with cement grout, microcement pastes possess advantages such as good groutability; however, this material is rarely used in a water-bearing sand layers as an effective reinforcement because of its poor stability, high bleeding and the easy shrinkage of hardened bodies (Wang and Sui, 2012). Although a series of chemical materials that can help mitigate these problems have been developed, they are extremely expensive and pollute the environment (Gao et al., 2018). Therefore, it is necessary to find a new material that demonstrates remarkable grouting performance while addressing the above problems; the material must not only have good working performance but also be ecofriendly and inexpensive.
The main objective of this work was to develop cement-asphalt composite grout (CACG) for water-bearing sand layers. In this work, CACG was prepared successfully via a simple strategy, and its excellent performance was demonstrated by a series of tests and an engineering application. Moreover, a possible formation mechanism is proposed.
Materials and Methods
In this study, based on the evaluation of the consulting, design and construction units, and reference to similar projects, the grouting materials for water-bearing sand layers require a moderate gel time, good pumpability, a high viscosity, low bleeding and shrinkage rates, and sufficient compressive strength. The purpose of the experiments was to determine whether the performance of CACG met the requirements for grouting water-bearing sand layers.
Raw Materials
The cement used was a superfine cement (#42.5) that complied with Chinese standard GB 175–2007. Bentonite (sodium) was obtained from a mining processing plant that conforms to the Chinese standard of bentonite (GB/T 20,973–2007). Emulsified asphalt (cationic type) was supplied by Chemical Co., Ltd. Some properties of the materials are listed in Table 1.
Testing Program
A schematic of the CACG fabrication process is shown in Figure 1. Firstly, appropriate amount of bentonite was initially mixed with the required water by a mixer at 1,000 rpm for 5 min to form fresh bentonite grout. Next, appropriate amount of superfine cement was added, and the fresh suspensions were mechanically mixed at 1,000 rpm for 5 min. Finally, the proper proportion of emulsified asphalt was added to the fresh suspensions and mixed for 5 min by vigorous stirring (1,000 rpm) to form CACG. All the processes were performed under a standard temperature (20 ± 2°C) and humidity (≥50%). CACG performance was altered by changing the number of components, and the testing scheme is shown in Table 2.
Testing Methods
In this work, the gel time of CACG was measured by the inverted cup method (tilted at 45°) as described in Zhang et al. (2018a). The fluidity was determined according to GBT-2419–2005. Bleeding was measured by conducting sedimentation tests according to DL/T5728-2016. The bulk shrinkage rate test was measured following the suggestions provided by Zhang et al. (2018b). The 28-day unconfined compressive strength (UCS) tests were conducted following the instructions of GB50107-2010 on cube specimens with a diameter ratio of 70.7 mm.
Results and Discussion
Gel Time and Fluidity
Gel time is a key parameter to characterize the pumpability of CACG. Figure 2 shows the effects of the bentonite dose and emulsified asphalt dose on the properties of CACG. As shown in Figure 2, with an increasing bentonite dose (from 5 to 15%), the gel time decreases from 150 to 87 min, and the decreasing amplitude is reduced when the bentonite dose reaches 11%. This is because bentonite particles have an excellent absorption capability, which can immobilize water and promote cement hydration (Manić et al., 1997; Pusch and Yong, 2003). With an increasing emulsified asphalt dose, the gel time slightly increases (Figure 2). When the emulsified asphalt dose is 20%, the gel time increases by 10.1%. Fluidity is a key parameter to determine the diffusion capacity of CACG. Figure 3 shows the effects of the bentonite dose and emulsified asphalt dose on the fluidity. With an increasing bentonite dose, the fluidity of CACG decreases, and a larger decrease occurs at the beginning (Figure 3); this result agrees with the results presented by Zhang et al. (2020). Figure 3 shows that with an increasing emulsified asphalt dose, the fluidity of CACG decreases. When the emulsified asphalt dose is 20%, the fluidity decreases by 23.8%. This is probably because the emulsified asphalt particles with a certain viscosity fill the space created by the cement-bentonite particles (Tregger et al., 2010).
