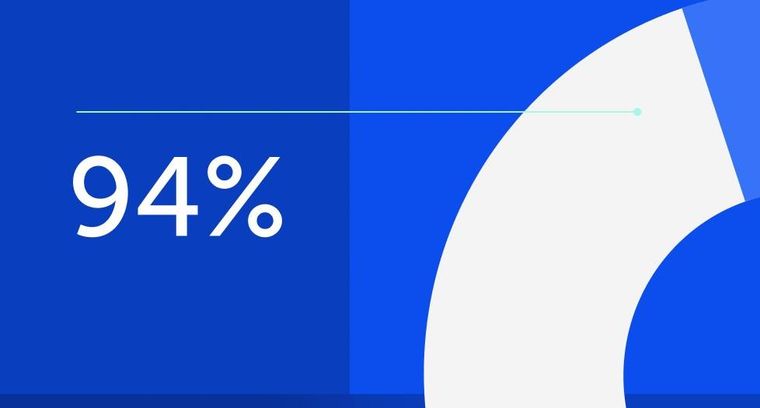
94% of researchers rate our articles as excellent or good
Learn more about the work of our research integrity team to safeguard the quality of each article we publish.
Find out more
ORIGINAL RESEARCH article
Front. Earth Sci., 30 January 2023
Sec. Structural Geology and Tectonics
Volume 10 - 2022 | https://doi.org/10.3389/feart.2022.1098674
This article is part of the Research TopicMultiple Field/Scale Rock Mechanics in Coordinated Exploitation of Coal and its Associated ResourcesView all 11 articles
As the key link of coal gangue slurry filling, slurry pipeline transportation is an important guarantee to realize the slurry mixing and safe transportation of gangue from solid powder. To realize the underground excavation gangue of the Huangling No. 2 coal mine without raising the ground, the slurry filling technology is proposed to transport the slurry made by gangue through the pipeline and fill it into the goaf. The phase composition and microstructure characteristics of underground excavation gangue in the Huangling No. 2 coal mine were analyzed by X-ray diffraction and an electron microscope scanning test, the slurry-forming properties of gangue powder with different particle sizes and gradations were studied, and the influence of gangue slurry concentration on its rheological properties was analyzed. The experimental results show that the gangue powder crushed using a cage crusher can be made into stable slurry when the particle grading size is the natural crushing gradation with the upper limit of particle size less than 3 mm. The viscosity of the slurry is positively correlated with the concentration. When the concentration is below 70%, the increase in viscosity is small, and when the concentration is above 70%, the increase in viscosity is significant. It is determined that the concentration of the Huangling No. 2 coal mine slurry is 70%. Based on the determination of slurry preparation parameters, the simulation analysis of slurry pipeline transportation was carried out, the influence of design velocity on the velocity distribution of the pipeline section and the variation law of slurry concentration was explored, and the design velocity of the project is determined to be 1.5 m/s. The engineering practice shows that the slurry preparation parameters are reasonable. The crushing and pulping of gangue under the ground and the safe transportation of a 6 km pipeline are realized, which provides a reference for similar engineering projects.
Gangue slurry filling is a technical method of crushing gangue into powder to produce slurry, which is transported through a pipeline and injected into the goaf of the working face. It can effectively solve the problem of green disposal of gangue faced by the coal industry (Matousek, 2002; Senapati and Mishra, 2017; Wang et al., 2018; Cruz et al., 2019), and its technical key lies in the reasonable determination of the main parameters of gangue slurry pulping and pipeline transportation, to ensure the long-distance safe transportation of slurry (Chen et al., 2015). The slurry pipeline transportation technology can use the small pipeline to complete the efficient transportation and backfilling of gangue, which has little impact on the normal production of underground coal mines (Qi et al., 2018; Wu et al., 2018; Rao et al., 2020; Wu et al., 2022). This technology has been continuously applied in engineering practice with its unique technical advantages (Hz et al., 2017; Singh et al., 2017), but it still needs to be continuously developed and improved to adapt to the transportation of different materials and different working conditions. Therefore, scholars at home and abroad have conducted many experiments and research studies.
