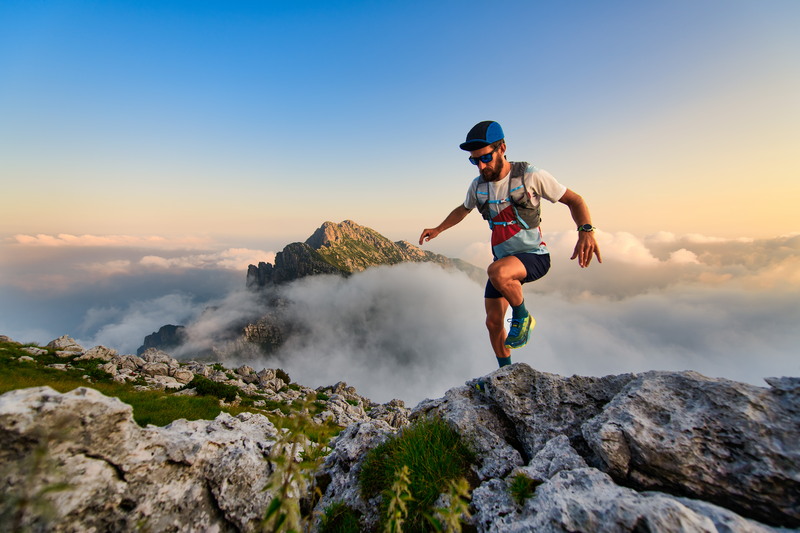
95% of researchers rate our articles as excellent or good
Learn more about the work of our research integrity team to safeguard the quality of each article we publish.
Find out more
ORIGINAL RESEARCH article
Front. Earth Sci. , 30 January 2023
Sec. Structural Geology and Tectonics
Volume 10 - 2022 | https://doi.org/10.3389/feart.2022.1110093
This article is part of the Research Topic Multiple Field/Scale Rock Mechanics in Coordinated Exploitation of Coal and its Associated Resources View all 11 articles
Due to the gradual depletion of shallow mineral resources at present, mines are now gradually entering the deep mining stage. To promote the safe and efficient green mining of deep coal resources and sustainable energy development, and to improve the production efficiency of paste filling mining, the research group has performed this study on the green filling mining technology and application of the working face. Taking working face 1241 (3) of the Xieqiao coal mine as the engineering background, the selection and experiment of filling materials were carried out, and the gangue, fly ash and cement produced by the Xieqiao coal mine were used as the filling aggregate. Next, the strength changes before and after paste filling was obtained by theoretical calculation. The strength at the early stage of filling was no less than 0.13 MPa, and that at the late stage of filling was no less than 2 MPa. Based on previous experimental research and theoretical calculation, the mixing pumping process of paste material ratio and the gangue crushing process were determined, and the filling pipeline system was designed. Then, based on the traditional coal mining technology, a filling mining technology of working face was designed and optimized. The field application of the research results shows that after the goaf of the working face had been filled, the ground pressure behavior of the coal wall of the working face was significantly weakened, and the stability of the surrounding rock of the working face was effectively controlled. Therefore, the method achieved good results, effectively controlled the stability of surrounding rock in goaf, and provided a theoretical basis and data support for realizing safe, efficient and green mining of deep coal resources. The results of this study bear important significance and application value.
Coal mines are the main energy sound in China, accounting for about 70% of the primary energy structure. In the foreseeable future, the status of coal as the main energy source in China is not expected to change. Coal is an important basic industry related to the national economic lifeline and energy security. With the gradual depletion of shallow coal resources, resource development continues to deepen. The mining of coal resources in wells several km deep has gradually become the new normal of development (De-Wei and Hai-Dong, 2019; Liu and Li, 2019). The theory and technology of synergistic and high-efficiency mining with low ecological damage of deep resources is one of the key scientific problems in the future development of mineral resources at depths of 1,000–2000 m (Min et al., 2022). Previous practice shows that filling mining can effectively control strata movement and prevent surface subsidence. Filling mining is the fundamental way in which to achieve safe, efficient and green mining of deep coal and associated resources (Li et al., 2020).