Bleeding and Bulk Shrinkage Rates
The stability of CACG can be assessed by the bleeding and bulk shrinkage rates, and the lower bleeding and bulk shrinkage rates of CACG means it is more stable. Figure 4 and Figure 4 show the bleeding rate of CACG in the tests. With an increasing bentonite dose, the bleeding rate decreases, and the decreasing and increasing amplitudes decrease when the bentonite dose is 11%. Compared with the bentonite dose, the emulsified asphalt dose demonstrates little influence. With an increasing emulsified asphalt dose, the bleeding rate slightly decreases. As shown in Figure 5, it can be inferred that with an increasing bentonite dose, the bulk shrinkage rate of CACG decreases greatly. Figure 5 shows that the emulsified asphalt dose does not have an obvious effect on the bulk shrinkage rate. In conclusion, the bentonite dose has a positive effect on the bleeding and bulk shrinkage rates, namely, bentonite substantially decreases the bleeding and bulk shrinkage rates of CACG. Similar experimental phenomena have also been reported in the literature (e.g., Vipulanandan and Sunder, 2012).
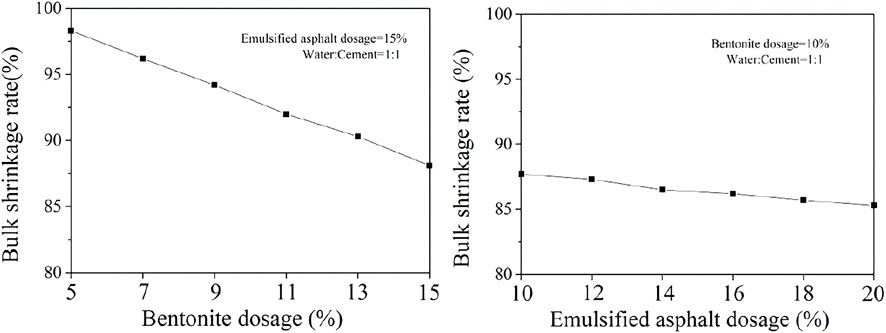
FIGURE 5. Influence of the bentonite dose and emulsified asphalt dose on the bulk shrinkage rate of CACG.
Unconfined Compressive Strength
Figure 6 shows the influence of the bentonite dose and emulsified asphalt dose on the unconfined compressive strength of 28-day CACG. Figure 6 shows that with an increasing bentonite dose, the 28-day unconfined compressive strength decreases. When the bentonite dose is 15%, the 28-day unconfined compressive strength decreases by 14.5%. Figure 6 shows that with an increasing emulsified asphalt dose, the 28-day unconfined compressive strength significantly decreases. When the emulsified asphalt dose is 20%, the 28-day unconfined compressive strength decreases by 31.5%. The bentonite in CACG adsorbs a large amount of free water and slows the hydration process of the cement (Horpibulsuk et al., 2012). Hence, the addition of excess bentonite will lead to a decreased reinforcement effect of the grouting.
Discussion
Formation Mechanism of CACG
The superior mechanical performance of CACG can be closely related to its microscopic structure. Figure 7A show the cross-sectional SEM images of CACG and cement grouts, respectively. As shown in Figure 7A, the cement gel in CACG were interconnected with each other to form a network by bentonite particles, and some asphalt film were uniformly distributed between networks to form an integrated whole. The above SEM observation shows that the structure of CACG is favorable because of its mechanical performance. The crystalline structure and composition of CACG were identified by XRD data, and the identified the typically overlapping by MDI Jade. As seen in Figure 4, the relatively strong and narrow diffraction peaks at 2θ = 5.20, 12.67, and 32.21 are generally considered as the characteristic peaks of SiO2; the diffraction peaks at 2θ = 4.89, 7.58, 34.513 and 36.46 are considered as the characteristic peaks of Ca(OH)2; the diffraction peaks at 2θ = 19.79, 27.54, 42.616 and 53.66 are considered as the characteristic peaks of Aft; the diffraction peaks at 2θ = 29.893, 47.534, and 52.116 are considered as the characteristic peaks of CaCO3.