Jaworska-Jóźwiak (2021) studied the influence of solid concentration on the shear stress and viscosity of lime slurry, obtained the variation characteristics of shear stress with concentration in different concentration ranges, and pointed out that the determination of the boundary concentration above which the increase in shear stress is exponential is a fundamental guideline in determining the transport parameters of fine-dispersive lime slurry. Through this method, the transportation efficiency and water consumption of the slurry pipeline transportation system are greatly improved. Singh et al. (2015) investigated the effect of particle size, solid concentration, and temperature on the rheology of the coal–water slurry through rheological and settlement experiments; the relationship between the slurry concentration and apparent viscosity of the coal–water mixture under different particle-size conditions was obtained, the transformation characteristics of the coal–water mixture state were analyzed, and the rheological model was obtained by fitting the change in the flow behavior of coal slurries. Feng et al. (2022) found that the flow velocity directly affects the transportation properties and then affects the pipe blockage and wear during the pipeline transportation of backfill slurry. Through experiments, the movement characteristics of solid materials in slurry at different flow rates were studied. The research results provide a reference for determining the reasonable flow rate of backfill slurry pipeline transportation. Li MZ (Senapati and Pothal, 2017; Li et al., 2018; Cheng et al., 2020; Li et al., 2020) analyzed the influence of the interaction between particles of different sizes on the particle dynamics, studied the influence of adding finer particles on the transport characteristics of the slurry in pipelines, and obtained the relationship between the main parameters of slurry and the movement law of solid particles during pipeline transportation.
The aforementioned scholars have carried out detailed studies on the function relationship of key parameters in the process of slurry pipeline transportation, which enriched the technical system of slurry pipeline transportation. Based on the previous research results, taking the second-phase slurry filling project of the Huangling No. 2 coal mine as the background, this study determined the key parameters of gangue slurry preparation on the basis of mastering the basic physical and chemical characteristics of gangue and slurry through on-site gangue sampling, physical and chemical analysis, slump and rheological experiments and determined the core parameters of slurry pipeline transportation through numerical simulation and analysis. The research results provide support for the industrial application of the grouting filling project for the green disposal of gangue in the Huangling No. 2 coal mine.
The Huangling No. 2 coal mine is located in Yan’an City, Shaanxi Province. The designed production capacity of the mine is 10.0 Mt/a. and the underground roadway excavation produces gangue of 0.2 Mt/a. As the minefield is located in the Huangling National Forest Park Reserve, to avoid environmental pollution caused by the ground discharge of gangue, the mine plans to use the method of gangue slurry filling to convert the gangue into slurry and inject it into the goaf.
The gangue slurry filling project of the Huangling No.2 coal mine is divided into two phases. The first phase of the project arranges the crushing and pulping system near the roadway of the working face. The gangue excavated underground was transported to the crushing and pulping system by car. After converting it into slurry, it was transported and injected into the goaf of the working face by the pipeline. The advantage of this arrangement is that the slurry pipeline transmission distance is short, usually less than 3 km, but the filling system only serves one working face, and its position will move continuously with the continuity of the working face. At present, the Huangling No. 2 coal mine has completed the first phase of the project, which has successfully verified the feasibility of slurry filling technology. Now the coal mine plans to carry out the second phase of the project. The second phase adopts a centralized layout, and the filling system is arranged near the gangue bin at the bottom of the shaft to make it serve the whole mine. However, this centralized layout mode has the disadvantage of a long slurry transportation distance, up to 6 km. Therefore, to ensure the success of the project, it is necessary to study the key parameters of gangue slurry preparation and pipeline transportation in detail. The system layout of phase II is shown in Figure 1.
To ensure the accuracy and credibility of the experimental results, the gangue used in this experiment was taken from the gangue bin of the Huangling No. 2 coal mine through field sampling. The particle size of the sampled gangue is −200 mm. Before the experiment, it was crushed to a particle size of −8 mm using a double-toothed roll crusher and a cage crusher. Combined with the actual situation of the project, the method of controlling the upper limit was used to change the particle size gradation of gangue powder, and the particle size and gradation within the limit were not adjusted. The powder with the upper limit of −8 mm, −5 mm, −3 mm, and −1.25 mm is named sample 1, sample 2, sample 3, and sample 4, respectively. Statistics of the particle size distribution curves of the four groups of gangue powder samples are shown in Figure 2.
The composition of gangue powder is tested using an X-ray diffractometer, and the test results are shown in Figure 3.
According to the standard powder diffraction data of various substances provided by the National Data Center of the Powder Diffraction Federation (TCPDS-ICDD), a comparative analysis was carried out according to the standard analysis method. The analysis results are as follows: the phase composition mainly includes quartz, kaolinite, some feldspar, mica, and a small amount of chlorite, calcite, siderite, pyrite, and other minerals.