Scholars have studied the ground mine pressure behavior of the comprehensive mining working face under the goaf, and proposed that the high support pressure of the coal pillar affects the stability of the surrounding rock of the working face here, which is prone to deformation and piecing (Xing et al., 2020; Pang et al., 2021). According to the mechanical model of the compression bar stability, the critical stress required for the instability of the coal wall and wall spalling at different layer heights was obtained in Reference (Zhang et al., 2020). Scholars have also studied the filling degree of goaf caused by equivalent direct roof fall backwardness in shallow buried large mining height working faces. This method divides filling into the full filling type and general filling type (Qing et al., 2019; Wang et al., 2019). According to the deformation characteristics of filling body, scholars determined four different mining affected areas, including early strength area, roof cutting area, old roof rotation area, and masonry beam stability structure formation area (Li et al., 2022a). In addition, the high-speed vortex pulping system was designed. After optimization, the pulping effect of the filling system was stable, and the filling sedimentation reduction effect was good (Sun et al., 2019; Acharya and Kharel, 2020). In view of the spatial distribution of the strength of tailings backfill with different grades, it is found that the strength of tailings backfill with different grades will gradually increase from top to bottom in the vertical direction (Chu et al., 2019; Petrov, 2019). Scholars have also optimized the filling mining process, by proposing overburden rock migration control technologies such as prevention and control of pipeline plugging and secondary filling (Liu et al., 2020a; Li et al., 2022b). They established a coordinated bearing model of filling, surrounding rock and coal pillar, and clarified the mechanism of their joint control on the bearing capacity of overlying strata (Li et al., 2020; Liu et al., 2021a). Scholars have also clarified the control mechanism of key overlaying strata on surface subsidence. Research and development partial filling mining technologies include strip filling in mined-out areas, subsequent filling in short wall caving areas, and overburden isolation grouting filling (Liu et al., 2021b; Ic et al., 2021; Pang et al., 2021). Scholars have studied the cause of surface subsidence in filling mining, and observed that it was mainly caused by the amount of roof and floor movement before filling and the amount of filling body compression (Liu et al., 2019; Zhang et al., 2019; Lin et al., 2021). Finally, scholars have studied the surrounding rock control mechanism of gob side entry retaining in deep big high mining with filling, and proposed the performance optimization of high-water material filling bodies, which ensures the stability of the size and structure of the reserved roadway (Sun et al., 2019; Liu et al., 2020b; Li et al., 2021; Cascone et al., 2022; Li et al., 2022c; Wang et al., 2022; Zhou et al., 2022).
For green filling mining in coal mines, scholars throughout the world have performed much work and obtained numerous research results. However, the selection of filling materials, construction technology and field application for green filling mining in deep coal mines must still be studied. In this paper, comprehensive research methods such as field investigation, theoretical analysis, numerical simulation, model construction, process optimization and field application are used to carry out the filling mining of deep coal mines from the aspects of determination of filling material parameters, selection of filling materials, process optimization and field application. This paper takes working face 1241 (3) of the Xieqiao coal mine of Anhui Huainan Mining Group as the engineering background, and proposes the high-efficiency production technology and application of filling mining. The results of this study bear important theoretical guidance and application significance for green mining.
Working face 1241 (3) of the Xieqiao coal mine is located in the fourth stage of 13–1 coal seam in the east of the west wing Group C mining area. The western part of the working face begins from the system roadway of the Group C mining area in the west wing, ends at fault F10 in the east, and begins at transport groove 1231 (3) in the north, and ends at the contour line of −610 m in the south. The upper part of working face 1231 (3) has been mined, yet the underlying strata 11–2 coal seam has not been excavated.
The 13–1 coal seam assignment in working face is stable, while the floor of the coal seam fluctuates slightly along the groove direction. According to the track, transport groove, cut coal thick spot and drilling coal thickness, the thickness of the coal seam on this working face is in the range of 4.5–6.7 m, with an average coal thickness of 5.1 m. The 13–1 coal seam is dominated by semi-bright briquette coal, which is black in color, large in size, and flaky in texture; it is shiny with grease, contains siderite, and a layer of mudstone with dirt bands is locally developed. The working face can be mined to a length of 257 m, inclined length of 100 m, and mining height control in the range of 2.7–3.6 m.