The components of CACG are superfine cement, bentonite, emulsified asphalt and water, each of which plays its own role. The possible formation mechanism of CACG is proposed: 1) First, the superfine cement particles are uniformly dispersed in the bentonite slurry, and there is a charge attraction between the superfine cement particles and bentonite particles to form cement–bentonite balls [20-21]. Then, a number of hydration products are formed that fill the pores that form in the cement–bentonite balls. Finally, stable cement–bentonite pellet structures are created. The macroscopic manifestations are that the stability of CACG is improved, and the bleeding and bulk shrinkage rates decrease. 2) After the emulsified asphalt is added to the cement–bentonite grout, a large amount of asphalt particles will adsorb on the surface of the cement–bentonite pellet structures to form an asphalt film, which wraps around the cement hydration products. As a result, some three-dimensional network structures are formed in CACG. Moreover, the asphalt particles adsorb on the surface of bentonite particles to form a water film, which decreases the friction among the bentonite particles. Moreover, the water film causes the asphalt particles to have the same charge properties; thus, they will not agglomerate into large particles. This is the reason why CACG is both uniformly dispersed and relatively stable.
Based on the excellent synergistic interactions among the superfine cement, bentonite and emulsified asphalt, CACG is a new grouting material with excellent performance and an adjustable gel time, good fluidity, high stability and satisfactory compressive strength.
Properties of CACG in Water-Bearing Sand Layers
Generally, grouting materials in water-bearing sand layers need very high fluidity, an adjustable gel time, lower bleeding and bulk shrinkage rates, and sufficient compressive strength. In this study, based on the requirements of the project participants, the recommended parameters for the grouting material include a gel time of more than 30 min to meet the pumping requirements, a bleeding rate of less than 5% and a bulk shrinkage rate of more than 80% to meet the grouting stability requirements, and a 28 days compressive strength of more than 2 MPa to meet the reinforcement requirements. The tests show that CACG is an excellent material for grouting in water-bearing sand layers with the recommended optimal percentage ratio of 1:1:0.065:0.2 for water, superfine cement, bentonite, and emulsified asphalt.
In situ Application
The motivation to develop CACG was to solve the pre-reinforcement problem, and a river embankment was planned to be reinforced in Hunan Province, China. By exploring along the axis of the river embankment, the geological conditions included filling and large amounts of sand and granite. The sand layer proportion in the area was above 40%, most of which was under the water level of the river. The water in the sand layer, which was in the river, increased the possibility of river embankment breakage during the flood season. At the beginning of river embankment construction, traditional grouting materials (cement grout and cement-sodium silicate) were used, but these materials could not meet the field requirements of the project participants. Based on the test results of this study, CACG was used in this project. CACG was prepared following the recommended amounts: a superfine cement/water ratio of 1, a bentonite content of 6.5%, and an emulsified asphalt content of 20%. Three rows of grouting holes were arranged in a plum blossom shape pattern, and the distance between each pair of grouting holes was 1 m. After grouting completion, drill hole sampling and hydraulic pressure tests were carried out to evaluate the grouting quality. The results showed that the unconfined compressive strength of the grouting body exceeded 2 MPa and that the ground hydraulic conductivity coefficient decreased to 3.6 × 10-6 cm/s. Moreover, the cost is about 420 RMB per cubic meter according to the local market price of the raw material (superfine cement about 800 RMB per ton, bentonite about 300 RMB per ton and emulsified asphalte is approximately 1850 RMB per ton), which is very competitive comparing with using other special grouting material.
Conclusion
In this paper, superfine cement–bentonite-based emulsified asphalt composite grout (CACG) was presented and demonstrated excellent field performance. The effects of the composition and formulation of CACG on its properties were investigated by a series of laboratory test results, and the advantages of CACG were demonstrated by field tests. The following major conclusions can be drawn:
1) CACG is an excellent grouting material that has a moderate gel time, good pumpability, a high viscosity, low bleeding and shrinkage rates, and sufficient compressive strength. Thus, such grouts can be used for grouting water-bearing sand layers, i.e., challenging areas that other grouting materials, such as cement grout, usually encounter.