To characterize the appearance of the crushed gangue particles, the scanning electron microscope test was carried out on them. Under the condition of high magnification (shown in the 1,000x picture), it can be seen that there are some cracks on the surface and the surface is uneven, as shown in Figure 4.
Combined with the test results of the X-ray diffraction energy spectrum, the gangue contains more kaolinite (flaky) and other minerals, and a small amount of “large” particles are wrapped by a large number of small particle sizes and flaky particles. In the pulping process, flaky kaolin minerals can be used as fine particles to wrap and suspend the gangue with large particle size, which is conducive to ensuring the stability of the slurry and realizing long-distance stable transportation (Sadrossadat et al., 2020).
To study the influence of the particle size and gradation of crushed gangue powder on the quality of slurry preparation, four groups of gangue samples with different particle sizes and gradations were configured into slurry with the concentration of 65%, 70%, and 75% respectively. No other additives or curing agents are added to the gangue slurry. The fluidity and stability of the configured slurry were studied through a slump experiment. The experiment process and results are shown in Figure 5, 6.
FIGURE 5. Slump test of gangue slurry with different concentrations. (A) Sample 1 at 65%, (B) sample 2 at 65%, (C) sample 3 at 65%, (D) sample 4 at 65%, (E) sample 1 at 70%, (F) sample 2 at 70%, (G) sample 3 at 70%, (H) sample 4 at 70%, (I) sample 1 at 75%, (J) sample 2 at 75%, (K) sample 3 at 75%, and (L) sample 4 at 75%.
The experiment results show that the slump of sample 1 is 283 mm at the concentration of 65%, and the stability and fluidity of the slurry are relatively good, but the distribution of large particles in the slurry can be clearly seen from the diffused slurry. When the concentration increases to 70% and 75%, there is an obvious material accumulation shape in the middle of the slump experiment, which indicates that the stability of the slurry is poor, easy to precipitate, and insufficient to form a stable and fluid slurry. The experiment results of sample 2 are better than those of sample 1. However, when the slurry concentration reaches 75%, there is also an obvious precipitation and accumulation due to the large solid material particles. When the upper limit of the particle size of gangue is reduced to less than 3mm, the experimental results of samples 3 and 4 show that the stability of the gangue slurry is good, the slurry basically remains homogeneous in the diffusion process, and there is no obvious accumulation of large particles in the middle. Therefore, it is considered that the gangue powder with particle grading of samples 3 and 4 can be made into stable slurry (Lee et al., 2009; Zhou et al., 2021).
Through the analysis of the four groups of gangue slump experiments with different particle sizes and gradations, the results show that the larger the content of coarse particles in the slurry, the worse its stability because the coarse particles are easily precipitated in the slurry flow process and cannot form a stable slurry (Vlasak and Chara, 2011; Li et al., 2022; Matoušek et al., 2022). When the particle grading size of the gangue powder is the natural crushing gradation with the upper limit of particle size less than 3 mm, it can be configured into slurry with good stability, that is, samples 3 and 4 meet the requirements of pulping. Therefore, to ensure the stability of the slurry and reduce the crushing cost of the gangue as much as possible, sample 3 is determined to be used as the gangue powder of the project, that is, it is determined to use the natural crushing gradation gangue powder with the upper limit of particle size of 3 mm for pulping.
On the basis of determining the particle size and gradation of the gangue powder, the gangue slurry with a mass concentration of 66%–76% was prepared, and the rheological properties of the gangue slurry were tested using an Anton Paar rheometer. The test was conducted in the shear mode. The rheological characteristic curves of slurries with different concentrations are sorted out according to the experimental test results, as shown in Figure 7.
It can be seen from Figure 7 that the shear stress of gangue slurry generally shows an increasing trend with the increase in the shear rate. When the slurry concentration is in the range of 66%–74%, the increase in the shear stress of slurry is gentle with the increase of shear rate. When the slurry concentration reaches 76%, the shear stress increases obviously with the increase in the shear rate. At the same shear rate, when the slurry concentration is less than 70%, the shear stress increases slightly with the increase of the slurry concentration. When the slurry concentration is less than 70%, the shear stress increases obviously with the increase in the slurry concentration.
The experimental results show that the higher the concentration, the greater the shear stress and shear rate required for the elastoplastic state transition of the slurry under the same particle size gradation. It can be seen from the analysis that the greater the concentration of coal gangue slurry is, the greater the force between the particles in the gangue slurry is, and the gangue particles are firmly bonded. Therefore, a larger shear force and shear rate are required to change the elastic state. The smaller the concentration of coal gangue slurry is, the weaker the internal structure of the slurry is and the easier it is to cause the coarse particles of the gangue to sink, causing segregation. According to the rheological experimental data, the relationship between the shear stress and viscosity of the slurry with different concentrations is drawn, as shown in Figure 8.