The comprehensive analysis is based on ground exploration drilling data and actual measurement data of working face 1231 (3), west wing track stone door, west wing belt stone door, and other measured data. The 13–1 coal seam in this working face is generally in a southward inclined monoclinal structure. There are two faults affecting this working face, and there is no collapse column or magmatic rock intrusion phenomenon.
The production of the coal mine filling working face is generally carried out alternately according to the process of “mining-filling.” To ensure the stability of the filling body, the working face should continue to advance after the solidification of the filling body in the previous cycle has become stable. That is, to say, the paste filling slurry is required to achieve condensation and solidification within 6–8 h, and has a strength which plays a supporting role on the roof on the basis of ensuring self-stability. Otherwise, it is necessary to extend the solidification waiting time of the paste filling material until it reaches the required strength, before it can be removed and isolated for the following cycle of coal mining. The strength of the paste filling body to meet the requirements of isolated demolition is usually called early strength.
The basic role of the early strength of the paste filling body involves two aspects. The first is to ensure that the new solidified paste filling body remains stable without damage under the action of self-weight stress, and the other is to bear the weight of the rock that may be unstable under the direct roof.
The self-weight stress of the filling body is used to determine the strength required for the self-stabilization of the filling body, as shown in Formula Eq. 1:
Where σc1 is the self-stability strength of filling body, MPa; γf is the paste bulk density, MN/m3; hf—filling height, m.
The unstable part of the rock under the direct roof shall be considered according to the rock gravity of the caving arch height in the area to be filled. The support height of the filling body is about half of the width of the area to be filled (i.e., filling step).
Therefore, the early strength of paste filling body can be calculated by Formula Eq. 2:
Where σc, 6∼8h is the early strength of filling body, MPa; γr is the direct roof rock bulk density, MN/m3; and bf is the filling step, m.
The Xieqiao coal mine adopts the 3–5 m large step distance for all paste filling. According to the maximum filling step distance of 5 m, the bulk density of the filling body is 0.02 MN/m3, the direct roof rock bulk density is 0.025 MN/m3, and the filling body height is 3.6 m. The early strength of the paste filling material should not be less than 0.13 MPa.
After the working surface has been pushed, the goaf is completely filled with the filling body to control the strata movement. This is the full mining and full filling method. The filling body in this method is always in a triaxial stress state under the combined action of roof, floor and surrounding rock. Therefore, the full mining and full filling method can use the Coulomb-Moore strength criterion to calculate the strength at the late stage of filling body σ1, as shown in Formula Eq. 3:
Where σ3 is the minimum principal stress; c is the cohesive force of materials; and φ is the internal friction angle of the material.
For the goaf filling body of the Xieqiao coal mine, σ3 takes the horizontal stress, c=0.2 MPa, φ=41°. After calculation, when the mining depth is about 600 m, the triaxial compressive strength of the filling body under full mining and full filling condition is 3.2 MPa.
Three theories can be used to calculate the load of the filling pillar: effective area theory, pressure arch theory, and Wilson’s two-zone constraint theory. As the effective area method is simple and can meet the engineering requirements, it has been widely applied. According to the effective area theory, the weight of the overlying strata over the mined-out width is transferred to the width of the left filling pillar. Therefore, the load P on the filling column can be calculated by Formula Eq. 4, as follows:
Where ρ=A/(W+A); γ is the average capacity of the overburden, MN/m3; H is the average mining depth, m; ρ is the recovery rate; A is the width of the filling pillar, m; and W is the mining breadth, m.
The strength of the filling pillar reflects the bearing capacity of the overlying strata, which acts as the basis for the stability of the filling pillar. According to the rock mechanics, the strength of the filling pillar is related to the strength of the filling block, and also depends on factors such as the size of the filling pillar, mining method, and load change. Therefore, the strength of the filling block tested in the laboratory cannot be directly used to evaluate the overall strength of the on-site filling pillar, and it is necessary to perform appropriate parameter conversion between the laboratory filling block and on-site filling pillar. At present, the overall strength of the filling pillar can adopt the calculation formula related to the width height ratio proposed by Bieniawski (Liu et al., 2021b), as shown in Formula Eq. 5:
Where σc is the uniaxial compressive strength of the filling block tested in the laboratory, MPa; when W/h>5, n = 1.4; and when W/h<5, n = 1.