2) CACG is a grouting material for grouting water-bearing sand layers, and the properties of CACG are highly dependent on its composition and formulation. The gel time, fluidity, and bleeding and bulk shrinkage rates of CACG are highly affected by the bentonite dose, while its compressive strength mainly depends on the emulsified asphalt dose. The recommended amounts of the components are as follows: a water/superfine cement ratio of 1, a bentonite content of 6.5%, and an emulsified asphalt content of 20%.
3) The effectiveness and economy of CACG were verified by a field case study of grouting water-bearing sand layers in a river embankment. The field test results of the grouting work not only met the requirements of the project participants but also resulted in excellent economic value. Thus, CACG has a high application value.
Data Availability Statement
The original contributions presented in the study are included in the article/Supplementary Material, further inquiries can be directed to the corresponding author.
Author Contributions
CL: Conceptualization, Experiment, Modification and Supervision, Formal analysis; LJ: Software, Validation, Writing—review and editing; WX: Methodology, Software, Validation, Writing—review and editing; JM: Modification and Supervision, Writing—review; LJ: Experiment, Modification and Supervision; JC: Experiment, Modification and Supervision.
Funding
This work was supported by the Natural Science Foundation of Hunan Province (2021JJ60063, 2019-JJ-50336 and 2020JJ5317), and the Major water conservancy science and technology project of Hunan Province (XSKJ2021000-09).
Conflict of Interest
The authors declare that the research was conducted in the absence of any commercial or financial relationships that could be construed as a potential conflict of interest.
Publisher’s Note
All claims expressed in this article are solely those of the authors and do not necessarily represent those of their affiliated organizations, or those of the publisher, the editors and the reviewers. Any product that may be evaluated in this article, or claim that may be made by its manufacturer, is not guaranteed or endorsed by the publisher.
References
Avxhiu, R. B., and Nenaj, S. S. (2002). Evaluation of the Field Water-Bearing Potential Using Geophysical Methods. AGU Fall Meeting Abstracts.
Esfeh, P. K., and Kaynia, A. M. (2020). Earthquake Response of Monopiles and Caissons for Offshore Wind Turbines Founded in Liquefiable Soil. Soil Dyn. Earthquake Eng. 136, 106213. doi:10.1016/j.soildyn.2020.106213
Gao, B., Ye, G., Zhang, Q., Xie, Y., and Yan, B. (2021). Numerical Simulation of Suction Bucket Foundation Response Located in Liquefiable Sand under Earthquakes. Ocean Eng. 235, 109394. doi:10.1016/j.oceaneng.2021.109394
Gao, X., Wang, X., and Liu, X. (20182018). New Chemical Grouting Materials and Rapid Construction Technology for Inclined Shaft Penetrating Drift-Sand Layer in Coal Mine. Adv. Mater. Sci. Eng. 2018, 1–5. doi:10.1155/2018/2797419
Horpibulsuk, S., Phojan, W., Suddeepong, A., Chinkulkijniwat, A., and Liu, M. D. (2012). Strength Development in Blended Cement Admixed saline clay. Appl. Clay Sci. 55 (7), 44–52. doi:10.1016/j.clay.2011.10.003
Huang, Y., Yashima, A., Sawada, K., and Zhang, F. (2009). A Case Study of Seismic Response of Earth Embankment Foundation on Liquefiable Soils. J. Cent. South. Univ. Technol. 16 (6), 994–1000. doi:10.1007/s11771-009-0165-5
Manić, V., Miljković, L. J., and Djurić-Stanojević, B. (1997). The 1H T1, Study of the Influence of clay Addition on portland Cement Hydration. Appl. Magn. Reson. 13, 231–239.
Panaiotov, A., Yankov, K., Milkov, K., and Radev, I. (1987). New Shaft Sinking Technology for Water-Bearing Sand Strata. Minno Delo;(Bulgaria) 42 (6).