Figure 8 shows that the plastic viscosity and yield stress of gangue slurry generally increase with the increase in concentration (Singh et al., 2020). However, the changes in different concentration ranges are different. In the range of 66–70%, the plastic viscosity of the slurry increases slowly with the increase in the concentration. When the slurry concentration is greater than 70%, the plastic viscosity of the slurry increases rapidly with the increase in the concentration. In the range of 66–72%, the yield stress of the slurry increases slowly with the increase in the concentration. When the slurry concentration is greater than 72%, the yield stress of the slurry increases rapidly with the increase in the concentration. After the slurry concentration continues to increase to a certain extent, minor changes will have a significant impact on the viscosity. In order to ensure the safe transportation of the slurry, the concentration of the slurry prepared in this test is determined to be 70%.
The gangue slurry shows complex mechanical phenomena in the process of pipeline transportation. At present, there is no accurate method to describe the flow characteristics of slurry in the pipeline (Gao et al., 2020). To study the internal particle migration law during the pipeline transportation of gangue slurry, Ansys Fluent software is used to simulate the pipeline transportation of high-concentration gangue slurry, study the micro-velocity distribution law of gangue slurry during pipeline transportation, and analyze the solid particle settlement law, so as to reasonably design the transportation velocity and ensure the safe operation of the system.
The Euler model is selected as the calculation model of this experiment, and the model is set as the standard K-εModel (Rathore et al., 2021). The geometric model is set according to the actual transportation conditions of the Huangling No. 2 coal mine, and an additional 4-km horizontal pipeline is set, that is, the total length of the model pipeline is 10 km, and the pipeline diameter is 99 mm.
The flow medium in the pipeline is the solid–liquid two-phase flow mixed with water and gangue particles. The liquid phase and solid phase are set at the inlet of the pipeline, in which the water density is 1,000 kg/m3 and the gangue density is 2,340 kg/m3. The particle-size grading of the gangue powder and the viscosity of the slurry are set according to the experimental test results.
This numerical simulation takes the gangue slurry with 70% concentration as the basic condition, and takes the slurry inlet velocity as the main factor to simulate the movement law of slurry in the pipeline during the transportation at the velocity of 0.5 m/s, 1.0 m/s, 1.5 m/s, and 2.0 m/s, respectively, so as to reasonably determine the transportation velocity of the industrial project.
To master the velocity, concentration distribution and change characteristics of the slurry in the pipeline under different working conditions, the velocity, concentration, and other data in the whole pipeline are monitored to analyze the stability of slurry pipeline transportation.
The velocity distribution cloud maps at different positions in the model are extracted. The maps show that the cross-section velocity of the pipeline experiences the process from uniformity to stratification and then to stability in the process of slurry pipeline transportation, which can be roughly divided into three stages. Stage 1: the velocity in the pipeline section is evenly distributed, stage 2: the velocity increases in the center of the pipeline, and stage 3: the velocity distribution in the pipeline is stable, as shown in Figure 9.
FIGURE 9. Velocity distribution cloud diagram in the pipeline section. (A) Stage 1. (B) Stage 2. (C) Stage 3.
Due to the same inlet velocity, the slurry flow velocity in the pipe section at the initial stage of transportation is basically uniform. With the increase of the conveying distance, the influence of friction between the slurry and pipe wall on the slurry movement gradually appears, resulting in the decrease in slurry velocity around the pipe wall. On the condition that the flow is constant, the velocity of the slurry in the center of the pipeline increases gradually, and finally, the velocity of the pipeline section is relatively stable.
The velocity distribution cloud diagram of the pipeline section when the velocity of the gangue slurry reaches the equilibrium state at different initial velocities during pipeline transportation is shown in Figure 9. It can be seen from Figure 10 that ① the conveying speed of the slurry in the pipeline section is distributed in a concentric circle, and the velocity distribution in the vertical and horizontal directions inside the pipeline is basically symmetrical. The velocity of slurry at the center of the pipeline is higher and that at the pipe wall is lower. ② According to the velocity distribution of slurry at the pipeline section, the section velocity of slurry is divided into a middle-flow core area and non-flow core area. When the inlet velocity increases from 0.5 m/s to 2.0 m/s, the range of the flow core area gradually increases, and the range of the low-velocity area near the pipe wall gradually decreases.