Since the filling surface of coal mine is a large area of filling and the height of coal seam is limited, the width-height ratio of filling pillar is much larger than 5. The parameter n in the above formula is 1.4, and the formula then becomes Formula Eq. 6:
According to the principle of coal pillar stability, the stability of filling pillar should conform to the relationship of Formula Eq. 7:
Where F is the safety factor, available from 1.2 to 2.0.
According to the above analysis, the strength at the late stage of the laboratory filling block required for filling can be deduced according to the formula, as shown in Formula Eq. 8:
It can be seen from the formula that the uniaxial strength of the filling body is greater than 1.93 MPa.
In the test of paste filling material in the Xieqiao coal mine, the uniaxial test strength of the filling body should be not less than 2 MPa.
Paste filling mining is a green mining method, that is, used to process coal gangue, coal fly ash and other solid waste on the ground into paste slurry with no critical velocity, and no need for dehydration. It uses a filling pump and gravity action to transport the paste slurry underground through a pipeline, thus filling the goaf quickly. To make gangue and other materials into qualified paste slurry, the proportion of fine particles less than 0.08 mm must reach more than 15%. Otherwise, the paste will undergo layered bleeding, which in severe cases will cause pipe blocking accidents, in which case the paste pipeline transportation system cannot operate normally.
At the beginning of filling, the important process of slurry pushing water should be carried out, so as to avoid the plugging accident of phase change of paste caused by free falling accelerated motion in drill holes for filling. In such a case, the paste will produce water-solid separation, and the bottom of the hole will undergo graded stiffening. In other words, it is necessary to fill the drilling filling pipeline with water, and control the flow velocity near the outlet of the filling pipeline, so that the first batch of paste slurry can be transported from the ground to the underground at a safe speed. In the process of slurry pushing water, the front of the paste pipeline will inevitably be diluted by the contact pipeline water, and this part of the paste diluted by water must not precipitate; if it does, it will also cause plugging accidents. The solution to this is that a small amount of paste in contact with pipeline water is made of fine particle material, usually with fly ash paste, i.e., fly ash, cement, and water mixed in equal proportion. Similarly, at the end of the filling, the paste must be flushed out of the filling pipe with water, and a small amount of fly ash paste must also be addded.
To solve the problem of difficult discharge of gangue in the Xieqiao coal mine, coal gangue is chosen as the paste filling aggregate, and the coal fly ash and cement are produced by the mine.
1) Physicochemical analysis of filling materials
Using coal gangue as the filling aggregate, unprocessed washed gangue and raw gangue cannot meet the requirements in production since, as a filling aggregate, it must be crushed to a size fraction with a maximum particle size of about 15 mm. Figure 1 shows the particle grade of crushed gangue, and Figure 2 is the curve partition diagram of the broken gangue particles.
It can be seen from the curve partition diagram that the gangue of the Xieqiao coal mine after crushing is mainly distributed in zone II. According to the national standard for fly ash for cement and concrete (GB1596-2017), the standard consistency water demand ratio of grade Ⅱ fly ash must exceed 105%, and the residual amount of 0.045 mm square hole sieve must not exceed 30%. The standard for grade III is 45%. To ensure the performance of filling slurry, fly ash should be sampled and analyzed when entering the field, to ensure that the fly ash is not lower than the grade III standard.
2) Mechanical experiment of backfill
After determining the filling materials, the research group carried out indoor test experiments on the strength of the filling body to determine whether the strength of the filling body could meet the needs of the field working face. The prepared filling paste material is shown in Figure 3. To reduce the influence of accidental errors on the experimental results, three groups of filling paste strength tests were carried out in this study. First, the filling paste was made. After full curing, the standard sample was removed with a coring machine, and it was placed in the mechanical testing system for testing.
The filling material after being damaged under compression is shown in Figure 4, and the stress-strain curve of the filling body is shown in Figure 5. It can be seen from Figure 4 that the failure mode of filling body under compression is basically the same as that of ordinary rock. The results show that the paste filling material has similar properties with rock after hardening. It can be seen from Figure 5 that the peak strengths of the hardened filling paste materials are 3.68, 3.71, and 3.58 MPa, respectively, with an average of 3.65 MPa. This exceeds the theoretical calculation value of 2 MPa, and the results meet the requirements of goaf filling at the working face. In addition, the filling body also has a certain post peak strength, which plays a significant role in controlling the stability of the goaf.