Pusch, R., and Yong, R. (2003). Water Saturation and Retention of Hydrophilic clay Buffer-Microstructural Aspects. Appl. Clay. Sci. 23 (1), 61–68. doi:10.1016/s0169-1317(03)00087-5
Saleh Asheghabadi, M., Sahafnia, M., Bahadori, A., and Bakhshayeshi, N. (2019). Seismic Behavior of Suction Caisson for Offshore Wind Turbine to Generate More Renewable Energy. Int. J. Environ. Sci. Technol. 16 (7), 2961–2972. doi:10.1007/s13762-018-2150-8
Sharp, M. K., and Adalier, K. (2006). Seismic Response of Earth Dam with Varying Depth of Liquefiable Foundation Layer. Soil Dyn. Earthquake Eng. 26 (11), 1028–1037. doi:10.1016/j.soildyn.2006.02.007
Tregger, N. A., Pakula, M. E., and Shah, S. P. (2010). Influence of Clays on the Rheology of Cement Pastes. Cement Concrete Res. 40, 384–391. doi:10.1016/j.cemconres.2009.11.001
Vipulanandan, C., and Sunder, S. (2012). “Effects of Meta-Kaolin Clay on the Working and Strength Properties of Cement Grouts,” in International Conference on Grouting and Deep Mixing, 1739–1747. doi:10.1061/9780784412350.0149
Wang, D., and Sui, W. (2012). Grout Diffusion Characteristics during Chemical Grouting in a Deep Water-Bearing Sand Layer. Int. J. Mining Sci. Technology 22 (4), 589–593. doi:10.1016/j.ijmst.2012.02.003
Wang, X., Yang, X., and Zeng, X. (2017). Seismic Centrifuge Modelling of Suction Bucket Foundation for Offshore Wind Turbine. Renew. Energ. 114, 1013–1022. doi:10.1016/j.renene.2017.07.103
Wu, Y.-q., Wang, K., Zhang, L.-z., and Peng, S.-h. (2018). Sand-layer Collapse Treatment: An Engineering Example from Qingdao Metro Subway Tunnel. J. Clean. Prod. 197, 19–24. doi:10.1016/j.jclepro.2018.05.260
Yu, H., Zeng, X., Li, B., and Lian, J. (2015). Centrifuge Modeling of Offshore Wind Foundations under Earthquake Loading. Soil Dyn. Earthquake Eng. 77, 402–415. doi:10.1016/j.soildyn.2015.06.014
Zhang, C., Fu, J., Yang, J., Ou, X., Ye, X., and Zhang, Y. (2018a). Formulation and Performance of Grouting Materials for Underwater Shield Tunnel Construction in Karst Ground. Construction Building Mater. 187 (7), 327–338. doi:10.1016/j.conbuildmat.2018.07.054
Zhang, C., Yang, J., Ou, X., Fu, J., Xie, Y., and Liang, X. (2018b). Clay Dosage and Water/cement Ratio of clay-cement Grout for Optimal Engineering Performance. Appl. Clay Sci. 163, 312–318. doi:10.1016/j.clay.2018.07.035
Keywords: grouting, water-bearing sand layer, superfine cement, bentonite, emulsified asphalt
Citation: Lei C, Jingwei L, Xiang W, Maiyong J, Jinyou L and Chu J (2022) Performance Study of a Superfine Cement–Bentonite-Based Emulsified Asphalt Composite Grout for Water-Bearing Sand Layers. Front. Earth Sci. 10:874341. doi: 10.3389/feart.2022.874341
Received: 12 February 2022; Accepted: 15 March 2022;
Published: 08 April 2022.
Edited by:
Chaojun Jia, Central South University, ChinaReviewed by:
Jiawei Xie, The University of Newcastle, AustraliaLianzhen Zhang, China University of Petroleum, China
Copyright © 2022 Lei, Jingwei, Xiang, Maiyong, Jinyou and Chu. This is an open-access article distributed under the terms of the Creative Commons Attribution License (CC BY). The use, distribution or reproduction in other forums is permitted, provided the original author(s) and the copyright owner(s) are credited and that the original publication in this journal is cited, in accordance with accepted academic practice. No use, distribution or reproduction is permitted which does not comply with these terms.
*Correspondence: Wang Xiang, d2FuZ3hpYW5nMDEyMDAyQDE2My5jb20=