FIGURE 10. Velocity distribution cloud diagram of the pipeline section under different flow velocities. (A) v=0.5 m/s. (B) v=1.0 m/s. (C) v=1.5 m/s. (D) v=2.0 m/s.
In the process of slurry pipeline transportation, when the transportation velocity is greater than the critical velocity, the slurry mainly moves in suspension, and the slurry stability is good. When the transportation velocity is less than the critical velocity, the slurry obviously has stratified movement and the solid particles in the bed will settle, which is not conducive to the safe transportation of the slurry.
According to the simulation calculation results, the slurry transportation velocity data at 0.05 d from the center line of the pipeline to the bottom are extracted after the slurry transportation velocity distribution in the pipeline section is stable under different design flow velocity conditions. The data show that when the inlet velocity increases from 0.5 m/s, 1.0 m/s, and 1.5 m/s to 2.0 m/s, the flow velocities at the measuring points near the pipe wall are 0.05 m/s, 0.06 m/s, 0.19 m/s, and 0.38 m/s, respectively, and the flow velocity at the pipe wall increases significantly.
To sum up, the design velocity of slurry pipeline transportation directly affects the movement state of slurry in the pipeline (Pinto et al., 2014; Singh et al., 2019). The larger the conveying speed, the larger will be the flow core area, and the slurry mainly moves in suspension. The smaller the conveying speed, the larger will be the non-flow core area, and the smaller the velocity of slurry near the pipe wall, the more obvious the slurry movement. Due to the settlement characteristics of gangue slurry, the stability is relatively low. Therefore, the conveying speed should be guaranteed during the conveying process. Considering the numerical simulation results and similar engineering experience, it is preliminarily determined that the slurry conveying speed should be greater than 1.0 m/s.
Whether the gangue slurry can be stably transported in the pipeline mainly depends on the movement state of the slurry (Chen et al., 2017). Ideally, the slurry transportation velocity is greater than the critical velocity to ensure that the slurry is in a turbulent state. However, according to the simulation results of slurry pipeline transportation velocity distribution, the velocity of slurry in the pipeline section will be redistributed due to the friction of the pipe wall. Even if the transportation velocity is greater than the critical velocity, the velocity of the slurry near the pipe wall during the transportation is relatively low. Therefore, the slurry near the pipe wall will have a push movement. During the push movement, the solid particles in the slurry will settle. With the increase of the transportation distance, the range of the push layer will continue to stack, which will eventually lead to the change in the slurry concentration in the pipeline (Calderon-Hernandez et al., 2020).
According to the calculation results, combined with the identification method of slurry quasi-homogeneous flow in engineering applications, the slurry mass concentration data at the top of the pipe (0.92 D from the bottom of the pipe) under different inlet speeds and different transportation distances are extracted, as shown in Figure 11.
Figure 11 shows that the slurry concentration changes during pipeline transportation, the concentration at the top of the pipeline gradually decreases, and the concentration at the bottom gradually increases. In general, the slurry shows sedimentation during transportation. With the increase in the transportation distance, the slurry settlement becomes more obvious. Under the same transportation distance, when the transportation speed increases from 0.5 m/s to 2.0 m/s, the smaller will be the change in the slurry concentration at the top of the pipeline, indicating that the stability of slurry transportation is better.
The ideal state of slurry pipeline stable transportation is homogeneous flow, but it is difficult to realize in practical engineering, so pseudo-homogeneous flow is usually used to judge whether the slurry can be transported safely. According to the engineering design standard for long-distance pipeline transportation of slurry, the pseudo-homogeneous flow needs to meet the requirements of C/Ca ≥ 0.8 (where C is the concentration at 0.92 Dn from the inner bottom of the pipe; Ca is the concentration at 0.5 Dn from the inner bottom of the pipe). By calculating the numerical simulation results according to this standard, the safe transportation distance of slurry at each transportation speed can be obtained, as shown in Figure 12. It can be seen that when the inlet speed is 0.5 m/s, 1.0 m/s, 1.5 m/s, and 2.0 m/s, the safe transmission distance is 3.5 km, 5.8 km, 9.3 km, and 17.0 km, respectively.