In summary, the filling materials obtained in this study are highly consistent with the rock materials in terms of strength and properties, and can meet the needs of goaf filling in deep coal mines.
1) System
The filling system of the Xieqiao coal mine consists of a ground filling station, filling pipeline and filling working face.
Ground filling station: The ground filling station is the production line of paste slurry, including the preparation, storage, transportation, batching, mixing, pumping, automatic control, and other links of raw materials. Automatic control is the central command system that ensures the reliable operation of the filling station. The paste filling system includes much equipment and complex technology, and is closely related to the production of the working face. It requires a highly automated control system as a guarantee.
Filling pipeline: This is the delivery means of paste slurry, including ground pipeline, underground pipeline and working surface pipeline along the control gate valve.
Filling face: The key devices of the filling face are the filling hydraulic support and shearer, which act as the key links affecting its efficiency and safety.
The filling system process mainly includes the mixing pumping process and gangue crushing process.
2) Proportioning mixing pumping process
The mixing pumping system adopts a double system arrangement, and the two systems run simultaneously. The flow chart of the designed mixing pumping process is shown in Figure 3. All of the materials after batching and weighing are added to the mixer and stirred into qualified paste, then added to the filling pump, then through the filling pipeline the materials are transported to the filling face to be filled. To ensure the safety and reliability of the system, two filling pumps were set up, with one as a backup, as shown in Figure 6:
3) Gangue crushing process
Mine gangue was adopted for the filling of the Xieqiao coal mine. The maximum particle size of gangue designed to enter the filling system was 500 mm. The maximum particle size of gangue after crushing processing needed to be controlled within 15 mm, and the gangue powder with particle size less than 0.08 mm was controlled at about 15%. Therefore, the gangue design adopted two-stage crushing processing, and the process flow is as shown in Figure 7:
1) Filling pipeline system composition
The function of paste filling pipeline system is to safely transport the paste filling material to the goaf under the action of pumping pressure or self-weight pressure of the filling pump. The filling pipeline system is mainly composed of the ground filling pipeline, filling drilling riser, filling trunk pipeline system, pipeline pressure online detection system, filling working face pipeline system, drainage pipeline, and its supporting valve group.
2) Filling pipeline path
The working face groove filling pipeline was arranged in the transportation groove and installed near the non-production side. The pipeline diameter was 219 mm and the wall thickness was 12 mm.
According to the field conditions of the Xieqiao coal mine and the opinions of mine owner, the filling path of filling working face 1241 (3) was determined as follows:
Ground filling station (filling pump) → ground pipeline 140 m → drilling pipeline 635 m → hole bottom chamber 5 m → −610 west wing track stone 523 m → transport groove 1241 (3) contact lane 50 m → transport groove 1241 (3) 400 m → working face 1241 (3) 100 m. The distribution valve was set up in the filling working face to fill the goaf. The filling pipeline system designed in this paper is mainly designed for the mining system of deep coal mines, which can fully meet the working requirements from the ground to the filling face, and can be optimized and adjusted according to different needs.
Along the pipeline are arranged in the floor, a fixed device is set, the spacing of which did not exceed 15 m, and paste filling pipeline field layout is shown as in Figure 8.
The coal seam in the working face was stable, with an average thickness of 5.1 m. The design adopted a single-strike long-wall comprehensive mechanized filling mining method, with backward mining in the area, and a filling method to deal with the goaf. Because the mine filling mining area was mainly concentrated at the late stage of CoalSeams in No.6 (with a coal thickness of about 3 m), the comprehensive rate of filling support multi coal seam adaptability, and the comprehensive efficiency of filling mining, the first filling face of working face 1241 (3) selection model for ZC5600/20/38 paste filling mining support. The mining thickness was set to 3.5 m, with top coal mining, as shown in Figure 9. The hydraulic support can adapt to multi seam mining, and can be adjusted according to the occurrence conditions of coal seams, thus improving the comprehensive efficiency of filling mining.
The filling mining area adopted long wall and fully mechanized filling mining method. The filling test of mining face 1241 (3) adopted long wall, comprehensive mechanized paste filling mining, with single knife circulation footage 0.8 m, a mining height of 3.5 m, the top coal set at 1.3 m, and single-class footage of 1.6 m. Five classes (40 h) were taken to complete a filling cycle, with a filling step 3.2 m, among which there were two classes of production, one class of isolation, one class of filling, and one class of solidification overhaul.
The working face adopted special paste filling support, and the single mining-filling circulation process was as follows: cutting coal → hanging net → moving support → pushing conveyor → filling area isolation → filling → solidification overhaul, as shown in Figure 10. A charge-back cycle is completed every 40 h. Compared with the traditional coal mining process, the process increased the filling area isolation, filling, solidification maintenance, and other processes.
Using the FLAC3D numerical simulation method, the distribution law of principal stress before and after filling in the goaf of the working face was simulated and analyzed. It can be seen from Figure 11 that there was a significant difference between the goaf filled and unfilled in the working face. After the goaf of the working face had been filled, the abutment pressure at the coal wall of the working face decreased significantly, and the stress concentration coefficient was about 2.2. When the goaf was not filled, the stress concentration factor at the coal wall was about 2.5. It can be seen from the figure that, after the goaf of the working face had been filled, the ground pressure appearance of the coal wall of the working face was significantly weakened, and the stability of the surrounding rock of the working face was effectively controlled.
It can be seen from Figure 12; Table 1 that, after the goaf had been treated by the filling method, the deformation values of the surface buildings were within the safe range. The results show that the filling of the goaf could not only effectively weaken the ground pressure appearance of the working face, but also effectively controlled the surface subsidence.
It can be concluded that the field application of the research results has achieved good results, effectively controlled the stability of surrounding rock in the goaf and the subsidence of the surface, and provided a theoretical basis and data support to achieve safe, efficient and green mining of deep coal resources, which bears important significance and promotion and application value.
Based on the above analysis, it can be concluded that the stress of coal wall before and after filling is obvious. Due to the existence of filling body, the ground pressure manifestation of the working face is significantly weakened, which provides favorable conditions for the stability control of the working face.
In this paper, the comprehensive research methods of indoor experiment, theoretical analysis and field application were used to carry out the research on green filling mining in deep coal mines. The study determines the filling materials and optimizes the filling mining technology of deep coal mines, which provides theoretical and data support for the filling mining of deep coal mines, and has important significance and value. The following main conclusions were obtained.
1) Taking working face 1241 (3) of the Xieqiao coal mine as the engineering background, this paper adopted the methods of indoor test and theoretical analysis to carry out the selection and experiment of filling materials. The minimum strengths of the filling body in the early and late stages were 0.13 and 2 MPa, respectively. The self-produced gangue, fly ash and cement of the Xieqiao coal mine were selected as the filling aggregate.
2) Based on the technical conditions of coal seam occurrence and mining in the Xieqiao coal mine, a single-strike longwall comprehensive mechanized filling mining technology was proposed. A safe and efficient filling mining technique was designed, and the supporting equipment for filling mining was improved, including the hydraulic support of the working face and the filling pipeline equipment.
3) The field application of the research results shows that, after the goaf of the working face had been filled, the ground pressure behavior of the coal wall of the working face was significantly weakened, and the stability of the surrounding rock of the working face was effectively controlled. The study has thus achieved good results, effectively controlled the stability of surrounding rock in goaf, and provided a theoretical basis and data support for achieving safe, efficient and green mining of deep coal resources. This bears important significance and application value.
The original contributions presented in the study are included in the article/supplementary material, further inquiries can be directed to the corresponding author.
Data curation,JH and CL Formal analysis, LY; Investigation, JL and FL All authors have read and agreed to the published version of the manuscript.
YL was employed by the company Sichuan Geotechnical Intelligent Measurement Technology Co, Ltd, Panzhihua.
JL and LF were employed by the company Huainan Mining (Group) Co., Ltd.
The remaining authors declare that the research was conducted in the absence of any commercial or financial relationships that could be construed as a potential conflict of interest.
All claims expressed in this article are solely those of the authors and do not necessarily represent those of their affiliated organizations, or those of the publisher, the editors and the reviewers. Any product that may be evaluated in this article, or claim that may be made by its manufacturer, is not guaranteed or endorsed by the publisher.