Through the aforementioned analysis, it can be seen that the design velocity of slurry pipeline transportation has a direct impact on the velocity distribution and settlement characteristics of the slurry. To ensure that the slurry is in a turbulent state and reduce the risk of pipe blockage caused by coarse particle deposition during slurry transportation, it is recommended that the transportation speed should be greater than 1.0 m/s by comprehensively considering the numerical simulation results and similar engineering experience. On this basis, by analyzing the settlement characteristics of slurry pipeline transportation, the safe transportation distance under each flow velocity is simulated and calculated. Combined with the actual working conditions of the project—the transportation distance is about 6 km—the transportation velocity of the slurry pipeline in the Huangling No. 2 coal mine is determined to be 1.5 m/s.
According to the research results, the Huangling No. 2 coal mine has completed the construction of an underground filling system. The excavated gangue is crushed from −300 mm to −3 mm through the three-level crushing system of a single-toothed roll crusher, a toothed roll crusher, and a squirrel cage crusher. Then, the unqualified powder of + 3 mm is removed by the relaxation screen with a hole diameter of 3 mm, and the gangue powder of −3 mm under the screen enters the horizontal mixer and is mixed with water into slurry with a mass concentration of 70%. Finally, the qualified slurry is pumped to the filling working face at a flow rate of 1.5 m/s through a slurry pipe with a diameter of 100 mm. Field operations are shown in Figure 13.
During field operation, through real-time monitoring of key positions of the slurry transmission pipeline, the data show that the pipeline pressure is normal. Before and after each operation, the underground staff carried out the clean water flushing process. During the whole joint commissioning process, there was no slurry sedimentation and pipe blockage, which was successfully applied.
Based on the second-phase grouting project of the Huangling No. 2 coal mine, to ensure the safe transportation of the gangue slurry to the working face and realize the filling of underground goaf, this paper systematically studies the key parameters of coal gangue slurry preparation and pipeline transportation through on-site sampling, laboratory experiments, and numerical simulation, combined with theoretical analysis. The main findings are as follows:
1) The coal gangue particle size grading with the upper limit of crushing particle size of 3 mm can be made into stable slurry, and the viscosity of the slurry is positively correlated with the concentration. When the concentration is below 70%, the viscosity growth is small, and when the concentration is above 70%, the viscosity growth significantly increased.
2) The transportation velocity of coal gangue slurry is distributed in concentric circles along the radial direction of the pipeline. The flow velocity of the pipeline section can be divided into the flow core zone with higher velocity in the middle and the non-flow core zone with lower velocity near the pipe wall. With the increase in the inlet velocity, the velocity near the pipe wall increases and the stability of slurry transportation increases. At the same time, with the increase in the conveying distance, the slurry sedimentation characteristics become increasingly prominent.
3) During the industrial test of grouting filling in the Huangling No. 2 coal mine, the upper limit of the gangue particle size is 3 mm, the slurry concentration is 70%, and the pipeline transportation speed is 1.5 m/s. The stability of slurry transportation is good during field operation.
The original contributions presented in the study are included in the article/Supplementary Material; further inquiries can be directed to the corresponding author.
LZ contributed to the conception of the study and helped perform the analysis with constructive discussions. WG performed the experiment and contributed significantly to analysis and manuscript preparation; TS performed the data analyses and wrote the manuscript.
This work was supported by the Key Science and Technology Projects of China Coal Group “Research on theory, technology and equipment of four-dimensional collaborative backfill of slurry pipeline in mining overburden fracture area of coal mine” (ZMYXM*CK-023).
Authors LZ and TS are/were employed by China Coal Energy Research Institute Co., Ltd.
The remaining author declares that the research was conducted in the absence of any commercial or financial relationships that could be construed as a potential conflict of interest.
All claims expressed in this article are solely those of the authors and do not necessarily represent those of their affiliated organizations, or those of the publisher, the editors, and the reviewers. Any product that may be evaluated in this article, or claim that may be made by its manufacturer, is not guaranteed or endorsed by the publisher.