Acharya, B. S., and Kharel, G. (2020). Acid mine drainage from coal mining in the United States – An overview. J. Hydrology 588, 125061. doi:10.1016/j.jhydrol.2020.125061
Cascone, T., Chelvanambi, M., and Wargo, J. A. (2022). Immunotherapy response-associated akkermansia: Canary in a coal mine. Trends Immunol. 43, 337–339. doi:10.1016/j.it.2022.03.007
Chu, W., Xiong, W., Ge, Z., and Cheng, Q. (2019). Predicting mine water inflow and groundwater levels for coal mining operations in the pangpangta coalfield, China. Environ. Earth Sci. 78 (5).
De-Wei, X. U., and Hai-Dong, L. I. (2019). Study on hydrogeological characteristics and water filling factors of wulasu mining area in dongsheng coalfield. Ground Water.
Ic, A., Ey, B., and Aoy, C. (2021). Sodium silicate effect on setting properties, strength behavior and microstructure of cemented coal fly ash backfill. Powder Technol. 384.
Li, H., Guo, K., and Guo, G. (2022). Strata and surface influence range of deep coal mining for mine land reuse. Environ. Earth Sci. 81, 68. doi:10.1007/s12665-022-10174-6
Li, L., Xie, D., Wei, J., Yin, H., Zhang, W., Man, X., et al. (2020). Analysis and control of water inrush under high-pressure and complex karstic water-filling conditions. Environ. Earth Sci. 79 (21), 493. doi:10.1007/s12665-020-09242-6
Li, S., Wang, J., Zhang, J., and Zhang, M. (2022). Effects of mining and reclamation on the spatial variability of soil particle size distribution in an underground coalmine area: A combination method using multi-fractal and joint multi-fractal theories. Environ. earth Sci. 81 (4), 117. doi:10.1007/s12665-022-10257-4
Li, X. L., Chen, S. J., Wang, S., Zhao, M., and Liu, H. (2021). Study on in situ stress distribution law of the deep mine taking Linyi Mining area as an example. Adv. Mater. Sci. Eng. 9 (4), 5594181–5594211. doi:10.1155/2021/5594181
Li, X. S., Peng, J., Xie, Y. L., Li, Q., Zhou, T., Wang, J., et al. (2022). Influence of high-temperature treatment on strength and failure behaviors of a quartz-rich sandstone under true triaxial condition. Lithosphere 2022, 3086647. doi:10.2113/2022/3086647
Lin, H., Yang, R., Lu, B., Li, Y., Fang, S., Fan, Z., et al. (2021). Overlying strata movement law of continuous mining and continuous backfilling cemented-fill mining. Environ. earth Sci. 80, 688. doi:10.1007/s12665-021-09993-w
Liu, H., Zhang, M., Su, L., Chen, X., and Sun, A. (2021). A boundary model of terrain reconstruction in a coal-mining subsidence waterlogged area. Environ. Earth Sci. 80 (5), 187. doi:10.1007/s12665-021-09508-7
Liu, S., Fu, M., Jia, H., and Li, W. (2019). Shear characteristics of cuneiform reaming anchorage bolts in coal mine roadways. Rock Mech. Rock Eng. 52 (6), 1931–1943. doi:10.1007/s00603-018-1670-3
Liu, S., and Li, W. (2019). Indicators sensitivity analysis for environmental engineering geological patterns caused by underground coal mining with integrating variable weight theory and improved matter-element extension model. Sci. Total Environ. 686 (10), 606–618. doi:10.1016/j.scitotenv.2019.04.393
Liu, S. M., Li, X. L., Wang, D. K., and Zhang, D. M. (2020). Investigations on the mechanism of the microstructural evolution of different coal ranks under liquid nitrogen cold soaking. Energy Sources A: Recovery Util. Environ. Eff., 1–17. doi:10.1080/15567036.2020.1841856
Liu, W., Liu, S., Tang, C., Qin, W., and Zhang, J. (2020). Evaluation of surface water quality after mine closure in the coal-mining region of guizhou, China. Environ. Earth Sci. 79 (18), 427. doi:10.1007/s12665-020-09167-0
Liu, Z., Dong, S., Wang, H., Wang, X., Nan, S., and Liu, D. (2021). Macroscopic and mesoscopic development characteristics of the top strata of middle ordovician limestone in the hanxing mining area. Environ. Earth Sci. 80 (16), 526–617. doi:10.1007/s12665-021-09859-1
Min, X., Xu, D., Hu, X., and Li, X. (2022). Changes in total organic carbon and organic carbon fractions of reclaimed minesoils in response to the filling of different substrates. J. Environ. Manag. 312, 114928. doi:10.1016/j.jenvman.2022.114928
Pang, L., Liu, W., Zheng, Q., Du, Y., Meng, X., and Li, X. (2021). Evaluation and analysis of metal mine filling based on numerical simulation and actual measurement. Environ. Earth Sci. 80, 505. doi:10.1007/s12665-021-09844-8
Petrov, P. (2019). Chemical and physicochemical parameters of recultivated embankments of maritsa-iztok mine in relation to development of soil formation process. Nat. Rev. Neurosci. 20 (2).
Qing, Z., Zheng, X., and Shao, M. (2019). Changes of solute transport characteristics in soil profile after mining at an opencast coal mine site on the loess plateau, China. Sci. Total Environ. 665, 142–152. doi:10.1016/j.scitotenv.2019.02.035
Sun, W., Xiao, E., Krumins, V., Dong, Y., Li, B., Deng, J., et al. (2019). Comparative analyses of the microbial communities inhabiting coal mining waste dump and an adjacent acid mine drainage creek. Microb. Ecol. 78, 651–664. doi:10.1007/s00248-019-01335-5
Wang, S., Li, X. L., and Qin, Q. Z. (2022). Study on surrounding rock control and support stability of Ultra-large height mining face. Energies 15 (18), 6811. doi:10.3390/en15186811
Wang, Z., Li, H., and Tang, R. (2019). Network analysis of coal mine hazards based on text mining and link prediction. Int. J. Mod. Phys. C 30 (07), 1940009–1940034. doi:10.1142/s0129183119400096
Xing, Y., Wang, J., Shaheen, S. M., Feng, X., Rinklebe, J., Zhang, H., et al. (2020). Mitigation of mercury accumulation in rice using rice hull-derived biochar as soil amendment: A field investigation. J. Hazard. Mater. 388, 121747. doi:10.1016/j.jhazmat.2019.121747
Zhang, J., Chen, L., Chen, Y., Ge, R., Shi, X., Zhou, K., et al. (2020). Discrimination of water-inrush source and evolution analysis of hydrochemical environment under mining in renlou coal mine, anhui province, China. Environ. Earth Sci. 79 (2), 61. doi:10.1007/s12665-019-8803-1
Zhang, J., Liu, J., and Wang, X. (2019). Research on risk assessment index system of coal mine occupational disease based on unascertained measure theory. Basic & Clin. Pharmacol. Toxicol. 125.
Keywords: sustainable development, deep mining, green mining, filling mining, deep coal mine
Citation: Hou J, Li C, Yuan L, Li J and Liu F (2023) Study on green filling mining technology and its application in deep coal mines: A case study in the Xieqiao coal mine. Front. Earth Sci. 10:1110093. doi: 10.3389/feart.2022.1110093
Received: 28 November 2022; Accepted: 09 December 2022;
Published: 30 January 2023.
Edited by:
Lishuai Jiang, Shandong University of Science and Technology, ChinaReviewed by:
Xuelong Li, Shandong University of Science and Technology, ChinaCopyright © 2023 Hou, Li, Yuan, Li and Liu. This is an open-access article distributed under the terms of the Creative Commons Attribution License (CC BY). The use, distribution or reproduction in other forums is permitted, provided the original author(s) and the copyright owner(s) are credited and that the original publication in this journal is cited, in accordance with accepted academic practice. No use, distribution or reproduction is permitted which does not comply with these terms.
*Correspondence: Junling Hou, aG91anVubGluZzIwMjJAMTYzLmNvbQ==
Disclaimer: All claims expressed in this article are solely those of the authors and do not necessarily represent those of their affiliated organizations, or those of the publisher, the editors and the reviewers. Any product that may be evaluated in this article or claim that may be made by its manufacturer is not guaranteed or endorsed by the publisher.
Research integrity at Frontiers
Learn more about the work of our research integrity team to safeguard the quality of each article we publish.