Calderon-Hernandez, J. W., Sinatora, A., de Melo, H. G., Chaves, A. P., Mano, E. S., Leal Filho, L. S., et al. (2020). Hydraulic convey of iron ore slurry: Pipeline wear and ore particle degradation in function of pumping time. Wear 203272, 450–451. doi:10.1016/j.wear.2020.203272
Chen, D., Jiang, X., Lv, S., Lv, G., Ma, Z., Yan, J., et al. (2015). Rheological properties and stability of lignite washery tailing suspensions. Fuel 141, 214–221. doi:10.1016/j.fuel.2014.10.067
Chen, X., Zhou, J., Chen, Q., Shi, X., and Gou, Y. (2017). CFD simulation of pipeline transport properties of mine tailings three-phase foam slurry backfill. Minerals 7 (8), 149–168. doi:10.3390/min7080149
Cheng, H., Wu, S., and Zhang, X. (2020). Effect of particle gradation characteristics on yield stress of cemented paste backfill. Int. J. Min. Metall. Mat. 27 (1), 10–17. doi:10.1007/s12613-019-1865-y
Cruz, N., Forster, J., and Bobicki, E. R. (2019). Slurry rheology in mineral processing unit operations: A critical review. Can. J. Chem. Eng. 97 (7), 2102–2120. doi:10.1002/cjce.23476
Feng, G., Wang, Z., Qi, T., Du, X., Guo, J., Wang, H., et al. (2022). Effect of velocity on flow properties and electrical resistivity of cemented coal gangue-fly ash backfill (CGFB) slurry in the pipeline. Powder Technol. 396, 191–209. doi:10.1016/j.powtec.2021.10.050
Gao, R., Zhou, K., Zhou, Y., and Yang, C. (2020). Research on the fluid characteristics of cemented backfill pipeline transportation of mineral processing tailings. Alexandria Eng. J. 59 (6), 4409–4426. doi:10.1016/j.aej.2020.07.047
Hz, A., Ldgsb, C., Jkd, E., Pena-Polo, F., and Bencomo, A. (2017). Heavy oil slurry transportation through horizontal pipelines: Experiments and CFD simulations. Int. J. Multiph. Flow 91, 130–141. doi:10.1016/j.ijmultiphaseflow.2016.04.013
Jaworska-Jóźwiak, B. (2021). Influence of solids concentration on solid-liquid transportation in a lime production plant. WSEAS Trans. Appl. Theor. Mech. 16, 28–36. doi:10.37394/232011.2021.16.4
Lee, Seong W., HuCui, J., and Huang, Yan H. (2009). Particle characteristics and analysis using a laser-based phase Doppler particle analyzer (PDPA) and statistical method. Part. Sci. Technol. 27 (3), 553–561. doi:10.1080/02726350903328845
Li, M. Z., He, Y. P., Liu, W. H., Huang, C., and Jiang, R. h. (2020). Effect of adding finer particles on the transport characteristics of coarse-particle slurries in pipelines. Ocean. Eng. 218 (5), 108160. doi:10.1016/j.oceaneng.2020.108160
Li, M. Z., He, Y. P., Liu, Y. D., and Huang, C. (2018). Effect of interaction of particles with different sizes on particle kinetics in multi-sized slurry transport by pipeline. Powder Technol. 338 (6), 693–702. doi:10.1016/j.powtec.2018.07.088
Li, Z., Guo, L., Zhao, Y., Peng, X., and Kyegyenbai, K. (2022). A particle size distribution model for tailings in mine backfill. Metals 12 (4), 594. doi:10.3390/met12040594
Matoušek, V., Chára, Z., Konfršt, J., and Novotny, J. (2022). Experimental investigation on effect of stratification of bimodal settling slurry on slurry flow friction in pipe. Exp. Therm. Fluid Sci. 132, 110561. doi:10.1016/j.expthermflusci.2021.110561
Matousek, V. (2002). Pressure drops and flow patterns in sand-mixture pipes. Exp. Therm. Fluid Sci. 26 (6), 693–702. doi:10.1016/s0894-1777(02)00176-0
Pinto, T. S., Junior, D. M., Slatter, P. T., and Leal Filho, L. (2014). Modelling the critical velocity for heterogeneous flow of mineral slurries. Int. J. Multiph. Flow 65, 31–37. doi:10.1016/j.ijmultiphaseflow.2014.05.013
Qi, C., Chen, Q., Fourie, A., Zhao, J., and Zhang, Q. (2018). Pressure drop in pipe flow of cemented paste backfill: Experimental and modeling study. Powder Technol. 333, 9–18. doi:10.1016/j.powtec.2018.03.070
Rao, N. D., Thatoi, D. N., and Biswal, S. K. (2020). Rheological study and numerical analysis of high concentration iron ore slurry pipeline transportation. Mater. Today Proc. 22, 3197–3202. doi:10.1016/j.matpr.2020.03.457
Rathore, R. K., Gupta, P. K., and Kumar, N. (2021). Numerical investigation of zinc tailings slurry flow field in a horizontal pipeline. Mater. Today Proc. 45, 2702–2706. doi:10.1016/j.matpr.2020.11.541
Sadrossadat, E., Basarir, H., Luo, G., Karrech, A., Durham, R., Fourie, A., et al. (2020). Multi-objective mixture design of cemented paste backfill using particle swarm optimisation algorithm. Miner. Eng. 153, 106385. doi:10.1016/j.mineng.2020.106385
Senapati, P. K., and Mishra, B. K. (2017). Feasibility studies on pipeline disposal of concentrated copper tailings slurry for waste minimization. J. Institution Eng. 98 (3), 277–283. doi:10.1007/s40032-016-0309-y
Senapati, S., and Pothal, J. K. (2017). Some studies on rheological and pipeline transportation of concentrated limestone-water slurry. Int. J. Fluid Mech. Res. 44 (4), 349–356. doi:10.1615/interjfluidmechres.2017017172
Singh, M. K., Kumar, S., and Ratha, D. (2020). Computational analysis on disposal of coal slurry at high solid concentrations through slurry pipeline. Int. J. Coal Prep. Util. 42 (2), 116–130. doi:10.1080/19392699.2017.1346632
Singh, M. K., Kumar, S., Ratha, D., and Kaur, H. (2017). Design of slurry transportation pipeline for the flow of muti-particulate coal ash suspension. Int. J. Hydrogen Energy 42 (30), 19135–19138. doi:10.1016/j.ijhydene.2017.04.259
Singh, M. K., Ratha, D., Kumar, S., and Kumar, D. (2015). Influence of particle-size distribution and temperature on rheological behavior of coal slurry. Coal Prep. 36 (1), 44–54. doi:10.1080/19392699.2015.1049265
Singh, V., Kumar, S., and Mohapatra, S.Thapar Institute of Engineering and Technology, Patiala, Punjab, 147004, IndiaNational Institute of technology, Jamshedpur, India (2019). Modeling of erosion wear of sand water slurry flow through pipe bend using CFD. J. Appl. Fluid Mech. 12 (3), 679–687. doi:10.29252/jafm.12.03.29199
Vlasak, P., and Chara, Z. (2011). Effect of particle size distribution and concentration on flow behavior of dense slurries. Part. Sci. Technol. 29 (1), 53–65. doi:10.1080/02726351.2010.508509
Wang, S. Y., Wu, A. X., Ruan, Z. E., Yin, S. h., Wang, Y., Wang, S.-Y., et al. (2018). Simulation of long-distance pipeline transportation properties of whole-tailings paste with high sliming. J. Cent. South Univ. Sci. Technol. 49 (10), 141–150. doi:10.1007/s11771-018-3724-9
Wu, A., Ruan, Z., and Wang, J. (2022). Rheological behavior of paste in metal mines. Int. J. Min. Metall. Mat. 29 (4), 717–726. doi:10.1007/s12613-022-2423-6
Wu, A. X., Yang, Y., Cheng, H. Y., Chen, S. M., and Han, Y. (2018). Status and prospects of paste technology in China. Chin. J. Eng. 40 (5), 517. doi:10.13374/j.issn2095-9389.2018.05.001, No.
Keywords: slurry pipeline transportation, gangue slurry filling technology, particle size and grading, design velocity, gangue disposal
Citation: Gu W, Zhu L and Song T (2023) Research on key parameters of pipeline transportation of waste rock treatment in underground residual space. Front. Earth Sci. 10:1098674. doi: 10.3389/feart.2022.1098674
Received: 15 November 2022; Accepted: 09 December 2022;
Published: 30 January 2023.
Edited by:
Yun Zhang, Xi’an University of Science and Technology, ChinaReviewed by:
Yang Xiao, Xi’an University of Science and Technology, ChinaCopyright © 2023 Gu, Zhu and Song. This is an open-access article distributed under the terms of the Creative Commons Attribution License (CC BY). The use, distribution or reproduction in other forums is permitted, provided the original author(s) and the copyright owner(s) are credited and that the original publication in this journal is cited, in accordance with accepted academic practice. No use, distribution or reproduction is permitted which does not comply with these terms.
*Correspondence: Tianqi Song, c29uZ3RpYW5xaTIwMjNAMTYzLmNvbQ==
Disclaimer: All claims expressed in this article are solely those of the authors and do not necessarily represent those of their affiliated organizations, or those of the publisher, the editors and the reviewers. Any product that may be evaluated in this article or claim that may be made by its manufacturer is not guaranteed or endorsed by the publisher.
Research integrity at Frontiers
Learn more about the work of our research integrity team to safeguard the quality of each article we publish.